精轧机说明书
精轧机轧钢工技术操作规程

精轧机轧钢工技术操作规程
轧制过程中的标准化操作
1换完辊环过第一支钢后,在集卷前或挂钩后,要迅速取样,检查成品尺寸,如果尺寸有问题,要尽快通知精轧机处的轧钢工适量调整轧机。
2 当成品高度尺寸符合要求,宽度偏小时,要放大第一架辊缝;反之,宽度偏大时,缩小第一架辊缝;成品宽度合格,高度偏小时,适量放大成品辊缝;成品宽度合格,高度偏大时,适量缩小成品辊缝;
3 要调整精轧机在用的第一架轧件尺寸,必须提前和主控台操作工取得联系,在下根钢进入精轧前,计划放大多少或减少多少要说明。
4不得随意调整在用的第二架到成品前架之间轧机。
5轧制稳定后,尺寸和表面质量逐盘检查并作好记录。
6 精轧机内发生堆钢事故时,冷却水自动关闭后方可开盖。
7精轧机在轧钢状态禁止调整轧机。
需要调整时,要联系主控台放慢些出钢节奏,在两根钢的间隔时间内调整。
8注意精轧前活套的运行状态,有异常通知主控台。
5停车检查的标准化操作
1轧机停止和冷却水关闭后,再开启保护罩。
2检查滚动导卫的导辊和导板状态,有问题就更换备用的导卫。
新换的导卫必须重新对中。
3检查滚动导卫的油气管和水管,有破损的要更换或处理。
4赤手接触辊环,温度偏高的要检查水管出水孔是否有异物堵塞。
5检查辊环冷却水管有无松动和偏离轧槽问题,有问题要处理。
6检查辊环有无涨裂或掉块问题,有问题通知班长。
7用手电照各架导卫内有无残留的铁皮。
8检查其他进出口导卫有无掉下和松动问题,然后重新安装紧固。
9下水口有氧化铁皮或刮钢,要清理干净。
精轧AGC功能说明

精轧AGC系统功能说明一、AGC系统概况由于带钢全长轧制中会遇到各种干扰,为了消除这些干扰的影响,减少带钢厚度公差,需设置精轧机组自动厚度控制系统,简称AGC系统,AGC系统是提高带钢全长厚度精度的主要手段。
AGC功能投入框图:二、AGC系统的功能GM-AGC,即轧制力AGC,即利用弹跳方程间接测量钢板厚度作为实测厚度进行反馈控制,这是AGC系统中基本的控制功能,根据GM-AGC中采用头部锁定值还是过程计算机设定值作为厚度基准可分为相对AGC(LK-AGC)或绝对AGC (AB-AGC),一般以绝对AGC为主。
KFF-AGC,即硬度前馈AGC,即将上游机架的实测轧制力所获得的硬度变化信息用于后面各机架进行前馈控制。
MN-AGC,即监控AGC,由于弹跳方程的精度不高,因此需利用未机架后测厚仪信号对厚度的系统偏差进行纠正。
三、 AGC算法GM-AGC轧制力AGC其基本原理就是弹跳方程,其本质就是轧机产生单位弹跳量所需要的轧制力。
北京北科麦思科自动化工程技术有限公司电话:(010) 89715559北京北科麦思科自动化工程技术有限公司 电话:(010) 89715559式中,h为轧机实际出口厚度;S 0为辊缝预设值; P 为实际轧制力; M 为轧机刚度;轧机刚度M 在轧机牌坊制作安装完成以后就已经确定,是一个常值,无法修改,但是在实际的控制过程中,人们却希望轧机的刚度可变,比如为了消除轧辊偏心的影响,人们希望轧机的刚度尽可能的小,但为了消除来料厚度及材料温度变化的影响,又希望轧机刚度尽可能的大,因此产生了变刚度的控制方式。
