新型液力反馈无油管采油工艺技术研究
一种新型的自动换向封闭液驱无杆采油系统

科技视界糊创新一种新型的自动换向封闭液驱无杆采油系统宋丕刘[1]任鹏昊[1]宋延文[1](山东威马泵业股份有限公司,山东莱芜271100)【摘要】常规有杆抽油设备安装工作量大、占地面积大,抽油杆在运行过程中会出现杆管偏磨的问题,长时间运行后,盘根、皮带等配件也会出现磨损,后期维护费用高,同时也会造成原油泄漏,污染环境。
基于这一技术难题根据液压原理研发了一种新型的自动换向封闭液驱无杆采油系统,避免了杆管偏磨,井口漏油等问题,尤其适用于斜井。
从地面液压控制系统、液压动力传输系统、井下抽油系统介绍了系统的结构组成,并分析了工作流程。
现场试验平稳无故障运行超过24个月,表明本系统可以满足油田生产需求,已经达到小批量规模。
【关键词】无杆液压驱动;液压超远程控制技术;封闭式;采油;偏磨0引言在石油工业,传统的米油设备主要是有杆抽油菜,通过地面驱动装置推拉抽油杆从而带动抽油泵进行往复运动,达到把原油从井底举升到地面的目的。
[2]此类举升设备,地面驱动装置主要有游梁式抽油机、皮带式抽油机和塔式抽油机,这种地面驱动装置存在的最大弊端是:安装过程中工作量大、占地面积也大,抽油杆在以后的运行过程中也会出现杆管偏磨的问题,长时间运行后,盘根、皮带等配件会出现磨损,后期维护费用高,同时也会造成原油泄漏,污染环境。
通过检索可知,为了克服以上技术的不足,目前有多种关于无杆采油装置的报道,包括水力活塞泵[3]、电动潜油泵、液力杆泵等,其中院水力活塞泵结构复杂、换向系统置于井眼内,高冲次、短冲程、短密封运行,可靠性差,而 且工作液和产出液在井下混合、地面需要设立工作液和产出液的分离设备,投资大、成本高、维修率高;电 动潜油泵供液不稳定、故障率高、电缆下井易损坏、适 应性差、寿命短;液力杆泵是把水力活塞泵的转向控制部分从井下移到井上,从而简化了井下部分的结构,采用了双管并行油路,地面设液压工作站,井下泵不设转向机构,其转向机构由地面控制设备控制,但 不能实现自动密封转换。
无油管采油技术及其应用_杜习广

有杆采油技术是目前油田的主要采油方式,它采用油管、抽油杆做为配套管柱。
由于液柱的冲击以及负荷的变化,管柱在抽油过程中会发生弹性伸缩,从而造成冲程损失,降低了泵效,而且由于用油管作为出油管道,由于井下腐蚀,管、杆的摩擦,经常出现油管漏失现象,严重影响了油井的正常生产。
特别是近年来因成本紧张,原材料涨价,油管投入严重不足,使这一矛盾更加突出。
为此本文开展了无油管采油技术的研究,通过在PC油田应用,取得了较好的效果,平均泵效提高了25%以上。
无油管抽油技术是用空心杆代替油管和实心抽油杆,将泵筒直接悬挂在套管上,用空心杆带动柱塞完成整个抽油过程,配套管柱组成从下到上依次为:丝堵,φ73mm沉砂管1根,φ73mm筛管2根,φ73mm尾管1根,下止转器,抽油泵,上止转器,φ89mm管2根,悬挂器,柱塞,拉杆,拨动轴,空心杆。
基本原理是用空心杆与卸掉出油凡尔罩的抽油泵柱塞连接,柱塞上部适当位置接有座封悬挂器的拨动轴,抽油泵悬挂器与泵筒连接,泵筒上下都装有防转扶正器便于座封,旋转空心杆时保持泵和悬挂器弹性卡瓦不随空心杆旋转,为防止空心杆在抽油时弯曲和偏磨,空心杆上装有扶正器。
该套管杆下井时,把拨动轴通过悬挂器内部轨道引入悬挂器内,由于拨动轴的拨叉只有正确的旋转方能从悬挂器中引出,因此在正常下井过程中,拨动器不能从悬挂器中脱出,这样就达到了空心杆带动悬挂器和泵筒下井的目的,当下至泵挂深度时,旋转空心杆一定圈数,这时装在空心杆上的拨动轴就会带动悬挂器的座封装置座封,使弹性卡瓦撑开,慢慢下放杆柱,当遇到套管节箍时,卡瓦就在该处,然后调整防冲距。
上冲程时,抽油机带动空心杆和柱塞上行固定凡尔打开,游动凡尔关闭,原油充满泵筒;下冲程时,固定凡尔关闭,游动凡尔打开,原油通过光杆,由光杆上的高压软管流入地面管线。
(1)常规抽油机井,且井斜小上部无套变,不能用于偏心井口。
(2)泵挂在800~1300m,油井日产液量在70t以下,含水量蜡量小于2%~3%。
液力反馈空心杆采油技术的应用

环境 ,无法形成 自锁 。在上行时 ,泵筒外壁所受压力高于内壁压力 , 泵筒 向里压缩 , 间隙变小 ,i,规泵在上行时 ,泵筒内壁所受压力高 t ̄ i- i 于外壁压力 ,泵筒向外扩张 ,间隙变大 ,故空心杆抽油泵较常规 泵间 隙漏 失小 ,具有高效工 作周期 长和高泵效 的特点 ;经刮砂 结构 的运 用 ,使得抽油泵具有刮砂和 自冲洗特性 ,不会造成砂卡柱塞。因此 , 空心杆抽油泵具有较好的防砂卡、防砂磨性能,配合携砂性能较好的 空心抽 浊杆,应用于 出砂油井 ,能有效延长油井的生产周期 ,提高空
