塑胶射出技术简介
塑胶射出成型

收缩下陷 收缩下陷是成型品表面呈现凹陷的现象,主要原因是 熔融材料冷却固化时的体积收缩所致。收缩下陷易发生 于成型品肉厚较厚部位、肋、凸毂的背面、注道的背面 等肉不均的部份。因此为了防止收缩下陷,基本上,成 型品的设计要适切。 收缩下陷是成型品收缩所致,易见于PE、PP、PA等 成型收缩率大于结晶性塑料材料。反之,以玻璃纤维强 化的塑料或充填无机质的塑料材料之成型收缩率甚少, 故其收缩下陷可减至最小。
19
流痕 流痕是熔融材料流动的痕迹,以浇口为中心而呈现的 条纹模样。 流痕是最初流入成型空间(模穴)内的材料冷却过快,而 与其后流入的材料间形成界线所致。
银白纹 银条是在成型品表面或表面附近,沿材料流动方向, 呈现的银白色条纹。
20
烧焦 一般所谓的烧焦,包括成型品表面因材料遇热所致的 变色及成型品的锐角部位或谷部、肋的前端等材料焦黑 的现象。 烧焦是滞留在模穴内的空气,在熔融材料进入时未能 迅速排出,被压缩而显著升温,再将材料烧焦所致。 黑条 黑条是在成型品上有黑色条纹的现象,其发生的原因是 成型材料的热分解所致;常见于热安定性不良的材料。 有效防止黑条发生的对策是防止加热缸内的材料温度过 高,减慢射出速度
13
毛边 熔融材料流入分模面或侧向滑板活动间隙时,会发生毛 边。 发生毛边的原因,基本上除了射出机对成型品的投影 面积无充分的合模(锁模)力之外,大都是模具与成型材料 所致。模具配件发生间隙或配件密着性不良的原因,是模 具设计制作不当或模具配件变形及磨损。模穴的熔融材料 流动性太好时,也会造成毛边,防止的方法是降低模具温 度、材料温度、射出压力及射出速度,但必须配合前项充 填不足问题,否则可能造成解决毛边问题而造成充填不足 的现象发生。
翘曲、扭曲 翘曲、弯曲都是从模具取出的成型品产生之变形,平 行边变形者称为翘曲。对角线方向的变形称为扭曲。 这些变形为成型时的各种内应力所致,原因大别如下: (1)脱摸时的内部应力所致。 (2)模具温度控制不充分或不均匀所致。 (3)材料或填充料的流动配向所致。 (4)成型条件不适当所致。 (5)成型品形状,肉厚等所致。
塑胶射出成形的原理

6.射出成形用材料---加熱則軟化的塑膠
成形收縮率
成形品的尺寸(常溫)通常都稍微小於模具尺寸(常溫),這縮小的比例叫做成 形收縮率.
各种塑膠的成形收縮率不同,例如聚苯乙烯是0.4%,而聚丙烯是1.6%(表1).
成形收縮率比較小的一群是結晶性小(非晶質)的材料,通常其粘度受成形時
的溫度的影響小,不會因溫度上升
射出成型現場實用技術手冊
使用塑膠材料應注意點
1.精密度稍差:膨脹係數大,通常比金屬類多一位數.此外,有些塑膠會因 濕度或經久變形或發生尺寸變化.
2.耐熱性通常不佳:耐高溫性較差,通常不超過100oC. 3.可燃性:大部分屬於可燃性,有些塑膠燃燒時產生有毒氣體.焚化時,容
易產生黑煙或腐蝕性氣體,或發熱量過大,容易損傷焚化爐. 4.強度不夠:除通常提到的破裂強度外,實際上則因剛性不足發生的困
熱硬化性塑膠:thermosets plastics
加熱則硬化的塑膠.成形後加熱固化. 酚樹脂,美拉明樹脂,尿素樹脂,聚酯,環氧樹脂,聚醯亞胺等. 成形: Molding,製成形狀物. 成形品: Moldings,經成形的塑膠製品. 模具: Mold,成形用的模(注進塑膠用). 射出成形: Injection molding 成形粒: Pellet,米粒狀的熱可塑性塑膠成形材料. Mpa : mega pascal : M=106(100萬倍) 1Pa = 1 N/m2 1N (牛頓) = 0.102kgf 1MPa = 10.2 kgf/cm2
流動狀,即變為可塑化狀態. • 3.這可塑化塑膠被柱塞擠向前方,由缸尖端的注嘴注入密封模具內,即射出. • 4.等模具內塑膠冷卻硬化後,打開模具,拿出成形品. • 5.一般使用的成形機都採用如圖2的螺桿式.
