全面生产维护课件
合集下载
TPM全面生产维护01

为日本工业的—种生存方式,这种新的制造概念最终被命名为全面质量管理 (TQM)。
当工厂维护的问题作为TQM程序部分被检查出来,一些通用概念看起来在维护环 境中就不太适合或不能发挥作用。原始的TQM概念做了一些修正。这些调整将维 护提升至全面质量管理程序的一个重要部分。
TPM是一个以制造业领先的创新,强调人的重要性。一个“能做”和“持续改进”
1960年前后
4
维修预防
(MP: Maintenance Prevention)
设计不发生故障的设备,设备FMEA
1960年前后
TPM全面生产维护01 设备部
TPM与TQM的关系
TPM是TQM演变而来的. TQM是W.Edwards Deming博士在影响日本工业的直接效果下发展得来.
Deming博士是在二战结束不久后在日本开始工作的,作为一个统计学家,他首次 向日本人展示了如何在制造过程中使用统计分析和如何在制造过程中使用效果数 据来控制质量。由日本工作理论建立的早期统计程序和效果质量控制概念很快成
----选择改进维修作业的对象 ----估计零件的寿命 ----选择点检点,确定和修改点检标准 ----备件标准的确定
TPM全面生产维护01 设备部
TPM流程图
TPM全面生产维护01 设备部
TPM的前提----推行5S活动
5S是现场管理的基础,是TPM(全面生产维护管理)的前提,是TQM(全面质量 管理)的第一步,也是ISO9000、ISO16949有效推行的保证。
5S能够营造一种“人人积极参与,事事遵守标准”的良好氛围。有了这种氛围, 推行ISO、TQM、及TPM就更容易获得员工的支持和配合,有利于调动员工的积 极性,形成强大的推动力。
平均故障间隔期(MTBF-Mean Time Between Failures) 指在规定时间内,设备无故障工作时间的平均值,它是衡量设备可靠性的尺度。
当工厂维护的问题作为TQM程序部分被检查出来,一些通用概念看起来在维护环 境中就不太适合或不能发挥作用。原始的TQM概念做了一些修正。这些调整将维 护提升至全面质量管理程序的一个重要部分。
TPM是一个以制造业领先的创新,强调人的重要性。一个“能做”和“持续改进”
1960年前后
4
维修预防
(MP: Maintenance Prevention)
设计不发生故障的设备,设备FMEA
1960年前后
TPM全面生产维护01 设备部
TPM与TQM的关系
TPM是TQM演变而来的. TQM是W.Edwards Deming博士在影响日本工业的直接效果下发展得来.
Deming博士是在二战结束不久后在日本开始工作的,作为一个统计学家,他首次 向日本人展示了如何在制造过程中使用统计分析和如何在制造过程中使用效果数 据来控制质量。由日本工作理论建立的早期统计程序和效果质量控制概念很快成
----选择改进维修作业的对象 ----估计零件的寿命 ----选择点检点,确定和修改点检标准 ----备件标准的确定
TPM全面生产维护01 设备部
TPM流程图
TPM全面生产维护01 设备部
TPM的前提----推行5S活动
5S是现场管理的基础,是TPM(全面生产维护管理)的前提,是TQM(全面质量 管理)的第一步,也是ISO9000、ISO16949有效推行的保证。
5S能够营造一种“人人积极参与,事事遵守标准”的良好氛围。有了这种氛围, 推行ISO、TQM、及TPM就更容易获得员工的支持和配合,有利于调动员工的积 极性,形成强大的推动力。
平均故障间隔期(MTBF-Mean Time Between Failures) 指在规定时间内,设备无故障工作时间的平均值,它是衡量设备可靠性的尺度。
TPM介绍课件(经典)pptx

对复制推广计划的执行情况进行评估 和反馈,不断完善和优化推广策略。
THANKS
感谢您的观看
关键设备识别和风险评估
关键设备识别
通过对设备的功能、性能、 可靠性等方面进行评估, 识别出对生产影响最大的 关键设备。
风险评估
对关键设备进行风险评估, 识别潜在的故障模式和影 响,以及可能的风险因素。
制定风险应对措施
根据风险评估结果,制定 相应的风险应对措施,如 加强监控、提高维修频率 等。
预防性维修策略制定和执行
预防性维修策略制定
01
根据设备的特性和故障模式,制定相应的预防性维修策略,如
定期更换易损件、清洗散热系统等。
维修计划制定
02
根据预防性维修策略,制定具体的维修计划,包括维修项目、
时间、人员等安排。
维修执行和记录
03
