某轻型商用车车架断裂CAE分析及改进方法
汽车车架纵梁开裂cae分析及改进设计
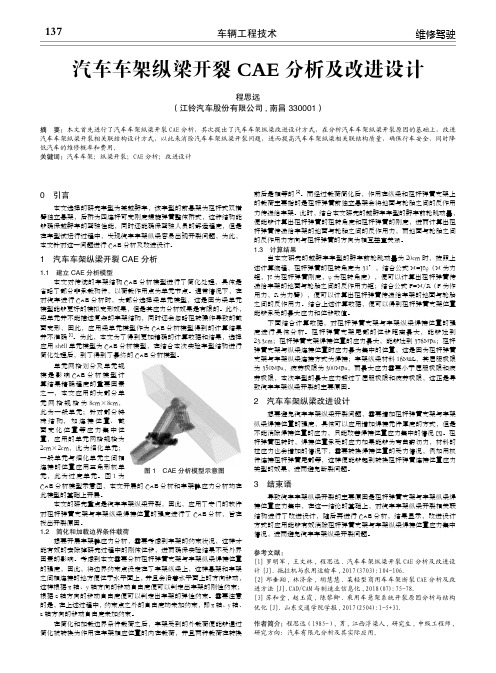
车辆工程技术137维修驾驶0 引言 本文选择的研究车型为某越野车,该车型的前悬架为扭杆式双横臂独立悬架,后桥为四连杆可变刚度螺旋弹簧整体桥式,这种结构能够确保越野车的驾驶性能,同时还能确保驾驶人员的舒适程度,但是在车型试运行过程中,发现汽车车架纵梁容易出现开裂问题,为此,本文针对这一问题进行CAE 分析及改进设计。
1 汽车车架纵梁开裂CAE 分析1.1 建立CAE 分析模型 本文对传统的车架结构CAE 分析模型进行了简化处理,具体是省略了部分非承载构件,以荷载作用点为单元节点。
通常情况下,在对汽车进行CAE 分析时,大部分选择梁单元模型,这是因为梁单元模型能够更好的模拟变形效果,但是其应力分析效果是有限的。
此外,梁单元并不能描述复杂的车架结构,同时还会忽略扭转操作导致的截面变形,因此,应用梁单元模型作为CAE 分析模型得到的计算结果并不准确[1]。
为此,本文为了得到更加精确的计算数据和结果,选择应用shell 单元模型为CAE 分析模型,在结合本次实验车型结构进行简化处理后,到了得到了最终的CAE 分析模型。
汽车车架纵梁开裂CAE 分析及改进设计程思远(江铃汽车股份有限公司,南昌 330001)摘 要:本文首先进行了汽车车架纵梁开裂CAE 分析,其次提出了汽车车架纵梁改进设计方式,在分析汽车车架纵梁开裂原因的基础上,改进汽车车架纵梁开裂相关联结构设计方式,以此来消除汽车车架纵梁开裂问题,进而提高汽车车架纵梁相关联结构质量,确保行车安全,同时降低汽车的维修概率和费用。
关键词:汽车车架;纵梁开裂;CAE 分析;改进设计 单元网格划分及单元规模是影响CAE 分析模型计算结果精确程度的重要因素之一,本文应用的大部分单元网格规格为8cm×8cm,此为一般单元;针对部分特殊结构,如连接位置、截面变化位置等应力集中位置,应用的单元网格规格为2cm×2cm,此为细化单元;一般单元与细化单元之间相连接的位置应用三角形板单元,此为过度单元。
半挂车车架开裂问题及优化设计

半挂车车架开裂问题及优化设计半挂车车架是连接半挂车车厢和车头的重要部件,起着支撑车厢和车载货物的作用。
近年来半挂车车架开裂问题时有发生,引起了行业和消费者的广泛关注。
开裂问题不仅影响了半挂车的使用寿命和安全性,也给半挂车制造企业带来了巨大的责任和经济压力。
对半挂车车架进行优化设计是当前亟待解决的问题。
一、半挂车车架开裂的原因半挂车车架开裂的原因主要包括以下几个方面:1.材料选择不当半挂车车架的主要材料一般为碳素钢或者合金钢,材料的质量直接影响了车架的强度和韧性。
而一些制造企业在为了节约成本的考虑,在材料选择上存在一定的问题,导致了车架的承载能力不足以承受长时间的使用和重载运输,从而容易导致开裂问题的发生。
2.焊接工艺不合理车架的焊接是其结构中至关重要的一环,焊接工艺的不合理会导致焊接点容易出现裂纹和断裂。
有些制造企业在焊接工艺上存在一定的瑕疵,例如焊接温度不稳定、焊接接头不充分等问题都会影响到车架的质量和稳定性。
3.设计不合理半挂车车架的设计不合理也是导致开裂问题的一个重要原因。
一些车架的结构设计存在缺陷,例如梁与横梁的连接处设计不合理、焊接接头过多等都会导致车架开裂的风险增加。
二、优化设计方案针对半挂车车架开裂问题,为了提高其使用寿命和安全性,需要从材料选择、焊接工艺和设计结构等方面进行优化设计。
1.选材优化在选材上应该选择高强度和高韧性的钢材作为半挂车车架的主要材料,以确保其有足够的承载能力和耐久性。
对于材料的质量和规格也应该严格把控,确保车架的材料达到相关标准和要求。
2.焊接工艺优化在焊接工艺上应该采用先进的焊接技术和设备,确保焊接接头的质量和稳定性。
需要加强对焊接工艺的管理和控制,严格执行相关规范和标准,避免焊接过程中出现瑕疵。
3.结构设计优化在车架的结构设计上需要考虑到力学和动力学的原理,避免出现应力集中和结构疲劳等问题。
对车架的连接部位和受力部位进行加固和优化设计,以提高其整体的稳定性和耐久性。
某轻型商用车车架断裂CAE分析及改进方法
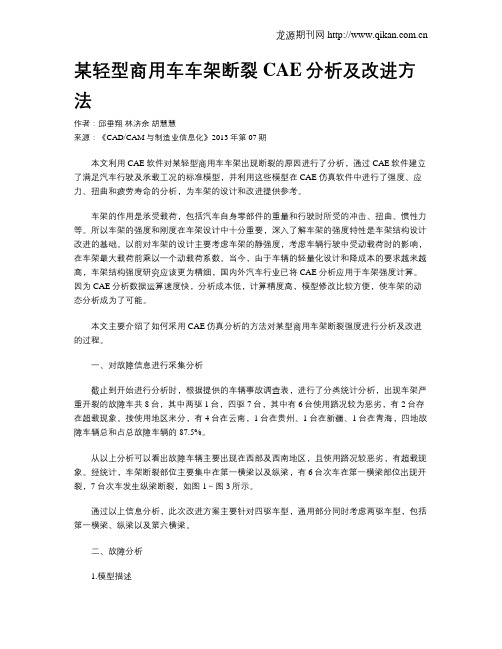
某轻型商用车车架断裂CAE分析及改进方法作者:邱垂翔林济余胡慧慧来源:《CAD/CAM与制造业信息化》2013年第07期本文利用CAE软件对某轻型商用车车架出现断裂的原因进行了分析,通过CAE软件建立了满足汽车行驶及承载工况的标准模型,并利用这些模型在CAE仿真软件中进行了强度、应力、扭曲和疲劳寿命的分析,为车架的设计和改进提供参考。
车架的作用是承受载荷,包括汽车自身零部件的重量和行驶时所受的冲击、扭曲、惯性力等。
所以车架的强度和刚度在车架设计中十分重要,深入了解车架的强度特性是车架结构设计改进的基础。
以前对车架的设计主要考虑车架的静强度,考虑车辆行驶中受动载荷时的影响,在车架最大载荷前乘以一个动载荷系数。
