闪速熔炼的铜精矿干燥技术
浅谈“双闪”铜冶炼的工艺探索及优化

浅谈“双闪”铜冶炼的工艺探索及优化摘要:伴随着铜冶炼高投料、高品位、高氧浓、高热负的技术的发展趋势,闪速熔炼系统,不断优化着热平衡问题和造渣问题,而关键设备的开发及应用,也使得适应高强度熔炼的炉体结构设计和冷却技术有了很大的改进。
闪速熔炼是近代发展起来的一种先进的冶炼技术,能耗低,规模大,具有劳动条件好、自动化水平和劳动生产率高的优点。
精矿喷嘴技术不断地完善,精矿干燥与输送、装料系统等辅助系统不断提升等等,结合实践不断优化,现场工艺的升级与功用的提升,“双闪”铜冶炼技术不断完善。
本文将从闪速冶炼工艺的配置优化与衔接,对双闪冶炼工艺运维与系统优化开展了深入探索。
关键词:冶金工程;闪速熔炼;工艺优化;系统运维1、“双闪”铜冶炼工艺简述闪速冶炼工艺是在闪速炉一步炼铜工艺的基础上开发应用的连续吹炼工艺,连续加料、连续送风、连续排烟。
从1995年首次工业应用以来,特别是在中国几个大型冶炼厂的应用,通过工艺、设备的不断改进,该工艺已经非常成熟可靠。
闪速吹炼采用固体铜锍高浓度富氧吹炼,烟气量小,烟气连续稳定,SO2浓度高,为烟气制酸创造了很好的条件,制酸的电耗和单位能耗是其他连续吹炼工艺无法比拟的;固体铜锍吹炼可以将熔炼和吹炼在时间和空间上分开,不再相互制约,为高作业率创造了条件,可以与任何能够生产高品位铜锍的熔炼工艺相匹配生产,如氧气底吹、富氧双侧吹等;炉体密闭性好,环保条件好,“双闪”工艺硫的捕集率超过99.9%;闪速吹炼炉的单炉产能大,目前年生产能力已经达到45万t粗铜,还有进一步提高的潜力,特别适合大规模生产。
对于30万t以上产能的冶炼厂,采用闪速吹炼工艺的单位投资和单位成本低,具有一定的投资和成本优势。
2、闪速冶炼的工艺流程及现场实践闪速熔炼是充分利用细磨物料巨大的活性表面,强化冶炼反应过程的熔炼方法。
将精矿经过深度干燥后,与熔剂经干燥一起用富氧空气喷入反应塔内,精矿粒子在空间悬浮1-3s 时间,与高温氧化性气流迅速发生硫化矿物的氧化反应,并放出大量的热,完成熔炼反应即造锍的过程。
铜冶炼技术对比解析

1992 1999 5家投产 16万吨/年矿 铜
单炉最高 产能
原料适应 性
原料预处 理
较差
粒度<1mm, 深度干燥, H2O<0.3%
适应性强
制粒或增湿, H2O 9%~11%
强
干燥,H2O< 1%
适应性强
适应性强
适应性强
粒度<100mm, 粒度<100mm, 制粒或增湿, H2O 10%~12% 不需要干燥。 不需要干燥。
S捕集率 炉寿命
150天
业内认可的先进熔炼工艺
闪速熔炼和熔池熔炼: ※Outokumpu闪速熔炼 ※ 浸没喷枪式熔炼(ISA/Ausmelt) ※ 三菱熔炼
闪速熔炼技术的进展
闪速炼铜工艺
●第一座炼铜闪速炉于1949年在芬兰哈里亚瓦尔塔 冶炼厂投入工业生产;目前还用于镍精矿的熔炼 ;1978年开始进行铜精矿的一步炼铜;1995年开 始进行冰铜的吹炼。 ●至今已有40台炼铜闪速炉建成投产,目前在运行 的有37台(其中有3台一步炼铜闪速炉,2台冰铜 吹炼闪速炉),6台炼镍闪速炉在生产。 ●炉体冷却结构的改进、冷却强度的提高,闪速炉 的单炉产能提高,最大达到原设计的3.65倍;闪 速炉的炉寿命延长,最长达到15年,一般10年左 右
产能大:单套系统最大铜产能超过40万吨/年
送风氧浓高:闪速熔炼氧浓达90%,ISA、
三菱、诺兰达熔炼氧浓达到65%,55%和 45%
自热或半自热熔炼:有效利用硫化矿物燃烧
所产生的热量;
冰铜品位高:均超过60%,可以高达75%
现代强化熔炼工艺的特点
高熔炼强度:闪速熔炼单炉铜精矿处理量首先突 破100万吨/年以上;Isa炉单炉铜精矿处理量达到 130万吨/年;三菱炉精矿处理量将超过100万吨/年 (温山)。 硫捕集率高,环保好:一般均超过95%。闪速熔 炼和三菱熔炼超过了99%,吨铜S的排放量不到 2kg,是最清洁的铜冶炼工艺 工艺控制自动化程度高:闪速炉实现了计算机在 线控制。
我国铜冶炼技术的进步及发展
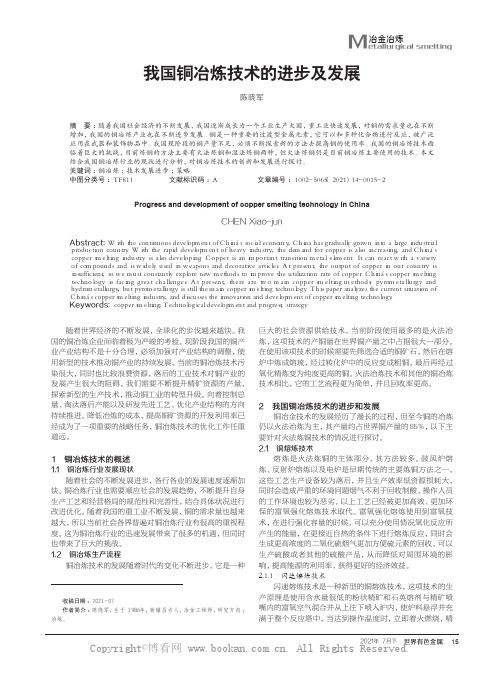
冶金冶炼M etallurgical smelting 我国铜冶炼技术的进步及发展陈晓军(新疆五鑫铜业有限责任公司,新疆 昌吉 831100)摘 要:随着我国社会经济的不断发展,我国逐渐成长为一个工业生产大国,重工业快速发展,对铜的需求量也在不断增加,我国的铜冶炼产业也在不断进步发展。
