650整机调试工艺
650T履带吊安装方案

650T履带吊安装方案650T履带吊是一种用于重型工程和建筑工地的大型起重设备。
在进行650T履带吊的安装时,需要考虑以下几个方面:安装地点的选择、设备搬运和安装、安装固定、安装验收等。
下面将详细介绍650T履带吊的安装方案。
一、安装地点的选择:1.地面承载能力强,能够适应650T履带吊的重量和工作要求;2.地面平整稳固,无大块障碍物,以便于吊机的移动和操作;3.周围没有大型设备或建筑物,以确保吊机的安全操作;4.远离居民区或高层建筑,以减少对周围环境和居民的影响。
二、设备搬运和安装:1.设备搬运:650T履带吊属于大型重型设备,搬运时需采用专业起重设备,比如行车和吊车进行搬运。
操作人员应具备相关的专业知识和经验,确保安全。
2.设备安装:(1)车身组装:将吊机的各个组件依照说明书进行组装,确保各个部件的安装准确无误。
(2)配重安装:根据吊机的工作要求,安装合适的配重块作为平衡重量。
配重安装应符合工程要求,并且牢固可靠。
(3)底盘安装:将吊机的底盘放置在预定的安装地点上,加固底盘,确保底盘的稳定性,并使其与地面紧密贴合。
三、安装固定:1.地面固定:将履带吊的底盘和地面进行固定,以提高整机的稳定性和安全性。
可以采用膨胀螺栓或其他牢固的固定方法,确保吊机在工作过程中不发生移动或倾倒。
2.配重固定:配重块是履带吊保持平衡的重要部分,需要根据工程要求进行牢固的固定,以确保吊机的安全使用。
四、安装验收:1.功能检测:在安装完成后,进行吊机的功能检测,包括起重能力、操作灵活度、液压系统等方面的检查,确保设备正常工作。
2.安全检查:检查吊机的安全装置,如限位器、安全防护等是否完好,并进行测试和调试。
3.测试运行:吊机安装完成后,在无人区进行测试运行,检查设备的运转情况和安全性能,确保吊机能够正常工作,无异常情况。
综上所述,650T履带吊的安装方案主要包括选择安装地点、设备搬运和安装、安装固定以及安装验收等步骤。
第九章整机总装与调试工艺

7.2.1 调试的目的与调试要点
7.2.1.1 调试的目的与过程 1.调试的目的 (1)发现设计的缺陷和安装的错误, 并改进与纠正,或提出改进建议。 (2)通过调整电路参数,确保产品的 各项功能和性能指标均达到设计要求。
7.2.1 调试的目的与调试要点
2.调试的过程 (1)通电前的检查(调试准备) 便于发现和纠正比较明显的安装错误。 (2)通电调试 包括: 通电观察、静态调试和动态调试。 (3)整机调试 包括:外观检查、结构调试、通电检查、 电源调试、整机统调、整机技术指标综合测 试及例行试验等。
7.2.1 调试的目的与调试要点
操作安全 操作环境要保持整洁。工作台及工作场 地应铺绝缘胶垫;调试检测高压电路时,工 作人员应穿绝缘鞋。 高压电路或大型电路或产品通电检测时, 必须有2人以上,才能进行。发现冒烟、打 火、放电等异常现象,应立即断电检查。 几个必须牢记的安全操作观念: 断开电源开关不等于断开了电源,不通 电不等于不带电,电气设备和材料的安全工 作寿命是有限的。
总装的装配方式 总装的装配方式,以整机结构来分有 整机装配和组合件装配。 整机装配:把零、部、整件通过各种 连接方法安装在一起,组成一个不可分的 整体,具有独立工作的功能。 组合件装配:整机则是若干个组合件 的组合体,每个组合件都具有一定的功能, 而且随时可以拆卸,如大型控制台,插件 式仪器等等。
7.1
第九章
整机总装与调试工艺
第七章
整机总装与调试工艺
整机总装 调试工艺
7.1
整机总装
总装是将各零、部、整件,按照设计要 求,安装在不同的位置上,组合成一个整 体,再用导线将元、部件之间进行电气连 接,完成一个具有一定功能的完整的机器, 以便进行整机调整和测试。 总装包括机械和电气两大部分。
电子整机的安装与调试
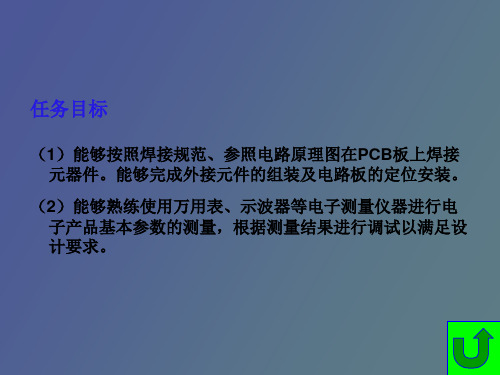
(1)能够按照焊接规范、参照电路原理图在PCB板上焊接 元器件。能够完成外接元件的组装及电路板的定位安装。
(2)能够熟练使用万用表、示波器等电子测量仪器进行电 子产品基本参数的测量,根据测量结果进行调试以满足设 计要求。
任务要求
(1)会使用电烙铁按照工艺要求焊接元器件,并保证无漏 焊、虚焊、错焊。
阻,安装要求如图6-25所示。
短路线
+
1N4148
图6-25 短路线、开关管、1/4W电阻安装示意
②IC插座、涤纶电容、小电解、大电解安装要求如图6-26 所示。电容要插到底,电解电容注意极性。
50V 1 µ F 50V 2 20µF
100 V 2n3J
图6-26 涤纶、电解电容安装示意
③三端稳压电路7812、7912应先固定散热片然后再安装 焊接。 3.面板上元器件安装与焊接
(2)会按照工艺要求加工、焊接导线,并在焊接完成后捆 扎导线。
(3)会进行波段开关、双联电位器等面板上元件的安装。 (4)会使用万用表、示波器进行产品的调试。
6.1 焊接工艺
6.1.1 手工焊接工具
电烙铁是手工焊接的基本工具,其作用是加热焊料和被焊金 属,使熔融的焊料浸润被焊金属表面并生成合金。 1.电烙铁的结构 电烙铁是由烙铁芯、烙铁头、外壳、手柄、接线柱等几部分 组成,如图6-1所示。
形。 ⑤将波段开关打到三角波,调整“三角波粗调”和“三角 波
细调”,测量输出端子波形,调整电位器W5使三角波的幅 度
为10VP-P。 3.整机检修
在调试前,若函数信号发生器工作不正常,应首先进行检 修,故障排除后方可进行调试。下面就常见的典型故障进行 介绍。
(1)无±12V输出 ①检查电源开关焊接是否正确。 ②检查变压器次级是否有18V交流电压输出。 ③检查7812、7912是否焊反、损坏。
仪器设备整机装配工艺作业指导书
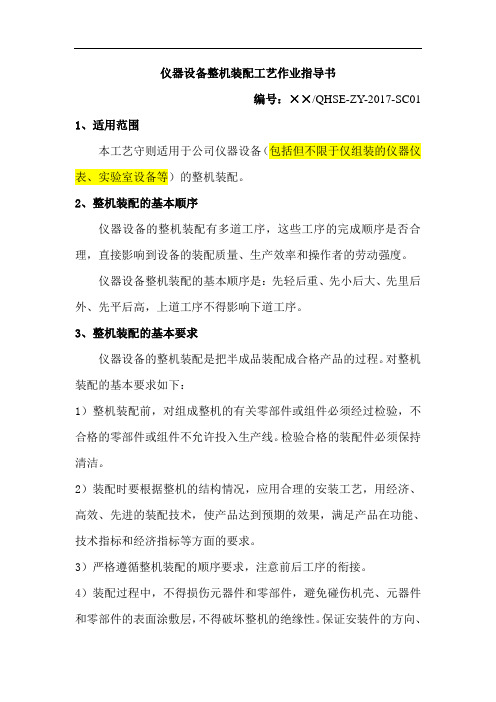
仪器设备整机装配工艺作业指导书编号:××/QHSE-ZY-2017-SC01 1、适用范围本工艺守则适用于公司仪器设备(包括但不限于仅组装的仪器仪表、实验室设备等)的整机装配。
2、整机装配的基本顺序仪器设备的整机装配有多道工序,这些工序的完成顺序是否合理,直接影响到设备的装配质量、生产效率和操作者的劳动强度。
仪器设备整机装配的基本顺序是:先轻后重、先小后大、先里后外、先平后高,上道工序不得影响下道工序。
3、整机装配的基本要求仪器设备的整机装配是把半成品装配成合格产品的过程。
对整机装配的基本要求如下:1)整机装配前,对组成整机的有关零部件或组件必须经过检验,不合格的零部件或组件不允许投入生产线。
检验合格的装配件必须保持清洁。
2)装配时要根据整机的结构情况,应用合理的安装工艺,用经济、高效、先进的装配技术,使产品达到预期的效果,满足产品在功能、技术指标和经济指标等方面的要求。
3)严格遵循整机装配的顺序要求,注意前后工序的衔接。
4)装配过程中,不得损伤元器件和零部件,避免碰伤机壳、元器件和零部件的表面涂敷层,不得破坏整机的绝缘性。
保证安装件的方向、位置、极性的正确,保证产品的电性能稳定,并有足够的机械强度和稳定度。
5)操作人员熟悉安装要求和熟练掌握安装技术,保证产品的安装质量,严格执行自检、互检与专职过程检验的“三检”原则。
装配中每一个阶段的工作完成后都应进行检查,分段把好质量关,从而提高产品的一次通过率。
