谐振式电液疲劳试验机的设计参考外文2
疲劳试验机

疲劳试验机概述疲劳试验机是一种用于评估材料、构件或产品在疲劳条件下的性能的实验设备。
通过施加重复的载荷和应变,疲劳试验机可以模拟产品在实际使用中所经历的循环负荷,以帮助工程师评估其可靠性和耐久性。
本文将讨论疲劳试验机的原理、应用领域以及常见的测试方法和注意事项。
原理疲劳试验机的工作原理基于材料的疲劳行为。
材料在受到交变载荷时,会发生应力集中和微裂纹的产生,并逐渐扩展形成裂纹。
当裂纹扩展到关键尺寸时,材料会发生破裂。
疲劳试验机可以模拟这个过程,以便评估材料的疲劳寿命和性能。
疲劳试验机通常由载荷系统、控制系统和测试样品支撑平台组成。
载荷系统可以施加不同频率和幅值的载荷,以模拟实际使用中的循环负荷。
控制系统可以实时监测载荷和应变,并根据预设的测试参数自动调整载荷的大小和频率。
测试样品支撑平台用于固定和支撑测试样品,并确保其受到均匀的载荷分布。
应用领域疲劳试验机在许多工业领域都有广泛的应用。
下面是一些常见的应用领域:1. 材料研究和开发:疲劳试验机可以用于评估不同材料的耐久性能,以指导材料的研发过程。
通过对不同材料进行疲劳试验比较,工程师可以确定最合适的材料选择,并优化产品设计。
2. 汽车和航空航天工业:汽车和航空航天工业中的许多部件都需要经受长时间的循环负荷。
疲劳试验机可以模拟这些循环负荷,并评估不同部件的疲劳寿命和性能。
这些数据对于设计更安全和可靠的汽车和飞机至关重要。
3. 建筑和土木工程:建筑和土木工程中的结构件需要经受长时间的加载和应变。
通过利用疲劳试验机,工程师可以评估结构件在长期使用情况下的疲劳性能,以确保其安全和可靠。
4. 能源领域:能源设备如风力涡轮机和太阳能板也需要经受循环负荷。
疲劳试验机可以模拟这些负荷,并评估设备的耐久性和寿命。
常见的测试方法和注意事项在进行疲劳试验时,有几种常见的测试方法可以选择:1. 应力控制法:在应力控制法中,试样会在恒定的应力水平下进行疲劳测试,通过监测试样的应变来评估疲劳寿命。
疲劳试验标准与疲劳试验机
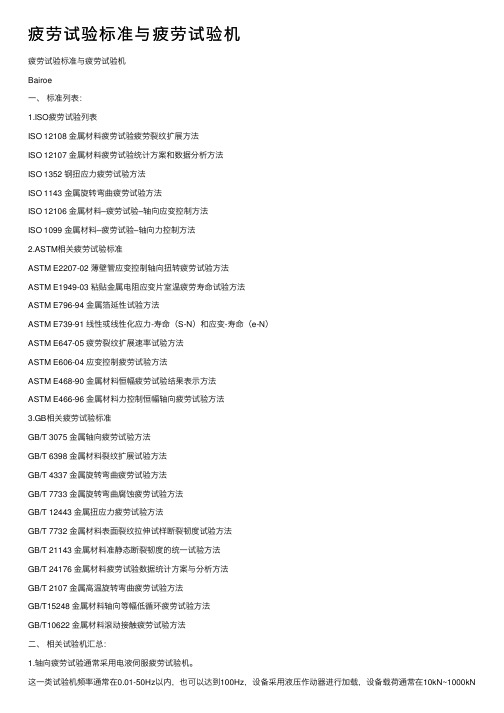
疲劳试验标准与疲劳试验机疲劳试验标准与疲劳试验机Bairoe⼀、标准列表:1.ISO疲劳试验列表ISO 12108 ⾦属材料疲劳试验疲劳裂纹扩展⽅法ISO 12107 ⾦属材料疲劳试验统计⽅案和数据分析⽅法ISO 1352 钢扭应⼒疲劳试验⽅法ISO 1143 ⾦属旋转弯曲疲劳试验⽅法ISO 12106 ⾦属材料–疲劳试验–轴向应变控制⽅法ISO 1099 ⾦属材料–疲劳试验–轴向⼒控制⽅法2.ASTM相关疲劳试验标准ASTM E2207-02 薄壁管应变控制轴向扭转疲劳试验⽅法ASTM E1949-03 粘贴⾦属电阻应变⽚室温疲劳寿命试验⽅法ASTM E796-94 ⾦属箔延性试验⽅法ASTM E739-91 线性或线性化应⼒-寿命(S-N)和应变-寿命(e-N)ASTM E647-05 疲劳裂纹扩展速率试验⽅法ASTM E606-04 应变控制疲劳试验⽅法ASTM E468-90 ⾦属材料恒幅疲劳试验结果表⽰⽅法ASTM E466-96 ⾦属材料⼒控制恒幅轴向疲劳试验⽅法3.GB相关疲劳试验标准GB/T 3075 ⾦属轴向疲劳试验⽅法GB/T 6398 ⾦属材料裂纹扩展试验⽅法GB/T 4337 ⾦属旋转弯曲疲劳试验⽅法GB/T 7733 ⾦属旋转弯曲腐蚀疲劳试验⽅法GB/T 12443 ⾦属扭应⼒疲劳试验⽅法GB/T 7732 ⾦属材料表⾯裂纹拉伸试样断裂韧度试验⽅法GB/T 21143 ⾦属材料准静态断裂韧度的统⼀试验⽅法GB/T 24176 ⾦属材料疲劳试验数据统计⽅案与分析⽅法GB/T 2107 ⾦属⾼温旋转弯曲疲劳试验⽅法GB/T15248 ⾦属材料轴向等幅低循环疲劳试验⽅法GB/T10622 ⾦属材料滚动接触疲劳试验⽅法⼆、相关试验机汇总:1.轴向疲劳试验通常采⽤电液伺服疲劳试验机。
这⼀类试验机频率通常在0.01-50Hz以内,也可以达到100Hz,设备采⽤液压作动器进⾏加载,设备载荷通常在10kN~1000kN之间(负荷系列数为:10、20、50、60、100、200、250、500、600、1000、2000),轴向电液伺服疲劳试验机通常配备的是楔形液压拉伸夹具,但根据试样情况也可配备其他的夹具。
电液伺服疲劳试验机技术参数

电液伺服疲劳试验机技术参数一、招标设备20KN电液伺服疲劳试验机1台。
★该产品须为国内知名品牌厂家生产的市场成熟稳定产品。
设备生产厂家必须具有该设备的制造计量器具许可证资质及通过相应质量体系认证;必须具有同型号设备在近3年内案例至少五家以上(提供合同复印件。
二、产品适用标准JJG 556-2011《轴向加荷疲劳试验机》、GB/T3075、HB5287、ASTM E647、ASTM E399、GB/T4161、GJB715、NASM1312标准等。
三、应用范围该设备主要用于对各种金属或非金属材料及零部件进行疲劳试验、断裂力学性能试验、拉压弯剪等静态性能试验等。
可配备高温炉、高低温环境箱等还可进行多种环境条件下的动静态力学性能试验。
四、主要技术指标1)最大试验力:±20kN。
2)最大动态幅值:20kN。
3)有效测量范围:2%~100%F.S。
4)静态试验力示值相对误差:≤±0.5%;动态试验力示值相对误差:≤±1%。
5)作动器行程(位移):±50mm。
6)位移测量精度:≤±0.3% F.S;位移分辨率:≤0.001mm。
7)变形测量精度:≤示值的±0.5%,有效范围为满量程的2%~100%F.S。
8)试验波形:正弦波、三角波、方波、斜波、梯形波、锯齿波、半正弦波、脉动三角波、脉动锯齿波、脉冲波、自定义波、组合波等;频率范围为0.001Hz ~ 50Hz;分辨率≤0.001Hz。
★9)最大载荷20kN,振幅±2mm时,可达到的最大频率不小于4Hz。
10)最大记数范围:109-1;计数误差:≤±1次。
11)控制模式:具有位移、负荷、变形三种控制模式,且模式可平滑转换。
★12)受力同轴度:≤6%。
★13)夹具形式:采用液压夹具,配置棒材及板材夹块各1套,三点弯家具1套。
★14)夹头间距:700mm。
并带T型槽工作台(有效工作长度≥800mm、宽度≥600mm)。
电液伺服疲劳试验机技术参数
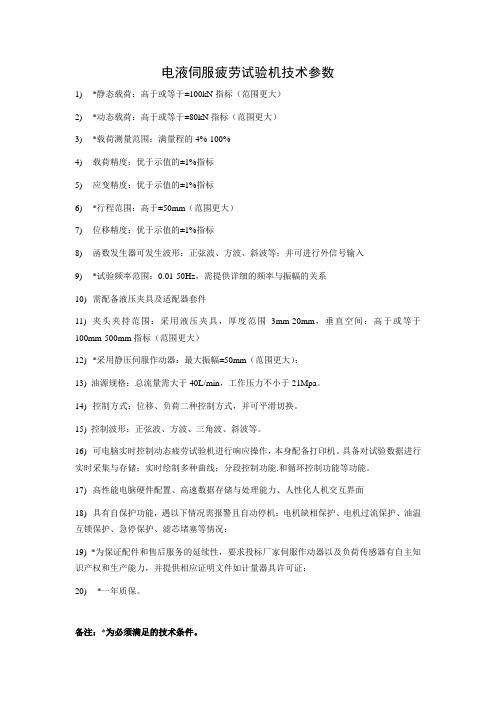
电液伺服疲劳试验机技术参数1) *静态载荷:高于或等于±100kN指标(范围更大)2) *动态载荷:高于或等于±80kN指标(范围更大)3) *载荷测量范围:满量程的4%-100%4) 载荷精度:优于示值的±1%指标5) 应变精度:优于示值的±1%指标6) *行程范围:高于±50mm(范围更大)7) 位移精度:优于示值的±1%指标8) 函数发生器可发生波形:正弦波、方波、斜波等;并可进行外信号输入9) *试验频率范围:0.01-50Hz,需提供详细的频率与振幅的关系10) 需配备液压夹具及适配器套件11) 夹头夹持范围:采用液压夹具,厚度范围3mm-20mm,垂直空间:高于或等于100mm-500mm指标(范围更大)12) *采用静压伺服作动器:最大振幅±50mm(范围更大);13) 油源规格:总流量需大于40L/min,工作压力不小于21Mpa。
14) 控制方式:位移、负荷二种控制方式,并可平滑切换。
15) 控制波形:正弦波、方波、三角波、斜波等。
16) 可电脑实时控制动态疲劳试验机进行响应操作,本身配备打印机。
具备对试验数据进行实时采集与存储;实时绘制多种曲线;分段控制功能.和循环控制功能等功能。
17) 高性能电脑硬件配置、高速数据存储与处理能力、人性化人机交互界面18) 具有自保护功能,遇以下情况需报警且自动停机:电机缺相保护、电机过流保护、油温互锁保护、急停保护、滤芯堵塞等情况;19) *为保证配件和售后服务的延续性,要求投标厂家伺服作动器以及负荷传感器有自主知识产权和生产能力,并提供相应证明文件如计量器具许可证;20) *一年质保。
备注:*为必须满足的技术条件。
电液伺服疲劳试验机技术参数

电液伺服疲劳试验机技术参数一、招标设备20KN电液伺服疲劳试验机1台。
★该产品须为国内知名品牌厂家生产的市场成熟稳定产品。
设备生产厂家必须具有该设备的制造计量器具许可证资质及通过相应质量体系认证;必须具有同型号设备在近3年内案例至少五家以上(提供合同复印件。
二、产品适用标准JJG 556-2011《轴向加荷疲劳试验机》、GB/T3075、HB5287、ASTM E647、ASTM E399、GB/T4161、GJB715、NASM1312标准等。
三、应用范围该设备主要用于对各种金属或非金属材料及零部件进行疲劳试验、断裂力学性能试验、拉压弯剪等静态性能试验等。
可配备高温炉、高低温环境箱等还可进行多种环境条件下的动静态力学性能试验。
四、主要技术指标1)最大试验力:±20kN。
2)最大动态幅值:20kN。
3)有效测量范围:2%~100%F.S。
4)静态试验力示值相对误差:≤±0.5%;动态试验力示值相对误差:≤±1%。
5)作动器行程(位移):±50mm。
6)位移测量精度:≤±0.3% F.S;位移分辨率:≤0.001mm。
7)变形测量精度:≤示值的±0.5%,有效范围为满量程的2%~100%F.S。
8)试验波形:正弦波、三角波、方波、斜波、梯形波、锯齿波、半正弦波、脉动三角波、脉动锯齿波、脉冲波、自定义波、组合波等;频率范围为0.001Hz ~ 50Hz;分辨率≤0.001Hz。
★9)最大载荷20kN,振幅±2mm时,可达到的最大频率不小于4Hz。
10)最大记数范围:109-1;计数误差:≤±1次。
11)控制模式:具有位移、负荷、变形三种控制模式,且模式可平滑转换。
★12)受力同轴度:≤6%。
★13)夹具形式:采用液压夹具,配置棒材及板材夹块各1套,三点弯家具1套。
★14)夹头间距:700mm。
并带T型槽工作台(有效工作长度≥800mm、宽度≥600mm)。
疲劳试验机技术参数
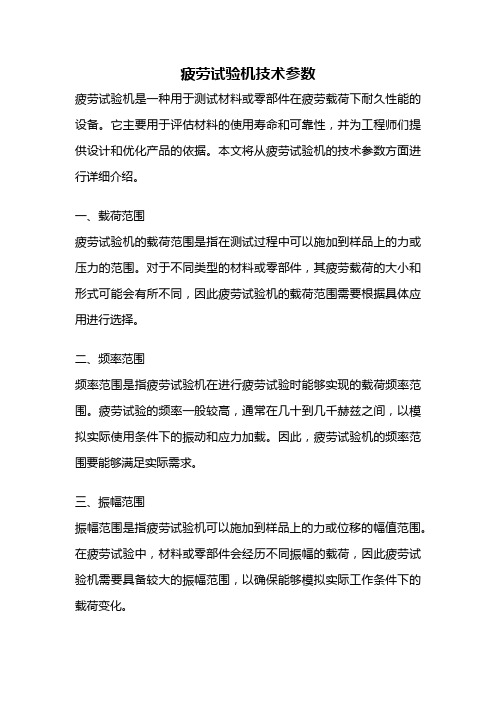
疲劳试验机技术参数疲劳试验机是一种用于测试材料或零部件在疲劳载荷下耐久性能的设备。
它主要用于评估材料的使用寿命和可靠性,并为工程师们提供设计和优化产品的依据。
本文将从疲劳试验机的技术参数方面进行详细介绍。
一、载荷范围疲劳试验机的载荷范围是指在测试过程中可以施加到样品上的力或压力的范围。
对于不同类型的材料或零部件,其疲劳载荷的大小和形式可能会有所不同,因此疲劳试验机的载荷范围需要根据具体应用进行选择。
二、频率范围频率范围是指疲劳试验机在进行疲劳试验时能够实现的载荷频率范围。
疲劳试验的频率一般较高,通常在几十到几千赫兹之间,以模拟实际使用条件下的振动和应力加载。
因此,疲劳试验机的频率范围要能够满足实际需求。
三、振幅范围振幅范围是指疲劳试验机可以施加到样品上的力或位移的幅值范围。
在疲劳试验中,材料或零部件会经历不同振幅的载荷,因此疲劳试验机需要具备较大的振幅范围,以确保能够模拟实际工作条件下的载荷变化。