射出成型基本

射出成型基础1)何谓塑胶塑胶是在成型加工过程中可以给予加热加压之高分子物质。
高分子物质虽然有然树脂和合成树脂,一般所谓的塑胶是指由石油提练出来的合成树脂。
塑胶有一个很大的特征,就是加热后会变型的特性。
因此可以很简单大量生产出各式各样的产品。
塑胶大致可分为热可塑性树脂和热硬化性树脂两种,大部份制品皆由这两各塑胶制成。
热可塑性树脂为在加热溶解流进模具内,再加热后会变硬,一旦硬化后,再怎么加热也不会变软的特质之塑胶。
还有最近有种叫耐高功能树脂和金属一样的强度,耐热及耐冲击之塑胶,跟人的皮肤一样很软一样很软之塑胶也已被开发,应用在各个领域。
2)何谓射出成型把材料加入加热筒加热溶解,在模具内进行注入(射出)以模具来冷却溶解材料而做成之成型品。
3)射出成型所必备之条件1.成型材料(树脂)2.材料干燥机(热风式,除湿式,真空式)3.射出成型机4.模具模温机(媒体:水,油,加热器)5.取出机6.粉碎机7.成型技术4)射出成型条件之5要素温度时间量(位置)根据这5要素之组合来找出成型条件速度压力5要素经常维持在安定及平衡下,就可做出安之成型。
温度材料干燥、加热筒温度、材料温度、模具温度、成品取出温度、室内温度、作动油温度、冷却温度时间材料干燥时间、计量时间、充填时间、保压时间、冷却时间、周期时间位置(量) 从料筒加入材料量、射出开始位置、射出最前进位置、射出终了位置、计量开始位置、松退量、射出量速度(螺杆回转) 、射出速度、开关模速度、顶出速度、松退速度压力5) 何谓成型条件先确认想要(设定)怎样的成型条件之5要素及怎样的(结果),再确认成型之成品在何种程度(设定范围)及(结果范围)为良品.成型条件表所必需记载之要件:A.记载设定值的范围及最终设定置B.记载结果的范围及最终结果C.记载成型品发生不良之位置2.找成型条件之顺序1) 在找出成型条件之前先了解成型之材料、成品、模具为何.A 确认树脂的特性在何种程度的时间,必须要以怎样的方法来干燥干燥不够不只会造成成型不良更会造成成形品原有特性降低.树脂温度在何种程度的温度范围内可以成形以何种程度的温度溶解,以何种程度的温度来分解.模具温度以何种程度的温度范围可以成形热变形温度为何种程度成品(模具)为何种厚制品或薄制品以此作为设定射出时间、冷却时间、材料温度、模具温度之判断基准.形状为何、充填不足时间可以脱模吗?以此作为设定射出速度、射出压力、材料量判断之基准.模具调温方式确认是用水调温,油来调温或是用加热片来调温.2) 成型的准备(1)料的干燥再确认温度、时间、方法。
射出成型基本原理.ppt

a.昇高料管溫度 b.昇高模具溫度 c.降低射出速度 d.加寬進澆口(如扇形) e.在豎澆道與橫澆道的接 縫或橫澆道分岐點.設材料 滯流區(冷料區).
九.銀條(起瘡)
原因
解決對策
原料中水份或揮發分.附 著模面的水分等氣化所 致成形機螺桿卷入空氣
a.原料必須依特性及作業 標準卻實除濕乾燥. b.增高模具溫度. c.降低料管溫度. d.減低射出速度. e.降低射出壓力. f.昇高螺桿背壓.
持在和初期粘度幾乎一
壓力降低太多時,就
樣的低粘度之流路設計 (流逆、澆口設計)及 成形條件是最理想的狀
會產生射出不足、縮 孔、焊線等成形不良。
況。
(四)、保壓工程
• •
•
•
模加若會封壓就少施 膛壓澆從前封是必加 而力口澆停人澆須的 造則密口止模口利壓 成壓封部保膛部用力 浪力後消壓內的澆保 費不仍失的。固口持 。會然,話在化密時
程
(三)、射出工程
• 1、適當的前端流動速度
• 通常,被射出的熔融樹脂,會流經澆道、流
道、澆口等流路進入模腔內。此時,為了使澆 道、流道部份之樹脂的前端流動速度對模具溫 度產生最小的影響,且提高剪斷發熱效果,基 本上應該是愈快愈好,但有些澆口方式會使成 形品發生射流,或在模腔部份速度太快或太慢 時,都會發生各式各樣的外觀不良。為了解決 這個問題,每一個流路都要進行射出速度的控 制,所以通常都會使用可以讓前端流動速度維 持在適當速度的多段射出速度控制成型機。
..
•
!
