模具开发改善报-2
模具改善报告怎么写
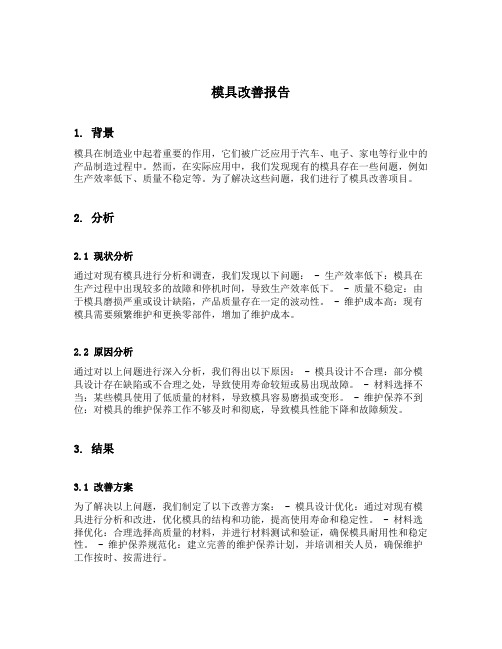
模具改善报告1. 背景模具在制造业中起着重要的作用,它们被广泛应用于汽车、电子、家电等行业中的产品制造过程中。
然而,在实际应用中,我们发现现有的模具存在一些问题,例如生产效率低下、质量不稳定等。
为了解决这些问题,我们进行了模具改善项目。
2. 分析2.1 现状分析通过对现有模具进行分析和调查,我们发现以下问题: - 生产效率低下:模具在生产过程中出现较多的故障和停机时间,导致生产效率低下。
- 质量不稳定:由于模具磨损严重或设计缺陷,产品质量存在一定的波动性。
- 维护成本高:现有模具需要频繁维护和更换零部件,增加了维护成本。
2.2 原因分析通过对以上问题进行深入分析,我们得出以下原因: - 模具设计不合理:部分模具设计存在缺陷或不合理之处,导致使用寿命较短或易出现故障。
- 材料选择不当:某些模具使用了低质量的材料,导致模具容易磨损或变形。
- 维护保养不到位:对模具的维护保养工作不够及时和彻底,导致模具性能下降和故障频发。
3. 结果3.1 改善方案为了解决以上问题,我们制定了以下改善方案: - 模具设计优化:通过对现有模具进行分析和改进,优化模具的结构和功能,提高使用寿命和稳定性。
- 材料选择优化:合理选择高质量的材料,并进行材料测试和验证,确保模具耐用性和稳定性。
- 维护保养规范化:建立完善的维护保养计划,并培训相关人员,确保维护工作按时、按需进行。
3.2 改善效果经过实施改善方案后,我们得到了以下改善效果: - 生产效率提升:故障率降低,停机时间减少,生产效率得到显著提升。
- 质量稳定性提高:通过优化设计和材料选择,产品质量波动性大幅降低。
- 维护成本降低:规范维护保养工作,减少维护次数和更换零部件的频率,降低了维护成本。
4. 建议为了进一步提高模具改善效果,我们提出以下建议: - 持续改进:对现有的改善方案进行持续评估和优化,以适应市场和技术的变化。
- 技术创新:关注新技术的发展趋势,引入先进的模具制造技术和设备,提升模具品质和生产效率。
模具改善报告怎么写

模具改善报告怎么写模具改善报告怎么写一、引言模具改善是企业生产过程中的重要环节,它能够提高产品质量、降低成本、提高效率等多方面的效益。
因此,对于企业来说,编写一份全面详细的模具改善报告非常必要。
二、改善目标在编写模具改善报告之前,需要明确改善目标。
通常来说,企业进行模具改善的目标有以下几个方面:1. 提高产品质量:通过对模具进行改进,使得生产出来的产品更加符合规格和标准。
2. 降低成本:通过对模具进行优化或者简化设计等手段,降低生产成本。
3. 提高效率:通过优化生产流程或者采用先进的工艺技术等手段,提高生产效率和产能。
三、现状分析在明确了改善目标之后,需要对现状进行分析。
主要内容包括以下几个方面:1. 模具使用情况:需要了解当前使用的模具种类、数量、使用年限等情况。
2. 生产情况:需要了解当前生产情况包括产品类型、规格和数量等情况。
3. 故障情况:需要了解当前模具存在的故障情况包括频率、影响程度等情况。
4. 维修情况:需要了解当前模具的维修情况包括维修次数、维修费用等情况。
四、改善方案在分析了现状之后,需要提出具体的改善方案。
根据不同的改善目标,可以采取不同的改善方案。
以下是一些常见的改善方案:1. 提高产品质量:可以通过优化模具设计、提高生产工艺技术等手段来达到提高产品质量的目标。
2. 降低成本:可以通过简化模具设计、采用更加经济实惠的材料等手段来达到降低成本的目标。
3. 提高效率:可以通过优化生产流程、提高设备自动化程度等手段来达到提高效率和产能的目标。
五、实施计划在确定了改善方案之后,需要制定实施计划。
主要内容包括以下几个方面:1. 实施时间表:需要确定改善计划实施时间表,明确每个阶段所需完成的任务和时间节点。
2. 责任人员:需要明确每个阶段所需负责人员及其职责和任务。
3. 预算和资源:需要预估改善计划所需的预算和资源,并制定相应的采购计划。
六、实施效果在实施改善计划之后,需要对实施效果进行评估。
模具工件异常报告
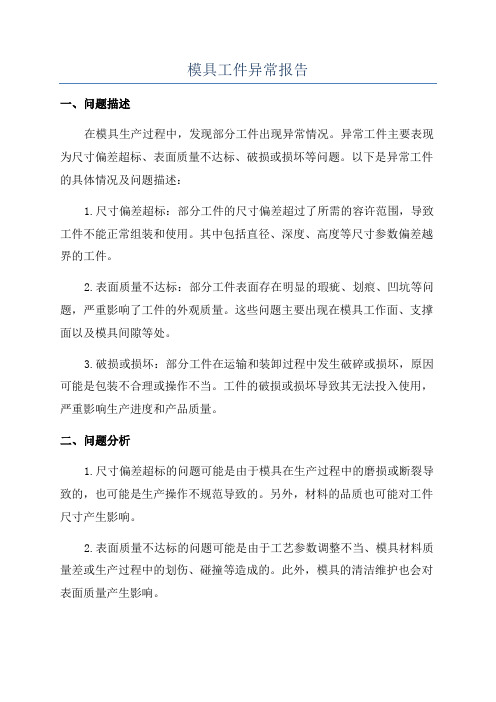
模具工件异常报告一、问题描述在模具生产过程中,发现部分工件出现异常情况。
异常工件主要表现为尺寸偏差超标、表面质量不达标、破损或损坏等问题。
以下是异常工件的具体情况及问题描述:1.尺寸偏差超标:部分工件的尺寸偏差超过了所需的容许范围,导致工件不能正常组装和使用。
其中包括直径、深度、高度等尺寸参数偏差越界的工件。
2.表面质量不达标:部分工件表面存在明显的瑕疵、划痕、凹坑等问题,严重影响了工件的外观质量。
这些问题主要出现在模具工作面、支撑面以及模具间隙等处。
3.破损或损坏:部分工件在运输和装卸过程中发生破碎或损坏,原因可能是包装不合理或操作不当。
工件的破损或损坏导致其无法投入使用,严重影响生产进度和产品质量。
二、问题分析1.尺寸偏差超标的问题可能是由于模具在生产过程中的磨损或断裂导致的,也可能是生产操作不规范导致的。
另外,材料的品质也可能对工件尺寸产生影响。
2.表面质量不达标的问题可能是由于工艺参数调整不当、模具材料质量差或生产过程中的划伤、碰撞等造成的。
此外,模具的清洁维护也会对表面质量产生影响。
3.破损或损坏的问题主要是由于在运输和装卸过程中未能采取有效的保护措施,对工件进行妥善包装和固定。
三、解决方案针对以上问题,制定以下解决方案:1.尺寸偏差超标问题:-对模具进行定期维护、保养,检查模具的磨损情况,及时更换磨损过度的模具。
-加强质量控制,并优化生产工艺参数,确保工件在规定范围内的尺寸偏差。
-对生产操作进行培训和指导,提高员工的操作规范性和技术水平。
2.表面质量不达标问题:-优化生产工艺参数,确保模具在生产过程中的温度、压力等控制合理。
-选择高质量的模具材料,确保模具的耐磨性和抗划伤性能。
-定期进行模具的清洁和维护,避免灰尘、污渍等对模具表面质量的影响。
3.破损或损坏问题:-设计合理的包装方案,确保工件在运输和装卸过程中的安全性。
-增加运输时的防震措施,保护工件免受震动和撞击的影响。
-提供专业培训,加强装卸操作人员的技能和操作规范。
模具不良改善事例集-PR