铜是一种重要的过渡型金属元素,它可以和多种化合物进行反应,被广泛应用在武器和装饰物品中。
我国现阶段的铜产量不足,必须不断探索新的方法去提高铜的使用率。
我国的铜冶炼技术面临着巨大的挑战,目前炼铜的方法主要有火法炼铜和湿法炼铜两种,但火法炼铜仍是目前铜冶炼主要使用的技术。
本文结合我国铜冶炼行业的现状进行分析,对铜冶炼技术的创新和发展进行探讨。
关键词:铜冶炼;技术发展进步;策略中图分类号:TF811 文献标识码:A 文章编号:1002-5065(2021)14-0015-2Progress and development of copper smelting technology in ChinaCHEN Xiao-jun(Xinjiang Wuxin Copper Co., Ltd., Changji 831100, China)Abstract: With the continuous development of China's social economy, China has gradually grown into a large industrial production country. With the rapid development of heavy industry, the demand for copper is also increasing, and China's copper smelting industry is also developing. Copper is an important transition metal element. It can react with a variety of compounds and is widely used in weapons and decorative articles. At present, the output of copper in our country is insufficient, so we must constantly explore new methods to improve the utilization rate of copper. China's copper smelting technology is facing great challenges. At present, there are two main copper smelting methods: pyrometallurgy and hydrometallurgy, but pyrometallurgy is still the main copper smelting technology. This paper analyzes the current situation of China's copper smelting industry, and discusses the innovation and development of copper smelting technology.Keywords: copper smelting; Technological development and progress; strategy随着世界经济的不断发展,全球化的步伐越来越快。
铜精矿的闪速熔炼

与细颗粒相比,粗颗粒不但具有比表面积小和 停留时间短的缺点,而且热传递和质传递系数也 小。
在干精矿中,粒度级别的分布是不均匀的, 全部颗粒达到同样的反应程度是不可能的。 对粗 颗粒会有反应不足,细颗粒则会反应过度。
2、反应塔内精矿氧化行为与熔炼产物的形成
精矿中最常见的矿物有黄铜矿(CuFeS2)和黄铁矿(FeS2)。闪 速炉内发生的总反应可以表达如下:
一般铜精矿,生产含铜为40%~60%的铜锍时, 反应的净热约为2500~3300kJ/(t·精矿)。
表5.3 精矿和燃料发热值的比较
名称
MJ/Kg
名称
MJ/Kg
烟煤
27.9 产出铜锍品位Cu80% 2.79
重油
43.0
铜精矿
(Cu29.5%,Fe26.0
%,
1.67
S31%)产出铜锍品位
Cu51%
