零件折弯干涉问题分析与举措研究
折弯加工问题

解决方法:不要随意调整中间板,用百分表对中间板 和下台面之间的距离进行调整。
加工角度不良
产品加工的角度左右角度不一致
原因5:折弯加工的时候在机床的两侧加工,造成 偏载加工。
解决方法:RG系列不具备偏载加工能力,偏载加工 会损坏机床请在机床的中心加工产品。对于具有偏载 加工能力的机床如HDS,FBDIII,HFE,等调整左右2 个D轴的参数来进行加工。
解决方法:将后定位拉开,测量实际的误差在机器 内部参数中进行补正。 后定位基准确认 原因4:一些细长的材料在加工(激光切割,剪切)中会变形 呈中间突起的扇型,影响加工精度。 解决方法:改变材料的加工工艺减小变形,对加工后 的零件进行整形,缩短2个后定位之间的距离 以减小误差 材料中间突起
在加工的时候用到后定位后拉的时候后来的位置点 的确认很重要,如果后拉点位置设定太浅,模具没有 压住材料后定位后来以后材料可能移动,造成折弯 尺寸不准 后定位后拉位置点的确认
左右尺寸不一致
下模肩R磨损 原因1:部分模具磨损后造成一条折弯线上的内R 不一致导致折弯延伸率不一致使得尺寸出现偏差 解决方法:对模具进行研磨修正
上模尖端磨损
原因2:模具对芯不正确使得下模没有和后定位平行 导致尺寸出现偏差
解决方法:重新进行模具对芯工作
左右尺寸不一致
原因3:在长期的使用中后定位在意外撞击, 自然变形的影响下会有部分倾斜
解决方法:重新安装模具并对芯
加工角度不良
产品加工的角度左右角度不一致
原因3:机器本体倾斜,造成加工角度不一致
解决方法:对机器的水平进行调整
原因4:机器在出厂和安装调试的时候中间板和下工 作台面之间的距离被调整在一个标准值上。所以每块 中间板的高度都有所不同。但在长期使用过程中,用户 拆装中间板,中间板本身的变形使得下工作台面之间 的距离发生了变化,使得加工角度不一致
折弯是的干涉现象

折弯是的干涉现象
对于二次折弯以上的折弯,精心行出现折弯工件与刀具相碰出现干涉,如图所示,黑色部分为干涉部分,这样就无法完成折弯,或者因为折弯干涉而导致折弯变形,钣金折弯的干涉问题,不涉及到太多的技术,只要了解一下折弯的形状和尺寸,在结构设计时避开折弯模就可以了。
对于翻孔攻丝来说,D值不能设计的太小,最小的D值可以根据材料厚度,翻孔外径,翻孔高度,所选折弯高的等参数计算,或者作图得到
在设计弯曲零件时,如果弯曲边需将弯边弯曲到毛边内侧时,一般应在事先在落料后加冲工艺孔,工艺槽,或者工艺缺口。
止裂槽或者切口,对于一条边的一部分折弯,为了避免撕裂和畸变,应开止裂槽或者缺口,特别是内弯角小于六十度的弯曲,更需要开止裂槽或者缺口,切口宽的一般大于板厚T,切口深度一般大于1.5T。
工艺槽工艺孔要正确处理,面板及工件能看得到的工件,可不加折弯拼角工艺孔,(如面板在加工过程中,为保持统一风格,均不设工艺缺口)其他应加折弯拼角工艺孔。
九十度方向的折弯搭碰的间隙规定
图纸设计时,对于没有特殊要求,不要标注九十度方向的折弯搭碰之间的间隙,一些不合理的间隙标注,反而影响加工厂家的工艺设计,加工厂家一般按照0.2~0.3的间隙进行设计。
突变位置的折弯
折弯件的折弯区应避开零件的突变位置,折弯线离变形区的距离L应大于弯曲半径R,即L≥R
一次压死边
一次压死边的方法,先用九十度折弯刀将板材折弯成三十度,再将折弯边压平,图中最小折弯边尺寸为零点五T其中t为材料厚度,压死边一般适用于板材为不锈钢板,镀锌板,覆铝锌板等。
电镀件不宜采用,因为压死边的地方会有夹酸液的现象。
一百八十度折弯
方法:先用三十度折弯刀折成三十度工件。
再将折弯边压平,压平后抽出垫板。
折弯常见问题及处理方法

折弯常见问题及处理方法一﹐折床加工内容1﹐L折按角度分为90˚折和非90˚折。
按加工分一般加工(L>V/2) 和特殊加工(L<V/2) 。
1>﹐模具依材质﹐板厚﹐成形角度来选。
2>﹐靠位原则1)以两个后定规靠位为原则﹐并以工件外形定位。
2)一个后定规靠位时﹐注意偏斜﹐要求与工件折弯尺寸在同一中心在线。
3)小折折弯时﹐反靠位加工为佳。
4)以靠后定规中间偏下为佳。
(靠位时后定规不易翘起)5)靠位边以离后定规近则为佳。
6)以长边靠位为佳。
7)以治具辅助靠位(斜边不规则靠位) 。
8)3>﹐注意事项1)要注意加工时的靠位方式和在各种靠位加工方式中后定规的运动方式。
模具正装时折弯﹐后定规要后拉﹐以防止工件在折弯时变形。
大工件内部折弯时﹐因工件外形较大﹐而折弯区较小﹐使刀具和折弯区难以重合﹐造成工件定位难﹐或折弯工件损坏。
为避免以上情况发生﹐可在加工的纵方向加一定位点﹐这样由两个方向定位加工﹐使加工定位方便﹐并提高加工安全性﹐避免工件损坏,提升生产效效率。
2﹐N折N折要根据形状不同采用不同的加工方式。
折弯时﹐其料内尺寸要大于4MM并且X尺寸的大小因模具外形而受到限制。
如果料内尺寸小于4MM﹐则采用特殊方法加工。
1>﹐根据料厚﹐尺寸﹐材质及折弯角度来选模。
2>﹐靠位原则保证工件不与刀具发生干涉1)保证靠位角度略小于90度。
2)最好用两个后定规靠位﹐特殊情况除外。
3>﹐注意事项1)折弯L折后﹐期角度要保证在90度或略小于90度﹐以方便加工靠位。
