一种含钒钢渣提钒的方法
从含钒钢渣中富集钒的方法与流程
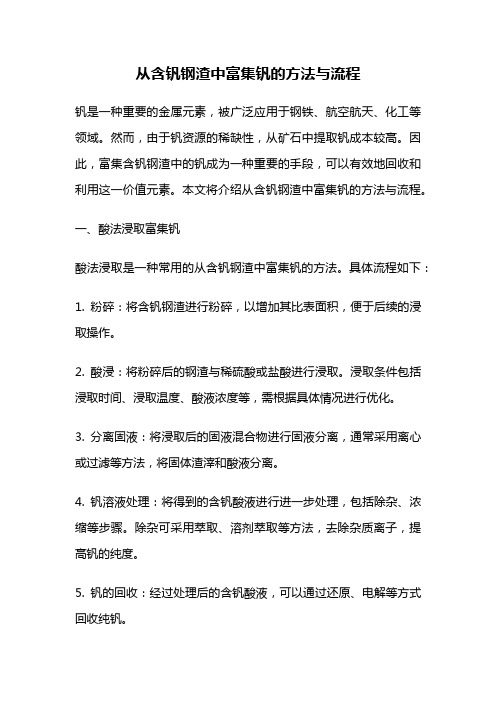
从含钒钢渣中富集钒的方法与流程
钒是一种重要的金属元素,被广泛应用于钢铁、航空航天、化工等领域。然而,由于钒资源的稀缺性,从矿石中提取钒成本较高。因此,富集含钒钢渣中的钒成为一种重要的手段,可以有效地回收和利用这一价值元素。本文将介绍从含钒钢渣中富集钒的方法与流程。
一、酸法浸取富集钒
酸法浸取是一种常用的从含钒钢渣中富集钒的方法。具体流程如下:
1. 粉碎:将含钒钢渣进行粉碎,以增加其比表面积,便于后续的浸取操作。
2. 酸浸:将粉碎后的钢渣与稀硫酸或盐酸进行浸取。浸取条件包括浸取时间、浸取温度、酸液浓度等,需根据具体情况进行优化。
3. 分离固液:将浸取后的固液混合物进行固液分离,通常采用离心或过滤等方法,将固体渣滓和酸液分离。
4. 钒溶液处理:将得到的含钒酸液进行进一步处理,包括除杂、浓缩等步骤。除杂可采用萃取、溶剂萃取等方法,去除杂质离子,提高钒的纯度。
5. 钒的回收:经过处理后的含钒酸液,可以通过还原、电解等方式回收纯钒。
二、矩阵冶金法富集钒
矩阵冶金法是另一种常用的从含钒钢渣中富集钒的方法。具体流程如下:
1. 热处理:将含钒钢渣进行热处理,使其中的钒转化为易溶性的钒化合物。热处理温度和时间需要根据钢渣的组成和性质进行调控。
2. 酸浸:将经过热处理的钢渣与酸性溶液进行浸取。浸取酸液的浓度和温度需要根据钢渣的特性进行优化。
3. 分离固液:将浸取后的固液混合物进行分离,得到固体渣滓和酸液。
4. 钒溶液处理:对得到的含钒酸液进行杂质去除和钒的富集。杂质去除可以采用萃取、溶剂萃取等方法。
5. 钒的回收:经过处理后的含钒酸液,可以通过还原、电解等方式回收纯钒。
含钒铁水转炉提钒渣冶炼方案(初稿)

含钒铁水转炉提钒渣冶炼方案
目录
1.钒相关基础知识 (4)
1.1钒元素的发现与发展 (4)
1.2国内钒的发展 (5)
1.3钒的矿物简介 (6)
1.4钒及其化合物的性质 (6)
1.4.1金属钒的性质 (6)
1.4.2金属钒的制备: (7)
1.4.3钒的主要氧化物 (7)
1.4.4含钒化合物的理化性能 (8)
1.5钒在钢铁上的应用 (9)
1.6钒的生产方法 (10)
2.转炉提钒基本原理 (11)
2.1转炉提钒的意义 (11)
2.2转炉提钒的原理 (12)
2.3铁质初渣与金属熔体间的氧化反应 (12)
2.4转炉提钒脱钒、脱碳规律 (12)
2.5铁水中钒与碳氧化的转化温度 (13)
2.6影响转炉提钒的主要因素 (15)
2.6.1铁水成分的影响 (15)
2.6.2 铁水中钒的影响 (15)
2.6.3.铁水硅的影响 (15)
2.6.4.吹炼终点温度对钒渣中全铁含量影响 (16)
2.6.5.供氧制度的影响 (17)
3.提取钒渣方法 (17)
3.1顶底复吹转炉提钒 (17)
3.2转炉单联法提钒 (18)
3.3攀钢转炉提钒工艺 (20)
3.3.1转炉提钒工艺流程图 (20)
3.3.2攀钢转炉提钒工艺过程 (20)
3.3.3攀钢转炉提钒主要设备参数 (21)
3.3.4攀钢转炉提钒用原材料 (21)
3.3.5 不同氧枪的提钒效果 (22)
3.3.6攀钢转炉提钒冷却制度 (23)
3.3.7攀钢转炉提钒终点控制 (24)
3.3.8出半钢和倒钒渣 (24)
3.3.9攀钢提钒钒渣 (25)