4、整机装配中的接线工艺1)接线工艺要求导线的作用是用于电路中的信号和电能传输,接线是否合理对整机性能影响较大。
如果接线不符合工艺要求,轻则影响电路信号的传输质量,重则使整机无法正常工作,甚至会发生整机毁坏。
整机装配时接线应满足以下要求:(1)接线要整齐、美观,在电气性能许可的条件下减小布线面积。
如对低频、低增益的同向接线尽量平行靠拢,分散的接线组成整齐的线扎。
(2)接线的放置要可靠、稳固和安全。
徐工650吨组装方案
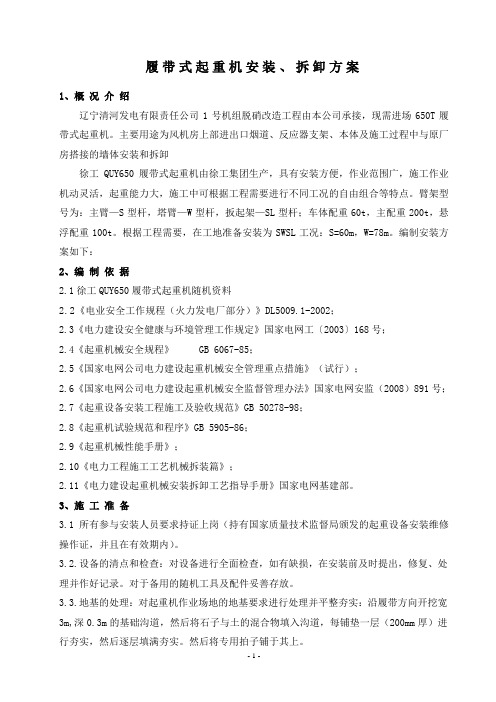
履带式起重机安装、拆卸方案1、概况介绍辽宁清河发电有限责任公司1号机组脱硝改造工程由本公司承接,现需进场650T履带式起重机。
主要用途为风机房上部进出口烟道、反应器支架、本体及施工过程中与原厂房搭接的墙体安装和拆卸徐工QUY650履带式起重机由徐工集团生产,具有安装方便,作业范围广,施工作业机动灵活,起重能力大,施工中可根据工程需要进行不同工况的自由组合等特点。
臂架型号为:主臂—S型杆,塔臂—W型杆,扳起架—SL型杆;车体配重60t,主配重200t,悬浮配重100t。
根据工程需要,在工地准备安装为SWSL工况:S=60m,W=78m。
编制安装方案如下:2、编制依据2.1徐工QUY650履带式起重机随机资料2.2《电业安全工作规程(火力发电厂部分)》DL5009.1-2002;2.3《电力建设安全健康与环境管理工作规定》国家电网工〔2003〕168号;2.4《起重机械安全规程》 GB 6067-85;2.5《国家电网公司电力建设起重机械安全管理重点措施》(试行);2.6《国家电网公司电力建设起重机械安全监督管理办法》国家电网安监(2008)891号;2.7《起重设备安装工程施工及验收规范》GB 50278-98;2.8《起重机试验规范和程序》GB 5905-86;2.9《起重机械性能手册》;2.10《电力工程施工工艺机械拆装篇》;2.11《电力建设起重机械安装拆卸工艺指导手册》国家电网基建部。
3、施工准备3.1 所有参与安装人员要求持证上岗(持有国家质量技术监督局颁发的起重设备安装维修操作证,并且在有效期内)。
3.2.设备的清点和检查:对设备进行全面检查,如有缺损,在安装前及时提出,修复、处理并作好记录。
对于备用的随机工具及配件妥善存放。
3.3.地基的处理:对起重机作业场地的地基要求进行处理并平整夯实:沿履带方向开挖宽3m,深0.3m的基础沟道,然后将石子与土的混合物填入沟道,每铺垫一层(200mm厚)进行夯实,然后逐层填满夯实。
巨冈650加工中心配机手册(刀臂式刀库)V1.1

巨冈650刀臂式加工中心配机手册撰写技术中心徐兵日期2011年1月5日版本V1.1版本更新记录项次更改内容纪录更改日期作者更改后版本01 初版定稿2007-7-30 张伟V1.002 重新修订2011-1-6 徐兵V1.11、重新编排手册结构。
2、刀库规格修改(1)将原修改刀号由MacroM06完成改为由PLCM50完成(2)增加刀库换刀流程中的警报及处理规格(3)刀臂和刀盘马达过载警报时做处理(4)增加警报列表目录第一章机床配置 (5)1.1控制器部分 (5)1.2轴向驱动 (5)1.3主轴、马达及变频器 (5)1.4刀库 (6)1.5周边设备 (6)第二章操作面板介绍 (7)2.1面板定义 (7)2.2操作说明 (7)第三章 IOR列表 (15)3.1 IO列表 (15)3.2 R暂存器 (16)第四章规格 (18)4.1 操作面板操作规格 (18)4.1.1 手动刀杯上/下 (18)4.1.2 手动刀库正/反转 (18)4.1.3 主轴定位 (18)4.2 M_code定义 (18)4.2.1 M_code动作规格说明 (20)4.3 S_code动作规格说明 (22)4.4 T_code动作规格说明 (22)4.5刀库动作规格 (22)4.5.1 T码备刀动作规格(PLC) (22)4.5.2 M06Txx换刀动作规格 (22)4.5.3 M50规格说明 (28)4.5.4 刀号更新规格 (33)4.5.5 刀库复位 (34)4.5.6 刀库保护规格 (22)第五章警报列表 (22)第六章调试步骤 (22)第七章配线图 (22)附录A 驱动器参数设定 (40)附录B控制器参数设定 (42)第一章机床配置1.1控制器部分项目名称规格说明1 控制器SUPER8 Servo4*1PIO5*12 显示器客制3 操作面板客制HK型号:4 键盘客制900型,键盘型态25 手轮远瞻6 输入输出板TB16IN 数量2TB16OUT 数量1TB16OUT-R8 数量17 软体Wince5.0 客制画面1.2轴向驱动项目名称规格说明1 X轴马达安川∑V1.3kw 增量式2 Y轴马达安川∑V1.3kw 增量式3 Z轴马达安川∑V3kw 增量式,带刹车1.3主轴、马达及变频器项目名称规格说明1 主轴BT402 主轴马达晟昌额定功率3.7KW额定频率50HZ马达级数4最高转速8000RPM编码器光学,1024PPR3 变频器蒙德400V5.5KW 光学编码器回授卡1.4刀库项目名称规格说明1 刀臂式刀库德大机械BT40,24把刀1.5周边设备项目名称规格说明1 主轴冷却机2 润滑机3 排削机选配第二章操作面板介绍2.1面板定义2.2操作说明电源开打开控制器电源,准备开始操作机械电源关机器使用完后,关掉控制器电源紧急停止在人员安全或机台操作发生安全顾虑时,压下此钮,机台所有机电控制会跳脱,此时,除了控制器尚有电源之外,伺服、主轴、加工液所有的重电皆跳脱以确保人员或机械的安全性.原点模式寻原点功能说明:当CNC 打开电源,必须做原点模式寻原点功能操作方式:1.由模式选择旋钮选择进入“原点模式”2.按机台运动方向控制键『X+,X-,Y+,Y-,Z+,Z-』C 机械开始复归至原点手动连动模式说明:使用者能藉由此模式,按“JOG”键来做机台移动.操作方式:1.模式选择旋钮选择进入“手动连动模式”2.按机台运动方向控制键『X+,X-,Y+,Y-,Z+,Z-』,机台将移动4.操作者能利用 JOG% 或 G01% 调整寸动切削量5.操作者按机台移动键和快速定位键“〰”在同时, CNC机台将以“快速定位”的速度来移动6.操作者能利用 G00% 快速寸动切削量G00 % :调整G00 % (F0 .25% .50% .100%)G01 % :调整G01/G02 /G03 切削率%备注:刀排推出后禁止手动“JOG”快速移动手动寸动模式说明:使用者能藉由此模式,按“JOG”键来做机台移动.操作方式:1.模式选钮选择“手动寸动模式”.2.按机台移动键『X+,X-,Y+,Y-,Z+,Z- 』,机台以固定的距离来移动.3.可藉由G00“旋钮开关”来调整固定移动的距离;移动的距离范围--- *1 : 1um,*10 : 10um ,*100 : 100umMPG 寸动模式说明:使用者能藉由此模式,旋转“MPG (移动手轮)”来做机台移动.操作方式:1.模式旋钮选择“MPG 寸动模式”2.选择欲移动的轴从模式旋钮3.选择增量距离4.按机台移动键『X+,X-,Y+,Y-,Z+,Z- 』,机台以固定的距离来移动;移动的距离范围---*1 : 1um , *10 : 10um , *100:100um , *1000 : 1000um自动加工模式说明:可使用此功能自动执行NC程序操作方式:1.