不 惜 賜 教 , 謝 謝
講 解 完 畢 , 請 大
20 04 07 14
家
等所 進以
1
行必 1
充須 分以
等
響成直使中 燥 的,未果 射 均 埃
塑胶射出机的工作原理

塑胶射出机的工作原理塑胶射出机是一种常见的塑料加工设备,主要用于将熔化的塑料通过压力射入模具中,形成所需的产品。
塑胶射出机的工作原理是一个复杂的过程,涉及到塑料的加热、熔化、注塑和冷却等多个环节。
下面将详细介绍塑胶射出机的工作原理,并分点列出各个环节的具体步骤:1. 塑料粒子的供给:塑胶射出机首先会将塑料粒子供给给料系统。
这些塑料粒子通常以颗粒状的形式被储存在料斗中,并通过给料机构被输送到加热筒内。
2. 加热与熔化:在加热筒中,塑料粒子会受到高温加热,直至达到熔化温度。
加热筒附近有一个加热圈,通过加热圈传递热量,将塑料颗粒加热到熔化点。
熔化后的塑料变成了一种粘稠的液体状态,称之为熔胶。
3. 射出系统的工作:熔胶进入射出系统后,通过螺杆的旋转将被推入射出筒中。
射出筒靠近射出模腔的一端设置有喷嘴,喷嘴通常有一个细小的孔,通过控制喷嘴的开启和关闭来控制塑料的流动。
当螺杆向前运转时,熔胶被推向喷嘴,并通过模腔中的孔口进入模具。
4. 模具的充填与冷却:熔胶进入模具后,会根据模具的形状充填成所需的产品形状。
在充填的同时,模具表面接触到的熔胶会迅速冷却,使得塑料变硬并保持所需的形状。
模具的冷却通常通过冷却水或者其他冷却系统来实现。
5. 模具开合与产品脱模:当塑料充填完毕并冷却后,模具会分离开来,形成成品。
模具的开合通常由液压系统控制,以确保模具的平稳运动。
一旦模具打开,成品产品就可以从模具中取出,完成整个射出过程。
需要注意的是,塑胶射出机的工作原理在实际生产中还需要考虑一些其他因素,如料温、射胶压力、模具温度等。
这些参数的调整会直接影响塑料制品的质量和生产效率。
总结起来,塑胶射出机的工作原理是将塑料粒子加热并熔化,然后通过射出系统将熔胶注入模具中,再经过冷却后形成所需的产品。
整个过程需要靠各个系统的协调工作,包括塑料供给、加热熔化、射出、模具充填与冷却等环节。
这种工作原理是目前塑料制品生产中最常用的方法之一。
塑料射出成形的原理
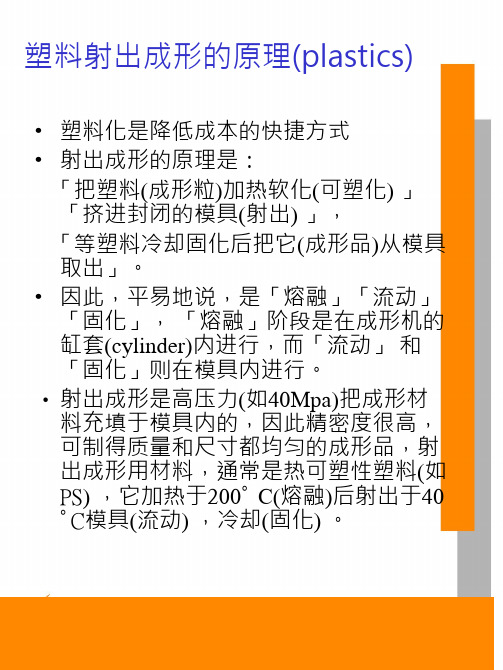
• 塑料化是降低成本的快捷方式 • 射出成形的原理是: 「把塑料(成形粒)加热软化(可塑化) 」 「挤进封闭的模具(射出) 」, 「等塑料冷却固化后把它(成形品)从模具 取出」。 • 因此,平易地说,是「熔融」「流动」 「固化」, 「熔融」阶段是在成形机的 缸套(cylinder)内进行,而「流动」 和 「固化」则在模具内进行。 • 射出成形是高压力(如40Mpa)把成形材 料充填于模具内的,因此精密度很高, 可制得质量和尺寸都均匀的成形品,射 出成形用材料,通常是热可塑性塑料(如 PS) ,它加热于200゚ C(熔融)后射出于40 ゚C模具(流动) ,冷却(固化) 。
浇道(runner)及浇口(gate)-型式2
• 侧面浇口(side gate)
•
•
•
•
特点:由模穴侧面或边缘进浇,最通用之浇口型, 矩形较多,亦称矩形浇口。 优点:易加工,成型品尺寸精确,浇口尺寸易加 工修改,分离容易,可防止塑料在射出过 程中发生逆流,浇口部分之摩擦黏滞生热 可帮助充填进行。 缺点:浇口移除之后加工较麻烦,成型品表面常 有浇口移除所留下痕迹,较不美观,压力 损失大,塑料充填性不佳,有时易造成充 填不足或中途固化。 用途:适用于大部份塑料。
L型的改善对策(3)
L型的改善对策(4)
流道设计的基本考虑一
流道设计的基本考虑二
• 单模穴或多模穴 • 自然平衡流道(多模穴模具) • 浇口数目 • 浇口位置 • 浇口形状 • 浇口尺寸 • 流道配置(多模穴模具) • 流道截面形状 • 流道尺寸 • 流道系统与成品重量比例 • 流道系与顶出机构的配合 • 节省塑料
流道设计的基本考虑三
• 流道系统对成品质量的影响
塑胶射出简介(1)

螺桿往復式射出裝置
動作原理及優點近似於螺桿預塑式,是國內採 用最多的射出成形機型式。
射出成形原理(1)
由固體塑料至產品成形大致可分為四個階段: (1)固體塑料的塑化階段輸送,並累積於螺桿前端,所產生的熔膠壓力會將螺桿往後推, 因而在螺桿前形成熔膠室。塑化過程的目即在於獲得到高均質性 的熔膠並累積於熔膠室。 (2)模穴充填階段 螺桿不旋轉,以類似活塞狀前移,將熔膠以高速注入模穴並使其 填滿模穴各部份位置。
