冲压车门成本分析
铰链材料成本分析报告

铰链材料成本分析报告标题:铰链材料成本分析报告摘要:本报告对铰链材料的成本进行了详细分析,从原材料成本、加工成本和运输成本三个方面进行了综合评估,并提出了优化建议。
通过对成本的分析,可以帮助企业合理控制铰链材料的采购、生产和销售,提高企业的经济效益。
一、引言铰链是一种连接机械零部件的重要方法,广泛应用于家具、木制品、门窗以及汽车等行业。
铰链材料的成本直接影响到产品的成本和竞争力。
本报告通过对铰链材料的成本进行分析,旨在帮助企业找到更优化的采购和生产方式,以提高经济效益。
二、原材料成本分析目前市面上常见的铰链材料主要有铁、不锈钢、铝等。
不同的材质对产品的质量和成本有着不同的影响。
以下是各种材质的特点和成本分析:1. 铁材:铁材是常见的铰链材料,主要优点是成本低廉,且强度和耐用性较好。
然而,铁材在长时间使用或者接触水气环境下容易生锈,需要进行表面处理以提高耐腐蚀能力。
2. 不锈钢:不锈钢材料成本相对较高,但具有优良的耐腐蚀性能,能够适应各种环境条件。
不锈钢铰链的使用寿命较长,可以减少更换和维修的成本,适合应用在对耐腐蚀要求较高的产品中。
3. 铝材:铝材的成本相对较低,重量轻,适合用于一些对强度和耐腐蚀要求较低的产品。
然而,铝材的强度和耐用性较差,需要根据产品的使用要求进行选择。
三、加工成本分析铰链材料的加工成本主要包括切割、冲压、焊接、抛光等工艺。
不同的材质和产品要求对加工工艺有着不同的要求。
以下是常见的加工成本分析:1. 切割:铰链材料的切割通常使用切割机等设备进行。
切割过程中,材料损耗较少,成本相对较低。
2. 冲压:冲压是将铰链材料通过冲压机进行成形的过程。
冲压过程中需要制作冲模,这增加了成本。
而且冲压的准确度和稳定性对产品的品质有着重要影响。
3. 焊接:铰链材料的焊接主要是将不同零部件通过焊接工艺进行连接。
焊接工艺需要增加设备和操作人员的成本。
4. 抛光:抛光可以提高产品的表面光滑度和观感。
然而,抛光加工通常需要使用研磨机等设备,增加了成本。
汽车“热成形钢板冲压件”材料手册
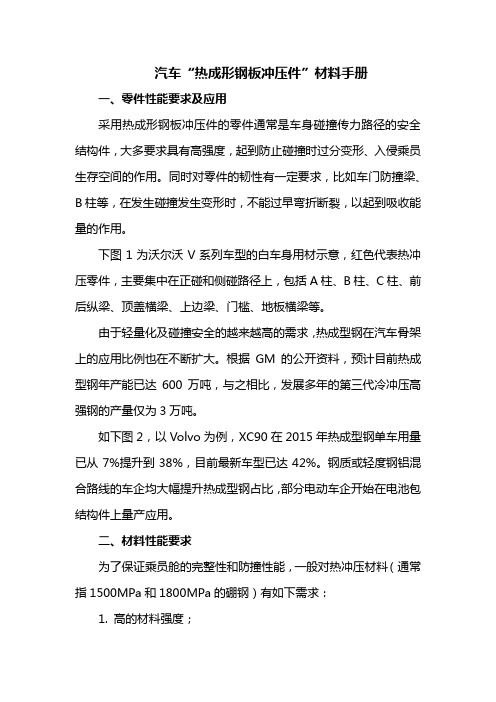
汽车“热成形钢板冲压件”材料手册一、零件性能要求及应用采用热成形钢板冲压件的零件通常是车身碰撞传力路径的安全结构件,大多要求具有高强度,起到防止碰撞时过分变形、入侵乘员生存空间的作用。
同时对零件的韧性有一定要求,比如车门防撞梁、B柱等,在发生碰撞发生变形时,不能过早弯折断裂,以起到吸收能量的作用。
下图1为沃尔沃V系列车型的白车身用材示意,红色代表热冲压零件,主要集中在正碰和侧碰路径上,包括A柱、B柱、C柱、前后纵梁、顶盖横梁、上边梁、门槛、地板横梁等。
由于轻量化及碰撞安全的越来越高的需求,热成型钢在汽车骨架上的应用比例也在不断扩大。
根据GM的公开资料,预计目前热成型钢年产能已达600万吨,与之相比,发展多年的第三代冷冲压高强钢的产量仅为3万吨。
如下图2,以Volvo为例,XC90在2015年热成型钢单车用量已从7%提升到38%,目前最新车型已达42%。
钢质或轻度钢铝混合路线的车企均大幅提升热成型钢占比,部分电动车企开始在电池包结构件上量产应用。
二、材料性能要求为了保证乘员舱的完整性和防撞性能,一般对热冲压材料(通常指1500MPa和1800MPa的硼钢)有如下需求:1. 高的材料强度;2. 良好的弯曲断裂韧性;3.均匀的组织性能;4.合适的成本;5.镀层材料还需求较好的耐蚀性(分为镀AS、镀锌和裸板);6.良好的热处理工艺性能(奥氏体化温度、临界冷却速度);7.良好的点焊、激光焊性能。
当然,现在随着汽车安全件的精细化设计需求,除了需求越来越高强度的硼钢(22MnB5、28MnB5、34MnB5)外,也需要中等强度的高韧性的热冲压材料作为软区材料,例如B柱的下端使用低合金高强钢6Mn6等,此类材料的需求为高弯曲韧性、良好的可焊性、较大的临界冷却速度,室温组织可以为铁素体、珠光体或马氏体组织。
三、行业用材分析1、行业用材现状•从基材来讲:①硬区:目前热冲压钢板主要应用的是1500MPa的22MnB5和1800MPa的34MnB5硼钢,用作硬区部位,即需要超高强度来减小或防止变形的部位;②软区:基于激光拼焊(TWB,Tailored Welded Blanks)技术的成熟,也有500/600MPa级的6Mn6、1000MPa级的8Mn*、1200MPa级的12Mn*等材料用于激光拼焊件的低强度部位,俗称软区。
冲压模具仿真分析报告范文

冲压模具仿真分析报告范文一、引言冲压模具在现代工业生产中起着至关重要的作用,它们被广泛应用于汽车、电子、家电等行业。
为了提高冲压模具的设计和加工质量,缩减生产成本和周期,仿真分析成为一种重要的手段。
本报告旨在通过冲压模具仿真分析,评估模具在冲压过程中的性能和效果。
二、仿真模型建立本次仿真分析选择了一款汽车车门内板的冲压模具作为探究对象。
起首,依据实际工程图纸,利用CAD软件建立了模具的三维几何模型。
然后,依据冲压工艺要求,确定了冲压过程中的材料参数、模具间隙等关键参数,并将其应用于仿真模型中。
三、仿真分析结果通过有限元分析软件,对建立的冲压模具进行了仿真分析。
起首,对模具进行了应力和变形分析。
结果显示,在冲压过程中,模具的应力集中区域主要集中在凸模和凹模的接触面,而变形主要发生在模具的弯曲部位。
进一步分析表明,模具的应力和变形状况均满足设计要求,不存在严峻的变形或破坏现象。
其次,对模具进行了冲压过程的仿真模拟。
通过动力学仿真分析,得到了冲压过程中模具的运动轨迹和变形状况。
结果显示,模具的运动与冲压工艺要求基本一致,冲压件的成型效果良好。