模式旋钮转至“自动加工模式”.2.在原点复归后,自动加工模式始有效.3.设定工作坐标(G54..G59) ,假如没有设定任何G54..G59在NC程序CNC内定值为 G54.4.到“刀具设定”设定刀具半径补偿及刀具长度补偿.5.按“起动”键,执行NC程序.6.假如必要情况,则按“紧急停止开关”开关暂停NC程序.MDI 加工模式说明:可用此功能执行单节程序,而不用去执行NC程序.操作方式:1.模式旋钮转至“MDI加工模式”2.在原点复归后,MDI加工模式始有效.3.在主画面下选择F4“执行加工画面”.4.按下 F3“MDI 输入”,荧幕中将显示一个对话框.5.在对话框键入资料后,按“ENTER”键输入资料.6.按“起动”键,执行MDI单节程序.7.假如目前单节程序语法正确,程序随着程序的执行而从荧幕上消失.MPG 模拟功能说明:可使用此功能检查NC程序操作方式:1.模式旋钮转至“自动模式”.2.按“MPG 模拟功能”按键,此按键灯“亮”.3.按“起动”键,执行NC程序.C 将改变机械状态从“就绪”变为“加工中”5.机器本身一直保持没有移动6.可旋转“旋转手轮”来执行NC程序.7.MPG(旋转手轮)旋转越快,机械移动速度越快.8.MPG (旋转手轮)停止,CNC机器本身也跟着停止.9.此功能可立即得知程序“能”/ “不能”加工.P.S. 此功能很人性化的辅助使用者去检查程序.程序空跑说明:本功能为检查NC程序操作方式:1.模式旋钮转至“自动模式”2.按“程序空跑”按键,此按键灯“亮”.3.按“起动”键,执行NC程序.C 将改变机械状态,从“就绪”变为“加工中”5.此功能可立即得知程序“能”/ “不能”加工.单节执行说明:可使用此功能检查NC程序操作方式:1.模式旋钮转至“自动模式”2.按“单节执行”键,其讯号灯将“亮”3.按“起动”键,执行NC程序.C 将执行NC程序,但是只有执行一个单节就停止C 将改变机械状态,从“加工中”变为“暂停”6.再次按下“起动”,则 CNC 将继续执行到下一单节.7.此功能针对使用者去将程序一个单节一个单节的检查.选择停止说明:可利用此功能设定NC程序中的M01是否停止 .操作方式:1.模式旋钮转至“自动模式”2.按“选择停止”键,其讯号灯将“亮”3.按“起动”键,执行NC程序.4.当 CNC 执行程序中有“M01”时,CNC 将停止 .C 将改变机械状态从“加工中”变为“暂停”6.此功能使用于换刀及工件检查.选择跳跃说明:可使用此功能设定机器执行到“/”该行是否执行或省略跳过. 操作方式:1.模式旋钮转至“自动模式”2.按“选择跳跃”键,其讯号灯将“亮”3. 按 “起动”键,执行NC 程序.4. 当 CNC 执行到含有 “/”符号的单节 ,CNC 将自动跳过此单节.5. 假如此键没有按, CNC 将会执行此单节.主轴控制主轴正转(CW)主轴停止主轴反转(CCW)主轴寸动 : 主轴转动时 ,按本键 ,主轴速度降为寸动速度工作灯开/关工作灯用加工液开/关加工液用油雾收集器1.主轴运行时自动启动油雾收集器2.主轴停止时延时2分钟停止油雾收集器 3.AUX1关才油雾收集器手动导轨打油1.按AUX2手动打油,比较好检查油路对刀吹气1.手动吹气清洁对刀仪表面及刀具表面,确保对刀仪精度第三章IOR列表3.1 IO列表输入功能输出功能I0 对刀信号(NO)O0 主轴启动I1 X轴正负硬体行程(NC)O1 手轮方向切换I2 X轴原点(NC)O2 切削液I3 气压不足警报(可选择NO|NC)O3 注油机I4 Y轴正负硬体行程(NC)O4 工作灯I5 Y轴原点(NC)O5 绿灯I6 油水分离马达过载警报(NO)O6 黄灯I7 Z轴正负硬体行程(NC)O7 红灯I8 Z轴原点(NC)O8 主轴松刀(电磁阀) I9 数刀信号(N0)O9 加工吹气(电磁阀) I10 对刀过行程(NC)O10 第四轴气刹(电磁阀) I11 刀臂0度信号(NC)O11 主轴中心出水I12 刀臂60度信号(NC)O12 油水分离机I13 刀臂刹车信号(NO)O13 排屑马达I14 刀杯上(NO)O14 主轴定位I15 刀杯下(NO)O15 攻牙模式I16 主轴警报(NO)O16 刀盘正转I17 紧急停止(NC)O17 刀盘反转I18 主轴油冷机异常(NC)O18 刀臂马达正转I19 空气压力不足(NC)O19 刀杯上I20 润滑压力不足(NO)O20 刀杯下I21 手动松夹刀(NO) O21 排屑机正转I22 主轴定位(NO) O22 排屑机反转I23 主轴过热(NO) O23 刀臂马达反转I24 夹刀故障(NO)O24I25 松刀故障(NO)O25I26 切削马达过载警报(NO)O26I27 MAG刀盘马达过载(NO)O27I28 ARM刀臂马达过载(NO)O28I29 第四轴原点(NC)O29I30 第四轴气刹检知(NO)O30I31 排屑马达过载(NO)O313.2 R暂存器R1 M Code控制器执行M CODE 时会将内容放在R1中 ,供 LADDER 读取R2 S Code 控制器执行S CODE 时会将内容放在R2中 ,供 LADDER 读取R3 T Code 控制器执行T CODE 时会将内容放在R3中 ,供 LADDER 读取R13 模式切换(1 Edit 2 Auto 3 MDI 4 JOG 5 INCJOG 6 MPG 7 Home)R14 MPG手轮倍率R15 主轴倍率R16 G01进给倍率R17 JOG倍率R18 G00倍率R33 Z轴机械坐标R36 主轴目前转速R50 目前刀杯号码R51 目标刀所在刀杯号码R52 总刀数R53 主轴转速检测R54 主轴转速检测R55 主轴转速检测R60 刀臂动作R81 打油时间(秒)R82 间隔打油时间(秒)R84 松刀检测延时(0.1秒)R85 夹刀检测延时(0.1秒)R86 油水分离机警报选择(0关闭 1开启)R87 主轴转速到达检测选择(0等待1不等待)R89 换刀点,此参数必须等于2803号参数才能换刀R90 对刀仪过行程跳Z轴负硬体行程功能选择(0关闭 1开启)R92 安全门功能选择(0关闭 1开启)R95 排屑机警报功能选择(0关闭 1开启)R96 氮气压不足警报接点功能选择(1常闭 2常开)R97 第4轴功能选择(0关闭 1开启)R98 主轴油冷机警报功能选择(0关闭 1开启)R99 风压不足警报选择(0关闭 1开启)R100 Z轴等于零点关闭水气油及主轴功能选择(0关闭 1开启)R101 目前刀杯号码(断电存储)R102 主轴刀具号码R103-R127 刀杯号码R590.3 三轴过行程请按(OT.REL)解除R590.7 X轴回零时请确认Z轴位置R590.8 Y轴回零时请确认Z轴位置R590.9 Z轴位置大于5MM不需要回零R611.1 X轴运动中R611.2 Y轴运动中R611.3 Z轴运动中R701 X轴运动方向R702 Y轴运动方向R703 Z轴运动方向R871 主轴有效速度第四章规格4.1 操作面板操作规格4.1.1 手动刀杯上/下(1)在[手动]/[手轮]/[寸动]模式下,按下[刀杯上]/[刀杯下];(2)刀杯到达刀杯上/下信号时,动作结束。
XJ650S中
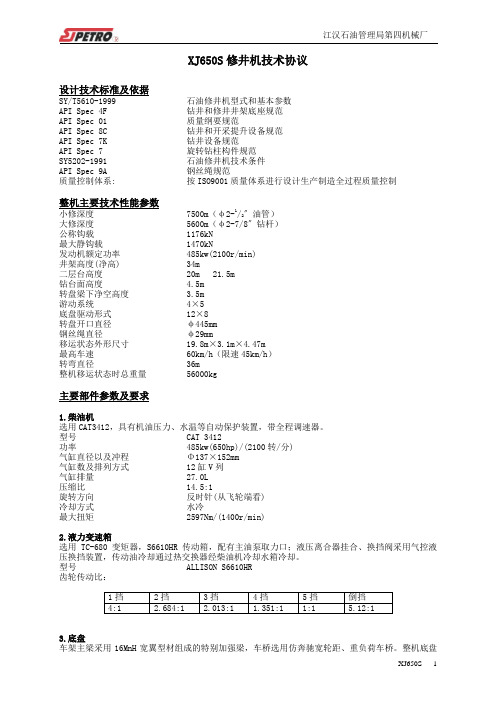
