重轨轧疤缺陷的检查发现及解决
钢轨生产表面缺陷分析与改进

钢轨生产表面缺陷分析与改进钢轨是铁路运输中不可或缺的组成部分,它必须具备足够的强度和稳定性,以确保列车的稳定行驶和运输安全。
然而,由于生产工艺和材料质量等因素的影响,钢轨表面往往存在各种缺陷问题,这些缺陷如果不能及时处理和改进,将会对运输安全产生不良影响。
1.1 表面气泡表面气泡是在钢铁冶炼和浇铸过程中,由于杂质或气体的存在,导致钢铁表面形成的气泡。
这些气泡如果未能及时处理,就会在钢轨表面形成小孔洞,对轨面的平整度和稳定性造成不良影响。
1.2 钢印钢印是在轧制过程中,因钢轨表面与轧辊表面有微小间隙,导致钢轨表面在轧制时产生压痕的现象。
如果钢轨表面的钢印较多、较深,就会对列车的稳定性和运行速度产生影响。
1.3 裂纹裂纹是指钢轨表面存在的裂缝和裂纹,这些裂缝和裂纹的存在,会导致钢轨表面的强度和稳定性降低,影响列车的安全行驶。
1.4 氧化皮氧化皮是指由于钢轨在生产、运输和存放过程中受到空气、水蒸气等氧化作用的影响,形成的一层薄薄的红色氧化物。
这些氧化皮如果不能及时清理,就会对钢轨表面的平整度和稳定性产生负面影响。
2.1 质量控制对于钢轨生产过程中产生的各种缺陷,必须进行严格的质量控制和管理。
这包括原材料的选择、熔炼和浇铸过程的控制、轧制过程的控制等方面,以确保钢轨表面的质量达到生产标准。
2.2 表面处理钢轨表面的氧化皮、钢印等缺陷通过表面处理的方式来改善。
钢轨表面的氧化皮可以通过机械削除或采用酸洗等化学处理方法来清理;钢印可以通过磨光或抛光等加工方法来改善。
2.3 检测和修补对于钢轨表面存在的裂纹等缺陷,必须及时进行检测和修补。
通过超声波检测等方法来探测钢轨表面的裂纹,然后通过切割、焊接等方式来进行修补和加强,以确保钢轨的强度和稳定性恢复到标准值。
三、结论钢轨生产表面缺陷是影响钢轨质量和安全的重要因素。
钢轨生产企业必须加强工艺控制和质量管理,通过表面处理、检测和修补等方法来改善钢轨表面的缺陷,并确保钢轨质量符合标准。
轧制缺陷及质量控制
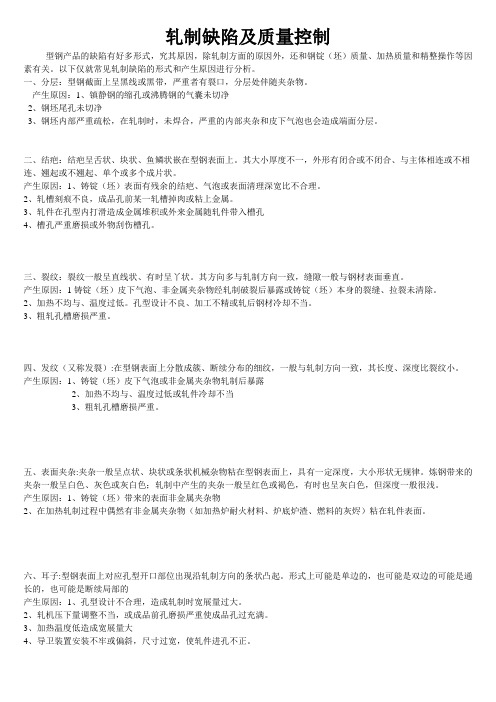
轧制缺陷及质量控制型钢产品的缺陷有好多形式,究其原因,除轧制方面的原因外,还和钢锭(坯)质量、加热质量和精整操作等因素有关。
以下仅就常见轧制缺陷的形式和产生原因进行分析。
一、分层:型钢截面上呈黑线或黑带,严重者有裂口,分层处伴随夹杂物。
产生原因:1、镇静钢的缩孔或沸腾钢的气囊未切净2、钢坯尾孔未切净3、钢坯内部严重疏松,在轧制时,未焊合,严重的内部夹杂和皮下气泡也会造成端面分层。
二、结疤:结疤呈舌状、块状、鱼鳞状嵌在型钢表面上。
其大小厚度不一,外形有闭合或不闭合、与主体相连或不相连、翘起或不翘起、单个或多个成片状。
产生原因:1、铸锭(坯)表面有残余的结疤、气泡或表面清理深宽比不合理。
2、轧槽刻痕不良,成品孔前某一轧槽掉肉或粘上金属。
3、轧件在孔型内打滑造成金属堆积或外来金属随轧件带入槽孔4、槽孔严重磨损或外物刮伤槽孔。
三、裂纹:裂纹一般呈直线状、有时呈丫状。
其方向多与轧制方向一致,缝隙一般与钢材表面垂直。
产生原因:1铸锭(坯)皮下气泡、非金属夹杂物经轧制破裂后暴露或铸锭(坯)本身的裂缝、拉裂未清除。
2、加热不均与、温度过低。
孔型设计不良、加工不精或轧后钢材冷却不当。
3、粗轧孔槽磨损严重。
四、发纹(又称发裂):在型钢表面上分散成簇、断续分布的细纹,一般与轧制方向一致,其长度、深度比裂纹小。
产生原因:1、铸锭(坯)皮下气泡或非金属夹杂物轧制后暴露2、加热不均与、温度过低或轧件冷却不当3、粗轧孔槽磨损严重。
五、表面夹杂:夹杂一般呈点状、块状或条状机械杂物粘在型钢表面上,具有一定深度,大小形状无规律。
炼钢带来的夹杂一般呈白色、灰色或灰白色;轧制中产生的夹杂一般呈红色或褐色,有时也呈灰白色,但深度一般很浅。
产生原因:1、铸锭(坯)带来的表面非金属夹杂物2、在加热轧制过程中偶然有非金属夹杂物(如加热炉耐火材料、炉底炉渣、燃料的灰烬)粘在轧件表面。
六、耳子:型钢表面上对应孔型开口部位出现沿轧制方向的条状凸起。
轧制缺陷及质量控制
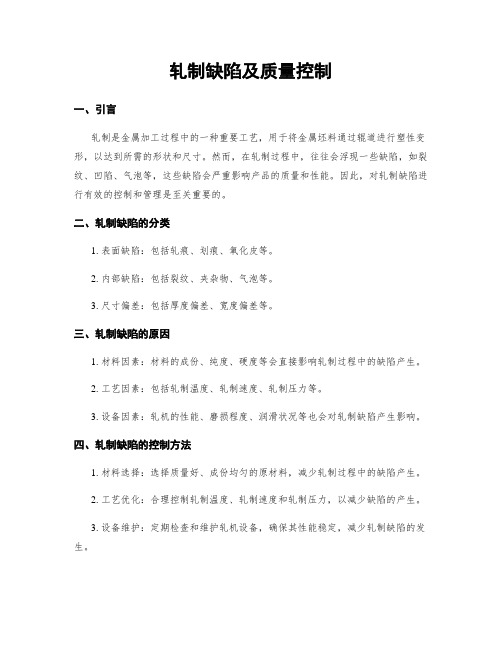
轧制缺陷及质量控制一、引言轧制是金属加工过程中的一种重要工艺,用于将金属坯料通过辊道进行塑性变形,以达到所需的形状和尺寸。
然而,在轧制过程中,往往会浮现一些缺陷,如裂纹、凹陷、气泡等,这些缺陷会严重影响产品的质量和性能。
因此,对轧制缺陷进行有效的控制和管理是至关重要的。
二、轧制缺陷的分类1. 表面缺陷:包括轧痕、划痕、氧化皮等。
2. 内部缺陷:包括裂纹、夹杂物、气泡等。
3. 尺寸偏差:包括厚度偏差、宽度偏差等。
三、轧制缺陷的原因1. 材料因素:材料的成份、纯度、硬度等会直接影响轧制过程中的缺陷产生。
2. 工艺因素:包括轧制温度、轧制速度、轧制压力等。
3. 设备因素:轧机的性能、磨损程度、润滑状况等也会对轧制缺陷产生影响。
四、轧制缺陷的控制方法1. 材料选择:选择质量好、成份均匀的原材料,减少轧制过程中的缺陷产生。
2. 工艺优化:合理控制轧制温度、轧制速度和轧制压力,以减少缺陷的产生。
3. 设备维护:定期检查和维护轧机设备,确保其性能稳定,减少轧制缺陷的发生。
4. 润滑控制:选择合适的润滑剂,保证轧制过程中的润滑效果,减少磨擦和磨损,降低缺陷产生的可能性。
五、质量控制措施1. 检测方法:采用超声波、X射线、磁粉探伤等非破坏性检测方法,及时发现和排除轧制缺陷。
2. 检测设备:使用高精度的检测设备,确保对轧制缺陷的检测准确性和可靠性。
3. 检测标准:制定严格的轧制缺陷检测标准,明确缺陷的类型、数量和尺寸要求。
4. 检测频率:根据产品的重要性和应用领域,确定合理的检测频率,确保产品质量的稳定性和可靠性。
六、案例分析以某钢铁公司为例,该公司采用了先进的轧制设备和严格的质量控制措施,成功地控制了轧制缺陷的发生。
通过优化工艺参数,选择高质量的原材料,并定期进行设备维护和润滑控制,该公司的产品质量得到了有效提升。
同时,该公司还建立了完善的质量检测体系,采用先进的检测设备和严格的检测标准,确保产品质量的稳定性和可靠性。