模具需具備之條件(動態方面)
在射出成形機鎖模壓力下,模具鋼材須有足夠的抗壓縮強度,不 會發生塑性變形或被壓碎裂的情形。 在射出成形機射出壓力下,模具鋼材在強性變形範圍內的變形量 須比樹脂的收縮量小。成品被頂出時,不會發生嵌口及表面刮傷 的情形。 在頂出壓力下,頂出銷截面積對頂出銷長度比不可過大,以防頂 出銷彎曲,可採用階段式頂出銷。頂出銷輿成品接觸的面積應儘 量大,以防成品有頂白的情形。 特殊結構體需堅固,動作行程需確實,以防撞壞模具本體,滑塊, 側蕊,壓板及旋退裝置。
塑膠的一般特性(缺點)
(1)耐熱性差-大部份的塑膠耐熱溫度約 在150℃以下。 (2)機械強度差-承受負荷,易生變形。 (3)低溫時易變脆性。 (4)大都為易燃物,且燃燒有毒性氣體產 生。
塑膠的分類
依溫度效應分類: (1)熱塑性塑膠-熱塑性塑膠在加熱時會隨溫度之升高而逐漸軟化, 但冷卻後則又固化稱之。屬於此類之塑膠有:PS、 ABS 、 AS 、 PC 、 PE 、 PP 、 PVC 、 PVDC、 PVAC、PVB、PA、POM 、 CA、CN、CAB、EC、PMMA、 PETP、PTFE、SI及氟素樹脂等。 (2)熱固性塑膠-熱固性塑膠在加熱之初被軟化而有可塑 性,再繼續加熱則成固化之物質稱之。 屬於此類之塑膠有:PF、UF,MF、PDAP 、UP 、 EP、PUR及伕楠樹脂等。
塑胶射出成型技术

塑胶射出成型技术射出成型技术射出理论1. 射出原理:乃利用塑料之热可塑性,2. 先将塑料原料经螺杆运转摩擦生热及料管电热之辅助而3. 溶解使成流体状态。
在经杜塞压力注入,4. 设计之模型穴内,5. 经冷却后取出而6. 成各种特殊形状之成形品。
7. 射出流程:锁模→射胶→熔胶→松退(冷却)→闭模→顶出成品认识塑胶:一般塑胶分类为两种(A)热固性(B)热可塑性,射出成型加工均使用热塑性塑胶。
热可塑性塑胶有两种区别分:结晶性塑胶及非结晶性塑胶一般结性塑胶在成型过程会结晶化成形收缩率较大,成型表面光泽良好。
1.结晶性塑胶有下列:PE PP PA PBT POM PPS PET非结晶性塑胶有下列:PS PBT POM PC PVC2.工程塑胶有下列:PA PBT POM PC NORYL(PPO)特殊工程塑胶有下列:PPS PET射出成型材料之成型条件成型时使原料恰当熔融所需之热量及温度;因为每种原料之熔融温度即比热不同而不同(此资料可由原料商提供)温度之设定可依照螺杆设计:进料段-低、压缩段-高、计量段-次之。
温度过低原料熔融不均、色泽不均、温度过高使原料分解变质。
射出成型条件之高设定1.锁模压力:锁模压力必许大於塑胶射入模内之总压力,过高塑料即可能由分模而溢出,锁模太大(过高)会损耗机器、模具及浪费电力,故适当的调整锁模。
是以成品射入模内分模面不出毛边为原则。
2.熔胶量之设定:首先找寻生产机器之最大射出量(PS)及螺杆之最大行程之资料最大射出量(PS)/螺杆最大行程=A(成品+夹头)重量/B=所需设定之熔胶A*生产原料之密度=B3.射出压力、速度、位置之设定:可利用分段射出,先设定一段之速度及压力位置后对照成品,再设定下一段之速度、压力位置以此类推、一般成型不管用几段射出,在完成之前一段必须调整到80%-90%,最后一段压力、速度均小,当保压用,位置用来控制毛边或缺料。
如果成品还是缩水可利用保压来补其不足。
塑胶射出机简介

塑膠射出機簡介塑膠射出機是利用高分子材料(熱塑性、熱固性),將材料加熱,使其達到熔融狀態,再藉由螺桿的壓力,使熔融狀態的材料射入模具中,然後在模具中冷卻成型(熱固性材料,是經由加溫使材料成型,需注意材料的熱膨脹係數,讓模具可以閉合的範圍內),這是塑膠成型中最重要、最普遍使用的技術。
射出成型之優劣優點缺點1. 產量高、生產速度快 1. 成品單售價低2. 材料價格低廉 2. 模具設計及製作成本高3. 可回收利用(熱塑性材料) 3. 機台及周邊設備成本高4. 製造大體積產品容易 4. 市場競爭大5. 需要工作人員少6. 可自動化生產高分子材料之簡介不同的高分子材料都有它的特性,而這些材料的製造條件都大不相同,產生出來的功能也不一樣,這些因素都會影響成品的結構強度及彈性,所以在製造塑膠成品時,我們必須先知道成品是要用於何處,了解它所需的功能,再選擇適當的塑膠材料來製造,使用塑膠材料時必須注意材料的縮水率,因為每個材料的縮水率都不同,以免造成成品尺寸上的差異。