XJ650S修井机技术协议设计技术标准及依据SY/T5610-1999 石油修井机型式和基本参数API Spec 4F 钻井和修井井架底座规范API Spec 01 质量纲要规范API Spec 8C 钻井和开采提升设备规范API Spec 7K 钻井设备规范API Spec 7 旋转钻柱构件规范SY5202-1991 石油修井机技术条件API Spec 9A 钢丝绳规范质量控制体系: 按ISO9001质量体系进行设计生产制造全过程质量控制整机主要技术性能参数小修深度7500m(φ2-1/〞油管)2大修深度5600m(φ2-7/8〞钻杆)公称钩载1176kN最大静钩载1470kN发动机额定功率485kw(2100r/min)井架高度(净高) 34m二层台高度20m 21.5m钻台面高度 4.5m转盘梁下净空高度 3.5m游动系统4×5底盘驱动形式12×8转盘开口直径φ445mm钢丝绳直径φ29mm移运状态外形尺寸19.8m×3.1m×4.47m最高车速60km/h(限速45km/h)转弯直径36m整机移运状态时总重量56000kg主要部件参数及要求1.柴油机选用CAT3412,具有机油压力、水温等自动保护装置,带全程调速器。
型号CAT 3412功率485kw(650hp)/(2100转/分)气缸直径以及冲程Φ137×152mm气缸数及排列方式12缸V列气缸排量27.0L压缩比14.5:1旋转方向反时针(从飞轮端看)冷却方式水冷最大扭矩2597Nm/(1400r/min)2.液力变速箱选用TC-680变矩器,S6610HR传动箱,配有主油泵取力口;液压离合器挂合、换挡阀采用气控液压换挡装置,传动油冷却通过热交换器经柴油机冷却水箱冷却。
型号ALLISON S6610HR齿轮传动比:3.底盘车架主梁采用16MnH宽翼型材组成的特别加强梁,车桥选用仿奔驰宽轮距、重负荷车桥。
电子产品整机调试工艺
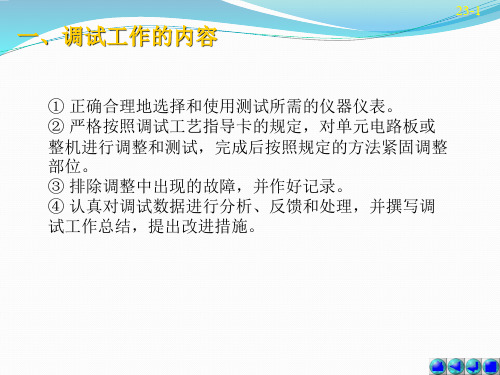
23-11
②测电阻值法 用于检查电路中电阻元件的阻值是否正确;检查电容器是否断 线、击穿和漏电;检查半导体器件是否击穿、开断及各PN结 的正反向电阻是否正常等。检查二极管和三极管时,一般用万 用表的R×100或R×1K挡进行测量。在检查大容量电容器 (如电解电容器)时,应先用导线将电解电容的两端短路,泄 放掉电容器中的存储电荷后,再检查电容有没有被击穿或漏电 是否严重,否则,可能会损坏万用表。在测量电阻值时,如果 是在线测试,还应考虑到被测元器件与电路中其它元器件的等 效并联关系,需要准确测量时,元器件的一端必须与电路断开。
对怀疑有故障的元器件,可用一个完好的元器件替代,置换 后若电路工作正常,则说明原有元器件或插件板存在故障,可作 进一步检查测定之。这种方法力争判断准确。对连接线层次较多、 功率大的元器件及成本较高的部件不宜采用此法。
对于集成电路,可用同一芯片上的相同电路来替代怀疑有故 障的电路。有多个与输入端的集成器件,如在实际使用中有多余 输入端时,则可换用其余输入端进行试验,以判断原输入端是否 有问题。
23-3
2.调试工艺文件的基本内容
① 根据国际、国家或行业颁布的标准以及待测产品 的等级规格具体拟定的调试内容。 ② 调试所需的各种测量仪器仪表、工具等。 ③ 调试方法及具体步骤。 ④ 调试所需的数据资料及图表。 ⑤ 调试接线图和相关资料。 ⑥ 调试条件与有关注意事项。 ⑦ 调试工序的安排及所需人数。 ⑧ 调试安全操作规程。
23-18
SD650系列伺服驱动器使用说明书

目录1综述 (1)1.1安全注意事项 (1)1.2技术规范 (4)2产品信息 (6)2.1产品到货检查 (6)2.2铭牌及型号说明 (6)2.3规格型号及额定电流 (7)3安装与接线 (8)3.1外形结构尺寸图 (8)3.2标准连接图 (10)3.3主回路端子接线图及器件选型 (11)3.4控制回路端子 (14)3.5多功能接点输入的连接 (18)3.6制动电阻(制动单元)的连接 (19)4调试与运行 (24)4.1操作面板的布局及功能说明 (24)4.2基本操作 (25)4.3调试流程 (27)5功能参数简表 (31)6故障诊断及对策 (49)7外围设备及选购件 (58)8定期检查与维护 (63)附录:Modbus通讯协议 (66)1综述首先感谢您购买本公司的SD650系列伺服驱动器。
本手册介绍了如何正确使用本产品以便获得良好的收益。
在使用产品(安装、接线、运行、维护、检查等)前,请务必认真阅读本手册。
另外,请在完全理解本手册所述的安全注意事项后再使用本产品。
1.1安全注意事项为保证安全、可靠、合理的使用本产品,请在完全理解本手册所述的安全注意事项后再使用该产品。
警示标志及其含义本手册中使用了下列标记,表示该处是有关安全的重要内容。
如果不遵守这些注意事项,可能会导致人身伤亡、本产品及关联系统损坏。
危险:如果操作错误,可能会造成死亡或重大安全事故。
警告:如果操作错误,可能会造成死亡或重大安全事故。
注意:如果操作错误,可能会造成轻伤。
重要:如果操作错误,可能导致本产品及关联系统损坏。
警示标志位置如下图所示:图1-1:SD650系列伺服驱动器外壳警示标志位置操作资质本产品必需由经过培训的专业人员进行安装、接线、运行、维护保养等操作。
本手册上所谓“经过培训的专业人员”是指在本设备上进行工作的人员必须经过专业的技能培训,熟悉设备的安装、接线、运行和维护保养,并正确应对使用中出现的各种紧急情况。
安全指导安全规则和警告标志是为了您的安全而提出的,是防止操作人员人身受到伤害、本产品及关联系统受到损坏而采取的措施;请在使用前能仔细阅读本手册,并严格按照本手册中的安全规则和警告标志进行操作。
数控机床调试步骤要求
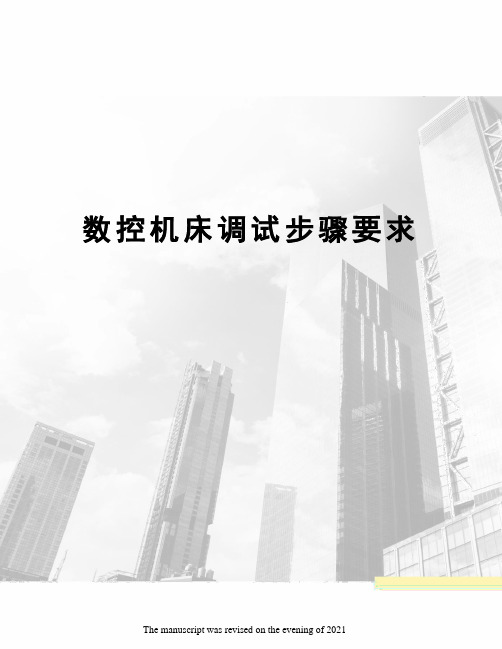
数控机床调试步骤要求 The manuscript was revised on the evening of 2021数控机床调试步骤要求(一)安装调试的前期准备工作:用户的准备事项,由售后服务人员联系落实。
(1)立式加工中心1.机床的吊运与安装:包括机床的吊运、开箱、安装、粗调水平、防锈油的清洗。
其中安装可采用混凝土地基加地脚螺钉固定机床,或直接使用随机的调整垫铁加地脚螺钉固定机床。
2.根据机床型号的不同确定外接电源线的线径,以下为各种型号机床参考线径:CY-VMC650采用10平方毫米左右线径。
CY-VMC850采用16平方毫米左右线径。
CY-VMC1060/1270/1370采用25平方毫米左右线径。
CY-VMC1580/1690/1890采用35平方毫米左右线径。
所有机床必须可靠接地。
3.安装调试前用户需购买以下备件物品:空压机,要求排量在立方米/分钟以上。
连接空压机至机床的PTV气管,外径为12毫米。
标准刀柄和拉钉:CY-VMC650/850/1060采用型号为BT-40刀柄和45°拉钉;CY-VMC1270/1370/1580采用型号为BT-50刀柄和45°拉钉。
刀具的购买:根据用户加工零件的实际情况,来确定购买不同夹持方式的刀柄和刀具,比如:铣平面用的盘铣刀柄和直径为Ф63、Ф80、Ф100不等的盘铣刀体及刀片。
强力铣夹头刀柄,主要方便于夹持直径较大的外圆铣刀和球头铣刀,例如夹持Ф20毫米的球头铣刀。