当今,由于车辆的轻量化设计和降成本的要求越来越高,车架结构强度研究应该更为精细,国内外汽车行业已将CAE分析应用于车架强度计算。
因为CAE分析数据运算速度快,分析成本低,计算精度高,模型修改比较方便,使车架的动态分析成为了可能。
本文主要介绍了如何采用CAE仿真分析的方法对某型商用车架断裂强度进行分析及改进的过程。
一、对故障信息进行采集分析截止到开始进行分析时,根据提供的车辆事故调查表,进行了分类统计分析,出现车架严重开裂的故障车共8台,其中两驱1台,四驱7台,其中有6台使用路况较为恶劣,有2台存在超载现象。
按使用地区来分,有4台在云南,1台在贵州、1台在新疆、1台在青海,四地故障车辆总和占总故障车辆的87.5%。
从以上分析可以看出故障车辆主要出现在西部及西南地区,且使用路况较恶劣,有超载现象。
经统计,车架断裂部位主要集中在第一横梁以及纵梁,有6台次车在第一横梁部位出现开裂,7台次车发生纵梁断裂,如图1~图3所示。
通过以上信息分析,此次改进方案主要针对四驱车型,通用部分同时考虑两驱车型,包括第一横梁、纵梁以及第六横梁。
二、故障分析1.模型描述传统的车架有限元模型分析一般采用梁单元,该方法简单方便,但是有些情况下精度不高,如在货箱上采用梁单元则过度简化。
商用车白车身开裂问题的研究和改进
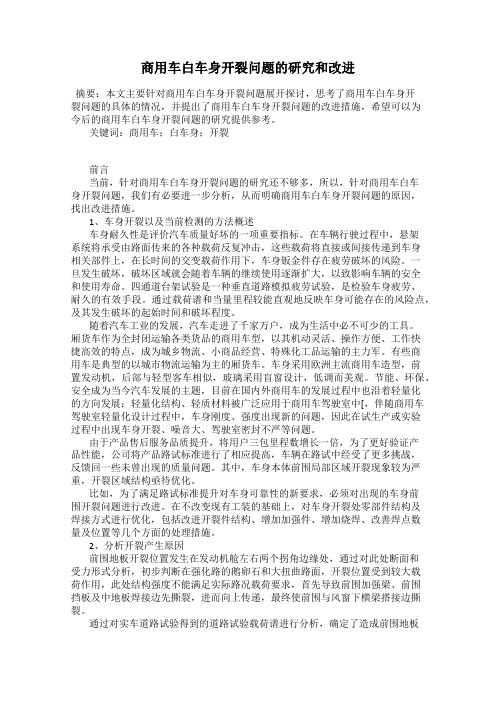
商用车白车身开裂问题的研究和改进摘要:本文主要针对商用车白车身开裂问题展开探讨,思考了商用车白车身开裂问题的具体的情况,并提出了商用车白车身开裂问题的改进措施,希望可以为今后的商用车白车身开裂问题的研究提供参考。
关键词:商用车;白车身;开裂前言当前,针对商用车白车身开裂问题的研究还不够多,所以,针对商用车白车身开裂问题,我们有必要进一步分析,从而明确商用车白车身开裂问题的原因,找出改进措施。
1、车身开裂以及当前检测的方法概述车身耐久性是评价汽车质量好坏的一项重要指标。
在车辆行驶过程中,悬架系统将承受由路面传来的各种载荷反复冲击,这些载荷将直接或间接传递到车身相关部件上,在长时间的交变载荷作用下,车身钣金件存在疲劳破坏的风险。
一旦发生破坏,破坏区域就会随着车辆的继续使用逐渐扩大,以致影响车辆的安全和使用寿命。
四通道台架试验是一种垂直道路模拟疲劳试验,是检验车身疲劳、耐久的有效手段。
通过载荷谱和当量里程较能直观地反映车身可能存在的风险点,及其发生破坏的起始时间和破坏程度。
随着汽车工业的发展,汽车走进了千家万户,成为生活中必不可少的工具。
厢货车作为全封闭运输各类货品的商用车型,以其机动灵活、操作方便、工作快捷高效的特点,成为城乡物流、小商品经营、特殊化工品运输的主力军。
有些商用车是典型的以城市物流运输为主的厢货车。
车身采用欧洲主流商用车造型,前置发动机,后部与轻型客车相似,玻璃采用盲窗设计,低调而美观。
节能、环保、安全成为当今汽车发展的主题,目前在国内外商用车的发展过程中也沿着轻量化的方向发展:轻量化结构、轻质材料被广泛应用于商用车驾驶室中[,伴随商用车驾驶室轻量化设计过程中,车身刚度、强度出现新的问题,因此在试生产或实验过程中出现车身开裂、噪音大、驾驶室密封不严等问题。
由于产品售后服务品质提升,将用户三包里程数增长一倍,为了更好验证产品性能,公司将产品路试标准进行了相应提高,车辆在路试中经受了更多挑战,反馈回一些未曾出现的质量问题。
168-车架异常开裂有限元分析
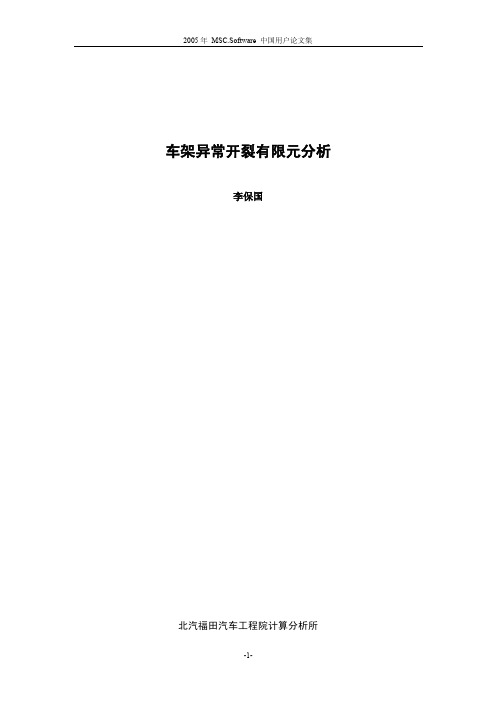
车架异常开裂有限元分析李保国北汽福田汽车工程院计算分析所车架异常断裂有限元分析AN ANALYSIS ON THE CAUSE OF FRAME ABNORMALFRACTURE李保国(北汽福田汽车工程院计算分析所)摘要:本文针对车架纵梁异常开裂现象,建立车架有限元模型,通过有限元静力学、动力学分析,找到了引起纵梁异常开裂的主要原因,提出了改进建议,经过市场检验,证明改进是有效的。
关键词:有限元,静力学,动力学Abstract:Static and Dynamic strength of the frame side rail was examined by numerical simulation using the FEA code MSC.Nastran . The analysis showed that it was the impact force of vehicle shake that resulted in the fracture of side rail. So a reinforcement side rail structure of frame was proposed, which made the strength of the frame side rail well.Key Words:FEM ,static ,dynamic1 前言车架是汽车设计的重要课题,因为它的好坏直接关系到汽车的一切性能(操纵稳定性、平顺性等)。
