R1粗轧机说明书
1780热轧厂粗轧R1辊缝控制系统

在启动 APC设定时,如果条件不允许,例如对 R1轧 机进行电动 APC位置设定,只有当目前的钢坯离开本轧 机后才能进行,否则,就会使本块钢轧废,甚至造成设备事 故。为了避免类似偶然事件的发生,在位置控制系统开始 动作之前,必须检查回路的连锁条件是否满足。对辊缝设 定而言,只有在轧机的负荷继电器或压头检测信号释放的 情况下,才能允许 APC控制回路投入运。 5 结论
R1自动标定操作,在 R1区域维护模式,R1处于自动 标定模式下,进行标定操作:按下自动启动按钮启动自动 标定时序,自动完成辊缝标定,同时显示标定状态。
R1辊缝、轧制力手动标定操作,在 R1区域维护模式, R1处于手动 标 定 模 式 下,进 行 标 定 操 作:轧 制 力 标 定 在 R1空载下标定,轧制力清零;辊缝标定通过手动压下电机 进行压靠,当轧制力达到设定值(5000千牛),按下标定按 钮进行辊缝清零,再手动打开辊缝,标定完成同时显示标 定完成状态。R1缝辊设定时压下输出控制示意图 6。
粗轧 R1压下装置由电动高速压下和电动精压下系
— 137—
Copyright©博看网. All Rights Reserved.
总第 279期 冶 金 设 备
2022年增刊(2)
统组成,高速压下系统用于设定辊缝,低速系统用于高精 度零位调整、上辊左右调平及卡钢时回松。同时采用电动 APC控制闭环控制系统,对轧机水平辊的辊缝调节,以实 现带钢的高精度轧制。
R1粗轧机说明书

mm热带连轧机R1四辊可逆轧机产品安装调试及使用说明书编号51226MSS集团有限公司设计研究院2004年7月MS1.用途:R1粗轧机是粗轧区的关键设备,与E1组成万能可逆轧机,当连铸坯经加热炉加热好后,除去氧化铁皮,由机前工作辊道送至E1R1机前,由机前推床将钢坯推正、对中轧线,经E1立辊轧边,再送入R1,经来回可逆轧制5~7道次,将厚度160的坯料轧制到规定的厚度、宽度,中间坯再由机后工作辊道送往热卷箱、飞剪区进行热卷及切头切尾,之后进入精轧机区进行轧制。
本设备工艺号为42,图号为51226.00。
相关设备有:支承辊换辊装置59294(工艺号43)工作辊换辊装置59312(工艺号43)E1立辊轧机51225(工艺号41)机前工作辊道53235(工艺号34,35,36,37,38,39)机后工作辊道53236(工艺号46,47,48,49)机前推床5277(工艺号40)机后推床5278(工艺号45)2.技术性能与基本参数坯料规格:160X750~1400X7200~12000mm(厚X 宽X长)中间坯规格:17~30(40)X750~1400X~最大长113mMS坯料最大重量:21t工作辊直径X辊身长:φ1050/φ980 X1550mm支承辊直径X辊身长:φ1350(最大)/φ1250(最小)X1500mm工作辊轴承:4列圆锥φ660.4Xφ812.8X365mm 支承辊轴承:Morgan48 X75 KL型油膜轴承最大轧制压力:3500KN最大轧制力矩:2X2000KN.m轧制速度:2.75~5.5m/s主电机型号:BPT6000-12交流变频电机2台主电机功率:6000KW主电机转速:50/100r/min轧辊最大开口度:新辊270mm压下速度:5-15-25mm/s压下电机型号:ZKSL-315-41压下电机功率:150KW压下电机转速:385/770r/min压下蜗轮副中心距:A=711.2mm压下蜗轮副速比:i=1.125X18.33=20.64 ZC1型压下螺丝规格:S508X48(P=24)mm双头锯齿型螺纹压下止推轴承:φ609.6 