产品标识检验状态控制过程
标识和可追溯性控制程序
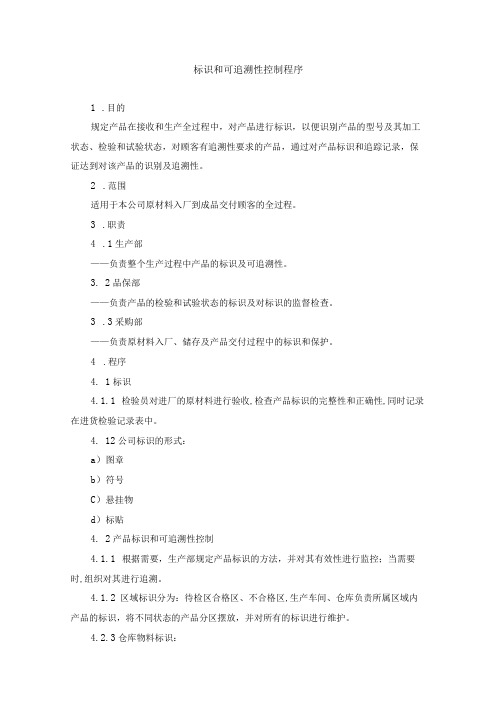
标识和可追溯性控制程序1.目的规定产品在接收和生产全过程中,对产品进行标识,以便识别产品的型号及其加工状态、检验和试验状态,对顾客有追溯性要求的产品,通过对产品标识和追踪记录,保证达到对该产品的识别及追溯性。
2.范围适用于本公司原材料入厂到成品交付顾客的全过程。
3.职责4.1生产部——负责整个生产过程中产品的标识及可追溯性。
3.2品保部——负责产品的检验和试验状态的标识及对标识的监督检查。
3.3采购部——负责原材料入厂、储存及产品交付过程中的标识和保护。
4.程序4.1标识4.1.1检验员对进厂的原材料进行验收,检查产品标识的完整性和正确性,同时记录在进货检验记录表中。
4.12公司标识的形式:a)图章b)符号C)悬挂物d)标贴4.2产品标识和可追溯性控制4.1.1根据需要,生产部规定产品标识的方法,并对其有效性进行监控;当需要时,组织对其进行追溯。
4.1.2区域标识分为:待检区合格区、不合格区,生产车间、仓库负责所属区域内产品的标识,将不同状态的产品分区摆放,并对所有的标识进行维护。
4.2.3仓库物料标识:a)当采购产品包装物上有明显标识,不需作另外标识。
b)当采购产品无标识或标识不清时,仓库管理员应对该采购产品进行标识。
标识可用标牌或卡片表示,标识产品内容应包括产品名称、型号、规格、数量、供方名称、物料批次号等信息。
c)注塑件零件须在零件表面刻印日期章与穴号以便追溯。
4.2.4生产过程产品标识生产过程中的产品标识,可以直接体现在《产品随工单》上反映出来的产品名称和数量。
4.2.5成品标识:最终产品以印有产品名称、型号、规格和批号标牌为标识,顾客有要求时,按照顾客的要求进行标识,如“无铅"、"RoHS"标识等。
4.2.6检验状态标识a)检验状态标识采用明显指示的标牌,表示合格、待检、不合格、报废等状Ob)品保部检验员在检验后应根据检验结果放置相应的检验状态标识,对报废的产品要隔离存放,对不合格的产品应放置在标有“不合格品”字样的区域、车辆与容器中。
IATF16949-2016产品标识和可追溯性控制程序

1.目的为防止生产过程中原辅材料到半成品、成品及不合格品的混用或误用,确保产品符合客户要求,并可追溯产品及过程的品质状况,特制定本程序。
2.适用范围适用于原/辅材料接收、制造过程到出货等所有阶段中不同的标识和可追溯方法。
适用于原/辅材料、外协件、半成品、成品、产品监视和测量及产品可追溯均适用。
3.职责与权限3.1 品质保证部:3.1.1负责原材料批次的检验状态追溯及供应商来料检验报告归档。
3.1.2 出货时出货信息的记录,建立电子表单。
3.1.3 负责生产执行状况的巡查,并要求制造各部对不符合进行改善。
3.1.4 负责所有结批批次的流程单档案的归档,并及时转给企管管理。
3.1.5 负责检查报检物料批次与实际供应商来货批次是否相符。
3.2 供应链管理部:3.2.1入库原辅材料、外协件、半成品、成品及产品的标识,监视和测量状态的控制,并在有可追溯性要求时,协助相关部门。
3.2.2负责原材料存储所属区域内产品的标识,及不同产品状态的区域划分及标识的维护。
3.2.3定期对仓库超期、优先使用、不合格物料的处理,负责组织呆滞物料的处理。
3.2.4仓库按照先进先出原则,报检时负责按照供应商批次进行报检,领料时按批次进行发料。
3.3 制造各部:3.3.1负责生产过程原辅材料、外协件、半成品、成品及产品的标识。
