精轧机组设备及功能
精轧区设备

概述:精轧除鳞机:除鳞箱的上盖是用液压缸开闭,使除鳞喷咀维修容易。
入口夹送辊有将带钢从精轧内拖出的作用,出口夹送辊兼给切头剪提供切尾速度信号。
F1E 立辊轧机:为了进一步提高板宽精度,并使中间坯对中于轧制中心线,在F1轧机入口侧设置立辊轧机。
工作辊轴向窜动的HCW 轧机:轧机通过工作辊轴向窜动,加上强力液压弯辊,可以改变轧辊的凸度,从而保证板形质量并延长轧辊的使用寿命。
F1-F7 全部采用HCW 轧机。
F1-F7 全部采用全液压H—AGC。
F1-F7 全部采用强力液压弯辊。
F1-F7 设工艺润滑水。
F1-F7 之间采用带钢冷却(F1-F3 强冷)。
F1-F7 采用氧化铁皮抑制。
F1-F7 采用轧辊分段冷却。
F1-F7 采用水压除尘。
F1-F7 轧机间采用液压活套。
F1-F7 采用横移列车式的快速换工作辊。
3.1. 精轧除磷机(051112050)用途:用以清除板坯二次氧化铁皮,并对板坯测速。
型式:夹送辊式高压水除鳞箱。
结构特点:精轧除机箱体是由两片机架通过横梁连接而成。
正常工作时,用液压缸辊缝设定将带材送入精轧机中,当发生事故时,用液压缸将带材从轧机中拉出。
上辊有飞剪切尾速度检测功能。
高压水喷嘴纵向交错布置,使喷射区域相互补充,避免出现水痕。
控制及联锁要求:1. 所有辊子速度应与飞剪精轧立辊轧机速度相匹配.2. 前后夹送辊正常工作时,液压缸处于夹紧状态; 事故时,前夹送辊液压缸工作,后夹送辊液压缸打开.。
3. 后夹送辊上辊具有飞剪切尾测速功能.4. 前后夹送辊辊缝预先设定, 除鳞过程中不再动作.5. 带钢进入除鳞机前,喷嘴开始喷水,带钢出夹送辊之后,停止喷水。
6. 换集水管时,上盖缸驱动至上盖与水平成900 后,换集水管,维修完成后。
驱动缸回落。
集水管维修后,送入除鳞机体内。
3.2. F1E 立辊轧机(051112051)用途:将中间坯正确导入精轧机并对中间坯边部进行轧制。
型式:吸附型、上传动式(不可逆轧制)。
热轧带钢精轧机组主要辅助设备

首钢技师学院
热轧带钢精轧机组主要辅助设备
1、飞剪
功能:将进入精轧机的带坯的低温和形状不良的头尾端剪切掉,防止
穿带过程中卡钢和低温头尾在轧辊表面产生辊印。 类型:转鼓式飞剪和曲柄式飞剪两类。
飞剪
转鼓式飞剪
曲柄式飞剪
首钢技师学院
热轧带钢精轧机组主要辅助设备
转鼓式飞剪
结构:上下转鼓各装 1 或 2 个剪刃。
结构:为双曲柄式,上下曲柄各装一个剪刃。
优点:曲柄式飞剪的剪切机构属于四连杆结构,能够保证剪切过程中, 上下剪刃接近做平行运动,同时在剪切区剪切基本上是垂直轧件,剪切端
面的质量较好。
缺点:这种机构的剪股和摆杆做摆动, 动负荷冲击大。
首钢技师学院
热轧带钢精轧机组主要辅助设备
2、边部加热器
功能:将带坯的边部温度加热补偿至与中部温度接近一致。
带坯在轧制过程中,边部温降大于中部温降,温差大约为 100 0C 左右。 边部温降大,在带钢横断面上晶粒组织
不均匀,性能差异大;同时,还将造成
轧制中边部裂纹和对轧辊严重的不均匀 磨损。
带坯俯视
类型:火焰型边部加热器和电磁感应加热型边部加热器。
首钢技师学院
热轧带钢精轧机组主要辅助设备
电磁感应加热型边部加热器 类型:固定型、地面小车移动型和悬挂式移动型。 。 边部加热器加热带坯厚度范围为 20~6O mm,边部加热范围为 80~ 15O mm,一般在距边部 25mm 处增加温度 80 0C 左右。 需边部加热器加热的钢种主要有:冷轧深冲钢、硅钢、不锈钢、合金
钢等。
1-轮子 2-框架 3-轨道 4-电缆入口 5-电缆软管 6-接触式探测器 7-感应器 8-中心挡板 9-边部加热器支架
三、热轧带钢设备及控制07(CS FSB)

2、精轧机组(Finishing Mill)精轧机组位于粗轧机出口辊道或热卷箱后面,是热轧带钢生产的核心部分主要设备:边部加热器(SH)、切头剪(CS)、剪前辊道、剪前侧导板、精轧除鳞机(FSB)、精轧立辊机前辊道(FE)、精轧机,测厚、板形、测宽、测温仪表等。
精轧机组的布置:2.1 边部加热器位置:切头剪前。
作用:补偿中间坯边部温度,使其与中部温度一致。
边部与中部温差100℃,造成组织性能不均,轧辊边部磨损大。
升温:80~26080~260 ℃针对钢种:冷轧深冲钢、硅钢、不锈钢、合金钢分类:火焰型:带保温罩和煤气烧嘴。
电磁感应型:悬挂式移动型边部加热器结构2.2 切头剪位置:粗轧机后精除鳞机前。
作用:将温度低、形状不良的中间坯头部切除,便于轧件顺利通过精轧机、输出辊道进入卷取机,防止对钢和轧辊表面硌痕。
形式:转鼓式:结构简单,可分别安装不同形状的剪刃分别切头/尾。
mm 。
最大剪切厚度6060mm单侧传动式:双侧传动式:异步剪切式:剪切断面质量好,不连刀。
mm,只有一对剪刃。
曲柄式:剪刃垂直剪切,剪切厚度范围大,最大8080mm转鼓式曲柄式转鼓剪2.3 精轧除鳞机(FSB)位置:精轧机入口。
作用:去除中间坯表面的二次氧化铁皮。
为适应中间坯厚度变化,保证最佳除鳞效果,喷嘴喷射高度可调节。
精轧除鳞机结构2.4 精轧前立辊(F1E )位置:位于F1轧机前。
作用:进一步控制带钢宽度,提高宽度精度,改善边部质量。
侧压量:最大2020mm(mm(坯厚6060mm)mm) 轧制力:最大100吨功能;AWC精轧前立辊结构RALRALRAL。
精轧AGC功能说明

精轧AGC系统功能说明一、AGC系统概况由于带钢全长轧制中会遇到各种干扰,为了消除这些干扰的影响,减少带钢厚度公差,需设置精轧机组自动厚度控制系统,简称AGC系统,AGC系统是提高带钢全长厚度精度的主要手段。
