M1_PtC_WG_Work_Plan_11Aug2015
海尔自由式电饮料机说明书

Table of Contents1Installation81.1Dimension Requirements81.2Product dimensions91.3Unpacking, moving and positioning the range101.4Wall attachment and anti-tip device111.5Electrical requirements141.6Gas supply requirements161.7For the installer23NOTE: This appliance must be installed solely and exclusively by a qualified technician. Any technical procedures must be carried out by an authorized technician.The safety messages will inform you of potential hazards, on how to avoid the risk of injury and what can occur if the instructions are not followed.IMPORTANT: Installation, gas connections and grounding must conform to applicable codes. Observe all codes and ordinances in force.Do not store or use gasoline or other flammable vapors, liquids or materials near this or any other appliance.NOTE : This range is manufactured for use with natural gas. To convert the appliance to LP/Propane gas, see the instructions in the Gas Conversion Kit provided in the literature package.The proper gas supply connection must be available. See “Gas supply requirements”.In the State of Massachusetts, the following installation instructions apply: • Installation and repairs must be performed by a Massachusetts qualified or licensed contractor, plumber, or gas fitter.• If using a ball valve, it shall be the T-handle type.• A flexible gas connector, when used, must not exceed 3 feet.NOTE : This range is NOT designed for installation in manufactured (mobile)homes or in recreational vehicles (RVs).DO NOT install this range outdoors .• Read all instructions• Proper installation is your responsibility. Have a qualified technician install and ground this appliance in accordance with these installation instructions.• It is the responsibility of the installer to comply with installation information specified on the model/serial ID plate. The ID Plates are visibly located on the back of the appliance and on the oven door frame. These ID plates must never be removed.• ELECTRICAL GROUNDING REQUIRED: See the “Electrical Requirements” section. It is the customer’s responsibility:• To contact a qualified electrician to install the appliance• To ensure that the electrical system is adequate and conforms with the national ANSI / NFPA 70 ELECTRICAL CODE – latest edition – Or the CANADIAN ELECTRICAL CODE, C22.11 – 1 and C22.2 No. 01982 – or latest edition – and all local codes and ordinances. IMPORTANT: Observe all codes and ordinances in force.• Before you plug the electrical cord into an outlet, make sure that all the appliance controls are in the OFF position.CAUTION: To eliminate the risk of burns or fire caused by reaching over hot surface burners, do not store items directly above the rangetop.• Never modify or alter the construction of the appliance. For example, do not remove adjustable legs, panels, wiring or anti-tip brackets/screws.• Do not obstruct oven vents or openings for heat exhaust.• Test the appliance immediately after installation, following the instructions in this booklet. If the appliance does not work properly, disconnect it from the electrical power supply and call the service center. DO NOT attempt to repair the appliance.• All adjustments and servicing must be performed by qualified installers or service technicians.• Do not leave the packing material around the home. Sort the various items of waste and take them to the nearest specialized waste collection facility.How to read the user manualThis user manual uses the following reading conventions:1. Use instruction sequence.• Single use instruction.SAVE THESE INSTRUCTIONSCAUTION : This unit is designed as a cooking appliance. For safety purposes, never use it for warming the room or as a space heater.InstallationInformation for the qualified technician: installation, operationand inspection.Safety instructionsInformationAdvice1 Installation1.1 Dimension Requirementsside wall or other combustible material;2. min. cabinet opening width;3. upper cabinet to countertop;4. min. when bottom of wood or metal cabinet is protected by not less than ¼”(0.64 cm) flame retardant millboard covered with not less than No. 28 MSG sheet steel, 0.015" (0.4 mm) stainless steel, 0.024" (0.6 mm) aluminum or 0.020" (0.5 mm) copper. 35" (889 mm) min. clearance between the top of the cooking surface and the bottom of an unprotected wood or metal cabinet. 5. max. upper cabinet depth.Y - Grounded outletPosition within 11 7/8" (300 mm) from the left rear corner of the range.X - Gas supply linePosition within 11 7/8" (300 mm) from the right rear corner of the range.NOTE: Install with zero clearance sides and back.E N1.2 Product dimensionsOverall dimensions: Location of gas and electrical connection points.Check the location where the range is to be installed. The range should be positioned for convenient access in the kitchen.The cabinet opening dimensions that are shown must be used. The indicated dimensions are the minimum clearances.When installing a range under existing cabinets that do not satisfy the minimum cabinet clearances, install a rangehood over the cooking surface to avoid burn hazards.An air curtain or other overhead range hood, which operates by blowing adownward airflow onto a range, shall not be used in conjunction with the gas range unless the hood and range have been designed, tested in accordance with ANSI Z21.1 and listed by an independent testing laboratory for combination use. This type of ventilation system may cause ignition and combustion problems with the gas cooking appliance resulting in personal injury or unintended operation.NOTE: Observe all governing codes and ordinances.Any openings in the wall or floor where the range is to be installed must be sealed.Some cabinet and building materials are not designed to withstand the heat that the oven produces during baking. Check with your builder or cabinet supplier to make sure that the materials used will not discolor, delaminate or sustain other damage.1.3 Unpacking, moving andpositioning the range• It is recommended that the grates, the griddle plate and burner heads, burner caps, front kick panel and oven racks be removed to facilitate handling. This will reduce the weight for moving.• When positioning the appliance during installation, do not use the door handle to lift up or move this appliance.• Remove the outer carton and packing material from the shipping base.• Remove angle-mounting brackets from the range.• Due to the weight, a dolly/fork lift with soft rubber tread wheels should be used to move this unit. The weight must be supported uniformly across the bottom.• The floor under the legs should be protected (wood, strips, carpet, paneling, etc.) before pushing the unit into position.• The anti-tip device must be installed, and the gas and electrical connections should be made before the range is placed in its final position.• Ensure that the burner caps are correctly positioned on the burner bases on the rangetop.• Legs should be installed near to where the appliance will be used as they are not secure for long transit. Keep the unit raised so the legs can be screwed into their couplings, then lower the range gently to prevent the legs and mounting hardware from being subject to any undue strain. Instead of tilting the unit, it is recommended that a pallet or lift jack be used.• For proper performance the range must be leveled. The range is leveled by adjusting the four legs to ensure that the unit is on a perfectly level plane. To accomplish this, screw or unscrew the second part of the legs. The adjustment range of the screw is 1.37 inches (35 mm).CAUTION: This unit is designed asa cooking appliance. For safetypurposes, never use it for warmingthe room or as a space heater.NOTE: this appliance must onlyuse the specific leveling legsprovided by the manufacturer.CAUTION• Contact a qualified installer or contractor to determine the proper method for drilling holes through the wall or floor material (such as ceramic tile, hardwood, etc.)• Failure to follow these instructions may result in damage to wall or floor coverings.Instructions for wall mounting (primary system)1. Assemble the fastening bracket.2.Align the base of the hook on thefastening bracket with the base of the slot on the wall fastening plate.3.Align the base of the fastening bracketwith the ground and tighten the screws to fix the measurements.e 50 mm for the distance from theside of the appliance to the bracketholes.E N5.Move the bracket onto the wall andmark the position of the holes to be drilled in the wall.6.After drilling the holes in the wall, usewall plugs and screws to fasten the bracket to the wall.7.Push the cooker towards the wall, andat the same time, insert the bracket in the plate fastened to the rear of the appliance.Instructions for floor mounting (secondary system)The secondary anti-tip device is to be attached to the floor when it is not possible to install the primary system. After having positioned and leveled the appliance the bracket has to be anchored to the floor and engaged in the slots at the rear of the appliance.1. Assemble the fastening bracket as shown in the figure. Join the two parts without tightening them too much since there willbe other adjustments to make.NOTE : According to the type of floor, the installer should supply the suitable fastening systems (Type of screw recommended 3/8").2. After having positioned and leveled the appliance, move the bracket close to the rear of the appliance and anchor it to the floor.3. The bracket attachment should insert into one of the central slots at the rear.4. Lower the bracket attachment until anchoring the appliance slot, tighten the nuts previously assembled. The anti-tip device works properly only if the bracket attachment is securely anchored to the appliance.1.5 Electrical requirementsFAILURE TO FOLLOW THESEINSTRUCTIONS COULDRESULT IN LOSS OF LIFE, FIREOR ELECTRICAL SHOCK.E NMake sure that the power line ratingmatches the specifications indicated on the ID plate. The ID Plates are visibly located on the back of the appliance and on the oven door frame.These ID plates must never be removed.• Wire size and connections must conform to the requirements of the National Electrical Code, ANSI/NFPA 70ELECTRICAL CODE (*) – last edition or CSA Standard C22.1-94, Canadian Electrical code, Part 1 (**) and CSA C22.2 No. O-91 or latest edition and all local codes and ordinances for the kilowatt rating of the range.IMPORTANT: Observe all governing codes and ordinances.• Your local codes and ordinances, of course, take precedence over these instructions. Complete electricalconnections according to local codes and ordinances.• lf codes permit and a separate grounding wire is used, it isrecommended that the suitability of the ground path be checked by a qualified electrician.• Check with a qualified electrician if you are not sure whether the range isproperly grounded. Do not ground to a gas pipe.• A 120-volt, 60-Hz, AC-only, 15-ampere, fused electrical supply is required. A time-delay fuse or circuit breaker is recommended. It isrecommended that a separate circuitserving only this appliance be provided.Recommended Grounding Method For your personal safety, this range must be grounded. This range is equipped with a 3-prong grounding plug. To minimize possible shock hazard, the cord must be plugged into a mating 3-prong groundingreceptacle, grounded in accordance with the National ANSI/NFPA 70 Electrical Code (latest edition*) or the Canadian Electrical Code (CSA)** and local codes and ordinances. lf a mating receptacle is not available, it is the personal responsibility and obligation of the customer to have a properly polarized and grounded 3-prong outlet installed by a qualified electrician.1.6 Gas supply requirementsCopies of the standards listed above may be obtained from:* National Fire ProtectionAssociation, 1 Batterymarch Park, Quincy, Massachusetts 02169-7471** CSA International, 8501 East Pleasant Valley Road, Cleveland OH 44131-5575WarningExplosion hazard• Use a new AGA or CSA-approved gas supply line.• Install a shut-off valve.• Securely tighten all gas connections.• lf connected to LP, have a qualified technician ensure that the gas pressure does not exceed a 14" W.C.P.• Examples of qualified technicians include licensed heating personnel, authorized gas company personnel, and authorized service personnel.• Failure to do so can result in loss of life, explosion, or fire.NOTE :• Observe all codes and ordinances in force.• The range must be connected to a standard gas supply.E NThis installation must conform with all local codes and ordinances. In the absence of local codes, installation must conform to American National Fuel Gas Code, ANSI Z223.1/NFPA 54 or, in Canada, the Natural Gas and Propane Installation Code, CSA B149.1.If local codes permit, a flexible metalappliance conductor with the new AGA or CSA design certified, 4-5 feet (1.2-1.5 m) long, 1/2" or 3/4" ID NPT, isrecommended for connecting this range to the gas supply line.Do not bend or damage the flexible connector when moving the range. The pressure regulator has 3/8" female pipe threads. You will need to determine the fittings required, depending on the dimension of your gas supply line, the flexible metal connector and the shut-off valve.The appliance should be installed in rooms that have a permanent air supply inaccordance with the standards in force. The room where the appliance is installed must have enough air flow for the regular combustion of gas and the necessary air change in the room itself. The air vents, protected by grilles, must be the right size to comply with current regulations and positioned so that no part of them is obstructed, not even partially. The room must be kept adequatelyventilated in order to eliminate the heat and humidity produced by cooking: inparticular, after prolonged use, you are recommended to open a window or to increase the speed of any fans.Gas connectionConnect the adapter C (ISO 228/1 - ½ NPT) to the gas inlet of the appliance A being sure to insert the supplied gasket B .Apply a suitable sealing substance (such as Teflon tape) between pressure regulator D and adapter C .Connect the pressure regulator D to the adapter C put on in the previous step (the arrow on the back of the regulator points towards the gas inlet of the appliance).Apply a suitable sealing substance (such as Teflon tape) between pressure regulator D and adapter E (½ NPT - ½ NPT) (not supplied).Connect the adapter E to the pressure regulator D .WARNING : The tightening torque of adapter (C / E) must not be greater than 36 ozf - 10 Nm.Due to problems of overall dimensions at the back, screw in the pressure regulator so that it is sloped at 45° vs the wall at the back of the appliance. Test the applianceFollow these instructions to leak test the appliance:Use a brush and liquid detergent to test all gas connections for leaks. Bubbles around connections indicate a leak. If a leak appears, shut off the gas valve controls and adjust the connections. Then check the connections again. Remove all the detergent product from the range. Replace the parts on the burner and turn the knobs on the gas tap valves.NEVER TEST FOR GAS LEAKS WITH A MATCH OR OTHER FLAMES.Shut-off valveThe supply line must be fitted with an approved shut-off valve.This valve should be located in the same room as the range and should be in a location where it can be easily opened and closed.Do not block access to the shut-off valve. The valve is necessary for turning the gas tothe appliance on or off.EN Incoming line pressureIncoming line pressure upstream from theregulator must be 1” (2.5 cm) W.C.P. higherthan the manifold pressure in order to checkthe regulator. Incoming line pressure to theregulator should be as follows for operationand checking the regulator setting:• Natural Gas: Set pressure to 5” W.C.P.Incoming line pressure of 6” - 10 1/2”W.C.P maximum.• LP Gas: Set pressure to 10” W.C.P.Incoming line pressure 11”- 13” W.C.P.maximum.Lubricating the surface burner gas valvesOver time, the surface burner gas valvesmay become stiff or jam. Clean theminternally and relubricate. This operationmust be carried out by a qualifiedtechnician.NOTE: The range must be isolatedfrom the gas supply piping systemby turning off the respectivemanual shut-off valve during anypressure testing of the gas supplypiping system.Assembling the backguardThe backguard must always be positioned and secured correctly on the appliance.1. Position the backguard above the top, taking care to align the holes.2. Secure the backguard to the top by tightening screws.3. For the two outermost screws, also tighten the supplied spacers, as per figure.Positioning and levelling• After making the gas and electrical connections, screw on the four feet supplied with the appliance.The appliance must sit level on the floor to ensure stability.• Screw or unscrew the bottom part of the foot until the appliance is stable and level on the floor.The backguard provided is an integral part of the product; it must be fastened to the appliance priorto installation.Heavy applianceRisk of damage to the appliance• Insert the front feet first and then the rearones.E NInstalling the front skirtingThe front skirting must always be positioned and secured correctly on the appliance.1. Use a screwdriver to remove the front screws underneath the storage compartment.2. Position the front skirting at the bottom of the appliance and line up the holes of the front skirting with the holes on the base of the appliance.3. Fasten the front skirting to the applianceusing the previously removed screws.Installing the side skirtingAfter installing the front skirting, the side skirting can be fastened correctly to the appliance.1. Use a screwdriver to remove the rear screw underneath the storage compartment.2. Position the side skirting on the lower side section of the appliance below the storage compartment.3. Insert the tabs on the side skirting into the slots on the rear part of the front skirting.4. Line up the hole on the side skirting with the rear hole on the base of the appliance.5. Fasten the side skirting to the appliance using the previously removed screw.6. Repeat the operations described abovefor the other side skirting section.23E N1.7 For the installer• The plug must remain accessible after the installation is complete. Do not kink or trap the mains connection cable.• The appliance must be fitted according to the installation diagrams.• Do not attempt to turn or stress the threaded elbow on the manifold. You risk damage to this part of the appliance which may void the manufacturer’s warranty.• Before leaving check all connections for gas leaks with soap and water. DO NOT use a naked flame for detecting leaks.• Ignite all burners individually and concurrently to ensure correct operation of the gas valves, burner and ignition.• Turn the gas knobs to the low position and observe stability of the flame for each burner individually and all together.• In case the appliance fails to operate correctly after all checks have been carried out, refer to the Authorised Assistance Centre in your area.• When satisfied with the appliance, please instruct the user on the correct method of operation.PAGE INTENTIONALLY LEFT BLANK。
Guardmaster 440C-CR30 Safety Relay 版本11 目录号440C-CR