钢轨常见缺陷产生原因及消除方法
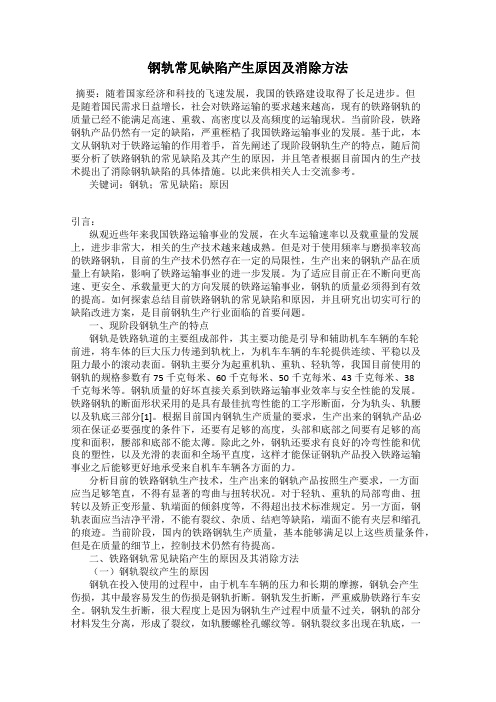
钢轨常见缺陷产生原因及消除方法摘要:随着国家经济和科技的飞速发展,我国的铁路建设取得了长足进步。
但是随着国民需求日益增长,社会对铁路运输的要求越来越高,现有的铁路钢轨的质量已经不能满足高速、重载、高密度以及高频度的运输现状。
当前阶段,铁路钢轨产品仍然有一定的缺陷,严重桎梏了我国铁路运输事业的发展。
基于此,本文从钢轨对于铁路运输的作用着手,首先阐述了现阶段钢轨生产的特点,随后简要分析了铁路钢轨的常见缺陷及其产生的原因,并且笔者根据目前国内的生产技术提出了消除钢轨缺陷的具体措施。
以此来供相关人士交流参考。
关键词:钢轨;常见缺陷;原因引言:纵观近些年来我国铁路运输事业的发展,在火车运输速率以及载重量的发展上,进步非常大,相关的生产技术越来越成熟。
但是对于使用频率与磨损率较高的铁路钢轨,目前的生产技术仍然存在一定的局限性,生产出来的钢轨产品在质量上有缺陷,影响了铁路运输事业的进一步发展。
为了适应目前正在不断向更高速、更安全、承载量更大的方向发展的铁路运输事业,钢轨的质量必须得到有效的提高。
如何探索总结目前铁路钢轨的常见缺陷和原因,并且研究出切实可行的缺陷改进方案,是目前钢轨生产行业面临的首要问题。
一、现阶段钢轨生产的特点钢轨是铁路轨道的主要组成部件,其主要功能是引导和辅助机车车辆的车轮前进,将车体的巨大压力传递到轨枕上,为机车车辆的车轮提供连续、平稳以及阻力最小的滚动表面。
钢轨主要分为起重机轨、重轨、轻轨等,我国目前使用的钢轨的规格参数有75千克每米、60千克每米、50千克每米、43千克每米、38千克每米等。
钢轨质量的好坏直接关系到铁路运输事业效率与安全性能的发展。
铁路钢轨的断面形状采用的是具有最佳抗弯性能的工字形断面,分为轨头、轨腰以及轨底三部分[1]。
根据目前国内钢轨生产质量的要求,生产出来的钢轨产品必须在保证必要强度的条件下,还要有足够的高度,头部和底部之间要有足够的高度和面积,腰部和底部不能太薄。
钢在轧制中常见的缺陷总结
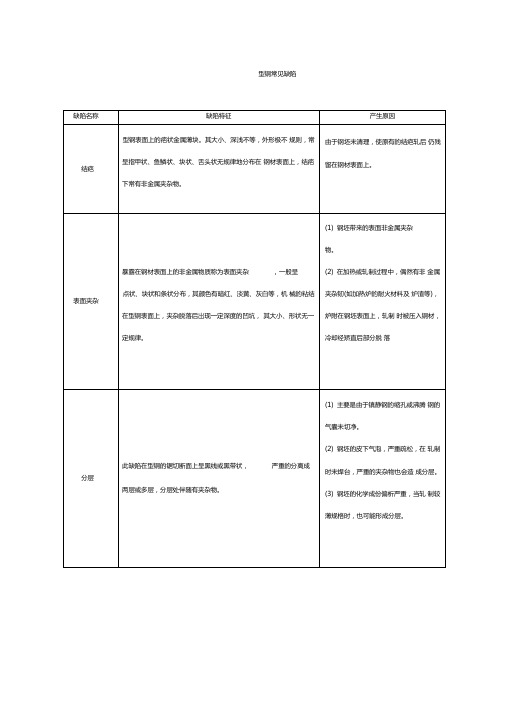
型钢常见缺陷型钢表面呈现的一种无规律分布的园形凸起称为凸包, 凸起部分的外缘比较园滑,凸包破裂后成鸡爪形裂口或舌形结钢坯有皮下气泡,轧制时未焊合。
疤,叫气泡。
多产生于型钢的角部及腿尖。
(1) 钢坯有裂缝或皮下气泡、非金属 夹杂物,经轧制破裂暴露。
(2) 加热温度不均匀,温度过低,轧 件在轧制时各部延伸与宽展不一顺轧制方向岀现在型钢表面上的线形开裂,一般呈直线形, 致。
有时呈“Y'形,多为通长出现,有时局部出现。
(3) 加热速度过快、炉尾温度过高或 轧制后冷却不当,易形成裂纹,此种 情况多发生在高碳钢和低合金钢 上。
尺寸超差是指型钢截面几何尺寸不符标准规定要求的统称。
尺寸超差(尺这类缺陷名目繁多,大部以产生部位以及其超差程度加以命 寸不合、规格名。
例工、槽、角钢的腿长、腿短、腰厚、腰薄及一腿长, 不合) 一腿短。
气泡(凸包)裂纹(1) 对工字钢成品孔腿长往往表现在 开口腿上,主要由于腰部压下量不 够,角钢和槽钢成品孔压下量的大 小,直接影响腿长和腿短。
(2) 切深孔切人太深,造成腿长无法 消除。
(3) 轧辊不水平或有轴向串动,以及 800咬入不正,成品孔夹板上偏等都 会造成一腿长,一腿短等。
(4) 腰的厚、薄主要是成品孔及成品 前孔压下量不合理所造成。
一般呈直线或弧形的沟槽,其深度不等,通长可见沟底,长划伤(刮伤、度自几毫米到几米,连续或断续地分布于钢材的局部或全擦伤、划痕) 长,多为单条,有时岀现多条。
型钢其一侧面沿轧制方向全长或周期性的缺少金属称缺肉, 缺肉缺陷处没有成品孔轧槽的热轧印迹,色暗、表面较粗糙。
耳子(1)导卫板安装不当,对轧件压力过大,将轧件表面划伤。
(2)导卫板加工不良,口边不圆滑,或磨损严重,粘有氧化铁皮,将轧件表面划伤。
(3)孔型侧壁磨损严重,当轧件接触时产生弧形划伤。
(4)钢材在运输过程中与表面粗糙的辊道、盖板、移钢机、活动挡板等接触划伤。
(1)孔型设计不良,轧辊车削不正确及轧机调整不当,使轧件进入成品孔时由于金属量不足,造成孔型充填不满。
重轨结疤的成因及改进途径探讨
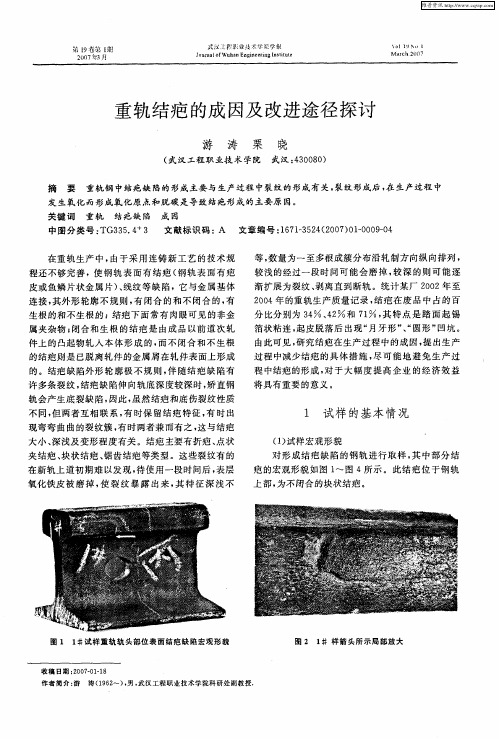
对 形成 结 疤缺 陷 的钢 轨进 行 取样 , 中部 分 结 其
疤 的宏观 形貌如 图 1 图 4所 示 。此结 疤位 于 钢轨 ~
上部, 为不 闭合 的块状结 疤 。
图1 1 #试样 重轨 轨 头 部位 表面 结疤 缺 陷 宏观 形 貌
轨会产 生底 裂 缺陷 , 因此 , 然 结疤和底 伤裂纹 性质 虽
不同, 但两 者互 相联 系 , 时保 留结 疤特 征 , 时 出 有 有Βιβλιοθήκη 1 试 样 的基本 情况
() 1 试样宏 观形貌
现弯 弯 曲曲的裂 纹簇 , 时两 者兼 而有 之 , 与结疤 有 这
大小、 深浅及 变形 程度 有关 。结疤 主要有 折疤 、 点状 夹 结疤 、 块状 结疤 、 齿结疤 等类 型 。这 些裂 纹有 的 锯 在 新轨上 道 初期难 以发 现 , 使用 一段 时间后 , 待 表层
图3 2 #试 样 重 轨 轨 头 部位 表 面 结 疤 缺 陷 宏 观 形 貌
图4 2 #样 箭 头 所 示 局 部 放 大
() 2 重轨钢 的化 学成 分 检验 所取 试样 的化学 成分如表 l 示 。取样部 所
出 , S P含 量 比较 低 , 就 减 少 了硫 化 物 夹 杂 和 其 、 这
皮 或鱼鳞 片状 金属 片) 线纹 等缺 陷 ,它 与金 属基 体 、
等 , 量 为一至 多根成 簇分 布沿轧 制 方向纵 向排列 , 数 较 浅 的经 过一 段时 间 可能 会 磨 掉 , 较深 的则 可 能 逐 渐 扩展 为裂纹 、 剥离直 到断 轨 。统计 某 厂 2 0 至 0 2年
维普资讯
第 1 卷 1 9 期
钢轨生产表面缺陷分析与改进
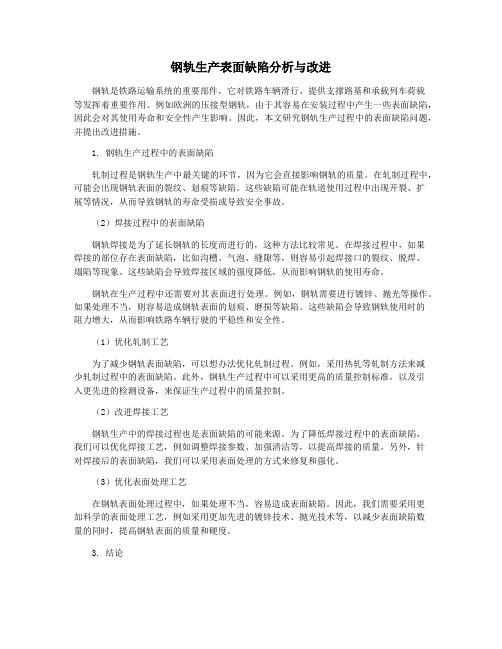
钢轨生产表面缺陷分析与改进钢轨是铁路运输系统的重要部件,它对铁路车辆滑行、提供支撑路基和承载列车荷载等发挥着重要作用。