4.八钢炼钢提钒渣方案 .......................................................................... 错误!未定义书签。
浅析含钒钢渣湿法提钒生产工艺与发展前景
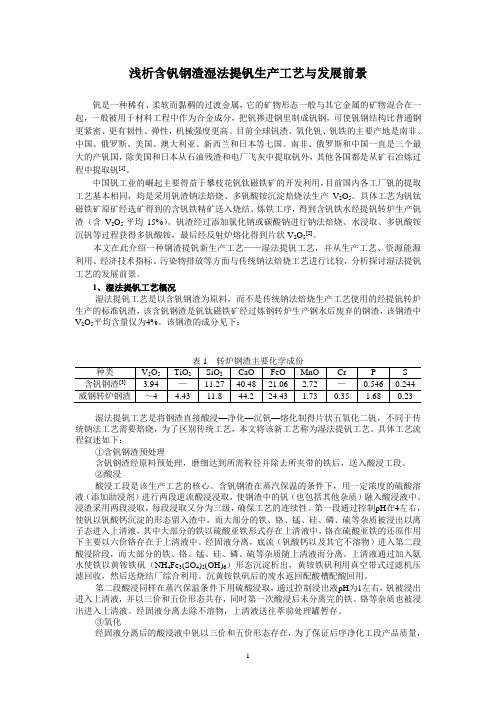
浅析含钒钢渣湿法提钒生产工艺与发展前景
钒是一种稀有、柔软而黏稠的过渡金属,它的矿物形态一般与其它金属的矿物混合在一起,一般被用于材料工程中作为合金成分,把钒掺进钢里制成钒钢,可使钒钢结构比普通钢更紧密、更有韧性、弹性,机械强度更高。目前全球钒渣、氧化钒、钒铁的主要产地是南非、中国、俄罗斯、美国、澳大利亚、新西兰和日本等七国。南非、俄罗斯和中国一直是三个最大的产钒国,除美国和日本从石油残渣和电厂飞灰中提取钒外,其他各国都是从矿石冶炼过程中提取钒[1]。
中国钒工业的崛起主要得益于攀枝花钒钛磁铁矿的开发利用,目前国内各工厂钒的提取工艺基本相同,均是采用钒渣钠法焙烧、多钒酸铵沉淀焙烧法生产V2O5。具体工艺为钒钛磁铁矿原矿经选矿得到的含钒铁精矿送入烧结、炼铁工序,得到含钒铁水经提钒转炉生产钒渣(含V2O5平均15%)。钒渣经过添加氯化钠或碳酸钠进行钠法焙烧、水浸取、多钒酸铵沉钒等过程获得多钒酸铵,最后经反射炉熔化得到片状V2O5[2]。
本文在此介绍一种钢渣提钒新生产工艺——湿法提钒工艺,并从生产工艺、资源能源利用、经济技术指标、污染物排放等方面与传统钠法焙烧工艺进行比较,分析探讨湿法提钒工艺的发展前景。
1、湿法提钒工艺概况
湿法提钒工艺是以含钒钢渣为原料,而不是传统钠法焙烧生产工艺使用的经提钒转炉生产的标准钒渣,该含钒钢渣是钒钛磁铁矿经过炼钢转炉生产钢水后废弃的钢渣,该钢渣中V2O5平均含量仅为4%。该钢渣的成分见下:
湿法提钒工艺是将钢渣直接酸浸—净化—沉钒—熔化制得片状五氧化二钒,不同于传统钠法工艺需要焙烧,为了区别传统工艺,本文将该新工艺称为湿法提钒工艺。具体工艺流程叙述如下:
第三章 提取钒渣方法详解

4、雾化提钒的特点
①雾化提钒反应的动力学条件好,有利于氧化反应进行,钒 氧化率高(可达到90%以上)。
②工艺简单、设备投资省、炉龄高、提钒作业率高,可半连
续化生产。 ③中间罐撇渣效果好。 ④铁水被压缩空气雾化,温降大,因此雾化提钒不必加冷 却剂,有时还要加硅铁氧化提温和改善流动性。
⑤工艺条件不太稳定 , 半钢温度低,渣铁分离效果差,钒
铁水击碎成雾状,雾状铁水和富氧空气强烈混合,使铁水和 氧的反应界面急剧增大,氧化反应迅速进行。压缩空气可对 反应区进行非常有效的冷却,使反应温度限制在对钒氧化有 利的范围内。
8
⑶被击碎的铁水在反应过程中汇集到雾化室底部通过半 钢出钢槽进入半钢罐,钒渣漂浮于半钢表面形成渣层,最后 将半钢与钒渣分离。 雾化提钒时,只有 50 ~ 60 %的钒氧化是在雾化室中完
目前世界上铁水提钒的方法主要有四种:
⑴ 摇包提钒——南非海威尔德 ⑵ 铁水包提钒——新西兰 ⑶ 空气底吹转炉提钒——俄罗斯丘索夫 ⑷ 氧气顶吹(复合吹炼)提钒——俄罗斯下塔吉尔和中
国攀钢、马钢、承钢。
一、雾化提钒
1、雾化提钒工艺
雾化提钒是攀
高炉铁水 铁水罐 140吨倾翻机 倾翻铁水进入中间罐 硅铁或 石英砂 雾化吹炼 半钢兑铁罐 半钢与钒渣分离 半钢 钒渣 富氧压缩 空气 脱硫
雾化提钒装置示意图
6
⑴ 雾化器 雾化器是雾化提钒的关键设备。 ① 其 设计制造是否优良不仅直接 影响到钒的氧化率、半钢温度等技 术指标,而且也直接影响到雾化室 寿命的高低。 ②好的雾化器 : 雾化效果好、 钒氧化率高、不反溅、好维护、寿