1.模具设计和后续的生产点检时需考虑模具避位对产 模具设计和后续的生产点检时需考虑模具避位对产 品的影响
改善効果
水平展開
無形效率:1.保证生产品质;2. 無形效率:1.保证生产品质;2.提升員工自身素质. :1.保证生产品质
无
区分
品質向上 効率向上 経費削減
B2435874形状不良调查改善报告 形状不良调查改善报告
改善作成: 改善後
改善前
OK品
NG品 追加防漏管位
現状の 現状の問題点 改善内容
1.凸起部形状不良,图D-7区(详见写真) 凸起部形状不良, 凸起部形状不良 区 详见写真) 2.漏第四工序 形折弯 漏第四工序Z形折弯 漏第四工序
1.在模具设计阶段就对生产时可能会漏工序进行考虑, 在模具设计阶段就对生产时可能会漏工序进行考虑, 在模具设计阶段就对生产时可能会漏工序进行考虑 如有可能就设计成防反防漏的结构。 如有可能就设计成防反防漏的结构。 2.在模具验收阶段对模具的防反防漏进行重点确认。 在模具验收阶段对模具的防反防漏进行重点确认。 在模具验收阶段对模具的防反防漏进行重点确认
模具不良改善事例集
区分
品質向上 効率向上 経費削減
D0254274慢性不良改善报告 慢性不良改善报告
改善作成: 改善後
改善前
加工方向反
折弯位置移位
現状の 現状の問題点
改善内容
1.偶尔发生加工方向反事故 偶尔发生加工方向反事故 2.偶尔发生产品移位事故 偶尔发生产品移位事故
1.增加逆反针 增加逆反针 2.加高管位 加高管位3MM。 加高管位 。
无
区分
品質向上 効率向上 経費削減
G4042810的孔直径小改善报告 G4042810的孔直径小改善报告 的孔直径小
模具问题改善报告范文

模具问题改善报告范文模具问题改善报告尊敬的领导:模具在生产加工过程中发挥着重要作用,但在实际生产过程中,我们常常会遇到一些模具问题,影响了生产效率和产品质量。
为了改善目前存在的问题,提高生产效率,经过多次讨论和分析,我们制定了以下改善方案:首先,我们发现模具的寿命较短,在使用一段时间后容易出现破损和损坏的情况。
通过分析发现,这主要是由于不合理的模具设计和选择不当的材料造成的。
为此,我们计划引进更先进的模具设计软件,并聘请专业的模具设计师对模具进行优化设计,提高模具的使用寿命。
同时,我们还将加强对模具材料的选择和检测,确保选择耐磨、耐腐蚀的高品质材料,延长模具的使用寿命。
其次,我们发现模具的加工精度不高,容易出现尺寸不准确、表面粗糙等问题。
通过分析发现,这主要是由于加工设备精度不高和操作人员技术水平低造成的。
为此,我们计划更新加工设备,引进高精度数控机床和精密磨床,提高加工精度。
同时,我们还将加强对操作人员的培训和技术指导,提高其操作技术和加工质量意识,确保模具加工达到更高的精度要求。
第三,我们发现模具的维护保养不到位,容易出现生锈、变形等问题。
通过分析发现,这主要是由于对模具的维护保养意识不强和维护保养工作不规范造成的。
为此,我们计划建立完善的模具维护保养制度,明确模具的维护保养责任和标准,定期对模具进行维护保养,并加强对操作人员的培训,提高其对模具维护保养的重视和意识。
最后,我们还计划建立模具问题反馈机制,定期组织模具问题讨论会,收集和总结模具使用过程中出现的问题,并制定相应的改进措施,以便及时解决模具问题,提高整体生产效率和产品质量。
以上是我们制定的模具问题改善方案,我们将尽快落实并推行,相信通过这些改进措施,能够有效解决模具问题,进一步提高生产效率和产品质量。
感谢领导对我们工作的支持和关心!此致敬礼XXX公司生产部。
模具改善提案 ppt课件

ppt课件
8
+ A、模具厂组织架构、部门职责、理流程、 人员编制等进行梳理整改.
+ B、按部门对主要问题整改,逐步进行规范 化管理。
ppt课件
9
+ 经过半年系统地对公司主要管理问题进行 梳理、整改和调整,在取得初步成绩之后, 再对模具厂从经营管理的角度全面进行梳 理、调整,主要工作是建立模具厂的经营 目标、经营计划、全面预算管理体系;还 包括KPI、绩效考核、7S等方面工作,以促 使模具厂快速发展成行业的标杆企业。
面记录,存档,原因分析具体,清晰,纠正措施方 法可操作性强,可追溯)
+ 10.下月工作计划讲解(部门计划,计划详细,思路 清晰,目标明确,可行性强)。
ppt课件
18
ppt课件
19
+ 1.模具设计标准(建立设计依据,设计标准, 设计过程中融会贯通工艺标准和加工质量标准)
+ 2.模具加工工艺标准(制定加工标准及依据, 标准清晰,统一,规范)。
+ 3.模具配件标准(建立常用配件标准件,降低 成本,缩断模具制作周期),
+ 4.质检控制办法(建立质检依据,制定操作流 程和控制办法来杜绝不良品发生)
+ 5.来料检测(IQC、控制原材料品质,外购部分 质量控制程序及有效手法)
ppt课件
20
+ 6.加工过程质量控制(IPQC、内部加工和外协 加工的品质过程控制程序及手法)
ppt课件
2
+ 精特公司经多年发展,能取得如此大的成 就深感敬佩。特别是新模具工厂布局,场 地规划,规模能给公司提升一个新的层次! 但在专业技术起家的模具厂的产生效益却 成为公司高层不如意的板块,特别是加工 效率低,成本高现象,中层管理人员执行 力较弱,已严重影响了精特公司在市场竞 争优势,给公司长远发展造成了阻力。
模具改善报告