X204.01mm满装锥形滚子止MS推轴承松卡电机型号:ZZJ-808松卡电机功率:37.3 KW松卡电机转速:575/1150 r/min松卡蜗轮副速比:i=50 zc1型单线蜗轮付主平衡液压缸规格:φ380(400) X610 柱塞型mm主平衡液压缸工作压力:7Mpa主平衡液压缸换辊时压力:16Mpa工作辊平衡压靠液压缸规格:8 X120 X400上辊/120下辊mm工作辊平衡压靠液压缸工作压力:7Mpa塞机架辊规格:2Xφ450X1360mm机架辊传动电机:交流变频45KWX370 r/min,YGP355M1-16机架牌坊外形尺寸:高X宽X厚=9660X4700X1435mm 牌坊单片净重:147t牌坊立柱断面:760X980=7448cm2上下工作辊装配件重量:53.56t上支承辊装配件重量: 56t下支承辊装配件重量: 46t支承辊更换移出行程:5280 mmMS支承辊更换移出速度:70 mm/s工作辊更换移出行程:6250 mm工作辊更换移出速度:100 mm/s主传动接轴型式:C型十字头万向接轴主传动接轴规格:φ960/φ1200X9830mm主传动接轴平衡液压缸:上轴φ200/φ110X450mm下轴用φ200/φ110X200mm主传动接轴平衡液压缸工作压力:7Mpa接轴换辊及抱紧液压缸:2Xφ125/φ90X260mm,16Mpa支承辊、工作辊轴向卡板缸:6Xφ80/φ56X80mm,16Mpa上导卫护板摆动气缸规格:φ200X550-MP4 mm下导卫护板摆动气缸规格:φ200X250-MP4 mm工作辊冷却水喷嘴数量/总耗量:4X19=76(个),250t/h 工作辊冷却水压力:8-10bar,浊环水支承辊冷却水喷嘴数量/总耗量:4X19=76(个),137t/h 支承辊冷却水压力:3-4bar,浊环水轧机本体总重量:820t3.设备外形图3.1机列图MS3.2本体外形图3.3压下原理图3.4轧辊窗口位置图4.结构及工作原理说明:4.1机列组成:轧机本体(51226.04—51226.11) ;主接轴及平衡(51226.01-51226.03)主电机及中间轴 J7002(东电图)工作辊换辊装置 59312支撑辊换辊装置 592944.2轧机本体:本轧机本体由机架、轧辊系统、压下及平衡装置、轧辊传动装置、上下导卫护板、轧辊水冷装置、机架辊装置、平台走梯、配管、及电气行程开关布置等组成。
粗轧区域设备参数
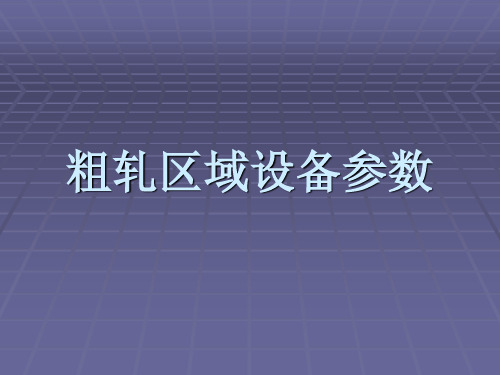
R1/R2轧机前后推床动作方式 R1/R2轧机前后推床动作方式
推床是由液压缸驱动上齿条,上齿条通过齿轮传动下齿轮, 推床是由液压缸驱动上齿条,上齿条通过齿轮传动下齿轮, 使左右推板同步动作,一侧推板的两个推杆机械同步, 使左右推板同步动作,一侧推板的两个推杆机械同步,实现 轧件对中,通过编码器实现开口度设定及对钢件测宽。 轧件对中,通过编码器实现开口度设定及对钢件测宽。
R1轧机前后工作辊道 R1轧机前后工作辊道
R1轧机前后工作辊道由:联轴器、冷却水系 R1轧机前后工作辊道由:联轴器、 轧机前后工作辊道由 甘油系统、螺栓紧固、电机等部分组成。 统、甘油系统、螺栓紧固、电机等部分组成。 简要性能:型式:交流单独传动 简要性能:型式:
辊子尺寸:Φ450x1780mm 辊子尺寸: 辊子数量:机前18根、机后18根 辊子数量:机前18根 机后18根 辊距: 辊距:800mm 传动电机:AC22kW160r/min调速 传动电机:AC22kW160r/min调速 辊面线数度: 辊面线数度:0~3.7m/s 辊子为实心锻钢辊,辊身为喷水冷却,辊颈为喷水冷却( 辊子为实心锻钢辊,辊身为喷水冷却,辊颈为喷水冷却(分 别单独控制) 别单独控制)
R1/R2轧机前后推床作用 R1/R2轧机前后推床作用
推床位于热连轧生产线粗轧机机前、 推床位于热连轧生产线粗轧机机前、机后工作辊道上方其作用是把在辊道 运输中跑偏的钢坯推正,对中轧制线并送入粗轧机进行多道次轧制, 运输中跑偏的钢坯推正,对中轧制线并送入粗轧机进行多道次轧制,以减 少或避免钢坯出现镰刀弯,对粗轧机轧制板型的好坏起着重要作用。 少或避免钢坯出现镰刀弯,对粗轧机轧制板型的好坏起着重要作用。推床 采用电气或液压伺服阀控制,当推板在完成对坯料对中的功能后,可以迅 采用电气或液压伺服阀控制,当推板在完成对坯料对中的功能后, 速退开, 速退开,以防止由于镰刀弯过大或不规整钢坯在轧制时对推板产生过大侧 向力而使推杆弯曲, 向力而使推杆弯曲,破坏设备。
粗轧区域设备参数
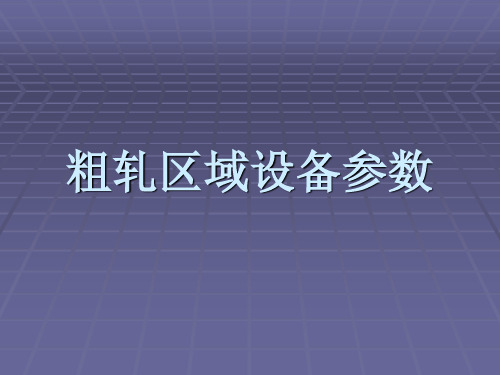
R1/R2轧机前后推床作用 R1/R2轧机前后推床作用
推床位于热连轧生产线粗轧机机前、 推床位于热连轧生产线粗轧机机前、机后工作辊道上方其作用是把在辊道 运输中跑偏的钢坯推正,对中轧制线并送入粗轧机进行多道次轧制, 运输中跑偏的钢坯推正,对中轧制线并送入粗轧机进行多道次轧制,以减 少或避免钢坯出现镰刀弯,对粗轧机轧制板型的好坏起着重要作用。 少或避免钢坯出现镰刀弯,对粗轧机轧制板型的好坏起着重要作用。推床 采用电气或液压伺服阀控制,当推板在完成对坯料对中的功能后,可以迅 采用电气或液压伺服阀控制,当推板在完成对坯料对中的功能后, 速退开, 速退开,以防止由于镰刀弯过大或不规整钢坯在轧制时对推板产生过大侧 向力而使推杆弯曲, 向力而使推杆弯曲,破坏设备。
高压水除鳞的重要性
钢坯在高温状态下被氧化, 钢坯在高温状态下被氧化,在其表面形成一 层致密的氧化铁皮(鳞皮)。 )。在轧制前如果不能 层致密的氧化铁皮(鳞皮)。在轧制前如果不能 将这层氧化铁皮除去, 将这层氧化铁皮除去,在轧制过程中它们会被轧 辊压入到带钢表面,影响其表面质量。 辊压入到带钢表面,影响其表面质量。残留的氧 化铁皮也会加速轧辊的磨损, 化铁皮也会加速轧辊的磨损,降低轧辊的使用寿 如带钢需要酸洗时, 命。如带钢需要酸洗时,残留的氧化铁皮会增加 酸洗的难度,增加酸耗。因此,在钢坯轧制前, 酸洗的难度,增加酸耗。因此,在钢坯轧制前, 必须除去表面的氧化铁皮。 必须除去表面的氧化铁皮。利用高压水的机械冲 击力来除去氧化铁皮(高压水除鳞) 击力来除去氧化铁皮(高压水除鳞)的方法是目 前最通行有效的作法。 前最通行有效的作法。
除磷后效果
除磷前效果
R1机前运输辊道 R1机前运输辊道
R1机前运输辊道由:联轴器、冷却水系统、 R1机前运输辊道由:联轴器、冷却水系统、 机前运输辊道由 甘油润滑系统、螺栓紧固、 甘油润滑系统、螺栓紧固、电机等部件组 成。 简要性能:型式: Φ 简要性能:型式:交流单独传动
1250mm热连轧机技术设计说明2005-7-15
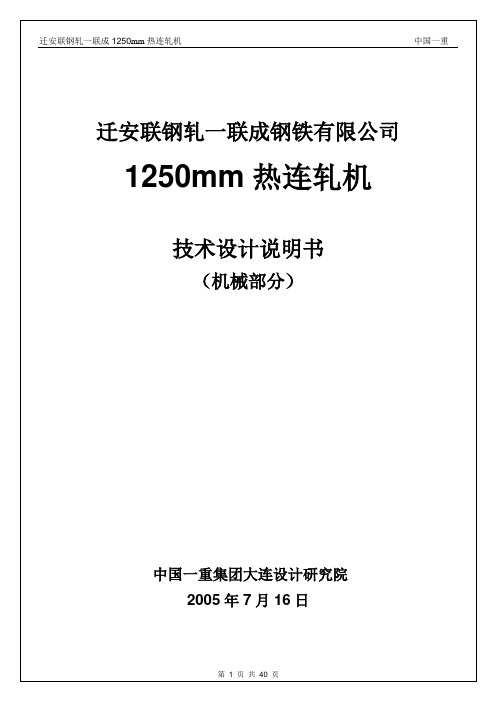
4.1.1
用途:将连铸的热坯由连铸车间送往上料辊道。
型式:交流变频调速电机单独传动。
辊子规格:Φ300×1250 mm
辊距:900 mm
结构特点:采用交流变频调速电机单独传动,辊道架为焊结结构,双止口定位。实心锻钢辊子,轴承座内循环水冷却。称量辊道整体落在称量装置上,传动电机对称布置,称量装置采用汽车衡结构。
4.1.4
用途:将称重后的板坯送至入炉辊道。
型式:交流变频调速电机单独传动。
辊子规格:Φ300×1250 mm
辊距:800 mm
7.采用滚筒式飞剪,减少板坯切头、切尾长度,提高收得率,圆弧剪刃,保证轧件顺利咬入精轧机组,减少精轧咬钢事故率。