四、控制方式疲劳试验机的控制方式主要有两种,即位移控制和力控制。
在位移控制模式下,试验机根据预设的位移曲线对样品施加力,以实现特定的疲劳载荷;而在力控制模式下,试验机会根据预设的力值对样品施加位移,以实现特定的疲劳载荷。
根据具体需求,选择适合的控制方式非常重要。
五、试验台尺寸试验台尺寸是指疲劳试验机用于放置样品的工作台面的尺寸。
试验台尺寸的选择应根据样品的大小和形状来确定,以确保样品能够被稳定地放置在试验台上,并且能够受到均匀的载荷作用。
六、试验空间试验空间是指疲劳试验机内部用于放置样品的空间大小。
试验空间的大小需要根据样品的尺寸和形状来确定,以确保样品在试验过程中有足够的空间进行振动或变形,并且不会与试验机的其他部件发生碰撞。
七、安全保护措施疲劳试验机在进行试验时需要保证操作人员的安全。
因此,疲劳试验机通常配备有多种安全保护措施,如安全门、紧急停止按钮、过载保护等,以保障试验过程的安全性。
总结起来,疲劳试验机的技术参数包括载荷范围、频率范围、振幅范围、控制方式、试验台尺寸、试验空间以及安全保护措施等。
电液伺服疲劳试验机:材料耐久性的“耐力测试者”

电液伺服疲乏试验机:料子耐久性的“耐力测试者”在料子科学和工程领域,对料子和结构在反复载荷作用下的耐久性进行评估是一项紧要的技术任务。
电液伺服疲乏试验机作为一种先进的料子耐久性测试设备,以其优化的试验原理、高精度和强大的试验本领,在料子和结构耐久性研究中发挥侧紧要作用。
本文将介绍该产品的原理、用途及其在料子科学中的应用。
电液伺服疲乏试验机紧要用于对料子和结构进行反复载荷作用下的耐久性测试。
它的工作原理基于电液伺服掌控技术。
试验机通过电液伺服掌控系统,精准明确掌控试验过程中的载荷、位移和频率等参数。
在测试过程中,试样受到周期性的载荷作用,模拟实际工作环境中的疲乏载荷。
通过监测试样的响应,如应变、位移和裂纹扩展等,可以评估料子和结构的耐久性。
该产品具有以下特点:1.高精度:该产品采用高精度的电液伺服掌控系统,能够精准明确掌控试验过程中的载荷、位移和频率等参数,满足各种耐久性测试的需求。
2.强大的试验本领:该产品通常具有较大的载荷范围和试验频率范围,能够模拟各种多而杂的工作环境,满足不同料子和结构的耐久性测试需求。
3.多种试验模式:该产品可以进行各种疲乏试验,如正弦波疲乏试验、三角波疲乏试验、随机载荷疲乏试验等,满足不同试验需求。
4.数据手记和分析:该产品通常配备有数据手记和分析系统,能够实时监测试样的响应,并进行数据分析和处理,供应认真的试验结果。
5.易于操作和维护:该产品操作界面友好,操作简便,便于非专业人员使用。
同时,结构紧凑,便于安装和维护。
总之,电液伺服疲乏试验机作为一种先进的料子耐久性测试设备,具有高精度、强大的试验本领、多种试验模式、数据手记和分析以及易于操作维护等优点。
它为料子科学和工程领域供应了一种可靠的耐久性测试手段,有助于评估料子和结构的耐久性,优化设计和提高工程安全性。
随着科技的不绝进步和料子科学的需求日益增长,该产品的应用将越来越广泛,为料子研究和工程发展供应强大的支持。
电液伺服疲劳试验机工作原理
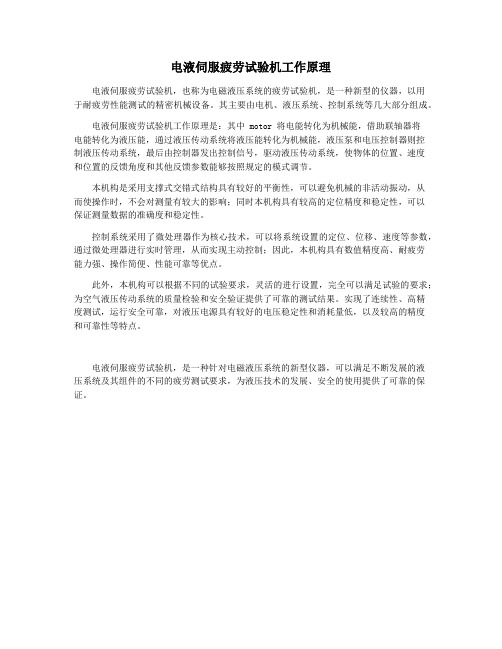
电液伺服疲劳试验机工作原理
电液伺服疲劳试验机,也称为电磁液压系统的疲劳试验机,是一种新型的仪器,以用
于耐疲劳性能测试的精密机械设备。
其主要由电机、液压系统、控制系统等几大部分组成。
电液伺服疲劳试验机工作原理是:其中 motor 将电能转化为机械能,借助联轴器将
电能转化为液压能,通过液压传动系统将液压能转化为机械能,液压泵和电压控制器则控
制液压传动系统,最后由控制器发出控制信号,驱动液压传动系统,使物体的位置、速度
和位置的反馈角度和其他反馈参数能够按照规定的模式调节。
本机构是采用支撑式交错式结构具有较好的平衡性,可以避免机械的非活动振动,从
而使操作时,不会对测量有较大的影响;同时本机构具有较高的定位精度和稳定性,可以
保证测量数据的准确度和稳定性。
控制系统采用了微处理器作为核心技术,可以将系统设置的定位、位移、速度等参数,通过微处理器进行实时管理,从而实现主动控制;因此,本机构具有数值精度高、耐疲劳
能力强、操作简便、性能可靠等优点。
此外,本机构可以根据不同的试验要求,灵活的进行设置,完全可以满足试验的要求;为空气液压传动系统的质量检验和安全验证提供了可靠的测试结果。
实现了连续性、高精
度测试,运行安全可靠,对液压电源具有较好的电压稳定性和消耗量低,以及较高的精度
和可靠性等特点。
电液伺服疲劳试验机,是一种针对电磁液压系统的新型仪器,可以满足不断发展的液
压系统及其组件的不同的疲劳测试要求,为液压技术的发展、安全的使用提供了可靠的保证。
电液伺服疲劳试验机技术指标

电液伺服疲劳试验机技术指标1. 引言好嘛,咱们今天聊聊一个非常重要的设备,那就是电液伺服疲劳试验机。
别看名字长得像个舌头打结的怪物,它其实是在各种材料和零件的疲劳测试中扮演着超级英雄的角色。
它可以帮助我们了解材料在长时间使用下的表现,像是给这些材料做个体检,看看它们到底能扛多久。
这种设备在航空、汽车、建筑等领域都非常关键,咱们可以说它是“千里之行,始于足下”的重要一环。
2. 电液伺服疲劳试验机的基本功能2.1 测试能力电液伺服疲劳试验机的主要功能就是进行疲劳测试,简单来说,就是模拟材料在实际使用中可能遇到的各种压力和拉力。
你想想,如果一个材料在使用过程中像打篮球一样,不停地被拉扯、扭转,最后是不是得折腾出点问题来?这时候,试验机就派上用场了。
它可以施加多种形式的力,比如循环加载、恒定加载等等,让你看到材料在压力下的“真实反应”。
2.2 控制系统这玩意儿的控制系统可是非常智能的哦!电液伺服技术结合了电子控制和液压驱动,这让它可以非常精确地控制施加的力和位移。
听起来高大上吧?实际上,它的操作界面也很友好,用户只需简单设置一下参数,试验机就会自动运行。
就像玩游戏一样,按下开始键,剩下的就让它自己搞定!这可真是“省心省力”的好帮手。
3. 技术指标3.1 载荷范围说到技术指标,最重要的就是载荷范围了。
一般来说,这种试验机的载荷范围可以从几百牛顿到几百千牛不等,具体要看你的需求。
简单来说,就是它能测多重的东西。
比如说,要测试一个汽车零件的承受能力,那当然得选一个能够施加足够力量的试验机。
这就像给你的体重秤选电池,得有足够的“马力”才能支持。
3.2 循环频率再说说循环频率,这可是个重要的参数。
它代表了试验机在单位时间内能进行多少次加载和卸载,一般是几赫兹到几十赫兹不等。
听起来可能有点复杂,但其实就像咱们上健身房,频率高了,锻炼效果就好,疲劳测试也是如此。
高频率能更快地模拟材料的使用情况,帮助我们快速找到潜在的问题。
电工英语词汇汉英互译(字母E)

electrohydraulic control,电液伺服阀
electrolysis humidity transducer[sensor],电解式湿度传感器
electrolytic cell,电解池
electrolytic hygrometer,电解湿度计
electrochemical analysis,电化学分析(法)
electrochemical analyzer,电化学式分析器
electrochemical transducer[sensor],电化学式传感器
electrode,电极
electrode potential,电极电位
electrode signal,电极信号
electromohic transducer[sensor],肌电图(EMG)传感器
electron beam exposure apparatus,电子束曝光机
electron beam processing machine,电子束加工机
electo-hydraulic servocontrolled fatigue testing machine,电液伺服疲劳试验机electro-optical
distance meter,光电测距仪
electroacoustic transducer,电声换能器
electroacoustical reciprocity theorem,电声互易定理
electric actuator,电动执行机构
electric contact liquid-in-glass thermometer,电接点玻璃温度计
谐振式数字化高频疲劳试验机[实用新型专利]
![谐振式数字化高频疲劳试验机[实用新型专利]](https://img.taocdn.com/s3/m/f226e56cb9d528ea80c77950.png)
专利名称:谐振式数字化高频疲劳试验机专利类型:实用新型专利
发明人:宋一兴,由广珍,张立伟
申请号:CN200420011681.3
申请日:20040319
公开号:CN2694257Y
公开日:
20050420
专利内容由知识产权出版社提供
摘要:一种谐振式数字化高频疲劳试验机,属于测试技术领域。
将电机固定在托盘上,电机连接有减速器,减速器上装有软轴,软轴通过传动带连接丝杆,在托盘的四个角上分别装有减振弹簧,减振弹簧的顶端固定在台面底部。
工作时,电机通过减速器、软轴、传动带带动丝杆旋转,使加载轻松、准确。
本实用新型在小载荷条件下能够顺利起动,并且测试精度高,系统质量配比合理。
申请人:长春仟邦测试设备有限公司
地址:130022 吉林省长春市南湖大路2030号
国籍:CN
代理机构:吉林长春新纪元专利代理有限责任公司
代理人:赵正
更多信息请下载全文后查看。
电液谐振式高频疲劳试验台动态特性研究

电液谐振式高频疲劳试验台动态特性研究
白继平;阮健;贾文昂
【期刊名称】《振动与冲击》
【年(卷),期】2013(032)009
【摘要】针对由单出杆液压缸与二位三通2D阀组成的电液谐振式高频疲劳试验台,因单出杆液压缸无杆腔与2D阀相连,有杆腔恒通油源.而2D阀突破常规电液伺服阀频宽极限,具有宽频带、高频响等特点,通过改变阀芯旋转速度及阀口轴向开度,可对系统分别进行变频、变幅控制.对采用2D阀控制技术的电液谐振式高频疲劳试验台建立数学、仿真模型,并对该试验台谐振工况进行仿真与实验研究,结果表明该系统谐振工况输出位移(载荷力)与激振力大,消耗外界功率低.
【总页数】5页(P95-99)
【作者】白继平;阮健;贾文昂
【作者单位】浙江工业大学机械制造及自动化教育部重点实验室,杭州310014;浙江交通职业技术学院海运学院,杭州311112;浙江工业大学机械制造及自动化教育部重点实验室,杭州310014;浙江工业大学机械制造及自动化教育部重点实验室,杭州310014
【正文语种】中文
【中图分类】TH81
【相关文献】
1.电磁谐振式高频疲劳试验系统动态特性分析 [J], 陈蓓;姜伟;高红俐;云燕;王建淼
2.新型电液激振试验台的高频特性研究 [J], 程辉;俞浙青;阮健;邢彤;白继平
3.立式电液疲劳试验机动态特性研究 [J], 白继平
4.基于位置控制的电液伺服弹簧疲劳试验台液压系统仿真研究 [J], 周恩涛;林君哲;乔建基;丛日
5.基于钢板弹簧疲劳检测的新型汽车结构试验台电液比例控制系统动态特性研究[J], 郑默思
