带材跟踪控制在拉矫重卷中的应用
物料跟踪系统在高线生产过程中的应用

103DOI:10.16660/ki.1674-098X.2010-5640-1092物料跟踪系统在高线生产过程中的应用①黄新峰1 杨军1 李员妹2 钱勤锋1(1.新余钢铁集团有限公司线棒材厂 江西新余 338001;2.中冶南方( 新余) 冷轧新材料技术有限公司 江西新余338025)摘 要:本文介绍了物料跟踪系统构成,以及物料跟踪在新钢线棒材厂高线生产过程的应用。
这套系统支撑高线组批、装炉、炉内加热、出炉、轧制、集卷、称重、入库、发货全线流程,满足线棒厂生产精细化管理的要求,使生产过程的物流和信息流同步,实现生产管理的在线化、集成化、合理化,提升新钢线棒厂的生产综合管理能力。
实践表明该系统符合新钢公司“智能制造、智慧工厂”推进工作,成效显著。
关键词:高线 物料跟踪系统 系统构成 跟踪流程中图分类号:F273 文献标识码:A 文章编号:1674-098X(2020)12(c)-0103-04Application of Material Tracking System in the Hi-Speed WireRod Production ProcessHUANG Xinfeng 1 YANG Jun 1 LI Yuanmei 2 QIAN Qinfeng 1(1.Wire & Rod Rolling Mill Plants, Xinyu Iron and Steel Group Co., Ltd., Xinyu, Jiangxi Province,338001 China;2.WISDRI (Xinyu) Cold Processing Engineering Co., Ltd., Xinyu, JiangxiProvince, 338025 China)Abstract: This paper introduces the structure of material tracking system and the application of material tracking in the Hi-Speed Wire Rod production process of Xin steel Wire & Rod Rolling Mill Plants. This system supports the whole process including batching, furnace charging, furnace heating, furnace discharging, rolling, volume collection, weighing, warehousing and delivery, which meets the requirements of Wire & Rod Rolling Mill Plants in the production of fine management, synchronizes the logistics and information f low in the production process, Realizes the production management online, integrated and rationalized, improves the comprehensive production management capacity of Xin steel Wire & Rod Rolling Mill Plants. The result shows that the system is in line with the promotion of "intelligent manufacturing and intelligent factory" of Xin steel, and the effect is remarkable.Key Words: Hi-speed wire rod; Material tracking system; System structure; Tracking process①作者简介:黄新峰(1984—),男,壮族,广西崇左人,本科,助理工程师,主要从事线棒材轧钢工艺技术及现场管理工作。
拉伸弯曲矫直机应用于铝带精整中的探讨

拉伸弯曲矫直机应用于铝带精整中的探讨摘要:拉伸弯曲矫直机是目前常用的材料矫直设备,能够在很大程度上满足热轧钢板的平直度要求,此种设备不仅具备辊式矫直机的特点,同时还具备拉力矫直机的优点,能够在张力辊拉伸和弯曲辊反复连续性的联合作用下,让热轧钢板发生形变,致使得到矫直后的板材,最大限度控制热轧钢的各种能够形状问题,提高板材的质量。
而对于铝带精整来说,单指铝板的加工,我国每年大约七层左右的铝板在市面上流通,并且在流通以前此类铝板都要经过精整,所以铝板带的生产加工工序进行优化和调整,是非常重要的,并且还要有效控制各铝板带的加工工序。
因此,本文概述拉伸弯曲矫直机的特点和矫正原理,介绍铝带精整的控制内容和原理,探讨矫直张力与初始张力的关系,以及带材运行速度变化对于矫直张力的影响。
关键词:拉伸弯曲矫直机;铝带精整;特点原理;应用探讨;在社会发展的推动作用下,铝带精整行业也随之得到发展,同时铝带的使用要求也在不断提高,其中就包括铝带的平直度。
相较于传统的拉力矫直机来说,让加工材料在极限作用力下发生形变,从而重新塑造材料的形状,直至达到预定的平直度,但是由于受到材料自身厚度变化的影响,随着厚度不断增加,拉力矫直机组在运行过程中,功率会不断增加,同时机组的尺寸也随之增加变大,同时能源方面的消耗也会不断增加;而辊式矫直机又只针对较厚的加工材料,对于厚度较小的材料来说与拉力矫直机相差不大,因此基于此种情况,将两种机组进行结合,研发出了拉伸弯曲矫直机,能够有效消除板材在进行加工时,内部应力不平衡的问题,实现既定平直度的要求,能够适用于不同厚度的加工板材,致使精整后的板材平直度能够满足要求。
1 概述拉伸弯曲矫直机的特点和矫正原理1.1特点想要了解拉伸弯曲矫直机的特点,首先要知道热轧板材自身会存在哪些问题和缺陷,如浪形、卷边等,能够直接影响板材板形的问题。
进而拉伸弯曲矫直机就是为了处理此类问题而出现的,热轧板材在拉伸弯曲矫直机的作用下能够有效改善板材的力学性能,例如:拉伸弯曲矫直机设备工作时,带材受到拉伸和弯曲的双重作用,拉伸作用下带材沿几何中心层被拉伸,弯曲作用下中心层向弯曲内侧偏移,而弹复时中心层并没有完全回到初始位置,从而产生了剩余延伸率,剩余延伸率就是改善板材板形的关键。
关于拉伸弯曲矫直机在使用中常见问题的讨论

8 2・
科技论 坛
关于拉伸弯 曲矫直机在使用中常见问题 的讨ห้องสมุดไป่ตู้
宋凤莲 ( 河 南省开封 市技 师学院, 河南 开封 4 7 5 0 0 0 )
摘 要: 板材 的平直度在 产品应 用中受到越 来越 多的关注, 因此矫 直机在 各种 薄带材生产线上越 来越 受到重视 , 本文介 绍 了 拉伸弯 曲矫 直机的矫正原理及矫 直机在应用 中的切入量 、 打滑、 延伸率补偿等 问题 , 以克服改进其不足 , 使 其作 用得到更加有效的发挥 。
盯t 广带铺 申 J 立力 h 一 带钢厚度 盯广屈服点 k 一系数, k =E 。 / 2盯i , E l 一 数 P 一 带钢曲率 从匕 式可看出日 , 中性层偏移量 A与拉伸应力 盯。 成正比。当 o r 。 为 零, 带钢处于纯弯曲状态时 , A为零。 在这 , 钢 缴 曲, 其
又由欧拉公 式得
e >8 2 >8l V> V2 > V1
我国 优质带钢的生产更多的贡献力量。 参考文献
可见, 被动辊的出口 速度 永远大于 ^ 口 速度。 【 l 降同 虎宽带钢拉矫机工作机理及性能优 化的 研究 北京: 北京 科技大 1 9 9 7. 4 2 2张力辊处于“ 电动状态” 。 当 张力辊工作于 ” 电 动状态时, 张力 辊 学. 处于主 。这时张力 辊在电 机的驱动下拖动特铮 隧 转, 见图2 。 设出 甫矫 直 理论与参数计算l 北京: 机械工业出 版襁1 9 9 口 张力辊线速度为 V E , 并令其与出口 带钢速度 海机电工业管理局. 宝 钢2 0 3 0 a r m冷轧 枳细机械设备关 键技术的探讨 v 。 。 相等, 同理可得其各段张力、 速度及拉伸应变: 耻 海: 上海科技文献出版社, l 9 8 &
高线精整区物料跟踪系统开发与应用