按照维修计划进行维修工作,并详细记录维修过程和结果,以
便后续分析和改进。
05
教育培训与技能提 升途径
TPM介绍课件(经 典)pptx
目录
CONTENTS
• TPM概述与基本原理 • 设备管理与维护策略 • 自主保全活动推进方法 • 计划保全活动实施过程 • 教育培训与技能提升途径 • 监督检查与持续改进机制构建
01
TPM概述与基本 原理
TPM定义及发展历程
定义
TPM(Total Productive Maintenance,全面生产维护)是一 种以提高设备综合效率为目标,以全系统的预防维修为过程, 全体人员参与为基础的设备保养和维修管理体系。
降低运营成本
通过预防性维护和减少维修费用, 降低运营成本。
设备管理重要性及挑战
• 增强企业竞争力:确保设备稳定运行,提高产品质量和客 户满意度,从而增强企业竞争力。
THANKS
感谢您的观看
关键设备识别和风险评估
关键设备识别
通过对设备的功能、性能、 可靠性等方面进行评估, 识别出对生产影响最大的 关键设备。
风险评估
对关键设备进行风险评估, 识别潜在的故障模式和影 响,以及可能的风险因素。
制定风险应对措施
根据风险评估结果,制定 相应的风险应对措施,如 加强监控、提高维修频率 等。
预防性维修策略制定和执行
预防性维修策略制定
01
根据设备的特性和故障模式,制定相应的预防性维修策略,如
定期更换易损件、清洗散热系统等。
维修计划制定
02
根据预防性维修策略,制定具体的维修计划,包括维修项目、
时间、人员等安排。
维修执行和记录
03
按照维修计划进行维修工作,并详细记录维修过程和结果,以
便后续分析和改进。
05
教育培训与技能提 升途径
TPM介绍课件(经 典)pptx
目录
CONTENTS
• TPM概述与基本原理 • 设备管理与维护策略 • 自主保全活动推进方法 • 计划保全活动实施过程 • 教育培训与技能提升途径 • 监督检查与持续改进机制构建
01
TPM概述与基本 原理
TPM定义及发展历程
定义
TPM(Total Productive Maintenance,全面生产维护)是一 种以提高设备综合效率为目标,以全系统的预防维修为过程, 全体人员参与为基础的设备保养和维修管理体系。
降低运营成本
通过预防性维护和减少维修费用, 降低运营成本。
设备管理重要性及挑战
• 增强企业竞争力:确保设备稳定运行,提高产品质量和客 户满意度,从而增强企业竞争力。
《TPM与PM分析》课件
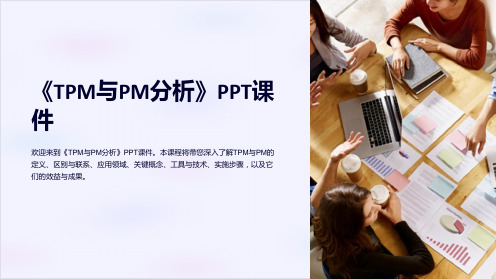
表 和资源需求。
员工培训
提供员工培训,使其掌握设备维护的 基本知识和技能。
TPM与PM的效益与成果
提高设备可靠性
TPM和PM的实施可以降低设 备故障率,提高生产线的稳 定性和可靠性。
增加生产效率
通过预防性维护和计划性维 护,TPM和PM可以减少设备 停机时间,提高生产效率。
TPM与PM的区别与联系
1 区别
TPM是一种全面性的生产维护方法,而PM是一种预防性的维护方法。
2 联系
两者都致力于提高设备的可靠性、降低故障率,以及提高生产效率。
TPM与PM的应用领域
制造业
TPM和PM广泛应用于制造业,包括汽车、电子、机械等行业。
能源
TPM和PM在能源领域,如电力、石油和天然气等行业也有广泛应用。
TPM与PM的工具与技术
保养检查单
记录设备保养工作的详细步骤 和频率。
设备停机分析
根本原因分析
分析设备停机原因和持续时间, 以改进生产效率。
追溯设备故障的根本原因,以 预防类似问题的再次发生。
TPM与PM的实施步骤
1
设备评估
2
评估设备状态和维护需求,制定相应
保养计划。
3
实施和监控
4
按计划执行设备维护工作,并监控维 护效果。
交通运输
TPM和PM在交通运输领域,如航空、铁路和航运等行业也发挥重要作用。
TPM与PM的关键概念
1 计划性维护
TPM和PM强调对设备的计划性维护,以预防故障和提高设备可用性。
2 设备保养
TPM和PM注重设备保养,包括清洁、润滑和更换磨损部件等。
3 员工参与
TPM和PM倡导员工积极参与设备维护,并提供培训和支持。
员工培训
提供员工培训,使其掌握设备维护的 基本知识和技能。
TPM与PM的效益与成果
提高设备可靠性
TPM和PM的实施可以降低设 备故障率,提高生产线的稳 定性和可靠性。
增加生产效率
通过预防性维护和计划性维 护,TPM和PM可以减少设备 停机时间,提高生产效率。
TPM与PM的区别与联系
1 区别