空心杆 采油技术是对常规有杆泵采油方法的改进 .省去机械举升 中的油管 ,采用高强度空心杆代替实心油杆作 为抽油机 的传动介质 ,
同时又作为出油通道完成采油的一项技术 。该技术 的运用 ,使得抽油 泵柱塞的有效冲程加长 ,无液柱回压漏失 ,可延长泵的工作周期 ,降 低作业 成本 , 而且空 心杆 临界压 载大 、 弯模量大 ,增加了杆柱抗失 抗 稳的能力 ,有效地改善 了抽 油杆柱 在井下的力学状态 ,防止抽油杆柱 在井下发 生偏磨 ,从而延 长抽 油杆柱 的使用寿 命 ,延长 油井 的免 修 期。针对常 规空心杆 采油存在的下行困难问题 ,泵效低 、锚定器作业 步骤繁琐等问题开 发了液力反馈 空心杆采油技术 ,它 采用上行排液 、
杆下行困难的问题。 ( )防砂 减磨技 术的运 用 ,有效提高泵效 ,延长使用寿 命。空 2
液 力反馈空心杆采油技术 主要 由井 口分流技术和井下采油技术两 部分组成 。井 口分流技术主要 由井 口密封 泵和 配套油管柱组成 ;井下 采油技 术主要 由空 心抽 油杆 、空心 杆扶 正器 、悬 挂器 、空心杆 抽油 泵 、止转扶正器等组 成。
在上冲程 中,用于空心杆采油的常规型抽油泵工作 时,固定阀打 开 ,游动阀关闭 ,空心杆与液体不存在相 对运动 ;而液力反馈 型空心 杆抽油泵在上冲程 中排油阀打开 ,进油阀关闭 ,空心杆 与排出液体存 在相对运动 。 以 ,液力反 馈型抽油泵 比常规型抽油泵 多增加 了抽油 所 机的上行载荷。 在下 冲程 中,用 于空心杆采 油的常规型 抽油泵 的固定 阀关 闭 ,
油井偏磨机理的分析与治理

会产生一个力,将抽油杆推向油管壁产生偏磨 。
1 . 4井液 腐蚀 的影 响
随着油 田综合含水的不 断升 高,矿化度较高 ,管杆腐蚀较 严重 ,偏磨磨损将增大腐蚀速度 ,管杆腐蚀反之也加剧了管杆
磨 损速 度 。 1 . 5套 损 、套 变影 响
常 规型无管 采油工艺采用去掉柱塞上游动凡尔 的普通抽油 泵 ,下行排 液 ,并受到空心杆流通面积的影响,存在下行困难
在上冲程 ,抽油机对抽油杆 做功 ,抽 油杆处于受拉状态 , 磨损主要 是管柱 的作用 。在下冲程 ,抽油杆对抽油机做功 ,由 于受 到井 液的阻尼作用及柱塞与泵筒的半 干摩擦阻力等因素影 响 ,相 当一部分抽油杆滞后于炉头的运动速度 ,容易产生弯曲 变形和横 向变形 ,导致变形的抽油杆 与油管发生接触抹茶偏磨
( 1 )抽油 杆扶 正 器
阻力 、惯 性力和摩擦力等多种载荷作用 ,随着井斜 角的增大 ,
各种力的轴向分量 减少而径 向分量增大 ,造成 油管和抽油杆的 偏磨 。
1 . 2生 产参数 的影响
扶正器具有较好 的扶 正效果 ,从而防止抽油杆柱弯曲后杆
管发生摩擦磨损 ,由滚动摩擦 代替滑动摩擦 ,有效地减小抽 油 机负荷。 ( 2)油管旋转器
粒 ,还会使切应力的力矩得到 加强 ,使金属表面磨损腐 蚀更加
严重 。 2 偏 磨 治理 方 法 2 . 1 有 杆 泵 防偏磨 配 套技 术
1 . 1受 井身 结构 影 响
油井 的井身结构都不是垂直的 ,有杆 泵采油系统是在倾斜 的状 态下工作 ,抽油杆受液柱重量 、杆柱 自身重量 、液体粘滞
为偏磨 ,抽油机井管杆 偏磨严重一直是造成油井倒 井频繁 、免 修期短 、维护作业工作 量大 的一个重要因素 ,也很 大程度上制 约着油田管理水平和开发效益的提高。
油田的机械采油工艺技术探析
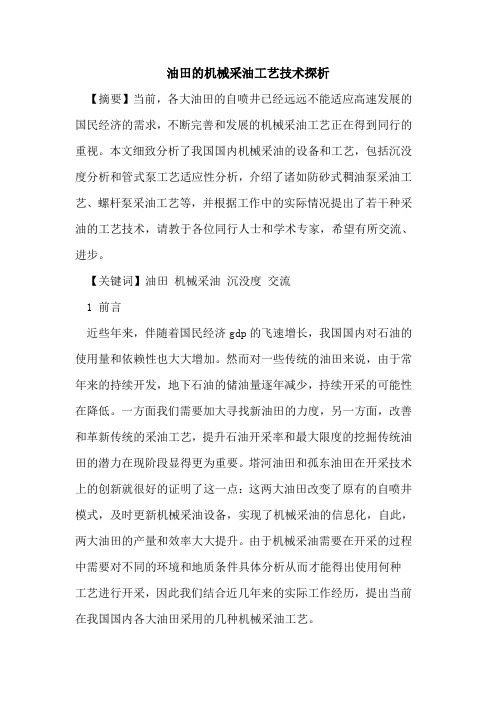
油田的机械采油工艺技术探析【摘要】当前,各大油田的自喷井已经远远不能适应高速发展的国民经济的需求,不断完善和发展的机械采油工艺正在得到同行的重视。
本文细致分析了我国国内机械采油的设备和工艺,包括沉没度分析和管式泵工艺适应性分析,介绍了诸如防砂式稠油泵采油工艺、螺杆泵采油工艺等,并根据工作中的实际情况提出了若干种采油的工艺技术,请教于各位同行人士和学术专家,希望有所交流、进步。
【关键词】油田机械采油沉没度交流1 前言近些年来,伴随着国民经济gdp的飞速增长,我国国内对石油的使用量和依赖性也大大增加。
然而对一些传统的油田来说,由于常年来的持续开发,地下石油的储油量逐年减少,持续开采的可能性在降低。
一方面我们需要加大寻找新油田的力度,另一方面,改善和革新传统的采油工艺,提升石油开采率和最大限度的挖掘传统油田的潜力在现阶段显得更为重要。
