Datenblatt-RLK-350-CN (1)
蓝客手持式综合维护终端LK-350使用说明
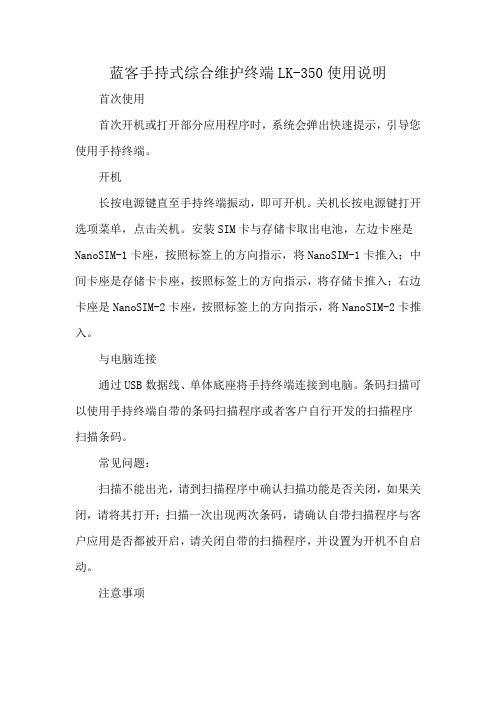
蓝客手持式综合维护终端LK-350使用说明
首次使用
首次开机或打开部分应用程序时,系统会弹出快速提示,引导您使用手持终端。
开机
长按电源键直至手持终端振动,即可开机。
关机长按电源键打开选项菜单,点击关机。
安装SIM卡与存储卡取出电池,左边卡座是NanoSIM-1卡座,按照标签上的方向指示,将NanoSIM-1卡推入;中间卡座是存储卡卡座,按照标签上的方向指示,将存储卡推入;右边卡座是NanoSIM-2卡座,按照标签上的方向指示,将NanoSIM-2卡推入。
与电脑连接
通过USB数据线、单体底座将手持终端连接到电脑。
条码扫描可以使用手持终端自带的条码扫描程序或者客户自行开发的扫描程序扫描条码。
常见问题:
扫描不能出光,请到扫描程序中确认扫描功能是否关闭,如果关闭,请将其打开;扫描一次出现两次条码,请确认自带扫描程序与客户应用是否都被开启,请关闭自带的扫描程序,并设置为开机不自启动。
注意事项
请勿将USB连接线及手持终端尾插部分浸水;请勿将机身内存占用满,否则会造成系统异常;扫描功能不用时,请关闭扫描头,请勿长期开启;扫描时请勿直视激光扫描头,以免误伤。
ARTISAN TECHNOLOGY GROUP 设备购买和售卖服务说明书
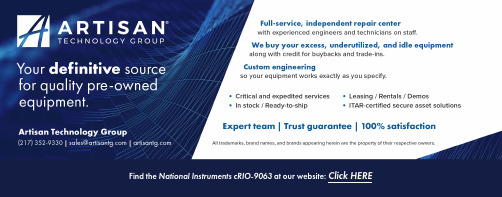
USER MANUALNI cRIO-9063Embedded Real-Time Controller with Reconfigurable FPGA forC Series ModulesThis document describes the features of the NI cRIO-9063 and contains information about mounting and operating the device.ContentsConfiguring the cRIO-9063 (2)Connecting the cRIO-9063 to the Host Computer or Network Using Ethernet (2)Configuring Startup Options (3)cRIO-9063 Features (4)Ports and Connectors (4)Buttons (9)LEDs (11)Chassis Grounding Screw (13)Internal Real-Time Clock (14)Battery (14)File System (14)Mounting the Device (15)Dimensions (16)Mounting Requirements (16)Ambient Temperature (17)Mounting the Device Directly on a Flat Surface (18)Mounting the Device on a Panel (19)Mounting the Device on a DIN Rail (21)Mounting the Device on a Rack (22)Mounting the Device on a Desktop (22)Worldwide Support and Services (25)Configuring the cRIO-9063You can connect the cRIO-9063 to a host computer or network and configure the startup options using the USB device port or the RJ-45 Gigabit Ethernet port 1.Tip Refer to the getting started guide on /manuals for basic configurationinstructions and information about connecting to a host computer using the USBdevice port. NI recommends using the USB device port for configuration, debug,and maintenance.Connecting the cRIO-9063 to the Host Computer or Network Using EthernetComplete the following steps to connect the cRIO-9063 to a host computer or Ethernet network using the RJ-45 Gigabit Ethernet port 1. NI recommends using the RJ-45 Gigabit Ethernet port 1 for communication with deployed systems.1.Power on the host computer or Ethernet hub.2.Connect the RJ-45 Gigabit Ethernet port 1 on the cRIO-9063 to the host computer orEthernet hub using a standard Category 5 (CAT-5) or better shielded, twisted-pairEthernet cable.Caution To prevent data loss and to maintain the integrity of your Ethernetinstallation, do not use a cable longer than 100 m (328 ft).The cRIO-9063 attempts to initiate a DHCP network connection the first time youconnect using Ethernet. The cRIO-9063 connects to the network with a link-local IP address with the form 169.254.x.x if it is unable to initiate a DHCP connection. Finding the cRIO-9063 on the Network (DHCP)Complete the following steps to find the cRIO-9063 on a network using DHCP.1.Disable secondary network interfaces on the host computer, such as a wireless accesscard on a laptop.2| | NI cRIO-9063 User Manual2.Ensure that any anti-virus and firewall software running on the host computer allowsconnections to the host computer.Note MAX uses UDP 44525. Refer to the documentation of your firewallsoftware for information about configuring the firewall to allow communicationthrough the UDP 44525.unch MAX on the host computer.4.Expand Remote Systems in the configuration tree and locate your system.Tip MAX lists the system under the model number followed by the serialnumber, such as NI-cRIO-9063-1856AAA.Configuring Startup OptionsComplete the following steps to configure the cRIO-9063 startup options in MAX.1.In MAX, expand your system under Remote Systems.2.Select the Startup Settings tab to configure the startup settings.cRIO-9063 Startup OptionsYou can configure the following cRIO-9063 startup options.NI cRIO-9063 User Manual| © National Instruments| 3Table 1. cRIO-9063 Startup Options (Continued)cRIO-9063 FeaturesThe cRIO-9063 provides the following features.Ports and ConnectorsThe cRIO-9063 provides the following ports and connectors.4| | NI cRIO-9063 User ManualFigure 1. cRIO-9063 Ports and ConnectorsB Device Port2.RS-232 Serial Port3.RJ-45 Ethernet Port 1B Host Port5.Power ConnectorRJ-45 Gigabit Ethernet PortThe cRIO-9063 has one tri-speed RJ-45 Gigabit Ethernet port. By default, the Ethernet port is enabled and configured to obtain an IP address automatically. The Ethernet port can be configured in MAX.The following table shows the pinout for the RJ-45 Gigabit Ethernet port.NI cRIO-9063 User Manual| © National Instruments| 5Note The Ethernet port performs automatic crossover configuration so you do notneed to use a crossover cable to connect to a host computer.The following NI Ethernet cables are available for the cRIO-9063.Related InformationEthernet LED Indicators on page 13Power ConnectorThe cRIO-9063 has a power connector to which you can connect a power supply. The following table shows the pinout for the power connector.6 | | NI cRIO-9063 User ManualThe cRIO-9063 has reverse-voltage protection.The following NI power supplies and accessories are available for the cRIO-9063.Related InformationPOWER LED Indicators on page 11RS-232 Serial PortThe cRIO-9063 has an RS-232 serial port to which you can connect devices such as displays or input devices. Use the Serial VIs to read from and write to the serial port. Refer to the LabVIEW Help for information about the Serial VIs.Find examples on how to use NI-Serial or NI-VISA to perform serial communication in the NI Example Finder. The NI Example Finder is located on the Help menu in the LabVIEW Help.Note The RS-232 serial port cannot be accessed by the user application when theConsole Out startup option is enabled.The following table shows the pinout for the RS-232 serial port.NI cRIO-9063 User Manual| © National Instruments| 7USB Host PortsThe USB host ports on the cRIO-9063 support common USB mass-storage devices such as USB Flash drives, USB-to-IDE adapters, keyboards, mice, and USB cameras.Caution Do not hot-swap USB devices while the cRIO-9063 is in a hazardouslocation or connected to high voltages. If the cRIO-9063 is not in a hazardouslocation, you can connect and disconnect USB devices without affecting operation.The following table shows the pinout for the USB host ports.The following NI cable is available for the cRIO-9063.8 | | NI cRIO-9063 User ManualRelated InformationFile System on page 14USB Device PortThe cRIO-9063 USB device port is intended for device configuration, application deployment, debugging, and maintenance. For example, you can use the USB device port to install software or driver updates during field maintenance instead of interrupting communication on the RJ-45 Ethernet ports.Caution Do not hot-swap USB devices while the cRIO-9063 is in a hazardouslocation or connected to high voltages. If the cRIO-9063 is not in a hazardouslocation, you can connect and disconnect USB devices without affecting operation. The following table shows the pinout for the USB device port.The following NI cable is available for the cRIO-9063.ButtonsThe cRIO-9063 provides the following buttons.NI cRIO-9063 User Manual| © National Instruments| 9Figure 2. cRIO-9063 Buttons1.RESET ButtonRESET ButtonPress the RESET button to reset the processor in the same manner as cycling power. Troubleshooting Network ConnectivityYou can use the RESET button to troubleshoot network connectivity.Complete the following steps to reset the network adapters to default settings.1.Hold the RESET button for 5 seconds, and then release it to boot the controller in safemode and enable Console Out.2.Hold the RESET button again for 5 seconds to boot the controller into safe mode, enableConsole Out, and reset network adapters to default settings.System ResetThe following figure shows the reset behavior of the cRIO-9063.Figure 3. Reset Button BehaviorPress and holdRESET button for ≥ 5 s Press and holdLEDsThe cRIO-9063 provides the following LEDs.Figure 4.cRIO-9063 LEDs1.POWER LED2.STA TUS LEDER1 LEDER FPGA1 LED5.RJ-45 Ethernet LEDsPOWER LED IndicatorsThe following table lists the POWER LED indicators.STA TUS LED IndicatorsThe following table describes the STATUS LED indicators.User LEDsYou can define the USER1 and USER FPGA1 LEDs to meet the needs of your application. The following table lists the USER1 and USER FPGA1 LED indicators.Ethernet LED IndicatorsThe following table lists the Ethernet LED indicators.Chassis Grounding ScrewThe cRIO-9063 provides a chassis grounding screw.Figure 5. cRIO-9063 Chassis Grounding Screw1.Chassis grounding screwFor EMC compliance, you must connect the cRIO-9063 to earth ground through the chassis ground screw. Use wire that is 2.1 mm2 (14 AWG) solid copper wire with a maximum length of 1.5 m (5 ft). Attach the wire to the earth ground of the electrode system of the facility.Caution If you use shielded cabling to connect to a C Series module with a plasticconnector, you must attach the cable shield to the chassis grounding terminal using2.1 mm2 (14 AWG) or larger wire. Attach a ring lug to the wire and attach the wireto the chassis grounding terminal. Solder the other end of the wire to the cableshield. Use shorter wire for better EMC performance.For more information about ground connections, visit /info and enter the Info Code emcground.Internal Real-Time ClockThe cRIO-9063 contains an internal real-time clock that maintains system time when the cRIO-9063 is powered off. The system clock of the cRIO-9063 is synchronized with the internal real-time clock at startup. You can set the real-time clock using MAX, or you can set the clock programmatically using LabVIEW.Refer to the specifications on /manuals for the real-time clock accuracy specifications. BatteryThe cRIO-9063 contains a lithium cell battery that stores the system clock information when the cRIO-9063 is powered off. There is only a slight drain on the battery when power is applied to the cRIO-9063 power connector. The rate at which the battery drains when power is disconnected depends on the ambient storage temperature. For longer battery life, store the cRIO-9063 at a cooler temperature and apply power to the power connector. Refer to the specifications on /manuals for the expected battery lifetime.The battery is not user-replaceable. If you need to replace the battery, contact NI. Refer to the specifications on /manuals for information about battery disposal.File SystemLabVIEW mounts USB devices to the media/sdx1 directory and creates symboliclinks /u, /v, /w, or /x to the media mount point, starting with /u if it is available. To prevent any file corruption to external storage devices, verify that any file IO operations with the specific drive finish before removing the device. Refer to the LabVIEW Help for more information.The file system of the cRIO-9063 follows conventions established for UNIX-style operating systems. Other LabVIEW Real-Time targets follow Microsoft Windows-style conventions. In order to facilitate