同时,仿真结果还表明,模具的运动过程中存在一定的震动,需要进一步优化模具结构以缩减震动影响。
四、结论与建议通过冲压模具仿真分析,得到了以下结论:1. 冲压模具的应力和变形状况满足设计要求,不存在严峻的变形或破坏现象。
2. 冲压过程中模具的运动与冲压工艺要求基本一致,冲压件的成型效果良好。
3. 模具的运动过程中存在一定的震动,需要进一步优化模具结构以缩减震动影响。
基于以上结论,我们提出以下建议:1. 在模具设计阶段,应重视优化模具结构,缩减震动影响,提高冲压过程的稳定性。
2. 针对模具的应力集中区域,可以思量增加材料的强度或改变接触面的外形,以提高模具的寿命和耐用性。
3. 进一步探究冲压模具的动力学特性,以优化运动轨迹,提高冲压件的成型精度和一致性。
五、总结本次冲压模具仿真分析报告对一款汽车车门内板的模具进行了全面的性能和效果评估。
汽车冲压件市场分析报告

汽车冲压件市场分析报告1.引言1.1 概述汽车冲压件作为汽车制造中不可或缺的一部分,对于汽车的外观和结构起着至关重要的作用。
本报告旨在对汽车冲压件市场进行全面的分析,包括市场概况、趋势分析以及竞争格局。
通过深入的研究和数据分析,我们将为读者提供有关汽车冲压件市场的全面了解,并提供发展前景和策略建议,帮助读者更好地把握市场动态,抓住机遇,迎接挑战。
1.2 文章结构文章结构部分的内容可以包括以下方面:本文将分为引言、正文和结论三个部分。
在引言部分,我们将对汽车冲压件市场进行概述,介绍本文的结构和目的,并对市场进行总结。
在正文部分,我们将分析汽车冲压件市场的概况、趋势和竞争格局。
在结论部分,我们将对汽车冲压件市场的发展前景进行展望,并提出相关的策略建议,最后对市场进行总结并展望未来。
通过这样的结构安排,读者可以清晰地了解本文的内容和逻辑,从而更好地理解汽车冲压件市场的情况和发展趋势。
1.3 目的目的:本报告旨在对当前汽车冲压件市场进行全面分析,包括市场概况、趋势分析、竞争格局以及市场发展前景等方面的内容。
通过深入研究,旨在为汽车冲压件相关企业提供市场发展的参考依据和战略建议,帮助企业更好地把握市场机遇,提升竞争力。
同时,也为汽车冲压件市场的相关机构和个人投资者提供全面的行业分析,帮助他们做出明智的投资决策。
1.4 总结总结部分:通过对汽车冲压件市场的深入分析,可以得出以下结论:随着汽车产业的持续发展,汽车冲压件市场将会保持较稳定的增长态势。
同时,市场竞争将会更加激烈,企业需加强技术创新和产品质量,以提升市场竞争力。
此外,随着环保意识的提升,轻量化、高强度冲压件将成为市场的发展趋势。
因此,企业需要制定相应的发展战略,加强研发投入,提高产品质量和技术水平,以应对市场的挑战和机遇。
总的来说,汽车冲压件市场将会面临更多的机遇和挑战,但有着广阔的发展前景。
2.正文2.1 汽车冲压件市场概况汽车冲压件市场概况部分的内容应包括对汽车冲压件市场的整体描述和分析。
汽车车身的冲压成形技术分析

汽车车身的冲压成形技术分析汽车车身的冲压成形技术是制造车身零部件的一种常用工艺。
它通过将金属材料卷料或板料置于冲模中,并通过压力使其在冲压机的压力下,通过冲切、折弯、拉伸和深冲等工艺完成零部件的成形。
下面将对汽车车身的冲压成形技术进行详细分析。
首先介绍汽车车身冲压成形的工艺流程。
冲压成形技术主要包括以下几个步骤:设计图纸、制造冲模、裁剪材料、上模、调整冲模、开始冲压、脱模、检查零件。
设计图纸是冲压成形的基础,其中包括了零件的尺寸、形状和工艺要求等信息。
制造冲模是冲压成形的关键步骤,它需要考虑到零件的形状和尺寸,以及材料的可冲性。
裁剪材料是将金属板材根据设计要求切割成相应的尺寸和形状。
上模是将裁剪好的金属板料放入冲模中,通过顶紧装置固定住。
调整冲模是根据工艺要求对冲模进行精调,以确保零件的成形质量。
开始冲压是利用冲压机的压力对金属板料进行成形,通过一系列的冲切、折弯、拉伸和深冲等工艺将材料冲压成所需的形状。
脱模是将成形好的零件从冲模中取出。
最后检查零件是对成形好的零件进行质量检查,以确保其满足设计要求。
其次是分析冲压成形技术的优点。
冲压成形技术具有以下几个优点:一是生产效率高。
由于冲压成形工艺是批量化生产,能够同时对多个零部件进行冲压,提高生产效率。
二是成形精度高。
冲压成形工艺是通过冲模的压力来完成的,可以保证零件的形状和尺寸的精度。
三是材料利用率高。
冲压成形工艺是根据设计的形状来进行冲压的,可以最大程度地利用材料,减少浪费。
四是成本低。
冲压成形工艺是采用批量化生产的方式,生产效率高,材料利用率高,可以降低成本。
最后是冲压成形技术的应用领域。
冲压成形技术在汽车工业中被广泛应用于车身零部件的制造。
例如车门、车顶、前后保险杠等零部件都是通过冲压成形技术制造的。
汽车车身的冲压成形技术是一种常用的制造工艺,具有生产效率高、成形精度高、材料利用率高和成本低的优点,广泛应用于汽车工业中。
汽车车门内板冲压成形工艺分析

缺陷检测ห้องสมุดไป่ตู้针对常见的冲压成形缺陷,采用特定的检测方法和技术手段,及时发现并处理缺 陷,避免批量质量问题。
质量追溯:建立完善的质量追溯体系,对每个环节进行记录和追踪,确保产品质量可追溯, 便于问题排查和解决。
冲压成形中的应力应变分析:板料在冲压过程中,会发生应力应变,其分布和大小对成形质量 有重要影响。
冲压成形中的缺陷分析:如起皱、开裂、回弹等,与材料性质、模具设计、工艺参数等因素有 关。
材料在冲压过程中的流动与变形规律 材料的应力应变行为 材料屈服准则和本构方程 材料硬化特性对冲压成形的影响
冲压速度:根据 材料厚度和成形 要求选择合适的 冲压速度,以保 证成形质量和效