3.3.2负责所属区域内产品监视和测量状态的标识,负责不同产品状态的区域划分及标识的维护。
3.3.3电芯产线负责生产过程批次的区分,各工序辅批号的编制、标识和区分,流程单的填写和归档,以便于查阅,并建立电子档追溯记录,及其它有可追溯性要求的标识管理。
3.3.4 Pack产线负责各工序成品、半成品打码标识,流程单的填写。
3.4计划管理部:负责计划批次的确定、下达及管理。
3.5 相关部门:配合实施本程序。
4.术语和定义4.1 标识:以指定的方式提供用以区别产品状态的标记。
4.2可追溯性:为溯源,根据产品标识,对产品的历史、应用情况和所处场所的判断。
IATF16949产品标识和可追溯性控制程序
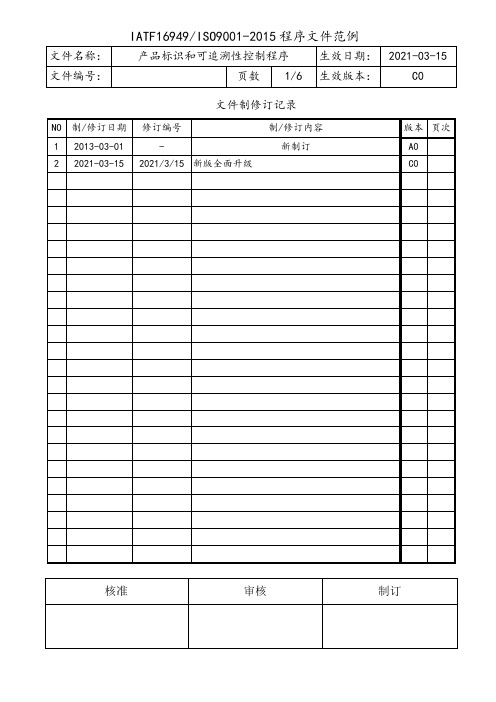
文件制修订记录
1.0目的
在接收、生产、交付和服务的全过程中,对产品进行产品标识和状态标识,以确保能识别产品及产品的状态,防止不同规格产品的混用或误用,防止未经检验或不合格产品流入下道工序,并确保在需要时能够实现追溯。
2.0范围
适用于本公司产品(包括原材料、半成品、成品、外购件等)的标识和可追溯性管理。
3.0职责
3.1 仓库负责仓储产品(包括原材料、半成品、成品、外购件等)的标识和标识的维护工作,防止材料的误领、误用。
3.2 生产部门负责所属区域内产品(包括原材料、半成品、成品、外购件等)的标识及标识的维护工作。
3.3 品保部检验员负责成品检验时的产品标识以及对产品标识的实施情况进行监督检查。
4. 0定义
4.1 产品标识:用于识别产品(包括半成品、成品、外购件等)的型号和供应商等特征的标记。
4.2 状态标识:用于识别产品(包括原材料、半成品、成品、外购件等)的检验或试验状态的标识,分待检、合格、不合格和特采等状态,可以用标签、印章、区域、标牌等方式表示。
4.3 包装标识:用于产品(包括半成品、成品、外购件等)的包装箱(或袋)上,能识别产品的名称、图号、数量、重量、生产日期、保质期和防护要求等
的标识。
包装标识可采用标签和印刷等方式表示。
5.0流程及说明
无
7.0需要保存的记录无。
产品标识和检验状态标识的方法和管理规定

武汉联宇技术有限公司
请示报告
联宇请字[2015]00*号
产品标识和检验状态的方法和管理规定
一.目的
为了规范产品生产过程中各环节的正常有序进行,乱堆乱放现象,技术状态的管理,产品质量能够溯源、追究问责、解决质量纠纷,更好的促进质量管理体系的推行,特制定本制度。
二.适用范围
生产车间、质量管理部、仓库、软件部。
三.具体规定
仓库应对采购回的原材料及生产合格的半成品入库后进行标识(这些标识包括半成品或零部件的名称,数量,划分区域等);在产品出厂发货时,仓库应在产品包装表面对产品进行型号或编号辨别性的标识。
质量管理部在生产的过程中对产品检验和试验状况进行标识,应采用标记法进行。
绿色(合格)、黄色(返工)、红色(不合格),质量管理部应以产品贴标形式对产品状态进行区分及隔离。
生产车间对半成品、成品、待检品、调试测试区等进行区域划分。
车间生产合格的出厂产品由生产部编写产品型号与出厂编号提交质量管理部,质量管理部必须将标有产品型号及出厂编号的合格证贴上,并对产品编号及型号存档记录。
必须具有唯一性,能达到可追溯的目的。
软件部应对软件产品的版本号、功能版本登记。
在产品交付后,软件版本有
更新时,需及时更新并替代原有版本并登记记录,必须具有唯一性,能达到可追溯的目的。
以上部门确保产品实现过程中需要标识的每个环节对产品进行唯一性标识,标识需清晰,必要时进行登记存档,能达到可追溯性,检索的目的。
标识和可追溯性控制程序