AGC功能投入框图:二、AGC系统的功能GM-AG,即轧制力AGC即利用弹跳方程间接测量钢板厚度作为实测厚度进行反馈控制,这是AGC系统中基本的控制功能,根据GM-AG(中采用头部锁定值还是过程计算机设定值作为厚度基准可分为相对AGC( LK-AGC或绝对AGC(AB-AGC,一般以绝对AGC为主。
KFF-AGC即硬度前馈AGC即将上游机架的实测轧制力所获得的硬度变化信息用于后面各机架进行前馈控制。
MN-AGC即监控AGC由于弹跳方程的精度不高,因此需利用未机架后测厚仪信号对厚度的系统偏差进行纠正。
三、AGC算法GM-AGCL制力AGC其基本原理就是弹跳方程,其本质就是轧机产生单位弹跳量所需要的轧制力。
式中,h为轧机实际出口厚度;S。
为辊缝预设值;P为实际轧制力;M为轧机刚度;轧机刚度M在轧机牌坊制作安装完成以后就已经确定,是一个常值,无法修改,但是在实际的控制过程中,人们却希望轧机的刚度可变,比如为了消除轧辊偏心的影响,人们希望轧机的刚度尽可能的小,但为了消除来料厚度及材料温度变化的影响,又希望轧机刚度尽可能的大,因此产生了变刚度的控制方式。
假设预设辊缝值为S o,轧机的刚度系数为M来料厚度为H。
,此时轧制压力为P】,则实际轧出厚度h i应为:当来料厚度或温度因某种原因有变化时,在轧制过程中必然会引起轧制压力和轧出厚度的变化,如果压力由P i变为P2,则轧出厚度h2为:当轧制压力由P】变为P2时,则其轧出厚度的厚度偏差△ h正好等于压力差所引起的弹跳量为:为了消除此厚度偏差,可以通过调节液压缸的位置来补偿轧制力变化所引起的轧机弹跳变化量,此时液压缸所产生的轧辊位置修正量△ x,应与此弹跳变化量呈正比,方向相反,为:式中C为变刚度系数KFF-AGCi机架出口厚度变化量可用下式计算:h| = A Hi H汁 A Ki--K汁 A Si、SA“(X i)C QX 为'P :H i,或 C式中,为i i机架入口厚度变动(从静态角度可认为H i h i-1)「K为1 i机架厚度变动"Si为i机架辊缝调节量主要扰动为温度变动,我们曾对不同成品规格当FTO有20O C变动时各机架轧制温度以及其变形阻力(硬度)的变动作了计算,由计算结果可知,不能用::K K匚相等的法则来表示各机架、水间的关系,而应采用Ki=:匚、K i其中一:为0.95〜1.05 因此可利用上游机架的实测轧制力P*来求出K!设叶R*—? (p为设定值)—CQC Q然后即可求出K i= v'K i各机架前馈控制量(使6^ =0 ),为;卩一、S = J K iC其中B ki=如上一机架有残余出口偏差h i-1,则亦可用于水i田:K i、S j =C Chi的动作时间可以每一机架咬钢后「时刻投入,X为检测机架机架所实测到的突发量发生时间(相对于咬钢时间),由于精轧组秒流量相当,因此i 机架仍可用怡来判断突发量的到达,「为提前量决定于压下系统的响应速度。
三、热轧带钢设备及控制07(CS_FSB)

2、精轧机组(Finishing Mill)精轧机组位于粗轧机出口辊道或热卷箱后面,是热轧带钢生产的核心部分主要设备:边部加热器(SH)、切头剪(CS)、剪前辊道、剪前侧导板、精轧除鳞机(FSB)、精轧立辊机前辊道(FE)、精轧机,测厚、板形、测宽、测温仪表等。
精轧机组的布置:2.1 边部加热器位置:切头剪前。
作用:补偿中间坯边部温度,使其与中部温度一致。
边部与中部温差100℃,造成组织性能不均,轧辊边部磨损大。
升温:80~26080~260 ℃针对钢种:冷轧深冲钢、硅钢、不锈钢、合金钢分类:火焰型:带保温罩和煤气烧嘴。
电磁感应型:悬挂式移动型边部加热器结构2.2 切头剪位置:粗轧机后精除鳞机前。
作用:将温度低、形状不良的中间坯头部切除,便于轧件顺利通过精轧机、输出辊道进入卷取机,防止对钢和轧辊表面硌痕。
形式:转鼓式:结构简单,可分别安装不同形状的剪刃分别切头/尾。
mm 。
最大剪切厚度6060mm单侧传动式:双侧传动式:异步剪切式:剪切断面质量好,不连刀。
mm,只有一对剪刃。
曲柄式:剪刃垂直剪切,剪切厚度范围大,最大8080mm转鼓式曲柄式转鼓剪2.3 精轧除鳞机(FSB)位置:精轧机入口。
作用:去除中间坯表面的二次氧化铁皮。
为适应中间坯厚度变化,保证最佳除鳞效果,喷嘴喷射高度可调节。
精轧除鳞机结构2.4 精轧前立辊(F1E )位置:位于F1轧机前。
作用:进一步控制带钢宽度,提高宽度精度,改善边部质量。
侧压量:最大2020mm(mm(坯厚6060mm)mm) 轧制力:最大100吨功能;AWC精轧前立辊结构RALRALRAL。
精轧机工作原理
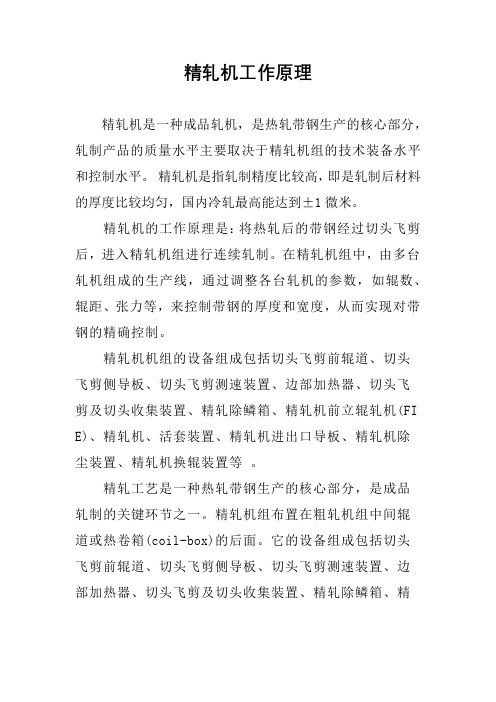
精轧机工作原理
精轧机是一种成品轧机,是热轧带钢生产的核心部分,轧制产品的质量水平主要取决于精轧机组的技术装备水平和控制水平。
精轧机是指轧制精度比较高,即是轧制后材料的厚度比较均匀,国内冷轧最高能达到±1微米。
精轧机的工作原理是:将热轧后的带钢经过切头飞剪后,进入精轧机组进行连续轧制。
在精轧机组中,由多台轧机组成的生产线,通过调整各台轧机的参数,如辊数、辊距、张力等,来控制带钢的厚度和宽度,从而实现对带钢的精确控制。
精轧机机组的设备组成包括切头飞剪前辊道、切头
飞剪侧导板、切头飞剪测速装置、边部加热器、切头飞
剪及切头收集装置、精轧除鳞箱、精轧机前立辊轧机(FI E)、精轧机、活套装置、精轧机进出口导板、精轧机除
尘装置、精轧机换辊装置等。
精轧工艺是一种热轧带钢生产的核心部分,是成品
轧制的关键环节之一。
精轧机组布置在粗轧机组中间辊
道或热卷箱(coil-box)的后面。
它的设备组成包括切头