弹簧夹头刀柄,主要方便于夹持小直径外圆铣刀和球头铣刀,例如夹持Ф3~Ф16毫米的外圆铣刀。
常用的刀柄规格型号为Ф32型刀柄。
一体式或分离式钻夹头刀柄,主要用于装夹直柄小直径钻头,常见刀柄规格型号为Ф3~Ф13毫米的钻夹头。
带扁尾莫氏锥孔刀柄,主要用于装夹锥柄钻头。
常用的刀柄规格型号是3号和4号莫氏锥孔刀柄。
不带扁尾莫氏锥孔刀柄,主要用于装夹锥柄外圆铣刀。
常用的刀柄规格型号是3号和4号莫氏锥孔刀柄。
内燃机装配调试工艺
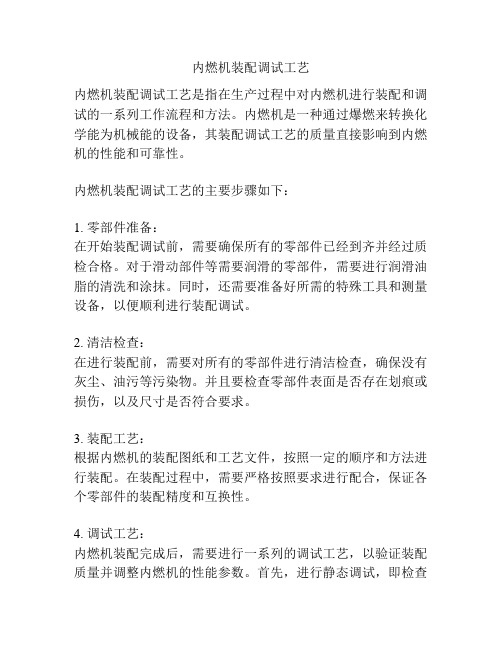
内燃机装配调试工艺内燃机装配调试工艺是指在生产过程中对内燃机进行装配和调试的一系列工作流程和方法。
内燃机是一种通过爆燃来转换化学能为机械能的设备,其装配调试工艺的质量直接影响到内燃机的性能和可靠性。
内燃机装配调试工艺的主要步骤如下:1. 零部件准备:在开始装配调试前,需要确保所有的零部件已经到齐并经过质检合格。
对于滑动部件等需要润滑的零部件,需要进行润滑油脂的清洗和涂抹。
同时,还需要准备好所需的特殊工具和测量设备,以便顺利进行装配调试。
2. 清洁检查:在进行装配前,需要对所有的零部件进行清洁检查,确保没有灰尘、油污等污染物。
并且要检查零部件表面是否存在划痕或损伤,以及尺寸是否符合要求。
3. 装配工艺:根据内燃机的装配图纸和工艺文件,按照一定的顺序和方法进行装配。
在装配过程中,需要严格按照要求进行配合,保证各个零部件的装配精度和互换性。
4. 调试工艺:内燃机装配完成后,需要进行一系列的调试工艺,以验证装配质量并调整内燃机的性能参数。
首先,进行静态调试,即检查各个部件的连接是否牢固,是否存在松动现象。
然后进行动态调试,包括检查运动部件的运转是否灵活,各个部件是否有异常声响等。
最后,进行试车和调整,通过调整供油、点火时间和点火能量等参数,确保内燃机能够正常启动和运转,并达到设计要求的性能。
5. 检验验收:内燃机装配调试完成后,需要进行全面的检验验收。
检验包括外观检查、尺寸测量、性能测试等,以确保装配质量和性能满足要求。
只有在验收合格后,才能将内燃机交付给用户或进行下一步的使用环境。
内燃机装配调试工艺的关键是精确操作和严格控制。
需要注意的是,装配和调试过程中应具备良好的协作和沟通,确保各环节之间的顺利进行。
同时,也需要不断总结和改进工艺,以提高装配质量、效率和可靠性。
通过科学合理的装配调试工艺,可以保证内燃机的性能和可靠性,满足用户的需求。
内燃机装配调试工艺是内燃机制造过程中至关重要的环节之一。
只有在装配和调试过程中严格按照规定的工艺进行操作,才能确保内燃机的质量和性能达到设计要求。
最新ipc-tm-650 中文资料讲解

IPC-TM-650 实验方法手册目·录Section 2.1 目视检测方法Visual Test Methods2.1.1 手动微切片法2.1.1.1 陶瓷物质金相切片2.1.1.2 半自动或全自动微切片设备2.1.2 针孔评估,染色渗透法2.1.3 镀通孔结构评估2.1.5未覆和覆金属材料表面检查2.1.6 玻纤厚度2.1.6.1 玻璃纤维的重量2.1.7玻璃纤维的纤维数量2.1.7.1 纤维数计算,有机纤维2.1.8 工艺2.1.9铜箔表面刮伤检验2.1.10 不溶解的双氰胺目视检验2.1.13 绕性印制电路材料内含物和空洞的检验Section2.2 物理量纲测试方法Dimensional Test Methods2.2.1 外观尺寸确认2.2.2 目视检测尺寸2.2.3 导体边界清晰度测量2.2.4 介电质尺寸稳定性和柔韧性2.2.6 钻孔孔径的测量2.2.7 镀通孔孔径的测量2.2.8 孔的位置2.2.10 孔位和线路位置2.2.11 连接焊盘重合度【层与层之间】2.2.12 重量方法测定铜的厚度2.2.12.1 处理后和未经处理的铜箔总厚度和外观因素2.2.12.2 剥离载体后铜箔重量和厚度2.2.12.3 可蚀刻载体铜箔重量和厚度测量2.2.13.1 孔内镀层厚度2.2.14 锡粉颗粒尺寸分配-对于类型1-4使用屏幕方法2.2.14.1 锡粉颗粒尺寸-使用显微镜测试方法2.2.14.2 锡粉颗粒尺寸-光学图片分析器方法2.2.14.3 最大锡粉颗粒的定义2.2.15 电线尺寸(扁平的线路)2.2.16 用钻孔样板来评估底片2.2.16.1 透明图评估原图底片2.2.17 金属箔表面粗糙度和轮廓(触针法)2.2.17A 金属箔表面粗糙度和外观(触针法)2.2.18 机械法测量基材板厚度2.2.18.1 切片测定基材覆铜厚度2.2.19 测量图形孔位2.2.19.1 剪切的层压板和半固化片长度、宽度和垂直度Section2.3化学量纲测试方法Chemical Test Methods2.3.1.1 覆金属铜箔层压板的化学清洗2.3.4.2 层压板、半固化片及涂胶箔产品的耐药品性(暴露于溶剂)2.3.4.3 基材的耐化学性(耐二氯甲烷)2.3.6 过硫酸铵蚀刻法2.3.7 氯化铁蚀刻法2.3.7.1 氯化铜蚀刻法2.3.9 印制线路板用材料的燃烧性2.3.10 印制线路板用层压板的燃烧性2.3.11 玻璃布结构2.3.14 印制、蚀刻、电镀测试2.3.15 铜箔或镀层的纯度2.3.16 半固化的树脂含量(灼烧法)2.3.16.1 半固化片的树脂含量(称重法)2.3.16.2 上胶后的半固化重量2.3.17 半固化片的数值流动百分度2.3.17.2“不流动”半固化片的树脂流动度2.3.18 半固化片的凝胶化时间2.3.19 半固化片的挥发物含量2.3.22 铜箔保护涂层质量2.3.23 热固性防旱的(耐久性)固化测试2.3.23.1 UV诱发的干膜阻焊剂的固化(耐久性)2.3.25 溶剂萃取的电阻率2.3.26 表面污染物的离子检测(动态法)2.3.31 U.V.固化物料的固化程度2.3.38 表面有机污染物的检测方法(企业内)2.3.39 表面有机污染物的检测方法(红外分析法)Section2.4 机械测试方法Mechanical Test Methods2.4.1 镀层附着力2.4.1.1 文字油墨附着力2.4.1.5 加工转移测定2.4.2.1 铜箔的弯曲疲劳和延展性2.4.4 层压板的弯曲强度(室温下)2.4.4.1 层压板的弯曲强度(高温下)2.4.6 热油冲击2.4.7 印制电路材料的加工性2.4.8 覆金属箔板的剥离强度班组班前安全活动记录教育类别:年月日。
终端整机组装工艺标准(共129页)