2)第二折加工时﹐要求靠位位置以加工面为中心来靠位。
3﹐Z折又称之为段差﹐即一正一反之折弯。
根据角度分斜边段差和直边段差。
折弯加工的最小尺寸是加工模具限制的﹐最大加工尺寸是由加工机台的外形决定的。
一般情况下﹐Z折的料内尺寸小于3.5T时﹐采用段差模加工。
大于3.5T时﹐则采用正常加工方法。
1>﹐靠位原则1)靠位方便﹐稳定性好。
钣金件折弯中常见问题及处理办法【干货】

钣金件折弯中常见问题及处理办法【干货】内容来源网络,由“深圳机械展(11万㎡,1100多家展商,超10万观众)”收集整理!更多cnc加工中心、车铣磨钻床、线切割、数控刀具工具、自动化、数字无人工厂、精密测量、3D打印、激光切割、钣金冲压折弯、精密零件加工等展示,就在深圳机械展.常用折弯模具常用折弯模具,如下图。
为了延长模具的寿命,零件设计时,尽可能采用圆角。
过小的弯边高度,即使用折弯模具也不利于成形,一般弯边高度L≥3t(包括壁厚)。
台阶的加工处理办法一些高度较低的钣金Z形台阶折弯,加工厂家往往采用简易模具在冲床或者油压机上加工,批量不大也可在折弯机上用段差模加工,如下图所示。
但是,其高度H不能太高,一般应该在(0~1.0)t,如果高度为(1.0~4.0)t,要根据实际情况考虑使用加卸料结构的模具形式。
这种模具台阶高度可以通过加垫片进行调整,所以,高度H是任意调节的,但是,也有一个缺点,就是长度L尺寸不易保证,竖边的垂直度不易保证。
如果高度H尺寸很大,就要考虑在折弯机上折弯。
折弯机分普通折弯机和数控折弯机两种。
由于精度要求较高,折弯形状不规则,通信设备的钣金折弯一般用数控折弯机折弯,其基本原理就是利用折弯机的折弯刀(上模)、V形槽(下模),对钣金件进行折弯和成形。
优点:装夹方便,定位准确,加工速度快;缺点:压力小,只能加工简单的成形,效率较低。
成形基本原理成形基本原理下图所示:折弯刀(上模)折弯刀的形式如下图所示,加工时主要是根据工件的形状需要选用,一般加工厂家的折弯刀形状较多,特别是专业化程度很高的厂家,为了加工各种复杂的折弯,定做很多形状、规格的折弯刀。
下模一般用V=6t(t为料厚)模。
影响折弯加工的因素有许多,主要有上模圆弧半径、材质、料厚、下模强度、下模的模口尺寸等因素。
为满足产品的需求,在保证折弯机使用安全的情况下,厂家已经把折弯刀模系列化了,我们在结构设计过程中需对现有折弯刀模有个大致的了解。
折弯的常见问题与解决方法

折弯的常见问题与解决方法折弯是一种常用的金属加工方法,可以用于制作各种零件和构件。
然而,在折弯过程中常会遇到一些问题,例如折弯角度不准确、折弯后出现裂纹等。
本文将就折弯的常见问题进行分析,并提供解决方法。
一、折弯角度不准确的问题折弯角度不准确是折弯过程中常见的问题之一。
造成折弯角度不准确的原因有很多,例如折弯机床的误差、模具的磨损等。
解决这个问题可以采取以下措施:1. 定期检查和维护折弯机床,确保其精度和稳定性;2. 定期更换模具,避免磨损导致的角度偏差;3. 在折弯前进行试样折弯,根据试样的角度偏差进行修正。
二、折弯后出现裂纹的问题在折弯过程中,材料容易发生变形和应力集中,导致出现裂纹。
解决这个问题可以采取以下措施:1. 控制折弯力度和速度,避免过大的应力集中;2. 选择合适的材料,避免材料的脆性导致裂纹;3. 在折弯前进行材料的热处理,提高其韧性和抗裂性能。
三、折弯后出现变形的问题折弯后出现变形是由于材料的弹性变形和塑性变形不均匀所导致的。
解决这个问题可以采取以下措施:1. 在折弯前进行材料的预弯处理,减少材料的弹性变形;2. 采用适当的折弯工艺,避免过大的应力集中;3. 在折弯后进行材料的热处理或回火处理,减少其残余应力。
四、折弯过程中出现划伤的问题在折弯过程中,材料与模具接触摩擦产生的划伤是常见的问题。
解决这个问题可以采取以下措施:1. 定期清洁和润滑模具,减少摩擦力;2. 使用合适的护板或垫片,减少材料与模具接触面积;3. 调整折弯工艺参数,减少材料与模具之间的摩擦。
五、折弯角度过小或过大的问题折弯角度过小或过大是由于工艺参数设置不当或模具磨损导致的。
解决这个问题可以采取以下措施:1. 调整折弯机床的工艺参数,确保角度的准确性;2. 定期检查和更换模具,避免磨损导致的角度偏差。
六、折弯过程中出现起皱的问题在折弯过程中,材料容易发生起皱的现象,影响零件的质量。
解决这个问题可以采取以下措施:1. 使用合适的模具和刀具,减少材料的变形;2. 控制折弯力度和速度,避免过大的应力集中;3. 在折弯前进行试样折弯,根据试样的起皱情况进行调整。
关于折弯件产品折裂的工艺分析及解决措施
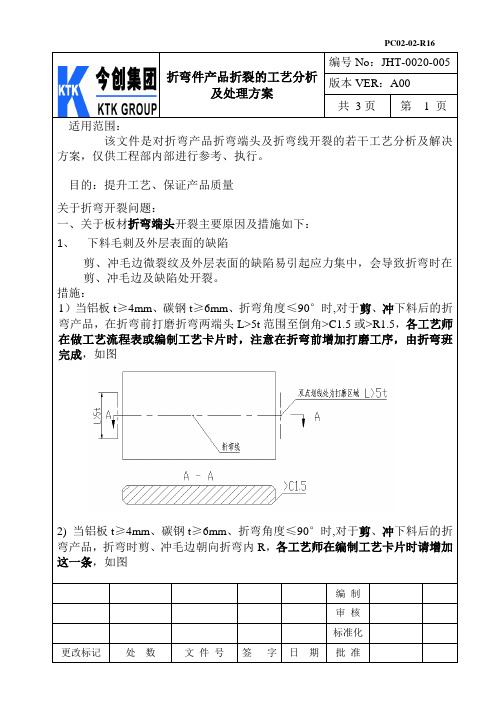
编号No:JHT-0020-005
版本VER:A00
共3页
第1页
适用范围:
该文件是对折弯产品折弯端头及折弯线开裂的若干工艺分析及解决方案,仅供工程部内部进行参考、执行。
目的:提升工艺、保证产品质量
关于折弯开裂问题:
一、关于板材折弯端头开裂主要原因及措施如下:
1、下料毛刺及外层表面的缺陷
共3页
第3页
4、热处理状态
措施:工艺师在审图时注意材料的热处理方式,有些产品要求表面处理状态为淬火或调质,如折弯产品做工艺时要考虑先折弯再进行失效处理。
