射线评片技巧(一):气孔、夹渣、夹钨射线底片影像特点讲课稿
射线检测底片上各种影像的识别 后附评片口诀
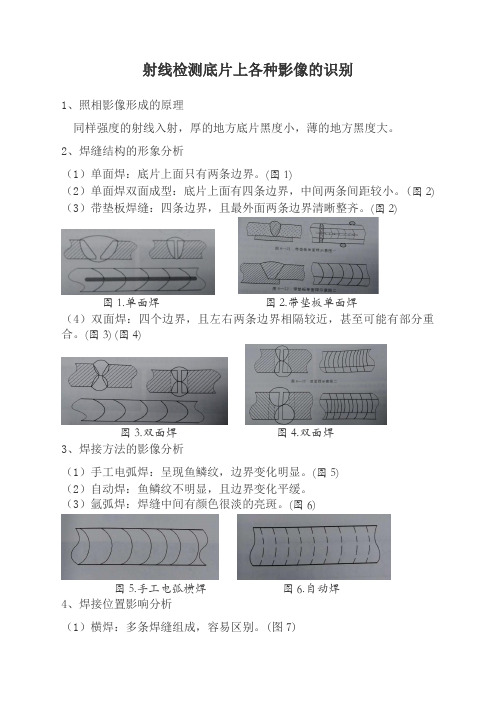
射线检测底片上各种影像的识别1、照相影像形成的原理同样强度的射线入射,厚的地方底片黑度小,薄的地方黑度大。
2、焊缝结构的形象分析(1)单面焊:底片上面只有两条边界。
(图1)(2)单面焊双面成型:底片上面有四条边界,中间两条间距较小。
(图2) (3)带垫板焊缝:四条边界,且最外面两条边界清晰整齐。
(图2)图1.单面焊图2.带垫板单面焊(4)双面焊:四个边界,且左右两条边界相隔较近,甚至可能有部分重合。
(图3) (图4)图3.双面焊图4.双面焊3、焊接方法的影像分析(1)手工电弧焊:呈现鱼鳞纹,边界变化明显。
(图5)(2)自动焊:鱼鳞纹不明显,且边界变化平缓。
(3)氩弧焊:焊缝中间有颜色很淡的亮斑。
(图6)图5.手工电弧横焊图6.自动焊4、焊接位置影响分析(1)横焊:多条焊缝组成,容易区别。
(图7)(2)立焊:鱼鳞纹较密,且焊缝宽度较大,存在亮斑。
(图8)图7.横焊图8.立焊(3)仰焊:与立焊影像难区别,鱼鳞纹密度稍大于立焊,也存在亮斑。
(图9)图9.仰焊5、焊缝中常见缺陷影像分析(1)分析要点:形状、位置、黑度。
(2)常见缺陷:气孔、夹渣、未焊透、未熔合、裂纹、钨夹渣。
其中未焊透、未熔合、裂纹、钨夹渣不参加评定。
a、气孔:(图10)形状:圆形、椭圆形、斜气孔(弥散形气孔),特点是外部轮廓比较规则。
黑度:气孔黑度较大,由中心向四周减淡(大气孔)位置:一般位于焊道投影中心位置。
b、夹渣:(图11) (图12)形状:圆形(点状)、长条形,特点是外部不规则。
黑度:黑度分布比较均匀,且黑度较淡。
位置:一般分布在焊道投影中心线到融合线之间。
图10.气孔图11.夹渣图12.线状夹渣c、未焊透:定义:坡口面没有熔化,该位置没有金属填充物,此类缺陷称为未焊透。
未焊透分为根部未焊透和中间未焊透。
形状:一条直线(存在长度和宽度变化)边界整齐。
黑度:均匀黑色。
位置:在焊道投影中间位置。
d、未熔合:(图13)定义:坡口面未熔化,且有填充金属,此类缺陷称为未熔合缺陷。
射线照相底片的评定ppt课件

评片基本知识
❖ (2) 影象细节观察是为了作出正确的分析判断。 ❖ 因细节的尺寸和对比度极小,识别和分辨是比较困难的,
为尽可能看清细节,常采用下列方法: ❖ 1.调节观片灯亮度,寻找最适合观察的透过光强; ❖ 2.用纸框等物体遮挡住细节部位邻近区域的透过光线; ❖ 3.使用放大镜进行观察; ❖ 4.移动底片,不断改变观察距离和角度。
4~100℃/秒,比铸锭冷却速高1000倍,在这样短的时间内,冶金反应是不平衡,也就是说是不完善的。 F、密集气孔,在焊缝的局部地方,气孔集聚成窝,多者十多个,少者五六个,直径大小不一,黑度深浅不均,轮廓有的清晰,有的不
清晰,通常是因起的弧,少收弧,所致与。基本金属的污染程
(1)评片应有专用的评片室。
❖ (3)各种工具用品 ❖ 放大镜:用于观察影象细节,一般为2—5倍。 ❖ 遮光板:观察底片局部区域或细节。 ❖ 直 尺:最好是透明塑料尺。 ❖ 手 套:避免评片人手指与底片接触,产生污痕。 ❖ 文 件:用于记录的各种规范、标准、图表。
人员条件要求
❖ 担任评片工作的人员应符合以下要求 ❖ 1.应经过系统的培训,并通过法定部门考核确认。 ❖ 2.应具有一定的评片实际工作经历和经验。 ❖ 3.除系统掌握射线检测理论知识外,还应具有焊接、材料
❖ 1.放大
影象放大是指底片上的影象尺寸大于物体的实际尺寸。 由于焦距比射源尺寸大很多,射源可视为“点源”,照 相投影可视为“中心投影”,影象放大程度与L1、L2有 关(图6.7),放大率M的计算公式为;
❖ M = W′/ W = L1+L2 / L1
❖ 一般情况下L1>>L2,所以,影象放大并不显著,底片 评定时一般不考虑放大产生的影响。
投影的基本概念
评片秘诀

一、探伤人员要评片,四项指标放在先*,底片标记齐又正,铅字压缝为废片。
二、评片开始第一件,先找四条熔合线,小口径管照椭圆,根部都在圈里面。
三、气孔形象最明显,中心浓黑边缘浅,夹渣属于非金属,杂乱无章有棱边。
四、咬边成线亦成点,似断似续常相见,这个缺陷最好定,位置就在熔合线。
五、未焊透是大缺陷,典型图象成直线,间隙太小钝边厚,投影部位靠中间。
六、内凹只在仰焊面,间隙太大是关键,内凹未透要分清,内凹透度成弧线。