飞剪前辊道、切头飞剪侧导板、切头飞剪测速装置、边
部加热器、切头飞剪及切头收集装置、精轧除鳞箱、精
轧机前立辊轧机(FIE)、精轧机、活套装置、精轧机进出口导板、精轧机除尘装置、精轧机换辊装置等。
精轧机说明书.(DOC)

高速线材精轧机组安装使用说明书制造单位:哈尔滨广旺机电设备制造有限公司设备图号: ZJF90d00使用客户:出厂日期:目录第一章、技术说明 (2)第二章、设备安装调整 (4)第三章、设备的使用维护与更换 (7)第四章、常见故障及排除 (13)第五章、附件 (14)精轧机组是高速线材车间的重要设备,为了保证精轧机组正常运转,用户须了解机组的性能、安装、运行与日常维护等基本常识。
本说明书就以上几个方面作了简单的介绍,用户在安装、使用机组前请先阅读本手册。
本说明书供武安文煜高线专用。
第一章技术说明一、设备用途本精轧机组为摩根五代顶交45°无扭重载高速线材精轧机组,图纸由国内设计转化完成。
本机组通过10机架连续微张力轧制,将上游轧机输送的轧件,轧制成φ5.5-φ20mm的成品线材。
二、设备主要性能参数1. 工艺参数:●来料规格:φ17—φ22mm●来料温度:>900℃●成品规格: φ5.5-φ20mm●主要钢种:碳钢、优质碳素钢、低合金钢、合金钢、焊条钢、冷镦钢等●第10架出口速度:≤95m/s(轧制φ6.5规格时)2. 设备参数:●机组组成:∅230轧机(5架)、∅170轧机(5架)、增速箱、大底座、挡水板与防水槽、缓冲箱、保护罩、联轴器、精轧机组配管等。
●机架数量: 10架(1-5架为∅230轧机,6-10架为∅170轧机同种规格的轧辊箱可以互换)●布置方式:顶交45°,10机架集中传动●辊环尺寸:∅230轧机:∅228.3/∅205×72mm∅170轧机:∅170.66/∅153×57.35/70mm ●传动电机: AC同步变频电机,功率: 5500kW●振动值:≤4.5 mm/s●噪音:≤80dB(距轧机1.5米处)●机组总速比(电机速度/装辊转速)见下表:●机组润滑方式:稀油集中润滑油压: 0.35MPa(点压力)总耗量:1200L/min油品: Mobil 525清洁度:10μ供油温度:38°C -42°C●保护罩液压系统:工作压力:15MPa系统流量:20 l/min●装辊工作压力:高压45 MPa -49.5MPa,低压22 MPa -25 MPa●卸辊工作压力:最大70MPa第二章设备安装调整一、安装调整顺序●将机组底座、增速箱、和主电机初步就位。
轧机机械设备介绍
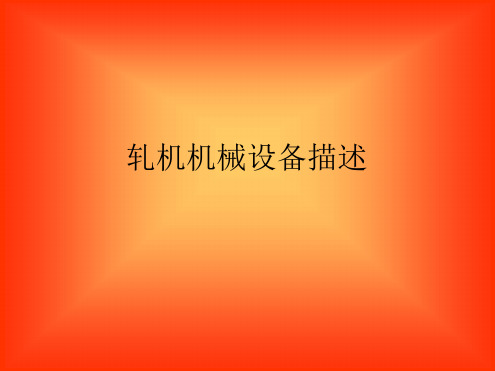
1.自动板型控制及超负荷保护 ,调整辊缝期望值 。
2. 实现板形、平坦度、凸度控制,生产出确定期望的带钢。
3.配合主传传动,产生不同的转速,以满足不同规格的轧制需要。
4. 工作辊更换装置可以实现快速换辊,以满足轧制节奏。
三、各部分功能原理:
底版及特殊件 :底板布置在轧机牌坊下面,用来支撑和对牌坊水平调 整的,并且通过T型螺栓与牌坊一起固定在基础上。
? 它是用来补偿上工作辊的磨损,保证AGC缸行程在一定的范围内调整, 阶梯垫板是通过液压缸移动的。
? 技术参数
? 阶梯垫推拉液压缸(带位置传感器) 数量:每机架 1 个
? ? 80 / 56 x 720 mm
? 最大横移速度: 100 mm/s
? 系统压力p = 29 Mpa(P=290bar,HP System)
楔板布置在底版和牌坊之间,在底板上对牌坊位置进行调整。
? 底版数量
每机架2件(每片牌坊1件)
? 楔板数量
每机架8件(每片牌坊4件)
? 材质:
? 底板
大型铸钢件
? 楔板
钢件
轧机牌坊
? 布置及功能:一个机架包括两片闭式牌坊,它们的底座和底板通过预紧 T形螺栓固定在基础上,牌坊通过上下横梁连接,牌坊的设计是用来 安装支撑辊和工作辊辊系及液压辊缝设定系统的。
? AGC油缸安装在上支承辊轴承座和轧机上阶梯垫之间。
? 作为轧机自动板型控制及超负荷保护,液压辊缝设定系统用来调整辊 逢期望值
? 技术参数
? 液压缸
数量:每机架 2个
? 液压缸外形尺寸
约 ? 1 050 / 970 x 120 mm
? (最佳工作行程:约7,5 – 55 mm)
f1f7精轧机组机械设备设备使用说明书

日钢1580F1-F7精轧机组机械设备
使用说明书
(包括功能、安装、操作、维护)
13272.302.00SM
13272.304.00SM
13272.305.00SM
13272.306.00SM
13272.307.00SM
(机械部分)
中国二重(德阳)重型装备责任有限公司
设计研究院
2006年3月25日
使用说明书13272.302.00SM 13272.304.00SM 13272.305.00SM 13272.306.00SM 13272.307.00SM
F1-F7精轧机组设
备
共88 页第7 页
1. 概述
F1-F7精轧区设备为1750mm热轧带钢工程的核心设备,位于热卷箱飞剪区之后、输出辊道和层流冷却区之前,包含精除鳞箱(13272.301.00)、F1-F7精轧机(13272.302.00)、精轧机(F1-F7)主传动装置(13272.303.00)、F1-F7机上配管(13272.307.00)、工作辊换辊小车(13272.305.00)、F1-F7快速换辊装置(13272.304.00)、F1-F7侧导板及导卫、活套装置(13272.306.00)。
其中主要设备F1-F7精轧机位于精除鳞箱后,可完成从中间坯料轧制到成品带钢的全轧制过程。
