机加工检验规范
机械加工工艺与检验规范
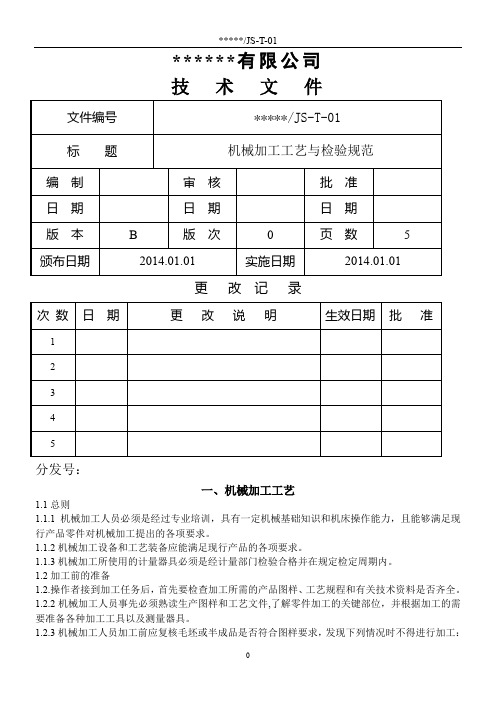
******有限公司技术文件更改记录分发号:一、机械加工工艺1.1总则1.1.1机械加工人员必须是经过专业培训,具有一定机械基础知识和机床操作能力,且能够满足现行产品零件对机械加工提出的各项要求。
1.1.2机械加工设备和工艺装备应能满足现行产品的各项要求。
1.1.3机械加工所使用的计量器具必须是经计量部门检验合格并在规定检定周期内。
1.2加工前的准备1.2.操作者接到加工任务后,首先要检查加工所需的产品图样、工艺规程和有关技术资料是否齐全。
1.2.2机械加工人员事先必须熟读生产图样和工艺文件,了解零件加工的关键部位,并根据加工的需要准备各种加工工具以及测量器具。
1.2.3机械加工人员加工前应复核毛坯或半成品是否符合图样要求,发现下列情况时不得进行加工:a、被加工件存在明显缺陷;b、被加工件与图样尺寸或形状不相符。
1.2.4按工艺规程要求准备好加工所需的全部工艺装备,发现问题及时处理。
对新夹具、模具等,要先熟悉其使用要求和操作方法。
1.3刀具与工件的装夹1.3.1刀具的装夹1.3.1.1在装夹各种刀具前,一定要把刀柄、刀杆、导套等擦试干净。
1.3.1.2刀具装后,应用对刀具装置或试切等检查其正确性。
1.3.2工件的装夹1.3.2.1在机床工作台上安装夹具时,首先要擦净其定位基面,并要找正其与刀具的相对位置。
1.3.2.2工件装夹前应将其定位面、装紧面、垫铁和夹具的定位、平紧面擦试干净,并不得有毛刺。
1.3.2.3按工艺规程中规定的定位基准装夹,若工艺规程中未规定装夹方式,操作者可自行选择定位基准和装夹方法,选择定位基准应按以下原则:a、尽可能使定位基准与设计基准重合;b、尽可能使各加工面采用同一定位基准;粗加工定位基准应尽量选择不加工或加工余量比较小的平整表面,而且只能使用一次;c、精加工定位基准应是已加工表面;d、选择的定位基准必须使工件定位夹方便,加工时稳定可靠。
1.3.2.4对无专用夹具的工件,装夹时应按以下原则进行找正;e、对划线工件应按划线进行找正;f、对不划线工件,在本工序后尚需继续加工的表面,找正精度应保证下工序有足够的加工余量;g、对在本工序加工到成品尺寸的表面,其找正精度应小于尺寸公差的三分之一;h、对在本工序加工到成品尺寸的未注尺寸公差和位置公差的表面,其找正精度应保证GB1804-C级GB1189-10级未注公差和位置公差的要求。
机加件通用检验标准
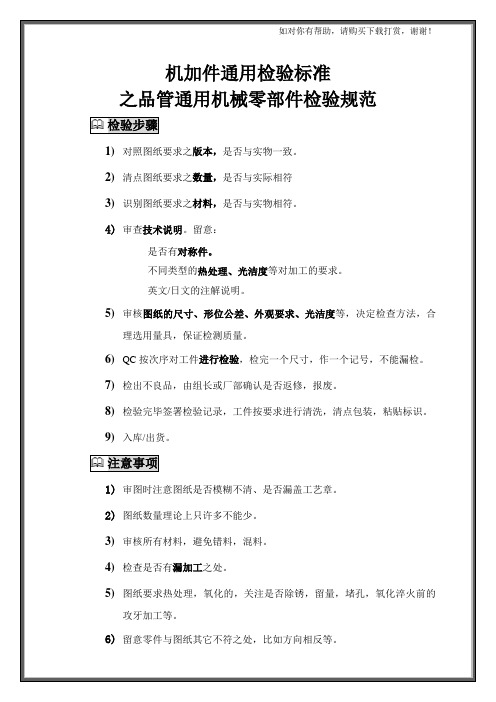
S 总≤被测面积的 5% 不限制 不限制 S≤4.0,P≤3 S 总≤被测面积的 5% 直径≤3.0,P≤5 不限制 不允许 S 总≤被测面积的 2% 不允许
不允许
S 为单个缺陷面积 (mm2) , P 为缺陷数量 (个) , L 为缺陷长度或间距 (mm)
尺寸检验
1.标注公差尺寸检验方法及标准: 用游标卡尺,高度尺,角度尺,百分表,平台,投影仪,高度测量仪或检测 夹具等进行检验: 标准:实测尺寸偏差应符合图纸公差要求。 2.未标注公差尺寸检验方法及标准: 用游标卡尺,高度尺,角度尺,百分表,平台,投影仪,高度测量仪或检测 夹具等进行检验: 标准:实测尺寸偏差应符合以下公差要求。 3.螺纹检验方法及标准: 使用符合 6g(外螺纹)或 6H(内螺纹)公差要求的螺纹规。 标准:符合通止规要求。
4 5 6
镀铬 镀锌 铝硬白
常用形位公差项目及符号:
分类 项目 直线度 平面度 符号 说明 直线度是用来限制母线、棱线、轴线及平面上某一 直线加工后的形状误差。 平面度是用来限制零件上一平面, 加工后不平程度 的形状误差。 圆度是用来限制迴转表面上某一垂轴截面的圆形 误差。 圆柱度是用来限制所给整个圆柱表面, 加工后的实 际形状对理想形状的偏离。 线轮廓用来限制零件上任一曲或曲面任一正截曲 线,加工后的实际形状对其理想形状的变动量。 面轮廓度是用来限制零件上任一曲面, 加工后的实
全跳动
形位公差代号标注示例及其文字说明:
项 目 示例 图解 说明 圆柱表面上任一 素线必须位于轴 向平面内,距离 为公差 0.02 的两 平行直线之间。 直 线 度 Φ 30 圆柱体的轴 线必须位于直径 为公差值 0.05 的 圆柱面内。 整个零件的轴线 必须位于直径为 公差值 0.05 的圆 柱面内。 上表面必须位于 距离为公差值 0.1 的两平行平面 内。 在垂直于轴线的 任一正截面上, 该圆必须位于半 径差为公差值 0.005 的两同心之 间。
机械加工检验规范