闪速熔炼的生产过程中,精矿中的硫化物氧 化以及造渣反应放出大量的热,辅之以热风或富 氧空气,使过程能半自热或自热进行。随着精矿 中的发热元素硫和铁的含量不同和矿物相组成不 同,氧化反应放出的热量也不同。
放出的热量还取决于氧化程度,即生产出的 铜锍品位越高,化学反应放出的热量就越多。表 5.3列出了典型的硫化铜精矿的发热值,并和普通 燃料发热值进行比较。
1、 奥托昆普闪速熔炼
奥 托 昆 普 闪 速 熔 炼 是 采 用 富 氧 空 气 或 723~1273K 的热风作为氧化气体。在反应塔顶部设置了下喷型精 矿喷嘴。干燥的精矿和熔剂与富氧空气或热风高速喷 入反应塔内,在塔内呈悬浮状态。物料在向下运动过 程中,与气流中的氧发生氧化反应,放出大量的热, 使反应塔中的温度维持在1673K以上。在高温下物料 迅速反应(2~3s),产生的熔体沉降到沉淀池内,完成 造冰铜和造渣反应,并进行澄清分离。
祥光_双闪_铜冶炼工艺及生产实践

祥光 双闪 铜冶炼工艺及生产实践周松林﹙祥光铜业有限公司,山东阳谷252327﹚摘要:介绍了祥光铜业 双闪 (闪速熔炼和闪速吹炼)铜冶炼工艺技术、主要设备、生产实践及存在问题与对策。
实践表明: 双闪 工艺是高效环保的炼铜技术,是未来铜冶炼的发展方向,祥光铜业是当今世界最清洁环保的绿色铜冶炼厂之一。
关键词:闪速熔炼;闪速吹炼;生产实践;环境保护中图分类号:T F 811 文献标识码:A 文章编号:1007-7545(2009)02-0011-05Xiangguang Double Flash Copper S melter Process and Production PracticeZH OU So ng lin(Xiangguang Copper Co.,Ltd,Yanggu,S handong 252327,China)Abstract:The Double Flash (Flash Sm elting and Flash Converting )copper smelting technique,m ain e quipments,productio n practice and existing pro blems and problem solutions of Xiangguang Copper are in tro duced.T he practice demonstrates that the Double Flash process is a high effective and environmentfriendly co pper sm elting technique and is a potential dir ectio n of the future co pper smelting dev elo pment.Xiang guang Copper is one of the clean and env ir onm ent friendly g reen copper sm elters in the pr esent w orld.Keywords:Flash Smelting ;Flash Converting;Pro duction practice;Env ir onm ent protection 作者简介:周松林(1961-),男,安徽祁门人,教授级高工,副总经理.祥光铜业有限公司(简称祥光铜业)是继美国肯尼柯特公司之后世界上第二座采用 双闪 (闪速熔炼FSF 和闪速吹炼FCF)工艺的铜冶炼厂,设计规模为年产40万t(一期20万t)阴极铜,140万t(一期70万t)硫酸,20t (一期10t)黄金,600t(一期300t )白银,工艺流程为 蒸气干燥!!!闪速熔炼!!!闪速吹炼!!!回转式阳极精炼!!!永久不锈钢阴极电解!!!高浓度SO 2转化制酸!!!卡尔多炉回收贵金属 。
铜冶炼水平与工艺水平

铜冶炼水平与工艺水平1)火法冶炼工艺当前,全球矿铜产量的75%-80%是以硫化形态存在的矿物经开采、浮选得到的铜精矿为原料,火法炼铜是生产铜的主要方法,特别是硫化铜精矿,基本全部采用火法冶炼工艺。
火法处理硫化铜精矿的主要优点是适应性强,冶炼速度快,能充分利用硫化矿中的硫,能耗低。
其生产过程一般由以下几个工序组成:备料、熔炼、吹炼、火法精炼、电解精炼,最终产品为电解铜。