F1-F7精轧机由六台全液压压下、带串辊、正弯辊板型控制的四辊不可逆轧机(F1-F7)组成, 每两台轧机之间间距为5500mm,由于装有液压AGC装置、正弯辊及工作辊水平串辊等装置,提高成品钢带的厚度精度和板型精度。
精轧区设备功能说明书

河北永年永洋扁钢工程精轧区设备控制功能说明书室审:组审:审核:设计:天津市中重科技电气传动自动化工程有限公司2012年10月一、精轧机组1. 概述●对开坯机轧出的中间坯进行连续轧制,轧成满足要求的合格热态成品;●轧机形式:短应力线轧机。
2. 电气元件●平辊轧机电机7台●立辊轧机电机3台●电机编码器10个●水平辊压下绝对值编码器10个●轧机扁头定位接近开关10个●换辊缸接近开关30个●横移缸接近开关3个●换辊小车接近开关60个●换辊缸电磁阀11个●立辊压下液压马达电磁阀12个●水平辊压下液压马达电磁阀32个●插销液压缸电磁阀20个●机架锁紧缸电磁阀20个●机架油流接近开关11个●减速机油流变送器11个●电机定转子温度检测仪表10个●●●3. 功能说明轧机传动●H1,H3,H4,H6,H7,H9轧机电机为1000kW,V2,V5,H10轧机电机为733kW,V8-1轧机电机为733kW,用于轧制大规格成品。
V8-2轧机电机为200KW,用于轧制小规格成品;所有轧机的电压等级为DC660V。
●传动形式:采用SIMOREG DC MASTER 6RA70 系列全数字调速系统;(其中1H,3H,H7,8V1,8V2为新控制柜,其余轧机控制柜为利旧装置。
)●网络形式:区域光纤以太网配以局部DP通讯。
辊缝调整●水平辊压下装置用来调整水平辊辊缝,其压下方式采用液压马达传动,绝对值编码器检测位置并在机旁操作箱数字显示仪表进行显示,轧机机身配有刻度盘方便人工观察;换辊●通过液压换辊缸和换辊小车实现换辊;●扁头定位:轧机自动以点动速度旋转至定位接近开关处停止,可以提高换辊速度;●在轧制状态时,机架锁紧液压缸前进,所有插销缸插紧,机架锁紧继电器有信号并且插销缸接近开关有信号时,表示机架已锁紧,插销缸到位,可以轧制。
4.联锁●对应机架锁紧,插销缸到位,润滑液压无故障,对应轧机已送电且无故障时,轧机才能启动。
(注意内控/外控)●轧机启动过程中,若机架锁紧信号消失或者润滑出现故障时,轧机将延时停止。
高线精轧机知识

高线精轧机知识一、高线精轧机概述高线精轧机是一种用于轧制金属线材的设备,广泛应用于钢铁、有色金属等行业。
其主要作用是通过连续轧制和塑性变形,将粗线材逐步压制成细线材,并达到一定的尺寸精度和表面质量要求。
高线精轧机通常由多个轧机组成,每个轧机都具有一对辊子,通过转动辊子来完成轧制过程。
二、高线精轧机的工作原理高线精轧机的工作原理是通过辊子的转动和线材的通过,使得线材在辊子之间受到挤压和塑性变形,从而达到减小线材直径和提高线材表面质量的目的。
整个过程中,线材在不同轧机之间经过多次轧制,逐渐减小直径,直至达到目标尺寸。
三、高线精轧机的主要部件1. 轧机辊子:是高线精轧机的核心部件,承担着线材的挤压和塑性变形任务。
辊子通常由优质的合金钢制成,具有高强度和耐磨性能。
辊子的表面经过精细抛光和硬化处理,以确保线材的表面质量。
2. 传动系统:用于驱动辊子的转动。
传动系统通常采用电机和减速器的组合,通过齿轮传动或皮带传动将动力传递给辊子。
3. 卷取系统:用于将轧制好的线材卷取起来。
卷取系统通常由卷取机构和张力控制系统组成,能够保证线材卷取的紧密度和稳定性。
4. 控制系统:用于对高线精轧机进行全面的控制和监测。
控制系统通常包括电气控制系统和液压控制系统,能够实现轧机的启停、速度调节、张力控制等功能,并对轧制过程进行实时监测和数据记录。
四、高线精轧机的应用领域高线精轧机广泛应用于钢铁、有色金属等行业。
在钢铁行业中,高线精轧机主要用于生产各种钢丝、钢绞线、钢绞线等产品。
在有色金属行业中,高线精轧机主要用于生产铝线、铜线等产品。
这些产品在建筑、交通、电力、通信等领域中都有广泛的应用。
五、高线精轧机的优势和发展趋势1. 高线精轧机能够实现线材直径的精确控制,提供高精度的线材产品,满足不同行业的需求。
2. 高线精轧机具有高效率和高自动化程度,能够实现连续生产和自动化控制,提高生产效率和产品质量。
3. 高线精轧机具有较小的占地面积和能耗,能够节约生产成本,提高经济效益。
精轧通用功能描述
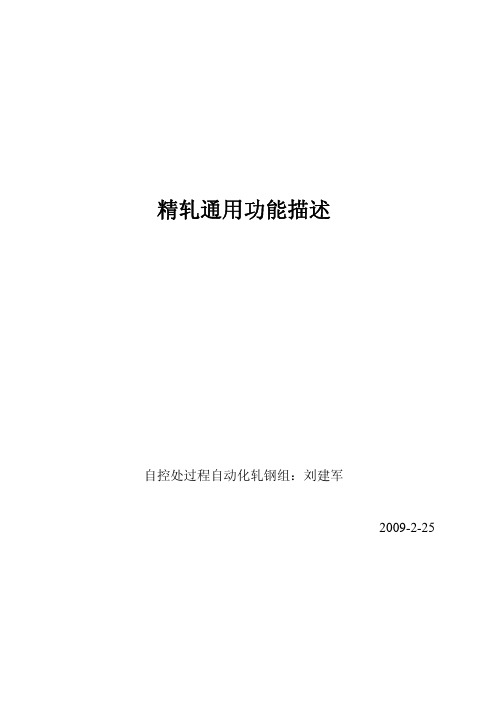
精轧通用功能描述自控处过程自动化轧钢组:刘建军2009-2-251、SDH(Setup Data Handling)SDH的功能就是从L2接收设定值报文,并将这些数据以适当的时刻、适当的带钢分配给不同的LFU。
SDH从L2接收整块轧材的轧制表,这是MTR(material tracking)的功能。
这里包括实际轧材ID和下一块轧材ID。
这些轧制表的数据存储在各个LFU自含的叫做“模块4”的设定数据分配子功能块里。
“模块4”提供所有LFU 有效的设定值输出。
SDH主要是跟L2、开环控制功能块、闭环控制功能块、传动有通讯接口。
SDH还通过读取通讯功能块的状态及错误位来监控所有的通讯接口,以避免产生错误的信息。
以下是SDH通讯接口原理图:一级SDH接收由L2来的数据是MTR所需要的实际带钢和下一块带钢的数据及带钢轧程数据。
由开/闭环控制功能块和传动发送给SDH的数据是相对于轧材ID的各LFU 的特定设定值。
由SDH发送给各开/闭环控制功能块和传动的数据是给各LFU的设定值(包括轧制表、再计算及设定值的再分配)。
数据根据位置、事件或以周期形式分配给各个需要数据的LFU。
2、ADP(Actual Data Preprocessing)ADP在现场仪表和过程自动化系统之间起联络功能。
ADP预处理是基本自动化和过程自动化之间的接口,基础自动化提供周期性的测量值,并根据过程自动化系统的需要将这些测量值传送给过程自动化。
ADP预处理的一个重要任务是周期性的压缩从测量装置收到的测量值,以减少容量,以便在将这些测量值发送给过程自动化时避免过载。
3、MTR(Material Tracking)精轧区域的MTR是从热卷箱到精轧出口区域。
MTR功能连接着所有MTR 所需要的传感器、摄像头、速度及位置传感器等。
有一个公差窗口用于增强轧制信号的可靠性,在特殊情况下,这些公差可以根据实际的轧制状况动态地增加或缩小。
物料跟踪位于轧制区域的单块物料,并在轧线产生一个本物料用于顺控(此LFE为LCO)的映像。
热轧1450精轧机设备组成及原理简介

精除鳞箱
• 1、组成:前后夹送辊、除鳞辊道、除鳞箱本体 • 2、采用前后夹送辊作用: • (1)、前后夹送辊与集水罩等形成密封箱体,防 止高压水和氧化铁皮飞剪;出口侧夹送辊可将带钢 表面水挤掉。 • (2)、压平带钢翘头 • (3)、事故时夹紧反转拉出带钢 • (4)、下夹送辊电机带编码器,控制辊子转速, 使飞剪、夹送辊、F1精轧机同步 • 3、喷嘴通过热金属检测器检测信号经过延时开始 喷射。
• (1)、组成:入口侧轨座、出口侧轨座、操作侧牌坊、传 动侧牌坊、上下横梁、支承辊锁紧装置(用液压缸带动锁紧 挡板对支承辊装置轴向锁紧,操作侧4个,一侧靠紧牌坊衬 板另一侧靠锁紧挡板)。
• (2)、点检:主要检查锁紧螺栓的紧固情况、液压缸工 作情况以及牌坊内侧滑板开口度尺寸(一般测量周期为1 个月,单侧滑板尺寸磨损超过0.5~1.5mm,需更换。)
• (1)、工作辊锁紧缸 • 防止工作辊轴向窜动,锁紧时轴承座耳座一端抵在移动座上,一端靠锁紧 挡板锁紧。窜辊时:锁紧缸及连接缸通过锁紧挡板将轴承座与移动座连接 为一体,操作侧窜辊缸带动移动座及工作辊一起实现窜辊。 • (2)、工作辊弯辊缸 • 轧制时中部轧制力大于两端轧制力,容易产生 • 为防止板形出现这种状况,加入弯辊机构,再两端加个反向的力补偿轧制 力的不同使板形平整。
精轧机入口侧导板 • 7、入口侧导板
• 位于每台轧机的入口处,在导位支架上,由液压缸进行开 口度调整及沿导位支架运动。用于轧件的导入和轧制中心 线的对中。
精轧机标高调整装置 • 8、标高调整装置
• 此装置位于轧机前,主要调整侧导板标高,包括7个导位 支架及标高调整,标高调整主要通过偏心套转动来实现, 传动形式为:电机通过减速机、联轴器、同步轴带动偏心 套转动。
精轧机说明书资料
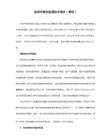
3 布置方式: 顶交45°,10机架集中传动 辊环尺寸: 230轧机: 228.3/205×72mm 170轧机:170.66/153×57.35/70mm 传动电机: AC同步变频电机,功率: 5500kW 振动值: ≤4.5 mm/s 噪音: ≤80dB(距轧机1.5米处) 机组总速比(电机速度/装辊转速)见下表: 机架号 总速比 No1 230轧机 1.1162049 No2 230轧机 0.9007968 No3 230轧机 0.7258774 No4 230轧机 0.5856341 No5 230轧机 0.4774616 No6 170轧机 0.2889899 No7 170轧机 0.227809 No8 170轧机 0.1838458 No9 170轧机 0.1466313 No10 170轧机 0.118334 机组润滑方式: 稀油集中润滑 油压: 0.35MPa(点压力) 总耗量:1200L/min 油品: Mobil 525 清洁度:10
9 箱的锥齿轮轴和惰轴后部的螺栓力矩;如果任何一个环节出现差异,则应调整到合格范围之内,所有工作做好后将所有辊箱一一对应合入锥箱。机组通油40分钟以上进行润滑冲洗,之后空载运转20分钟后方可升速过钢。在85m/s~90m/s速度时间段结束后要重点进行以下工作:在线检测辊箱轧辊轴的轴向和径向间隙,检测双唇密封圈的密封状况;在线检测锥箱纵轴两端轴承座的振动情况;在线检测增速箱输出轴的振动情况;检查润滑油的精度等级不超过7级。确认各处均在合格范围之内后方可升速。升速后严格监控设备各关键部位的温升和振动值,不能超过合格范围。 附:机组的测振位置图10#锥箱8#锥箱6#锥箱4#锥箱2#锥箱1#锥箱3#锥箱5#锥箱7#锥箱9#锥箱增速箱23456789101112131415161718192021222324251
f1-f7

(15)工作辊稍微向前以使勾头抬起脱离轴承座,如不能抬起,采用人工处理方法。
(16)工作辊换辊小车完全退出横移列车,信号给出。此步必须确认换辊小车退出横移列车,否则会联ห้องสมุดไป่ตู้横移平台动作。
到此时,假如要进行支撑辊更换,可以在这一步停止工作辊换辊程序,转到支撑辊更换程序,当换完支承撑辊后,假如要把旧工作辊推回机架,这种情况从第22步开始;假如换新辊,继续即可。
入口导卫
位置和作用:在机架前引导轧件,F1—F7上、下全部采用气缸驱动式摆动机构,摆入时擦辊器贴靠在工作辊上,摆出时让出换辊辊道。入口侧工作辊冷却水管固定在其上,工作辊冷却水装有调节阀,可以按工艺要求调节或开闭工作辊冷却水。
F1—F7入口侧还设有工艺润滑,下入口导位上还设有侧导板喷水孔道。
出口导卫
假如是推旧辊,必须人工抬起勾头,推新辊时为了防止勾头不能自动打起,也可以人工抬起。
(25)工作辊换辊小车回到磨辊间,信号给出。
(26)工作辊提升轨道放下到位。
(27)工作辊平衡切换到高压。
(28)上工作辊和上支承辊放下60mm.