常見的塑膠材料1 聚乙烯(PE)優點缺點1. 耐塞性優 1. 耐熱性劣2. 衛生無毒 2. 耐候性劣3. 耐水性、耐藥品性優 3. 成形收縮大4. 電器特性優5. 柔軟性優(LDPE)用途1. 各種容器(密閉容器)2. 包裝袋3. 玩具類4. 廚房用品5. 機械部品2 聚丙烯(PP)優點缺點1. 耐熱性優 1. 低溫時的耐衝擊性劣2. 塑膠中最輕者 2. 耐候性不佳3. 電氣特性優4. 耐藥品性優用途1. 各種容器(耐熱用)2. 玩具類3. 耐熱的工業部品3 聚氯乙烯(PVC)優點缺點1. 柔軟程度可自由調整 1. 耐熱、耐寒性劣2. 硬且強韌(H) 2. 耐衝擊性劣3. 耐候性優 3. 耐撓曲性劣4. 耐水性、耐藥品性優5. 價格便宜用途1. 玩具類2. 透明瓶子3. 水管4 聚苯乙烯(PS)優點缺點1. 成形性佳 1. 耐衝擊性劣2. 剛性佳、表面硬度大 2. 耐熱性、耐候性劣3. 透明性優 3. 可溶於溶劑4. 電器特性優5. 抗酸、鹼性佳用途1. 玩具類2. 文具3. 梳子5ABS優點缺點1. 外觀物性佳、價格合理 1. 耐候性劣2. 電鍍特性優 2. 可溶於溶劑3. 在低溫時耐擊性優4. 成形收縮率小,尺寸精度優5. 抗酸、鹼性優用途1. 玩具類2. 電池箱3. 日用品6 POM優點缺點1. 強韌、富彈性 1. 耐候性劣2. 耐疲勞性特優 2. 抗強酸力弱3. 具自潤性,摩擦抵抗小4. 耐藥品性5. 耐熱性優用途1. 需負荷重之工業用品(GEAR、CAM、SPRING)2. 汽車、電器製品3. 玩具類4. 金屬的代替品7 PMMA優點缺點1. 透明性特優 1. 耐衝擊性劣2. 硬度高、表面光澤性優 2. 易有傷痕3. 耐候性優4. 成形性良好5. 電氣特性好用途1. 代替玻璃的工業材料(防風鏡、電視防護鏡、鍾錶)2. 電氣器品(照明器具)3. 隱形眼鏡射出成型機料斗料斗可以存放一定數量的塑膠材料,可避免補料不及。
1.塑胶镜片射出成型技术简介

塑膠鏡片射出成型技術簡介第一章:簡介1-1塑膠鏡片的優缺點製品的產量高、價格低,又可實現輕薄短小的產品需求,但以往被認為精度不高,無法取代傳統的金屬或玻璃等。
但近年來由於塑膠材料的研發及射出成形技術的精進,已經大大的改變了這個市場。
在光學元件的領域中,塑膠鏡片早已進入了高精度的時代,從早期拋棄式的相機鏡片,到現在需要高精度的讀取頭物鏡,塑膠鏡片充分發揮塑膠產品的特色,也超越了塑膠產品的瓶頸。
在光電產業蓬勃發展的今天,本課程將帶領各位進入塑膠鏡片射出成形的技術領域,瞭解鏡片的開發流程和相關技術。
塑膠製品生產速度快,適合大量及自動化的生產,所以容易降低價格﹔塑性良好因此耐衝擊﹔因為塑膠比重低,因此重量相對的較輕,可以讓整個系統重量降低﹔而且成品形狀自由度高,可以將系統的機構元件與光學元件合併,減少零件數量,並簡化系統組裝程式﹔利用這樣的優點,我們可以設計特殊架構的光學元件。
有優點就有缺點,塑膠的缺點有:溫度特性差:和玻璃相較,塑膠容易受環境影響光學特性。
因為一旦耐熱溫度低,熱膨脹係數大,光學元件就會變形而影響光學特性。
精度較玻璃低:塑膠由於材料特性的關係,因此不均勻性較高,容易產生收縮變形,導致精度不容易控制。
抗刮力差:塑膠的機械強度較低,材質的硬度不像玻璃堅硬,因此抗刮力差。
與光學玻璃相較,材料種類較少:由於光學玻璃發展已有很長一段時間,所以塑膠鏡片和其相較之下,材料種類較少,而且折射率較低,大約在1.5到1.6之間,分佈較狹窄。
有雙折射現象:造成光學性能降低。
要有一定的產量才符合經濟效益:塑膠射出成形的模具價格十分昂貴,一個模具開下去,可能需要幾十萬或百萬的費用,所以如果沒有達到一定的產量規模,便不符合經濟效益。
大小受限制:塑膠鏡片射出成形在∮100mm以上的精度不足,會有成形上的問題,也可以說尺寸愈大,精度愈難控制。
1-2塑膠鏡片的應用塑膠鏡片可以應用在相機、數位相機用的觀景窗、鏡頭鏡片;投影機、背投式電視用的鏡頭鏡片;最好的例子是CD/DVD讀取頭上所用的pickup lens 、grating lens、DOE,年產量在數億顆以上;還有LCD面板上的背光板、導光板也可以看到塑膠鏡片的應用;在各種光學系統中,光學元件適合在塑膠鏡片上作微細結構,產生繞射、折射、分光或偏光現象,因此也適合應用在Frenel lens, F-θ lens上。