Release NotesOriginal InstructionsGuardmaster 440C-CR30 Safety Relay, Revision 11Catalog Number 440C-CR30-22BBBSummary of ChangesThis publication contains the following new or updated information. This list includes substantive updates only and is not intended to reflect all changes.About This PublicationThese release notes supplement the existing documentation supplied with your product. Read this document before using Guardmaster® 440C-CR30 safety relays.Firmware Revision HistoryAvailability of Enhancements and Anomaly FixesEnhancements are available in the safety relay only if it is at the required firmware revision or higher and the Connected Components Workbench™ or Studio 5000 Logix Designer® project contains a safety relay that is configured with the required firmware revision or higher. If the project contains a safety relay revision that is lower than the required revision for an enhancement, then the project is still valid but the enhancement will not be available until the project is upgraded to the minimum supported revision.Fixes for firmware anomalies are available as long as the safety relay firmware revision is at the minimum revision or higher. The configured safety relay revision must be of the same major revision.The following tables provide a list of enhancements, known anomalies, and corrected anomalies for the CR30 safety relay firmware revisions.EnhancementsTopicPage Updated Firmware Revision History 1Updated Table 22Updated image in step 23Revision Description6.004First revision release [safety firmware 0A.01]6.006Minor revision release [safety firmware 0A.02]7.006Major revision release [safety firmware 0A.02]8.013Major revision release [safety firmware 0A.02]9.004Major revision release [safety firmware 0A.02]10.004Major revision release [safety firmware 0A.03]10.009Minor revision release [safety firmware 0A.03]10.010Minor revision release [safety firmware 0A.03]10.011Minor revision release [safety firmware 0A.03]Table 1 - EnhancementsEnhancement (1)DescriptionAvailable From Firmware RevisionLock control function support New Lock Control function is now supported forissuing an unlock request to a safety gate withguard locking.10.004Mode selection function support New Mode Selection Safety Monitoring Function is now supported.10.004Mute function enhancements New Muting function block has been enhanced to support a mute enable input, a mute fault manual monitored reset and now offers a secondary output based on the override status.10.004Status function supportNew Status functions for monitoring andannunciating function block faults or ‘waiting for reset’ conditions.10.004Reusable feedback supportNew ability to apply feedback inputs to multiple Safety Output Functions.10.004Single input And withRestartenhancement New ability for the And with Restart logic function to support one input.10.004PanelView Plus Tag browsing support With release 8.00 of FactoryTalk® View Studio, PanelView™ Plus can communicate to CR30 safety relays using EDS parameter browsing over EtherNet/IP™.9.004Nesting of Logic Level Function blocksNew ability to use the output state of a logic block immediately above another logic block as an input condition.9.004Inverting of Logic Level Inputs/Outputs New ability to invert (logical NOT) of inputs and outputs of Logic Level function blocks.9.004Output Loop Safety Monitoring Function support New Output Loop Safety Monitoring Function that allows the logical state of a Safety Output Function to be used as an input condition.9.004RS Flip-Flop Logic Function support New RS Flip-Flop Logic function is now supported in the Logic level columns of the Logic Editor.9.004440C-ENET plug-in supportThe EtherNet/IP plug-in provides both I/O messaging and explicit messaging. The safety relay can now be configured over EtherNet/IP using either Connected Component Workbench or an Add-on Profile (AOP) in Studio 5000 Logix Designer application.8.013Standard Signal Safety Monitoring Function support New Standard Signal Safety Monitoring Function that allows the use of standard control signals from digital plug-ins or communication ports to be used in the logic of the safety relay.8.013Project Upgrade featureProjects developed for earlier versions of firmware can be automatically converted into the latest version of firmware supported.8.0132080-MEMBAK-RTC plug-in support Project backup and restore are supported on CR30 safety relays through the 2080-MEMBAK-RTC module.7.0062080-IQ4 plug-in supportThe 2080-IQ4 digital input plug-in provides 4-pt standard rated 12/24V DC digital input expansion. It can be used in slot 1 and/or slot 2 module bays.7.0062Rockwell Automation Publication 440C-RN001H-EN-P - December 2020Guardmaster 440C-CR30 Safety Relay, Revision 11 Release NotesAnomalies2080-OB4 plug-in support The 2080-OB4 digital output plug-in provides 4-pt standard rated 12/24V DC sourcing output expansion. It can be used in slot 1 and/or slot 2 module bays.7.0062080-OW4I plug-in supportThe 2080-OW4I relay output plug-in provides 4-pt standard rated relay output, individually isolated, 2A expansion. It can be used in slot 1 and/or slot 2 module bays.7.006Unique function block name supportUnique names can be assigned to the Safety Monitoring Function blocks and the Safety Output Function blocks. These names are stored in the project that is loaded to the safety relay and can be recovered by an upload.7.006Password protection Software connections including Upload, Download,and Connect can be restricted through passwordprotection.7.006(1)For more information, see publication 440C-UM001.Table 2 - Known and Corrected AnomaliesAnomalyDescriptionAffected Firmware Revisions Corrected Firmware Revision Discrepancy Fault on Power-upDevices with pulse testing outputs would sometimes cause a discrepancy fault in the CR30 safety relay upon power-up. On power-up, the Channel Test during the first logic scan when transitioning from self-test to run mode has been removed to help prevent the discrepancy fault.See publication 440C-UM001 for details.6.0046.0067.0068.0139.00410.00410.00910.01010.011Memory Module Incompatibility Safety relay fails to recognize 2080-MEMBAK-RTC memory modules that are manufactured on or after 2016/02/11.APBC000280011 6.0046.0067.0068.0139.00410.00410.00910.010Memory Module Update When updating a safety relay from a previous firmware revision to firmware 10 using thememory module the restore operation must be performed twice (the first process updates thefirmware, the second process restores the user configuration). 6.004 6.0067.0068.0139.004Configuration loss on power cycleDuring specific power down conditions, the safety relay could be interrupted while writing a fault condition to its nonvolatile memory. On power up, the memory is evaluated as corrupted and the user configuration is discarded.APBC00026898 6.0046.0067.0068.0139.00410.00410.009Connection failure with Add-on Profile (AOP) major revision 1The safety relay rejects an I/O connection that originates from the safety relay AOP (versions 1.013 and versions 1.014) when Compatible Keying and Major Revision 8 or later is configured.APBC000271569.00410.004Download faultA download could result in a major fault on the safety relay, Type 06, Code 20 – Configuration Fault.APBC000251087.0068.0139.00410.004Download over Ethernet faultA download over Ethernet to the safety relay could result in a Type 05, Code 00 – Internal Safety Synch Fault.APBC000236608.0139.00410.004Unexpected disconnect from safety relay Occasionally Connected ComponentsWorkbench software would unexpectedly disconnect while connected to a password protected safety relay.APBC000248668.0139.004Table 1 - Enhancements (Continued)Enhancement (1)DescriptionAvailable From Firmware RevisionLocked by another connection error Attempts to connect to the safety relay arerejected and erroneously reports “CR30 has been locked by another, new connection is not allowed.”APBC000248678.0139.004No reconfiguration after EEPROM fault After the safety relay experiences a memory fault (Type 5 Code 00), the safety relay does not accept a new download.APBC00024866 6.0046.0067.0068.0139.004Muting L-Type reports incorrect fault description Under specific configuration conditions, the Muting T Type function block incorrectly reports a mute sensor timing fault when actually a sequence fault occurred.APBC000237318.0139.004Network address changes require power cycle Changes to the 440C-ENET Ethernet portsettings, duplicate IP address detection, and DHCP vs. static IP address settings may require a power cycle to take effect.APBC000241338.0139.004Power-up faultVariations in 24V DC supply power to the CR30 safety relay during power-up could lead to power fault: Type 04, Code 01.APBC000244266.0046.0067.0068.013Discrepancy fault after power-upVariations in 24V DC supply power to the CR30 safety relay during power-up could lead to adiscrepancy fault on any dual channel Safety Monitoring Function: “One channel open after reset” 6.0046.0067.0068.013Empty fault logModbus reporting of the fault log always returns 0, indicating no fault, even if faults are present in the log.APBC00025011 6.0046.0067.0068.013Incorrect Mode The safety relay will return to Run Mode after downloading a valid configuration to a unit that has experienced a nonrecoverable fault.APBC000257716.0046.0067.0068.013Modbus fault state cleared in Program Mode The safety relay does not report faultinformation over Modbus once the safety relay is placed in Program Mode.6.0046.0067.0068.013Memory module firmware update failure The memory module is unable to upgrade a firmware revision 7 safety relay to version 8 or later 7.006L-Type muting override conditionOverride for L-Type muting cannot be initiated when only the light curtain is interrupted (no mute sensors).6.0046.0067.006Two Hand Control at power up Two Hand Control does not fault at power up if buttons are pressed. 6.0046.0067.006Override conditionsFor muting applications, mute sensor interrupted or timing faults should be only conditions that allow override to be initiated.6.0046.0067.006Serial port doesnot shutdownWhen the serial port is configured as shutdown,it still responds to Modbus messages.APBC00020590 6.0046.0067.006Input filters greater than 200 ms create nonrecoverable fault When an input filter of greater than 200 ms is configured on any Safety Monitoring function, a nonrecoverable fault is generated when the configuration is downloaded to the safety relay.APBC00020589 6.0046.0067.006Missing plug-in slot 1 without fault log entry A missing plug-in module configured in slot 1 and not actually present results in a fault but no fault log entry is created.APBC00018493 6.0046.0067.006Plug-inmismatch with duplicate fault log entriesA mismatch between the plug-in present on slot 1 and the actual plug-in present results in duplicate entries in the fault log.APBC000205086.0046.0067.006Plug-in outputs fail to configure When Plug-in outputs terminals are selected asoutputs for Safety Output Functions, they fail toturn on when the corresponding Safety OutputFunction turns on.APBC000201036.004 6.006Table 2 - Known and Corrected Anomalies (Continued)AnomalyDescriptionAffected Firmware Revisions Corrected Firmware RevisionRockwell Automation Publication 440C-RN001H-EN-P - December 20203Guardmaster 440C-CR30 Safety Relay, Revision 11 Release NotesUse DMK FilesFirmware for the CR30 safety relay beginning with firmware revision 10.009 uses a new file format called *.DMK. These files are named for easy identification, for example: 440C-CR30-22BBB_10.009.dmk.ControlFLASH™ software, version 13 or later, supports the format. ControlFLASH software is automatically installed as part of Studio 5000 Logix Designer application installation, version 28 or later. You can download ControlFLASH software from the Rockwell Automation Product Compatibility and Download Center (PCDC - rok.auto/pcdc ) separately, if necessary.You are not required to install the new firmware file format. When you download *.DMK files from the Rockwell Automation PCDC, ControlFLASH softwareautomatically saves the folder location where the *.DMK files were downloaded. As a result, ControlFLASH software can easily locate *.DMK files.You can use the Browse option to access and configure the folders that ControlFLASH software monitors as shown:Upgrade Safety Relay FirmwareThis procedure shows you how to update the firmware in a CR30 safety relay using ControlFLASH. To download the latest CR30 safety relay firmware revision, go to the PCDC (PCDC - rok.auto/pcdc ) and select your desired revision.On CR30 safety relays, you can upgrade your safety relays through the Ethernet port on the 440C-ENET plug-in module and the USB.Through USB1.Verify successful RSLinx® Classic communications with you CR30 safety relay by USB using RSWho. The CR30 safety relay uses the AB_VBP-x driver.2.Start ControlFLASH (Start > All Programs > FLASH Programming Tools > ControlFlash) and click Next >.3.Select the catalog number of the CR30 safety relay (440C-CR30-22BBB) that you are updating and click Next >.4.Select the safety relay in the browse window and click OK.Communication fault without fault log entryIf the host microprocessor within the CR30safety relay loses communication with the safety processors a fault is generated but no fault log entry is createdAPBC00020302 6.0046.006Fault log index changes after power cycleAfter a power cycle of the safety relay,previously detected faults index by one within the fault log.APBC000186376.004 6.006Inverted image of downloadprogram notcompared After performing a download, the inverted datais sent back from the safety relay to Connected Components Workbench software but not compared as an additional diagnostic check.APBC00020430 6.004 6.006Download through virtual image failsDownload of a program to the safety relay occasionally fails due to connection timeout when downloading through a virtual image.6.004 6.006ATTENTION: All Ethernet settings are reverted to factory default after a ControlFLASH firmware update.Table 2 - Known and Corrected Anomalies (Continued)AnomalyDescriptionAffected Firmware Revisions Corrected Firmware Revision IMPORTANTTo update your safety relay successfully, it must be in Program Mode or BOOT Loader mode. The safety relay can be placed into Program Mode from the Graphic Overview screen in Connected Component Workbench software, the Logic Configuration tab in the Logix Designer module profile or placed in BOOT Loader mode by holding the MEM/ID button located below the USB port on the safety relay during power-up.Publication 440C-RN001H-EN-P - December 2020 | Supersedes Publication 440C-RN001G-EN-P - April 2016Copyright © 2020 Rockwell Automation, Inc. All rights reserved. Printed in the U.S.A.Rockwell Otomasyon Ticaret A.Ş. Kar Plaza İş Merkezi E Blok Kat:6 34752 İçerenköy, İstanbul, Tel: +90 (216) 5698400 EEE Yönetmeliğine UygundurAllen-Bradley, Connected Components Workbench, ControlFLASH, expanding human possibility, FactoryTalk, Guardmaster, PanelView,Rockwell Automation, RSLinx, and Studio 5000 Logix Designer are trademarks of Rockwell Automation, Inc.EtherNet/IP is a trademark of ODVA, Inc.Trademarks not belonging to Rockwell Automation are property of their respective companies.Your comments help us serve your documentation needs better. If you have any suggestions on how to improve our content, complete the form at rok.auto/docfeedback .For technical support, visit rok.auto/support.Waste Electrical and Electronic Equipment (WEEE)Rockwell Automation maintains current product environmental compliance information on its website at rok.auto/pec .At the end of life, this equipment should be collected separately from any unsorted municipal waste.5.Verify the revision, and click Next > to continue.6.Click Finish.7.Click Yes to initiate the update.The next screen shows the download progress.If you see the following error message, verify that the safety relay is in Run mode. If so, change to Program or BOOT Loader mode by pressing theMEM/ID switch during power-up of the CR30 safety relay, click OK, and try again.When the update is complete, you see a screen similar to the following.Click OK to complete the update.。
ArmorPOINT RTD 和热电枪输入模块目录号 1738-IR2M12、1738-IT2IM1