七、未熔合它斜又扁,常规透照难发现,它的位置有规律,都在坡口与层间。
八、横裂纵裂都危险,横裂多数在表面,纵裂分布范围广,中间稍宽两端尖。
九、还有一种冷裂纹,热影响区常发现,冷裂具有延迟性,焊完两天再拍片。
十、有了裂纹很危险,斩草除根保安全,裂纹不论长和短,全部都是Ⅳ级片。
十一、未熔和也很危险,黑度有深亦有浅,一旦判定就是它,亦是全部Ⅳ级片。
十二、危害缺陷未焊透,Ⅱ级焊缝不能有,管线根据深和长,容器跟着条渣走**。
十三、夹渣评定莫着忙,分清圆形和条状,长宽相比3为界,大于3倍是条状。
十四、气孔危害并不大,标准对它很宽大,长径折点套厚度,中间厚度插入法。
十五、多种缺陷大会合,分门别类先评级,2类相加减去Ⅰ,3类相加减Ⅱ级。
十六、评片要想快又准,下拜焊工当先生,要问诀窍有哪些,焊接工艺和投影。
注:*四项指标系底片的黑度、灵敏度、清晰度、灰雾度必须符合标准的要求。
**指单面焊的管线焊缝和双面焊的容器焊缝内未焊240850884透的判定标准。
压力容器无损检测陈钢、沈功田(中国特种设备检测研究中心,北京 100013)摘要:球形储罐是储存各种气体和液化气体的常用压力容器之一,在石油、化工、冶金和城市燃气供应等方面得到广泛使用。
综述了球形储罐在制造、安装和使用过程中不同阶段可能出现的缺陷和分别采用的各种无损检测方法,包括射线检测、超声检测、磁粉检测、渗透检测、电磁涡流检测、声发射检测和磁记忆检测等技术。
分别介绍了这些无损检测方法的特点。
射线底片缺陷评定
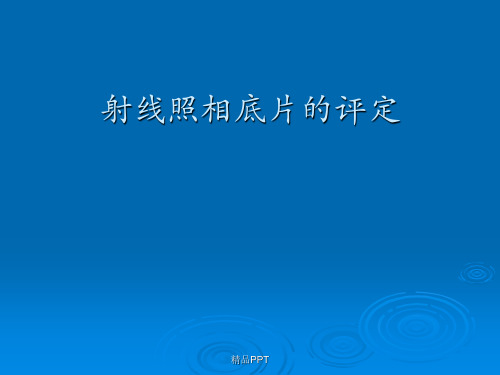
(2).斜针状气孔:在底片上多呈现为各种条虫状的影像,一端
保持着气孔的胎生园(或半圆形),一端呈尖细状, 其宽窄变化是 均匀逐渐变窄(细),黑度淡而均匀,轮廓尚清晰,这种气孔多沿结 晶方向长条状,其外貌取决于焊缝金属的凝固方式和气体的来 源决定。一般多成人字形分布(CO),少数呈蝌蚪状(氢气 孔)。如图12所示。 (3)缩孔:按其成因可分为晶间缩孔和弧坑缩孔。
③带垫板(衬环)的焊根未焊透:在底片上常出现在钝边 的一侧或两侧,外形较规则,靠钝边侧保留原加工痕迹( 直线状),靠焊缝中心侧不规则,呈曲齿(或曲弧)状, 黑度均匀,轮廓清晰。当因根部间隙过小、钝边高度过大 而引起的未焊透,或采用缩口边做衬垫以及用机械加工法 在厚板边区加工成垫环的未焊透和双面焊未焊透影像雷同 ,如图20、21、22所示。
B.条状ห้องสมุดไป่ตู้杂物:在底片上,其形态和条渣雷同,但 黑度淡而均匀,轮廓欠清晰,无棱角,两端成尖细 状。多残存在焊缝金属内部,分布多在焊缝中心部 位(最后结晶区)和弧坑内,局部过热区残存更明 显。如图17。
精品PPT
精品PPT
精品PPT
精品PPT
精品PPT
精品PPT
⑶未焊透:主要是因母材金属之间没有熔化,焊缝 熔敷金属没有进入接头根部造成的缺陷。按其焊接 方法可分为单面焊根部未焊透、双面焊X型坡口中 心根部未焊透和带衬垫的焊根未焊透。 ①单面焊根部未焊透:在底片上多呈现出为规则的、 轮廓清晰、黑度均匀的直线状黑线条,有连续和断 续之分。垂直透照时,多位于焊缝影像的中心位置, 线条两侧在5X放大镜观察可见保留钝边加工痕迹。 其宽度是依据焊根间隙大小而定。两端无尖角(在 用容器未焊透两端若出现尖角,则表示未焊透已扩 展成裂纹)。它常伴随根部内凹、错口影像,如图 18所示。
射线底片缺陷评定
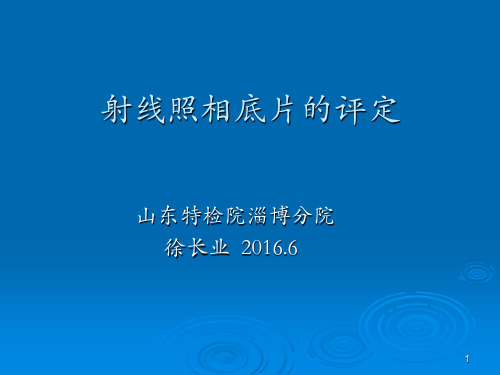
29
④烧穿:焊接过程中,熔化金属由焊缝背面流出后 所形成的空洞,称烧穿。它可分为完全烧穿(背面 可见洞穴)和不完全烧穿(背面仅能见凸起的鼓 疱),在底片的焊缝焊接时流影像中,其形貌多为 不规正的圆形,黑度大而不均匀,轮廓清晰的影像, 烧穿大多伴随塌漏同生。如图35、36所示。 ⑤焊瘤:即在焊接时熔敷金属流淌到焊缝之外的母 材表面而未与母材熔合在一起所形成的球状金属物。 在底片上多出现在焊趾线(并覆盖焊趾)外侧光滑 完整的白色半圆形的影像,焊瘤与母材之间为层状 未熔合,瘤中常伴有密集气孔。如图37所示。
4
B.弧坑缩孔:又称火口缩孔。主要是因焊缝的末端未填满, 而在后面的焊接焊道又未消除而形成的缩孔。在底片上的焊 缝凹坑(或弧坑)黑色浅淡的影像中,有一黑度明显大于周 围黑度的块状影像。黑度均匀,轮廓欠清晰,外形不正规, 有收缩的线纹。如图14所示。
5
6