(29)梯形止推块到1位。
(30)上工作辊和上支撑辊放下105mm。
1).切换梯形垫块到支撑辊更换位。
2).支撑辊换辊推拉杆前进到机架(C形勾必须先打起),到达后,再用C形钩卡住推拉杆头。
3).下支撑辊锁紧块打开,人工确认到位。
支撑辊换辊装置
安装位置和功能:支撑辊更换装置安装在操作侧,且位于工作辊换辊装置下面。当工作辊侧移平台吊开后,就可看到支撑辊换辊用的更换架,更换架装在导轨上作为支撑辊更换的拖架,上支撑辊是通过一板凳压在下支撑辊轴承座上。支撑辊从机架上抽出和推入都是通过液压缸动作来实现的,该液压缸是安装在工作辊换滚缸基础之下,固定再支撑辊换辊拖架上。
精轧机组设备及功能
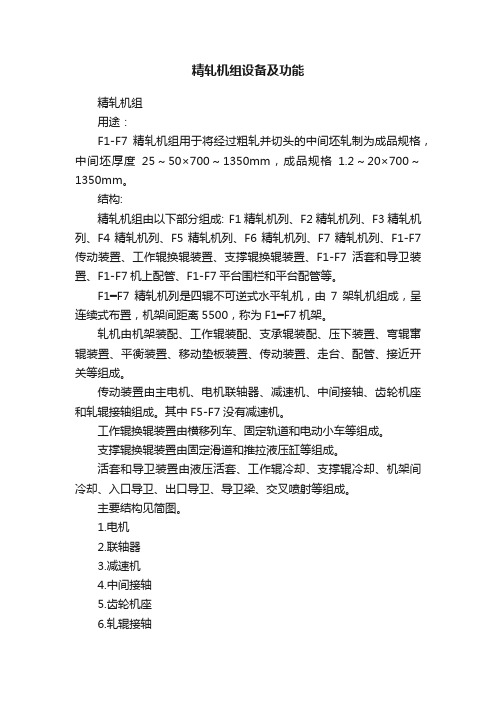
精轧机组设备及功能精轧机组用途:F1-F7精轧机组用于将经过粗轧并切头的中间坯轧制为成品规格,中间坯厚度25~50×700~1350mm,成品规格1.2~20×700~1350mm。
结构:精轧机组由以下部分组成: F1精轧机列、F2精轧机列、F3精轧机列、F4精轧机列、F5精轧机列、F6精轧机列、F7精轧机列、F1-F7传动装置、工作辊换辊装置、支撑辊换辊装置、F1-F7活套和导卫装置、F1-F7机上配管、F1-F7平台围栏和平台配管等。
F1━F7精轧机列是四辊不可逆式水平轧机,由7架轧机组成,呈连续式布置,机架间距离5500,称为F1━F7机架。
轧机由机架装配、工作辊装配、支承辊装配、压下装置、弯辊窜辊装置、平衡装置、移动垫板装置、传动装置、走台、配管、接近开关等组成。
传动装置由主电机、电机联轴器、减速机、中间接轴、齿轮机座和轧辊接轴组成。
其中F5-F7没有减速机。
工作辊换辊装置由横移列车、固定轨道和电动小车等组成。
支撑辊换辊装置由固定滑道和推拉液压缸等组成。
活套和导卫装置由液压活套、工作辊冷却、支撑辊冷却、机架间冷却、入口导卫、出口导卫、导卫梁、交叉喷射等组成。
主要结构见简图。
1.电机2.联轴器3.减速机4.中间接轴5.齿轮机座6.轧辊接轴7.精轧机本体三、主要技术参数四辊精轧机主要技术参数表轧机名称 F1 F2 F3 F4 F5 F6 F7最小工作辊直径mm 720 720 720 720 540 540 540最大工作辊直径mm 800 800 800 800 600 600 600工作辊辊身长度mm 1700 1700 1700 1700 1700 1700 1700最小支撑辊直径mm 1250 1250 1250 1250 1250 1250 1250最大支撑辊直径mm 1350 1350 1350 1350 1350 1350 1350支撑辊辊身长度mm 1500 1500 1500 1500 1500 1500 1500最大轧制力t 3500 3500 3500 3500 3000 3000 3000最大轧制力矩t*m 177.6 149.7 100 47.8 36.7 29.8 27.5最大弯辊力/单侧t 150 150 150 150 120 120 120轧机线速度(最大辊径时)基速(m/s) 1.26 1.632 2.4 3.49 4.71 6.28 8.01最高速(m/s) 3.15 4.236 6.336 9.22 12.44 15.39 18.54轧机线速度(最小辊径时)基速(m/s) 1.134 1.476 2.16 3.14 4.24 5.652 7.21 最高速(m/s) 2.835 3.804 5.7 8.29 11.2 13.85 16.68推荐减速机速比 4.65 3.92 2.62 1.8主电机DC/AC AC AC AC AC AC AC AC功率kW 6000 6000 6000 6000 6000 6000 6000基速r/min 125 150 150 150 150 200 255最高速r/min 350 400 400 400 400 490 5901、设备结构及功能上部支撑辊平衡装置位置和作用:上支撑辊的平衡装置安装在牌坊连接梁的顶部。
F1-F7精轧机组机械设备设备使用说明书

F1-F7精轧机组机械设备设备使用说明书
使用说明书
(包括功能、安装、操作、维护)
13272.302.00SM
13272.304.00SM
13272.305.00SM
13272.306.00SM
13272.307.00SM
(机械部分)
中国二重(德阳)重型装备责任有限公司
设计研究院
2006年3月25日
使用说明书13272.302.00SM 13272.304.00SM 13272.305.00SM 13272.306.00SM 13272.307.00SM
F1-F7精轧机组设
备
共88 页第7 页
1. 概述
F1-F7精轧区设备为1750mm热轧带钢工程的核心设备,位于热卷箱飞剪区之后、输出辊道和层流冷却区之前,包含精除鳞箱(13272.301.00)、F1-F7精轧机(13272.302.00)、精轧机(F1-F7)主传动装置(13272.303.00)、F1-F7机上配管(13272.307.00)、工作辊换辊小车(13272.305.00)、F1-F7快速换辊装置(13272.304.00)、F1-F7侧导板及导卫、活套装置(13272.306.00)。
其中主要设备F1-F7精轧机位于精除鳞箱后,可完成从中间坯料轧制到成品带钢的全轧制过程。
F1-F7精轧机由六台全液压压下、带串辊、正弯辊板型控制的四辊不可逆轧机(F1-F7)组成, 每两台轧机之间间距为5500mm,由于装有液压AGC装置、正弯辊及工作辊水平串辊等装置,提高成品钢带的厚度精度和板型精度。
轧机机组主要设备及功能

轧机机组主要设备及功能装置布置在轧机入口,偏转钢带和调节钢带位置。
其辊子相对垂直方向有小纠偏辊角度倾斜,辊子表面覆橡胶以提高摩擦力,降低噪音,平滑、稳定调节钢带中心张紧辊穿带卷扬焊缝检测仪可为轧机提供高的后张力,可快速响应帮助钢带穿过轧机入口检测焊点处的小孔,自动控制轧机降速或变规格该装置为上切式液压剪,布置在轧机入口纠偏辊后,由螺旋尺调节剪刃间隙,入口液压剪在换支撑辊、断带及其他情况下剪切带三辊张紧装稳定轧机入口钢带置侧导向装置在穿带时为钢带对中轧机机架轧制钢板斜楔调整机利用斜楔板和阶梯板调节轧制线高度,使之处于恒定的高度,不受轧辊直径构变化的影响。
每个上下中间辊驱动侧轴承座带窜动钩,中间辊窜动由液压缸驱动进行轴向窜动获得最佳孔型。
可单辊窜动或上下辊同时窜动,窜动速度根据轧制速度和轧制力确装置定。
平衡块内的液压缸平衡上支撑辊,窜动块内的液压缸可和轧辊一起窜动,对轧辊弯辊和中间辊起平衡和弯辊作用。
工作辊弯辊缸推动轴承座对工作辊进行正负弯平衡系统辊,这种设计通过比例阀进行平衡和弯辊的切换,正负弯辊的过渡可进行快速响应厚度控制,高可靠性、寿命长和维修周期长,可根据轧辊辊径变化全行程调节,无需选择轧辊辊径,液压缸安装在牌坊窗口底部,阀台压上系统和力马达阀安装在液压缸上,两个液压缸提供轧制力,并可手动控制,全自动控制压下装置,同步控制以确保两侧平行运动,力马达阀安装在液压缸上以减少厚度控制的响应时间。
