111_奚乐_Process Manager在汽车制动器设计优化中的应用
纯电动汽车制动器系统优化与效能提升

纯电动汽车制动器系统优化与效能提升(请注意,以下内容为人工智能生成的回答,仅供参考)纯电动汽车制动器系统的优化与效能提升是一项重要的研究课题。
随着电动汽车市场的快速发展,制动器系统的性能优化成为了提高车辆安全性和驾驶体验的关键。
首先,我们需要考虑的是制动器系统的设计与构成。
电动汽车制动器系统一般由制动器、传感器、控制器和液压系统等组成。
我们可以从以下几个方面对这些组件进行优化。
一是制动器的材料和设计。
材料的选择和设计的合理性直接影响到制动器的性能。
例如,采用高效的摩擦材料,可以提高制动器的制动力和稳定性。
此外,制动器的结构设计也很关键,优化制动器盘与制动器片的接触面积和接触压力分布,可以提升制动器的效能。
二是传感器的性能和精度。
传感器可以实时监测车辆的速度、制动力和制动距离等关键参数,根据这些参数进行制动系统的控制。
因此,传感器的性能和精度对于制动器系统的效能提升具有重要意义。
我们可以考虑采用更先进的传感技术,提高传感器的灵敏度和响应速度。
三是控制器的优化。
控制器是制动器系统的大脑,负责监测传感器信息并根据需要控制制动力的大小和分配。
优化控制器的算法和逻辑,可以提高制动器系统的响应速度和稳定性。
此外,采用智能控制算法,可以根据行车状态和道路情况自适应调整制动力的大小,进一步提升制动器系统的效能。
最后是液压系统的优化。
液压系统是传输制动力的重要组成部分。
优化液压系统的设计和调整液压元件的参数,可以提高制动器的制动力传输效率和响应速度。
此外,还可以考虑采用先进的液压技术,如电液传动系统,进一步提升液压系统的性能。
总结来说,纯电动汽车制动器系统的优化与效能提升需要从制动器的材料和设计、传感器的性能和精度、控制器的优化以及液压系统的优化等多个方面入手。
通过合理的优化和协同设计,可以提高制动器系统的性能和安全性,为驾驶者提供更好的驾驶体验。
不断推动制动器系统技术的创新与发展,也将为纯电动汽车行业的可持续发展做出贡献。
制动系统的优化设计与仿真分析
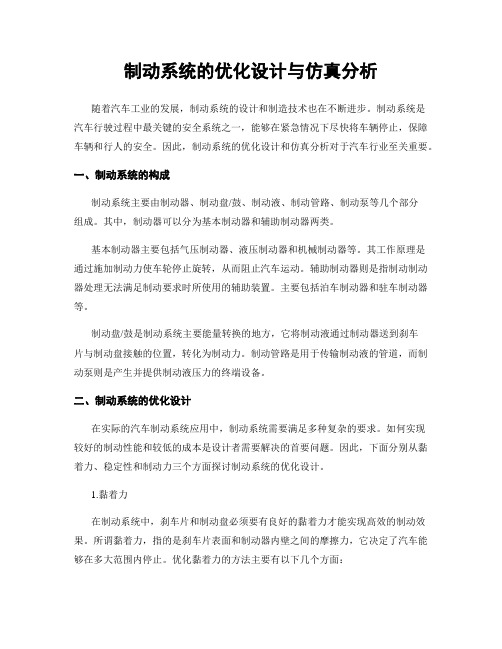
制动系统的优化设计与仿真分析随着汽车工业的发展,制动系统的设计和制造技术也在不断进步。
制动系统是汽车行驶过程中最关键的安全系统之一,能够在紧急情况下尽快将车辆停止,保障车辆和行人的安全。
因此,制动系统的优化设计和仿真分析对于汽车行业至关重要。
一、制动系统的构成制动系统主要由制动器、制动盘/鼓、制动液、制动管路、制动泵等几个部分组成。
其中,制动器可以分为基本制动器和辅助制动器两类。
基本制动器主要包括气压制动器、液压制动器和机械制动器等。
其工作原理是通过施加制动力使车轮停止旋转,从而阻止汽车运动。
辅助制动器则是指制动制动器处理无法满足制动要求时所使用的辅助装置。
主要包括泊车制动器和驻车制动器等。
制动盘/鼓是制动系统主要能量转换的地方,它将制动液通过制动器送到刹车片与制动盘接触的位置,转化为制动力。
制动管路是用于传输制动液的管道,而制动泵则是产生并提供制动液压力的终端设备。
二、制动系统的优化设计在实际的汽车制动系统应用中,制动系统需要满足多种复杂的要求。
如何实现较好的制动性能和较低的成本是设计者需要解决的首要问题。
因此,下面分别从黏着力、稳定性和制动力三个方面探讨制动系统的优化设计。
1.黏着力在制动系统中,刹车片和制动盘必须要有良好的黏着力才能实现高效的制动效果。
所谓黏着力,指的是刹车片表面和制动器内壁之间的摩擦力,它决定了汽车能够在多大范围内停止。
优化黏着力的方法主要有以下几个方面:(1)选择合适的材料。
选择合适的刹车片材料可以改善制动器与制动盘之间的黏着力,从而提高制动性能。
目前主流的刹车片材料有金属、有机和陶瓷等,不同材料的优缺点也不同。
(2)改善制动盘表面。
制动盘表面会因为使用而损耗,会影响刹车片与制动盘之间的黏着力。
对制动盘进行适当的处理或涂层处理可以改善黏着性能。
(3)优化刹车片结构。
刹车片的厚度和面积也会影响制动性能。
适当增加刹车片的面积或者采用具有弹性可调的刹车片结构可以增强黏着性能。
制动器工艺流程

制动器工艺流程制动器是一种用于汽车或其他机械设备上的重要安全装置,用于控制车辆的行驶速度和停车。
制动器工艺流程是指制动器的生产过程,包括设计、加工、装配和调试等环节。
以下是一篇关于制动器工艺流程的700字文章。
制动器工艺流程是制动器生产过程中的关键环节,它决定了制动器的质量和性能。
制动器工艺流程可以分为设计、加工、装配和调试四个阶段。
首先是设计阶段。
制动器的设计非常重要,因为它关系到制动器的性能和可靠性。
设计师需要根据车辆的要求和制动器的使用条件,确定制动器的结构和参数。
设计师还需要使用计算机辅助设计软件进行制动器的模拟分析,确保制动器的性能满足要求。
接下来是加工阶段。
在加工阶段,制动器的零部件需要通过机械加工、热处理和表面处理等工艺进行加工和处理。
其中,机械加工是最关键的环节,它包括车削、铣削、钻孔和磨削等工序,确保零部件的尺寸和形状满足设计要求。
热处理是为了提高零部件的硬度和强度,使其能够承受车辆制动时的高温和高压力。
表面处理是为了提高零部件的耐腐蚀性和耐磨性,使其能够在恶劣的环境下工作。
然后是装配阶段。
在装配阶段,各个零部件需要按照设计图纸进行组装。