机械加工检验规范总则2.1.1检验人员必须具有一定的专业知识和实际工作经验,且能满足先行产品对检验工作的各项要求.2.1.2检验人员所用的计量器具必须是经计量部门校验合格并在规定的检定周期内.2.1.3检验人员验收产品前应熟读相关图样和技术文件,了解零件的关键尺寸及装配关系要点.2.1.4检验人员必须严格按照图样和技术文件所规定的要求对零件进行判定. 2.1.5检验人员应对车间在制品按规定进行标识.见附录A2.1.6检验人员必须定期六个月最长1年参加专业知识培训,学习和接受先进的检测方法,以提高自身的业务水平.检验制度检验人员在检验过程中,严格执行以下规定.2.2.1首检制度对每个操作者加工的第一个零件,应进行全方位的检定,并如实填写记录. 2.2.2巡检制度对工艺文件规定的关键零件或关键工序实行巡检制度,确保关键零件加工全过程处于受控状态.2.2.3转序检验制度对即将转入下道工序的零件,应全数进行检验,严禁不合格品流入下道工序.2.2.4完工检对即将入库的产品必须进行完工检已注证明检验合格的工序可以免检,检验内容包括:a、尺寸和形状是否符合图样要求;b、有无漏加工工序.检验方法2.3.1基本尺寸和形状检验2.3.1.1外径的测量a、测量零件外径尺寸时,至少应在周向两个部位进行测量,并进行记录,两次测量的切点交角应在60°-120°之间,最大与最小半径之差即为该外径圆度误差.b、当零件同直径长度大于50mm时,应作直线度检查,利用刀口尺工作面与外径母线接触,观察漏光度,然后对照标准光隙进行判断.c、当零件同直径长度大于40mm时,应作圆柱度检查,即在同直径长度方向范围内,分别取较大间隔的三个位置进行外径测量,方法同 2.3.1.1 a,取其中误差值最大两组作记录并计算圆柱度误差值.2.3.1.2内径的测量测量零件内径尺寸时,至少应在周向三个部位进行测量,并进行记录,三次测量的接点连线交角应在50°-70°之间,最大与最小半径之差为该内径圆度误差.b、当同直径长度大于40mm时,应作圆柱度检查,即在同直径长度方向范围内,分别取较大间隔两位置进行测量,方法同 2.3.1.2a,选取其中误差值较大的两组作记录,并计算圆柱度误差.2.3.1.3长度测量考虑到端面与轴线的垂直度误差,在测量零件长度时,至少应在周向两个不同位置上进行测量并作记录,两次测量的切点连线交角应在60°-120°之间.2.3.1.4验收标准图样或技术文件未注尺寸公差,按GB1804-C级,未注形位公称按GB1184-10级规定验收.2.3.2螺纹测量2.3.2.1外螺纹测量a、外螺纹外径方法同2.3.1.1 a、c.b、外螺纹中径用螺纹环规或三针测量.c、外螺纹小径用螺纹环规通规检测.2.3.2.2内螺纹测量a、内螺纹外径用螺纹塞规通规检测.b、内螺纹内径方法见2.3.1.2 a.c、内螺纹中径用螺纹塞规检测.2.3.2.3螺纹有效长度内外螺纹的有效长度,应采用螺纹副旋合的方法进行检测.2.3.2.4验收标准a、螺纹的大、中、小径应按图样要求的精度等级进行验收.b、螺纹的有效长度公差,按HY/QT001 紧固件检验规范中的要求执行.2.3.3表面平面的检测2.3.3.1表面粗糙度的检测采用样块比较法进行比较判断.2.3.3.2平面度的检测应采用打表法检测,即平板上放置三个可调支承,将零件测量面朝上放置于支承点上,调整支承点,使三点等高千分表在三点上的读数均为零,打表所测得峰谷值即为该平面的平面度误差.2.3.3.3验收标准按图样规定的精度等级进行验收.2.3.4位置度检测2.3.4.1同轴度跳动检测用两顶尖或刀口状V形块模拟基准轴线,用带表头的测量架进行测量,旋转工件一周后,记录表面轮廓峰谷值,沿轴线方向移动测量架,测得若干截面,取各截面中最大值为该零件的同轴度或跳动误差.2.3.4.2平行度误差的检测采用厚薄差法,即用外径千分尺测量被测零件各测量位置的厚度,取最大与最小值厚度之差,作为该平面度误差.2.3.4.3垂直度误差检测a、采用比较法测量零件的垂直度,以平板工作面模拟基准轴线,刀口角尺与平板基准面构成垂直基准,将被测零件放置于刀口状的V形块上,工件一端与档板固定,将刀口角尺的工作面与被测零件的平面相靠,观察两侧之间的光隙,用标准光隙或塞尺确定其间隙值.b、将被测件在V形块上转一角度,按照2.3.4.3 a进行测量,如此重复若干次,取其中最大值为该零件的垂直度误差.3.3.4.4对称度误差检测a、本体的闸板腔对称度检查,应以闸板移动腔侧面作为模拟基准,进行检测.b、不重要部位对称度的测量,可直接通过厚薄法进行.。
机械加工检验标准及规范

机械(金属切削)加工检验标准及规范机械(金属切削)加工检验标准1. 目的2. 范围3. 规范性引用文件4. 尺寸检验原则5. 检验对环境的要求6. 外观的检验7. 表面粗糙度的检验8. 线性尺寸和角度尺寸公差要求9. 形状和位置公差的检验10.螺纹的检验11.检验计划12.判定规则1.目的为了明确公司金属切削加工检验标准,使检验作业有所遵循,特制定本标准。