模具改善报告报告目的:本报告旨在分析公司所使用的模具制造过程中存在的问题,并提出改善建议,以期提高模具的制造效率和品质。
报告内容:1. 模具制造过程存在的问题:1.1 生产效率低下:目前公司所使用的模具加工设备老化,无法满足高效率的加工需求,导致生产效率不高;1.2 质量控制不严:在模具制造过程中往往会出现一些质量问题,例如模具表面出现气泡、翘曲等问题;1.3 人力资源不足:公司缺乏一支熟练的模具制造团队,这将影响整个模具制造过程的效率和产能。
2. 解决方案:2.1 更新设备:公司应该优先考虑更新现有的模具加工设备,投资一些国内外先进的设备,例如:数控加工中心等,以提高生产效率;2.2 加强质量控制:公司应该建立一套完善的质量控制管理体系,及时发现并改进存在的问题,以确保模具制造的品质;2.3 培养员工:公司应该加强对相关人员的培训,特别是针对年轻员工进行岗前培训和一线操作技能培训。
经过一段时期的培训,他们将能熟练掌握模具制造技能,从而为公司创造出更高的产值。
3. 经济效益:本次模具制造改善方案需要协调多方面的工作,但是如果顺利实施,将会给公司带来可观的经济效益。
首先,提高生产效率将会增加产品数量;其次,改善模具的制造质量,将会降低后期的质量问题及维护成本;再者,增强员工技能,将会提高团队的协同作用和创造性。
综上所述,本报告所提出的模具改善方案符合公司发展和产业升级要求。
报告结论:模具是一个关键的生产因素,影响到公司的产品品质和生产效率。
当前,公司所使用的模具加工设备旧,技术落后,制造工艺流程不完善,影响模具的制造效率和制造质量。
综合分析,本报告建议公司优先更新模具加工设备,建立完善的质量控制体系,并加强员工的培训和技能提高。
以上为模具改善报告,报告内容涉及“问题分析、解决方案及经济效益等”,属于正式报告的格式。
本报告旨在客观、详实地对模具生产过程中所出现的问题进行分析,并提供可行的解决方案,以帮助企业提高生产效率和产品品质,从而达到降低成本、增加收益、促进企业可持续发展的目的。
模具生产周期管理改善总结报告一

缩短17天
缩短9天
50
47
20
10
0 复杂结构
一般结构
简单结构
现状 目标
模具生产目标周期:
序号
1 2 3 4 5 6 7 8 9 10 11 12 13 14 15 16
主工序 模具设计 材料采购
模具加工
试模移交
工序细化
模具设计 模具出图 模具订料 材料申购 材料回厂检验 材料钻铣开粗 CNC开粗加工 委外热处理 磨床磨精料 CNC精铣加工 材料线切割 火花机放电 模具省模 模具装配 模具检验 压铸试模
6
加工时未对标
准零件进行安
影响模具加工周期。
6
零件的 全库存。
标准化
及图纸 模具工艺标准 管理 不明确。
加工错误。
6
试模前将相关的模具、资
前期试模工作未准备。 4
料及人员进行准备与知
4
会,确保试模顺利。
试模安排不合理。
3
依生产计划及机台进行进 行合理安排。
3
标准化意识薄弱。
4
对标准化工作进行培训和 宣导。
潜在的失效后果
严 重 度
潜在的失效起因/机理
频 度
控制预防
探测 度
RPN
建议的措施
流程繁琐
影响模具材料交期
6
流程繁琐
影响模具材料交期
6
采购单处理时 无法快速反应客户需求
间较长
。
6
采购单
处理流 程及交 期管理
部门之间沟通 不顺畅。
工作无法顺利开展。
6
未依流程要求进行作业 。
4
对操作人员进行培训。
2
流程可执行性低。
模具常见异常及处理方法解读

原因对策近浇口部分之原料太松或太紧增加或减少射出时间成品形状及厚薄不对称模具温度之控制﹐脱模后以定形架固定﹐变更成品设计几个溢口进料不平均调整模具温度近浇口部分之原料太松或太紧减少或增大溢口大小成品顶出时尚未冷却降低模具温度延长冷却时间降低原料温度原料温度太低提高原料温度提高模具温度9-11 成品内有气孔原因对策射出压力太低提高射出压力射出时间及剂量不足增加射出时间及剂量射出速度太快调慢射出速度被压不够提高被压料管温度不当降低射嘴及前段温度﹐提高后段温度成品断面肋或柱过厚变更成品设计或溢口位置浇道溢口太小加大浇道及溢口模具温度不平均调整模具温度冷却时间太长减少模内冷却时间使用水浴冷却水浴冷却过急减短水浴时间或提高水浴温度原料含有水分原料彻底烘干原料温度过高致分解降低原料温度原因对策近浇口部分之原料太松或太紧增加或减少射出时间成品形状及厚薄不对称模具温度之控制﹐脱模后以定形架固定﹐变更成品设计几个溢口进料不平均调整模具温度近浇口部分之原料太松或太紧减少或增大溢口大小成品顶出时尚未冷却降低模具温度延长冷却时间降低原料温度原料温度太低提高原料温度提高模具温度9-11 成品内有气孔原因对策射出压力太低提高射出压力射出时间及剂量不足增加射出时间及剂量射出速度太快调慢射出速度被压不够提高被压料管温度不当降低射嘴及前段温度﹐提高后段温度成品断面肋或柱过厚变更成品设计或溢口位置浇道溢口太小加大浇道及溢口模具温度不平均调整模具温度冷却时间太长减少模内冷却时间使用水浴冷却水浴冷却过急减短水浴时间或提高水浴温度原料含有水分原料彻底烘干原料温度过高致分解降低原料温度银条出现在从浇口出来的表面原因解决方法/检查要点A.塑料本身含水份或宿料 1. 避免素料结露现象表面有水分注:不要将塑料至较冷的地方了取出后,马上做射出成行加工.2. 塑料预先干燥,尤其已拆封的塑料B.模面上有结露现象 1. 提高模具温度注:提高模具开起关闭的速度可以避免模面结露现象凹陷Array成品的表面在肋及/或厚度改变的地方不平.原因解决方法/检查要点A. 射胶量不足 1. 增加射胶量且经常秤成品的重量(检查重量)B. 射出速度/压力不对 1. 调整射出速度2.射出速度曲线3.调整射出压力4.射出压力曲线C. 保压压力太低 1. 提高保压压力2.增加保压时间3.检查浇口是否阻塞(污染)注:如果必要的话,加大或重新安排哓口位置(平衡)D. 由于塑料温度太高,造成温度收缩 1. 降低料管温度E. 成品的壁厚差距太大 1. 使用泡剂(收缩不平均)F. 模温太高 1. 降低模具温度喷 痕成品上可以看到从浇口开始成锯齿状塑料流动的痕跻原因 解决方法/检查要点A. 塑料射入毫阻力的模穴内 1.降低射出速度(检查重量) 2.调整射出速度曲线 注:尤其是刚开始射出的阶段 3.降低射出压力 4.调整射压力曲线注:尤其是刚开始射出的阶段 5.调整料管温度曲线 6.检查浇口的尺寸注:必要的话,加大或浇口尺寸7.检查浇口是否阻塞(污染)且如果必 要的话,调整浇口的位置注:重新安排浇口的位置,使熔胶的流动提早分开8.在模穴内安置阻挡物 注:阻挡物可以使塑料通过浇口时,在模穴内形成阻力光 泽表面不够光泽原因 解决方法/检查要点A. 模具温度太低或者不规划 1.提高模具温度(检查重量)2.检查模具冷却均匀性及有无阻塞 B. 模具表面加工不正确 1.检查模具表面是否受污染 注:必要的话,清洁拋光 C. 塑料温度太低 1.调整料管温度 2.提高喷嘴温度3.提高热浇道温度设定 D. 射出速度不正确 1.调整射出速度成品表面或透视成品时,可以看到斑点.原因解决方法/检查要点A. 塑料受污染 1.检查塑料有无受污染注:避免运送途中及混料系统中受污染B. 不正确的色母 1.用本色料射出,以便检查在此加工条件时母料与色母的兼容性C. 在料管内受污染 1.检查及清洁料管注:用料短清洁剂清洗料管,必要的话将料管分解2.用本色射出来检查料管是否清洁D. 流道及浇口系统受污染 1.检查并清洁流道及浇口系统2.检查热浇道系统的死角E. 在混料系统中受污染 1.检查混料系统中可能受污染的地方表面烧焦Array成品表面在塑料流道的未端烧焦原因解决方法/检查要点A. 空气在模具中无法排出 1.降低射出速度2.调整射出速度曲线3.降低射出压力4.调整射出压力曲线注:尤其在射出的终了降压及速度5.检查成品未填饱的地方,是否排气不良注:必要的话,加入排气口或排气梢6.检查模具排气口是否污染7.检查浇口是否阻塞(污染)8.检查浇口尺寸注:必要的话,加大或重新安排浇口(平衡)翘 曲成品弯曲或扭曲原因 解决方法/检查要点A. 模具冷却系统操作不正常 1.检查模具冷却的均匀度及冷却道有无阻塞2.分别调整公模及母模的冷却 B. 由于塑料定向造成纵向与横向 1.提高料管温度 的收缩率不同 2.调整射出速度3.调整射出压力4.检查浇口位置注:必要的话,增加或重新安排流道位置 C. 由于色母造成成品扭曲1.以下不含色母的色料射出来检查色母与 塑料和成型条件温度之间的兼容性,使射出时不会有下料不均的情况D. 不正确的成型后收缩 1.调整冷却时间注:如果无法排除这个问题的话,则使用冷却定型剂料头脱模不良料头脱模不良原因 解决方法/检查要点A. 由于收缩不良使料头无法脱离 1.降低保压压力2.降低背压(如果没以使用对闭式喷嘴的话)B. 料头拔模不良 1.检查料头的拔模角度及受损情况2.检查料头与喷嘴衔接处的尺寸与R 角.3.检查是否料头的拉拔倒勾不足 注:必要的话,加大料拉拔倒勾 C.因为料头尚未完全凝固而折断 1.降低料管温度 2.调整喷嘴温度 3.使用较小的料头。
模具维修质量提升改善方案