评价车架设计和结构的好坏,首先系统的考虑受力、重量、花费、竞争对手分析、顾客需求等,以求达到系统的最佳匹配。
文中针对我公司某轻型卡车焊接车架在山区发生车架异常开裂的现象,进行该车的有限元分析,并提出改进建议,经市场检验,该改进是有效。
2 有限元分析模型和边界条件本次分析采用IDEAS建立有限元模型,车架纵梁、横梁等薄壳结构采用壳单元模拟,板簧支架等支持件采用实体单元模拟,驾驶室、货箱装置货物以集中质量代替,以MSC.Nastran 求解。
某轻卡驾驶室后悬置龙门架断裂问题分析
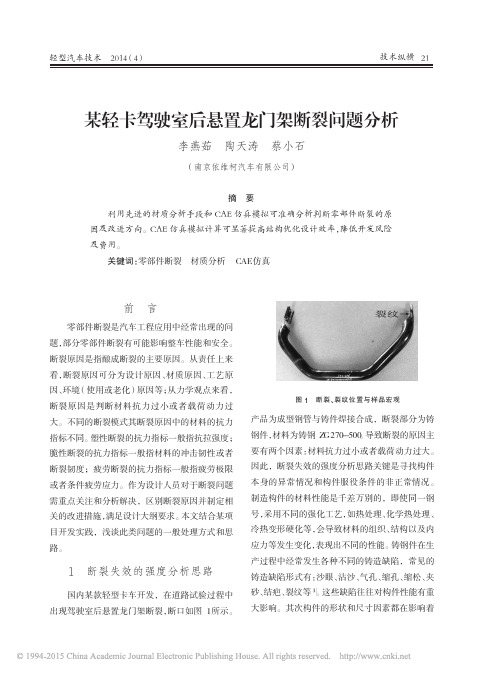
轻型汽车技术2014(4)图1断裂、裂纹位置与样品宏观技术纵横某轻卡驾驶室后悬置龙门架断裂问题分析李燕茹陶天涛蔡小石(南京依维柯汽车有限公司)摘要利用先进的材质分析手段和C A E 仿真模拟可准确分析判断零部件断裂的原因及改进方向。
C A E 仿真模拟计算可显著提高结构优化设计效率,降低开发风险及费用。
关键词:零部件断裂材质分析CAE仿真零部件断裂是汽车工程应用中经常出现的问题,部分零部件断裂有可能影响整车性能和安全。
断裂原因是指酿成断裂的主要原因。
从责任上来看,断裂原因可分为设计原因、材质原因、工艺原因、环境(使用或老化)原因等;从力学观点来看,断裂原因是判断材料抗力过小或者载荷动力过大。
不同的断裂模式其断裂原因中的材料的抗力指标不同。
塑性断裂的抗力指标一般指抗拉强度;脆性断裂的抗力指标一般指材料的冲击韧性或者断裂韧度;疲劳断裂的抗力指标一般指疲劳极限或者条件疲劳应力。
作为设计人员对于断裂问题需重点关注和分析解决,区别断裂原因并制定相关的改进措施,满足设计大纲要求。
本文结合某项目开发实践,浅谈此类问题的一般处理方式和思路。
国内某款轻型卡车开发,在道路试验过程中出现驾驶室后悬置龙门架断裂,断口如图1所示。
产品为成型钢管与铸件焊接合成,断裂部分为铸钢件,材料为铸钢ZG270-500。
导致断裂的原因主要有两个因素:材料抗力过小或者载荷动力过大。
因此,断裂失效的强度分析思路关键是寻找构件本身的异常情况和构件服役条件的非正常情况。
制造构件的材料性能是千差万别的,即使同一钢号,采用不同的强化工艺,如热处理、化学热处理、冷热变形硬化等,会导致材料的组织、结构以及内应力等发生变化,表现出不同的性能。
铸钢件在生产过程中经常发生各种不同的铸造缺陷,常见的铸造缺陷形式有:沙眼、沾沙、气孔、缩孔、缩松、夹砂、结疤、裂纹等[1]。
这些缺陷往往对构件性能有重大影响。
其次构件的形状和尺寸因素都在影响着前言1断裂失效的强度分析思路21轻型汽车技术2014(4)技术纵横应力状态,缺口的尖锐程度决定着应力集中,一般在该处容易形成断裂失效的起始点。
某车型减振器支架断裂原因分析及改进方案
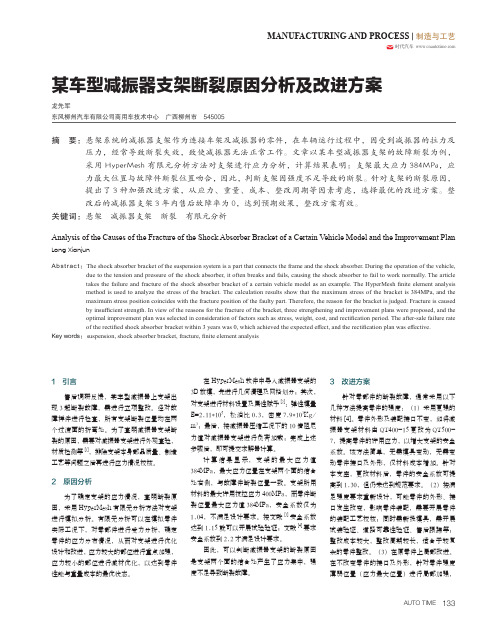
MANUFACTURING AND PROCESS | 制造与工艺 时代汽车 某车型减振器支架断裂原因分析及改进方案龙先军东风柳州汽车有限公司商用车技术中心 广西柳州市 545005摘 要: 悬架系统的减振器支架作为连接车架及减振器的零件,在车辆运行过程中,因受到减振器的拉力及压力,经常导致断裂失效,致使减振器无法正常工作。
文章以某车型减振器支架的故障断裂为例,采用HyperMesh有限元分析方法对支架进行应力分析,计算结果表明:支架最大应力384MPa,应力最大位置与故障件断裂位置吻合,因此,判断支架因强度不足导致的断裂。
针对支架的断裂原因,提出了3种加强改进方案,从应力、重量、成本、整改周期等因素考虑,选择最优的改进方案。
整改后的减振器支架3年内售后故障率为0,达到预期效果,整改方案有效。
关键词:悬架 减振器支架 断裂 有限元分析1 引言售后调研反馈,某车型减振器上支架出现3起断裂故障,需进行立项整改。
经对故障样件进行检查,所有支架断裂位置均在两个过渡面的折弯处。
为了查明减振器支架断裂的原因,需要对减振器支架进行外观查验,材质检测等[1],排除支架本身部品质量、制造工艺等问题之后再进行应力情况校核。
2 原因分析为了确定支架的应力情况,查明断裂原因,采用HyperMesh有限元分析方法对支架进行模拟分析。
有限元分析可以在模拟零件实际工况下,对零部件进行受力分析,确定零件的应力分布情况,从而对支架进行优化设计和改进,应力较大的部位进行重点加强,应力较小的部位进行减材优化,以达到零件性能与重量成本的最优状态。
在HyperMesh软件中导入减振器支架的3D数模,先进行几何清理及网格划分;其次,对支架进行材料设置及属性赋予[2]:弹性模量E=2.11*105,松泊比0.3,密度7.9*103Kg/m3;最后,按减振器压缩工况下的10倍阻尼力值对减振器支架进行负荷加载;完成上述步骤后,即可提交求解器计算。
某高端商用车车架裂纹分析与解决方案
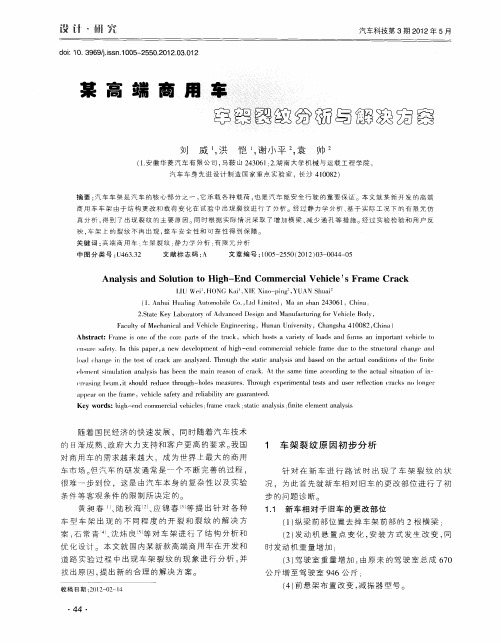
fl 3.5k = 7 g F 31
= 1 l = 5 .5k 2 37 g