(4)夹渣:按其形状可分为点状(块状)和条状,按其成分 可分为金属夹渣和非金属夹渣。 ①点状(块状): A.点(块)状非金属夹渣:在底片上呈现为外形无规则,轮廓 清晰,有棱角、黑度淡而均匀的点(块)状影像。分布有密集 (群集)、链状,也有单个分散出现。主要是焊剂或药皮成渣 残留在焊道与母材(坡口)或焊道与焊道之间。如图15所示。 B.点状金属夹渣:如钨夹渣、铜夹渣。钨夹渣在底片上多呈现 为淡白色的点块状亮点。轮廓清晰、大多群集成块,在5X放 大镜观察有棱角。铜夹渣在底片上多呈灰白不规正的影像,轮 廓清晰,无棱角,多为单个出现。夹珠,在底片上多为圆形的 灰白色影像,在白色的影像周围有黑度略大于焊缝金属的黑度 圆圈,如同句号“O”或“ C”。主要是大的飞溅或断弧后焊 条(丝)头剪断后埋藏在焊缝金属之中,周围一卷黑色影像为 未熔合。
24
射线检测评片技巧

射线检测评片技巧评片技巧是放射科技师的重要职责之一,因此需要具备良好的医学知识背景以及丰富的工作经验。
下面将介绍一些常用的射线检测评片技巧:1.仔细观察:评片时应仔细观察片子中的每个细节,包括骨骼结构的完整性、软组织的异常、器官的形态和大小等。
对于不同的放射线检查,要注意观察与该检查相关的特定结构。
2.正确的标记和定位:评片时,对于每一张片子都要正确标记左右、上下、前后,确保能准确的判断疾病的位置和性质。
同时,片子的取向也需要正确,以便医生能够准确判断。
3.对比度的评估:评估片子的对比度是非常重要的,它可以决定影像的清晰度以及对病变的显示情况。
对比度的选择应根据具体病情来决定,过高或过低的对比度都会影响医生的判断。
4.病变的形态学特征:根据病变的形态学特征,可以判断病变的良恶性及其可能的病理类型。
例如,恶性肿瘤通常具有不规则的形状,边界模糊,而良性肿瘤则具有规则的形状,边界清晰。
5.密度和纹理的评估:除了形态学特征外,片子中的密度和纹理也是非常重要的评估指标。
密度的不均匀分布可以提示病灶的存在,而纹理的变化可以反映器官或组织的病变情况。
6.与患者病史的结合:评估片子时,要结合患者的病史以及其他检查结果,以便作出更准确的诊断。
一个病变的诊断不仅依赖于片子本身的表现,还需与其他信息相结合。
7.及时反馈:评片后,要及时向医生提供评估结果。
有时射线检查是为了排除疾病,如果片子未显示明确的异常,可以适当提醒医生对其他病因进行考虑。
8.不断学习和提升:射线检测评片技巧是一个不断学习和提升的过程。
放射科技师应不断学习新的医学知识,了解新的技术和方法,并在实践中不断积累经验,提升自己的评片水平。
总而言之,射线检测评片技巧是放射科技师在工作中不可或缺的一部分。
通过合理的评片技巧,可以为医生提供准确的诊断信息,为患者的治疗和康复提供有力的支持。
放射科技师需要综合运用医学知识、工作经验和专业技能,不断提高自身评片水平,提供更优质的服务。
射线评片技术讲稿

b) 设备要求: ①观片灯:应有足够的光强度,最大亮度应能满足评片的要求
,主要性能应符合JB/T 7903的有关规定。亮度应可调,性 能稳定,安全可靠,且噪音应<30dB。观片时用遮光板应能 保证底片边缘不产生亮光的眩晕而影响评片。 ②黑度计:黑度计可测的最大黑度应不小于4.5,测量值的误 差应不超过±0.05。黑度计至少每6个月校验一次。 ③评片用工具:放大镜应为3至5倍,应有0—2cm长刻度标尺 ,不宜采用高倍放大镜,因易引起影像畸变。所用评片尺应 有读数准确的刻度。
•
d)从底片上获得的质量信息:
从底片上获得缺陷的有无、性质、数量及分布情况等。 获得缺陷的二维尺寸(长、宽)信息,沿板厚方向尺寸可用黑
度大小表示。 能预测缺陷可能扩展和张口位移的趋向。 能依据标准、规范对被检物的质量作出合格与否的评价。 能为安全质量事故及材料失效提供可靠的分析凭证。
e)正确评判底片的意义: 预防不可靠工件转入下道工序,防止材料和工时的浪
•
1.3 评片人员要求
射线检测人员的未经矫正或经矫正的近(距)视 力和远(距)视力应不低于5.0(小数记录值为 1.0), 测试方法应符合GB 11533的规定。从事评 片的人员应每年检查一次视力。
•
1.4 相关知识要求
a)人的视觉特性: 人在较暗的环境中对黄光最敏感,其次是白光,橙色
无损检测射线底片缺陷评定
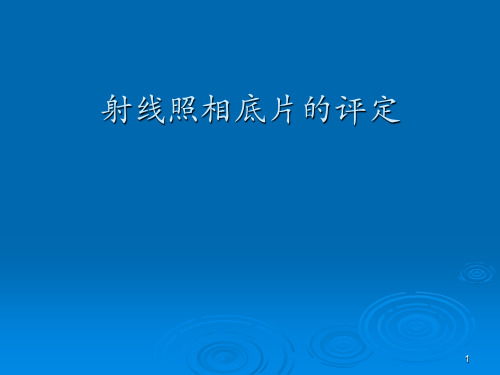
15
16
17
18