1.0目的:明确生产、储存过程中产品标识和检验状态标识要求,防止不同类型产品发生混淆,确保产品识别和可追溯性。
2.0范围:适用于原材料、工序产品、半成品及成品的生产、储序、包装、交付、运输的整个过程的标识及追溯。
3.0定义:3.1 产品标识:指产品身份(识别)标识,即对产品、物料做出供识别性的标记。
3.2 产品检验和试验状态标识:即对经检验后的产品做出状态标识,包括合格、不合格、退货、特采、待处理等常用五种状态。
4.0 职责:4.1 仓库员确保所有材料,成品于入库时均有明确标识,客户有特殊要求时贴上客户要求的出货标签或其它的标识。
4.2生产部负责在制品在生产过程中的标识及成品在包装后/入库前的标识,确保追溯的连贯性。
4.3 品质部负责进料、制程品及成品的检验及试验状态的标识,负责标识要求和方法的制定,必要时制定追溯要求及方法,确认产品实现的全过程的标识的完整性和有效性。
5.0 程序:5.1 标识内容5.1.1 产品品质缺陷标识使用范围:原材料{包括包装材料}、工序产品、半成品及成品。
5.1.2 产品标识的方式包括:区域标识、挂牌标识、标贴标识,特殊记号标识。
5.1.3 检验状态标识的方式包括:区域标识、挂牌标识、标贴标识,印章标识。
5.2 进料标识办法5.2.1 当供应商送料入厂后,以其包装外的品名、规格、数量、订单号、生产日期、Lot No.批号及ROHS等信息。
5.2.2 供应商将本公司采购的物料送至待检区,仓管员依请购单核对送货单和相关资料及实物,分免检和必检物料按《监视和测量设备控制程序》作业。
5.2.3 品质部IQC 负责检验,若检验为合格,则于原材料的明显处贴上“进料合格标签”。
合格标签上记录物料名称,型号规格,供应厂商,生产日期,有效日期,数量,有效期,检查员,检查日期。
合格标签与特采标签上有月份标志(月份颜色相同)合格标签为绿色,特采标签为黄色。
5.2.4检验合格,仓管员将采购物资移至相应合格品区域,并依据有关仓库管理制度安排入库。
产品标识控制程序

1. 目的:对生产和服务过程进行有效控制,采用规定的方法对产品进行标识,防止在实现过程中产品及其质量状态的混淆,造成误用,以确保满足顾客的需求和期望。
2. 范围:适用于产品的生产、贮存、安装和服务的全过程中应保持产品状态的标识包括原辅材料、中间产品、成品的标识以及因各种原因退回公司的产品。
3. 职责3.1 质量部负责产品检验状态标识的实施和管理,负责对各部门标识的使用情况是否符合规定要求进行监督。
3.2 生产采购部负责所属区域内产品的标识的使用及标识的维护管理。
3.3 综合办公室负责仓储区标识的实施和管理。
4.内容4.1 产品的标识方式有4.1.1 检验状态标识:合格、不合格、待检。
在仓库以标牌和合格区、不合格区、待验区、退换货区作为标识。
4.1.2生产状态标识:贴(挂)在产品上的标识卡、标签、合格证。
4.1.3使用状态标识:货位卡。
4.1.4 唯一性标识:根据公司情况,编制《生产批号管理制度》,规定原辅材料、中间产品、成品的批号标识方法,保证标识的唯一性以便实现追溯。
4.2 外购产品(原材料)的标识方法及控制4.2.1 外购产品入库后的标识采用待检区、合格区、不合格区。
4.2.2外购产品在进厂后放入原材料仓库黄色“待检区”,以“原辅料货位卡”注明该产品物料名称、批号、数量、规格、供货单位等信息后悬挂黄色“待检”标识牌。
4.2.3 质量部检验员对外购产品进行检验,并对抽取的样品进行标识,合格后出具“检验报告”后方可入库(每批产品都应有检验记录),放入仓库的“合格区”。
4.2.4 入库后及时完善“原辅料货位卡”,各作业部门(生产车间、仓库)对作业区域内的物品进行标识,并做好领用/使用记录。
4.2.5 检验和使用中发现的不合格物料,应做“不合格”标识,明确不合格品名称、批号、数量等,放入“不合格区”。
4.3 中间产品的标识方法及控制4.3.1 生产过程中的产品批号按《生产批号管理制度》执行。
a)生产过程中连续工序转换的流水线作业方式,操作人员采用过程操作记录上进行标识,直到该批产品包装过程结束而终止。
GJB9001C标识和可追溯性控制程序

文件制修订记录1.0 目的标识分为产品标识、产品的检验和试验状态标识。
本程序规定了通过对生产和服务提供全过程中产品和产品状态的标识,达到防止混淆和误用以及在需要时可追溯的目的。
2.0 范围适用于军品标识、产品的检验和试验状态标识和可追溯性控制。
3.0 职责3.1 XXX部是标识和可追溯性的主管部门,负责标识的制作、发放、实施和监督。
3.2 车间负责产品生产过程中可追溯性标识的实施,保持标识的完整清晰。
3.3 XXX部库房管理人员负责入库原材料按区域堆放,检验人员负责原材料检验和试验状态标识。
3.4 保管或使用原材料的各单位应指定专人负责进行原材料分装后质量状态标识的移植,做好标识的移植记录。
4.0 工作程序4.1 过程识别本程序包括三个方面的内容,即产品标识、产品检验和试验状态标识、产品可追溯性标识。
标识和可追溯性过程的输入是对标识和可追溯性的要求,输出是标识的结果。
本程序包括的活动有:标识的内容、形式、方法的确定,标识的制作,标识的控制与管理。
4.2 过程流程图标识和可追溯性控制过程流程图见图1。
省略4.3 过程控制的内容4.3.1 产品标识4.3.1.1 产品标识的内容产品标识的内容一般包括:1.产品名称或代号;2.型号、规格;3.检验和试验状态;4.生产批号、编号;5.质量状况;6.生产单位;7.生产者;8.检验者;9.生产日期、贮存期限;10.检验日期、周检期。
根据产品所处的不同阶段或特点,具体标识允许含有上述的部分内容,但一般要求是应能通过该标识和相应记录追溯到其它内容。
4.3.1.2 产品标识的形式根据产品的特点和需要,可选用下列形式标识的一种或几种组合:a) 标签标识对化工原材料产品、药剂产品等可将标识制作在标签上,再将标签粘贴在产品的包装物上,或将标签与产品放在一起。
b) 印记标识有特殊要求的产品可以用各种印记(如激光打标、钢印等)在被标记表面或包装物上做标识。
c) 涂漆标识对于板材、线材等,用涂漆的方法在被标记表面做标识。
产品标识和可追溯性控制程序
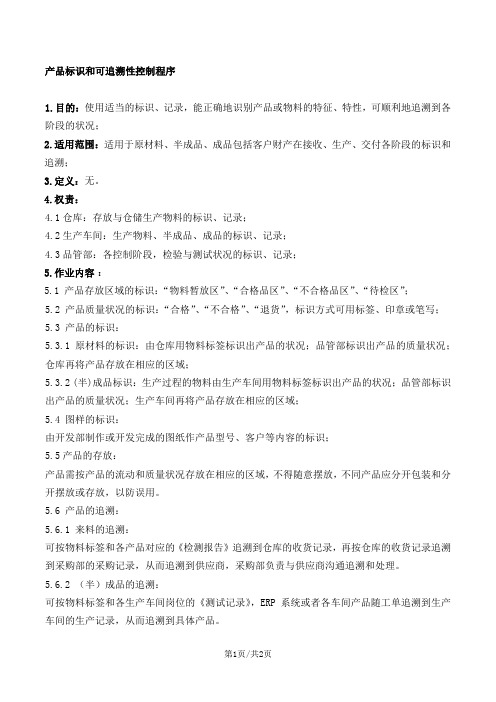
产品标识和可追溯性控制程序1.目的:使用适当的标识、记录,能正确地识别产品或物料的特征、特性,可顺利地追溯到各阶段的状况;2.适用范围:适用于原材料、半成品、成品包括客户财产在接收、生产、交付各阶段的标识和追溯;3.定义:无。
4.权责:4.1仓库:存放与仓储生产物料的标识、记录;4.2生产车间:生产物料、半成品、成品的标识、记录;4.3品管部:各控制阶段,检验与测试状况的标识、记录;5.作业内容﹕5.1 产品存放区域的标识:“物料暂放区”、“合格品区”、“不合格品区”、“待检区”;5.2 产品质量状况的标识:“合格”、“不合格”、“退货”,标识方式可用标签、印章或笔写;5.3 产品的标识:5.3.1 原材料的标识:由仓库用物料标签标识出产品的状况;品管部标识出产品的质量状况;仓库再将产品存放在相应的区域;5.3.2 (半)成品标识:生产过程的物料由生产车间用物料标签标识出产品的状况;品管部标识出产品的质量状况;生产车间再将产品存放在相应的区域;5.4 图样的标识:由开发部制作或开发完成的图纸作产品型号、客户等内容的标识;5.5产品的存放:产品需按产品的流动和质量状况存放在相应的区域,不得随意摆放,不同产品应分开包装和分开摆放或存放,以防误用。