装配工人需要仔细阅读图纸,了解每个零部件的位置和安装顺序。
装配工人还需要使用各种工具和设备,确保零部件的精确装配和正确连接。
在装配过程中,装配工人还要进行各种检测和测试,确保制动器的安装质量和性能。
最后是调试阶段。
在调试阶段,制动器需要进行各种调试和测试,确保其性能和功能都符合设计要求。
调试工人需要根据相关标准和规范,进行制动器的调整和检测。
调试工人还需要使用各种仪器和设备,对制动器的制动力、制动距离、制动平衡等进行测量和评估。
如果发现制动器存在问题,调试工人还需要进行相应的调整和修复。
综上所述,制动器工艺流程是制动器生产过程中的关键环节。
通过设计、加工、装配和调试四个阶段,可以保证制动器的质量和性能符合要求。
制动器工艺流程的每一个环节都需要工人们的精心操作和严格监控,以确保制动器的安全可靠性。
基于电动汽车动力系统的制动器性能分析与改进
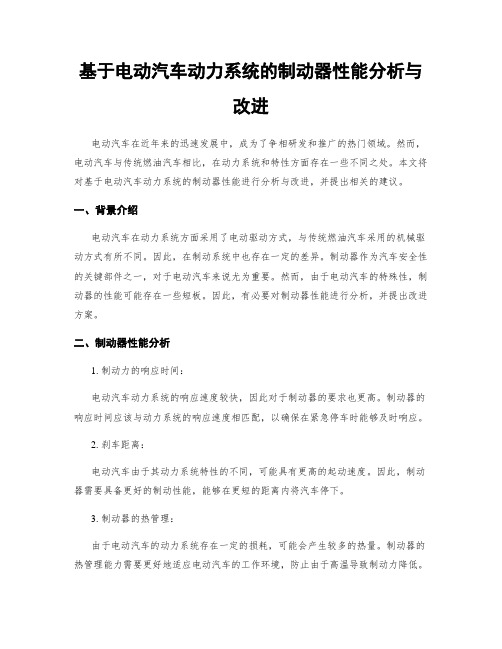
基于电动汽车动力系统的制动器性能分析与改进电动汽车在近年来的迅速发展中,成为了争相研发和推广的热门领域。
然而,电动汽车与传统燃油汽车相比,在动力系统和特性方面存在一些不同之处。
本文将对基于电动汽车动力系统的制动器性能进行分析与改进,并提出相关的建议。
一、背景介绍电动汽车在动力系统方面采用了电动驱动方式,与传统燃油汽车采用的机械驱动方式有所不同。
因此,在制动系统中也存在一定的差异。
制动器作为汽车安全性的关键部件之一,对于电动汽车来说尤为重要。
然而,由于电动汽车的特殊性,制动器的性能可能存在一些短板。
因此,有必要对制动器性能进行分析,并提出改进方案。
二、制动器性能分析1. 制动力的响应时间:电动汽车动力系统的响应速度较快,因此对于制动器的要求也更高。
制动器的响应时间应该与动力系统的响应速度相匹配,以确保在紧急停车时能够及时响应。
2. 刹车距离:电动汽车由于其动力系统特性的不同,可能具有更高的起动速度。
因此,制动器需要具备更好的制动性能,能够在更短的距离内将汽车停下。
3. 制动器的热管理:由于电动汽车的动力系统存在一定的损耗,可能会产生较多的热量。
制动器的热管理能力需要更好地适应电动汽车的工作环境,防止由于高温导致制动力降低。
三、改进方案1. 优化制动系统的控制算法:制动系统的控制算法对于实现快速响应和优化制动力的分配极为重要。
可以通过对制动系统的算法进行优化,提高制动器的性能。
2. 采用新型制动器材料:传统的制动器材料可能无法满足电动汽车的制动需求。
可以考虑采用具有更高温度稳定性和制动性能的新型材料,以提高制动器的性能。
3. 引入智能热管理系统:为了更好地适应电动汽车的工作环境,可以引入智能热管理系统来控制制动器的温度。
该系统可以根据温度变化自动调节制动器的冷却风扇和冷却液的供给,以确保制动器在高温环境下的正常工作。
4. 加强制动器的冷却设计:电动汽车在长时间行驶过程中,大量的动力系统损耗会产生热量,严重影响制动器的性能。
汽车刹车系统的设计与优化
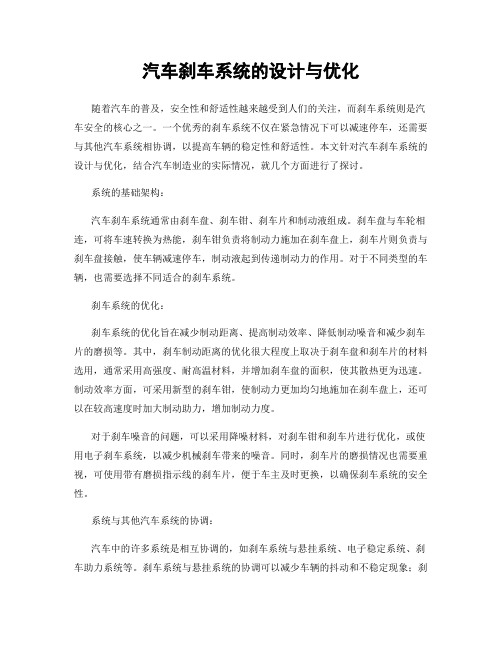
汽车刹车系统的设计与优化随着汽车的普及,安全性和舒适性越来越受到人们的关注,而刹车系统则是汽车安全的核心之一。
一个优秀的刹车系统不仅在紧急情况下可以减速停车,还需要与其他汽车系统相协调,以提高车辆的稳定性和舒适性。
本文针对汽车刹车系统的设计与优化,结合汽车制造业的实际情况,就几个方面进行了探讨。
系统的基础架构:汽车刹车系统通常由刹车盘、刹车钳、刹车片和制动液组成。
刹车盘与车轮相连,可将车速转换为热能,刹车钳负责将制动力施加在刹车盘上,刹车片则负责与刹车盘接触,使车辆减速停车,制动液起到传递制动力的作用。
对于不同类型的车辆,也需要选择不同适合的刹车系统。
刹车系统的优化:刹车系统的优化旨在减少制动距离、提高制动效率、降低制动噪音和减少刹车片的磨损等。
其中,刹车制动距离的优化很大程度上取决于刹车盘和刹车片的材料选用,通常采用高强度、耐高温材料,并增加刹车盘的面积,使其散热更为迅速。
制动效率方面,可采用新型的刹车钳,使制动力更加均匀地施加在刹车盘上,还可以在较高速度时加大制动助力,增加制动力度。
对于刹车噪音的问题,可以采用降噪材料,对刹车钳和刹车片进行优化,或使用电子刹车系统,以减少机械刹车带来的噪音。
同时,刹车片的磨损情况也需要重视,可使用带有磨损指示线的刹车片,便于车主及时更换,以确保刹车系统的安全性。
系统与其他汽车系统的协调:汽车中的许多系统是相互协调的,如刹车系统与悬挂系统、电子稳定系统、刹车助力系统等。
刹车系统与悬挂系统的协调可以减少车辆的抖动和不稳定现象;刹车系统与电子稳定系统的协调可以保持车辆在制动时的稳定性;刹车系统与刹车助力系统的协调可以减轻车主在制动时所需的力道,提高刹车的使用舒适性。
总之,汽车刹车系统的设计与优化需要结合实际情况进行建议,以确保刹车系统的安全性、稳定性和舒适性,既能保证车主的驾驶安全,也能提高汽车刹车系统的使用寿命和经济效益。
家用车制动盘的多目标优化设计

家用车制动盘的多目标优化设计作者:王所国沈精虎石乐来源:《青岛大学学报(工程技术版)》2021年第04期摘要:針对某家用车制动盘的结构改进问题,本文对家用车制动盘进行多目标优化。
为避免优化的盲目性,提高设计效率,首先对建立的制动盘有限元模型进行灵敏度分析,得出制动盘各尺寸参数对制动性能的影响度。