Installation InstructionsArmorPOINT RTD and Thermocouple Input ModulesCatalog numbers 1738-IR2M12, 1738-IT2IM12, Series A Table of ContentsTopic Page Important User Information2 Environment and Enclosure3 Preventing Electrostatic Discharge3About the Module4Mount the I/O Base5Install the Module6 Remove the Module from the Mounting Base6Wire the Module7 Communicate with the Module8 Interpret Status Indicators10 Specifications122 ArmorPOINT RTD and Thermocouple Input ModulesImportant User InformationSolid-state equipment has operational characteristics differing from those of electromechanical equipment. Safety Guidelines for the Application, Installation and Maintenance of Solid State Controls (Publication SGI-1.1 available from your local Rockwell Automation sales office or online at/literature/) describes some important differences betweensolid-state equipment and hard-wired electromechanical devices. Because of this difference, and also because of the wide variety of uses for solid-state equipment, all persons responsible for applying this equipment must satisfy themselves that each intended application of this equipment is acceptable.In no event will Rockwell Automation, Inc. be responsible or liable for indirect or consequential damages resulting from the use or application of this equipment.The examples and diagrams in this manual are included solely for illustrative purposes. Because of the many variables and requirements associated with any particular installation, Rockwell Automation, Inc. cannot assume responsibility or liability for actual use based on the examples and diagrams.No patent liability is assumed by Rockwell Automation, Inc. with respect to use of information, circuits, equipment, or software described in this manual.Reproduction of the contents of this manual, in whole or in part, without written permission of Rockwell Automation, Inc., is prohibited.Throughout this manual, when necessary, we use notes to make you aware of safety considerations.Publication 1738-IN005B-EN-E - January 2013ArmorPOINT RTD and Thermocouple Input Modules 3Publication 1738-IN005B-EN-E - January 2013Environment and EnclosurePreventing Electrostatic DischargeATTENTION: This equipment is intended for use in overvoltage Category II applications (as defined in IEC 60664-1), at altitudes up to 2000 m (6562 ft) without derating.This equipment is considered Group 1, Class A industrial equipment according to IEC/CISPR 11. Without appropriate precautions, there may be difficulties with electromagnetic compatibility in residential and other environments due to conducted and radiated disturbances.This equipment is supplied as enclosed equipment. It should not require additional system enclosure when used in locations consistent with theenclosure type ratings stated in the Specifications section of this publication. Subsequent sections of this publication may contain additional information regarding specific enclosure type ratings, beyond what this product provides, that are required to comply with certain product safety certifications.In addition to this publication, see:•Industrial Automation Wiring and Grounding Guidelines, RockwellAutomation publication 1770-4.1, for additional installation requirements.•NEMA Standard 250 and IEC 60529, as applicable, for explanations of thedegrees of protection provided by different types of enclosure.ATTENTION: This equipment is sensitive to electrostatic discharge, which can cause internal damage and affect normal operation. Follow these guidelines when you handle this equipment:•Touch a grounded object to discharge potential static.•Wear an approved grounding wriststrap.•Do not touch connectors or pins on component boards.•Do not touch circuit components inside the equipment.•Use a static-safe workstation, if available.•Store the equipment in appropriate static-safe packaging when not in use.4 ArmorPOINT RTD and Thermocouple Input ModulesPublication 1738-IN005B-EN-E - January 2013About the ModuleThe ArmorPOINT™ I/O family consists of modular I/O modules. The sealed IP67 housing of these modules requires no enclosure. Note that environmental requirements other than IP67 may require an additional appropriate housing. I/O connectors are sealed M12 (micro) style. The mounting base ships with the module. The 1738-IR2M12 module is shown here.ArmorPOINT RTD and Thermocouple Input ModuleDescriptionDescription1Connector M12-A 3LED indicators2Connector M12-B3ArmorPOINT RTD and Thermocouple Input Modules 5Publication 1738-IN005B-EN-E - January 2013Mount the I/O BaseMount the I/O base on a wall or panel, using the screw holes provided in the base.Mounting Diagram for ArmorPOINT Base with AdapterFollow the instructions to install the mounting base.y out the required points as shown above in the drilling dimension diagram.2.Drill the necessary holes for M4 (#8) machine or self-tapping screws.3.Mount the base using M4 (#8) screws.4.Ground the system using the ground lug connection. The ground lug connectionis also a mounting hole.Mounting BaseIMPORTANTThe module must be mounted on a grounded metal mounting plate or otherconductive surface.KeyswitchGround lug connectionLatching mechanism6 ArmorPOINT RTD and Thermocouple Input ModulesInstall the ModuleFollow the instructions to install the ArmorPOINT input module.ing a bladed screwdriver, rotate the keyswitch on the mounting base clockwiseuntil the number 6 aligns with the notch in the base.2.Position the module vertically above the mounting base. The module bridgestwo bases.3.Push the module down until it engages the latching mechanism. Y ou hear aclicking sound when the module is properly engaged. The locking mechanismlocks the module to the base.Remove the Module from the Mounting BaseFollow the instructions to remove the module from the mounting base.1.Insert a flat blade screwdriver into the slot of the orange latching mechanism.2.Push the screwdriver toward the I/O module to disengage the latch. The modulelifts up off the base.3.Pull the module off the base.Publication 1738-IN005B-EN-E - January 2013ArmorPOINT RTD and Thermocouple Input Modules 7Publication 1738-IN005B-EN-E - January 2013Wire the ModuleFollow the wiring instructions for the ArmorPOINT input modules.1738-IR2M121738-IT2IM12IMPORTANTAnalog modules have earth grounded metal rings. This should be considered when choosing shielded cables and grounding techniques.ATTENTION: Make sure all connectors and caps are securely tightened to properly seal the connections against leaks and maintain IP67 requirements.(View into connector) Pin 1 No connectPin 2 Input 0A (M12-A)Input 1A (M12-B) Pin 3 Input 0C (M12-A)Input 1C (M12-B) Pin 4 Input 0B (M12-A)Input 1B (M12-B) Pin 5 No connect(View into connector) Pin 1 CJC +Pin 2 TC 0 + (M12-A)TC 1 + (M12-B) Pin 3 CJC -Pin 4 TC 0 - (M12-A)TC 1 - (M12-B) Pin 5 No connect8 ArmorPOINT RTD and Thermocouple Input ModulesPublication 1738-IN005B-EN-E - January 2013Communicate with the ModuleI/O messages are sent to (consumed) and received from (produced) the ArmorPOINT I/O modules. These messages are mapped onto the processor’s memory. TheArmorPOINT RTD I/O input module produces 6 Bytes of input data (scanner Rx – status) and fault status data. The ArmorPOINT thermocouple I/O input module produces 8 Bytes of input data (scanner Rx – status) and fault status data. They do not consume I/O data (scanner Tx).Default Data Map – 1738-IR2M12Message size: 6 Bytes15141312111009080706050403020100Produces (scanner Rx)Input channel 0 high byte Input channel 0 low byte Input channel 1 high byteInput channel 1 low byte Status byte for channel 1Status byte for channel 0ORURHHA LLA HA LACM CFORURHHA LLA HA LACM CFConsumes (scanner Tx)No consumed data Where:OR = Overrange; 0 = No error, 1 = Fault UR = Underrange; 0 = No error, 1 = FaultHHA = High/High Alarm; 0 = No error, 1 = Fault LLA = Low/Low Alarm; 0 = No error, 1 = Fault HA = High Alarm; 0 = No error, 1 = Fault LA = Low Alarm; 0 = No error, 1 = FaultCM = Calibration Mode; 0 = Normal, 1 = Calibration mode CF = Channel Fault Status; 0 = No error, 1 = FaultArmorPOINT RTD and Thermocouple Input Modules 9Publication 1738-IN005B-EN-E - January 2013Default Data Map – 1738-IT2IM12Message size: 6 Bytes15141312111009080706050403020100Produces (scanner Rx)Input channel 0 high byte Input channel 0 low byte Input channel 1 high byteInput channel 1 low byte Status byte for channel 1Status byte for channel 0OR UR HHA LLA HA LACM CFORURHHA LLA HA LACM CFORURCold junction temperature(Selectable channel 0, channel 1, or average of both channels 0 and 1)Consumes (scanner Tx)No consumed data Where:OR = Overrange; 0 = No error, 1 = Fault UR = Underrange; 0 = No error, 1 = FaultHHA = High/High Alarm; 0 = No error, 1 = Fault LLA = Low/Low Alarm; 0 = No error, 1 = Fault HA = High Alarm; 0 = No error, 1 = Fault LA = Low Alarm; 0 = No error, 1 = FaultCM = Calibration Mode; 0 = Normal, 1 = Calibration mode CF = Channel Fault Status; 0 = No error, 1 = Fault10 ArmorPOINT RTD and Thermocouple Input ModulesPublication 1738-IN005B-EN-E - January 2013Interpret Status IndicatorsThis module has the following indicators:•Adapter, DeviceNet and POINTBus status indicators •System and Adapter power indicators•Individual I/O status indicators for inputs and outputsIndicator Status for ModulesStatusDescriptionModule statusOff No power applied to device.Green Device operating normally.Flashing green Device needs commissioning due to missing, incomplete, or incorrect configuration.Flashing red Recoverable fault.RedUnrecoverable fault – may require device replacement.Flashing red/green Device is in self-test.I/O status indicatorNetwork status indicatorModule status indicator 1738-IR2M12ArmorPOINT RTD and Thermocouple Input Modules 11Publication 1738-IN005B-EN-E - January 2013Network status OffDevice is not online:- Device has not completed dup_MAC-id test.- Device not powered – check module status indicator.Flashing green Device is online but has no connections in the established state.Green Device is online and has connections in the established state.Flashing red One or more I/O connections are in timed-out state.RedCritical link failure – failed communication device. Device detected error that prevents it from communicating on the network. Possible duplicate MAC ID or baud rate mismatch.Flashing red/green Communication faulted device – the device has detected anetwork access error and is in communication faulted state. Device has received and accepted an Identity Communication Faulted Request – long protocol message.I/O statusOff Module in CAL mode.Solid green Normal (channel scanning inputs).Flashing green Channel being calibrated.Solid red Major channel fault.Flashing redChannel at end of range (over or under).Indicator Status for ModulesStatusDescription12 ArmorPOINT RTD and Thermocouple Input ModulesPublication 1738-IN005B-EN-E - January 2013SpecificationsArmorPOINT RTD and Thermocouple Input Modules – 1738-IR2M12, 1738-IT2IM12AttributeValueInputs per module 1738-IR2M12 – 2 single-ended, nonisolated1738-IT2IM12 – 2 differential, individually isolatedResolution1738-IR2M12 – 16 bits, 9.5 mV/cnt, 0.03 °C/cnt (Pt385 @ 25 °) 1738-IT2IM12 – 15 bits plus sign, 2.5 mV/cnt Thermocouple type (and resolution average over span)1738-IT2IM12 only Sensor Range Resolution (average over span)Type B 30…1820 °C 3 counts/°C Type C 0…2315 °C 6 counts/°C Type E -270…1000 °C 24 counts/°C Type J -210…1200 °C 21 counts/°C Type K -270…1372 °C 13 counts/°C Type N -270…1300 °C 11 counts/°C Type R -50…1768.1 °C 4 counts/°C Type S -50…1768.1 °C 4 counts/°C Type T-270…400 °C15 counts/°CRTD sensors supported1738-IR2M12 only100 Ω Pt α = 0.00385 Euro (-200…870 °C) 200 Ω Pt α = 0.00385 Euro (-200…630 °C) 100 Ω Pt α = 0.003916 U.S. (-200…630 °C) 200 Ω Pt α = 0.003916 U.S. (-200…630 °C) 10 Ω Cu α = 0.00427 (-200…260 °C) 100 Ω Ni α = 0.00618 (-60…250 °C) 120 Ω Ni α = 0.00672 (-60…250 °C) 120 Ω Ni α = 0.00618 (-60…250 °C)Cold junctioncompensation range 1738-IT2IM12 – 0…70 °C Input range 1738-IR2M12 – 0…600 Ω 1738-IT2IM12 – ±75 mV Absolute accuracy (1)0.1% full scale @ 25 °C Accuracy drift w/temp30 ppm/°CArmorPOINT RTD and Thermocouple Input Modules 13Publication 1738-IN005B-EN-E - January 2013Input update rate (per module)1738-IR2M1240 ms @ Notch = 50 Hz33 ms @ Notch = 60 Hz (default) 20 ms @ Notch = 100 Hz 17 ms @ Notch = 120 Hz 10 ms @ Notch = 200 Hz 8 ms @ Notch = 240 Hz 7 ms @ Notch = 300 Hz 5 ms @ Notch = 400 Hz 4 ms @ Notch = 480 Hz 1738-IT2IM1220 ms @ Notch = 50 Hz17 ms @ Notch = 60 Hz (default) 10 ms @ Notch = 100 Hz 8 ms @ Notch = 120 Hz 5 ms @ Notch = 200 Hz 4 ms @ Notch = 240 Hz 3 ms @ Notch = 300 Hz 3 ms @ Notch = 400 Hz 2 ms @ Notch = 480 HzStep response (per channel)60 ms @ Notch = 50 Hz 50 ms @ Notch = 60 Hz 30 ms @ Notch = 100 Hz 25 ms @ Notch = 120 Hz 15 ms @ Notch = 200 Hz 13 ms @ Notch = 240 Hz 10 ms @ Notch = 300 Hz 8 ms @ Notch = 400 Hz 6 ms @ Notch = 480 Hz Input resistance 1738-IT2IM12 only – 1 M ΩInput impedance 1738-IT2IM12 only – 100 K ΩConversion typeDelta Sigma Common mode rejection ratio 120 dBNormal mode rejection ratio100 dB -3 dbNotch filter13.1 Hz @ Notch = 50 Hz 15.7 Hz @ Notch = 60 Hz 26.2 Hz @ Notch = 100 Hz 31.4 Hz @ Notch = 120 Hz 52.4 Hz @ Notch = 200 Hz 62.9 Hz @ Notch = 240 Hz 78.6 Hz @ Notch = 300 Hz 104.8 Hz @ Notch = 400 Hz 125.7 Hz @ Notch = 380 Hz Data format Signed integerMaximum overload1738-IR2M12 – No input protection1738-IT2IM12 – Input not overvoltage protected(1)Includes offset, gain, non-linearity and repeatability error termsArmorPOINT RTD and Thermocouple Input Modules – 1738-IR2M12, 1738-IT2IM12AttributeValue14 ArmorPOINT RTD and Thermocouple Input Modules Publication 1738-IN005B-EN-E - January 2013General SpecificationsAttributeValueMounting base screw torque M4 (#8) screw,0.85 Nm (7.5 lb-in.) in aluminum, 1.8 Nm (16 lb-in.) in steel Calibration Factory-calibratedPOINTBus current 1738-IR2 – 220 mA @ 5V DC 1738-IT2I – 175 mA @ 5V DC Power dissipation, max 1.0 W Thermal dissipation, max 3.3 BTU/hrIsolation voltage Tested at 50V rms (1738-IT2I has isolation between individual channels)Dielectric test 1000V rms flash for 1s External DC power No external power requiredLED indicators1 green/red – module status indicator, logic side 1 green/red – network status indicator, logic side2 green/red – input status indicators, logic side Dimensions, HxWxD 31.75 x 66.80 x 107.95 mm (1.25 x 2.63 x 4.25 in.)Weight0.289 kg (0.637 lb)Enclosure type rating Meets IP65/66/67 (when marked)Wiring category (1) 1 – on signal ports Keyswitch position6(1)Use this Conductor Category information for planning conductor routing. Refer to Industrial Automation Wiring and Grounding Guidelines, publication 1770-4.1.Environmental SpecificationsAttributeValueTemperature, operatingIEC 60068-2-1 (Test Ad, Operating Cold), IEC 60068-2-2 (Test Bd, Operating Dry Heat),IEC 60068-2-14 (Test Nb, Operating Thermal Shock): -20…60 °C (-4…140 °F)Temperature, storageIEC 60068-2-1 (Test Ab, Unpackaged Nonoperating Cold), IEC 60068-2-2 (Test Bb, Unpackaged Nonoperating Dry Heat), -40…85 °C (-40…185 °F)Relative humidityIEC 60068-2-30 (Test Db, Unpackaged Nonoperating Damp Heat): 5…95% noncondensingArmorPOINT RTD and Thermocouple Input Modules 15Publication 1738-IN005B-EN-E - January 2013Vibration IEC60068-2-6 (Test Fc, Operating): 5 g @ 10…500 HzShock, operating IEC60068-2-27 (Test Ea, Unpackaged Shock): 30 gShock, nonoperating IEC60068-2-27 (Test Ea, Unpackaged Shock): 50 gEmissions Emissions CSPR 11: Group 1, Class A ESD immunityIEC 61000-4-2:6 kV contact discharges 8 kV air dischargesRadiated RF immunityIEC 61000-4-3:10V/m with 1 kHz sine-wave 80% AM @ 30 MHz…1000 MHz 10V/m with 200 Hz 50% pulse 100% AM @ 900 Mhz EFT/B immunity IEC 61000-4-4:±3 kV @ 5 kHz on signal ports Surge transient immunity IEC 61000-4-5:±2 kV line-earth(CM) on shielded portsConducted RF immunityIEC 61000-4-6:10Vrms with 1kHz sine-wave 80% AM @ 150 kHz…80 MHzCertificationsCertification (when product is marked)(1)Valuec-UL-us UL-listed Industrial Control Equipment, certified for US and Canada CEEuropean Union 89/336/EEC EMC Directive, compliant with: EN 61000-6-4; Industrial Emissions EN 50082-2; Industrial ImmunityEN 61326; Meas./Control/Lab., Industrial Requirements EN 61000-6-2; Industrial Immunity C-TickAustralian Radiocommunications Act, compliant with: AS/NZS CISPR 11; Industrial Emissions(1)See the Product Certification link at for Declaration of Conformity, Certificates, and other certification details.Environmental SpecificationsAttributeValueRockwell Automation SupportRockwell Automation provides technical information on the Web to assist you in using its products. At /support/, you can find technical manuals, a knowledge base of FAQs, technical and application notes, sample code and links to software service packs, and a MySupport feature that you can customize to make the best use of these tools.For an additional level of technical phone support for installation, configuration and troubleshooting, we offer TechConnect support programs. For more information, contact your local distributor or Rockwell Automation representative, or visit /support/.Installation AssistanceIf you experience a problem within the first 24 hours of installation, please review the information that's contained in this manual. You can also contact a special Customer Support number for initial help in getting your product up and running.New Product Satisfaction ReturnRockwell Automation tests all of its products to ensure that they are fully operational when shipped from the manufacturing facility. However, if your product is not functioning and needs to be returned, follow these procedures.Documentation FeedbackYour comments will help us serve your documentation needs better. If you have any suggestions on how to improve this document, complete this form, publication RA-DU002, available at /literature/.United States or Canada 1.440.646.3434Outside United States or CanadaUse the Worldwide Locator at/support/americas/phone_en.html , or contact your local Rockwell Automation representative.United StatesContact your distributor. You must provide a Customer Support case number (call the phone number above to obtain one) to your distributor to complete the return process.Outside United StatesPlease contact your local Rockwell Automation representative for the return procedure.Publication 1738-IN005B-EN-E - January 2013Supersedes Publication 1738-IN005A-EN-E - June 2004Copyright © 2013 Rockwell Automation, Inc. All rights reserved.Allen-Bradley, Rockwell Automation, ArmorPOINT, and T echConnect are trademarks of Rockwell Automation, Inc.Trademarks not belonging to Rockwell Automation are property of their respective companies.。
DNVGL- Software_ Sesam 2015介绍