五氧化二钒
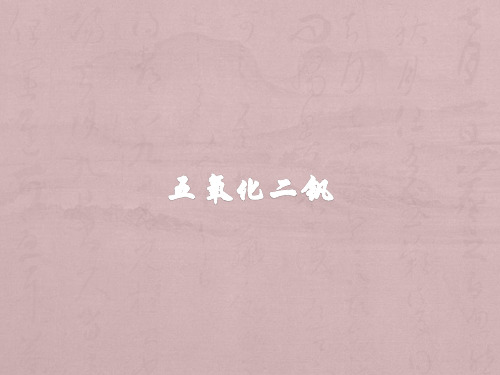
一般以原料分为以下几种: 1)钒渣提钒;2)含钒钢渣提钒;3)钠化渣 提钒;4)石煤提钒;5)钒矿钙化提钒;6) 含钒铀矿提钒;7)铝土矿提钒等
是在氧化气氛下,物料从低温到高温再逐渐降 温的连续过程,主要物理化学反应包括:
1)在300℃左右金属铁氧化 2)在500℃~600 ℃黏结相铁橄榄石氧化并分解 3)在600℃~700 ℃尖晶石氧化分解 4)在600℃~700 ℃五氧化二钒与钠盐反应生成溶于水的钒 酸钠 + 5)在600℃~700 ℃五氧化二钒与铁、锰、钙等氧化物生成 溶于酸但不溶于水的钒酸盐
钒溶液铵盐沉淀是将钒酸钠溶液用硫酸调节 到一定酸度,加入铵盐,在加热搅拌的条件 下沉淀结晶出橘黄色的多钒酸按(APV),沉 淀后上层液(母液)含钒在0.1g/L以下。反应 方程式为:
6NaVO3+2H2SO4+2NH4Cl=(NH4)2V6O16 +2Na2SO4+2H2O
+ 由于钒在不同浓度和pH的溶液中存在的形
式有复杂的变化,其沉淀的晶体结构也呈 多样性,这为酸法铵盐沉淀控制增加了难 度。 + 主要生成两种沉淀物,其一是橘黄色的多 钒酸铵、其二是棕红色或砖红色的絮状多 钒酸盐沉淀,由于其杂质含量高,过滤性 能差,生产过程应该避免它的生产。
第五章含钒铁水炼钢工艺及钢渣钒渣提钒ppt课件

c.吹炼后期,为防止产生大量低熔点物质,不利于炉衬挂 渣和保护炉衬,需适当降低枪位,控制终点(FeO)含量不能过 高,这样在出钢时,随着炉温的降低,有MgO微粒析出,使 炉渣粘稠,能挂于炉壁上。
2、终点控制
攀钢采用低拉增碳法。超低碳钢采用RH脱碳,中高碳钢 采用增碳法补碳。
三、钒渣的作用 ①钒渣直接冶炼钒铁 ②钒渣作为生产钒化合物原料 ③用钒渣使钢直接合金化
⑶渣料加入Байду номын сангаас间和炉渣的控制 攀钢渣料一般分两批加入,第一批占总渣料的60%以上,其余在第二批
分小批加入。如拉碳后需调整炉渣或炉温,则再加入第三批渣料。 ①渣料加入时间
第一批渣料在兑铁前或开吹时加入,包括石灰、镁质材料和酸性材料。 第二批渣料在第一批渣料化好、化透后分小批量多次加入(每次不超过 0.5吨),这样有利于石灰熔化,避免炉渣“返干”,同时还可以较好控制 炉内泡沫渣,防止喷溅和溢渣,在吹炼终点前3~5min全部加完。 第三批渣料是否加入,根据拉碳后硫、磷去除情况而定。 注意:无论加几批渣料或加多少渣料,都必须保证终点炉渣化好,确 保渣料的有效利用。
钒渣
铁水 化学 成分
铁水
半钢
提钒前后铁水和半钢成分及温度
C% Si% Mn% V%
P%
S%
3.9~4. 0.05~0.2
6
0
0.1~0.30
提钒工艺技术

洗涤
目的:在NH4Cl+NaV03---NH4VO3+NaCl 反应中,由于生产Na盐等物质,易造成 成品V2O5纯度不够,所以要进行洗涤。 洗涤的方法:锦利公司采用工业用水洗 涤“黄饼”。
熔化
熔化:V2O5熔点为637℃,采用反射炉, 加热将多钒酸铵(APV)熔化。采用反射炉 熔化这种方法回收率一般在95%左右, 炉内分三步完成:脱水、脱氨、熔化。
钠化带
从600℃开始到焙烧最高温度之间的阶段。 焙烧最高温度应控制在800℃,温度过低造 成生烧,温度过高易结球、结块造成过烧 (宁愿生烧都不能过烧)。
主要反应:
V2O5+Na2CO3--->NaVO3+CO2 V2O5+Na2SO4--->NaVO3+SO2 V2O5+NaCl+H2O--->NaVO3+HCl
片状
V2O598
98
0.25 0.30 0.05 0.03 0.02
1.5
片状
化 工
V2O597
97
0.25 0.30 0.05
0.1
0.02
1.0
2.5
粉状
要求小于0.1mm以下,可增 碳酸钠、氯化钠、硫酸钠 在钒含量一定的情况下, 大钒渣的表面比,与钠盐更 等等。采用混合钠盐作为 配入的钠盐越多越容易生 最高温度不能超过 800℃。 好的接触反应。但是过细也 添加剂可降低成本,同时 有充分的时间才能使钒渣和 成低熔点物质 ,会使炉料粘 会增加磨矿成本 ,输送及焙烧 钠盐完全反应。 提高转换率和降低浸出液 结。少了会使钒渣中的钒 过程粉尘量大和难回收等困 的碱性。但不能单一使用 不能充分反应。 难,浸出后的残渣难过滤。 食盐或芒硝作为添加剂, 会影响焙烧效果。
钒如何提炼的原理
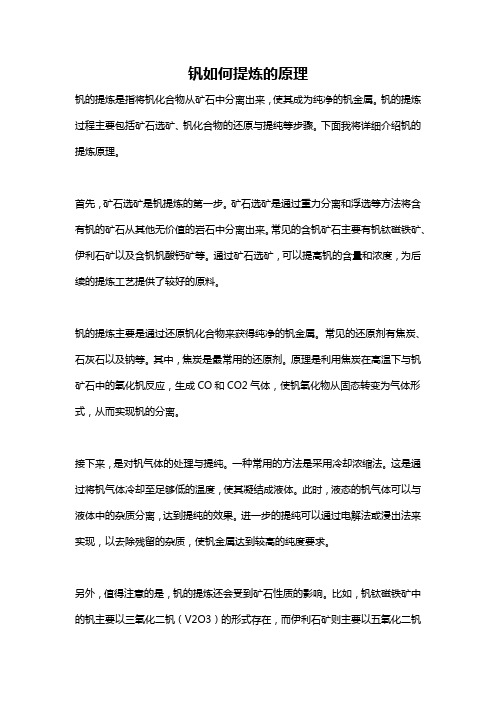
钒如何提炼的原理
钒的提炼是指将钒化合物从矿石中分离出来,使其成为纯净的钒金属。钒的提炼过程主要包括矿石选矿、钒化合物的还原与提纯等步骤。下面我将详细介绍钒的提炼原理。
首先,矿石选矿是钒提炼的第一步。矿石选矿是通过重力分离和浮选等方法将含有钒的矿石从其他无价值的岩石中分离出来。常见的含钒矿石主要有钒钛磁铁矿、伊利石矿以及含钒钒酸钙矿等。通过矿石选矿,可以提高钒的含量和浓度,为后续的提炼工艺提供了较好的原料。
钒的提炼主要是通过还原钒化合物来获得纯净的钒金属。常见的还原剂有焦炭、石灰石以及钠等。其中,焦炭是最常用的还原剂。原理是利用焦炭在高温下与钒矿石中的氧化钒反应,生成CO和CO2气体,使钒氧化物从固态转变为气体形式,从而实现钒的分离。
接下来,是对钒气体的处理与提纯。一种常用的方法是采用冷却浓缩法。这是通过将钒气体冷却至足够低的温度,使其凝结成液体。此时,液态的钒气体可以与液体中的杂质分离,达到提纯的效果。进一步的提纯可以通过电解法或浸出法来实现,以去除残留的杂质,使钒金属达到较高的纯度要求。
另外,值得注意的是,钒的提炼还会受到矿石性质的影响。比如,钒钛磁铁矿中的钒主要以三氧化二钒(V2O3)的形式存在,而伊利石矿则主要以五氧化二钒
(V2O5)的形式存在。因此,不同的矿石需要采用不同的提炼方法和工艺,以获得最佳的提炼效果。
总结起来,钒的提炼原理是通过矿石选矿、还原和提纯等步骤,将钒化合物从矿石中分离出来,获得纯净的钒金属。矿石选矿能够提高钒的含量和浓度,还原过程通过还原剂将钒氧化物转变为气体形式分离钒元素,提纯过程通过冷却浓缩、电解或浸出等方法去除杂质,使钒金属达到较高的纯度要求。不同的矿石需要采用不同的提炼方法和工艺,以获得最佳的提炼效果。这些步骤和方法的应用和改进,使得钒的提炼过程更加高效和经济。
钒钛磁铁矿提钒工艺技术综述(1)
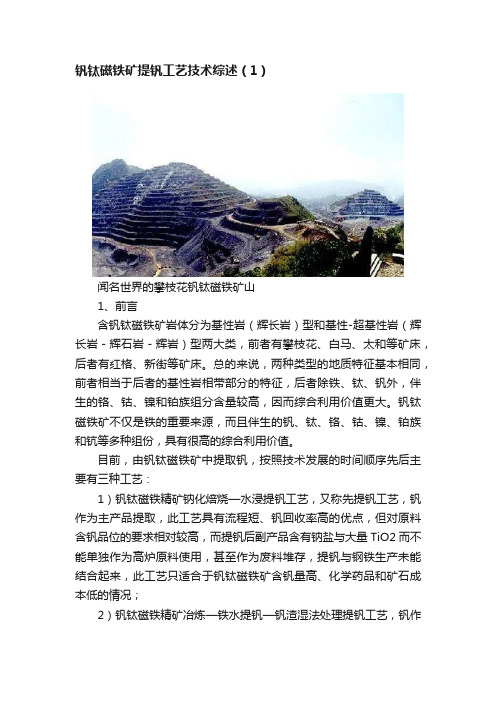
钒钛磁铁矿提钒工艺技术综述(1)
闻名世界的攀枝花钒钛磁铁矿山
1、前言
含钒钛磁铁矿岩体分为基性岩(辉长岩)型和基性-超基性岩(辉长岩-辉石岩-辉岩)型两大类,前者有攀枝花、白马、太和等矿床,后者有红格、新街等矿床。总的来说,两种类型的地质特征基本相同,前者相当于后者的基性岩相带部分的特征,后者除铁、钛、钒外,伴生的铬、钴、镍和铂族组分含量较高,因而综合利用价值更大。钒钛磁铁矿不仅是铁的重要来源,而且伴生的钒、钛、铬、钴、镍、铂族和钪等多种组份,具有很高的综合利用价值。
目前,由钒钛磁铁矿中提取钒,按照技术发展的时间顺序先后主要有三种工艺:
1)钒钛磁铁精矿钠化焙烧—水浸提钒工艺,又称先提钒工艺,钒作为主产品提取,此工艺具有流程短、钒回收率高的优点,但对原料含钒品位的要求相对较高,而提钒后副产品含有钠盐与大量TiO2而不能单独作为高炉原料使用,甚至作为废料堆存,提钒与钢铁生产未能结合起来,此工艺只适合于钒钛磁铁矿含钒量高、化学药品和矿石成本低的情况;
2)钒钛磁铁精矿冶炼—铁水提钒—钒渣湿法处理提钒工艺,钒作
为副产品回收,也是目前由钒钛磁铁矿提取钒最主要、经济上最为合理的工艺,此工艺可以利用含钒品位低的原料;
3)钒钛磁铁精矿非高炉冶炼—电炉熔分/电炉深还原—熔分渣提钒/铁水提钒工艺,此法能耗低、环保好,钒的收得率高,是提钒技术的发展方向。
目前,前两种钒钛磁铁矿提钒工艺各有优点和缺点,不是单纯的工艺改进和完善,因此,第二种工艺并没有完全替代第一种工艺,而是以第二种工艺为主,两种提钒工艺共存的方式存在。
从含钒钢渣酸浸液中萃取钒的试验研究
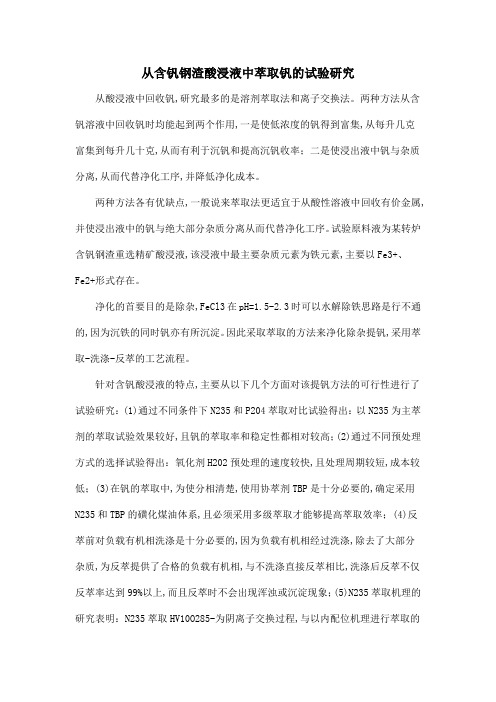
从含钒钢渣酸浸液中萃取钒的试验研究
从酸浸液中回收钒,研究最多的是溶剂萃取法和离子交换法。两种方法从含钒溶液中回收钒时均能起到两个作用,一是使低浓度的钒得到富集,从每升几克富集到每升几十克,从而有利于沉钒和提高沉钒收率;二是使浸出液中钒与杂质分离,从而代替净化工序,并降低净化成本。
两种方法各有优缺点,一般说来萃取法更适宜于从酸性溶液中回收有价金属,并使浸出液中的钒与绝大部分杂质分离从而代替净化工序。试验原料液为某转炉含钒钢渣重选精矿酸浸液,该浸液中最主要杂质元素为铁元素,主要以Fe3+、
Fe2+形式存在。
净化的首要目的是除杂,FeCl3在pH=1.5-2.3时可以水解除铁思路是行不通的,因为沉铁的同时钒亦有所沉淀。因此采取萃取的方法来净化除杂提钒,采用萃取-洗涤-反萃的工艺流程。
针对含钒酸浸液的特点,主要从以下几个方面对该提钒方法的可行性进行了试验研究:(1)通过不同条件下N235和P204萃取对比试验得出:以N235为主萃剂的萃取试验效果较好,且钒的萃取率和稳定性都相对较高;(2)通过不同预处理方式的选择试验得出:氧化剂H202预处理的速度较快,且处理周期较短,成本较低;(3)在钒的萃取中,为使分相清楚,使用协萃剂TBP是十分必要的,确定采用
N235和TBP的磺化煤油体系,且必须采用多级萃取才能够提高萃取效率;(4)反萃前对负载有机相洗涤是十分必要的,因为负载有机相经过洗涤,除去了大部分杂质,为反萃提供了合格的负载有机相,与不洗涤直接反萃相比,洗涤后反萃不仅反萃率达到99%以上,而且反萃时不会出现浑浊或沉淀现象;(5)N235萃取机理的研究表明:N235萃取HV10O285-为阴离子交换过程,与以内配位机理进行萃取的
一种含钒钢渣提钒方法
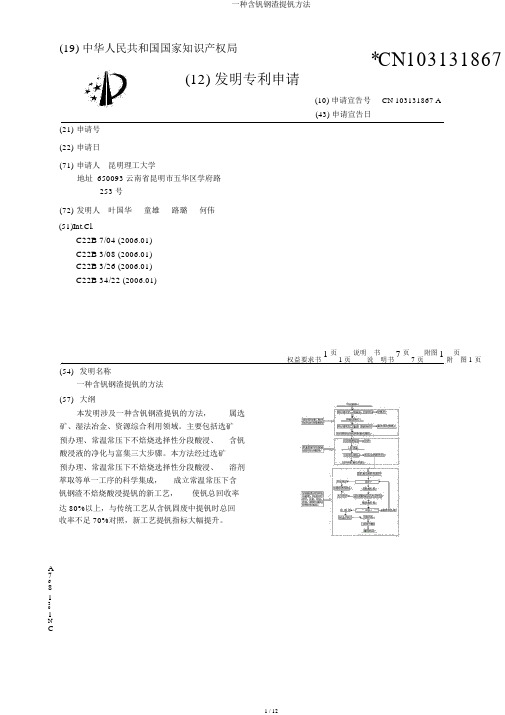
一种含钒钢渣提钒方法
(19) 中华人民共和国国家知识产权局*CN103131867
(12)发明专利申请
(10) 申请宣告号CN 103131867 A
(43) 申请宣告日
(21)申请号
(22)申请日
(71)申请人昆明理工大学
地址 650093 云南省昆明市五华区学府路
253 号
(72)发明人叶国华童雄路璐何伟
(51)Int.Cl.
C22B 7/04 (2006.01)
C22B 3/08 (2006.01)
C22B 3/26 (2006.01)
C22B 34/22 (2006.01)
权益要求书1页
1页
说明
说
书
明书
7页
7 页
附图1
附
页
图 1 页
(54)发明名称
一种含钒钢渣提钒的方法
(57)大纲
本发明涉及一种含钒钢渣提钒的方法,属选矿、湿法冶金、资源综合利用领域。主要包括选矿
预办理、常温常压下不焙烧选择性分段酸浸、含钒酸浸液的净化与富集三大步骤。本方法经过选矿
预办理、常温常压下不焙烧选择性分段酸浸、溶剂萃取等单一工序的科学集成,成立常温常压下含钒钢渣不焙烧酸浸提钒的新工艺,使钒总回收率达 80%以上,与传统工艺从含钒固废中提钒时总回
收率不足 70%对照,新工艺提钒指标大幅提升。
A
7
6
8
1
3
1
N
C
CN 103131867 A 权利要求书
1/1 页
1.一种含钒钢渣提钒的方法,其特点在于详尽步骤包括以下:
(1)将含钒钢渣破碎、磨矿后在依照旧规工艺在磁场强度为 0.08T ~ 0.25T 的条件下进行弱磁选,获取的磁性物质为磁性铁精矿,其余为磁选尾矿,尔后将磁性铁精矿加水调整至矿浆浓度 15 ~ 30wt%,在冲程 6 ~ 14mm、冲次 280 ~ 440r/min 的条件下依照旧规工艺
含钒钢渣提钒研究背景、意义、目的与方法研究

含钒钢渣提钒研究背景、意义、目的与方法研究
1钒化合物性质及其应用 (1)
2钒资源在我国的分布情况 (2)
3 提钒工艺的发展 (3)
4现行含钒钢渣提钒方法简述 (3)
4.1 酸浸-碱溶法 (3)
4.2 钠化焙烧提钒法 (4)
4.3 钙化焙烧提钒法 (4)
4.4 溶剂萃取法 (4)
4.5 离子交换提钒法 (5)
5研究目的和意义 (5)
5.1 目的 (5)
5.2 意义 (6)
1钒化合物性质及其应用
如果说钢是虎,那么钒就是翼,钢含钒犹如虎添翼。只需在钢中加入百分之几的钒,就能使钢的弹性、强度大增,抗磨损和抗爆裂性极好,既耐高温又抗奇寒,难怪在汽车、航空、铁路、电子技术、国防工业等部门,到处可见到钒的踪迹。此外,钒的氧化物已成为化学工业中最佳催化剂之一,有“化学面包”之称。
主要用于制造高速切削钢及其他合金钢和催化剂。把钒掺进钢里,可以制成钒钢。钒钢比普通钢结构更紧密,韧性、弹性与机械强度更高。钒钢制的穿甲弹,能够射穿40厘米厚的钢板。但是,在钢铁工业上,并不是把纯的金属钒加到钢铁中制成钒钢,而是直接采用含钒的铁矿炼成钒钢。
钒的盐类的颜色真是五光十色,有绿的、红的、黑的、黄的,绿的碧如翡翠,黑的犹如浓墨。如二价钒盐常呈紫色;三价钒盐呈绿色,四价钒盐呈浅蓝色,四价钒的碱性衍生物常是棕色或黑色,而五氧化二钒则是红色的。这些色彩缤纷的钒的化合物,被制成鲜艳的颜料:把它们加到玻璃中,制成彩色玻璃,也可以用来制造各种墨水。
五氧化二钒的半导体性质的发现和其在光学工业中作为抗静电涂层的应用,为它的研究开辟了新纪元。近年来,对作为功能材料的五氧化二钒的研究已经受到了广泛的重视,它的溶胶—凝胶制备技术也取得了鼓舞人心的进步。具有层状结构的五氧化二钒凝胶膜显示出有趣的电子、离子和电化学性质,此外,五氧化二钒还具有光电导性质。根据这些性质开展的应用研究也取得了长足的进步,例
氧化二钒
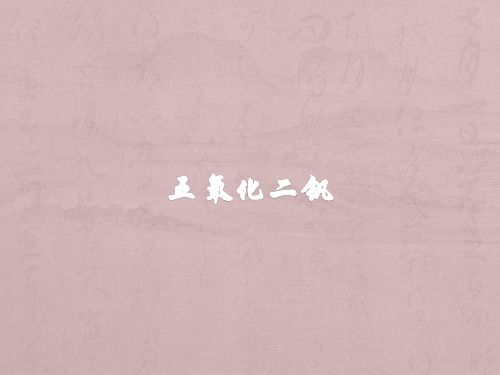
谢谢
前三种方法统称为从钒钛磁铁矿中提钒,我 国钒资源的存在决定了其生产方式。 接下来主要介绍钒渣提钒。
+ 原料:钒渣
+ 辅料:钠盐(碳酸钠、硫酸钠)或钙盐 (碳酸钙)、铵盐(氯化铵或硫酸铵)。
+ 产品:片状或粉状五氧化二钒,含量一般 为97~99%。
+ 以钒渣作为原料生产五氧化二钒主要包括 原料预处理、焙烧、钒溶液沉淀结晶和钒 酸盐分解、干燥及熔炼等五个工序。工艺 流程如下图
Hale Waihona Puke Baidu
+ 多钒酸铵是一种铵的聚钒酸盐,根据沉淀