机构件认识--塑料射出成型

机构件认识–塑料射出成型引言塑料射出成型是一种常用的塑料加工方法,广泛应用于各个领域,包括汽车、电子、医疗等行业。
本文将介绍塑料射出成型的基本原理、工艺流程以及常见的机构件制造。
一、塑料射出成型的基本原理塑料射出成型是将加热熔化的塑料通过高压注射到封闭的模具腔内,待塑料冷却固化后,通过开模取出成型的一种加工方法。
其基本原理包括以下几个环节:1.加料和熔融:将颗粒状塑料原料加入射出机的进料斗中,通过螺杆转动将塑料原料逐渐推进到加热筒内进行熔融。
2.射出和充模:熔融的塑料通过螺杆的旋转和加压作用,被注射到封闭模具的腔内。
同时,塑料填充整个模腔,保持一定的压力,使塑料能够充分填充模具中的空洞。
3.冷却和固化:注射到模腔内的塑料在一定时间内进行冷却和固化,使其具备一定的强度和形状稳定性。
4.开模和脱模:一旦塑料固化完成,模具会自动开启,将成型的零件推出。
二、塑料射出成型的工艺流程塑料射出成型的工艺流程通常包括以下几个关键步骤:1.原料准备:选取适当的塑料原料,并按照工艺要求进行预处理,如干燥、染色等。
2.射出机调试:根据塑料的特性和工艺要求,调整射出机的温度、压力、速度等参数,确保注射过程中塑料能够达到理想的熔融状态和充模效果。
3.模具设计和制造:根据待生产的机构件的设计要求,设计和制造射出模具。
模具的质量和结构会直接影响到成品的质量和生产效率。
4.成型工艺优化:根据模具的具体情况和塑料的特性,优化射出过程中的参数,如温度、压力、冷却时间等,以提高产品的质量和产量。
5.成型品质检验:对成型的机构件进行尺寸、外观、物理性能等各方面的检验,确保产品符合设计要求和客户需求。
6.后续处理:对成型的机构件进行后续处理,如去除模具标记、修整边缘、喷涂等。
三、常见的塑料射出成型机构件制造塑料射出成型广泛应用于各个行业的机构件制造,下面列举一些常见的机构件制造过程:1.零件外壳:例如电子产品、汽车零件等,这些机构件通常需要具备良好的外观质量和一定的强度,塑料射出成型可以满足这些要求。
塑料射出成形的原理

塑料射出成形的原理1.塑料熔融:将固体塑料颗粒加热至熔融状态,通常通过加热器加热塑料料筒中的原料。
在料筒中,螺杆将塑料推送到加热区域,并通过加热带将其熔化。
在被熔化的状态下,塑料经过混炼,确保其均匀性,以及与其他添加剂和颜料的混合。
2.射出注塑:将熔融态的塑料材料通过射出筒传送到射出嘴端,然后注射到模具的射出系统中。
射出系统通常由一个射出筒和一个射出嘴组成。
当塑料材料被注入到模具中时,射出嘴的阀门关闭以防止漏料。
3.压力和冷却:一旦塑料进入模具中,会施加一定压力以保持模具的形状。
这种压力通常由射出机的液压系统提供。
此外,模具内的冷却系统会通过冷却介质(如水)迅速降低塑料温度,促使其固化。
4.分离和排出:在塑料冷却和固化之后,模具会打开以分离成型件和废料。
成型件通常有一个喷嘴可以用来排出气体,是为了减少模具中的空气气体。
废料可以回收再利用,以减少浪费并提高效率。
1.高效生产:塑料射出成形是一种快速且连续的生产方法,可以在短时间内生产大量的塑料制品。
这是因为塑料射出成形每次只需要几秒钟至几分钟的周期时间。
2.复杂形状:塑料射出成形可以制造复杂的三维形状,具有细节丰富的内部空间和壁厚变化。
这是因为模具的设计可以根据需要进行定制,以实现所需的形状。
3.高精度:塑料射出成形具有高精度和重复性,可在0.001英寸的尺寸范围内制造产品。
这是因为模具的精确度高,并且注射过程经过精确控制。
4.多材料应用:塑料射出成形可以使用多种塑料材料进行生产,如聚丙烯、聚氨酯、聚碳酸酯等。
这使得塑料射出成形具有广泛的应用领域,在汽车、电子、医疗器械等行业得到广泛应用。
总结起来,塑料射出成形是一种通过将加热熔融态的塑料注入到模具中,通过压力冷却和固化成型的塑料加工方法。
它具有高效生产、制造复杂形状、高精度和适用于多材料的优势。
这种加工方法已经成为现代塑料制造业中不可或缺的一种技术。
射出成型法
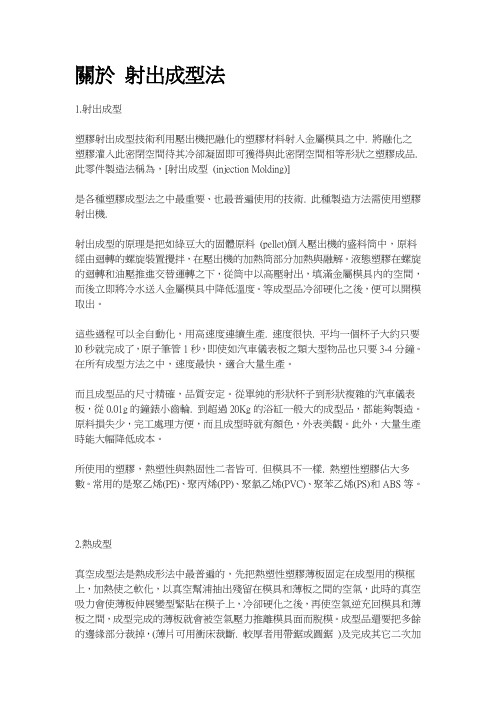