轻量化材料:如高强度钢、铝合金等,可有效降低车身重量,提高燃油经济性和 动力性能。
新型成形工艺:如热冲压、温冲压等,可提高材料成形极限和零件强度,降低生 产成本。
复合材料:如碳纤维复合材料,具有高强度、轻量化和可设计性等优点,是未来 汽车车门内板冲压成形工艺的重要发展方向。
智能化技术:如人工智能、大数据等,可实现冲压成形工艺的智能化控制和优化, 提高生产效率和产品质量。
模具刚度与强度:确保模具在冲压 过程中具有足够的刚度和强度,避 免变形和损坏。
添加标题
添加标题
添加标题
添加标题
模具结构设计:采用易于加工、装 配和维修的结构,降低制造成本。
模具冷却系统:优化冷却系统设计, 提高冷却效果,减少模具温度波动 和热疲劳损伤。
研发背景:传统冲压成形工艺存在局限性,新型工艺应运而生 主要技术:激光冲压成形、热冲压成形等 应用领域:汽车制造、航空航天等 优势与效果:提高材料利用率、减少生产成本、提高产品性能等
汽车冲压制造技术
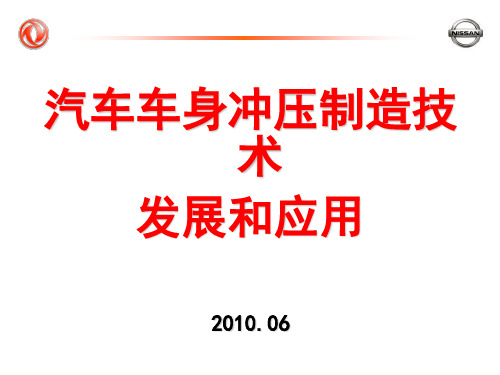
2010.06
汽车车身冲压技术的发展
趋势:随着整车要求更安全,更环保,更低能耗,需要车身
轻量化而更坚固,车身冲压在安全、环保、高品质、高效率、
低成本、数字化制造不断发展
材料:高强度钢板及激光拼焊板的应用
工艺:热冲压成形和液压成型技术的应用
设备:高速冲压自动线和伺服压力机的发展 模具:模具技术和有限元分析CAE技术在冲压 成形中快速发展和应用 2010年冲压规划工作介绍
冲压材料的发展
高强度及超高强度钢板的定义 随着整车轻量化和安全法规的碰撞安全性要求提高,冲压材料向着高强 度方向发展。高强度钢板在汽车应用上发展很快,目前在欧洲轻量化概念化车的用 材中,高强度钢板约占用80%左右。强度在270—780MPa应用的最多。
按抗拉强度划分: 高强钢:TS≥340MPa(冷轧) 70 TS≥370MPa(热轧及酸洗) 60 超高强钢:TS>590MPa 按屈服强度划分: 高强钢:YS≥210MPa
自动化成本/万 元 2100*2 1200*3
压力机/万 元 6000*2 6000*3
土建/万元 1800*2 1800*3
废料输送+天车/ 万元 80*2+(110+70) *2
合计/万 元 20320 27780
80*3+(110+70) *3
表2,运行投资对比 冲压线类别 机械手系统 机器人系统 班制 自动化 线/条 2 3 年人工成本/万 元 160*2 160*3 水电气/万元 12.5*2 12.5*3 备件费用 40*2 40*3 合计/万元 425.6 637.5
冲压设备的发展
冲压设备的发展
人工冲压线
汽车车身的冲压成形技术分析

汽车车身的冲压成形技术分析汽车车身是汽车的重要组成部分,它直接影响到汽车的外观、安全性能和乘坐舒适度。
而汽车车身的制造过程中,冲压成形技术是一种常见的加工方法。
通过对汽车车身冲压成形技术的分析可以了解到其在汽车制造中的重要性和应用场景。
一、汽车车身冲压成形技术的基本原理汽车车身冲压成形技术是利用模具对金属板材进行加工成形的一种方法。
其基本原理是通过将金属板材置于冲床上,然后利用冲头对金属板材施加压力,使得金属板材受力后产生塑性变形,最终形成所需的形状。
冲压成形技术的优点包括成本低、效率高、精度好等,因此在汽车车身制造中得到广泛应用。
1. 材料选取:汽车车身冲压成形技术中常用的金属材料包括冷轧板、热轧板、镀锌板等,其选取需要考虑到材料的强度、塑性、成本等因素。
2. 模具设计:模具是冲压成形技术的重要工具,其设计需要考虑到所需成型的形状、尺寸精度、成本等因素。
同时模具的选材、热处理等对成形质量也有重要影响。
3. 冲压工艺:在冲压成形过程中,需要考虑到冲头的选择、冲程的设置、冲头对板料的压力等因素,以保证成形质量和生产效率。
4. 成形工艺:汽车车身的冲压成形中,常见的工艺包括拉延成形、弯曲成形、拉伸成形等,针对不同部位的成形需求选择不同的工艺。
5. 成品检验:对成形后的汽车车身进行检验,检查其尺寸精度、表面质量、成形缺陷等,以保证成品的质量。
目前汽车车身冲压成形技术已在汽车制造中得到广泛应用,它可以应用于汽车车身的各个部位。
例如汽车的车门、车顶、车窗框、车尾等部位都可以通过冲压成形技术进行加工制造。
而且随着汽车车身对轻量化、强度提升等性能要求的不断增加,冲压成形技术的应用也在不断扩大。
随着汽车工业的不断发展,汽车车身冲压成形技术也在不断创新和完善。
目前一些先进的汽车制造技术已经应用于汽车车身冲压成形中,例如激光冲压成形、气动冲压成形等技术。
这些技术能够提高成形效率、提升成形质量、降低成本,有望成为未来汽车车身制造的发展方向。
汽车车门外板冲压模具设计
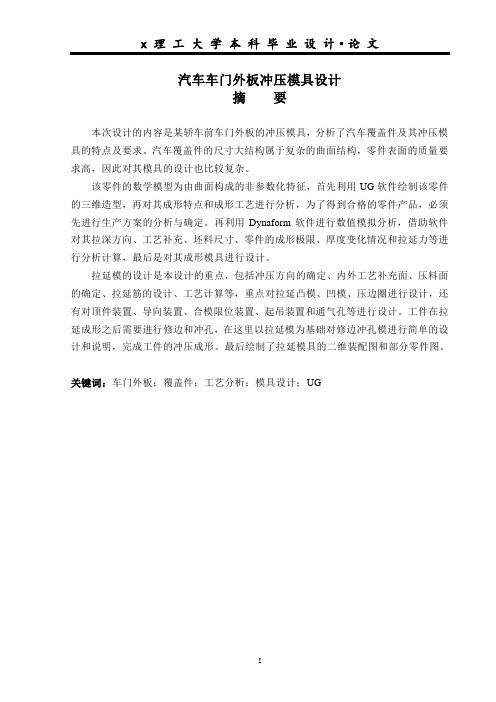
汽车车门外板冲压模具设计摘要本次设计的内容是某轿车前车门外板的冲压模具,分析了汽车覆盖件及其冲压模具的特点及要求。
汽车覆盖件的尺寸大结构属于复杂的曲面结构,零件表面的质量要求高,因此对其模具的设计也比较复杂。
该零件的数学模型为由曲面构成的非参数化特征,首先利用UG软件绘制该零件的三维造型,再对其成形特点和成形工艺进行分析,为了得到合格的零件产品,必须先进行生产方案的分析与确定。
再利用Dynaform软件进行数值模拟分析,借助软件对其拉深方向、工艺补充、坯料尺寸、零件的成形极限、厚度变化情况和拉延力等进行分析计算,最后是对其成形模具进行设计。
拉延模的设计是本设计的重点,包括冲压方向的确定、内外工艺补充面、压料面的确定、拉延筋的设计、工艺计算等,重点对拉延凸模、凹模、压边圈进行设计,还有对顶件装置、导向装置、合模限位装置、起吊装置和通气孔等进行设计。