TPM是一种全面性的生产维护方法,而PM是一种预防性的维护方法。
2 联系
两者都致力于提高设备的可靠性、降低故障率,以及提高生产效率。
TPM与PM的应用领域
制造业
TPM和PM广泛应用于制造业,包括汽车、电子、机械等行业。
能源
TPM和PM在能源领域,如电力、石油和天然气等行业也有广泛应用。
TPM与PM的工具与技术
保养检查单
记录设备保养工作的详细步骤 和频率。
设备停机分析
根本原因分析
分析设备停机原因和持续时间, 以改进生产效率。
追溯设备故障的根本原因,以 预防类似问题的再次发生。
TPM与PM的实施步骤
1
设备评估
2
评估设备状态和维护需求,制定相应
保养计划。
3
实施和监控
4
按计划执行设备维护工作,并监控维 护效果。
交通运输
TPM和PM在交通运输领域,如航空、铁路和航运等行业也发挥重要作用。
TPM与PM的关键概念
1 计划性维护
TPM和PM强调对设备的计划性维护,以预防故障和提高设备可用性。
2 设备保养
TPM和PM注重设备保养,包括清洁、润滑和更换磨损部件等。
3 员工参与
TPM和PM倡导员工积极参与设备维护,并提供培训和支持。
全面生产维护(TPM)讲义

❖ 1)设备购置时选型有误。过多地考虑技术储备,盲 目追求加工中心的兼容性,结果是在用精密机床加工 非精密、低附加值和低效率的零件,导致部分功能闲 置。
❖ 2)相关的工艺装备不配套。在刀具、夹具、量具、 软件、维修和环境等方面的投资不足,造成机床使用 的寿命和效率的低下。
❖ 3)工艺编排不合理。没有根据精益生产的“一个流” 去编排产品加工的工艺过程,只是根据设备的种类编 组,在某一工步或工序节省了部分时间,而没有从根 本上提高效率。
投资或员工的加班加点也就是资源的投入实现的。但是这种资源投入型
的生产方式由于固定成本的增加并不能有效提高企业生产经营的效益,
同时这种粗放型的生产方式也不利于资源的节约和环境保护。
❖ 现代设备管理的理念是通过加强设备管理,提高设备的综合效率以 实现生产能力的提高。因为生产设备综合效率的提高可以减少各种形式 的设备非计划停机时间,从而实现提高设备生产能力的目标。
❖ 为了解决这些问题,美国等制造业提出了“事后维 修(Breakdown Maintenance ,BM)”,即当装 备出现故障后马上采取应急措施进行事后处置。
❖ 这一时期,设备最显著的特点是半自动、手动操作 设备多,结构也简单,因此工人可以自己动手修理, 现象是不坏不修、坏了再修。
❖ BM从上世纪初一直持续到40 年代。
❖ (2)预防维修
❖ 上世纪50年以后,开始出现复杂设备,复杂设备由大 量零件组成,修理所占用的时间已成为影响生产的一 个重要因素。
❖ 另外,人们发现设备故障总在某个部位出现,因此在 维护时主要去查找薄弱部位并对其进行改良。
❖ 为了尽量减少设备修理对生产的影响,苏联提出计划 维修制度;美国提出预防维修制度,即PM (Preventive Maintenance / 1951 ) ,即通过对设 备的“物理性检查”预防其故障的发生,从而达到延 长设备使用寿命的目的。
❖ 2)相关的工艺装备不配套。在刀具、夹具、量具、 软件、维修和环境等方面的投资不足,造成机床使用 的寿命和效率的低下。
❖ 3)工艺编排不合理。没有根据精益生产的“一个流” 去编排产品加工的工艺过程,只是根据设备的种类编 组,在某一工步或工序节省了部分时间,而没有从根 本上提高效率。
投资或员工的加班加点也就是资源的投入实现的。但是这种资源投入型
的生产方式由于固定成本的增加并不能有效提高企业生产经营的效益,
同时这种粗放型的生产方式也不利于资源的节约和环境保护。
❖ 现代设备管理的理念是通过加强设备管理,提高设备的综合效率以 实现生产能力的提高。因为生产设备综合效率的提高可以减少各种形式 的设备非计划停机时间,从而实现提高设备生产能力的目标。
❖ 为了解决这些问题,美国等制造业提出了“事后维 修(Breakdown Maintenance ,BM)”,即当装 备出现故障后马上采取应急措施进行事后处置。
❖ 这一时期,设备最显著的特点是半自动、手动操作 设备多,结构也简单,因此工人可以自己动手修理, 现象是不坏不修、坏了再修。
❖ BM从上世纪初一直持续到40 年代。
❖ (2)预防维修
❖ 上世纪50年以后,开始出现复杂设备,复杂设备由大 量零件组成,修理所占用的时间已成为影响生产的一 个重要因素。
❖ 另外,人们发现设备故障总在某个部位出现,因此在 维护时主要去查找薄弱部位并对其进行改良。
