4 ANB200SP_PM_Checklist_ Parts_service__doc_EN_111105_01_GS
Hewlett-Packard Model 355C, 355D, 355E, and 355F V
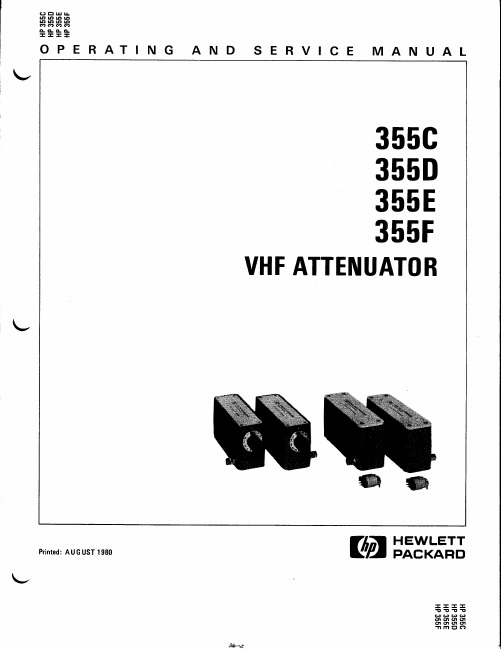
\-'"
Model355C/D/E/F
Page 3
Do not exceed the RF power rating of
0.5W auerage, or 2450W peak with a
maximum pulse width of 200 ps. Do not connect an attenuator RF input or output connector to greater than !5 Vdc.
(J luFttl!
r6Clf 6- o- o-
OPERATING
\-
AND SERVICE MANUAL
355C 355D 355E 355F
VHF ATTENUATOR
U
Printed: AU G UST 1980
\-
@@
rcE H"=&TJJ
If the attenuator must be connected to a
deuice with a potential gxeater than x5 Vdc, use a blocking capacitor.
Accessories Supplied
The 355E and 355F programmable attenuators are
trically. A procedure for checking electrical per-
formance is given under "Operator's Check" (see
PERFORMANCE TESTS). If the contents of the shipment are incomplete, if there is mechanical damage or defect, or if the instrument does not pass the electrical performance test, notify the nearest Hewlett-Packard office. If the shipping con-
Gap Checker ISA3-#L 安装说明书
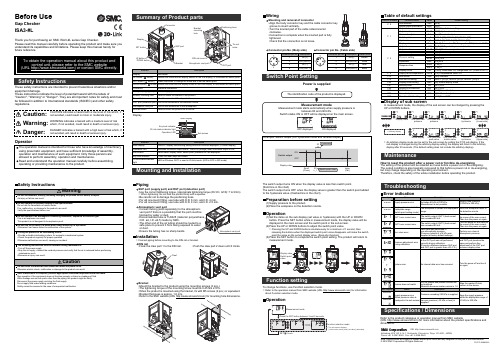
Before UseGap CheckerISA3-#LSafety InstructionsPipingSUP port (supply port) and OUT port (detection port)•Use the correct tightening torque. (Appropriate tightening torque (Rc1/8 • G1/8): 7 to 9 Nm)∗: When tightening, do not hold the product body with a spanner.•Be careful not to damage the positioning boss.•For ø6 one-touch fitting, use tube with O.D. 6 mm, and I.D. 4 mm.•For ø4 one-touch fitting, use tube with O.D. 4 mm, and I.D. 2.5 mm.Safety InstructionsMounting and InstallationThank you for purchasing an SMC ISA3-#L series Gap Checker.Please read this manual carefully before operating the product and make sure you understand its capabilities and limitations. Please keep this manual handy for future reference.These safety instructions are intended to prevent hazardous situations and/or equipment damage.These instructions indicate the level of potential hazard with the labels of"Caution", "Warning" or "Danger". They are all important notes for safety and must be followed in addition to International standards (ISO/IEC) and other safety regulations.Atmospheric vent portblocked by water or dust.O.D. ø4, I.D. ø2.5) made by SMC.or dust.•Ensure the tubing has no sharp bends.OperatorTie rod holesBracket holeBracket•Mount the bracket to the product using the mounting screws (3 pcs.).•The tightening torque of the mounting screw must be 0.45 Nm ±10%.•When the product is mounted using the bracket, fix with M5 screws (2 pcs.) or equivalent.•Bracket thickness is approx. 1.6 mm.•Refer to the SMC website (URL ) for mounting hole dimensions.Switch point valueFunction selection mode∗: The sub screen displays[ the function name ] and [ set value ] alternately.The switch output turns ON when the display value is less than switch point.(Solid line in the chart)The switch output turns OFF when the display value is greater than the switch point added to the hysteresis value. (Dashed line in the chart)To change functions, use Function selection mode.∗: Refer to the operation manual from SMC website (URL ) for information about Function selection mode.Installation∗: Connect piping before mounting to the DIN rail or bracket.DIN rail•Hook the claw part 1 to the DIN rail. •Push the claw part 2 down until it clicks.WiringMounting and removal of connector•Align the body connector key and the cable connector key groove to insert vertically.•Turn the knurled part of the cable sideconnector clockwise.•Connection is complete when the knurled part is fully tightened.Check that the connection is not loose.Switch Point SettingOperation(1)Set the items on the sub display (set value or hysteresis) with the UP or DOWN button. Press the SET button while in measurement mode, the display value will be displayed in the main screen and the switch point in the sub screen.(2)Press the UP or DOWN buttons to adjust the switch point value.∗: Pressing the UP and DOWN buttons simultaneously for a minimum of 1 second, thenreleasing the buttons when the displayed switch point value disappears, will make the switch point the same as the current display value. (Snap shot function)(3)Press the SET button to complete the switch point setting. The product will return to measurement mode.Function settingOperationDisplay of sub screenIn measurement mode, the display of the sub screen can be changed by pressing the ∗: Arbitrary displaypeak value hysteresis bottom value (Upper side)MaintenanceHow to reset the product after a power cut or forcible de-energizingThe setting of the product will be retained as it was before a power cut or de-energizing.The output condition is also basically recovered to that before a power cut or de-energizing,but may change depending on the operating environment.Therefore, check the safety of the whole installation before operating the product.Specifications / DimensionsRefer to the product catalogue or operation manual from SMC website(URL ) for more information about the product specifications and dimensions.Akihabara UDX 15F , 4-14-1, Sotokanda, Chiyoda-ku, Tokyo 101-0021, JAPAN Phone: +81 3-5207-8249 Fax: +81 3-5298-5362URL TroubleshootingConnector pin No. (Body side)Connector pin No. (Cable side)Power is suppliedPreparation before setting(1)Supply pressure to the product.(2)Place the workpiece on the detection nozzle.Note: Specifications are subject to change without prior notice and any obligation on the part of the manufacturer.© 2018 SMC Corporation All Rights Reserved Display∗: An arbitrary display mode can be set for the sub screen by setting the [F10] sub display. If the sub display is changed during the arbitrary display setting, the display will return to the arbitrary display after 30 seconds. (The default setting does not include the arbitrary display).PS ※※-OMW0010。
柔性检查作用域套件-USB 产品说明书
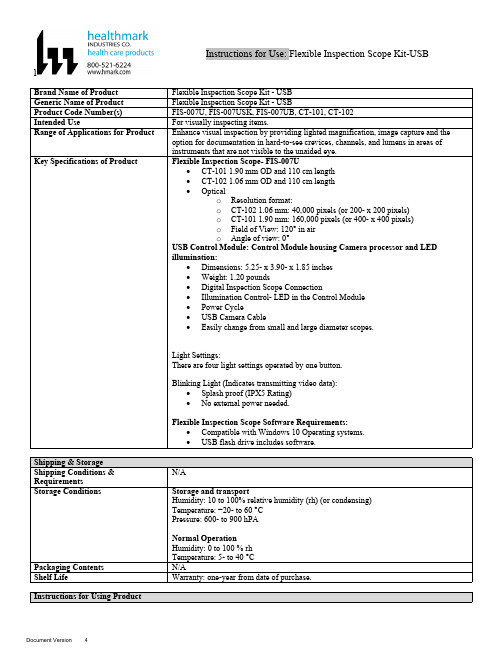
lInstructions for Use: Flexible Inspection Scope Kit-USB Brand Name of ProductFlexible Inspection Scope Kit - USB Generic Name of ProductFlexible Inspection Scope Kit - USB Product Code Number(s)FIS-007U, FIS-007USK, FIS-007UB, CT-101, CT-102Intended UseFor visually inspecting items.Range of Applications for ProductEnhance visual inspection by providing lighted magnification, image capture and the option for documentation in hard-to-see crevices, channels, and lumens in areas of instruments that are not visible to the unaided eye.Key Specifications of Product Flexible Inspection Scope- FIS-007U∙CT-101 1.90 mm OD and 110 cm length∙CT-102 1.06 mm OD and 110 cm length∙Opticalo Resolution format:o CT-102 1.06 mm: 40,000 pixels (or 200- x 200 pixels)o CT-101 1.90 mm: 160,000 pixels (or 400- x 400 pixels)o Field of View: 120° in airo Angle of view: 0°USB Control Module: Control Module housing Camera processor and LEDillumination:∙Dimensions: 5.25- x 3.90- x 1.85 inches∙Weight: 1.20 pounds ∙Digital Inspection Scope Connection∙Illumination Control- LED in the Control Module∙Power Cycle∙USB Camera Cable∙Easily change from small and large diameter scopes.Light Settings:There are four light settings operated by one button.Blinking Light (Indicates transmitting video data):∙Splash proof (IPX5 Rating)∙No external power needed.Flexible Inspection Scope Software Requirements:∙Compatible with Windows 10 Operating systems.∙USB flash drive includes software.Unpacking Flexible Inspection Scope:Carefully inspect for shipping damage. If there is any damage contact the shipping carrier and Heatlhmarkcustomer service 800-521-6224 immediately.USB Control Module: (Fig. 1).1.Digital Inspection Scope Connection 2.Illumination Control 3.Power Cycle B (Type C) on the right side of the boxFigure 1Flexible Inspection Scope™: (Fig. 2).∙CT-101 1.90 mm O.D. and 110 cm length ∙CT-102 1.06 mm O.D. and 110 cm lengthLarge1.90 mmSmall 1.06 mmFigure 2Flexible Inspection Scope™ Features3214Light/Illumination Settings: (Fig. 3).∙Five (5) light settingso Light on control indicats setting levelo Fifth setting is OFF∙Press light button to advance to next setting.∙Fifth setting turns the light OFF.Figure 3Power Cycle ButtonPress button to RESET camera (Fig. 4).Figure 41.Flexible Inspection Scope™ Plug (Fig. 5).Contains camera video connection as well as LED Light for illumination.1Figure 52.Flexible Working Length (Fig. 6).The portion of the Flexible Inspection Scope™ that is inserted into an item during visual inspection.The measuring scale markings on the Flexible Working Length are in centimeters (accuracy = ± 0.5 cm)2Figure 63.Distal Camera (Fig. 7).Distal portion of Flexible Inspection Scope™ that contains the camera lens3Figure 7SOFTWARE INSTALLATION:Note: This section is done only once when connecting the scope to the computer for the first time.∙System Requirements: MS Windows 10∙Install the Flexible Inspection Scope™ Software from the USB flash drive on a computer.Note: If you have any IT policies that may block this installation, please contact your IT team to give access to Healthmark scope viewer to install.1. Insert the USB Flash drive into your computer, and double click on the Healthmark Scope Viewer installer package to begin installation.2. The “Welcome to the Healthmark Scope Viewer Setup Wizard” screen pops up. Click on Next.3. Select the first tab Typical or setup type of your choice, click Next.4. Click Install and wait for installation to complete.5. Click Finish.STARTING SOFTWARE & CONNECTING SCOPE TO PC:(Fig 8).1.Open the Windows PC viewer software.2.Connect the Control Module to PC using USB Cable.3.Plug the Flexible Inspection Scope into the Control Module.4.In the viewer software, click Settings and Select USB Video Device, click on the desiredresolution, select the preferred Video Output Format, and then Click OK.5.Press the Power Cycle Button.Figure 86.Now you can start using the scope.Verifing OperationFollowing the steps listed below will ensure the proper use and performance of the Flexible Inspection Scope™. The Flexile Inspection Scope™ can be checked for normal operation by connecting it as described in the Startup section of this IFU.Normal operation includes:∙An image appearing on your computer monitor or HDMI Monitor.∙ A blinking light on Control Module near the Power Cycle button that indicates the image feed is transmitting.∙White light emitting from the distal end of the Digital Inspection Scope.∙An LED light on the control module top panel that indicates the light intensity of the device. Using SoftwareHealthmark Scope Viewer Software (Fig. 9).1.Capture button: Captures a Reference Image and saves it to the Reference Image folder.2.Main Image Window: Displays the image from the camera.3.Reference Image Window: Displays a reference image.4.Clear Button: Removes the image from the Reference image window.5.Open Reference Image button: Allows selection of a reference image from the Reference Imagefolder.6.Settings Button: Click to select the video camera and resolution settings.7.File Location Button: Click to change location where captured images are being saved.8.File Location Window: Shows the file path where captured images are being saved currently.9.Capture Image Button: Captures images and adds them to the File Location selected by the user(as shown in the File Location Window).10.Capture Video button: Click to record video. Click again to stop recording video.11.File Prefix: Type in text that you would like included in the file name of Captured Images.Figure 9Selecting Video Device or CameraFollow the directions below to select the video device or camera used to capture images using the Flexible Inspection Scope™ Viewer Software. (Fig. 10).1.Click Settings button in the lower left of the Scope Viewer software to display a list of videodevices or cameras being detected by your computer2.Select a device for capturing images using the Scope Viewera.The example below shows a webcam and USB Video Device in the Settings box. Select theUSB Video Device for the Flexible Inspection Scope™.b.You can also select your preferred Video Output Format from the dropdown box3.Click OK to view the selected Video Device.231Figure 10Capturing Still PicturesFollow the instructions for capturing still pictures from the Main Image Window.Select the Capture Image button. (Fig. 11).Figure 11Note: When an image is captured, “Image Captured” in red text will flash on the lower portion of the screen and a new file will appear in the Files Location.Capturing Video ImagesFollow the instructions below for capturing video from the Main Image Window.1.Select the Capture Video Button (Fig. 12).Figure 122.When the video is recording “Recording…” in red text will appear toward the bottom of thesoftware window.3.To stop recording, click Stop Capture. (Fig. 13).Figure 13Setting File PrefixFollowing the steps below allows you to create a file prefix that will appear after the underscore of image file names save to the File Location specified by the user.1.Click in the field next to File Prefix.2.Enter the characters that you would like to be included in the file name. (Fig 14).Figure 14Setting Location for Saved FilesFollowing the steps below allows you to set the file location of saved images using the Scope Viewer software.1.Click the File Location button.2.Select the file location you want to save captured images. (Fig 15).Figure 15Displaying Reference ImageThere are two ways to display a still image in the Reference Image Window on the Scope Viewer software.1.To display an image currently being displayed in the Main Image Window, click the Capture button. Note: The images will be saved in a file folder titled Reference Images in the designated File Location that the user specified in the File Location field. (Fig. 16).Figure 162.To display a saved image in the Reference Image Window from your File Location:a.Click the Open Reference Image button (Fig. 16 above).b.Select the file you want to display (Fig. 17 below).c.Click the OK Button, to display the image in the Reference Image Window. (Fig. 17).Figure 17Switching to a Different Flexible Inspection Scope™ on the Control Module:1.Press the Power button on the Control Module once.2.Disconnect the current Flexible Inspection Scope from the Control Module.3.Repeat the steps in the “STARTING SOFTWARE & CONNECTING SCOPE TO PC” procedure.Inserting Scope in ItemFigure 1Rotating Device to Avoid ObstacleFigure 2 Performing InspectionWipe down the Flexible Inspection Scope™ with a compatible wipe. Follow the manufacturer’s (Mfr.’s)Instructions for Use (IFU) for appropriate wipe usage. Click here to see the Chemical Compatibility Chart(PDF) for approved cleaning.The Flexible Inspection Scope™ is made of the same material as other common endoscopes. Any wipe,solution, or low temperature (≤ 60 °C [140 °F]) method intended for the reprocessing of endoscopes is likelycompatible with the Generation II Flexible Inspection Scope™ Catheters if used according to the productlabeling.Solutions Containing (Flexible Inspection Scope Only)Alcohol Ethoxylates Neutral or Near-Neutral pH DetergentsEnzymatic Cleaning Solutions Enzymatic DetergentsSodium Borated, Decahydrate Tetrapotassium PyrophosphateFlexible Inspection Scope™ has a fluid ingress protection rating of IPX7 (Waterproof) and can withstandimmersion in fluid up to one (1)-meter in depth for up to 30 minutes.Control Module USB has a fluid ingress protection rating of IPX5 (Water resistant) and can withstand asustained, low pressure water jet spray for up to three minutes.For Thorough Cleaning: CablesFollow the cleaning agent Mfr.’s IFU.1.Unplug and disconnect all components from the Control box prior to cleaning.2.Do not submerge or soak the cable for disinfection (cable is not waterproof).3.Wipe thoroughly with non-linting wipe moistened with facility approved neutral detergent. Use theappropriate brushes with detergent solution to remove any residues from areas that cannot bereached with the wipes.For Thorough Cleaning: Control Module1.Unplug and disconnect all components from the Control box prior to cleaning.2.Do not submerge or soak the cable for disinfection (Control Box is not waterproof).3.Wipe thoroughly with non-linting wipe moistened with facility approved neutral detergent. Use theappropriate brushes with detergent solution to remove any residues from areas that cannot bereached with the wipes.Note: Do NOT soak. Control Module and cables are not waterproof and should not be immersed.N/ACleaning –AutomatedDisinfection Control Module and CablesThese may be cleaned with alcohol based disinfectant wipes.Compatible agents (wipes and solutions) for disinfecting Flexible Inspection Scope™ and ControlModule:∙Hydrogen peroxide∙Isopropyl alcohol (IPA)∙Sodium hypochlorite (Bleach)∙Ortho-phenylphenol∙Quaternary ammonium.High-Level Disinfection (Flexible Inspection Scope™ Only)∙Select only disinfecting solutions listed in the compatible disinfecting methods.∙Follow all recommendations regarding health-hazards, dispensing, measuring, and storage from the Mfr. of cleaning and disinfecting agents.∙Soak the Flexible Inspection Scope™ in selected disinfecting solution per Mfr.’s IFU.∙Rinse the Flexible Inspection Scope™ with critical (sterile) water, again, following the disinfecting solutions Mfr.’s instructions.Reprocessing Chemical Compatibility Chart (PDF): Click here.。