**注:各工艺师对所负责产品要做到跟踪服务、现场监督,将此类问题彻底杜绝。
编制
审核
标准化
更改标记
处数
文件号
签字
日期
批准
剪、冲毛边微裂纹及外层表面的缺陷易引起应力集中,会导致折弯时在剪、冲毛边及缺陷处开裂。
措施:
1)当铝板t≥4mm、碳钢t≥6mm、折弯角度≤90°时,对于剪、冲下料后的折弯产品,在折弯前打磨折弯两端头L>5t范围至倒角>C1.5或>R1.5,各工艺师在做工艺流程表或编制工艺卡片时,注意在折弯前增加打磨工序,由折弯班完成,如图
3)严格按“折弯工艺守则”、“折弯机通用工艺”执行,选择正确的折弯刀排、折弯槽口。
4)当上述措施执行后仍有缺陷时,可采取氧-乙炔火焰加热、烘烤,铝材温度控制在200°左右,钢板控制在500~600°范围内。
注:以第1)、2)、3)条为主要执行措施,第4)条为辅助措施。
2、折弯R较小
措施:当铝板t≥4mm、碳钢t≥6mm;折弯R≤t;折弯角度≤90°时,可适当建议设计更改折弯R至R>t也可按第1条措施执行。
折弯行业痛点解析及应对策略
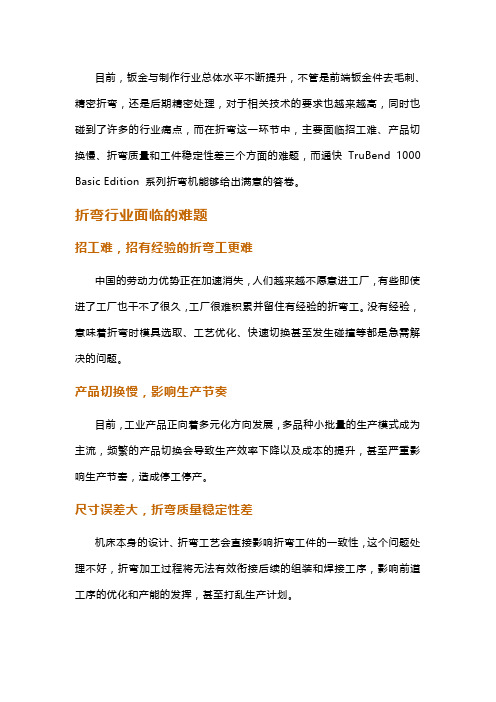
目前,钣金与制作行业总体水平不断提升,不管是前端钣金件去毛刺、精密折弯,还是后期精密处理,对于相关技术的要求也越来越高,同时也碰到了许多的行业痛点,而在折弯这一环节中,主要面临招工难、产品切换慢、折弯质量和工件稳定性差三个方面的难题,而通快TruBend 1000 Basic Edition 系列折弯机能够给出满意的答卷。
折弯行业面临的难题招工难,招有经验的折弯工更难中国的劳动力优势正在加速消失,人们越来越不愿意进工厂,有些即使进了工厂也干不了很久,工厂很难积累并留住有经验的折弯工。
没有经验,意味着折弯时模具选取、工艺优化、快速切换甚至发生碰撞等都是急需解决的问题。
产品切换慢,影响生产节奏目前,工业产品正向着多元化方向发展,多品种小批量的生产模式成为主流,频繁的产品切换会导致生产效率下降以及成本的提升,甚至严重影响生产节奏,造成停工停产。
尺寸误差大,折弯质量稳定性差机床本身的设计、折弯工艺会直接影响折弯工件的一致性,这个问题处理不好,折弯加工过程将无法有效衔接后续的组装和焊接工序,影响前道工序的优化和产能的发挥,甚至打乱生产计划。
通快TruBend 1000 Basic Edition 系列折弯机的特点通快TruBend 1000 Basic Edition 系列折弯机是一种便捷、可靠、智慧型机床,如图1 所示,它集合了通快折弯产品的精华,配备强大的系统设计、高品质的组件和直观的编程系统,具备较高的工艺精度和严格的安全标准,运行稳定可靠,客户可以通过经济实惠的价格享受通快的超高品质,是体验通快折弯技术的理想入门产品。
图1 通快TruBend 1225 折弯机通快TruBend 1000 Basic Edition 系列折弯机操作智能简便,配备通快自主研发的RA 智控系统,能智能导入图纸,实现自动编程并匹配模具,让开工生产变得前所未有的经济迅捷;全自动液压夹具系统可实现快速换刀,从而有效减少模具装卸时间;四轴后挡料系统可确保钣金件的正确定位,重复性高,有助于轻松实现复杂部件的折弯。
钢材折弯开裂的影响因素及改进措施
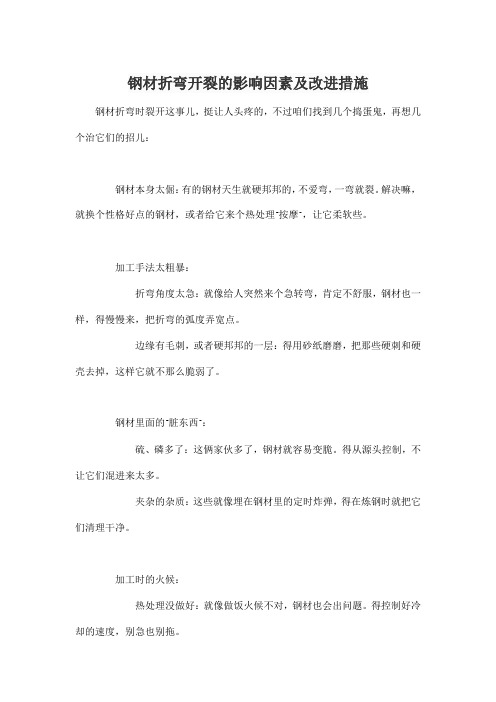
钢材折弯开裂的影响因素及改进措施钢材折弯时裂开这事儿,挺让人头疼的,不过咱们找到几个捣蛋鬼,再想几个治它们的招儿:
钢材本身太倔:有的钢材天生就硬邦邦的,不爱弯,一弯就裂。
解决嘛,就换个性格好点的钢材,或者给它来个热处理“按摩”,让它柔软些。
加工手法太粗暴:
折弯角度太急:就像给人突然来个急转弯,肯定不舒服,钢材也一样,得慢慢来,把折弯的弧度弄宽点。
边缘有毛刺,或者硬邦邦的一层:得用砂纸磨磨,把那些硬刺和硬壳去掉,这样它就不那么脆弱了。
钢材里面的“脏东西”:
硫、磷多了:这俩家伙多了,钢材就容易变脆。
得从源头控制,不让它们混进来太多。
夹杂的杂质:这些就像埋在钢材里的定时炸弹,得在炼钢时就把它们清理干净。
加工时的火候:
热处理没做好:就像做饭火候不对,钢材也会出问题。
得控制好冷却的速度,别急也别拖。
设计和操作上的讲究:
设计时多动动脑筋:提前规划好哪里弯,怎么弯,让钢材的潜力发挥出来。
操作时有技巧:先弯后剪,或者在容易裂的地方预先打个小洞减减压,都是好办法。
综上所述,要想让钢材听话,不折不裂,咱们得从钢材本身、加工方法、材料纯净度、热处理工艺,到设计和操作技巧,全方位照顾到。
这样,钢材就能乖乖弯成你想要的样子啦!。
管子折弯问题实践总结

报错一:管子端部弯曲时,左右弯切换时可能会出现。
要求: 所弯管材必须是直的,若两端有弯曲现象,需要注意。
管子没有夹住
报错二:热缩皮长短不一致,在上下模切换时可能会出现。
原因:上模和下模直径不同,上模弯管时是带有热缩皮的,下模不带皮。
若用上模弯不带皮的,系统接收到报错信号,即停止运行。
三段热缩皮
问题一:在用下模折弯时,可能会出现划伤现象。
对策:在管接头处戴上帽。
正常情况
扭曲一
扭曲二
对策:加大模具间的开口,但是开口过大会带来较大弯曲角度误差,尽量不要动。
干涉一:绿色为干涉.