例如欧洲的压接型钢轨,由于其容易在安装过程中产生一些表面缺陷,因此会对其使用寿命和安全性产生影响。
因此,本文研究钢轨生产过程中的表面缺陷问题,并提出改进措施。
1. 钢轨生产过程中的表面缺陷轧制过程是钢轨生产中最关键的环节,因为它会直接影响钢轨的质量。
在轧制过程中,可能会出现钢轨表面的裂纹、划痕等缺陷。
这些缺陷可能在轨道使用过程中出现开裂、扩展等情况,从而导致钢轨的寿命受损或导致安全事故。
(2)焊接过程中的表面缺陷钢轨焊接是为了延长钢轨的长度而进行的,这种方法比较常见。
在焊接过程中,如果焊接的部位存在表面缺陷,比如沟槽、气泡、缝隙等,则容易引起焊接口的裂纹、脱焊、塌陷等现象。
这些缺陷会导致焊接区域的强度降低,从而影响钢轨的使用寿命。
钢轨在生产过程中还需要对其表面进行处理。
例如,钢轨需要进行镀锌、抛光等操作。
如果处理不当,则容易造成钢轨表面的划痕、磨损等缺陷。
这些缺陷会导致钢轨使用时的阻力增大,从而影响铁路车辆行驶的平稳性和安全性。
(1)优化轧制工艺为了减少钢轨表面缺陷,可以想办法优化轧制过程。
例如,采用热轧等轧制方法来减少轧制过程中的表面缺陷。
此外,钢轨生产过程中可以采用更高的质量控制标准,以及引入更先进的检测设备,来保证生产过程中的质量控制。
(2)改进焊接工艺钢轨生产中的焊接过程也是表面缺陷的可能来源。
为了降低焊接过程中的表面缺陷,我们可以优化焊接工艺,例如调整焊接参数、加强清洁等,以提高焊接的质量。
另外,针对焊接后的表面缺陷,我们可以采用表面处理的方式来修复和强化。
(3)优化表面处理工艺在钢轨表面处理过程中,如果处理不当,容易造成表面缺陷。
因此,我们需要采用更加科学的表面处理工艺,例如采用更加先进的镀锌技术、抛光技术等,以减少表面缺陷数量的同时,提高钢轨表面的质量和硬度。
3. 结论本文对钢轨生产过程中的表面缺陷问题进行了分析,并提出了相应的改进措施,以期提高钢轨表面的质量,降低钢轨使用过程中的故障率和事故风险。
钢轨表面结疤缺陷的检验和分析

钢轨表面结疤缺陷的检验和分析任安超 吉 玉 蒋跃东(武汉钢铁(集团)公司技术中心 武汉:430080)摘 要 采用金相检验和电子探针的方法,对钢轨表面缺陷进行了检验分析。
揭示了钢轨表面缺陷的低倍以及高倍的形貌和特征,进而探索其产生的原因。
关键词 钢轨 缺陷 结疤 折叠中图分类号:T G335.4+3 文献标识码:A 文章编号:167123524(2005)03200082031 前言某厂2002年~2004年间共生产钢轨20余万吨,下表是近三年该厂生产的钢轨因钢质不良判为废品的统计情况。
表1 废品钢质不良年度结疤%裂纹%夹杂%劈头%汽泡%分层%200233.75 1.03 1.5210.9318.5134.26200342.0515.75 2.3413.587.2419.04200470.680.850.61 3.7410.3424.12从以上的统计结果看,造成废品偏高的第一位原因主要是钢轨表面的结疤严重,它严重地影响了钢轨一级品率,并且随着产量的增加,结疤在废品中的比率越来越大。
本文对钢轨表面结疤的形成原因进行研究。
2 试验方法由于以往生产的钢轨经常出现结疤现象,据不完全统计钢轨底部结疤居多,头部次之。
于是我们在正常生产中跟踪50Kg/m的U71Mn钢轨,对结疤缺陷的钢轨分别在头部、底部取样,具体缺陷部位如图1、图2、图3所示。
然后通过低倍、金相检验和电子探针,来描述结疤缺陷的特征。
进一步研究出结疤缺陷出现的 图1 1#钢轨头部结疤宏观形貌 图2 2#钢轨头部结疤宏观形貌 收稿日期:200526218. 作者简介:任安超,男(1976~),武汉钢铁(集团)公司技术中心,轧钢专业工程师. 图3 3#钢轨底部结疤宏观形貌 图4 1#钢轨结疤低倍形貌规律并分析其产生的原因。
3 试验结果和分析3.1 低倍检验结果1#样低倍组织正常,轨头下颚部结疤的色泽与基体明显不同,缺陷处显示出轻微的凹凸不平,深色的斑点为大小不一,形状不同的凹坑粗糙面,因而在光线下显深色,且两者之间存在裂纹(见图4);2#样低倍组织正常,轨头侧边有一条浅显的小裂纹,裂纹沿边缘终止于基体(见图5);3#低倍组织亦正常,轨底侧边结疤的裂纹终止于基体,且无色泽差别(见图6)。
钢轨生产表面缺陷分析与改进

钢轨生产表面缺陷分析与改进钢轨是铁路运输系统中的重要部件,其质量直接关系到列车运行的安全性和舒适性。
钢轨的生产质量十分重要。
在钢轨生产过程中,表面缺陷是制约产品质量的重要因素之一。
本文将对钢轨生产过程中常见的表面缺陷进行分析,并提出改进措施,以提高钢轨的质量和安全性。
一、表面缺陷的分类在钢轨生产过程中,表面缺陷主要包括劈裂、火花、气泡、氧化皮等。
这些缺陷会影响钢轨的强度、耐磨性和表面光洁度,直接影响列车的运行安全和舒适性。
1. 劈裂劈裂是指钢轨表面出现的裂纹,主要有疲劳裂纹、应力腐蚀裂纹等。
劈裂会导致钢轨的强度下降,严重时会造成钢轨的断裂,对列车运行安全构成威胁。
2. 火花火花是指钢轨表面出现的烧痕,主要由于轧辊磨损不均匀或轧制温度过高导致的局部过热。
火花会影响钢轨的表面硬度和耐磨性,降低钢轨的使用寿命。
二、表面缺陷的原因分析钢轨生产过程中,表面缺陷主要是由原材料质量、轧制工艺参数、轧辊磨损、轧辊冷却等因素共同影响导致的。
具体来说,原材料含杂质多、组织不均匀、氧化层厚度大等会导致表面缺陷;轧制工艺参数不合理、轧辊磨损不均匀、冷却不当等也会导致表面缺陷。
三、改进措施为了减少钢轨表面缺陷,提高钢轨的质量和安全性,需要从原材料控制、轧制工艺优化、轧辊管理、冷却系统改进等方面进行改进。
1. 原材料控制需要加强对原材料的质量控制。
对钢水进行严格化验,确保原材料的纯度和组织均匀度;加强对氧化层控制,减少氧化皮的产生;加强对杂质控制,减少气泡和火花的产生。
2. 轧制工艺优化需要优化轧制工艺参数。
根据原材料的不同特性和轧制工艺的要求,合理调整轧制温度、轧制速度、轧制压力等参数,以减少火花和气泡的产生;优化轧制过程中的冷却控制,减少劈裂的产生。
3. 轧辊管理轧辊是直接接触原材料的部件,其磨损和质量直接影响钢轨的质量。