目录Table of Contents1终端整机工艺(gōngyì)辅料应用121.1概述(ɡài shù) 121.2整机工艺辅料清单(qīngdān)及辅料变更申请管理要求13 1.3辅料存储环境及使用(shǐyòng)要求132终端螺钉紧固工艺标准 152.1工艺概述152.1.1螺钉紧固152.1.2螺钉规格定义162.1.3扭矩172.1.4紧固扭矩182.2设备及工装要求182.2.1电批182.2.2批头192.2.3螺钉自动送料机构212.2.4自动螺钉机222.2.5锁螺钉夹具232.2.6扭矩测试计252.3设备及工装点检维护要求272.4工艺操作规范272.4.1锁螺钉操作步骤272.4.2操作注意事项282.4.3扭矩设定规范292.4.4扭力校验注意事项302.5常见失效和检验方法302.5.1机牙螺钉302.5.2自攻螺钉313终端热熔工艺标准333.1工艺概述333.2设备和工装要求333.2.1设备概述333.2.2设备规格要求343.2.3设备安全要求343.3热熔工装夹具设计353.3.1夹具结构353.3.2热熔头外形373.3.3夹具设计注意事项383.4工艺操作规范383.4.1操作规范383.4.2不同材料的热熔温度压力设置推荐表393.4.3操作注意事项413.5设备维护及点检(diǎn jiǎn)要求413.6常见(chánɡ jiàn)失效及在线检验标准423.6.1外观(wàiguān)检测423.6.2设备常见故障及排除(páichú)方法42 4终端粘贴工艺标准444.1工艺概述444.1.1TP背胶粘贴444.1.2天线背胶粘贴444.2设备工装要求444.2.1设备规格要求444.2.2TP压合夹具:454.2.3天线压合夹具474.2.4夹具点检保养要求484.3背胶粘贴操作规范494.3.1TP背胶粘贴规范494.3.2天线背胶粘贴504.4在线检验504.4.1TP粘贴压合在线检验504.4.2天线粘贴压合在线检验 515终端TP点胶工艺标准515.1工艺概述515.2工艺环境要求525.3设备工装要求525.3.1点胶设备、喷胶设备要求525.3.2点胶机、喷胶机设备使用及注意事项545.3.3点胶机、喷胶机程序设置规范545.3.4TP组装及预压设备和治具575.3.5TP组装保压治具615.4胶水使用规范655.4.1单组份胶水特性655.4.2乐泰3542胶水使用要求 655.4.3富乐9652胶水使用要求 665.5TP点胶操作规范675.5.1准备阶段675.5.2点胶685.5.3TP组装 685.5.4预压685.5.5保压685.6TP喷胶操作规范695.6.1准备阶段695.6.2TP喷胶 695.6.3TP喷胶胶路检查705.6.4TP组装 705.6.5预压705.6.6保压705.7在线(zài xiàn)检验705.7.1成品外观(wàiguān)检查 705.7.2在线(zài xiàn)可靠性验证716终端激光打标(dǎ biāo)工艺标准736.1工艺概述736.2设备和工装要求736.2.1设备分类736.2.2设备系统组成746.2.3设备安全要求746.2.4夹具设计规范756.2.5夹具设计注意事项766.3工艺操作规范766.3.1工作步骤766.3.2开关机766.3.3焦距调整766.3.4软件参数说明776.3.5脚本文件说明796.3.6参数调试技巧796.3.7操作注意事项806.4设备维护点检816.4.1维护点检内容816.4.2维护点检表格816.4.3维护注意事项826.5常见失效及在线检验要求836.5.1常见异常处理对照表836.5.2外观检验836.5.3设备故障及排除方法857终端超声波焊接工艺标准867.1工艺概述867.2设备和工装要求867.2.1超声波塑胶焊接设备867.2.2超声波焊接设备的结构 867.2.3设备安装调试说明877.2.4焊头(工装上模)设计要求887.2.5定位夹具(工装下模)设计要求89 7.3工艺操作规范897.3.1安装焊头897.3.2超声波检测897.3.3底模固定及焊头调整897.4设备的点检与维护907.4.1日常点检项目907.4.2设备维护项目907.5常见失效及在线检验标准907.5.1在线检验与问题分析对策907.5.2可靠性验证918终端标签打标(dǎ biāo)工艺标准错误!未定义书签。
第一台整机样机硬件调试总结报告1

第一台整机样机硬件调试总结报告一、第一台整机样机的硬件调试过程。
从12月16日,aerodyn公司汉斯开始布机舱内的电缆开始,到12月29日机舱内各设备硬件基本调试成功。
第一台整机样机机舱内布线、接线以及设备硬件通道的调试基本上进行了2周的时间。
这一段的工作可以分为3个阶段。
第一阶段是由汉斯指导进行机舱内电缆的布线以及我们自己进行的接线工作。
第二阶段是aerodyn公司struve和李洪涛来以后,重新进行电缆的布线和接线工作。
第三阶段是由我们配合李洪涛进行机舱内各设备的硬件调试工作。
下面把这三个阶段的主要工作简要的总结一下。
第一阶段是从12月16日到12月17日。
汉斯首先根据struve提供的电气原理图的顺序来确定机舱内电缆的走线的方向、数量和规格。
下来根据各外部用电设备在机舱中所处的位置以及电缆桥架的走向来确定相应电缆的长度。
这一阶段共布线大约48根,并对偏航电机、液压阀等容易接线的部件进行了接线。
第二阶段是从12月18日到12月22日。
Struve和李洪涛重新进行电缆的布线和接线工作。
由于第一阶段在电缆桥架进行布线时,没有考虑到强弱电电缆的区别,同时电缆之间交叉。
故重新对电缆进行了布线。
经过重新布线后,强弱电在电缆桥架中分离,强电电缆靠电缆桥架内侧,弱点信号电缆靠电缆桥架外侧。
同时在布线时把电缆按顺序摆放,使电缆不产生交叉和缠绕,这样在电缆桥架中摆放电缆既是为了技术的要求,同时又能达到美观方便的要求。
在这一段时间的工作中,从struve身上学习到最大的体会是要有良好的工作习惯和工作态度。
在工作中首先打扫卫生,保持电缆桥架和机舱支架上的卫生。
防止有铁屑等对电缆造成破坏。
下来在工作中按照很高的标准来要求每一项工作,这样就可以保证整体工作的高质量。
同时在工作时注意保持工作环境的卫生,以及工具的及时归位。
第三阶段是从12月23日至12月29日。
Struve走后,由李洪涛为主,我们配合其对目前机舱柜上连接的所有设备的硬件输入和输出通道进行测试。
双声道BTL功放整机装配与调试
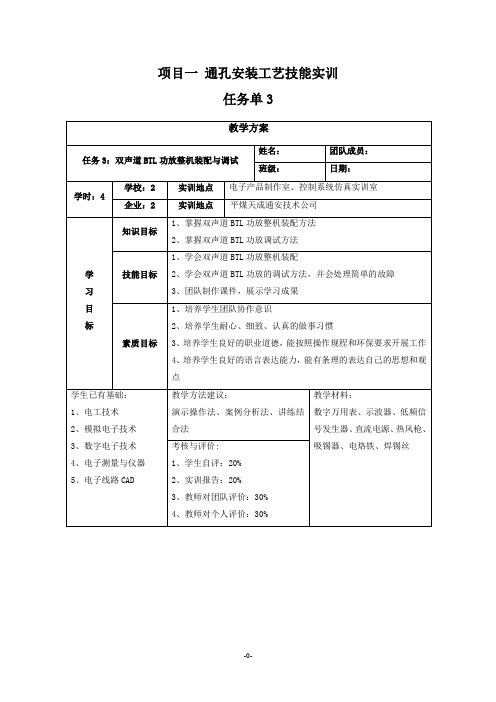
项目一通孔安装工艺技能实训任务单3一、任务布置1. 完成双声道BTL功放整机装配2.完成双声道BTL功放的调试操作,并会处理简单的故障3.团队制作课件,展示学习成果二、相关知识组装完元件的电子产品,按照电子产品的生产工艺要求,要分步地进行电路调试和测试,使其技术指标达到设计要求,对于故障机还需进行检修。
主要是培养学生具有一般电子产品的调试和测试能力、产品故障的分析和解决问题的能力。
本任务对应国家职业技能电子产品维修工和调试工相关操作能力要求。
电子产品整机装配的工艺流程因设备的种类、规模不同,其构成也有所不同,但基本工序大致可分为装配准备、装联、调试、检验、包装、入库等几个阶段,整机装配工艺过程见图3.1。
图3.1 整机装配工艺流程三、技能要点(一)双声道BTL功放整机装配过程1.安装印制电路板将印制电路板装入机箱中,并将四个角用自攻螺丝固定。
将TDA2030的散热片与元件之间加注导热硅胶,以提高其散热效果。
2.焊接导线将环形变压器固定在机箱内,并紧固好螺丝,接上电源进线,变压器输出端接入功放电源输入端。
同时将电源指示灯、音量电位器、电源按键、音频输入接线柱、音频输出接线柱等连接导线焊接到相应位置。
3.扎线将音频输入线、音频输出线、变压器输出线、音量电位器接线等导线分组用线扎捆在一起,排放整齐。
4.固定装外壳将机箱上盖盖好,并用螺丝固定。
5.检查总装完毕,检查安装是否牢固,表面是否有划痕,通电试机。