蓝桥系统S200系列BIOS电池FRU套装产品安装指南说明书
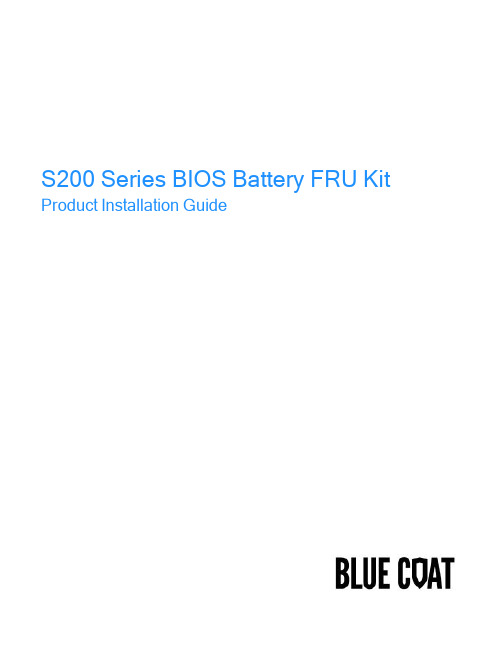
S200Series BIOS Battery FRU Kit Product Installation GuideBlue Coat Systems,Inc Upgrade Installation GuideThird Party Copyright Notices©2016Blue Coat Systems,Inc.All rights reserved.BLUE COAT,PROXYSG,PACKETSHAPER,CACHEFLOW, INTELLIGENCECENTER,CACHEOS,CACHEPULSE,CROSSBEAM,K9,DRTR,MACH5,PACKETWISE, POLICYCENTER,PROXYAV,PROXYCLIENT,SGOS,WEBPULSE,SOLERA NETWORKS,DEEPSEE,DS APPLIANCE,CONTENT ANALYSIS SYSTEM,SEE EVERYTHING.KNOW EVERYTHING.,SECURITY EMPOWERS BUSINESS,BLUETOUCH,the Blue Coat shield,K9,and Solera Networks logos and other Blue Coat logos are registered trademarks or trademarks of Blue Coat Systems,Inc.or its affiliates in the U.S.and certain other countries.This list may not be complete,and the absence of a trademark from this list does not mean it is not a trademark of Blue Coat or that Blue Coat has stopped using the trademark.All other trademarks mentioned in this document owned by third parties are the property of their respective owners.This document is for informational purposes only.BLUE COAT MAKES NO WARRANTIES,EXPRESS,IMPLIED,OR STATUTORY,AS TO THE INFORMATION IN THIS DOCUMENT.BLUE COAT PRODUCTS,TECHNICAL SERVICES,AND ANY OTHER TECHNICAL DATA REFERENCED IN THIS DOCUMENT ARE SUBJECT TO U.S.EXPORT CONTROL AND SANCTIONS LAWS, REGULATIONS AND REQUIREMENTS,AND MAY BE SUBJECT TO EXPORT OR IMPORT REGULATIONS IN OTHER COUNTRIES.YOU AGREE TO COMPLY STRICTLY WITH THESE LAWS,REGULATIONS AND REQUIREMENTS,AND ACKNOWLEDGE THAT YOU HAVE THE RESPONSIBILITY TO OBTAIN ANY LICENSES, PERMITS OR OTHER APPROVALS THAT MAY BE REQUIRED IN ORDER TO EXPORT,RE-EXPORT, TRANSFER IN COUNTRY OR IMPORT AFTER DELIVERY TO YOU.Americas:Blue Coat Systems,Inc.384Santa Trinita Ave.Sunnyvale,CA94085****************************************************************************Rest of the World:Blue Coat Systems International SARL3a Route des Arsenaux1700Fribourg,Switzerland2Blue Coat Systems,Inc Upgrade Installation Guide ContentsThird Party Copyright Notices2 Safety Warnings and Cautions5 Power and Electrical Warnings5 CAUTION5 System Access Warnings5 CAUTION5 To avoid personal injury or property damage,the following safety instructions apply whenever accessingthe inside of the product:5 CAUTION6 CAUTION6 Cooling and Airflow Warning6 Electrostatic Discharge(ESD)Warning6 CAUTION6 Remove the S200Series Top Cover8 Remove the S200Series PCIe Riser Card9 Replace the S200Series BIOS Battery10 Install the S200Series PCIe Riser Card12 Reinstall the S200Series Top Cover13 Finish the BIOS Battery Replacement14 Verify the SG-S200BIOS Battery Installation15 Verify the Appliance Time Settings173Blue Coat Systems,Inc Upgrade Installation GuideThe contents of the Blue Coat BIOS battery FRU kits are shown below.Please verify the contents of the upgrade kit before continuing with the installation.If any items are missing,please contact your Blue Coat Support contact for assist-ance.To replace the BIOS battery,Blue Coat recommends the following tools and items.4Blue Coat Systems,Inc Upgrade Installation Guide Safety Warnings and CautionsCaution:This product is designed to work with power systems having a grounded neutral.To reduce therisk of electric shock,do not plug this product into any other type of power system.Contact a qualified elec-trician if you are not sure what type of power is supplied to your building.Power and Electrical WarningsCAUTIONThe power button,indicated by the stand-by power marking,DOES NOT completely turn off the system ACpower.5V standby power is active whenever the system is plugged in.To remove power from system,youmust unplug the AC power cord from the wall outlet.If your system uses more than one AC power cord,make sure all AC power cords are unplugged before you open the chassis,or add or remove any non hot-plug components.The power supply in this product contains no user-serviceable parts.Do not open the power supply.Haz-ardous voltage,current,and energy levels are present inside the power supply.Return to manufacturer forservicing.To avoid risk of electric shock,turn off the appliance and disconnect the power cord,tele-communications systems,networks,and modems attached to the appliance before opening it.The power cord set included with the appliance meets the requirements for use in the country of purchase.Use the power cord that shipped with the appliance.If this appliance is to be used in another country,pur-chase an AC power cord set that is approved for use in that country(18AWG recommended).The power cord must be rated for the product and for the voltage and current marked on the product's elec-trical ratings label.The voltage and current rating of the cord should be greater than the voltage and currentrating marked on the product.In addition,the cross-sectional area of the wires must be a minimum of1.00mmðor18AWG or18AWG,and the length of the cords must be between1.8m(6feet)and3.6m(12feet).System Access WarningsCAUTIONTo avoid personal injury or property damage,the following safety instructions apply whenever accessing theinside of the product:n Turn off all peripheral devices connected to this product.n Turn off the system by pressing the power button to off.n Disconnect the AC power by unplugging all AC power cords from the system or wall outlet.n Disconnect all cables and telecommunication lines that are connected to the system.5Blue Coat Systems,Inc Upgrade Installation Guiden Retain all screws or other fasteners when removing access cover(s).Upon completion of accessing inside the product,refasten access cover with original screws or fasteners.n Do not access the inside of the power supply.There are no serviceable parts in the power supply.Return to manufacturer for servicing.n Power down the server and disconnect all power cords before adding or replacing any non hot-plug component.n When replacing a hot-plug power supply,unplug the power cord to the power supply being replaced before removing the power supply from the server.CAUTIONn If the server has been running,any installed processor(s)and heat sink(s)may be hot.Unless you are adding or removing a hot-plug component,allow the system to cool before opening the covers.Toavoid the possibility of coming into contact with hot component(s)during a hot-plug installation,becareful when removing or installing the hot-plug component(s).CAUTIONn To avoid injury do not contact moving fan blades.If your system is supplied with a guard over the fan, do not operate the system without the fan guard in place.Cooling and Airflow WarningCarefully route cables as directed to minimize airflow blockage and cooling problems.For proper cooling and airflow,operate the system only with the chassis covers installed.Operating the sys-tem without the covers in place can damage system parts.To install the covers:1.Check first to make sure you have not left loose tools or parts inside the system.2.Check that cables,add-in boards,and other components are properly installed.3.Attach the covers to the chassis according to the product instructions.Electrostatic Discharge(ESD)WarningCAUTIONESD can damage disk drives,boards,and other parts.We recommend that you perform all procedures at an ESD workstation.If one is not available,provide some ESD protection by wearing an antistatic wrist strap attached to chassis ground-any unpainted metal surface--on your server when handling parts.Always handle boards carefully.They can be extremely sensitive to ESD.Hold boards only by their edges.After removing a board from its protective wrapper or from the server,place the board component side up on6Blue Coat Systems,Inc Upgrade Installation Guide a grounded,static free e a conductive foam pad if available but not the board wrapper.Do notslide board over any surface7Blue Coat Systems,Inc Upgrade Installation GuideRemove the S200Series Top CoverThe S200Series top cover protects the primary system components.You must remove this panel to access the option cards,hard disk drives,and DIMMs.You must power down the appliance and take proper safety measures before opening the appliance.ALWAYS observe proper electrostatic discharge(ESD)conventions.Attach an ESDprotective wrist strap to your wrist and to the chassis.Ensure that the appliance is onan ESD-safe work surface or ground the unit appropriately.Blue Coat does notassume responsibility or liability for damage resulting from ESD.1.Remove the top cover captive thumbscrew by either using either your fingers or a screwdriver.2.Push the top cover towards the rear of the appliance then lift to remove the cover.Set the top cover aside at a safelocation.8Blue Coat Systems,Inc Upgrade Installation Guide Remove the S200Series PCIe Riser CardThe S200Series is equipped with a PCIe riser card that mounts the NIC in a horizontal position.You must remove the riser card from the appliance before you can attach a NIC.ALWAYS observe proper electrostatic discharge(ESD)conventions.Attach an ESDprotective wrist strap to your wrist and to the appliance chassis.Ensure that the appli-ance is on an ESD-safe work surface or ground the unit.Blue Coat does not assumeresponsibility or liability for damage resulting from ESD.1.Pull the release latches to unlock the riser card.Unlocking the release latches also unseats the riser card.2.Hold the edges of the riser card and lift straight up to remove from the appliance.9Blue Coat Systems,Inc Upgrade Installation GuideReplace the S200Series BIOS BatteryThe Blue Coat S200series appliances feature a replaceable CR2450BIOS battery.The battery located near the PCIe riser card and must be removed to provide safe access to the battery holder.The BIOS battery details for the S200series are shown below.ALWAYS observe proper electrostatic discharge(ESD)conventions.Attach an ESDprotective wrist strap to your wrist and to the chassis.Ensure that the appliance is onan ESD-safe work surface or ground the unit appropriately.Blue Coat does notassume responsibility or liability for damage resulting from ESD.Do not install batteries which are not explicitly supported by the appliance.Install-ation and use of unauthorized batteries might damage the appliance and will inval-idate your Blue Coat service contract!1.To remove the existing BIOS battery,release the battery by pressing the clip with the flat-blade screwdriver.Thebattery should tilt upward,slightly out of the battery holder.Remove the battery.If necessary,use the pliers to lift the battery out of the battery holder.Properly dispose of the old BIOS battery.Please recycle old and unused Blue Coat products!Visit https://www.blue-/support/support-policies/recycling-blue-coat-products for moreinformation.2.Install the new battery( +positive side up)by inserting it at an angle towards the battery holder retaining clip and10Blue Coat Systems,Inc Upgrade Installation Guide then press down to secure it.Blue Coat Systems,Inc Upgrade Installation GuideInstall the S200Series PCIe Riser CardThe S200Series is equipped with a PCIe riser card that mounts the NIC in a horizontal position.When you reinstall the riser card,take additional care to prevent scratching any board surfaces.ALWAYS observe proper electrostatic discharge(ESD)conventions.Attach an ESDprotective wrist strap to your wrist and to the appliance chassis.Ensure that the appli-ance is on an ESD-safe work surface or ground the unit.Blue Coat does not assumeresponsibility or liability for damage resulting from ESD.1.Verify that the appliance power cord is unplugged.2.Remove the appliance top cover.3.Align the PCIe riser card with the posts on the chassis and press down to seat into place.4.Lock the PCIe riser card in place by closing the two lockdown clips on riser card.Verify that the module is flat andaligned with the rest of the adjoining chassis structures before reinstalling the appliance cover.Blue Coat Systems,Inc Upgrade Installation Guide Reinstall the S200Series Top CoverThe S200Series top cover protects the primary system components.You must remove this panel to access the option cards,hard disk drives,and DIMMs.You must power down the appliance and take proper safety measures before opening the appliance.ALWAYS observe proper electrostatic discharge(ESD)conventions.Attach an ESDprotective wrist strap to your wrist and to the chassis.Ensure that the appliance is onan ESD-safe work surface or ground the unit appropriately.Blue Coat does notassume responsibility or liability for damage resulting from ESD.1.Reinstall the rear cover by sliding the panel towards the front of the appliance.2.Secure the top cover by tightening the captive screw.Blue Coat Systems,Inc Upgrade Installation GuideFinish the BIOS Battery ReplacementFinish the BIOS battery replacement by reconnecting the cables and verifying the installation.1.Reinstall the appliance cables as they were originally configured.2.Power on the appliance.Blue Coat Systems,Inc Upgrade Installation Guide Verify the SG-S200BIOS Battery InstallationLog in to your ProxySG appliance using a supported Web browser(see the SGOS Release Notes for a list of supported browsers):1.Open a Web browser.2.Disable the browser’s pop-up blocker or configure it to allow pop-ups from the appliance’s IP address.ing a secure connection,enter any IP address assigned to the appliance,followed by the HTTPS console portnumber(8082by default).For example:https://192.0.2.2:80824.Enter the user name and password you specified during configuration to access the appliance.5.Select Maintenance>System&Disks>Environment.6.Select View Sensors.Blue Coat Systems,Inc Upgrade Installation Guide7.Scroll down to+3V battery voltage and verify the status is OK.Blue Coat Systems,Inc Upgrade Installation Guide Verify the Appliance Time SettingsIf you exited from the Management Console,log back in to the appliance.1.Select Configuration>General>Clock.2.Go to Current time and verify that the time settings are accurate.If necessary,update the time settings asappropriate。
UF200_operation for Chinese
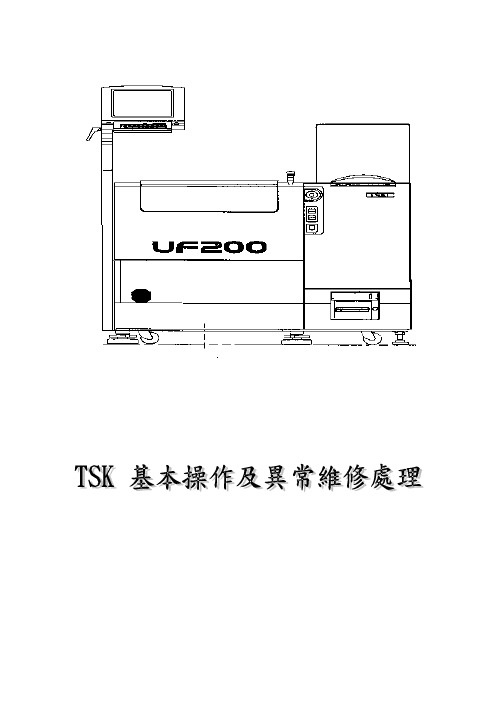
目录*TSK 细部介绍…………………………P2~P3*SET UP 步骤…………………………P4~P25(生产参数设定…………P6~P11)(对针……………………P18~P19)(试打针痕………………P20~P22)(针偏时如何移动针痕……P23~P24)*异常处理………………………………P26~P38(重开机…………………P30~P38) *WAFER扫描异常如何处理………………P29~P44 *测试中如何将PROBE CARD取出清针…P45~P46 *SET UP INK………………………………P47~P59TSK 细部介绍M a r k e r S w itc h (In k in g 專用)θ軸的旋轉控制(C h u ck 的旋轉)Z軸的升降(Ch u c k 的升降)Z U P (下針壓)D A TA IN (黃)J O Y S T IC K S T O P (橙)S TA R T (綠)H e a d sta g eP ro b e C a r d H o ld e r**SET UP步骤(TSK屏幕为触碰式屏幕点选你要的字段即可进入内页设定你要的功能)选取<DEVICE PARAMETER CHANGE>点选DEVICE字段,点选后字段会反白出现反白后,在点选<ENT>会出现许多DEVICE名称,请照例举的步骤点选(EX:选取AN80007A=>DEVICE DATA READ=>ENT) ENT**选好DEVICE后,必须设定生产参数的设定点选<OPERATION SETTINGS>点选框框中的2个STOP(stop befor probing:wafer开始测试之前停止)(stop after probing:wafer 测完之后停止)点选<PROBER MODE SETTINGS>按NEXT PAGE 到第4页选取<MAP OUTPUT SETTINGS>,<MAP INPUT SETTINGS>进内页设定后再选取PREVIOUS MENU即跳回前一页MAP OUTPUT SETTINGS里:将Output Map Data 设定为1(选取后才会将测后数据储存,请注意非常重要),Output Map Data To:选0(为存至磁盘)据),Input Map Data From选0(数据源磁盘)至第3页选取<MULTI PASS PROBING SETTINGS>Die For Multi Pass Probing(设定要测试项目是0:正常,1:Fail die,2:pass die,3:自行选取特定BIN)如是选3,请在选取 CAT. DATAOF DIRET/MULTI PASS PROBING选你所需要的特定BIN将你要的特定BIN选取后会变成红色YES,在按<ENT>,后跳至主画面选取<DEVICE PARAMETER CHANGE>至第3页Direct Multi Pass Probing Execute 选1(是否回收fail功能) Kind of Direct Multi Pass Probing选1:Set Cat(自行设定)在点选<CAT. DATA OF DIRECT/MULTI PASS PROBING>选取特定BIN回到主画面,参数设定已完成至主画面选取<CARD CHANGE>选取<CARD CHANGE START>将测试头移开将Probe Card放至Probe Card Holder将测试头Mount 回去后选取<CARD CHANGE END>选取<LOT SETTINGS>选取<Lot>使之反白输入所要测试之批号(ex:AHT4Q)Lot:会出现你刚所输入之批号,后按<ENT>开始侦测WAFER,准备生产。