高线精整区物料跟踪系统开发与应用随着现代制造业的发展,高线精整区已成为生产线上不可或缺的环节。
然而,由于该区域内物料繁多、种类复杂,如何有效跟踪物料的流动情况成为了生产管理的一大难题。
为了解决这一问题,开发和应用高线精整区物料跟踪系统显得尤为重要。
本文将探讨该系统的开发与应用、优势及展望。
一、高线精整区物料跟踪系统开发高线精整区物料跟踪系统的开发涉及到硬件、软件两个方面。
在硬件方面,系统需要使用传感器、标签等设备来实现对物料的识别和跟踪。
传感器可以采集物料进入和离开高线精整区的信号,标签则用于对物料进行标记,方便系统进行识别。
同时,为了保证物料跟踪的准确性和实时性,还需要保证传感器和标签的稳定性和高效性。
在软件方面,需要开发一套可视化的物料跟踪系统。
该系统能够接收传感器和标签发送的信息,进行数据处理和分析,并实时显示物料的流动情况。
除此之外,还需要设置相应的报警功能,以便在发生异常情况时及时提醒工作人员。
二、高线精整区物料跟踪系统应用高线精整区物料跟踪系统的应用可以极大地提高生产线的效率和精确度。
首先,该系统可以实现对物料的自动化跟踪。
通过将传感器和标签与生产线相连,系统可以实时监测物料的流动情况,准确记录物料的进出时间和位置,并自动生成相应的报表和图表。
这样一来,管理人员可以通过系统直观地了解物料的运行状况,提高对物料的管理效率。
其次,物料跟踪系统可以帮助发现生产线上的问题。
系统可以记录下物料进出高线精整区的时间和位置,一旦出现物料丢失、堵塞等问题,系统会自动报警,提醒工作人员及时处理。
这样不仅可以及时发现问题,也可以避免生产线的停工和物料浪费。
再次,高线精整区物料跟踪系统还可以实现对物料的历史数据分析。
通过对物料的流动情况进行统计和分析,系统可以提供生产线上各个环节的效率评估和改进建议。
这将有助于企业提高生产线的整体效率和质量水平。
三、高线精整区物料跟踪系统的优势相比传统的物料跟踪方式,高线精整区物料跟踪系统具有以下优势:1.提高了物料跟踪的准确性和实时性。
铝板带热连轧机带材跟踪控制

带材 跟踪 是计算 机控 制 系统 通过 建立跟 踪模 型
和检测区域边界传感器的中断信号 ,实时判断从加 热炉到卷材运输区域之间带材的实际位置 ,并根据
实际位置和跟踪方向启动相应的功能程序 ,对指定 的带材准确地进行控制 、数据采样和操作指导 ,实 现轧 制过 程 自动化 … 1。
12 跟踪 的方 法 .
p r e・
Ke r s h t a d m l fr u i u h e ;s i ;c mp tr u o t a o y wo d : o n e mi m n t lo a l m set tp r s o u e ;a tma z t n i i
前 言
铝板带 热 连 轧 具 有 高 效 率 和 规模 化 效 益 的 特
一
跟踪系统的硬件主要 由跟踪传感器 、一级计算 机 、二级计 算机 和数据 传输 网络 构成 。跟踪传感 器
包括 冷 金 属 探 测 器 ( MD) 负 荷 继 电 器 ( R 等 , C 和 L) 用于 检测带 材 的头尾部 ,产生 中断信号 。一级计 算 机完 成跟踪 中断信号 的处理 、跟踪 方 向的判 断 、带 材数 据 的管理 ,当轧线 上 同时存 在多块 带材 时 ,一
中图分类号 :T 35 1 。G 3 . G 3 .3 T 355 6 文献标 识码 :B 文章编 号:10 —49 z0 14 O 2 05 88(06o 一 O3—0 3
Tr c n r lo tTa d m i o u n m ti s a e Co to fHo n e M l f rAlmi u S rp l
非线性 、时滞性等特点和产品的高质量要求 , 决定 了热连轧机需要采用快响应 、高精度和高可靠性 的
跟踪控制算法在材料成型工艺中的应用研究

跟踪控制算法在材料成型工艺中的应用研究材料成型工艺在现代工业生产中起着至关重要的作用,它涉及到各种材料的加工和成型过程。
而在这个过程中,精确的控制和跟踪是非常关键的,这就需要借助于跟踪控制算法的应用。
本文将探讨跟踪控制算法在材料成型工艺中的应用研究。
一、材料成型工艺的挑战材料成型工艺的复杂性和多变性给控制和跟踪带来了许多挑战。
首先,不同的材料在成型过程中会出现不同的物理变化,如熔化、固化、收缩等,这就需要根据具体的材料特性来设计相应的控制算法。
其次,材料成型工艺中的温度、压力等参数会不断变化,这就需要实时地对这些参数进行监测和调整。
此外,材料成型工艺中的形状和尺寸要求也非常高,因此需要精确地控制和跟踪成型过程中的形状和尺寸。
这些挑战都需要借助于跟踪控制算法来解决。
二、传统的控制算法的局限性在过去的几十年中,传统的控制算法在材料成型工艺中得到了广泛应用,如PID控制算法、模糊控制算法等。
然而,这些传统的控制算法存在一些局限性。
首先,它们往往是基于经验和规则的,对于复杂的材料成型过程很难进行精确的控制。
其次,它们对于材料成型过程中的非线性和时变性的处理能力有限。
此外,它们往往只能实现单目标的控制,无法同时实现多目标的控制。
因此,需要一种更加高效和精确的控制算法来解决这些问题。
三、跟踪控制算法的原理和应用跟踪控制算法是一种基于模型的控制算法,它通过建立材料成型过程的数学模型来实现对成型过程的控制和跟踪。
跟踪控制算法的主要原理是通过与实际成型过程进行比较,不断调整控制参数,使得模型输出与实际输出尽可能接近。
跟踪控制算法可以根据具体的需求和材料特性进行调整,可以实现对温度、压力、形状和尺寸等多个参数的控制和跟踪。
跟踪控制算法在材料成型工艺中的应用非常广泛。
例如,在注塑成型工艺中,通过跟踪控制算法可以实现对注塑温度和压力的精确控制,从而保证注塑成型的质量和形状。
在挤出成型工艺中,通过跟踪控制算法可以实现对挤出速度和温度的控制,从而保证挤出成型的尺寸和形状。
带材拉弯矫直过程中张力波动及打滑探讨