❖ 为了尽量减少设备修理对生产的影响,苏联提出计划 维修制度;美国提出预防维修制度,即PM (Preventive Maintenance / 1951 ) ,即通过对设 备的“物理性检查”预防其故障的发生,从而达到延 长设备使用寿命的目的。
TPM培训ppt课件

专业技术培训
定期组织维修人员参加专业技术 培训,提高维修技能水平。
维修案例分享
鼓励维修人员分享维修经验和案 例,促进经验交流和技术提升。
新技术学习与应用
引导维修人员关注行业新技术, 积极学习并应用于实际工作中。
多能工培养策略在TPM中应用
跨岗位培训
实施跨岗位培训计划,使操作人员和维修人员能 够掌握多个岗位的技能。
阐述目视化管理的实施步骤,包括确定目标、制定计划、选择工具 、实施改善等。
浪费识别与消除方法
浪费的定义与分类
解释浪费的概念和分类,如时间浪费、物料浪费、人力浪费等,并指出其对企业生产的影 响。
浪费识别方法与技巧
介绍浪费识别的常用方法和技巧,如价值流分析、工艺流程图等,并结合实际案例进行讲 解。
浪费消除策略与措施
01
02
03
设备分类原则
根据设备功能、重要性、 使用频率等因素进行合理 分类,便于后续管理。
编码规范制定
统一设备编码格式,包括 设备类型、序列号、生产 厂家等信息,确保设备信 息的唯一性和可追溯性。
设备标识管理
在设备上粘贴标识牌,标 明设备名称、规格型号、 使用部门等信息,方便识 别和管理。
设备台账建立与管理要求
维修策略类型
维修策略优化
根据设备维修需求和资源情况,选择 合适的维修策略,如事后维修、定期 维修、状态维修等。
通过对设备维修数据的分析,发现设 备维修中存在的问题和不足,对维修 策略进行持续改进和优化,提高设备 维修效率和质量。
维修计划制定
针对不同类型的设备,制定相应的维 修计划,明确维修周期、维修内容、 维修标准等,确保设备维修工作的有 序进行。
台账建立
全面生产维护(TPM)
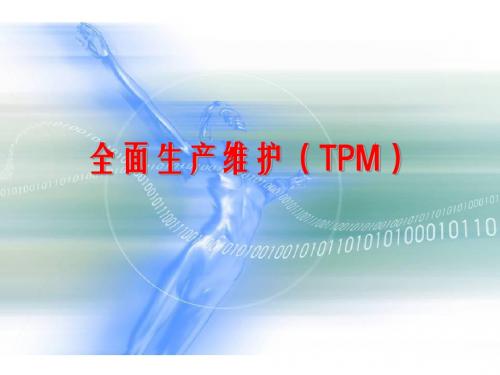
4、PM分析法
P — M :任何现象(Phenomena)都其有物理原因
(Physical),其产生的问题(Problem)可以防止
(Prevented)。4P与材料(Materials)、设备(Machines)、
机理(Mechanisms)和人(Manpower)有关。通过4P找4M,以
查找原因。
全面生产维护(TPM)
丰田屋
通过杜绝一切浪费、以精简生产流程,达成下列目标: 最佳品质、最低成本、最短交货期、最佳安全性、最高员工士气 (Q、C、D、S、M) 及时生产JIT
在正确的时间里,生产 正确数量的正确产品 制定周密的生产计划 连续畅流式流水线 后拉式看板系统 快速切换 物流整合
员工与团队
区分 S T E P 要 点 公司内报上记载 TPM公司内讲习会宣言 干部 : 按级别封闭式研修 一般 : 大会宣讲教育 委员会, 专门分会 推进事务局 确定目标和效果预测 导 入 实 施 阶 段 区分 S T E P 要 点 追求生产效率化的极限 项目组活动 工作岗位小团队活动 阶段类别方式, 诊断和合格证 改良保全,计划保全,预防保全
• 根据定义计算: 方法1:根据“实际合格产量与负荷时间内理论产 量的比值。”实际合格产量为400-8=392件,负荷 时间=480-20=460分,理论产量为460÷0.5=920, 392÷920=42.6% 方法2:根据“合格品的净生产时间占总可用生产时 间的比例”,合格品净生产时间为:392件 ×0.5=196分钟,可用生产时间为480-20=460分钟, 196÷460=42.6%
类别 影 响 设 备 效 率 名称
1、故障LOOS
含义
因故障而发生的停产、维修和部件更换的损失
TPM全面生产维护培训图文PPT课件

TPM 历程
*
以构筑企业组织结构,追求最大限度提高经营系统效率为目标。 以生产体系的全体为对象,确立预防 “灾害、故障、不良”等所有浪费的体制。 包括生产、开发、销售、管理等所有部门。 从总裁到第一线工作人员的全体员工参加。 依靠重复小组的活动达到浪费为 0。
TPM 历程
*
TPM活动内容
建立健全 追求生产系统效率极限化的体质
2000
提高率
201%
单位:百万美圆
综合效率
83.8
87.5
79.9
70
80
90
1998
1999
2000
提高
38
%
人均生产量
307
392
210
100
300
500
1998
1999
2000
提高
87
%
单位:台/套
不良率
12584