( ) 箱将 力平 均 分布 到两 边 悬 臂上 , 4 . g 2水 01 。 4k
( ) 动机+ 3发 变速 箱 受 力计 算 , 受 力分析 图见 其
M _
,
C支 点 的 支 反 力 为 : l.8k 86 33 g 前 轮 受 力 : 3 .6k 27 93 g 后 轮 受 力 : 5 . g 2 133 k 4 ( ) 梁 剪 力 图 如 图 8 其 中 红 色 部 位 为 裂 纹 位 6纵 ,
置 。
I J I r』』 J r j r
道 路 实 验 过 程 中 出现 车 架 裂 纹 的 现 象 进 行 分 析 , 并 找 出 原 因 , 出新 的 合 理 的 解 决 方案 。 提
收 稿 日期 : 0 2 0 ~ 4 2 l — 2 1
( ) 驶室 重量增 加 , 3驾 由原 来 的驾 驶室 总成 6 0 7
公 斤增 至 驾 驶 室 9 6公 斤 : 4
商 用 车车 架 由于 结 构 更 改和 载 荷 变 化在 试 验 中出 现裂 纹 进 行 了 分 析 。经过 静 力 学 分 析 、 于 实 际工 况 下 的 有 限 元仿 基
一一~ ~~一 . ~ _. i~一 耄一 一 一- ~~ .薹 一一 ~… _~ ~ 一~ 薹咖 一 ~一
中 图分 类 号 : 4 33 U6 . 2
文 献标 志 码 : A
文 章 编 号 :0 5 2 5 (0 2 0 — 0 4 0 l0 — 5 0 2 1 ) 3 0 4 — 5
随 着 国 民 经 济 的 快 速 发 展 , 同 时 随 着 汽 车 技 术
半挂车车架开裂问题分析及优化设计
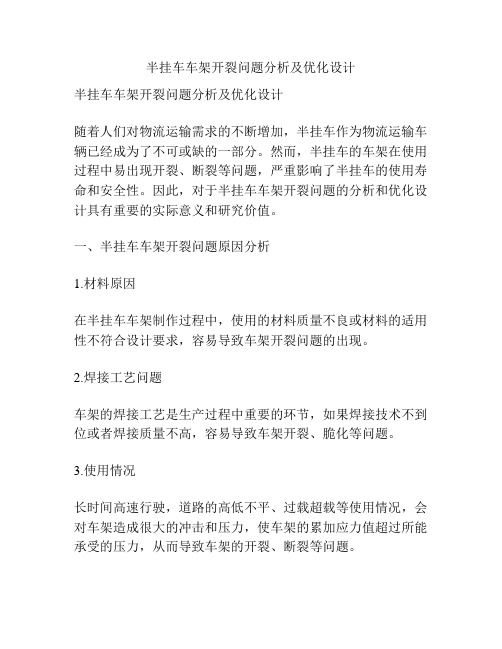
半挂车车架开裂问题分析及优化设计半挂车车架开裂问题分析及优化设计随着人们对物流运输需求的不断增加,半挂车作为物流运输车辆已经成为了不可或缺的一部分。
然而,半挂车的车架在使用过程中易出现开裂、断裂等问题,严重影响了半挂车的使用寿命和安全性。
因此,对于半挂车车架开裂问题的分析和优化设计具有重要的实际意义和研究价值。
一、半挂车车架开裂问题原因分析1.材料原因在半挂车车架制作过程中,使用的材料质量不良或材料的适用性不符合设计要求,容易导致车架开裂问题的出现。
2.焊接工艺问题车架的焊接工艺是生产过程中重要的环节,如果焊接技术不到位或者焊接质量不高,容易导致车架开裂、脆化等问题。
3.使用情况长时间高速行驶,道路的高低不平、过载超载等使用情况,会对车架造成很大的冲击和压力,使车架的累加应力值超过所能承受的压力,从而导致车架的开裂、断裂等问题。
二、半挂车车架的优化设计1.材料优化在生产半挂车车架时,应选择高质量、优良的材料,并严格检验检测,确保材质的符合设计要求,这样可以有效降低车架出现开裂问题的风险。
2.焊接工艺优化采用优秀的焊接技术和焊接材料,以及先进的焊接设备,可以有效提高焊接质量,降低车架开裂问题的出现率。
3.结构设计优化在车架的结构设计过程中,应考虑到实际使用情况,采用科学合理的结构设计,并在设计过程中进行有限元分析和模拟试验,最终确定最优的结构设计方案。
4.车身附加件的优化半挂车车身的结构不同于普通汽车,车身附加件设计不合理、连接方式与其他部分不协调等问题都会导致车架的开裂,因此,在车身附加件的选择、设计与安装上需严格按照规范操作。
三、总结:半挂车车架开裂问题的解决方法并非一朝一夕、过程繁琐。
综合针对材料、工艺、设计问题展开分析,正确选用材料、采取正确的生产工艺和结构设计,才能最大限度地确保半挂车车架的使用寿命和安全性。
通过这些优化设计的措施,可以有效地降低半挂车车架的开裂、断裂问题发生率,保证半挂车在物流运输中的平稳运行和安全运载。
差速器壳体断裂的CAE计算分析
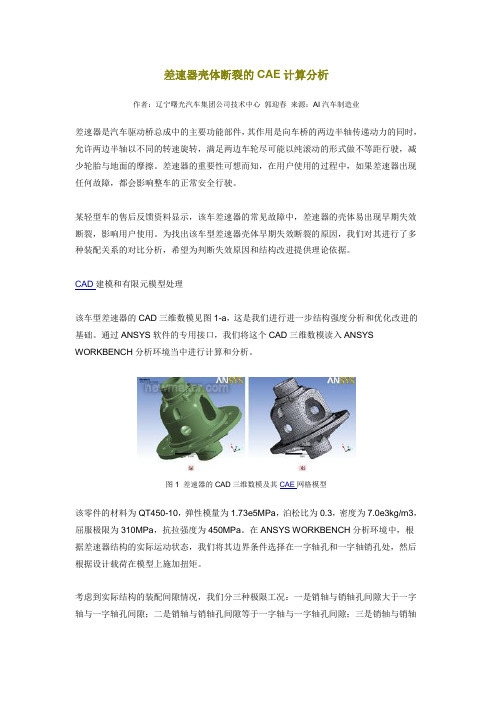
差速器壳体断裂的CAE计算分析作者:辽宁曙光汽车集团公司技术中心郭迎春来源:AI汽车制造业差速器是汽车驱动桥总成中的主要功能部件,其作用是向车桥的两边半轴传递动力的同时,允许两边半轴以不同的转速旋转,满足两边车轮尽可能以纯滚动的形式做不等距行驶,减少轮胎与地面的摩擦。
差速器的重要性可想而知,在用户使用的过程中,如果差速器出现任何故障,都会影响整车的正常安全行驶。
某轻型车的售后反馈资料显示,该车差速器的常见故障中,差速器的壳体易出现早期失效断裂,影响用户使用。
为找出该车型差速器壳体早期失效断裂的原因,我们对其进行了多种装配关系的对比分析,希望为判断失效原因和结构改进提供理论依据。
CAD建模和有限元模型处理该车型差速器的CAD三维数模见图1-a,这是我们进行进一步结构强度分析和优化改进的基础。
通过ANSYS软件的专用接口,我们将这个CAD三维数模读入ANSYS WORKBENCH分析环境当中进行计算和分析。
图1 差速器的CAD三维数模及其CAE网格模型该零件的材料为QT450-10,弹性模量为1.73e5MPa,泊松比为0.3,密度为7.0e3kg/m3,屈服极限为310MPa,抗拉强度为450MPa。