第19卷第4期V o l .19№41998青岛建筑工程学院学报 Jou rnal of Q ingdao In stitu te of A rch itectu re and Engineering带材拉弯矫直过程中张力波动及打滑探讨Ξ肖 林 杨成仁 刘琨明 苏逢荃(青岛建筑工程学院机械工程系,青岛266033)摘 要 对拉矫开始时带材延伸率的变化情况进行了分析,提出了延伸率过渡阶段和延伸率稳定阶段的概念,并指出在过渡阶段带材延伸率是变化的.根据过渡阶段带材延伸率变化的事实,分析了采用延伸率直接控制方式的拉矫机在起、制动阶段带材张力波动以及带材和张力辊之间打滑的原因,并提出了延伸率控制应遵循的原则.关键词 拉伸弯曲矫直机,拉伸弯曲矫直,控制,带材中图法分类号 T G 333.23在带钢的连续拉伸弯曲矫直中拉伸和弯曲是两个缺一不可的基本因素,带钢的拉伸弯曲矫直效果之所以比普通的辊式矫直要好其原因就在于对带钢施加了张力.从目前情况看,张应力的取值一般为(1 10~1 3)Ρs .在拉弯过程中带钢的张力应保持在某一值而且不变从而建立稳定的拉矫过程.但是,由于多种原因带钢的张力会产生波动,张力波动使张力辊传动装置承受动载荷而过早损坏.张力波动过大会使带钢在张力辊上打滑,带钢在张力辊上打滑会产生延伸率损失[1],带钢得不到应有的延伸.因此对带钢的张力波动进行分析和研究是非常必要的.图1 连续拉伸弯曲矫直机1,2,3,4为张力辊5,6,7为弯曲辊1 张力波动和打滑图1为一连续拉弯矫直机的示意图,1#辊和2#辊组成入口张力辊组,3#和4#组成出口张力辊组,bc 为弯曲段.带钢在张力辊上的打滑可分为弹性打滑(或隐性打滑)和整体打滑(显性打滑或摩擦滑动).弹性打滑是由于缠绕在张力辊上的带钢的不均匀弹性变形引起的.其特点是与张力辊接触的带钢上的不同的点相对于张力辊表面具有不同的相对速度,例如:在入口张力辊组中,a 点处带钢与张力辊表面之间的相对速度就大于f 点的相对速度.弹性打滑是不可避免的,它将使张力辊表面产生磨损.关于弹性打滑的情况和原因已有明确的阐述[1].本文主要对整体打滑进行讨论.Ξ冶金部有偿资助项目 收稿日期:1998-05-28由于多种原因,带钢的张力会产生变化,称为张力波动.张力的波动使张力辊传动装置过载或承受动载荷而提前损坏,某冷轧厂酸洗机组拉矫机的情况证明了这一点.设备的损坏会给生产带来很大的影响,造成很大的经济损失.当带钢两端的张力差大于带钢和辊子之间的摩擦力时,带钢和张力辊之间将产生打滑,如果不考虑带钢本身的弹性变形,整个带钢将以相同的相对速度相对于张力辊打滑,因此称为整体打滑.带钢的整体打滑将会产生延伸率损失,使带钢达不到理想的矫直效果.可见张力波动和带钢的整体打滑都是极其有害的.带钢的整体打滑是张力波动引起的,因而下面重点对张力波动进行分析2 延伸率的直接控制方式与张力波动2.1 延伸率和延伸率控制方式拉弯矫直机中最主要的工艺参数是带材的延伸率.可以把延伸率分为带材延伸率和设备延伸率.带材的实际延伸率称为带材延伸率.弯曲辊的压下量和张力的大小决定了带材延伸率.对于某一规格的金属带材只要控制了弯曲辊的压下量和带材张力就控制了延伸率,这种方式可称为延伸率间接控制方式.反之,也可以通过直接控制前后张力辊组的转速差来控制带材延伸率,可称之为延伸率直接控制方式.前后张力辊的相对转速差为∆e =(v 2-v 1) v 1×100◊.把∆e 称为设备延伸率,带材的实际延伸率用∆表示.应当注意的是:设备延伸率和带材延伸率这两者并不总是相等.如果带材在张力辊上打滑,带材延伸率将小于设备延伸率.2.2 带材延伸率的变化与张力辊转速调整在拉矫开始一小段时间内带材延伸率实际上是从小到大变化的(如图2所示),这一阶段为延伸率过渡阶段.过渡阶段后延伸率达到所希望的带材延伸率∆x ,为延伸率稳定阶段.图2 带钢上的应变分布假设带材所受张力为T ,并暂不考虑张力沿带材长度的变化,T 一般取值为1 10~1 3T s ,T s 是与屈服应力对应的张力.相应的张应力和应变分别为ΡT (一般为(1 10~1 3)Ρs )和ΕT ((1 10~1 3)Εs ),ΕT =ΡT E ,E 为带材的弹性模量.在图2中bc 段表示弯曲辊组的长度,带材在be 段经过拉伸和弯曲的联合作用后会产生弹塑性延伸,其纵向应变将从纯弹性应变ΕT 增加到所需要的带材延伸率∆x (可达到3◊左右).也就是说,如果带材上的某一物质单元在拉弯过程中从b 点走到e 点,那么它的纵向应变将从ΕT 增加到∆x .这一物质单元从e 点走到d 点其纵向应变保持∆x 不变.其应变变化情况见图2中的实线曲线.显然,只有当拉矫前原始位置在b 点的带材物质单元经历了从b 点到e 点的过程之后,带材延伸率才能达到所需要的带材延伸率∆x .此后的阶段为延伸率稳定阶段.此前的阶段为延伸率过渡阶段.延伸率过渡阶段时间t g 就是带材上的一物质单元从b 点走到e 点所用的时间.实际上图2中的实线曲线既是延伸率稳定阶段ad 之间带材上各点的纵向应变分布又是带材上一物质点从a 点走到d 点时此物质点处的带材应变变化情况.图2中的虚线曲线是带材刚开始拉矫时的情况,此时带材的张力刚建立起来.在刚开始拉矫时,除弯曲辊处小段长度外带材的绝大部分都没有经历塑性变形.24 青岛建筑工程学院学报 第19卷从图2可以看到:在刚开始拉矫时和在延伸率稳定阶段,ad 之间各点的纵向应变只是位置的函数,Ε=Ε(x ).但是,在延伸率过渡阶段,ad 之间不同的点具有不同的变形历史,例如:如果带材上的一个点在拉矫开始时处于m 点的位置,那么在过渡阶段其应变将沿曲线12345变化.所以在过渡阶段带材的纵向应变也与变形过程有关,即:Ε=Ε(x ,t ).在此用时间t 表示变形过程中的某一状态点而不是纯粹的时间.t 时刻ad 之间Ε(x ,t )的平均值就是此时刻的带材延伸率∆(t ).即:∆(t )=∫ ad Ε(x ,t )d x (1)图3 带钢延伸率的变化 图3是带材延伸率∆(t )的变化曲线示意图.在过渡阶段带材延伸率∆(t )从ΕT 到∆x 在延伸率稳定阶段(t ≥t g )∆(t )=∆x.了解带材延伸率的变化情况可以正确地控制设备延伸率∆e (前后张力辊组的转速差).在忽略弹性打滑的前提下,如果转速差∆e <∆(t )就达不到希望的矫直效果;如果∆e >∆(t )就会在带材中产生太大的张力,造成带材打滑或设备损坏.显然,应该有:∆e =∆(t )(2) 这一关系不仅应在带材延伸率稳定阶段满足,也应在过渡阶段满足.如果出口张力辊组的转速为n out ,入口张力辊组的转速为n in ,转速与带材延伸率之间应满足以下关系:n out -n in n out =∆(t )(3)式(3)整理后得:n in n out =1-∆(t )(4)式(3)或(4)对于所有的拉弯矫直机都是适用的.显然,应该按照公式(3)或(4)对前后张力辊组的转速进行调整以保证所需要的带材延伸率及正常的工作张力.在拉矫机的稳定运转阶段前后张力辊的转速一般满足公式(4).但是,应当注意的是,在拉矫机的加速和减速阶段前后张力辊的转速一般不满足公式(4).这将给带材矫直质量和设备带来严重的问题.2.3 延伸率直接控制方式与张力波动连续拉弯矫直机张力辊的驱动方式有以下几种:直流电机单独驱动、液压马达单独驱动、集体驱动、带差动机构的集体驱动、混合驱动等.对应于延伸率的2种控制方式,上述张力辊的5种驱动方式可归为2类:液压马达单独驱动是属于延伸率间接控制方式;直流电机单独驱动可以采用转速控制(即延伸率直接控制)也可以采用力矩控制(延伸率间接控制);其他都属于延伸率直接控制方式.对于延伸率间接控制方式,不存在设备延伸率和带材延伸率不相等的问题.在此主要对延伸率直接控制方式进行分析.2.3.1 集体驱动方式 在张力辊采用集体驱动方式的连续拉弯矫直机上,前后2个张力辊组之间采用变速齿轮箱连接以保证所需要的前后张力辊组之间的转速差,从而实现所需要的带材延伸率∆x .也就是说,一旦开始拉矫,前后张力辊组的速度差就想迫使带材的延伸率为∆x ,且∆x 的值远远大于正常情况下刚开始拉矫时的延伸率值ΕT .显然,在开始拉矫时如此大的速34第4期 肖 林等:带材拉弯矫直过程中张力波动及打滑探讨 度差必将在带材内引起很大的张力,按照∆x与ΕT的比例推算,此张力将达到正常工作张力的十几倍以上.当然,在张力还没有达到如此之大之前带材已经在张力辊上打滑.也可以如下表述:开始拉矫时前后张力辊组的速度差给带材施加了一个很大的载荷,此张力载荷大的足以使带材在张力辊上打滑.根据上面的分析,可以得出如下的结论:对于前后张力辊组采用集中驱动的拉弯矫直机,在延伸率过渡阶段必定会产生过大的带材张力,此张力会引起张力波动和带材在张力辊上打滑,使矫直机的运行状态不稳定.显然,前后张力辊组采用集中驱动的拉弯矫直机存在明显的先天缺陷.2.3.2 带差动机构的集体驱动方式 对于前后张力辊组采用差动装置的拉弯矫直机,前后张力辊组的转速差是由延伸率控制电机控制的.按照传动关系,有:n out=n i,n out-n in=n y i y(5)式中 n,i分别是主传动电机的转速和主传动电机到出口张力辊的速比;n y,i y分别是延伸率控制电机的转速和延伸率控制电机到入口张力辊的速比把公式(4)代入公式(5)并整理可得:n y n =i yi∆(t)(6) 在采用带差动机构的集体驱动方式的连续拉弯矫直机上,只要延伸率电机的转速与主传动电机转速保持公式(6)所确定的相互关系,就可以保证所需要的带材延伸率∆及正常的带材张力T.如果两个转速之间不保持上述关系(例如:延伸率电机的转速过小或过大)就不能保证所需要的带材延伸率或产生过大的张力.两者不协调的问题最可能发生在加速和减速阶段,在此阶段延伸率电机的转速和主传动电机的转速都处于变速过程,两者很难保持公式(6)所确定的相互关系.某冷轧厂酸洗机组拉弯矫直机的实际情况证明了这一点.“1#~4#辊传动系统中的悬臂齿轮箱,在升降速过程中,发现无规律不定期的抖动,抖动时,整个减速箱剧烈摇晃,且发出极大的撞击声,抖动的时间不长,一般在半分钟之内,至10秒种左右,有时抖动并不明显,但却能听到发自主减速箱内的齿轮撞击声。
拉弯矫直机工艺研究