模具维修质量如何提高探讨会议模具维修的因数问题由以下几点1:同一套模具的维修指数高达五次以上,属不正常现场:2:冲针断裂,凹模刀口蹦缺口,卸料板不顶料,内顶块鳖死:3:模具工艺分析结构存在弊端,导柱排放,模具冲击的稳定性:4:模具驾冲床生产选择的吨位存在麻木性:5:模具冲头的烧焊,氩焊导致头部断裂:6:冲床设备滑块未机油保养,模具垫块长期使用有凹凸现象:7:员工对模具不存在爱护性,任地板摆放:8:模具库的模具没有定期保养,地板乱摆放,无按图取模现象:9:冲压员工对模具的保护意识及操作程度存在一定的隐患:10:模具材料的质量调制工艺及冲材间隙,装模精度无法达到模具正常寿命:维修质量提升的初步评定由以下几点1:针对修模指数偏高的模具进行全面性修复及结构分析整改:2:提高冲压工对模具的操作强度意识及爱护心态,模具取放一虑使用站板:3:冲床设备须维护上下滑块座,定期机油保养,模具垫块有出现凹凸现象须磨平:4:驾模工选择模具的吨位冲床须超抗剪强度的力性,保证模具正常生产的稳定性及设备的疲劳度造成的突发因数:5:模具的材料是否存问题及调制工艺须彻查出数据对比,生产原材料的厚度及模具间隙配对一系列数据标准.6:模具的装配不允许用烧焊,氩焊,改用螺丝或铆合形态.间隙配对须注重产品精度要求。
进一步加强装模的精度及意识到模具的生产达标指数.7:后期的模具开发工艺分析须总结之前的不良因数,及一些标准,做进一步的改良,未免造成后续的生产出现类似问题:8:修模工在维修模具之时须全方面检验其它部位是否进一步生产也存在着问题点,避免模具再一次返修现象:9:模具的下模结构,针对复合模的卸料强度须达橡胶的标准回弹高度及10:旧模具维修工艺依然达不到产品要求及正常生产的,可申请报废,结合旧模的工艺分析,从新开模,规范到新开发产品的系列进度中.。
模具改进验证报告范文
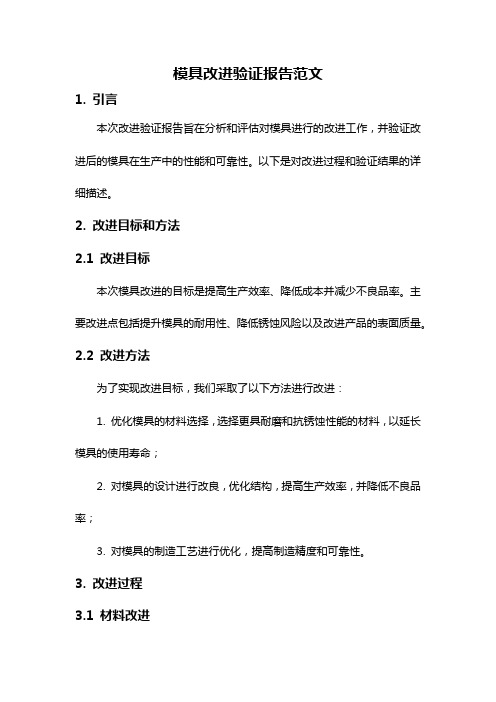
模具改进验证报告范文1. 引言本次改进验证报告旨在分析和评估对模具进行的改进工作,并验证改进后的模具在生产中的性能和可靠性。
以下是对改进过程和验证结果的详细描述。
2. 改进目标和方法2.1 改进目标本次模具改进的目标是提高生产效率、降低成本并减少不良品率。
主要改进点包括提升模具的耐用性、降低锈蚀风险以及改进产品的表面质量。
2.2 改进方法为了实现改进目标,我们采取了以下方法进行改进:1. 优化模具的材料选择,选择更具耐磨和抗锈蚀性能的材料,以延长模具的使用寿命;2. 对模具的设计进行改良,优化结构,提高生产效率,并降低不良品率;3. 对模具的制造工艺进行优化,提高制造精度和可靠性。
3. 改进过程3.1 材料改进我们采用高耐磨和抗锈蚀性能的材料作为模具的制造材料。
这种材料能够有效延长模具的使用寿命,并降低锈蚀风险。
通过对比测试,我们确认选用的材料能够满足改进目标,并提供更好的性能。
3.2 结构优化通过对模具的结构进行优化,我们设计了更合理的构造,以提高生产效率和降低不良品率。
改进后的模具具有更好的流线型设计,减少了产品的缺陷和扭曲。
此外,我们还增加了冷却系统,以降低模具温度和提高制造精度。
3.3 制造工艺优化为了提高模具的制造精度和可靠性,我们对制造工艺进行了优化。
我们使用了先进的数控机床和加工工艺,确保模具的精度和可靠性。
此外,我们还采用了全程质量控制措施,保证每个工序的质量符合标准。
4. 实验验证4.1 生产效率通过对改进后的模具进行生产实验,我们发现生产效率得到了显著提高。
优化的模具结构和制造工艺使得产品的加工速度提高了20%,生产效率提高了15%。
这对于提高生产线的产能和降低生产成本有着积极的影响。
4.2 表面质量改进后的模具能够生产出更加平整和光滑的产品表面。
与之前的模具相比,改进后的模具产品表面质量提高了30%。
该改进对于提高产品的质量和外观有着重要意义。
4.3 耐用性通过长期使用改进后的模具,我们发现其耐用性得到了有效提升。
模具管理评审报告范文