the porting of applications from those targets, this target supports the Windows-style /C home directory. This path is bound to the UNIX-style directory /home/ lvuser.Various LabVIEW Real-Time system files which would be accessible from C: (or /C) on other LabVIEW Real-Time targets are found in different locations on this target.UNIX-style file systems support the concept of a symbolic link, which allows access to a file using an alternative file path. For example, it is possible to link /C/ni-rt/system, where dynamic libraries are deployed on other LabVIEW Real-Time targets, to /usr/local/lib, where they are stored on the cRIO-9063, if the application requires this.For more information, visit /info and enter the Info Code RT_Paths.Mounting the DeviceTo obtain the maximum allowable ambient temperature of 55 °C, you must mount thecRIO-9063 horizontally on a flat, metallic, vertical surface such as a panel or wall. You can mount the cRIO-9063 directly to the surface or use the NI Panel Mounting Kit. The following figure shows the cRIO-9063 mounted horizontally.Figure 6. cRIO-9063 Horizontal Mounting1.UpYou can also mount the cRIO-9063 in other orientations, on a nonmetallic surface, on a35-mm DIN rail, on a desktop, or in a rack. Mounting the cRIO-9063 in these or other configurations can reduce the maximum allowable ambient temperature and can affect the typical accuracy of modules in the cRIO-9063. For more information about typical accuracy specifications for C Series modules and temperature deratings caused by different mounting configurations, visit /info and enter the Info Code criotypical.Caution Make sure that no C Series modules are in the cRIO-9063 beforemounting it.Tip Before using any of these mounting methods, record the serial number fromthe back of the cRIO-9063 so that you can identify the cRIO-9063 in MAX. Youwill be unable to read the serial number after you mount the cRIO-9063.DimensionsThe following figures show the front and side dimensions of the cRIO-9063. For detailed dimensional drawings and 3D models, visit /dimensions and search for the module number.Figure 7. cRIO-9063 Front DimensionsFigure 8. cRIO-9063 Side DimensionsMounting RequirementsYour installation must meet the following requirements for cooling and cabling clearance. Allow 25.4 mm (1.00 in.) on the top and the bottom of the cRIO-9063 for air circulation, as shown in the following figure.Figure 9. cRIO-9063 Cooling DimensionsAllow the appropriate space in front of C Series modules for cabling clearance, as shown in the following figure. The different connector types on C Series modules require different cabling clearances. For a complete list of cabling clearances for C Series modules, visit /info and enter the Info Code crioconn.Figure 10. cRIO-9063 Cabling ClearanceAmbient TemperatureMeasure the ambient temperature at each side of the cRIO-9063, 63.5 mm (2.50 in.) from the side and 25.4 mm (1.00 in.) forward from the rear of the cRIO-9063, as shown in the following figure.Figure 11. cRIO-9063 Ambient T emperature Location1.Location for measuring the ambient temperatureMounting the Device Directly on a Flat SurfaceFor environments with high shock and vibration, NI recommends mounting the cRIO-9063 directly on a flat, rigid surface using the mounting holes in the cRIO-9063.What to Use•cRIO-9063•Screwdriver, Phillips #2•M4 or number 8 screw (x2), user-provided, longer than 23.00 mm (0.91 in.) to pass all the way through the cRIO-9063What to DoComplete the following steps to mount the cRIO-9063 directly on a flat surface.1.Prepare the surface for mounting the cRIO-9063 using the Surface Mounting Dimensions .2.Align the cRIO-9063 on the surface.3.Fasten the cRIO-9063 to the surface using the M4 or number 8 screws appropriate for thesurface. Tighten the screws to a maximum torque of 1.3 N · m (11.5 lb · in.).Surface Mounting DimensionsThe following figure shows the surface mounting dimensions for the cRIO-9063.Figure 12. cRIO-9063 Surface Mounting Dimensions 4.1 mm (0.16 in.)47.0 mm(1.85 in.)47.2 mm(1.86 in.)30.6 mm (1.20 in.)41.1 mm(1.62 in.)Mounting the Device on a PanelYou can use the NI panel mounting kit to mount the cRIO-9063 on a panel.What to Use•cRIO-9063•Screwdriver, Phillips #2•NI panel mounting kit, 779097-01–Panel mounting plate–M5 or number 10 screw (x4)What to DoComplete the following steps to mount the cRIO-9063 on a panel.1.Align the cRIO-9063 and the panel mounting plate.2.Fasten the panel mounting plate to the cRIO-9063 using the screwdriver and M5 ornumber 10 screws. NI provides these screws with the panel mounting kit. Tighten the screws to a maximum torque of 1.3 N · m (11.5 lb · in.).Note You must use the screws provided with the NI panel mounting kitbecause they are the correct depth and thread for the panel mounting plate. 3.Fasten the panel mounting plate to the surface using the screwdriver and screws that areappropriate for the surface. The maximum screw size is M5 or number 10.Panel Mounting DimensionsThe following figure shows the panel mounting dimensions for the cRIO-9063.20| | NI cRIO-9063 User ManualFigure 13. cRIO-9063 Panel Mounting DimensionsMounting the Device on a DIN RailYou can use the NI DIN rail mounting kit to mount the cRIO-9063 on a standard 35-mm DIN rail.What to Use•cRIO-9063•Screwdriver, Phillips #2•NI DIN rail mounting kit, 779019-01–DIN rail clip–M4 × 25 flathead screw (x2)What to DoComplete the following steps to mount the cRIO-9063 on a DIN rail.1.Align the cRIO-9063 and the DIN rail clip.NI cRIO-9063 User Manual| © National Instruments| 212.Fasten the DIN rail kit to the cRIO-9063 using the screwdriver and M4 × 25 flathead screws. NI provides these screws with the DIN rail mounting kit. Tighten the screws to amaximum torque of 1.3 N · m (11.5 lb · in.).Note You must use the screws provided with the NI DIN rail mounting kitbecause they are the correct depth and thread for the DIN rail clip.Clipping the Device on a DIN RailComplete the following steps to clip the cRIO-9063 on a DIN rail.1.Insert one edge of the DIN rail into the deeper opening of the DIN rail clip.2.Press down firmly to compress the spring until the clip locks in place on the DIN rail.Caution Ensure that no C Series modules are in the cRIO-9063 before removing itfrom the DIN rail.Mounting the Device on a RackYou can use the following rack mount kits to mount the cRIO-9063 and other DIN rail-mountable equipment on a standard 482.6 mm (19 in.) rack.•NI Sliding Rack-Mounting Kit, 779102-01•NI Rack-Mounting Kit, 781989-01Note You must use the NI DIN rail mounting kit, 779019-01, in addition to a rack-mounting kit.Mounting the Device on a DesktopYou can use the NI desktop mounting kit to mount the cRIO-9063 on a desktop.What to Use •cRIO-9063•Screwdriver, Phillips #1•Screwdriver, Phillips #2•NI desktop mounting kit, 779473-0122 | | NI cRIO-9063 User ManualFigure 14. Components of the NI Desktop Mount Kit1.Desktop mounting brackets (x2)2.Adapter bracket3.M3x14 screws (x2)4.M3x20 screws (x2)What to DoComplete the following steps to mount the cRIO-9063 on a desktop.NI cRIO-9063 User Manual| © National Instruments| 23e a #1 Phillips screwdriver to remove the two screws from the back of the chassis onthe front-panel side.e the screwdriver and the two M3x20 screws to attach the adapter bracket to thechassis.3.Align one of the end brackets with the mounting hole at one of the ends of the chassis.e a #2 Phillips screwdriver to tighten the captive screw on the end bracket.5.Repeat steps 2 and 3 to attach the other end bracket to the other end of the chassis. Desktop Mounting DimensionsThe following figures show the desktop mounting dimensions for the cRIO-9063.24| | NI cRIO-9063 User ManualFigure 15. cRIO-9063 Desktop Mounting Front Dimensions17.2 mm22.9 mmFigure 16. cRIO-9063 Desktop Mounting Side DimensionsWorldwide Support and ServicesThe NI website is your complete resource for technical support. At /support, you have access to everything from troubleshooting and application development self-help resources to email and phone assistance from NI Application Engineers.Visit /services for NI Factory Installation Services, repairs, extended warranty, and other services.Visit /register to register your NI product. Product registration facilitates technical support and ensures that you receive important information updates from NI.A Declaration of Conformity (DoC) is our claim of compliance with the Council of the European Communities using the manufacturer’s declaration of conformity. This system affords the user protection for electromagnetic compatibility (EMC) and product safety. You can obtain the DoC for your product by visiting /certification. If your product supports calibration, you can obtain the calibration certificate for your product at /calibration.NI cRIO-9063 User Manual| © National Instruments| 25NI corporate headquarters is located at 11500 North Mopac Expressway, Austin, Texas, 78759-3504. NI also has offices located around the world. For telephone support in the United States, create your service request at /support or dial 1 866 ASK MYNI (275 6964). For telephone support outside the United States, visit the Worldwide Offices section of / niglobal to access the branch office websites, which provide up-to-date contact information, support phone numbers, email addresses, and current events.Refer to the NI Trademarks and Logo Guidelines at /trademarks for information on NI trademarks. Other product and company names mentioned herein are trademarks or trade names of their respective companies. For patents covering NI products/technology, refer to the appropriate location: Help»Patents in your software, the patents.txt file on your media, or the National Instruments Patent Notice at /patents. Y ou can find information about end-user license agreements (EULAs) and third-party legal notices in the readme file for your NI product. Refer to the Export Compliance Information at /legal/export-compliance for the NI global trade compliance policy and how to obtain relevant HTS codes, ECCNs, and other import/export data. NI MAKES NO EXPRESS OR IMPLIED WARRANTIES AS TO THE ACCURACY OF THE INFORMA TION CONTAINED HEREIN AND SHALL NOT BE LIABLE FOR ANY ERRORS. U.S. Government Customers: The data contained in this manual was developed at private expense and is subject to the applicable limited rights and restricted data rights as set forth in FAR 52.227-14, DFAR 252.227-7014, and DFAR 252.227-7015.© 2016 National Instruments. All rights reserved.。
Aolynk-S1508LV100R004版本说明书

Aolynk S1508LV100R004版本说明书杭州华三通信技术有限公司Aolynk S1508LV100R004版本说明书关键词:Logo切换摘要:此版本系Logo切换版本缩略语:缩略语英文全名中文解释VLAN Virtual Local Area Network 虚拟局域网ServiceofQoS Quality服务质量目录1 版本信息 (4)1.1 版本号 (4)1.2 历史版本信息 (4)1.3 版本配套表 (4)2 版本使用限制及注意事项 (4)3 版本特性说明 (5)3.1 版本硬件特性 (5)3.2 版本软件特性 (5)4 版本变更说明 (5)4.1 特性变更说明 (5)4.2 命令行变更说明 (5)4.3 MIB变更说明 (5)4.4 操作方式变更说明 (5)5 存在问题与规避措施 (6)6 解决问题列表 (6)7 配套资料 (6)7.1 配套资料清单 (6)7.2 配套产品资料的获取方法 (6)8 版本升级操作指导 (6)表目录表1 历史版本信息表 (4)表2 版本配套表 (4)表3 特性变更说明 (5)表4 配套手册清单 (6)表5 从网站查询和下载资料的说明 (6)1 版本信息1.1 版本号版本号:S1508LV100R0041.2 历史版本信息表1历史版本信息表版本号基础版本号发布日期备注S1508LV100R004S1508LV100R0032007-05-16无S1508LV100R003S1508LV100R0012006-09-30无S1508LV100R001首次发布2006-04-29无1.3 版本配套表表2版本配套表系列以太网交换机产品系列 AolynkS1500型号S1508L内存需求无FLASH需求无BOOTROM版本号无目标文件名称S1508LV100R004.exeQUIDVIEW版本号无CAMS版本号无WEB版本号无备注无2 版本使用限制及注意事项无3 版本特性说明3.1 版本硬件特性无3.2 版本软件特性无4 版本变更说明4.1 特性变更说明表3特性变更说明版本号项目描述硬件特性更新无S1508LV新增特性:100R004软件特性更新显示配置:增加显示当前配置按钮。