干涉二:这种情况坚决不能再次出现,查看模拟窗口。
啃皮一: 皮薄,模具与所弯管子不一致。
啃皮二
情况一:更换滑模,防止端部弯扁。
(11型)
情况二:吹气,去除管材内壁的细小颗粒粉尘。
情况三:芯棒尽可能靠近前端,可以避免弯曲处起皱。
情况四:改善热缩管端部截面,可以避免管子折弯时扭曲。
零件弯曲变形的分析研究与改进措施

零件弯曲变形的分析研究与改进措施摘要:一些机械零件在长期受到外加环境载荷和内部环境的共同作用下后,就可能会逐渐损失自身零件原有的力学机械性能及物理、化学或其他特殊性能,直至不能完全恢复到继续正常运行服役的特殊现象,我们称之为零件弯曲变形所导致的零件失效现象。
根据零件弯曲变形的特点、所受载荷的类型及所处条件的不同,零件弯曲变形的原因可归纳为受力引起的弯曲变形,热处理过程中引起的弯曲变形以及弹性及塑性变形几类。
在实际操作中,由于不同客观因素的影响,机械零件会发生变形,这不仅影响了企业的经济效益而且缩短了产品的使用寿命。
激烈的市场竞争中企业要提高竞争力,就必须研究机械零件变形的原因和改进措施。
关键词:机械零件、弯曲变形、原因分析、方法措施1零件弯曲变形研究意义机械加工的性能不仅仅关系着企业的切身利益,而且关系到机械加工过程中的安全。
好的机械加工设备在为企业发展带来最大经济效益基础的同时还有效地降低了机械零件安全事故发生的最大可能性。
因此,在机械加工零件的使用过程中,避免加工零件发生变形尤为重要,零件变形加工时机械操作技术人员自身应充分考虑到各种因素和环境条件,在加工过程中及时采取适当防护措施以防止零件变形,使一件成品零件能正常加工使用。
那么为了能够使这些零件材料变形的加工事故尽可能不发生或少量的发生,就需要我们去详细分析这些零件材料加工发生变形的主要原因,确定这些零件加工变形的可靠解决措施,以此为实现现代企业战略目标提供坚实的基础。
2变形原因分析2.1受力引起的弯曲变形(1)内力作用引起的变形当车床机械加工重要零件时,可用机械夹具固定整个工件。
为了能够保证零件在加工过程中不至于出现松动损坏情况,必须要特别注意对切削力的自动控制,灵活地改变切削力以便于保证松动工件始终低于规定夹紧切削力。
同时,为了能够保证整个零件材料加工的正常有序进行,还需要及时调整整个工件上下受力平衡情况,以此来保证整个工件上下的受力平衡。
折弯的常见问题与解决方法

折弯的常见问题与解决方法折弯是一种常见的金属加工方法,用于将金属板材弯曲成所需的形状。
在折弯过程中,可能会遇到一些常见的问题,如折痕不均匀、折弯角度不准确等。
本文将介绍一些折弯过程中常见的问题及其解决方法。
1. 折痕不均匀折痕不均匀是折弯过程中常见的问题之一,可能会导致零件尺寸不准确或外观质量差。
以下是一些解决方法:1.1 调整折弯机设置首先,检查折弯机的设置是否正确。
确保上模和下模之间的间隙适当,并根据材料的厚度和硬度调整折弯机的压力。
另外,检查模具是否清洁,以确保材料能够均匀地弯曲。
1.2 调整折弯工艺参数其次,调整折弯工艺参数,如折弯速度和折弯力度。
如果折弯速度过快或折弯力度不足,可能会导致折痕不均匀。
通过逐步调整这些参数,找到最佳的折弯工艺参数,以获得均匀的折痕。
1.3 优化模具设计另外,优化模具设计也可以改善折痕的均匀性。
合理设计模具的几何形状和角度,可以减少材料在折弯过程中的应力集中,从而避免折痕不均匀的问题。
2. 折弯角度不准确折弯角度不准确是另一个常见的问题,可能会导致零件尺寸偏差或装配问题。
以下是一些解决方法:2.1 校准折弯机首先,检查折弯机的角度校准情况。
使用角度测量工具,如角度尺或角度测量仪,检查折弯角度是否准确。
如果发现角度偏差较大,需要对折弯机进行校准,以确保折弯角度的准确性。
2.2 调整折弯工艺参数其次,调整折弯工艺参数也可以改善折弯角度的准确性。
合理选择折弯力度和折弯速度,以获得所需的折弯角度。
同时,注意材料的回弹性,根据材料的特性进行适当的修正。
2.3 使用辅助夹具另外,使用辅助夹具可以帮助提高折弯角度的准确性。
夹具可以提供额外的支撑和定位,确保材料在折弯过程中保持正确的位置和角度。
根据零件的形状和尺寸,设计和制造适用的夹具,以提高折弯角度的精度。
3. 材料拉伸或变形在折弯过程中,材料可能会发生拉伸或变形,导致折弯后的零件尺寸不准确或形状失真。
以下是一些解决方法:3.1 选择合适的材料首先,选择合适的材料可以减少材料的拉伸或变形。
一个折弯干涉的解决办法及分析!