假设预设辊缝值为S 0,轧机的刚度系数为M ,来料厚度为H 0,此时轧制压力为P 1,则实际轧出厚度h 1应为:当来料厚度或温度因某种原因有变化时,在轧制过程中必然会引起轧制压力和轧出厚度的变化,如果压力由P 1变为P 2,则轧出厚度h 2为:当轧制压力由P 1变为P 2时,则其轧出厚度的厚度偏差Δh 正好等于压力差所引起的弹跳量为:为了消除此厚度偏差,可以通过调节液压缸的位置来补偿轧制力变化所引起的轧机弹跳变化量,此时液压缸所产生的轧辊位置修正量Δx ,应与此弹跳变化量呈正比,方向相反,为:式中C 为变刚度系数。
【机械制造行业】精轧机组机械设备设备使用说明书
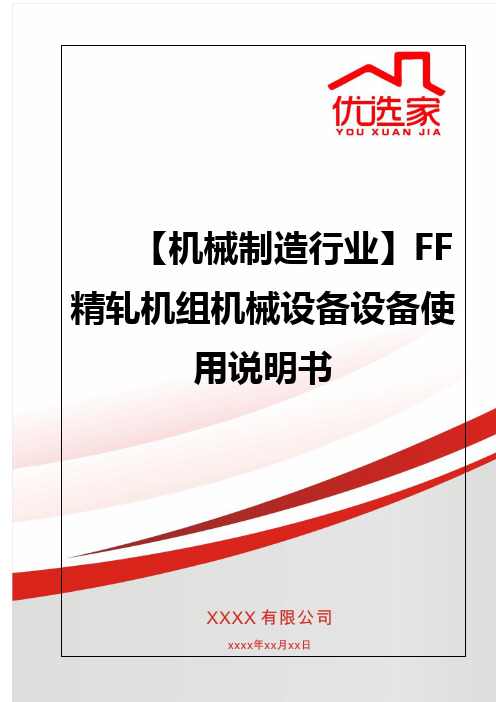
7.4.4.接近开关65
7.4.5.设备的试运转65
7.5.工作辊换辊小车66
7.6.平台和配管67
8.设备的操作使用68
8.1.轧制带钢68
8.2.设备停车70
8.3.精轧机开口度调整70
8.4.精轧机上支承辊垫板的调整71
8.5.精轧机轧制标高调整72
8.5.1.换工作辊后的标高调整72
6.4.冷却系统51
6.4.1.机前工作辊冷却水51
6.4.2.防轧辊剥落及活套冷却水51
6.4.3.F1-F7机架间带钢冷却及侧喷水51
7.设备的安装、调整和试运转52
7.1.F1-F7精轧机54
7.1.1.安装基本要求55
7.1.2.工作辊、支承辊装配和安装56
7.1.3.设备调试及要求57
7.1.4.试轧58
5.3.3.接近开关31
5.3.4.工作辊的更换32
5.4.F1-F7支承辊换辊装置37
5.4.1.支承辊的更换38
5.5.工作辊换辊小车42
5.6.活套43
6.液压、润滑、气动和冷却系统44
6.1.液压系统44
6.2.润滑系统46
6.2.1.自动干油润滑46
6.2.2.人工干油润滑46
6.3.气动系统50
5.2.1.入口侧导板27
5.2.2.出口导卫27
5.2.3.导卫支架和标高调整装置28
5.2.4.工作辊冷却装置28
5.2.5.机架间冷却装置29
5.2.6.保护罩和侧喷装置29
5.2.7.活套29
5.2.8.检测装置29
5.3.F1-F7工作辊换辊装置31
5.3.1.横移装置31
1500宽带精轧机产品安装调试使用说明书

支承辊轴承座随平衡装置的横梁一起沿机架窗口内侧滑板上、下滑板。 支承辊轴承的轴向定位由装在机架操作侧牌坊上的四个轴端卡板实 现,这些轴端卡板由四个液压缸驱动。 支承辊的更换为液压缸拉出式,依靠专门的支承辊换辊机实现,换 上支承辊时用换辊支架将其支承在下支承辊轴承座上,一起由换辊机拉 出或送入。 移动垫板装置 移动垫板由移动平面框架、阶梯垫板、固定滑道等组成,由液压缸 驱动。主要用于换辊时平衡缸的快速抬起及补偿辊径变化时对压下AGC 缸行程的影响。 每机架都装配有移动垫板装置,其安装于机架窗与辊缝调节液压缸 (HGC缸)之间。由一个液压缸驱动,操作侧和传动侧机械组合。驱动 止推块的液压缸装配有位置测量系统,其安装在液压缸里,目的是为确 保止推块达到准确位置。 因为辊缝调节液压缸有一限定的行程,使用止推块的目的是较小的 调节液压缸行程而获得较大的辊缝范围,其调节范围是10——65mm。这 样就能补偿各种不同的工作辊辊径带来的影响。 因为新的辊径对止推块装置的计算是必要的,在换辊时,计算的可 能范围由计算机来完成当止推块运行到各种不同的位置时,校准是必要 的。校准以后才能将新的止推块推进,当调整同样的止推块时,不需要 校准,同样适应工作辊检测时的拉出与推进,止推块的位置改变。止推 块有四种位置可选: 1位置:止推块厚度:90mm 工作液压缸行程:630mm 2位置:止推块厚度:45mm 工作液压缸行程:420 3位置:止推块厚度:0mm 工作液压缸行程:210mm 4位置:当更换支撑辊时,滑块锁住HGC缸 工作液压缸行程:0mm