2. 范围本标准适用于切削加工(包括外协、制程、出货过程)各检验特性的检验。
在本标准中,切削加工指的是:车削加工、铣削加工、磨削加工、镗削加工、刨削加工、孔加工、拉削加工和钳工作业等。
本标准不适用于锻造、钣金、焊接后的检验,其检验标准另行制定。
本标准规定了尺寸检验的基本原则、对环境的要求、外观检验标准、线性尺寸公差要求、形位公差要求、表面粗糙度的检验、螺纹的检验、检验计划和判定准则。
注:本标准不拟对长度、角度、锥度的测量方法进行描述,可参看相关技术手册;形位公差的测量可参看GB/T1958-1980;3. 规范性引用文件下列文件中的条款通过本标准的引用而成为本标准的条款。
GB/T (ISO 2859-1:1989) 计数抽样检验程序第1部分:GB/T 1804- 2000 (ISO2768-1:104989) 一般公差未注公差的线性和角度尺寸的公差GB/T 1184 - 1996(ISO2768-2:1989) 形状和位置公差未注公差值GB/T 1958-1980 形状和位置公差检测规定GB/T 1957-1981 光滑极限量规4. 尺寸检验原则基本原则所用验收方法应只接收位于规定的尺寸验收极限的工件。
对于有配合要求的工件,其尺寸检验应符合泰勒原则,孔或轴的作用尺寸不允许超过最大实体尺寸。
阿贝原则被测量线应处于被测量线或被测量线的延长线上。
最小变形原则为了保证测量结果的准确可靠,应尽量使各种因素的影响而产生的变形为最小。
最短尺寸链原则为保证一定的测量精度,测量链的环节应减到最少,即测量链应最短。
机械加工件检验规范
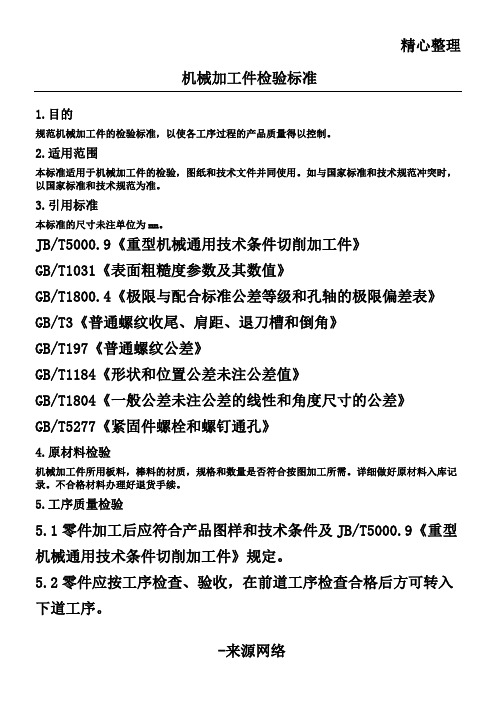
精心整理机械加工件检验标准1.目的规范机械加工件的检验标准,以使各工序过程的产品质量得以控制。
2.适用范围本标准适用于机械加工件的检验,图纸和技术文件并同使用。
如与国家标准和技术规范冲突时,以国家标准和技术规范为准。
3.4.5.5.1零件加工后应符合产品图样和技术条件及JB/T5000.9《重型机械通用技术条件切削加工件》规定。
5.2零件应按工序检查、验收,在前道工序检查合格后方可转入下道工序。
5.3铸钢件、铸铁件、有色金属铸件、锻件加工后如发现有砂眼、缩孔、夹渣、裂纹等缺陷时,在不降低零件强度和使用性能的前提下,允许按照相关标准的有关规定修补,经检验合格后方可继续加工。
5.4加工后的零件不允许有毛刺,除产品图样有要求外,不允许5.55.65.75.85.91)23)镀层表面允许有不严重的流痕及轻微的刮痕印,允许工件边缘色彩稍淡;4)钝化膜有一定的光泽,不到呈暗褐无光的泥巴色;5)钝化膜应牢固,用布揩擦不掉;在50℃~60℃的热水中煮1小时,颜色无显着减退。
6)镀层厚度8~12μm。
5.10表面热镀锌涂层的质量要求:1)表面应均匀、无毛刺、过烧、挂花、伤痕等缺陷,不得有影响2123455.12.1零件图样中未注明倒角时,按JB/T5000.9中表1规定倒角。
5.12.2零件图样中未注明倒圆尺寸又无清根要求时,应按JB/T5000.9中表2规定倒圆。
5.12.3螺纹1)普通螺纹精度按GB/T197规定的6H/6g执行。
2)普通螺纹收尾、肩距、退刀槽和倒角尺寸按GB/T3执行。
3)加工的螺纹表面不允许有黑皮、磕碰、乱扣和毛刺等缺陷。
4)内、外螺纹旋入侧在加工螺纹前必须倒角,外螺纹为45°,5于123)μm;值不4。
5.13.3角度(倾斜度)的未注公差见JB/T5000.9中表5。
5.13.4未注直线度和平面度见JB/T5000.9中表6。
5.13.5未注垂直度公差见JB/T5000.9中表7。
机械制造行业产品质量检验规范
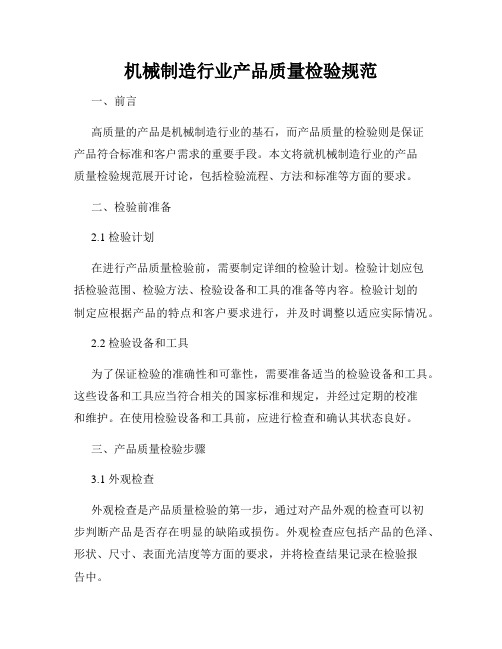
机械制造行业产品质量检验规范一、前言高质量的产品是机械制造行业的基石,而产品质量的检验则是保证产品符合标准和客户需求的重要手段。
本文将就机械制造行业的产品质量检验规范展开讨论,包括检验流程、方法和标准等方面的要求。
二、检验前准备2.1 检验计划在进行产品质量检验前,需要制定详细的检验计划。
检验计划应包括检验范围、检验方法、检验设备和工具的准备等内容。
检验计划的制定应根据产品的特点和客户要求进行,并及时调整以适应实际情况。
2.2 检验设备和工具为了保证检验的准确性和可靠性,需要准备适当的检验设备和工具。
这些设备和工具应当符合相关的国家标准和规定,并经过定期的校准和维护。
在使用检验设备和工具前,应进行检查和确认其状态良好。