塔河油田和孤东油田在开采技术上的创新就很好的证明了这一点:这两大油田改变了原有的自喷井模式,及时更新机械采油设备,实现了机械采油的信息化,自此,两大油田的产量和效率大大提升。
由于机械采油需要在开采的过程中需要对不同的环境和地质条件具体分析从而才能得出使用何种工艺进行开采,因此我们结合近几年来的实际工作经历,提出当前在我国国内各大油田采用的几种机械采油工艺。
2 石油开采中常见的工艺技术2.1 抽油泵效的分析从技术层面上分析,电泵井泵效的最合理状态为80%~120%这一区间,如我国当前油田中泵效在80%以上的总共有51口油井,它们的平均泵效均已达到了102%.,如果泵效低于30%则被认为过于偏低。
泵效偏低的缘由多种多样,可能是油井的供液不足,还可能因为抽油泵的工作参数选择不当造成,或是原油粘度较差所致。
但根据实际工作经验来看,泵排量的选择不正确是普遍的原因,平均沉没度高达1357m 以上,并且平均泵效也应达到102.0%,地层能量才能充足,供液能力才会强。
当前我国有10口油泵泵效低于30%,它们的泵效偏低也多是有以上提到的原因造成的,因此在工作时要特别注意[1]。
一种新型无杆液力活塞抽油泵的研制
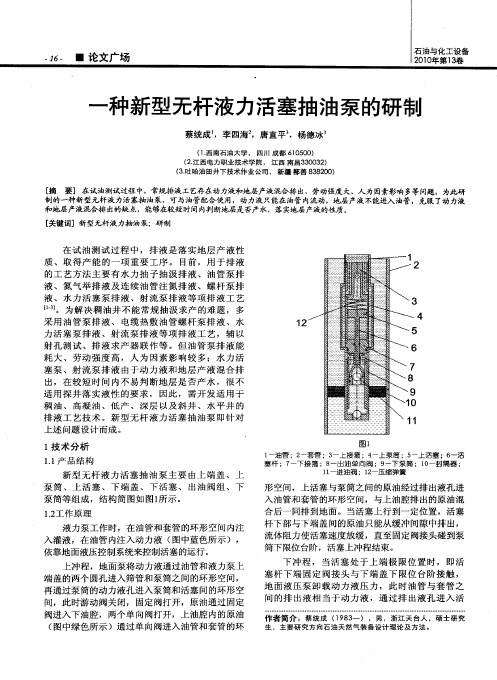
[ 要] 在试油测试过程 中,常规排液工艺存在动力液和地层产 液混合排 出、劳动强度 大、人 为因素影响多等问题 ,为此研 摘 制的一种新型无杆液力活塞抽 油泵,可与油管配合使 用,动力液只能在 油管 内流动 ,地层产液不能进入 油管 ,克服 了动 力液 和地层产液混合排 出的缺点,能够在较短 时间内判 断地层是 否产水,落实地层产液的性质 。
[ 关键词]新型无杆 液力抽油泵;研制
在 试 油 测试 过 程 中 ,排 液 是 落 实 地 层产 液 性 质 、取 得 产 能 的一 项 重 要 工 序 。 目前 ,用 于排 液 的工 艺 方 法 主 要 有 水 力 抽 子 抽 汲 排 液 、 油 管泵 排 液 、氮 气 举 排 液 及 连 续 油 管 注 氮 排 液 、 螺杆 泵 排 液 、水 力 活 塞 泵 排 液 、射 流 泵 排 液 等 项 排液 工 艺 u。】 为 解 决 稠 油井 不 能 常 规 抽汲 求 产 的难 题 , 多 采 用 油 管 泵 排 液 、 电缆 热 敷 油 管 螺 杆 泵排 液 、水 力 活 塞 泵 排 液 、射 流 泵 排 液 等 项 排 液 工 艺 ,辅 以 射 孔 测 试 、排 液 求 产 器 联 作 等 。但 油 管泵 排 液 能 耗 大 、劳 动 强 度 高 ,人 为 因素 影 响 较 多 ;水 力 活 塞 泵 、射 流 泵 排 液 由于 动 力 液和 地 层产 液 混 合 排 出 ,在 较 短 时 间 内不 易 判 断 地 层 是 否产 水 ,很 不 适 用 探 井 落 实 液 性 的 要 求 ,因 此 , 需 开发 适 用 于 稠 油 、高 凝 油 、低 产 、深 层 以及 斜 井 、水 平 井 的 排 液 工 艺 技 术 。新 型 无 杆 液 力 活 塞 抽 油泵 即针 对 上述 问题设 计而 成 。
降低油田晚期开采成本新方法——无油管杆式泵套管举液装置的应用效果

矿 场试 验
HY .a e T 油气 管 理 局 在 7 H h PI T 3 9 和9 1 号2 2 a 0 口井 中安装了上述 的无 l
管) 和停产井 ;很难或不能用 油管 下放
规定尺寸泵 的小径井 ( 井和 大修后套 新
管 内补 贴的井 )。
采出液通过孔眼l 进入尾管9 的上部 ,封
通常 ,粘 液在 圆管 中流 动 时 ,压
头损失根据 下列公 式确定 :
h:一 / 6 . 4/
一
隔器8 的轴 向槽 ,再 通过部件 7 的孔 眼3
简化使 用方案
研 究 了几 种 无 油管 杆 式泵 装 置 的 使用方案 ,并通过 由俄罗斯技术监督代
流入 封隔器上部的井 筒。安装在井底的 装 置卸载 时通过 部件7 闭 ,封隔器 隔 关
开 了井筒 内的上下 空间 。通过部件 7 的
L
一
一
P
d
2 动 力 粘 度 , P为 液体 密度 ,L 油管 长度 ,d 为 为油 管直径 , 为液流速 度 ,g 自由 为 落体加速度 。 由公式 ( 1)可见 ,在驱 动方式 、 杆式泵排液量和采 出液特性不变 的条件 下 ,影响杆式泵地下部分液压摩 阻的主 要因素是 :举液管 的液流通过面 积 ;杆 和液体的流动速度 ;液流 的有效粘度 。 因此 ,为 降 低粘 滞 摩擦 力 对 泵装 置 的 负 面影 响 ,液 流 的有效 粘 度 、举 液 管中的杆 和液流的流动速度应该尽可 能低 ,举 液管的通过面积尽可能大 。在