Sesam DeepC——主要对锚泊系统进行非线性时域耦合分析。用户界面友好, 方便建立细长柔性构件(如立管和锚链线) 、海洋环境条件(风、浪、流)等 的建模。模型和结果具有三维可视化功能。程序可以直接从 HydroD 中导出浮 体的水动力特性参数,如不同频率下的波浪激励力、附加质量和阻尼系数,之 后利用模块 Simo 和 Riflex 求解非线性时域运动方程。在耦合分析的基础上, DeepC 还可以对立管或者锚链线的疲劳寿命进行计算和统计预报;也可以进行 单立管的设计分析。DeepC 扩展模块还具有多体计算的功能,可同时考虑由多 个浮式结构物、系泊及立管系统、连接管线组成的复杂系统的耦合分析问题。
Page 3 of 19
Sesam HydroD——船舶及浮式结构物的稳性和水动力性能分析,包括浮体时域 及频域水动力计算。典型的比如重力式平台,驳船,所有类型的船舶,半潜平 台,张力腿平台,FPSO 或者 Spar 等等。根据不同的计算要求,利用 HydroD 进行设计分析流程如下:首先需要一个涵盖结构、分舱和质量分布等信息的模 型(通常是有 GeniE 建模) ,然后找出平衡位置,进行稳性分析,从而进行水 动力的计算,最后可以导出载荷和加速度等信息,并且可以将这些信息加载到 结构模型上去进行结构分析。HydroD 含有两个计算内核,一个是 WADAM,用于 无航速浮体的频域水动力计算;一个是 WASIM,用于有航速船的时域水动力计 算。两个计算内核公用一套前后处理工具,为用户带来便捷。
Page 5 of 19
GeniE CGEO
GeniE CCBM
GeniE CCPL
Presel Wajac GeniE Splice
Sestra
Usfos Installjac Xtract
Alfa Laval FCM LPG 液化石油气燃料条件调节模块说明书