拉弯矫直机的工艺研究摘要:本文简要介绍了国内某冷轧厂重卷机组拉弯矫机的构造,探讨了工艺参数的设置,优化了板型c翘的工艺参数。
关键词:拉弯矫直机工艺参数板型冷轧板带是钢铁工业的主要产品之一,它是汽车、家电、造船、航空航天等行业的重要原材料,其表面质量直接影响最终产品的质量和性能。
在板带制造过程中,由于原材料、轧制设备和加工工艺等诸多方面的原因,导致连铸板坯、热轧带钢和冷轧带钢表面出现裂纹、氧化皮、结疤、辊印、刮伤、孔洞、鳞皮、表皮分层、麻点、划伤和浪形等不同类型的缺陷[1],严重影响产品的使用,给下游企业带来了一定的经济损失。
对于冷轧产品,板型和划伤缺陷是必须预防的,一旦出现必须查找原因并及时作出解决方案。
基于此,本文对国内某冷轧厂重卷机组的关键技术进行了阐述,并就其在控制板型的过程进行了探讨,从而获得最佳的工艺参数。
1.拉弯矫直机构造拉弯矫直机本体由入、出口通带辊、两弯两矫的四个单元辊座、上辊座吊挂装置、隔离辊、下辊座压上装置、辊缝快速打开机构,换辊装置、机架等组成,如图1所示。
左右机架用横梁联接在一起,通带辊可上下移动,用于带材进出矫直机本体时导向和快速打开时引导带钢。
1#、2#弯曲单元、3#、4#矫直单元的下辊座分别由四对蜗轮蜗杆升降机构进行升降,通过工作辊来调节带钢变形量,蜗轮蜗杆由电机传动。
通过位移传感器检测调整量。
1#、2#弯曲单元各由上下辊系组成,各上辊系由工作辊、中间辊和分段支撑辊组成。
下辊系由工作辊、中间辊、分段支撑辊组成。
3#、4#矫直单元由上、下辊系组成,3#矫直单元上辊系及4#矫直单元的下辊系由工作辊、中间辊、分段支撑辊组成。
3#矫直单元下辊系及4#矫直单元上辊系由两个φ230的工作辊组成。
1#、2#弯曲单元和3#矫直单元之间分别有一个φ230的隔离辊,用于使带钢保持在同一平面,避免带钢正反弯曲曲率不同。
fig.1 substance diagram of withdrawal straightening stands fig.2 substance diagram of plate strip2.拉弯矫直机工艺参数通过对上述拉弯矫直机的阐述,可以将其简化为三个部分,一部分是弯曲,经过塑性延伸产生均匀弯曲的弯曲辊系;一部分是矫直,消除浪形、c翘和l翘的矫直辊系;最后一部分是提供塑性变形张力的张力辊系。
重卷的CU320-2DP