N=6000kW 125/320/min AC N=6000kW 125/330/min AC N=6000kW 125/330(345)/min AC N=6000kW 100/265/min AC N=6000kW 130/345/min AC N=6000kW 160/400/min AC 主传动速比: i1 =4.65 i2 =3.92 i3 =2.62 i4 =1 i5 =1 i6 =1 压下装置: F1~F6 液压AGC 轧辊轴串装置: F1~F6 液压 轧辊弯辊装置: F1~F6 液压 测压仪: F1~F3 测压力 17500kN F4~F6 测压力 15000kN 压下速度: 3mm/s 轧辊开口度: max60mm 液压AGC缸(每架): F1-F6: 2×φ965/φ890×115mm 工作压力25/6MPa 支承辊平衡缸(每架): F1-F6: φ380/φ360×290mm 工作压力16MPa 工作辊弯辊缸(每架): F1-F3: 4×φ170/φ150×95mm F4-F6: 4×φ170/
精轧机说明书.(DOC)

高速线材精轧机组安装使用说明书制造单位:哈尔滨广旺机电设备制造有限公司设备图号: ZJF90d00使用客户:出厂日期:目录第一章、技术说明 (2)第二章、设备安装调整 (4)第三章、设备的使用维护与更换 (7)第四章、常见故障及排除 (13)第五章、附件 (14)精轧机组是高速线材车间的重要设备,为了保证精轧机组正常运转,用户须了解机组的性能、安装、运行与日常维护等基本常识。
本说明书就以上几个方面作了简单的介绍,用户在安装、使用机组前请先阅读本手册。
本说明书供武安文煜高线专用。
第一章技术说明一、设备用途本精轧机组为摩根五代顶交45°无扭重载高速线材精轧机组,图纸由国内设计转化完成。
本机组通过10机架连续微张力轧制,将上游轧机输送的轧件,轧制成φ5.5-φ20mm的成品线材。
二、设备主要性能参数1. 工艺参数:●来料规格:φ17—φ22mm●来料温度:>900℃●成品规格: φ5.5-φ20mm●主要钢种:碳钢、优质碳素钢、低合金钢、合金钢、焊条钢、冷镦钢等●第10架出口速度:≤95m/s(轧制φ6.5规格时)2. 设备参数:●机组组成:∅230轧机(5架)、∅170轧机(5架)、增速箱、大底座、挡水板与防水槽、缓冲箱、保护罩、联轴器、精轧机组配管等。
●机架数量: 10架(1-5架为∅230轧机,6-10架为∅170轧机同种规格的轧辊箱可以互换)●布置方式:顶交45°,10机架集中传动●辊环尺寸:∅230轧机:∅228.3/∅205×72mm∅170轧机:∅170.66/∅153×57.35/70mm ●传动电机: AC同步变频电机,功率: 5500kW●振动值:≤4.5 mm/s●噪音:≤80dB(距轧机1.5米处)●机组总速比(电机速度/装辊转速)见下表:●机组润滑方式:稀油集中润滑油压: 0.35MPa(点压力)总耗量:1200L/min油品: Mobil 525清洁度:10μ供油温度:38°C -42°C●保护罩液压系统:工作压力:15MPa系统流量:20 l/min●装辊工作压力:高压45 MPa -49.5MPa,低压22 MPa -25 MPa●卸辊工作压力:最大70MPa第二章设备安装调整一、安装调整顺序●将机组底座、增速箱、和主电机初步就位。
精轧机组维护使用说明书--新版

精轧机组维护使用说明书哈飞工业机电设备制造公司目录第一章预精轧机区设备 (3)第二章3#飞剪、2#卡断剪、碎断剪、侧活套 (4)第三章精轧机组 (6)第四章增速箱 (11)第五章夹送辊 (11)第六章吐丝机及其相关设备 (13)第七章机组装配与试车 (15)第八章精轧机组的分解与重装 (22)第九章设备日常维护 (59)第十章设备大修 (61)第十一章易损件和备件清单 (76)前言无扭精轧机组是高速线材车间的重要设备,机组中使用了高精度、高转速的圆柱斜齿轮、锥齿轮、油膜轴承和滚动轴承,各零件的加工精度、动平衡精度以及安装精度的要求都很高,因此,了解精轧机组及其相关设备的性能、结构、安装、使用与日常维护等是保证轧机正常运转的重要环节。
第一章预精轧机区设备1.1悬臂式预精轧机组位置:位于13V轧机出口处。
轧机号为:14H、15V、16H、17V。
作用:通过4机架无扭无张力连续轧制,将坯料轧制成满足精轧机组要求的的尺寸及精度。
结构:机组由4架∅285轧机组成,平立交替布置,机架间设有立式活套。
轧机为悬臂辊环式结构,其特点如下:①轧机为轧辊箱插入式机构。
机架由轧辊箱和齿轮箱组成,轧辊箱插入齿轮箱即构成轧机机架。
②轧辊箱箱体带有一法兰面板用来与齿轮箱连接,箱体内装有偏心套机构用来调整辊缝。
偏心套内装有摩根系列油膜轴承与轧辊轴,在悬臂的轧辊轴端用锥套固定辊环。
水平机架与立式机架共用一种轧辊箱,可以互换。
③水平机架的齿轮箱内由输入轴和同步轴共两根带有齿轮的传动轴组成,机架可由一标准减速器调整速比。
④立式机架的齿轮箱内的传动系统比水平机架多了一对螺旋伞齿轮,用来改变传动方向和调整速比,其余部分与水平机架相同;平立轧机齿轮均采用SKF滚动轴承。
⑤辊缝的调节是旋转一根带左、右丝扣和螺母的丝杆,使两组偏心套相对旋转,两轧辊轴的间距随偏心套的偏心相对轧线对称移动而改变辊缝,并保持原有轧线及导卫的位置不变。
⑥辊环通过锥套连接在悬臂的轧辊轴上,用专用的换辊工具更换辊环。
F1-F7精轧机组机械设备设备使用说明书

F1-F7精轧机组机械设备设备使用说明书
使用说明书
(包括功能、安装、操作、维护)
13272.302.00SM
13272.304.00SM
13272.305.00SM
13272.306.00SM
13272.307.00SM
(机械部分)
中国二重(德阳)重型装备责任有限公司
设计研究院
2006年3月25日
使用说明书13272.302.00SM 13272.304.00SM 13272.305.00SM 13272.306.00SM 13272.307.00SM
F1-F7精轧机组设
备
共88 页第7 页
1. 概述
F1-F7精轧区设备为1750mm热轧带钢工程的核心设备,位于热卷箱飞剪区之后、输出辊道和层流冷却区之前,包含精除鳞箱(13272.301.00)、F1-F7精轧机(13272.302.00)、精轧机(F1-F7)主传动装置(13272.303.00)、F1-F7机上配管(13272.307.00)、工作辊换辊小车(13272.305.00)、F1-F7快速换辊装置(13272.304.00)、F1-F7侧导板及导卫、活套装置(13272.306.00)。
其中主要设备F1-F7精轧机位于精除鳞箱后,可完成从中间坯料轧制到成品带钢的全轧制过程。