ApplicationLPG is free from sulphur, virtually eliminating SOx emissions. It is a mixture of hydrocarbons, mainly of n-butane, i-butane, propane and a small percentage of ethane, not higher than 8%. These components can be mixed in different percentages, leading to a wide spread of compositions for use as fuel, and consequently a wide range of operative conditions.Building on the experience with Fuel Conditioning Modules for standard fuels (HFO, MDO, MGO), for low flashpoint fuels (methanol) and for special applications (crude oil), Alfa Laval, in cooperation with MAN Energy Solutions, developed the Fuel Conditioning Module (FCM) LPG, a high pressure booster module designed to feeding the new MAN B&W ME-LGIP two strokes engine.The module design and process was developed to be able to handle the new specific challenges of the LPG as a fuel: the FCM LPG is able to process the full range of LPG compositions available on the market, is able to react to the quick changes of the engine load and is protecting it against the solid pollutants contained in the product.Benefits•Module designed to serve the requirements of the LPGengine•Proven technology in MAN R&D facilities for effectiveprocess control•Automatic control of the LPG fuel conditioning and safety functions, and of the START/STOP procedures •Modular plug-and-play solution that can be adapted to the different deck layouts and process conditions•Turn-key skid mounted solution, for easy installation •Independent from the cargo handling system•System design ready to operate with ammonia asalternative of LPG fuel HMI — real-time Process Flow Diagram OverviewDesign & Standard configurationThe new FCM LPG is an independent system, with its own fully automated control cabinet, applicable both to LPG carriers and to non-LPG carriers fueled with LPG. It consists of a low-pressure (LP) and a high-pressure (HP) module, and of a control cabinet.As standard option, a heating media loop for the control of the LPG temperature can be built on the HP skid itself. The complete pipework is made of AISI 316L stainless steel.The module is suitable for the installation on the deck under a shelter or inside the compressor room in case of a ship carrying LPG as cargo.The FCM LPG is equipped with a completely dedicated automation system developed by Alfa Laval. The software was developed using a modular architecture; this allows it to adaptto different layouts and configurations on board, without changing the control logic developed with MAN-ES.A graphical 15” touchscreen panel (Human Machine Interface)ensures a simple safe operator experience, sharing the same intuitive interface used on the new generation of Alfa Laval systems.Alfa Laval FCM LPG is working as a close loop with theengine, thus receiving the return of LPG from it and securing the cargo from receiving any pollutants coming from the engine.Refer to the figures below for an overview of the possiblealternative designs for marine application.Alternative designs available for marine applicationTechnical DataOptionsThe relevant regulations and international guidelines clearly state that venting of hydrocarbons into the atmosphere should be avoided as far as practically possible. Moreover, the dispersion of the vented gas will is critical, which must be considered in the design.It is then helpful, economical and ethical to recover as much LPG as possible after purging of the engine, the FVT (fuel valve train) or even the LFSS (Low-Flashpoint Supply System)in case of maintenance. For this reason, Alfa Laval developed the LPG recovery system as an option.When an engine and FVT purging event occurs, the “return from engine” line is diverted to the recovery system and all the LPG and nitrogen flows into this system.The system works as a liquid/gas separator, providing full liquid LPG recovery and partial LPG gas recovery. Therecovered LPG, contaminated with seal oil, is then re-injected into the FCM LPG module.This document and its contents are subject to copyrights and other intellectual property rights owned by Alfa Laval Corporate AB. No part of this document may be copied, re-produced or transmitted in any form or by any means, or for any purpose, without Alfa Laval Corporate AB’s prior express written permission. Information and services provided in this document are made as a benefit and service to the user, and no representations or warranties are made about the accuracy or suitability of this information and these services for any purpose. All rights are reserved.200000121-1-EN-GB© Alfa Laval Corporate ABHow to contact Alfa LavalUp-to-date Alfa Laval contact details for all countries are always available on our website at 。
各行业英文对照表
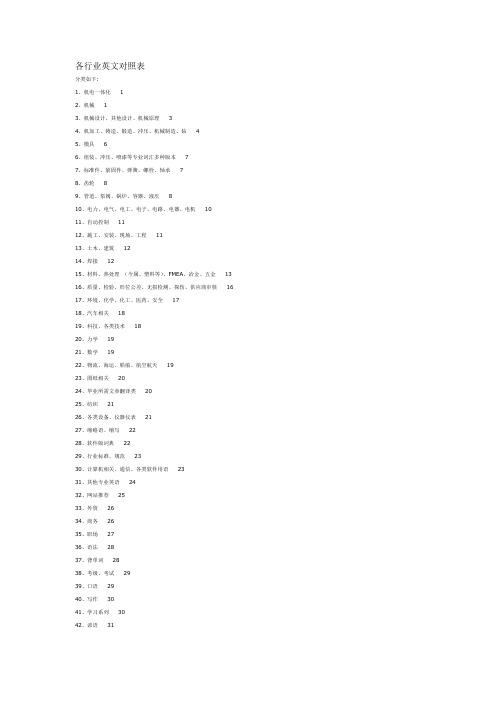
各行业英文对照表分类如下:1、机电一体化 12、机械 13、机械设计、其他设计、机械原理 34、机加工、铸造、锻造、冲压、机械制造、钻 45、模具 66、组装、冲压、喷漆等专业词汇多种版本77、标准件、紧固件、弹簧、螺栓、轴承78、齿轮89、管道、泵阀、锅炉、容器、液压810、电力、电气、电工、电子、电路、电器、电机1011、自动控制1112、施工、安装、现场、工程1113、土木、建筑1214、焊接1215、材料、热处理(今属、塑料等)、FMEA、冶金、五金1316、质量、检验、形位公差、无损检测、探伤、供应商审核1617、环境、化学、化工、医药、安全1718、汽车相关1819、科技、各类技术1820、力学1921、数学1922、物流、海运、船舶、航空航天1923、图纸相关2024、毕业所需文章翻译类2025、纺织2126、各类设备、仪器仪表2127、缩略语、缩写2228、软件版词典2229、行业标准、规范2330、计算机相关、通信、各类软件用语2331、其他专业英语2432、网站推荐2533、外贸2634、商务2635、职场2736、语法2837、背单词2838、考级、考试2939、口语2940、写作3041、学习系列3042、谚语3143、翻译3144、其他321、机电一体化一、附件下载篇The Mechatronics Handbook, 2002 (pdf, 1230页) /read.php?tid=465882机电专业英语(pdg格式,扫描件,共294页) /read.php?tid=2341机电工程专业英语(txt) /read.php?tid=379244Oxford English for Electrical and Mechanical Engineering (PDF 35MB) /read.php?tid=433637专业(机电)词汇汇总英汉对照(20个TXT文件) /read.php?tid=447250二、非下载篇2、机械一、附件下载篇English for Technical Students (EFTS) (PDF格式,175页) /read.php?tid=431499Mechanical_Engineers_Handbook (2001年版的800多页) /read.php?tid=431032mechanical engineers handbook (共2000多页,123M, 4个PDF) /read.php?tid=4073422003版英文书籍《Mechanical_Engineers_Data_Handbook》(pdf, 354页)/read.php?tid=401526英汉机械工程大词典(PDF格式,有书签,共1324页) /read.php?tid=22515机械翻译词汇(PDF格式,超清晰版,共123页) /read.php?tid=16306機構英文專用術語(DBTEL excel多页链接,繁体) /read.php?tid=120605机械专业英语(pdf,清晰,共135页,全英文,非词典) /read.php?tid=442234Professional words (word文档,包括电工、金属材料、热机、除灰、水电、供水、消防、结构、环保) /read.php?tid=39253机械词语翻译(pdf格式,共123页) /read.php?tid=2432机械名词解释(word文档,2000多个) /read.php?tid=57994机械工程名词PDF版(1、2分别为148,243页) /read.php?tid=412306赛尔集团内部资料-最新实用机械专业英语汇总pdf格式/read.php?tid=1832711楼A-Z词汇(word 文档) /read.php?tid=20373A-G字母开头的机械英语单词(几个TXT文档) /read.php?tid=194246机械英语Word 版整理/read.php?tid=30666分享我收集的机械英语(4个word文档,与其他资料有重复) /read.php?tid=97007机械行业部分英汉对照(与其它机械英语有重复) /read.php?tid=53521机械词汇(几个txt) /read.php?tid=438448机械专业英语词汇(pdf, 15页) /read.php?tid=299923机械专业英语(txt) /read.php?tid=399140机械专业英语(word, 26页) /read.php?tid=247505机械专业英语(word, 9页) /read.php?tid=246588机械专业英语词典(1楼,DOS界面) /read.php?tid=435032机械英语生词本出炉/read.php?tid=442910机械英语(6个文档) /read.php?tid=413955机械专业词汇(word文档,300页) /read.php?tid=391269一些机械英语词汇(word, 99页,有汽车的,外贸的,热处理的等,不是很全) /read.php?tid=398277本人多年收集的机械英语集(10个word&txt文档) /read.php?tid=166962已整理,比较全的机械专业英语(7个文档合集,有贴图) /read.php?tid=342834机械常用英语单词(word文档,82页,按笔划排序,6楼补充资料73页word) /read.php?tid=381169机械通用词汇(整理过的,word,50页) /read.php?tid=387352《机械专业英语词汇》(共218页word) /read.php?tid=287422机械英语对照(word, 68页) /read.php?tid=342137英汉对照机械术语(word, 8页) /read.php?tid=1933122099个机械方面的英语词汇(pdf, 50页) /read.php?tid=179413机械相关专业英语(word, 17页) /read.php?tid=464867我在网上收集了一些关于机械翻译的资料/read.php?tid=352006《汉英词典》机械类专用词汇(word, 按笔划排序,50页) /read.php?tid=248469[机械资料]机械英语名词解释(PDF, 50页) /read.php?tid=2277机械中的常用英语(word文档,共119页) /read.php?tid=244162机械专业英语词汇自己整理和收集的/read.php?tid=277036机械专业英语词汇汇编(5个txt) /read.php?tid=211858Mechanical Engineering phrases chinese-english reference(EXCEL) /read.php?tid=284092machinery component maintenance and repair (一本关于机械设备维护的好书,PDF,全英文,641页) /read.php?tid=445276词根记忆法& 一些机械词汇(2个word文档) /read.php?tid=350184机械中英习题(word, 13页) /read.php?tid=2338基础机械德语教程(pdf, 非清晰版) /read.php?tid=444990机械德语基础词汇!!(汽车化工机械类)/read.php?tid=444992机械专业英语(word版)/read.php?tid=477622二、非下载篇机械英文/read.php?tid=17789机械英语汇总词汇/read.php?tid=27673机械英语汇总/read.php?tid=2431机械类英语汇总/read.php?tid=370324机械单词(与很多资料有重复内容) /read.php?tid=69886机械词汇/read.php?tid=181418机械零件中英词汇对照/read.php?tid=199202机械英语/read.php?tid=213121机械专业英语/read.php?tid=104444机械词汇/read.php?tid=261504一些机械常用英汉对照词汇/read.php?tid=445397专业英语/read.php?tid=443728机械英语词汇(综合型)/read.php?tid=419019机械类相关英语大全(3个word文档,资料与其他资料有重复) /read.php?tid=416619机械英语词汇(a开头) /read.php?tid=381959机械英语11 /read.php?tid=405004新查了些机械方面的英语(1楼焊接方面) /read.php?tid=404796机械工程材料常用词汇/read.php?tid=252060十几年老翻译专业词汇/read.php?tid=124337机械类专利翻译词汇汇总(大约3000个)/read.php?tid=464222机械.中英文对照名词解释/read.php?tid=218731机械专业词汇表/read.php?tid=233371机械专业英语词汇/read.php?tid=288646英汉对照机械术语/read.php?tid=485112机械方面的词汇/read.php?tid=4868333、机械设计、其他设计、机械原理一、附件下载篇机械设计中英文词汇对照(三个word文档) /read.php?tid=21358机械设计名词术语中英文对照表(txt格式) /read.php?tid=15853机械设计名词术语中英文对照表(pdf格式,共35页,A-Z) /read.php?tid=38593机械设计名词术语中英文对照(pdf格式,共8页) /read.php?tid=351677机械名词术语翻译(word, 31页) /read.php?tid=166385机械设计专业术语的英语翻译(word, 16页) /read.php?tid=377426机械设计英语术语大全(word, 9页) /read.php?tid=380689机械设计常用词汇(意大利-英语-汉语, pdf, 96页) /read.php?tid=387161Standards for engineering design and manufacturing(12个pdf) /read.php?tid=428163Mechanical Engineering Design 7th edtion (全英文,pdf格式,共18章,400多页,主要是一些机械设计中的计算实例) /read.php?tid=435808Engineering Design in Three Dimension(大学3D设计书本资料键盘录入) /read.php?tid=379683TANK DESIGN CALCULATION FOR ENGLISH(PDF 格式) /read.php?tid=110067Designing Capable and Reliable Products (设计可行、可靠的产品, 408 pages) /read.php?tid=431044 Hydraulic seal of cylinder (pdf by Busak+Shamban) /read.php?tid=425058机械原理(英文10个ppt)/read.php?tid=150854Designing with Plastic(PDF, 84页) /read.php?tid=480735二、非下载篇机械设计及周边其他用语英汉对照/read.php?tid=2443机械设计名词术语中英文对照表相同资料不同格式资料合并/read.php?tid=16775机械设计工作人员常用软件大会集/read.php?tid=465505机械设计部分外语/read.php?tid=11261平面设计/read.php?tid=2453机械类常用英语:机械设计类/read.php?tid=361300机械原理常用词汇/read.php?tid=448322机械原理部分外语/read.php?tid=11259机械制图部分外语/read.php?tid=11263机械製图常用词汇/read.php?tid=4483124、机加工、铸造、锻造、冲压、机械制造、钻一、附件下载篇金属加工专业词汇(PDF, 10页) /read.php?tid=2301金属工艺学专业词汇(和切削的相关度比较高, word, 6页) /read.php?tid=179842 1楼加工中心英语(word文档,7页,同机床行业常用英文对照/read.php?tid=2282) /read.php?tid=2454机械加工工艺装备基本术语--英-汉/read.php?tid=421106机械加工常用基础英语名词术语翻译对照大全(txt) /read.php?tid=318365机械加工类英语(word, 33页) /read.php?tid=320330Machinery's Handbook 27th Edition /read.php?tid=423917Cutting Tool Applications (18个PDF,全英文) /read.php?tid=419582机床和铣床翻译(word, 2页) /read.php?tid=315914工艺词汇(中英文,word双排,13页) /read.php?tid=177569常用加工机械(word, 2页) /read.php?tid=227191Machining课(机械加工)时加国老师用的英文讲义/read.php?tid=124463英汉金属塑性加工词典(pdf, 287MB) /read.php?tid=312971铸造术语(中英文对照)(word文档,共42页) /read.php?tid=39941铸件教程(英文, pdf, 179页)/read.php?tid=356857铸造常用词汇(word, 2页) /read.php?tid=192787铸造名词术语GB5611-1998 (PDF,182页)/read.php?tid=267888常用铸造词汇的中英文对照和解释(word,1页, PDF11页) /read.php?tid=251220铸造学专业英语词汇(1~31卷,word, 共128页)/read.php?tid=464263Die Casting Alloy Data(pdf, 18页) /read.php?tid=463550What is High Pressure Die Casting(word, 25页) /read.php?tid=338307die casting design (全英文版的书,185页) /read.php?tid=426333Rapid Die Heating for Low-Stress Die Attach(pdf, 10页) /read.php?tid=284965锻铸造关连词汇(word, 4页) /read.php?tid=79892锻铸造关连词汇(word, 13页) /read.php?tid=481947HOW TO BUY FORGINGS (pdf, 6页, 锻造) /read.php?tid=403834冲压英语(word文档,2页) /read.php?tid=2274冲压专业在实践中常用的英语(word, 5页) /read.php?tid=2461Tool-Engineering-Calculator (excel格式) /read.php?tid=390775sour drilling material (pdf, 12页) /read.php?tid=123726机械制造专业英语(章跃,机械工业出版社) /read.php?tid=411529机械制造业翻译词汇/read.php?tid=318360钻井液管汇说明书改动(word, 7页) /read.php?tid=443249 (1楼)铸造术语标准翻译(excel多页分类) /read.php?tid=472114Machining and Metalworking Handbook (McGraw-Hill Handbooks,PDF,976页) /read.php?tid=487100机床行业常用英文对照(同加工中心英语(word文档,7页) /read.php?tid=2454) /read.php?tid=2282二、非下载篇机械加工常用工具英汉对照/read.php?tid=448289常用英语:加工方法/read.php?tid=392537机加英语(一)/read.php?tid=240675机床英汉对照/read.php?tid=485105加工中心英语/read.php?tid=2311/read.php?tid=470615常用加工机械英语/read.php?tid=104447机加工专业(单词/词组)中英对照/read.php?tid=446285铸造常用词中英文对照及简释/read.php?tid=55445铸造、滚动轴承、机床行业常用词中英文对照及简释/read.php?tid=141823铸造厂评估报告英文版/read.php?tid=213697机械铸造类专业术语/read.php?tid=470504锻铸造关连用语/read.php?tid=485115铸件涂层coating of casting /read.php?tid=217929连铸英语/read.php?tid=254939冲压机械及周边关连用语英汉对照/read.php?tid=115797冲压加工工序名称中英文对照表/read.php?tid=141042冲压英语/read.php?tid=2447机械类常用英语系列之冲压模具-零件类/read.php?tid=248000机械工具英语/read.php?tid=153292机械类常用英语:砂轮用语/read.php?tid=418978砂轮用语中英文对照/read.php?tid=111042粗切削与精切削(中英)/read.php?tid=260042线切割放电加工关连用语中英文对照/read.php?tid=113644制造业中常用的英文缩写/read.php?tid=441031常用刀具词汇英语/read.php?tid=389573制造业常用英语词汇/read.php?tid=89976机械类常用英语之射出成形关联用语/read.php?tid=1126395、模具一、附件下载篇模具术语(word文档,47页) /read.php?tid=2294 1楼模具(机械)英语词汇表(word文档,131页) /read.php?tid=2294 2楼模具類相關英語/read.php?tid=58313模具英语(excel格式) /read.php?tid=11111 (1楼)注塑模具英語(pdf,共7页) /read.php?tid=212266机械英语\模具\模具英语词汇表(pdf格式,共10页) /read.php?tid=211179模具相关英语(word文档,38页)/read.php?tid=448135flat die and pocket die(一篇关于冲模的英文论文) /read.php?tid=441754mold design(21页,PDF) /read.php?tid=434679拉深模设计中拉深壁起皱的分析(原英文资料和翻译) /read.php?tid=429892useful knowledge (模流1) (pdf, 256页) /read.php?tid=401659模具英語單詞(pdf, 19页) /read.php?tid=401653模具专业英语(txt) /read.php?tid=125729塑料挤压模具设计(英文版,21页,PDF)/read.php?tid=254689Progressive_die_sequence_design_for_deep_drawing_round_cups_using_finite_element_analysis (模具类的英文文章. 宁言军,PDF 4页) /read.php?tid=284941模具英语(5个word,1个PDF,1个DWG) /read.php?tid=206659二、非下载篇冲压模具/read.php?tid=29172冲模术语(中英对照)/read.php?tid=263934模具专业英语/read.php?tid=2273模具词汇/read.php?tid=37378模具常用刀具与工作法用语/read.php?tid=2336模具钢材及零件英语/read.php?tid=2294模具工程常用词汇/read.php?tid=55116常用模具英语/read.php?tid=2429模具成形不良用语中英文对照/read.php?tid=111038各种模具常用成形方式中英文对照/read.php?tid=112641各式模具分类用语中英文对照/read.php?tid=247995模具英语/read.php?tid=262744机械英语词汇之模板、零件、塑件&模具/read.php?tid=349433各式模具分类用语中英文对照/read.php?tid=431994模具成形不良用语英汉对照/read.php?tid=2442模具相关英语/read.php?tid=5639模具术语(英汉对照)/read.php?tid=260587挤出机、锁模机及立式注塑成型机技术参数型号规格翻译/read.php?tid=471461成型工艺、熔胶段工艺流程及条件介绍/read.php?tid=471452塑料模具常用的英日中词汇汇总/read.php?tid=4873076、组装、冲压、喷漆等专业词汇多种版本一、附件下载篇机械专业术语(组装、冲压、喷漆等专业词汇,PDF格式) /read.php?tid=2281机械专业术语(word文档,组装、冲压、喷漆等专业词汇) /read.php?tid=2278(/read.php?tid=2288重复)模具相关英语(word, 组装、冲压、喷漆等专业词汇繁体版) /read.php?tid=13611机械与工厂英语(word, 39页,前31页同组装、冲压、喷漆等词汇) /read.php?tid=244349机械与工厂英语(word, 共76页,前57页同组装、冲压、喷漆等专业词汇) /read.php?tid=52513常用的机械英语词汇(2个word文档,机械词汇表-模具10页;综合15页大部分重复组装、冲压、喷漆等专业词汇) /read.php?tid=415085二、非下载篇7、标准件、紧固件、弹簧、螺栓、轴承一、附件下载篇标准件中英文对照表紧固件中英文对照表扣件中英文对照表(PDF, 9页,宁波龙益金属工业有限公司) /read.php?tid=38812机械,钣金,常用紧固件英语(3个word文档) /read.php?tid=244613紧固件常用英文对照(pdf, 5页) /read.php?tid=465086国家紧固件标准GBT 与汉语、英语对照表共享(word, 6页) /read.php?tid=265356常用弹簧中英文对照表(word文档,2页) /read.php?tid=421137VDI2230 (关于如何计算螺栓连接方面的,一边是德文的,一边是英文的,主要是讲德语地区的应用标准) /read.php?tid=402157中外螺纹查询工具(exe直接运行,汉化版见14楼) /read.php?tid=120668行业标准规范英汉对照/read.php?tid=391097轴承的英文名称(PDF, 5页) /read.php?tid=244641Stainless Steel Fasteners Design Handbook (pdf,23页) /read.php?tid=403826二、非下载篇标准件的行业对照/read.php?tid=406559行业标准规范英汉对照/read.php?tid=141488紧固件类英语词汇/read.php?tid=2299紧固件专业英语词汇/read.php?tid=37299螺丝产品名称(线材)中英文对照(简体、繁体) /read.php?tid=113640螺纹知识/read.php?tid=438441螺丝产品名称中英文对照(螺丝螺) /read.php?tid=2439THREAD /read.php?tid=378061螺丝相关的英语(材料,加工,设备。
TSI TF-Series Flow Station安装说明书