的条件不同,沉淀产物的分子组成不易,
其分子式主要是NH4)2V12O31·nH2O 、 (NH4)2V6O16·nH2O,受热不稳定分解成氨 气以及五氧化二钒。由于氨气在该温度下
是一种强还原剂,能将五氧化二钒还原成
四氧化二钒,若有足够的氧气,四价钒重
新被氧化为五价钒。
+ 1)在300℃左右金属铁氧化 + 2)在500℃~600 ℃黏结相铁橄榄石氧化并分解 + 3)在600℃~700 ℃尖晶石氧化分解 + 4)在600℃~700 ℃五氧化二钒与钠盐反应生成溶于水的钒
酸钠 + 5)在600℃~700 ℃五氧化二钒与铁、锰、钙等氧化物生成
溶于酸但不溶于水的钒酸盐
+ 上述产物在水浸时,可溶性的杨溶解到水中, 部分产物将发生水解。
浅析含钒钢渣湿法提钒生产工艺与发展前景
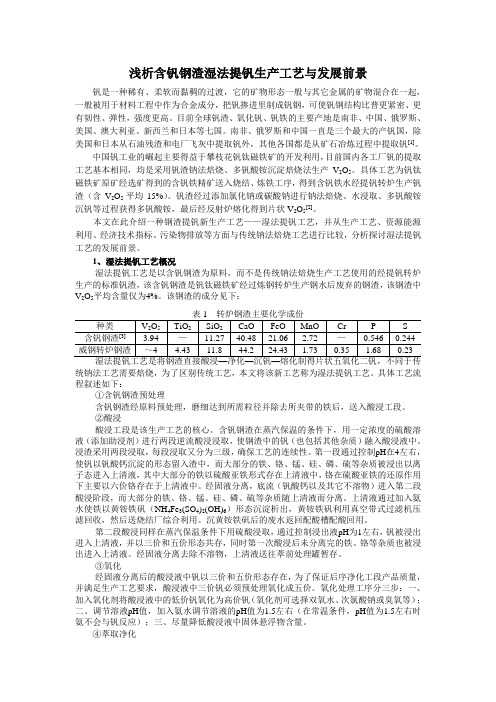
浅析含钒钢渣湿法提钒生产工艺与发展前景
钒是一种稀有、柔软而黏稠的过渡,它的矿物形态一般与其它金属的矿物混合在一起,一般被用于材料工程中作为合金成分,把钒掺进里制成钒钢,可使钒钢结构比普更紧密、更有韧性、弹性,强度更高。目前全球钒渣、氧化钒、钒铁的主要产地是南非、中国、俄罗斯、美国、澳大利亚、新西兰和日本等七国。南非、俄罗斯和中国一直是三个最大的产钒国,除美国和日本从石油残渣和电厂飞灰中提取钒外,其他各国都是从矿石冶炼过程中提取钒[1]。
中国钒工业的崛起主要得益于攀枝花钒钛磁铁矿的开发利用,目前国内各工厂钒的提取工艺基本相同,均是采用钒渣钠法焙烧、多钒酸铵沉淀焙烧法生产V2O5。具体工艺为钒钛磁铁矿原矿经选矿得到的含钒铁精矿送入烧结、炼铁工序,得到含钒铁水经提钒转炉生产钒渣(含V2O5平均15%)。钒渣经过添加氯化钠或碳酸钠进行钠法焙烧、水浸取、多钒酸铵沉钒等过程获得多钒酸铵,最后经反射炉熔化得到片状V2O5[2]。
本文在此介绍一种钢渣提钒新生产工艺——湿法提钒工艺,并从生产工艺、资源能源利用、经济技术指标、污染物排放等方面与传统钠法焙烧工艺进行比较,分析探讨湿法提钒工艺的发展前景。
1、湿法提钒工艺概况
湿法提钒工艺是以含钒钢渣为原料,而不是传统钠法焙烧生产工艺使用的经提钒转炉生产的标准钒渣,该含钒钢渣是钒钛磁铁矿经过炼钢转炉生产钢水后废弃的钢渣,该钢渣中V2O5平均含量仅为4%。该钢渣的成分见下:
统钠法工艺需要焙烧,为了区别传统工艺,本文将该新工艺称为湿法提钒工艺。具体工艺流程叙述如下:
- 1、下载文档前请自行甄别文档内容的完整性,平台不提供额外的编辑、内容补充、找答案等附加服务。
- 2、"仅部分预览"的文档,不可在线预览部分如存在完整性等问题,可反馈申请退款(可完整预览的文档不适用该条件!)。
- 3、如文档侵犯您的权益,请联系客服反馈,我们会尽快为您处理(人工客服工作时间:9:00-18:30)。
(10)申请公布号 (43)申请公布日 2013.06.05C N 103131867 A (21)申请号 201310077492.X
(22)申请日 2013.03.12
C22B 7/04(2006.01)
C22B 3/08(2006.01)
C22B 3/26(2006.01)
C22B 34/22(2006.01)
(71)申请人昆明理工大学
地址650093 云南省昆明市五华区学府路
253号
(72)发明人叶国华 童雄 路璐
何伟
(54)发明名称
一种含钒钢渣提钒的方法
(57)摘要
本发明涉及一种含钒钢渣提钒的方法,属选
矿、湿法冶金、资源综合利用领域。主要包括选矿
预处理、常温常压下不焙烧选择性分段酸浸、含钒
酸浸液的净化与富集三大步骤。本方法通过选矿
预处理、常温常压下不焙烧选择性分段酸浸、溶剂
萃取等单一工序的科学集成,构建常温常压下含
钒钢渣不焙烧酸浸提钒的新工艺,使钒总回收率
达80%以上,与传统工艺从含钒固废中提钒时总
回收率不足70%相比,新工艺提钒指标大幅提升。
(51)Int.Cl.