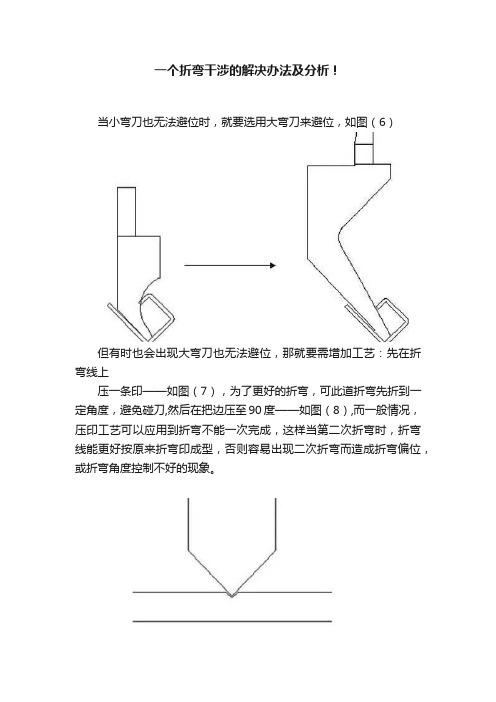
一个折弯干涉的解决办法及分析!当小弯刀也无法避位时,就要选用大弯刀来避位,如图(6)但有时也会出现大弯刀也无法避位,那就要需增加工艺:先在折弯线上压一条印——如图(7),为了更好的折弯,可此道折弯先折到一定角度,避免碰刀,然后在把边压至90度——如图(8),而一般情况,压印工艺可以应用到折弯不能一次完成,这样当第二次折弯时,折弯线能更好按原来折弯印成型,否则容易出现二次折弯而造成折弯偏位,或折弯角度控制不好的现象。
所以在设计的过程中也要考虑这样的问题,在满足要求的情况尽量避免出现采用这样的工艺,因为这样没有直接折弯的效果好,而且尺寸和角度都可能有偏差。
折弯机还可以用于工件压死边,先把工件折弯到30度,再用平刀把工件压死,但一般可用普通冲床完成的压死边尽量不安排到折弯机,因为冲床压死边的效果相对比较好点。
在折弯过程中除了工件与折弯刀干涉,当工件的尺寸比较大时还可能会出现折弯时与折弯机干涉。
在我们安排工艺的时候,很多时候都要考虑是否好折弯,能否折弯的问题,因为折弯是一个很重要的工艺,折弯是否好操作直接影响到折弯质量的保证,而很多时候出现的质量问题都是出自于折弯尺寸没有控制好,所以在设计的过程中也要特别关注折弯的问题,这个关系到产品量产时质量的稳定性。
对于不同板厚,它的折弯尺寸都是有限度的,不能过小,一般多与下刀模有关系,一般的原则是:下刀模选取板厚6倍的刀槽,这样折弯系数与经验值最符合。
一般刀槽的分类按刀槽的外宽分如图(9),分别是6号和10号槽。
但选用够小的刀槽折弯时,很容易出现压痕,一般6号槽以下的压痕都比较明显,所以当工件表面不处理时,当折弯边比较小时,有明显的压痕,一来影响外观,二来容易生锈,所以在设计时要注意。
由图(10)可以看到,对于10号槽,折弯线到定位边的距离必须要大于5.0mm才可能折弯。
由此可知道,一般4号槽是最小的刀槽,折弯线到定位边的距离需大于2.0mm,而一般4号槽多用于薄板(1.2mm以下),因为如果折弯厚板,需要的压力比较大,槽较小时,容易压爆刀槽。
装配活动干涉结构分析报告

装配活动干涉结构分析报告1. 引言装配活动是制造工程中的关键环节,常常涉及多个零部件的组合与连接。
然而,在装配过程中,由于设计和制造上的一些原因,可能会出现零部件之间的干涉现象,即零部件在安装过程中相互干扰,导致装配困难或无法完成装配的情况。
本报告旨在对装配活动干涉结构进行分析,找出干涉问题的原因,并提出相应的解决方案。
2. 干涉现象的分析通过对装配活动的观察和测量,我们发现了两个零部件之间的干涉现象。
具体表现为,在装配过程中,零部件无法正确安装到目标位置,或者在安装过程中出现卡阻,无法继续往下安装。
通过进一步的分析,我们发现干涉主要出现在两个主要区域:连接接口和活动行程。
接下来,我们将对这两个区域的干涉现象进行详细分析。
2.1 连接接口干涉分析在连接接口处,我们发现两个零部件的尺寸存在较大的误差,导致连接时形成了干涉现象。
通过测量,我们发现其中一个零部件的直径超出了设计要求,而另一个零部件的孔的直径也小于设计要求。
这种误差可能是由于制造过程中的尺寸控制不严格导致的。
2.2 活动行程干涉分析在零部件的活动行程中,我们发现一个零部件在运动过程中与另一个零部件有冲突。
通过进一步观察,我们发现这两个零部件的运动轨迹存在交叉,导致运动过程中的干涉现象。
可能的原因是设计时未考虑到两个零部件在活动行程中的交叉情况,或者设计中的安全间隙设置不合理。
3. 解决方案根据干涉现象的分析,我们提出以下解决方案来解决装配活动中的干涉问题。
3.1 连接接口问题的解决方案针对连接接口处的干涉问题,我们建议采取以下措施:1. 提高制造过程中的尺寸控制精度,确保零部件的尺寸符合设计要求。
2. 对于零部件之间的连接接口,可以采取设计可调节的连接方式,如螺纹连接或配合销连接,以便调整连接尺寸。
3.2 活动行程问题的解决方案针对活动行程中的干涉问题,我们建议采取以下措施:1. 通过优化零部件的设计,调整零部件的运动轨迹,避免交叉情况的发生。
机械零件加工中的变形与对策探讨

机械零件加工中的变形与对策探讨机械零件加工是制造业中的关键环节之一,而在加工过程中,零件变形是一个常见的问题。
变形会影响零件的精度和质量,甚至会导致整个加工过程的失败。
探讨机械零件加工中的变形与对策对于提高加工质量和效率具有重要意义。
一、机械零件加工中的变形原因1.材料性质:材料的热胀冷缩系数不同、内应力大、塑性差等因素会导致机械零件加工过程中的变形。
2.加工工艺:加工温度、切削力、切削速度等因素都会影响零件的变形。
3.加工设备:加工设备的精度、刚性、稳定性等因素也会对零件的变形产生影响。
1.选择合适的材料:在机械零件加工中,选择合适的材料是非常重要的一环。
材料的热胀冷缩系数、内应力、塑性等性质都会直接影响零件的变形情况。
选择合适的材料对于减少零件变形至关重要。
2.优化加工工艺:在进行机械零件加工时,优化加工工艺可以有效减少零件的变形。
通过控制加工温度、切削力、切削速度等参数,尽可能减少材料的内应力,避免零件的变形。
3.加工设备的优化:选择精度高、刚性好、稳定性强的加工设备可以有效减少零件的变形。
定期对加工设备进行检查和维护也是非常重要的,确保加工设备的正常运转。
4.采用适当的工艺措施:在零件加工过程中,可以采用适当的工艺措施来减少零件的变形,如采用逐级切削和冷却、采用适当的余量等。