轧制力测量用来检测单边轧制力系统用于支撑工作辊传动接轴,安装在驱动侧牌坊上,换辊时,托架支撑上下接接轴托架轴轧机侧部位,使其处在水平换辊位,也就是将接轴端部支撑在水平位置,以便平稳地换辊,其中上接轴由液压缸穿带导板将钢带头部导入工作辊,防止断带时产生的瓢曲和碎带损伤乳化液喷嘴防缠导板保护轧辊不受断带造成的损坏,换辊时,由气缸在导向辊上将其抽出。
摆动式穿带保证轧机之间的稳定穿带,该导板仅在穿带时升起,正常轧制时由气缸降至导板最低位防溅装避免轧辊之间带钢宽度方向之外的乳化液外泄和溅落在钢板上空气吹扫装用于吹扫测厚仪、测速仪处钢带的乳化液置轧机清洗装热水或清洁剂冲洗轧机内部,通过清洗有效地减少轧辊在产品上的印迹,降置低工作量和工作时间。
精轧机工作原理
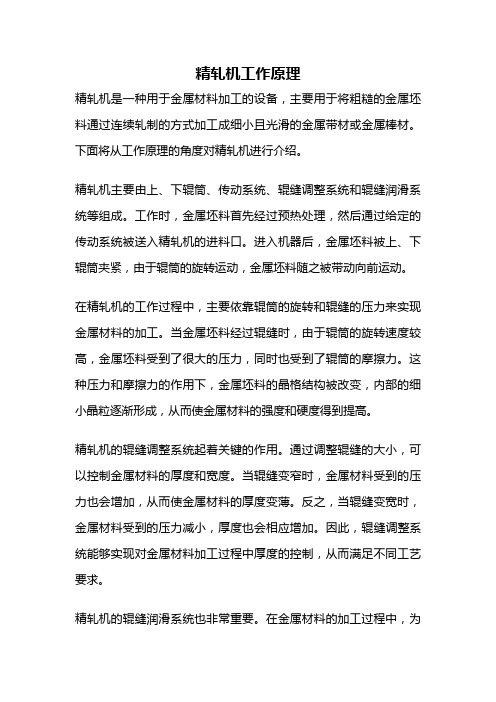
精轧机工作原理精轧机是一种用于金属材料加工的设备,主要用于将粗糙的金属坯料通过连续轧制的方式加工成细小且光滑的金属带材或金属棒材。
下面将从工作原理的角度对精轧机进行介绍。
精轧机主要由上、下辊筒、传动系统、辊缝调整系统和辊缝润滑系统等组成。
工作时,金属坯料首先经过预热处理,然后通过给定的传动系统被送入精轧机的进料口。
进入机器后,金属坯料被上、下辊筒夹紧,由于辊筒的旋转运动,金属坯料随之被带动向前运动。
在精轧机的工作过程中,主要依靠辊筒的旋转和辊缝的压力来实现金属材料的加工。
当金属坯料经过辊缝时,由于辊筒的旋转速度较高,金属坯料受到了很大的压力,同时也受到了辊筒的摩擦力。
这种压力和摩擦力的作用下,金属坯料的晶格结构被改变,内部的细小晶粒逐渐形成,从而使金属材料的强度和硬度得到提高。
精轧机的辊缝调整系统起着关键的作用。
通过调整辊缝的大小,可以控制金属材料的厚度和宽度。
当辊缝变窄时,金属材料受到的压力也会增加,从而使金属材料的厚度变薄。
反之,当辊缝变宽时,金属材料受到的压力减小,厚度也会相应增加。
因此,辊缝调整系统能够实现对金属材料加工过程中厚度的控制,从而满足不同工艺要求。
精轧机的辊缝润滑系统也非常重要。
在金属材料的加工过程中,为了减小辊筒与金属材料之间的摩擦力,增加金属材料的延展性,必须保证辊缝处有足够的润滑剂。
润滑剂能够形成一层薄膜,减小辊筒与金属材料之间的接触面积,从而减小摩擦力。
同时,润滑剂还能起到冷却作用,防止金属材料因为摩擦而过热。
精轧机是一种通过连续轧制来加工金属材料的设备。
它主要依靠辊筒的旋转和辊缝的压力来实现金属材料的加工,通过辊缝调整系统和辊缝润滑系统的配合,能够实现对金属材料厚度和宽度的控制。
精轧机的工作原理简单明了,但在实际应用中,还需要根据具体的金属材料和工艺要求进行参数的调整和控制,以确保加工质量的稳定性和一致性。
- 1、下载文档前请自行甄别文档内容的完整性,平台不提供额外的编辑、内容补充、找答案等附加服务。
- 2、"仅部分预览"的文档,不可在线预览部分如存在完整性等问题,可反馈申请退款(可完整预览的文档不适用该条件!)。
- 3、如文档侵犯您的权益,请联系客服反馈,我们会尽快为您处理(人工客服工作时间:9:00-18:30)。
位置及作用:交叉喷射集管固定在F2—F7机架的前部,用以喷射抑制氧化铁皮和其它扬尘用水。
出口吹扫
位置和作用:出口吹扫包括设在F7后的蒸气侧喷和吹风装置,用以吹净水蒸气和粉尘,保证F7后测厚仪、测温仪、凸度仪和板形仪的正常工作。
工作辊的换辊装置
安装位置和功能:在精轧机操作侧安装换辊装置,此装置带有侧移平台和换辊缸;侧移平台是对每架轧机两套工作辊来设计的,当更换支撑辊时,侧移平台可以用横车移开。工作辊可通过轧辊更换缸来抽出或推入轧机。
三、主要技术参数
四辊精轧机主要技术参数表
轧机名称 F1 F2 F3 F4 F5 F6 F7
最小工作辊直径 mm 720 720 720 720 540 540 540
最大工作辊直径 mm 800 800 800 800 600 600 600
工作辊辊身长度 mm 1700 1700 1700 1700 1700 1700 1700
最小支撑辊直径 mm 1250 1250 1250 1250 1250 1250 1250
最大支撑辊直径 mm 1350 1350 1350 1350 1350 1350 1350
支撑辊辊身长度 mm 1500 1500 1500 1500 1500 1500 1500
最大轧制力 t 3500 3500 3500 3500 3000 3000 3000
DC/AC AC AC AC AC AC AC AC
功率 kW 6000 6000 6000 6000 6000 6000 6000
基速 r/min 125 150 150 150 150 200 255
最高速 r/min 350 400 400 400 400 490 590
因此操作模式可以分为如下三个阶段:
—不供应水(轧机因更换轧辊而停止)
—越为最大水量的20℅来供水(轧制间隙时)
—选择最大量供水(轧钢状态)
机架间冷却
位置和作用: 在轧机之间装有一个循环水集管,并且用来防止在薄板的表面形成氧化铁皮。此外,在轧制过程中用来冷却机架间的带钢。因此带钢的温度可以得到控制。每个冷却区域装有一个气动控制阀,从而使在整个工作过程中可以不断地对水量进行调节。机架间底步对头部进行导向的横梁采用内部水冷却。活套辊也采用内部水冷却。这两个采用同一个水冷系统,每个机架有一个阀来控制水的开关。
平衡力应比静平衡装置重量高20——30﹪,平衡液压缸是单杆液压缸,通过活塞杆侧的液压箱供给流体,然后通过活塞杆侧的孔流进活塞。因为这样在活塞底部区域的工作压力大。
闭和回路的控制信息由一个位置传感器和一个压力传感器来完成。在位置控制过程中支撑辊须降低,确切的位置由辊径和移动垫板是否使用来决定。提升和平衡的程序由压力控制来完成。
活套装置
位置和作用:安装在每两个机架之间,用于支撑带钢,形成调节轧机动态速度变化的套量,维持机架间带钢的张力,参与精轧机组的调速控制。
4.位移传感器
1) 用于移动垫板换位(共7台)
位移传感器置于液压缸尾部,用于控制阶梯垫板的位置。每机架都装配有移动垫板装置,其安装于机架窗口与辊缝调节液压缸(AGC缸)之间。由一个液压缸驱动,操作侧和传动侧机械组合。驱动移动垫板的液压缸装配有位置测量系统,其安装在液压缸里,目的是为确保移动垫板达到准确位置。
出口侧导板
位置和作用:导板安装在每个机架的出口侧,用来将轧出的带钢送出机架。
工作辊冷却
位置和作用:冷却水通过喷射头喷在精轧机工作辊上,用于过钢时轧辊的冷却和润滑。冷却的最主要目的是保持轧辊在轧钢过程中的温度基本保持不变,在停机时水量减少,停机时水量的参考值越为最大流量的20℅,这一数值调试时设定好并在试运转中来设定。
数量: 4个/每架,共16个.