(二)双声道BTL功放调试1.所有元器件焊接完成后目视检查元器件:型号、规格、数量及安装位置,方向是否与图纸符合。
焊点检查:有无虚、漏、桥接、飞溅等缺陷。
2.电源电路调试将环形变压器次级线圈交流12V接入电源电路,在空载的情况下正常直流输出电压应在±14V,并且电源指示灯亮。
将数字万用表电流档串接入电源电路,此时电流表应该瞬时电流较大,然后电流跌到最小(200mA以内),若电流始终较大,应断电检查。
FP650火焰光度计说明书
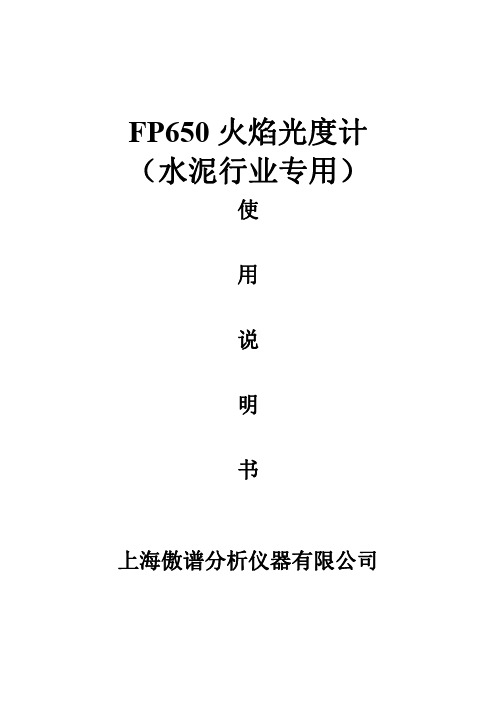
6)、计算:
在测试中标准溶液的浓度为 15.0μg/ml,测得样品的浓度度为
二 、调试: 1)、打开主机电源开关,打开泵启动开关,压力表显示 0.13~0.2mpa 间.
2)、把进样管插入蒸馏水中吸入蒸馏水,吸蒸馏水时注意观察废液杯是 否有废液匀速的排出,如废液排出不是很匀速请观察雾化器下方的乳胶管中是否 有气泡,如有气泡请用手挤压乳胶管将气泡排出,如果还是不行请吸酒精 3~4 分 钟进行清洗,再吸蒸馏水观察一下, 废液排出是否匀速,这时气泡因该已排 除.(这一步非常重要,如没搞好会引起仪器的不稳定)
FP650 火焰光度计 (水泥行业专用)
使 用 说 明 书
上海傲谱分析仪器有限公司
1、 原理简述 2、 用途 3、 主要技术指标 4、 仪器正常使用条件 5、 仪器体积、重量、成套性、燃料说明 6、 仪器的结构 7、 使用前的准备 8、 仪器的操作 9、 保养和维护
1、 原理简述: 从分子结构理论了解到:原子的外层电子总沿着固定的轨
50 都能兼顾,但相对的数据误差就大一点. 用户熟悉操作火焰光度计后,定能得到理想的测试方案. 4、关.关机后,仪器 燃气阀可不必旋动,仍维持原状态.因为到下一次使用时,如燃料不变, 那燃烧状况也不会有大的变化,所以待下一次开机点火时,就不必对 火焰状况多加调整.若下一次使用时,点火困难,可稍增大燃气量,待 引燃后,稍加调整即可. 9、 保养和维修
变化量≤3℅.每分钟测量 1 次,共测定 6 次,仪器示值的相对 最大变化量≤15℅ 5、 重复性: ≤3℅ 6、 线性误差:K: ≤0.005mmol∕L
Na: ≤0.03mmol∕L 7、 响应时间:<8s 8、 样品吸喷量:<6mL∕min 4、 仪器正常使用条件 a) 环境温度:+10℃~+35℃; b) 相对湿度:≤ 85%; c) 仪器应水平放置于无震动的工作台上,避免强光直接照射,周
- 1、下载文档前请自行甄别文档内容的完整性,平台不提供额外的编辑、内容补充、找答案等附加服务。
- 2、"仅部分预览"的文档,不可在线预览部分如存在完整性等问题,可反馈申请退款(可完整预览的文档不适用该条件!)。
- 3、如文档侵犯您的权益,请联系客服反馈,我们会尽快为您处理(人工客服工作时间:9:00-18:30)。
底图总号更改标记数量文件号签名日期签名日期编制第页1一调试所需设备1.FLUKE189数字万用表一块2.TEK A622交直流电流钳一套3.随机工具一套4.DYNALIZERIII 高压测试系统一套5.假负载一套(包括150kV假负载、500mA假负载及透视假负载)7 X光机测试平台一套(包括计算机系统、影像系统和相关附件)8 TDS3012B型示波器一台9 延伸板一套10 液压搬运车一台二联机准备1.高压电缆装配工艺将高压头用绸布和酒精擦拭干净,干燥后才能予以装配。
打开高压发生器的“十”“一”板盖子,用同样的方式擦拭清洁高压插座,待干燥后予以装配。
在TANK两个高压头插座中分别注入高压用绝缘油5毫升左右。
高压头插入插座中,轻轻转动至合适的位置按下之后,拧紧压盖,注意极性不能接反。
发生器下柜门侧旋转阳极端子排按球管电缆信号标识分别接到公共端、主绕组、启动绕组,和温控开关上。
2.控制台信号线联接工艺将数据线的两端分别插入发生器接口板和控制台的相应插座中,并将螺丝拧紧。
3.电源线联接工艺将380V三相五线制电缆从高压柜后面板圆孔中穿入。
将三根火线接到60A保险管上端插头,零线、地线分别接到接线柱上。
三上电前准备工作使用性 1 检查高压发生器内所有接插件的状态(要求接触良好、无插错或反接现象等);2 高压发生器内所有保险丝的状态(无断路);3 检查三相进线、地线、零线是否联接正确无短路;4 用万用表测量旋转阳极端子排的白、兰线间电阻值就为14Ω左右,白、黑线间电阻应为45Ω左右。
四整机功能测试步骤1 检查输入总电源电压是否为380伏,若正常则打开电源总开关,检测发生器主保险丝之间电源电压。
2 关掉发生器主电源,用万用表测量主输入端电压,确认没有电压后扣上保护盖,重新打开电源,发生器接口板上DS1应有效,关闭电源。
3 拔下CPU板上的J13插头,AEC板,I/O扩展板连接电缆。
按下发生器接口板的ON按钮,检测并记录下发生器接口板右下方各测试点的电压是否正常。
测试完后,按下OFF按钮,然后将插头插上,按下发生器接口板的ON按钮,再测试一遍各点电压是否正常。
4 DIP开关设置1)发生器CPU板检查SW1设置,将SW1-1,-2,-6,-7,-8拨到ON位置,SW1-3,-4,-5拨到OFF位置。
SW1-8拨到OFF位置,通电后将CPU板出厂默认设置存储到RAM中。
关电后将SW1-8拨到ON位置。
2)控制台CPU板检查SW1的设置,所有开关应设到OFF,将SW1-8拨到ON位置。
通电后将控制台出厂默认设置存储到RAM中。
关电后将SW1-8拨到OFF位置。
5 打开控制台上电源开关,并观察控制台显示MEMORY TEST…..will be display底图总号更改标记数量文件号签名日期签名日期编制第页2HIGH FREQUENCY GENERATOR 50 KW WILL BE DISPLAYEDTHE next screen will show console software revision and power soft revision 6 在高压发生器柜内,检查如下情况:1)高压电源辅助驱动板上D43亮2)在CPU板上检查如下指示灯应有效:使用性DS38 +5VDS41 +15VDS43 -15VDS45 +12VDS46 -12V按下ON按钮打开电源,观察高压CPU板上的自检灯是否以1Hz频率闪烁、左上角的通讯指示灯是否闪烁,右边的状态灯的状态是否正常;3)辅助驱动板上的LED D12、D15、D43应同时有效,8秒后应听到交流接触器吸合声音同时LED D16 有效。