關於射出成型法1.射出成型塑膠射出成型技術利用壓出機把融化的塑膠材料射入金屬模具之中. 將融化之塑膠灌入此密閉空間待其冷卻凝固即可獲得與此密閉空間相等形狀之塑膠成品. 此零件製造法稱為,[射出成型(injection Molding)]是各種塑膠成型法之中最重要、也最普遍使用的技術. 此種製造方法需使用塑膠射出機.射出成型的原理是把如綠豆大的固體原料(pellet)倒入壓出機的盛料筒中,原料經由迴轉的螺旋裝置攪拌,在壓出機的加熱筒部分加熱與融解。
液態塑膠在螺旋的迴轉和油壓推進交替運轉之下,從筒中以高壓射出,填滿金屬模具內的空間,而後立即將冷水送入金屬模具中降低溫度。
等成型品冷卻硬化之後,便可以開模取出。
這些過程可以全自動化,用高速度連續生產. 速度很快. 平均一個杯子大約只要l0秒就完成了,原子筆管1秒,即使如汽車儀表板之類大型物品也只要3-4分鐘。
在所有成型方法之中,速度最快,適合大量生產。
而且成型品的尺寸精確,品質安定。
從單純的形狀杯子到形狀複雜的汽車儀表板,從0.01g的鐘錶小齒輪. 到超過20Kg的浴缸一般大的成型品,都能夠製造。
原料損失少,完工處理方便,而且成型時就有顏色,外表美觀。
此外,大量生產時能大幅降低成本。
所使用的塑膠,熱塑性與熱固性二者皆可. 但模具不一樣. 熱塑性塑膠佔大多數。
常用的是聚乙烯(PE)、聚丙烯(PP)、聚氯乙烯(PVC)、聚苯乙烯(PS)和ABS等。
2.熱成型真空成型法是熱成形法中最普遍的,先把熱塑性塑膠薄板固定在成型用的模框上,加熱使之軟化,以真空幫浦抽出殘留在模具和薄板之間的空氣,此時的真空吸力會使薄板伸展變型緊貼在模子上,冷卻硬化之後,再使空氣逆充回模具和薄板之間,成型完成的薄板就會被空氣壓力推離模具面而脫模。
成型品還要把多餘的邊緣部分裁掉,(薄片可用衝床裁斷. 較厚者用帶鋸或圓鋸)及完成其它二次加工(如鑽孔. 沖孔等) 才算完成。
需要大量生產時使用鋁模,少量生產時則使用石膏模、塑膠模或電鑄模。
塑胶射出成型技术讲义(A)

塑胶射出成型技术讲义(A)目录一、塑膠成型的種類→15分二、塑膠射出成型的基本→30分三、成型品設計的基本→30分四、塑膠射出成型經常遭遇的問題→20分五、塑膠射出成型理想化的有關事項→20分六、造成問題的有關原因→25分七、成型事故與對策→25分一、塑膠成型的種類大多數的成型都是將塑膠加熱熔融后,在模具中或經由模具以壓、抽、擠、滾、吹或吸而使之成為我們所要的行狀l成型的種類l射出成型Injection Moldingl擠壓成型Extrusionl吹塑成型Blow Moldingl真空成型Vacuum Formingl壓縮成型Compression Moldingl發泡成型Expanded Formingl滾塑成型Rotation Moldingl鑄塑成型Casting Moldingl層積成型Lamination二、塑膠射出成型的基本(一)塑膠的優點─輕而堅韌,便宜,成型加工容易l使用塑膠的目的1.為了降低材料費用成本2.減輕重量3.避免生銹或腐蝕4.為了實現理想形狀5.實現理想造型和外觀6.隔熱性好7.電絕緣性好l使用塑膠材料時應注意點1.精密度稍差2.耐熱性不佳3.可燃性5.耐溶劑性,耐油性低6.會劣化7.不具電磁波屏蔽性(二)塑膠射出成型的優點─大量制造精密產品l射出成型的原理l射出成型是塑膠成型的代表方法l射出成型的生產力高l射出成型品的精度高(三)射出成型機的原理(四)射出成型用模具的基本l堅固的模具是成型的基本l產品的生產計劃和設計應預先l充分檢討l模具的基本構造(三種)l模具的重點在于防止變形和通氣(五)射出成型品設計原則l目的─便宜,快而大量生產1.加脫模斜度2.成品厚度應均勻3.形狀易簡單4.不要有銳角角隅5.注重實績l射出成型用材料1.加熱則軟化的塑膠2.熱可塑性塑膠3.結晶性與非結晶性材料4.成型的收縮率5.流動性的目標三、成型品設計的基本(一)成型品設計的基本要件l掌握必要特性1.首先盡量詳列使用條件2.根據使用條件列舉必要特性表,依據重要性,當完成設計構想時,再據該表評價,以利設計進行。
塑胶射出成型知识

拉模
發生原因:拉模可發生于產品內外各部位,常見于 各邊緣,孔位,卡鉤.模具斜度不夠,咬花太粗糙, 前模損壞,成型過飽均可造成拉模.
解決對策:按原料出廠規定要求提前烘干原料,降 低射出速度與加料轉速,縮短松退位置,加大背壓, 水口料不可粉碎太大顆粒,要與原料配比使用,加 大模具進膠口.如必要時對產品厚薄可進行修改模 具.