9435
15675
0
10000
20000
1998
1999
2000
单位:PPM
可使用性 x 运行率 x 合格率
Overall Equipment Effectiveness 综合设备利用率
=
六大类损失
1. 设备故障停机
6. 启动阶段和产量减少
5. 生产中有次品
3. 怠工和小故障
4. 速度减慢
2. 调试和调节
可使用性损失
运行损失
质量损失
净生产时间
怠工& 速度损失
生产作业时间
TPM使企业效率达到最佳
TPM
Input 投入
Output 产出
产出 投入
=
*
以构筑企业组织结构,追求最大限度提高经营系统效率为目标。 以生产体系的全体为对象,确立预防 “灾害、故障、不良”等所有浪费的体制。 包括生产、开发、销售、管理等所有部门。 从总裁到第一线工作人员的全体员工参加。 依靠重复小组的活动达到浪费为 0。
TPM 历程
*
TPM活动内容
建立健全 追求生产系统效率极限化的体质
2000
提高率
201%
单位:百万美圆
综合效率
83.8
87.5
79.9
70
80
90
1998
1999
2000
提高
38
%
人均生产量
307
392
210
100
300
500
1998
1999
2000
提高
87
%
单位:台/套
不良率
12584
9435
15675
0
10000
20000
1998
1999
2000
单位:PPM
可使用性 x 运行率 x 合格率
Overall Equipment Effectiveness 综合设备利用率
=
六大类损失
1. 设备故障停机
6. 启动阶段和产量减少
5. 生产中有次品
3. 怠工和小故障
4. 速度减慢
2. 调试和调节
可使用性损失
运行损失
质量损失
净生产时间
怠工& 速度损失
生产作业时间
TPM使企业效率达到最佳
TPM
Input 投入
Output 产出
产出 投入
=
全面生产维护知识讲义(PPT 51页)
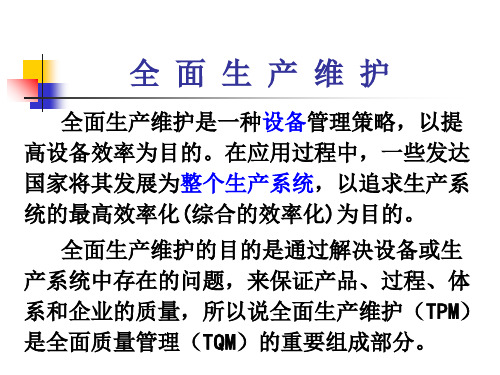
1 ,清除 在隐患,清 动,使领导者 指导什么是
初 垃圾、 除老化、不 提高观察能力、垃圾、什么是
期 废物。 合理的地方,动手能力和重 设备老化;
清
使检修设备 视设备的想法; 指导“清扫
扫
更加方便。 建立“清扫 就是检验”。
就是检验”的
意识
步 活动 骤 内容
对设备 的目标
对人的目标
管理者对 步骤的指导
设备点检的具体内容和特点
所谓的点检,是按照一定的标准、一定周期、对 设备规定的部位进行检查,以便早期发现设备故障隐患, 及时加以修理调整,使设备保持其规定功能的设 备管 理方法。
值得指出的是,设备点检不仅仅是一种检查方式, 而且是一种制度和管理方法。
设备点检制的特点是: A、定人。设立设备操作者兼职的和专职的点检员; B、定点。明确设备故障点,明确点检部位、项目 和内容;
八 大 支 柱
自 主 保 全
计 划 保 全
质 量 保 全
逐 项 改 善
业 务 改 善
初 期 管 理
教 育 培 训
安 全 环 境
两
目视管理活动
基 础
5S管理活动
目视管理
目视管理是利用形象直观、色彩适宜的各种视 觉感知信息来组织现场生产活动,达到提高劳动生 产率目的的一种管理手法,也是一种利用人的视觉 进行“一目了然”管理的科学方法。
活动目标 提高设备的效率
提高整个生产系统 的效率
活动对象
建立良好的设备维护 体系
构筑零损失的管理 体系
参与部门 生产部门、设备部门 企业的所有部门
参与人员 相关部门的所有人员 企业的全部人员
活动方式 自主的小组活动
自主活动和职务活 动相结合
全面生产维护 ppt课件
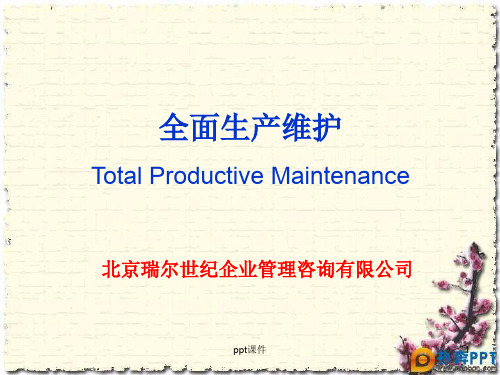
P:Productivity Q:Quality
C:Cost
D:Delivery
S:Safety
M:Morale ppt课件
8
一 TPM基本知识
5 TPM的发展历史
1 事后维护 (BM :Breakdown Maintenance) 故障后再维护;
1950年以前
6 全面生产维护
(TPM : Total Productive Maintenance) 全员参加型的维护 1980年以后
ppt课件
21
二 设备前期管理
7 LCC(Life Cycle Cost)寿命周期成本分析
费用
设备前期管理
设备后期管理
规划 设计 制造 初期管理
稳定使用
老化
时间