在ANSYS WORKBENCH分析环境中,根据差速器结构的实际运动状态,我们将其边界条件选择在一字轴孔和一字轴销孔处,然后根据设计载荷在模型上施加扭矩。
考虑到实际结构的装配间隙情况,我们分三种极限工况:一是销轴与销轴孔间隙大于一字轴与一字轴孔间隙;二是销轴与销轴孔间隙等于一字轴与一字轴孔间隙;三是销轴与销轴孔间隙小于一字轴与一字轴孔间隙。
另外,考虑到该零件的断裂可能是由于局部应力集中过大造成的,本次分析采用实体单元,并尽量控制网格大小和密度,共划分为269456个节点,88192个单元,得到CAE网格模型如图1-b所示。
CAE的计算结果我们采用线弹性计算方法,同时也基于销轴、一字轴没有损坏的前提条件下,对差速器壳体的强度进行计算和分析。
运用CAE技术进行汽车车架结构的分析与优化设计

从以上分析可以查找出车架的薄弱环节以及工况,然后根据实际情况来优化相关结构。显而易见,这一车架的弯曲程度较小一些,因此,可以选择在弯曲工况的情况下来优化分析车辆的轻量化。
优化设计的数字模型体现在以下几点:
Min(wt(thck)
t max-str≤210
0.001≤THCK≤0.003.
跨度不平度对于汽车运动造成的激励一般属于20HZ之下的垂直振动,有激起车架一阶扭转共振的可能性,不过,因为车身和车架之间的刚性连接能够抑制这一阶振型,所以需要全面分析整车模态。
2.2道路激励下瞬态响应分析
模拟车架满载工况之下受到激励瞬态动力学分析,将位移激励设置于两前轮的悬架弹簧底部,模拟前两轮的边坡过程。对于路面尺寸,则是按照定远试车场搓板路给出,路面激励属于半正弦波形,坡高为20mm,波长是400mm。
通过分析表明,本车架的扭转刚度是极高的,在轻型汽车车架中占据重要的作用。再加上横梁密布,在抵抗扭转变形的时候产生了较高的效果。
通常情况下,车架的应力状态一般都是位于低压力状态中,平均von-mises平均等效应力是2611Pa,只能够在前后悬架的约束之下呈现出较高的应力水平。
2动力学分析
动力学分析主要包含载荷作用历程以及时间有联系的问题。它涉及到模态分析和道路激励下瞬态响应分析两种。
1.2对于车架弯曲刚度的分析
当进行弯曲刚度以及扭转刚度分析的时候,不必考虑悬架产生的影响。
当前悬约束所有自由度的时候,后悬板簧的前端部位约束UX、UY、UZ。板簧的后端部位只是约束侧向位移UY以及绕Z轴的转动自由度。将载荷作用于前后纵梁连接位置中,一共包含24个加载节点,荷载大小为1000N。目前阶段,要想防止误差取出24位移的平均值,可以依照相关材料公式来获取车架的抗弯刚度值。
某微型客车车架结构的CAE分析与优化设计

某微型客车车架结构的CAE分析与优化设计本文运用几种CAE技术对某微型客车车架进行了结构分析与优化设计,首先,计算了静力挠度,静态弯曲、扭转刚度,然后求解了固有模态,并在此基础上获得典型道路激励下的瞬态响应,此外,还对车架典型薄壁梁结构的耐撞性吸能特性进行研究,配合实验数据,对车架结构进行了合理的改进设计,实现了满足轻量化要求的静态优化设计目标,彰显CAE技术在汽车研发过程中的作用日益重要。
0 综述CAE(计算机辅助工程分析)技术的兴起及应用,滞后于CAD(计算机辅助设计)技术,尤其在汽车工业以及机械行业。
当前,在中国汽车行业CAD技术已广泛得到应用,在产品设计过程中已经摈弃手工绘图的时代,将企业中的图纸信息数字化,大大节省成本;而对于产品进入验证阶段所必需的试验,对所设计的产品进行符合国家相关法规标准的强度、刚度、NVH、耐撞性等方面的评价,企业必须对概念样品进行一次一次的试验、修改、再试验、再修改的反复过程,最后才可以定型,生产销售。
相对于在产品设计初期的方案拟定、图纸绘制工作所耗费的人力、物力、财力,在设计进入验证阶段的反复试验评价和改进样品的费用可谓是天壤之别。
然而,CAE技术已在国外大型汽车企业中广泛应用,用以降低成本,缩短新车开发周期,应对瞬息万变的汽车市场需求,我国大部分汽车企业也都接触到CAE的研发工具,但应用的能力还不强,真正应用到产品研发中的企业还是很少,运用CAE 软件进行分析的能力决定所开发产品的水平。
本文结合某微型客车车架结构,对其进行轻量化以及耐撞性能优化设计,效果良好,得到厂家的肯定与应用。
各工况分析的模型采用基于该微型客车CAD模型的有限元模型,减少建模的误差,进行分析。
该车架的有限元模型如图1所示。
图1 车架有限元模型有限元分析软件采用ANSYS release7.0,模型采用四节点四边形壳单元,有少量三角形单元比例,单元尺寸6"8mm,单元数共计144943,节点数151124,点焊依据工艺流程规定的位置布置,车架模型中共有4458个焊点;材料属性依据企业提供的参数设置,E=203Gpa,ρ=7.89×10-6 kg/mm3,μ=0.31。
汽车前副车架开裂失效分析

图3 CAE分析状态
Research and / nZL^>?4Si \ +
Discussion /
kU