需要做好轧辊的管理工作,加强轧辊的检测、维护和更换工作,确保轧辊的平整度和表面质量。
4. 冷却系统改进需要改进轧制过程中的冷却系统。
钢轨生产表面缺陷分析与改进

钢轨生产表面缺陷分析与改进钢轨作为铁路运输中的重要组成部分,承载着列车的重量和行驶的力度。
钢轨的质量对于列车的安全和运输的稳定性至关重要。
在钢轨生产过程中,难免会出现一些表面缺陷,这些缺陷可能会影响钢轨的使用寿命和安全性。
对钢轨生产表面缺陷的分析与改进显得尤为重要。
一、钢轨生产表面缺陷的分类钢轨生产过程中常见的表面缺陷主要包括裂缝、气孔、夹子、夹砂等。
裂缝是指在钢轨的表面或内部出现的断裂现象,这种缺陷可能会引起钢轨的疲劳断裂,严重影响钢轨的使用寿命和安全性。
气孔是指钢轨表面或内部的气体凝聚形成的孔洞,这种缺陷也会降低钢轨的强度和抗腐蚀性能。
夹子是指钢轨表面夹杂有炉渣、氧化皮等杂质的现象,这种缺陷容易引起表面脱落或者氧化腐蚀。
夹砂是指在钢轨表面残留的砂粒,这些砂粒会增加钢轨的磨损,降低使用寿命。
钢轨生产表面缺陷的原因主要包括材料质量、工艺参数、生产设备、操作技术等方面。
材料质量不过关是造成钢轨表面缺陷的重要原因之一。
如果原材料中存在太多的夹杂杂质、气孔等缺陷,会直接影响到钢轨的质量。
工艺参数不合理也容易导致钢轨的表面缺陷。
在轧制过程中,如果温度、速度等参数控制不当,容易产生裂缝、气孔等缺陷。
生产设备的精度和稳定性也会影响到钢轨的质量。
如果设备存在问题或者运行不稳定,也容易导致钢轨表面缺陷的产生。
操作技术水平也是影响钢轨质量的重要因素。
如果操作人员不熟练或者操作不规范,也容易导致缺陷的产生。
针对钢轨生产表面缺陷,可以采取以下改进措施:1. 加强原材料质量控制。
通过严格的原材料采购和检验,确保原材料的质量达标,减少夹杂杂质、气孔等缺陷。
2. 优化生产工艺参数。
对轧制工艺进行优化,合理控制轧制温度、速度等参数,减少裂缝、气孔等缺陷的产生。
3. 提升生产设备的精度和稳定性。
对生产设备进行定期维护和检修,保证设备的正常运行,减少因设备问题导致的缺陷。
4. 加强操作技术培训。
对操作人员进行培训,提高其操作技术水平和安全意识,减少因操作人员原因导致的缺陷。
浅析重轨轧疤缺陷原因及改进措施
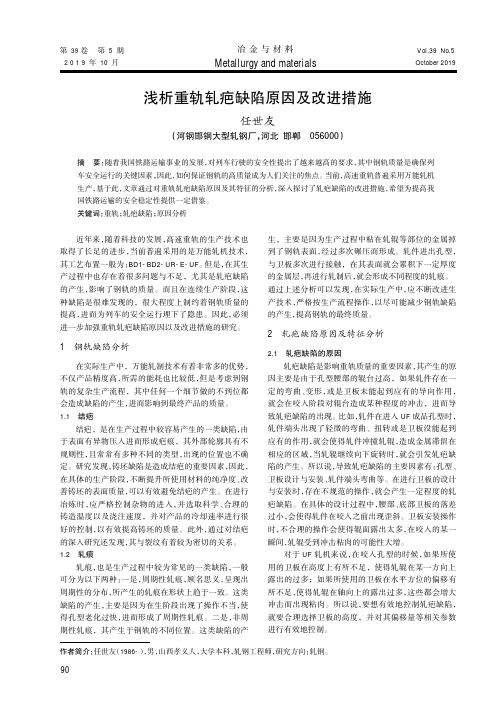
浅析重轨轧疤缺陷原因及改进措施任世友(河钢邯钢大型轧钢厂,河北邯郸056000)摘要:随着我国铁路运输事业的发展,对列车行驶的安全性提出了越来越高的要求,其中钢轨质量是确保列车安全运行的关键因素,因此,如何保证钢轨的高质量成为人们关注的焦点。
当前,高速重轨普遍采用万能轧机生产,基于此,文章通过对重轨轧疤缺陷原因及其特征的分析,深入探讨了轧疤缺陷的改进措施,希望为提高我国铁路运输的安全稳定性提供一定借鉴。
关键词:重轨;轧疤缺陷;原因分析Metallurgy and materials作者简介:任世友(1986-),男,山西孝义人,大学本科,轧钢工程师,研究方向:轧钢。
近年来,随着科技的发展,高速重轨的生产技术也取得了长足的进步,当前普遍采用的是万能轧机技术,其工艺布置一般为:BD1-BD2-UR-E-UF 。
但是,在其生产过程中也存在着很多问题与不足,尤其是轧疤缺陷的产生,影响了钢轨的质量。
而且在连续生产阶段,这种缺陷是很难发现的,很大程度上制约着钢轨质量的提高,进而为列车的安全运行埋下了隐患。
因此,必须进一步加强重轨轧疤缺陷原因以及改进措施的研究。
1钢轨缺陷分析在实际生产中,万能轧制技术有着非常多的优势,不仅产品精度高,所需的能耗也比较低,但是考虑到钢轨的复杂生产流程,其中任何一个细节做的不到位都会造成缺陷的产生,进而影响到最终产品的质量。
1.1结疤结疤,是在生产过程中较容易产生的一类缺陷,由于表面有异物压入进而形成疤痕,其外部轮廓具有不规则性,且常常有多种不同的类型,出现的位置也不确定。
研究发现,铸坯缺陷是造成结疤的重要因素,因此,在具体的生产阶段,不断提升所使用材料的纯净度、改善铸坯的表面质量,可以有效避免结疤的产生。
在进行冶炼时,应严格控制杂物的进入,并选取科学、合理的铸造温度以及浇注速度,并对产品的冷却速率进行很好的控制,以有效提高铸坯的质量。
此外,通过对结疤的深入研究还发现,其与裂纹有着较为密切的关系。
重轨轧疤缺陷原因分析及改进措施
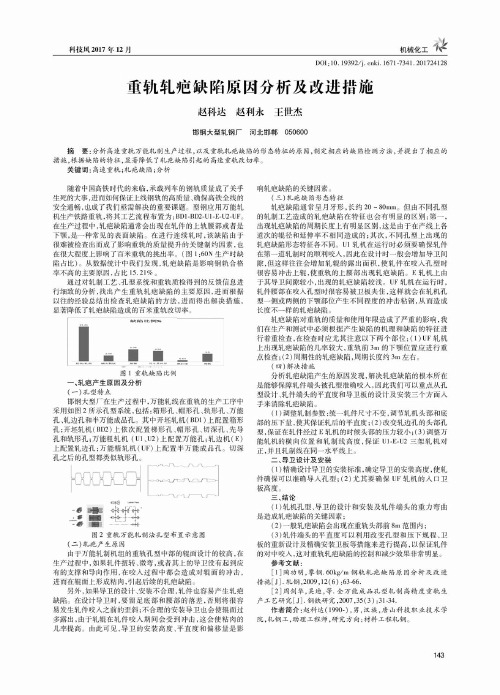
科技风2017年12月机械化工D O I:10.19392/j.c n k i.1671-7341.201724128重轨轧疤缺陷原因分析及改进措施赵科达赵利永王世杰邯钢大型轧钢厂河北邯郸050600摘要:分析高速重轨万能轧制生产过程,以及重轨轧疤缺陷的形态特征的原因,制定相应的缺陷检测方法,并提出了相应的 措施,根据缺陷的特征,显著降低了轧疤缺陷引起的高速重轨改切率。
关键词:高速重轨;轧疤缺陷;分析随着中国高铁时代的来临,承载列车的钢轨质量成了关乎 生死的大事,进而如何保证上线钢轨的高质量、确保高铁全线的 安全通畅,也成了我们亟需解决的重要课题。
型钢应用万能轧 机生产铁路重轨,将其工艺流程布置为:B D1-BD2-U1-E-U2-U F。
在生产过程中,轧疤缺陷通常会出现在轧件的上轨腰部或者是 下颚,是一种常见的表面缺陷。
在进行连续轧时,该缺陷由于 很难被检查出而成了影响重轨的质量提升的关键制约因素,也 在很大程度上影响了百米重轨的挑出率。
(图1:0%O生产时缺 陷占比)。
从数据统计中我们发现,轧疤缺陷是影响钢轨合格 率不高的主要原因,占比15.21%。
通过对轧制工艺、孔型系统和重轨质检得到的反馈信息进 行细致的分析,找出产生重轨轧疤缺陷的主要原因,进而根据 以往的经验总结出检查轧疤缺陷的方法,进而得出解决措施,显著降低了轧疤缺陷造成的百米重轨改切率。
图1重轨缺陷比例一、轧疤产生原因及分析(一)孔型特点邯钢大型厂在生产过程中,万能轧线在重轨的生产工序中 采用如图2所示孔型系统,包括:箱形孔、帽形孔、轨形孔、万能 孔、轧边孔和半万能成品孔。
其中开坯轧机%Q D1&上配置箱形 孔;开坯轧机(B D2)上依次配置梯形孔、帽形孔、切深孔、先导 孔和轨形孔;万能粗轧机%U1、U2 &上配置万能孔;轧边机%E&上配置轧边孔;万能精轧机%U F&上配置半万能成品孔。