_____________________TSI and TSI logo are registered trademarks of TSI Incorporated. MODEL TF-SERIES FLOW STATIONINSTALLATION INSTRUCTIONSFigure 1. TF-Series Thermal Flow StationThe following paragraphs detail the procedure for determining optimum placement of the TF-Series Flow Station in typical installation applications.Installation of the TF-Series Flow Station with straight duct lengths equal to or greater thanindicated in the Minimum Placement Guidelines below is critical for proper performance of the airflow measurement station.Minimum Placement GuidelinesPlacement of the TF-Series Flow Station is critical for proper operation and accuracy of the airflowmeasurement station. Figure 2 shows minimum placement requirements for the TF-Series Flow Station in typical applications. Probe placement is expressed in multiples of ‘Sim ple Equivalent Duct Diameter – “D ,” which is determined as follows:D = (duct width + duct height) / 21. Using the illustration in Figure 2 that most closely matches the install ation, multiply the calculated “D”value from above by the value indicated in the application illustration. This is the calculated location for the TF-Series Flow Station. 2. Mark the duct location and install the TF-Series Flow Station at the calculated location.TF-Series Flow Station can beinstalled downstream of hotwater coil only.Figure 2. TF-Series Flow Station Minimum Placement Requirements GuideFigure 3. TF-Series Installation Flow Station Applications and OrientationThe TF-Series Flow Station is designed for use indoors in ducts up to 16 inches and in VAV terminal box applications TF-Series airflow measurement station sensor probes are designed for insertion mounting through one side of the duct or VAV box. Mount the instrument in an accessible location to permit set up.Locate the instrument so that the attached instrument cable will reach the TSI controller or customer-provided junction box.The installed location of the TF-Series Flow Station is critical for proper performance. Refer to the previous recommended location for the TF-Series Flow Station.Ensure that adequate clearance exists to permit insertion of the probe, and to allow clearance for the instrument enclosure.External duct insulation that interferes with mounting should be temporarily removed prior to installation. Mounting requires a 0.875 inches (22.2 mm) hole on the insertion side of the duct.1. Determine where the TF-Series airflow measuring station is to be located as indicated on the engineer'splans. 2. Carefully open the TF-Series Flow Station package and inspect for damage. If damage is noted, immediatelyfile a claim with carrier.3.Locate and mark the point on the duct or VAV box where the probe will be inserted using the previousMinimum Placement Guidelines section of this document. Refer to Figure 3 and Figure 4 for TF-Series Flow Station dimensions and probe orientation.ing a 0.875 inch (22.2 mm) hole saw, drill the insertion side hole marked in the previous step.5.Place the probe through the mounting hole, making sure that the gasket is seated firmly against the integralmounting bracket. Ensure that the edge of the TF-Series Flow Station mounting bracket is parallel to the edge of the duct or VAV terminal box, and that the airflow arrow printed on it is oriented in the direction of actual airflow. Ensure that the gasket is firmly seated against the bracket, and then fasten the mounting bracket at the four mounting holes using appropriate sheet metal screws.6.Route the TF-Series Flow Station instrument cable to the TSI monitor or controller. Refer to the followingsections of this document for instrument set up and operation.Mounting Bracket Detail ViewUnits in inches (mm)TF-Series Sensor Probe / Transmitter Detail ViewsFigure 4. TF-Series Flow Station Installation DimensionsTF-Series Flow Station—Preparation for UsePreparation for use consists of connecting 24 VAC power and analog signal output wires from the TF-Series Flow Station to the TSI monitor or controller, and if required, setting the TF-Series Flow Station analog output switch options (measurement mode, output signal type and full scale range options).TF-Series Flow Station InterconnectionsThe TF-Series Flow Station is equipped with a plenum rated 18 AWG interconnecting cable for power and analog output(s). Connect 24 VAC power and analog output(s) to TSI monitor or controller as outlined in the following paragraphs. Refer to Figure 5.TF-Series Analog Output Connections24 VAC power must be deactivated before making connections to the instrument.The 24 VAC input ground (GND) connection is shared with the analog output signal ground. If an isolated output is desired, a dedicated isolation transformer is required to power the TF-Series Flow Station.The TF-Series provides an analog output to indicate airflow or equivalent velocity pressure, with an optional analog output to indicate air temperature. The analog outputs are not isolated from the power input. Connect the analog output at the white wire and the signal common at the black wire to the TSI monitor or controller using twisted pair cable as shown in Figure 5.TF-Series Flow Station 24 VAC Power Connections24 VAC power must be deactivated before making connections to the instrument.The 24 VAC input ground (GND) connection is shared with the analog output signal ground. If an isolated output is desired, a dedicated isolation transformer is required to power the TF-Series Flow Station.The TF-Series Flow Station requires a power source capable of providing 22.8 to 26.4 VAC at 5 VA. Connect 24 VAC power between the red wire and black wires as shown in Figure 6.The TF-Series Flow Stations are equipped with a common 24 VAC ground and analog output signal common(s). The analog output(s) must be wired with dedicated common wire(s).Sharing the common wire with the 24 VAC return may cause voltage drop leading to inaccurate readings.NOTES:1.The 24 VAC common and analog output signal commons are non-isolated. Do not share power withother non-isolated devices.2.On multiple TF-Series Flow Station installations ensure that all TF-Series Flow Stations are wired to thesame terminals on the 24 VAC power source.3.Connect cable drains to earth ground at one end of each cable only.TF-Series Flow Station Analog Output Option Switch SettingsTo access the field selectable analog output option switches, remove the four retaining screws at each corner of the TF-Series Flow Station enclosure cover. The option selector switches are part of a four-switch DIP package labeled CONFIG. Figure 7 shows the TF-Series circuit board and individual switches for setting TF-Series Flow Station measurement mode, output voltage and output full-scale values. Factory default switch settings are all OFF, resulting in airflow measurement mode, 0 to 10 VDC analog output and 0 to 3,000 FPM full scale range. If desired, these settings can be changed using the CONFIG switch as shown in Figure 6 and as described in the following paragraphs:Figure 7. TF-Series Flow Station Circuit Board DetailSwitch 2 Position Output OFF (default) 0–10 VDC ON2–10 VDCSwitch 1 Position Switch 3 Position Switch 4 Position Full Scale Range OFF (default)OFF (default)OFF (default)3,000 fpm (15.24 m/s) OFF ON OFF 2,000 fpm (10.16 m/s) OFF OFF ON 1,000 fpm (5.08 m/s) TF-Series Flow Station Circuit BoardActivity Green LED IndicatorSW1-SW4 CONFIG DIP SWITCH OUTPUT OPTION SELECTOR SW1 – AIR FLOW/EQUIVALENT VELOCITY PRESSURE SW2 - 0-10/2-10 VDCSW3 / SW4 - OUTPUT SCALE (See Detail below)CONFIG DIP Switch DetailSW1 SW2 SW3 SW4TSI Incorporated – Visit our website for more information. USA Tel: +1 800 874 2811 UK Tel: +44 149 4 459200 FranceTel: +33 1 41 19 21 99Germany Tel: +49 241 523030 India Tel: +91 80 67877200ChinaTel: +86 10 8219 7688 SingaporeTel: +65 6595 6388P/N 6008233 Rev. C ©2018 TSI Incorporated Printed in U.S.A.TF-Series Flow Station Initial Start Up / Normal OperationThe following procedure is intended for initial start-up of the TF-Series Flow Station. Following the initial set up, no further user activity is required during normal operation.1. Remove the cover to the electronics enclosure by removing the four screws on the cover.2. Make sure that the 24 VAC circuit breaker used to power the TF-Series Flow Station is turned OFF untilall wiring is complete! 3. Confirm 24 VAC connection from the power source to the TF-Series Flow Station 24 VAC wire (redwire) as outlined in the TF-Series Flow Station 24 VAC Power Connections section of this document. 4. Confirm common ground 24 VAC and signal ground connection from the power source to the TF-SeriesFlow Station at the black wire. 5. Confirm TF-Series Flow Station analog signal output connection at the white wire, to the analog input ofthe BAS as outlined in TF-Series Analog Output Connections section of this document. Note that the ground of the BAS must be at the same voltage reference as the ground of the TF-Series Flow Station and the power source. 6. Set the desired analog output options using CONFIG switches SW1 to SW4 as outlined in the TF-SeriesFlow Station Analog Output Option Switch Settings section of this document. 7. Activate the 24 VAC power source to power on the TF-Series Flow Station.8. Check to confirm that the TSI controller or BAS is receiving the analog output signal indicatinginstrument airflow or equivalent velocity pressure. 9. Following a brief instrument initialization, the green Activity LED will continuously flash ON for1 second, then OFF for 1 second. This indicates normal operation. In the event of a sensor fault, the LED will continuously flash ON for2 seconds, and OFF for 2 seconds.Converting the Output Signal from Linear to Volumetric Flow —FPM to CFMThe TF-Series Flow Station analog output airflow (FPM) can easily be converted to an equivalentvolumetric flow (CFM) by multiplying the indicated flow velocity by the free area at the sensor installation location (in square feet). For example, assuming an installation in a 12-inch round duct, using the0 to 10 VDC scale and the 3,000 FPM full scale output range options, an output of 5 VDC from the TF-Series Flow Station indicates a flow velocity of 1,500 FPM. (5 VDC is one-half of the 0 to 10 VDC output,corresponding to one-half of the 0 to 3,000 FPM scale, which equals 1,500 FPM). The TF-Series Flow Station installed duct location area in this example is calculated at 0.785 ft 2 (using x the duct radius 2, or 3.14 x 0.5 ft 2). Multiplying the indicated instrument output of 1,500 FPM by 0.785 ft 2 yields an equivalent volumetric flow of 1,177.5 CFM.In most HVAC environments, periodic maintenance and calibration is not required or recommended*.*Depending on the application, it may be necessary to periodically inspect and clean sensors using compressed air or a small brush. Factory performance returns immediately after cleaning. Recalibration is NOT required. Periodic inspection of the sensors is advised, and accessibility must be considered in these applications.。
八大黑科技助力网络世界长治久安