原料制备工序:将铜精矿、燃料、熔剂等物料进行预处理,使之符合不同冶炼工艺的需要。
熔炼工序:通过不同的熔炼方法,对铜精矿造硫熔炼,炼成含铜、硫、铁及贵金属的冰铜,使之与杂质炉渣分离;补出的含二氧化硫烟气经收尘后用于制造硫酸或其他硫制品,烟尘返回熔炼炉处理。
吹炼工序:除去冰铜中的硫铁,形成含铜及贵金属的粗铜,炉渣和烟尘返回上一工序处理。
火法精炼工序:将粗铜中硫等杂质进一步去除,浇铸出符合电解需要的阳极板。
电解精炼工序:除去杂质,进一步提纯,生产出符合标准的阴极铜成品,并把金银等贵金属富集在阳极泥中。
传统熔炼方法如鼓风炉熔炼、反射炉熔炼和电炉熔炼,由于效率低、能耗高、环境污染严重而逐渐被新的富氧强化熔炼工艺所代替[[3]新的富氧强化熔炼可分为闪速熔炼和熔池熔炼两大类,前者包括奥托昆普型闪速熔炼和加拿大国际镍公司闪速熔炼等,后者包括诺兰达法、三菱法、艾萨法、奥斯麦特法和瓦纽可夫法以及我国自主开发的水口山法、白银炉熔炼、金峰炉熔炼等技术。
铜锍吹炼方法有传统的卧式转炉、连续吹炼炉、虹吸式转炉。
新型吹炼技术包括艾萨吹炼炉、三菱吹炼炉和闪速吹炼炉等。
粗铜的火法精炼在阳极炉内进行,对于转炉产出的液态粗铜采用回转式阳极炉或固定式反射炉精炼,经氧化、还原等作业进一步脱除粗铜中的铁、铅、锌、砷、锑、铋等杂质,并浇铸成含铜99.2%-99.7%的阳极板。
铜电解工艺有传统电解法、永久阴极电解法和周期反向电流电解法3种。
目前大多数电解铜厂都使用传统电解法,永久阴极电解法和周期反向电流电解法是20世纪70年代以来发展的新技术。
铜冶炼闪速熔炼及熔池熔炼技术探讨
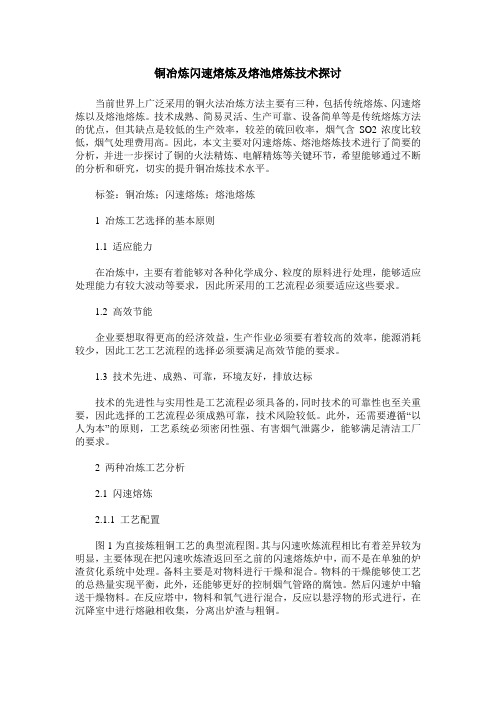
铜冶炼闪速熔炼及熔池熔炼技术探讨当前世界上广泛采用的铜火法冶炼方法主要有三种,包括传统熔炼、闪速熔炼以及熔池熔炼。
技术成熟、简易灵活、生产可靠、设备简单等是传统熔炼方法的优点,但其缺点是较低的生产效率,较差的硫回收率,烟气含SO2浓度比较低,烟气处理费用高。
因此,本文主要对闪速熔炼、熔池熔炼技术进行了简要的分析,并进一步探讨了铜的火法精炼、电解精炼等关键环节,希望能够通过不断的分析和研究,切实的提升铜冶炼技术水平。
标签:铜冶炼;闪速熔炼;熔池熔炼1 冶炼工艺选择的基本原则1.1 适应能力在冶炼中,主要有着能够对各种化学成分、粒度的原料进行处理,能够适应处理能力有较大波动等要求,因此所采用的工艺流程必须要适应这些要求。
1.2 高效节能企业要想取得更高的经济效益,生产作业必须要有着较高的效率,能源消耗较少,因此工艺工艺流程的选择必须要满足高效节能的要求。
1.3 技术先进、成熟、可靠,环境友好,排放达标技术的先进性与实用性是工艺流程必须具备的,同时技术的可靠性也至关重要,因此选择的工艺流程必须成熟可靠,技术风险较低。
此外,还需要遵循“以人为本”的原则,工艺系统必须密闭性强、有害烟气泄露少,能够满足清洁工厂的要求。
2 两种冶炼工艺分析2.1 闪速熔炼2.1.1 工艺配置图1为直接炼粗铜工艺的典型流程图。
其与闪速吹炼流程相比有着差异较为明显,主要体现在把闪速吹炼渣返回至之前的闪速熔炼炉中,而不是在单独的炉渣贫化系统中处理。
备料主要是对物料进行干燥和混合。
物料的干燥能够使工艺的总热量实现平衡,此外,还能够更好的控制烟气管路的腐蚀。
然后闪速炉中输送干燥物料。
在反应塔中,物料和氧气进行混合,反应以悬浮物的形式进行,在沉降室中进行熔融相收集,分离出炉渣与粗铜。
在余热锅炉中进行炉子烟气的冷却。
部分烟尘也会被余热锅炉收集,在电收尘器中收集剩余的颗粒,通常所有烟尘都返回炉子中。
视所选择的渣型和氧势而定,在粗铜闪速熔炼炉渣中,铜的含量为15%-25%。
祥光铜业双闪“技术”工艺流程
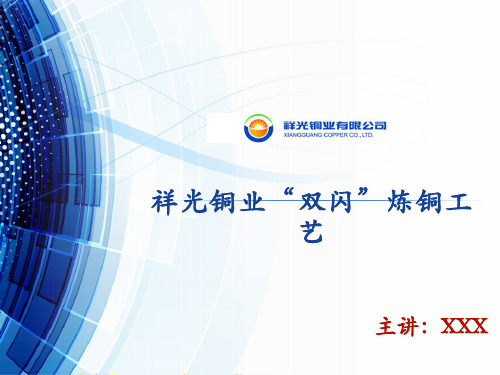
石灰熔剂被用来生成熔融钙铁渣 ,相比铁硅渣而言更好 , 因为四氧 化三铁在钙铁渣中溶解度更强。同时加入少量的石英砂来改变炉渣 成分,从而提高耐火砖炉衬的寿命。 闪速吹炼反应产出品位为98.5 %的粗铜,粗铜定期由放铜口放出,通 过溜槽流入阳极炉进行精炼;吹炼炉渣定期通过溜槽流入渣水淬装置 , 经水淬后用胶带运输机输送到脱水仓中静置脱水后用汽车运输至精 矿库中储存,经配料后送闪速熔炼炉。 未反应的硫化物被气流带走,利用位于沉淀池顶部靠近上升烟道与 沉淀池顶部交界处的喷嘴喷入氧气,使它们在上升烟道燃烧。 闪速吹炼炉产出的烟气在余热锅炉中冷却,然后进入沉尘室及电收 尘器除尘,除尘后的烟气送制酸。