三、产品质量检验步骤3.1 外观检查外观检查是产品质量检验的第一步,通过对产品外观的检查可以初步判断产品是否存在明显的缺陷或损伤。
外观检查应包括产品的色泽、形状、尺寸、表面光洁度等方面的要求,并将检查结果记录在检验报告中。
3.2 尺寸检验尺寸检验是产品质量检验的关键环节之一,对产品的关键尺寸进行准确的测量和判定能够直接反映产品的质量水平。
尺寸检验应采用适当的测量工具和方法,比如卡尺、游标卡尺、坐标测量机等,并按照相关的国家标准和规定进行操作和记录。
3.3 功能性能检验功能性能检验是产品质量检验的核心内容,通过检测产品的功能性能能够评估产品是否能够满足客户的需求和使用要求。
功能性能检验应采用适当的测试方法和设备,比如负载试验台、运行试验台等,并按照相关的国家标准和规定进行操作和记录。
3.4 耐久性检验耐久性检验是对产品的使用寿命和耐用性进行评估的重要手段。
耐久性检验应采用适当的试验装置和方法,比如疲劳试验机、振动试验台等,并按照相关的国家标准和规定进行操作和记录。
3.5 环境适应性检验环境适应性检验是对产品在不同环境条件下的适应性进行评估的重要手段。
环境适应性检验应采用适当的试验方法和设备,比如恒温恒湿试验箱、盐雾试验箱等,并按照相关的国家标准和规定进行操作和记录。
机加工检验规范
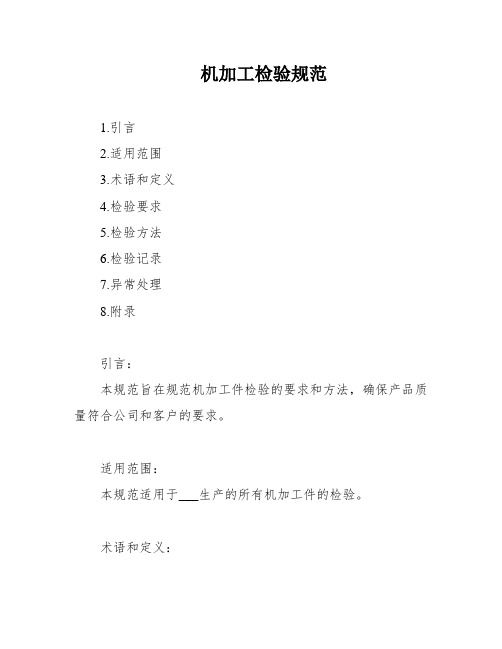
机加工检验规范1.引言2.适用范围3.术语和定义4.检验要求5.检验方法6.检验记录7.异常处理8.附录引言:本规范旨在规范机加工件检验的要求和方法,确保产品质量符合公司和客户的要求。
适用范围:本规范适用于___生产的所有机加工件的检验。
术语和定义:1.机加工件:指在机械设备上通过切削、铣削、钻孔等方式加工成形的零部件。
2.检验:指对机加工件进行各项检测以确保其质量符合要求的活动。
3.合格品:指经过检验符合要求的机加工件。
4.不合格品:指经过检验不符合要求的机加工件。
检验要求:1.外观检验:应检查机加工件的表面是否有明显划痕、裂纹、氧化等缺陷。
2.尺寸检验:应检查机加工件的尺寸是否符合要求。
3.材质检验:应检查机加工件的材质是否符合要求。
4.功能检验:应检查机加工件的功能是否符合要求。
检验方法:1.外观检验:应使用肉眼和放大镜进行检查。
2.尺寸检验:应使用测量工具进行检查,如卡尺、游标卡尺等。
3.材质检验:应使用化学分析仪进行检查。
4.功能检验:应使用相应的设备进行检查,如试验台、模拟器等。
检验记录:1.检验记录应详细记录检验日期、检验人员、检验结果等信息。
2.检验记录应保存至少两年。
异常处理:1.对于不合格品,应及时进行处理,如返工、报废等。
2.对于多次不合格品,应进行原因分析,并采取相应的措施进行改进。
附录:1.机加工件检验报告模板。
2.机加工件检验记录表。
1.目的本文旨在介绍___。
Ltd的产品检验标准,以确保产品质量符合标准要求。
2.范围本检验标准适用于___。
Ltd所有产品的检验,包括但不限于铁路设备、机械零部件等。
3.规范性引用文件本检验标准引用以下文件:GB/T 1804-2000 一般尺寸公差GB/T 1184-1996 钢铁表面缺陷分类和规定GB/T 1167-1983 螺纹检验方法GB/T 3478-1995 机械零部件表面粗糙度的测量和评定GB/T 1800-1996 基本公差制度4.检验条件所有产品在出厂前必须经过以下检验条件:外观检查表面粗糙度检查线性尺寸和角度尺寸公差检查形状和位置公差检查螺纹检查沉孔检查5.包装防护所有产品在出厂前必须进行适当的包装和防护,以确保产品完好无损。
机械加工件检测标准

机械加工件检测标准1、目的:通过严格执行三检,“首件检验”、“巡回检验”、“完工检验”将检验工件与工序控制紧密结合,对每一工序的质量问题或可能出现的质量问题不放过,不合格品不能转入下工序,从而提高产品质量。
2、适用范围:所有加工件3.检验原则3.1.检验人员必须具有一定的专业知识和实际工作经验,且能满足现行产品对检验工作的各项要求。
3.2.检验人员所用的计量器具必须是经计量部门校验合格并在规定周期内。
3.3.检验人员验收产品前应熟读相关图样和技术文件,了解零件的关键尺寸及装配关系要点。
3.4 检验人员必须严格按照图样和技术文件所规定的要求对零件进行判定。
4.检验依据检测依据按图纸及工艺卡检测5.检测种类:“工序自检”“首件检验”、“巡回检验”、“完工检验”5.1.工序自检:工件完成工序后进行自检,自检合格后在工艺卡进行签字;5.2.首件检验:批量工件必须首件检验后,才能开始加工5.2.1.对首件,根据加工工艺要求,核实首件产品或工件(毛坯)产品的质量特性是否符合要求。
对首批检查的工件,操作者必须做好自检,在操作者缺乏检测手段时,也应对工件外观质量自检,合格后送质量专员检查。