以制动盘表面温度最低与最大等效应力值最小作为目标函数,建立优化数学模型,采用Ansys Workbench中的多目标遗传算法进行求解,优化后进行仿真验证。
优化结果表明,优化后最高温度降低了13.1%,最大应力降低了11.5%,既节省了优化时间又改进了制动盘的结构,实现了制动盘的多目标优化设计。
该研究为盘式制动器设计提供了参考。
关键词:制动盘; 优化设计; 多目标优化; 灵敏度分析; Ansys Workbench中图分类号: U463.51+2 文献标识码: A随着小型家用汽车的普及,交通事故的发生量逐年增加,汽车的行驶安全更加引起人们的重视。
作为制动系统关键部件的制动盘,其性能直接影响车辆的行驶安全[1]。
盘式制动器具有良好的制动性能,广泛用于家用车的制动系统[2],制动盘作为盘式制动器的关键部件直接决定制动性能的好坏。
针对盘式制动器的优化设计,不少学者进行了大量研究。
赵树国等人[3]利用Optistruct软件对汽车盘式制动器进行了拓扑优化,优化后的制动器质量减少了45%;华逢志等人[4]以小型轿车前轮盘式制动器为研究对象,基于Ansys Workbench软件对钳体和支架进行了优化设计;沙智华等人[5]通过分析制动盘沟槽的角度、宽度、密度之间的交互关系对制动盘最大温度值和最大等效应力值的影响完成了对制动盘的优化设计;吴家虎[6]以制动时的温升最小和制动盘尺寸最小为目标函数,利用多目标遗传算法对盘式制动器进行了优化设计;阚云峰[7]以制动过程中的最高制动温度以及允许出现的最大制动力矩为目标函数对盘式制动器进行优化并得到了试验验证;潘公宇等人[8]以散热筋尺寸为优化对象,对盘式制动器进行了有限元分析与优化。
轻量化设计对紧凑型轿车盘式制动器性能的优化

轻量化设计对紧凑型轿车盘式制动器性能的优化随着社会的发展和人们对车辆安全的日益重视,汽车制动系统的性能和轻量化设计变得尤为关键。
盘式制动器作为汽车制动系统的核心组成部分之一,其性能对车辆制动效果和安全性起着重要作用。
本文将关注轻量化设计如何对紧凑型轿车盘式制动器的性能进行优化,以满足汽车制动系统的需求。
首先,轻量化设计可以通过材料选择和结构优化来减轻制动器的质量,从而提高车辆的燃油经济性和操控性能。
对于制动器材料的选择,轻量高强度材料如碳纤维复合材料、陶瓷材料等可以用来替代传统的钢铁材料,减轻制动器质量的同时提高导热性能和制动效果。
同时,结构优化可以通过减少冗余材料和增加刚度来减轻制动器的质量。
例如,通过使用切割或孔洞工艺来减少盘式制动器的重量,或者采用复合结构的盘式制动器以提高刚度和耐热性。
其次,轻量化设计还可以通过减小制动器转动惯量来优化制动器的性能。
制动器转动惯量的减小可以减小制动力矩对车辆动力系统的影响,提高车辆的操控性能和燃油经济性。
为了减小转动惯量,可以采用空心结构的盘式制动器或者减小盘式制动器的外径。
此外,通过优化刹车主缸的设计和减小弹簧力矩的大小,也可以减小制动器转动惯量。
另外,轻量化设计还可以通过优化制动器的散热性能来提高制动器的性能。
盘式制动器在制动过程中产生大量的热量,必须通过散热来保证制动器的正常工作。
优化制动器的散热性能可以有效地降低制动温升,避免制动衰减和制动退化现象的发生。
为了提高散热性能,可以采用切割散热片或者增加散热片的数量和面积来增大散热效果。
此外,也可以通过增加制动器的通风孔数量和大小来增加空气流通,加快散热。
最后,轻量化设计对紧凑型轿车盘式制动器的性能优化还需要考虑制动器的可靠性和安全性。
轻量化设计不能牺牲制动器的强度和耐久性。
因此,在轻量化设计时,需要经过充分的强度计算和试验验证,确保制动器在各种工况下的安全可靠性。
此外,还需要考虑制动器在恶劣环境下的耐腐蚀性和抗疲劳性,以保证制动器的长期稳定性和可靠性。
汽车刹车系统设计中制动效能评价与刹车盘优化

汽车刹车系统设计中制动效能评价与刹车盘优化随着汽车行业的发展和技术的不断进步,汽车刹车系统作为车辆安全的重要组成部分之一,其设计和性能的优化显得尤为重要。
本文将探讨汽车刹车系统中制动效能评价的方法和刹车盘的优化方案。
刹车系统制动效能评价是衡量刹车系统性能优劣的关键指标之一,它直接影响着车辆的刹车性能和驾驶安全。
在汽车制动效能评价中,最常用的指标是制动距离、刹车力、刹车温度和刹车稳定性。
制动距离是指车辆从刹车出发到完全停下所需的距离,它是评价刹车系统制动性能的重要指标。
制动距离越短,说明刹车系统的制动效果越好,车辆的安全性越高。
在刹车系统设计过程中,需要注意刹车盘和刹车片的选材,以及刹车系统的液压传动性能。
刹车力是刹车系统输出给车轮单位面积的制动力大小,它对刹车系统的制动效果有着直接的影响。
刹车力的大小与刹车盘和刹车片的材料、形状以及刹车系统的液压传动系统密切相关。
为了提高制动力的稳定性和可靠性,可以采用刹车盘双层结构和刹车片多片设置的方式来增加刹车系统的刹车力输出。
刹车温度是指刹车过程中刹车盘和刹车片的温度变化情况。
刹车过程中,由于制动摩擦产生的热量会导致刹车盘和刹车片温度升高,如果刹车温度过高,会降低刹车力的输出、损坏刹车盘和刹车片,并且影响刹车系统的制动效果。
为了降低刹车温度,可以采用通风散热的刹车盘设计、优化刹车片材料的导热性能和增加刹车盘的厚度等措施。
刹车稳定性是指刹车系统在刹车过程中的稳定性和可靠性。
刹车稳定性的好坏对驾驶员操作的便利性和行车安全性有着重要影响。
为了提高刹车系统的稳定性,可以采用防抱死系统(ABS)和电子稳定控制系统(ESP)等刹车辅助系统,以及合理设计刹车盘和刹车片的接触面积和接触形状。
刹车盘作为刹车系统的关键部件之一,其设计和优化对刹车系统的性能和稳定性有着重要影响。
刹车盘的材料选择、结构设计和制造工艺对刹车系统的制动效果有着直接影响。
为了优化刹车盘的性能,可以选择抗热疲劳性能好的材料,例如碳陶瓷复合材料,在增加刹车盘的刚度的同时,减轻刹车盘的质量,提高制动效果。
汽车制动性能评价与建议系统的开发与应用
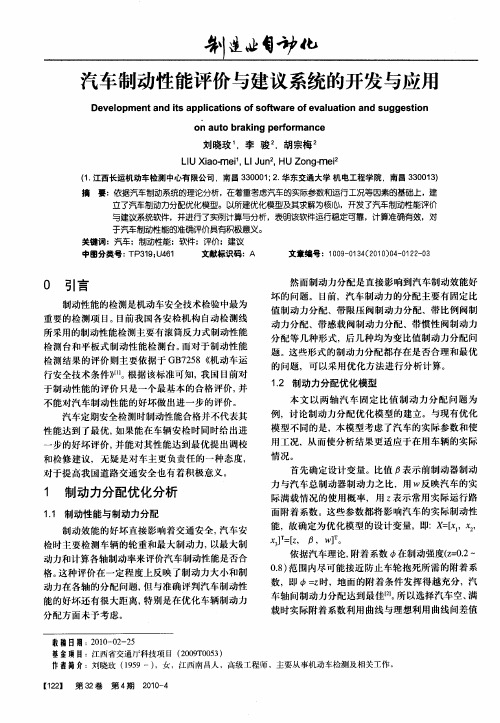
题。这些 形式 的制动 力分配都 存在 是否合理 和最优 的问 题,可 以采用优 化方法 进行分 析计 算。
1 制动力分配优化模型 . 2
本 文 以两 轴汽车 固定 比 值 制动 力 分 配 问题 为
例 ,讨论制 动力分 配优化 模型 的建立 。与现 有优化
模型不 同的 是,本 模型 考虑 了汽车 的实际参数 和使
步的好 坏评价 , 并能 对其性 能达到 最优提 出调校
用工况 ,从而使分 析结 果更适 应于在 用车辆 的实际
情况。
和检修建 议, 无疑 是对车 主更 负责任 的一种 态度 , 对于提高 我国道 路交通 安全也 有着积 极意义 。
首先确 定设计变 量。比值 表 示前制动器 制动 力与汽 车总制 动器制 动力之 比,用 W反映汽 车的实
o u ob a igp f r a c n a t r k n ero m n e
刘晓玫 ’ 。李 骏 。胡宗梅
L U Xiom e 1 L u 2 HU Z n - e l a - i I n 。 o g- i 。 J m
(. 1 江西长运机动车检测 中心有限公 司。南 昌 3 0 0 : . 东交通大学 机 电工程学院 .南昌 3 0 1) 3 0 1 2华 303 摘 要: 依据汽车制动系统的理论分析 , 在着重考虑汽车 的实 际参数和运行工况等因素的基础上 , 建 立了汽车制动力分配优化模型。以所建优化模型及其求解为核心 , 开发 了汽车制动性能评价 与建议 系统软件 ,并进行 了实例计算与分析 ,表明该软件运行稳定可靠,计算准确有效,对 于汽车制动性能的准确评价具有积极意义。 关键词 :汽车;制动性能;软件 ;评价;建议 中图分类号: 3 9 U 6 TP 1 ; 4 1 文献标识码 :A
汽车制动系统的性能改进与优化

汽车制动系统的性能改进与优化汽车制动系统是车辆行驶中至关重要的安全保障之一。
随着汽车工业的发展和技术的进步,人们对汽车制动系统的性能与安全要求也不断提高。
为满足用户的需求,制动系统的性能改进与优化成为一个重要的研究领域。
本文将从几个方面介绍汽车制动系统的性能改进与优化。
一、制动性能的提升制动性能的提升是汽车制动系统改进的关键目标之一。
主要包括制动力矩的增加和制动效率的提高。
1. 制动力矩的增加制动力矩是制动系统提供制动力的能力,直接影响到汽车的制动性能。
制动力矩的增加可以通过以下几种方式来实现:(1)升级制动器:采用更大口径的制动器、改进制动器材料、增加制动器的数量等方式,提高制动器的制动力矩输出。
(2)提升制动液性能:选择高温抗气泡和抗蒸发性能更好的制动液,提高液压传动性能,增加制动力矩输出。
2. 制动效率的提高制动效率是指在单位时间内达到期望制动力的能力,对于制动系统的灵敏性和控制性能具有重要影响。
制动效率的提高可以通过以下几种方式来实现:(1)加强制动器与制动盘(鼓)的接触面积:增大制动盘(鼓)的直径、改进刹车片形状等方式,增加制动器与制动盘(鼓)的接触面积,提高制动效率。
(2)优化制动器的工作参数:通过调整制动器的压力、制动力分配等参数,使制动系统在各种工况下都能保持较高的制动效率。
二、制动系统的防抱死技术制动系统的防抱死技术是为了防止车轮在制动时出现抱死现象,保持车辆的行驶稳定性和操控性能。
常见的制动系统防抱死技术包括:反馈防抱死系统(ABS)、电子制动力分配系统(EBD)和牵引力控制系统(TCS)等。
1. 反馈防抱死系统(ABS)反馈防抱死系统通过控制制动器的工作压力,实时监测车轮的转速和制动器的工作状态,防止车轮在制动时抱死,提高车辆的制动稳定性和操控性能。
2. 电子制动力分配系统(EBD)电子制动力分配系统根据车辆的负荷情况和车轮的附着力,自动调节制动器的工作力度,使各个车轮的制动力分布更为合理,提高制动系统的整体性能和稳定性。
制动器生产线精益生产的应用

一
l l 0 一
( 责任编辑 伍 彬)
( 上接第 9 O页 )
【 2 】 刘树华. 精益生产【 M】 . 北京: 机械工业 出版社, 2 0 1 0 . 【 3 ] 大野耐一. 丰 田生产 方式【 M】 . 北京,生产线实现 了柔性化生产 ,在前制
差时,应及时采取措施进行必要的调整,如调整垫板 、调整 安全器底板垂直度来消除焊后变形的影响;用锉 刀调整安全 器与底板的止 口配合 ;调整底板水平位置,使得齿轮与齿条 啮合理想等 。如噪声无法排除必须更换严重磨损的零件或将
了解测试 原理的用户往往认为这样的超负荷运转会对防坠安
全器造成 破坏 性的影响 ,所 以在检定后的安装使用 中一旦 出 现异 响就会怀 疑是测试 试验造成 了机器损坏 。 通 过对问题防坠器 的现场检查和拆解 ,我们发现 了造成
员应加强理论学 习和工作实践 ,严格按照使用规程和说明书 操作设备 。检验部 门和生产厂家在检验标定过程中应 同时对 其进行维修保养 ,包括清洁制动带表面 ,打磨锥鼓表面 ,更