西门子200PLCSP8安装指南
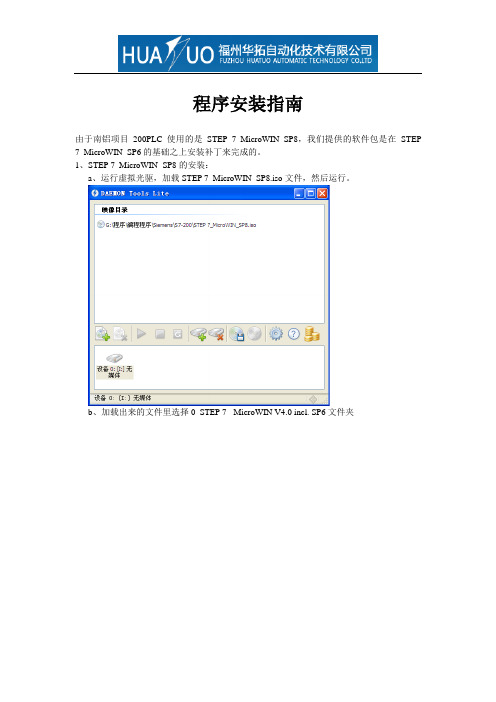
程序安装指南由于南铝项目200PLC使用的是STEP 7_MicroWIN_SP8,我们提供的软件包是在STEP 7_MicroWIN_SP6的基础之上安装补丁来完成的。
1、STEP 7_MicroWIN_SP8的安装:a、运行虚拟光驱,加载STEP 7_MicroWIN_SP8.iso文件,然后运行。
b、加载出来的文件里选择0_STEP 7 - MicroWIN V4.0 incl. SP6文件夹c、打开1_Service_Pack 8文件夹后选择,运行Setup文件。
d、得到的是英文版的安装向导,选择英文,点确定。
e、弹出英文版安装向导(中文界面可以在安装完成后设置)。
点Next..f、点Y es.g、更改安装路径,点击Next。
h、安装进度。
i、点下一步。
j、勾选“我接受许可协议中的条款”,点击安装。
k、点击安装完成。
l、选择立即重启电脑。
点Finish。
m、在控制板里的添加删除程序你把MicroWIN V4.0 SP6删除,点击是。
n、完成卸载,点Finish。
o、打开虚拟光驱里的文件,选择1_Service_Pack 8文件夹打开。
p、选择MicroWIN文件夹打开。
q、运行STEP7-MicroWIN_V40_SP8。
r、弹出安装向导窗口,点击Next。
s、选择安装语言,选择英语,点击确定。
t、弹出安装向导窗口,点击Next。
u、点击Y es。
v、更改安装路径,点击Next。
w、安装进度。
x、点下一步。
y、勾选“我接受许可协议中的条款”,点击安装。
z、点击安装完成。
aa、选择立即重启电脑。
点Finish。
EMC 低端存储维护手册
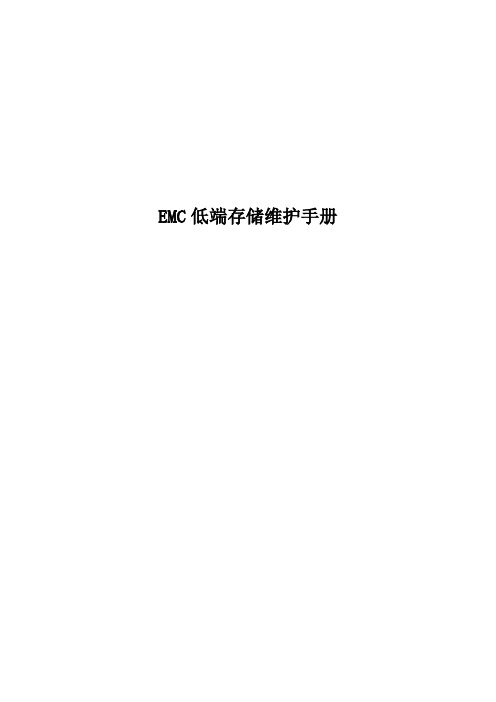
在前面板上看不见,需拆下前面板才能看见)
(1)3 个热插拔风扇模块(3) SPE 电源指示灯(绿灯)
SPE 错误指示灯 (黄灯)
CX600 / CX700 Storage Processor Enclosure (SPE)--后视图
(1) Storage Processors A
B:故障指示灯 C:用户管理网络端口
D:服务管理网络端口,仅限于EMC 服务人员使用
E:管理串口 F:SPS 监控端口
二
CX4-120 / 240 / 480 Storage Processor Enclosure (SPE)—前视图
A0:电源模块
A1:电源模块
B0:电源模块
B1:电源模块
C:CPU 模块A
E:I/O Annex(I/O 扩展模块)
CX4-960 Storage Processor (SP)—细节图
A:Power LED(电源指示灯)
B:Fault LED(故障指示灯)
C:Unsafe to Remove LED
D1-D4:I/O Module(I/O 模块)
CX4-960 Management Module—细节图
Disk Array Enclosure (DAE) --后视图
Two Link Control Card (LCC)
(1) LCC 状态灯--绿色表示电源,黄色表示有错误 (2) Expansion 端口(HSSDC)--灯亮表示有信号
E:NMI(系统维护用,勿触动)
二
CX4-960 Storage Processor Enclosure (SPE)—前视图
A1:Power Supply A(电源模块A)
ASPP4C-1021-B ASPP4C-1021-W 4-Way Surge Powerboa

User GuideModel: ASPP4C-1021-B / ASPP4C-1021-W4-Way Surge Powerboardwith USB-C ChargingInput AC 230-240V , 50Hz, 10A Total Loading Max 10A 2400W Surge Protection 190JUSB Output DC 5V , 2.4A Max. USB-C Output DC 5V , 3A Max. Power Cable 1.8m Mass580gDimensions (W x H x D)330 x 33 x 55 mmGENERAL SAFETY WARNINGSGeneral Safety WarningsFor the safety of yourself and others, follow all instructions and take notice of all the warnings. When adhered to, these safety precautions can reduce the risk of fire, electric shock and injury. This product complies with Australian Safety standard AS/NZS 3105, AS/NZS 62368.1 to ensure the safety of the product.The RCM is a visible indication of a product’s compliance with all applicable ACMA regulatory arrangements, including all technical and record-keeping requirements.IMPORTANT•Damage: If the powerboard or cord is damaged, contact the After Sales Support line for advice. Do notattempt to open the board or replace the cord. The cord must be replaced by appropriately qualified personnel.•Repair: If the powerboard requires repair, contact the After SalesSupport line; never disassemble or modify the powerboard or attempt to service it yourself.•Run the power supply cord in such a way that there will be no risk of anyone pulling it inadvertently or tripping over it.•The powerboard is not intended for use by persons (including children) with reduced physical, sensory or mental capabilities, or lack of experience and knowledge, unless they have been given supervision or instruction by a person responsible for their safety.•Young children should be supervised to ensure they do not play with the powerboard. Close supervision is always necessary when any appliance is used by or near children.• The surge powerboard is designed for indoor use in dry places only.• Do not exceed a maximum loading of 2400 watts.• For safety reasons, always use earth connections.• Only use the powerboard with the power supply cord fully unwound.•Before installing the powerboard, make sure to place it away from: heat sources, radiators or other products that produce heat; areas with high temperatures, high humidity or direct sunlight; excess dirt and dust; open windows and any place where water may get to the unit.•Do not immerse the cord, plug or the surge powerboard in water or other liquid, or expose the electrical connections to water or other liquid.•Unpack the powerboard and keep the original packaging carton and materials in a safe place. It will help prevent any damage if thepowerboard needs to be transported in the future, and you can use it to store the powerboard when it is not in use.•The powerboard should always be repacked in its original packaging whenever transporting to prevent any possible damage to the product.•When not in use: Disconnect from the power source and store in a cool, dry and well ventilated location out of direct sunlight, and not subject to humidity.• Warning: Discard this powerboard if the supply cord is damaged.•Warning: The socket outlet should be located near the equipment and should be easily accessible.Responsible disposal of the productAt the end of its working life, do not throw this product out with your household rubbish. An environmentally friendly method of disposal will ensure that valuable raw materials can be recycled. Contact your local authority for your nearest recycling centre. Electrical and electronic items contain materials and substances which, if handled or disposed of incorrectly, could potentially behazardous to the environment and human health.Responsible disposal of the packaging The packaging of the product has been selected from environmentally friendly materials and can usually be recycled. Please ensure these are disposed of correctly. Plastic wrapping can be asuffocation hazard for babies and young children, please ensure all packaging materials are out of reach and are safely disposed of. Please ensure they areoffered for recycling rather than throwing these materials away.Cleaning the productOnly use a soft, dry cloth for cleaning the product; do not use a damp cloth. Never clean with industrial strength polish, wax, benzene, paint thinner, air freshener, lubricant, detergent or other chemicals. Wipe off any moisture, dirt or dust on the power sockets and plug pins with a clean, dry cloth.。
面向支持系统的飞机维护工作手册 AMTOSS
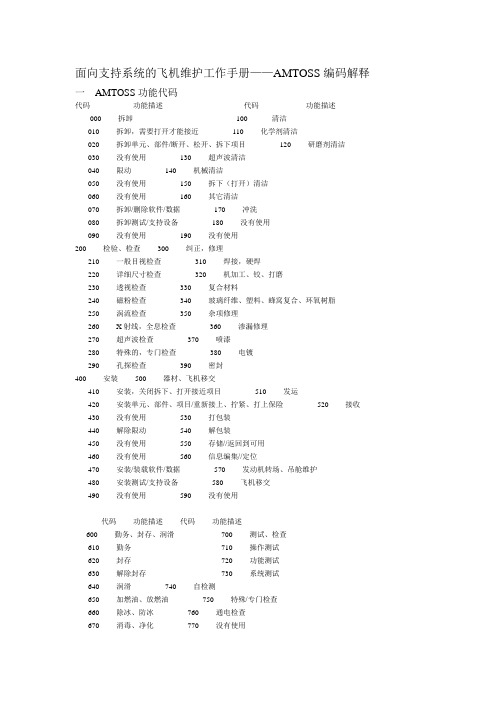
任何引入的零件、子组件、部件或组件的接收活动。
53打包装
安装零件、子组件、部件或组件到装运容器。还包括管路的封盖和堵塞的安装等。
54解包装
从装运容器卸下零件、子组件、部件或组件。包括所有保护材料的拆除。
55存储//返回到可用
存储是指在不使用期间,零件、子组件、部件或子组件的安全保存。可能要求单元服务和特殊的手工。
为保证执行任务而需要提供接近通道的部件、结构件、管道或项目的拆卸或断开。
02拆卸单元、部件/断开、松开、拆下项目
单元、(可能包含在附属硬件中的)作为工作标记的部件的拆卸;
为完成工作将要移开的附在部件上的管路、螺母、夹具、支架等的断开、松开、拆卸,
诸如灯泡、插座、透镜、衬垫、轴承挡板、螺钉等子工作项目的拆卸;
面向支持系统的飞机维护工作手册——AMTOSS编码解释
一AMTOSS功能代码
代码功能描述代码功能描述
000拆卸100清洁
010拆卸,需要打开才能接近110化学剂清洁
020拆卸单元、部件/断开、松开、拆下项目120研磨剂清洁
030没有使用130超声波清洁
040限动140机械清洁
050没有使用150拆下(打开)清洁
在飞机、系统、单元上用来帮助执行工作或子工作的、除测试设备之外的支持设备(诸如吊车、液压车、安全锁、特殊工具等)的拆卸。
09没有使用
10清洁
11化学剂清洁
是指通过使用化学清洁剂除去表面的污垢,包括涉及化学剂的清洁工作的任何组合,还包括清洁剂的准备。
12研磨剂清洁
通过湿的或干的颗粒状研磨剂的撞击除去零件的表面污垢。
72功能测试
功能测试过程要求确保系统或单元在各方面的功能应该符合最低可接收的系统或单元的设计说明。功能测试要求补充的地面支持设备,并且应该比操作测试更加详细、具体。为了保持系统或单元的可靠性在可接收的水平,功能测试应该包含执行精确的测试所有需要的信息,而不用去参考额外的文档。
FUJITSU PRIMERGY RX200 S4 服务器使用说明书

CA92276-8407-01Thank you for purchasing our product. Before you start using your server, please read carefully the additional notes described below.December 2008FUJITSU LIMITED1. Setting for onboard LAN controller on Windows Server 2003 or Windows Server 2003 x64[IMPORTANT]When the server runs on Windows Server 2003 or Windows Server 2003 x64, the onboard LAN controller may not work properly (*) with some applications. To avoid the symptom, make sure to disable the TCP Chimney Offload setting by following the instruction below.1. Start Windows Server 2003 or Windows Server 2003 x64.2. Select [Start] – [Run] and type in "cmd" to activate the command prompt.3. Enter the following command on the command prompt, and press <ENTER>.4.(You do not need to restart the server after this command.)* Example of the cases where the LAN controller does not work properly1) When the data transfer is performed through FTP1-1 "426 Connection Closed; transfer aborted" is displayed.1-2 The FTP connection is disconnected and the data cannot be transferred through FTP .2) When an application that connects to SQL Server by using TCP/IP is used, you may intermittently receive one of the following error messages when the application connects to SQL Server.2-1 [Microsoft] [ODBC SQL Server Driver] [DBNETLIB] General Network errorRefer to the network manuals in this case.2-2 [Microsoft] [SQL Native Client] Communication link failure2-3 System.Data.SqlClient.SqlException: A transport-level error has occurred when sending the request to the server2. Warning Messages of ServerView Remote Connector upon OS startup[Symptom]When all the conditions described later are met, the warning message below may be recorded on the Application Event Log upon the startup of the server.[Conditions]1) ServerView Agent for Windows is installed, and2) The system is highly-loaded during startup.[Cause]The heavy load during the system startup causes the delay in the processing to initializeServerView Remote Connector. This warning message is to report that the service startup isnot completed within the certain period of time, and not that the service startup has failed.[Remedy]Even if the message is recorded due to the delay in the processing to initialize theServerView Remote Connector service, the processing continues. The service isautomatically started after the completion of the initialization, so no special action is required.* The ServerView Remote Connector service is used with the following ServerView functions. Even if this service is not active, no other functions are affected.- Performance Manager- Power MonitorSupplementary Information: How to ConfirmFollow either of the procedures below to confirm whether the ServerView Remote Connector service is running normally.1) When Performance Manager is used-Start the Performance Manager from the ServerView S2.-Select the server for which you want to confirm the ServerView Remote Connector service operation from the left side frame.-Select the [Report View] tab.-Select any report, and click on the [Show >>] button.If the graph is displayed, the ServerView Remote Connector service is running normally and no change is required. When the service is not running normally, the following dialog is displayed.Note: It is necessary to make the report setting beforehand.For the usage of Performance Manager, refer to "ServerView User's Guide".2) When Power Monitor is used-Start the Power Monitor from the ServerView S2.-Select the server for which you want to confirm the ServerView Remote Connector service operation from the left side frame.-Select the [Data] tab.If the graph is displayed, the ServerView Remote Connector service is running normally and no change is required. When the service is not running normally, the following dialogs are displayed.A) The following dialog box is displayed and left open.B) After the dialog in (A), the following window is displayed.Note: For the usage of Power Monitor, refer to "ServerView User's Guide".When the ServerView Remote Connector is not running normally, restart the service by following the procedure below. (There is no need to reboot the system.)[Control Panel] - [Administrative Tools] - [Services] - [ServerView Remote Connector]Select <Restart Service>.3. About the latest ServerViewServerView in "PRIMERGY StartUp Disc" attached to this product does not support BIOS 1.09/iRMC 3.32A.Please download and use ServerView from the following URL when you use BIOS 1.09/iRMC 3.32A./global/services/computing/server/ia/driver/*The number of version of BIOS is displayed in the first line on the POST screen.A part surrounded with a frame is the number of the version of the BIOS.“PhoenixBIOS Version 4.06 Rev. 1.01. 2529”※You could confirm the iRMC firmware version in the following steps.- BIOS SetupTurn on the server and press F2 key to go to BIOS setup window. Then open "Info" window by pressing F1 key to check the iRMC firmware version.example) iRMC Firmware 001.66A4. Updates for "PRIMERGY RX200 S4 User's Guide" (B7FH-5141-01EN)Chapter 4 "4.3 Storing the System Configuration Information" (Page 77)Deletion Delete the incorrect description below.■ Creating "Server Management Tools" disk"Server Management Tools" disk is required to be created when stated as "blank" on the label of the "Server Management Tools" disk, supplied with the server. Create Server Management Tools by referring to "4.4 Creating Maintenance Tools and Driver Disks" (p.82).4.3.1 Storing the BIOS Information and the Remote Management Controller Information (Page 79) Deletion Delete the following notes.The file name is given as "cmosfile" when a file name is not input.4.3.2 Recovering the BIOS / Remote Management Information (Page 79 - 80)Correction There is a misspelling on the command line.4 Enter the following command and press the [Enter] key.Incorrect:A:╲SMT>biosreset.batA:╲SMT>biosrest.batCorrect:the following notes.・ The file name is given as "cmosfile" when a file name is not input."4.3.1Storing the BIOS Information and the Remote Management Controller Information" (Page 78) and"4.3.2 Recovering the BIOS / Remote Management Information" (Page 79)Deletion Delete the incorrect description below."Server Management Tools" disk is required to be created when stated as "blank" on the label of the "Server Management Tools" disk, supplied with the server. Create Server Management Tools by referring to "4.4 Creating Maintenance Tools and Driver Disks" (p.82).Chapter 6 "6.4.2 Installable Memory Modules and Notes" (Page 129)Correction There is an incorrect description under the "How to identify a memory module ".Incorrect:Identification labelCorrect:Addition Add the "Identification label patterns" table below.Identification label patternsWhen a memory module is placed with the circled corner in the above figure shown on the lower left side, the identification labels are applied in one of the following patterns.Table: Identification Label PatternsPattern Label A Label B Label C1 - - -2 Applied - -3 - Applied -4 - -Applied5 AppliedApplied -6 Applied - Applied7 -AppliedApplied8 Applied Applied AppliedChapter 7 "7.2 BIOS setup utility""7.2.8 Advanced System Configuration Submenu" (Page 177~178)Addition Added the setup menu item as bellow.Item Setting DescriptionMemory Throttling ・Disabled(Initial value)・EnabledSetting for memoryMemory Power Mode ・Performance(Initial value)・EnergySetting for power control of memory.High Bandwidth Enabled(unchangeable)Setting for FSB (Front Side Bus).Enhanced Idle Power State Disabled(Initial value)EnabledSetting for power control under OS idlingstate."7.2.10 IPMI Submenu" (Page 180)Correction There are errors in the Setting and the description for "Clear System Event Log".table: Items on the IPMI SubmenuItem Setting DescriptionClear System Event Log ・Disabled(Initial value)・Enabled Sets whether or not to delete the logs stored in the System Event Log (SEL)."7.2.17 Exit Menu" (Page 189)Correction There is an error in the description for "Get Default Vaules".Incorrect: "Local IP address", "Subnet Mask", and "Gateway Address" in the LAN Settingssubmenu are not reset.Correct: All of the submenus in the LAN Settings are not reset.Appendix A Server Specifications (Page 226~229)Correction There is an error in the “table: Server Specifications” , “Supported OS”.(SAS model/SATA model)Correcttable: Server specifications (SAS model)Item Functions and specificationsType DisklessTypeProduct name PRIMERGY RX200 S4 (SAS model) 3.5-inch HardDisk TypePRIMERGY RX200 S4 (SAS model)2.5-inch Hard Disk TypeProduct ID PGUR2041A PGUR204AA PGUR2041A2 PGUR204AA2Chipset Intel®3000Standard Intel® Xeon® Processor E5205(1.86GHz/6MB)Intel® Xeon®Processor L5410(2.33GHz/12MB)Intel® Xeon®Processor E5205(1.86GHz/6MB)Intel® Xeon®Processor L5410(2.33GHz/12MB)Conversion kit/Add-on Intel® Xeon® Processor X5260(3.33GHz/6MB)Intel® Xeon® Processor E5405(2GHz/12MB)Intel® Xeon® Processor E5420(2.50GHz/12MB)Intel® Xeon® Processor X5460(3.16GHz/12MB)Intel® Xeon® Processor X5270(3.50GHz/6MB)Intel® Xeon® Processor X5470(3.33GHz/12MB)Intel® Xeon®ProcessorL5410(2.33GHz/12MB)Intel® Xeon®Processor X5260(3.33GHz/6MB)Intel® Xeon®Processor E5405(2GHz/12MB)Intel® Xeon®Processor E5420(2.50GHz/12MB)Intel® Xeon®Processor X5460(3.16GHz/12MB)Intel® Xeon®ProcessorL5410(2.33GHz/12MB)CPUNumber ofmultiplication1(Max.2)Correcttable: Server specifications (SATA model)Item Functions and specificationsType DisklessType Product name PRIMERGY RX200 S4 (SATA model) 3.5-inch Hard Disk TypeProduct ID PGUR2041B PGUR204ABChipset Intel®3000Standard Intel® Xeon® Processor E5205 (1.86GHz/6MB)Intel® Xeon® Processor L5410(2.33GHz/12MB)Conversion kit/Add-onIntel® Xeon® Processor X5260 (3.33GHz/6MB)Intel® Xeon® Processor E5405 (2GHz/12MB)Intel® Xeon® Processor E5420 (2.50GHz/12MB)Intel® Xeon® Processor X5460 (3.16GHz/12MB)Intel® Xeon® Processor X5270(3.50GHz/6MB)Intel® Xeon® Processor X5470(3.33GHz/12MB)Intel® Xeon® Processor L5410(2.33GHz/12MB)CPUNumber ofmultiplication1(Max.2)Addition Add the “■Supported OS” below.■ Supported OSThe following OSes are supported.• Windows Server 2008 Standard (32-bit)• Windows Server 2008 Standard (64-bit)• Windows Server 2008 Enterprise (32-bit)• Windows Server 2008 Enterprise (64-bit)For details refer to following URL./global/services/computing/server/ia/5.Updates for "PRIMERGY RX200 S4 Configuration Sheets" (CA92276-8032-01)B Configuration Sheets of BIOS Setup Utility Parameters"B.2 Parameters in the Advanced menu / Advance System Configuration Submenu" (Page 11) Addition Added the setup menu item as bellow.Item Initial value Setting Memory Throttling Disabled ( )EnabledMemory Power Mode Performance ( )EnergyHigh Bandwidth Enabled ( )DisabledEnhanced Idle PowerStateDisabled ( )Enabled"B.2 Parameters in the Advanced menu / IPMI Submenu" (Page 12)Correction There is an error in the “Clear System Event Log”. The value of “Clear System Event Log” can bechanged. The initial value of “Clear System Event Log” is “Disabled”.。