7 高压系统参数设置1)进入高压系统参数设置旧底图总号打开电源的同时按下RESET键,控制台将显示如下:1 Enter password (4)3 2按图示依次按下1、2、3、4按键后,控制台将显示如下:* GENERATOR SETUP *UTILITY APR EDITOR:DISABLEDGEN CONFIGURATIONDATA LINKEX IT SETUP按下GEN CONFIGURATION旁边的按键,控制台将显示如下:* GEN CONFIGURATION *TUBE SELECTION AEC SETUPGENERATOR LIMITS AEC CALIBRATIONRECEPETOR SETUP FLUORO SETUPI/O CONFIGURATION TUBE CALIBRATIONEXIT2)设置球管参数在GEN CONFIGUARATION菜单中,选择TUBE SELECTION,控制台将显示如下:* TUBE SELECTION *TUBE 1TUBE 2EXIT选择TUBE 1,控制台将显示如下:*TUBE 1 SELECTION*A192 0.6/1.2 G256 0.6/1.2A256 0.6/1.0 G292 0.6/1.2A292 0.6/1.2 G108 0.3/1.0A272 0.3/0.6 RAD8 1.0/2.0》》底图总号更改标记数量文件号签名日期签名日期编制第页3按“《”和“》”翻页,选择与所使用的球管相对应的X线球管的型号(目前所使用的球管为R/F :A132;R:RAD12若没有此两种型号需用计算机下载),选择完毕后,控制台窗口将显示如下:*TUBE 1 A132 0.6/1.2 12*TUBE SPEED:LOW MAX SF KW HS:MAX LF KW LS: MAX LF KW HS:MAX KV:150》RETURN设置TUBE SPEED为LOW。
继续翻页,显示如下:*TUBE 1 A132 0.6/1.2 12*使用性MAX SF MA:320ANODE HU W ARNING :80%ANODE HU LIMIT: 90%》》继续翻页,显示如下:*TUBE 1 A132 0.6/1.2 12*SF STANDBY: 2.5A FIL BOOST : 200mSLF STANDBY:2.5A FIL PREHEAT:800mSSF MAX:5.4A旧底图总号注:对A132或RAD12的X线球管大、小灯丝ST ANDBY电流改为2.5A,设置完“TUBE SELECTION”,返回“GEN CONFIGUARATION”,选择“GENERATOR LIMITS”,控制台将显示如下:*GENERATOR LIMITS*MAX KW: 50MAX MA: 500MIN MA: 10 +MIN MAS: 630 -EXIT设置完毕后,选择“EXIT”返回主菜单“GEN CONFIGURATION”。
3)接收方式设置选择“RECEPTOR SETUP”,选择R/F接收方式,控制台LCD窗口将显示如下:*RECEPTOR SETUP*[SYM]RECEPTOR SYM:[SYM] MEMORY:DEFFLUORO HANG:2SEC REM TOMO BUT:200MSRAD HANG:0SEC +LAST IMAGE HOLD : 40mS -《》所有设置均如图所示:*RECEPTOR SETUP*[SYM]TUBE :1 AEC CHANNEL: 3TOMO: NO INTERFACE OPTS: 0FLUORO:YES +SERIAL: YES -EXIT 》注:如果为12寸调试,则INTERFACE :1.9寸为缺省值。
*RECEPTOR SETUP*[SYM]SF/LFSWITCH: MAN DEFAULTAEC BACKUP : FIXED使用性AEC BACKUP MAS :500 +AEC BACKUP MA : 3200 -《》注:FLUORO:选择透视功能底图总号更改标记数量文件号签名日期签名日期编制第页4SERIAL:选择连续摄影AEC CHANNEL:选择AEC通道,选择3FLUORO HANG:透视结束后,旋转阳极延长时间,设置为2S。
RAD HANG:摄影结束后,旋转阳极延长时间,设置为0S。
旧底图总号4)透视、曝光参数设置设置完毕接收方式后,返回“GENERATOR SETUP”,下一步,进行透视参数设置,选择“FLUOROSETUP”,控制台将显示如下:*FLUORO SETUP*[SYM]TUBE 1 0%HU MAG : 0DOSE LIMITS II MODES :2ABS SETUP FL-RAD KV XFER: 3MIN FLUORO KV :40 +LAST IMAGE HOLD : 40 -EXIT 》DOSE:0选择"ABS SETUP" ,控制台将显示如下:*ABS SETUP*TUBE 1 0%HU MAG : 0LOOP GAIN :30 AUTOMA/KV CURVE :3NOMINAL DOSE :80 ABS CHANNEL: 5DOSE 1: 60 +DOSE 2: 100 -《》DOSE 剂量百分率设置,一般正常情况下,缺省为DOSE0,通常设置为正常剂量的80%,设置DOSE1为正常剂量的60%,DOSE2为正常剂量的100%,这样方可以满足一些特殊情况下的剂量要求。
AUTO MA/KV CURVE: MA/KV 自动转换曲线选择,一般选择曲线3。
下一页为:*ABS SETUP*TUBE 1 0%HU MAG : 0SIGNAL GAIN :25 +PL GAIN : 20 -》《DOSE :0设置完毕透视参数后,返回“GEN CONFIGURATION”菜单,关闭电源。
8控制台显示测试(Console Rad Tests)并将结果记入调试记录中使用性步骤动作状态1 按下面板上的ON 面板电源开2 按下面板上的OFF 面板电源断开3 按下面板上的ON打开电源面板电源开4 按下从1到6的按钮每一个按钮对应的LED灯亮注意:在6、7、8步骤中的TECH SELECT的按钮在编程模式下禁止6 按TECH SELECT 选择AEC AEC LED灯亮,KV灯亮,mA灯亮,“AEC”mAS或mS值显示基于AEC备份模式选择7 按TECH SELECT 选择mAS mAS灯亮,KV灯亮,mAS灯亮8 按下TECH SELECT 选择mA/mS mA/mS LED灯亮,KV灯亮,mA灯亮,mS灯亮9 按下KV+/-按钮KV值增加(按“+”);KV值减小(按“-”)底图总号更改标记数量文件号签名日期签名日期编制第页5旧底图总号10 按下mA+/-按钮mA值增加(按“+”);mA值减小(按“-”)11 按下mS+/-按钮mS值增加(按“+”);mS值减小(按“-”)12 在选择AEC状态下按DENSITY+/-按钮DENSITY值增加(按“+”);DENSITY值减小(按“-”)13 按FOCUS按钮大小灯丝灯交替点亮14 在选择AEC状态下按FILM SCREEN按钮FILM SCREEN 灯(I、II、III)顺序点亮15 选择AEC状态下按FIELD 按钮LED灯出现[L+C+R],[R]、[C]、[R+C]、[L]、[L+R]、[L+C]组合闪亮16 按下电源OFF键关闭电源9 透视功能测试在测试此项功能时,确定透视功能已经连接1 按下面板上的ON键电源打开2 选择1~6的按钮按钮上的灯亮3 按下DOSE键17 在DOSE键顺序按下时LCD显示屏上的DOSE值改变4 按下MAG键20,按MAG+/-键MAG值改变5 按下ABS键19,进入ABS模式ABS键灯亮,LCD显示屏上,KV和mA上方的AUTO灯亮6 按下ABS键19退出ABS模式,按透视KV+/-键KV值增加(按“+”),KV值减小(按“-”)7 按透视mA+/-键mA值增加(按“+”),mA值减小(按“-”)8 按OFF键电源断开五整机调试步骤1、更换RAM芯片将发生器CPU板上的RAM芯片U25更换为DS1230Y-120,跳过第4步不用进行训管;已经焊在板上的芯片,在调整灯丝板后训管。