表参 加 的验 收 ,取 得 了 C 3 TAH P 的 P P C0 — 4 4 0 3 3 6号许可证 。这 些方案为 :将泵通过锚定装置锚定在套 管上 ;将泵通过封隔器锚定在套管上 ; 将泵下放至井底或通过 自 封封隔器将其
新型节能稠油无杆采油工艺试验与应用

孟晓春等:新型节能稠油无杆采油工艺试验与应用第9卷第2期(2019-02)大港油田稠油油藏动用地质储量占总储量的30%,主体分布在枣园、王官屯、羊三木、刘官庄等区块;原油黏度高,50℃条件下地面原油黏度为200~16800mPa·s,井筒流动性差,油藏整装程度低,无法配套蒸汽驱、火烧油层等热采开发技术,需配套电加热、井筒掺水、加药等降黏措施辅助生产;开采能耗大,抽油机配套电加热工艺,单井年运行能耗费用高达30万元;一次性投入及维护成本高,较抽油机有杆泵一次性投入增加25万元,井筒掺水、加药投入增加7万元。
因此,高黏稠油油藏面临降投入和降运行成本的技术需求[1]。
电动潜油螺杆泵举升工艺具有系统效率高、直驱无减速装置、无杆采油等工艺优点,同时螺杆泵利用挤压增压方式,剪切作用小,适合发展稠油冷采举升工艺。
大港油田首先开展了电动潜油螺杆泵新型无杆泵举升工艺配套研究试验,为大港油田稠油区块效益开发和大斜度井的工艺配套提供了有效技术途径。
1工艺原理及适用条件1.1工艺原理电动潜油螺杆泵采油系统是将潜油电动机置于井下机组的底端,通过保护器、联轴器组件与螺杆泵的转子下端直接连接,利用电缆将电力传送至井下潜油电动机,电动机通过转子输出扭矩驱动螺杆泵运转,将井液举升到地面。
电动潜油螺杆泵井筒配套主要由螺杆泵、联轴器、保护器、永磁同步电动机、测温测压装置等组成[2](图1)。
图1电动潜油螺杆泵管柱1.2工艺特点1)井筒机组配套:低转速大扭矩永磁同步电动机+保护器+联轴器+PCM螺杆泵+智能测温测压装置。
2)地面控制系统配套:智能启停及保护+运行监测及智能控制+数据远传及诊断系统。
3)相比于贝克休斯潜油螺杆泵,应用了10级永磁同步电动机,配套变频控制,转速降为80~新型节能稠油无杆采油工艺试验与应用孟晓春1韩歧清2韩涛2陈锐2(1.大港油田公司第二采油厂;2.大港油田公司采油工艺研究院)摘要:大港油田稠油油藏动用地质储量占比大,原油黏度高,开采能耗大,油藏整装程度低,无法配套蒸汽驱、火烧油层等热采开发技术。
采油工程新技术探索

采油工程新技术探索随着采油技术的发展,越来越多的新技术被引入到现代采油工程中。
这些新技术既可以提高采油效率,又可以降低生产成本,同时也能保护环境和提高安全性。
本文将介绍一些最新的采油技术,包括水力压裂、超声波技术、脉冲式喷气装置等。
水力压裂技术是一种常用的油藏改造技术,在油井中注入高压高能的液体,以破碎油藏岩石并加大储层有效透气性。
通过水力压裂技术,可以提高油井的产能以及生产收益。
水力压裂技术也可以用来改善非常致密的岩石,以改进抽油机的效率。
超声波技术是一个新兴的采油技术,其应用十分广泛。
在超声波采油中,通过应用高频声波,可以引起油藏岩石中的微小振动,以此增加储层透气性和产能。
此外,还可以利用超声波技术来促进储层油的提取和流动。
与水力压裂技术相比,超声波技术更具有针对性和可控性,可以更好地适应不同的油藏类型。
脉冲式喷气装置是一种新型油井清洗装置,可以通过产生超声波来解决难以清洗的问题。
脉冲式喷气装置不仅可以清洗油井,还可以通过改变波形来改进储层透气性。
通过这种装置,可以在不使用化学物质的情况下清洗油井,降低环境污染。
除了这些技术,还有许多其他新的采油技术,如新型材料的使用、电磁加热技术、内突破技术等,它们都有着广泛的应用前景。
这些技术的出现为采油工程的发展提供了更多的选择和可能性,同时也为当前的能源危机提供了解决方案。
在今后的采油工程中,这些技术将会得到更广泛的应用,以满足不断增长的能源需求。
总之,随着新科技的涌现,油藏开发技术也在不断发展。
新技术的应用不仅提高了采油效率和现代采油工程的水平,还为应对当前能源危机提供了新思路和解决方案。
因此,在采油工程中,应不断探索和引进新技术,推动采油技术不断发展和创新。
解决油井偏磨问题---液力驱动无杆采油设备

三、MBS液力采油泵技术简介