因版权原因,仅展示原文概要,查看原文内容请购买。
谐振式电液疲劳试验机的设计毕业设计论文

本科毕业设计(论文) 题目:谐振式电液疲劳试验机的设计学院:机械学院专业:机械工程及自动化班级: 2008级 7 班学号: 200810310115 学生姓名:刘申指导老师:阮键提交日期: 2012年5月1日浙江工业大学学位论文原创性声明本人郑重声明:所提交的学位论文是本人在导师的指导下,独立进行研究工作所取得的研究成果。
除文中已经加以标注引用的内容外,本论文不包含其他个人或集体已经发表或撰写过的研究成果,也不含为获得浙江工业大学或其它教育机构的学位证书而使用过的材料。
对本文的研究作出重要贡献的个人和集体,均已在文中以明确方式标明。
本人承担本声明的法律责任。
作者签名:日期:年月日学位论文版权使用授权书本学位论文作者完全了解学校有关保留、使用学位论文的规定,同意学校保留并向国家有关部门或机构送交论文的复印件和电子版,允许论文被查阅和借阅。
本人授权浙江工业大学可以将本学位论文的全部或部分内容编入有关数据库进行检索,可以采用影印、缩印或扫描等复制手段保存和汇编本学位论文。
本学位论文属于1、保密□,在______年解密后适用本授权书。
2、不保密□。
(请在以上相应方框内打“√”)作者签名:日期:年月日导师签名:日期:年月日谐振式电液疲劳试验机的设计学生姓名:刘申指导教师:阮健教授浙江工业大学机电学院摘要在工业生产中,人们发现在交变应力的作用下,机械零件往往会在远低于材料强度极限的情况下发生破坏,这就是疲劳失效。
疲劳失效已经成为正常工作状况下零件、材料的主要失效形式。
零件材料的使用性能与材料的疲劳特性密切相关。
用于研究材料疲劳特性的试验成为疲劳试验。
疲劳试验已经成为为工程技术领域的基本试验,而疲劳试验机是研究材料疲劳特性的基本设备。
疲劳试验机有很多种类,其中电液疲劳试验机是其中很重要的一类。
电液疲劳试验机具有响应速度快、输出功率大、测量和控制精度高等特点,已经在航空、航天、军事、冶金、交通、工程机械等领域得到了广泛应用。
装载机结构件疲劳试验机的设计

装载机结构件疲劳试验机的设计蔡应强;肖龙海【摘要】In this work, electro-hydraulic servo technology and programmable logic controller (PLC) technology were used to design the special fatigue strength test system to find the stress weak region of loader structure components, optimize the structure designing, and improve the fatigue life,The system adopted the test scheme with frontand side loading.The touch screen and PLC controller can remotely control the two servo hydraulic cylinder motion to simulate the load of structure components.The test system can run 24 hours unattended for a long time, and meet the requirements of different types of structure components of loaders.The results of experiment show that the fatigue testing machine can run stable and reliably.%为了查找装载机结构件应力薄弱部位,优化结构设计、提高疲劳寿命,采用电液伺服技术和可编程逻辑控制器(PLC)控制技术设计一套专门测试结构件疲劳强度的试验系统.该系统采用整机正面加侧面的加载方案,由触摸屏和PLC控制器远程控制2个伺服液压缸动作以模拟结构件受载,可实现24 h无人值守试验,适用于各种型号装载机结构件的疲劳试验.试验结果表明:该试验机运转平稳,可靠性高.【期刊名称】《华侨大学学报(自然科学版)》【年(卷),期】2017(038)002【总页数】6页(P141-146)【关键词】疲劳试验机;装载机;结构件;电液伺服;远程控制【作者】蔡应强;肖龙海【作者单位】集美大学轮机工程学院, 福建厦门 361021;华侨大学机电及自动化学院, 福建厦门 361021;福建省船舶与海洋工程重点实验室, 福建厦门 361021;集美大学轮机工程学院, 福建厦门 361021;华侨大学机电及自动化学院, 福建厦门361021;福建省船舶与海洋工程重点实验室, 福建厦门 361021【正文语种】中文【中图分类】TH871.3装载机工况复杂,车架和动臂等结构件在作业过程中承受着动力装置传递的力矩载荷、工作阻力载荷、恶劣路况的冲击载荷等,在应力薄弱部位易发生疲劳破坏[1].目前,在设计阶段,一般以最危险载荷为设计载荷,以有限单元法寻找最大应力区与最大变形区,以便在结构设计上增强薄弱部位[2].而结构件的疲劳失效在设计阶段难以处理,只有通过大量市场反馈信息改进[3],成本高、周期长、数据滞后,不利于新机型的推广应用.考虑到装载机作业载荷以低频、大振幅、重载荷为主,本文设计电液驱动型疲劳试验机,通过模拟其典型工况下的负载,获取试验样机结构件的应力分布数据和疲劳失效数据,为发现设计缺陷和结构优化提供可靠依据. 1.1 试验机结构方案轮式装载机的工作循环包括插入、铲装、举升、卸载4个作业过程,需要依次克服插入阻力、转斗阻力矩、掘起阻力和卸载阻力等[4-5].上述作业阻力直接作用于铲斗,并通过铰链传递到动臂、车架等结构件.由于路况复杂、随机作业载荷波动剧烈等原因,车架、动臂等结构件容易发生疲劳断裂.王继新等[6]对正载、左偏载、右偏载、满载转弯、一后轮离地、满载制动、满载运输、满载动臂平伸、满载举升最高位置等17种工况做了应力对比分析.结果表明:各工况下结构件应力较大的位置基本相同,其中,应力较大的工况是正载铲掘作业、偏载铲掘作业及有侧向力铲掘的作业工况.以此为出发点模拟受载,考虑到台架试验的可行性,将装载机整车(去除轮胎和驾驶室)连同底盘用带铰接的支撑钢板安装于T型槽平台上(图1),并使整车机构可以绕支点1和2旋转.采用电液伺服加载的方式,设计一套液压系统和控制系统,控制液压缸3以一定的方式加载于铲斗正面,液压缸4(图中未画出)加载于铲斗侧面,以模拟铲斗的水平和侧向受载.1.2 加载力分析以某ZL50型装载机为例,其工作机构是由铲斗、动臂、摇臂、拉杆、机架、动臂液压缸缸套、动臂液压缸活塞杆、铲斗液压缸缸套和铲斗液压缸活塞杆等构件组成的空间机构,且左右对称,两侧铲斗液压缸、动臂液压缸、拉杆、摇臂液压缸的运动学、动力学特性完全一致,可简化为平面机构[7-8].为确定加载力的大小和方向,绘制平面机构运动简图,如图2所示.图2中:Fs为拉杆的拉力,N;Fx为水平反作用阻力,N;Fy为垂直反作用阻力,N;Fbu为摇臂液压缸拉力,N;Fbo为动臂液压缸拉力,N;L1,L2,L3为Fs,Fx,Fy到G点的力臂;L4,L5为Fs,Fbu到D点的力臂;L6,L7,L8,L9为Fy,Fx,Fbu,Fbo到A点的力臂;G为装载机净质量,kg.根据装载机动臂与铲斗在G点、D点、A点的力矩平衡,可得装载机垂直反作用阻力Fy,即式(1)中:d为动臂液压缸通孔直径;P为动臂液压缸两腔压力差.由式(1)可得装载机水平反作用阻力Fx与垂直反作用阻力Fy的关系式,即Fy=140.2-0.627 3·Fx.采用文献[9]提供的装载机作业工况铲斗受力计算方法,得到正载最大水平驱动力Fx,3为104.2 kN,则根据式(2)可得Fx,3为74.8 kN.偏载水平驱动力98.3 kN,侧向力41.7 kN.疲劳寿命试验中,正载情况下液压缸3的加载力=128.3 kN,液压缸3与水平面倾角α3=arctan =35.7°;而偏载情况下液压缸3的加载力为125.8 kN,倾角为38.6°,侧载液压缸4的加载力为41.7 kN. 试验样机参数,如表1所示.1.3 加载频次参考国外装载机最低期望使用寿命数据[1],各斗容量装载机最低期望寿命如表2所示.以ZL50型轮式装载机为例,其斗容量为3 m3,其期望使用寿命为8 000 h,则疲劳寿命试验中载荷总加载次数N为.式(3)中:T为期望使用寿命,取8 000 h;t为单个铲装循环用时,视作业形式不同通常在30~50 s之间,取40 s.统计数据表明,在实装作业中,平均每5次铲装循环发生1次偏载,其中,偏载同时承受侧载约占1/4[6].因此,正载情况加载57.6万次,偏载情况加载10.8万次,偏载同时承受侧载情况加载3.6万次.疲劳试验机液压系统主要为加载试验提供动力,根据图1所示的结构和加载试验所需达到的性能,设计疲劳试验机液压系统,如图3所示.图3中:M1,M2为变频电机;M3,M4为电机;C1~C8为手动球阀;XJ1~XJ4为行程接近开关;YV1~YV11为电磁阀线圈.疲劳试验机液压系统的主要技术参数,如表3所示,可实现泵组空载启动、两级调压、手动流量调节、循环过滤、多点测压、失压监测等功能.为确保试验机实现24 h无人值守正常运转,对变量柱塞泵、电液控制阀、电磁换向阀及压力传感器都采用冗余设计,控制系统可根据传感器、继电器、行程接近开关的反馈数据判断系统工作状况,如检测到故障,可根据预设方案自动切换备用泵组和阀组工作.经设计计算,选定正面加载缸最大行程300 mm,内径160 mm,活塞杆直径90mm;侧面加载缸最大行程200 mm,内径125 mm,活塞杆直径70 mm.加载泵采用A7V55型变量柱塞泵,公称排量55 mL·r-1.在额定压力16 MPa下,最大正面加载力可达321.5 kN,侧面加载力可达196.3 kN,通过调整系统压力、流量和泵的排量,可满足装载机各种结构件疲劳试验需要.试验机控制系统主要用于实现按预定动作对被试结构件反复加载/卸载预定次数,同时监测试验过程中的各种信号,进行故障自动诊断及故障处理,保证系统安全运行及试验的顺利进行,可实现本地和远程独立调试和试验.本地控制采用 MCC控制柜实现,可完成本地/远程控制转换、液压泵启/停、加载/卸荷、急停、异常报警等,主要实现系统各设备的功能测试,为远程自动控制做准备.远程控制采用触摸屏+PLC控制器的上下位机结构.触摸屏提供人机交互,完成试验参数设置、状态监测和显示、报警信息显示及操作指令下达等功能;PLC完成系统逻辑控制,实时采集液压系统状态参数、进行自动实验、故障诊断、故障处理及实验数据的记录.本地控制和远程控制均可通过对各电磁阀的控制独立进行系统调试和试验.根据要求,各工况下的电磁阀线圈通电规则,如表4所示.表4中:YV3/YV4和YV5/YV6,YV7/YV8和YV9/YV10形成互锁,同一时刻只有一个通电.在调试和试验过程中,均应遵循表4的规则.