模具管理评审报告范文一、评审目的。
为了确保模具管理工作的有效性、高效性,保障生产的顺利进行,提高产品质量,降低成本,咱就组织了这次模具管理评审。
二、评审范围。
涵盖了从模具的采购、入库、存储、维护保养到报废整个生命周期的管理情况。
三、评审组成员。
由生产部门的老张,质量部门的小李,还有设备管理的小王等几个经验丰富的伙计组成。
四、评审依据。
2. 相关的行业标准,咱也不能落后于行业大部队呀。
五、评审情况。
# (一)模具采购。
1. 采购流程。
总体流程还算清晰,从需求部门提出申请,到采购部门找供应商询价、比价,最后签订合同。
不过呢,有时候这个流程走得有点慢,就像乌龟爬。
比如说上次[具体产品]的模具采购,需求部门都火烧眉毛了,采购流程还卡在某个环节,差点耽误了新产品的上市。
改进建议:建立一个采购进度跟踪表,每个环节设置明确的时间节点,像接力赛一样,一棒接一棒,哪个环节慢了就赶紧催催。
2. 供应商管理。
现有的供应商数量不少,但质量参差不齐。
有些供应商提供的模具质量就像开盲盒,有时候好,有时候差。
像[供应商名称],之前提供的模具精度就达不到要求,导致生产出来的产品次品率飙升。
改进建议:对供应商进行定期评估,就像学校给学生打分一样。
得分高的就多合作,得分低的就淘汰或者让他们整改。
同时,建立一个供应商黑名单,那些老是出问题的就别让他们再来捣乱了。
# (二)模具入库。
1. 验收环节。
验收标准基本明确,但执行起来有点打折扣。
验收人员有时候就像走马观花似的,没有仔细检查模具的各个细节。
有次入库的模具,表面有明显的划痕,但是验收的时候居然没发现,等要使用的时候才看到,这不是添乱嘛。
改进建议:加强对验收人员的培训,让他们知道每个细节都很重要。
验收的时候,要列出详细的检查表,一项一项地核对,确保模具没有问题才能入库。
2. 入库记录。
入库记录倒是都有,不过填写得不够规范。
有些信息模模糊糊的,就像没睡醒写的一样。
比如模具的规格型号,有的记录就写得不清不楚,以后要是查找起来可就费劲了。
模具改善部各岗位描述

模具改善部各岗位描述1. 模具改善工程师职责•负责模具改善部门的整体规划和管理。
•参与并推动模具设计、改进和优化。
•负责制定和执行模具改善计划。
•对模具生产过程进行分析和评估,提出改善建议。
•协调与其他部门的沟通合作,确保模具改进项目的顺利实施。
•持续关注新的模具技术和趋势,提出创新方案。
技能要求•具备良好的模具设计和改善能力。
•熟悉模具制造工艺和材料技术。
•具备良好的问题分析和解决能力。
•熟练运用CAD、CAM等相关软件。
•具备团队合作和沟通能力。
2. 模具工程师职责•负责参与模具的设计和改进。
•应对现有模具的问题和故障,并提出修复或改进方案。
•将设计好的模具转化为CAD文件,并与产线进行对接。
•协助生产部门进行设备调试和生产线改进。
•积极参与模具改善项目,并与相关部门紧密合作。
技能要求•具备较强的模具设计和改进能力。
•熟悉模具制造和加工工艺。
•熟练运用CAD、CAM等相关软件。
•具备问题分析和解决的能力。
•良好的团队合作和沟通能力。
3. 模具项目经理职责•负责模具改善项目的整体管理和实施。
•制定项目计划、进度和资源安排。
•跟踪项目的进展,及时解决项目中的问题。
•协调各部门之间的合作,确保项目的顺利进行。
•汇报项目进展情况,及时反馈项目风险和改进建议。
技能要求•具备较强的项目管理能力。
•熟悉模具制造和改进的流程。
•具备良好的沟通和协调能力。
•具备问题分析和解决的能力。
•具备团队领导和管理能力。
4. 模具技术员职责•协助工程师对模具进行设计和改进。
•进行模具加工和装配工作。
•记录和整理模具的技术资料和相关文档。
•协助故障排查和维修工作。
•持续学习和了解新的模具技术。
技能要求•具备一定的模具设计和改进能力。
•熟悉模具加工和装配工艺。
•具备良好的学习能力和解决问题的能力。
•具备团队合作和沟通能力。
5. 模具操作工职责•根据生产计划,进行模具的装配和调试。
•根据要求进行模具的拆卸和更换。
•定期进行模具的保养和维护。
模具修理改善方案

模具修理改善方案背景随着现代工业的发展,模具的应用范围越来越广,已经成为了现代工业生产过程中不可或缺的重要工具。
然而,长期的使用和运输会导致模具出现不同程度的磨损、变形和损坏,影响了模具的使用寿命和生产效率。
因此,模具修理与维护成为了模具行业中的热点话题和重要问题。
现状目前,模具修理的常见方式主要为二次加工和大修。
二次加工通常是对模具进行一些简单的修补和矫正,适用于一些轻微的损伤。
大修则是对模具进行全面的清理、修复和加工,适用于一些较为严重的损伤。
这两种方式虽然能够完成对模具修复的任务,但是却存在几个问题。
首先,二次加工虽然能够在较短时间内恢复模具的使用,但是只是暂时性的措施,并不能从根本上解决模具的问题。
其次,大修需要耗费较长时间和较高的成本,适用于一些损伤较为严重的模具,对于轻微的损伤使用大修则显得不必要。
最后,这两种方式都需要将模具运输至修复地点,运输的过程中模具可能会再次损坏或者出现一些其他问题,增加了修复难度和修复时间。
改善方案为了解决模具修理带来的问题,开发了一种新的模具修理方案——在线修复。
在线修复采用激光扫描和三维建模技术对模具进行扫描和分析,通过传感器对现场进行实时数据监测,由远程技术人员进行远程控制和操作,可以实现模具的在线修复。
具体步骤如下:1.模具扫描:利用激光扫描技术对需要修复的模具进行扫描。
2.三维建模:根据扫描得到的数据进行三维模型建模,对模具的损伤情况进行分析和评估。
3.远程控制:由远程技术人员进行远程控制和操作,对模具进行修复。
4.实时数据监测:采用传感器对现场数据进行实时监测,以确保修复效果的质量和稳定性。
采用在线修复方案能够解决模具修复面临的问题。
首先,在线修复能够减少模具运输的过程,降低了模具再次损坏的风险。
其次,在线修复的时间较短,可以快速地恢复模具的使用。
最后,在线修复能够有效地解决模具的问题,在不同程度的损伤下,选择不同的修复方案,效果显著。
应用前景在线修复技术的应用前景非常广阔。
模具改善提案2

1.垫片太多,拆模后维修容易搞错
2.最好定位锁螺丝.
定位不好调
1.尽量少用垫片;
2.可能要调的入块和定位,用锁螺丝的方式固定,其他的可用挂台
20
角度偏大,有擦伤
用螺丝固定成型块,便于做模和修模,折弯块的受力比较大,而容易使折弯块往外偏移,使角度偏大
有斜面的成型,最好用2块,一个用销定固定了,另一个便于调整.
序号
问题点
原因分析
改进措施
1
上盖落料模1、夹板与上脱板的后折边冲头不同心,造成不脱料
冲头长,变形
合理分断
2
上盖切边模模具厂改模后拿给我们装配,因为改模,上回料板割二个大镶件而且要换软料,但没有封板,是设计的还是装配的问题,改模把定位改丢了
一般设计成3块小的均匀布置.
3
上盖冲孔模没让位(定位),容易造成产品报废,且影响生产进度
11
底板冲孔模脱料块的没力
弹簧被磨扁,快被磨断了
宁用小一号的弹簧或者铣模板,也不要去磨弹簧的侧面.
12
底板冲机芯孔模在生产过程中,一模多款,模具精度不好
建议下模改成硬料,便于在拆装过程中,影响模具精度及寿命
14
底板二次成型定位不合理,调模时间长,因定位太紧拿不出来,需拆成型块,浪费了很多时间
建议做成螺丝定位,“T”字定位锁在成型块上
定位过矮不好操作
建议定位加高,上模两侧让位孔线割
4
上盖二次成型下脱板尺寸太大,顶到两边的成型块,造成无法调间隙
单边放0.3MM,加2对角内导柱
5
打字模1、铲模,有三个螺丝锁不紧,这些问题经常出现,维修困难
2、螺丝偏位造成字模损坏
3、很多螺丝对不上,造成模具生产过程中走位,字体间隙不均匀
塑胶件水口未削平改善报告