设备前期管理应充分集中生产和维修工程师的丰富经验,尽可能 地考虑维护预防(MP)和无维护设计。其目标是:在设备投资规划期 就争取设计在可靠性、维修性、经济运行及安全方面都达到最高水平, 减少从设计到稳定运行的时间和费p用pt课,件让企业以最少的人力进行保全。 22
不重视维护数据、信息
降低设备故障率和保证设备 的完好
重视维修信息和维修资料 的利用
追求设备的高效率运转
要求提高维修工的素质 ppt课件 注重操作工的素质
10
一 TPM基本知识
7 TPM活动体系图
超一流企业
顾客满意 员工满意 社会满意
六大效果
生产 质量 成本 交期 安全 意识
八 大 支 柱
两大基石
推进向
WCM - World Class Manufacturing 世界级制造 LM - Lean Manufacturing 精益生产
- 1、下载文档前请自行甄别文档内容的完整性,平台不提供额外的编辑、内容补充、找答案等附加服务。
- 2、"仅部分预览"的文档,不可在线预览部分如存在完整性等问题,可反馈申请退款(可完整预览的文档不适用该条件!)。
- 3、如文档侵犯您的权益,请联系客服反馈,我们会尽快为您处理(人工客服工作时间:9:00-18:30)。
全面生产维护
Total Productive Maintenance
PPT学习交流
1
目录
一. TPM基本知识 二. 设备的前期管理 三. 设备的初期管理 四. 自主保全 五. 专业保全 六. 其他设备维护方法 七. TPM推行的步骤
PPT学习交流
2
前言
1 墨菲定律:
• 凡事只要有可能出错,那就一定会出错。
PPT学习交流
4
一 设备TPM基本知识
1 设备重要性 1.1科学技术的发展促进了设备的发展,使得生产越 来越依靠设备智能化的作用。 1.2设备的固有质量决定了产品的质量。 1.3设备的运行效率决定了生产的效率。 1.4设备的使用费用影响了生产的成本。 1.5设备的可靠性(MTBF—mean time between failures平均故障时间)影响了以上全部。
2 海恩法则:
• 每一起严重事故的背后,必然有29次轻微事故和300起未 遂先兆以及1000起事故隐患。
• 事故的发生是量的积累的结果;
• 再好的技术,再完美的规章,在实际操作层面,也无法取 代人自身的素质和责任心。
PPT学习交流
3
前言
3 世界级制造
WCM = LM + TQM + TPM + SCM
如果追求“0”的目标,在竞争中一定会胜利
防止故障
日常保全
清扫、注油、检查
测定故障 定期检查 诊断技术
故障维修 提前对策 预防保全
-如果同行也追求“0” 那么速度是胜败的关键
• 全员参与(Small Group Activity)
预防保全
-提高组织成员的能力 -为提高热情而活跃组织
延长寿命
-组织成果的最大化
要求对所有设备进行维修
要求设备的更新
不重视维护数据、信息
降低设备故障率和保证设备 的完好
重视维修信息和维修资料 的利用
追求设备的高效率运转
要求提高维修工的素质 PPT学习交流注重操作工的素质
10
一 TPM基本知识
7 TPM活动体系图
超一流企业
顾客满意 员工满意 社会满意
六大效果
生产 质量 成本 交期 安全 意识
查找薄弱部位对其进行改良 1960年以后
4 维修预防 (MP: Maintenance Prevention)
设计不发生故障的设备,设备FMEA 1965年前后
PPT学习交流
9
一 TPM基本知识
6 传统设备管理与TPM的区别
传统设备管理
TPM
重视完全恢复性的修理
重视设备可靠性、易维护 性、运转效率、合格性的提 升
涉及所有部门的活动
全员参与
小组自主活动
PPT学习交流
设 备 综 合 效 率 最 高
7
一 TPM基本知识
4 生产现场管理的目标—PQCDSM • P产能:时间运转率、设备维修时间 • Q品质:不良品与良品率、客诉 • C成本:设备能源等耗费、备件库存、保养费用 • D交期:计划达成率 、按时交货率 • S安全:安全事故件数 • M士气:个案改善数、 TPM活动参与率
PPT学习交流
5
一 设备TPM基本知识
2设备的生命周期 2.1定义
设备从需求产生到最终报废的时间历程。 2.2设备生命历程
设备前期管理 需求产生 调研、规划 设备设计 制造/采购 设备验收
初期管理
维护规范 制定
规范培训
自主保全
专业保全
个别维护 故障维修 数据分析 设备改造 设备报废
设P备PT学后习期交流管理
PPT学习交流
12
一 TPM基本知识
8 应改变的设备管理思想