4.1断口分析 在开裂位置上表面进行观察,焊道附件钢 板表面存在焊渣,裂纹扩展已延伸至焊道上, 裂纹存在转折(见图4);下表面观察,裂纹 为贯穿状态,长度为4 mm (见图5);边缘 冲切面状态较好,无明显冲切痕迹(见图6)。 对断口进行宏观分析,断口表面腐蚀,但 钢板边缘可见疲劳台阶,断裂起始于冲切面与 上表面交界处,断裂性质为疲劳断裂(见图7 )。 4.2材质分析 4.2.1化学成分分析 在断口附近取样进行化学成分分析,测试 结果见表1,满足SAPH440材料的化学成分 要求,结果合格。 4.2.2硬度分析 为分析焊接对开裂位置材料性能的影响, 在断口附近与远离断口与焊道的基材位置分别 进行维氏硬度测试,测试结果见表2,硬度值 接近。 4.2.3金相分析 对开裂件进行金相分析,开裂源区附近平 行于断口方向存在另一条裂纹,表面存在腐蚀 坑(见图8),断口处金相组织为铁素体+珠 光体(见图9),远离断口位置金相组织为铁 素体+珠光体(见图10),组织基本一致。
剧开裂对应位置应力集中,导致疲劳寿命降低,是副车架在试验过程中开裂的主要因素。通过CAE分析,得知在加速
与制动工况下,开裂位置受力最大。分别选取2台设计状态与失效状态的副车架,模拟加速与制动工况进行台架试验
验证。试验验证结果显示,设计状态下的副车架循环次数最低提升41 %,能够满足整车耐久试验要求。 关键词:前副车架;焊接;开裂;应力集中
表3对比验证结果
样件
试验结果
备注
161 环境技术 / Environmental Technology
绑 0宀
半挂车车架开裂问题及优化设计
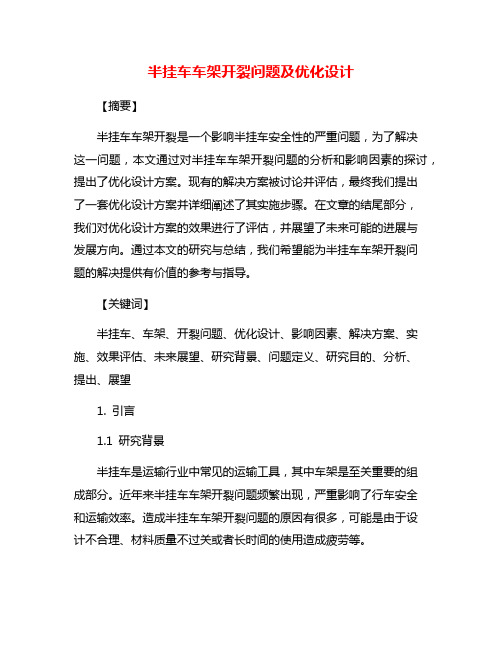
半挂车车架开裂问题及优化设计【摘要】半挂车车架开裂是一个影响半挂车安全性的严重问题,为了解决这一问题,本文通过对半挂车车架开裂问题的分析和影响因素的探讨,提出了优化设计方案。
现有的解决方案被讨论并评估,最终我们提出了一套优化设计方案并详细阐述了其实施步骤。
在文章的结尾部分,我们对优化设计方案的效果进行了评估,并展望了未来可能的进展与发展方向。
通过本文的研究与总结,我们希望能为半挂车车架开裂问题的解决提供有价值的参考与指导。
【关键词】半挂车、车架、开裂问题、优化设计、影响因素、解决方案、实施、效果评估、未来展望、研究背景、问题定义、研究目的、分析、提出、展望1. 引言1.1 研究背景半挂车是运输行业中常见的运输工具,其中车架是至关重要的组成部分。
近年来半挂车车架开裂问题频繁出现,严重影响了行车安全和运输效率。
造成半挂车车架开裂问题的原因有很多,可能是由于设计不合理、材料质量不过关或者长时间的使用造成疲劳等。
针对半挂车车架开裂问题,许多相关研究已经展开,但仍然存在一些问题有待解决。
本研究旨在全面分析半挂车车架开裂问题的根本原因,探讨影响因素,研究现有解决方案的不足之处,并提出优化设计方案来解决这一问题。
通过对半挂车车架开裂问题的研究,不仅可以提高半挂车的安全性和稳定性,还可以减少运输过程中的损失,提高运输效率。
本研究具有重要理论和实践意义。
希望通过本研究,能够为半挂车车架的设计和制造提供一定的指导和帮助,提高半挂车的整体性能和使用寿命。
1.2 问题定义半挂车车架开裂问题是指在运输过程中,半挂车车架出现裂纹或者断裂现象,严重影响了车辆的安全性和运输效率。
这一问题不仅会导致货物损失和人员伤亡,还会增加维修成本和运输公司的运营风险。
如何有效解决半挂车车架开裂问题成为当前需要重点关注和研究的课题。
问题定义具体包括以下几个方面:半挂车车架开裂问题的根本原因是什么?可能是由于材料选择不当、设计不合理或者制造工艺不到位导致的;半挂车车架开裂问题的发生频率有多高?不同的路况、负载条件和使用环境下,开裂问题的发生情况是否有所差异?半挂车车架开裂问题对运输安全和效率的影响有多大?开裂问题发生后,可能会导致什么样的后果?这些问题的答案将有助于我们更深入地理解半挂车车架开裂问题的本质,为后续的研究和优化设计提供有力支持。
某车型台架试验车身开裂研究与改进
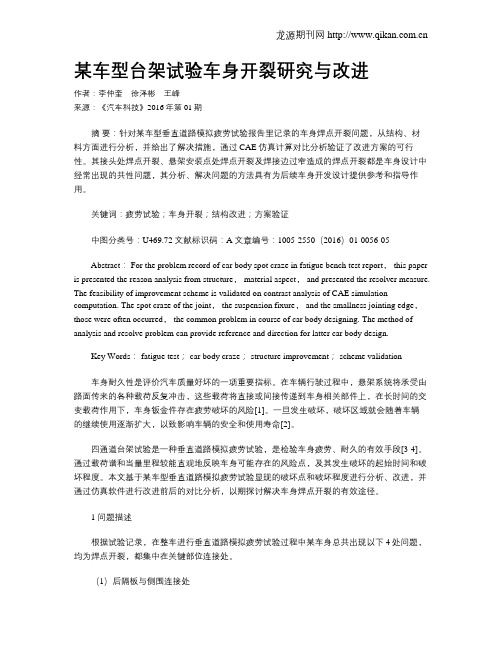
某车型台架试验车身开裂研究与改进作者:李仲奎徐泽彬王峰来源:《汽车科技》2016年第01期摘要:针对某车型垂直道路模拟疲劳试验报告里记录的车身焊点开裂问题,从结构、材料方面进行分析,并给出了解决措施,通过CAE仿真计算对比分析验证了改进方案的可行性。
其接头处焊点开裂、悬架安装点处焊点开裂及焊接边过窄造成的焊点开裂都是车身设计中经常出现的共性问题,其分析、解决问题的方法具有为后续车身开发设计提供参考和指导作用。