换失效 的零部件 ,清理安全器 内部的积水、积油、杂物和锈
齿轮 轴与轴瓦间的 间隙过大造成 的。在试验 台上试验 时动作 速 度往往偏离正常值 ,与 吊笼上行时承受负载一样 ,此 时防
测量和制 动性 能的测量 ,在制动性能的测量中可 以采用试验
其次是检 查各组导轮、齿轮 齿条的工作情 况,用塞尺检查导 轮工作面与导轨间隙是否保持在 0 . 5 m m左右,齿轮 与齿条 的 侧隙是否满足 0 . 5 m m  ̄0 . 7 m m的要求 , 检查 齿面磨痕和变形情 况来确定是否更换齿条;然后是检查注油情况和上 下行接触
汽车制动器的应用现状及发展趋势4700字

汽车制动器的应用现状及发展趋势4700字刘军(农业部南京农业机械化研究所,江苏南京210014)摘要:制动器是汽车制动系统中重要的组成部件,其优良的性能是人们的出行安全的重要保障。
随着我国高速公路网的快速发展以及路况复杂程度的增加,人们对于制动系统工作可靠性的需要也日益迫切。
论述了现有汽车制动器的发展现状,分析各自的特点并对汽车制动器的发展趋势进行了展望。
关键词:制动器;发展现状;展望0 引言近年来,我国的高速公路网迅速发展,车流密度和行车速度逐渐增加,路况也变得更加复杂,这使得我国高速交通事故频频发生。
为了保障汽车行车的安全性,研制优良的行车制动系统已然成为了当今汽车设计的热点。
汽车制动系统要求具有足够的制动力,良好的制动可靠性,制动器是制动系统中最重要的一个部件,其好坏决定了汽车是否具有优良的制动性能。
目前用途最广泛的制动器有鼓式制动器和盘式制动器这两类。
鼓式制动器又名块式制动器,是较早出现的制动器,主要依靠制动块压紧制动轮来实现刹车。
盘式制动器刹车作用过程与鼓式比较相似,利用制动盘与静止摩擦片接触来产生摩擦从而使车轮减速实现刹车的目的[1-4]。
1 国内外研究现状1.1 鼓式制动器国内外研究现状鼓式制动器一般由制动底板、制动蹄片、制动分泵、制动鼓以及连杆弹簧等组成,它首先通过液压装置将液压力传递到制动分泵上,然后再通过连杆弹簧将制动蹄片向外推出使其与制动鼓产生相对摩擦而阻止汽车前进。
从汽车诞生至今己有百年的历史,国内外许多专家学者对制动器都做出了大量的、开拓性的研究,涉及到摩擦学、动力学、振动理论和接触力学等多个研究领域。
国内也有很多学者对汽车制动器进行了相关研究。
韩文明等[5]分析单双自由度制动蹄效能因数与摩擦片上的径向合力作用点位置和摩擦系数变化间的关系,后将制动效能因数分解为摩擦自增势或自减势和杠杆增力作用两部分,进而分析每部分制动效能因数的变化特性,并得出提高制动效能稳定性的有效方法,为鼓式制动的改进提供了理论依据。
基于ANSYS_Workbench软件的汽车盘式制动器轻量化设计及实践
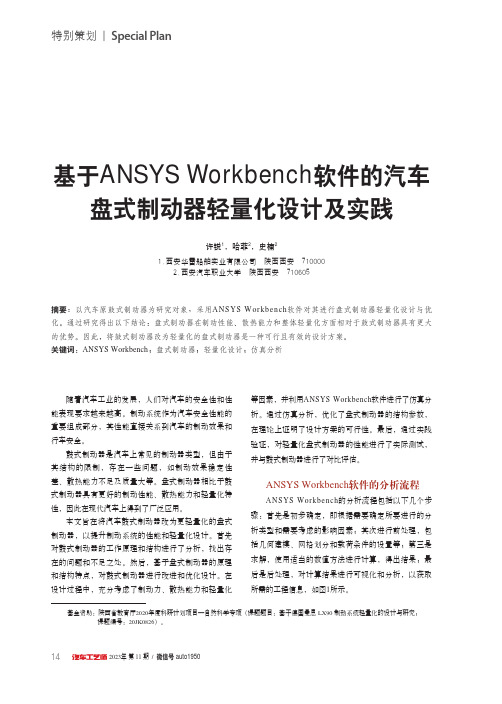
基于ANSYS Workbench软件的汽车盘式制动器轻量化设计及实践许锐1,哈菲2,史楠21.西安华雷船舶实业有限公司 陕西西安 7100002.西安汽车职业大学 陕西西安 710605摘要:以汽车原鼓式制动器为研究对象,采用ANSYS Workbench软件对其进行盘式制动器轻量化设计与优化。
通过研究得出以下结论:盘式制动器在制动性能、散热能力和整体轻量化方面相对于鼓式制动器具有更大的优势。
因此,将鼓式制动器改为轻量化的盘式制动器是一种可行且有效的设计方案。
关键词:ANSYS Workbench;盘式制动器;轻量化设计;仿真分析随着汽车工业的发展,人们对汽车的安全性和性能表现要求越来越高。
制动系统作为汽车安全性能的重要组成部分,其性能直接关系到汽车的制动效果和行车安全。
鼓式制动器是汽车上常见的制动器类型,但由于其结构的限制,存在一些问题,如制动效果稳定性差、散热能力不足及质量大等。
盘式制动器相比于鼓式制动器具有更好的制动性能、散热能力和轻量化特性,因此在现代汽车上得到了广泛应用。
本文旨在将汽车鼓式制动器改为更轻量化的盘式制动器,以提升制动系统的性能和轻量化设计。
首先对鼓式制动器的工作原理和结构进行了分析,找出存在的问题和不足之处。
然后,基于盘式制动器的原理和结构特点,对鼓式制动器进行改进和优化设计。
在设计过程中,充分考虑了制动力、散热能力和轻量化等因素,并利用ANSYS Workbench软件进行了仿真分析。
通过仿真分析,优化了盘式制动器的结构参数,在理论上证明了设计方案的可行性。
最后,通过实践验证,对轻量化盘式制动器的性能进行了实际测试,并与鼓式制动器进行了对比评估。
ANSYS Workbench软件的分析流程ANSYS Workbench的分析流程包括以下几个步骤:首先是初步确定,即根据需要确定所要进行的分析类型和需要考虑的影响因素;其次进行前处理,包括几何建模、网格划分和载荷条件的设置等;第三是求解,使用适当的数值方法进行计算,得出结果;最后是后处理,对计算结果进行可视化和分析,以获取所需的工程信息,如图1所示。
毕业设计论文轿车盘式制动器设计及优化

摘要
盘式制动器主要用于行车制动,其制动效能稳定,在汽车中得到广泛的应用。首先通过了解制动器的设计要求,对盘式制动器进行初始设计;然后再对盘式制动器进行优化设计。本设计通过对摩擦片的中心圆半径、摩擦片直径、制动盘的直径、活塞直径、制动盘厚度、油缸内的油压等参数的优化设计,以制动时间、制动盘的厚度、制动盘的温升作为优化设计目标,建立盘式制动器的优化设计数学模型。选用合理的优化设计方法,编写MATALB程序,通过优化程序的运行,得到最终优化结果,从而得出盘式制动器较合理的尺寸。