反应,同时通过反应塔顶的3个氧气天然气烧嘴补充反应塔熔炼内物
料过程所需的热量。并以90%以上的返回率处理熔炼及吹炼过程产生 的烟灰。余热锅炉和电收尘器的烟尘采用气力输送系统输送至熔炼 炉顶,烟灰由布袋收尘器收集后进入烟灰仓,废气则由排风机放空 ,烟灰仓中的烟灰由失重螺旋带入风动流槽,与干矿混合后流入中 央精矿喷嘴(能力为320t/h),进入反应塔进行熔炼反应。
在反应塔生成冰铜及炉渣的熔融物落入沉淀池。因比重差别,冰
铜和炉渣分离。生产出品位70%左右的冰铜通过流槽排放至冰铜粒化
室,进行冰铜水淬。炉渣则排放至渣包中,通过渣包车运送到选矿 车间缓冷后进行磨碎、浮选,渣精矿重新返回闪速炉熔炼。
闪速熔炼烟气通过上升烟道排出,并用余热锅炉的进行强制循环
冷却。在余热锅炉内降温除尘后,进入沉降室、电收尘器进一步净 化除尘。净化后的烟气通过闪速炉排烟风机送至硫酸车间制酸。
5、“双闪”工艺管理
蒸汽干燥机
闪速炉炉体结构图
反应塔 是悬挂在炉子钢
结构上,内衬耐火砖的圆筒形 塔。耐火材料内衬由安装在砖 层之间的铜冷却水套来保护免 受热冲击。
铜冶炼的现状及其发展状况
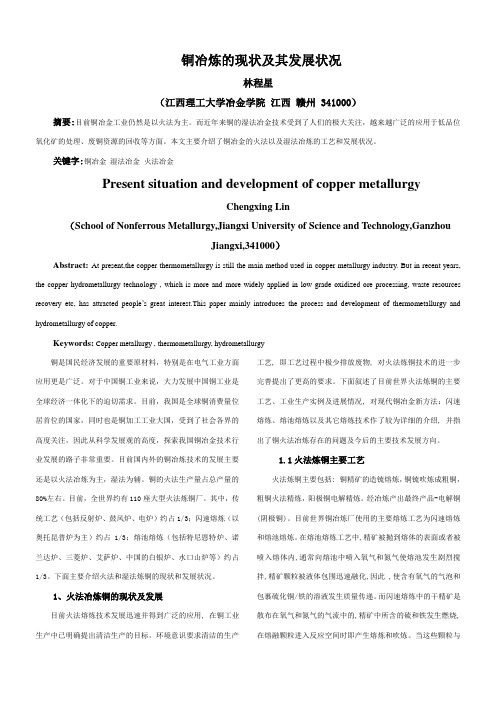
铜冶炼的现状及其发展状况林程星(江西理工大学冶金学院江西赣州 341000)摘要:目前铜冶金工业仍然是以火法为主。
而近年来铜的湿法冶金技术受到了人们的极大关注,越来越广泛的应用于低品位氧化矿的处理、废铜资源的回收等方面。
本文主要介绍了铜冶金的火法以及湿法冶炼的工艺和发展状况。
关键字:铜冶金湿法冶金火法冶金Present situation and development of copper metallurg yChengxing Lin(School of Nonferrous Metallurgy,Jiangxi University of Science and Technology,GanzhouJiangxi,341000)Abstract: At present,the copper thermometallurgy is still the main method used in copper metallurgy industry. But in recent years, the copper hydrometallurgy technology , which is more and more widely applied in low grade oxidized ore processing, waste resources recovery etc, has attracted people’s great interest.This paper mainly introduces the process and development of thermometallurgy and hydrometallurgy of copper.Keywords: Copper metallurgy , thermometallurgy, hydrometallurgy铜是国民经济发展的重要原材料,特别是在电气工业方面应用更是广泛。
最新4铜精矿的闪速熔炼汇总

对某些工厂反应塔操作数据的统计表明:在 不同的反应塔的高度下,平均气流速度为1.4~ 4.7m/s时,相应的气体停留时间如图5.5所示。
19
5 7.5
4
7.6
气流的平均停留时间,s
3
7.1
7.5
5.7 6
7.1
2
7.5 2
1
1
2
3
4
5
反应塔内平均气流速度,m/s(数据点旁的数字是反应塔的高
度)
4铜精矿的闪速熔炼
闪速熔炼是将经过深度脱水(含水小于0.3%)的粉 状精矿,在喷嘴中与空气或氧气混合后,以高速度(60~ 70m/s)从反应塔顶部喷入高温(1450~1550℃)的反应 塔内。
精矿颗粒被气体包围,处于悬浮状态,在2~3s内就 基本上完成了硫化物的分解、氧化和熔化等过程。
熔融硫化物和氧化物的混合熔体落下到反应塔底部的 沉淀池中汇集起来,继续完成冰铜与炉渣最终形成过程, 并进行沉清分离。