无论在任何情况下,首件检验未经检验合格,不得进行批量生产或继续加工作业。
5.2.2.工作班开始加工的第一个工件;5.2.3.调换操作者后加工的第一个工件;5.2.4. 更换(调整)工艺装备或更换模具后加工的第一个工件;5.2.5.更换材料批(炉)号后加工的第一个工件;5.2.6. 代用材料后加工的第一个工件;5.2.7.检验内容:根据检验标准的要求,核对首件产品的质量特性值是否真正符合要求;对首件检验合格,批准生产加工,首件检验不合格,进行不合格品的处理,同时分析不合格原因,采取改进措施后加工,产品继续首件检验,直至合格为止。
5.3.巡回检验:5.3.1.由检验人员在生产现场,进行日常巡回监督检查,重点监控工序质量和典型零件质量;5.3.2根据检验标准、图纸和工艺的要求、检验、核对巡检产品的质量特性值是否真正符合要求;5.3.3.若巡检某质量特性值不合格,应按《不合格品报告单》处理,同时。
机加工检验规范(完整资料).doc
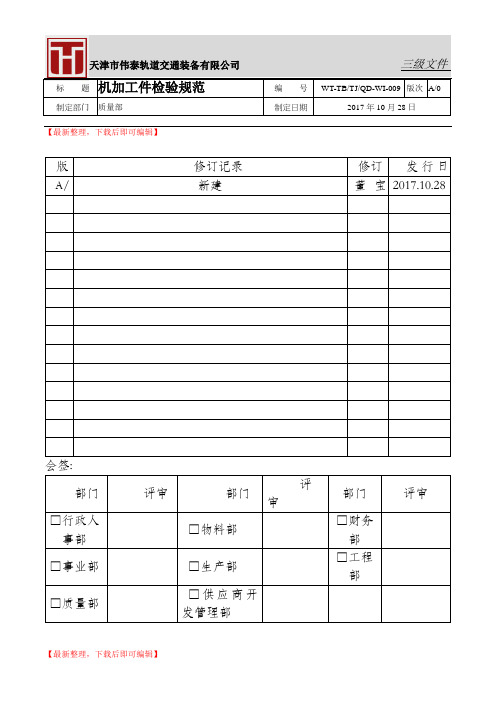
标题机加工件检验规范编号WT-TB/TJ/QD-WI-009 版次A/0 制定部门质量部制定日期2017年10月28日【最新整理,下载后即可编辑】版修订记录修订发行日A/新建董宝2017.10.28部门评审部门评审部门评审□行政人事部□物料部□财务部□事业部□生产部□工程部□质量部□供应商开发管理部标题机加工件检验规范编号WT-TB/TJ/QD-WI-009 版次A/0 制定部门质量部制定日期2017年10月28日批准:编制:董宝国审核:1目的 (3)2范围 (3)3规范性引用文件 (3)4检验条件 (3)5包装防护 (3)6外观 (3)7表面粗糙度的检验 (4)8线性尺寸和角度尺寸公差要求 (4)9形状和位置公差的检验 (5)10螺纹的检验 (5)11沉孔的检验 (6)12检验基本原则 (6)13记录 (6)标题机加工件检验规范编号WT-TB/TJ/QD-WI-009 版次A/0制定部门质量部制定日期2017年10月28日1目的为了明确公司金属切削加工检验标准,使检验作业有所遵循,特制定本标准。
2范围本标准适用于切削加工(包括外协、外购、制程、成品)各检验特性的检验。
在本标准中,切削加工指的是:车削加工、铣削加工、磨削加工、镗削加工、刨削加工、孔加工、螺纹加工、拉削加工和钳工作业等。
本标准规定了尺寸检验的基本原则、对环境的要求、外观检验标准、线性尺寸公差要求、形位公差要求、表面粗糙度的检验、螺纹的检验、检验计划和判定准则。
3规范性引用文件下列文件中的条款通过本标准的引用而成为本标准的条款。
GB/T 2828.1-2003 (ISO 2859-1:1989) 计数抽样检验程序第1部分:GB/T 1804- 2000 (ISO2768-1:104989) 一般公差未注公差的线性和角度标题机加工件检验规范编号WT-TB/TJ/QD-WI-009 版次A/0 制定部门质量部制定日期2017年10月28日尺寸的公差GB/T 1184 - 1996(ISO2768-2:1989) 形状和位置公差未注公差值GBT 1958-2004 产品几何量技术规范(GPS) 形状和位置公差检测规定.pdfGB-T 1800.3-1998 极限与配合基础第3部分:标准公差和基本偏差数值表.pdf4检验条件4.1正常日光下(晴天);照度为 100lx~200lx 的灯光下进行(相当于40-60W的白炽灯光下,物件距光源65~100cm)。
机械加工工艺与检验规范

******有限公司技术文件更改记录分发号:一、机械加工工艺1.1总则1.1.1机械加工人员必须是经过专业培训,具有一定机械基础知识和机床操作能力,且能够满足现行产品零件对机械加工提出的各项要求。
1.1.2机械加工设备和工艺装备应能满足现行产品的各项要求。
1.1.3机械加工所使用的计量器具必须是经计量部门检验合格并在规定检定周期内。
1.2加工前的准备1.2.操作者接到加工任务后,首先要检查加工所需的产品图样、工艺规程和有关技术资料是否齐全。
1.2.2机械加工人员事先必须熟读生产图样和工艺文件,了解零件加工的关键部位,并根据加工的需要准备各种加工工具以及测量器具。
1.2.3机械加工人员加工前应复核毛坯或半成品是否符合图样要求,发现下列情况时不得进行加工:a、被加工件存在明显缺陷;b、被加工件与图样尺寸或形状不相符。
1.2.4按工艺规程要求准备好加工所需的全部工艺装备,发现问题及时处理。
对新夹具、模具等,要先熟悉其使用要求和操作方法。
1.3刀具与工件的装夹1.3.1刀具的装夹1.3.1.1在装夹各种刀具前,一定要把刀柄、刀杆、导套等擦试干净。