工件在拉延成形之后需要进行修边和冲孔,在这里以拉延模为基础对修边冲孔模进行简单的设计和说明,完成工件的冲压成形。
最后绘制了拉延模具的二维装配图和部分零件图。
关键词:车门外板;覆盖件;工艺分析;模具设计;UGThe design of car door panels stamping dieAbstract: The content is designed for a car before the car door panel stamping dies, analyzes and stamping automotive panel characteristics and requirements. Large size structure of an automobile covering parts are complex surface structure, high quality requirements of the part surface, so the design of their molds more complicated.Mathematical model of the part of the grounds of non-parametric feature curved surface, the first use of UG software to draw three-dimensional modeling of the part, and then analyzed the characteristics shaping and forming processes, in order to get qualified parts products must be produced programs Analysis and determination. Reuse Dynaform numerical simulation analysis software, with the software to its drawing direction, forming limit addendum, blank size, part thickness changes and drawing force of analysis and calculation, and finally the design of its mold.Drawing die design is the focus of this design, including stamping direction is determined, both inside and outside addendum, binder determination drawbead design, process calculation, focusing on drawing punch, die, blankholder ring design, as well as for top pieces of equipment, guides, clamping stopper, lifting device and the vent, etc. design. After forming the workpiece drawing needed trimming and punching, drawing die in here with the basis for trimming punching die design and simple instructions to complete the stamping workpiece shape. Finally, draw the two-dimensional drawing die assembly drawing and some parts Fig.Key words:car door panels;cover;process pnalysis;mold design;UG目次摘要................................................ 错误!未定义书签。
汽车后门不锈钢门槛条冲压工艺-概述说明以及解释

汽车后门不锈钢门槛条冲压工艺-概述说明以及解释1.引言1.1 概述概述随着汽车产业的不断发展,汽车后门不锈钢门槛条作为一种重要的组装部件,在车辆安全性和美观性方面起着至关重要的作用。
不锈钢门槛条可以有效保护车辆后门的边缘,防止因乘坐人员的进出而造成的划伤和磨损。
同时,它也具备一定的装饰性,能够提升整车的外观品质。
本文将侧重探讨汽车后门不锈钢门槛条的冲压工艺。
冲压工艺是一种常用的金属加工工艺,通过将金属材料置于模具中,利用模具的压力作用使其产生塑性变形,从而制成所需形状的零件。
在汽车后门不锈钢门槛条的制造中,冲压工艺被广泛应用。
本文将首先介绍汽车后门不锈钢门槛条的重要性,以及其在车辆安全性和美观性方面的作用。
接着,将详细探讨汽车后门不锈钢门槛条的冲压工艺,包括材料选用、模具设计、冲压工艺参数等等。
通过对冲压工艺的深入研究和分析,将为汽车后门不锈钢门槛条的生产提供一定的指导和参考。
最后,本文将总结所述内容,并展望未来汽车后门不锈钢门槛条冲压工艺的发展趋势。
我们相信,随着科技的不断进步和工艺的不断创新,汽车后门不锈钢门槛条的冲压工艺将不断优化和提高,为汽车行业带来更高水平的安全性和美观性。
1.2文章结构文章结构应该包括以下几个部分:1. 引言:介绍文章的背景和意义,解释为什么选择研究汽车后门不锈钢门槛条的冲压工艺。