ARTISAN TECHNOLOGY GROUP 设备购买、买家退货、交易换用信息说明书

E/S/M/B Series Calibration Procedure for NI-DAQ mx™This document contains information about calibrating NationalInstruments E, S, M, and B Series data acquisition (DAQ) devices.This document does not discuss programming techniques or compilerconfiguration. The National Instruments DAQmx driver contains onlinehelp files that have compiler-specific instructions and detailed functionexplanations. You can add these help files when you install NI-DAQmx onthe calibration computer.E/S/M/B Series devices should be calibrated at a regular interval as definedby the measurement accuracy requirements of your application. NationalInstruments recommends that you routinely perform a complete calibrationat least once every year (once every two years for some M Series devices).You can shorten this interval based on the accuracy demands of yourapplication or requirements of your processes.ContentsConventions (2)Software (3)Documentation (3)Password (4)Test Equipment (4)Test Considerations (5)Calibration Process (6)Calibration Process Overview (6)Initial Setup (6)Self-Calibration (7)E/S/M/B Series Verification Procedure (7)Analog Input Verification (7)Analog Output Verification (12)Counter Verification (14)E/S/M/B Series Adjustment Procedure (16)Device Test Limits (19)Using the Tables (20)Range (20)Test Point (20)24-Hour Limits (20)1-Year Limits (20)Counters (20)E Series Device Test Limits (21)NI 6011E—16-Bit Resolution (21)NI 6023E/6024E/6025EFamily—12-Bit Resolution (23)NI DAQCard-6024E—12-Bit Resolution (24)NI 6030E/6031E/6032E/6033EFamily—16-Bit Resolution (26)NI 6034E/6035E/6036E Family—16-Bit Resolution (29)NI DAQCard-6036E—16-Bit Resolution (31)NI 6040E Family—12-Bit Resolution (33)NI 6052E Family—16-Bit Resolution (36)NI DAQCard-6062E—12-Bit Resolution (39)NI 6070E Family—12-Bit Resolution (42)S Series Device Test Limits (45)NI PCI-6110/6111 Family—12-Bit Resolution (45)NI 6115 Family—12-Bit Resolution (47)NI 6120 Family—16-Bit Resolution (50)NI 6122/6123 Family—16-Bit Resolution (52)NI 6132/6133 Family—14-Bit Resolution (53)NI 6143 Family—16-Bit Resolution (55)M Series Device Test Limits (56)NI 6220/6221/6224/6225/6229Family—16-Bit Resolution (56)NI 6250/6251/6254/6259 Family—16-Bit Resolution (58)NI 6280/6281/6284/6289 Family—18-Bit Resolution (60)B Series Device Test Limits (64)NI 6010—16-Bit Resolution (64)NI 6013/6014 and NI 6015/6016Families—16-Bit Resolution (66)ConventionsThe following conventions appear in this manual:»The » symbol leads you through nested menu items and dialog box optionsto a final action. The sequence File»Page Setup»Options directs you topull down the File menu, select the Page Setup item, and select Optionsfrom the last dialog box.This icon denotes a note, which alerts you to important information.E/S/M/B Series Calibration Procedure for bold Bold text denotes items that you must select or click in the software, suchas menu items and dialog box options. Bold text also denotes parameternames and hardware labels.italic Italic text denotes variables, emphasis, a cross reference, or an introductionto a key concept. Italic text also denotes text that is a placeholder for a wordor value that you must supply.monospace Monospace text denotes text or characters that you should enter from thekeyboard, sections of code, programming examples, and syntax examples.This font is also used for the proper names of disk drives, paths, directories,programs, subprograms, subroutines, device names, functions, operations,variables, filenames, and extensions.monospace italic Italic text in this font denotes text that is a placeholder for a word or valuethat you must supply.Platform Text in this font denotes a specific platform and indicates that the textfollowing it applies only to that platform.SoftwareCalibration requires one of the following:•The latest NI-DAQmx driver—NI-DAQmx includes high-levelfunction calls to simplify the task of writing software to calibratedevices. The driver supports many programming languages, includingLabVIEW, LabWindows™/CVI™, C/C++, C#, and Visual Basic .NET.•Calibration Executive—The National Instruments CalibrationExecutive integrated environment is used for verifying and adjustingNI measurement devices. No programming is required. CalibrationExecutive users should refer to the Calibration Executive Help at/manuals instead of this document. DocumentationIf you use Calibration Executive, refer to the Calibration Executive Help at/manuals instead of this document.If you are using the NI-DAQmx driver, the following documents are yourprimary references for writing your calibration utility:•The NI-DAQmx C Reference Help includes information about thefunctions in the driver.•The DAQ Getting Started Guide for NI-DAQ 8.0 or later providesinstructions for installing and configuring NI-DAQ devices.© National Instruments Corporation3E/S/M/B Series Calibration Procedure for NI-DAQmx•The NI-DAQmx Help includes information about creating applicationsthat use the NI-DAQmx driver.•E/M/S Series Calibration Hardware Adapter Installation Guideprovides information on installing and operating the E/M/S Seriescalibration hardware adapter.For more information about the devices you are calibrating, refer to yourdevice user documentation.PasswordThe default password for password-protected operations is NI.Test EquipmentNational Instruments recommends that you use the following instrumentsfor calibrating an E/S/M/B Series device:•Calibrator—Fluke 5700A. If that instrument is unavailable, use ahigh-precision voltage source that is at least 50 ppm accurate for12-bit boards, 10 ppm for 16-bit boards, and 10 ppm for 18-bit boards.•DMM—NI 4070. If that instrument is unavailable, use a multiranging6 1/2-digit DMM with an accuracy of 40 ppm. The•Counter—Hewlett-Packard 53131A. If that instrument is unavailable,use a counter accurate to 0.01%.•Low thermal copper EMF plug-in cables—Fluke 5440A-7002.Do not use standard banana cables.•Shielded DAQ cable—NI recommends using shielded cables, asdescribed in Table 1.Table 1. Recommended CablesDevice CableE/S/B Series devices with a 68-pin SCSI IISH68-68-EPconnectorSHC68-68-EP, SHC68-68-EPM, SHC68-68-SE/S/M Series devices with 68-pin VHDCIconnectorsE Series devices with a 100-pin connector SH1006868. Connect the 68-pin cable labeledMIO-16 to the accessory. The 68-pin cablelabeled Extended I/O remains unconnected.M/B Series devices with a 37-pin D-SUBSH37F-37M-1connectorE/S/M/B Series Calibration Procedure for •One of the following DAQ accessories:–E/M/S Series calibration hardware adapter—The E/M/S Seriescalibration hardware adapter connects your calibration equipmentto your 68-pin E/S/M Series device. If you programmaticallycontrol this fixture, you will not need to disconnect and reconnectcables at each step of the procedure.calibration equipment from Connector 0 and reconnect to Connector 1 midway through theverification procedure.–SCB-68—The SCB-68 is a shielded I/O connector block with68 screw terminals for easy signal connection to 68- or 100-pinDAQ devices.–CB-68LP/CB-68LPR/TBX-68—The CB-68LP, CB-68LPR,and TBX-68 are low-cost termination accessories with 68 screwterminals for easy connection of field I/O signals to 68-pin DAQdevices.–BNC-2110—The BNC-2110 is a desktop and DIN rail-mountableBNC adapter you can connect to DAQ devices.–CB-37F-LP—The CB-37F-LP is a low-cost terminationaccessory with 37 screw terminals for easy connection of field I/Osignals to 37-pin DAQ devices.Test ConsiderationsConnection and environmental considerations:•Keep connections to the device as short as possible. Long cables andwires can act as antennae, which could pick up extra noise that wouldaffect measurements.•Use shielded copper wire for all cable connections to the device.Use twisted-pair wire to eliminate noise and thermal offsets.•Maintain the ambient temperature between 18–28 °C. (The devicetemperature will be greater than the ambient temperature.)•Keep relative humidity below 80%.•Allow a warm-up time of at least 15 minutes for PCI/PCI Express/PXIdevices and 30 minutes for DAQCard/DAQPad devices to ensure thatthe measurement circuitry is at a stable operating temperature.© National Instruments Corporation5E/S/M/B Series Calibration Procedure for NI-DAQmxE/S/M/B Series Calibration Procedure for NI-DAQmx Calibration ProcessThis section provides instructions for verifying and adjusting your device.Note If you use Calibration Executive, refer to the Calibration Executive Help at/manuals instead of this document.Calibration Process OverviewThe calibration process has four steps:1. Initial Setup —Configure your device in NI-DAQmx.2.E/S/M/B Series Verification Procedure —Verify the existing operationof the device. This step allows you to confirm that the device wasoperating within its specified range prior to calibration.3.E/S/M/B Series Adjustment Procedure —Perform an externalcalibration that adjusts the device calibration constants with respect toa known voltage source.4.Perform another verification to ensure that the device is operatingwithin its specifications after adjustment.These steps are described in detail in the following sections. Although NIrecommends that you verify all ranges, you may wish to save time bychecking only the ranges used in your application.Initial SetupThe device must be configured in Measurement & Automation Explorer(MAX) to communicate with NI-DAQmx.The following procedure describes how to configure a device in MAX.1.Install the NI-DAQmx driver software.2.Power off the computer that will hold the device, and install the device in an available slot.3.Power on the computer and launch Measurement & Automation Explorer (MAX).4.Configure the device identifier and select Self-Test to ensure that thedevice is working properly.Note When a device is configured with MAX, it is assigned a device identifier. Eachfunction call uses this identifier to determine which DAQ device to calibrate.