工作原理 上行程:中心管打入高压动力液,进入上 行泵筒内腔,上行泵筒上行,带动小柱塞、 上出油阀、小泵筒、大柱塞、下出油阀、大 泵筒上行,液压腔A被压缩,压力上升,此时 下出油阀关闭,A腔产液进入B腔,克服产液 柱的压力,顶开上出油阀,进入油管。
5 6
下行程:地面动力液压力降低,由于 产液液柱和油套环空液柱的压差作用,形成 液力反馈力,上出油阀关闭。在液力反馈力 的作用下,上行泵筒、上行柱塞、小柱塞、 上出油阀、小泵筒、大柱塞、下出油阀、大 泵筒下行,上行泵筒内的乏动力液压回地面 存储罐。同时,A腔体积增大,吸入B腔产液, B腔压力降低,吸入泵外产液。
悬挂抽油泵参数: CYB(Φ 32-Φ83)×(3-5)液力反馈泵 说明: 以上液力采油装置部分参数,对于国内不同的井况, 需对设计参数进行不同的调整; 动力液在地面加压,加压方式有多种,如油田注水管 网里的高压污水、专用活塞泵装置、抽油机带动井口往复泵 等,以上介绍为地面撬装站方式。
四、特点
1、地面动力液驱动井下动力缸,带动抽油泵柱塞,实现采油过程。 没有抽油杆上下运动,不存在杆管磨损问题。 2、由于产液液柱、动力液液柱 相互平衡,系统负载只有面积为 泵径、高度为动液面深度的液柱,比有杆采油设备少抽油杆重量载 荷。 3、利用有限的自循环水基溶液传递液压驱动的动力,简化了地 面设备和流程,地面设备完全实现撬装化,结构简单紧凑,易于管 理、运输和维护; 4、由于没有抽油杆伸缩引起的冲程损失,与有杆采油设备相比, 泵效高。 5、适用范围广,包括水平井、稠油井、结构复杂井、高含气井。 6、使用寿命长于其他水力采油设备。
23.29
27.15 29.48 38.9
3.35
3.91 4.25 5.6
N80-1非调质无缝油井管工艺控制技术的研究的开题报告
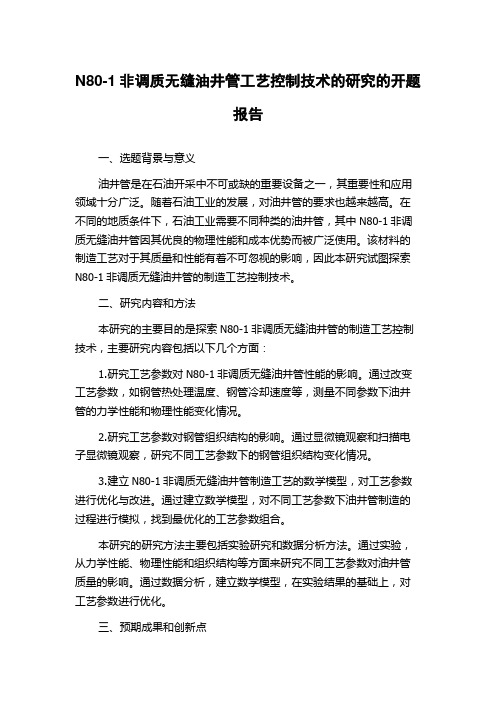
N80-1非调质无缝油井管工艺控制技术的研究的开题报告一、选题背景与意义油井管是在石油开采中不可或缺的重要设备之一,其重要性和应用领域十分广泛。
随着石油工业的发展,对油井管的要求也越来越高。
在不同的地质条件下,石油工业需要不同种类的油井管,其中N80-1非调质无缝油井管因其优良的物理性能和成本优势而被广泛使用。
该材料的制造工艺对于其质量和性能有着不可忽视的影响,因此本研究试图探索N80-1非调质无缝油井管的制造工艺控制技术。
二、研究内容和方法本研究的主要目的是探索N80-1非调质无缝油井管的制造工艺控制技术,主要研究内容包括以下几个方面:1.研究工艺参数对N80-1非调质无缝油井管性能的影响。
通过改变工艺参数,如钢管热处理温度、钢管冷却速度等,测量不同参数下油井管的力学性能和物理性能变化情况。
2.研究工艺参数对钢管组织结构的影响。
通过显微镜观察和扫描电子显微镜观察,研究不同工艺参数下的钢管组织结构变化情况。
3.建立N80-1非调质无缝油井管制造工艺的数学模型,对工艺参数进行优化与改进。
通过建立数学模型,对不同工艺参数下油井管制造的过程进行模拟,找到最优化的工艺参数组合。
本研究的研究方法主要包括实验研究和数据分析方法。
通过实验,从力学性能、物理性能和组织结构等方面来研究不同工艺参数对油井管质量的影响。
通过数据分析,建立数学模型,在实验结果的基础上,对工艺参数进行优化。
三、预期成果和创新点通过对N80-1非调质无缝油井管的制造工艺控制技术进行研究,本研究的预期成果包括以下几个方面:1.确定N80-1非调质无缝油井管制造工艺的优化方案。
通过实验和数学模型分析,找到最优化的工艺参数组合,提高产品质量和工艺效率。
2.深入探究不同工艺参数对钢管组织结构的影响。
通过显微镜观察和扫描电子显微镜观察,深入了解不同工艺参数对钢管组织结构影响的机理和规律。
3.为石油工业提供高质量、高效率的N80-1非调质无缝油井管。
液力反馈无油管采油技术

液力反馈无油管采油技术
罗燕;张雷;孙衍东;姜东;徐建礼;张俊清;赵刚;解立春;赵金玲
【期刊名称】《石油机械》
【年(卷),期】2007(35)1
【摘要】针对常规无油管采油技术存在的一系列问题,提出了液力反馈无油管采油技术.该技术将液力反馈原理应用到设计中,增加了杆柱下行动力,有效地解决了杆柱下行困难问题.该技术主要由井口分流技术和井下采油技术2部分组成,运用井口分流技术可直接对常规井口进行无油管采油.井下采油技术主要由空心抽油杆、空心杆扶正器、悬挂器、无油管抽油泵、防转器组成,其中无油管抽油泵和悬挂器是该技术的关键部件.现场应用表明,该技术在偏磨油井中使用,平均可延长生产周期3~6个月,平均提高泵效5%~8%,防偏磨效果明显.