8.F1~F7四辊精轧机设全液压长行程AGC压下系统,对厚度进行自动控制,F1~F7采用HCW技术,并配有强力弯辊可得到良好的板材质量。
9.压下系统中安装测压仪、位移传感器用以进行压力、位置信号反馈和控制。
4.1.7
用途:联接入炉辊道及加热炉受料台架,支承板坯在推钢机推力下滑至加热炉受料台架上。采用铸造框架结构。
4.1.8
用途:阻挡钢坯运行。
结构特点:固定挡板由挡板、弹簧及固定底座组成,当板坯撞到挡板后退10mm后,缓冲弹簧受压缩后退后直至板坯停止运动。共2台。
4.1.9
用途:将炉前出炉位置上已加热好的板坯自加热炉中托出放于出炉辊道上。
15.精轧机采用液压横移列车式快速换辊。
16采用层流冷却系统,水量自动控制,以获得最佳的带钢冷却效果。
17.采用固定式地下三助卷辊液压卷取机。卷筒采用低惯量无级液压涨缩式,助卷辊和夹送辊液压驱动。
粗轧篇
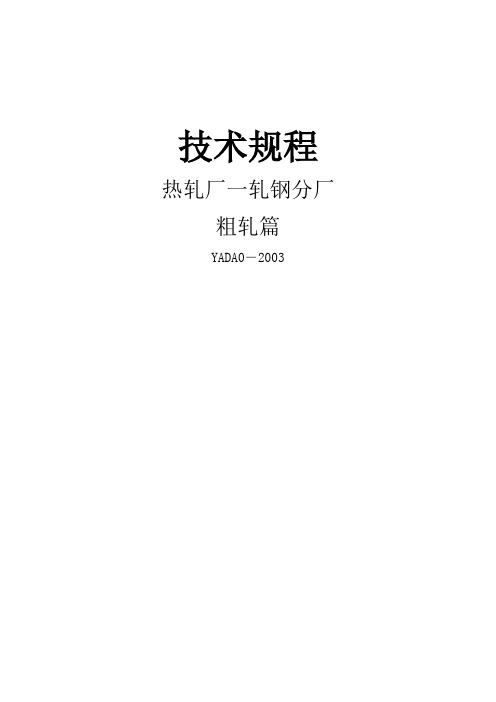
3)最大轧制力和轧辊开度 机架 最大轧制力 t 行程 mm 4)轧辊尺寸范围 机架 Rl R2 R3 R4
R1 3000 350
R2 4000 350
R3 4000 350
R4 4000 350
工作辊Φmm*Lmm (1350-1200)*2050 (1200-1080)*2050 (1200-1080)*2050 (1200-1080)*2050
1.功能说明 除鳞系统主要作用是通过高压除鳞水进行板坯粗大氧化铁皮的去除,确保后道工序轧制 时产品表面质量。 2.除鳞设备及工艺参数 1)除鳞设备的布置 在 El 前的辊道上有一个除鳞箱,箱内上下各有两根集管,改造后上下集管前后错开分 布。 在 E1 前侧面,每侧有两个喷嘴(用于坯侧面除鳞) 在 Rl 前,上下各有一根集管。 在 R2 前,上下各有一根集管。 在 R2 后,上下各有一根集管。 在 E3 前,上下各有一根集管。 在 E4 前,上下各有一根集管。 2)除鳞设备参数(参数说明见示意图) a)1#除鳞箱 每根集管喷嘴数 20 个 喷嘴间距(约) 100 mm 坯与喷嘴垂直间距(约) 200 mm 水嘴型号:694.807。 散射角(α):27-30°。 偏转角(λ):15°。 倾斜角(β):15°。 b)机架间除鳞 集管喷嘴数:R1:2*17 个,R2:2*18 个,R3:上 15 个/下 19 个,R4:上 13 个/下 19 个. 喷嘴间距(约) R1: 118mm, 111mm, 上 133mm/下 105mm, 上 154mm/下 105mm. R2: R3: R4: 水嘴型号:R1:694.847,R2:694.807,R3R4 上:694.727,R3R4 下:694.887。 散射角(α):27-30°。 偏转角(λ):15°。 倾斜角(β):15°。 垂直高度(约) :R1:H 上 360mm,H 下 160mm, R2:H 上 230mm,H 下 210mm, 1. R3:H 上 395mm,H 下 210mm, R4:H 上 400mm,H 下 200mm. 3)除鳞水压力 160bar 4)水嘴更换周期 a) 除鳞箱、R1 前、R3R4 前:一年。 b) R2 前:四个月。 c) R2 后:二年。
轧机安装手册
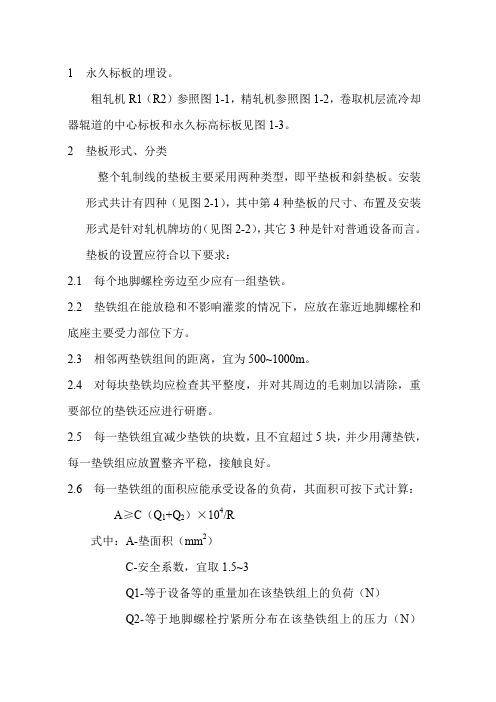
1永久标板的埋设。
粗轧机R1(R2)参照图1-1,精轧机参照图1-2,卷取机层流冷却器辊道的中心标板和永久标高标板见图1-3。
2垫板形式、分类整个轧制线的垫板主要采用两种类型,即平垫板和斜垫板。