可以提及相关的市场需求和应用前景。
2. 文章目的:明确本文的研究目标和意图,说明希望通过研究汽车后门不锈钢门槛条的冲压工艺可以达到什么样的效果和目的。
3. 文章结构:本文将按照以下方式展开研究:3.1 汽车后门不锈钢门槛条的重要性:首先介绍汽车后门不锈钢门槛条在整个汽车结构中的重要作用,探讨其具有的功能和特点。
通过分析市场需求和应用实例,展示不锈钢门槛条对汽车整体品质和使用体验的重要影响。
3.2 汽车后门不锈钢门槛条的冲压工艺:详细介绍汽车后门不锈钢门槛条的冲压工艺,包括材料的选择、冲压工艺的流程和参数设定,以及工艺中可能遇到的挑战和解决方案。
汽车车身冲压工艺质量控制与分析

成都航空职业技术学院毕业设计汽车车身冲压工艺质量控制与分析专业:汽车制造与装配班级:512888姓名:晓风学号:*************二零一五年六月摘要本文通过对汽车车身冲压工艺质量控制与分析,对汽车整车制造厂冲压工艺流程,工艺特点有着详细的介绍。
并且阐述汽车冲压件质量控制对汽车整车质量的作用和意义,分析影响汽车白车身冲压件质量的因素,以及控制的措施和应用方法,对覆盖件生产工艺过程的详细介绍,并且结合个人的社会实践经验,分析工具在白车身冲压质量控制的应用方法等。
汽车在生活中是人们出行的主要交通工具,随着社会的发展和科技的进步,汽车制造业的发展方向已经被发达国家及部分新兴工业国家在未来发展的主要方向,也被作为其国民经济支柱产业。
通过对汽车车身冲压工艺质量控制与分析,不仅提高冲压件的质量,同时还提高整车的品质。
关键词:冲压,质量控制,覆盖件ABSTRACTThis article through to the car body stamping process quality control and analysis, Stamping process to vehicle manufacturers, Process characteristics with detail, And automotive stamping parts quality control function and meaning of the quality of vehicle, Analysis of the influencing factors on the quality of the car white body stamping parts, As well as the control measures and application of the method. The covering parts production process in detail, And combining with the personal experience of social practice. Analysis tools in white body stamping application of quality control, etc.Car in the life is the main transport people travel. With the development of the society and the progress of science and technology. The development direction of automobile manufacturing industry has been developed countries and some emerging industrial countries the main direction of development in the future. Also referred to as the national economy pillar industry.Through to the automobile body stamping process quality control and analysis, not only improve the quality of stamping parts.At the same time also improves the quality of the vehicleKeywords: stamping, quality control, covering parts第一章绪论1.1引言我国汽车工业从无到有,从小到大,发展成为一个完整的工业体系。
热冲压发展现状及未来趋势分析

热冲压发展现状及未来趋势分析热冲压技术是一种利用高温和高压将金属材料加热变软后形成所需形状的成形方法。
在制造业中,热冲压技术被广泛应用于汽车制造、家电制造、航空航天等领域。
本文将对热冲压的发展现状和未来趋势进行分析。
首先,热冲压技术的发展现状。
随着现代制造业的进步和发展,热冲压技术在各个行业中得到了广泛应用。
特别是在汽车制造领域,热冲压技术被认为是一种可以提高零部件质量、降低成本并提高生产效率的高效成形技术。
例如,利用热冲压技术可以制造出更轻、更坚固和更安全的汽车车身部件,如车门、车顶等。
此外,在家电制造行业,利用热冲压技术可以制造出更加精密和高效的家电零部件,如冰箱铝合金门壳、洗衣机水箱等。
其次,热冲压技术的未来趋势。
从技术发展角度来看,热冲压技术将继续朝着更高的成形速度、更精密的成形质量和更低的能源消耗方向发展。
一方面,随着高温和高压控制技术的不断改进,热冲压设备的成形速度将不断提高,从而进一步增加生产效率。
另一方面,随着材料科学的发展,新型高强度、高耐热金属材料的出现将使得热冲压技术能够应用于更严苛的工况。
此外,热冲压技术也将与其他先进制造技术结合,如先进模具制造技术、智能控制技术等,进一步提高成形质量和生产效率。
在市场需求方面,热冲压技术也面临着新的机遇和挑战。
随着国家对于节能环保的重视和汽车工业的发展,对于轻量化和高强度汽车零部件的需求不断增加。
而热冲压技术正可以满足这一需求,通过减少材料厚度和提高材料的强度,可以制造更轻、更强的汽车车身零部件。
此外,随着家电行业的快速发展,对于高效和精密制造的需求也在不断提高,热冲压技术可以满足家电制造行业对于高质量零部件的需求。
然而,热冲压技术也面临一些挑战。
首先,热冲压设备的投资成本相对较高,对于一些中小规模企业来说可能难以承受。
其次,热冲压技术在操作过程中需要严格控制温度和压力等参数,操作难度较大,对技术人员的要求较高。
此外,热冲压设备在长时间高温高压环境下工作,对设备的性能和稳定性要求较高。
国内外冲压工艺现状分析
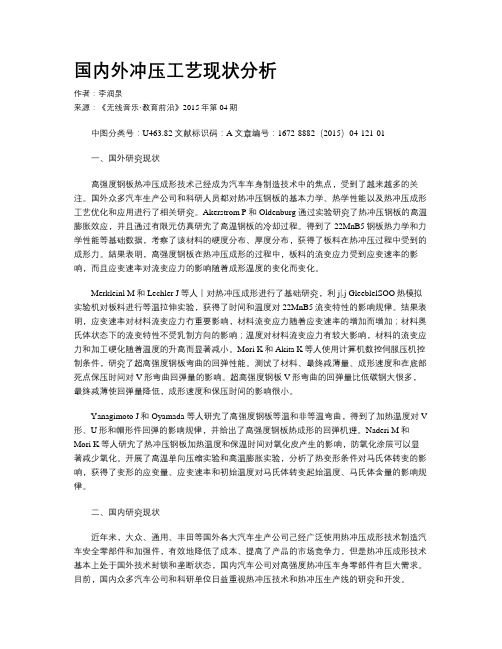
国内外冲压工艺现状分析作者:李润泉来源:《无线音乐·教育前沿》2015年第04期中图分类号:U463.82 文献标识码:A 文章编号:1672-8882(2015)04-121-01一、国外研究现状高强度钢板热冲压成形技术己经成为汽车车身制造技术中的焦点,受到了越来越多的关注。
国外众多汽车生产公司和科研人员都对热冲压钢板的基本力学、热学性能以及热冲压成形工艺优化和应用进行了相关研究。
Akerstrom P和Oldenburg 通过实验研究了热冲压钢板的高温膨胀效应,并且通过有限元仿真研宄了高温钢板的冷却过程。
得到了 22MnB5钢板热力学和力学性能等基础数据,考察了该材料的硬度分布、厚度分布,获得了板料在热冲压过程中受到的成形力。
結果表明,高强度钢板在热冲压成形的过程中,板料的流变应力受到应变速率的影响,而且应变速率对流变应力的影响随着成形温度的变化而变化。
Merkleinl M和Lechler J等人丨对热冲压成形进行了基础研究,利j|.j GleeblelSOO热模拟实验机对板料进行等温拉伸实验,获得了时间和温度对22MnB5流变特性的影响规律。
结果表明,应变速率对材料流变应力冇重要影响,材料流变应力随着应变速率的增加而增加;材料奥氏体状态下的流变特性不受乳制方向的影响;温度对材料流变应力有较大影响,材料的流变应力和加工硬化随着温度的升高而显著减小。
Mori K和Akita K等人使用计算机数控伺服压机控制条件,研究了超高强度钢板弯曲的回弹性能。
测试了材料、最终减薄量、成形速度和在底部死点保压时间对V形弯曲回弹量的影响。
超高强度钢板V形弯曲的回弹量比低碳钢大很多,最终减薄使回弹量降低,成形速度和保压时间的影响很小。
Yanagimoto J和Oyamada 等人研宄了高强度钢板等温和非等温弯曲,得到了加热温度对V 形、U形和帽形件回弹的影响规律,并给出了高强度钢板热成形的回弹机理。
Naderi M和Mori K等人研宄了热冲压钢板加热温度和保温时间对氧化皮产生的影响,防氧化涂层可以显著减少氧化。
汽车车门内板冲压成形工艺分析

汽车车门内板冲压成形工艺分析•该文分析了某轿车车门内板的成形工艺及易产生的缺陷,并据此制定了其合理的冲压工艺方案。
文章通过对拉延成形过程的模拟与分析,得出了合理的工艺方案,目的是为类似零件工艺方案的制定提供参考。
汽车覆盖件具有尺寸大、相对厚度小、形状复杂等特点,决定了在冲压成形中板料变形的复杂性,变形规律不易被掌握,不能定量地对主要工艺参数和模具参数进行计算,在工程实践中还主要运用经验类比来进行冲压工艺设计。
一、冲压工艺制定1.零件工艺分析图1所示为某轿车车门内板零件图,材料为St14,料厚0.8mm。
从图可以看出,该零件形状复杂,高差较大,局部成形较多,板料的变形不是单纯的拉延成形,而是存在一定程度的胀形变形,是典型的汽车覆盖件。
图1中的a和b处,由于窗框部分进行内工艺补充后,形成了零件的反成形形状,这部分形状的成形一般不能靠外部材料进行补充,只能靠该部分板料的胀形成形来实现,胀形成形深度较深,a和b处大约有20mm左右,且转角部R较小,因此在拉延成形过程中很容易出现破裂。
在零件的c处,存在大约12mm高的台阶,此部分若在第一次拉延过程中直接成形,则压料面可能有以下两种分法:(1)将c部分作为压边面的一部分,即将分模线分在零件侧壁圆角处,这样由于台阶对板料的进料阻力较大,易导致零件在拉延过程中可能产生破裂;(2)将c部分作为凸模的一部分,即将分模线分在c部分外侧的法兰上,则在拉延过程中该区域的板料是悬空的,在径向拉应力和切向压应力的作用下,材料集中收缩到此处,可能导致零件的该部分起皱,甚至有迭料的可能。
由上面的工艺分析可知,该覆盖件成形难度大,成形工艺较复杂。
图1 某轿车车门内板零件图2.工艺方案的制定产品冲压成形工艺的确定过程,就是分析和预测板料在变形过程中可能产生的缺陷,并采取一定的措施,以消除和防止冲压缺陷,同时考虑制造能力、冲压设备、投资成本等因素。
根据本零件的工艺性和本身的结构特点,结合实际生产情况,车门内板的工艺过程如下:拉延+切角;二次拉延+切边+冲孔;切边+冲孔;侧切+侧冲孔翻孔+冲孔+整形;整形+冲孔。
汽车钣金热冲压技术详解

内容
1. 热冲压工艺流程及其典型应用 2. 热冲压钢板 3. 热冲压设备 4. 热冲压钢板加热方式 5. 热冲压优缺点分析 6. 热冲压零件的检测技术 7. 热冲压技术成本分析
2、热冲压钢板
从成分分为:
Mn-B系
宝钢热冲压用钢
Mn-Mo-B系 北美、欧洲等的热冲压用钢
Mn-Cr-B系 高淬透性的热冲压用钢