5.6 产品的追溯:5.6.1 来料的追溯:可按物料标签和各产品对应的《检测报告》追溯到仓库的收货记录,再按仓库的收货记录追溯到采购部的采购记录,从而追溯到供应商,采购部负责与供应商沟通追溯和处理。
5.6.2 (半)成品的追溯:可按物料标签和各生产车间岗位的《测试记录》,ERP系统或者各车间产品随工单追溯到生产车间的生产记录,从而追溯到具体产品。
5.6.3 客户退货或投诉追溯:当有客户退货或投诉时由客户提供产品的收货记录,从而追溯到本厂的送货记录,再可追溯到各岗位的生产和检验记录,从而追溯到具体产品。
5.6.4 产品的可追溯性,由品管部负责追溯,相关部门协助追溯。
产品标识和可追溯控制程序
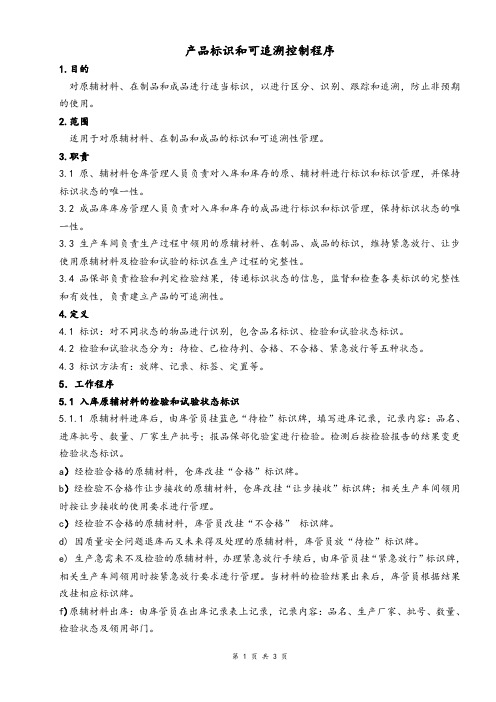
产品标识和可追溯控制程序1.目的对原辅材料、在制品和成品进行适当标识,以进行区分、识别、跟踪和追溯,防止非预期的使用。
2.范围适用于对原辅材料、在制品和成品的标识和可追溯性管理。
3.职责3.1 原、辅材料仓库管理人员负责对入库和库存的原、辅材料进行标识和标识管理,并保持标识状态的唯一性。
3.2 成品库库房管理人员负责对入库和库存的成品进行标识和标识管理,保持标识状态的唯一性。
3.3 生产车间负责生产过程中领用的原辅材料、在制品、成品的标识,维持紧急放行、让步使用原辅材料及检验和试验的标识在生产过程的完整性。
3.4 品保部负责检验和判定检验结果,传递标识状态的信息,监督和检查各类标识的完整性和有效性,负责建立产品的可追溯性。
4.定义4.1 标识:对不同状态的物品进行识别,包含品名标识、检验和试验状态标识。
4.2 检验和试验状态分为:待检、已检待判、合格、不合格、紧急放行等五种状态。
4.3 标识方法有:放牌、记录、标签、定置等。
5.工作程序5.1 入库原辅材料的检验和试验状态标识5.1.1 原辅材料进库后,由库管员挂蓝色“待检”标识牌,填写进库记录,记录内容:品名、进库批号、数量、厂家生产批号;报品保部化验室进行检验。
检测后按检验报告的结果变更检验状态标识。
a)经检验合格的原辅材料,仓库改挂“合格”标识牌。
b)经检验不合格作让步接收的原辅材料,仓库改挂“让步接收”标识牌;相关生产车间领用时按让步接收的使用要求进行管理。
c)经检验不合格的原辅材料,库管员改挂“不合格”标识牌。
d) 因质量安全问题退库而又未来得及处理的原辅材料,库管员放“待检”标识牌。
e) 生产急需来不及检验的原辅材料,办理紧急放行手续后,由库管员挂“紧急放行”标识牌,相关生产车间领用时按紧急放行要求进行管理。
当材料的检验结果出来后,库管员根据结果改挂相应标识牌。
f)原辅材料出库:由库管员在出库记录表上记录,记录内容:品名、生产厂家、批号、数量、检验状态及领用部门。
检验和试验状态控制程序
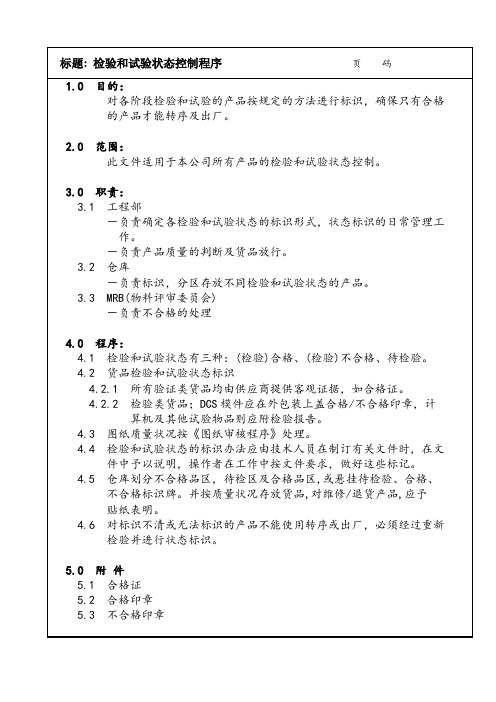
1.0目的:
对各阶段检验和试验的产品按规定的方法进行标识,确保只有合格
的产品才能转序及出厂。
2.0范围:
此文件适用于本公司所有产品的检验和试验状态控制。
3.0职责:
3.1工程部
-负责确定各检验和试验状态的标识形式,状态标识的日常管理工
作。
-负责产品质量的判断及货品放行。
算机及其他试验物品则应附检验报告。
4.3图纸质量状况按《图纸审核程序》处理。