切深 孔之后的孔型都类似轨形孔。
钢轨生产表面缺陷分析与改进

钢轨生产表面缺陷分析与改进钢轨作为铁路运输的重要组成部分,其质量和表面缺陷对铁路的安全运行至关重要。
钢轨生产过程中的表面缺陷分析和改进非常重要。
本文将对钢轨生产过程中的表面缺陷进行分析,并提出改进措施。
钢轨生产过程中常见的表面缺陷包括轨顶裂缝、轨脚裂缝、轨头掏槽、轨腹掏槽、焊接缺陷等。
这些缺陷可能会导致钢轨的损坏、断裂甚至造成事故。
对于轨顶裂缝和轨脚裂缝这类缺陷,通常是由于生产过程中的温度控制不当所导致的。
在轧制钢轨时,应严格控制温度,避免过热或过冷引起的开裂问题。
还应加强对轧辊和轧道板的维护,保证其表面光洁度,减少表面起槽,从而减少裂缝的发生。
对于掏槽缺陷,主要是由于电火花机械加工未能完全清除焊接瑕疵所致。
在生产过程中,应严格控制焊接工艺参数,确保焊接质量,避免出现焊接缺陷。
对于已经存在掏槽缺陷的钢轨,可以进行补焊或更换,以提高钢轨的使用寿命和安全性。
对于表面缺陷的改进措施,还应加强对原材料的质量控制。
钢轨生产过程中的原材料应经过严格的检测和筛选,确保其无内在缺陷。
还应加强对生产设备的维护和管理,及时更换老化和损坏的设备,保证生产过程的稳定性和质量。
还应加强生产过程的监控和数据分析。
通过对生产过程中的数据进行收集和分析,可以及时发现问题,及时采取相应的措施进行改进。
可以通过数据分析确定合适的温度控制范围,减少裂缝的发生。
还可通过数据分析优化焊接工艺参数,提高焊接质量。
钢轨生产过程中的表面缺陷分析和改进是非常重要的。
通过加强温度控制、质量控制、设备维护和数据分析等措施,可以提高钢轨的质量和使用寿命,保障铁路的安全运行。
鞍钢重轨生产轧痕缺陷产生原因及控制措施
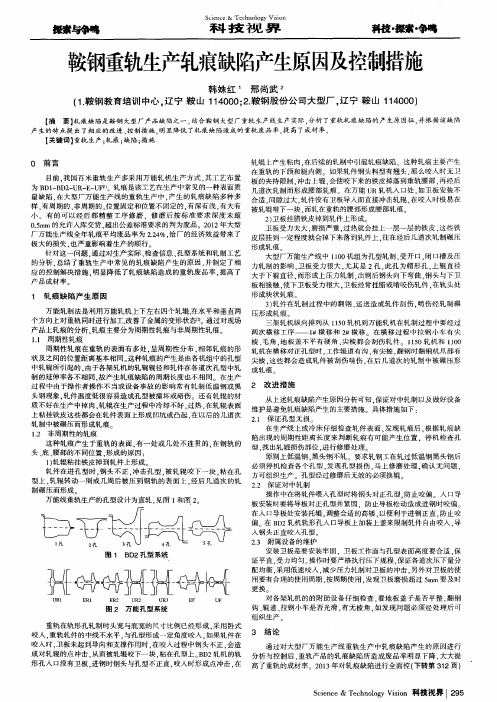
【 关键词 】 重轨 生产 ; 轧痕 ; 缺 陷; 措施
0 前 言
目前 . 我 国百米重轨生产 多采用万能 轧机生产方式 . 其工艺 布置 为B D1 一 B D 2 ~ UR — E — Up “ 轧痕是该 工艺在生产中常见的一种表面质 量缺 陷 . 在大型厂万能生产线 的重轨生产 中 . 产生 的轧痕缺 陷多种 多 样. 有周期 的、 非周期 的. 位置 固定和位置不 固定 的, 有深有浅 , 有 大有 小 有 的可 以经后部 精 整工 序修磨 .修 磨后 按标 准要 求深度 未 超 0 . 5 am的允许入库交货 . r 超 出公差标准要求 的判为废 品。2 0 1 2年大型 厂万能生产线全年轧痕平 均废品率为 2 . 2 4 %. 给厂的经济效 益带 来了 极大 的损失 , 也严重影响着生产 的顺行 。 针对这~ 问题 . 通过对生产实际 、 检查信息 、 孑 L 型系统 和轧制 工艺 的分 析 . 总结了重轨生产 中常见的轧痕缺 陷产生 的原 因 , 并制定 了相 轧辊上产生粘肉 . 在后续 的轧制中引起轧痕缺陷 。这种轧痕 主要产生 在重轨的下颌和腿内侧 如果 轧件钢头料型有 翘头 , 那 么咬入时无卫 板的夹持限制 . 冲击上辊 . 会使 咬下来 的铁皮掉 落到重 轨腰 部 , 再经后 几道次轧制而形成腰部轧 痕。在万能 U R轧机入 口处 , 如卫板安装不 合适 . 间隙过大 . 轧件没有卫板导入而直接冲击 轧辊 , 在咬人时极易在 被轧辊啃下一块 , 而 轧 在 重 轨 的腰 部 形成 腰 部轧 痕 。 2 ) 卫板挂腊铁皮掉到轧件上形成 。 卫板受力太大 . 磨 损严 重 . 过热就会 挂上一层一层 的铁 皮 , 这些铁 皮层挂到一定程度就会掉下来落到轧 件上 . 往在 经后几 道次轧制碾压 形成轧痕。 大型厂万能生产线中 1 1 0 0机组 为孔 型轧制 . 受开 口. 闭 口槽及压 力轧制 的影 响 , 卫板受力很大 , 尤 其是 2 孔, 此 孔为帽形孔 , 上 辊直径 大于下辊直径 . 而形成上压力轧制 . 出钢后钢头向下弯曲 . 钢头与下卫 板相接触 . 使下卫板受力很大 , 卫板经常挂腊或啃咬伤 轧件 , 在轨头处 形成块状轧痕 。 3 ) 轧件在轧 制过程 中的 翻钢 、 运送造成轧 件刮伤 , 啃伤经轧制碾 压形成轧痕 三架轧机纵 向排列从 1 1 5 0轧机到万能轧机在轧制过程 中要经过 两次横移 工序—— 1 # 横 移和 2 #横移 在横 移过程 中拉钢小 车有尖 棱、 毛角 , 地板盖不平有 硬角 、 尖棱 都会刮伤轧件 1 1 5 0轧机和 1 1 0 0 轧机在横移对正孔型时 , 工作辊道有沟 、 有尖棱 , 翻钢时翻钢机爪部有 尖棱 . 这 些都 会造成轧件被刮伤 啃伤 . 在后 几道次 的轧制 中被碾压形 成 轧 痕
钢轨生产表面缺陷分析与改进
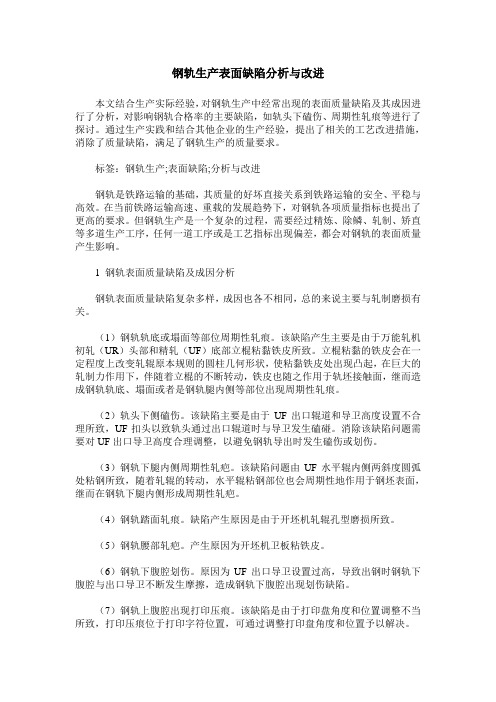
钢轨生产表面缺陷分析与改进本文结合生产实际经验,对钢轨生产中经常出现的表面质量缺陷及其成因进行了分析,对影响钢轨合格率的主要缺陷,如轨头下磕伤、周期性轧痕等进行了探讨。
通过生产实践和结合其他企业的生产经验,提出了相关的工艺改进措施,消除了质量缺陷,满足了钢轨生产的质量要求。
标签:钢轨生产;表面缺陷;分析与改进钢轨是铁路运输的基础,其质量的好坏直接关系到铁路运输的安全、平稳与高效。
在当前铁路运输高速、重载的发展趋势下,对钢轨各项质量指标也提出了更高的要求。
但钢轨生产是一个复杂的过程,需要经过精炼、除鳞、轧制、矫直等多道生产工序,任何一道工序或是工艺指标出现偏差,都会对钢轨的表面质量产生影响。
1 钢轨表面质量缺陷及成因分析钢轨表面质量缺陷复杂多样,成因也各不相同,总的来说主要与轧制磨损有关。
(1)钢轨轨底或塌面等部位周期性轧痕。
该缺陷产生主要是由于万能轧机初轧(UR)头部和精轧(UF)底部立棍粘黏铁皮所致。
立棍粘黏的铁皮会在一定程度上改变轧辊原本规则的圆柱几何形状,使粘黏铁皮处出现凸起,在巨大的轧制力作用下,伴随着立棍的不断转动,铁皮也随之作用于轨坯接触面,继而造成钢轨轨底、塌面或者是钢轨腿内侧等部位出现周期性轧痕。
(2)轨头下侧磕伤。
该缺陷主要是由于UF出口辊道和导卫高度设置不合理所致,UF扣头以致轨头通过出口辊道时与导卫发生磕碰。