总结
1#和2#拉矫线有四个CU320-2DP控制单元,分布在三个传动柜(G05、G07、G09)和圆盘剪操作台。
G05柜内的CU320-2DP控制单元主要用于收卷电机风机、S4.1电机风机、圆盘剪操作侧电机风机、圆盘剪传动侧电机风机、废边电机风机的控制及反馈;G07柜中的CU320-2DP控制单元用于入口夹送电机风机、出口夹送电机风机、S3.1电机风机、S3.2电机风机、检查站夹送电机风机的控制及反馈;G09中的CU320-2DP控制单元用于S2.1电机风机、S2.2电机风机、S1.2电机风机、开卷电机风机的控制及反馈;圆盘剪操作台的CU320-2DP控制单元用于开口度的最大最小位、操作侧的侧间隙大小、传动侧侧间隙的大小、废边卷取工作位、废边卷取打开位、推料板低位、最大卷径位、排料机构大小的限位。
3#重卷线有三个CU320-2DP控制单元,分布在两个逆变柜当中(G05、G06,其中G06柜内有两个)。
G05逆变柜中的CU320-2DP控制单元用于开卷风机、开卷抱闸、废边卷风机的控制;G06逆变柜中的第一个CU320-2DP控制单元用于卷取风机、卷曲抱闸、操作侧主电机风机、传动侧主电机风机的控制;G06逆变柜中的第二个CU320-2DP控制单元作为备用。
1#线出口操作台的高速计数器测带钢长度的原理为:脉冲增量编码器通过软连接与电机轴相连,电机轴旋转一周编码器输出的脉冲数是固定值设为A,计数器统计的总脉冲数N除以A得到电机轴旋转的圈数B。
而B与夹送辊旋转的圈数成正比例故可以依据B求得出口夹送辊旋转的圈数C。
而夹送辊的周长是固定值设为D,则带钢的长度L=D*C。
组态两个S7-300站以太网通讯时,需要在每个S7-300Z站的硬件配置中插入CP模块,且站间网络地址不能冲突。
一种拉矫机参数集成控制系统与方法
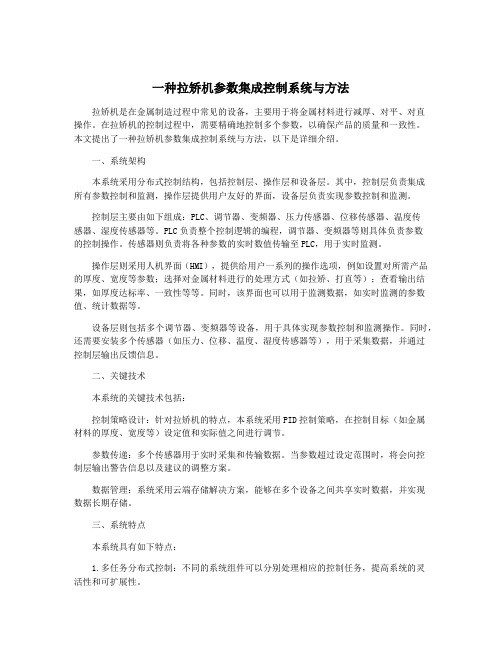
一种拉矫机参数集成控制系统与方法拉矫机是在金属制造过程中常见的设备,主要用于将金属材料进行减厚、对平、对直操作。
在拉矫机的控制过程中,需要精确地控制多个参数,以确保产品的质量和一致性。
本文提出了一种拉矫机参数集成控制系统与方法,以下是详细介绍。
一、系统架构本系统采用分布式控制结构,包括控制层、操作层和设备层。
其中,控制层负责集成所有参数控制和监测,操作层提供用户友好的界面,设备层负责实现参数控制和监测。
控制层主要由如下组成:PLC、调节器、变频器、压力传感器、位移传感器、温度传感器、湿度传感器等。
PLC负责整个控制逻辑的编程,调节器、变频器等则具体负责参数的控制操作。
传感器则负责将各种参数的实时数值传输至PLC,用于实时监测。
操作层则采用人机界面(HMI),提供给用户一系列的操作选项,例如设置对所需产品的厚度、宽度等参数;选择对金属材料进行的处理方式(如拉矫、打直等);查看输出结果,如厚度达标率、一致性等等。
同时,该界面也可以用于监测数据,如实时监测的参数值、统计数据等。
设备层则包括多个调节器、变频器等设备,用于具体实现参数控制和监测操作。
同时,还需要安装多个传感器(如压力、位移、温度、湿度传感器等),用于采集数据,并通过控制层输出反馈信息。
二、关键技术本系统的关键技术包括:控制策略设计:针对拉矫机的特点,本系统采用PID控制策略,在控制目标(如金属材料的厚度、宽度等)设定值和实际值之间进行调节。
参数传递:多个传感器用于实时采集和传输数据。
当参数超过设定范围时,将会向控制层输出警告信息以及建议的调整方案。
数据管理:系统采用云端存储解决方案,能够在多个设备之间共享实时数据,并实现数据长期存储。
三、系统特点本系统具有如下特点:1.多任务分布式控制:不同的系统组件可以分别处理相应的控制任务,提高系统的灵活性和可扩展性。
2.快速响应:系统实现了实时监测和控制参数的能力,确保快速响应异常情况。
3. 数据可视化:操作层提供用户友好的界面,用于对数据的实时监测和管理。
热轧卷取机控制对跟踪技术的运用

宏 跟 踪 主 要 是 允 许 在卷 取 区 内要 存 在有2 块 带钢 ,才能 在 理论 上 达到 最快 的 生 产 速度 。微 跟 踪 这种 方 法主 要是 针 对4 种 主 要 的卷 径 的计 算方 法 ,并 且 通 过 比 较和分析卷径的主要的计算方法 ,获得 项最佳 的结果。同时为了有效 的提高 热轧卷机的跟踪的精确度 ,采取 的主要 方法是 ,校验前滑率 ,并且在实 际的例 子 中取得 了比较 好 的应用 效果 。 热轧 卷 取机 的跟踪 技术 跟踪技术主要指 的是 ,热轧机的一 项 自动 化 的控 制技 术 ,同时 也 是 更 好 的 完 成 卷 取 机 的 控制 功 能 的最 关 键 的一 项 技 术 。 卷 取机 具 有 众 多 的功 能 ,包 括 对 速度的控 制功 能 ,张力与压力的控制功 能。这项 控制 功能都与跟踪信号有着极 其 密 切 的关 系 。在 进 行 一 个 热 轧 卷 取 机 的 生 产过 程 中 ,要 允 许 在 卷 取 机 的 入 口 之间,存在2 块带钢,只有实施了一项完 善并且 十分可靠 的跟踪策略之后 ,才能 在最 大 的 限度 上 ,发 挥 出生 产 节 奏 的潜 能。
1 校 验前 滑率 对尾部实施 跟踪策略 ,实施定位功 能 ,却 很难 对 卷 取 机 中 的每 一 卷 都 能 准 确 的 实 施定 位 。在 运 用 积 分 法 对 尾 部 的 相关部位 ,进行位置跟踪 的时候 ,因为 尾部的速度发生波动 ,影响到卷取机的 计算的精确度 。因此应该尽量的减小在 尾 部定 位 阶段 卷 取 机 的速 度 。 由于 尾部 的 不平 滑带 来 一 定 的计 算 误 差 ,因 此应 该 采用 二 次 减 速 进 行 设 定 。当 带尾 距 离 卷 取机 的距 离 为 L 1 的 时候 ,应 该启 动一 次 带钢 ,来 进 行 减 速 。把 卷 取 的 速度 减 到一定 的平 台的速 度 。 2冷金 属检 测器 的选 用与 维护 冷 金 属 检 测 器 是 造 成 跟踪 失败 的一 个最 主要 的原 因,尤其是对于卷取 区域 来说 ,应该采用冷金属双备份 配置 ,来 增加感应 的面积 ,用来检测待钢头尾部 十分 不 规 则 的部 分 。 除此 之外 ,还 能 加 快 响应 的速 度 。 为 了 相应 的减 少 轧 钢 过 程 中产生的过多的水 汽干扰 ,就必须要 在检测器上安装强力风机进行吹扫 。 3咬钢信号丢失的补救措施 很有可能因为某 种原 因,精轧机咬 钢信号并没有及 时的传送 到卷取 区的控 制器当 中,容易造成卷取机并没有选 中 造成堆钢的现象 。为有效 的避免这种事 故 的发生 ,可以通过采集精轧机后的高 温计信号作为精 轧机 咬钢信号 的补充。 在 经 过 检测 器 的 时候 ,要 及 时 的选 取 卷 取机 ,用来保证生产 的连续性 。尤其是 试 生 产 的初 期 ,曾经 发 生 过 因 为 咬 钢信 号的丢失 ,引起 的堆钢事故。通过采用 检测器信号进行有效 的补偿之后 ,才从 根本上杜绝 了因为发生咬钢信号丢失造 成堆 钢事 故 的发生 。 4卷径 的计 算方 法 因此 在 一 项 工 程 的运 用 中 ,主要 采 用 了4 种方法 ,对卷径计算 ,再通过 比较 分 析 的方 法 ,获 得 一 项 最 佳结 果 。首 先 是 通 过 进 入 到 卷 取 机 中 的 带钢 的长 度 , 来 计 算 卷 径 。根 据一 项未 跟 踪 之 后 ,得 到 带 头 的 位 置 。 然后 才 能 获 得 带 钢 进 到 卷取机的长度 ,再根据带钢 的厚度 ,计 算出钢卷的外径 。这种方法 ,能够在一
冷轧重卷拉矫控制系统自主开发及应用