⑷未熔合:可分为坡口未熔合、焊道之间未熔合、单面焊根部 未熔合。 ①坡口未熔合:按坡口型式可分为V型坡口和U型坡口未熔合: A.V型(X)型坡口未熔合:常出现在底片焊缝影像两侧边缘区 域,呈黑色条云状,靠母材侧呈直线状(保留坡口加工痕迹), 靠焊缝中心侧多为弯曲状(有时为曲齿状)。垂直透照时,黑 度较淡,靠焊缝中心侧轮廓欠清晰。沿坡口面方向透照时会获 得黑度大、轮廓清晰、近似于线状细夹渣的影像。在5×放大 镜观察仍可见靠母材侧具有坡口加工痕迹(直线状),靠焊缝 中心侧仍是弯曲状。该缺陷多伴随夹渣同生,故称黑色未熔合, 不含渣的气隙称为白色未熔合。垂直透照时,白色未熔合是很 难检出的。如图23所示。 B.U型(双U型)坡口未熔合:垂直透照时,出现在底片焊缝影 像两侧的边缘区域内,呈直线状的黑线条,如同未焊透影像, 在5X放大镜观察仍可见靠母材侧具有坡口加工痕迹(直线状), 而靠焊缝中心侧可见有曲齿状(或弧状),并在此侧常伴有点 状气孔。黑度均匀,轮廓清晰,也常伴有夹渣同生,倾斜透照 19 时,形态和V型的相同,如图24所示。
2
1.2缺陷在底片上成像的基本特征
1.2.1圆形缺陷 ⑴气孔:在焊缝中常见的气孔可分为球状气孔、条状气孔和 缩孔。 球状气孔:按其分布状态可分为均布气孔、密集气孔、链状 气孔、表面气孔。球孔,在底片上多呈现为黑色小圆形斑点, 外形较规则,黑度是中心大,沿边缘渐淡,轮廓清晰可见。 单个分散出现,且黑度淡,轮廓欠清晰的多为表面气孔。密 集成群(5个以上/cm2)叫密集气孔,大多在焊缝近表面, 是由空气中氮气进入熔池造成。平行于焊缝轴线成链状分布 (通常在1cm长在线有4个以上,其间距均≤最小的孔径)称 为链状气孔,它常和未焊透同生。一群均匀分布在整个焊缝 中的气孔,叫均布气孔,见图10示。
射线底片评定口诀
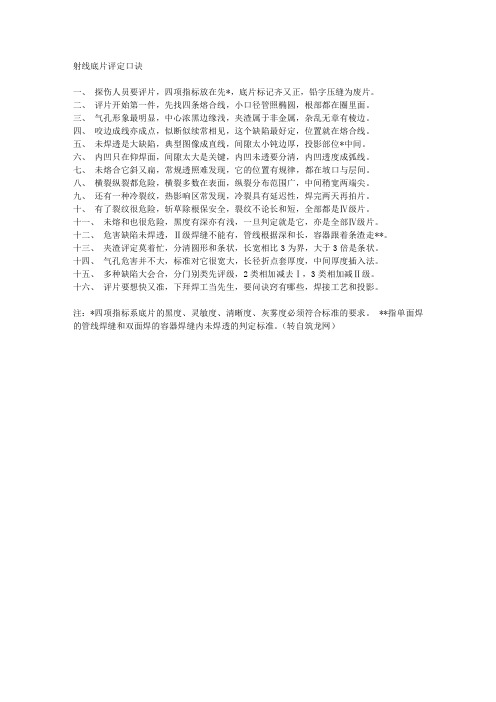
射线底片评定口诀
一、探伤人员要评片,四项指标放在先*,底片标记齐又正,铅字压缝为废片。
二、评片开始第一件,先找四条熔合线,小口径管照椭圆,根部都在圈里面。
三、气孔形象最明显,中心浓黑边缘浅,夹渣属于非金属,杂乱无章有棱边。
四、咬边成线亦成点,似断似续常相见,这个缺陷最好定,位置就在熔合线。
五、未焊透是大缺陷,典型图像成直线,间隙太小钝边厚,投影部位*中间。
六、内凹只在仰焊面,间隙太大是关键,内凹未透要分清,内凹透度成弧线。
七、未熔合它斜又扁,常规透照难发现,它的位置有规律,都在坡口与层间。
八、横裂纵裂都危险,横裂多数在表面,纵裂分布范围广,中间稍宽两端尖。
九、还有一种冷裂纹,热影响区常发现,冷裂具有延迟性,焊完两天再拍片。
十、有了裂纹很危险,斩草除根保安全,裂纹不论长和短,全部都是Ⅳ级片。
十一、未熔和也很危险,黑度有深亦有浅,一旦判定就是它,亦是全部Ⅳ级片。
十二、危害缺陷未焊透,Ⅱ级焊缝不能有,管线根据深和长,容器跟着条渣走**。
十三、夹渣评定莫着忙,分清圆形和条状,长宽相比3为界,大于3倍是条状。
十四、气孔危害并不大,标准对它很宽大,长径折点套厚度,中间厚度插入法。
十五、多种缺陷大会合,分门别类先评级,2类相加减去Ⅰ,3类相加减Ⅱ级。
十六、评片要想快又准,下拜焊工当先生,要问诀窍有哪些,焊接工艺和投影。
注:*四项指标系底片的黑度、灵敏度、清晰度、灰雾度必须符合标准的要求。
**指单面焊的管线焊缝和双面焊的容器焊缝内未焊透的判定标准。
(转自筑龙网)。
射线评片技巧
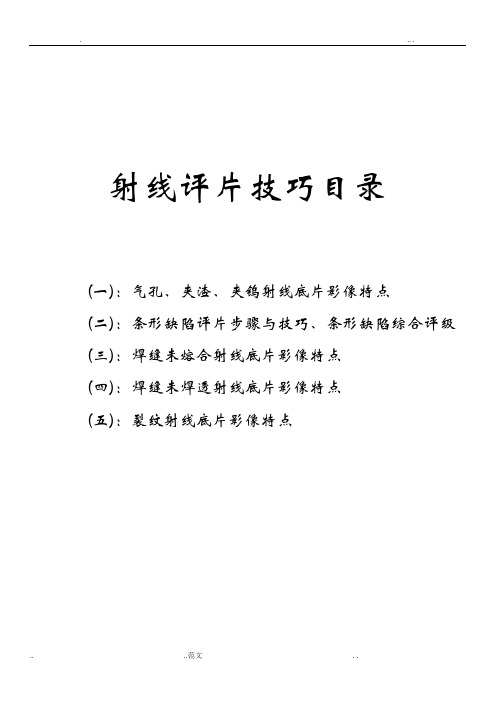
射线评片技巧目录(一):气孔、夹渣、夹钨射线底片影像特点(二):条形缺陷评片步骤与技巧、条形缺陷综合评级(三):焊缝未熔合射线底片影像特点(四):焊缝未焊透射线底片影像特点(五):裂纹射线底片影像特点(一):气孔、夹渣、夹钨射线底片影像特点按照JB/T4730-2005《承压设备无损检测》第2部分射线检测篇介绍,焊接接头中的缺陷按性质区分为裂纹、未熔合、未焊透、条形缺陷和圆形缺陷五类。
在《射线检测评片》栏目中将介绍该五类性质的缺陷成因、缺陷评片技巧、评级方法,分享在工作中遇见的射线检测案例。
本文介绍圆形缺陷(气孔、密集气孔、夹渣、夹钨)评片技巧和缺陷定量评级。
一、圆形缺陷的评片缺陷长宽之比小于等于3(L/N<=3),且非裂纹、未焊透和未熔合危害性缺陷。
对接接头焊缝常见的圆形缺陷包括圆形气孔、非金属夹渣、夹钨等性质缺陷。
圆形缺陷示意图1、气孔(1)气孔成因在《焊缝气孔形成机理及超声检测波形特性》文中详细介绍了焊缝气孔形成的原因。
气孔分为单个气孔和密集性气孔。
气孔降低了焊缝的金属致密性,降低焊接接头的强度、韧性等力学性能。
(2)气孔射线成像特点气孔部充满气体,射线穿过气孔几乎不会形成材质衰减。