PacketShaper 产品说明书
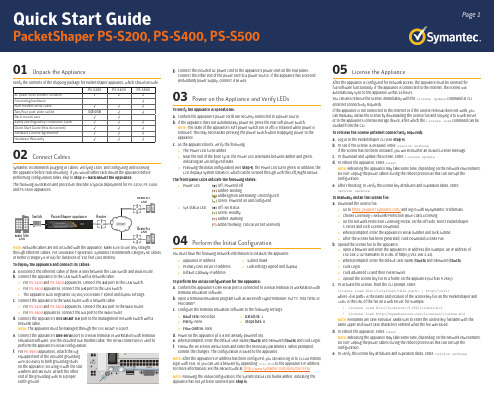
Page 101 Unpack the ApplianceVerify the contents of the shipping package for PacketShaper appliance, which should include:PS-S200PS-S400PS-S500AC power cords (number included)122Grounding hardware √Null-modem serial cable √√√Two/four post slide-rail kit Optional√√Rack-mount ears√√Safety and Regulatory Compliance Guide √√√Quick Start Guide (this document)√√√Software License Agreement √√√Hardware Warranty√√√02 Connect CablesSymantec recommends plugging in cables, verifying LEDs, and configuring and licensingthe appliance before rack-mounting. If you would rather rack-mount the appliance before performing configuration tasks, skip to Step 7—Rack-Mount the Appliance .The following illustration and procedure describe a typical deployment for PS-S200, PS-S400, and PS-S500 appliances.Note: Network cables are not included with the appliance. Make sure to use only straight-through Ethernet cables. For 1000Base-T operation, Symantec recommends Category 5E cables or better (Category 6 or 6A) for distances of 330 feet (100 meters). To deploy the appliance and connect its cables:a. Disconnect the Ethernet cable (if there is one) between the LAN switch and WAN router.b. Connect the appliance to the LAN switch with a network cable:o For PS-S200 and PS-S400 appliances, connect the 2:0 port to the LAN switch. o For PS-S500 appliances, connect the 1:0 port to the LAN switch.o The appliance auto-negotiates 10/100/1000 Base-T speed and duplex settings.c. Connect the appliance to the WAN router with a network cable:o For PS-S200 and PS-S400 appliances, connect the 2:1 port to the WAN router. o For PS-S500 appliances, connect the 1:1 port to the WAN router.d. Connect the appliance’s SYS MGMT 0:0 port to the management network switch with a network cable.Note: The appliance must be managed through the SYS MGMT 0:0 port.e. Connect the appliance’s DB9 seria l port to a serial terminal or workstation with terminal emulation software. Use the included null-modem cable. The serial connection is used to perform the appliance’s initial configuration.f. For PS-S500 appliances, attach the lug-equipped end of the included grounding wire (10 AWG) to both grounding studs on the appliance, securing it with the star washers and M5 nuts. Attach the other end of the grounding wire to a proper earth-ground.g. Connect the included AC power cord to the appliance’s power inlet on the rear panel. Connect the other end of the power cord to a power source. If the appliance has a second (redundant) power supply, connect it as well.03 Power on the Appliance and Verify LEDsTo verify the appliance is operational:a. Confirm the appliance’s power cords are securely connected to a power source.b. If the appliance does not automatically power on, press the rear soft power switch.Note: The state of the appliance’s soft power switch (on or off) is retained when power is removed. This may necessitate pressing the power switch when reapplying power to the appliance.c. As the appliance boots, verify the following: o The Power LED turns amber.o Near the end of the boot cycle, the Power LED alternates between amber and green, indicating an unconfigured state. o Following the initial configuration (see Step 4), the Power LED turns green. In addition, the LCD displays system statistics, which can be scrolled through with the Left/Right Arrows.The front-panel LEDs indicate the following states:: o Power LED (•) Off: Powered off (•) Amber: Booting(•) Amber/green alternating: Unconfigured (•) Green: Powered on and configuredo Sys Status LED (•) Off: No status (•) Green: Healthy (•) Amber: Warning (*) Amber blinking: Critical (or not licensed)04 Perform the Initial ConfigurationYou must have the following network information to initialize the appliance: o Appliance IP addresso Subnet masko Primary DNS server IP address o Link settings (speed and duplex)o Default Gateway IP addressTo perform the initial configuration for the appliance:a. Confirm the appliance’s DB9 serial port is connected to a serial terminal or workstation with terminal emulation software.b. Open a terminal emulation program such as Microsoft HyperTerminal®, PuTTY, Tera Term, or ProComm™.c. Configure the terminal emulation software to the following settings: o Baud rate: 9600 bps o Data bits: 1 o Parity: none o Stops bits: 8 o Flow control: noned. Power on the appliance (if it is not already powered on).e. When prompted, enter the default User Name [touch ] and Password [touch ] and click Login.f. Follow the on-screen instructions and enter the necessary parameters. When prompted, commit the changes. The configuration is saved to the appliance.Note: After the appliance’s IP address has been configured, you can also log in to CLI via remote login with SSH, or you can use a browser by appending /cli.htm to the appliance’s IP address. For more information, see the PacketGuide at: /docs/DOC9776Note: Following the initial configuration, the System Status LED blinks amber, indicating the appliance has not yet been licensed (see Step 5).05 License the ApplianceAfter the appliance is configured for network access, the appliance must be licensed for full software functionality. If the appliance is connected to the Internet, the license will automatically sync to the appliance within 24 hours.You can also retrieve the license immediately with the license update command in CLI (Internet connectivity required).If the appliance is not connected to the Internet or if the license retrieval does not work, you can manually install the license by downloading the license file and copying it to a web server or to the appliance’s internal storage device, after which the license load command can be invoked from the CLI.To retrieve the license (Internet connectivity required):a. Log in to the PacketShaper CLI (see Step 4).b. To see if the license is installed, enter: version verboseIf the license has not been installed, you will encounter an Invalid License message.c. To download and update the license, enter: license update d. To reboot the appliance, enter: resetNote: Rebooting the appliance may take some time, depending on the network environment. DO NOT unplug the power cables during the reboot process as this can corrupt the configuration.e. After rebooting, to verify the license key attributes and expiration dates, enter: version verbose To manually install the license file:a. Download the license file:o Go to https:/// and log in with MySymantec credentials. o Choose Licensing > Network Protection (Blue Coat) Licensing.o On the Network Protection Licensing Portal, on the left side, select PacketShaper S Series and click License Download. o When prompted, enter the appliance’s serial number and click Submit. o After the license has been generated, click Download License File.b. Upload the license file to the appliance:o Open a browser and enter the appliance’s IP address (for example, an IP address of 192.168.2.42 translates to a URL of https://192.168.2.42). o When prompted, enter the default User Name [touch ] and Password [touch ]. o Click Login.o Click Advanced UI and then File Browser.o Upload the license key file to a folder on the appliance (such as 9.256/).c. To activate the license, from the CLI prompt, enter:license load file://localhost/<file path> | http://<url>where <file path> is the name and location of the license key file on the PacketShaper and <url> is the URL of the file on a web server, for example:• license load file://localhost/9.256/license.bcl• license load /licenses/license.bcl Note: Filenames are case sensitive. Make sure to enter the license key filename with the same upper and lower case characters entered when the file was saved.d. To reboot the appliance, enter: resetNote: Rebooting the appliance may take some time, depending on the network environment. DO NOT unplug the power cables during the reboot process as this can corrupt the configuration.e. To verify the license key attributes and expiration dates, enter:version verbosePacketShaper PS-S200, PS-S400, PS-S500RouterSwitch Main Site LANBranch 1LANBranch 2LANPacketShaper AppliancePage 2PS-S200, PS-S400, PS-S500 Quick Start Guide 06 Perform a Graceful ShutdownBefore proceeding to rack-mounting the appliance, log in to the PacketShaper CLI and perform a graceful shutdown of the appliance.To perform a graceful shutdown:a. Log in to the PacketShaper CLI (see Step 4).b. Enter: shutdownWarning: Do not power off the appliance with the soft power switch or by removing the power cables! Abruptly removing power can result in irreparable data loss. Always use the shutdown command from the CLI to power off the appliance.07 Rack-Mount the ApplianceThe slide-rail mounting kit included with the PS-S400 and PS-S500 appliances (available as an option for PS-S200 appliances) allows the appliance to be rack-mounted in a two- or -four-post equipment rack. The slide-rail kit includes the following parts:Note: To rack-mount the appliance, you may need an M4 nut driver or adjustable wrench, #2 Phillips head screwdriver, and rack screws.Note: The following procedure documents how to install the appliance in a four-post equipment rack. For comprehensive information on rack-mounting the appliance, including other configurations, see the S-Series Maintenance and Upgrade Guide at: /docs/DOC9795To install the appliance in a four-post equipment rack:a. Disassemble the two slide-rail assemblies:o Fully extend each slide-rail by sliding out the inner rails until they reach the stop.o Release the white slide latches (toward the rear of the inner rails) and slide the inner rails all the way out. o Slide-rails are symmetrical and can be used with either side of the chassis.b. Attach the two inner rails to the appliance:o Align each inner rail to the mounting posts on each side of the chassis. Slide the rail toward either the front (PS-S200 and PS-S400) or rear (PS-S500) of the chassis until each of the mounting posts snap into place.o Secure the inner rails to the appliance with M3 screws:• For PS-S200 and PS-S400 appliances, use one M3 screw in the center of each rail.• For PS-S500 appliances, use two M3 screws in each rail.c. For PS-S200 and PS-S400 appliances, install the two rack ears. Align them with the mounting posts on the chassis sides near the front of the appliance and secure them with the included fasteners.d. Assemble the two slide-rails and install them in the rack:o Loosely attach Rail_C to Rail_A. Secure the rails with three M3 screws inserted through the slot in Rail_C and screwed into three holes in Rail_A. Make sure the screws areequidistant from each other so the load will be evenly distributed on the rail. Do not yet fully tighten the screws.Note: The precise attachment location of the screws will depend on how far Rail_C will extend or retract to fit the rack. It may be necessary to remove Rail_C from Rail_A to determine the proper installation length. o Install the assembled slide-rails in the rack:• Secure the front bracket for Rail_A to the outside front of the rack using two rack screws. Do not yet fully tighten the screws. You will do so after the appliance is installed in the rack.• Extend or retract Rail_C to align the rear bracket with the outside rear of the rack. Secure the bracket with two M3 screws. Do not yet fully tighten the screws. You will do so after the appliance is installed in the rack.• Tighten the side-mounting screws for Rail_C.• Verify the slide-rail assemblies are installed at the same rack eight.e. Install the appliance in the rack:o Align the inner rails attached to the appliance with the slide-rails in the rack and slide the appliance half-way into the track.o Press the gray locking tabs on the inner rails to slide the appliance all the way into the rack. o Slide the appliance out of the rack, far enough to access the rack screws. Fully tighten the rack screws for the front and rear brackets to secure the slide-rails to the rack.o Gently push the appliance all the way to the back of the rack and tighten the thumbscrews on the retaining ears to prevent the appliance from sliding out.f. Reconnect the cables as documented in Step 2—Connect Cables and verify the appliance is functioning as in Step 3—Power On the Appliance and Verify LEDs .Technical Supporto Contact Informationhttps:///en_US/contact-support.html o MySymantechttps://DocumentationPacketShaper Software Documentationo /docs/DOC9776Appliance Documentationo S-Series Maintenance and Upgrade Guide /docs/DOC9795o S200 Series Safety and Regulatory Compliance Guide /docs/DOC10311 o S400 Series Safety and Regulatory Compliance Guide /docs/DOC9996 o S500 Series Safety and Regulatory Compliance Guide/docs/DOC10248CAUTION:Before rack-mounting the appliance:o Power off the appliance and disconnect all cables.o Verify that the weight of the system does not exceed the rack’s fully populated weight limit. For more information, refer to the manufacturer’s instructions included with the rack. o For weight stability, load the rack from the bottom up. o Read the “Rack Mount Warnings” section of the Safety and Regulatory Compliance Guide . o Take adequate safety and grounding measures to avoid creating anelectrical shock hazard and to prevent bodily injury.Rail_CRail_ARail_B (2)(used only for 2-post racks)Rail_C。
戴尔 PowerEdge 2800 系统仅限服务部件更换程序说明书