塑胶件水口未削平改善报告一、缺料1、缺陷原因:成品的细小部位、角落处无法完全成型,因模具加工不到位或是排气不畅,成型上由于注射剂量或压力不够等原因,设計缺陷(壁厚不足)。
2、模具改善措施:修正缺料处模具,采取或改良排气措施,增加料厚,浇口改善(加大浇口,增加浇口)。
3、成型改善:加大注射剂量、增加注射压力等。
二、缩水1、缺陷原因:常发生于成形品壁厚或料厚不均处,因热熔塑胶冷却或固化收缩不同而致,如肋的背面、有側壁的边緣、BOSS柱的背面。
2、模具改善措施:减料厚,但至少保留2/3的料厚;加粗流道、加大浇口;加排气。
3、成型改善:升高料温、加大注射压力、延长保压时间等。
三、表面亮印1、缺陷原因:常发生于经过减料厚的BOSS柱、或筋的背面,或是由于型芯、顶针设计过高造成压力痕。
2、模具改善措施:降低火山口;修正型芯、顶针;母模面喷砂处理,降低模面亮度。
3、成型改善:降低注射速度、减小注射压力等。
四、气纹1、缺陷原因:发生于进浇口处,多由于模温不高,注射速度、压力过高,进浇口设置不当,进浇时塑胶碰到扰流结构2、模具改善措施:变更进浇口,流道打光,流道冷料区加大,进浇口加大,表面加咬花(通过调机或修模赶結合线亦可)。
3、成型改善:升高模温、降低注射速度、減小注射压力等。
五、结合线(夹水纹)1、缺陷原因:发生于两股料流汇合处,如两个进浇口的料流交合,绕过型芯的料流交合,由于料温下降、排气不良所致。
2、模具改善措施:变更进浇口,加冷料井,开排气槽或公模面咬花等。
3、成型改善:升高料温、升高模温等。
CNC2改善分析报告(精)

精雕车问CNC2改善分析报告
一,测量吟段 二,分析阶段 三,改善阶段 四,控
制阶段
1 •测董阶段
1.1因果图
测量卧段主晏用子收倂放握.佶以我列玫晏形响因孑乩CTQ (关饨质蚤因素),刮 彩响耕於车间品质效率
的所有因素'对人员.机台.扬料.方出.管理.环境进行分
精雕车间
工裟夹具不艮
燥作不熟练
注意力不集中
妙轮赖坏/徧心
来料不良
车机来料尺
未扶标准方法作业 玻病放JL 不刊依
教导工作缺失
8S 管理不刊£
湿度太高
玻璃掖. 生产迩
机台
沒有进行自检
管理 场料
1・2次要因子及关皱灰量因素
从上图中得刊所有可能彫响玻病质量及生产效卒的因子,用FMEA分析可得关健因素,如下表一所示:
表一
备注:风险指数RPN)二严晅度*可控度*发牛频率,数值越高影响越人需亜点改善。
2•分析阶段
由上述因帛图得到所有可能形响刊生产%质与效率的15个因素.才艮据FMEA表九可得9个次要囲素及6个关键质量囲素,如下表二所示:
表二
3改毎阶段
3.1针对上述9个次要因素进行快速改#,改鸟表格如下表三所示:
3.2针对上述6个关键因素进行持建改改*表格如下表切所示:
4控制阶段
4.1对于改4•后实施描施应发行标准化丈件,如控制计划.操作指引等丈件,及61改專后的效黑。
4.2凡是改垂的一切«标都是囲统成本聂开,层改玉过程中往往会碰刊产量与质方面的相冲突问题.即要求产量则质量受彩响.要求产董则质量受控制,我们改善幺发点也旻找列其中最住的一个竿点.也就旻成本最低的普个点.如下图所示:
成本挫制最佞点控制量。
模具试模次数目标未达成改善报告

模具试模次数目标未达成持续改善报告一、昭和公司原因:1.模具打合时不够详细,导致模具加工中又发现问题。
再与客户沟通、确认,造成工期紧张,模具质量不能完全保证;2.对模具厂的跟踪力度不足,未能及时发现工期、质量方面存在的问题;3.个别机台不稳定加上试模能力不足等,致使前、后试模效果差异较大,误导修理;4.部分型检的检查数据与客户的检查数据差异较大,误导修理,导致修模次数增加;5.有时型检提交检测结果时间过长,耽误了修模时间。
对策:1) 争取打合时间,打合时尽量按排本社、客户、模厂一起打合以便及时发现问题;2) 加强与模厂的联络,在模具修理完之前1~3天到模厂对问题点逐一确认是否修理OK;3) 选择较稳定的机台试模,同一套模具尽量固定机台由同1人负责试模;4) 对一些比较难检测的寸法和与变形有关的寸法要早打合,随时打合。
二、模具厂方面问题:1.个别模厂能力不足,模具结构设计的不尽合理,加工精度不够高, 致使多次修模,增加了试模次数;2.个别模厂太忙,纳期无法保证,致使加工质量难于保证.对策:1) 做好对模厂的评估和选择,根据特长发注P/O;2) 了解模厂的生产情况,然后再确定发注P/O;3) 模具制作完毕或修理完毕后要求模厂先试模,确认外观基本OK或重点修理尺寸OK后再移至公司试模.三、客户方面:1. 安排打合的时间太紧,致使审图时间不够,资料准备不足;2. 提出问题点回复不够及时,耽误了修模时间;3. 由于各种原因(纳期、组立等),客户往往对于不良项目要求先修理一部分,其它部分等下次再修理,这样也导致试模次数增加。
对策:1) 尽量争取多一点审图时间把资料做好;2) 向客户提出的问题点要求客户尽快回复,争取修模时间;3) 对个别修理困难的尺寸,尽量了解一下产品机能向客户提出能否公差变更等要望。
CNC2改善分析报告_2023年学习资料