消除该缺陷问题需要对UF出口导卫高度合理调整,以避免钢轨导出时发生磕伤或划伤。
(3)钢轨下腿内侧周期性轧疤。
该缺陷问题由UF水平辊内侧两斜度圆弧处粘钢所致,随着轧辊的转动,水平辊粘钢部位也会周期性地作用于钢坯表面,继而在钢轨下腿内侧形成周期性轧疤。
(4)钢轨踏面轧痕。
缺陷产生原因是由于开坯机轧辊孔型磨损所致。
(5)钢轨腰部轧疤。
产生原因为开坯机卫板粘铁皮。
(6)钢轨下腹腔划伤。
原因为UF出口导卫设置过高,导致出钢时钢轨下腹腔与出口导卫不断发生摩擦,造成钢轨下腹腔出现划伤缺陷。
钢轨生产表面缺陷分析与改进

钢轨生产表面缺陷分析与改进钢轨是铁路交通重要的基础设施之一,其质量直接关系到铁路运输的安全和稳定。
钢轨的生产质量和表面缺陷对于铁路交通的安全和运行至关重要。
本文将针对钢轨生产中的表面缺陷进行分析,并提出一些改进措施,以提高钢轨的质量和安全水平。
一、钢轨表面缺陷的类型钢轨的表面缺陷主要包括裂纹、夹渣、气孔、夹砂等。
1. 裂纹裂纹是钢轨表面最常见的缺陷之一,主要分为疲劳裂纹和热裂纹两种。
疲劳裂纹主要是由于车轮与钢轨之间的接触疲劳所导致,而热裂纹则是由于钢轨在冷却过程中发生温度梯度过大所引起的。
2. 夹渣夹渣是指在钢轨表面和内部夹杂有氧化物或炉渣等杂质,主要是由于生产过程中未能及时清除或过滤掉这些杂质所导致的。
3. 气孔气孔是指钢轨内部存在气体气泡所形成的孔洞,主要由于生产中未能完全排除气体或钢液中存在气体导致的。
钢轨表面缺陷的存在对铁路运输的安全和稳定造成了严重的影响。
1. 表面裂纹会导致钢轨的寿命大大缩短,严重时可能引发断轨事故,对铁路运输的安全构成威胁。
2. 夹渣、气孔、夹砂等缺陷会导致钢轨的强度和硬度降低,容易引发损坏和断裂,影响铁路的正常运行。
三、改进措施针对钢轨生产中存在的表面缺陷,需要采取一系列的改进措施,以提高钢轨的质量和安全水平。
1. 完善生产工艺流程设立严格的工艺标准和流程,加强钢轨生产过程中的监控和控制,确保每一个环节都能够达到规定的要求。
加强生产工艺中的检测和测试,及时发现和处置存在的缺陷。
2. 提高原材料质量加强对原材料的选择和管控,优化钢材的化学成分和物理性能,提高原材料的质量。
加强对原材料的检测和筛选,确保原材料不带有夹渣、气孔和夹砂等缺陷。
3. 强化设备维护定期对生产设备进行维护和保养,保证设备处于良好的工作状态。
设立严格的设备检查制度,及时发现和修复设备的故障和缺陷,确保设备的稳定运行。
4. 加强人员培训加强对生产人员的培训和教育,提高生产人员的技术水平和质量意识。
建立健全的员工激励机制,激发员工的积极性和创造性,确保员工能够按照规定的要求进行生产作业。
轧制缺陷及质量控制

轧制缺陷及质量控制一、引言轧制是金属加工过程中的重要环节,对于金属产品的质量和性能具有重要影响。
轧制缺陷是指在轧制过程中产生的各种不良现象,如裂纹、夹杂物、不均匀变形等。
为了保证轧制产品的质量,需要进行有效的质量控制和缺陷检测。
本文将详细介绍轧制缺陷的分类、检测方法以及质量控制措施。
二、轧制缺陷的分类1. 表面缺陷:包括划痕、氧化皮、凹陷等。
2. 内部缺陷:包括夹杂物、气泡、裂纹等。
3. 形状缺陷:包括厚度不均匀、宽度不均匀、边缘不平整等。
三、轧制缺陷的检测方法1. 目视检测:通过人眼观察轧制产品的表面和断面,判断是否存在明显的缺陷。
2. 磁粉检测:利用磁性粉末吸附在轧制产品表面的磁性缺陷上,通过观察磁粉的分布情况来判断是否存在缺陷。
3. 超声波检测:利用超声波的传播特性,通过检测超声波的反射和传播时间来判断轧制产品内部是否存在缺陷。
4. X射线检测:利用X射线的穿透性,通过观察X射线照片来判断轧制产品内部是否存在缺陷。
5. 红外热像检测:利用红外热像仪记录轧制产品表面的热分布情况,通过观察热图来判断是否存在缺陷。
四、轧制缺陷的质量控制措施1. 原材料控制:选择质量良好的原材料,确保原材料的化学成份和物理性能符合要求。
2. 轧制工艺控制:合理控制轧制温度、轧制速度和轧制压力,避免轧制过程中的过热和过冷现象。
3. 设备维护控制:定期对轧机设备进行检修和维护,确保设备的正常运行和精确度。
4. 操作工艺控制:培训操作人员,提高其对轧制工艺的理解和操作技能,减少人为操作引起的缺陷。
5. 缺陷修复控制:对于轧制产品中的一些小缺陷,可以采取修复措施,如打磨、热处理等,以提高产品的外观和性能。
五、案例分析以某钢厂的冷轧钢板生产线为例,该生产线采用磁粉检测和超声波检测相结合的方式进行轧制缺陷的检测。
经过对轧制产品的检测分析,发现存在少量的夹杂物和裂纹缺陷。
针对这些缺陷,钢厂采取了以下措施:首先,加强原材料的筛选和质量控制,确保原材料的纯净度和均匀性;其次,优化轧制工艺参数,减少轧制过程中的应力和变形;最后,对于存在的缺陷,进行修复处理,并进行再次检测,确保产品的质量符合要求。
鞍钢重轨生产轧痕缺陷产生原因及控制措施
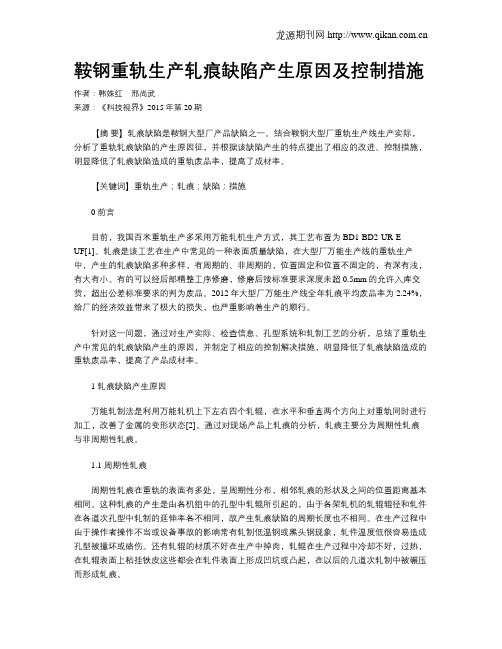
鞍钢重轨生产轧痕缺陷产生原因及控制措施作者:韩姝红邢尚武来源:《科技视界》2015年第20期【摘要】轧痕缺陷是鞍钢大型厂产品缺陷之一。
结合鞍钢大型厂重轨生产线生产实际,分析了重轨轧痕缺陷的产生原因征,并根据该缺陷产生的特点提出了相应的改进、控制措施,明显降低了轧痕缺陷造成的重轨废品率,提高了成材率。
【关键词】重轨生产;轧痕;缺陷;措施0 前言目前,我国百米重轨生产多采用万能轧机生产方式,其工艺布置为BD1-BD2-UR-E-UF[1]。
轧痕是该工艺在生产中常见的一种表面质量缺陷,在大型厂万能生产线的重轨生产中,产生的轧痕缺陷多种多样,有周期的、非周期的,位置固定和位置不固定的,有深有浅,有大有小。
有的可以经后部精整工序修磨,修磨后按标准要求深度未超0.5mm的允许入库交货,超出公差标准要求的判为废品。
2012年大型厂万能生产线全年轧痕平均废品率为2.24%,给厂的经济效益带来了极大的损失,也严重影响着生产的顺行。
针对这一问题,通过对生产实际、检查信息、孔型系统和轧制工艺的分析,总结了重轨生产中常见的轧痕缺陷产生的原因,并制定了相应的控制解决措施,明显降低了轧痕缺陷造成的重轨废品率,提高了产品成材率。