© National Instruments Corporation 7E/S/M/B Series Calibration Procedure for NI-DAQmxSelf-CalibrationSelf-calibration should be performed after the device has warmed up for therecommended time period. Call self-calibration before doing the firstverification. This function measures the onboard reference voltage of thedevice and adjusts the self-calibration constants to account for any errorscaused by short-term fluctuations in the environment. When youself-calibrate a device, no external signal connections are necessary.E/S/M/B Series Verification ProcedureVerification determines how well the DAQ device is meeting itsspecifications. By performing this procedure, you can see how your devicehas operated over time. You can use this information to help determine theappropriate calibration interval for your application.The verification procedure is divided into the major functions of the device.Throughout the verification process, use the tables in the Device Test Limitssection to determine if your device needs to be adjusted.Analog Input VerificationSince E/S/M/B Series devices have many different ranges, you must checkmeasurements for each available range. Because there is only one ADC onE, M, and B Series devices, you only need to perform verification on oneanalog input channel. For S Series devices, you must perform verificationon all analog input channels.Use the following procedure to check the performance of the analog input.1.Refer to Table 2 to determine connections between the device and thecalibrator.NI-DAQ Function CallLabVIEW Block DiagramCall DAQmxSelfCal with thefollowing parameters:Device_Name[]: dev1E/S/M/B Series Calibration Procedure for NI-DAQmx 2.Choose the table from the Device Test Limits section that correspondsto the device you are verifying. This table shows all acceptable settingsfor the device type. NI recommends that you verify all ranges,although you may want to save time by checking only the ranges usedin your application.3.Set the calibrator voltage to the test value indicated in the device table.4.Create a task using DAQmxCreateTask .Table 2. Calibrator Connections DeviceConnections *E/M/BSeries •Connect the positive output of the calibrator to AI 0 (pin 68).•Connect the negative output of the calibrator to AI 8 (pin 34).•If your calibrator has a guard connection, connect that terminal to AI GND.•If your calibrator does not have a guard connection and has a floating output,connect the negative output to AI GND. If the calibrator output is not floating,do not make any other connections. For more information, refer to the userdocumentation for the device you are using.•If you are using the E/M/S Series calibration hardware adapter, connect thedevice as described in the E/M/S Series Calibration Hardware AdapterInstallation Guide .S Series •Connect the positive output of the calibrator to AI 0 + (pin 68).•Connect the negative output of the calibrator to AI 0 – (pin 34).•If your calibrator has a guard connection, connect that terminal to AI GND.•If your calibrator does not have a guard connection and has a floating output,connect the negative output to AI GND. If the calibrator output is not floating,do not make any other connections. For more information, refer to the userdocumentation for the device you are using.•If you are using the E/M/S Series calibration hardware adapter, connect thedevice as described in the E/M/S Series Calibration Hardware AdapterInstallation Guide .* Pin numbers are given for 68-pin connectors only. If you are using a BNC, 32-pin, 37-pin, or 100-pin connector, refer to your device user documentation for signal connection locations.NI-DAQ Function CallLabVIEW Block Diagram Call DAQmxCreateTask withthe following parameters:taskName :AIVerificationTasktaskHandle : &taskHandle LabVIEW does not require this step.© National Instruments Corporation 9E/S/M/B Series Calibration Procedure for NI-DAQmx 5.Add a channel to the task using DAQmxCreateAIVoltageChan(DAQmx Create Virtual Channel VI ) and configure the channel. Use the tables in the Device Test Limits section to determine the minimum and maximum values for your device.6.(NI 628x Devices Only) Configure the lowpass filter.7.Configure timing for the voltage acquisition usingDAQmxCfgSampClkTiming (DAQmx Timing VI ).NI-DAQ Function CallLabVIEW Block Diagram Call DAQmxCreateAIVoltageChanwith the following parameters:taskHandle : taskHandlephysicalChannel : dev1/ai0nameToAssignToChannel :myVoltageChannelterminalConfig :DAQmx_Val_Cfg_DefaultminVal : –10.0maxVal : 10.0units : DAQmx_Val_VoltscustomScaleName : NULLNI-DAQ Function Call LabVIEW Block Diagram Call DAQmxSetChanAttributewith the following parameters:taskHandle : taskHandleChannel : ““Attribute :DAQmx_AI_Lowpass_EnableValue : 0 (filter off) or1 (filter on)Note (PCI-MIO-16XE-50 (NI 6011E) and NI 6115/6120 Devices) Use the following alternativeparameters: rate : 20000.0sampsPerChan : 200008.(12-Bit E Series Devices) Configure dither to be on. It is accessedthrough a property node.9.Start the acquisition using DAQmxStartTask (DAQmx Start Task VI ).NI-DAQ Function CallLabVIEW Block DiagramCallDAQmxCfgSampClkTimingwith the following parameters:taskHandle : taskHandle source : NULL rate : 100000.0 activeEdge :DAQmx_Val_RisingsampleMode:DAQmx_Val_FiniteSampssampsPerChan : 10000NI-DAQ Function Call LabVIEW Block DiagramCallDAQmxSetAIDitherEnablewith the following parameters:taskHandle : taskHandle channel []:MyVoltageChannel bool32: TRUENI-DAQ Function Call LabVIEW Block DiagramCall DAQmxStartTask with the following parameter:taskHandle : taskHandle10.Acquire 10,000 points of voltage data using DAQmxReadAnalogF64(DAQmx Read VI ). If you are calibrating NI 6115/6120 orPCI-MIO-16XE-50 (NI 6011E) devices, acquire 20,000 points of voltage data.11.Average the voltage values that you acquired. Compare the resultingaverage to the upper and lower limits listed in the table. If the result is between these values, the device passes the test.12.Clear the acquisition using DAQmxClearTask(DAQmx Clear Task VI ).13.For E/M/B Series devices, repeat steps 4 through 12 until all valueshave been verified. For S Series devices, repeat steps 4 through 12 for all channels and all values.14.Disconnect the calibrator from the device.You have finished verifying the analog input levels on your device.NI-DAQ Function CallLabVIEW Block DiagramCallDAQmxReadAnalogF64 with the following parameters:taskHandle : taskHandle numSampsPerChan : –1 timeout : 10.0 fillMode :DAQmx_Val_GroupByChannel readArray : dataarraySizeInSamples : 10000 sampsPerChanRead : &read reserved : NULLNI-DAQ Function CallLabVIEW Block DiagramCall DAQmxClearTask with the following parameter:taskHandle : taskHandleAnalog Output VerificationThis procedure checks the performance of the analog output. Skip this step if the device you are calibrating does not have analog output circuitry. Check measurements using the following procedure:1.Most E/S/M/B Series devices have two analog outputs, AO 0 and AO 1. Some M Series devices have four analog outputs. This test checks all analog output channels. Connect your DMM to AO 0 as shown in Table 3.For M Series devices with four analog outputs, AO 0 and AO 1 are on Connector 0 and AO 2 and AO 3 are on Connector 1.2.Choose the table from the Device Test Limits section that corresponds to the device you are verifying. This table shows all acceptable settings for the device. NI recommends that you verify all ranges, although you may want to save time by checking only the ranges used in your application.3.Create a task using DAQmxCreateTask .4.Add an AO voltage task using DAQmxCreateAOVoltageChan (DAQmx Create Virtual Channel VI ) and configure the channel, AO 0. Use the tables in the Device Test Limits section to determine the minimum and maximum values for your device.Table 3. Connections to Analog OutputsAnalog OutputDMM Positive Input *DMM Negative Input *AO 0Connector 0, AO 0 (pin 22)Connector 0, AO GND (pin 55)AO 1Connector 0, AO 1 (pin 21)Connector 0, AO GND (pin 55)AO 2Connector 1, AO 2 (pin 22)Connector 1, AO GND (pin 55)AO 3Connector 1, AO 3 (pin 21)Connector 1, AO GND (pin 55)* Pin numbers are given for 68-pin connectors only. If you are using a BNC, 32-pin, 37-pin, or 100-pin connector, refer to your device user documentation for signal connection locations.NI-DAQ Function CallLabVIEW Block DiagramCall DAQmxCreateTask with the following parameters:taskName : MyAOVoltageTask taskHandle : &taskHandleLabVIEW does not require this step.5.Start the generation using DAQmxStartTask (DAQmx Start Task VI ).6.Write a voltage to the AO channel using DAQmxWriteAnalogF64 (DAQmx Write VI ).7.Compare the resulting value shown by the DMM to the upper and lower limits in the table. If the value is between these limits, the device passes the test.NI-DAQ Function CallLabVIEW Block DiagramCallDAQmxCreateAOVoltageChan with the following parameters:taskHandle: taskHandle physicalChannel : dev1/aoO nameToAssignToChannel :AOVoltageChannel minVal : –10.0 maxVal : 10.0units : DAQmx_Val_Volts customScaleName : NULLNI-DAQ Function Call LabVIEW Block DiagramCall DAQmxStartTask with the following parameters:taskHandle : taskHandleNI-DAQ Function Call LabVIEW Block DiagramCall DAQmxWriteAnalogF64 with the following parameters:taskHandle : taskHandle numSampsPerChan : 1 autoStart : 1 timeout : 10.0 dataLayout :DAQmx_Val_GroupByChannel writeArray : &datasampsPerChanWritten :&samplesWritten reserved : NULL8.Clear the acquisition using DAQmxClearTask (DAQmx Clear Task VI ).9.Repeat steps 3 through 8 until all values have been tested.10.Disconnect the DMM from AO 0, and reconnect it to AO 1, making theconnections shown in Table 3.11.Repeat steps 3 through 10 for all AO channels on the device.12.Disconnect your DMM from the device.You have finished verifying the analog output levels on your device.Counter VerificationThis procedure verifies the performance of the counter. E/S/M/B Series devices have only one timebase to verify, so only Counter 0 needs to be checked. It is not possible to adjust this timebase, so only verification can be performed. Perform checks using the following procedure.1.Connect your counter positive input to CTR 0 OUT (pin 2) and your counter negative input to D GND (pin 35).2.Create a task using DAQmxCreateTask .3.Add a counter output channel to the task usingDAQmxCreateCOPulseChanFreq (DAQmx Create Virtual Channel VI ) and configure the channel.NI-DAQ Function CallLabVIEW Block DiagramCall DAQmxClearTask with the following parameter:taskHandle : taskHandleNI-DAQ Function Call LabVIEW Block DiagramCall DAQmxCreateTask with the following parameters:taskName :MyCounterOutputTask taskHandle : &taskHandleLabVIEW does not require this step.4.Configure the counter for continuous square wave generation using DAQmxCfgImplicitTiming (DAQmx Timing VI ).5.Start the generation of a square wave using DAQmxStartTask (DAQmx Start Task VI ).The device begins to generate a 5 MHz square wave when the DAQmxStartTask function completes execution. 