變形
發生原因:塑膠制品未充分冷卻時托模,頂出梢對 其表面施加外力引起變形.冷卻速度不均勻,冷卻 慢的收縮下陷造成反翹.產品切面厚薄不均勻,導 致冷卻速度不均勻.
差)
射出成型操作要項(三)
四.關模壓力 A:過低—塑料易于關模線溢出 B:過高—機器,模具易損耗,浪費電力 五.射出壓力 A:過低—短射,縮水 B:過高—毛邊大,過飽,焦斑,內應力強,粘模,模
具易損 嚴重時滑塊,叉銷,模具變形斷裂.
射出成型操作要項(四)
六.射出速度 A:太慢—短射,縮水 B:太快—毛邊大,過飽,焦斑,粘模 七.螺桿轉速 A:太慢—原料塑化不均,周期延長 B:太快—原料過熱,料斗處結塊 螺桿對原料有壓縮,輸送,熔融,計量四大功能
塑膠件重點管制項目及部位
色差:先目視比對樣品無明顯差異再以儀器測試. 尺寸:由于塑膠熱脹冷縮現象明顯,故尺寸的測量
需于產品完全冷卻后進行. 咬花:各部位是否符合圖面規格或與樣品一致,是
否有咬花過粗或過細的現象. 燙金字體是否有短射,印刷部位是否縮水凹陷. 頂針,鑲塊,涵位是否有歪斜,過高或下陷. 各卡鉤,定位柱是否有拉白,短射,變形等不良. 各版本,材質,日期指針是否指錯或指向空白部位. 各類外觀缺失是否達到東驊品質標准.
- 1、下载文档前请自行甄别文档内容的完整性,平台不提供额外的编辑、内容补充、找答案等附加服务。
- 2、"仅部分预览"的文档,不可在线预览部分如存在完整性等问题,可反馈申请退款(可完整预览的文档不适用该条件!)。
- 3、如文档侵犯您的权益,请联系客服反馈,我们会尽快为您处理(人工客服工作时间:9:00-18:30)。
塑膠射出技術知識
東莞致通電腦有限公司
一.什麽叫注射成型? 什麽叫注射成型?
注射成型又叫注射模塑膠,是一種注射兼 模塑的成型方法,注射是將聚合物組分的粉料與 粒料,通過注射料斗,進入機筒內通過機筒外部 加熱和螺杆旋轉産生的剪切摩擦熱,使物料經壓 了加熱,輸送,排氣,壓縮,混合,均化等,
1.射出時間不能相差正負2秒 2.冷卻時間不能相差正負2秒 3.料管溫度不能相差實際的上下10℃ 4.計量行程不能相差上下10cm,速度不能相 差上下15%,壓力不能相差上下5%
東莞致通電腦有限公司
5.射料行程位置不能相差上下10cm(每段), 速度不能相差上下15%,壓力不能相差5% 6.保壓時間不能相差正負2秒,保壓壓力不能 相差上下5%,保壓速度不能相差上下15% 7.鎖模低壓行程位置不能相差上下2cm,速度 不能相差上下5%,壓力不能相差上下3%
東莞致通電腦有限公司
8.鎖模快速行程位置不能相差上下10cm, 速 度不能相差上下5%,壓力不能相差上下5%(各 股行程位置壓力等) 9.開模行程位置不能相差上下10cm,速度不能 相差上下10%,壓力不能相差上下5%(各股行程 位置壓力等) 10.周期不能相差正負2秒.
1.注射成型的射出機也稱注射機 2.模具 3.相關配套設備
東莞致通電腦有限公司
三.注射機的基本組成
1.注射裝置, 2.合模裝置, 3.液壓轉動系統 4.電器控制系統組成
東莞致通電腦有限公司
四.各種注射機形式
1.立式注塑機, 2.角式注塑機, 3.臥式注射射機的表現規格
1.鎖模力 鎖模力(KN)即噸位或安士,根據常規 注射機有:50T-4000T不等規格,用安士表 示有4安士,8安士,12安士等. 2.注射容量
東莞致通電腦有限公司
陸.射出成形重要參數
1.溫度 主要包括原料加溫預熱溫度,原料熔 融溫度和模具溫度 2.壓力 主要包括關模壓力,開模壓力,射出 壓力,頂出壓力和背壓壓力
東莞致通電腦有限公司
作用於塑化,(溫度組分熔融狀態),塑化的物料 在噴嘴鐵阻擋下,積於機筒的前端然後借助於 柱塞,或螺杆,向塑化好的低溫模具中,再經保 壓,冷卻,定型後開啓模具,頂出製品,得到與模 腔幾何尺寸相似鐵塑膠製品,這就是注塑成型, 也叫注射成型.
東莞致通電腦有限公司
二.注射成型需要的設備
東莞致通電腦有限公司
3.時間 包括原料射出時間、滯留 時間及冷卻時間. 4.速度 包括射出速度,開模速度,頂出 速度,關模速度及螺桿速度.
東莞致通電腦有限公司
七.成型條件
成型條件:是經過多次試模,確認.記錄 下來的資料,並經過審核承認,才能生效 的生産資料,
東莞致通電腦有限公司
八.正常成型條件稽核重點: 正常成型條件稽核重點: