QC成果减少精轧机组月导卫更换次数.pptx
质量管理小组(QC)—活动成果报告PPT课件

.
10
4、常见问题 (1)不能为目标值的确定提供依据; (2)与课题不对应; (3)提供数据不充分或数据来源不明。 5、不使用现状调查的情况 (1)指令性课题:目标值是直接明确的,不需要现
状调查,但要进行目标可行性分析,来确定目标 能否实现。
(2)创新型课题:是研制新产品,开发新技术,是 前人从未做过的,无现状可调查。
.
9
五、现状调查
1、目的:掌握问题的严重性,找出存在的主要问题,为确 定目标值提供依据。
2、常用方法、工具:调查表;排列图;直方图、控制图等。 3、注意事项 (1)必须用数据说话
* 收集数据要有客观性。 * 收集数据要有可比性。 * 收集数据要有时间约束。 (2)对数据要进行整理、分类、分层。 (3)要在现场观察、跟踪,掌握第一手资料。
.
7
四、QC小组活动课题的选择
1、原则要求:小,实,活,新,特。 2、课题分类: (1)改进型(问题解决型):现场型;服务型;攻关型;管理型。 * 现场型课题特点:课题小,难度低,周期短,效益不一定大。 * 服务型课题特点:课题小,难度低,周期短,社会效益明显。 * 攻关型课题特点:课题难,周期长,投入大,经济效益显著。
.
8
4、选题注意事项 (1)课题宜小不宜大,问题好解决。
* 活动时间短,一般3—6个月; * 对策能自己完成,易发挥小组成员作用; * 解决身边的问题,易调动积极性; * 易总结出成果。 (2)课题名称要一目了然。 * 能以特性值表达的课题; * 特性值要有可比性。
例:《降低**产品的不合格率》(正确) 《提高循环水系统的制冷温差》(正确)
.
2
一、QC成果质量的评定标准
选题明确 方法正确 对策准确 效果比较显著
QC成果--降低机械故障停机时间资料PPT课件

1
确认标准
2
确认过程
3
要因确认七
要 因
更换间隔
更换间隔
更换间隔
更换间隔
更换间隔
平均间隔
左前轮
53天
72天
38天
45天
29天
47.4天
右前轮
44天
57天
60天
79天
38天
55.6天
左后轮
41天
33天
64天
49天
52天
47.8天
右后轮
64天
78天
81天
78天
80天
76.2天
支撑轮轴承更换间隔统计
制表:李绪东 时间:2011年4月6日
设备维修QC小组
定尺机锁紧块磨损
图纸《20054217_01_A》标注:以1个月为使用周期,定尺机的锁紧块磨损程度低于3mm。
小组以1个月为间隔对定尺机锁紧块进行更换,并对更换下来的锁紧块的磨损程度进行测量,结果发现各锁紧块平均磨损程度为2.08mm,符合标准。
课题活动时间
2011.1-2011.12
活动次数
一年一次
选题理由
2010年大型H型钢生产线共停机5323分钟,设备维护费用较多,设备综合效率较低,为此,2011年型钢厂提出要进一步降低大型线的停机时间,以达到降本增效的目的。
我们对2010年设备的停机做了分析,并绘制排列图如下:
机械故障停机时间远高于其他原因的停机时间,所以我们将课题选定为:
确认内容
1
确认标准
2
确认过程
3
要因确认四
非 要 因
照片:任启亮 时间:2011年4月12日
设备维修QC小组
QC小组改善课题ppt课件

1
1
0
0
0
不合格数量(点)
5
7
5
7
4
4
6
5
合计检验数量(点)
500000
500000
500000
500000
500000
500000
500000
500000
目标(PPM)15 Nhomakorabea1515
15
15
15
15
15
不良率(PPM)
10
14
10
14
8
8
12
10.86
在实施了以上措施后,对20XX.7.15-20XX.7.21期间的印刷质量进行了效果检查,见图九、图十。并利用折线图对改善前后SMT印刷不良率进行了数据对比,见图十一。
堵孔
5
1.43
30
4.42
92.91
立件
4
1.14
31.14
3.54
96.45
其它
3
0.86
32
2.65
99.1
锡珠
1
0.29
32.29
0.9
100
合计点数
113
32.29
\
100
\
表二
主 要 不 良
从上图我们可以清楚地看到短路和少锡在累计影响度中占比达80.53%,所以此次6Sigma管理活动将短路和少锡作为重点改善对象。
3、钢模清洗不彻底
4、锡膏使用时间过长
图八
五、改 进 —— 制 定 并 实 施 改 善 对 策
项目
主要因素
拟定对策
目标
措施
完成日期
QC活动降低--课件

不良分布
平面端与内径是处 要 因 平面端与内径处
小结:当NC内径-端面跳动>0.05mm时, 内径目残不良比NC内径-端面跳动≤ 0.改05进m小m组, 专用章
产生的内径目残不良率要高61%
粗加工平面磨床加工完U\V面之后气缸工件的内径与端面直角度不能保证在合格的精度
陈
缺点
因NC第二工程以V面为基准
①开槽后 ②到V面磨削
①清洗后 ②到U面磨削
加工,磨床以U面先为基准 磨削产生内径与端面的直角 度有误差,导致内径目残不稳
定
(内径与端面直角度: 0.06)
合格定义:100%熟悉岗位改标进准小组专用章
规格书熟悉程度和执行性差
陈周英 朱东华 林占男
验证时间 2006年7月10日
10
要因论证(3)
末端原 因
验证方 法
③ V面铆钉孔/排气口有毛刺凸出
判
小批生产内径--端面直角度对比 验证场所
GMCC部品车间
定
验证情况
加工工艺 开槽后①
平面磨床 工序②
检查
作业描述
OP1
OP2
OP1
OP2
精车
精车 判定
规格
0.02mm 以下
0.02mm 0.02mm 0.02mm 0.01mm 0.01mm
以下
以下 以下
以下
以下
X向精度
0.01
0.01
0.01
0.01
0.01
0.01
OK
Z向精度 0.012
0.06
0.015 0.03
0.008 0.009 OK
经过确认主轴纵向和横向跳动在规格内,确认精度合格
13非要因改进小组专用章末端原因夹爪上有铁屑判定验证方法现场确认验证验证场所nc和精车设备验证情况验证结果夹具设计本身无法粘附铁削工件夹紧状况ok验证人林占男朱东华吴志全验证时间2006年7月9号场所设备名数量确认状况气缸粗加nc8件8件夹具夹紧部位设有避空位精加工内圆磨床2件2件夹具夹紧部位设有避空位8要因论证778非要因改进小组专用章末端原因设备主轴精度差nc精车判定验证方法用打表法对设备主轴跳动量检测验证场所gmcc部品车间验证情况验证结果经过确认主轴纵向和横向跳动在规格内确认精度合格验证人叶建辉孙洪标朱东华吴志全验证时间2006年7月8号工序op1op2op1op2精车精车判定确认人规格002mm以下002mm以下002mm以下002mm以下001mm以下001mm以下孙洪标朱东华叶建辉刘志伟x向精度001001001001001001okz向精度0012006001500300080009ok14非要因改进小组专用章要因确定磨床加工时工艺不合理磨床加工时工艺不合理经过小组严格论证后得出以下三个主要原因
《降低发动机“空压机”故障项次》QC成果通报
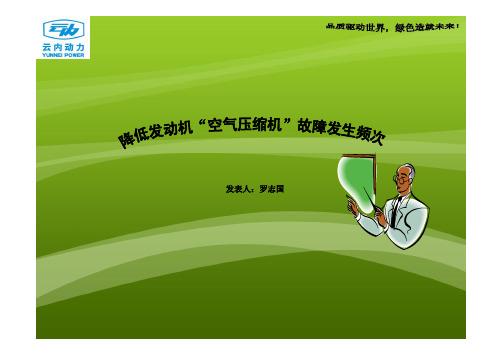
如能抑制上述三项故障发生,则 可有效降低空压机故障频次!
五、原因分析
不 打 气 、 打 气 慢
品质驱动世界 绿色造就未来
阀片密封不严
“阀板部件”锈蚀 阀片结胶
“阀板部件” 抗锈蚀能力差
√
排气窜机油
空
压
排
机
气
故 障
窜 机 油
空 压 机 漏 油
活塞、活塞环、气缸壁 配合间隙变大 活塞环对口
泵体内部机油过多 气缸内压力低,
组员
效果确认、成果总结
制 表:罗志国
时 间:2010年1月5日
二、QC小组活动计划
时间
项目
周期
选择课题 2天
现状调查 2天
原因分析 20天
要因确认 27天
设定目标 1天
制定对策 2天
对策实施 58天
效果验证 15天
巩固措施 2天
总结打算 2天 制 表:
品质驱动世界 绿色造就未来
小组活动甘特图
2010年
品质驱动世界 绿色造就未来
发表人:罗志国
公司简介:
昆明云内动力股份有限公司
品质驱动世界 绿色造就未来
总部位于美丽的云南昆明,为国家大型企 业,是国家重点扶持国内最大的“多缸小缸 径”柴油机开发、生产、销售企业。主要产 品为:乘用、商用、农用等汽车柴油发动机 及非道路用柴油发动机。目前,公司与多家 国内知名汽车厂进行合作,产品足迹现已遍 布国内及东南亚、非洲等地区。
拆解10台故障标记为“窜机油”的空压机,结 果8台气缸壁有明显磨损痕迹。
是要因
罗志国 2010.02.05
3
操作者缺乏培训,导致活塞环对口
拆解57台“窜机油”空压机,只发现2台活塞环 对口。
QC改善案例精品PPT课件

计划 实际
D
对策实施
计划 实际
C
效果验证
计划 实际
A
巩固措施
计划 实际
总结打算
计划 实际
课题背景
主机现场 客户不满
ZL20DBA为我公司为徐工特机提供的油缸: 1、3月10日主机厂反馈此型号油缸有内泄装切现象,共4件; 2、7月30日主机厂反馈此型号油缸有内泄装切现象,共2件。
造成返工 返修
换缸
车间要求 进行改善
倒角及油口毛刺依靠目测和手测
确认标准: 确认质量意识
确认方法: 调查验证
确认人: 王海元
确认时间: 2012.8.23
确认情况:通过调查总装工序5名操作者的2011年度 的绩效考核发现,他们的考核排名比较靠前,只有一 人排名偏后。
姓名 年度考 月度考核 绩效考评 得分 考评等级
毕春虎 32.9 46.8 79.7 159.4 优秀
实完好件数 发出数
80
80
40
40
80
80
42
42
60
60
40
40
40
40
40
40
40
40
接收数 80 40 80 42 60 40 40 40 40
通过前期数据统计分析,6~8月份因装切更换OK圈数量为20个,在这 期间共生产四个批次180件产品,得出此ZL20DBA的装切不良率为11.1%。
课题确定
12-07-11 ZL20DBA 涂装油缸 Φ100×Φ55×785
12-08-16 ZL20DBA 涂装油缸 Φ100×Φ55×785
12-09-05 ZL20DBA 涂装油缸 Φ100×Φ55×785
QC成果 减少生产影响时间

七、制定对策
序 号 1 要因 目标 对策 措施 完成时间 负责人
轴承固有 质量不稳定
保证上轧线的 轴承无预装缺 陷。 保证上轧线的 轧机无预装缺 陷。
保证轴承装配精度和 质量。
与厂家协调沟通提高内在 2011.1-2月 质量,修订个别技术参数。
王介双 张利彬
2
操作规程 执行不严
严格按工艺规程操作。
小组名称新兴铸管股份公司轧钢部高线qc小小组类型攻关型活动课题加强轧机装配管理减少生产影响时间小组成立日期19977活动时间20111201112tqc教育时间人均30小时以上活动次数平均每月10次小组成立时间1997年光辉业绩2002年全国优秀qc成果三等奖中质协2004年优秀qc成果2008200920102011年河北省冶金系统qc成果一等奖2008200920102011年河北省优秀qc成果奖小组成员表序号姓名文化程度职务技术等级组内分工本科段长工程师全面中专副段长技师组织实施硕士工程师助工组织实施中专班长高级工组织实施中专班长技师组织实施中专班长高级工调查统计高中班长技师制定方案中专班长技师组织实施一现状轧机生产工作条件恶劣温度高粉尘大而前期由于对设备性能不够了解对轧机轴承的安装和维护不到位常常出现轧机轴承烧损现象而不得不临时重新装配轧机严重影响了高线的生产
小组成员表
序号 1 2 3 姓名 王介双 裴军良 龚汉涛 岗龄 男 男 男 文化程度 本科 中专 硕士 职务 段长 副段长 工程师 技术等级 工程师 技师 助工 组内分工 全面 组织实施 组织实施
4
5 6 7 8
赵敬涛
李志勇 张立 翟有祥 张立斌
男
男 男 男 男
中专
中专 中专 高中 中专
班长
班长 班长 班长 班长
物流部QC成果汇报修改版减少机车轮缘偏磨
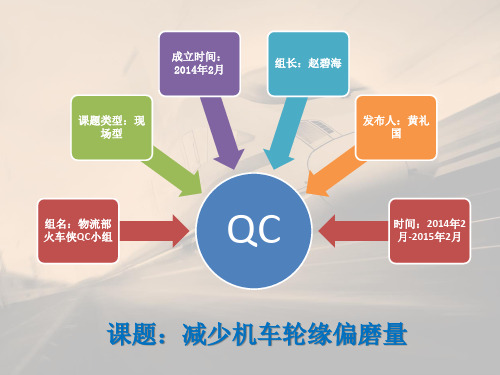
制定对策
方案一:固体润滑棒润滑
加装原轮车缘轮润缘滑润装滑置装原置理图
方案二:油润式机车轮轨润滑装置
复合石墨棒安装在导管中,在弹 簧的压力下,与机车轮缘接触, 随着车轮的转动,涂抹于轮缘的 磨擦表面,形成固体润滑膜,减 小轮缘与钢轨的磨擦
优点:结构简单、装卸方便;造价较低; 不易燃;不易污染轮轨,不影响 机车牵引力、制动力
确车认速结果对影轮响缘程偏判度磨定
储准油罐为正最常1/低3罐限,度且标喷551月 月 93::112301日 日 05黄唐礼熠00国223322
201联4.络5.线 储罐6k缺m/油h ,导
12-5.19 致轮缘干磨, 区间3KM处 磨损10严km重/h 。
轻微
轻微
5月14日 13:48
0232
2#道口
磨影13响km小/h
轻微
验证负责人:黄礼国、李治特 测速工具:LKJ2000列车运行记录仪
确认要因
序号
问题点
确认方式
确要认因标验准证表 机负车责滑人行 机时车间空转 确认结果
判定
时间
车号
作业计划
柴油机 转速
自阀 减压量
空转次数 滑行次数
7
机车滑行
添 业乘 时调 ,查 操5月9: 纵:132观手日0 察法司与0机轮23作缘3 磨耗情况的关系,记录 滑 磨行 情次 况数51月0,:13观1日5察轮0缘23偏2
分析原因
人 机车通过 曲线速度快
机 轮缘与钢轨 接触条件差
轮缘润滑脂加注 不及时
责任心不强
机车滑行 司机操纵不当
机车空转
法
存在急躁心理
同一轮对左右 轮径差值大
曲线半径小 曲线较多 机车蛇形运动剧烈 雨季线路高低 变化
电力行业QC成果减少一体化远动系统故障次数PPT课件
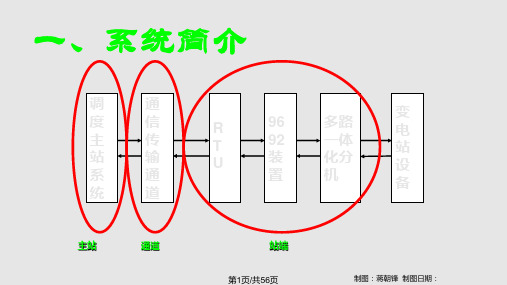
排列图
频数(次)
124 485总线通信中断 93
N=124
累计频率
90% 94% 84% 74% 92
100% 75%
62 31
1
12 7 23
50%
25% 58
4
5
第15页/共56页 制图:蒋朝锋 制图日期:
五、确定目标
一
体
化
远 动
135
124
系 120
统 故
105
障 90
72
次 数
75 60
八、要因确认
1、一体化分机箱体内温度过高; 2、没有防拉死措施; 3、485总线不匹配; 4、485总线接线方式错误; 5、雷电; 6、操作过电压; 7、接地不良。
第23页/共56页
一体化分机箱体内温度过高
2003年1月-12月一体化远动系统故障情况
20
15
10
5
6
8
10
11
7
17
15
14
13 10
现状 目标
第16页/共56页 制图:蒋朝锋 制图日期:
六、目标可行性分析
1、目标值分析
12×6=72(次)
2003年全年一体化远动系统故障次数
20 15 10 56 0
8 7 10 11
17 15 14
13
10
7 6
1月 2月 3月 4月 5月 6月 7月 8月 9月 10月 11月 12月
第17页/共56页
制图:蒋朝锋 制图日期:
一、系统简介
调
通
度
信
主
传
站
输
系
通
统
道
优秀获奖QC课题降低桥式起重机故障率PPT课件

序 号
故障类型
1 重量显示故障
2 传动机构故障
3 限位、开关故障
4
钢丝绳报废
5
其他故障
故障 时间 (h)
840
71
56
48
35
累计 (h)
840 911 967 1015 1050
累计 (%)
80 87 92 97 100
制表人:XX , 制表时间 :2016.3.15
故障时间(h)
一、课题选择
累计(%)
月份 8月份
总台时 (h)
2768
重量显
示故障 188 台时(h)
9月份 2313 166
10月份 2584 137
11月份 12月份
2106 1762128源自1191月份 1490 102
6个月 汇总 13023
840
制表人:XX ,制表时间:2016.3.30
结论:通过以上数据进行计算得出桥式起重机重量显示的故障率为840h/13023h*100%=6.45%。
XX
9
吊装物件重量偏大
吊装物件重量是 否过大
现场调查 联合厂房 单台吊车吊装重量小于32T。 XX
2016.5.15 2016.5.20
制表人:XX,制表时间: 2016.5.25
要因确认一:操作规程未规定
小组成员查阅2跨东桥式起重机(18台桥式起重机规格型号、操作规程一致)司机室内张贴 《桥式起重机安全操作规程》,内容中有相关规定。
工作环境温度过高
测量显示屏工作环 境温度
现场测量
联合厂房
温度是否在说明书标准范围 低于60℃以下。
XX
2016.4.28
1、检查连接情况,焊接牢
qc七大手法-QC成果减少捣固机摩擦片损坏频次 精品
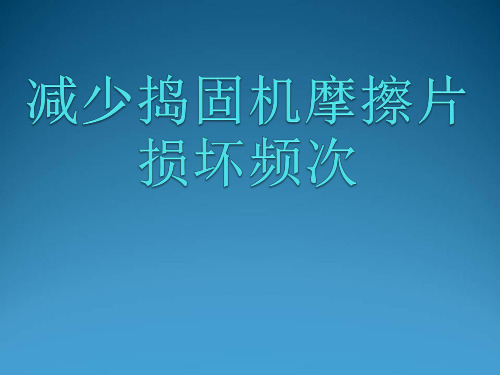
扇形夹 紧装置
集中捣固过程夹紧装置突然
关闭,对运行中的捣固锤产生冲 击,此部位摩擦片在距锤头3-4米 处。
断裂位置普遍位于夹紧油缸
上下一米内。根据摩擦片断裂的 数据分析,此原因导致摩擦片断 裂的比例约为60% 。
要因确定
捣固锤摩擦片粘接 A
过程中表面未清理干净 Nhomakorabea要因
D 捣固启动时的落锤
速度过快
捣固过程中驱动速度 B
120
70% 60%
50%
90
40%
60
52
30%
20%
30
10
5
7 10%
0 0%
0%
断裂 老化 剥壳起层 开胶 其他
影响捣固锤摩擦片使用寿命的因素排列图
N=89
80 70 60 50 40 40 30 20 10 0 0%
断裂
45%29 其他
98%
99%
110000%%
90%
78%
80%
70%
60%
七、要因验证
验证四:捣固过程中驱动速度过快
摩擦片 老化
捣固机的驱动电机启动 速度设为65r/min。捣固锤 还未完全将煤饼夯实时,偏 心轮就开始执行捣固锤下一 次上抛动作,使捣固锤摩擦 片的冲击增大。高频率的摩 擦作用,使摩擦片的温度逐 渐升高,导致摩擦片老化加 剧,出现裂纹甚至断裂。
七、要因验证
验证五:捣固启动时的落锤速度过快
夹紧装置 油缸轴
捣固锤
偏心轮
捣固锤在初始下落过程中一般与偏心轮的接触次数在2-3次,第一 次接触的位置在距捣固锤头3-4米处,对此处的摩擦片造成多次冲击, 从而影响摩擦片使用寿命,摩擦片易出现老化裂纹现象。
机车安全QC成果,减少运行安全隐患,保证内燃机车行车安全

杜绝机车运行故障保证行车安全小组名称:XX机务段QC小组组长:发表人:发表程序一、小组概况二、选题理由三、实现目标值的可行性分析四、具体做法PDCA循环1、现状调查2、设定目标3、原因分析4、制定对策5、对策实施6、效果检查五、综合效果评价1、社会效益2、企业效益六、巩固措施及标准化七、体会及今后打算1、学习活动情况2、QC 小组活动过程示意图3、TQM 管理活动总循环图图—3年12障,保图—1图—2杜绝机车运行故障保证行车安全XXXX公司XX机务段XX车间QC小组一、小组概况及内容介绍本届小组成员情况表2、小组活动内容组织学习、研讨、教育、培训活动二、选题理由图表1—2图表2—1三、实现目标的可行性分析经过小组成员讨论,认为实现目标有以下有利条件:1、具备《机车乘务员学习手册》、XXx线路纵断面图及联运相关要求,可制定符合XX的乘务员一次标准化作业流程。
2、乘务员具备一定的应急故障处理能力,可综合业务水平较高乘务员的经验编制内燃机车应急故障处理方法。
3、内燃车间有抱轴段备机车,便于组织乘务员进行专项培训学习。
4、设立学习室,可对休班乘务员进行专业知识培训。
四、具体做法PDCA循环1、现状调查:2017年1月1日至3月31日,小组成员分别对影响XXx内燃机车运行的因素进行了调查,经过汇总、统计、分析,其结果见图表5—1。
图表5—1影响XXx机车安全运行隐患统计表2、目标设定:3、原因分析:因果分析图5-2影响内燃机车行车安全☆的因素是什么?图表5—34.制定对策图表5—4对策表5、对策实施根据对策表中的要因、现状、目标、措施,我们进行了有针对性的布置,具体到人,逐一落实。
做法如下:一、部分乘务员不了解各区段的注意事项,作业不标准。
经过长时间观察,部分乘务员在标准化作业执行方面有所欠缺,司机在特殊区段操纵存在不足之处,如:呼唤应答存在漏喊、错喊问题,司机采取制动时机不准问题等等,诸如类似上述的问题,我们将所有出现的乘务员易忽略的问题进行全面梳理,从而减少作业不标准问题的发生。
简约实用QC小组工作成果汇报品管圈护理课件

04
05
加强护理人员培训,提高专 业技能和服务意识,提升工
作效率。
成果二:优化护理服务流程
总结词:重新设计并优化了 护理服务流程,提升了患者 满意度。
04
引入患者满意度调查机制, 及时收集患者反馈,针对性 地改进服务流程。
01 03
详细描述
02
简化护理操作流程,减少不 必要的工作环节,降低操作 时间。
行动阶段则是对检查 的结果进行处理,总 结经验教训,持续改 进。
因果图分析法
因果图分析法也称为鱼骨图分析 法,是一种用于分析问题原因的
方法。
通过绘制因果图,将问题的原因 逐级展开,找出问题的根本原因
,为制定改进措施提供依据。
因果图可以帮助小组成员全面地 分析问题,集思广益,共同寻找
解决问题的方法。
成果三:降低护理差错率
总结词:通过严格的质量控制和持续改 进,有效降低了护理差错率。
建立护理差错报告和反馈机制,及时发 现并纠正差错,防止类似问题再次发生 。
加强护理人员培训和教育,提高风险意 识和应对能力。
详细描述
制定并实施严格的护理操作规范和质量 控制标准。
QC小组工作方法
03
PDCA循环
题和解决方案。
分享各自科室的优秀经验和做法 ,促进护理服务的整体提升和发
展。
加强与其他科室的协作配合,共 同完成医院各项任务和工作,提
高医院整体运营效率。
培养更多专业的QC小组人才
加强QC小组人才的培养和引进,提高 QC小组的专业素质和能力水平。
鼓励QC小组积极参与国内外学术交流 和研讨活动,了解最新的质量管理理 念和方法,提高QC小组的创新能力和 水平。
QC成果:降低单位常用设备故障维修率

降低培训学院常用设备故障维修率工程维护部维护突击队QC成果2011-12-22目录一、概况 (1)二、选题课题 ....................................... 错误!未定义书签。
三、现状调查 ....................................... 错误!未定义书签。
四、设定目标 ....................................... 错误!未定义书签。
五、原因分析 (6)六、确定要因 (7)七、制定对策 (10)八、对策实施 (11)九、效果检查 (15)十、制订巩固措施 (18)十一、总结及打算 (18)一、概况“维护突击队”QC小组成立于2011年4月,主要任务是有计划、针对性地对客场所降低设备故障率有效地进行预防性维护,消除故障隐患,提高用电设备的使用性能,从而确保培训学院对客场所用电设备零故障,我维护突击队以降低设备故障率为重点,以全面提升对客服务的满意度为目标。
1、小组简介2、活动计划二、选题理由1、培训学院由于高耗能设备较多、设备老化残旧等因素,综合能耗及使用性能故障率却出现了较为明显的上升的形态;因此,加大力度有效控制能耗设备的维修率上升的态势是刻不容缓的!2、培训用电设备分布存在点多面广,结构复杂、设备老化等特点,同时集客房、教学场所、办公场所、机房等于一身,要控制学院设备故障率,选取为故障率较频繁的复杂设备进行攻关,寻找突破口,以助借鉴及推广。
为此,特成立维护突击队QC小组,对培训学院的2011年1月—6月对客场所(餐饮部、康乐部、客房部)与7月—12月作对比。
重点部位进行重点攻关,对今后学院综合设备维护控制具有较大的经济效益以及服务提升的重要意义。
如果通过进一步改善设备设施运行支撑保障工作,为建设信息化酒店,塑造了信息应用新形象更有效地减少设备的故障率发生是一件迫不及待重要工作。
三、现状调查:附设备故障满意度调查表:鉴于对客场所用电设备故障数量日趋上升的态势,小组决定将:降低培训学院设备故障维修率作为本次活动的课题。
QC改善成果发布模板PPT精选文档

= (年质量成本低减+年节约人工成本)-改善成本 =(1565+1380)-230=2715元/年
年节约成本 112379元
36
十一、效果确认
四 无形效果确认
解决问题能力
QC知识
个人能力
工作热情
团队意识
实施前 实施后
解决问题能力 QC知识 工作热情 团队意识 个人能力
实施前:3分 实施后:4分
一二 三四 周周 周周
6
四、目标设定
目标设定背景: 双马对我司提出堵油孔工序漏序的改善 要求,市场对堵油孔漏序的改善要求. 目标设定:堵油孔工序漏序数量由6件/月降低到0件/月
0件/月
目标: 质量零 缺陷
Page 7
7
五、目标可行性分析
本小组在2012年的品质改善活 动取得了较好的改善效果,同时 积累了一定的品质改善经验
合金钻花
失败
。
。
31
十、对策实施
2-3采用进口锋钢钻花
进口锋钢钻花
失败
32
十、对策实施
2-4采用5mm铣刀先定位
先定位
成功
33
十一、效果确认
一 产品品质确认
作业员检查品质
组长确 认
作业员 检查
品质确 认
品质合格放入下道工序
班长确认
班长确认品质 正常批量生产
太好了!品质合格,可以正常投入生产使用!34
作业指导书
38
十三、总结与反省
活动中的难点和不足
一:在本次活动过程中, 由于生产任务较重,个别圈 员参与活动的积极性不高
二:小组部分成员对QC道 具运用不够熟练 ,改善思维 局限化等
改进方向
- 1、下载文档前请自行甄别文档内容的完整性,平台不提供额外的编辑、内容补充、找答案等附加服务。
- 2、"仅部分预览"的文档,不可在线预览部分如存在完整性等问题,可反馈申请退款(可完整预览的文档不适用该条件!)。
- 3、如文档侵犯您的权益,请联系客服反馈,我们会尽快为您处理(人工客服工作时间:9:00-18:30)。
制表时间 :2011年4月
二、导卫装置简介
导卫是高速线材轧机的最重要的工艺件之一,它的质量好坏 直接影响生产节奏及产品质量。导卫的主要作用是顺利引导轧件 进入轧辊孔型并顺利地将轧件导出, 滚动导卫总成一般由导卫盒 体、导板、支撑臂及其调整装置、中问轴及其调整装置、导辊、 导辊轴承、导辊轴、轴套、防尘盖、油气润滑系统和水冷却系统 等20几个部件精密组装而成。如果导卫安装不当或使用过程中维 护不到位,很容易引起堆钢。
损严重
制图/制表人:狄增文
制表时间 :2011年4月10日
结论:导辊磨损严重占导卫更换次数的56.5%,是主要问题。
六、设定目标值
目标:将导卫的月更换次数由平均的125次降低到110次, 柱状图如下:
110
制图:狄增文 2011年4月10日
六、设定目标值
确定目标的依据
1、车间任务:每月精轧机导卫的更换次数不大于110次,必 须完成 2、分 析:对2月份使用时间小于4小时的导卫更换情况排列 图可知:导辊磨损严重占整个换导卫次数的一半,若解决导辊 磨损则可减少在线使用少于4小时的导卫更换次数23次(使用 时间小于4小时的导卫更换次数=46-46*50%=23次),则精 轧机导卫更换次数则可减少到102次(精轧机组导卫更换次数 =125-23=102次)。 3、最好历史水平:对比总结2008年宣龙高线一高线各月安全 生产快讯,4月、6月、11月、每月的更换导卫次数均小于110 次。
工作计划
4月
5月
6月
7月
8月
9月
10月
11月
上中下上 中下上 中下上中下上中下上中下上中下上中下
1 选择课题
2 现状分析
3 确定目标值
4 原因分析
5 确定要因
6 制定对策表
7 对策实施
8 效果检查
9 效益计算
10 巩固措施
11
总结及下一 步打算
制表人:狄增文
制表时间 :2011年4月
五、现状调查
调查一:
减少精轧机组月导卫更换次数
汇报提纲
小组概况 导卫装置简介 选题理由 活动计划 现状调查 设定目标值 原因分析 要因确认 制定对策 实施对策
效果检查 巩固措施及标准化 总结回顾及今后打算
一、小组概况
小组名称 课题名称 课题类型 活动时间 运用工具 活动次数 序号 1 2 3 4 5 6 7 8 9 10 11
姓名 张翔宇 靳海生 张翼会 闫旭东 费少杰 田菲菲 田亮 杨富成 白捷 狄增文 肖金华