2
1、 奥托昆普闪速熔炼
奥 托 昆 普 闪 速 熔 炼 是 采 用 富 氧 空 气 或 723~1273K 的热风作为氧化气体。在反应塔顶部设置了下喷型精 矿喷嘴。干燥的精矿和熔剂与富氧空气或热风高速喷 入反应塔内,在塔内呈悬浮状态。物料在向下运动过 程中,与气流中的氧发生氧化反应,放出大量的热, 使反应塔中的温度维持在1673K以上。在高温下物料 迅速反应(2~3s),产生的熔体沉降到沉淀池内,完成 造冰铜和造渣反应,并进行澄清分离。
入口初始速度对气体在塔内的停留时间起着决定性的作
用。
15
公式是在等温情况下得出的。 由于化学反应产生的热使塔内的气体瞬间被加热到高温 (1300℃以上),气体体积膨胀扩张了喷射锥空间,因而 真实速度将大大减少。 对高为9m,直径为6m的反应塔,当入口初速度为30m/s 时 ,气流在塔内的停留时间约为2s。
火法专题

火法冶炼铜是在冶金炉中,100℃以上高温条件下,从铜精矿中提取铜的炼铜方法。
该方法由铜熔炼、铜锍吹炼和粗铜精炼三大工序组成,其中精炼又分为火法精炼和电解精炼两种。
(一)铜熔炼依其出现时间的早晚和生产技术与装备水平可分为传统方法和炼铜新工艺两类。
按冶炼过程物料存在的状态和炼铜炉型,又可分成熔池熔炼和悬浮熔炼。
鼓风炉、反射炉和电炉熔炼法,一般归属于传统方法;而闪速熔炼、诺兰达法、白银法、奥斯麦特法可称之为炼铜新工艺。
1.闪速熔炼该方法是在高温高速空气流或氧气流中,将硫化铜精矿熔炼成铜锍的炼铜法,属于悬浮熔炼类型。
闪速熔炼现有两种炉型:一为芬兰奥托昆普(Outokumpu )闪速炉;一为加拿大国际镍公司(Inco)闪速炉。
同反射炉熔炼比,闪速熔炼能耗低,烟气SO2浓度高,有利于生产硫酸,机械化自动化水平高,生产能力大,可实现清洁生产。
缺点是设备庞大,原料准备复杂,烟尘率高,炉渣含铜高,需要贫化处理。
上述两种炉型中,芬兰奥托昆普闪速炉发展最快(工艺流程见图3),至1997年,全世界已建成投产奥托昆普炼铜闪速炉35座,其中中国有2座。
该方法炼铜生产能力占世界矿产铜的一半以上。
(1)奥托昆普闪速炉的熔炼特征该方法充分利用了硫化铜精矿粒度细、比表面积大的特性和精矿中S、Fe氧化放出热量的潜能,强化了熔炼过程同时节约了能源。
熔炼过程是,将干燥到含水低于0.3%的铜精矿用高速气流(>100m/s)喷入反应塔——一垂直反应空间内,在矿物氧化和辅助燃料燃烧产生高温下,铜精矿发生以下主要熔炼反应:熔炼产生的熔体落入与反应塔相接的水平卧式沉淀池中,继续完成如下主要反应:Cu2O+FeS====Cu2S+FeO2FeO+SiO2====2FeO·SiO2熔炼产出的熔融体在沉淀池中分为炉渣和铜锍上下两层,铜锍经放铜口放出,送转炉吹炼;炉渣经渣口连续放入电炉进一步贫化以回收渣中铜,烟气经余热锅炉回收余热、收尘系统收下烟尘后,送去生产硫酸。
铜精矿的闪速熔炼

13
图 5.4 反应塔内的气体-精矿流散布示意图(中央喷嘴)
14
等温气体喷射时的速度衰减由下式表达: Ux=12.4U0r0/x (5-1) 式中,Ux为从入口点开始的x距离上的中心喷射速度 (m/s);U0为入口初始速度(m/s);r0为入口喷嘴半径(m) 。 式(5-1)说明,气流的终点速度乃由入口初始速度决定, 入口初始速度对气体在塔内的停留时间起着决定性的作 用。
闪速熔炼有以下的特点:
1.焙烧与熔炼结合成一个过程; 2.炉料与气体密切接触,在悬浮状态下与气相进行传热和
传质;
3.FeS与Fe3O4、FeS与Cu2O(NiO)、以及其它硫化物与氧 化物的交互反应主要在沉淀池中以液—液接触的方式进行。
闪速熔炼按不同的工作原理可分为两种基本形式:
1.精矿从反应塔顶垂直喷入炉内的奥托昆普闪速炉(图 5.1); 2.精矿从炉子端墙上的喷嘴水平喷入炉内的印柯闪速炉 (图5.2)。
闪速熔炼是将经过深度脱水(含水小于0.3%)的粉
状精矿,在喷嘴中与空气或氧气混合后,以高速度(60~
70m/s)从反应塔顶部喷入高温(1450~1550℃)的反应塔内。
精矿颗粒被气体包围,处于悬浮状态,在2~3s内就
基本上完成了硫化物的分解、氧化和熔化等过程。 熔融硫化物和氧化物的混合熔体落下到反应塔底部的 沉淀池中汇集起来,继续完成冰铜与炉渣最终形成过程, 并进行沉清分离。 炉渣在单独贫化炉或闪速炉内贫化区处理后再弃去。