4.4检验和试验状态的标识办法应由技术人员在制订有关文件时,在文
件中予以说明,操作者在工作中按文件要求,做好这些标记。
4.5仓库划分不合格品区,待检区及合格品区,或悬挂待检验、合格、
不合格标识牌。并按质量状况存放货品,对维修/退货产品,应予
贴纸表明。
4.6对标识不清或无法标识的产品不能使用转序或出厂,必须经过重新
检验并进行状态标识。
5.0附件
5.1合格证
5.2合格印章
5.3不合格印章
3.2仓库
-负责标识,分区存放不同检验和试验状态的产品。
3.3 MRB(物料评审委员会)
-负责不合格的处理
4.0程序:
4.1检验和试验状态有三种:(检验)合格、(检验)不合格、待检验。
4.2货品检验和试验状态标识
4.2.1所有验证类货品均由供应商提供客观证据,如合格证。
4.2.2检验类货品;DCS模件应在外包装上盖合格/不合格印章,计
标识和可追溯性控制程序
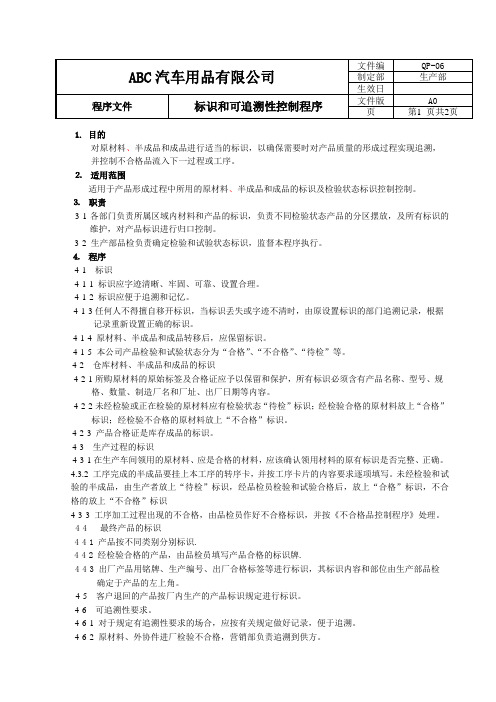
1. 目的对原材料、半成品和成品进行适当的标识,以确保需要时对产品质量的形成过程实现追溯,并控制不合格品流入下一过程或工序。
⒉适用范围适用于产品形成过程中所用的原材料、半成品和成品的标识及检验状态标识控制控制。
⒊职责3·1各部门负责所属区域内材料和产品的标识,负责不同检验状态产品的分区摆放,及所有标识的维护,对产品标识进行归口控制。
3·2生产部品检负责确定检验和试验状态标识,监督本程序执行。
⒋程序4·1标识4·1·1标识应字迹清晰、牢固、可靠、设置合理。
4·1·2标识应便于追溯和记忆。
4·1·3任何人不得擅自移开标识,当标识丢失或字迹不清时,由原设置标识的部门追溯记录,根据记录重新设置正确的标识。
4·1·4 原材料、半成品和成品转移后,应保留标识。
4·1·5本公司产品检验和试验状态分为“合格”、“不合格”、“待检”等。
4·2仓库材料、半成品和成品的标识4·2·1所购原材料的原始标签及合格证应予以保留和保护,所有标识必须含有产品名称、型号、规格、数量、制造厂名和厂址、出厂日期等内容。
4·2·2未经检验或正在检验的原材料应有检验状态“待检”标识;经检验合格的原材料放上“合格”标识;经检验不合格的原材料放上“不合格”标识。
4·2·3产品合格证是库存成品的标识。
4·3生产过程的标识4·3·1在生产车间领用的原材料、应是合格的材料,应该确认领用材料的原有标识是否完整、正确。
4.3.2 工序完成的半成品要挂上本工序的转序卡,并按工序卡片的内容要求逐项填写。
未经检验和试验的半成品,由生产者放上“待检”标识,经品检员检验和试验合格后,放上“合格”标识,不合格的放上“不合格”标识4·3·3 工序加工过程出现的不合格,由品检员作好不合格标识,并按《不合格品控制程序》处理。
产品检验和试验状态标识控制程序
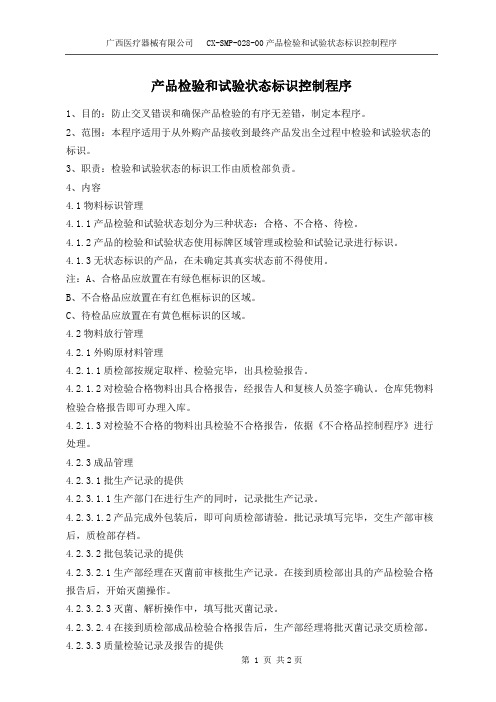
产品检验和试验状态标识控制程序1、目的:防止交叉错误和确保产品检验的有序无差错,制定本程序。
2、范围:本程序适用于从外购产品接收到最终产品发出全过程中检验和试验状态的标识。
3、职责:检验和试验状态的标识工作由质检部负责。
4、内容4.1物料标识管理4.1.1产品检验和试验状态划分为三种状态:合格、不合格、待检。
4.1.2产品的检验和试验状态使用标牌区域管理或检验和试验记录进行标识。
4.1.3无状态标识的产品,在未确定其真实状态前不得使用。
注:A、合格品应放置在有绿色框标识的区域。
B、不合格品应放置在有红色框标识的区域。
C、待检品应放置在有黄色框标识的区域。