权利要求书1页 说明书7页 附图1页
(19)中华人民共和国国家知识产权局(12)发明专利申请权利要求书1页 说明书7页 附图1页(10)申请公布号CN 103131867 A
*CN103131867A*
1/1页
1.一种含钒钢渣提钒的方法,其特征在于具体步骤包括如下:
(1)将含钒钢渣破碎、磨矿后在按照常规工艺在磁场强度为0.08T ~0.25T 的条件下进行弱磁选,得到的磁性物质为磁性铁精矿,其余为磁选尾矿,然后将磁性铁精矿加水调整至矿浆浓度15~30wt%,在冲程6~14mm 、冲次280~440r/min 的条件下按照常规工艺进行重选,得到的比重大的物质为重选精矿,比重小的物质为重选尾矿;
(2)在常温常压条件下进行Ⅰ段预浸除杂,将步骤(1)中得到的重选精矿在硫酸溶液中按照固液比1:1~6g/ml 混合并调整混合液的pH 值为3~4,在搅拌强度为100~500转/min 的条件下搅拌浸出0.5~6h ,经固液分离得到Ⅰ段浸渣和含铁酸浸液;在常温常压条件下进行Ⅱ段浸出提钒,将Ⅰ段浸渣在硫酸溶液中按照固液比1:1~6g/ml 混合并调整混合液的pH 值为0.3~2,经固液分离得到Ⅱ段浸渣和含钒酸浸液;
(3)首先将步骤(2)中的含钒酸浸液按照常规工艺依次进行萃前氧化、酸度调节和萃取,萃取的上层清液为负载有机相,下层为萃取废液,上下层分离后将负载有机相进行洗涤除杂,在常温条件下,将负载有机相加入活性硫酸盐溶液中,按照相比O/A=1~6的条件下洗涤3~15min ,洗涤完毕后得到的上层清液为载钒有机相,下层为洗涤废液,将上下层分离,即可得到载钒有机相和洗涤废液,洗涤废液按常规工艺处理后返回浸出;
(4)将步骤(3)中得到的载钒有机相按照常规工艺进行反萃,反萃后得到的上层液为卸载有机相,下层液为反萃液,卸载有机相返回萃取步骤使用,反萃液按照常规工艺进行铵盐沉钒,将铵盐沉钒得到的沉淀产品按照常规工艺进行煅烧分解,最终制得的精钒产品。
2.根据权利要求1所述的含钒钢渣提钒的方法,其特征在于:所述含钒钢渣产生于含钒铁水的炼钢过程,具体成分包括V 2O 5 1~5wt%,CaO 40%~60wt%,TFe 10%~25wt%。
3.根据权利要求1所述的含钒钢渣提钒的方法,其特征在于:所述含钒钢渣破碎、磨矿后的粒度为小于74μm 的占含钒钢渣的55wt%以上。
4.根据权利要求1所述的含钒钢渣提钒的方法,其特征在于:所述含钒酸浸液在萃取之前按照常规工艺进行萃前氧化是将含钒酸浸液中的钒离子全部氧化为5价,溶液颜色从蓝绿色变成棕黄色,酸度调节是调整含钒酸浸液pH 为1.0~2.5。
5.根据权利要求1所述的含钒钢渣提钒的方法,其特征在于:所述活性硫酸盐为硫酸钠或硫酸铵,浓度为0.2~0.8mol/L 。权 利 要 求 书CN 103131867 A
一种含钒钢渣提钒的方法
技术领域
[0001] 本发明涉及一种含钒钢渣提钒的方法,属选矿、湿法冶金、资源综合利用领域,具体是一种常温常压下含钒钢渣不焙烧酸浸提钒的新工艺,即“含钒钢渣选矿预处理-常温常压下不焙烧选择性分段酸浸提钒”。
背景技术
[0002] 含钒钢渣产生于含钒铁水的炼钢过程,有以下特点:一,它一般是废弃资源,量大价低;二,钙和铁含量高、钒含量低;三,钒的分布比其它含钒矿物要复杂得多,分散、细小、弥散于多种矿物相中。这种既分散又细小的人造矿,属极难处理矿,难以直接选矿分离。[0003] 从含钒钢渣中提钒主要有两类途径。一是对钢渣进行火法冶炼,炼出高钒渣,再进一步提钒。该法易产生磷在铁水中的循环富集,加重炼钢脱磷任务。俄罗斯下塔吉尔钢铁联合公司对该法进行了有益探索,但未见成功报道。攀钢在上世纪80年代以来开展了矿热炉熔炼含钒钢渣试验,取得了成功,但要完全打通流程,仍需做大量工作。二是将钢渣作为原料直接提钒,这一般需要经过湿法冶金的过程。传统的湿法提钒多为钠化焙烧的工艺,但该工艺污染重、回收率低,而且不适于钢渣提钒。科研工作者还对含钒钢渣不焙烧直接酸浸提钒和钠化焙烧-碳酸化浸出提钒工艺进行过研究,钠化焙烧-碳酸化浸出工艺打通了全流程,钒总回收率为55%~60%,但该工艺物耗量大、生产成本高,仅适用于品位较高的原料;钢渣不焙烧直接酸浸提钒工艺虽有浸出率高的优点,但耗酸量太大,成本过高,在探索试验之后没有进一步研究,该工艺尚未打通。再加上,钒、铁分离是钢渣提钒的关键,而不焙烧直接酸浸提钒,大量铁离子亦会与钒一起进入浸出液,造成浸出液难以净化,严重影响后续工艺。现有的净化除铁方法虽多,但这些方法主要是针对溶液,却忽视了从溶液中铁杂质产生的源头即浸出工序来除铁。如能浸出阶段实现钒、铁分离,则可在净化除杂等方面更具优势,其工艺应用前景广阔。
[0004] 还有研究致力于空白焙烧-碱浸、氧压浸出等以降低焙烧污染并提高转化率,但碱浸成本高、指标不理想,而氧压酸浸如何实现工业生产还有待进一步研究。近30多年还出现了一些新技术,如矿浆电解、微生物浸出、选择性析出等,其原理与方法都具有普遍适用性、部分已用于钢渣提钒的研究,但技术尚不成熟,多处于实验室研究阶段。
[0005] 对于含钒钢渣的选矿预处理,目前也无成熟的工艺。基于“含钒钢渣难以直接选矿分离”的观念,现有工艺往往首先就将“选矿技术”排除在外,殊不知提钒技术是一个大整体,很多意义不大的单元筹合起来整体意义就大了。况且,现今提钒成本高、能耗大,最主要的原因还是钒品位太低,若能够通过初步的选矿稍稍提高钢渣中的钒品位无疑具有重要的现实意义。
[0006] 总之,现行的提钒工艺方法虽多,但普遍存在污染重、回收率低等缺点,而且难以适应含钒钢渣的特点,推广应用受到限制。
发明内容