6.Compare the value read by your counter to the test limits shown on the device table. If the value falls between these limits, the device passes the test.NI-DAQ Function CallLabVIEW Block DiagramCallDAQmxCreateCOPulseChanFreqwith the following parameters:taskHandle : taskHandle counter : dev1/ctr0nameToAssignToChannel :CounterOutputChannel units : DAQmx_Val_HzidleState : DAQmx_Val_Low initialDelay : 0.0 freq : 5000000.0 dutyCycle : .5NI-DAQ Function Call LabVIEW Block DiagramCallDAQmxCfgImplicitTimingwith the following parameters:taskHandle : taskHandle sampleMode :DAQmx_Val_ContSamps sampsPerChan : 10000NI-DAQ Function Call LabVIEW Block DiagramCall DAQmxStartTask with the following parameter:taskHandle : taskHandle7.Stop the generation using DAQmxStopTask (DAQmx Stop Task VI ).8.Clear the generation using DAQmxClearTask (DAQmx Clear Task VI ).9.Disconnect the counter from your device.You have verified the counter on your device.E/S/M/B Series Adjustment ProcedureUse the E/S/M/B Series adjustment procedure to adjust the analog input and output calibration constants. At the end of each calibration procedure, these new constants are stored in the external calibration area of the EEPROM. These values are password-protected, which prevents theaccidental access or modification of any calibration constants adjusted by the metrology laboratory. The default password is NI .Perform adjustment of the device with a calibrator using the following procedure.1.The calibrator connections depend on the resolution of the device you are calibrating. Refer to Table 4 to determine connections between the device and the calibrator.NI-DAQ Function CallLabVIEW Block DiagramCall DAQmxStopTaskwith the following parameter:taskHandle : taskHandleNI-DAQ Function CallLabVIEW Block DiagramCall DAQmxClearTask with the following parameter:taskHandle : taskHandle2.Set your calibrator to output a voltage of 3.75 V for the NI 6010, 5.0 V for the NI 6120, 4.5 V for the NI 6143, and 7.50 V for all other devices.Table 4. Calibrator ConnectionsDevice Connections *12-bit E Series•Connect the positive output of the calibrator to AI 8 (pin 34).•Connect the negative output of the calibrator to AI SENSE (pin 62).•Connect AO 0 (pin 22) line to AI 0 (pin 68).•If your calibrator and computer are floating with respect to each other, connect the negative output of the calibrator to AI SENSE (pin 62) and AI GND (pin 29).•If you are using the E/M/S Series calibration hardware adapter, connect the device as described in the E/M/S Series Calibration Hardware Adapter Installation Guide .16-bit E Series •Connect the positive output of the calibrator to AI 0 (pin 68).•Connect the negative output of the calibrator to AI 8 (pin 34).•If your calibrator and computer are floating with respect to each other, connect the negative output of the calibrator to the AI GND line (pin 32) and AI 8 (pin 34).•If you are using the E/M/S Series calibration hardware adapter, connect the device as described in the E/M/S Series Calibration Hardware Adapter Installation Guide .16-bit M Series 18-bit M SeriesS Series•Connect the positive output of the calibrator to AI 0 + (pin 68).•Connect the negative output of the calibrator to AI 0 – (pin 34)•If your calibrator and computer are floating with respect to each other, connect the negative output of the calibrator to the AI GND line (pin 32) and AI 0 – (pin 34).•If you are using the E/M/S Series calibration hardware adapter, connect the device as described in the E/M/S Series Calibration Hardware Adapter Installation Guide .* Pin numbers are given for 68-pin connectors only. If you are using a BNC, 32-pin, 37-pin, or 100-pin connector, refer to your device user documentation for signal connection locations.3.Open a calibration session on your device using DAQmxInitExtCal (DAQmx Initialize External Calibration VI ). The default password is NI .4.Perform an external calibration adjustment usingDAQmx X SeriesCalAdjust (DAQmx Adjust X -Series Calibration VI ), where X is the letter of the device series.Note (NI 6010 Devices) Use DAQmxMSeriesCalAdjust (DAQmx Adjust M-SeriesCalibration VI ).Note (NI 6013/6014/6015/6016 Devices) Use DAQmxESeriesCalAdjust (DAQmx AdjustE-Series Calibration VI ).NI-DAQ Function CallLabVIEW Block DiagramCall DAQmxInitExtCal with the following parameters:deviceName : dev1 password : NIcalHandle : &calHandleNI-DAQ Function CallLabVIEW Block DiagramCallDAQmx X SeriesCalAdjustwith the followingparameters:calHandle : calHandle referenceVoltage : 7.55.Save the adjustment to the EEPROM, using DAQmxCloseExtCal (DAQmx Close External Calibration ). This function also saves the date, time, and temperature of the adjustment to the onboard memory.Note If the device fails the calibration procedure, no constants will be written to theEEPROM.6.Disconnect the calibrator from the device.The device is now calibrated with respect to your external source.After calibrating the device, you may want to verify the analog input and output operation. To do this, repeat the E/S/M/B Series Verification Procedure section.Device Test LimitsThe tables in this section list the specifications for E/S/M/B Series devices. The specifications are divided into analog input, analog output, and counter/timer tables of values.The tables display the specifications for both 1-year and 24-hourcalibration intervals. The 1-year limits display the specifications that the devices should meet if it has been one year between calibrations. When a device has been calibrated with an external source, the values shown in the 24-hour tables are the valid specifications.Note NI 6122, NI 6123, NI 625x , and NI 628x devices have 2-year and 24-hourcalibration intervals.NI-DAQ Function CallLabVIEW Block DiagramCall DAQmxCloseExtCal with the following parameters:calHandle : calHandle action : DAQmx_Val_Action_Commit。
G2540xs L2+ Managed Switch Quick Start Guide
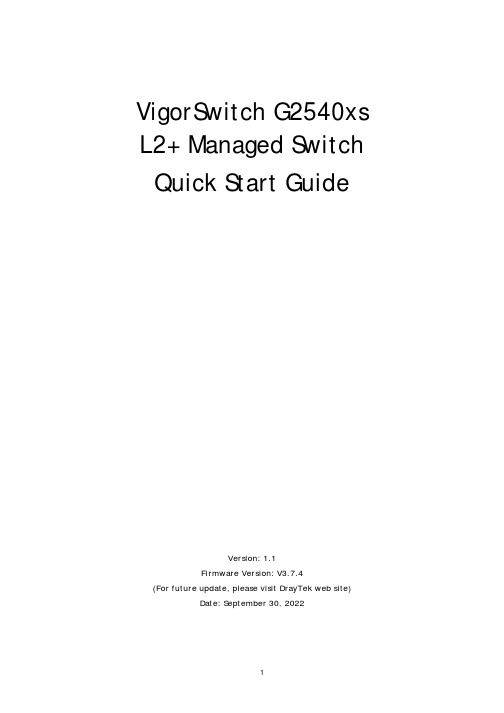
VigorSwitch G2540xs L2+ Managed Switch Quick Start GuideVersion: 1.1Firmware Version: V3.7.4(For future update, please visit DrayTek web site)Date: September 30, 20221. P a c k a g e C o n t e n tVigorSwitchQuick Start GuideRack Mount Kit (brackets)Console CableThe type of the power cord depends on the country that the switch will be installed.UK-type Power CordEU-type Power CordUSA/Taiwan-type Power CordAU/NZ-type Power CordIf any of these items is found missing or damaged, please contact your local supplier for replacement.2.P a n e l E x p l a n a t i o n3.H a r d w a r e I n s t a l l a t i o nThis section will guide you to install the switch through hardware connection and configure the switch’s settings through web browser.3.1N e t w o r k C o n n e c t i o nBefore starting to configure the switch, you have to connect your devicescorrectly.Use the Ethernet cable(s) to connect None-PoE devices to the Vigor switch.All device ports are in the same local area network.3.2R a c k-M o u n t e d I n s t a l l a t i o nThe switch can be installed easily by using rack mount kit.1.Fasten the rack mount kit on both sides of theVigorSwitch using specific screws.2.Then, install the VigorSwitch (with rack mount kit)on the 19-inch chassis by using other four screws.4.S o f t w a r e C o n f i g u r a t i o nBefore using the switch, perform the following steps:1.Set up a physical path between the configured the switch and a PC by aqualified UTP Cat. 5e cable with RJ-45 connector.If a PC directly connects to the switch, you have to setup the same subnetmask for PC and the switch. Default values of the managed switch are listed as follows:IP Address 192.168.1.224Subnet Mask 255.255.255.0DHCP Client Enabled (On)Username adminPassword admin2.After configuring correct IP address on your PC, open your web browser andaccess switch's IP address.The home page of VigorSwitch will be shown as below:C u s t o m e r S e r v i c eIf the switch cannot work correctly after trying many efforts, please contact your dealer for further help right away. For any questions, please feel free to send ***************************.GPL Notice This DrayTek product uses software partially or completely licensed under the terms of the GNU GENERAL PUBLIC LICENSE. The author of the softwaredoes not provide any warranty. A Limited Warranty is offered on DrayTekproducts. This Limited Warranty does not cover any software applications orprograms.To download source codes please visit:GNU GENERAL PUBLIC LICENSE:https:///licenses/gpl-2.0Version 2, June 1991For any question, please feel free to contact DrayTek technical support at****************************************.B e a R e g i s t e r e d O w n e rWeb registration is preferred. You can register your Vigor router viahttps://.F i r m w a r e&T o o l s U p d a t e sDue to the continuous evolution of DrayTek technology, all switches will be regularly upgraded. Please consult the DrayTek web site for more information on newest firmware, tools and document s. https://EU Declaration of ConformityWe DrayTek Corp. , office at No.26, Fushing Rd, Hukou, Hsinchu Industrial Park, Hsinchu 303, Taiwan, declare under our sole responsibility that the product●Product name: 48+6 ports 10G up-link Switch●Model number: VigorSwitch G2540xs●Manufacturer: DrayTek Corp.●Address: No.26, Fushing Rd, Hukou, Hsinchu Industrial Park, Hsinchu 303, Taiwan.is in conformity with the relevant Union harmonisation legislation:EMC Directive 2014/30/EU, Low Voltage Directive 2014/35/EU and RoHS 2011/65/EU with reference to the following standardsStandard Version / Issue dateEN 550322015+AC:2016 Class AEN 61000-3-22014 Class AEN 61000-3-32013EN 550352017EN 62368-12014 +A11:2017EN IEC 63000:2018 2018Hsinchu November 25, 2019Calvin Ma /President .(place) (date) (Legal Signature)Declaration of ConformityWe DrayTek Corp. , office at No.26, Fushing Rd, Hukou, Hsinchu Industrial Park, Hsinchu 303, Taiwan, declare under our sole responsibility that the product●Product name: 48+6 ports 10G up-link Switch●Model number: VigorSwitch G2540xs●Manufacturer: DrayTek Corp.●Address: No.26, Fushing Rd, Hukou, Hsinchu Industrial Park, Hsinchu 303, Taiwan●Importer: CMS Distribution Ltd: Bohola Road, Kiltimagh, Co Mayo, Irelandis in conformity with the relevant UK Statutory Instruments:The Electromagnetic Compatibility Regulations 2016 (SI 2016 No.1091), The Electrical Equipment (Safety) Regulations 2016 (SI 2016 No.1101), and The Restriction of the Use of Certain Hazardous Substances in Electrical and Electronic Equipment Regulations 2012 (SI 2012 No. 3032) with reference to the following standards:Standard Version / Issue dateEN 550322015+AC:2016 class AEN 61000-3-22014EN 61000-3-32013EN 550352017EN 62368-12014+A11:2017EN IEC 63000:2018 2018Hsinchu2nd July, 2021Calvin Ma / President . (Place) (Date) (Legal Signature)Copyrights © All rights reserved. This publication contains information that is protected by copyright. No part may be reproduced, transmitted, transcribed, stored in a retrieval system, or translated into anylanguage without written permission from the copyright holders.Trademarks The following trademarks are used in this document:●Microsoft is a registered trademark of Microsoft Corp.●Windows 8, 10, 11 and Explorer are trademarks of Microsoft Corp.●Apple and Mac OS are registered trademarks of Apple Inc.●Other products may be trademarks or registered trademarks of their respectivemanufacturers.Safety Instructions ●Read the installation guide thoroughly before you set up the switch.●The switch is a complicated electronic unit that may be repaired only be authorized andqualified personnel. Do not try to open or repair the switch yourself.●Do not place the switch in a damp or humid place, e.g. a bathroom.