Dell™ PowerEdge™ 2800 Systems Service -Only Parts Replacement ProceduresBefore You BeginRecommended ToolsServicing a Tower SystemSCSI Backplane BoardControl Panel AssemblySystem BoardRemoving the System From the RackNotes, Notices, and CautionsAbbreviations and AcronymsFor a complete list of abbreviations and acronyms, see your Installation and Troubleshooting Guide .Information in this document is subject to change without notice.© 2004 Dell Inc. All rights reserved.Reproduction in any manner whatsoever without the written permission of Dell Inc. is strictly forbidden.Trademarks used in this text: Dell , the DELL logo, and PowerEdge are trademarks of Dell Inc.Other trademarks and trade names may be used in this document to refer to either the entities claiming the marks and names or their products. Dell Inc. disclaims any proprietary interest in trademarks and trade names other than its own.NOTE: A NOTE indicates important information that helps you make better use of your computer.NOTICE: A NOTICE indicates either potential damage to hardware or loss of data and tells you how to avoid the problem.CAUTION: A CAUTION indicates a potential for property damage, personal injury, or death.Back to Contents PageDell™ PowerEdge™ 2800 Systems Service -Only Parts Replacement ProceduresBefore You BeginRecommended ToolsServicing a Tower SystemSCSI Backplane BoardControl Panel AssemblySystem BoardRemoving the System From the RackBefore You BeginThe procedures in this document require that you remove the cover and work inside the system. While working inside the system, do not attempt to service the system except as explained in this document and in the Installation and Troubleshooting Guide and the User's Guide available on . Always follow the instructions closely, and ensure that you review all safety precautions in the Product Information Guide .The Installation and Troubleshooting Guide contains information on system indicators, messages, and codes; system diagnostics; troubleshooting; parts removal and replacement procedures; and jumpers, switches, and connectors.The User's Guide contains information on the System Setup program.Recommended ToolsYou may need the following items to perform the procedures in this section:lKey to the system keylock l#2 Phillips screwdriver l Wrist grounding strapServicing a Tower SystemlBefore removing the cover and accessing parts within the system, you must place the tower system on its side with the system cover facing up. l If stabilizer feet are attached, remove them or orient the system so that the feet extend over the edge of the work surface.SCSI Backplane BoardRemoving the SCSI Backplane Board1.If applicable, remove the bezel.2.Turn off the system and attached peripherals, and disconnect the system from the electrical outlet and peripherals.3.Remove the system cover.4.Slide the drive tray to the maintenance position. See Figure 1-1.a. Using a #2 Phillips screwdriver, loosen the captive screw that secures the drive tray release lever to the chassis.b. Rotate the drive tray release lever toward the front of the system.c. While grasping both sides of the front panel, slide the drive tray forward as far as possible.CAUTION: See your Product Information Guide for complete information about safety precautions, working inside the computer, and protecting against electrostatic discharge.CAUTION: Only trained service technicians are authorized to remove the system cover and access any of the components inside the system. See your Product Information Guide for complete information about safety precautions, working inside the computer, and protecting againstelectrostatic discharge.Figure 1-1. Moving the Drive Tray to the Maintenance Position5.Disconnect the SCSI data cable(s) from the SCSI backplane. See Figure 1-2.Figure 1-2. Connectors on Back of SCSI Backplane6.If applicable, disconnect the 1x2 backplane power cable from the SCSI backplane. See Figure 1-2.7.To disconnect the control panel cable from the SCSI backplane, grasp the cable's white plastic pull-tab and pull the cable connector directly away fromthe backplane. For the location of the connector on the backplane, see Figure 1-2.8.Unlock and slide the SCSI hard drive(s) out of the system at least 5 cm (2 inches).9.Slide the diskette/optical drive carrier out of the system at least 5 cm (2 inches), to disconnect the carrier from the backplane.10.Remove the SCSI backplane:NOTICE: Note the relative position of each SCSI data cable if more than one cable is attached to the SCSI backplaneNOTICE: When disconnecting the control panel cable, hold the white pull-tab next to the control panel cable connector to prevent damage to the SCSI backplane or the cable itself.NOTICE: To prevent damage to the drives and backplane, you must disengage or remove the SCSI drives from the system before removing thebackplane.NOTICE: If you completely remove the drives from the system, you must note the number of each drive and temporarily label them before removal, so you can replace them in the same locations.a.Lift the spring-loaded blue retention pin away from the front of the backplane, then slide the backplane upward. b. When the backplane cannot slide upward any farther, pull the backplane toward the back of the system to remove it from the retention hooks.11.If applicable, remove the daughter card from the SCSI backplane. See Figure 1-2 for the location of the daughter card connector on the SCSI backplane.Installing a SCSI Backplane Board1.If applicable, install the daughter card on the new backplane.2.Install the new backplane:a. Lower the backplane into the system and carefully feed the control cable through the opening in the backplane.Ensure that any other cables will not interfere or be damaged when installing the new backplane.b.Align the backplane with the retention hooks on the chassis, then fit the backplane over the retention hooks. c. Slide the backplane downward until the blue retention pin snaps into place.3.Connect the control panel cable to the control panel connector on the SCSI backplane. See Figure 1-2.To prevent disconnecting the cable from the control panel, deflect the end of the cable to connect it; do not pull on the cable itself.4.If applicable, reconnect the 1x2 backplane power cable to the SCSI backplane. See Figure 1-2.5.Reconnect the SCSI data cable(s) to the backplane, being very careful to install them in their original locations.6.Return the drive tray to the operating position.a. While grasping both sides of the front panel, slide the drive tray toward the system board until it meets resistance.Ensure that cables are not trapped or damaged as you move the drive tray.b.Rotate the drive tray release lever toward the back of the system. c. Using a #2 Phillips screwdriver, tighten the captive screw that secures the drive tray release lever to the chassis.7.Reinstall the SCSI hard drives in their original locations.8.Replace the diskette/optical drive carrier.9.Reinstall the cover.10.If you removed the feet from a tower system, reinstall them now and place the system in an upright position.11.Reconnect the system to the peripherals and electrical outlet, and turn on the system.12.If applicable, reattach the bezel.Control Panel AssemblyRemoving the Control Panel Assembly1.If applicable, remove the bezel.2.Turn off the system and attached peripherals, and disconnect the system from the electrical outlet and peripherals.3.If the system is a rack system located low enough in the rack to prevent access to the underside of the system chassis, remove the system from therack and place it on a work surface.See "Removing the System From the Rack ."CAUTION: Only trained service technicians are authorized to remove the system cover and access any of the components inside the system. See your Product Information Guide for complete information about safety precautions, working inside the computer, and protecting againstelectrostatic discharge.4.Remove the system cover.5.Remove the SCSI hard drives or filler panels from the center drive bay.6.Slide the drive tray to the maintenance position. SeeFigure 1-1.a. Using a #2 Phillips screwdriver, loosen the captive screw that secures the drive tray release lever to the chassis.b. Rotate the drive tray release lever toward the front of the system.c.While grasping both sides of the front panel, slide the drive tray forward as far as possible.7.If the system is not installed in a rack, place the system on its side as shown in Figure 1-3 or Figure 1-4, with the front edge of the system overhangingthe edge of the work surface.8.Remove the control panel assembly.See Figure 1-3 or Figure 1-4 for the relative location of the control panel assembly. If you are working on a system installed in a rack, the control panel assembly is located under the front edge of the drive tray.a. From inside the center hard drive bay, open the control panel cable clamp on the floor of the drive tray.b.Disconnect the control panel cable from the SCSI backplane. Grasp the cable's white plastic pull-tab and pull the cable connector directly away from the backplane. For the location of the connector on the backplane, see Figure 1-2. c.Using a #2 Phillips screwdriver, remove the screws that secure the control panel assembly to the front panel. (Tower systems have three screws; rack systems use two screws.) See Figure 1-3 or Figure 1-4. d. Remove the control panel assembly from the system by sliding the control panel assembly toward the back of the chassis, then remove theassembly.Figure 1-3. Removing the Control Panel Assembly (Tower System)Figure 1-4. Removing the Control Panel Assembly (Rack System)NOTICE: Before removing SCSI hard drives from the system, you must note the number of each drive and temporarily label them before removal, so you can replace them in the same locations.NOTICE: A rack-configuration system is prone to tipping over if placed on its side.NOTICE: When disconnecting the control panel cable, hold the white pull-tab next to the control panel cable connector to prevent damage to the SCSI backplane or the cable itself.NOTE: While removing the control panel assembly, be careful not to damage the interface cable.Installing the Control Panel Assembly1.Holding the new control panel assembly in one hand, feed the control panel cable into the opening in the system chassis.2.Install the new control panel assembly in the system:a. Align the assembly with the opening in the chassis.b. Fit the assembly into the chassis, then slide it toward the system front panel.c. While holding the assembly in position against the front panel, secure it with the Phillips screws. (Tower systems have three screws; racksystems use two screws.)3.Secure the control panel cable in the clamp on the drive tray. See Figure 1-3 or Figure 1-4.4.Connect the control panel cable to the SCSI backplane.To prevent disconnecting the cable from the control panel, deflect the end of the cable to connect it; do not pull on the cable itself.5.If applicable, carefully lower the system to the horizontal position as shown in Figure 1-1.6.Return the drive tray to the operating position.a. While grasping both sides of the front panel, slide the drive tray toward the system board until it meets resistance.Ensure that cables are not trapped or damaged as you move the drive tray.b. Rotate the drive tray release lever toward the back of the system.c. Using a #2 Phillips screwdriver, tighten the captive screw that secures the drive tray release lever to the chassis.7.Reinstall the SCSI hard drives or filler panels in their original locations.8.Reinstall the cover.9.If you removed the feet from a tower system, reinstall them now, and place the system in an upright position.10.If applicable, replace the system in the rack.11.Reconnect the system to the peripherals and electrical outlet, and turn on the system.12.If applicable, reattach the bezel.System BoardRemoving the System Board1.If applicable, remove the bezel.2.Turn off the system and attached peripherals, and disconnect the system from the electrical outlet.3.If the system is a tower system, place it on a work surface.4.Open the system.5.Slide the drive tray to the maintenance position. See Figure 1-1.a. Using a #2 Phillips screwdriver, loosen the captive screw that secures the drive tray release lever to the chassis.b. Rotate the drive tray release lever toward the front of the system.c. While grasping both sides of the front panel, slide the drive tray forward as far as possible.6.Disconnect any cables attached to expansion cards in the expansion card cage.7.Remove the expansion-card cage. See "Removing the Expansion-Card Cage" in the Installation and Troubleshooting Guide .8.Remove the processor fans and center fan bracket. See "Removing a Processor Fan" and "Removing the Center Fan Bracket" in the Installation andTroubleshooting Guide .9.Remove the memory module fans and back fan bracket. See "Removing a Memory Module Fan" and "Removing and Replacing the Back Fan Bracket" inthe Installation and Troubleshooting Guide.10.Remove the memory cooling shroud. See Figure 6-16 in the Installation and Troubleshooting Guide .11.Remove the memory modules. See "System Memory" in the Installation and Troubleshooting Guide .12.Unlock the power supplies from the system and slide them back 5 cm (2 inches). See "Power Supplies" in the Installation and Troubleshooting Guide .13.Remove the processor(s). See "Processor" in the Installation and Troubleshooting Guide .14.If applicable, remove the RAID key.See Figure 7-7 in "Activating the Integrated RAID Controller" in the Installation and Troubleshooting Guide.15.If applicable, remove the RAC card:a. Deflect the four blue plastic standoffs away from the edges of the card, then lift the front edge of the card to disconnect the card from the systemboard.b. Lift the card from the system.16.If applicable, disconnect the parallel port cable from the system board.17.Remove the center fan assembly cradle.Lift the release tab, then slide the cradle toward the edge of the system board and lift the cradle out of the system. See Figure 1-5.Figure 1-5. Removing the Center Fan Assembly CradleCAUTION: Only trained service technicians are authorized to remove the system cover and access any of the components inside the system. See your Product Information Guide for complete information about safety precautions, working inside the computer, and protecting againstelectrostatic discharge.18.To remove the system board:a. Lift up the blue retention pin and slide the system board toward the front of the system to disengage the board from the retention tabs on thechassis. See Figure 1-6.b. Lift the system board out of the system.Figure 1-6. Removing the System BoardInstalling the System Board1.Unpack the new system board.2.Holding the system board by its front edge and the memory module socket ejectors, carefully lower the system board into the chassis, making sure thatthe I/O connectors on the back edge of the board fit underneath the ledge on the inside of the chassis back panel.When the board is properly positioned, the tabs on the chassis will fit through the corresponding slots in the system board.3.Slide the system board tray toward the back of the chassis until the retention pin snaps into place.4.Replace the center fan assembly cradle.5.If applicable, replace the RAC card. See "Installing a RAC Card" in the Installation and Troubleshooting Guide .6.If applicable, replace the RAID key. See "Activating the Integrated RAID Controller" in the Installation and Troubleshooting Guide .7.If applicable, reconnect the parallel port cable to the system board.CAUTION: Only trained service technicians are authorized to remove the system cover and access any of the components inside the system. See your Product Information Guide for complete information about safety precautions, working inside the computer, and protecting againstelectrostatic discharge.8.Slide the power supply(s) back into the system and secure them with the relase levers. 9.Replace the memory modules. See "Installing Memory Modules" in the Installation and Troubleshooting Guide . 10.Replace the processor(s). See "Replacing a Processor" in the Installation and Troubleshooting Guide . 11.Replace the back fan bracket and center fan bracket. See "Removing and Replacing the Back Fan Bracket" and "Replacing the Center Fan Bracket" in the Installation and Troubleshooting Guide 12.Replace the fans. See "Fans" in the Installation and Troubleshooting Guide . 