5.加工过程中的监控与调整:在零件加工过程中,及时监控零件的变形情况,并进行及时的调整,可以有效减少零件的变形。
机械零件加工中的变形是一个复杂的问题,需要综合考虑材料、工艺、设备等多方面因素,并采取有效的对策控制。
只有在全面控制变形的因素和采取相应的对策措施的情况下,才能有效地减少零件的变形,提高加工质量和效率。
机械零件加工中的变形与对策是一个非常重要的课题。
只有不断深入研究和实践,不断总结和创新,才能不断提高零件加工质量和效率,为制造业的发展做出贡献。
机械制造工艺中的弯曲变形分析与控制

机械制造工艺中的弯曲变形分析与控制引言机械制造工艺在现代工业生产中起着至关重要的作用。
然而,由于材料和加工过程的特性,机械零件在制造过程中常常会出现弯曲变形的现象。
本文将探讨机械制造工艺中弯曲变形的原因、影响因素以及相应的控制方法。
一、原因分析机械零件的弯曲变形往往源于材料的弹性变形。
在受力作用下,由于材料内部的晶粒结构以及分子之间的相互作用,材料会发生形状改变,进而导致弯曲变形。
此外,工艺参数的选择以及制造中的不良操作也会增加零件的弯曲变形程度。
二、影响因素1. 材料特性:材料的硬度、强度、韧性等特性将直接影响零件的弯曲变形。
通常情况下,硬度越高的材料越不容易发生弯曲变形。
2. 制造工艺:制造中使用的工艺参数,如加热温度、加热时间、冷却速度等,可能会改变零件的组织结构,从而导致弯曲变形。
3. 设计缺陷:不合理的零件设计往往也是引起弯曲变形的主要原因之一。
例如,零件的截面过于窄小、局部刚度不足等都会导致弯曲变形加剧。
三、分析与控制方法1. 数值仿真分析:利用有限元分析等数值仿真方法,对零件在受力情况下的变形进行模拟与分析,可以有效预估并控制弯曲变形。
通过调整材料的厚度、加强材料的刚度等措施,可以减轻弯曲变形的程度。
2. 工艺参数优化:合理选择制造工艺中的参数,如用火工艺的加热温度、压铸工艺的铸造温度等,是控制弯曲变形的重要手段。
通过对工艺参数的优化调整,可以改善零件的强度和刚度,减少弯曲变形风险。
3. 合理设计:在零件的设计阶段,应该充分考虑到零件在受力情况下的变形特性。
避免过度依赖材料的强度和硬度,合理设计截面和局部加强部位,从而减轻零件的弯曲变形。
结语机械制造工艺中的弯曲变形是一种常见且困扰着制造企业的问题。
只有通过深入分析、优化工艺参数以及合理设计,才能有效控制弯曲变形的发生,提高零件的质量和性能。
在未来的发展中,我们应该不断探索新的解决方案,推动机械制造工艺的研究与创新,为行业的可持续发展做出贡献。
折弯时发生干涉现象的分析及解决方法
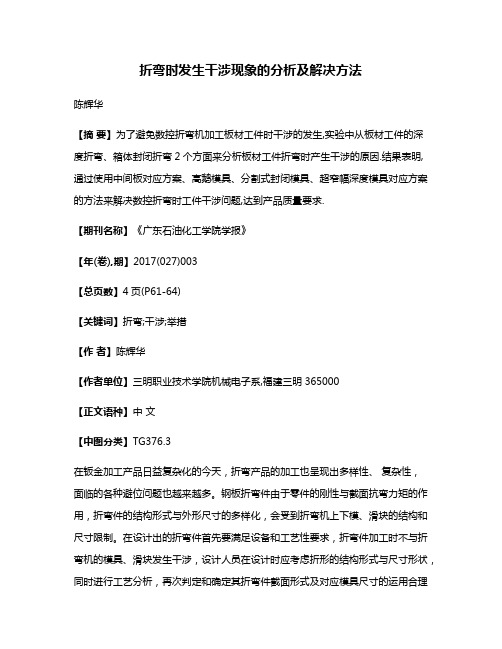
折弯时发生干涉现象的分析及解决方法陈辉华【摘要】为了避免数控折弯机加工板材工件时干涉的发生,实验中从板材工件的深度折弯、箱体封闭折弯2个方面来分析板材工件折弯时产生干涉的原因.结果表明,通过使用中间板对应方案、高鹅模具、分割式封闭模具、超窄幅深度模具对应方案的方法来解决数控折弯时工件干涉问题,达到产品质量要求.【期刊名称】《广东石油化工学院学报》【年(卷),期】2017(027)003【总页数】4页(P61-64)【关键词】折弯;干涉;举措【作者】陈辉华【作者单位】三明职业技术学院机械电子系,福建三明365000【正文语种】中文【中图分类】TG376.3在钣金加工产品日益复杂化的今天,折弯产品的加工也呈现出多样性、复杂性,面临的各种避位问题也越来越多。
钢板折弯件由于零件的刚性与截面抗弯力矩的作用,折弯件的结构形式与外形尺寸的多样化,会受到折弯机上下模、滑块的结构和尺寸限制。
在设计出的折弯件首先要满足设备和工艺性要求,折弯件加工时不与折弯机的模具、滑块发生干涉,设计人员在设计时应考虑折形的结构形式与尺寸形状,同时进行工艺分析,再次判定和确定其折弯件截面形式及对应模具尺寸的运用合理性[1-4]。
对于2 次或以上的折弯件,经常出现零件与模具相碰和撞击,这样就产生干涉现象。
当零件外形尺寸足够大时,还会出现折弯件与滑块相碰而干涉。
1.1 合理最小边延尺寸折弯加工最终完成时,材料与下模的两肩必然要正面全部接触,那么下模的最小边缘尺寸选定为90oV槽,也是下模V槽的斜边长度,其计算为=0.7×L,式中:L 为下模最大开口长度,mm,如图1所示。
当下模的开口最大长度为10 mm时,折弯的材料长度最小边缘尺寸应为7 mm。
如果没有达到这个尺寸要求,上模易向右边移动,下模易向左边移动,工件在下模中溜滑,上下模严重不对芯,容易发生干涉现象,导致零件不成形[5]。
1.2 合理的上、下模高度尺寸与设计深度折弯时上模高度有两种情况,分别为中间板种类和标准板种类。
弯曲件常见质量问题改善对策
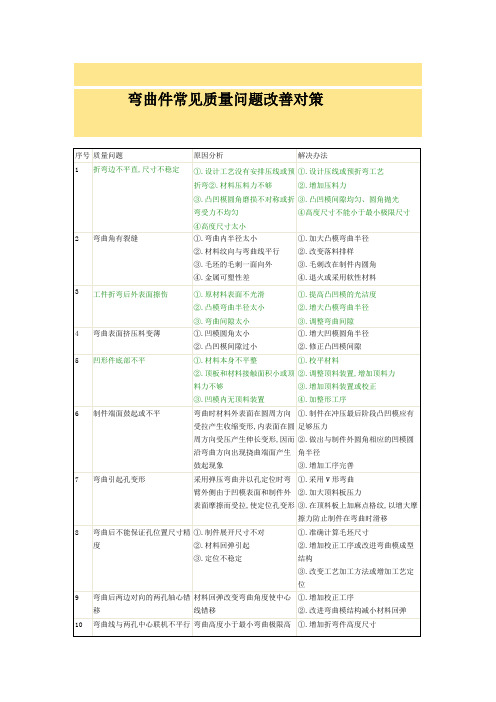
②.做出与制件外圆角相应的凹模圆角半径
③.增加工序完善
7
弯曲引起孔变形
采用弹压弯曲并以孔定位时弯臂外侧由于凹模表面和制件外表面摩擦而受拉,使定位孔变形
①.采用V形弯曲
②.加大顶料板压力
③.在顶料板上加麻点格纹,以增大摩擦力防止制件在弯曲时滑移
8
弯曲后不能保证孔位置尺寸精度
①.制件展开尺寸不对
②.材料回弹引起
③.定位不稳定
①.准确计算毛坯尺寸
②.增加校正工序或改进弯曲模成型结构
③.改变工艺加工方法或增加工艺定位
9
弯曲后两边对向的两孔轴心错移
材料回弹改变弯曲角度使中心线错移
①.增加校正工序
②.改进弯曲模结构减小材料回弹