4.2物料放行管理4.2.1外购原材料管理4.2.1.1质检部按规定取样、检验完毕,出具检验报告。
4.2.1.2对检验合格物料出具合格报告,经报告人和复核人员签字确认。
仓库凭物料检验合格报告即可办理入库。
4.2.1.3对检验不合格的物料出具检验不合格报告,依据《不合格品控制程序》进行处理。
4.2.3成品管理4.2.3.1批生产记录的提供4.2.3.1.1生产部门在进行生产的同时,记录批生产记录。
4.2.3.1.2产品完成外包装后,即可向质检部请验。
批记录填写完毕,交生产部审核后,质检部存档。
4.2.3.2批包装记录的提供4.2.3.2.1生产部经理在灭菌前审核批生产记录。
在接到质检部出具的产品检验合格报告后,开始灭菌操作。
4.2.3.2.3灭菌、解析操作中,填写批灭菌记录。
4.2.3.2.4在接到质检部成品检验合格报告后,生产部经理将批灭菌记录交质检部。
4.2.3.3质量检验记录及报告的提供4.2.3.3.1成品出来后,填写请验单向质检部请验。
4.2.3.3.2质量人员在接到请验单后,据请验单上内容准备取样。
4.2.3.3.3质量人员取样后按检验周期及检验方法进行检验,以企业内控质量标准为依据进行检验并出具检验报告。
4.2.3.4检验合格报告交质检部经理审核签章后,将一份检验报告及批检验记录交质检部,其余报告交生产部。
产品标识控制程序

产品标识控制程序1目的通过对原料、辅料、包装材料、物资、产品等做出标识,达到识别产品,掌握产品控制状态,确保产品质量、工作责任的可追溯性。
2范围适用于原料、辅料、包装材料、物资、半成品、成品标识和追溯。
3职责3.1仓库负责入库原料辅料、包装材料、物资的标识。
3.2生产车间负责生产过程中半成品、成品以及生产区域暂存的原辅料、包装材料、物资的标识。
3.3品质管理人员负责原料、辅料、包装材料、半成品、成品等不合格品的标识和监督管理。
4程序要求4.1 标识4.1.1标识的分类对生产过程中原辅料、包装物、物资、半成品、成品等进行适当标识,标识分为产品标识和监视与测量状态标识。
a. 产品标识包括:标签、标识牌、标识单、合格证、装箱单、编号等,产品标识在有追溯性要求时,应是唯一性的,以便于追溯。
b. 监视和测量状态标识包括:商检报告、出厂检验、试验、检测资料以及产品生产过程中监视和测量状态的标识。
c. 监视和测量状态标识分为待检、合格、不合格三类。
4.1.2标识的方法和要求4.1.2.1产品标识的方法可以是贴标签、打印喷码、压标识单、挂标牌和生产过程的质量卡等。
标识应位置醒目、字迹清楚、易识别,并保持外观整洁。
4.1.2.2监视和测量状态标识时,应对产品进行划区域标识,对于合格、不合格和待检验等产品分区域存放,明确标识。
4.1.2.3 当无法进行区域标识时,可采用记录方式进行标识。
4.2产品标识4.2.1采购原辅料标识4.2.1.1仓库库管员对入库原料分类、分批保管,以标牌或标识单等形式标明入库原料的品名、规格、数量、生产厂家、入库日期、检验状态等,确保库存原料标识正确、清晰、可追溯。
4.2.1.2仓库库管员对入库辅料、包装材料、物资进行分类、分批保管,以标牌或标识单等形式标明入库辅料、包装材料、物资的品名、规格、数量、生产厂家(或产地)、入库时间、保质期限、检验状态等,确保标识规范。
4.2.2产品实现过程标识4.2.2.1生产车间负责生产过程中原料、辅料、包装材料、物资、半成品、成品的标识及维护。
产品标识和可追溯性控制程序
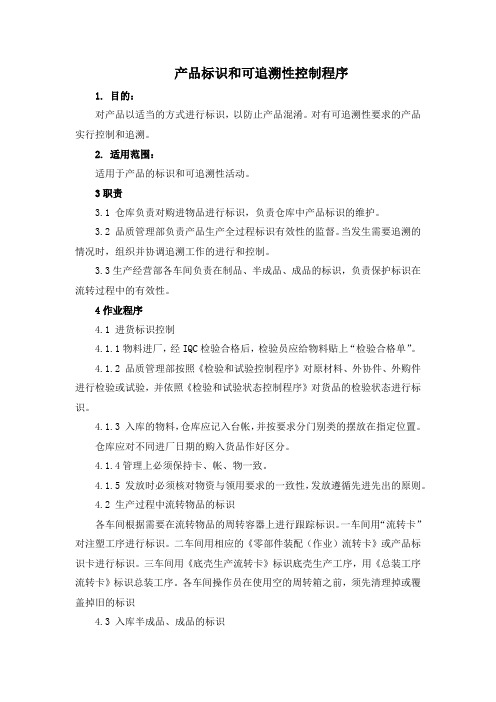
产品标识和可追溯性控制程序