制表人:狄增文
轧钢一车间导卫QC小组
成立时间
2010年1月
减少精轧机组月导卫的更换次数
注册时间
2011年1月
现场型
注册号
XGGS-Q11-9
2011.4-2011.11
小组人数
11人
统计表、调查表、对策表、树图、折线图、柱状图、雷达图
明显的看出导卫的在线使用时间不到4小时的情况占总替换导卫次数 的将近40%,每次更换时间需10分钟,所以提高导卫的有效使用时间 是达到车间要求的关键。
五、现状调查
调查三:
狄增文对2月份使用时间小于4小时的导卫进行检查分析,并作出如下统计:
更换导卫次数主次问题统计表
序 号
更换导卫 原因
频数 (次 )
累计频 数( 次)
累计百 分比( %)
1
导辊磨损 严重
26
26
56.5
2
断轴
8
34
73.9
3 插件松动 5
39
84.8
4 导板磨损 4
43
93.5
5
其它
3
46
100
更换导卫主次问题排列图
频数 (次)
46
N=46
累计百分比 (%)
100
93.5
73.9 84.8
26
56.5
0
50
主要问题
8
5
4
3
0
0
导 辊 磨 断轴 插件松动 导板磨损 其它
查阅2010年2月至12月精轧机组导卫在线使用时间统计如下:
分项 频数(次) 累计频数(次) 累计百分比%
4小时以下 563
4-8小时
759
563 1322
41.22 96.78
8小时以上
44
1366
100
制表人:狄增文
制表时间 :2011年4月5日
统计得知:对2010年2月到12月份精轧机组导卫在线使用时间可以
七、原因分析
为了找到问题的所在,我们小组成员集思广益,运用头脑风暴法利 用树图对产生故障的原因进行了分析:
设备
导 人员
辊 磨 损
备件
严 重
工艺
油气润滑系统故障 冷却水系统故障
责任性失误 调整不到位 维护不到位
材质问题 匹配性问题 料型调整不当
油气管堵塞
冷却水过滤网损坏 技能培训不达标
开口度对中度调整误差大于1mm
及时更换 导辊耐磨时间低于 4小时 不同厂家的备件不 匹配
对有磨损堵塞裂纹等缺 陷的配件没有及时更换
导辊耐磨时间低于4小 时 不同厂家的备件不匹配
插件拉伤松动脱落
制图:狄增文
制表时间 :2011年5月5日
八、要因确认
要因确认计划表
序号
1 2 3 4 5 6 7
末端原因
油气管堵塞
冷却水过滤网损坏
技能培训不达标
开口度对中度误差 大于1mm
对有磨损堵塞裂纹 等缺陷的配件没有
69
3
127
7月份
52
64
6
122
8月份
56
69
2
127
9月份
55
68
4
127
10月份
49
74
3
126
11月份
54
70
5
129
12月份
49
76
3
128
2010年精轧机组导卫更换次数
制表人:狄增文
制表时间 :2011年4月5日
统计得知: 2010年月平均精轧机组导卫更换次数达125次。
五、现状调查
调查二:
在日常的生产中,滚动导卫故障 频繁,造成冲钢多,备件消耗大,因此 解决滚动导卫故障问题是保证高线工艺 顺行的关键。
三、选题理由
车间要求
每月精轧机导卫的更换次数不大于110次。
工艺要求
导卫备件的消耗费用减少百分之10
生产现状
2010年月平均精轧机组导卫更换次数达 125次。
四、活动计划
时间进度
序 列
每月两次
出勤率
99%
性别பைடு நூலகம்
年龄
职称
文化程度
职务
男
42
高技工
大专
副主任
男
40
高级工程师
大专
组长
男
32
助理工程师
大专
装配工
男
32
助理工程师
大专
装配工
男
27
助理工程师
大专
装配工
男
31
工程师
大专
装配工
男
35
工程师
大专
装配工
男
33
高级工
大专
装配工
男
37
技师
大专
装配工
男
26
助理工程师
本科
装配工
女
34
工程师
大学
活动指导
查阅2010年宣龙高线一高线各月安全生产快讯,由班中更换精轧机组导卫 的时间对导卫的在线使用时间进行统计:
2010年精轧机组导卫更换次数表
4小时以下(次) 4-8小时(次) 8小时以上(次) 合计(次)
2月份
46
66
4
116
3月份
45
70
4
119
4月份
50
71
4
125
5月份
52
62
6
120
6月份
55