Roof-bows
Bumper Armatures Front & Rear
A Pillar Reinforcements
2 Piece A Pillar Reinforcements Side Impact Beams and Waste Reinforcements
钢管热冲压 典型应用
1.2 钢管热冲压
快速移到压机
快速合模、成形,保压冷 却到100-2000C。组织全 部为马氏体
抗拉强度为400 -600Mpa左右 的BORON钢板
随室温冷却, 激光(模具) 切边、冲孔
得到抗拉强度为 1500Mpa左右的零件
若采用裸板则进行喷丸处 理以去除零件表面氧化皮
1、热冲压工艺流程及其典型应用
Time in the tool
2、热冲压钢板
镀层钢板热冲压:
➢ 加热、冲压过程中无氧化皮 ➢ 无需喷丸处理 ➢ 成本高 ➢ 零件储存过程不生锈 ➢ 零件耐腐蚀性能好 ➢ 加热过程中镀层易和陶瓷辊粘结
非镀层钢板热冲压:
➢ 加热、冲压过程中有氧化皮 ➢ 需喷丸处理 ➢ 成本低 ➢ 零件储存过程易生锈 ➢ 零件耐腐蚀性能稍差 ➢ 焊接性好
USIBOR1500介绍:
2、热冲压钢板
Aluminium (90%) and Silicon铝(90%)和硅
冲压工艺中怎样控制成本【最新版】
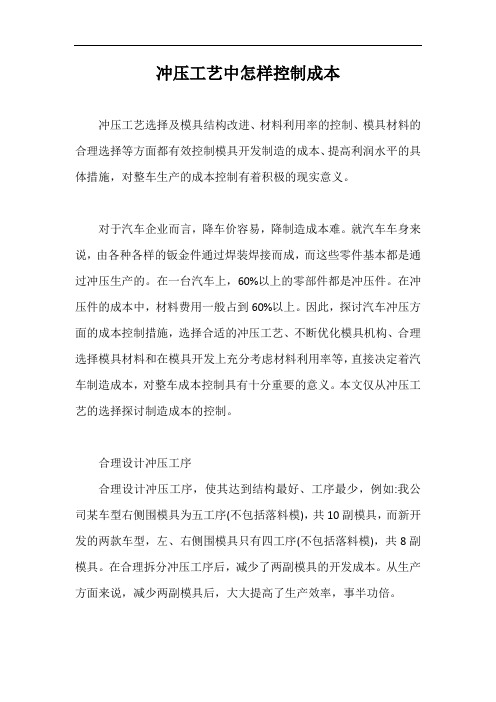
冲压工艺中怎样控制成本冲压工艺选择及模具结构改进、材料利用率的控制、模具材料的合理选择等方面都有效控制模具开发制造的成本、提高利润水平的具体措施,对整车生产的成本控制有着积极的现实意义。
对于汽车企业而言,降车价容易,降制造成本难。
就汽车车身来说,由各种各样的钣金件通过焊装焊接而成,而这些零件基本都是通过冲压生产的。
在一台汽车上,60%以上的零部件都是冲压件。
在冲压件的成本中,材料费用一般占到60%以上。
因此,探讨汽车冲压方面的成本控制措施,选择合适的冲压工艺、不断优化模具机构、合理选择模具材料和在模具开发上充分考虑材料利用率等,直接决定着汽车制造成本,对整车成本控制具有十分重要的意义。
本文仅从冲压工艺的选择探讨制造成本的控制。
合理设计冲压工序合理设计冲压工序,使其达到结构最好、工序最少,例如:我公司某车型右侧围模具为五工序(不包括落料模),共10副模具,而新开发的两款车型,左、右侧围模具只有四工序(不包括落料模),共8副模具。
在合理拆分冲压工序后,减少了两副模具的开发成本。
从生产方面来说,减少两副模具后,大大提高了生产效率,事半功倍。
采用联合安装方式联合安装的操作方式就是在同一副模具内,完成两个或者两个以上工序内容的作业方式,例如:我公司最具有代表性的某车型加油口盒,就是采用联合安装方式来实现的。
某车型中加油口盒,共有五副模具,如果连线生产就需要占用五台机床来满足其要求。
为了提高生产效率,减少对机床的占用,将后三副模具采用联合安装的方式,组合拼装在同一副模具上,如图1所示。
这样一来某车型中加油口盒只有三副模具了。
合并后的一副模具,每完成一个冲次就相当于原来三副模具的冲次,生产效率提高了,机床占用压力也就减少了。
与此同时,三副模具合并在一副模具上,模具采用也减少了,重量轻了,成本降低了。
联合安装的作业方式,一般常用于中、小型冲压件,大型件、外板件等产品表面质量要求高的零件建议不采用。
拉延模上安装废料切刀的工艺方案减少冲压工序是控制冲压成本的一种重要途径。
基于AutoForm的轿车车门玻璃导轨冲压工艺分析
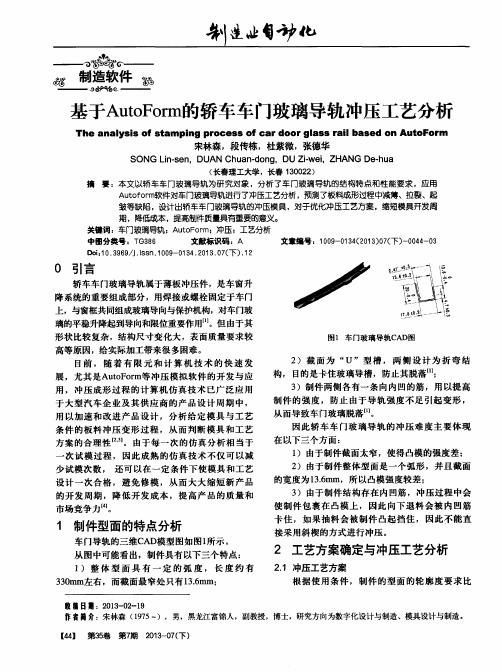
— —
訇 4 b
一
制 造 软件
_——一 0 杏 - c ————_ = -
基于A u t o F o r m的轿 车车 门玻璃导轨冲压工艺分析
The anal y si s of s t am pi ng pr ocess o f car door gl as s r ai l b ased on Aut oF or m
卡住 ,如果抽料会被制件凸起挡住 ,因此不能直 接 采 用斜楔 的方式进 行 冲压 。
2 工艺方案确定 与冲压 工艺分析
2 . 1 冲压工艺方案 根据使 用条件 ,制件 的型面 的轮廓度要求 比
救穗 日麓 :2 0 1 3 -0 2 -1 9 作者简介 : 宋林森 ( 1 9 7 5 一 ),男 ,黑龙江富锦人 ,副教授 ,博士 ,研究方 向为数字化设计与制造 、模具设计与制造 。 [ 4 4 1 第3 5 卷 第7 期 2 0 1 3 - 0 7 ( 下)
A u t o f o r m 软件对车门玻璃导轨进行了冲压工艺分析,预测了板料成形过程中减薄、拉裂、起 皱等缺陷,设计出轿车车门玻璃导轨的冲压模具 ,对于优化冲压工艺方案,缩短模具开发周 期,降低成本,提高制件质量具有重要的意义。 关键词 : 车 门玻璃导轨 ;A u t o F o r m ;冲压 ;工艺分析 中圈分类号 :T G3 8 6 文献标识码 :A 文章编号 :1 0 0 9 - 0 1 3 4 ( 2 0 1 3 ) 0 7 ( 下) 一0 0 4 4 - 0 3
在 以下三 个方 面 : 1 ) 由于 制件截 面 太窄 ,使 得 凸模 的强度 差 ;
用 ,冲压成形过程的计算机仿真技术已广泛应用 于大型汽车企业及其供应商的产品设计周期 中, 用 以加 速 和 改进 产 品设 计 ,分 析 给 定 模 具 与 工艺
汽车车门外板全工序回弹分析与补偿的应用