【总页数】3页(P42-44)
【作者】罗燕;张雷;孙衍东;姜东;徐建礼;张俊清;赵刚;解立春;赵金玲
【作者单位】胜利油田有限公司采油工艺研究院;胜利油田有限公司采油工艺研究院;胜利油田有限公司采油工艺研究院;胜利油田有限公司采油工艺研究院;胜利油田有限公司采油工艺研究院;胜利油田有限公司采油工艺研究院;胜利油田有限公司桩西采油厂;长庆油田分公司第一采油厂;长庆油田分公司第一采油厂
【正文语种】中文
【中图分类】TE9
【相关文献】
1.液力反馈空心杆采油技术的应用 [J], 杨苹;赵玉泉;向明光
2.液力反馈空心杆采油技术 [J], 金海峰
3.液力反馈泵无油管采油工艺杆柱力学分析 [J], 冯国强;韩岐清;滕国权;李少甫;冯国勇
4.小套管井无油管采油技术的研究与应用 [J], 董元军;郑振兴;孟凡晶;古光明;孙渊平
5.液力反馈空心杆采油技术研究与应用 [J], 卜文胜;方绍燕
因版权原因,仅展示原文概要,查看原文内容请购买。
采油工艺技术创新研究祖里甫卡尔·阿不来提何青加力肯·达吾列提别克张浩

采油工艺技术创新研究祖里甫卡尔·阿不来提何青加力肯·达吾列提别克张浩发布时间:2023-06-18T09:02:48.119Z 来源:《科技新时代》2023年6期作者:祖里甫卡尔·阿不来提何青加力肯·达吾列提别克张浩[导读] 原油的开采是多种产业发展的重要基础,提高其开采效率具有重要意义。
为了提高油田机械采油技术的技术水平,有必要推动相关采油工艺的不断创新和改进。
目前,机械采油技术已成为我国该领域的重点研究对象之一,需要根据油田实际情况应用相应的技术手段,促进机械采油技术效益的不断提高。
克拉玛依红山油田有限责任公司新疆克拉玛依 834000摘要:原油的开采是多种产业发展的重要基础,提高其开采效率具有重要意义。
为了提高油田机械采油技术的技术水平,有必要推动相关采油工艺的不断创新和改进。
目前,机械采油技术已成为我国该领域的重点研究对象之一,需要根据油田实际情况应用相应的技术手段,促进机械采油技术效益的不断提高。
关键词:采油工艺;技术创新;研究1采油技术管理的基本原则1.1 采油技术管理的技术化从我国石油生产技术管理的现状来看,技术化原则是管理中最基本、最关键的原则。
对于石油生产人员来说,他们必须熟悉各种石油生产操作技术,并能够灵活地将其应用于工作中。
同时,还要求相应的技术和管理人员具备良好的技能基础,以便在采油工作实施过程中应对各种突发情况,并根据实际情况采取科学合理的采油措施,以保证采油工程技术的科学合理应用。
1.2采油技术管理制度化采油技术的管理是一项极其复杂的工程,技术应用中的任何错误都会对最终的采油质量和效果产生非常不利的影响。
因此,为了更好地保证采油工程技术的作用,有必要根据我国油田开采现状和采油技术的各种管理要求,开发一套全面的采油技术管理系统,以实现采油技术的高效管理。
只有这样,才能全面保证采油工作各方面的有序开展。
2石油采油工程技术存在的不足2.1 采油过程中存在的不足在实施采油时,通常可以分为三个不同的阶段,即初级采油阶段。
无管采油新技术及其应用
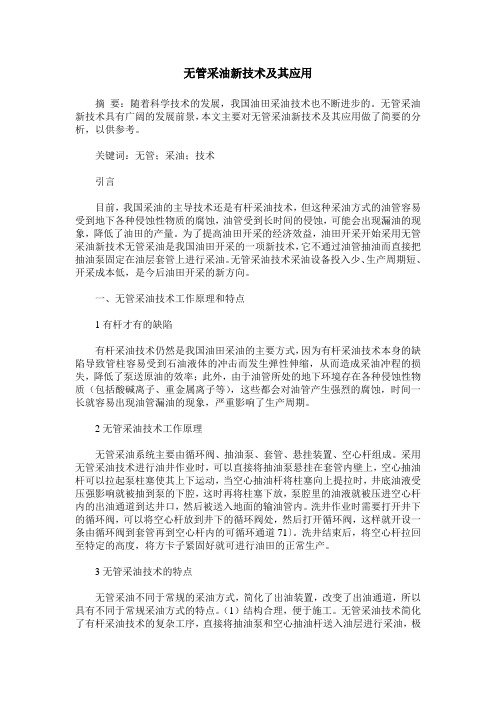
无管采油新技术及其应用摘要:随着科学技术的发展,我国油田采油技术也不断进步的。
无管采油新技术具有广阔的发展前景,本文主要对无管采油新技术及其应用做了简要的分析,以供参考。
关键词:无管;采油;技术引言目前,我国采油的主导技术还是有杆采油技术,但这种采油方式的油管容易受到地下各种侵蚀性物质的腐蚀,油管受到长时间的侵蚀,可能会出现漏油的现象,降低了油田的产量。
为了提高油田开采的经济效益,油田开采开始采用无管采油新技术无管采油是我国油田开采的一项新技术,它不通过油管抽油而直接把抽油泵固定在油层套管上进行采油。
无管采油技术采油设备投入少、生产周期短、开采成本低,是今后油田开采的新方向。
一、无管采油技术工作原理和特点1有杆才有的缺陷有杆采油技术仍然是我国油田采油的主要方式,因为有杆采油技术本身的缺陷导致管柱容易受到石油液体的冲击而发生弹性伸缩,从而造成采油冲程的损失,降低了泵送原油的效率;此外,由于油管所处的地下环境存在各种侵蚀性物质(包括酸碱离子、重金属离子等),这些都会对油管产生强烈的腐蚀,时间一长就容易出现油管漏油的现象,严重影响了生产周期。
2无管采油技术工作原理无管采油系统主要由循环阀、抽油泵、套管、悬挂装置、空心杆组成。
采用无管采油技术进行油井作业时,可以直接将抽油泵悬挂在套管内壁上,空心抽油杆可以拉起泵柱塞使其上下运动,当空心抽油杆将柱塞向上提拉时,井底油液受压强影响就被抽到泵的下腔,这时再将柱塞下放,泵腔里的油液就被压进空心杆内的出油通道到达井口,然后被送入地面的输油管内。
洗井作业时需要打开井下的循环阀,可以将空心杆放到井下的循环阀处,然后打开循环阀,这样就开设一条由循环阀到套管再到空心杆内的可循环通道71〕。
洗井结束后,将空心杆拉回至特定的高度,将方卡子紧固好就可进行油田的正常生产。
3无管采油技术的特点无管采油不同于常规的采油方式,简化了出油装置,改变了出油通道,所以具有不同于常规采油方式的特点。