1.3.1.2刀具装后,应用对刀具装置或试切等检查其正确性。
1.3.2工件的装夹1.3.2.1在机床工作台上安装夹具时,首先要擦净其定位基面,并要找正其与刀具的相对位置。
1.3.2.2工件装夹前应将其定位面、装紧面、垫铁和夹具的定位、平紧面擦试干净,并不得有毛刺。
1.3.2.3按工艺规程中规定的定位基准装夹,若工艺规程中未规定装夹方式,操作者可自行选择定位基准和装夹方法,选择定位基准应按以下原则:a、尽可能使定位基准与设计基准重合;b、尽可能使各加工面采用同一定位基准;粗加工定位基准应尽量选择不加工或加工余量比较小的平整表面,而且只能使用一次;c、精加工定位基准应是已加工表面;d、选择的定位基准必须使工件定位夹方便,加工时稳定可靠。
1.3.2.4对无专用夹具的工件,装夹时应按以下原则进行找正;e、对划线工件应按划线进行找正;f、对不划线工件,在本工序后尚需继续加工的表面,找正精度应保证下工序有足够的加工余量;g、对在本工序加工到成品尺寸的表面,其找正精度应小于尺寸公差的三分之一;h、对在本工序加工到成品尺寸的未注尺寸公差和位置公差的表面,其找正精度应保证GB1804-C级GB1189-10级未注公差和位置公差的要求。
机加工检验规范

会签:1目的......................................................................... 2范围......................................................................... 3规范性引用文件............................................................... 4检验条件..................................................................... 5包装防护..................................................................... 6外观......................................................................... 7表面粗糙度的检验............................................................. 8线性尺寸和角度尺寸公差要求................................................... 9形状和位置公差的检验......................................................... 10螺纹的检验.................................................................. 11沉孔的检验.................................................................. 12检验基本原则................................................................ 13记录........................................................................1目的???为了明确公司金属切削加工检验标准,使检验作业有所遵循,特制定本标准。
机械加工工艺与检验规范

******有限公司技术文件更改记录一、机械加工工艺1.1总则1.1.1机械加工人员必须是经过专业培训,具有一定机械基础知识和机床操作能力,且能够满足现行产品零件对机械加工提出的各项要求。
1.1.2机械加工设备和工艺装备应能满足现行产品的各项要求。
1.1.3机械加工所使用的计量器具必须是经计量部门检验合格并在规定检定周期内。
1.2加工前的准备1.2.操作者接到加工任务后,首先要检查加工所需的产品图样、工艺规程和有关技术资料是否齐全。
1.2.2机械加工人员事先必须熟读生产图样和工艺文件,了解零件加工的关键部位,并根据加工的需要准备各种加工工具以及测量器具。
1.2.3机械加工人员加工前应复核毛坯或半成品是否符合图样要求,发现下列情况时不得进行加工:a、被加工件存在明显缺陷;b、被加工件与图样尺寸或形状不相符。
1.2.4按工艺规程要求准备好加工所需的全部工艺装备,发现问题及时处理。
对新夹具、模具等,要先熟悉其使用要求和操作方法。
1.3刀具与工件的装夹1.3.1刀具的装夹1.3.1.1在装夹各种刀具前,一定要把刀柄、刀杆、导套等擦试干净。