F1-F7精轧机由六台全液压压下、带串辊、正弯辊板型控制的四辊不可逆轧机(F1-F7)组成, 每两台轧机之间间距为5500mm,由于装有液压AGC装置、正弯辊及工作辊水平串辊等装置,提高成品钢带的厚度精度和板型精度。
13269.302-309.00-精轧机组说明书说明书

福建三钢集团有限责任公司中板轧钢工程3000四辊精轧机区安装使用说明书13269.302.0013269.303.0013269.304.0013269.305.0013269.306.0013269.307.0013269.308.0013269.309.00(机械部分)中国第二重型机械集团公司设计研究院2006年03月25日目录1.概述 (3)2.机器用途 (4)3.精轧机区域组成及相关设备 (5)4.规格及性能 (6)5.机列及轧机设备装配图 (8)6.精轧机前后工作辊道 (8)6.1工作原理 (8)6.2 控制联锁 (9)6.3润滑方式 (9)6.4机器的安装、调试和试运行 (9)6.5机器的维护与安全 (10)6.6主要配套件及电气元件清单 (11)7.精轧机前后推床 (12)7.1工作原理 (12)7.2 结构说明 (13)7.3控制联锁 (14)7.4液压润滑 (16)7.5 使用要求 (16)7.6主要配套件及电气元件清单 (17)8.3000四辊可逆精轧机 (18)8.1工作原理 (18)8.2 四辊精轧机组成 (19)8.3 结构说明 (20)8.4 液压缸规格及工作状态 (27)8.5 联锁要求 (30)8.6 滚动轴承目录 (32)8.7电气设备清单 (33)8.8安装的基本步序 (36)8.9 安装基本要求 (36)8.10使用要求 (37)9.机架辊及其更换 (41)9.1用途 (41)9.2 技术规格 (41)9.3 结构说明 (42)9.4主要配套件及电气元件清单 (43)10.换辊装置 (44)10.1用途 (44)10.2 技术规格 (44)10.3原理及结构说明 (45)10.4工作辊换辊步骤 (46)10.5支承辊换辊步骤 (53)10.6工作辊换辊装置的安装及维护 (59)10.7支承辊换辊装置的安装及维护 (60)10.8主要配套件 (60)11.主传动装置 (63)11.1用途 (63)11.2 技术特性 (63)11.3 结构概述 (65)11.4 螺栓预紧 (66)11.5 润滑 (66)11.6 安装与调整 (67)11.7 试运转 (68)11.8 维护与安全 (68)11.9 主要配套件 (69)2.机器用途福建三钢3000四辊精轧机区设备是福建三钢集团有限责任公司中板轧钢工程的核心设备,包括四辊精轧机、机前后回转工作辊道、机前后推床、换辊装置、主传动等。
- 1、下载文档前请自行甄别文档内容的完整性,平台不提供额外的编辑、内容补充、找答案等附加服务。
- 2、"仅部分预览"的文档,不可在线预览部分如存在完整性等问题,可反馈申请退款(可完整预览的文档不适用该条件!)。
- 3、如文档侵犯您的权益,请联系客服反馈,我们会尽快为您处理(人工客服工作时间:9:00-18:30)。
高速线材精轧机组安装使用说明书制造单位:哈尔滨广旺机电设备制造有限公司设备图号: ZJF90d00使用客户:出厂日期:目录第一章、技术说明 (2)第二章、设备安装调整 (4)第三章、设备的使用维护与更换 (7)第四章、常见故障及排除 (13)第五章、附件 (14)精轧机组是高速线材车间的重要设备,为了保证精轧机组正常运转,用户须了解机组的性能、安装、运行与日常维护等基本常识。