●The switch should be used in a sheltered area, within a temperature range of 0 to +45Celsius.●Do not expose the switch to direct sunlight or other heat sources. The housing andelectronic components may be damaged by direct sunlight or heat sources.●Do not deploy the cable for LAN connection outdoor to prevent electronic shock hazards.●Keep the package out of reach of children.●When you want to dispose of the switch, please follow local regulations on conservation ofthe environment.Warranty We warrant to the original end user (purchaser) that the device will be free from any defects in workmanship or materials for a period of two (2) years from the date of purchase from the dealer.Please keep your purchase receipt in a safe place as it serves as proof of date of purchase. Duringthe warranty period, and upon proof of purchase, should the product have indications of failuredue to faulty workmanship and/or materials, we will, at our discretion, repair or replace thedefective products or components, without charge for either parts or labor, to whatever extentwe deem necessary tore-store the product to proper operating condition. Any replacement willconsist of a new or re-manufactured functionally equivalent product of equal value, and will beoffered solely at our discretion. This warranty will not apply if the product is modified, misused,tampered with, damaged by an act of God, or subjected to abnormal working conditions. Thewarranty does not cover the bundled or licensed software of other vendors. Defects which do notsignificantly affect the usability of the product will not be covered by the warranty. We reservethe right to revise the manual and online documentation and to make changes from time to timein the contents hereof without obligation to notify any person of such revision or changes. Regulatory InformationFederal Communication Commission Interference StatementThis equipment has been tested and found to comply with the limits for a Class A digital device, pursuant to Part 15 of the FCC Rules. These limits are designed to provide reasonable protection against harmful interference in a residential installation. This equipment generates, uses and can radiate radio frequency energy and, if not installed and used in accordance with the instructions, may cause harmful interference to radio communications. However, there is no guarantee that interference will not occur in a particular installation. If this equipment does cause harmful interference to radio or television reception, which can be determined by turning the equipment off and on, the user is encouraged to try to correct the interference by one of the following measures:●Reorient or relocate the receiving antenna.●Increase the separation between the equipment and receiver.●Connect the equipment into an outlet on a circuit different from that to which the receiver is connected.●Consult the dealer or an experienced radio/TV technician for help.This device complies with Part 15 of the FCC Rules. Operation is subject to the following two conditions:(1) This device may not cause harmful interference, and(2) This device may accept any interference received, including interference that may cause undesired operation. Caution: Any changes or modifications not expressly approved by the party responsible for compliance could void the user's authority to operate the equipment.More update, please visit .。
达纳特尔 TM 900 900M 系列测试设备操作手册说明书
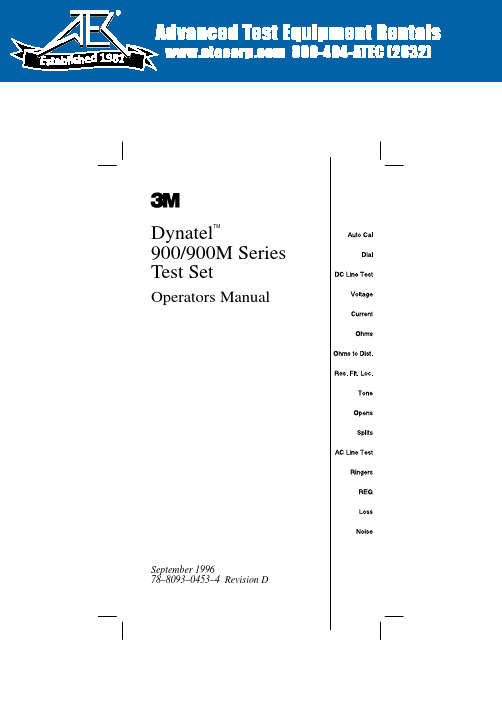
Dynatel TM900/900M Series Test SetOperators ManualSeptember 199678–8093–0453–4 Revision DAdvanced Test Equipment Rentals 800-404-ATEC (2832)®E s t a b l i s h e d 1981SpecificationsSection 3Page 723.965/965M Subscriber Loop AnalyzerA.MeasurementsFunction Range Resolution Accuracy AC Voltage:0 to 75 VAC 0.1V 0.7V 75 to 250 VAC 1.0V 3%DC Voltage:0 to 100 VDC 0.1V 0.5V 100 to 350 VDC 1.0V 3%DC Current:0 to 100 mA DC 0.1 mA 0.3 mA (Zin = 430 ohms)Resistance 1:0 to 100 Mohms 100 ohms 1% @ 50 kohms @ 50 kohms Loss:–40 to +10 dBm 0.1 dB 0.2 dB(Zin = 600 ohms)200 to 5,000 Hz Noise Metallic 2:10 to 50 dBrnC 0.1 dB 0.5 dB0 to 10 dBrnC 0.3 dB 2.0 dB(Zin = 600 ohms)Noise to Ground:40 to 100 dBrnC 0.1 dB 0.5 dB (Zin = 600 ohms)Longitudinal Balance with Tone Option 3:62 to 51 dB 0.1 dB 2.0 dB 51 to 40 dB 0.1 dB 1.0 dB Opens 1:(normal mode)0 to 9.99 kft 10 ft @ 10 kft+1%10k ft to 100k ft 100 ft +1/–10%0 to 30000 m 3 m @ 500 m 1.5 m ±1%@ 500 m Tolerance to Leakage, Normal Mode: >15 kohm to ground / 190kohm to battery Opens 1:(special mode)0 to 999 ft 1 ft+1%1 kft to 10 kft 100 ft @ 10 kft +1/–10%0 to 30000 m 3 m @ 500 m 6m ±1%@ 500 m Tolerance to Leakage, Special Mode: >1200 ohms to ground / 18 kohms to battery Frequency Measurement:20 to 20,000 Hz 1 Hz 2 Hz (during Loss, single frequency only)SpecificationsSection 3Page 73Measurements continued...Function Range Resolution Accuracy Ground Resistance:0 to 500 ohms 1 Ohm 3 ohms Loop and C.O.Resistance:0 to 5000 ohms 1 Ohm +10% +50 ohms (read through the REG key assuming on-hook resistance is known)Caller I.D.Option:–4 dBm to –32 dBmNote:1Perform a self-calibration before taking the readings.2C-message specifications have an additional frequency-dependent tolerance. Refer to “IEEE Standard 743-1984.”The 965/965M far exceeds these tolerances. For most frequencies the total error is less than 0.7 dB.3The optional longitudinal balance function obtains a result in agreement with “IEEE STANDARD 455-1985 Standard Test Prodedure for Measuring Longitudinal Balance for Telephone Equipment Operating in the Voice Band” at the specified tolerance for power influence less than approximately 80 dBrnc. When power influence is above 80 dBrnc, the test set reverts to a hybrid of the IEEE method and the method of calculating longitudinal balance by taking the difference between power influence andnoise metallic.4The splits function does not have accuracy tolerances.B.Resistance Fault LocateNote: Accuracy is dependent on power influence noise; the resistance fault specifications are for low noise situations.Function Range Resolution Accuracy 1,2Fault Range:Up to 30 MohmsResistance to Fault:30 to 9 ohms 0.01 Ohm +0.1% RTS +0.01 Ohm (@ 70° no noise)10 to 99 ohms 0.01 Ohm +0.1% RTS+0.01 Ohm100 to 999 ohms 0.1 Ohm +0.2% RTS 1k to 7 kohms 1.0 Ohm +1.0% RTSResistance to Distance Conversion Resolution:3 1 ft to 1,000 ft 0.1 ft 1k ft to 10k ft 1.0 ft10k ft to 100k ft 10.0 ft1 to 99 m 0.1 m 100 to 999 m 1.0 m1000 to 30000 m10.0 m Temperature Sensor:0° to 140° F 1° F +2° F –18° to 60° C .5° C +1° C Noise Immunity:7VAC limit for all frequenciesSpecificationsSection 3Page 74Note:1See figures next page for accuracies. All resistance to faultmeasurement accuracies have an added factor of (2 x 10 -8) RF ohms.2Single pair hookup measurement accuracy is strictlydependent on whether the reference pair is exactly the same electrical length as the faulted pair. Accuracies are doubled for single pair hookup.3Accuracy depends on correct temperature setting as well as gauge accuracy of copper. The temperature can be read by the built-in sensor or can be operator-entered.2 –----1.5–----1 –----.5 –----0 – Accuracy in ohms for Various Fault ResistancesMaximum Error in ohms Resistance to Strap in ohms2102040420 Mohms10 Mohms<1 Mohm30 Mohms100400100020010510152025303540010002000300040005000600070008000900010000Maximum Error in Feet Accuracy for 24 Gauge for Various Fault Resistances Distance to strap in Feet30 Mohms20 Mohms10 Mohms< 1 MohmSpecificationsSection 3Page 75/(76 blank)C.OutputsTones Frequency Level Impedance Identification:577.5 Hz 6V PK to PK 100 ohms (Current limited to 6 mA)Precision Tones:404, 1004, 0 dBm + 0.2 dB 600 Ohm 2804 +1 Hz Harmonic distortion: <45 dB (up to 10th harmonic)User-Entered Tone:Frequency Resolution Frequency Amplitude Range Accuracy Accuracy 2 to 100 Hz +0.1%+1%+1dB100 to 1 kHz +1.0%+1%+1dB1 kHz to 10 kHz +3.0%+1%+1dB 10 kHz to 20 kHz +3.0%+1%+3dBHarmonic distortion: <45 dB (up to 10th harmonic)Dial Frequency Remarks DTMF:Standard 100 msec on 100 msec off meets CCITT Q.23 Standard for frequency and amplitude i.e. +1 Hz @ –10 dBm +1 dBDial Pulse:10 pulses 60 msec break per sec 40 msec make R–T600 msec between digits D.EnvironmentOperation StorageTemperature:0° to +140° F –40° to 165° F–18° to 60° C –40° to 74° CHumidity:0 to 100%0 to 100% (condensing) (condensing)Altitude:0 to 15,000 ft 0 to 40,000 ft 0 to 5000 m 0 to 12000 m Shock:Can withstand a drop onto a wood surface from a distance of four ft (1.25 m)E.DimensionsHeight 7.0 in/ 18 cmWidth 10.5 in/ 27 cmDepth 7.5 in/ 19 cmWeight 7.5 lbs/ 3.4 kg Cord length 5 ft/ 1.5 mF. Battery PowerThe operating time between battery change-out or charges depends on temperature of set and operation modes used.For non-rechargeable batteries typical operating time is about 200hours between battery change-out.For rechargeable batteries typical operating time is about 80 hours between charges.。
Arista 7020 Series 1 RU-Gen 3 Data Center Switches

Chapter5 Configuring the SwitchArista switches ship from the factory in Zero Touch Provisioning(ZTP)mode.ZTP configures the switchwithout user intervention by downloading a startup configuration file or a boot script from a locationspecified by a DHCP server.To manually configure a switch,ZTP is bypassed.The initial configurationprovides one username(admin)accessible only through the console port because it has no password.When bypassing ZTP,initial switch access requires logging in as admin,with no password,through theconsole port.Then you can configure an admin password and other password protected usernames.This manual configuration procedure cancels ZTP mode,logs into the switch,assigns a password toadmin,assigns an IP address to the management port,and defines a default route to a networkgateway.Step1Provide power to the switch(Section4.1).Step2Connect the console port to a PC(Section4.2).As the switch boots without a startup-config file,it displays the following through the console:The device is in Zero Touch Provisioning mode and is attempting todownload the startup-config from a remote system. The device will notbe fully functional until either a valid startup-config is downloadedfrom a remote system or Zero Touch Provisioning is cancelled. To cancelZero Touch Provisioning, login as admin and type 'zerotouch cancel'at the CLI.localhost login:Step3Log into the switch by typing admin at the login prompt.localhost login:adminStep4Cancel ZTP mode by typing zerotouch cancel.IMPORTANT:This step initiates a switch reboot.localhost>zerotouch cancelStep5After the switch boots,log into the switch again by typing admin at the login prompt.Arista EOSlocalhost login:adminLast login: Fri Mar 15 13:17:13 on consoleStep6Enter global configuration mode.localhost>enablelocalhost#configStep7Assign a password to the admin username with the username secret command.localhost(config)#username admin secret pxq123Step8Configure a default route to the network gateway.localhost(config)#ip route 0.0.0.0/0 192.0.2.1Step9Assign an IP address(192.0.2.8/24in this example)to an Ethernet management port.localhost(config)#interface management 1localhost(config-if-Ma1/1)#ip address 192.0.2.8/24Step10Save the configuration by typing write memory or copy running-config startup-config.localhost#copy running-config startup-configWhen the management port IP address is configured,use this command to access the switch from a host,using the address configured in step9:**************.2.8Refer to the Arista Networks User Manual for complete switch configuration information.。