远程操纵台包括触摸屏、操作按钮、开关、指示灯等,工作界面如图4所示.采用西门子Smart1000型触摸屏,具有高分辨率宽屏显示、人机界面友好、经济实用、性价比高等特点[10],其开发工具为WinCC flexible.通过触摸屏设置试验参数后,可操作触摸屏上的虚拟开关,也可通过操纵台上的开关按钮进行试验.采用西门子S7-226CN型PLC控制器(含24路DI和16路DO,继电器输出),并扩展了8路数字量输出模块EM222CN(继电器型)和4路模拟量输入模块EM231CN.控制系统硬件结构,如图5所示.触摸屏HMI软件功能模块,如图6所示.触摸屏的初始工作界面(图4左侧),包括手动调试、自动实验和报警信息模块.手动调试模块,用于进行试验系统各元件的手动控制,以确定信号传递是否正常,元件能否正常工作,为进行自动实验做准备,如图7所示.自动实验模块用于进行自动加载试验,包括参数设置、实验过程、报警信息、故障恢复等4个子模块,如图8所示.故障诊断与处理是系统的重要功能,是保证24 h无人值守自动实验的关键.故障信号的来源主要包括液位继电器LJ1~LJ2,电机热继电器FR1~FR3,压力继电器PJ1~PJ3,行程接触开关XJ1~XJ4等数字量信号和压力传感器、温度传感器等模拟量信号.故障诊断参数包括主备机组的选择、温度阀值、压力阀值和持续时间等.系统根据这些参数进行故障诊断,并进行机组切换或停机等相应处理.为了验证该疲劳试验机的稳定性和可靠性,对某ZL50型轮式装载机车架-工作机构联合体进行加速疲劳寿命试验.根据加载力Ft的分析结果,偏载情况下液压系统正面加载压力调定为6.3 MPa,侧面加载压力调定为3.4 MPa,泵排量设为40 mL·r-1,取加速系数为5,则加载周期为8 s.若每天24 h连续等幅加载,完成72万次加载试验需历时66.7 d.鉴于本次试验的目的是为了验证系统的稳定性和可靠性,为了节省时间,只进行偏载、偏载加侧载的试验,按照每3次偏载进行1次偏载加侧载的方式循环加载,试验现场如图9所示.前车架的疲劳裂纹,如图10所示.试验结果表明:偏载试验达到6万次,偏载加侧载达到2万次时,未发现前后车架、动臂等出现疲劳裂纹;继续加载到9万次和3万次后,发现前车架结构出现了两处裂纹,如图10圈中所示(为便于观察,使用了显影剂观测).图10中:裂纹1位于左侧前桥连接板加强肋板顶部焊接处,裂纹2位于左侧翼箱下支撑肋板前端面与内侧板焊接处,均处于应力集中位置.继续加载至10万次和3.3万次时,动臂右外侧耳板焊缝与动臂横梁右下角焊缝出现裂纹;加载至12万次和4万次时,左侧动臂板发生严重断裂破坏,试验终止,共加载约16万次,试验过程稳定.根据上述试验结果和正载与偏载的发生概率,参考加速疲劳寿命试验循环加载次数与装载机使用寿命之间的关系,对被试结构件的疲劳寿命进行反推,可知被试装载机前车架的疲劳寿命为4 400~6 700 h,动臂的疲劳寿命为7 400~8 900 h.按照8 000 h期望使用寿命,可知该试验样机的前车架结构没有达到设计要求.需要指出的是,鉴于条件限制,上述结论是以理论分析和计算数据为加载条件所得出,如能通过外场试验得到装载机各工况下的随机载荷谱,再编成加载谱输入到前述控制系统中,通过加载缸施加于试验样机,则得到的疲劳失效数据更为客观、可靠.以装载机结构件为试验对象,根据装载机作业工况特点,应用电液伺服驱动技术设计结构件疲劳试验机.将机电液一体化技术相结合,采用上下位机的系统结构控制液压系统进行疲劳加载试验;利用传感器技术和自动检测技术,主动监测故障并自动切换备用泵组和阀组,可实现24 h无人值守试验.系统运转稳定,可靠性高,可在实验室环境下模拟装载机结构件在各工况下的随机受载,为装载机结构件的优化设计提供参考依据.【相关文献】[1] 马相明,孙霞,张强.轮式装载机典型作业工况构建与分析[J].山东大学学报(工学版),2015,45(5):82-87.[2] 钟丽萍.基于有限元分析的装载机铲斗结构优化[J].中国工程机械学报,2011,9(1):68-72.[3] 杜宏宇,李济顺,杨芳,等.机械结构件疲劳监测方法及试验装置设计[J].矿山机械,2015(10):116-120.[4] 朱牧之,赵升吨.动态疲劳试验机传动方式的合理性探讨[J].机床与液压,2013,41(13):164-167.[5] 张英爽,王国强,王继新,等.轮式装载机半轴载荷谱编制及疲劳寿命预测[J].吉林大学学报(工学版),2011,41(6):1646-1651.[6] 王继新,沈勇,胡季.基于虚拟零件轮式装载机前车架有限元分析[J].煤矿机械,2010,31(4):93-95.[7] 蔡应强,陈清林,丁旭光.轮式装载机前车架的有限元分析与结构优化[J].华侨大学学报(自然科学版),2016,37(1):27-31.[8] 蔡应强,丁旭光.基于虚拟样机的轮式装载机前车架动态载荷分析[J].集美大学学报(自然科学版),2015,20(6):450-456.[9] 陈树勋,梁光明,李会勋.轮式装载机前车架结构载荷计算、有限元分析与优化设计[J].工程机械,2007,38(6):37-42.[10] 胡俊飞,阮健,李胜,等.电液高频疲劳试验机的控制系统设计研究[J].浙江工业大学学报,2015,43(1):58-61.。
- 1、下载文档前请自行甄别文档内容的完整性,平台不提供额外的编辑、内容补充、找答案等附加服务。
- 2、"仅部分预览"的文档,不可在线预览部分如存在完整性等问题,可反馈申请退款(可完整预览的文档不适用该条件!)。
- 3、如文档侵犯您的权益,请联系客服反馈,我们会尽快为您处理(人工客服工作时间:9:00-18:30)。
Piezoelectric fatigue testing machines and devicesClaude Bathias*Department of Mechanical Engineering,CNAM/ITMA,2rue Conte,75003Paris,France Received 26November 2004;received in revised form 9September 2005;accepted 29September 2005Available online 6May 2006AbstractDuring the 1990s several methods have been developed around the word in order to test specimens at very high fatigue life.In our laboratory an ultrasonic fatigue testing system was designed and built 15years ago to determine crack growth threshold and S –N curve of metals.Those first results were published in ASTM STP 1231(1994),ASTM STP1411(2002)and in proceedings of Fatigue 2002.This paper sums up the progress of such fatigue testing machines and devices from this date.Ó2006Elsevier Ltd.All rights reserved.Keywords:Gigacycle fatigue;Piezoelectric fatigue machines;High frequency devices1.IntroductionFrom an historical point of view it is said that the first ultrasonic fatigue machine was constructed by Mason in the year of 1950.With the development of computer sci-ences several laboratories have to develop their own machines and design practical test borato-ries of Willertz in the US,Stanzl in Austria,Bathias in France,Ishii in Japan and Puskar in Slovakia,are among leading laboratories in this field.Ultrasonic fatigue test machines in these laboratories are not the same,but some components are the same for all machines.Three most important ones are:a high frequency generator that gener-ates 20kHz sinusoidal electrical signals,a transducer that transforms the electrical signal into mechanical vibration,and a control unit.Early ultrasonic fatigue test machines performed only uni-axial (one-dimensional)and constant amplitude tests,and so the control unit and other parts were not very complicated.In the last two decades,pro-gress has been made to extend the ultrasonic fatigue tech-nique to variable amplitude loading conditions,low or high temperature environments,torsional or multiaxial tests,and so on.Thus,designing a modern ultrasonic fati-gue test machine may involve mechanical,electrical,opti-cal,magnetic and thermal considerations.In France,Bathias used a first ultrasonic fatigue test machine in 1967on the principle of Mason [1].As described in an early review paper [2],the rather restrictive uses of the ultrasonic fatigue test method