本说明书就以上几个方面作了简单的介绍,用户在安装、使用机组前请先阅读本手册。
本说明书供武安文煜高线专用。
第一章技术说明一、设备用途本精轧机组为摩根五代顶交45°无扭重载高速线材精轧机组,图纸由国内设计转化完成。
本机组通过10机架连续微张力轧制,将上游轧机输送的轧件,轧制成φ5.5-φ20mm的成品线材。
二、设备主要性能参数1. 工艺参数:●来料规格:φ17—φ22mm●来料温度:>900℃●成品规格: φ5.5-φ20mm●主要钢种:碳钢、优质碳素钢、低合金钢、合金钢、焊条钢、冷镦钢等●第10架出口速度:≤95m/s(轧制φ6.5规格时)2. 设备参数:●机组组成:∅230轧机(5架)、∅170轧机(5架)、增速箱、大底座、挡水板与防水槽、缓冲箱、保护罩、联轴器、精轧机组配管等。
●机架数量: 10架(1-5架为∅230轧机,6-10架为∅170轧机同种规格的轧辊箱可以互换)●布置方式:顶交45°,10机架集中传动●辊环尺寸:∅230轧机:∅228.3/∅205×72mm∅170轧机:∅170.66/∅153×57.35/70mm ●传动电机: AC同步变频电机,功率: 5500kW●振动值:≤4.5 mm/s●噪音:≤80dB(距轧机1.5米处)●机组总速比(电机速度/装辊转速)见下表:●机组润滑方式:稀油集中润滑油压: 0.35MPa(点压力)总耗量:1200L/min油品: Mobil 525清洁度:10μ供油温度:38°C -42°C●保护罩液压系统:工作压力:15MPa系统流量:20 l/min●装辊工作压力:高压45 MPa -49.5MPa,低压22 MPa -25 MPa●卸辊工作压力:最大70MPa第二章设备安装调整一、安装调整顺序●将机组底座、增速箱、和主电机初步就位。
●生产线从头至尾拉一根轧制中心线,线上系两个吊锤和一些红布条(警示作用)。
●按图一和图二调整机组底座,使机组底座的轧制中心和设计轧制中心线重合,机组底座的22个测量点的高度差不大于0.03mm。
●将10个机架装配到机组底座之前,必须用油石将接触面进行研磨去毛刺,同时安装好各锥箱的主进油管路(出厂前10个机架的相对位置关系已经调整好,注意各个调整垫片的位置必须和出厂前的记录保持一致),将10个机架装配到机组底座上,接触面间隙要求不大于0.02mm,复检各个机架间的同轴度。
●按图三和图四调整好增速箱,图三中的B值取0.3mm即可。
●调整主电机,使主电机的输出轴中心在水平方向与增速箱输入轴的中心重合,在高低上比增速箱输入轴的中心高0.3mm。
●连接好各个接手。
●连接好各进油回油管路,装好分水块,连接好各进水管。
●安装好各联轴器的供油管和回油管及联轴器保护罩。
●装好挡水板与防水槽、缓冲箱。
●安装弦线信号检测器。
●安装机组保护罩及保护罩液压缸等附件。
至此,精轧机组调整安装完毕。
二、安装要求●机架间的联轴器两轴倾斜应小于1/1500;机架两个纵轴的任意位置的同轴度应小于φ0.05mm。
●机组整体轧制中心线的偏差应小于φ0.775mm。
(图一)轧制方向(图二)增速箱中心距(图三)(图四)第三章设备的使用、维护与更换一、使用合理科学地使用设备,有利于提高设备的利用率,延长设备的使用寿命。
首次轧钢前的准备工作。
机组在生产现场经冷试车验收合格后,将进入轧钢阶段,由于此前辊环和导位均未安装,因此需做相应准备工作。