输 出侧通过不同规格逆变器连接 至各设备
电机 ,逆 变器 用 于将 直 流 电逆 变 为一 定 频 率 的 交 流 电 ,驱动 相 应 电机 。逆变 器 直 流 侧 设 置 电 容 ,用 于储 存 直 流 电能 ,并 通过 快 熔 连 接 到 直 流母 线 。 由 于 电机 距 离 逆 变 器较 近 ,逆 变 器 输 出侧不 设 置输 出 电抗 器 。 公 共 直 流 母 线 为各 逆 变 器 提 供 适 当等 级 的 直 流 电压 。 逆变 器 工 作 于 电动状 态 时 ,电能 从 直 流母 线 逆变 后 输 出到 电机 ;逆 变 器 工 作 与 制
此 外 ,为 防止 大 容 量 逆 变 器 中 间直 流 快 熔 熔 断浪 涌 对 小 容 量 逆变 器 的影 响 ,设 备 并 柜 时 要 考 虑将 容量 相 当 的逆 变 器就 近排 放 ,并 在 大 、 小 容 量 逆 变 器 问 直 流母 线 加 装 白振荡 吸 收二 极 管。
过接触器合分 闸 ,并设置快熔保护 。为防止变
频 系 统 对 动 力 电 网 的谐 波 干 扰 ,进 线 侧 还 配 置
E MC滤 波器 。
要保证带钢静止状态下转 矩控制 与速度 控
制 的精 度 ,除 上卷 小 车 、卸 卷 小 车 外 ,各设 备
均需 设 置 测 速 码 盘 ,采 取 闭 环矢 量 控 制 方 式 。
自主开 发设 计 了一 级和二 级 控制 系统 。
P L C选用 西 门子 S 7 — 4 0 0系列 ,S 7 — 4 0 0是 具
有 中高档 性 能 的 P L C,采 用 模 块化 无 风 扇设 计 , 适 用 于 对 可 靠 性 要 求 极 高 的 大 型 复 杂 的 控 制 系 统 ,机组 的顺 序控 制 部分 由 C P U 4 1 4 — 2 D P完成 ,
拉弯矫直技术在高精度铝板带材生产中的应用

一般来说高精度铝板带材产品的平直度可谓体现产品质量 的关键指标其重要性是毋庸置疑的 尽管进行热轧冷轧生产时 利用了不同板形管控工艺然而目前在包装与印刷以及建筑等不 同行业当中均提高了铝板带材的平直度标准仅仅借助从前的 方式难以达到高精度产品的需要 所以当轧制以后需要运用拉 弯矫直技术使铝板带材相应的平直度得以提升
一拉弯矫直机运作机制和应用成效 铝板带材是生产过程中缺陷的形成问题 从根本上来说因 为铝板带材的宽度方向会受到各种不一样的内应力作用让其朝 着宽度的方向与纵向纤维间形成了一定的长度差值 为了提高铝 板带材的平整度应该在铝板带材的长度方向上面施加大于相应 的材料屈服极限的应力作用让长短纤维一起形成塑性变形的 现象当应力出现松弛的情况之后相应延伸的纤维会得以有效 保留让铝板带材在纵向上的长度与内应力近似保持相同的方 向 完 成 矫 平 的 任 务 !"# 对于拉弯矫直机而言以有关材料自身的弹塑性延伸理论当 作依据可以实现矫平铝板带材 具体的原理是待矫平的铝板带 材受到由张力辊组施加的张力作用之后借助上下交替布设的多 组较小直径的弯曲辊基于拉伸与弯曲共同影响之下在长度的 方向上形成了一定的塑性纵向延伸现象进而使铝板带材当中的 纵向内应力布设的不均匀性变小达到了对铝板带材平直度优化 的目的 鉴于铝板带材不算最佳的弹塑型材料所以拉弯矫直的矫 直成效和铝板带材最初的板形与硬化模量太小情况密切关联 一 般而言硬化模量较小的材料非常易于矫平 通过拉弯矫直处理 后铝板带材的板形得到一定优化不过彻底去除之前的板形缺 陷 是 不 可 能 的 难 以 得 到 最 佳 的 平 直 度 !$# 二铝板带材缺陷的形成和危害 当铝板带材进行轧制的时候其轧辊的辊缝外形将被诸多不 同因素所干扰比如常见的轧辊产生了弹性变形不均匀磨损等 情况导致辊型和辊缝的外形均产生了相应的变化造成铝板带 材在宽度的方向出现了延伸不均匀的现象也让纵向纤维在长度 方向出现了相应的长度差值形成铝板带材的板形缺陷问题 具 体包含了双边单边中间以及翘曲等不同的缺陷 通常情况下铝板带材板形缺陷的形成既带给所生产产品 的平直度严重的不良影响 也降低了轧制生产过程当中的稳定 性 所以进行轧制的时候应该科学管控铝板的板形 基于对铝 板板形缺陷问题解决的目的很多国家均加快了对辊缝控制技术 的研发和应用速度 比如进行轧机使用的过程中借助轧辊倾斜 调控液压弯辊以及轧辊分段冷却等不同的处理方式与此同时 可以利用铝板带材板形自动管控系统完成在线检测与闭环管控 的任务以便获得更好的生产成效 鉴于铝板带材的板形受到诸 多 因 素 的 干 扰 导 致 板 形 的 缺 陷 依 然 难 以 彻 底 管 控 !%# 三拉弯矫直技术在高精度铝板带材生产当中的应用措施
冷轧生产:拉矫模拟操作手册

