三头蜗杆车削技术
如何在数控车床上车削多线蜗杆齿形
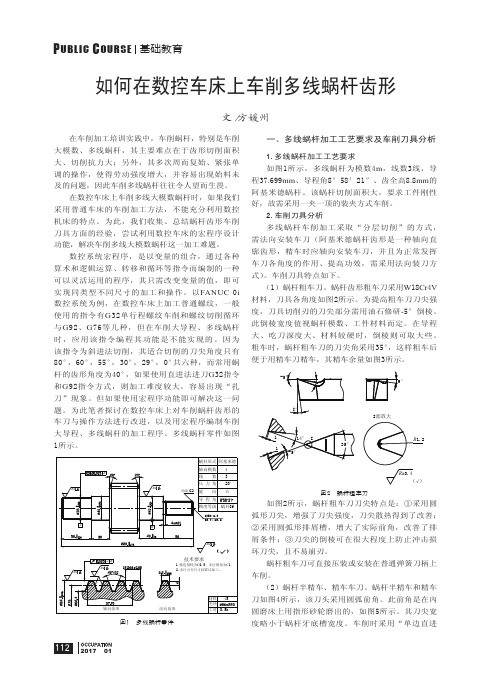
P UBLIC C OURSE基础教育如何在数控车床上车削多线蜗杆齿形文/方媛州在车削加工培训实践中,车削蜗杆,特别是车削大模数、多线蜗杆,其主要难点在于齿形切削面积大、切削抗力大;另外,其多次周而复始、紧张单调的操作,使得劳动强度增大,并容易出现始料未及的问题,因此车削多线蜗杆往往令人望而生畏。
在数控车床上车削多线大模数蜗杆时,如果我们采用普通车床的车削加工方法,不能充分利用数控机床的特点。
为此,我们收集、总结蜗杆齿形车削刀具方面的经验,尝试利用数控车床的宏程序设计功能,解决车削多线大模数蜗杆这一加工难题。
数控系统宏程序,是以变量的组合,通过各种算术和逻辑运算、转移和循环等指令而编制的一种可以灵活运用的程序,其只需改变变量的值,即可实现同类型不同尺寸的加工和操作。
以FANUC 0i数控系统为例,在数控车床上加工普通螺纹,一般使用的指令有G32单行程螺纹车削和螺纹切削循环与G92、G76等几种,但在车削大导程、多线蜗杆时,应用该指令编程其功能是不能实现的。
因为该指令为斜进法切削,其适合切削的刀尖角度只有80°,60°,55°,30°,29°,0°共六种,而常用蜗杆的齿形角度为40°,如果使用直进法进刀G32指令和G92指令方式,则加工难度较大,容易出现“扎刀”现象。
但如果使用宏程序功能即可解决这一问题。
为此笔者探讨在数控车床上对车削蜗杆齿形的车刀与操作方法进行改进,以及用宏程序编制车削大导程、多线蜗杆的加工程序。
多线蜗杆零件如图1所示。
图1 多线蜗杆零件一、多线蜗杆加工工艺要求及车削刀具分析1.多线蜗杆加工工艺要求如图1所示,多线蜗杆为模数4m,线数3线,导程37.699mm、导程角8°58′21″、齿全高8.8mm的阿基米德蜗杆。
该蜗杆切削面积大,要求工件刚性好,故需采用一夹一顶的装夹方式车削。
2.车削刀具分析多线蜗杆车削加工采取“分层切削”的方式,需法向安装车刀(阿基米德蜗杆齿形是一种轴向直廓齿形,精车时应轴向安装车刀,并且为正常发挥车刀各角度的作用、提高功效,需采用法向装刀方式)。
多头蜗杆车削
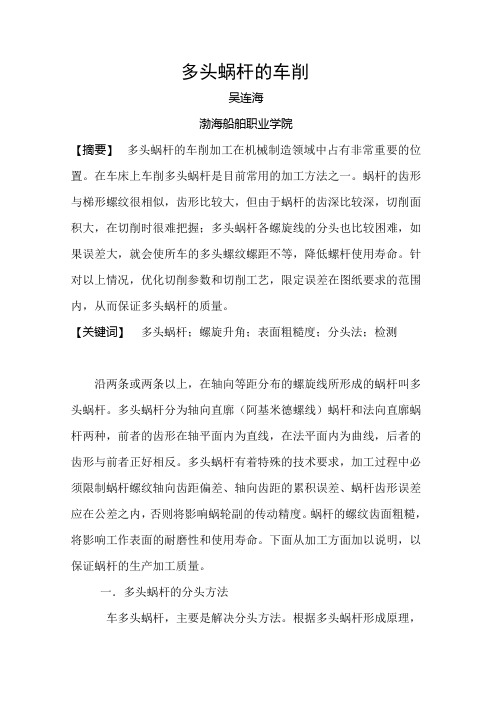
多头蜗杆的车削吴连海渤海船舶职业学院【摘要】多头蜗杆的车削加工在机械制造领域中占有非常重要的位置。
在车床上车削多头蜗杆是目前常用的加工方法之一。
蜗杆的齿形与梯形螺纹很相似,齿形比较大,但由于蜗杆的齿深比较深,切削面积大,在切削时很难把握;多头蜗杆各螺旋线的分头也比较困难,如果误差大,就会使所车的多头螺纹螺距不等,降低螺杆使用寿命。
针对以上情况,优化切削参数和切削工艺,限定误差在图纸要求的范围内,从而保证多头蜗杆的质量。
【关键词】多头蜗杆;螺旋升角;表面粗糙度;分头法;检测沿两条或两条以上,在轴向等距分布的螺旋线所形成的蜗杆叫多头蜗杆。
多头蜗杆分为轴向直廓(阿基米德螺线)蜗杆和法向直廓蜗杆两种,前者的齿形在轴平面内为直线,在法平面内为曲线,后者的齿形与前者正好相反。
多头蜗杆有着特殊的技术要求,加工过程中必须限制蜗杆螺纹轴向齿距偏差、轴向齿距的累积误差、蜗杆齿形误差应在公差之内,否则将影响蜗轮副的传动精度。
蜗杆的螺纹齿面粗糙,将影响工作表面的耐磨性和使用寿命。
下面从加工方面加以说明,以保证蜗杆的生产加工质量。
一.多头蜗杆的分头方法车多头蜗杆,主要是解决分头方法。
根据多头蜗杆形成原理,分头方法有轴向分头法和圆周分头法两类。
1.轴向分头法第一条螺旋槽车好后,把车刀沿着工件轴向方向移动一个齿距,再车第二条螺旋槽。
1.1小滑板刻度分头法即第一条螺旋槽车好后,利用小滑板刻度,使车刀移动一个齿距。
小滑板刻度盘转过格数可用下式计算 K=p/a式中 K---刻度盘转过格数p---工件齿距(mm)a---小滑板刻度盘每格移动的距离(mm).1.2百分表分头法第一条螺旋槽车好后,把百分表磁力座固定在大拖板上,触头顶在刀架上,然后将百分表调整至零位,移动小滑板,直至百分表指针变化一个齿距为止。
测量中要注意百分表测量杆与床身的平行。
1.3量块分头法在采用直进法车削螺纹时,先要在大拖板上和小拖板上各装一个固定挡块,在车第一头时,小拖板上的触头应和大拖板上的触头靠紧。
蜗杆的车削方法实习难点
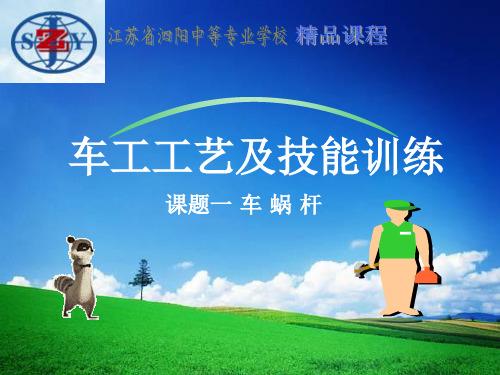
相关工艺知识 3、蜗杆的车削方法 (1)蜗杆车刀 ①蜗杆粗车刀 车左右刀刃间的夹角要小于两 倍齿形角,刀头宽度应小于齿根槽宽,切削钢料 时,应磨有10°~15°的纵向前角径向后角6° ~8°,左刃后角(3°~5°),右刃后角( 3°~5°)刀夹适当倒圆
相关工艺知识
②蜗杆精车刀 车刀左右刀刃之间夹角应等于两倍齿形角 一般前角磨成0°
相关工艺知识
(2)车刀的装夹 通常采用万能角尺找正车刀刀尖间的位置,将万能 角尺的一边靠住工件外园,观察万能角尺的另一 边和车刀刃口的间隙。如有偏差,可转动刀架或 重新装夹车刀来调整刀尖角的位置。
相关工艺知识
(3)车削方法 采用开倒、顺车切削,蜗杆的车削方法和车梯形螺 纹相似,粗车后,留精车余量0.2-0.4mm,由 于蜗杆螺距大,齿形深,切削面积大,因此精车 时,采用均匀的在车削过程中,应观察切屑深度 过程,会发生“啃刀”现象,在车削过程中,应 观察切屑情况控制切削用量,防止“扎刀”,最 后再用刀尖角略小于齿形角的车刀,精车蜗杆底 径,把齿形修整清晰。
(2)蜗杆分度图上的法向齿厚公差或轴向齿厚 公差符合标准要求。 (3)蜗杆分度图径向跳动量不大于允许范围