在射线底片上气孔呈暗色斑点,中心黑度较大。
单个气孔边缘较浅平滑过渡,轮廓规则较清晰,密集气孔成团状。
气孔大多是球形的,也可以有其它形状,气体的形状与焊接条件密切有关。
单个气孔缺陷密集性气孔2、非金属夹渣(1)夹渣成因焊缝夹渣形成原因主要有以下几点:•在焊接每层焊道层间清渣不干净;•焊接电流过小、焊接速度过快;•焊接操作过程不当;•母材坡口设计加工不当;•液态金属冷却速度过快等;第一条是焊缝产生夹渣的直接原因,第二到第五条原因是由于焊渣在液态金属中浮渣不及时而残留在焊缝中。
焊缝中存在非金属夹渣,当焊缝承受应力过程中在夹渣周围会形成裂纹扩展,裂纹发展到一定程度焊缝开裂。
夹渣严重降低了焊接件强度、韧性等力学性能。
射线探伤の评片学习(有图)
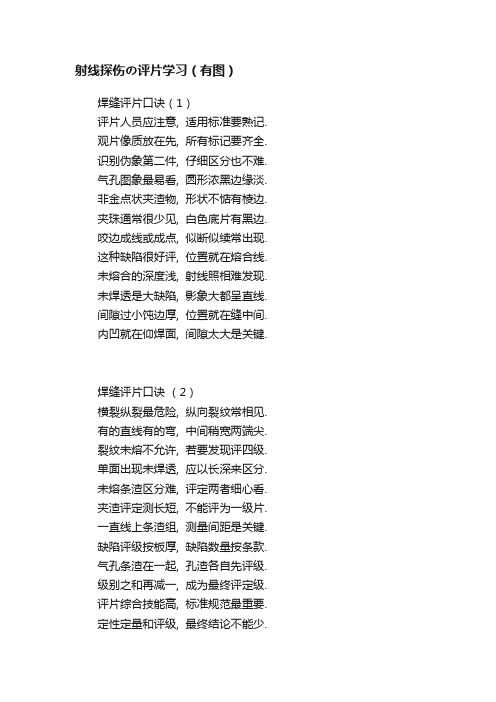
射线探伤の评片学习(有图)焊缝评片口诀(1)评片人员应注意, 适用标准要熟记.观片像质放在先, 所有标记要齐全.识别伪象第二件, 仔细区分也不难.气孔图象最易看, 圆形浓黑边缘淡.非金点状夹渣物, 形状不惦有棱边.夹珠通常很少见, 白色底片有黑边.咬边成线或成点, 似断似续常出现.这种缺陷很好评, 位置就在熔合线.未熔合的深度浅, 射线照相难发现.未焊透是大缺陷, 影象大都呈直线.间隙过小饨边厚, 位置就在缝中间.内凹就在仰焊面, 间隙太大是关键.焊缝评片口诀(2)横裂纵裂最危险, 纵向裂纹常相见.有的直线有的弯, 中间稍宽两端尖.裂纹未熔不允许, 若要发现评四级.单面出现未焊透, 应以长深来区分.未熔条渣区分难, 评定两者细心看.夹渣评定测长短, 不能评为一级片.一直线上条渣组, 测量间距是关键.缺陷评级按板厚, 缺陷数量按条款.气孔条渣在一起, 孔渣各自先评级.级别之和再减一, 成为最终评定级.评片综合技能高, 标准规范最重要.定性定量和评级, 最终结论不能少.下面参照几张典型底片和实物示意图,便于大家理解和记忆一、评片前的准备工作1)工具准备:应准备评片尺,记录笔,放大镜,记录表格2)检查评片设备是否完好:二、评片前首先仔细研究提供的信息:1)材料厚度主要评定体积性缺陷体积性缺陷主要分为条状缺陷与圆形缺陷。
长径与短径之比大于3者为条状缺陷,不大于3为圆形缺陷。
对于条状缺陷主要用于评定等级。
级别单个条形缺陷的最大长度一组条形缺陷的累计最大长度Ⅰ不允许Ⅱ≤T/3(最小可为4) 且≤20在长度为12T的任意选定条形缺陷评定区,相邻缺陷间距不超过6L的任一组的累计长度不超过T,但最小可为4Ⅲ≤2T/3(最小可为6)且≤30在长度为6T的任意选定条形缺陷评定区相邻缺陷间距不超过3L的任一组的累计长度不超过T,但最小可为6Ⅳ大于Ⅲ级对于圆形缺陷主要用于缺陷评定区的确定与评定等级评定区10×1010×2010×30母材公称厚度≤10>10~15 >15~20 >25~50 >50~100 >100Ⅰ 1 2 3 4 5 6Ⅱ 3 6 9 12 15 18Ⅲ 6 12 18 24 30 38Ⅳ缺陷点数大于Ⅲ级或缺陷长径大于T/2缺陷长径≤1>1~2 >2~3 >3~4 >4~6 >6~8 >8缺陷点数 1 2 3 6 10 15 25综合评级:在圆形缺陷评定区内同时存在圆形缺陷与条形缺陷,应当进行综合,综合评级的级别为圆形缺陷评定级别加条形缺陷评定级别减一。
射线评片技巧(一):气孔、夹渣、夹钨射线底片影像特点
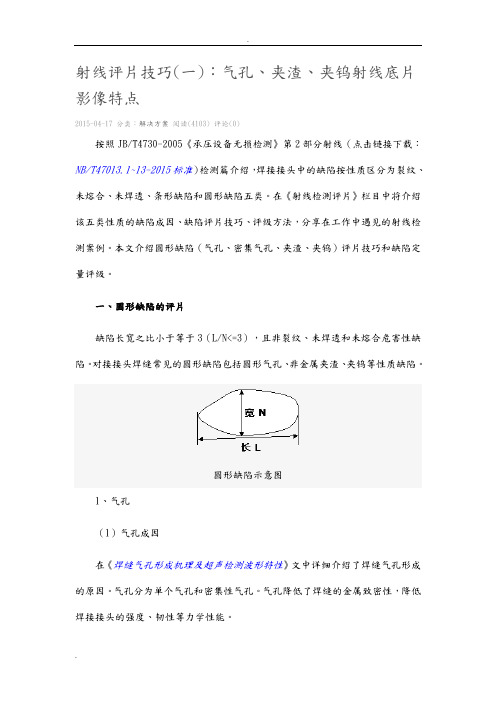
射线评片技巧(一):气孔、夹渣、夹钨射线底片影像特点2015-04-17 分类:解决方案阅读(4103) 评论(0)按照JB/T4730-2005《承压设备无损检测》第2部分射线(点击链接下载:NB/T47013.1~13-2015标准)检测篇介绍,焊接接头中的缺陷按性质区分为裂纹、未熔合、未焊透、条形缺陷和圆形缺陷五类。
在《射线检测评片》栏目中将介绍该五类性质的缺陷成因、缺陷评片技巧、评级方法,分享在工作中遇见的射线检测案例。
本文介绍圆形缺陷(气孔、密集气孔、夹渣、夹钨)评片技巧和缺陷定量评级。
一、圆形缺陷的评片缺陷长宽之比小于等于3(L/N<=3),且非裂纹、未焊透和未熔合危害性缺陷。
对接接头焊缝常见的圆形缺陷包括圆形气孔、非金属夹渣、夹钨等性质缺陷。
圆形缺陷示意图1、气孔(1)气孔成因在《焊缝气孔形成机理及超声检测波形特性》文中详细介绍了焊缝气孔形成的原因。
气孔分为单个气孔和密集性气孔。
气孔降低了焊缝的金属致密性,降低焊接接头的强度、韧性等力学性能。