1拉矫1.1功能介绍拉矫机对带钢进行预破鳞和改善板形,为带钢酸洗及切边提供良好条件。
1.2监控画面拉矫监控画面如下:拉矫监控画面1.2.1监控内容拉矫画面中的监控内容有:1.2.2操控内容辅助操作台和拉矫操作台如下所示:1.拉矫准备:1)调用并下达工艺参数;【调用工艺参数】后,需要观察各设定值(蓝底)是否合理,如超出正常范围,需修改后在进行【下达工艺参数】,否则会提示错误。
正确设定值参考下表:2)辅助操作台中【吹扫装置】-【投入】,【除尘装置】-【投入】,【1#焊缝检测装置】-【投入】,【2#张力辊】-【投入】,【2#张力辊压辊】-【抬起】,【2#测张辊】-【投入】,【1#弯曲辊】-【使能】,【2#弯曲辊】-【使能】,【矫直辊】-【使能】,【3#张力辊】-【投入】,【3#测张辊】-【投入】,【3#张力辊压辊】-【抬起】;3)入口液压站就绪(入口段共用);4)拉矫机稀油润滑站就绪;5)以上准备条件满足后,【就绪】指示灯亮起,表示准备工作完成。
2.拉矫自动模式:1)将【模式选择】切到【自动】;2)点击【自动启动】,在系统的控制下自动完成全部拉矫操作。
2.拉矫手动模式:1)将【控制模式】切到【手动】;2)点击【手动启动】,带钢向前运动,开始拉矫操作;3)焊缝到达拉矫机前时,依次点击【1#弯曲辊】-【抬起】、【2#弯曲辊】-【抬起】、【矫直辊】-【抬起】,避开焊缝;4)待焊缝通过后,依次点击【1#弯曲辊】-【压下】、【2#弯曲辊】-【压下】、【矫直辊】-【压下】;1.3拉矫机稀油润滑站拉矫机稀油润滑站用于为拉矫机区域各设备提供稀油润滑。
1.3.1监控画面润滑站监控画面包括:1.调节元器件a)冷却器和循环泵:降低油箱中润滑油温度。
b)电加热器:升高油箱中润滑油温度。
c)注油阀:向油箱注入润滑油,提高液位。
d)抽油阀:从油箱中抽出润滑油,降低液位。
e)主油泵:为润滑控制系统提供合格压力和流量的润滑油。
2.目标控制元器件a)油箱:控制要求包括如下i.温度:温度正常值为40~50°C。
最新带材跟踪控制在拉矫重卷中的应用

带材跟踪控制在拉矫重卷中的应用带材跟踪控制在拉矫重卷中的应用关键词:带材跟踪光电开关编码器二级控制系统冷轧拉矫机组生产线相对较长,进行新带卷穿带时带钢从开卷机到卷取机需耗时30分钟左右。
本机组增设了电焊机与活套,生产同规带钢时只需穿带一次,利用电焊机作用将前后带钢的带头带尾焊到一块,从而节约生产时间,提供生产效率。
如何确定不同卷的带钢在生产线上的情况,从而进行控制,带材跟踪系统便解决了这个问题。
拉矫机组带材跟踪分一级系统(现场硬件检测)和二级系统(带材的数据的管理)两部分。
两者在一级计算机和二级计算机中分别进行,但都以一级系统的位置跟踪结果为基础。
一级系统的微跟踪是对生产线各带材的位置及其状态进行跟踪。
二级系统的宏观跟踪是对各带材的数据进行跟踪以使带材和数据互相对应。
一级计算机和二级计算机数据交换通过以太网完成。
一、拉矫机组现场设备及检测元件安装情况介绍图1所示为拉矫机组现场设备布置图,图中机械设备(带英文标识)从右向左依次为:开卷机、开头机(由伸缩刮板、夹送辊、弯曲辊组成)、切头剪、1#夹送辊、立导辊、电焊机、月牙剪、2#夹送辊、1#张力辊组(由1#-4#张力辊组成)、矫直机、2#张力辊组(由5#-8#张力辊组成)、活套、3#张力辊组(由9#、10#张力辊组成)、纠偏辊、圆盘剪、检查台、3#夹送辊、涂油机、切尾剪、出口转向辊、卷取机。
为了更好的进行带材跟踪、带长测量,现场设备上安装了许多光电开关、光电编码器。
开头机的弯曲辊由上下两辊组成,弯曲辊上辊轴端安装有一台光电编码器用于开卷卷径计算和进行自动定尺切头、切尾控制时的定长送料检测。
入口张力辊组由1#-4#张力辊组组成。
1#张力辊上安装一台光电编码器,用于焊缝跟踪控制。
矫直机前装有光电开关,用于检测焊缝,参与控制矫直辊系打开。
圆盘剪前安装有检测装置支架。
支架上安装有光电开关,用于检测焊缝,并由编码器配合控制,使焊缝准确停在圆盘剪处。
出口转向辊为单辊结构的空转辊,轴端安装有一个光电编码器,用于测量机组线速度和计量卷曲长度。
拉矫重卷机组用途及工艺