关键词:疲劳试验;车身开裂;结构改进;方案验证中图分类号:U469.72 文献标识码:A 文章编号:1005-2550(2016)01-0056-05Abstract: For the problem record of car body spot craze in fatigue bench test report, this paper is presented the reason analysis from structure, material aspect, and presented the resolver measure. The feasibility of improvement scheme is validated on contrast analysis of CAE simulation computation. The spot craze of the joint, the suspension fixure, and the smallness jointing edge,those were often occurred, the common problem in course of car body designing. The method of analysis and resolve problem can provide reference and direction for latter car body design.Key Words: fatigue test; car body craze; structure improvement; scheme validation车身耐久性是评价汽车质量好坏的一项重要指标。
商用车前保险杠支架断裂分析与优化

10.16638/ki.1671-7988.2019.19.017商用车前保险杠支架断裂分析与优化史季青,王淼,高军委,陆豪,郭宁(陕西汽车控股集团有限公司技术中心,陕西西安710200)摘要:针对某商用车在试验场进行强化路面试验过程中保险杠支架出现断裂的问题,基于保险杠总成及试验场路面数据,通过有限元的方法找出保险杠支架断裂的原因,提出优化方案,并对优化方案进行验证,显示保险杠支架优化后较优化前性能得到明显改善,并经后期样车验证问题得以解决。
关键词:保险杠;有限元分析;扫频激励中图分类号:U463.83 文献标识码:A 文章编号:1671-7988(2019)19-45-03Analysis and Optimization on Front Bumper Support Fracture forCommercial VehicleShi Jiqing, Wang Miao, Gao Junwei, Lu Hao, Guo Ning( Technical Center, Shaanxi Automobile Group Co., Ltd., Shaanxi Xi`an 710200 )Abstract: In view of a commercial vehicle in the process of strengthening pavement test, the bumper bracket fracture. Based on the bumper assembly and pavement data of the test site, the reason of the bumper support fracture is found out by the finite element method, and the optimization scheme is put forward to verify the optimization scheme, which shows that the performance of the bumper support is improved after optimization. And the problem of sample car verification was eliminated.Keywords: Bumper; Finite element analysis; Sweep excitationCLC NO.: U463.83 Document Code: A Article ID: 1671-7988(2019)19-45-03前言车辆在行驶过程中,承受来自地面不平度、轮胎激励和来自发动机的各种激励,而往往在一些车辆附件的分析验证过程中,忽视了这些激励对附件的影响,从而产生各种各样的振动问题。
某车型悬置紧固件断裂问题分析及紧固参数设定研究
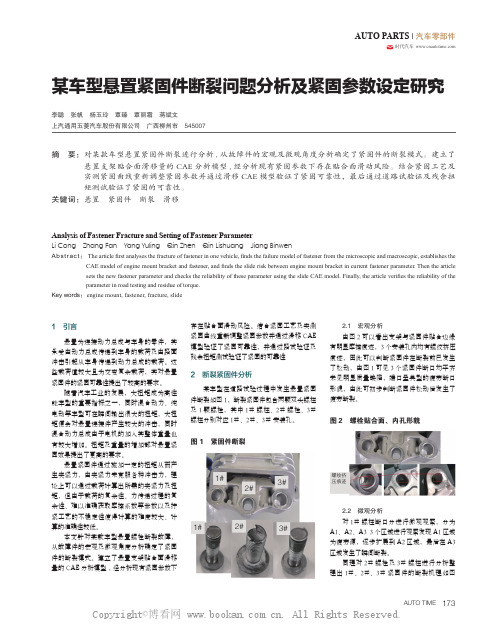
瞬断区
瞬断区
3#
次疲劳源区
瞬断区 疲劳扩展区
主疲劳源区
次疲劳源区
3 滑移分析
建立悬置支架、紧固件滑移 CAE 模型如 图 5,建立了悬置支架与支架间的接触模型, 通过该模型可计算出两个金属支架的相对滑 移量从而判断紧固件的夹紧力是否足够,该 模型需输入载荷及紧固件预紧力。
图 5 滑移分析模型
3.2 夹紧力获取 该车型采用的拧紧方式为扭矩法,设定 扭矩值为 110+/-10N.m,可根据以下公式 得到对应的夹紧力,也可根据夹紧力实测曲 线如图 6 得到,为使夹紧力更贴合实际,本 为采用实测曲线进行计算。
AUTO TIME 173
Copyright©博看网 . All Rights Reserved.