5)用于F5-F7工作辊轴向窜动(共12台)
位移传感器置于液压缸内部,用于控制窜辊缸的位置。每个工作辊2个,每架轧机共4个。工作辊轴向窜动量±100 mm。
工作辊换辊装置由横移列车、固定轨道和电动小车等组成。
支撑辊换辊装置由固定滑道和推拉液压缸等组成。
活套和导卫装置由液压活套、工作辊冷却、支撑辊冷却、机架间冷却、入口导卫、出口导卫、导卫梁、交叉喷射等组成。
主要结构见简图。
1.电机 2.联轴器 3.减速机 4.中间接轴 5.齿轮机座 6.轧辊接轴 7.精轧机本体
支撑辊换辊装置
安装位置和功能:支撑辊更换装置安装在操作侧,且位于工作辊换辊装置下面。当工作辊侧移平台吊开后,就可看到支撑辊换辊用的更换架,更换架装在导轨上作为支撑辊更换的拖架,上支撑辊是通过一板凳压在下支撑辊轴承座上。支撑辊从机架上抽出和推入都是通过液压缸动作来实现的,该液压缸是安装在工作辊换滚缸基础之下,固定再支撑辊换辊拖架上。
位置和作用:在机后从上下方向引导轧件防止轧件上翘和钻钢,F—F7相同,它们都支撑在一个导位架上,上导位用气缸拉起擦辊器贴靠在上工作辊上,下导卫板自重使擦辊器贴靠在下工作辊上,出口侧工作辊冷却水管固定在其上,工作辊冷却水装有调节阀,可以按工艺要求调节或开闭工作辊冷却水。
入口侧导板
位置和作用:导板安装在机架入口侧的轧制线上下部位,用于将进来的带钢导入辊缝中。
最大轧制力矩 t*m 177.6 149.7 100 47.8 36.7 29.8 27.5
最大弯辊力/单侧 t 150 150 150 150 120 120 120
轧机线速度
(最大辊径时) 基速(m/s) 1.26 1.632 2.4 3.49 4.71 6.28 8.01
最高速(m/s) 3.15 4.236 6.336 9.22 12.44 15.39 18.54
数量: 2个/每架,共14个.
3)用于上支撑辊平衡装置(共7台)
平衡支撑辊的液压缸安装于上横梁的中间,由液压缸活塞杆上的滑动轴承支撑,横梁,连接杆和平衡杆形成了上支撑辊的悬吊结构。
支撑辊平衡系统用来平衡支撑辊,对辊缝无作用力,上支撑辊装置,辊缝调节液压缸,移动垫板装置和支撑辊的平衡系统须紧靠轧机机架轭。
带有传动轴夹持的工作辊弯辊和窜辊
位置和作用:固定式的弯辊缸安装在机架窗口内的两侧表面,弯辊缸座用于安装弯辊缸,工作侧有工作辊锁紧装置,传动侧有主轴夹持装置。其作用是轴向移动工作辊,对工作辊进行正弯辊,控制带钢的板形。
支撑辊轴承座和部件
位置和作用:支撑辊轴承座将由辊缝设定系统施加的力传送到支撑辊上,支撑辊装在支撑辊轴承座上的油膜轴承中。支撑轴承座位于传动和操作侧的机架窗口内。操作侧的轧辊轴承座在液压推动的固定板来进行轴向定位。上下支撑辊轴承座在操作侧有一个推力轴承。
油膜轴承
位置和作用:油膜轴承用于安装支撑辊。油膜轴承是最合适的承受产生在机架间的高轧制力的轴承。锥套安装在轧辊颈部,衬套安装在轧辊轴承座上。轴承面对辊身一侧带有特殊的密封系统。
支撑辊
位置和作用:支撑辊安装在两侧的轴承箱内的油膜轴承中。支撑辊支撑着工作辊并且传递轧制力。
轧机的轧制线调整和支撑辊更换台架
轧机线速度
(最小辊径时) 基速(m/s) 1.134 1.476 2.16 3.14 4.24 5.652 7.21
最高速(m/s) 2.835 3.804 5.7 8.29 11.2 13.85 16.68
推荐减速机速比 4.65 3.92 2.62 1.8
主电机
液压辊缝设定系统
位置和作用:液压辊缝设定缸安装在上支撑辊轴承座和上部机架连接架之间。液压辊缝设定系统用来调整预期的辊缝,并用作最终的自动厚度控制元件和过载保护。
轧机机架上的提升轨道
位置和固定在轧机机架上,滑动导轨用螺栓拧紧在提升轨道上,轨道在液压缸的推动下在牌坊窗口中安全的进行升降动作。提升导轨在液压推动下做垂直调整,用来将工作辊提升到轧辊换辊位置。
F1━F7精轧机列是四辊不可逆式水平轧机,由7架轧机组成,呈连续式布置,机架间距离5500,称为F1━F7机架。
轧机由机架装配、工作辊装配、支承辊装配、压下装置、弯辊窜辊装置、平衡装置、移动垫板装置、传动装置、走台、配管、接近开关等组成。
传动装置由主电机、电机联轴器、减速机、中间接轴、齿轮机座和轧辊接轴组成。其中F5-F7没有减速机。
1、设备结构及功能
上部支撑辊平衡装置
位置和作用:上支撑辊的平衡装置安装在牌坊连接梁的顶部。液压缸的活塞杆通过轨梁与两个导轨连接,他们分别分布在轧机机架的入口和出口侧,上支撑辊轴承座用挂钩连接在轨道上。
垫块缩回装置
位置和作用:安装在各个机架顶部和液压压下缸之间。它用来补偿上工作辊磨削后的偏差,将压下缸的行程保持在特定的范围内,垫块有液压缸拖动。
其位置精确度为±2mm。
为能将垫板块拉出或推进一个新位置,支撑辊平衡系统在此之前必须下降约15——20mm,在换辊时,垫板块的转换由一个自动程序来完成。新的位置选定后,使用按钮或键盘开始自动程序,在地面操作点操作面板上,使用点动或手动模式也可对垫板块的位置进行调整。
每架轧机1个,阶梯垫板有4个工作位置,每2个位置之间的距离为210mm,前3个位置垫板厚度分别90 mm \45 mm \0 mm,第4个位置为换辊位置。
入口导卫
位置和作用:在机架前引导轧件,F1—F7上、下全部采用气缸驱动式摆动机构,摆入时擦辊器贴靠在工作辊上,摆出时让出换辊辊道。入口侧工作辊冷却水管固定在其上,工作辊冷却水装有调节阀,可以按工艺要求调节或开闭工作辊冷却水。
F1—F7入口侧还设有工艺润滑,下入口导位上还设有侧导板喷水孔道。
出口导卫
对支撑辊的更换,没有自动程序,在这种情况下须通过手动的操作方式,
按相关的按钮来完成,上支撑辊的提升由压力控制来完成,设定值是一个约130bar的恒定值。地面操作点的显示器用来监控上支撑辊的移动。更换支撑辊时,移动垫板块须移到4位置,滑块锁住HGC缸,才能降低支撑辊。