8.1 原有的管理思想 无可奈何:问题那么多,这么多年来都没有解决,不可能做好。 事不关己:设备管理是设备部门的事情,与我无关。 保守怀疑:成本、质量、效率能这么好,不可能! 盲目乐观:我们已经做到够好啦,不需要改变了。 被动执行:无所谓了,领导让我们做什么,就做什么呗。 叶公好龙:TPM确实不错,但我们实际问题特殊,没用。 纠结思想:降低设备成本是否会影响产品质量。
WCM - World Class Manufacturing 世界级制造 LM - Lean Manufacturing 精益生产
TQM - Total Quality Management 全面质量管理 TPM - Total Preventive Maintenance 全面生产维护 SCM - Supply Chain Management 供应链管理
6
一 设备TPM基本知识
3 TPM的定义
TPM是源于日本现代设备管理维护制度,它是以达到最高的设备 综合效率为目标,确立以设备生命周期为对象的生产设备维护全系统, 涉及设备的计划、使用、维修等所有部门,从最高领导到第一线工人 全员参加,依靠开展小组自主活动来推行的生产维护。
建立对设备整个寿命周期的生产维护
P:Productivity Q:Quality
C:Cost
D:Delivery
S:Safety
M:Morale PPT学习交流
8
一 TPM基本知识
5 TPM的发展历史
1 事后维护 (BM :Breakdown Maintenance) 故障后再维护; 1950年以前
6 全面生产维护
(TPM : Total Productive Maintenance) 全员参加型的维护 1980年以后
2 预防维护 (PM :Preventive Maintenance) 对周期性故障提出的维护 1955年前后
5 生产维护 (PM: Productive Maintenance)
综合上述维护方法,系统的维护方案 1970年前后
3 改良维护 (CM : Corrective Maintenance )
-排除物理性、心理性缺陷
-排除强制劣化
ቤተ መጻሕፍቲ ባይዱ
TPM = PM + ZD + SG活动
-消灭慢性不良 -延长原有寿命
预防医学
-MP(维护预防)+PM(预防维护)+CM(改善维护)
• “0”目标 (Zero Defect零缺陷)
-追求赚钱的体质(制造成本、产品成本、
日常
健康
提前
现金流改善)
预防
检查
治疗
-与同行的水平无关
八 大 支 柱
两大基石
推进方向
前 自专个 质环事人 期 主业别 量境务才 管 保保改 改改改培 理 全全善 善善善养
彻底的5S
岗位职务性的小集团活动
PPT学习交流
11
一 TPM基本知识
7 TPM的3大思想
• 预防哲学 (Productive Maintenance)
-确立预防的条件(分析问题,防止未然)
Total Productive Maintenance
PPT学习交流
1
目录
一. TPM基本知识 二. 设备的前期管理 三. 设备的初期管理 四. 自主保全 五. 专业保全 六. 其他设备维护方法 七. TPM推行的步骤
PPT学习交流
2
前言
1 墨菲定律:
• 凡事只要有可能出错,那就一定会出错。
PPT学习交流
4
一 设备TPM基本知识
1 设备重要性 1.1科学技术的发展促进了设备的发展,使得生产越 来越依靠设备智能化的作用。 1.2设备的固有质量决定了产品的质量。 1.3设备的运行效率决定了生产的效率。 1.4设备的使用费用影响了生产的成本。 1.5设备的可靠性(MTBF—mean time between failures平均故障时间)影响了以上全部。
2 海恩法则:
• 每一起严重事故的背后,必然有29次轻微事故和300起未 遂先兆以及1000起事故隐患。
• 事故的发生是量的积累的结果;
• 再好的技术,再完美的规章,在实际操作层面,也无法取 代人自身的素质和责任心。
PPT学习交流
3
前言
3 世界级制造
WCM = LM + TQM + TPM + SCM
如果追求“0”的目标,在竞争中一定会胜利
防止故障
日常保全
清扫、注油、检查
测定故障 定期检查 诊断技术
故障维修 提前对策 预防保全
-如果同行也追求“0” 那么速度是胜败的关键
• 全员参与(Small Group Activity)
预防保全
-提高组织成员的能力 -为提高热情而活跃组织
延长寿命
-组织成果的最大化
要求对所有设备进行维修
要求设备的更新
不重视维护数据、信息
降低设备故障率和保证设备 的完好