制动系至少有行车制动装置和驻车制动装置。前者用来保证第一项功能和在不长的坡道上行驶时保证第二项功能,而后者则用来保证第三项功能。除此之外,有些汽车还设有应急制动和辅助制动装置。
汽车质量是汽车生产企业的生命线,其中安全性能尤为重要。汽车制动系统是汽车行驶的一个重要主动安全系统,其性能的好坏对汽车的行驶安全有着重要影响。随着汽车的行驶速度和路面情况复杂程度的提高,更加需要高性能长寿命的制动系统。其中汽车制动器是汽车制动系统的制动执行装置,制动器的性能直接影响到汽车制动系统的可靠性,因此对汽车汽车制动器的安全性设计提出了更高的要求。
汽车优化设计理论与方法的推广和普及,大大地缩短了产品开发周期,降低了生产成本。这对于那些面临着要进行多型号小批量生产并且客户的要求在不断地改变的企业来说,采用优化设计将大大减少设计的工作量并节省从客户发单到开始生产的时间,从而增强企业的竞争力。
本设计以小轿车为例进行汽车盘式制动器的优化设计,并且前后轮都使用盘ห้องสมุดไป่ตู้制动器为前提条件的。此次毕业设计的题目是“轿车盘式制动器设计及优化”,首先对盘式制动器进行初始设计,然后建立优化设计数学模型,编写程序,通过程序运行后得到盘式制动器的合理结构尺寸。
汽车制动器系统压力容积模拟计算
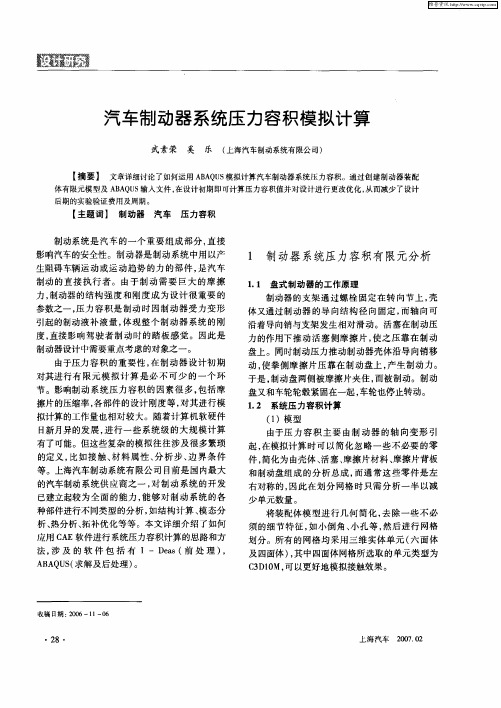
图1 为整个装配体 的有限元模型。
片材料和制动盘组成。
图 l 装配体的有限元模型
图 2 摩擦片压缩 率计算模 型
对于一些需要重点关注 的区域 , 如摩 擦片与 盘的接触部分 以及 壳体可能产生应力集 中位置 , 要保证足够的单元数量和合理的单元形状。
( )接触定 义 2
为了加快计算速度 , 仅取制动盘的部分外表 面使用壳单元划分 网格, 并将活塞和盘设 为刚体 。
维普资讯
汽车制动器系统压 力容积模拟计算
武素荣 奚 乐 ( 海汽车制动系统有限公司) 上
【 摘要 】 文章详细 讨论了如何运用AA U 模拟计算汽车制动器系统压力容积。通过创建制动器装配 BQ S
体有限元模型及 A A U 输入文件 , BQ S 在设计初期即可计算压力容积值并对设计进行更改优化, 从而减少了设计
擦片的压缩率 , 各部件 的设计 刚度等 , 对其进行模
拟计算的工作量也相对较大。随着计算机软硬件
日 新月异的发展 , 进行 一些系统级 的大规模计算
有了可能。但这些复杂的模拟往往涉及很多繁琐 的定义 , 比如接触 、 材料 属性 、 分析 步、 界条件 边
等。上海汽车制动系统有限公司 目前是 国内最大 的汽车制动 系统供应商之一 , 对制动 系统 的开 发 已建立起较为 全面的能力 , 能够对制动 系统 的各
的轴 向强加一个很小 的位移 , 使各部件 分别 向制
动盘靠近 , 以去除刚体 自由运动 , 免计算不 收 避 敛。在 A A U . B Q S 5之后也可以用稳定命令控制 6
计算所需 的边界条件 , 除了制动盘以外 , 其余零件
均 由互相之间的接触来约束运动。
45优化在汽车制动器设计中的应用--奚乐

优化方法在汽车制动器设计中的应用奚乐大陆汽车系统(上海)有限公司优化方法在汽车制动器设计中的应用Optimization Application in Brake Design奚乐(大陆汽车系统(上海)有限公司)摘要: 借助于优化方法,设计人员在概念阶段即可对结构根据需求进行合理化分布,以减少后期大量的改良工作。
本文通过某汽车制动器压力容积的优化为例,详细介绍了如何运用OptiStrcut软件进行拓扑优化的过程。
应用表明该方法能准确的预测计算压力容积值并对设计进行更改优化,从而达到降低成本的目的。
关键词:优化制动器压力容积OptiStruct拓扑优化Abstract Applying the theory of optimization, designer is possible to have improved material distribution in the concept status. This paper introduced the process for a topology optimization of brake volume consumption by the use of Hyper-OptiStruct. The result indicates that this method is efficient to estimate the value of volume consumption and optimize the design, thereby the cost is reduced.Key words:optimization,brake volume consumption,topology optimization,OptiStruct1 概述机械结构分析目前已经成为机械设计中非常重要的一个辅助手段,而作为体现机械工业水平的汽车行业中,结构分析及优化更是在近年来得到很大的应用和提高。
制动器的设计优化与性能改善
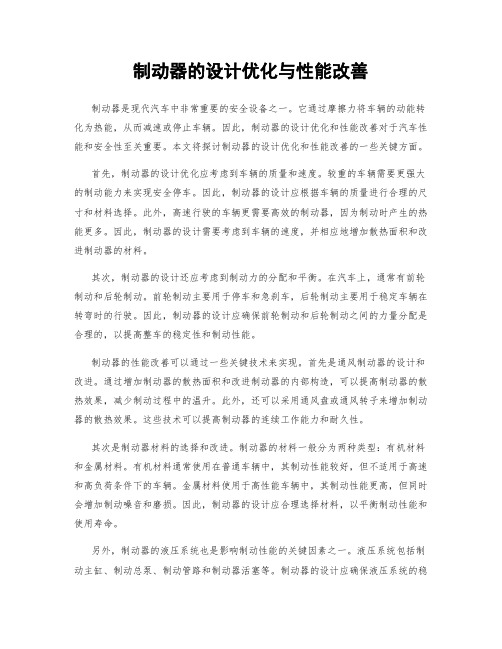
制动器的设计优化与性能改善制动器是现代汽车中非常重要的安全设备之一。
它通过摩擦力将车辆的动能转化为热能,从而减速或停止车辆。