10
弯曲线与两孔中心联机不平行
①.增加折弯件高度尺寸
②.改进折弯件工艺方法
11
带切口的制件向下挠曲
切口使两直边向左右张开,制件底部出现挠度
①.改进制件结构
②.切口处增加工艺留量,使切口连接起来,弯曲后再将工艺留量切去
12
弯曲后宽度方向变形,被弯曲部位在宽度方向出现弓形挠度
由于制件宽度方向的拉深和收缩量不一致产生扭转和挠度
①.增加弯曲压力
②.增加校正工序
③.保证材料纹向与弯曲方向有一定角度
②.凸凹模间隙过小
①.增大凹模圆角半径
②.修正凸凹模间隙
5
凹形件底部不平
①.材料本身不平整
②.顶板和材料接触面积小或顶料力不够
③.凹模内无顶料装置
①.校平材料
②.调整顶料装置,增加顶料力
③.增加顶料装置或校正
④.加整形工序
6
折弯件常见缺陷有哪些?如何处理及预防
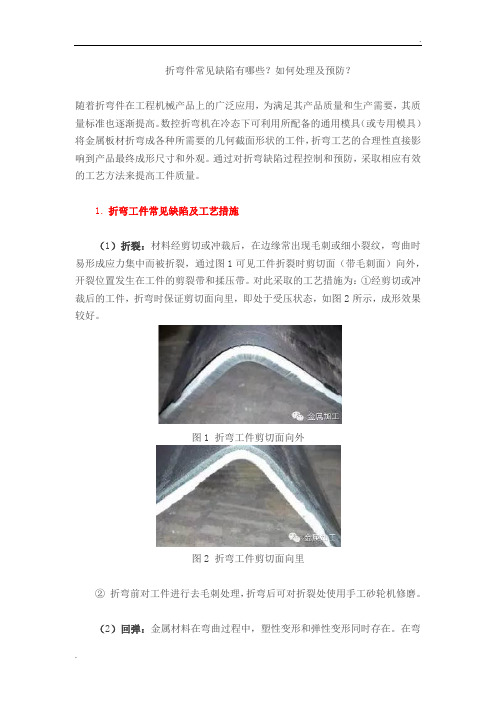
折弯件常见缺陷有哪些?如何处理及预防?随着折弯件在工程机械产品上的广泛应用,为满足其产品质量和生产需要,其质量标准也逐渐提高。
数控折弯机在冷态下可利用所配备的通用模具(或专用模具)将金属板材折弯成各种所需要的几何截面形状的工件,折弯工艺的合理性直接影响到产品最终成形尺寸和外观。
通过对折弯缺陷过程控制和预防,采取相应有效的工艺方法来提高工件质量。
1. 折弯工件常见缺陷及工艺措施(1)折裂:材料经剪切或冲裁后,在边缘常出现毛刺或细小裂纹,弯曲时易形成应力集中而被折裂,通过图1可见工件折裂时剪切面(带毛刺面)向外,开裂位置发生在工件的剪裂带和揉压带。
对此采取的工艺措施为:①经剪切或冲裁后的工件,折弯时保证剪切面向里,即处于受压状态,如图2所示,成形效果较好。
图1 折弯工件剪切面向外图2 折弯工件剪切面向里②折弯前对工件进行去毛刺处理,折弯后可对折裂处使用手工砂轮机修磨。
(2)回弹:金属材料在弯曲过程中,塑性变形和弹性变形同时存在。
在弯曲结束时,因弹性变形的恢复而产生回弹,如图3所示。
回弹现象直接影响工件的尺寸精度,须加以控制。
对此采取的工艺措施为:①角度补偿法。
若工件折弯角度为90°,折弯机下槽(V形)开口角度可选择78°。
图3 折弯工件回弹②加压时长增加校正法。
在弯曲终了时进行加压校正,延长折弯机上模、工件、下槽的接触时间,以增加下槽圆角处的塑性变形程度,使拉压区纤维的回弹趋势互相抵制,从而减少回弹。
( 3 )凸起:对于中厚板(厚度t≥6mm)折弯,情况比较特殊,折弯线附近区域在弯曲过程中会出现纤维组织变长,造成折弯圆角处形成凸起,通过对车间成形工件观察,圆角凸起大小随板厚增加而增大。
对部分工件质量要求较高的,圆角凸起会影响焊接或装配尺寸精度,需采取工艺措施去除。
对此采取的工艺措施为:①若采用热切割设备下料,工艺人员在板件展开下料时,对下料图以折弯线为中心作向里凹圆弧,去掉多余板料,如图4所示,其中R为圆弧半径。
浅谈钣金件弯曲质量控制

本文首先分析了钣金件弯曲中回弹和裂纹问题的质量控制,其次针对实际加工中常用的不锈钢和铝板两种材料弯曲时的质量控制进行了阐述。
弯曲是指把板材、棒材、管材或型材加工成具有一定角度和形状的零件的成形方法,是钣金冲压加工中的常见工序。
一般说来,弯曲工序需要保证钣金件弯曲部位的圆角半径、零件的结构、形状、尺寸等几大方面。
实际加工中,钣金件弯曲的质量问题最常见的为回弹,其次是裂纹,其他还包括翘曲、扭曲、尺寸偏移、孔偏移等问题,本文主要针对加工产生最多的回弹和裂纹问题进行分析,并给出质量控制措施。
钣金零件弯曲质量控制分析钣金件弯曲回弹质量控制弯曲成形过程中,毛坯在外载荷的作用下会产生塑性和弹性两种形式的变形。
一旦外部载荷撤除,产生的弹性变形会即刻消失,而塑性变形还能继续保持。
零件由于弹性变形的存在,形位尺寸会产生与加载方向相反的变形,这个变形就是回弹。
回弹量的大小影响因素较为复杂,要确保回弹过程中的质量控制,就要分析其影响因素。
⑴影响回弹的因素及控制对策1)材料选择材料选择取决于材料的力学性能,也就是说,材料的屈服极限越高,弹性模量越小,则弯曲后回弹越大,加工硬化现象越严重,回弹量也越大。
因此为防止材料对回弹的影响,工艺设计人员应尽量选择屈服点小、弹性模量大、硬化指数小的材料。
2)钣金件的结构钣金件弯曲时,相对弯曲半径r/t,当此数值较小时,零件内、外表面切向变形的总应变值较大,产生的弹性应变就相应减小,回弹量较小,反之则大。
因此钣金件弯曲时,相对半径必须超出比例系数,但应尽量选择较小的系数值。
此外,在确保钣金件使用的前提下,可以在弯曲区域压制加强筋,从而增加零件界面惯性力矩,从而抑制回弹的产生。
3)零件工艺性原因钣金件弯曲时,弯曲角度越大,变形区长度越大,回弹角也越大;此外,实际生产中,施加的弯曲力越大,变形越大,则回弹量越小;最后,采用无底凹模进行自由弯曲时,回弹量较大,反之采用校正弯曲时,模具采用V 形件进行校正,则回弹量较小。
- 1、下载文档前请自行甄别文档内容的完整性,平台不提供额外的编辑、内容补充、找答案等附加服务。
- 2、"仅部分预览"的文档,不可在线预览部分如存在完整性等问题,可反馈申请退款(可完整预览的文档不适用该条件!)。
- 3、如文档侵犯您的权益,请联系客服反馈,我们会尽快为您处理(人工客服工作时间:9:00-18:30)。
弯顺序不当引起的折弯干涉。如图 l 3 , 折弯T序为魁折 弯2 处, ] - 件 模具发生干涉 , 该方案不可行 , 如图 1 4 。