mx
相关工艺知识
2、来制蜗杆车削时的有关尺寸计算 (1)周节 P= (2)全齿高 h=2.2 (3)分义园直径 d1=d0-2mx (4)齿根园直径 df=d1-2.4mx (5)齿顶宽Sa=0.843mx (6)齿根槽宽ef=0.697mx (7)导程角 tg= (8)法向齿厚Sn=
相关工艺知识
4、蜗杆的测量方法 (1)用三针和单针测量,方法与梯形螺纹测量相 同。 (2)齿厚测量法:将齿高卡尺读数调整到等于齿 顶高法向卡入齿廊,亦使齿轮卡尺和蜗杆轴线大 似相交成一个角的角度,作少量转动,此时的最 小读数,即是蜗杆分义图直径处的法向齿厚Sn 。
三头蜗杆车削技术
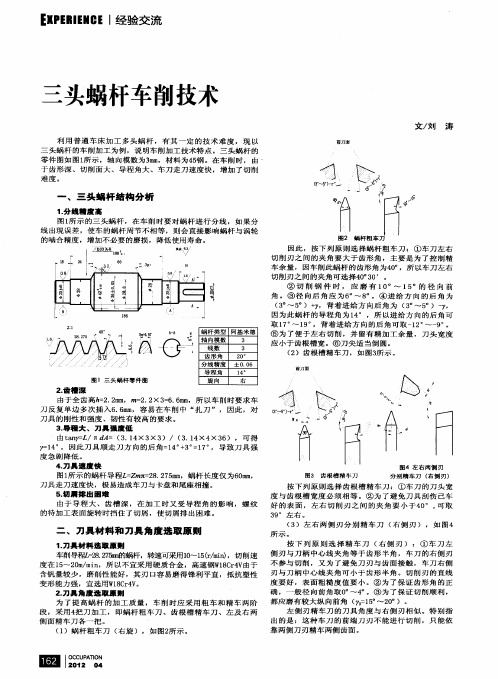
涛
前刀面
/1 r\ \
oo 吲
L ̄ 、
却
、
三 头 蜗 杆 结 构 分 析
G
。
1分线 精 度 高 . 图 l 示 的三 头 蜗 杆 ,在 车 削 时 要对 蜗 杆 进 行 分 线 ,如 果分 所 线 出现 误 差 ,使 车 的蜗杆 周 节 不相 等 ,则 会直 接 影 响蜗 杆 与 涡轮 的 啮合 精度 ,增 加不 必要 的磨损 ,降 低使 用 寿命 。
2. 槽 深 齿 由于全 齿 高 h 2 2l,m= . = . II Il I 2 2×3 6 6 ,所 以车 削 时要 求 车 =.咖 刀反复单边多次插入66皿 . m ,容 易在 车 削 中 “扎 刀 ” , 因此 ,对 刀 具 的 刚性 和 强 度 、韧 性 有较 高 的要 求 。 3. 程大 、刀 具 强度 低 导 由t n = a T L/Ⅱd A= ( . 4×3 31 X3)/ ( . 4×4×3 31 6) ,可 得 y 4 =1 。。 因此 刀 具 顺 走 刀 方 向的 后角 =1 + 。 1 ,导 致 刀 具 强 4。 3 = 7。 度 急 剧 降低 。 4 刀具 速 度 快 . 图1 所示 的蜗 杆 导程 Z = 8 2 5 m = mu 2 . 7 m ,蜗杆 长 度 仅 为6 r , 0 m a 刀 具走 刀 速度 快 ,极 易造 成车 刀 与卡 盘和 尾 座 相撞 。 5 切■ 排 出 困难 . 由于 导 程 大 、 齿 槽 深 ,在 加 工 时 又 受 导 程 角 的 影 响 , 螺 纹 的待加 工 表 面 旋转 时 挡 住 了切 屑 ,使 切 屑 排 出 困难 。
E P RE O 经验交流 X E IN EI