2
1、 奥托昆普闪速熔炼
奥托昆普闪速熔炼是采用富氧空气或 723~1273K
的热风作为氧化气体。在反应塔顶部设置了下喷型精
矿喷嘴。干燥的精矿和熔剂与富氧空气或热风高速喷 入反应塔内,在塔内呈悬浮状态。物料在向下运动过 程中,与气流中的氧发生氧化反应,放出大量的热, 使反应塔中的温度维持在 1673K 以上。在高温下物料
第四次课_铜精矿的闪速熔炼

闪速熔炼有以下的特点:
1.焙烧与熔炼结合成一个过程; 2.炉料与气体密切接触,在悬浮状态下与气相进行传热和
传质;
3.FeS与Fe3O4、FeS与Cu2O(NiO)、以及其它硫化物与氧 化物的交互反应主要在沉淀池中以液—液接触的方式进行。
闪速熔炼按不同的工作原理可分为两种基本形式:
1.精矿从反应塔顶垂直喷入炉内的奥托昆普闪速炉(图 5.1); 2.精矿从炉子端墙上的喷嘴水平喷入炉内的印柯闪速炉 (图5.2)。
为喷嘴和炉型设计的改进提供基础。
13
精矿颗粒和气体的运动规律 从反应塔顶部喷嘴喷出的气-固(精矿)混合流,离开喷
嘴后,在塔内形成了两个区域:
1.喷嘴口附近的喷射区(或称入口区); 2. 扩张气流区 (如图5.4中的截面A-A以下)。 扩张区延续到熔池面上时流体形状改变。此时的气流速 度称为终点气流速度。
7
2、印柯闪速炉熔炼
印柯闪速炉熔炼法也称之为氧焰熔炼法,该 法是用工业氧(95~98%O2)将干精矿和熔剂从 炉子两端水平喷入炉子的反应区,炉料在熔池上 面的炉膛空间强烈氧化,熔炼产出冰铜和炉渣。 冰铜品位45~48%,渣含铜0.6%~0.7%。烟 气SO2含量70~80%。由于采用工业氧,烟气量 很小。
19
在沉淀池内的主要反应有以下几类: (1)Fe3O4的还原反应
[FeS] + 3(Fe3O4) + = 10(FeO) + SO2 (5-5)
在有SiO2存在的情况下,FeO与SiO2造渣,使Fe3O4 的还原变得容易。影响该反应进行的因素是炉渣中 Fe3O4的活度、Fe/SiO2、锍品位、二氧化硫分压和 温度以及各相之间接触的动力学条件。 根据图5.5,可以确定出沉淀池终渣中Fe3O4的含 量(%)与锍品位的关系。
《铜精矿的闪速熔炼》课件

配料系统通常包括原料储存、计 量、输送和混合等装置,通过自 动化控制系统实现精确控制和调 整。
混合系统
混合系统的作用是将配料系统输送来 的各种原料进行均匀混合,以确保进 入闪速熔炼炉的原料质量稳定。
混合系统通常采用高效混合设备,如 搅拌器、混合器等,通过强化搅拌和 混合,减小原料之间的粒度和密度差 异,提高混合效果。
铜精矿的配料与混合
配料原则与要求
根据冶炼要求,确定配料比例, 确保原料成分符合标准。
混合方法与设备
介绍混合设备的类型和工作原理 ,以及混合效果的评估方法。
铜精矿的闪速熔炼
01
闪速熔炼原理
阐述闪速熔炼的基本原理和技术特点。
02
闪速熔炼设备
介绍闪速熔炼炉的构造、工作原理和使用维护方法。
03
熔炼工艺参数
该技术采用高温、高反应速 率的生产条件,使反应在最 佳条件下进行,提高了生产 效率。
同时,该技术采用先进的烟 气处理和余热回收技术,能 够减少对环境的污染和能源 的浪费。
02 铜精矿闪速熔炼的工艺流程
铜精矿的准备
铜精矿的来源与特点
介绍不同来源的铜精矿及其特点,如品位、杂质含量等。
铜精矿的预处理
包括破碎、磨细、筛分等工序,以确保精矿粒度合格,满足 熔炼要求。
02
该技术利用了高温、高反应速率的条件下,铜精矿中的 硫化物与氧气发生快速氧化反应,生成二氧化硫气体, 同时释放出铜和铁等有价金属。
03
铜精矿闪速熔炼技术的核心在于控制炉温和反应速率, 使反应在最佳条件下进行,以提高金属回收率和降低能 耗。
铜精矿闪速熔炼技术的历史与发展
铜精矿闪速熔炼技术起源于20世纪初,最初是为了解决当时铜矿资源品位下降、成 本上升的问题而开发的。
铜精矿的闪速熔炼
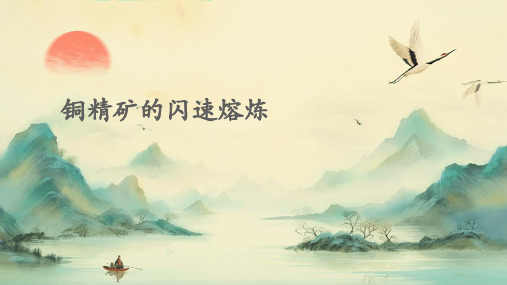
配备专业的紧急救援队伍和设备,确 保在事故发生时能够迅速展开救援。
05
闪速熔炼的应用与发展
闪速熔炼的应用领域
铜冶炼
闪速熔炼技术广泛应用于铜精矿 的冶炼,能够高效地处理低品位、
高杂质的铜精矿,产出高质量的 阴极铜。
工业硅生产
在工业硅生产中,闪速熔炼技术通 过控制适宜的反应条件,实现高效 率、低能耗的生产。