因此,制动器的设计优化和性能改善对于汽车性能和安全性至关重要。
本文将探讨制动器的设计优化和性能改善的一些关键方面。
首先,制动器的设计优化应考虑到车辆的质量和速度。
较重的车辆需要更强大的制动能力来实现安全停车。
因此,制动器的设计应根据车辆的质量进行合理的尺寸和材料选择。
此外,高速行驶的车辆更需要高效的制动器,因为制动时产生的热能更多。
因此,制动器的设计需要考虑到车辆的速度,并相应地增加散热面积和改进制动器的材料。
其次,制动器的设计还应考虑到制动力的分配和平衡。
在汽车上,通常有前轮制动和后轮制动。
前轮制动主要用于停车和急刹车,后轮制动主要用于稳定车辆在转弯时的行驶。
因此,制动器的设计应确保前轮制动和后轮制动之间的力量分配是合理的,以提高整车的稳定性和制动性能。
制动器的性能改善可以通过一些关键技术来实现。
首先是通风制动器的设计和改进。
通过增加制动器的散热面积和改进制动器的内部构造,可以提高制动器的散热效果,减少制动过程中的温升。
此外,还可以采用通风盘或通风转子来增加制动器的散热效果。
这些技术可以提高制动器的连续工作能力和耐久性。
其次是制动器材料的选择和改进。
制动器的材料一般分为两种类型:有机材料和金属材料。
有机材料通常使用在普通车辆中,其制动性能较好,但不适用于高速和高负荷条件下的车辆。
金属材料使用于高性能车辆中,其制动性能更高,但同时会增加制动噪音和磨损。
因此,制动器的设计应合理选择材料,以平衡制动性能和使用寿命。
另外,制动器的液压系统也是影响制动性能的关键因素之一。
液压系统包括制动主缸、制动总泵、制动管路和制动器活塞等。
制动器的设计应确保液压系统的稳定性和灵敏度,以提高制动的响应速度和控制精度。
此外,还可以采用先进的液压控制技术,如电控制动系统或防抱死制动系统,以提高制动的安全性和稳定性。
111_奚乐_Process Manager在汽车制动器设计优化中的应用
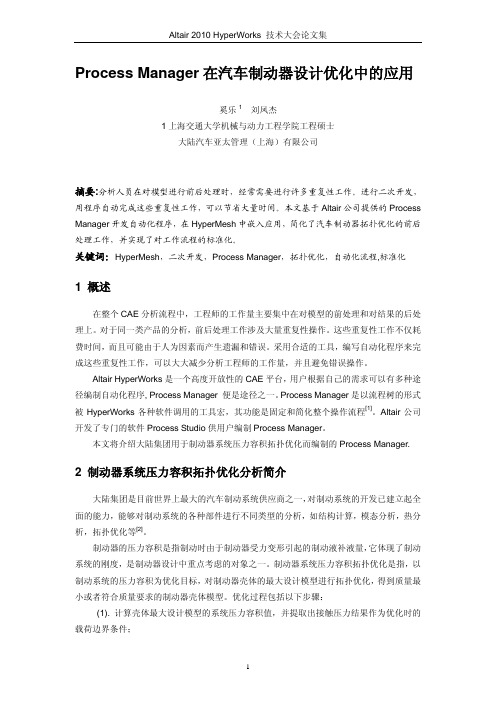
Process Manager在汽车制动器设计优化中的应用奚乐1刘凤杰1上海交通大学机械与动力工程学院工程硕士大陆汽车亚太管理(上海)有限公司摘要:分析人员在对模型进行前后处理时,经常需要进行许多重复性工作。
进行二次开发,用程序自动完成这些重复性工作,可以节省大量时间。
本文基于Altair公司提供的Process Manager开发自动化程序,在HyperMesh中嵌入应用,简化了汽车制动器拓扑优化的前后处理工作,并实现了对工作流程的标准化。
关键词:HyperMesh,二次开发,Process Manager,拓扑优化,自动化流程,标准化1 概述在整个CAE分析流程中,工程师的工作量主要集中在对模型的前处理和对结果的后处理上。
对于同一类产品的分析,前后处理工作涉及大量重复性操作。
这些重复性工作不仅耗费时间,而且可能由于人为因素而产生遗漏和错误。
采用合适的工具,编写自动化程序来完成这些重复性工作,可以大大减少分析工程师的工作量,并且避免错误操作。
Altair HyperWorks是一个高度开放性的CAE平台,用户根据自己的需求可以有多种途径编制自动化程序, Process Manager 便是途径之一。
Process Manager是以流程树的形式被HyperWorks各种软件调用的工具宏,其功能是固定和简化整个操作流程[1]。
Altair公司开发了专门的软件Process Studio供用户编制Process Manager。
本文将介绍大陆集团用于制动器系统压力容积拓扑优化而编制的Process Manager.2 制动器系统压力容积拓扑优化分析简介大陆集团是目前世界上最大的汽车制动系统供应商之一,对制动系统的开发已建立起全面的能力,能够对制动系统的各种部件进行不同类型的分析,如结构计算,模态分析,热分析,拓扑优化等[2]。
制动器的压力容积是指制动时由于制动器受力变形引起的制动液补液量,它体现了制动系统的刚度,是制动器设计中重点考虑的对象之一。
- 1、下载文档前请自行甄别文档内容的完整性,平台不提供额外的编辑、内容补充、找答案等附加服务。
- 2、"仅部分预览"的文档,不可在线预览部分如存在完整性等问题,可反馈申请退款(可完整预览的文档不适用该条件!)。
- 3、如文档侵犯您的权益,请联系客服反馈,我们会尽快为您处理(人工客服工作时间:9:00-18:30)。
Process Manager在汽车制动器设计优化中的应用
奚乐1刘凤杰
1上海交通大学机械与动力工程学院工程硕士
大陆汽车亚太管理(上海)有限公司
摘要:分析人员在对模型进行前后处理时,经常需要进行许多重复性工作。
进行二次开发,用程序自动完成这些重复性工作,可以节省大量时间。
本文基于Altair公司提供的Process Manager开发自动化程序,在HyperMesh中嵌入应用,简化了汽车制动器拓扑优化的前后处理工作,并实现了对工作流程的标准化。
关键词:HyperMesh,二次开发,Process Manager,拓扑优化,自动化流程,标准化
1 概述
在整个CAE分析流程中,工程师的工作量主要集中在对模型的前处理和对结果的后处理上。
对于同一类产品的分析,前后处理工作涉及大量重复性操作。
这些重复性工作不仅耗费时间,而且可能由于人为因素而产生遗漏和错误。
采用合适的工具,编写自动化程序来完成这些重复性工作,可以大大减少分析工程师的工作量,并且避免错误操作。