13.Replace the memory cooling shroud. 14.Replace the expansion-card cage. See "Installing the Expansion-Card Cage" in the Installation and Troubleshooting Guide . 15.If you disconnected any cables from the expansion cards, reconnect them now. 16.Return the drive tray to the operating position.a. While grasping both sides of the front panel, slide the drive tray toward the system board until it meets resistance.Ensure that cables are not trapped or damaged as you move the drive tray.b.Rotate the drive tray release lever toward the back of the system. c. Using a #2 Phillips screwdriver, tighten the captive screw that secures the drive tray release lever to the chassis.17.Reinstall the cover.18.If you removed the feet from a tower system, reinstall them now.19.Reconnect the system to the peripherals and electrical outlet, and turn on the system.20.If applicable, reattach the bezel.Removing the System From the RackIf you are removing the control panel from a system in the lowest rack location, follow these instructions to remove the system from the rack.1.Loosen the thumbscrews that secure the front panel to the front vertical rails (at the front of the rack cabinet).2.Pull the system out of the rack on its slide assemblies until the slide assembly lock snaps into place at the fully extended position.3.While pressing the system locking mechanism release button, pull the system forward to release the system from the rack rails. See Figure 1-7.ing two to four people, grasp the system at each corner and lift the system up and out of the slide assemblies. See Figure 1-7.5.The shoulder screws should lift out of the outermost slide section. If you have difficulty, make certain that the shoulder screws in the slide assembly arealigned with their opening on the top of the slide.6.Place the system on a smooth work surface.Figure 1-7. Removing the System from a RackCAUTION: Removing a system from a position high up in the rack cabinet will require up to four people and may require a sturdy, elevatedplatform to stand on. A mechanical lifting platform or similar equipment of the proper capacity may also be useful. If you attempt to remove and lower the system without enough people to safely perform the task, you risk personal injury to yourself and to others and damage to the system.Back to Contents PageDell™ PowerEdge™ 2800 Systems Service -Only Parts Replacement ProceduresNotes, Notices, and CautionsAbbreviations and AcronymsFor a complete list of abbreviations and acronyms, see your Installation and Troubleshooting Guide .Information in this document is subject to change without notice.© 2004 Dell Inc. All rights reserved.Reproduction in any manner whatsoever without the written permission of Dell Inc. is strictly forbidden.Trademarks used in this text: Dell , the DELL logo, and PowerEdge are trademarks of Dell Inc.Other trademarks and trade names may be used in this document to refer to either the entities claiming the marks and names or their products. Dell Inc. disclaims any proprietary interest in trademarks and trade names other than its own.Back to Contents PageNOTE: A NOTE indicates important information that helps you make better use of your computer.NOTICE: A NOTICE indicates either potential damage to hardware or loss of data and tells you how to avoid the problem.CAUTION: A CAUTION indicates a potential for property damage, personal injury, or death.。
USB接口的RF模块用户指南说明书

CUSTOMER’S CODE RF-Module-USB-Adapter PANASONIC’S CODEPANxxxxDATE11.09.2012TABLE OF CONTENTS1.Scope of this Document (2)2.Description for the Module (2)2.1.Schematic (3)2.2.Description of the USB-Adapter (4)2.3.Connection of the Wireless Moduls (5)3.Software Handling (5)3.1.Device Drivers (5)4.RoHS Declaration (6)5.History for this Document (6)6.Related Documents (6)7.General Information (7)8.Life Support Policy (7)CUSTOMER’S CODE RF-Module-USB-Adapter PANASONIC’S CODEPANxxxxDATE11.09.20121. SCOPE OF THIS DOCUMENTThis User Guide applies to the RF-Module-USB-Adapter which can be used for following Panasonic Modules: PAN2580ETU, PAN4561ETU, PAN4580ETU,PAN7580ETU. The intension is to enable our customers to easily and fast integrate our modules in their product.This guide describes the Hardware and gives usefull hints.2. DESCRIPTION FOR THE MODULEWith the RF Module USB Adapter it is possible to connect following Panasonic ETU-Boards (ETU = EasyToUse) directly with the USB-port of a PC:Customer’s Code Panasonic’s CodePAN2580ETU ENW59635xxxFPAN4561ETU ENWC9A30xxEFPAN4580ETU ENWC9A33xxEFPAN7580ETU ENW59635x3CFPlease contact your local sales office for further details on additional options and services, by visiting /eu/ or write an e-mail to wireless@CUSTOMER’S CODE RF-Module-USB-Adapter PANASONIC’S CODE PANxxxxDATE11.09.20122.1. SCHEMATIC+5V10n F100n F10k+3V 3U S B _A4µ7+3V 3100n F000+5V+3V 34µ7 /n .c .4µ74µ7 /n .c .+3V 3C P 2102270270+3V 3n .c .0270C 3C 1S 1R 3D N 2D P 3G N D @1G N D @2U S B _G N D4U S B _V C C 1X 1G N D @3G N D @4L 1C 2C 4R 7R 8R 9R 10123456789101131211415161718192021222324B Y P A S S6G N D5V _E N 7V _I N 2V _O U T1V _O U T _S E N S E4C 6C 7C 8R E G I N 7VD D6G N D3V B U S 8D +4D -5R S T9S U S P E N D 12S U S P E N D11R I 2D C D 1D T R 28D S R 27T X D 26R X D 25R T S 24C T S 23I C 1G N D E X P G N D M D 1R 4D 2R 6R 1R 2R 5D 3RE S E T U A R T _R X U A R T _T X U A R T _C T SU A R T _R T S V 1.1+Reset Button: Press the button to reset the connected module Converts 5V from USB to 3.3V. Max. output current: 300mA Serial Interface: USB to UART bridgeConnected to pin 3 of the module connector (red, active on high level) D2 Connected to pin 4 of the module connector (red, active on high level) D3 USB-connection (green, active when the USB-connection is OK) Pin Header: Connect the Wireless module to these pin-headerLDO(USB to 3.3V)USB-PlugSerial InterfaceLED D3(USB connection OK)LED D1 and D2(Connected to pin 3 and pin4 of the module)SOFTWARE HANDLINGDEVICE DRIVERSThe USB Interface uses the SINGLE-CHIP USB TO UART BRIDGE CP2102 from Please install the ‘CP210x USB to UART Bridge VCP Drivers’ on your computer toCUSTOMER’S CODE RF-Module-USB-Adapter PANASONIC’S CODEPANxxxxDATE11.09.20124. ROHS DECLARATIONDeclaration of environmental compatibility for supplied products:Hereby we declare to our best present knowledge based on declaration of our suppliers that this product do not contain by now the following substances which are banned by Directive 2002/95/EC (RoHS) or if contain a maximum concentration of 0,1% by weight in homogeneous materials for•Lead and lead compounds•Mercury and mercury compounds•Chromium (VI)•PBB (polybrominated biphenyl) category•PBDE (polybrominated biphenyl ether) categoryAnd a maximum concentration of 0,01% by weight in homogeneous materials for•Cadmium and cadmium compounds5. HISTORY FOR THIS DOCUMENTRevision Date Modification / Remarks0.10 11.05.2012 1st preliminary version.6. RELATED DOCUMENTSFor an update, please search in the suitable homepage.[1] Silabs CP2101 Datasheet/Support%20Documents/TechnicalDocs/cp2102.pdf[2] The latest driver for Silabs CP2102/products/mcu/Pages/USBtoUARTBridgeVCPDrivers.aspxCUSTOMER’S CODE RF-Module-USB-Adapter PANASONIC’S CODEPANxxxxDATE11.09.20127. GENERAL INFORMATION© Panasonic Industrial Devices Europe GmbH 2012.All rights reserved.This product description does not lodge the claim to be complete and free of mistakes. Please contact the related product manager in every case.If we deliver ES samples to the customer, these samples have the status Engineering Samples. This means, the design of this product is not yet concluded. Engineering Samples may be partially or fully functional, and there may be differences to be published Data Sheet.Engineering Samples are not qualified and are not to be used for reliability testing or series production.Disclaimer:Customer acknowledges that samples may deviate from the Data Sheet and may bear defects due to their status of development and the lack of qualification mentioned above. Panasonic rejects any liability or product warranty for Engineering Samples. In particular, Panasonic disclaims liability for damages caused by•the use of the Engineering Sample other than for Evaluation Purposes, particularly the installation or integration in an other product to be sold by Customer, •deviation or lapse in function of Engineering Sample,•improper use of Engineering Samples.Panasonic disclaimes any liability for consequential and incidental damages.In case of any questions, please contact your local sales partner or the related product manager.8. LIFE SUPPORT POLICYThis Panasonic product is not designed for use in life support appliances, devices, or systems where malfunction can reasonably be expected to result in a significant personal injury to the user, or as a critical component in any life support device or system whose failure to perform can be reasonably expected to cause the failure of the life support device or system, or to affect its safety or effectiveness. Panasonic customers using or selling these products for use in such applications do so at their own risk and agree to fully indemnify Panasonic for any damages resulting.。
HP Device Manager 4.7 管理员指南
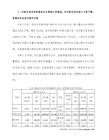
HP Device Manager 4.7©Copyright 2015–2017 HP Development Company, L.P.ARM 是 ARM Limited 的注册商标。
Java 是 Oracle 和/或其子公司的注册商标。
Linux® 是 Linus Torvalds 在美国和其他国家/地区的注册商标。
Microsoft、Windows 和 Windows Server 是 Microsoft Corporation 在美国和/或其他国家/地区的注册商标或商标。
Pentium 是 Intel Corporation 在美国和其他国家/地区的商标。
保密的计算机软件。
需要有 HP 颁发的有效许可证才能拥有、使用或复制。
与 FAR 12.211 和 12.212 相一致,依据供应商的标准商业许可将“商业计算机软件、计算机软件文档和用于商业单位的技术数据”许可给美国政府使用。
本文档中包含的信息如有更改,恕不另行通知。
随 HP 产品和服务附带的明确有限保修声明中阐明了此类产品和服务的全部保修服务。
本文档中的任何内容均不应理解为构成任何额外保证。
HP 对本文档中出现的技术错误、编辑错误或遗漏之处不承担责任。
第四版: 2017 年 7 月第一版:2015 年 8 月文档部件号: 834476-AA4用户输入语法项您必须输入用户界面的文本以等宽字体表示。
项目说明无括号或大括号的文本您必须完全依原样键入的项目<尖括号内的文本>您必须提供的值的占位符; 省略括号[方括号内的文本]可选项; 省略括号{大括号内的文本}您只能从其中选择一项的一组项目; 省略大括号|项目分隔符,用于分隔您只能从其中选一项的项目; 省略竖线...可以或必须重复的项目; 省略省略号iiiiv 用户输入语法项目录1 入门 (1)术语与定义 (1)存储库协议 (2)部署示例 (3)2HPDM Console 概述 (4)登录 HPDM Console (4)设备选项卡 (5)HPDM Gateway 选项卡 (6)显示设备属性 (7)基本资产信息 (7)收集完整的资产信息 (8)显示完整的设备资产信息 (8)3 设备发现 (9)自动注册(常规瘦客户机) (9)DNS 服务记录 (9)创建 DNS 服务记录 (9)故障排除 (10)设置静态域名(仅适用于 Windows) (10)自动注册(CoIP 零客户机) (10)使用 DNS 服务记录 (10)使用 DHCP 供应商类别选项 (11)搜索设备 (12)使用 Walking With IP Range(用 IP 范围扫描)的方法 (12)配置 IP 范围 (12)使用 Walking With IP List(用 IP 列表扫描)方法 (12)手动注册设备 (13)手动注册多个设备 (13)4 任务和任务模板 (14)任务模板 (14)创建任务模板 (14)将任务模板添加到“收藏夹”列表 (15)v导出任务模板 (15)导入任务模板 (15)从负载中生成模板 (15)复制 Deploy Image 模板以用于不同的 OS 类型 (16)模板序列 (16)基本模板序列 (16)高级模板序列 (16)任务 (17)执行任务 (17)任务状态图标 (18)任务参数 (18)任务延迟 (19)显示任务属性 (19)暂停任务 (19)继续任务 (20)重新发送任务 (20)取消任务 (20)删除任务 (20)显示任务日志 (20)显示任务的成功率 (21)打开用于远程控制的 VNC 查看器 (21)打开结果模板 (21)查看所有用户的任务 (21)任务规则 (21)添加新规则 (21)5 设备管理 (23)查看设备 (23)删除设备 (23)分组设备 (24)使用 DHCP 标签设置分组信息 (24)切换到手动分组 (24)添加新手动分组 (24)动态分组 (24)创建新动态分组方案 (25)切换到动态分组 (25)快速搜索 (25)过滤设备 (25)创建新的设备过滤器 (25)vi编辑设备过滤器 (25)安全过滤器 (26)检查网络连接状态 (26)远程控制设备 (27)电源管理 (27)管理常规瘦客户机 (27)更改设备的主机名 (27)捕获和部署连接 (27)克隆和部署设置 (28)应用自定义设置 (28)管理文件和注册表设置 (29)捕获文件 (30)部署文件 (30)删除文件 (31)管理设备注册表设置 (31)克隆注册表设置 (31)添加、编辑和删除注册表设置 (31)远程执行命令 (32)远程执行 Windows 脚本 (33)暂停 _File and Registry 任务 (33)添加或删除程序记录 (33)运行脚本 (33)使用 SCEP 注册证书 (34)管理 PCoIP 零客户机 (34)捕获连接 (34)部署连接 (35)更新固件 (35)6 映像操作 (36)不使用 PXE 的映像 (36)捕获不使用 PXE 的映像 (36)不使用 PXE 的映像捕获期间保留的设置 (37)部署不使用 PXE 的映像 (37)不使用 PXE 的映像部署期间保留的设置 (38)使用 PXE 的映像 (38)创建 PXE Deploy 模板 (39)导入映像文件 (39)将 Deploy Image 模板转换为 PXE Deploy 模板 (39)复制现有 PXE Deploy 模板,以用于不同的 OS (39)vii将设备配置为从 PXE 引导 (40)本地更改引导顺序 (40)远程更改引导顺序 (40)为 PXE 映像配置 DHCP 服务器 (42)DHCP 服务器与 HPDM Server 安装在不同的物理服务器上 (42)DHCP 服务器与 HPDM Server 安装在同一物理服务器上 (42)为 PXE 映像配置 Linux DHCP 服务器 (43)为 PXE 映像配置路由器 (43)为 PXE 映像在传统 Neoware 设备上配置 BIOS 设置 (44)部署映像 (44)故障排除 (44)7 存储库管理 (46)配置 HPDM Master Repository (46)配置 HPDM Child Repository (46)删除 HPDM Child Repository (46)导出库 (47)导入库 (47)同步库 (47)内容管理 (47)查看详细的相关文件信息 (48)从 HPDM Master Repository 删除内容 (48)从 Files Captured(已捕获文件)类别下载内容 (48)库映射 (48)批处理映射 (48)每个设备映射 (48)8 安全性管理 (49)用户管理 (49)添加用户 (49)删除用户 (49)向组分配用户 (49)更改用户的密码 (49)为用户分配安全过滤器 (50)添加组 (50)向组分配权限 (50)向组分配用户 (50)viii使用 LDAP 和 Active Directory 进行用户身份验证 (51)配置 (51)导入用户和组 (52)身份验证管理 (53)密钥管理 (54)HPDM Gateway 访问控制 (55)9 报告管理 (56)添加报告 (56)编辑报告 (56)删除报告 (56)生成报告预览 (57)10HP Update Center (58)生成任务模板 (58)配置 HP Update Center 代理设置 (58)11HPDM Server Backup and Restore Tool (60)备份 HPDM Server (61)恢复 HPDM Server (62)12HPDM Port Check Tool (63)13HPDM Archive Tool (64)14 分组工具 (65)在自定义脚本中使用 groupingtoolex 命令 (65)示例命令 (65)定期调用自定义脚本 (65)示例程序 (66)15HPDM Agent 轮询和错误日志记录 (67)HPDM Agent 轮询 (67)错误日志记录 (67)HPDM Agent 日志记录 (67)HPDM Gateway 日志记录 (67)ixHPDM Server 和 HPDM Console 日志记录 (68)HPDM Master Repository Controller 日志记录 (68)附录 A 任务模板参考 (69)文件和注册表 (69)Agent (69)连接 (69)映像 (70)操作 (70)设置 (70)模板序列 (71)附录 B 端口参考 (72)HPDM Console 端口(入站) (72)HPDM Console 端口(出站) (72)HPDM Server 端口(入站) (73)HPDM Server 端口(出站) (73)HPDM Gateway 端口(入站) (74)HPDM Gateway 端口(出站) (74)HPDM Agent 端口(入站) (75)HPDM Agent 端口(出站) (76)存储库端口(入站) (77)存储库端口(出站) (78)索引 (80)x1入门要查找最新的 HPDM 软件、管理员指南(本文档)、白皮书和版本说明:访问 ftp:///pub/hpdm。
Parker SSD Drives PMAC电机Alignment for C005 Pos Fbk
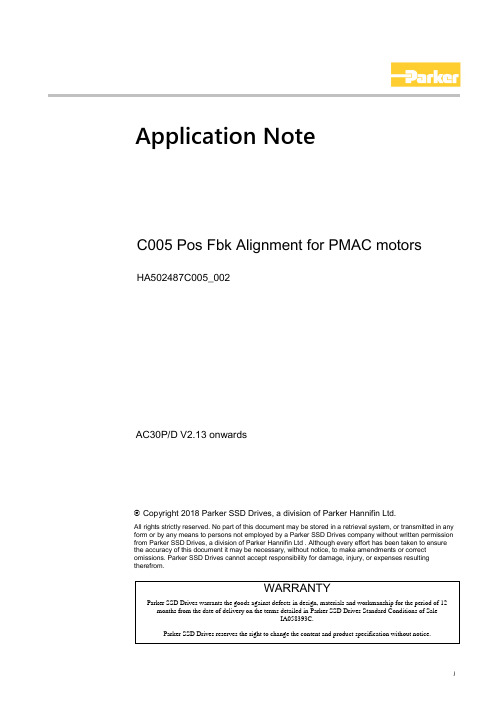
Application NoteC005 Pos Fbk Alignment for PMAC motorsHA502487C005_002AC30P/D V2.13 onwardsCopyright 2018 Parker SSD Drives, a division of Parker Hannifin Ltd.All rights strictly reserved. No part of this document may be stored in a retrieval system, or transmitted in any form or by any means to persons not employed by a Parker SSD Drives company without written permission from Parker SSD Drives, a division of Parker Hannifin Ltd . Although every effort has been taken to ensure the accuracy of this document it may be necessary, without notice, to make amendments or correct omissions. Parker SSD Drives cannot accept responsibility for damage, injury, or expenses resulting therefrom.iRequirementsIntended UsersThis Application Note is to be made available to all persons who are required to install,configure or service equipment described herein, or any other associated operation.The information given is intended to enable the user to obtain maximum benefit from theequipment.Application AreaThe equipment described is intended for industrial motor speed control utilising AC induction orAC synchronous machines.PersonnelInstallation, operation and maintenance of the equipment should be carried out by qualifiedpersonnel. A qualified person is someone who is technically competent and familiar with allsafety information and established safety practices; with the installation process, operation andmaintenance of this equipment; and with all the hazards involved.HazardsRefer to the Safety Information given at the front of the Product Manual supplied with everyParker SSD Drives product.iiC005P OS F BK A LIGNMENT FOR PMACM OTORSAbstractThis Application Note gives information and how to use the Pos Fbk Alignment feature to align position frommotor feedback to the PMAC motor back EMF. This is required to run the PMAC motor in Vector Control mode. Pre-RequisiteThe pre-requisites are :- a AC30 drive- a feedback attached to the motor with the associated feedback option fitted into the drive.Parameters described below are part of PMAC Motor Data and Pos Fbk Aligmnent. IntroductionBy definition, the motor Vector Control is based on the assumption that the back EMF is crossing the 0V line in a positive direction when the electrical position is also crossing the 0° line in a positive way. Another requirement is to insure a positive ‘encoder/resolver’ rotation with a positive electrical motor rotation ( U, V, W ).1The Pos Fbk Alignment feature is used to automatically calculate any offset between the Zero encoder absolute position and the motor back EMF, as well as selecting the correct wiring of the motor ( U, V, W sequence ) with the encoder position.The feature needs to be run at least once with a PMAC motor associated to an absolute encoder type.The feature needs to be run after each power cycle with a PMAC motor associated to a relative encoder type (pulse encoder for example ). In that case, the absolute position information is lost by the power cycle and thealignment is required after power ON.The feature is run on a motor free to rotate, no load attached to the motor shaft.Regardless of the Alignment Method selected, the motor should move during the sequence.Pos Fbk Alignment operation2 Methods can be selected to align feedback and motor.Alignment Method = MANUALThe motor is moved to an electrical position corresponding to the motor phase selected by Alignment On Motor parameter.This electrical position depends on the PMAC Wiring type selected and on the real motor phase wiring.PMAC Encoder Offset is calculated by looking at real position from the active encoder compared to theoretical position where the motor is.So, it depends also on the encoder settings ( inverted or not ).For standard connections ( correct U, V, W motor wiring sequence and position from encoder varying in a positive way looking at the motor front shaft ), position offset is extracted and written back into PMAC Encoder Offset.Correct connection of the encoder means that a clockwise rotation of the motor front shaft equals a positiveposition variation.Correct motor wiring means phase U, V, W rotating in a correct sequence for a clock wise rotation of the motor front shaft.Considering a standard connection, the following table gives possible encoder and PMAC Wiring settings and results on speed control :** Looking the front shaft of the motor23*** The motor is uncontrolled. It could overspeed, be stalled, or running at constant speed without any control.Alignment Method = AUTOMATICIn case of a correct wiring of encoder and/or motor phases, the sequence is as follows :Current%Elec pos 1 2 3 4 5 6 7 8 9 10 11 12States 210°-30°90°During the final state ( 11 ) , the Alignment Offset is automatically calculated and is passed back to 1808 PMAC Encoder OffsetAlso 1809 PMAC Wiring is set to STANDARDIn the case of a wrong wiring of encoder and/or motor phases, the sequence is as follows :Current%Elec pos 1 2 3 4 5 6 7 8 9 10 11 12 13 14 15 16 17 18States 210°-30°90°From State 4 to 9, a wrong direction as been detected, and the direction should be reverted. Alignment Direction is set to REVERSE.During the final state ( 17 ), the Alignment Offset is automatically calculated and is passed back to 1808 PMAC Encoder OffsetAlso 1809 PMAC Wiring is set to REVERSE.In that case, the direction of motor rotation has been changed during the Pos Alignment sequence. Please verify if the new direction is compatible with your application.If you want to change it, please change the Invert parameter of the active encoder used to control the motor and run again the Pos alignment sequence.Setting up Alignment Method = DIRECTION TEST allows to verify the direction of positive electrical position by slowly rotating the motor. A correct wiring of the motor phases should turn the motor in a clockwise direction looking at the front shaft of the motorThe motor is slowly rotated with the following sequence U, V, W, U, V, W…..It allows to verify the rotation direction and detect any wiring inversion on the motor phases.Active encoder Invert parameter has no effect during this test.Looking at the position variation from the active encoder may help to know if the active encoder is correctlywired.Considering a correct connection of the motor phases :When running this Method, either set 1257 Seq Stop Method to DISABLE VOLTAGE or 0505 Zero SpeedThreshold to 1% otherwise you may end up with a motor rotating at slow speed for 60s without any possibility to stop it.Running the sequenceThe feature is run on a motor free to rotate, no load attached to the motor shaft.Regardless of the Alignment Method selected, the motor should move during the sequence.The sequence is validated by Alignment Enable input.The drive waits for a START/TORQUE ON condition to start the cycle.The sequence can be stopped by a STOP/TORQUE OFF command anywhere during the cycle.A successful sequence sets Alignment Ended = TRUE.A STOP/TORQUE OFF command is needed to stop the sequence.If Alignment Method is set to AUTOMATIC, it is possible that the direction of motor rotation for apositive setpoint could be reversed. The parameter PMAC Wiring can be changed by the sequence ifan incompatibility of direction between the encoder and the motor phases wiring is found.Alignment on Power OnAs the feature needs to be run after each power cycle with a PMAC motor associated to a relative encoder type ( pulse encoder for example ), a parameter 1796 Alignment On Power On xould bet set up to TRUE.4Set to TRUE, it automatically trips the drive after a power up on a Start command until an Alignment sequence is run and completed successfully.ApplicationBelow is a simple example on how to force the system to run a Pos Alignment sequence on the first start after power_up :Alignment On Power On has been set to TRUEAlignment Method is set to Manual ( It could have been set to AUTOMATIC ).Alignment Enable is TRUE from Start-up.The first start command will run the Pos Alignment sequence.A running and successfully sequence resets Alignment_Enable to FALSE.A 1s negative pulse is generated at the end of the sequence ( positive at Q output of TP_1). This information can be used to toggle any command to start the system.The feature is run on a motor free of rotation, no load attached to the motor shaft.Depending of the Alignment Method selected, the motor is moving during the sequence.56。
Siemens ET 200 SP fail-safe Output Modules使用时可能出现的
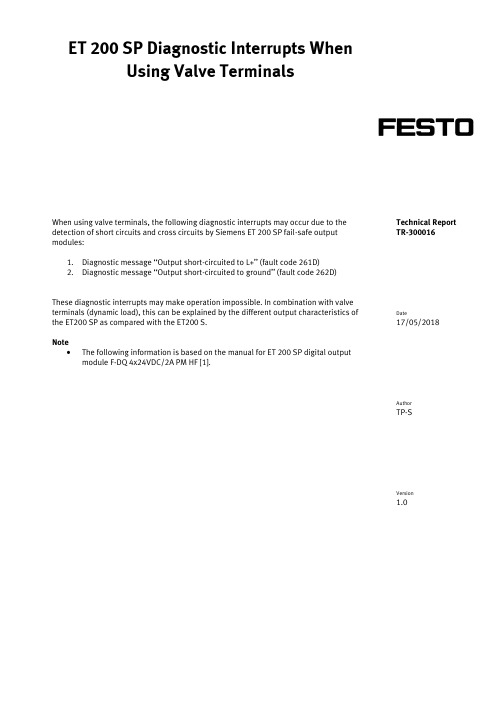
When using valve terminals, the following diagnostic interrupts may occur due to the detection of short circuits and cross circuits by Siemens ET 200 SP fail-safe output modules:1. Diagnostic message “Output short -circuited to L+” (fault code 261D)2. Diagnostic message “Output short -circuited to ground” (fault code 262D)These diagnostic interrupts may make operation impossible. In combination with valve terminals (dynamic load), this can be explained by the different output characteristics of the ET200 SP as compared with the ET200 S.Note• The following information is based on the manual for ET 200 SP digital outputmodule F-DQ 4x24VDC/2A PM HF [1].ET 200 SP Diagnostic Interrupts WhenUsing Valve TerminalsTechnical Report TR-300016Date17/05/2018AuthorTP-SVersion1.0Error descriptionA short circuit (cross circuit) is detected by means of the dark test within a period of time after switching the valve terminal on, which cannot be precisely specified.The following information concerning diagnostic message “output short circuited toL+/ground” is included in the user manual for ET 200SP digital output module F-DQ4x24VDC/2A PM HF (table 6-6, pages 39):ExplanationSection of the user manual, “B.1 Connecting capacitive loads”, indicates that loads with capacitances may result in the detection of a short circuit. This is because the capacitances are not adequately discharged during the configured readback time.The capacitances included in the valve terminals are EMC measures (electromagnetic compatibility) and must be used on account of the harmonised standards for EMC guideline 2014/30/EU, for which reason they cannot be reduced.If no valves are activated during the dark test, existing capacitance is not discharged quickly enough. Furthermore, different numbers of valves on the valve terminal can be switched during the dark test. This results in a dynamic load for the fail-safe output which can also affect the dark test.Solution – Step 1: Increase Readback Time Dark TestAccording to the recommendation included in the section entitled “Setting readback time dark test” (page 21), a higher value should be selected for maximum dark test readback time. If an excessively large value is selected, the valves of the connected valve terminal are switched off and on. As a rule, this switching off and on is audible as a “clattering” sound. These switching operations result in wear and must be taken into consideration when calculating the MTTF D value, resulting in massive restriction of the T10D value and thus the service life of the valves as well.As a first step towards a possible solution, you should try to increase “dark test readback time”. If maximum readback time for the dark test cannot be increased, the “Output short-c ircuited to L+” fault may occur sporadically again and again.If the diagnostic message cannot be eliminated by increasing “dark test readback time”, either the wiring or the used modules will have to be changed.Be sure to observe maximum permissible dark time for the installed valves. This information can be found in the product reliability data sheet for the valves where it’s designated “max. negative test pulse with 1 signal”.Solution – Step 2: Switch Off of Every Valve Terminal Separately Via a Fail-safe Output If a fault message occurs directly after activating the fail-safe output, switch-on current may be too high. This might be the case if you switch off several valve terminals at the same time with a single fail-safe output. In this case, you should try to switch off each valve terminal separately via a fail-safe output. This solution may be possible if you can subsequently increase “dark test readback time”. However, we cannot guarantee that this modification will work as a solution for you because of the above described dynamic load change.Be sure to observe maximum permissible dark time for the installed valves. This information can be found in the product reliability data sheet for the valves where it’s designated “max. negative test pulse with 1 signal”.Solution – Step 3: Increase Load Current with ResistorThe following procedure is described in appendix “B.1 Connecting capacitive loads”, in the section entitled “Remedy for detection a short circuit”:1.Determine the load current and capacitance of the load.2.Locate the operating point in the diagram above (comment: the figure containscharacteristic curves for the switching of capacitive loads relative to configureddark and light test times).3.If the operating point is above the curve, you must increase the load current untilthe new operating point is below the curve by connecting a resistor in parallel. This solution may be possible if only individual valves are switched and short connecting cables are used. As a rule, however, it’s not possible to foresee how many valves will be switched on during the dark test. Consequently, this solution is unusable for most applications.Be sure to observe maximum permissible dark time for the installed valves. This information can be found in the product reliability data sheet for the valves where it’s designated “max. negative test pulse with 1 signal”.Solution – Step 4: Hardware ChangeIf you do not succeed in eliminating the diagnostic message with the two previous solution steps, the hardware must be changed. The following options are available to this end:e of distributed I/O system Siemens ET 200S.e of fail-safe power module Siemens F-PM-E 24 V DC / 8 A PPM (article no.6ES7 136-6PA00-0BC0) instead of fail-safe digital output module Siemens F-DQ4x24 V DC / 2 A PM high feature (article no. 6ES7 136-6DB00-0CA0).e of a valve terminal with directly integrated PROFIsafe, i.e. with CPX andPROFIsafe shutoff module CPX-FVDA-P2 (part no. 1971599) from Festo.If a valve terminal with PROFIsafe shutoff module CPX-FVDA-P2 is used, we are certain that the required short and cross circuit detection functions perfectly in the application.Literature[1] Manual of ET 200SP Digital output module F-DQ 4x24VDC/2A PM HF (6ES7136-6DB00-0CA0), edition 07/2013, A5E03858037-01[2] CPX Terminal Output Module CPX-FVDA-P2, Description (8022607 EN 1209NH[8022613]ImprintPublisher:Festo AG & Co. KGEditorial team:Jürgen KühnlePortfolio ManagementTP-SRuiter Straße 8273734 EsslingenGermanyPhone +49 (0)711 347-4468Fax +49 (0)711 347-54-4468*************************Technical Report TR-300016, 1.0Translation of the original document in German.The German version of this report was completed on 17/05/2018.© Copyright: Festo AG & Co. KG. All rights reserved, including rights to foreign language translations. No part of these publications may be reproduced, transmitted, processed, duplicated or distributed by any means, electronic, mechanical or otherwise, without the written consent from Festo AG & Co. KG. Designations of products mentioned in the publication, which are also registered trademarks, have not been specifically identified. Consequently, designations which do not include the registered trademark symbol (®) cannot be construed as unprotected trade names. No indication regarding the existence of protection by means of patent or utility model is included either.。
4520模块中文操作手册
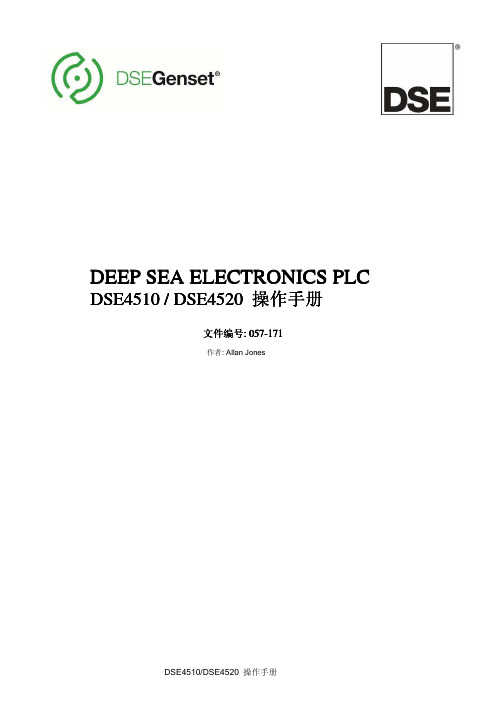
3.2 端口说明.................................................................................................................... 9
3.3 电源要求.................................................................................................................... 9
3.8 通讯端口.................................................................................................................. 15
3.9 通讯端口用法........................................................................................................... 15
本出版物设计到符号释义本出版物设计到符号释义本出版物设计到符号释义本出版物设计到符号释义
DEEP SEA ELECTRONICS PLC
DSE4510 / DSE4520 操作手册
文件编号: 057-171
作者: Allan Jones
DSE4510/DSE4520 操作手册
DSE4510/4520 操作手册
DSE商标以及名称是Deep Sea Electronics公司在英国注册的。
本出版物内所有带有注册商标标志的产品名称归各自公司所有。
Deep Sea Electronics公司保留对本文档进行修订的权利,若有改动,恕不另行通知。
Endress+Hauser Promass 200 HART (0x0054) 的软件更新说明说明
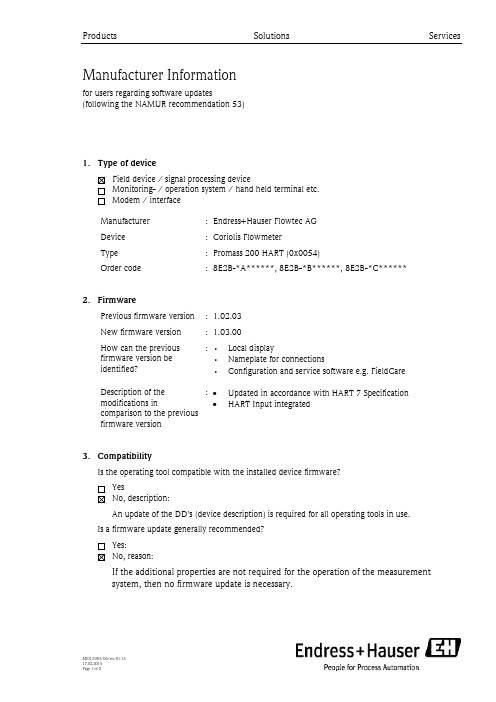
for users regarding software updates(following the NAMUR recommendation 53)1.Type of deviceField device / signal processing deviceMonitoring- / operation system / hand held terminal etc.Modem / interfaceManufacturer:Endress+Hauser Flowtec AGDevice :CoriolisFlowmeterType :Promass200HART(0x0054)Order code :8E2B-*A******, 8E2B-*B******,8E2B-*C****** 2.FirmwarePrevious firmware version : 1.02.03New firmware version : 1.03.00How can the previous firmware version be identified? :•Local display•Nameplate for connections •Configuration and service software e.g. FieldCareDescription of the modifications in comparison to the previous firmware version :∙Updated in accordance with HART 7 Specification ∙HART Input integratedpatibilityIs the operating tool compatible with the installed device firmware?YesNo, description:An update of the DD's (device description) is required for all operating tools in use.Is a firmware update generally recommended?Yes:No, reason:If the additional properties are not required for the operation of the measurement system, then no firmware update is necessary.for users regarding software updates(following the NAMUR recommendation 53)4.Instruction manualIs a new instruction manual necessary due to the modification of the firmware?YesNoWhich manual corresponds to the new firmware?optionsManual Identification Device CommunicationPromass 200 HART Operating instructions BA01027D/06/EN/15.14The new instruction manuals can be referred in Internet: - area …DOWNLOAD“- declaration of the device and kind of manual5.PriceChange in price of device in comparison with the predecessor version?Yes, new list price and update costs (without installation) are enclosedNo。
MyPro 电子产品维修服务套件说明书
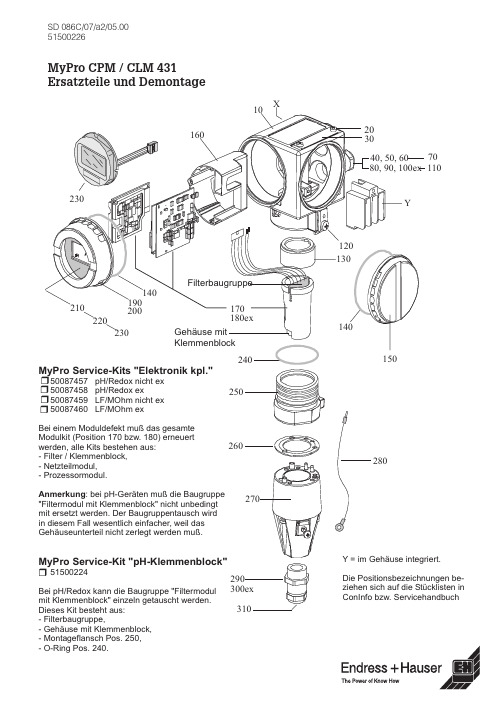
Modulkit (Position 170 bzw. 180) erneuert
werden, alle Kits bestehen aus:
260
- Filter / Klemmenblock,
- Netzteilmodul,
- Prozessormodul.
Anmerkung: bei pH-Geräten muß die Baugruppe "Filtermodul mit Klemmenblock" nicht unbedingt
290 300ex
310
20 30
40, 50, 60 70 80, 90, 100ex 110
Y 120 130
140 150
280
Y = included in the housing. All positions refer to ConInfo or Service Manual part lists.
must not be disassembled.
MyPro service kit "pH terminal block" r 51500224
At pH/ORP the filter module w. terminal block may be exchanged seperately This kit consists of: - Filter module, - Box with terminal block, - Mounting flange pos. 250, - O-ring pos. 240.