安装形式共计有四种(见图2-1),其中第4种垫板的尺寸、布置及安装形式是针对轧机牌坊的(见图2-2),其它3种是针对普通设备而言。
垫板的设置应符合以下要求:2.1 每个地脚螺栓旁边至少应有一组垫铁。
2.2 垫铁组在能放稳和不影响灌浆的情况下,应放在靠近地脚螺栓和底座主要受力部位下方。
2.3 相邻两垫铁组间的距离,宜为500~1000m。
2.4 对每块垫铁均应检查其平整度,并对其周边的毛刺加以清除,重要部位的垫铁还应进行研磨。
2.5 每一垫铁组宜减少垫铁的块数,且不宜超过5块,并少用薄垫铁,每一垫铁组应放置整齐平稳,接触良好。
2.6 每一垫铁组的面积应能承受设备的负荷,其面积可按下式计算:A≥C(Q1+Q2)×104/R式中:A-垫面积(mm2)C-安全系数,宜取1.5~3Q1-等于设备等的重量加在该垫铁组上的负荷(N)Q2-等于地脚螺栓拧紧所分布在该垫铁组上的压力(N)可取螺栓的许可抗拉力R-基础或地坪混凝土的单位面积抗压强度(Mpa),可取混凝土设计强度2.7 垫板安装后检查垫板与垫板间、垫板与设备底座间间隙,用0.05mm塞尺检查,塞入面积不得超过垫板面积的1/3。
2.8 垫板紧固后,垫板组的各垫板应相互点焊牢固。
3 粗轧前导板3.1 设备垫铁采用型式3。
3.2 粗轧前导板定位尺寸A,距粗轧机距离较远,如果粗轧除鳞机前期已经安装完毕,可以用除鳞机作为定位基准(见图3)。
3.3 粗轧前导板找正,沿轧制中心方向挂钢线,打摇杆给辊道定位,在辊道上任意6点,用N3仪器测量标高,同时控制水平度,也可用1m平尺和0.2mm/m水平进行控制。
3.4 检测器具配N3水准仪、1米平尺、0.2mm/m水平仪、卷尺等。
吉林钢铁热轧厂工艺操作规程-粗轧(试行)

吉林建龙钢铁有限责任公司热轧厂粗轧工艺操作规程(试行)发布日期:2011年04月20日实施日期:2011年04月20日受控状态:(发放纸制文件时填写)发放编号:(发放纸制文件时填写)目录1 范围 (1)2 操作台面介绍 (1)2.1操作台及地面站的布置功能与翻译 (1)2.1.1操作台面按钮功能介绍 (2)2.1.2地面站台面布置 (4)3 HMI主画面介绍 (7)3.1主画面页头及颜色状态说明 (7)3.2画面说明 (7)3.3主画面功能键说明 (9)4粗轧启、停车 (10)4.1启车条件的确认 (10)4.1.1油、电的确认 (10)4.1.2水的投用 (11)4.2.启车 (12)4.3.停车 (13)4.3.1正常停车 (13)4.3.2快停 (13)4.3.3急停 (13)5侧导板操作 (13)5.1侧导板标定 (13)5.1.1辊道停转操作 (13)5.2侧导板的操作 (15)5.2.1自动模式 (15)5.2.2手动模式 (15)5.2.3侧导板短行程 (15)6立辊轧机操作 (15)6.1立辊轧机的标定 (15)6.2立辊轧机的操作 (16)6.2.1轧制模式 (16)6.2.2AWC和SSC功能控制 (17)7水平轧机操作 (18)7.1水平轧机的标定 (18)7.2水平轧机操作 (19)8粗轧区水的操作 (19)8.1除鳞箱操作 (19)8.2辊道冷却水操作 (20)8.3冷却水操作 (20)9模拟轧制 (21)9.1带设备模拟 (21)9.2不带设备模拟 (21)9.3单体设备模拟 (21)10废品推出装置 (22)11自动轧制时的调整、干预、修正 (22)12换辊操作 (23)12.1立辊换辊操作 (23)12.2平辊换辊操作 (24)12.2.1R1工作辊的更换 (24)12.2.2支承辊的更换 (25)1 范围本规程规定了热板厂粗轧区域设备的操作调整、初始化、粗轧轧辊更换及粗轧区域轧制状态下的轧制操作。
- 1、下载文档前请自行甄别文档内容的完整性,平台不提供额外的编辑、内容补充、找答案等附加服务。