1.3.1.2刀具装后,应用对刀具装置或试切等检查其正确性。
1.3.2工件的装夹1.3.2.1在机床工作台上安装夹具时,首先要擦净其定位基面,并要找正其与刀具的相对位置。
1.3.2.2工件装夹前应将其定位面、装紧面、垫铁和夹具的定位、平紧面擦试干净,并不得有毛刺。
1.3.2.3按工艺规程中规定的定位基准装夹,若工艺规程中未规定装夹方式,操作者可自行选择定位基准和装夹方法,选择定位基准应按以下原则:a、尽可能使定位基准与设计基准重合;b、尽可能使各加工面采用同一定位基准;粗加工定位基准应尽量选择不加工或加工余量比较小的平整表面,而且只能使用一次;c、精加工定位基准应是已加工表面;d、选择的定位基准必须使工件定位夹方便,加工时稳定可靠。
1.3.2.4对无专用夹具的工件,装夹时应按以下原则进行找正;e、对划线工件应按划线进行找正;f、对不划线工件,在本工序后尚需继续加工的表面,找正精度应保证下工序有足够的加工余量;g、对在本工序加工到成品尺寸的表面,其找正精度应小于尺寸公差的三分之一;h、对在本工序加工到成品尺寸的未注尺寸公差和位置公差的表面,其找正精度应保证GB1804-C级GB1189-10级未注公差和位置公差的要求。
机加件通用检验标准

分类项目符号说明形状公差直线度直线度是用来限制母线、棱线、轴线及平面上某一直线加工后的形状误差。
平面度平面度是用来限制零件上一平面,加工后不平程度的形状误差。
圆度圆度是用来限制迴转表面上某一垂轴截面的圆形误差。
圆柱度圆柱度是用来限制所给整个圆柱表面,加工后的实际形状对理想形状的偏离。
线轮廓度线轮廓用来限制零件上任一曲或曲面任一正截曲线,加工后的实际形状对其理想形状的变动量。
面轮廓度面轮廓度是用来限制零件上任一曲面,加工后的实际形状误差。
位置公差定向平行度平行度用来限制零件上一直线或平面对基准直线或平面,加工后所产生的不垂直程度的误差。
垂直度垂直度用来限制零件上一直线或平面对基准直线或平面,加工后所产生的不垂直程度的误差。
倾斜度倾斜度用来限制零件上一斜面或斜直线,对基准平面倾斜角度的误差。
定位同轴度同轴度用来限制共轴表面中被测表面轴线对基准轴线歪斜程度。
对称度对称度用来限制加工表面的对称平面对基准平面或轴线歪斜的程度。
位置度位置度用来限制零件加工后的一些实际点、线、面、对其理想位置的最大偏离量。
跳动圆跳动圆跳动用来限制零件上圆柱面、圆锥(任意迴转曲面)及端面上,某一横截面(或直径位置上)上,迴转一周测得对基准轴线(或平面)的最大偏离量。
全跳动全跳动用来限制零件上迴转面或端面,整个表面对基准轴线(或平面)的最大偏离量。
形位公差代号标注示例及其文字说明:项目示例图解说明直线度圆柱表面上任一素线必须位于轴向平面内,距离为公差0.02的两平行直线之间。
Φ30圆柱体的轴线必须位于直径为公差值0.05的圆柱面内。
整个零件的轴线必须位于直径为公差值0.05的圆柱面内。
平面度上表面必须位于距离为公差值0.1的两平行平面内。
圆度在垂直于轴线的任一正截面上,该圆必须位于半径差为公差值0.005的两同心之间。
圆柱度圆柱面必须位于半径差为公差值0.006的两同轴圆柱面之间。
线轮廓度实际曲线必须位于包络以理想曲线为中心的一系列直径为0.1圆的两包络线之间。
机械加工工艺与检验规范
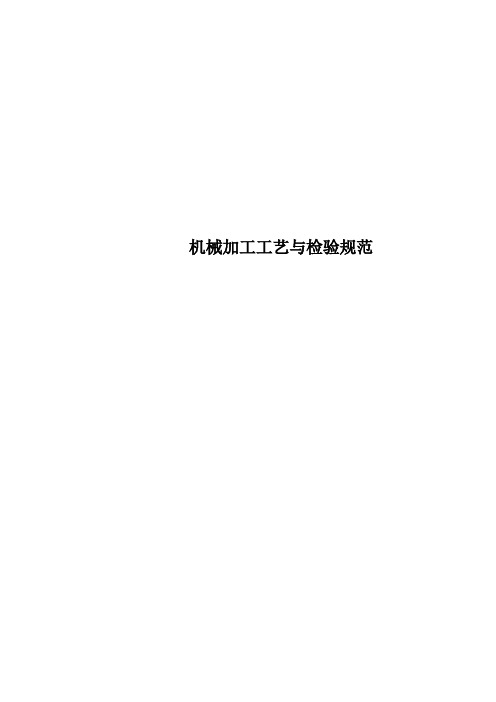
机械加工工艺与检验规范******有限公司技术文件更改记录分发号:一、机械加工工艺1.1总则机械加工人员必须是经过专业培训,具有一定机械基础知识和机床操作能力,且能够满足现行产品零件对机械加工提出的各项要求。
机械加工设备和工艺装备应能满足现行产品的各项要求。
机械加工所使用的计量器具必须是经计量部门检验合格并在规定检定周期内。
1.2加工前的准备1.2.操作者接到加工任务后,首先要检查加工所需的产品图样、工艺规程和有关技术资料是否齐全。
1.2.2机械加工人员事先必须熟读生产图样和工艺文件,了解零件加工的关键部位,并根据加工的需要准备各种加工工具以及测量器具。
1.2.3机械加工人员加工前应复核毛坯或半成品是否符合图样要求,发现下列情况时不得进行加工:a、被加工件存在明显缺陷;b、被加工件与图样尺寸或形状不相符。
按工艺规程要求准备好加工所需的全部工艺装备,发现问题及时处理。
对新夹具、模具等,要先熟悉其使用要求和操作方法。
1.3刀具与工件的装夹刀具的装夹.1在装夹各种刀具前,一定要把刀柄、刀杆、导套等擦试干净。
.2刀具装后,应用对刀具装置或试切等检查其正确性。
工件的装夹.1在机床工作台上安装夹具时,首先要擦净其定位基面,并要找正其与刀具的相对位置。