1.目的:
对产品以适当的方式进行标识,以防止产品混淆。
对有可追溯性要求的产品实行控制和追溯。
2.适用范围:
适用于产品的标识和可追溯性活动。
3职责
3.1 仓库负责对购进物品进行标识,负责仓库中产品标识的维护。
3.2 品质管理部负责产品生产全过程标识有效性的监督。
当发生需要追溯的情况时,组织并协调追溯工作的进行和控制。
3.3生产经营部各车间负责在制品、半成品、成品的标识,负责保护标识在流转过程中的有效性。
4作业程序
4.1 进货标识控制
4.1.1物料进厂,经IQC检验合格后,检验员应给物料贴上“检验合格单”。
4.1.2 品质管理部按照《检验和试验控制程序》对原材料、外协件、外购件进行检验或试验,并依照《检验和试验状态控制程序》对货品的检验状态进行标识。
4.1.3 入库的物料,仓库应记入台帐,并按要求分门别类的摆放在指定位置。
仓库应对不同进厂日期的购入货品作好区分。
4.1.4管理上必须保持卡、帐、物一致。
4.1.5 发放时必须核对物资与领用要求的一致性,发放遵循先进先出的原则。
4.2 生产过程中流转物品的标识
各车间根据需要在流转物品的周转容器上进行跟踪标识。
一车间用“流转卡”对注塑工序进行标识。
二车间用相应的《零部件装配(作业)流转卡》或产品标识卡进行标识。
三车间用《底壳生产流转卡》标识底壳生产工序,用《总装工序流转卡》标识总装工序。
各车间操作员在使用空的周转箱之前,须先清理掉或覆盖掉旧的标识
4.3 入库半成品、成品的标识。
产品检验状态标识管理制度
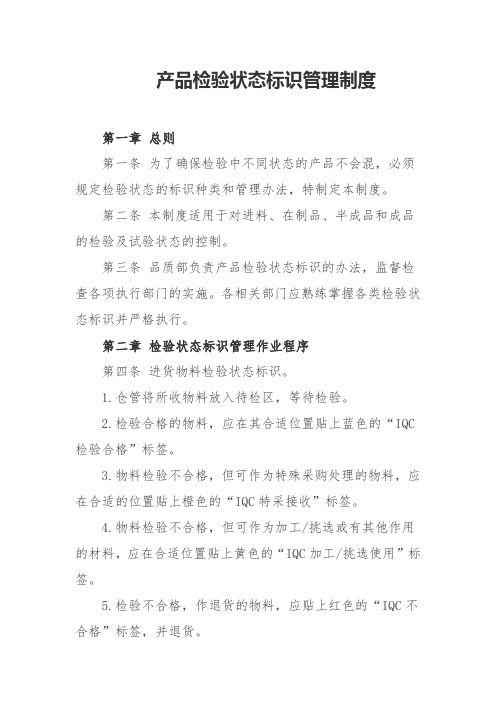
产品检验状态标识管理制度第一章总则第一条为了确保检验中不同状态的产品不会混,必须规定检验状态的标识种类和管理办法,特制定本制度。
第二条本制度适用于对进料、在制品、半成品和成品的检验及试验状态的控制。
第三条品质部负责产品检验状态标识的办法,监督检查各项执行部门的实施。
各相关部门应熟练掌握各类检验状态标识并严格执行。
第二章检验状态标识管理作业程序第四条进货物料检验状态标识。
1.仓管将所收物料放入待检区,等待检验。
2.检验合格的物料,应在其合适位置贴上蓝色的“IQC 检验合格”标签。
3.物料检验不合格,但可作为特殊采购处理的物料,应在合适的位置贴上橙色的“IQC特采接收”标签。
4.物料检验不合格,但可作为加工/挑选或有其他作用的材料,应在合适位置贴上黄色的“IQC加工/挑选使用”标签。
5.检验不合格,作退货的物料,应贴上红色的“IQC不合格”标签,并退货。
第五条单个不合格品标识:生产过程中检查或自检发现单个不合格品时,在其相应部位贴上红色箭头纸或者放在有“不合格品”红色标签区域内。
第六条五金、塑胶车间QC巡检状态标识。
1.做好的产品应该放在待检区域或生产机器旁待检。
2.巡检员巡检合格后,在半成品或成品批次标识卡上盖蓝色的“QC巡检合格”章,或者放在“合格”产品区域内。
3.虽然不合格,但可以接受的产品批次,可以在产品上贴橙色的“QC巡检让步接收”标签。
4.不合格产品,如需返工处理,应贴上黄色的“QC巡检返工”标签。
5.如只能作为报废处理的产品,应该贴上“QC巡检报废”标签。
第七条五金、塑胶车间QA半成品入仓检验状态标识。
1.未被检验的产品,放在待检区域内,贴上“QA正在检查中”标牌。
2.入仓检验合格,在半成品标识卡上盖蓝色的“QA检查合格”章。
3.检验不合格但可以接受的,贴上橙色“QA让步接收”标签。
4.不合格需返工的半成品,贴上黄色的“QA放工”标签。
5.不合格须作为报废处理的,贴上红色“QA报废”标签。