appeared to be partly due to the lack of commercially available test equipment,forcing the individ-ual investigators to work with improvised facilities not readily amenable to standardized experimental conditions.2.Tension–tension and tension–compression fatigue test machinesAs stated above,the common components of an ultra-sonic fatigue test machine must include the following three components:1.A power generator that transforms 50or 60Hz voltage signal into ultrasonic 20kHz electrical sinusoidal signals.2.A piezoelectric (or magnetostrictive)transducer excited by the power generator,which transforms the electrical signal into longitudinal ultrasonic waves and mechanical vibration of the same frequency.3.An ultrasonic horn that amplifies the vibration coming from the transducer in order to obtainthe/locate/ijfatigueInternational Journalof Fatigue0142-1123/$-see front matter Ó2006Elsevier Ltd.All rights reserved.doi:10.1016/j.ijfatigue.2005.09.020*Tel.:/fax:+33140272322.E-mail address:bathias@cnam.fr .required strain amplitude in the middle section of the specimen.These three parts are special devices required for the production of ultrasonic fatigue load.Other ultrasonic machine components may include recording systems and measuring systems.The function of the system in Fig.1is to make the spec-imen vibrate in ultrasonic resonance at one of its longitudi-nal modes.The displacement amplitude reaches its maximum U0at the end of the specimen,which can be measured by means of a dynamic sensor,while the strain excitation in push–pull cycles(load ratio R=À1)attains the maximum in the middle section of the specimen that produces the required high frequency fatigue stress.The information recorded may include ultrasonic cyclic dis-placement amplitude U0,the evolution of the fatigue crack growth,which enables us to determine the fatigue crack growth rate d a/d N,and stress intensity factor K max,calcu-lated by analytical or numerical methods[1].During ultrasonic fatigue tests,the maximum strain val-ues can be measured directly using miniature strain gauges, suitably positioned on the sample surface.The dynamic displacement amplitude at the specimen extremity,U0,is measured by an opticfibre sensor,which permits measurements of the displacement from1to 199.9l m,with a resolution of0.1l m.The magnification factor of stress can then be calculated according to these measurements.For a virgin specimen(without a crack), the vibratory stress and strain can also be determined at the midsection.This maximum strain value thus deter-mined is then confirmed to be accurate by the use of the above-mentioned strain gauge.In addition,a system of video–camera–television has been used for the control of crack initiation and propagation.This system refines events to1/25th of a second and magnifies specimen surface140–200times.Because specimens of ultrasonic fatigue vibrate in reso-nance,a free end is sufficient for symmetric loading condi-tions(R=À1),which avoids the large and cumbersome arrangements for gripping the specimen as often encoun-tered in conventional fatigue testing(Fig.2).If there is a static load,the situation is different.Superposing a mean stress or displacement upon the symmetric tension–compression cycle can create a complex cyclic loading with R>À1.Therefore,an additional horn will be added at another end of the specimen,as shown in Fig.3.This kind of test machine is particularly useful interest to efficiently study fatigue endurance and fatigue crack growth behaviour of materials subjected to elasto-plastic low cycle fatigue loading superposed on vibration stress cycles with high frequency.(See Fig.3.)A generator with a converter composed of six piezo-ceramics is chosen to provide vibration energy.This ultrasonic generator 900BA is made by Branson Ultrasonic Corporation.It has a maximum power of2kW and provides a sinusoidal signal for the converter that is the source of mechanical vibration.This amplifier maintains automatically the intrinsic frequency of the mechanical system in the range of19.5–20.5kHz.The converter,horn and specimen form a mechanical vibration system with four stress nodes(null stress)and three displacement nodes(null displacement) for an intrinsic frequency of20kHz.Here,the stressand Fig.1.Full resonance system in Bathias’laboratory with schematic view of apparatus.C.Bathias/International Journal of Fatigue28(2006)1438–14451439displacement are considered to be longitudinal.In Fig.4,points B,C (connected points),point A and converter top are stress nodes.The specimen centre is a displacement node,and the stress is the maximum there.The horn must vibrate at a frequency of 20kHz.Depending on the specimen loading,the horn is designed