•冲模技术•汽车车门外板全工序回弹分析与补偿的应用杜武昌,唐远柱天津柯麦特模具技术有限公司技术中心(天津300300)【摘要】随着我国的汽车工业不断发展,各车企之间的竞争也在不断加剧,在新车型的开发 过程中,车身外覆盖件外观质量和尺寸精度要求越来越高,从而给汽车模具生产行业也提 出更高的要求,汽车外覆盖件在冲压成形时会产生各种类型的缺陷,其中回弹仍是汽车冲 压行业的一个挑战。
通过一个成功的前车门外板案例,借助Autoform软件阐述一种汽车 外覆盖件全工序回弹分析和补偿的应用。
全工序模拟完全按照模具实际生产现场的边界 条件进行模拟,同时通过稳健性分析以确认各因子的影响,最终保证回弹补偿的准确性,可为汽车外覆盖件回弹补偿提供参考。
关键词:汽车外覆盖件;前车门外板;回弹;补偿;Autoform;全工序模拟中图分类号:TG385.2 文献标识码:BDOI :10.12147/ki.1671-3508.2020.05.008Application of Springback Simulation andCompensation of Automobile Door Outer Panel【Abstract】With the continuous development of the automobile industry in China,the competition between automobile companies is also increasing.In the process of developing new automobile,the quality and size accuracy of automobile panel are increasingly high.Thus to the die production industry also put forward higher requirements,the panel will produce various types of defects during stamping,springback is a challenge for the automobile stamping industry.Through a successful study of the front door outer panel,this paper expound the application of automobile panel process springback simulation and compensation with Autoform software.The full cycle simulation is done according to the boundary conditions of the actual production site of the die.A t the same time,the influence of each affecting factor is confirmed by the sigma simulation,and the accuracy of the springback compensation is finally guaranteed, which can provide reference for the springback compensation of the other automobile parts.Key words:automobile panel;front door otr;springback;compensation;Autoform;full cycle simulationi引言回弹仍是汽车冷冲压生产中最重要的问题,这是 冲压件生产时导致车身零件不合格的重要原因。
汽车车门制造冲压工艺分析

汽车车门制造冲压工艺分析摘要:在对汽车车门进行制造时,所使用的材料以及制造工艺都会影响车门的强度与钢度。
大部分汽车车门的制造过程是冲压,焊装,涂装最后与车身其他部件总装为一个白车身。
汽车车门的制造工艺是整车工艺的一个缩影,从小见大,了解它也就能帮助我们了解整车制造工艺。
笔者介绍了一种冲压工艺方法在汽车车门内板上的具体应用,降低了拉延模具制造难度,降低了制造成本。
关键词:车门材料;冲压工艺;分析一、制件冲压工艺概述冲压件一般需经过拉延/修边+冲孔/整形(或翻边)+冲孔等工序才能得到合格产品。
对于稍微复杂的钣金件,通过拉延仅能得到冲压件大概轮廓,经过后序的修边冲孔,再配合整形翻边等工序才能得到最终零件。
整形翻边等工艺可以降低拉延深度,简化拉延模面的形状,提高成形性,也就是提高了模具制造的可实现性及易操作性。
以常见的车门外板为例,展示普通冲压外覆盖件的工艺流程。
车门外板采用4步工序实现了零件的制造过程,因车门外板拉延深度较小,型面相对简单,因此采用的是一次拉延成形的方法,配合后面的修边、冲孔、翻边工序而成,这种一次拉延的冲压工艺方案是通过拉延得到基本的零件轮廓,后期的整形、翻边等都是对R角的微小型面进行小范围改变,这种工艺方法在实际生产中广泛应用,但同时也存在如下缺点和不足:(1)一次拉延工序得到几乎整个零件的全部形状特征,后工序主要是修边、冲孔、翻边,以及对局部的(小面积的)难以一次成形的型面做整形,得到零件。
此工艺比较死板,灵活变动的空间较小,限制了工艺设计的多样性。
(2)因为是一次拉延得到了零件的基本形状,所以拉延深度是固定的,零件的造型决定了拉延深度的大小,也就决定了成形的可实现性。
对于拉延深度较大的零件就存在拉延状态不稳定及拉延开裂的风险。
(3)拉延深度较大的零件拉延工序存在拉毛风险,为减少拉毛的概率,对于拉延模质量要求较高,比如硬度、光洁度都要提升一个等级,同时也要加强模具的日常保养维护,增加了制造成本。