1 轧痕缺陷产生原因万能轧制法是利用万能轧机上下左右四个轧辊,在水平和垂直两个方向上对重轨同时进行加工,改善了金属的变形状态[2]。
通过对现场产品上轧痕的分析,轧痕主要分为周期性轧痕与非周期性轧痕。
1.1 周期性轧痕周期性轧痕在重轨的表面有多处,呈周期性分布,相邻轧痕的形状及之间的位置距离基本相同。
这种轧痕的产生是由各机组中的孔型中轧辊所引起的,由于各架轧机的轧辊辊径和轧件在各道次孔型中轧制的延伸率各不相同,故产生轧痕缺陷的周期长度也不相同。
在生产过程中由于操作者操作不当或设备事故的影响常有轧制低温钢或黑头钢现象,轧件温度低很容易造成孔型被撞坏或硌伤。
还有轧辊的材质不好在生产中掉肉,轧辊在生产过程中冷却不好,过热,在轧辊表面上粘挂铁皮这些都会在轧件表面上形成凹坑或凸起,在以后的几道次轧制中被碾压而形成轧痕。
铁路60Kg重轨表面质量刮伤、轧疤的改进研究
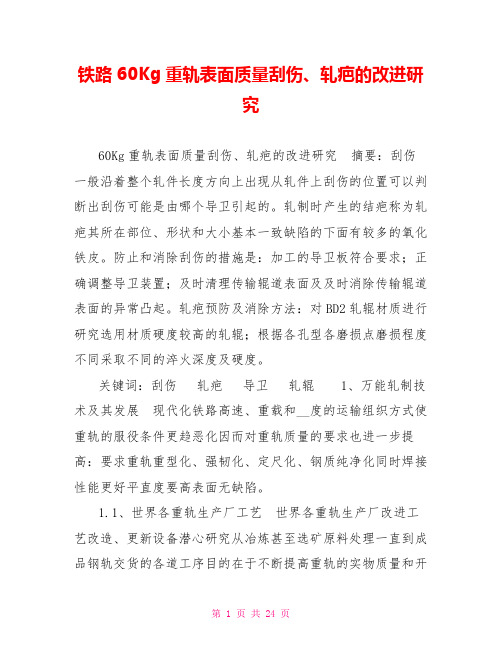
铁路60Kg重轨表面质量刮伤、轧疤的改进研究60Kg重轨表面质量刮伤、轧疤的改进研究摘要:刮伤一般沿着整个轧件长度方向上出现从轧件上刮伤的位置可以判断出刮伤可能是由哪个导卫引起的。
轧制时产生的结疤称为轧疤其所在部位、形状和大小基本一致缺陷的下面有较多的氧化铁皮。
防止和消除刮伤的措施是:加工的导卫板符合要求;正确调整导卫装置;及时清理传输辊道表面及及时消除传输辊道表面的异常凸起。
轧疤预防及消除方法:对BD2轧辊材质进行研究选用材质硬度较高的轧辊;根据各孔型各磨损点磨损程度不同采取不同的淬火深度及硬度。
关键词:刮伤轧疤导卫轧辊1、万能轧制技术及其发展现代化铁路高速、重载和__度的运输组织方式使重轨的服役条件更趋恶化因而对重轨质量的要求也进一步提高:要求重轨重型化、强韧化、定尺化、钢质纯净化同时焊接性能更好平直度要高表面无缺陷。
1.1、世界各重轨生产厂工艺世界各重轨生产厂改进工艺改造、更新设备潜心研究从冶炼甚至选矿原料处理一直到成品钢轨交货的各道工序目的在于不断提高重轨的实物质量和开发高速(200km/h/以上)轨。
使重轨生产技术自90年代起有了突飞猛进的发展。
重轨轧制是重轨生产中的重要一环直接影响着重轨产品质量和综合机械性能目前重轨轧制主要有两种方法:孔型轧制法和万能轧制法。
法国的阿央日厂首创了重轨万能轧制技术该厂研制的万能轧制原理就是用万能轧机和轧边机交替地对金属进行加工成形。
在万能轧机上从4个垂直方向上给轧件施加很大的压下量同时控制轨腰、轨底和轨头厚度.延伸率相当大每道次达到1.25~1.40轨底、轨头翼缘部分尺寸由轧边机控制最终由半万能精轧机轧成成品其流程为:连铸坯在由Ф1340mm 万能轧机和Ф1036mm 轧边机组成的可逆串列式机组中轧制5道次最后在中1280mm 的万能精轧机上进行精轧。
主要设备包括:两座Ф5Omm×2250mm粗轧机架一座Ф1340mm 的万能机架水平辊Ф1170mm立辊Ф900mm;一座Ф1036mm轧边机轧辊Ф920mm辊身长度为838mm;一座Фl280mm 的半万能精轧机架水平辊Ф1100mm立辊Ф800mm。
- 1、下载文档前请自行甄别文档内容的完整性,平台不提供额外的编辑、内容补充、找答案等附加服务。
- 2、"仅部分预览"的文档,不可在线预览部分如存在完整性等问题,可反馈申请退款(可完整预览的文档不适用该条件!)。
- 3、如文档侵犯您的权益,请联系客服反馈,我们会尽快为您处理(人工客服工作时间:9:00-18:30)。
重轨轧疤缺陷产生原因分析及其解决措施摘要:本文根据武钢重轨生产线的工艺特点,结合生产实际和孔型特点,分析了重轨轧疤缺陷的产生原因以及形态特征,制定出合适的缺陷检查方法,并根据该缺陷产生的特点提出了相应的改进方法,明显降低了轧疤缺陷造成的重轨改切率。
关键词:万能轧制、轧疤、缺陷、卫板1 前言作为铁路的重要组成部分,重轨起着支撑和导向列车的双重作用,也是影响铁路行车安全的重要因素。
在高速运行列车的作用下,重轨表面缺陷部位容易产生应力集中并扩展,直接危害到列车的运行安全,甚至导致断轨,引起严重后果。
轧疤缺陷是重轨生产中常见的一种表面缺陷,一般出现在重轨的下颚或者是上鱼尾板面(即上腰)部位。
连续生产时,在轧制段较难检查出该缺陷,这也一度制约着重轨质量的提高,影响挑出率。
通过对产检系统及时反馈的重轨检查信息以及对孔型系统和轧制工艺的分析,总结了重轨轧疤缺陷的产生原因,并制定了相应的轧疤缺陷的检查方法,提出了解决措施,明显降低了轧疤缺陷造成的重轨改切率。
2 轧疤缺陷产生原因及特征分析2.1 孔型特点武钢重轨万能轧制线生产高速重轨时采用的孔型系统见图1,包括:箱形孔、帽形孔、轨形孔、万能孔、轧边孔和半万能成品孔①。
其中开坯轧机(BD1)上配置箱形孔;开坯轧机(BD2)上依次配置梯形孔、帽形孔、切深孔、先导孔和轨形孔;万能粗轧机(UR)上配置万能孔;轧边机(E)上配置轧边孔;万能精轧机(UF)上配置半万能成品孔。
图1 重轨万能轧制法孔型布置示意图切深孔之后的孔型都类似轨形孔②,孔型中腿、颚部与腰部呈一定角度α,如图2所示,图中H 表示头部,B表示底部。
角度α随着轧制道次的不同而存在差异,计其斜度为cotα=a/h。
图2 轨形孔示意图2.2 轧疤缺陷产生原因由于重轨孔型腰部的辊台较高,若轧件发生微弯、扭转或者卫板未起到导向和支撑作用时,在咬入过程中都会造成对辊台的冲击,从而在辊台上产生粘肉,在后续的轧制中引起轧疤缺陷。
以轧件进入UF 成品孔型为例,见图3,轧件通过UF 的入口卫板进入孔型过程时,如果轧件端头发生微弯、扭转或者卫板未起到应有的作用,轧件可能撞击图4中方框部位所示轧辊,金属粘在该区域,在轧辊旋转到下一周期后将压入轧件下颚,导致轧疤缺陷。
因此,孔型、卫板设计和安装以及轧件端头弯曲是造成重轨轧疤缺陷的三个关键因素。
U F 穿钢示意图U F 入口下卫板U F 下辊咬入易咬偏区域U F 入口上卫板U F 上辊图3 UF 卫板穿钢示意图 图4咬入撞击部位示意图BD2切深孔之后的各孔型产生轧疤缺陷得容易程度见表1。
从表中综合评价可以看出,当孔型的cot α≤0.363158时,基本上都会出现轧疤缺陷,而且图2中的R 过渡导角越小,在轧辊上越容易产生冲击粘肉现象。