液力反馈型空心杆采油技术的设计研究的开题报告

液力反馈型空心杆采油技术的设计研究的开题报告一、研究背景石油资源作为能源供应的主要来源之一,对于世界的经济发展起着至关重要的作用。
然而,石油的开采难度极大,尤其是在获得传统的储量之后,有必要对非常规油藏进行开发。
目前在油田开发领域中,空心杆采油技术已经被广泛采用。
但是,随着井深度的增加和粘度的提高,空心杆采油技术存在着很大的缺陷,如容易出现卡杆、破裂等问题,旋转平衡性差,导致了无法有效地提高采油效率,降低生产成本的问题。
本研究的设计目的是探究一种新型液力反馈型空心杆采油技术,该技术采用液力反馈系统来解决上述问题,目的是提高采油效率和降低生产成本。
二、研究目标本研究的主要目标是:1. 设计一种液力反馈型空心杆采油技术原型;2. 实现原型的制造和试验,并获取试验数据;3. 对试验结果进行分析和评价。
三、研究内容本研究的内容主要包括以下三个方面:1. 液力反馈型空心杆采油技术的理论研究:通过对液力反馈技术的原理和应用进行深入研究,探讨其应用于空心杆采油技术的可行性和优势。
2. 液力反馈型空心杆采油技术的设计:依据理论分析和实验数据,对液力反馈型空心杆采油技术进行设计,包括设计液力反馈系统和整体结构设计。
3. 实验研究:制造设计出的液力反馈型空心杆采油技术原型进行试验,并获取试验数据,通过对试验数据进行分析和评价,评估新型液力反馈型空心杆采油技术的实用效果和经济效益。
四、研究方法本研究主要采用以下研究方法:1. 文献资料法:通过搜集和阅读文献,了解液力反馈技术和空心杆采油技术的基本原理和应用,为设计新型液力反馈型空心杆采油技术提供理论依据。
2. 理论分析法:通过对液力反馈系统、空心杆采油技术和液力反馈型空心杆采油技术的原理和运行过程进行分析,为设计提供指导和参考。
3. 实验研究法:对设计的新型液力反馈型空心杆采油技术原型进行试验,并根据试验结果对其进行分析和评价,以验证其实用效果和经济效益。
五、论文结构本论文主要分为以下几个部分:第一章:研究背景和研究目的。
液力反馈型空心杆抽油泵的设计

液力反馈型空心杆抽油泵的设计石油机械新产品开发液力反馈型空心杆抽油泵的设计姜东“黄曰成(上海交通大学机械工程学院)(胜利油田有限公司胜利采油厂)罗文莉罗燕程正全(胜利油田有限公司采油工艺研究院)装置、工作泵筒、工作柱塞、进油阀等组成。
悬点载荷分析表明,这种泵在下行程时,与常规泵相比,增加了杆柱的下行动力而减少了下行阻力,有效地解决了常规泵空心抽油杆采油工艺中空心抽油杆柱下行困难的问题,并可提高抽油泵的泵效,延长空心抽油杆的使用寿命。
液力反馈型空心杆抽油泵的应用,可改进空心抽油杆采油工艺,提高采油的整体效率,将对空心抽油杆采油工艺的推广应用起积极作用。
主题词空心杆采油抽油杆抽油泵液力反馈设计空心抽油杆采油工艺技术作为一种新工艺,由于具有节省大量油管材料费及作业费的优点,在油田已逐渐开始应用。
但是现有常规空心抽油杆采油工艺技术采用的是具有常规原理的抽油泵,工作时下行排液,受到空心抽油杆流通面积的影响,存在下行阻力大、下行困难等问题,对泵效及空心抽油杆的使用寿命产生不良影响。
为此,笔者提出一种用于空心抽油杆采油利用液力反馈原理的空心杆抽油泵,可有效解决空心抽油杆下行困难的问题。
结构特点及工作原理这种空心杆抽油泵主要由反馈长柱塞、反馈泵筒、出油阀、接箍、旋转装置、工作泵筒、工作柱塞、进油阀等组成,其结构见。
液力反馈型空心杆抽油泵有2个柱塞,上面小柱塞与下面大柱塞串联,具有液力反馈功能,增加空心抽油杆柱的下行动力,提高空心抽油杆的使用寿命,延长油井的有效生产周期。
泵的上部为长柱塞短泵筒,下部为长泵筒短柱塞,且柱塞采用等径1一反馈长柱塞;2反馈泵筒;3―出油阀;4接箍;5―旋转装置;6―工作泵筒;7―工作柱塞;8―进油阀;9一下接头刮砂柱塞结构,因此具有较好的防砂卡、防砂磨性能,配合携砂性能较好的空心抽油杆,可应用于出砂油井,能有效延长油井的生产周期,提篼空心抽油杆采油工艺在出砂油井的应用效果。
正常使用时,空心抽油杆与反馈长柱塞相连接,并由空心抽油杆将抽油泵整体送人井内。
- 1、下载文档前请自行甄别文档内容的完整性,平台不提供额外的编辑、内容补充、找答案等附加服务。
- 2、"仅部分预览"的文档,不可在线预览部分如存在完整性等问题,可反馈申请退款(可完整预览的文档不适用该条件!)。
- 3、如文档侵犯您的权益,请联系客服反馈,我们会尽快为您处理(人工客服工作时间:9:00-18:30)。
新型液力反馈无油管采油工艺技术研究
【摘要】无油管采油工艺采用直径较大的空心杆代替实心杆带泵工作,空心杆的临界压载和抗弯模量均是实心杆的3倍以上,大大地增加了杆柱抗失稳的能力。
计算结果表明,在空心杆柱上加适量的扶正器,就可以完全避免空心杆柱在井下发生受压失稳,因此该工艺具有良好的发展前景。
该工艺从根本上解决了偏磨的问题,大幅度降低油井的开采成本,延长油井的生产周期,达到油井偏磨治理的先进水平。
【关键词】液力反馈无油管采油工艺
在有杆泵采油系统中,抽油杆和油管的偏磨不仅降低抽油杆的强度,造成抽油杆断裂,而且还会磨穿油管壁,造成油管漏失,影响油井的正常生产。