so that the displacement is amplified between B and C usu-ally 3–9times.It means that the geometry between B and C must be determined.The finite element method may be required when the geometrical shape is complex.The mechanical system composed of a converter,a horn and a specimen is linear.All stress and displacement fields are linear.It is necessary to measure the amplitude of one of them.3.High temperature test equipmentThe test equipment consists of a heating device in the middle.Fig.5is a photograph of this system for crack growth testing.In the specimen the temperature is constant over the length of 5–6mm.The television images can be recorded on a videocassette during the tests.The fatigue crack growth rate can easily be determined up to the order of 10À9mm/cycle.For the experiments at elevated temper-atures,a high-frequency inductor is used and the testtem-Fig.2.Vibratory stress and displacement field and computer controlsystem.Fig.3.Ultrasonic fatigue superposed on static loading.1440 C.Bathias /International Journal of Fatigue 28(2006)1438–1445perature can reach to1000°C.The computer system has a thermocouple board that can send the temperature ana-logue signal to an A/D converter,so that the computer is able to control heating of the specimen by using a circuit breaker.Because the Young’s modulus decreases at high temper-atures,the resonance length of ultrasonic fatigue specimen will be shorter than that at ambient temperature.For tem-perature sensitive materials,this change must be taken into account.For example,in a crack growth experiment,we usually start crack initiation at ambient temperature with adequate resonance length.Then,by cutting offboth ends, we can obtain the resonance length at high temperature.An early design of ultrasonic fatigue equipment at high temperature can be found in reference[3].The system described there is capable of studying fatigue crack growth rate and fatigue thresholds at22kHz,at elevated tempera-ture of200–500°C in argon environment in heat chamber, and at20°C using water as a coolant.4.Low temperature test equipmentLet us now discuss the possibility of testing materials at low temperature.A system for ultrasonic fatigue tests at cryogenic temperature has also been developed in our lab-oratory[4].In the laboratory,liquid nitrogen,liquid hydro-gen and liquid helium are used to create a cryogenic temperature atmosphere.However,liquefied gasses are expensive,especially liquid helium.The fatigue tests at very low temperature for titanium alloys used in space rockets need a lot of liquefied gas because the tests would take a very long time,if the conventional fatigue testing were employed.This is another advantage of the ultrasonic fati-gue method that can contribute to the reducing testing time considerably.The machine with a computer control system works at20kHz at cryogenic temperatures(77and20K) for studying fatigue behavior of the titanium alloys used in rocket engines.The device consists of three parts:a cryostat,a mechan-ical vibrator and a controlled power generator.Fig.6 shows the principal aspects of this machine,which is sim-pler than a conventional hydraulic machine.The functions of the converter and the horn are the same as in other ultra-sonic fatigue apparatus:the converter changes an elec-tronic signal into a mechanical vibration;the horn plays the role of displacement amplifier.A Dewar cryostat con-tains liquefied gasses to keep the testing temperature constant.Ultrasonic fatigue tests at cryogenic temperatures for load ratio R>À1are also possible by adding a second horn to the other end of the specimen.Another example of low temperature test system is that of Stanzl’s laboratory[5],where a temperature environ-ment of77K is guaranteed by liquidnitrogen.Fig.5.Specimen installed in the machine including measuring and heatingdevices.Fig.6.Low temperature and high frequency fatigue testing machine.C.Bathias/International Journal of Fatigue28(2006)1438–144514415.Thin sheet test equipmentThe geometry of ultrasonic fatigue specimens is usually with either cylindrical or plane form with reduced section in the central part to form a higher stress to accelerate the test process.Theoretically,as the excitation frequency of the machine coincides with one of the resonance frequencies of the specimen,the specimen will vibrate in that fre-quency.To put this theory into practice,however,is not an easy task.On the one hand,thefinishing of specimens to the design requirement is a delicate work.On the other hand,the horn where the specimen is installed may change the real frequency of vibration of the system,if the connection is not well designed.This is the use espe-cially for load ratio R>À1when another