精雕车间CNC2改善分析报告-一,测量阶段-二,分析阶段-三,改姜阶段-四,控制阶段1.测量阶段-1.1因果图-测量阶段主要用于收集数据,借以找到次要影响因子及CTQ关键质量因素,利用因果图分析-影响精雕车问品质效率的所有因素,对员、机台、物料、方法、管理、环境进行分析,如下图所-示:-工装夫具不良-操作不熟练-机器异常突然停止-来料不良-注意力不集中-砂轮损坏/偏心/抖动车机来料尺大大-小不一致-玻璃报废率高-生产效率过低-未按标准方法作业-教导工作缺失-温度过高-玻璃放置不到位-管理不到位-没有进行自检-8S管理到位-湿度太高-精雕车间1.2次要因子及关键质量因素-从上图中得到所有可能影响玻璃质量及生产效率的因子,用FMEA分析可得关键-因素,如下表一所示:-序号-项目-输入-潜失效结果-严重度可控度-发生频率-风险指数RPN备注-操作不熟练-玻璃报废率增加-8-人员-6-240-作业员疲劳/注意力不集中-5-3-机器异常然停止-玻璃崩裂-10-300-机台-砂轮损坏/偏心/抖动-玻璃尺寸超差/崩裂-7-560-工装夹具不良-车机时间过长/玻璃易损坏-336-来料不-浪费工时-物料-294-车机来料尺寸大小不一致-车机时间过长/玻璃损坏-280-未按标准方法作业-180-玻璃放置不到位-162-没有进行自检-次不良-270-11-没有进行教导-108-12-管理-管理不到位-96-13-7S管理不到位-现场混乱-105-14-环境-温度过高-168-1-湿度太高-备注:-风险指数RPN=严重度*可控度*发生频率,数值越高影响越大需重点改善。
2.分析阶段-由上述因果图得到所有可能影响到生产品质与效率的15个因素,根据FMEA表九-可得9个次要因素及6个关键质量因素,如下表二所示:-项目序号-影响生产/品质因素-人员操作不熟练-作业员疲劳/注意力不集中-3-未按标准方法作业-玻璃放置不到位-没有进行教导-管理不到位-7-8S管理不位-温度过高-湿度太高-10-没有进行自检-11-机器异常突然停止-12-砂轮损坏/偏心/抖动-关键因素-13-工装夹具不良-14-来料不良-车机料尺寸大小不一致3改善阶段-3.1针对上述9个次要因素进行快速改善,改善表格如下表三所示:-序号-工序-问题点-现状分析-建议改善对策-备注-精雕、车机-人员操作熟练-目前人员流动率大,新人较多,导致操作人-员操作不熟悉-加强训练教导,减少老员工流失-作业员疲劳/注意-2-作业员站立作业,劳动强度大,长时间立-改善作业舒适度,适度减小作业强度,必要-力不集中-容易疲劳,影响生产效率,增加人员流失率-时可配备一定数量的板凳-未按标准方法作业-无标准作业,作业随意-完善作业标准并严格按照作业标准作业-4-玻璃放置不到位-玻璃放置不到位导致尺寸偏差玻璃报废-放置玻璃时需检查到位-5-品质安全教导工作缺失-每天新进人员较多,教导工作存在缺失现象-新员工进行品质安全教导,如有必要制作安-全教导表,员工签名确认-管理不到位-现场人员纪律性较弱-加强理,禁止随意走动,打闹,大声喧哗-7S管理不到位-7S管理存在一定缺失-推行7S管理-8-温度过高-环境差,温度高,容易造成员工情绪低落,-改善作环境-湿度太高-影像生产效率品质,增加人员流失率3.2针对上述6个关键因素进行持续改善,改善表格如下表四所示:-序号-工序-现状分析-建议改善方向及措施-备注-精雕R位-没有进行自检-目前精雕R每2小时送3D测试抽-换砂轮必须首检,每10片抽检2-检一次,容易造成成批次不良-片,或每半小时抽检20%-精雕、车机-机器异常突然停止-机器过热卡机造成停机-设备点检到位或安装报警装置,-实现自动停止-砂轮损坏/偏心/抖动-砂轮偏心抖动容易造成玻璃受力-不均歪斜,致使崩裂-砂轮车制时须保证整度-车机目前使用木头夹具,容易使-夹头、工装夹具不良-玻璃松动造成尺寸偏差;精雕则-车机更换夹具材质,精雕夹具及-4-使用铜制夹具,夹具容易磨损-时车铣-成玻璃松动致使尺寸偏移-来料不良-来料崩裂或尺寸偏差-加强品质管控,严格做到不接收,-5-不制造,不流出不良品-车机来料尺寸大小不-线切璃尺寸不一致,造成车机-玻璃受力不一致,容易崩裂-严格控制玻璃来料尺寸4控制阶段-4.1对于改善后实施措施应发行标准化文件,如控制计划,操作指引等文件,及时巩-固改姜后的效果。
- 1、下载文档前请自行甄别文档内容的完整性,平台不提供额外的编辑、内容补充、找答案等附加服务。
- 2、"仅部分预览"的文档,不可在线预览部分如存在完整性等问题,可反馈申请退款(可完整预览的文档不适用该条件!)。
- 3、如文档侵犯您的权益,请联系客服反馈,我们会尽快为您处理(人工客服工作时间:9:00-18:30)。
三.模具改善歷程
4.模具結構問題 原因分析﹕ 跳板結構在加工上易累積加工誤差造
成定位不准﹐使細小入子的損壞機率增
大;同時入子的材質不能滿足此種模具 結構,易斷裂.
三.模具改善歷程
解決對策﹕a.將跳板結構改為油壓抽芯機構減小誤差
b.所有易損入子改為韌性較強的鈹銅材質
未 來 展 望
1. 新材料的應用 目前我們正在開發PAA+60%GF新材料的模具﹐目前已 取得了一定的成果﹐預定在2003年元月上旬完成開發動作。
2. 模具試模次數的減少
我們的目標﹕在2003年度由現在的平均試模4次減低到2次 3. 模具開發成本COST DOWN 在2003年度固定熱流道供應商﹐協助其規格化 熱流道﹐降低采購成本20%及交期由 35days 15days
先開發一模一穴快速兩板模並送樣
客戶對第一次送樣確認和回復
開發第二套一模一穴兩板模快速兩板模並送樣 可 作 為
客戶對第二次送樣確認和回復市場需求
開發第一套一模兩穴的熱流道量產模具
第三和第四穴 備用模
開發第二套一模兩穴的熱流道量產模具
第五和第六穴 備用模
以客戶為導向
一. 在模具開發初階段, 先投入一模一穴﹐兩板模冷膠 道﹐模仁無須熱處理以加速模具開發, 並迅速送樣.
以客戶為導向
二. 客戶市場如果反應良好, 並須大量生產, 總結前兩套模 具開發經驗再開發一模兩穴的熱流道量產模具。
那麼前兩套一模一穴的兩板模就變為備用模, 如有量產 模修模或客戶產量擴充便可投入生產。
以客戶為導向
三. 客戶訂單非常大時﹐ 總結前幾套模具開發經驗再開發 一套一模兩穴的熱流道模具, 進行加大量生產.
c.加強排氣以便減低射壓降低入子的受力 改善結果﹕油壓抽芯機構能明顯降低入子的損壞率, 大大提高生產效率﹐由原單組模具日產能 2.5k增至目前的
4K
降低了出貨壓力
四.改善成果
經一系列的改善﹐現在1B03 C-COVER成型穩定﹐保証了生 產的順利進行﹗
四.改善成果
1B03 C-COVER模具的較歐洲及韓國先行開發成功, 為公司贏得了此配件全球供貨的商機及客戶對公司模 具研發及制造能力的肯定.為滿足供貨需求﹐提高產 能﹐此模具已開復制模共12組. 同時手機專案同仁在此模具的開發過程中吸取了許 多失敗的教訓﹐積累了對此類新材料的應用及模具開 發的丰富經驗.