(2)气孔射线成像特点气孔内部充满气体,射线穿过气孔几乎不会形成材质衰减。
在射线底片上气孔呈暗色斑点,中心黑度较大。
单个气孔边缘较浅平滑过渡,轮廓规则较清晰,密集气孔成团状。
气孔大多是球形的,也可以有其它形状,气体的形状与焊接条件密切有关。
单个气孔缺陷密集性气孔2、非金属夹渣(1)夹渣成因焊缝夹渣形成原因主要有以下几点:∙在焊接每层焊道层间清渣不干净;∙焊接电流过小、焊接速度过快;∙焊接操作过程不当;∙母材坡口设计加工不当;∙液态金属冷却速度过快等;第一条是焊缝产生夹渣的直接原因,第二到第五条原因是由于焊渣在液态金属中浮渣不及时而残留在焊缝中。
焊缝中存在非金属夹渣,当焊缝承受应力过程中在夹渣周围会形成裂纹扩展,裂纹发展到一定程度焊缝开裂。
夹渣严重降低了焊接件强度、韧性等力学性能。
(2)夹渣射线成像特点焊缝金属包裹着非金属夹杂物形成夹渣、射线穿过夹渣有一定的衰减,但远远小于焊缝金属对射线的衰减。
射线底片评定技术课件

1
1、评片工作的基本要求
缺陷是否能够通过射线照相而被检出,取决于若 干环节。
首先,必须使缺陷在底片上留下足以识别的影象, 这涉及到照相质量方面的问题。
其次,底片上的影象应在适当条件下得以充分显 示,以利于评片人员观察和识别,这与观片设备和环 境条件有关。
第三,评片人员对观察到的影象应能作出正确的 分析与判断,这取决于评片人员的知识、经验、技术 水平和责任心。
6
1.3评片人员要求
⑴应经过系统的培训,并通过法定部门考核确认。一 般要求具 有RTⅡ级资格证书人员担任。
⑵应具有一定的评片实际工作经历和经验。
⑶除系统掌握射线检测理论知识外,还应具有焊接、 材料等相关知识。
⑷应熟悉射线检测标准以及被检测试件的设计制造规 范和有关管理法规。
⑸应充分了解被检测试件的状况,如材质、焊接和热 处理工艺,以及表面形态等。
亮度必须可调,以便观察不同黑度底片时满足上述要求。
观察低黑度区域时将光强减小,而在观察高黑度区域时将光强 调大。光源的颜色通常为白色,也可以使用橙色或黄绿色的光 源。
观片灯应有足够大的照明区,一般不小于300mm×80mm, 实际使用时采用遮光板改变照明区域面积,使其略小于底片尺 寸。观察屏各部分照明应均匀,照射到底片上的光应是散射的。 观片灯应散热良好,绝缘好,噪声低(<30dB)。
9
⑵表观对比度与观片条件 ② 表观对比度:
是指那些对显示缺陷不起作用的所有光 线(Ls),如室内环境光线、底片上缺陷周 围的透过光线等,进入眼体,会使人眼辨别 影像黑度差能力下降,这种下降的黑度差值 ΔDa,称为表观对比度,从式中 ΔDa≈ΔD/(1+N’),(式中N’=Ls/L)看出 Ls越 大,N’就越大,即ΔDa越小。所以应尽量避 免那些对显示缺陷不起作用光线进入眼中。
射线照相底片的评定
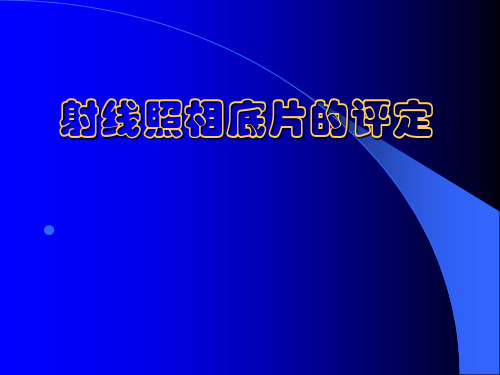
影象放大是指底片上的影象尺寸大于物体的实际尺寸。 由于焦距比射源尺寸大很多,射源可视为“点源”,照 相投影可视为“中心投影”,影象放大程度与L1、L2有 关(图6.7),放大率M的计算公式为;
M = W′/ W = L1+L2 / L1
一般情况下L1>>L2,所以,影象放大并不显著,底片 评定时一般不考虑放大产生的影响。
投影的基本概念
2.畸变 对于同一物体,正投影和斜投影所得到的影象形状不
同,如果正投影得到的象视为正常,则认为斜投影的 象发生了畸变。 实际照相中,影象畸变大部分是由投射线和投影面不 垂直的斜投影造成的。此外,当投影面不是平面时(胶 片弯曲),也会引起或加剧畸变。球形气孔在斜投影中 畸变影象为椭园形裂纹影象有时会畸变为一个有一定 宽度的,黑度不大的暗带。 畸变会改变缺陷的影象特征,给缺陷的识别和评定带 来困难。
投影的基本概念
4.相对位置改变
比较正投影方式照相的底片和斜投影方式照相的底片, 可以发现底片上影象的相对位置发生变化。例如图6.9 (下图)中,不同的投影角度使a、b、c、d点在底片
上的相对位置改变。
影象位置是判断和识别缺陷的重要依据之一,相对位置 改变有时会给评片带来困难,需要通过观察,推测投影 角度,作出正确判断。
与评片基本要求的相关知识
一、温度高
以手工电弧焊为例,其电弧温度高达6000~ 8000℃,使焊件与电焊条之间发生强烈熔化和蒸 发(熔滴的平均温度达1800~2400℃),外界的气 体(如:N2、02、H2等)大量的分解溶入熔池,其 数量比炼钢要大很多倍。然而,因焊缝金属吸收气 体量有限,那么凝固后的金属,有可能产生气孔, 使机械性能下降。