horn is neces-sary or when plane specimens are very thin.It was indicated long ago[3]that the use of a two-horn system and a positive constant mean stress is favoured for avoid-ing transverse vibration.A series of thin sheet tests of ferrous materials[6]have been conducted.The purpose is to determine the fatigue strength(or S–N curve)at109cycles and the threshold of cracking at a small propagation speed of10À12m/cycle, both at a stress ratio of R=0.1.The key to the execution of the test is how tofix the thin specimen to the ends of amplifying horns.We cannot use the same kind of setscrew as that used in the attachment of ordinary specimens(spec-imens with the thickness–length ratio of6–8%).Among the methods for linking two steel components,are riveting, bolt jointing,welding and gluing(Fig.7).6.High pressure piezoelectric fatigue machineIt is well known that it is difficult to carry out a fatigue test under high pressure with a conventional machine.The problem comes from the displacement of an actuator through the wall of an autoclave.The use of a piezoelectric fatigue system eliminates this problem because it is easy to get zero displacement at the location where the horn under a pressure crosses the wall of the autoclave.Thus,a high-pressure piezoelectric fatigue machine which works up to300bars has been built in our labora-tory.The machine is shown in Fig.8.Fig.7.Test system of thinsheet.Fig.8.Autoclave description.1442 C.Bathias/International Journal of Fatigue28(2006)1438–1445With this device,it has been shown that hydrogen under a pressure of100bars has an effect on S–N curve of IN718 and of Ti6Al4V at room temperature.7.Ultrasonic fretting fatigueFretting fatigue is generally promoted by high fre-quency,motions vibratory in low amplitude and com-monly occurs in clamped joints and shrunk-on components[7,8].The surface damage produced by fretting can take the form of fretting wear or fretting fatigue where the materials’fatigue properties can be seriously degraded. Fretting fatigue is a combination of fretting and fatigue processes.It involves a number of factors,including mag-nitude and distribution of contact pressure,the amplitude of relative slip,friction forces,surface conditions,contact materials,cyclic frequency and also environment.Great efforts have been made to quantify fretting fatigue in terms of these factors,but limited success has been achieved. More often,fretting fatigue characteristics are studied in the laboratory experimentally by using a contact pad clamped to a fatigue specimen in order to determine S–N curves with fretting and thereby to establish the fatigue strength reduction factor for a particular material.But these studies,generally performed on the conventional ten-sion–compression fatigue machine with a low frequency, have some drawbacks:(1)The slip amplitude of fretting fatigue is usually cou-pled with the fatigue stress and to change the slip amplitude,pads with different gauge length are needed;(2)The frequency is low and is not appropriate to simu-late the high frequency small elastic vibration cycles of mechanical,acoustical or aerodynamical origin.On the other hand,in some industries,such as the automobiles and the railways,the determination of high cyclic fretting fatigue properties up to108or even109cycles is necessary.The experiment is bound to be time-consuming and uneconomical.In our laboratory,an ultrasonic fretting fatigue test technique at a frequency of20kHz has been developed, in which the fretting slip amplitude can be changed without changing the fretting pads.Fig.9shows a schematic dia-gram of an experimental set-up.It consists of two parts. Thefirst is the ultrasonic fatigue test machine,which has been widely used in the fatigue test for both endurance and crack propagation.Each element in the machine is designed to have a resonant frequency about20kHz and an automatic unit maintains the whole system operating at the resonant frequency.The second is afixture to hold the two cylinder pads pressed against the specimen by two springs.The normal contact force is measured and controlled by the displacement of the springs.Moreover, the use of the springs will eliminate a discernible changes in load should wear occur.The whole experimental system is controlled by a PC.The test system has the functions of regulating test parameters,recording the relative slip amplitude,normal force and stress.By changing the position of pads along the specimen axis,the desired value of relative slip ampli-tude can be obtained.The stress of fretting fatigue test is determined by the position of the pads for the loadratio Fig.9.Schematic experimental system for ultrasonic fretting-fatigue.C.Bathias/International