SD 086C/07/a2/05.00 51500226
MyPro CPM / CLM 431 Spare parts and disassembling
PixiePlus Device Control Module Installation Guide

(Decora™ wall plate not included)PXE-DCM+PXE-DCM-BLUE+PXE-DCM-AMBER+ Patent US 7,334,067ContentsImportant Safety InstructionsElectrical WarningI. IntroductionII. Installation OverviewIII. Wiring PixiePlus to Display Device IV. PixiePlus InstallationV. Program PixiePlusVI. Configuring Special Features VII. CloningVIII. Complete InstallationIX. OperationX. TroubleshootingXI. Technical Specifications WarrantyFCC ComplianceCopyright 1 2 3 4 5 9 14 17 19 20 21 2223Important Safety Instructions1) Read these instructions.2) Keep these instructions.3) Heed all warnings.4) Follow all instructions.5) Do not use this apparatus near water.6) Clean only with dry cloth.7) Do not block any ventilation openings. Install in accordance with the manufac-turer's instructions.8) Do not install near any heat sources such as radiators, heat registers, stoves, or other apparatus (including amplifiers) that produce heat.9) Do not defeat the safety purpose of the polarized or grounding type plug. A polar-ized plug has two blades with one wider than the other. A grounding type plug has two blades and a third grounding prong. The wide blade or the third prong is pro-vided for your safety. When the provided plug does not fit into your outlet, consult an electrician for replacement of the obsolete outlet.10) Protect the power cord from being walked on or pinched particularly at plugs, convenience receptacles, and the point where they exit from the apparatus.11) Only use attachments/accessories specified by the manufacturer.12) Use only with a cart, stand, tripod, bracket, or table specified by the manufac-turer, or sold with the apparatus. When a cart is used, use caution when moving the cart/apparatus combination to avoid injury from tip-over.13) Unplug this apparatus during lightning storms or when unused for long periods of time.14) Refer all servicing to qualified service personnel. Servicing is required when the apparatus has been damaged in any way, such as power-supply cord or plug is damaged, liquid has been spilled or objects have fallen into the apparatus, the ap-paratus has been exposed to rain or moisture, does not operate normally, or has been dropped.WARNING - To Reduce the Risk of Fire Or Electric Shock, Do Not Expose This Ap-paratus To Rain Or Moisture.Apparatus shall not be exposed to dripping or splashing and no objects filled with liquids, such as vases, shall be placed on the apparatus.Electrical WarningThe PXE-DCM+ is a low-voltage device. Never install the PixiePlus in an electrical back box containing high-voltage wiring. This would cause a serious electrical danger and violate United States national electrical codes.Discrete Control BlankIf the button did not seem to learn correctly, press any other button on the PixiePlus, then press the target button again to rearm it, and repeat the learning procedure. 8. Repeat for Each Button: While still in learning mode, program and verifyeach button.9. Set a button to Macro Mode: If a button has been programmed with multiple commands, the button may be configured to send all commands with a single but-ton press. By default, buttons are configured to Round Robin mode.After verification, and while still in learning mode, press and hold the button you wish to set to Macro mode for approximately five seconds. The PixiePlus will beep three times to indicate that it has now been set to Macro mode.Each button must be independently set to Macro mode.If a button is reprogrammed or the entire device is erased, the code will automati-cally default back to Round Robin mode.A button set to Macro mode that is pressed and held will repeat only the last code in the macro. The button will send only one instance of each code, except the final code. The final code will repeat for as long as the button is held.There is a 600 millisecond delay between each code in the series. Some devices may not be able to respond to multiple commands sent this frequently.10. Controlling Multiple Units of the Same DeviceOne PixiePlus may send identical codes to multiple units of the same device without any additional configuration. For example, you may control two identical projectors with a single PixiePlus by adding an additional IR emitter and wiring it from the Pix-iePlus to a second projector. A single button press on the PixiePlus will send identi-cal codes to both devices, and the PixiePlus will control them in tandem.11. Controlling Multiple DevicesDifferent buttons on a single PixiePlus may be programmed with codes from differ-ent remote controls.Example: You wish to control power and source selection on a projector, and vol-ume on an IR-controllable amplifier.To do so, wire one IR emitter to the LCD monitor and the second IR emitter to the amplifier. Program the PixiePlus power and source buttons with the codes from the LCD monitor remote control. Program the PixiePlus volume buttons with the volume control codes from the amplifier remote control.One PixiePlus may learn IR commands from remote controls from different devices. Each button can be configured to send a single command (normal operation) or multiple commands (macro mode) with a single button press.V. Program PixiePlus cont’dExample: You wish to configure the PixiePlus to send a power command to a pro-jector and a separate power command to an amplifier with single press of the Pix-iePlus POWER ON button.To do so, program the PixiePlus POWER ON button with two commands, Power On from the projector remote, and Power On from the amplifier remote. Then configure the PixiePlus POWER ON button to Macro mode.12. To Erase All Buttons: Set the device to Learning Mode. Press and hold any two buttons to erase the PixiePlus. The whole keypad will blink, first slowly, then quickly. Then all buttons will go dark and the PixiePlus will beep four times, indicat-ing that it has been erased. Once a device has been erased there is no way to un-erase it.13. To Exit Learning Mode: Gently remove the paper clip to exit Learning Mode. Be sure not to hold any buttons while removing the paper clip, or the unit will be set to cloning mode.14. Final Test of Learned Codes: Verify that the IR emitter bud has been placed directly over the IR detector on the device the PixiePlus controls. Press the Pix-iePlus button that you wish to test. A red LED labeled “IR Activity” will blink when the code is being sent, but the emitter bud does not illuminate.15. Troubleshooting: If you cannot control the device, be sure that the emitter bud is positioned correctly. If some buttons work but others do not, try re-programming the buttons that do not work. Make sure that you press the button on the remote for at least one second during learning.Fluorescent lights can interfere with IR signals. Check if the projector is close to a fluorescent light source. If so, try turning off the lights. If this restores control, cover the IR emitter bud and display device IR receiver window with an IR-opaque shield, such as gaffer's tape.See Section X. Troubleshooting beginning on page 21 for more tips.VI. Configuring Special Features1. Configuring the Inactivity Shutdown TimerThe Inactivity Shutdown Timer will automatically shut the display device down if it is not used for a configurable length of time.Example: The PixiePlus Inactivity Shutdown Timer is set to three hours. If no button is pressed on the PixiePlus for three hours, the PixiePlus will begin to beep and flash in warning 120 seconds before three hours has elapsed. If no button is pressed, at three hours the PixiePlus will send all codes programmed to the POWER OFF button.2. Security KeylockThe Security Keylock locks the PixiePlus during disuse to prevent unauthorized use. It disables the keys on the PixiePlus after POWER OFF is pressed, until a Se-curity Keycode is entered on the standard PixiePlus keypad. If the proper code is not entered, the system cannot be turned on or used.Use of the Security Keylock feature requires the DISCRETE POWER ON and POWER OFF keypad module to be inserted. If your device remote has only a “tog-gling power” key, you may still use this module if you program both POWER ON and POWER OFF with the same (toggle) code.How the Security Keylock WorksWhen POWER OFF is pressed, the PixiePlus enters a “locked” state and all keypad buttons go dark.When the system is locked, any button press other than POWER ON is understood as a Security Keycode entry. A soft chirp is emitted, but the key does NOT illuminate and no control operation is performed. If the correct code sequence is entered, the system unlocks, the interface illuminates, and normal operation is restored until the next time POWER OFF is pushed and the system locks again.If the entered code is not correct, the system emits a long beep and remains locked. Security Keycodes may be one to six button presses long. Codes can use any key on the keypad other than POWER ON.By default the Security Keylock feature is off, and the default Security Keycode is OFF-OFF-OFF.To Configure the Security Keylock1. Press and hold both POWER ON and POWER OFF while gently inserting a paper clip into the PixiePlus programming aperture. The PixiePlus will enter “Secu-rity Keylock configuration mode” and communicate the current Security Keylock set-tings as follows:- The Red Status LED indicates whether the Security Keylock feature is enabled (LED is on) or disabled (LED is off).- The PixiePlus will show the existing Security Keycode by illuminating each button in the code in sequence, pausing briefly, then repeating the code.2. To enable or disable the Security Keycode feature, press POWER ON to toggle between enabled/disabled.3. To change the Security Keycode, enter a new code by pressing a sequence of up to six keys, using any keys in any combination, except POWER ON. After the code is entered, the PixiePlus will immediately show the new Security Keycode.hands.IX. OperationPowerPower buttons control power on the projector or monitor. The PixiePlus is always on, and its LED backlit buttons remain continually illuminated, unless the Security Keylock is active.SourceSource button inserts control input selection on the projector or monitor.VolumeIf the PixiePlus is not used to control volume, a blank button insert may be used.Control BlankToggling Discrete(4-Button)Discrete(2-Button)Toggling DiscreteX. TroubleshootingProgramming ProblemsVerify that the PixiePlus is in learning mode for programming. The Status LED con-tinually blinks red when the PixiePlus is in learning mode.The Status LED is solid red and the PixiePlus beeps loudly each time you try to arm a key for learning.The ambient light is too bright. Shield the PixiePlus from ambient light sources and try to re-program.If the buttons appear to program properly but do not control the device, verify each code is correctly learned immediately after it has been programmed. The button will blink rapidly to indicate it is in verification mode. Push the button and the IR emitter will emit the corresponding code.When the PixiePlus is emitting a code in verification mode, you should see the Sta-tus LED flicker at a consistent strength and frequency. If the flickering seems un-even, verify that you are holding the remote control in the correct ’sweet spot’ and described in Section V, Part 3.If the Status LED does not flicker rapidly when the remote control is emitting a code, verify that the batteries in your remote control are fresh.The PixiePlus beeps three times as soon as the paper clip is inserted into the pro-gramming aperture.The PixiePlus beeps three times when it is toggled between two-button and four-button Source Selection modes. This is done by pressing and holding any button while inserting the paperclip. Is one of the buttons being activated while the paper clip is being inserted?This can happen if a button is stuck – check all buttons to make sure they are not caught in a depressed position. If not, it is possible that the button contacts on the PixiePlus circuit board are being shorted. Remove the bezel and check for solder or bits of wire that could bridge the button contacts. Then reseat the buttons, re-attach the bezel, and try entering programming mode again. If this does not correct the problem, please contact SP Controls Technical Support.Operation ProblemsThe PixiePlus does not power the projector/monitor on.Is the PixiePlus display dark, and does it chirp when any button is pressed? If so, the PixiePlus Security Keylock is active. See page 16 for information on how to con-figure and/or retrieve the Security Keylock code.If the Security Keylock is not set, verify that the projector or monitor powers on nor-mally with its own remote control or settop controls. If it does not, it may not be plugged in or may require service.X. Troubleshooting cont’dThe PixiePlus does not control the projector/monitor.Be sure that the code was programmed correctly – try reprogramming the unit.Confirm that the IR emitter bud is positioned directly over the receiver on the IR win-dow of the device you are controlling. Some devices are sensitive to accurate placement.Fluorescent lights can interfere with IR signals. Check if the projector is close to a fluorescent light source. If so, try turning off the lights. If this restores control, cover the IR emitter bud and display device IR receiver window with an IR-opaque shield,such as gaffer's tape. Some opaque tapes do not block IR.The device will not switch to one of the inputs.Some display devices will not switch to certain inputs if there is no signal present Control is intermittent.If you are using a device manufactured by Philips, Magnavox, or Koss, please con-sult the SP Controls PXE-DCM Philips Protocol Application Note for additional pro-gramming instructions.If you are still unable to control your device, please contact SP Controls Technical Support for further assistance.XI. Technical SpecificationsThe PixiePlus is UL listed and CE certified .Package TypeDimensions Weight (PCB with bezel and 3insert modules)Power SupplyOutput Type Recommended WireSingle-Gang Decora™ Mounting 4.130” (h) x 1.745” (w) x .90” (d)2.5 oz 6VDC, 300mA IR Emitter/RS-232 (programming RS232commands requires PXE-PGM-TOOL, soldseparately)18- to 22- Gauge 3-conductor stranded copperwireWarrantySP Controls warrants all PixiePlus products and accessories against defects in ma-terials and workmanship for a period of five years from the date of purchase.Although SP Controls thoroughly tested and reviewed this documentation, there is no warranty, express or implied, with respect to quality, merchantability, or fitness for a particular purpose. Therefore, the PixiePlus and accessories are provided "as-is" and the purchaser assumes the entire risk as to quality and performance.There are no obligations or liabilities on the part of the SP Controls Corporation for consequential damages arising out of or in conjunction with the use or performance of these products or other indirect damages with respect to loss of profit, revenue, or cost of removal and/or replacement. Some states do not allow the exclusion or limitation of incidental or consequential damages, so the above limitation or exclu-sion may not apply to you. This warranty gives you specific legal rights, and you may also have other rights that vary from state to state. SP Controls' maximum lia-bility shall not exceed the price paid by the user.All implied warranties, including warranties for merchantability and/or fitness, are limited in duration to three (3) years from the date of purchase. Proof of purchase must be provided with any claim.FCC ComplianceThis equipment generates radio frequency energy and if not installed in accordance with the manufacturer's instructions may cause radio interference.This equipment complies with part 15, Subpart J of the FCC rules for a Class A computing device. This equipment also complies with the Class A limits for radio noise emission from digital apparatus set out in the Radio Interference Regulation of the Canadian Department of Communications. These above rules are designed to provide reasonable protection against such interference when operating the equipment in a commercial environment. If operation of this equipment in a residen-tial area causes radio frequency interference, the user and not SP Controls, Inc., will be responsible.COPYRIGHTPixie™, PixiePlus™, and the SP Controls switch logo are trademarks of SP Con-trols, Inc. Decora™ is a registered trademark of Leviton Manufacturing Co. All other trademarks mentioned in this manual are the properties of their respective owners. No part of this document may be reproduced or transmitted in any form or by any means, electronic or mechanical, for any purpose, without express written permis-sion of SP Controls, Inc.© 2010 SP Controls, Inc. All rights reserved.Changes or modifications made to this equipment not expressly approved by SP Controls, Inc., could void the user's authority to operate the equipment.SP Controls, Inc. assumes no responsibility for any errors that appear in this docu-。
- 1、下载文档前请自行甄别文档内容的完整性,平台不提供额外的编辑、内容补充、找答案等附加服务。
- 2、"仅部分预览"的文档,不可在线预览部分如存在完整性等问题,可反馈申请退款(可完整预览的文档不适用该条件!)。
- 3、如文档侵犯您的权益,请联系客服反馈,我们会尽快为您处理(人工客服工作时间:9:00-18:30)。
服务销售人员问题清单
服务经理面试用
1 备件销售
1.1 是否有零件与精品专员?
(如:展示、备货、更新、促销等)
可能的回答是否在一定
程度上
是零件与精品专员
能够描述工作职责
全职
在零件与精品部门工作3年以上
注:
所作回答主要反映出服务部门/零部件部门员工的敬业职责。
1.2 精品专员是否具备销售技能?
可能的回答是否在一定
程度上
是销售培训
商业培训
销售研讨会
零件/精品研讨会
注:
所作回答主要反映出该精品专员的职业资格。
1.3 零件与精品领域是否有奖励机制?
可能的回答是否在一定
程度上
是个人佣金
部门红利
年度任务协议上规定的红利
非现金奖励
注:
所作回答主要反映出奖励机制是否能激发员工动力。
1.4 零件专柜的摆设是否有利于销售?
可能的回答是否在一定
程度上
是标识系统
展示看台
宣传手册
悬挂标识
快速周转的产品
季节性产品
注:
所作回答主要反映出零件专柜区域有利于销售的因素。
1.5 精品展示场所是否以便利顾客的方式布置?
可能的回答是否在一定
程度上
是与客户休息区很近
使用奥迪提供的产品
目前/大概精品产品范围
精品陈列颇具吸引力
模型销售员,精品展示辅助工具
注:
所作回答主要反映出零件与精品陈列区域的布局是否便利顾客?
2 零件与精品服务部门
2.1 前台是否扮演销售点的角色?
可能的回答是否在一定
程度上
是为预约客户提供专门的促销产品
展示新产品,季节性产品,维护修理包
注:
所作回答主要反映出前台主动为客户提供的服务范围。
2.2 顾客休息区是否被利用为服务信息资源区?
回答是否在一定
程度上
是目前产品/促销资料
宣称手册,传单,产品陈列,新闻报道
保险产品资料
注:
所作回答主要反映出顾客休息区是否在客户等待时间内扮演了信息中心的角色。
2.3 服务顾问是否能应付客户的询问?
可能的回答是否在一定
程度上
是服务顾问熟悉当前所有零件/精品促销活动
服务顾问能够向客户说明产品的益处与并使客户接受产品
价格
注:
从所作回答判断服务顾问目前所掌握的产品知识。
3 服务接待处/服务销售
3.1 服务接待处是否扮演“展示厅/销售厅”的角色?
可能的回答是否在一定
程度上
是有利于销售的布局,舒服的氛围
电脑桌
零件/精品展示处摆放有家具
陈列/特别促销/海报/展示台零件及精品范围
注:
从所作回答判断服务接待区布局是否便利顾客,有利于销售。
3.2 服务接待处是否完成接车前重要工作?
可能的回答是否在一定
程度上
是使预约到访客户感到放松
服务顾问非常熟悉标准服务接待流程
能够使用服务清单
客户做最终的决定
接待客户期间未被打扰
注:
所作回答主要反映出实现理想服务接待的可能性(可能,一定程度上可能,不可能)
3.3 服务接待处是否完成接车前重要工作?
可能的回答是否在一定
程度上
是服务顾问参加过销售员培训
服务顾问非常熟悉销售流程要求
服务顾问引导出客户的意愿与要求
服务顾问能够运用给客户带来的益处/优势表述
服务顾问能使用展示的零件向客户介绍产品的益处与其吸引
力所在
为服务接待处起草特殊产品与服务
服务部门/销售部门设有服务顾问奖励机制
注:
所作回答主要反映出实现理想服务接待的可能性(可能,一定程度上可能,不可能)
4 服务营销
4.1 您所在的销售区域,市场行情怎么样?
可能的回答是否在一定
程度上
是服务市场开发令人满意
过去三年服务活动减少
执行客户挽回方案
注:
所作回答主要反映出其所在销售区域的市场行情发生的变化。
4.2 在服务营销领域,落实了哪些措施?
可能的回答是否在一定
程度上
是起草服务营销活动年度计划
举办厂家活动
充分的广告营销活动
充分发送直接邮件
根据目标客户群选择邮件地址
通常会以电话的形式对邮件进行跟踪
所有主要数据都及时更新并维护
为客户进行价值计算
为客户提供高性价比的各种预算方案
利用网络与客户进行互动
注:
所作回答主要反映出市场营销活动的准备工作是否充分,执行力度是否足够。
5 结束语—自我评估
5.1 您对服务部门进行的产品销售以及服务销售的满意度如何?
5.2 您认为哪些地方可以改进?尤其是服务顾问哪些方面需要改进?
5.3 服务顾问在销售方面有哪些优势与弱势?。