八大黑科技助力网络世界长治久安作者:来源:《信息化建设》2021年第11期2021年國家网络安全宣传周网络安全博览会于10月8日起在西安国际会展中心举办。
本届博览会重点展示党的十八大以来网络安全领域重大成就,展示网络安全前沿技术、新型产品,以及示范应用。
其中八项前沿黑科技,为维护网络安全再添助力。
腾讯安全算力盒子腾讯安全算力盒子于网安周首发。
该盒子基于腾讯天幕PaaS的高性能安全算力算法能力,以腾讯云星星海灵动水系AC221计算型服务器为底层硬件,聚合科恩实验室、NDR、SOC等优秀产品和技术能力,是自主研发、安全可控的云原生信创安全盒子。
HiSecEngine USG12000系列AI防火墙HiSecEngine USG12000系列AI防火墙,具有高效、智能、安全的特点。
在高效方面,提供4.8T防御能力,可以同时支持保护480万人上网。
在智能方面,恶意文件威胁检出率达到97%,威胁误报率小于0.05%。
在安全方面,做到了芯片级别可信启动、防篡改,通过供应可信、硬件可信、软件可信三个维度打造产品的内生安全能力。
全国态势感知系统360全国态势感知平台描绘了一张上至全国、下至区域街道可以横向对比的全息地图,能准确定位到网络漏洞、网络威胁实际发生的街道和楼宇,帮助城市安全运营者快速定位被攻击者,进一步完善网络安全建设。
冬奥网络安全运行指挥中心系统作为北京2022年冬奥会和冬残奥会官方网络安全服务和杀毒软件赞助商,奇安信打造了“冬奥网络安全运行指挥中心系统”。
作为北京冬奥会网络安全保障服务的“大脑”,这套指挥系统将全面掌握着每一个场馆、每一处设备的安全动态和威胁风险,并能做到及时响应,守护冬奥会的网络安全。
天通卫星通信天通卫星通信是我国首个自主研制和应用的卫星移动通信系统,中国电信为独家承担天通卫星移动通信业务运营的基础电信运营企业。
天通卫星通信的卫星、芯片、终端、信关站等系统均为我国自主研发,可提供稳定可靠、安全保密的卫星移动通信,确保卫星网络通信和信息安全可管可控。
I-Trac 7, 11, 15 行版本女婿卡信号模块移除工具说明书
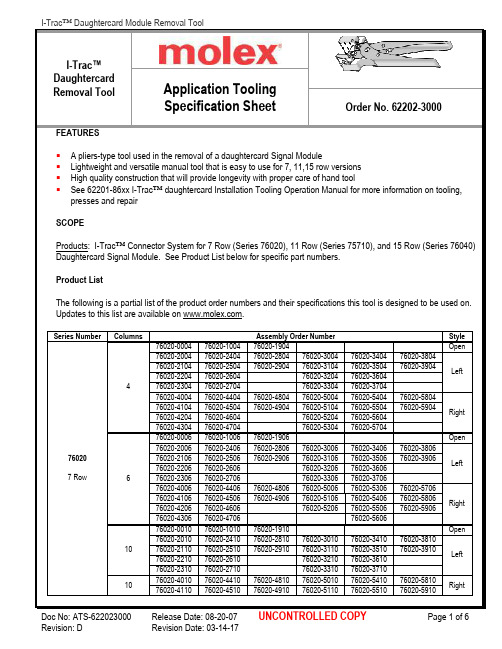
FEATURESA pliers-type tool used in the removal of a daughtercard Signal ModuleLightweight and versatile manual tool that is easy to use for 7, 11,15 row versionsHigh quality construction that will provide longevity with proper care of hand toolSee 62201-86xx I-Trac™ daughtercard Installation Tooling Operation Manual for more information on tooling, presses and repairSCOPEProducts: I-Trac™ Connector System for 7 Row (Series 76020), 11 Row (Series 75710), and 15 Row (Series 76040) Daughtercard Signal Module. See Product List below for specific part numbers.Product ListThe following is a partial list of the product order numbers and their specifications this tool is designed to be used on. Updates to this list are available on .Series Number Columns Assembly Order Number Style76020 7 Row 476020-0004 76020-1004 76020-1904 Open 76020-2004 76020-2404 76020-2804 76020-3004 76020-3404 76020-3804Left 76020-2104 76020-2504 76020-2904 76020-3104 76020-3504 76020-390476020-2204 76020-2604 76020-3204 76020-360476020-2304 76020-2704 76020-3304 76020-370476020-4004 76020-4404 76020-4804 76020-5004 76020-5404 76020-5804Right 76020-4104 76020-4504 76020-4904 76020-5104 76020-5504 76020-590476020-4204 76020-4604 76020-5204 76020-560476020-4304 76020-4704 76020-5304 76020-5704676020-0006 76020-1006 76020-1906 Open 76020-2006 76020-2406 76020-2806 76020-3006 76020-3406 76020-3806Left 76020-2106 76020-2506 76020-2906 76020-3106 76020-3506 76020-390676020-2206 76020-2606 76020-3206 76020-360676020-2306 76020-2706 76020-3306 76020-370676020-4006 76020-4406 76020-4806 76020-5006 76020-5306 76020-5706Right 76020-4106 76020-4506 76020-4906 76020-5106 76020-5406 76020-580676020-4206 76020-4606 76020-5206 76020-5506 76020-590676020-4306 76020-4706 76020-56061076020-0010 76020-1010 76020-1910 Open 76020-2010 76020-2410 76020-2810 76020-3010 76020-3410 76020-3810Left 76020-2110 76020-2510 76020-2910 76020-3110 76020-3510 76020-391076020-2210 76020-2610 76020-3210 76020-361076020-2310 76020-2710 76020-3310 76020-37101076020-4010 76020-4410 76020-4810 76020-5010 76020-5410 76020-5810Right 76020-4110 76020-4510 76020-4910 76020-5110 76020-5510 76020-5910I-Trac™DaughtercardRemoval Tool Application ToolingSpecification Sheet Order No. 62202-300076020-4210 76020-4610 76020-5210 76020-561076020-4310 76020-4710 76020-5310 76020-5710Series Number Columns Assembly Order Number Style75710 11 Row 575710-0005 75710-1005 Open 75710-2005 75710-2305 75710-2605 75710-3005 75710-3305 75710-3605Left 75710-2055 75710-2355 75710-2655 75710-3055 75710-3355 75710-365575710-2105 75710-2405 75710-2705 75710-3105 75710-3405 75710-370575710-2155 75710-2455 75710-2755 75710-3155 75710-3455 75710-375575710-2205 75710-2505 75710-2805 75710-3205 75710-3505 75710-380575710-2255 75710-2555 75710-2855 75710-3255 75710-3555 75710-385575710-4005 75710-4305 75710-4605 75710-5005 75710-5305 75710-5605Right 75710-4055 75710-4355 75710-4655 75710-5055 75710-5355 75710-565575710-4105 75710-4405 75710-4705 75710-5105 75710-5405 75710-570575710-4155 75710-4455 75710-4755 75710-5155 75710-5455 75710-575575710-4205 75710-4505 75710-4805 75710-5205 75710-5505 75710-580575710-4255 75710-4555 75710-4855 75710-5255 75710-5555 75710-5855675710-0006 75710-1006 Open 75710-2006 75710-2306 75710-2606 75710-3006 75710-3306 75710-3606Left 75710-2056 75710-2356 75710-2656 75710-3056 75710-3356 75710-365675710-2106 75710-2406 75710-2706 75710-3106 75710-3406 75710-370675710-2156 75710-2456 75710-2756 75710-3156 75710-3456 75710-375675710-2206 75710-2506 75710-2806 75710-3206 75710-3506 75710-380675710-2256 75710-2556 75710-2856 75710-3256 75710-3556 75710-385675710-4006 75710-4306 75710-4606 75710-5006 75710-5306 75710-5606Right 75710-4056 75710-4356 75710-4656 75710-5056 75710-5356 75710-565675710-4106 75710-4406 75710-4706 75710-5106 75710-5406 75710-570675710-4156 75710-4456 75710-4756 75710-5156 75710-5456 75710-575675710-4206 75710-4506 75710-4806 75710-5206 75710-5506 75710-580675710-4256 75710-4556 75710-4856 75710-5256 75710-5556 75710-5856875710-0008 75710-1008 Open 75710-2008 75710-2308 75710-2608 75710-3008 75710-3308 75710-3608Left 75710-2058 75710-2358 75710-2658 75710-3058 75710-3358 75710-365875710-2108 75710-2408 75710-2708 75710-3108 75710-3408 75710-370875710-2158 75710-2458 75710-2758 75710-3158 75710-3458 75710-375875710-2208 75710-2508 75710-2808 75710-3208 75710-3508 75710-380875710-2258 75710-2558 75710-2858 75710-3258 75710-3558 75710-385875710-4008 75710-4308 75710-4608 75710-5008 75710-5308 75710-5608Right 75710-4058 75710-4358 75710-4658 75710-5058 75710-5358 75710-565875710-4108 75710-4408 75710-4708 75710-5108 75710-5408 75710-570875710-4158 75710-4458 75710-4758 75710-5158 75710-5458 75710-575875710-4208 75710-4508 75710-4808 75710-5208 75710-5508 75710-580875710-4258 75710-4558 75710-4858 75710-5258 75710-5558 75710-58581075710-0010 75710-1010 Open 75710-2010 75710-2310 75710-2610 75710-3010 75710-3310 75710-3610Left 75710-2050 75710-2350 75710-2650 75710-3050 75710-3350 75710-365075710-2110 75710-2410 75710-2710 75710-3110 75710-3410 75710-371075710-2150 75710-2450 75710-2750 75710-3150 75710-3450 75710-375075710-2210 75710-2510 75710-2810 75710-3210 75710-3510 75710-381075710-2250 75710-2550 75710-2850 75710-3250 75710-3550 75710-385075710-4010 75710-4310 75710-4610 75710-5010 75710-5310 75710-5610 Right 75710-4050 75710-4350 75710-4650 75710-5050 75710-5350 75710-565075710 75710-4110 75710-4410 75710-4710 75710-5110 75710-5410 75710-571010 75710-4150 75710-4450 75710-4750 75710-5150 75710-5450 75710-5750 RightMaintenanceIt is recommended that each operator of the tool be made aware of, and responsible for, the following maintenance steps:1.Remove dust, moisture, and other contaminants with a clean brush, or soft, lint free cloth.2.Do not use any abrasive materials that could damage the tool.3.Make certain all pins; pivot points and bearing surfaces are protected with a thin coat of high qualitymachine oil. Do not oil excessively.4.When tool is not in use, store in a clean, dry area.5.There are no repair parts available for this tool. Should the tool be damaged a new tool is required.CAUTION: Molex specifications are valid only when used with Molex connectors and tooling.Americas Headquarters Lisle, Illinois 60532 U.S.A. 1-800-78MOLEX******************Far East North HeadquartersYamato, Kanagawa, Japan81-462-65-2324*****************Far East South HeadquartersJurong, Singapore65-6-268-6868*****************European HeadquartersMunich, Germany49-89-413092-0*****************Corporate Headquarters2222 Wellington Ct.Lisle, IL 60532 U.S.A.630-969-4550Fax: 630-969-1352Visit our Web site at 。
过程管理(PDCA环)在军用软件研制质量控制中的应用

的复 杂 性 ,软 件 的复 杂 性 主 要 来 自于软 件 需 求 的 制 单 位 的 软 件 工 程 化 管 理 基 本 上 是 按 照 G JB 复 杂 性 ,对 软 件 需 求 的 正 确理 解 是保 障软 件 质 量 9 0 2 0 质 量 管理 体 系 要 求 标 准 要 求 实施 0 1 09 的重 要 环 节 ; ( )易 出错 :软 件 生产 过程 涉 及 一 系列 的 “ 7 信 息 转 移 ” 在 信 息 转移 的任 何环 节 都 有 可 能 发 生错 ,
2 3
过 程 管 理 ( 环 ) 在 军 用 软件 研 制 质 量控 制 中 的 应 用 P Dc A
提 高 软 件 产 品的 可 移 植 性 ; 5 0 A-2 0 军 用 软 件研 制 能 力 成 熟度 模 型 在 00 08
( 6)复 杂 性 :软 件 的 复 杂 性 既 来 自它 所 处 理 武 器 装 备 承 研 单 位 评价 工作 , 以提 高 军 用软 件 研
软 件 ,无 论 是 装 备 信 息 化 建 设 的 需 要 ,还 是 新 型 委 军 工 定型 委 员 会颁 布 了 军用 软 件 产 品 定 型 管
智 能 武 器 的研 发 ,从 太 空 到 深 海 ,软 件 的 影 子 无 理 办法 》 ,总 装 备 部颁 布 了 ( 用 软 件 质量 管 理 规 ( 军
处 不 在 。软 件 的规 模 越 来 越 大 ,其 复 杂 性 程 度 越 定 ;2 0 0 7年 ,航 空军 工 产 品定 型 委 员 会 印发 了
来 越 高 ,其 地 位 和 作 用越 来 越 重 要 ,未 来 的 发展 , ( 空 军工 产 品配 套 软 件 定 型 管 理 工 作 细 则 。这 ( 航
CIVACON 7500 系列接地盒说明书