.2工件装夹前应将其定位面、装紧面、垫铁和夹具的定位、平紧面擦试干净,并不得有毛刺。
.3按工艺规程中规定的定位基准装夹,若工艺规程中未规定装夹方式,操作者可自行选择定位基准和装夹方法,选择定位基准应按以下原则:a、尽可能使定位基准与设计基准重合;b、尽可能使各加工面采用同一定位基准;粗加工定位基准应尽量选择不加工或加工余量比较小的平整表面,而且只能使用一次;c、精加工定位基准应是已加工表面;d、选择的定位基准必须使工件定位夹方便,加工时稳定可靠。
.4对无专用夹具的工件,装夹时应按以下原则进行找正;e、对划线工件应按划线进行找正;f、对不划线工件,在本工序后尚需继续加工的表面,找正精度应保证下工序有足够的加工余量;g、对在本工序加工到成品尺寸的表面,其找正精度应小于尺寸公差的三分之一;h、对在本工序加工到成品尺寸的未注尺寸公差和位置公差的表面,其找正精度应保证GB1804-C级GB1189-10级未注公差和位置公差的要求。
- 1、下载文档前请自行甄别文档内容的完整性,平台不提供额外的编辑、内容补充、找答案等附加服务。
- 2、"仅部分预览"的文档,不可在线预览部分如存在完整性等问题,可反馈申请退款(可完整预览的文档不适用该条件!)。
- 3、如文档侵犯您的权益,请联系客服反馈,我们会尽快为您处理(人工客服工作时间:9:00-18:30)。
1.目的
规范加工制品的检查标准,以使各工序加工过程的质量给予管控,从而确保出货成品的质量满足客户要求。
2.范围
本标准适用于机加加工的制品,依照图纸检查;图纸未标注时依照相适应的国家标准进行检验。
3.定义
3.1首件:
a.本工序依照某图纸所加工的第一个部件;
b.中间切换加工其他部件后,继续加工剩余数量加工的第一个部件;
c.正在生产设备发生故障时的部件及设备故障排除后加工的第一个部件;
d.前一天未完成,继续加工的第一个部件;
e.加工中设备更换后加工的第一个部件;
f.加工中作业人员更换后加工的第一个部件;
3.2半成品:
a. 本组别最后一道工序加工完成后,转入其他组别需要继续加工的制品;
b. 本组别最后一道工序加工完成后,需要外协表面加工处理的制品;
4.3 成品
本组别最后一道即最终工序加工完成后的制品;
4. 职责
4.1 品质部:负责送检产品的检验工作,并记录检验结果。
4.2 生产部:负责产品的检验通知及组织不合格产品的返工。
4.2.1 机加工产品检验通知
①机加组每天完工的成品放置成品待检区,然后通知品质人员前去检验。
②当天要出货的产品提前通知品质人员前去检验,避免发生漏检,或者延误发货时间。
5.工作流程
5.1
→
→
Y
→
→
↑Y ↓N ↓
←
N
←
N
←
↓Y ↓Y
Y
→
↓
N
→
5.2检验作业流程图(如下):
6.相关文件
根据ISO 2768-m 标准进行判定是否合格
材质、数量 确认
Y → 抽样 → 尺寸 检查 ↑Y ╲N ↘ ╱ ↙ N ↓Y 接收待检品及
图纸
→ 待检品与图纸一致确认
N → 联络 作业员 确认 N ← 手动试 装配确认 ↑Y ↓Y ╱ ↙ N ↖ N ╲
返工 全检 ← 全数 退回 ↓Y 外观 检查 ↖ N ╲ ↓N 主管或技术 担当判定
↓Y ╲Y ↘ 报废 半成品 继续流动 检查表单 记录
←
成品 入库
抽检方式以AQL标准进行抽检
7.检验要求及方法
7.1被测品与其对应图纸比对确认其各加工工序是否全部完成,有无漏序;
7.2 材质、数量确认依照图纸标注确认;
7.3尺寸确认:
a.被测品本体长、宽(高)、厚是否一致;
b.图纸标注公差要求的先行检查;其次检查一般公差尺寸。
7.4手动试装配确认:
a.螺纹、螺母确认:使用所对应配套型号螺母、螺纹手动试装配确认;
b.柱状尺寸确认:通常图纸公差要求负公差场合时,使用对应尺寸轴承手动试装配确认;
C.凹状尺寸确认:通常图纸公差要求正公差场合时,使用对应尺寸轴承手动试装配确认。
7.5表面粗糙度(光洁度)检查:
a.图纸标注时,依照所要求使用样块比较法进行检查;
样块比较法:
以样块工作面的表面粗糙度为标准,仅凭触觉(如手摸)或视觉(可借助放大镜,比较显微镜等)于待检查的工件表面进行比对,从而判别被检查表面粗糙度是否合乎要求。
在进行比较时所选用样块和被检查工件的加工方法必须相同,同时样块的材料、形状、表秒你色泽等应尽可能的与被检查工件一致。
判断的准则是根据工件加工痕迹的深浅来决定表面粗糙度是否符合图纸要求。
当被检查工件表面的加工痕迹深浅程度相当于或者小于样块工作面加工痕迹深度时,则被检查工件表面粗糙度一般不大于样块的标记公称值。
b.图纸未标注时依照《产品表面检验规范》,依照所要求使用样块比较法进行检查。
7.6倒角、倒圆角:依照图纸要求检查,焊接用预留焊接孔除外,但表面确保光滑平整。
8修改履历。