表1 各孔型产生轧疤缺陷的容易程度孔型 部位 R a h cot α 卫板冲击粘肉 切深孔H9037.64341.107059下卫板○B90 46.34 98.5 0.470457 ○ 先导孔H3618.3270.677778下卫板○R RABB 28 20.26 62 0.326774 ○轨形孔H 25 12.57 21.8 0.576606下卫板○B 28 20.7 57 0.363158 ●UF H 8.1 9.57 28.7 0.333449上下卫板●B 20.4 12.65 37.95 0.333333 ○ER H 17 10 30.2 0.331126上下卫板◎B 22 12.65 37.95 0.333333 ○UR H 17 16.6 49.8 0.333333上下卫板△B 22 12.65 37.95 0.333333 ○EF H 17 10.37 31.1 0.333441上下卫板◎B 22 12.65 37.95 0.333333 ○注:○表示咬入瞬间孔型对轧件端头有冲击粘肉,分值为0;◎表示偶尔冲击粘肉,分值为1;△表示容易冲击粘肉,分值为2;●表示容易冲击粘肉,分值为3。
此外,卫板设计和安装不合理,也容易在轧件上产生轧疤缺陷。
卫板设计时,如果腰部与底部卫板的落差不够,容易导致轧件在咬入之前歪斜。
卫板安装不合理将造成辊面露出太多,在轧件咬入瞬间轧辊受冲击粘肉的几率增大。
对于BD2轧机,由于没有设计上卫板,在咬入过程对轧件的夹持作用较小。
对于UF轧机,如图3所示,在轧件咬入孔型的瞬间,如果卫板的整体高度偏矮,轧辊在高度方向上露出偏多;如果整体卫板在水平方向的偏移不够,轧辊在轴向方向上露出偏多,轧辊露出的面积越大,越容易受冲击产生粘肉。
另外,如果A点偏低,B点稍高,容易导致轧件咬入不正,撞击辊台而粘肉的几率增大。
因此,卫板的高度、偏移量以及平直度是控制轧疤缺陷的重要因素。
轧件端头弯曲也是在咬入过程造成轧辊受冲击粘肉的重要原因。
在卫板和压下量难以保证轧件端头平直时,金属量相对较多的一侧更容易冲击轧辊,产生粘肉。
2.3 轧疤缺陷形态特征轧疤缺陷通常呈月牙形,长约20~80mm,深约3~5mm,见图5。
但不同孔型产生的轧疤缺陷的特征会有所区别。
首先,轧疤缺陷出现的周期长度不同。
由于各道次的辊径和延伸率各不相同,故产生轧疤缺陷的周期长度不相同。
表2为经常出现轧疤缺陷的孔型,以及各孔型出现的轧疤缺陷周期长度。
图5 下颚轧疤缺陷实物图表2 各孔型出现轧疤缺陷的周期长度孔型辊径范围/mm 延伸率/%出现周期长度/mUF 1040-1160 1.053163912 3.4-3.8E 900-990 1.063597254 3-3.3UR 1040-1200 1.347360865 4.4-5.1BD2第5孔900-1000 2.5 7-7.8其次,不同孔型上出现的轧疤缺陷形态特征各不同。
由于轧件在BD2轧机的第5孔咬入时没有上卫板的支撑和导向作用,咬入不稳定,导致轧疤缺陷常出现在重轨的上腰部,长度一般在40~80mm。
UR轧机在第一道轧制时必须保证轧件容易咬入,因此卫板间隙较大,轧辊露出的面积较多,轧件咬入孔型时容易冲击上辊,轧疤缺陷容易出现在重轨的上腰部,长度一般约为30~50mm。
E轧机上的精轧前道次,由于其卫板间隙较小,出现的轧疤缺陷较浅。
UF轧机上,轧件在咬入孔型时,腰部被上下卫板夹住,常在孔型的一边下颚部位或同时在孔型的两边下颚部位出现冲击粘肉,但粘肉程度不一,因此出现的轧疤缺陷长度也不一,一般在30mm以下。
轧疤缺陷严重影响了重轨的使用,因此必须根据缺陷产生的机理和形态特征进行重点检查,质量检查时应重点注意以下几个部位。
(1)由于UF轧机上容易出现轧疤缺陷,应重点检查重轨的前3m的下颚位置;(2)腰部轧疤缺陷一般出现重轨的前4~7m的范围;(3)通长的周期性轧疤缺陷,周期长度一般为3.4~3.8m。
3解决措施从轧疤缺陷的产生原因分析可知,保证轧件端头准确咬入孔型是解决该缺陷的根本所在。
应主要从孔型、轧件端头的平直度和卫板的设计及安装三个方面入手以消除轧疤缺陷。
3.1孔型及轧件端头平直度(1)调整压下规程:在保证轧件尺寸不变的前提下,调整万能轧机的头、底的压下规程,以保证轧件轧后平直;(2)修改轧边孔头部孔型,保证轧件经过E轧机时头部压力较小;(3)调整万能轧机的横向位置和轧制线高度,保证UR-E-UF三架轧机对正,并且轧制线在同一水平线上;(4)调整E轧机出口卫板安装位置,保证出口卫板距离辊面约5mm,同时向操作侧(DS侧)偏移,以保证轧件对中咬入;(5)BD2轧机采用翻钢机夹持轧件,预先将其翻正并对中,然后再咬入。
3.2卫板设计及安装(1)制定合适的卫板安装标准保证卫板的安装高度,确保轧件能够准确的导入孔型。
万能轧机的出口卫板向DS侧偏移,以达到导正轧件的目的;万能轧机的入口卫板向DS侧偏移,尽量减少轧件端头冲击孔型的几率。
而对于UF轧机,尤其要保证入口卫板的高度。
(2)修改卫板的设计方案(a)根据BD2第5个孔型中轧件头部和腰部的标准差,设计出合理的卫板;(b)在万能孔型的头部增加卫板。
4 轧疤缺陷控制效果通过采用以上改进措施后,生产中重轨的轧疤缺陷得到了较好控制。
2010年轧疤缺陷造成的重轨改切率明显下降,见图6所示,从1月份的1.62%下降到了12月份的0.33%。
轧疤缺陷造成的重轨改切率0.000.400.801.201.602.001月2月3月4月5月6月7月8月9月10月11月12月月份改切率(%)图6 2010年轧疤缺陷造成的重轨改切率5结论(1)孔型、卫板设计和安装以及轧件端头弯曲是产生轧疤缺陷的关键因素;(2)在重轨前7m 范围内可以检查出有无轧疤缺陷; (3)通过采用修改孔型及压下规程、重新设计和安装卫板等措施后,提高了轧件端头的平直度,保证了轧件对中咬入,减少了重轨轧疤缺陷,控制效果明显。
参考文献:① 周剑华,吴迪,等. 全万能成品孔型轧制高精度重轨生产工艺研究[J]. 钢铁研究,2007,35(3):31~34. ② 吴迪,赵宪明. 万能孔型轧制高精度重轨的研究[J]. 轧钢,2000,17(3):12~14.。