Dell Data Protection 控制台用户指南.pdf_1700898517.963764
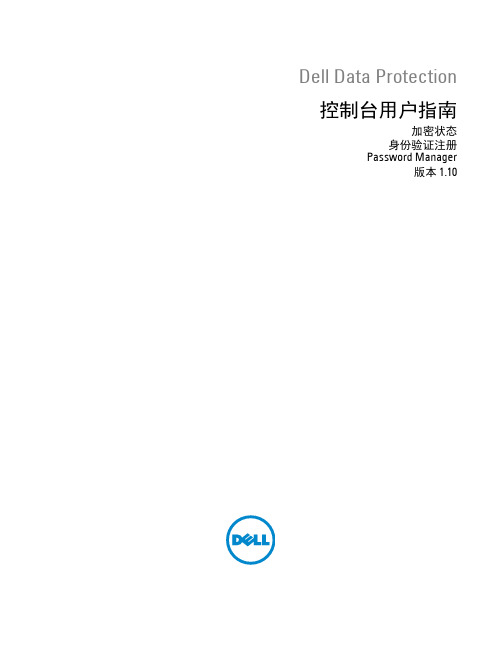
Dell Data Protection 控制台用户指南加密状态身份验证注册Password Manager版本 1.10© 2016 Dell Inc.Dell Data Protection | Encryption、Dell Data Protection | Endpoint Security Suite、Dell Data Protection | Endpoint Security Suite Enterprise、Dell Data Protection | Security Tools 和 Dell Data Protection | Cloud Edition 整套文件中使用的注册商标和商标:Dell™ 和 Dell 徽标、Dell Precision™、OptiPlex™、ControlVault™、Latitude™、XPS®和 KACE™ 是 Dell Inc.的商标。
Cylance®和 Cylance 徽标是 Cylance, Inc.在美国和其他国家/地区的注册商标。
McAfee®和 McAfee 徽标是 McAfee, Inc.在美国和其他国家/地区的商标或注册商标。
Intel®、Pentium®、Intel Core Inside Duo®、Itanium®和 Xeon®是 Intel Corporation 在美国和其他国家/地区的注册商标。
Adobe®、Acrobat®和 Flash®是 Adobe Systems Incorporated 的注册商标。
Authen Tec®和 Eikon®是 Authen Tec 的注册商标。
AMD®是 Advanced Micro Devices, Inc.的注册商标。
Microsoft®、Windows®和 Windows Server®、Internet Explorer®、MS-DOS®、Windows Vista®、MSN®、ActiveX®、Active Directory®、Access®、ActiveSync®、BitLocker®、BitLocker To Go®、Excel®、Hyper-V®、Silverlight®、Outlook®、PowerPoint®、OneDrive®、SQL Server®和 Visual C++®是 Microsoft Corporation 在美国和/或其他国家/地区的商标或注册商标。
思科商务 350 系列托管交换机快速入门指南说明书
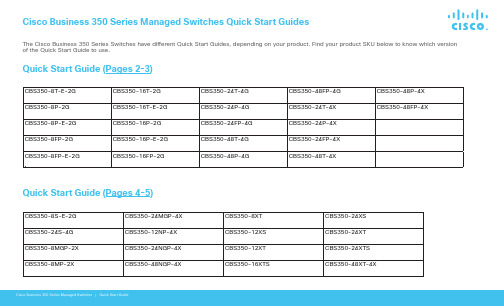
Cisco Business 350 Series Managed Switches Quick Start GuidesThe Cisco Business 350 Series Switches have different Quick Start Guides, depending on your product. Find your product SKU below to know which version of the Quick Start Guide to use.Quick Start Guide (Pages 2-3)Quick Start Guide (Pages 4-5)CBS350-8T-E-2G CBS350-16T-2G CBS350-24T-4G CBS350-48FP-4G CBS350-48P-4X CBS350-8P-2G CBS350-16T-E-2G CBS350-24P-4G CBS350-24T-4X CBS350-48FP-4XCBS350-8P-E-2G CBS350-16P-2G CBS350-24FP-4G CBS350-24P-4X CBS350-8FP-2G CBS350-16P-E-2G CBS350-48T-4G CBS350-24FP-4X CBS350-8FP-E-2GCBS350-16FP-2GCBS350-48P-4GCBS350-48T-4XCBS350-8S-E-2G CBS350-24MGP-4X CBS350-8XT CBS350-24XS CBS350-24S-4G CBS350-12NP-4X CBS350-12XS CBS350-24XT CBS350-8MGP-2X CBS350-24NGP-4X CBS350-12XT CBS350-24XTS CBS350-8MP-2XCBS350-48NGP-4XCBS350-16XTSCBS350-48XT-4XCisco Business 350 Series Managed SwitchesThank you for choosing the Cisco Business 350 Series Switch.These switches are designed to be operational right out of the box as standard switches.In the default configuration, the switch forwards packets between the connected devices afterpowering up.Cisco Business 350 Series Managed Switches | Quick Start GuideQUICK START GUIDEFirst, You’ll Need...●RJ-45 Ethernet cables (Category 5e or higher)for connecting network devices●Tools for mounting the hardware●Computer with an Ethernet port (or adapter) and a web browser(Firefox, Chrome, Safari, or Edge)● A mobile device with Wi-Fi capability (to set up using the mobile app)Get ConfiguredGet Connected©2021 Cisco and/or its affiliates. All rights reserved. Cisco and the Cisco logo are trademarks or registered trademarks of Cisco and/or its affiliates in the U.S. and other countries. To view a list of Cisco trademarks, go to this URL: https:// /go/trademarks. Third-party trademarks mentioned are the property of their respective owners. The use of the word partner does not imply a partnership relationship between Cisco and any other company. (1110R)Plug the power cord of the switch into an outlet.Cisco Business 350 Series Managed SwitchesThank you for choosing the Cisco Business 350 Series Switch.These switches are designed to be operational right out of the box as standard switches.In the default configuration, the switch forwards packets between the connected devices afterpowering up.4What’s in the Box●Cisco Business 350 Series SwitchCisco Business 350 Series Managed Switches | Quick Start GuideQUICK START GUIDEFirst, You’ll Need...●RJ-45 Ethernet cables (Category 5e or higher)for connecting network devices●Tools for mounting the hardware●Computer with an Ethernet port (or adapter) and a web browser(Firefox, Chrome, Safari or Edge)● A mobile device with Wi-Fi capability (to set up using the mobile app)35Get ConfiguredGet Connected©2021 Cisco and/or its affiliates. All rights reserved. Cisco and the Cisco logo are trademarks or registered trademarks of Cisco and/or its affiliates in the U.S. and other countries. To view a list of Cisco trademarks, go to this URL: https:// /go/trademarks. Third-party trademarks mentioned are the property of their respective owners. The use of the word partner does not imply a partnership relationship between Cisco and any other company. (1110R)For Cisco support and additional documentation, including mounting instructions and the Administration Guide, visit https:///go/cbs350.Preparing Your SwitchUsing the Mobile App: Connect the switch to an existing wireless network. This could be a wireless access point(shown above), wireless router, or mesh extender. You will need something to act as your DHCP server (a router or switch as shown above). Once connected, proceed to the “Get Configured” section to download the app.Using the Web User Interface (UI): Connect a computer to one of the switch ports with an Ethernet cable. Make sure your computer is on and proceed to the Web UI Setup instructions under the “Get Configured” section.MountingFor detailed mounting instructions, please see the “Get Support” section.Plug the power cord of the switch into an outlet.Scan the QR code here to download the app or go to /go/cbsapp and follow the installation instructions.Download the Cisco Business Mobile appGet Support。
4520模块中文操作手册
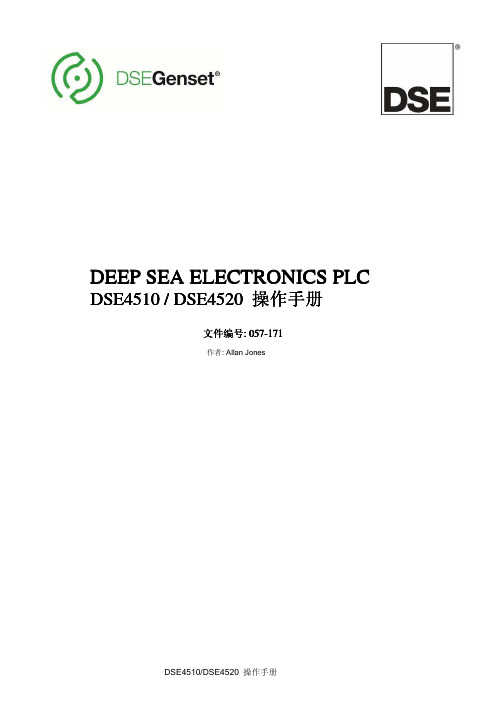
3.2 端口说明.................................................................................................................... 9
3.3 电源要求.................................................................................................................... 9
3.8 通讯端口.................................................................................................................. 15
3.9 通讯端口用法........................................................................................................... 15
本出版物设计到符号释义本出版物设计到符号释义本出版物设计到符号释义本出版物设计到符号释义
DEEP SEA ELECTRONICS PLC
DSE4510 / DSE4520 操作手册
文件编号: 057-171
作者: Allan Jones
DSE4510/DSE4520 操作手册
DSE4510/4520 操作手册
DSE商标以及名称是Deep Sea Electronics公司在英国注册的。
本出版物内所有带有注册商标标志的产品名称归各自公司所有。
Deep Sea Electronics公司保留对本文档进行修订的权利,若有改动,恕不另行通知。
Dell Update Packages 版本 7.1 用户指南说明书
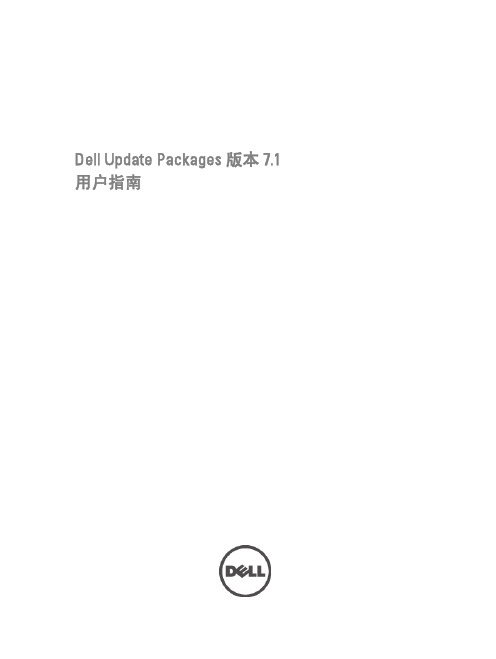
Dell Update Packages 版本 7.1用户指南注、小心和警告注: “注”表示可以帮助您更好地使用计算机的重要信息。
小心: “小心”表示可能会损坏硬件或导致数据丢失,并说明如何避免此类问题。
警告: “警告”表示可能会造成财产损失、人身伤害甚至死亡。
© 2012 Dell Inc.本文中使用的商标:Dell™、Dell 徽标、Dell Boomi™、Dell Precision ™、OptiPlex™、Latitude™、PowerEdge™、PowerVault™、PowerConnect™、OpenManage™、EqualLogic™、Compellent™、KACE™、FlexAddress™、Force10™和 Vostro™是 Dell 公司的商标。
Intel®、Pentium®、Xeon®、Core®和 Celeron®是 Intel 公司在美国和其他国家/地区的注册商标。
AMD®是 Advanced Micro Devices 公司的注册商标,AMD Opteron™、AMD Phenom™和 AMD Sempron™是 AMD (Advanced Micro Devices) 公司的商标。
Microsoft®、Windows®、Windows Server®、Internet Explorer®、MS-DOS®、Windows Vista®和 Active Directory®是微软公司在美国和/或其他国家/地区的商标或注册商标。
Red Hat®和 Red Hat® Enterprise Linux®是 Red Hat 公司在美国和/或其他国家/地区的注册商标。
Novell®和 SUSE®是 Novell 公司在美国和其他国家/地区的注册商标。
Eaton Addressable 3 Channel I O Unit ULCIO351 用户指南

Technical DataSignalling Line Circuit Style 7, Class A Supervised, Power LimitedCurrent1.14mA (nom) 1.36mA (Max)Operating Voltage (nom)24VDC (nom)Line Impedance50Ω (nom)Inputs 1, 2, 3 Contact Only Initiating Circuit Style C, Class B Supervised power limitedVoltage 8.4VDC (Max)Current 1mA (Max)Line Impedance 16Ω (Max)Trigger Resistance 5.6kΩ (nom)End Of Line Resistor22kΩ (nom)Output 1, 2, 33 Contact Set ProgrammableVoltage 24VDC (nom) 30VDC (Max) Contact Rating 1 (Max) A Resistive, PF1Switching Power 33kΩ (min)Power factor1 (nom)EnvironmentalOperating Temperature 0°C - 49 °C Humidity (Non Condensing)93% RHStandardsUL864 9th EditionCompatibilitySuitable for use with Eaton Addressable Fire SystemsPhysical CharacteristicsDimensions 180mm x 129mm x 60mmWeight0.28kg Ingress ProtectionIP65Installation1. Separate the two halves of the unit.2. Drill out (or knock out) the required cableentries in the surface mounting back-box.3. Fit the back-box in position and pass the wires into it.4. Connect the unit according to the diagram below.5. Recommended cable Type FPLP (plenum cable), Type FPLR(riser cable), or Type FPLNotes:N No addressing of the interface is required. See control panel operation for details.DescriptionSLC Field Wiring (input)Input 1, 2, 3Output 1, 2, 3Wiring Gauge 12 Max AWG 12 Max AWG 12 Max AWG Wiring ClassClass A Style 7Class B Style C NA Ground Fault Impedance0.1Ω0.1Ω0.1ΩSupervised, power limited YesYesProgrammableInpuo 1, 2, 3 Operation :Normal Standby (Default), Alarm, NAC Silenced, Alarm Reset, Trouble, supervisory ,Drill (Features programmable using PC site installer)Ouopuo 1, 2, 3 Operations: Normal Standby. AlarmNots:N 1. The end of line resistor must always be fitted, even if theinputs are unused. Installer / Service Engineer must ensure it is fitted.2. Monitored inputs can detect open circuit, short circuit orground faults3. Output relays are volt-free contacts and are not monitored,but must be connected to power limited source.4. Each I/O channel consumes a separate address and has thefacility for separate text for each channel.Soandard CNnntcoiNneTeChNICal DaTa 25-16303-A December 2018eaoNnEMEA Headquarters Route de la Longeraie 71110 Morges, Switzerland Eaton.euTEL: +44 (0) 1302 321541FAX: +44 (0) 1302 303220********************************************© 2018 EatonAll Rights ReservedEaton is a registered trademark.All trademarks are property of their respective meaoNn eltcorical Syeotme lod.Wheatley Hall Road Doncaster DN2 4NBTEL: +44 (0) 1302 303303 FAX: +44 (0) 1302 367155。
西门子 S7-300 指令列表 说明书
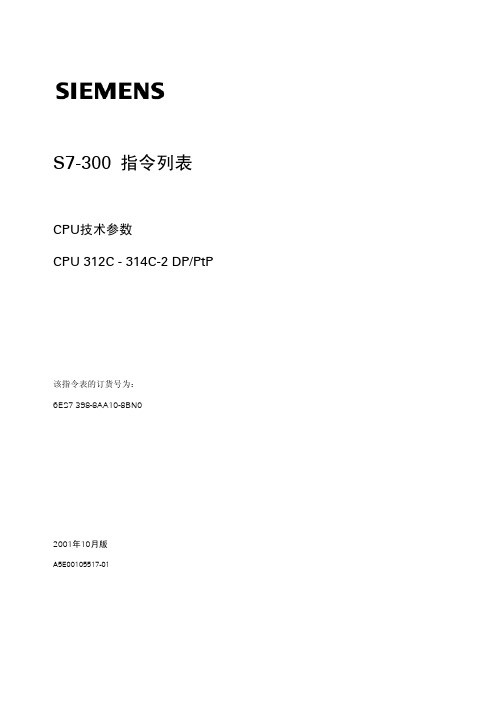
CPU技术数 CPU 312C - 314C-2 DP/PtP
该指令表的订货号为: 6ES7 398-8AA10-8BN0
2001年10月版
A5E00105517-01
西门子公司版权所有©2001。保留所有权利 未经明确的书面授权,禁止复制、传递或使用本手册或其中的内容。 违者必究。保留所有权利包括专利权、实用新型或外观设计专有权。 西门子股份有限公司 自动化与驱动集团 工业自动化系统部 邮政信箱4848,纽伦堡D- 90327
西门子股份有限公司
郑重声明 我们已核对过,本手册的内容与所述硬件和软件相符。但错误在所难 免,不能保证完全的一致。本手册中的内容将定期审查,并在下一版 中进行修正。欢迎提出改进意见。
®Siemens AG 2001 若有改动,恕不另行通知。
6ES7398-8AA10-8BN0
目录
指令表的有效范围 .............................................................................................................................................. 1 地址标识符和参数范围....................................................................................................................................... 1 缩写词和助记符..........................................................................................