Journal of Fatigue28(2006)1438–14451443R=À1.For R>À1,the total stress is the superposition of static stress applied by the traction machine and the dynamic stress of vibration.According to the position of pads in the specimen axis, the displacement that provokes the fretting can be chosen between0.1l m and tens of microns.By a gauge mounted on the specimen at point x i=0,vibration deformation of the specimen can be measured.It is worth recalling that the reason for Mason’s pioneer work on the ultrasonic fatigue machine was to study fret-ting[9].8.Torsion fatigue testingIn a review article,Stanzl indicated that more recently time a new technique and equipment has been developed [10],which allows one to perform torsion fatigue at ultrasonic frequencies.The mechanical parts of this equipment must be designed so that torsion resonance vibration can be generated(Fig.10).As the shear mod-ulus is smaller than Young’s modulus,all vibrating parts, including the specimens,must be smaller in order to obtain the resonance.Besides this difference,theotherFig.10.Piezoelectric torsion test equipment in Bathias’Laboratory.Fig.11.System for ultrasonic fatigue experiments in three-point bending.1444 C.Bathias/International Journal of Fatigue28(2006)1438–1445experimental details,such as amplitude measurement and control are much the same as those for the axial ultra-sound fatigue loading.The superposition of axial load is possible and has been investigated in measurements on ceramic materials.Superposition of small compressive loads leads to a lifetime twice as long as that of pure cyclic20kHz torsion loads because of the increased fric-tion forces[10,11].9.Three-point bending fatigue testingThe three-point bending ultrasonic fatigue testing sys-tem developed in the Bathias’laboratory is illustrated in Fig.11.This system was developed for testing certain aluminium alloy based metal-matrix composites used in automobile industry or brittle materials such as ceramics or tita-nium–aluminium alloys.The system containing generator, converter,booster,acoustic horn and specimen is con-trolled by a personal computer.A static load or a static dis-placement is introduced with a tensile testing machine through the booster.Thus,the piezoelectric fatigue machine bending is able to work from R=0.1to R=0.5 and beyond,at20kHz.The maximum displacement in the middle of the three-point bending specimen is of the order of30l m.An advantage of this technique is the small size of the specimen,less than1inch!10.ConclusionsDuring the1990s,several devices have been designed using piezoelectric converters working at20or30kHz. Several advantages have been underlined:•This new method is recommended to study the gigacycle fatigue and the threshold regime.•The duration of a test is at least400times shorter than with a conventional machine.It saves money.•The piezoelectric fatigue machines are able to work at negative R ratio and very high R ratio.•This system is able to operate at high temperature,cryo-genic temperature,high gas pressure,fretting-corrosion, torsion and three-point bending. AcknowledgementsThe author is grateful for many comments and discus-sions from Professor PC,Paris.References[1]Wu,T,Bathias C.Contract DRET No.8707101,ITMA/CNAM;1991.[2]Bathias C,de Monicault JM,Baudry G.Automated piezoelectricfatigue machine for severe environments.ASTM STP 2002;1411:3–15.[3]Stanzl S et al.Ultrasonic Fatigue,Fatigue1996;96:1887–98.[4]Ebara R.Corrosion fatigue in practical problems.In:Nisitani H,p,and Exp Fract :Comp.Mech.Publ.;1994.p.347–76.[5]Huo T.Ultrasonic fatigue of Ti and alloys at cryogenic temperature,the`se de doctorat,CNAM;1996.[6]Buchinger L,Stanzl S,Laird C.Dislocation structures produced bylow-amplitude fatigue of copper single crystals at77K.Philos Mag A 1990;62(6):633–51.[7]Wang Q,Bathias C.Re´alisation d’un syste`me de fatigue vibratoire surtoˆles minces,Partie I:Conception et mise au point,Contrat Renault-Rapport96-2,ITMA/CNAM;1996.[8]Lindley TC.Fretting Fatigue in Engineering Alloys.Int J Fatigue1981;19(s1):s39–49.[9]Mason e of high amplitude strains in studying wear andultrasonic fatigue in metals.In:Well JM,Buck Roth OLD,Tien JK, editors.Ultrasonic fatigue,proceedings of thefirst international conference on fatigue and corrosion fatigue up to ultrasonic frequencies.(PA)USA:The Metallurgical Society of AIME;1982.p.87–102.[10]Stanzl S.Fatigue testing at ultrasonic frequencies.J Soc Environ Eng1986;25(1):11–6.[11]Mayer HR,Tschegg EK,Stanzl-Tschegg S.High cycle fatiguemeasurements on ceramic materials in combined loading.In:Fourth international conference on biaxial and multiaxial fatigue.Paris: ESIS;1994.p.357–8.C.Bathias/International Journal of Fatigue28(2006)1438–14451445。