Altair HyperWorks是一个高度开放性的CAE平台,用户根据自己的需求可以有多种途径编制自动化程序, Process Manager 便是途径之一。
Process Manager是以流程树的形式被HyperWorks各种软件调用的工具宏,其功能是固定和简化整个操作流程[1]。
Altair公司开发了专门的软件Process Studio供用户编制Process Manager。
本文将介绍大陆集团用于制动器系统压力容积拓扑优化而编制的Process Manager.
2 制动器系统压力容积拓扑优化分析简介
大陆集团是目前世界上最大的汽车制动系统供应商之一,对制动系统的开发已建立起全面的能力,能够对制动系统的各种部件进行不同类型的分析,如结构计算,模态分析,热分析,拓扑优化等[2]。
制动器的压力容积是指制动时由于制动器受力变形引起的制动液补液量,它体现了制动系统的刚度,是制动器设计中重点考虑的对象之一。
制动器系统压力容积拓扑优化是指,以制动系统的压力容积为优化目标,对制动器壳体的最大设计模型进行拓扑优化,得到质量最小或者符合质量要求的制动器壳体模型。
优化过程包括以下步骤:
(1). 计算壳体最大设计模型的系统压力容积值,并提取出接触压力结果作为优化时的载荷边界条件;
(2). 用Altair OptiStruct 对最大壳体进行单个零件分析,得出约束反力;
(3). 用Altair OptiStruct 对最大壳体进行拓扑优化。
并查看结果。
(4). 计算优化后模型的压力容积值。
本文所介绍的Process Manager涵盖第(2), (3)步的前后处理工作。
3 Process Manager在制动器拓扑优化过程中的应用
图1 Process Manager 流程图
程序首先将第(1)步中的计算模型导入到HyperMesh中,对模型进行清理,因为只需对壳体进行优化,所以要删除其余所有零件,载荷,分析步等信息,并且施加新的载荷和分析步。
如果不用自动化程序,手工进行这些操作,需要15-25分钟左右的时间。
但使用自动化程序,分析人员只需要输入所需参数,这一步的工作两三分钟即可完成。
图2 分析模型用户界面
分析运行结束后在HyperMesh中查看约束反力。
不需要进入后处理操作界面,可以查看约束反力值。
这个约束反力值将作为下一步优化载荷边界。
图3 查看约束反力
拓扑优化的前处理过程同样只需在用户界面上输入相应参数,程序即可自动建立拓扑优化模型。
图4优化模型用户界面
如图5所示,在优化模型定义界面,可以定义模型的轴向,上一步所获得的约束反力值,拔模方向,以及优化质量目标,最小单元尺寸,和离散度。
其他优化参数采用默认值。
如果用户要修改其他优化参数,需要到Analysis -> optimization ->opti control界面进行修改。
图5 优化参数输入
递交优化分析后,Process Manager最后一步让用户很方便地对结果进行后处理。
程序自动将边界条件隐藏,以便观察优化形状。
图6 查看优化形状
另外,因为OptiStruct和abaqus对entity set的命名规则不一致,程序会自动将entity sets 重命名,并输出abaqus格式的单元集文件。
OptiStruct格式Abaqus格式
图7不同格式的单元集文件
4 小结
Altair公司提供的Process Studio平台,使得用户编制Process Manager非常方便。
程
序核心是用TCL (Tool Command Language)编写的。
TCL是一种通用的计算机脚本语言,简单实用。
使用Process Manager将整个工作流程自动化,标准化,即节省时间,又避免了失误。
减轻了分析人员前后处理的工作量。
5 参考文献
[1] 朱君鸣,HyperWorks二次开发以及流程自动化。
Altair 2009 HyperWorks 技术大会论
文集。
[2] 奚乐,优化方法在汽车制动器设计中的应用。
2007 Altair 大中国区用户技术大会论文集
Process Manager Application in Optimization of
Brake Design
Abstract: It's a common problem for FEA engineers to have to do many repetitive work during pre- and post-processing. Further development to automatically process these repetitive work can improve work efficiency. This paper introduces the automatic process developed in Process Manager of Altair, which is used in HyperMesh and decreases the workload of Brake topology optimization and standardize the work process.
Key words:HyperMesh,Further development,Process Manager,topology optimization,automatic process,standard work process。