1、打开机组保护罩至极限位置,插入限位销;2、拆去辊箱的保护帽;3、拆去辊箱的外滑环,取出隔环,重新装好外滑环;4、按要求装入锥套和辊环;5、重新装好辊箱的保护帽;6、装好导位,接好油气润滑;7、调整辊缝;8、将弦线检测器接好;9、点动试辊;10、试喷水;11、拔出机组保护罩限位销,合上机组保护罩;12、通水、通油(在进行以上操作时,润滑油可一直供给);13、检查各个润滑节点的供油压力;14、转车。
轧钢过程的速度提升。
对于新安装的生产线来讲,从热过钢开始,到出口速度达95m/s(这里指的出口速度是指轧制规格为φ6.5,第10架精轧机的出口速度),需经过以下的速度时间过程:1、速度75~84m/s的轧制时间为60个工作日。
这个速度时间段特别重要,它既是设备的磨合期,也是操作人员对设备的熟悉摸索阶段。
设备通过这段时间的运转,零部件机加和装配时的残余内应力可以完全释放出来,达到最终状态;齿轮等转动零件经过这段时间的负荷运转磨合,可以消除前期零件加工时的一些表面缺陷,增加接触区域,提高运转的稳定性;设备的前期安装,部件或零件间存在部分连接虚应力,通过一段时间的运转振动,可以消除这部分虚应力;操作人员经过这段时间的操作摸索,对每个零部件都有了一定的认识和熟悉,也为下阶段的提速打好心理和技术上的基础;本阶段的速度提升梯度小于2m/s。
2、速度85~90m/s的轧制时间为20个工作日。
这个速度时间段是设备的恢复稳定阶段,同时也是对设备加工精度的校验阶段。
也就是说,通过这个时间段,就完全可以看出整体设备的加工制造精度,判断出设备是否具有提速的潜质和可能。
本阶段的速度提升梯度小于2 m/s。
3、速度91~95m/s 的轧制时间约为20个工作日。
这个时间段不是特别固定,只要在一个速度上稳定正常轧制,各种参数检测正常,就可以提至更高速度轧制,但要注意,速度的提升梯度为1m/s。
设备在每个速度时间段除了做日常的维护检查工作外,在准备提速时,针对每个时间段还另有不同的检查侧重点。
在75m/s~84m/s速度时间段结束后要重点进行以下工作:将辊箱全部从锥箱中抽出,检查辊箱的各个重要参数(如轴的侧隙和轴向间隙等),重新校核各个螺栓的紧固力矩,检查齿面的磨损啮合区域;检查锥箱与机组底座的连接状况,重新拧紧各个螺栓,重新校核锥箱锥箱的锥齿轮轴和惰轴后部的螺栓力矩;如果任何一个环节出现差异,则应调整到合格范围之内,所有工作做好后将所有辊箱一一对应合入锥箱。
机组通油40分钟以上进行润滑冲洗,之后空载运转20分钟后方可升速过钢。
在85m/s ~90m/s 速度时间段结束后要重点进行以下工作:在线检测辊箱轧辊轴的轴向和径向间隙,检测双唇密封圈的密封状况;在线检测锥箱纵轴两端轴承座的振动情况;在线检测增速箱输出轴的振动情况;检查润滑油的精度等级不超过7级。
确认各处均在合格范围之内后方可升速。
升速后严格监控设备各关键部位的温升和振动值,不能超过合格范围。
附:机组的测振位置图10#锥箱8#锥箱6#锥箱4#锥箱2#锥箱1#锥箱3#锥箱5#锥箱7#锥箱9#锥箱增速箱23456789101112131415161718192021222324251X:沿轧制线方向Y:如图所示Z:如图所示二、维护日常维护是保证轧机正常连续运转的重要一环,维护项目和维护周期见下表:辊箱维护:辊箱在工作时直接接触轧件,它是精轧机组中最容易损坏的部件,因此对辊箱的特别要细心。
1、定期更换双唇密封圈、抛油环。