重视维修信息和维修资料 的利用
追求设备的高效率运转
要求提高维修工的素质 PPT学习交流注重操作工的素质
10
一 TPM基本知识
7 TPM活动体系图
超一流企业
顾客满意 员工满意 社会满意
六大效果
生产 质量 成本 交期 安全 意识
查找薄弱部位对其进行改良 1960年以后
4 维修预防 (MP: Maintenance Prevention)
设计不发生故障的设备,设备FMEA 1965年前后
PPT学习交流
9
一 TPM基本知识
6 传统设备管理与TPM的区别
传统设备管理
TPM
重视完全恢复性的修理
重视设备可靠性、易维护 性、运转效率、合格性的提 升
涉及所有部门的活动
全员参与
小组自主活动
PPT学习交流
设 备 综 合 效 率 最 高
7
一 TPM基本知识
4 生产现场管理的目标—PQCDSM • P产能:时间运转率、设备维修时间 • Q品质:不良品与良品率、客诉 • C成本:设备能源等耗费、备件库存、保养费用 • D交期:计划达成率 、按时交货率 • S安全:安全事故件数 • M士气:个案改善数、 TPM活动参与率
PPT学习交流
5
一 设备TPM基本知识
2设备的生命周期 2.1定义
设备从需求产生到最终报废的时间历程。 2.2设备生命历程
设备前期管理 需求产生 调研、规划 设备设计 制造/采购 设备验收
初期管理
维护规范 制定
规范培训
自主保全
专业保全
个别维护 故障维修 数据分析 设备改造 设备报废
设P备PT学后习期交流管理
PPT学习交流
12
一 TPM基本知识
8 应改变的设备管理思想
8.1 原有的管理思想 无可奈何:问题那么多,这么多年来都没有解决,不可能做好。 事不关己:设备管理是设备部门的事情,与我无关。 保守怀疑:成本、质量、效率能这么好,不可能! 盲目乐观:我们已经做到够好啦,不需要改变了。 被动执行:无所谓了,领导让我们做什么,就做什么呗。 叶公好龙:TPM确实不错,但我们实际问题特殊,没用。 纠结思想:降低设备成本是否会影响产品质量。
WCM - World Class Manufacturing 世界级制造 LM - Lean Manufacturing 精益生产
TQM - Total Quality Management 全面质量管理 TPM - Total Preventive Maintenance 全面生产维护 SCM - Supply Chain Management 供应链管理
6
一 设备TPM基本知识
3 TPM的定义
TPM是源于日本现代设备管理维护制度,它是以达到最高的设备 综合效率为目标,确立以设备生命周期为对象的生产设备维护全系统, 涉及设备的计划、使用、维修等所有部门,从最高领导到第一线工人 全员参加,依靠开展小组自主活动来推行的生产维护。
建立对设备整个寿命周期的生产维护
P:Productivity Q:Quality
C:Cost
D:Delivery
S:Safety
M:Morale PPT学习交流
8
一 TPM基本知识
5 TPM的发展历史
1 事后维护 (BM :Breakdown Maintenance) 故障后再维护; 1950年以前
6 全面生产维护
(TPM : Total Productive Maintenance) 全员参加型的维护 1980年以后
2 预防维护 (PM :Preventive Maintenance) 对周期性故障提出的维护 1955年前后
5 生产维护 (PM: Productive Maintenance)
综合上述维护方法,系统的维护方案 1970年前后
3 改良维护 (CM : Corrective Maintenance )
-排除物理性、心理性缺陷
-排除强制劣化
ቤተ መጻሕፍቲ ባይዱ
TPM = PM + ZD + SG活动
-消灭慢性不良 -延长原有寿命
预防医学
-MP(维护预防)+PM(预防维护)+CM(改善维护)
• “0”目标 (Zero Defect零缺陷)
-追求赚钱的体质(制造成本、产品成本、
日常
健康
提前
现金流改善)
预防
检查
治疗
-与同行的水平无关
八 大 支 柱
两大基石
推进方向
前 自专个 质环事人 期 主业别 量境务才 管 保保改 改改改培 理 全全善 善善善养
彻底的5S
岗位职务性的小集团活动
PPT学习交流
11
一 TPM基本知识
7 TPM的3大思想
• 预防哲学 (Productive Maintenance)
-确立预防的条件(分析问题,防止未然)