评片基本知识
(2) 影象细节观察是为了作出正确的分析判断。 因细节的尺寸和对比度极小,识别和分辨是比较困难
射线评片技术讲稿
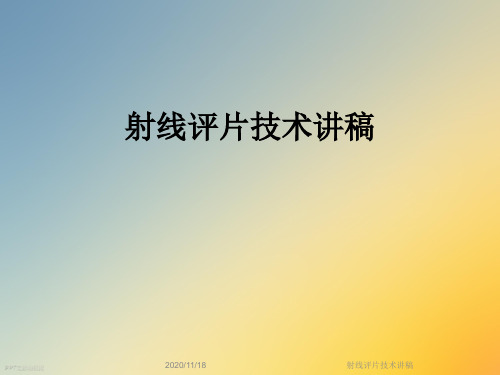
PPT文档演模板
射线评片技术讲稿
c)标记:底片上的种类和数量应符合有关标准 和工艺的规定。常用标记分为识别标记:如 工件编号、焊缝编号、部位编号及透照日期; 定位标记:如中心定位标记、搭接标记及标 距带等;返修标记:如R1、R2等。所有标记 均应放置距焊址不少于5mm。
d)伪缺陷:因透照操作或暗室操作不当,或由 于胶片,增感屏质量不好,在底片上留下的 缺陷影像,如划痕、折痕、水迹、静电感光、 指纹、霉点、药膜脱落、污染等。上述伪缺 陷均会影响评片的正确性,造成漏判和误判, 要求在有效评定区内不允许有伪缺陷影像存 在。
a) 环境: 要求评片室应独立、通风和卫生,室温不宜过高(应 备有空调),室内光线应柔和偏暗,室内亮度应在30cd/m2 为宜。室内噪音应控制在<40dB。
b) 设备要求:
①观片灯:应有足够的光强度,最大亮度应能满足评片的要求, 主要性能应符合JB/T 7903的有关规定。亮度应可调,性能 稳定,安全可靠,且噪音应<30dB。观片时用遮光板应能保 证底片边缘不产生亮光的眩晕而影响评片。
PPT文档演模板
射线评片技术讲稿
d)从底片上获得的质量信息:
从底片上获得缺陷的有无、性质、数量及分布情况等。 获得缺陷的二维尺寸(长、宽)信息,沿板厚方向尺寸可用黑
度大小表示。 能预测缺陷可能扩展和张口位移的趋向。 能依据标准、规范对被检物的质量作出合格与否的评价。 能为安全质量事故及材料失效提供可靠的分析凭证。
②黑度计:黑度计可测的最大黑度应不小于4.5,测量值的误 差应不超过±0.05。黑度计至少每6个月校验一次。
③评片用工具:放大镜应为3至5倍,应有0—2cm长刻度标尺, 不宜采用高倍放大镜,因易引起影像畸变。所用评片尺应有 读数准确的刻度。
射线评片讲座[专业内容]
![射线评片讲座[专业内容]](https://img.taocdn.com/s3/m/1beb986919e8b8f67c1cb9ea.png)
高等教育
41
夹渣的形态特征
高等教育
42
高等教育
43
按形态:夹渣可分为点状夹渣、块状夹渣、 条状夹渣等。
单个点状夹渣
高等教育
条状夹渣
44
夹渣的形态特征
高等教育
45
高等教育
46
气孔的形成
气孔是指焊接时,熔池中的气泡在凝固时未能 逸出,而残留下来所形成的空穴。
气孔产生部位和形状
气孔分内气孔和外气孔两种:小的很小,在显 微镜下才能看到,大的可达φ6mm以上。气孔 是由于气体熔解于液态金属内,在冷却中金属 熔解度降低,部分气体企图进入大气,但遇到 金属结晶的阻力,使它不能顺利的逸出而残留 于金属内,形成了内气孔,或逸在表面形成外 气孔
高等教育
39
夹渣的特征
(2)条状夹渣(Bb) a.条状夹渣,在底片上呈现带有不规则,两端呈
棱角(或尖角),大多是沿焊缝方向延伸成条状的, 宽窄不一,黑度不均匀,轮廓清晰影像,这种夹渣 常伴随焊道之间和焊道与母材之间的未熔合同 生. b.条状夹杂物:在底片上,其形态和条状夹渣 雷同,但黑度淡而均匀,轮廓不清晰,两端成尖细 状,多残存在焊缝金属内部,出现在焊缝轴线(中 心)部位和弧坑内,特别是焊缝局部过烧(热)区 更明显
黑度1与黑度2之间有个黑度差△D,此值 越大则对比度越大,如缺陷与母材间的 对比度越大缺陷的图像的边界就越清晰 (清晰度越大)缺陷就越容易识别。
高等教育
13
焊接工艺、结构和焊接缺陷
要了解手工电焊、手工氩弧焊、(埋弧)自动 焊的波纹特征,包括焊缝的起弧点与收弧点的 形状。
要了解不开坡口(相当于I型坡口)、V型坡口、 U型坡口、X型坡口以及坡口钝边的特点及应用 范围
- 1、下载文档前请自行甄别文档内容的完整性,平台不提供额外的编辑、内容补充、找答案等附加服务。
- 2、"仅部分预览"的文档,不可在线预览部分如存在完整性等问题,可反馈申请退款(可完整预览的文档不适用该条件!)。
- 3、如文档侵犯您的权益,请联系客服反馈,我们会尽快为您处理(人工客服工作时间:9:00-18:30)。
射线评片技巧(一):气孔、夹渣、夹钨射线底片影像特点
射线评片技巧(一):气孔、夹渣、夹钨射线底片影像特点
2015-04-17 分类:解决方案阅读(4103) 评论(0)