- 2、"仅部分预览"的文档,不可在线预览部分如存在完整性等问题,可反馈申请退款(可完整预览的文档不适用该条件!)。
- 3、如文档侵犯您的权益,请联系客服反馈,我们会尽快为您处理(人工客服工作时间:9:00-18:30)。
mm热带连轧机R1四辊可逆轧机产品安装调试及使用说明书编号51226MSS集团有限公司设计研究院2004年7月MS1.用途:R1粗轧机是粗轧区的关键设备,与E1组成万能可逆轧机,当连铸坯经加热炉加热好后,除去氧化铁皮,由机前工作辊道送至E1R1机前,由机前推床将钢坯推正、对中轧线,经E1立辊轧边,再送入R1,经来回可逆轧制5~7道次,将厚度160的坯料轧制到规定的厚度、宽度,中间坯再由机后工作辊道送往热卷箱、飞剪区进行热卷及切头切尾,之后进入精轧机区进行轧制。
本设备工艺号为42,图号为51226.00。
相关设备有:支承辊换辊装置59294(工艺号43)工作辊换辊装置59312(工艺号43)E1立辊轧机51225(工艺号41)机前工作辊道53235(工艺号34,35,36,37,38,39)机后工作辊道53236(工艺号46,47,48,49)机前推床5277(工艺号40)机后推床5278(工艺号45)2.技术性能与基本参数坯料规格:160X750~1400X7200~12000mm(厚X 宽X长)中间坯规格:17~30(40)X750~1400X~最大长113mMS坯料最大重量:21t工作辊直径X辊身长:φ1050/φ980 X1550mm支承辊直径X辊身长:φ1350(最大)/φ1250(最小)X1500mm工作辊轴承:4列圆锥φ660.4Xφ812.8X365mm 支承辊轴承:Morgan48 X75 KL型油膜轴承最大轧制压力:3500KN最大轧制力矩:2X2000KN.m轧制速度:2.75~5.5m/s主电机型号:BPT6000-12交流变频电机2台主电机功率:6000KW主电机转速:50/100r/min轧辊最大开口度:新辊270mm压下速度:5-15-25mm/s压下电机型号:ZKSL-315-41压下电机功率:150KW压下电机转速:385/770r/min压下蜗轮副中心距:A=711.2mm压下蜗轮副速比:i=1.125X18.33=20.64 ZC1型压下螺丝规格:S508X48(P=24)mm双头锯齿型螺纹压下止推轴承:φ609.6 X204.01mm满装锥形滚子止MS推轴承松卡电机型号:ZZJ-808松卡电机功率:37.3 KW松卡电机转速:575/1150 r/min松卡蜗轮副速比:i=50 zc1型单线蜗轮付主平衡液压缸规格:φ380(400) X610 柱塞型mm主平衡液压缸工作压力:7Mpa主平衡液压缸换辊时压力:16Mpa工作辊平衡压靠液压缸规格:8 X120 X400上辊/120下辊mm工作辊平衡压靠液压缸工作压力:7Mpa塞机架辊规格:2Xφ450X1360mm机架辊传动电机:交流变频45KWX370 r/min,YGP355M1-16机架牌坊外形尺寸:高X宽X厚=9660X4700X1435mm 牌坊单片净重:147t牌坊立柱断面:760X980=7448cm2上下工作辊装配件重量:53.56t上支承辊装配件重量: 56t下支承辊装配件重量: 46t支承辊更换移出行程:5280 mmMS支承辊更换移出速度:70 mm/s工作辊更换移出行程:6250 mm工作辊更换移出速度:100 mm/s主传动接轴型式:C型十字头万向接轴主传动接轴规格:φ960/φ1200X9830mm主传动接轴平衡液压缸:上轴φ200/φ110X450mm下轴用φ200/φ110X200mm主传动接轴平衡液压缸工作压力:7Mpa接轴换辊及抱紧液压缸:2Xφ125/φ90X260mm,16Mpa支承辊、工作辊轴向卡板缸:6Xφ80/φ56X80mm,16Mpa上导卫护板摆动气缸规格:φ200X550-MP4 