CIVACON JUNCTION BOXES7500 SERIES INSTALLATION INSTRUCTION MANUALMANUAL PART NUMBERH50457PAMARCH 20124304 N. MATTOX RD.KANSAS CITY, MO 64150CIVACONH50457PACAUTION: To prevent sparking and vapor ignition in hazardous area, use only hand and air powered tools when installing this unit! 1. PRODUCT DESCRIPTIONThe Model 7500 series of Junction Boxes are a series of general purpose junction boxes design to be used in conjunction with CIVACON’s line of Rack Monitor equipment. These junction boxes provide for easy wiring and maintenance of the plug and cord set to the Overfill Detection Rack Monitor.The Model 7500 Series Junction Boxes come in 4 standard configurations. Each configuration is listed and described below.7500 Junction Box, Standard7510 Junction Box, Thermistor w/Breakaway Plug7520 Junction Box, w/Deadman Switch7540 Junction Box, Optic w/Breakaway PlugOther models with specific options are also available. Please contact the factory for more information on those products.The Junction Boxes each contain a 12 position terminal block and are intended for use with intrinsically safe circuits only. You cannot use these junction boxes for 120 or 240 VAC circuits, or any other non-intrinsically safe circuitry. 2. INSTALLATION AND MOUNTINGThe ideal location of the junction box would be on a support rack in an area which is in close proximity to the loading location and has easy access for maintenance purposes. The mounting location should be located at least 24" off of floor level. This will allow sufficient room for the plug and cord set strain relief spring. Once a suitable location is determined, drill two 3/8 inch holes in the support rack at the desired location. The bolt hole drill pattern for mounting the Junction Box is included on page 2 of this instruction manual. Pages 3 & 4 can be removed from this manual for use as a template and may be missing. Please return the template to this manual section when finished.Once the holes have been drilled in the proper locations, bolt the junction box(s) to the support rack using lock washers to properly ground the unit(s).INSTRUCTIONS3. WIRINGWhen wiring the 7500 series of Junction Boxes, refer to the wiring instructions for the appropriate Rack Monitor being installed. If using a 7510 or 7540 junction box with the breakaway plug, refer to page 5 for wiring diagrams.CAUTION:DO NOT CONNECT 120 OR 240 VAC, OR ANY NON-APPROVED CIRCUITRY THROUGH THESE JUNCTION BOXES.Wire the DEADMAN Switch, if so equipped, into left-hand terminals 11 and 12. On the right-hand side, wire it in series with the wire from terminal 6 to the monitor, as shown. Use this template for drilling the mounting holes in the support structure.CIVACON H50457PACIVACON H50457PATHIS PAGE IS LEFT BLANKCIVACON H50457PACIVACON H50457PACIVACONH50457PAWARNING: CIVACON products should be used in compliance with applicable federal, state, and local laws and regulations. Product selection should be based on physical specificationsand limitations, compatibility with the environment, and the material to be handled. CIVACON MAKES NO WARRANTY OF FITNESS FOR A PARTICULAR USE.4. WARRANTYAll parts and products are thoroughly inspected and tested from the time raw material is received at our plant, until the product is completed. We guarantee that all products are free from defects in materials and workmanship for a period of one year from the date of shipment. Any product that may prove defective within said one year period will, at our option, be promptly repaired, or replaced, or credit given for future orders. This warranty shall not apply to any product which has been altered in any way, which has been repaired by any party other than an authorized service representative, or when such a failure is due to misuse or conditions of use. We shall have no liability for labor costs, freight costs, or any other cost or charges in excess of the amount of invoice for the products.THIS WARRANTY IS IN LIEU OF ALL OTHER WARRANTIES, EXPRESS ORIMPLIED, AND SPECIFICALLY THE WARRANTIES OF MERCHANTABILITY AND FITNESS FOR A PARTICULAR PURPOSE.4.1 TECHNICAL ASSISTANCEIf at any time during the installation a question arises that is not covered in this Installation Instruction, or with any other applicable documents referenced, feel free to call the CIVACON ELECTRONICS TECHNICAL ASSISTANCE LINE :In the U.S.A., Call 1-800-5 CIVACON (800-524-8226)For the CUSTOMER SERVICE DEPARTMENT: In the U.S.A., Call 1-888-526-5657. In other countries, call your local agent.4304 N. MATTOX RD. * KANSAS CITY, MO 64150 PH: (816) 741-6600 * FAX: (816) 741-1061 (888) 526-5657 (888) 634-1433。
PTC推出首款基于角色的应用程序TechPackAccess
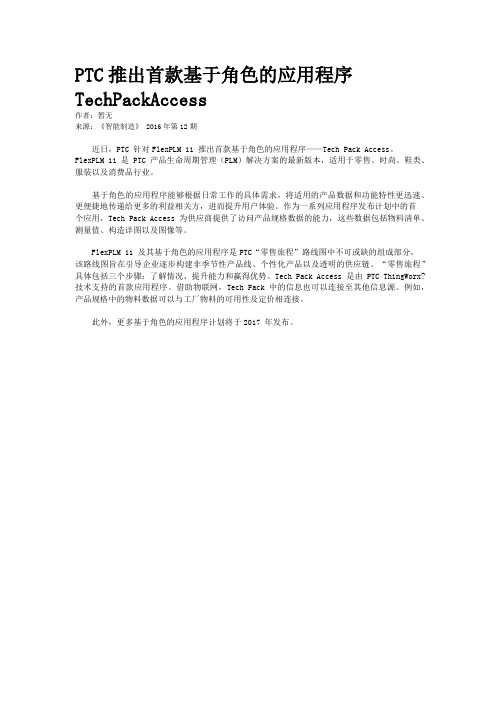
PTC推出首款基于角色的应用程序TechPackAccess
作者:暂无
来源:《智能制造》 2016年第12期
近日,PTC 针对FlexPLM 11 推出首款基于角色的应用程序——Tech Pack Access。
FlexPLM 11 是PTC 产品生命周期管理(PLM)解决方案的最新版本,适用于零售、时尚、鞋类、服装以及消费品行业。
基于角色的应用程序能够根据日常工作的具体需求,将适用的产品数据和功能特性更迅速、更便捷地传递给更多的利益相关方,进而提升用户体验。
作为一系列应用程序发布计划中的首
个应用,Tech Pack Access 为供应商提供了访问产品规格数据的能力,这些数据包括物料清单、测量值、构造详图以及图像等。
FlexPLM 11 及其基于角色的应用程序是PTC“零售旅程”路线图中不可或缺的组成部分,
该路线图旨在引导企业逐步构建非季节性产品线、个性化产品以及透明的供应链。
“零售旅程”具体包括三个步骤:了解情况、提升能力和赢得优势。
Tech Pack Access 是由PTC ThingWorx? 技术支持的首款应用程序。
借助物联网,Tech Pack 中的信息也可以连接至其他信息源。
例如,产品规格中的物料数据可以与工厂物料的可用性及定价相连接。
此外,更多基于角色的应用程序计划将于2017 年发布。
PLC软件的开发管理

PLC软件的开发管理
黄一民
【期刊名称】《机电设备》
【年(卷),期】2014(000)006
【摘要】针对当前船舶设备PLC程序普遍存在的技术运用不规范现象,本文通过借鉴计算机软件开发的相关标准要求,探讨了规范PLC软件开发过程的工作流程,提出了PLC 软件全生存期质量保证的具体措施。
【总页数】4页(P30-33)
【作者】黄一民
【作者单位】海军驻上海704所军事代表室,上海 200031
【正文语种】中文
【中图分类】U665.13
【相关文献】
1.提高中小型软件企业软件开发管理能力的研究 [J], 王嘉星;
2.提高中小型软件企业软件开发管理能力的研究 [J], 王嘉星
3.从软件开发管理看中印软件业的发展 [J], 李卓卡;张京靖
4.从软件开发管理看中印软件业的发展 [J], 李卓卡; 张京靖
5.软件项目:管理、技术宜分家——谈软件开发管理新模式 [J], 刘文威
因版权原因,仅展示原文概要,查看原文内容请购买。
PTC扩展全新应用程序生命周期管理(ALM)解决方案组合

PTC扩展全新应用程序生命周期管理(ALM)解决方案组合
作者:暂无
来源:《智能制造》 2016年第2期
PTC 近日宣布,公司扩展了全新的应用程序生命周期管理(ALM)解决方案组合,以加快软
件和系统工程的发展。
此次扩展涵盖了PTC 全球软件开发、PTC 基于模型的系统工程、PTC 软
件建模以及PTC 系统需求与验证解决方案。
该解决方案组合以订阅的方式提供,将简化解决方
案获取和许可管理流程,让客户更高效地开展协作。
PTC ALM 解决方案能够成功实现跨团队与学科的协作、自动化和复用。
这些解决方案针对
软件工程师、系统工程师、系统需求与质量分析师以及流程架构师的需求而量身定制,并支持
他们与整个产品团队的协作。
Autodesk Navisworks 2015 产品说明书

Quantification in Autodesk ® Navisworks ® 2015Streamline your design-to-cost processes with Autodesk NavisworksTake the guesswork out of budgeting with more effective cost estimation and control.Overcome data disarrayProject quantification requires coordination among multiple project teams. Autodesk ® Navisworks ® helps make it easy to consolidate more accurate design data and engineering information from different sources and disciplines (supporting over 50 different formats).Giving you a single model for whole-project quantification, you can create new estimates as a project progresses by updating the Navisworks project model and exporting takeoffs to shareable spreadsheets or importing them into your cost estimation system.*Cost early and oftenMany firms wait until a design is nearly finished to estimate project costs. But, to include price in your decision making, you must be able to start providing project quantities very early on.Autodesk Navisworks software minimizes manual processes and cuts the time needed for a takeoff from days to just minutes. With 3D models, 2D drawings, or both, you can produce a takeoff at any point in the process. And by continuously updating quantities, it’s much easier to stay in line with cost parameters—helping you identify high-cost problems sooner.Realize efficiencies without disrupting workflowManual quantification has many pitfalls, yet many firms are reluctant to change their workflows. Autodesk Navisworks is straightforward and intuitive —designed to work the way you think. Your workflow stays the same, but it is faster, easier, and produces more accurate results.Perform smarter takeoffsCustomer expec tations and market demands drive c ompetitive pric ing. From the start, Autodesk Navisworks helps you ensure that projects can be constructed within budget by coordinating digital construction information throughout the quantification process.And by collecting and synchronizing design data, your takeoffsare more accurate, providing early awareness of the cost implications of design changes and helping you choose alternatives in line with your budget.Learn MoreGet the full report for a closer look at how Autodesk Navisworks can help you control costs for your next building or construction project.* Quantification is available in Autodesk Navisworks Simulate and Manage 2015 software products and later releases.Autodesk, the Autodesk logo and Navisworks are registered trademarks or trademarks of Autodesk, Inc., and/or its subsidiaries and/or affiliates in the USA and/or other countries. All other brand names, product names, or trademarks belong to their respective holders. Autodesk reserves the right to alter product and services offerings, and specifications and pricing at any time without notice, and is not responsible for typographical or graphicalerrors that may appear in this document. © 2015 Autodesk, Inc. All rights reserved.。
运载火箭通用发射软件测试平台设计

运载火箭通用发射软件测试平台设计
丁芳颐;刘江
【期刊名称】《现代防御技术》
【年(卷),期】2015(043)004
【摘要】详述了一种基于外设组件互连标准(PCI)总线技术和可编程逻辑控制器(PLC)技术的运载火箭通用发射软件测试平台,利用它可以脱离发射控制系统实物对发射软件以及其发出的点火、紧急关机等时串进行全面测试,模拟各种硬件故障和软件故障,从而提高测试覆盖性,保证发射的可靠性和安全性.
【总页数】6页(P178-183)
【作者】丁芳颐;刘江
【作者单位】北京航天自动控制研究所,北京100854;北京航天自动控制研究所,北京100854
【正文语种】中文
【中图分类】V448.25+3
【相关文献】
1.运载火箭控制系统通用仿真软件设计平台 [J], 陈宜成;朱友忠
2.通用嵌入式系统软件测试平台的设计 [J], 沈永清;徐中伟
3.舰艇武器发射系统跨平台通用软件框架设计与应用 [J], 安娜;姜杨
4.舰艇武器发射系统跨平台通用软件框架设计与应用 [J], 安娜;姜杨
5.基于柔性测试技术的发射装置通用测试平台设计 [J], 赵文;璩金超
因版权原因,仅展示原文概要,查看原文内容请购买。
Atlas Copco ToolsNet 8 生产线监控与分析软件说明书

打游戏不回女朋友信息检讨书致女朋友的检讨书尊敬的女友:首先,我诚挚地向你道歉。
我知道我在最近的一段时间里没有给予你足够的关注和陪伴,特别是在与你交往的过程中,我过于沉迷于打游戏,忽略了你的存在和需要。
我深感自己的行为不负责任,对你造成了伤害和失望,我深感愧疚和后悔。
作为一个男友,我理应在关系中尽到责任和义务,给予你陪伴和关注。
然而,在游戏的世界里,我沉迷其中,忽略了与你的交流和沟通。
我意识到这对你来说是很不公平的,我没有给你足够的重视和关心。
我知道,作为我的女友,你有权得到我的时间和关心,而我没有做到这一点,我深感抱歉。
沉迷于游戏,对于我个人来说,也是一个很大的问题。
我明白这种不良的习惯对我的人生和未来是有害的,它不仅浪费了我大量的时间和精力,也阻碍了我在其他方面的成长和进步。
我再次意识到游戏对我造成的负面影响,我下定决心要改变,并且努力做出积极的改变。
我的不对行为不仅仅是对你造成伤害,还对我们的关系带来了破坏。
我真诚地希望能够重新建立起我们之间的信任和联系。
我会努力做好自己,认真对待我们的关系,并且愿意为此付出努力。
为了改变个人的游戏沉迷问题,我已经制定了一些计划和措施。
首先,我会设定一个合理的游戏时间,严格遵守,并将其与我日常生活的其他方面平衡。
其次,我会更加积极地参与各类户外活动和运动,以增加身体的锻炼,减少对游戏的依赖。
同时,我会主动寻求帮助和支持,从朋友和家人那里得到积极的影响和鼓励。
除了改变自己的行为,我也希望能够倾听你的感受和需要。
我会更加关注你的情绪和需求,并作出相应的回应。
我希望我们能够坦诚地交流,解决我们之间的问题,建立一个互相尊重和支持的关系。
最后,我要再次向你表达我由衷的歉意。
我对我的行为感到惭愧和懊悔。
我深深意识到,一个好的男友应该有更多的责任感和成熟度,而我目前的表现不符合这个标准。
我真诚地希望能够通过努力改变自己的行为和态度,重新赢得你的信任和爱。
谢谢你给我机会来写这封检讨书,并且给我改过自新的机会。
测试工具在军用嵌入式软件测试中的应用

测试工具在军用嵌入式软件测试中的应用
刘超华;赵勇
【期刊名称】《电脑编程技巧与维护》
【年(卷),期】2009(000)010
【摘要】阐述了对军用嵌入式软件进行单元测试、静态测试、动态测试时的基本测试方法,以及如何将一些测试工具与测试工作进行有机地结合,从而使测试工作更加高效.
【总页数】2页(P44-45)
【作者】刘超华;赵勇
【作者单位】海军飞行学院,葫芦岛,125001;海军飞行学院,葫芦岛,125001
【正文语种】中文
【中图分类】TP3
【相关文献】
1.嵌入式软件测试工具中间结构的设计与实现 [J], 李晓龙;陆建华;沈雷;罗西;严少清
2.嵌入式软件测试工具LOGISCOPE [J], 郭群
3.嵌入式软件测试工具静态分析研究 [J], 赵嘉;
4.军用嵌入式软件测试技术研究 [J], 周平平;张俊;罗海鹰;李翔
5.军用嵌入式软件测试技术研究 [J], 周平平;张俊;罗海鹰;李翔
因版权原因,仅展示原文概要,查看原文内容请购买。