双唇密封圈的正常使用周期为7个工作日左右,密封圈和抛油环工作状况不好会直接影响到辊箱的漏水和漏油,加速油膜轴承的磨损,影响轧机的使用寿命,甚至烧损辊箱。
平时严密监控轧机的进水情况,尽量做到提前预防,勤更换双唇密封圈,发现抛油环有划痕,应立即更换。
2、在线定期检测轧辊轴的参数。
在线检测轧辊轴的径向和轴向间隙,可以作为是否将辊箱拆下到精装间进行大修的唯一因素。
每个辊轴的轴向和径向间隙都有一个合格范围值,在辊箱装配结束后这个固定的数值就已经形成。
当辊箱投入运行后,每周要在线检测辊轴的轴向和径向间隙,把此数值和装配后的数值进行比较,如果轴向间隙差不小于0.03毫米,或径向间隙差不小于0.05毫米时,辊箱应立即拆下进行彻底检查修复。
这里应注意,在线检测以上数据时应该拆去辊环和锥套。
3、定期检查辊箱的磁性丝堵。
每月都要打开辊箱的磁性丝堵,检查其表面的污渍状况。
丝堵表面只允许有轻微的污渍存在,如果其表面有大量磨粒或脏物存在,则说明有些零件被磨损,造成润滑系统污染,或润滑系统本身过滤有问题,此时润滑系统应采取进一步净化手段。
4、定期分解辊箱检查。
辊箱在投入运转一定时间后,虽然在线检测轴向和径向间隙仍然在合格范围内,但也要拆下进行彻底分解检查,做到事故提前预防。
转速最高的两架椭圆孔型的轧辊箱,从投入运行并连续轧制150个工作日,应将其拆下进行彻底分解检查;其它椭圆孔型辊箱的检查时间是六个月一次;圆孔型辊箱的检查时间是七到八个月一次;检查的重点是油膜轴承、齿轮、轴表面、阻尼垫片,调整螺母、调整丝杠。
每次拆卸,油膜轴承和阻尼垫片都应进行更换,其它零件如果仅仅是轻微磨损,则可以重新装配使用,如果零件磨损严重(指所有零件),则更换相应零件后重新装配使用。
锥箱、增速箱的维护:锥箱和增速箱不直接接触轧件,损坏的机率相对较低,除设备振动和噪音异常时进行检查,每年设备大修时检查外,其他时间不必要进行单独维护。
锥箱下线后重点的维护项目为,检查各处螺栓力矩,检查啮合齿轮的着色和侧隙及齿面磨损状况,检查各轴的径向和轴向间隙,更换阻尼垫片和油膜轴承,检查各滚动轴承的磨损状况,检查各润滑管路的连接状况。
增速箱下线后重点维护项目为,检查齿轮的着色和侧隙,检查各轴的径向和轴向间隙,检查滚动轴承的磨损状况,检查阻尼垫片的压痕(如压痕明显,则须更换),检查各润滑管路的连接状况。
三、更换由于设备需要离线维修和维护,因而涉及到在线设备的更换问题。
下面简述辊箱、锥箱、增速箱的更换过程。
辊箱。
辊箱的拆除,将进水管拆去,将其和锥箱的连接螺栓拆下,用顶丝将辊箱顶起,用天车将其吊下;辊箱的安装,安装时以辊箱和锥箱间的定位销为基准,将辊箱落入锥箱后(注意,合箱前将设备结合面清洗干净,用油石除去高点,在锥箱的结合面均匀涂一层平面厌氧密封胶—可赛新515或乐泰515),将各个连接螺栓拧紧,将进水管连接号。
锥箱。
锥箱的拆除,拆去其两端的联轴器保护罩,拆去其两端联轴器的连接螺栓,拆去进油回油管路,将箱体和管路进油口缝好,拔出其与机组底座的定位销,用天车将锥箱轻轻扶住,拆去锥箱与机组底座间的螺栓,用天车将其吊下(注意保管号锥箱与机组底座间的调整垫片);锥箱的安装,将结合面处清洗干净,用油石除去高点,将调整垫片放到机组底座上,将锥箱吊到机组底座上,接好锥箱主进油管路,拧紧锥箱与机组底座的连接螺栓,打表调整其与两相邻锥箱的同轴度,通过增减调整垫片使锥箱间的同轴度在合格范围内,重新铰锥箱与机组底座的销孔,打入定位销,接好进油回油管路,连接好两端的联轴器,装好两端的联轴器保护罩。