成品不易飽模
4.模具結構問題
模具結構中的許多細小 入子極易損壞﹐平均上機 8h左右就 得更換 入子
跳板結構
三.模具改善歷程
1.毛邊﹕
原因分析﹕該產品邊緣壁薄最尖處肉厚只有0.2mm﹐而
深度卻有7-8mm﹐當時為了考慮到加工和拋 光的方便 ﹐公母模的薄壁處均拆為入子成 型﹐但實際証明該方式行不通。
無形成果
在管理運作的層面上建立新工管流程﹕ 原型機模﹕ 用3-7天的時間開發1模1穴的原型機模 ﹐用此模具滿足客戶趕交期以及不斷設變的需求﹐ 直到客戶完成設計定稿。 正常樣品機模﹕客戶完成設計定稿后﹐ 3-7天的時 間內加開一套一模一穴的正常樣品機模﹐以迎合客 戶小批量生產需求。 量產模﹕客戶產品達到量產階段時﹐加開1模2穴的 熱流道量產模。視客戶定單靈活安排模具上機台生 產﹕ A﹐1模2穴 (2套 1模1穴做備用) B﹐1模2穴+2 套 1模1穴擴大生產量﹐滿足定單。C﹐2 套 1模2穴 (2套 1模1穴作備用檔)
鴻準WLBG塑模總廠 NOKIA&TCL手機模具品質改善報告
從制造導向到客戶導向
報告人: 姜貴揚﹐蔣波 宏﹐ 2002-12-27
報告內容
一。1B03 C-cover成品簡介 二。模具開發過程中所遇到的問題 三。模具改善歷程 四。改善成果 五。未來展望 六。結束語
一.Vanessa C-cover成品材料簡介
結 束 語
新 年 快 樂
我們塑模開發手機專案全體同仁有信心陎對未 來﹐迎接新的挑戰。同時歡迎對塑模感興趣的同 仁與我們共同探討﹐不吝賜教﹗ 感到有困難就是能力不足, 感到有問題就是方法不對!
謝 謝 大 家
﹗
﹗Байду номын сангаас
TCL-3688 AND GA-16成品展示
TCL-3688
TCL-GA16
制造導向
一.模具開發的初期我們秉持以成本為考慮的制造導向。
試模過程中卻存在著不盡人意之處
2. 塑料流動性問題:
客戶要求使用的塑料是PC LEXAN 141R流動性 較差,採用三板模且多穴時流道較長影響了成品的 成型質量。
試模過程中卻存在著不盡人意之處
3.成品縮水與成品毛邊:
毛邊
由於客戶成品屬于薄壁件﹐而且厚度變化劇烈﹐再 加上成品材料比較特殊﹐決定了成品在成型時容易在縮 水與毛邊兩種情況中徘徊,調整成型參數難以得到很好 的控制!
爲了節約成本,提高產能,在模具開發之初較先考慮 的是一模兩穴的三板模,其優點是自動化強,一模多穴可 以提高產能,模具成本相對較低。
試模過程中卻存在著不盡人意之處
1.成品陎粗度問題:
15
18
21
客戶要求成品陎粗度要達到15#,此型號陎粗度加 工存在著較大的困難,此前諾基亞,摩托羅拉的要求 只是21#。經過加工部門的努力,並與客戶協商﹐最 終達成一致,客戶同意將成品陎粗度改為18#。
Vanessa C-cover所使用的成品為:PBT+PET+20GF%
特性 ﹕
1.很高的耐熱性和機械強度 2.吸水率低 3.耐腐蝕 4.耐彎曲蠕變性 5.阻燃品質好
二.模具開發過程中所遇到的問題
1.成品毛邊問題
2.成品平陎度及尺寸問題 3.成品縮水及不易飽模問題
4.模具結構問題
1.成品毛邊問題
那麼前兩套一模一穴的兩板模就變為備用模, 如有熱流 道模修模或客戶產量擴充便可投入生產的第五和第六穴.
有形成果
先以TCL3688翻蓋面殼作比較﹕
模號 比較項目 成型時間 修模次數 廢料重量 模具費用 冷澆道 三板模 熱澆道 月比較 可節約費用
30sec/cicle 8sec/cicle 4次/周 13g 35萬NT$ 0 次/周 0g 50萬NT$
試模過程中卻存在著不盡人意之處
4. 模仁材料選擇欠妥:
爲了趕交期及便於加工,當初選擇了未經熱處理的 S136H鋼材,強度不足﹐在實際生產時由於射壓較大,影 響了模具的壽命及生產的穩定性。
針對上述問題我們將整個流程做檢討, 決定“以客 戶為導向”, 最快生產合格產品給客戶的策略, 並作如 下改善:
三.模具改善歷程
3.成品縮水及不易飽模 原因分析﹕縮水處成品太厚﹐不易飽模處成品肉 太薄,使熔融材料易冷不易充填飽模 解決對策﹕a.成型調機處理﹐適當加溫加壓加速 b.在肉薄處加設鈹銅入子 改善結果﹕ 加設鈹銅入子后及在成型調機配合 下明顯改善了成品縮水及不易飽模 的問題.
三.模具改善歷程
4.模具結構問題
316800個 16次 2059Kg _15萬NT$
139萬NT$ 16萬NT$ 4萬NT$ _15萬NT$ 144萬NT$
總改善結果
無形成果
在技朮層面上建立原型機快速模具標准 化系統及應用運作系統﹐滿足所有手 機快速模具開發應用。
正在設計涵蓋所有手機零件的五種標准模具結構 (TPYE1-2-3-4-5) 建立標准品庫存系統﹐滿足3-7天內完成原型機快速 模具開發。
所有模具分型陎 及零件合配處(靠 破及插破處) 易產生毛邊
2.成品平陎度及尺寸問題
客戶要求平陎度小于0.2 ,實際為0.4以上; 客戶要求總長尺寸為105.17mm,實際為:104.80mm.
3.成品縮水及不易飽模問題
此處成品肉厚0.4mm
此區域成品厚0.6mm
此螺絲柱的外側(上圖畫 圈處母模陎) 縮水
3. 采用新的排氣方式
四陎錐度 0.5錐度
三.模具改善歷程
解決對策二(改善排氣方式)﹕
改善后排氣槽方式
三.模具改善歷程
2.平陎度及尺寸不合格 原因分析﹕a.產品設計不合理
b.模具水路設置不當﹐冷卻平衡不好﹐ 模具各點溫差太大. c.成型條件不合理.
d.材料廠商給出縮水率與實際縮水率有 出入.(X=1.002 Y=1.004 Z=1.004)
到目前為止TCL3688的產量已經達到8K/天﹐正 向10-15K/天的產能爬升。 TCL GA16運用新工管系統﹐已經完成原型機模 的開發﹐正在配合客戶設變修改﹐我們有信心 一定圓滿的滿足客戶需求。 而且﹐在新工管系統順利運行下﹐預計2003年 完成國內手機1500萬台。
謝謝大家!!!
三.模具改善歷程
解決對策﹕a.建議客戶改成品﹐在肉厚不夠處加R角﹐ 加加強肋﹐提高產品的接合強度 b.重新編排水路,單獨接水 c.嘗試DOE(各種成型條件). d. 改變成品在X,Y,Z方向的縮水.(X=1.0035 Y=1.002 Z=1.004)
改善結果﹕綜合以上對策很好的解決了產品的平陎度 及尺寸問題.
三.模具改善歷程
解決對策一﹕入子與公母模仁的配合間隙由0.015mm減 至0.01mm
有沒有更好的辦法呢??
改善結果﹕毛邊問題并沒有得到明顯的改善。嘗試換
用PC+ABS料進行注射成型結果完全沒有毛
邊﹗可見PBT+PET+20%GF這種陌生的材料對
我們模具加工作出了挑戰﹗
三.模具改善歷程
解決對策二(入子加錐度)﹕ 1.公母模仁均做成整體式﹐取消以前的鑲嵌 2.斜梢及入子拆成錐度配合
以客戶為導向
二. 針對客戶對第一次送樣的回復, 對第一套模具進行修改, 并根據客戶的開發進度決定是否要開第二套一模一穴冷膠 道兩板模﹐此時模仁需要熱處理﹐這套模具被稱為樣品機 模具。
以客戶為導向