Testo 350 Firmware Update Guide

testo 350 Firmware Update GuideBefore downloading the firmware, please check the firmware version of your testo 350 analyzer. Select Instrument Diagnosis, press OK / Device Information, press OK for the information screen.To download the firmware update go to Testo /firmware.html and check the downloadable firmware version. The version number must be higher than the one listed at 350 Information screen.Click on the firmware link and download the ZIP compressed file to your computer. Right click on the file and select Extract All. This will create a folder in the same directory where the ZIP file was downloaded to. The new folder will have two folders 350 Control Unit and 350 Analyzer Box with the firmware update .bin files inside. If the ZIP file doesn’t open, it might be corrupted. Try to download again.The firmware update has two steps in two stages starting with the Control Unit update first, then the update of the 350 Box. Please make sure that the right files and in the right order are selected for the update.Control Unit update: 350 Box:bootrel_v1.16.bin bootrelf_v1.16.binappcurel_v1.09.bin apboxdbg_v1.09.binUpdate preparation:1.Make sure that the Control Unit is fully charged before firmware update.2.Turn off the Control Unit, pull power plug off the 350 Box, and remove theControl Unit from the main box.Control Unit firmware update:3.Press down and hold the Up Arrow.4.Press the Power button.5.Release both buttons when the Firmware Update appears at thebottom of the screen.6.Plug in the USB cable, wait through Windows messages about installingthe new hardware.7.Open the Windows Explorer / File Manager and look for the newexternal drive letter.8.Copy the bootrel_v1.16.bin file to that drive. The drive will disconnectfor a while and reappear again.9.Copy the appcurel_v1.09.bin file to the same drive.10.The Control Unit’s screen will show the update progress. Whenfinished, disconnect the USB cable.11.After completion of the update the Control Unit will automaticallyreboot.12.Do not return Control Unit to the analyzer box.The 350 Box firmware update:1.Make sure that the Analyzer Box isunplugged; it has to be disconnectedfrom the AC and the unit should not beshowing flashing lights.2.Turn the 350 Box upside down, openthe sensors compartment plate.3.Locate the micro switch at sensor slot 3,push down and hold the button with apin or end of the paper clip.4.When holding the button down, plug inthe power cable to the AC receptor.5.When the status light start flashinggreen and red, release the paper clipfrom the micro switch, and the lightswill continue flashing.6.Connect the Analyzer Box to the computer with the USB cable and wait for the computer to recognize the Boxas an external drive (as in #5 Control Unit update).7.First copy the bootrelf_v1.16.bin file.8.After the drive letter disappears and reconnects again, copy the apboxdbg_v1.09.bin file to the external drive.9.Wait for GREEN flashing lights to signal the end of update.10.Disconnect the USB cable; pull out the power cable, and the update procedure is completed.Troubleshooting:If the Control Unit freezes and locks up, during the update, it can be reset using the paper clip.For the Control Unit use the access hole shown in the picture, and push in thepaper clip wire briefly to reset.To reset the Analyzer Box press the micro switch button at the S1 slot.。
Datenblatt-RLK-402-CN (1)

150 200 128 108 114 443 247 356 203 301 176 68000 900 170 127 201 16 M14 90 11,2 4205.150.201.000000
160 210 128 108 114 449 245 363 202 310 175 72500 900 159 121 201 16 M14 90 11,9 4205.160.201.000000
42 75 51 41 45 175 99 139 81 116 70 2900 140 252 130 37 8 M8 35 1,2 4205.042.201.000000
45 75 51 41 45 175 99 139 81 116 70 3200 140 235 141 37 8 M8 35 1,1 4205.045.201.000000
75 115 86 70 76 238 145 193 122 165 108 10500 280 164 107 73 10 M10 60 3,3 4205.075.201.000000
80 120 86 70 76 265 156 212 129 179 113 13500 339 185 123 73 12 M10 60 3,5 4205.080.201.000000
130 180 128 108 114 373 222 302 186 259 165 44200 680 147 106 201 12 M14 90 10,0 4205.130.201.000000
140 190 128 108 114 409 235 329 195 280 170 55500 794 159 117 201 14 M14 90 10,6 4205.140.201.000000
350错误代码

信息
LT:End step error temperature, driver)
(power,
可能原因/结论 CS351
LT:Motor contactor will not
128
4
CS351,LTU350/1
close
129
1 Arcnet pack too long
Permissible temperature too
Ergospin 损坏
建议方法
⇒ 在 BS350 中取消选择角度 冗余 ⇒ 更换损坏元件或同等修理
351
3 ErgoSpin:Calibration error
Ergospin 损坏
⇒ 更换损坏元件或同等修理
352
353 354
355
356
357
358 359 360 361 362 363 错误 代码
115
1 Motor identifier change
⇒ 安装合适 EC 马达
116
1 LT:CAN job log file error
⇒ 查找并更换故障元件
⇒ 重新启动,如果错误再次发
117
3 LT:CAN bus monitoring error
生
⇒ 更换损坏 LT 或相同维修
结合“561”
手柄,马达或扭矩转换器的温 ⇒ 调节/减少拧紧时间
度报警级别
手柄,电机或扭矩转换器的温
4 ErgoSpin: Temperature error
⇒ 调节/减少拧紧时间
度
⇒检查拧紧程序并按需调整
3 ErgoSpin: Overload
目标角度可能没有设扭矩监控 参照错误 1001,355,371
- 1、下载文档前请自行甄别文档内容的完整性,平台不提供额外的编辑、内容补充、找答案等附加服务。
- 2、"仅部分预览"的文档,不可在线预览部分如存在完整性等问题,可反馈申请退款(可完整预览的文档不适用该条件!)。
- 3、如文档侵犯您的权益,请联系客服反馈,我们会尽快为您处理(人工客服工作时间:9:00-18:30)。
48-1
48-2
特点
•轮毂和轴同心
•针对于轴直径在5 mm 到50 mm 之间
应用范例
安装两个胀紧套RLK350为了消除工业门驱动轴和链轮齿间的反向间隙。
在组装过程中,锁紧元件和链轮齿同心。
链轮齿能容易的排成一线,在轴和圆周轴向方向。
扭矩和轴向力的同时传输
列表中传输的扭矩M 是指轴向力F = 0 kN 时,同理,列表中的轴向力F 是指扭矩M = 0Nm 时。
如果扭矩和轴向力被同时传输,传输的扭矩和轴向力就会减少。
请参考54页到55页的技术指导。
订购示范
胀紧套RLK350,轴外径d = 50 mm :
•RLK350,尺寸50x80
零件编号:4208.050.001.000000
安装
如果轮毂不能自由的移动到右侧,例如由于轴肩,M \F \P W 和P N 的值下降37%,最小值能被减少。
见55页技术指导。
欢迎询问或要求缩紧盘RLK350的安装说明及指导。
可传输的扭矩和轴向力如49页,可能存在的公差值和要求的外形和材料特点如下表。
如超过此公差范围,请联系我们。
公差
•轴直径d 公差要求为h8•轮毂内径D 公差要求为H8表面质量
实心轴和空心轴接触面的表面粗糙度R a ≤ 3,2 μm 。
材质要求
如下所列适用于轴和轮毂:•弹性变形系数170 kN/mm 2
传输扭矩和轴向力
L 2L 1
B ød
øD H 8
ød h 8
øK m i n
N min
øD
51613,510112418211620164,01,6176551,03M2,5 100,010 4208.005.001.00000061613,510112418211620165,01,7147551,03M2,5 100,012 4208.006.001.00000071713,510,5112518221621166,51,9134551,03M2,5 100,013 4208.007.001.00000081813,510,5112618231622168,02,0113501,03M2,5 100,015 4208.008.001.00000092015,512,51329202619241812,52,8123551,04M2,5 120,020 4208.009.001.000000102015,512,51329202619241812,52,5110551,04M2,5 120,019 4208.010.001.000000112215,512,51331202819261815,02,7100501,04M2,5 120,024 4208.011.001.000000122215,512,51331202819261816,52,892501,04M2,5 120,022 4208.012.001.00000014262016,517362533243123304,3103551,84M3 160,039 4208.014.001.00000015282016,517382535243323334,494501,84M3 160,044 4208.015.001.00000016322116,517482942263925648130654,54M4 160,067 4208.016.001.00000017352520,521493244304128688124604,54M4 200,090 4208.017.001.00000018352520,521493244304128738117604,54M4 200,087 4208.018.001.00000019352520,521493244304128788111604,54M4 200,083 4208.019.001.00000020382620,52159375133473115015143759,04M5 200,100 4208.020.001.00000022402620,52161375333493116014128709,04M5 200,110 4208.022.001.00000024473225267144624058382502014775164M6 250,200 4208.024.001.00000025473225267144624058382602014175164M6 250,190 4208.025.001.000000285032252685507243654044031179100166M6 250,180 4208.028.001.00000030553225268949774369394703117595166M6 300,220 4208.030.001.00000032553225268949774369395003116495166M6 300,270 4208.032.001.000000356037303110057865077467304116395166M6 300,250 4208.035.001.000000386537303110457905082468004215490168M6 350,360 4208.038.001.000000406537303110457905082468404214790168M6 350,430 4208.040.001.0000004575443536134741136310057 1 3005715090378M8 350,630 4208.045.001.0000005080
443536
138731186310557 1 90076
184115378M8 350,700 4208.050.001.000000
49-2
49-1
尺寸
技术数据零件编号
轮毂材质的屈服强度R e [N/mm 2]可传输的扭矩
或轴向力
接触面压力
螺栓重量锁紧
大小200320500轴轮毂扭矩个数尺寸长度d D B
L 1L 2K min N min K min N min K min N min M F P W P N M S
mm mm mm mm mm mm mm mm mm mm mm Nm kN N/mm 2N/mm 2Nm mm kg。