按照JB/T4730-2005《承压设备无损检测》第2部分射线(点击链接下载:NB/T47013.1~13-2015标准)检测篇介绍,焊接接头中的缺陷按性质区分为裂纹、未熔合、未焊透、条形缺陷和圆形缺陷五类。
在《射线检测评片》栏目中将介绍该五类性质的缺陷成因、缺陷评片技巧、评级方法,分享在工作中遇见的射线检测案例。
本文介绍圆形缺陷(气孔、密集气孔、夹渣、夹钨)评片技巧和缺陷定量评级。
一、圆形缺陷的评片
缺陷长宽之比小于等于3(L/N<=3),且非裂纹、未焊透和未熔合危害性缺陷。
对接接头焊缝常见的圆形缺陷包括圆形气孔、非金属夹渣、夹钨等性质缺陷。
圆形缺陷示意图
1、气孔
(1)气孔成因
在《焊缝气孔形成机理及超声检测波形特性》文中详细介绍了焊缝气孔形成的原因。
气孔分为单个气孔和密集性气孔。
气孔降低了焊缝的金属致密性,降低焊接接头的强度、韧性等力学性能。
(2)气孔射线成像特点
气孔内部充满气体,射线穿过气孔几乎不会形成材质衰减。
在射线底片上气孔呈暗色斑点,中心黑度较大。
单个气孔边缘较浅平滑过渡,轮廓规则较清晰,密集气孔成团状。
气孔大多是球形的,也可以有其它形状,气体的形状与焊接条件密切有关。
单个气孔缺陷
密集性气孔
2、非金属夹渣
(1)夹渣成因
焊缝夹渣形成原因主要有以下几点:
•在焊接每层焊道层间清渣不干净;
•焊接电流过小、焊接速度过快;
•焊接操作过程不当;
•母材坡口设计加工不当;
•液态金属冷却速度过快等;
第一条是焊缝产生夹渣的直接原因,第二到第五条原因是由于焊渣在液态金属中浮渣不及时而残留在焊缝中。
焊缝中存在非金属夹渣,当焊缝承受应力过程中在夹渣周围会形成裂纹扩展,裂纹发展到一定程度焊缝开裂。
夹渣严重降低了焊接件强度、韧性等力学性能。
(2)夹渣射线成像特点
焊缝金属包裹着非金属夹杂物形成夹渣、射线穿过夹渣有一定的衰减,但远远小于焊缝金属对射线的衰减。
射线底片上夹渣呈暗色斑点,黑度分布无规律,轮廓不圆滑不规则,小点状夹渣轮廓较不清晰。
非金属夹渣
3、夹钨
(1)夹钨成因
钨极承载电流的能力较差,过大的电流会引起钨极熔化和蒸发,其微粒有可能进入熔池,形成夹钨。
(2)夹渣射线成像
金属钨射线的衰减系数比钢大,透过金属钨后的射线能量比钢低,胶片吸收射线产生的光电子更少。
在底片上成亮色,轮廓清晰。
夹钨缺陷
以下为实际工作中的射线底片
夹渣和圆形气孔缺陷底片
夹渣气孔夹钨缺陷底片
圆形缺陷(链状气孔)底片
密集气孔缺陷底片
双影双壁透照圆形缺陷底片
虫状气孔底片
二、圆形缺陷的评级
圆形缺陷的评级参考JB/T4730-2005《承压设备无损检测》第2部分射线检测标准讲解,该标准规定的评级方法:
“5.1.5.1圆形缺陷用圆形缺陷评定区进行质量分级评定,圆形缺陷评定区为一个与焊缝平行的矩形,其尺寸见表8。
圆形缺陷评定区应选在缺陷最严重的区域。
5.1.5.2 在圆形缺陷评定区内或与圆形缺陷评定区边界线相割的缺陷均应划入评定区内。
将评定区内的缺陷按表9的规定换算为点数,按表10的规定评判焊接接头的质量级别。
“
表8 缺陷评定框
表9 缺陷点数换算表
表10 缺陷评级表
举例说明:
例子:若母材公称厚度(母材测量厚度)为19mm,首先判断底片上的缺陷非裂纹、未焊透和未熔合危害性缺陷。
再根据表8采用10×10的正方形评定框,框住最严重的部位,测量缺陷的长度。
若在该评定框内分别有编号为A、B、C、D四个缺陷,测量长度分别为3mm、4mm、2mm、5mm。
根据表9换算成点数分别为3个、6个、2个、10个,总共点数相加为3+6+2+10=21个点。
母材厚度为18mm,共换算为21个点大于III的最大点数18,根据表10评为IV 级。
若验收等级为III级,则该焊接件焊缝质量不合格。
备注:
1、>1-2表示,大于1且小于等于2(该范围包含2不包含1)。
精品文档
2、由于材质或结构等原因,进行返修可能会产生不利后果的焊接接头,经合同各方同意,各级别的圆形缺陷点数可放宽1点~2点。
(比如在测量圆形缺陷点在换算成点数,若点数为18,母材厚度为19mm,严格按照JB/T4730.2-2005标准的评级表评为IV级。
若放宽1点,则为17点评为III。
)
3、对致密性要求高的焊接接头,制造方底片评定人员应考虑将圆形缺陷的黑度作为评级的依据,将黑度大的圆形缺陷定义为深孔缺陷,当焊接接头存在深孔缺陷时,焊接接头质量评为Ⅳ级。
4、如下表中所示,母材厚度在规定范围内不计点数的缺陷尺寸。
若母材公称厚度为23mm,当缺陷长径小于0.5mm,则该缺陷不计入点数换算。
缺陷不计点数的缺陷尺寸
收集于网络,如有侵权请联系管理员删除。