为提高抽油井的生产周期,节约生产成本和提高抽油井的经济效益,有必要对管杆偏磨的治理另寻途径,开发和引进先进的防偏磨技术,提高胜利油田防偏磨技术水平。
1 无管采油工艺的发展
国外,无油管采油工艺主要分为两种,一种方式是直接由实心抽油杆联接常规泵下入井内,以套管为液流通道,这种方式因受套管密封质量及携砂能力的限制,极易造成抽油泵的砂卡、砂埋,对高含水期井液杂质较多的井况非常不适应;另一种方式是采用空心杆联接经改造的空心杆抽油泵下入井内,以空心杆内孔作为液流通道,这种方式因具有携砂能力强,不受套管密封性能的限制等特点,现已被广泛采用。
该技术在泵上接套管接箍锚定装置,用于固定泵筒,采用正转空心杆座封、反转空心杆解封的方式座封锚定装置,存在以下问题:
(1)采用普通抽油泵与之配套使用,存在下行困难问题。
(2)锚定器锚定机构的座封解封作业步骤繁琐、一次成功率低。
尤其是反向转动空心杆解封易出现空心杆的脱扣,特别是一旦柱塞发生砂卡,则不能实施旋转解封操作,有可能造成油井的大修。
(3)采用空心杆采油专用井口设备,不能利用现有常规有杆泵井口设备进行工作和管理。
井口设备复杂,不便于维护。
本项目主要针对以上的在井下生产管柱上的三点问题,开展研究工作。
同时针对具体油井的供液、含水、粘度等井况的不同,为了优选合适的泵径、泵深、管杆组合,开展了无管采油软件的研究及编制工作,用以对现场施工进行理论上的支持及指导。
2 液力反馈无油管采油工艺技术研究
针对胜利油田采油厂的油藏和生产特点,研究形成了适合于胜利油田采油厂
应用的液力反馈无油管采油工艺管柱及配套技术,该技术主要由井口分流系统和井下采油系统两部分组成,基本上解决了本项目在生产管柱上的三个难题。
经过设计研究,已完成了现场施工准备工作,达到现场实施的条件。
2.1 设计采用了新型井口分流系统
该井口分流系统主要由井口密封泵和配套油管柱组成,该系统巧妙地在井口配置一井口密封泵,通过这个密封泵将空心杆杆柱转换为有杆泵常规生产杆柱,将空心杆内的流体分流到环空内,从而可以利用现有的有杆泵生产井口设备进行无油管采油,实现了无油管采油的常规生产管理,降低生产成本。
井下采油系统主要由空心抽油杆、空心杆扶正器、悬挂器、无油管抽油泵、防转器等组成
2.2 设计使用了新型无油管液力反馈式抽油泵
该抽油泵采用大小柱塞串联的形式,一部分采用长柱塞短泵筒形式,另一部分采用长泵筒短柱塞形式,采用等径刮砂柱塞结构,具有液力反馈功能,增加了下行的动力,解决了常规无油管采油工艺存在的杆柱下行缓慢、阻力大的问题。
图1 无油管抽油泵结构示意图
工作原理:
下冲程时,大柱塞上部的泵腔体积增大,压力降低,出油阀关闭,当压力降低到小于进油阀下方的沉没压力时,进油阀打开,液体进入大柱塞上部泵腔,为进液过程;上冲程时,大柱塞上部的泵腔体积减小,压力上升,进油阀关闭,当压力升高到大于出油阀以上的液柱压力时,出油阀打开,井液进入小柱塞,顺着空心杆向上排出液体,该过程为排液过程。
这样,循环往复便完成了井液的抽汲。
从理论上,我们对常规型与液力反馈型两种无油管采油工艺中抽油机悬点最大、最小载荷进行了力学分析对比,进一步阐明了液力反馈无油管工艺是可增加下行动力的。
分析结果表明,由于液力反馈无油管工艺抽汲方式为上行排液、下行进液,与常规无油管采油工艺相比,上行程增加了两种上行阻力:一是由于液体在空心杆内流动产生的液流阻力;二是液柱压力作用于大、小柱塞截面差产生的液压力。
下行程减少了液体在空心杆内流动产生的下行液流阻力,增加了液柱作用于小柱塞产生的下行动力。
因此,新工艺能有效解决管柱下行困难的问题,提高空心杆的使用使命,延长油井的有效生产期。
2.3 改进了井下悬挂装置
采用地面旋转扩张下放锚定于套管接箍的锚定方式,释放采用直接上提管柱的方式,操作简单、可靠,整套工具防腐处理,具有较强的防腐性能,可保证长期安全工作。
工作原理:
当配套管、杆柱下入井内至预定泵挂深度时,在防转器的作用下抽油泵泵筒不转动,旋转空心抽油杆柱,带动悬挂器径向扩张撑在套管壁上,然后慢慢下放杆柱,遇到套管接箍时悬挂器继续扩张,完成锚定过程。
直接上提杆柱,悬挂器回弹复原位,脱离套管接箍,管柱随即提出,完成释放过程。
2.4 设计使用了新型防转器
为了使整个工艺更加完善,符合现场应用的条件,设计了新型防转器。
防转器的作用是使下部管柱在空心杆柱旋转时不随转,配合悬挂装置完成悬挂杆柱的目的。
结构组成:主要由锚体、锚爪、弹簧等组成
工作原理:
工具下入井内预定位置后,管柱正转,锚爪锚住套管内壁,使得与之相连的部分管柱不随转,起到锚定的作用。
管柱反转,即可释放锚定。
目前研究形成的液力反馈无油管采油工艺生产管柱整体具有如下特点:
(1)该工艺能有效解决常规无油管采油工艺存在的管柱下行困难的问题,提高空心杆的使用使命,延长油井的有效生产期;
(2)该工艺可直接采用常规井口进行无油管采油,减少了现场管理难度,提高了井口的安全可靠程度;
(3)空心杆的临界压载和抗弯模量均是实心杆的3倍,大大地增加了杆柱抗失稳的能力,而且由于空心杆与套管间间隙的增加5倍,在空心杆柱上加适量的扶正器,就可以完全避免空心杆柱在井下发生受压失稳,防偏磨效果明显;。