mm下导卫护板摆动气缸规格:φ200X250-MP4 mm工作辊冷却水喷嘴数量/总耗量:4X19=76(个),250t/h 工作辊冷却水压力:8-10bar,浊环水支承辊冷却水喷嘴数量/总耗量:4X19=76(个),137t/h 支承辊冷却水压力:3-4bar,浊环水轧机本体总重量:820t3.设备外形图3.1机列图MS3.2本体外形图3.3压下原理图3.4轧辊窗口位置图4.结构及工作原理说明:4.1机列组成:轧机本体(51226.04—51226.11) ;主接轴及平衡(51226.01-51226.03)主电机及中间轴 J7002(东电图)工作辊换辊装置 59312支撑辊换辊装置 592944.2轧机本体:本轧机本体由机架、轧辊系统、压下及平衡装置、轧辊传动装置、上下导卫护板、轧辊水冷装置、机架辊装置、平台走梯、配管、及电气行程开关布置等组成。
4.3机架:机架是轧机骨架,其他各个部件基本上都安装在机架上,它承受全部的轧制力及轧机的冲击震动。
机架的刚性和强度是保证轧钢产品精度和设备可靠性的关键。
本轧机机架由两片整铸封闭框架式牌坊及上下横梁、地脚轨座等组成。
牌坊采用较纯净的低碳钢铸造,经加工后净重达147t,其立柱断面达7448cm2,具有很强的刚性,也是本设备中外形最大,重量最重的零件。
牌坊窗口镶有耐磨衬板,以便于安装工作辊和MS支承辊装置,牌坊上部有装压下螺母的孔,其顶面用来安装压下装置,在牌坊窗口下部安装有耐磨板,用来安装下支承辊换辊支座,牌坊下部外侧各有一个地脚板,通过地脚螺栓安装在轨座上。
牌坊内面上中下各设有多个凸台和加工面,用于安装上下横梁及导卫护板等用。
操作侧牌坊外侧面上装有上下支承辊轴向卡板装置和上下工作辊轴向卡板装置。
在牌坊窗口中部留有安装工作辊平衡液压缸块之处,并在耐磨衬板之后设有专用于提升换工作轨道的吊板槽,可以利用支承辊平衡装置提升工作辊换辊轨道,以保证上下工作辊顺利更换。
上横梁是焊接件,由螺栓和定位键与两片牌坊相连接,用于平衡装置安装。
下横梁也是焊接件,上面设有更换支承辊用的滑板,下横梁通过两端定位键卡在两片牌坊之间。
两底座板为铸钢件,与牌坊地脚板相接处加工特有缺口,通过双楔及地脚螺栓将牌坊紧固在底座板和基础上。
入口侧底座板与E1立辊轧机共用,因而设计得比较大,另外在牌坊入口侧均加工有凸台和螺孔,以便与E1立辊轧机紧密相连。
4.4轧辊系统轧辊系统由上下工作辊(51226.04.05)、上下支承辊(51226.04.04)、支承辊换辊座(51226.04.09),及鞍座(51226.04.06)组成。
MS工作辊直接与红热钢坯相接触,并且传递很大的轧制力矩和轧制压力,本轧机选用半钢轧辊辊面Hs48~55,两端支承选用4列圆锥滚子轴承,上轴承座为T型,下辊轴承座为倒T型,并设有滚轮及定位顶杆,保证上下辊换辊时上下辊面自然脱开,形成四支点接触,能顺利更换。
上下工作辊传动端为扁圆头,直插入接轴套筒,使轧辊转动。
支承辊:根据轧制工艺要求,工作辊直径不能很大,在大的轧制压力下会产生很大的挠度,为此设直径较大的支承辊来承受轧制力。
大直径的支承辊使轧制刚度增大,以保证钢板有较好的板型,本轧机支承辊新辊辊径φ1350 X1500,采用4%铬钢锻制或复合铸制,并与精轧机完全相同辊面硬度达65~75Hs,两端支承采用Morgan48-75 KL型油膜轴承,保证在大轧制压力下轴承可靠性高、摩擦系数小、寿命长。