滑块部分由滑块 、 油缸及机械挡块微调结构组成。 左 弯 2 处后折弯 1 处, 方案可行 ; 而T序为先折弯 l 处后折
朽 油缸 『 占 1 定在 机 架 上 ,通 过液 压使 活 塞杆 带 动滑 块 下 运动, 机 械挡 块 由数 控 系统控 制 调节 数 值 。可 见 , 滑块 与
限 制 最 后 一 道
图 1 2所示 。
如 用于夫于 9 0 。 的 自由折弯 , 通过增加或减少不 同厚度的镶 折 弯 的运 动 , 3 )折 弯 件
一
在加T过程中 , 由于本 身 T 艺
设计 的 问题 , 可 导 致 在 加 1 的
过程 中发 生 折
, . j 滑 块
卜 j 尺寸 , I 1 艺人 员在T 艺分 析 时 , 必 须再 次判 定 和 确定 其 折 弯件 与 f : 模、 折 弯件 与下模及 折 弯件 与滑 块 3 类干涉。
此处 干涉是指折弯件 与』 二 模轮廓包含的区域发生 r 遮蔽 ,判断某一 次折弯是否产生干涉可以看作对于某 ・ 遮蔽 。 下面具体分析折弯件 与. k 模的干涉类型, 其不外乎
个“ L ” j 板 拼 焊 、 但 需 考虑 前期坡 制造 成 本 、 焊 接 变
形、 — r 件的整体强度 与外观质鞋等的影响 , 腆厦选择 .
3 . 2 工 艺措 施
1 ) 在既 能 用 弯模 。 义 能用 直模 折 弯 的 件 , 量 选 用
解 决方寨
嚣 稻篓 辫 工艺 , 工装 , 臻舆 , i 坌 断 ,越潮 , 维偿 , 改造
零 件折弯干 涉问 题分析与举 措研究
江 春 林
( 辽宁瑞丰专用车 制造 有限公司 , 辽宁 海城 l 1 4 2 0 0 )
,
并
0 引 言
上模 和机床导轨相连 , 由1 . 作油缸带动 L 下往复运动 , 完
4 )在 满 足最
作台轮廓包含的区域发生_ r 遮蔽 ,下模f涉的判断一 小 折 弯 半 径 设
汁强 度 的 条 件 下 , 更 改 板 厚 或 材 料 以 便 使 用 弯 模 进
断差。其关键 寸 ‘ 由断差高度 h 决定, h 值 由 v形槽中心 行折 弯 。 如若 B 一 4 / Q 3 4 5 B槽 形件 的结 构 尺 寸I ; } ! 制了 折 弯, 但用弯模折 弯不会干涉 ,因 B - - 4 / Q 3 4 5 B 最小折 弯半径为
用如图 4 5两 种 。
1 )零 件 的 结 构 尺 寸 局 限 引起 的与 直 模 、 弯模 干涉 . 如图
9 ~ l 0所示 。
பைடு நூலகம்
2 )折 j 边
, . 2 下模
或 四 边 的 箱 型
】 折弯机的下模 主要分为单 v形 、 整体形 ( N形 ) 与镶 零 件 ,如 图 l 先前 已折 块镶嵌形等结构, 如图 6 ~ 8 所示 。 单 V形主要用于具有分 所 示 , 段 式 模 具 的折 弯 机 ; 整体形( N形 ) 是 常 用 的一 种 下模 结 构, 它具 有 多个 V形槽 的下模 体 ; 镶嵌 式 结构 的下 模 主要 块 来实 现 不同 的下 模开 口。 弯 的 折 弯 边 会
干涉 。
下模置于 作台上 ,此处干涉足指折弯件 与下模和
般 在折 弯 前进 行 . . 与下 模 干 涉 的零 件 主要 表 现 为 “ z ” 形件 , z形 折 弯又 称 为断 蔗 , 如【 皋 ]l 5 , 根 据 成形 角 度分 为 直边 断 差 和 斜 边 到 下模 体边 缘 的最 小 距 离 曰 、 折 弯 网 角半 径 、 板厚 t 所 决定 ( 如图 l 6 ) , 即 h ≥B + 2 t + R。
1 . 1 上模
对于 2 次或 2 次以 卜 的折弯件 ,经常 出现零件与模 件与滑块相碰而干涉。因此 , 折弯件干涉的主要形式有 :
2 . 折 弯件 与 上模 干 涉
备和1 - 艺性要求 , 加工时不 与 折弯机的模具 、 滑块 发生干 具相 碰 而 干涉 。 当零件 外形 尺 寸足 够大 时 , 还会 出现折 弯
以下 4种 情况 :
} : 模是折弯机重要部件之一 ,主要有直臂式与 曲臂 折弯点 ,弯曲前 和弯曲后的弯曲件是否 与上述轮廓发生
式 的结 构 我 公 司 的直臂 式 根据 不 同 的模柄 结 构 可分 为 1 ~ 3 所 示 j种 ; 曲臂 式 的模具 根 据喉 深不 同 , 我公 司 常
B 一 4 / Q 3 4 5 B更 改 为 B 一 5 / Q 2 3 5 B , 町在不 改 结 构 尺寸 的 ( 1 ) 刖o ( R1 0 的模 具为直 模 ) , 不 能使 用 弯模 . 此, 考 虑 将
前提下实现折弯, 5 ) 更改为拼焊结构。折弯件 町拆分为两个“ 1 ” 形或 一
成板 料 折 弯 。 2 折 弯件 干涉 的分 析
钢板 折 弯 件 可提 高 零 件 的 刚性 与 截 面 抗 弯 力 矩 , 但 折 弯件 的 结 构形 式 与外 形 尺寸 往 往 受 到折 弯 机 上 下 模 、
滑块的结构和尺寸限制。为了使设计 出的折弯件满足设
涉 .没计 人 员在 没计 之初 就 要首 先考 虑折形 的结 构 形式 截面形 式 及对 应 尺寸 的合理 性 。 1 折弯 设备 的概 况
4 ) 上模选择不当引起的折弯干涉 采用弯模 才能折
2 0 6 机械工程师 2 0 1 4 年第1 期
鼹决 方 寨
工艺 / 工装 , 税目 , 诌断 , 趋测 , 维铬 , 改造 嚣
弯的零件 , 却选择 j , 直模
2 . 2 折 弯件 与 下模 干 涉
1 9的结 构 , 『 f 肖除