低成本
闪速熔炼工艺流程简单,操作 稳定,能够降低生产成本和提 高经济效益。
环保友好
闪速熔炼产生的烟气经过处理 后能够达到环保标准,减少对 环境的污染。
灵活性
闪速熔炼可以根据原料成分和 产品质量要求进行灵活调整, 适应不同原料和产品的需求。
03
闪速熔炼的设备与操作
闪速熔炼的主要设备
反应塔
余热锅炉
反应塔是闪速熔炼的核心设备,用于完成 铜精矿的熔炼过程。塔内设有矿石分布器 、反应剂喷嘴等关键部件。
安全防护措施
配备齐全的安全防护设备, 如防护眼镜、手套、口罩 等,确保操作人员的安全。
定期检查维护
对设备进行定期检查和维 护,确保设备正常运行, 及时发现并排除安全隐患。
事故应急处理
应急预案制定
制定详细的事故应急预案,明确应急 处理流程和责任人。
紧急救援措施
安全疏散与警戒
在事故发生时,及时组织现场人员疏 散,设置警戒线,防止次生事故的发 生。
其他领域
除铜冶炼和工业硅生产外,闪速熔 炼技术在其他有色金属冶炼领域也 有所应用,如镍、钴、锌等。
闪速熔炼技术的发展趋势
技术创新
随着科技的不Leabharlann 进步,闪速熔炼 技术也在不断创新和完善,以提
高生产效率和产品质量。
浅谈“双闪”铜冶炼工艺在中国的优化和改进

浅谈“ 双闪” 铜冶炼工艺在中国的优化和改进摘要:闪速炉是一种高效强化后的冶金炉,具有节能环保的优点,其最大的特点就是可以充分利用炉料的巨大比表面。
自从“双闪”铜冶炼工艺出现之后,成为了稳定可靠的铜冶炼工艺,是中国的一些新建的大型铜冶炼企业的首选工艺。
但因为造价比较高,在中国还没有大范围普及,并且由于“双闪”工艺是引进的国外的,因此在中国的企业使用时,要对其进行优化和改进,以使其更适应中国的企业环境和冶炼条件。
关键词:“双闪”铜冶炼工艺;优化;改进;中国前言伴随着国家经济的不断发展和进步,我国对铜这种金属的需求也越来越旺盛。
但我们也都知道,铜金属开采出来以后,需要进行人工的加工,才能满足我们生活和生产的要求。
这就使得为了提高铜冶炼工艺的生产效率,要不断的寻求更加先进、高效并且环保的铜冶炼工艺来满足我国对铜金属的需求。
“双闪”工艺出现以后,引起了我国铜冶炼企业的关注,并且在我国一些大型企业已经逐渐运用。
但因为“双闪”工艺是引起的,所以为了使其更好的适应我国的企业环境和企业要求,要不断的对其进行优化和改进,尤其是在当前我国对生态环境保护越来越重视的情况下,更要对“双闪”铜冶炼工艺不断的优化和改进。
一、“双闪”铜冶炼工艺简介“双闪”铜冶炼工艺指的是闪速熔炼工艺和闪速吹炼工艺,两者综合到一块称之为“双闪”工艺。
这种“双闪”铜冶炼工艺和传统的一些铜冶炼工艺相比较,有着生产效率高、可以充分利用能源并且环保等特点,现在已经逐渐成为我国大型的新建的炼铜企业所选择的主流的工艺之一。
就目前来看,“双闪”工艺是世界上最先进的铜冶炼技术,在世界范围内都是处在领先地位的。
自从“双闪”铜冶炼工艺1995年的时候在肯尼柯特铜冶炼厂应用以来,经过20余年的发展和完善,已经成为非常稳定可靠的铜冶炼工艺。
二、“双闪”铜冶炼工艺在中国的优化和改进的必要性前面我们已经知道,“双闪”铜冶炼工艺在环保和生产效率提高上都具备一定的优势,这主要是因为在吹炼过程中,产生的烟气量比较小并且也较为恒定,低空的污染,这就使得炉体烟气处理设备体积小,在系统密闭的情况下没有SO2的寿命较长,耐火材料消耗也较低。
闪速熔炼的基本原理
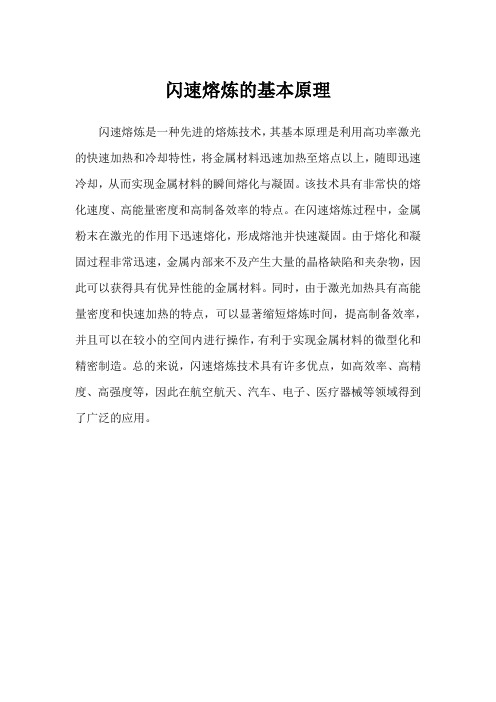
闪速熔炼的基本原理
闪速熔炼是一种先进的熔炼技术,其基本原理是利用高功率激光的快速加热和冷却特性,将金属材料迅速加热至熔点以上,随即迅速冷却,从而实现金属材料的瞬间熔化与凝固。
该技术具有非常快的熔化速度、高能量密度和高制备效率的特点。
在闪速熔炼过程中,金属粉末在激光的作用下迅速熔化,形成熔池并快速凝固。
由于熔化和凝固过程非常迅速,金属内部来不及产生大量的晶格缺陷和夹杂物,因此可以获得具有优异性能的金属材料。
同时,由于激光加热具有高能量密度和快速加热的特点,可以显著缩短熔炼时间,提高制备效率,并且可以在较小的空间内进行操作,有利于实现金属材料的微型化和精密制造。
总的来说,闪速熔炼技术具有许多优点,如高效率、高精度、高强度等,因此在航空航天、汽车、电子、医疗器械等领域得到了广泛的应用。