拉矫重卷机组用途及工艺本拉矫重卷机组用于将冷轧带卷经拉伸弯曲矫直、切边后进行分卷。
生产工艺简述该机组的来料带卷由车间的天车吊运到机组前部的来料存料台架上, 存料台带有带卷检测传感器。
采用手动上卷或自动上卷的方式,上卷小车手动横移到存料台带卷的下方,将带卷托起并横移,在带卷进入卷筒之前,由人工目测操作小车的鞍座升降,使带卷的中心在高度方向对准开卷机卷筒中心。
高度方向对准后,小车继续横移,根据开卷机卷筒上的标尺和人工目测进行操作控制使带卷基本上对准机组中心线,将带卷套到开卷机的卷筒上。
或高度方向、水平方向自动定位,高度方向由激光测距传感器检测带卷与传感器距离,并计算卷径,卷材宽度由光电开关和光电编码器检测,按自动上卷方式完成上卷过程。
轴头支撑抬起支撑卷筒,小车的鞍座下降,同时开卷机卷筒涨径再将压辊压下,小车退回。
上卷完成。
开头时,先将带头旋转到合适位置,由人工在开卷机后侧将带卷上的捆扎带剪断。
开头机的刮板摆起伸出至工作位置。
点动开卷机,让带卷转动,使带头打开并沿着开头矫直机的刮板前进进入开头矫直机的夹送辊,夹送辊的上辊压下夹住带材。
开头机的刮板缩回摆下。
点动开卷机和开头机,使带材继续前进,经过五辊矫直机的直头后,带材头部进入切头剪。
完成带卷的开头。
CPC系统投入工作。
开头机与开卷机间张力开卷。
切头时,首先将切头剪后的摆动导板台摆起。
开头机、五辊矫直机向前送料,带头进入切头剪,送料停止。
切头剪进行剪切,将带头切断。
切下的废带头掉入废料小车。
根据需要重复该过程,完成带材的切头。
或设定剪切长度,自动切头。
带材继续向前送进,人工辅助带头经过焊机。
当带头通过1# 张力辊后,1#压辊压下,继续向前送料,带头依次通过2#、3#、4#张力辊后,2#压辊压下,1#、2#、3#、4#张力辊与前面设备一起继续向前送带,使带材通过矫直机本体,并通过5#、6#、7#、8#张力辊后,3#、4#压辊压下;5#、6#、7#、8#张力辊与前段设备一起联动送料。
- 1、下载文档前请自行甄别文档内容的完整性,平台不提供额外的编辑、内容补充、找答案等附加服务。
- 2、"仅部分预览"的文档,不可在线预览部分如存在完整性等问题,可反馈申请退款(可完整预览的文档不适用该条件!)。
- 3、如文档侵犯您的权益,请联系客服反馈,我们会尽快为您处理(人工客服工作时间:9:00-18:30)。
带材跟踪控制在拉矫重卷中的应用
摘要:本文结合对莱钢冷轧拉矫机组调试、维护,着重介绍了带材跟踪系统在拉矫机组中的应用。
关键词:带材跟踪光电开关编码器二级控制系统
冷轧拉矫机组生产线相对较长,进行新带卷穿带时带钢从开卷机到卷取机需耗时30分钟左右。
本机组增设了电焊机与活套,生产同规带钢时只需穿带一次,利用电焊机作用将前后带钢的带头带尾焊到一块,从而节约生产时间,提供生产效率。
如何确定不同卷的带钢在生产线上的情况,从而进行控制,带材跟踪系统便解决了这个问题。
拉矫机组带材跟踪分一级系统(现场硬件检测)和二级系统(带材的数据的管理)两部分。
两者在一级计算机和二级计算机中分别进行,但都以一级系统的位置跟踪结果为基础。
一级系统的微跟踪是对生产线各带材的位置及其状态进行跟踪。
二级系统的宏观跟踪是对各带材的数据进行跟踪以使带材和数据互相对应。
一级计算机和二级计算机数据交换通过以太网完成。
1拉矫机组现场设备及检测元件安装情况介绍
图1所示为拉矫机组现场设备布置图,图中机械设备(带英文标识)从右向左依次为:开卷机、开头机(由伸缩刮板、夹送辊、弯曲辊组成)、切头剪、1#夹送辊、立导辊、电焊机、月牙剪、2#夹送辊、1#张力辊组(由1#-4#张力辊组成)、矫直机、2#张力辊组(由5#-8#张力辊组成)、活套、3#张力辊组(由9#、10#张力辊组成)、纠偏辊、圆盘剪、检查台、3#夹送辊、涂油机、切尾剪、出口转向辊、卷取机。
图1拉矫机组机械布置图
为了更好的进行带材跟踪、带长测量,现场设备上安装了许多光电开关、光电编码器。
开头机的弯曲辊由上下两辊组成,弯曲辊上辊轴端安装有一台光电编码器用于开卷卷径计算和进行自动定尺切头、切尾控制时的定长送料检测。
入口张力辊组由1#-4#张力辊组组成。
1#张力辊上安装一台光电编码器,用于焊缝跟踪控制。
矫直机前装有光电开关,用于检测焊缝,参与控制矫直辊系打开。
圆盘剪前安装有检测装置支架。
支架上安装有光电开关,用于检测焊缝,并由编码器配合控制,使焊缝准确停在圆盘剪处。
出口转向辊为单辊结构的空转辊,轴端安装有一个光电编码器,用于测量机组线速度和计量卷曲长度。
2 二级控制系统
二级系统主要完成以下功能:
(1)检测并判断跟踪传感器的状态变化(2) 生产数据管理(3) 根据标志在生产区域生成跟踪,并读取数据(4)根据跟踪传感器的状态变化,实时更新人机界面(HMI)上的跟踪信息。
为了保证带材的实际位置与跟踪信号一致,在跟踪程序中通过设置感应时间间隔,来保证跟踪信号的准确性。
此外,操作人员可根据根据带材的实际位置及时进行修正,最大限度地避免因跟踪信号错误造成的控制混乱。
操作人员可以通过人机界面(HMI)实时监控和修正带材跟踪。
3 带材跟踪控制功能介绍
3.1开卷机区域
在待卷区域1#、2#鞍座边上均装有光电开关,一旦带钢被吊装到相应的鞍座上后,光电开关发送信号到PLC,HMI画面上有相关显示,带卷(On saddles)位置(EN. 1 saddle 1/ EN. 1 saddle 2/)。
经操作工按生产计划对带卷进行生产确认后(confirmed),操作工可通过人工上卷或自动上卷方式新卷带钢上到开卷机,PLC接到开卷机卷筒涨径,活动支撑闭合信号后,程序确认带钢位置,监控画面上有相关显示。
3.2 焊接操作
带卷带头已经开头夹送辊、五辊矫直机送到焊机入口,并调整好带头在焊机中的位置。
前一只带卷带尾与后一只带卷的带头已位于焊机中,操作工操作电焊机进行焊接工作。
焊接过程由焊机自动完成对带头、剪切、焊接等工作。
焊接完成后,电焊机的打孔装置会在焊缝前面2cm住中间位置打一直径为3cm的圆孔,便于后面设备安装的光电开关进行焊缝检测工作。
3.3 过焊缝时的穿带操作
带材跟踪的最主要的作用就是完成焊缝跟踪。
焊接完成后,运用矫直段“联合点动”功能,将1#夹送辊与1#张力辊之间
形成的活套拉平。
开头夹送辊、五辊矫直机、1#夹送辊上辊打开退出工作,开卷机加载张力,机组全部设备进入联动状态低速运行,进入过焊缝穿带工作状态。
运行过程中延伸率设定为零,入口、出口张力辊之间保持微张力。
1#张力辊上的光电编码器检测跟踪焊缝位置。
焊缝到达月牙剪位置时停止,月牙剪剪切完成后机组继续低速运行,焊缝到达矫直机入口时,焊缝检测光电开关发讯,矫直机辊系快速打开,焊缝通过矫直机后辊系再快速闭合。
焊缝到达圆盘剪,焊缝检测光电开关发讯,由编码器检测、控制使焊缝准确停止在圆盘剪处,此时操作工可进行圆盘剪的调整操作和更换剪刃的操作。
当焊缝到达分切剪时穿带过程结束。
3.4 卷取机区域
当焊缝到达分切剪时,操作工操作分切剪剪掉焊缝,然后根据卷取机选择用钳口工作还是使用助卷器工作,进行分切后的再穿带操作。
当卷取机卷取带钢2~3圈后,画面上会显示带卷状态情况。
当卷取机卷取长度或卷取重量后,机组进行分卷操作,再进行卸卷操作。
卸卷完成后,画面上显示带卷状态。
结束语
当带材跟踪出现异常时,会影响其他与跟踪信号相关的功能程序。
例如自动减速控制、剪刀剪切长度控制、分切收尾控制等。
带材跟踪系统在莱钢冷轧拉矫机组应用以来,曾发生由于现场检测元件损坏,影响了分切收尾操作的事件,这就要求加强对传感器的日常维护和预防性检修工作。
总体而言,带材跟踪控制系统完全满足了拉矫机组的生产要求。
参考文献
郑申白,曾庆亮.轧制过程自动化基础[M].北京:冶金工业出版社,2005,P131~P135
注:文章内所有公式及图表请以PDF形式查看。