AUTO PARTS | 汽车零部件
图 3 1# 螺柱微观形貌
A1
裂纹源
即悬置系统 28 工况力作为输入力,经计算其 中第 25 工况力为最易引起滑移的工况,以下 计算以第 25 工况力作为输入力,力值如表 1 所示。
悬置紧固件通过施加一定的扭矩从而产 生夹紧力,由夹紧力来克服各种冲击力,理 论上可以通过载荷计算出所需的夹紧力及扭 矩,但由于载荷的复杂性、力传递过程的复 杂性、难以准确获取摩擦系数等参数以及拧 紧工艺的不稳定性使得计算的难度较大、计 算的准确性较低。
本文针对某款车型悬置螺栓断裂故障, 从故障件的宏观及微观角度分析确定了紧固 件的断裂模式。建立了悬置支架贴合面滑移 量的 CAE 分析模型 , 经分析现有紧固参数下
图 2 螺栓贴合面、内孔形貌
螺纹挤 压痕迹
2.2 微观分析 对 1# 螺柱断口分进行微观观察,分为 A1、A2、A3 3 个区域进行观察发现 A1 区域 为疲劳源,逐步扩展到 A2 区域,最后在 A3 区域发生了瞬间断裂。 同理对 2# 螺栓及 3# 螺柱进行分析整 理出 1#、2#、3# 紧固件的断裂机理如图
中国汽车技术论坛_轻型货车车架纵梁异常开裂原因的分析

轻型货车车架纵梁异常开裂原因的分析周志革王金刚崔根群河北工业大学车辆工程系轻型货车车架纵梁异常开裂原因的分析The Analysis on the Cause of Side Rail AbnormalFracture in Light Vehicle周志革王金刚崔根群(河北工业大学车辆工程系)摘要:车架的可靠性对整车的安全有着重要的意义。
针对轻型货车在行驶过程中纵梁撕裂的问题,应用有限元分析软件对车架的强度进行了分析,并通过实验的方法证明了计算模型的正确性。
分析结果表明:减震器支架在车辆行驶过程中对纵梁的冲击导致了纵梁的开裂。
根据实际工艺要求,提出了改进措施,使得开裂区域的应力值降低了61%。
关键词:车架纵梁有限元开裂Abstract: The reliability of an automobile frame is very important to the safety. Static strength of the frame was examined by numerical simulation using the finite element method (FEM) for solving the fracture of side rail of light vehicle. In the mean time, the correctness of the FEM model was verified by the experiment. The FEM result showed that the impact of damping force from vibration absorber resulted in the fracture of side rail. An improved bracket structure of vibration absorber was suggested based on the actual process, and the stress decreased by 61%.Key Words:frame, side rail, FEM, fracture1 前言车架不但承担发动机、车身、底盘、货物和乘客的重量,而且还承受汽车行驶时所产生的各种力和力矩。
某商用车摆锤冲击安全性CAE分析与改进设计
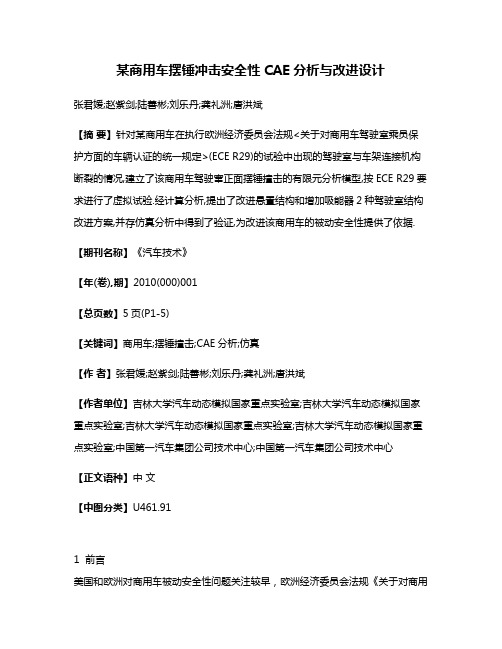
某商用车摆锤冲击安全性CAE分析与改进设计张君媛;赵紫剑;陆善彬;刘乐丹;龚礼洲;唐洪斌【摘要】针对某商用车在执行欧洲经济委员会法规<关于对商用车驾驶室乘员保护方面的车辆认证的统一规定>(ECE R29)的试验中出现的驾驶室与车架连接机构断裂的情况,建立了该商用车驾驶窜正面摆锤撞击的有限元分析模型,按ECE R29要求进行了虚拟试验.经计算分析,提出了改进悬置结构和增加吸能器2种驾驶室结构改进方案,并存仿真分析中得到了验证,为改进该商用车的被动安全性提供了依据.【期刊名称】《汽车技术》【年(卷),期】2010(000)001【总页数】5页(P1-5)【关键词】商用车;摆锤撞击;CAE分析;仿真【作者】张君媛;赵紫剑;陆善彬;刘乐丹;龚礼洲;唐洪斌【作者单位】吉林大学汽车动态模拟国家重点实验室;吉林大学汽车动态模拟国家重点实验室;吉林大学汽车动态模拟国家重点实验室;吉林大学汽车动态模拟国家重点实验室;中国第一汽车集团公司技术中心;中国第一汽车集团公司技术中心【正文语种】中文【中图分类】U461.911 前言美国和欧洲对商用车被动安全性问题关注较早,欧洲经济委员会法规《关于对商用车驾驶室乘员保护方面的车辆认证的统一规定》(ECE R29)是检测商用车驾驶室被动安全性能的统一要求。
国外许多商用车生产厂家和研究机构都已深入开展商用车被动安全性的仿真分析和试验研究工作,其中包括商用车驾驶室的抗撞性分析、前后防护装置分析和碰撞过程中驾驶室内乘员伤害分析等[1~4]。
虽然国内的相应法规尚不全面,但许多商用车生产厂家及高校都已开始关注和研究商用车的被动安全性[5~8]。
本文结合某商用车的被动安全性开发,采用试验和CAE仿真分析相结合的方法,依据ECE R29法规中关于商用车摆锤撞击安全性的要求进行某商用车驾驶室结构改进设计。
2 试验与建模2.1 ECE R29商用车正面撞击试验ECE R29包括商用车正面撞击试验(试验A)、车顶强度试验(试验B)和后围强度试验(试验C)3项试验。
基于CAE技术的汽车传动轴中间支撑开裂分析

中国第一汽车集团公司技术中心 张建振 常连霞
1 传动轴CAE分析技术
推测该车中间支撑吊板开裂的 可能原因,从载荷、强度、频率3个 方面归纳基于CAE技术进行传动轴 分析的基本思路,见图1。
(1)Hypermesh环境下进行前 处理
将PRO/E中建立的传动轴三 维模型导入Hypermesh中,使用 ABAQUS模板下二阶实体网格单 元,对模型进行划分。对轴管、前
(3)ADAMS多体动力学分析获 得载荷
首先,在ADAMS/Aview中建立 传动轴的多体动力学简化模型。该 模型中考虑了后端花键套之间的滑 动摩擦,以及中间支撑的实际测量 刚度和根据Hypermesh模型计算得 到的质量惯量特性。
根据频率分析结果,确定传动 轴共振转速下变速器最大传动比、 直接挡(或超速挡)工况下传递到
机器人力控精密装配技术是首次应用在汽车发动机活塞的装配工艺上。力控制技术与动力总成装配自动化生产线的完美结合, 实现了替代人工并有效改善健康和安全、保证始终如一的高产品质量与有效节省生产空间的三大优点。ABB柔性精加工技术包含了 力控压力控制和力控速度控制加工工艺,以及自动表面寻找路径功能。对于不确定位置的装配体,可 以迅速准确的找到与之相匹配的装配路径,一举实现了自动装配工艺上的技术突破和飞跃。
表1 考虑后桥时传动轴总成的一阶弯曲模态
Hz
图1 基于CAE技术的传动轴分析思路
振型 一阶水平 一阶垂直
传动轴频率 56.7 65.8
前中间支撑频率 28.2 36.3
后中间支撑频率 28.2 22.8
46 汽 车 工 艺 与 材 料 AT&M
2009年第8期
数 字化园地
D I G I TA L
DOMAIN