该油膜轴承为单侧止推式,所以上支承辊两轴承座有连接件相连,下支承辊轴承座由于卡在换辊底座上,故不再用连接件。
下支承辊轴承座下部中心有一个弧面垫与换辊底座上的垫板相接触,在轧辊受很大轧制力而弯曲时,轴承座通过弧面垫能小量转动自位。
在换辊底座两侧设置有可调垫板,可以根据辊子重磨直径变化而改变垫板规格,以保证轧制辊面标高固定在一个规定范围内。
换辊底座底面也设有耐磨滑板和油沟,以便换辊时滑移出机架窗口。
鞍座是一个焊接件,仅在更换支承辊时,保持上下支承辊支承成一体之用。
MS4.5压下及平衡装置压下装置是用来调节轧辊辊缝用的,R1压下采用两台直流调速电机分别通过一对伞齿轮变向带动ZC-1型蜗杆再传动蜗轮和压下螺丝,蜗轮由六齿花键传递扭矩,压下螺丝通过固定在牌坊上梁中的压下螺母,螺丝端部装有锥形滚子止推轴承和测压头的安全臼,在平衡液压缸和平横梁配合作用下,迫使上辊系部分在牌坊窗口上下运动。
平衡装置由装在上横梁上的柱塞液压缸通过横梁、T形杆和滑轨组成,滑轨通过螺栓紧固在T形杆上,滑轨内侧钩部与上支承辊轴承座T型钩部相接,滑轨外侧钩可以与镶嵌在牌坊滑板之间吊板相接,在通常轧辊开口度内,仅滑轨内侧钩紧紧钩住上支承辊轴承座,使其紧靠在压下螺丝端部安全臼上,消除压下螺纹等间隙,当压下螺丝向下压时,主平衡缸的油被迫压回到蓄能罐内。
当压下螺丝上升时,平衡装置带着上支承辊上升,这时装在牌坊窗口腰部的工作辊平衡缸活塞杆顶着上工作辊辊面紧靠支承辊辊面而一起运动,并消除油膜轴承间隙,保证轧钢咬钢、抛钢时不会产生大的冲击和振动。
当换辊时,压下装置将上支承辊超过最大开口度再上升时,装在平衡T形梁上的滑轨外部钩带着吊板与换工作轨道一起上升,再将下工作辊上升,通过顶杆再顶起上工作辊,这时上下工作辊通过滚轮及顶杆联成一体,并且全部重量都落在四个滚轮再作用到换辊轨道上,此时轨道刚好与外部MS换辊桥架上轨道接平,就可以进行换辊。
当非正常操作发生卡钢和座辊时,压下电机已不能提升上辊系时,通过气胎磨擦片式离合器,将松卡装置与压下蜗杆结合,以极低提升速度可以将轧辊提升。
松卡装置是一台37kW直流电机带动一对速比为50蜗轮副,通过气胎离合器与压下蜗杆相连。
在压下螺丝顶端设有MTS型位置传感器和一极限行程开关,用以对压下位置设定和极限保护。
4.6轧辊主传动装置上下工作辊通过十字头万向接轴直接与上下主电机相连,本轧机采用12极交-交变频电机,上电机在后,下电机在前布置,上电机多一中间轴。
十字头万向接轴采用整体铸钢叉头带内外套滚子轴承十字头C型,十字包与中间空心轴采用法兰及端面齿相连,中间空心轴中部设有滑动轴瓦及液压平衡装置。
轧辊端设有耐磨衬板和导引套的套筒与轧辊扁头相联,外部在传动侧牌坊上还设有接轴套筒液压抱紧装置,以便在抽出工作辊时,保持接轴套筒位置不变。
4.7上下导卫护板和轧辊水冷装置为保证正常轧制在入口、出口侧均设有上下导卫护板,以防轧件上翘、扣头产生故障,上导卫护板装在牌坊上由气缸和配重保证上导卫护板内侧擦辊板紧贴工作辊面,下导卫护板则采用梳形齿通过中心轴与机架辊固定导卫板装在一起,靠自重压在下辊MS面上,与辊面接触处装有聚四氟乙稀板,以帮助擦去辊面在轧钢时粘着的氧化皮等污物,换辊时通过气缸将导卫板摆出牌坊窗口。
在上下工作辊和支承辊的入口、出口侧均设有轧辊冷却水喷射集管,工作辊喷射8-10bar的冷却水,支承辊喷射3~4bar 的冷却水,冷却水通过专用喷嘴均匀地喷在辊面,保证在轧钢时辊面温度≤80℃4.8机架辊装配在R1牌坊入口和出口侧各设置一根φ450×1360实心单传动机架辊,两端支承为双列调心滚子轴承,其轴承座(与下导卫支承座共用)由楔板紧卡在牌坊内侧特设台座上,辊子传动端牙嵌有一内花键套,由穿过传动侧牌坊花键轴和能伸缩的万向轴与交流变频电机相接,进行传动。