果 表 的指 针 都 处 于 同 一 位 置 ,说 明 刀 的 角度 已 装 好 。用 此 种 方法 对 刀 ,要 求 在磨 刀 时 采用 的样 板 如 图6 所示 。 在 车 蜗 杆 的 过 程 中采 用 的 切 削 液 是 用 纯 碱 与 皂 粉 的 比 此样 板 要 求B 与C 平 行 ,A 与B 、c 面 面 面 面 面垂 直 。 为 3: 约 1 5 g 1( . k )加 水 3 k 混合 稀 释 而 成 ,该 切 削 液 主要 0g ③ 分 线 方 法 。笔 者 采 用 的 是轴 向 分 线 法 , 先 调 整 好 小 特 点是 可 以 使 切 屑 顺 利 排 出 ,拖 板 与机 床 导 轨 平 行 度 后 ,利 用 小滑 板 刻度 确 定 直 线 移 动 洁 ,切 削 时没 有 油 烟 影 响等 优 点 。 分 线 , 在 车 好 一 条 螺 旋 槽 后 , 利用 小 滑 板 刻 度 配 合 百 分 表 使 车 刀 移 动 一 个 螺 距 ,再 车 相 邻 的 另 一 条 螺 旋 槽 ,从 而 达 四 、三 头 蜗 杆 实 际 - 过 程 r 到分 线 的 目的 。 ④ 车 削 方 法 。采 用 开 倒 、 顺 车 方 法 切 削 。并 使 蜗 杆 的 三 头蜗 杆 的轴 向模 数 为m 3 n = n ,齿 形角 为2 o  ̄ o ,螺旋 线 方 向 为右 旋 , 导程 角 为 1 4。,工 件 材料 为 4 钢 ,毛 坯 为热 轧 圆 粗 车 刀 在 刚 车 好 的槽 的 范 围 内 进 行 左 右 切 削 。车 好 第 一 螺 5 旋 槽 以后 ,再 车 第 二 条 、第 三 条 、 螺 旋 槽 , 由于 刚 才 切 槽 钢 ,尺寸为  ̄5 X 10 m 0 9 m o在机 械加 工前 ,安排调 质处理 T 3 。 2 5 刀 宽 度 已经 控 制 蜗 杆 槽 粗 车 的 宽 度 , 所 以能 控 制 好 每 单 边 工 序 安排 应 将 粗 车 、精 车 分 开 , 工件 装 夹 要 牢 固 。 都 留0 2Ⅱ的精 车 余 量 ,如 图 7 示 。 .Ⅱ n 所 1粗 车各 外 圜 . ( ) 用 三 爪 自定 心 卡 盘 装 夹 毛 坯 外 圆 , 伸 长 约 1 1 O m,车 平 端 面 ,粗 车 蜗 杆 外 圆 (4 lm / 4× 1 6 m 2 m 的 外 ' 0m 。 8m 圆至 3 ×4 . m 。 2 的外 圆至 2 × 1 . m 。 O 1 5 m 5 7 7 5 m ( 2)掉 头 夹 工 件  ̄4 4的外 圆 , 校 正 后 夹 紧悬 伸 长 度 约 图7倒 、顺车削方法 7 m ,车 端 面 ,保 证 总 长 1 7u。 0m 8 nn ( 3)粗 车 (2 的外 圆至 2 /0 ' 2×2 . m , 粗 车 2 的外 圆 95m 5 5 精 车蜗 杆 . 至 2 7×2 . m 。 车 2 的 外 圆 至 3 1 5m 8 0×2 m 3 m。 ( )用 两 顶 尖 装 夹 。先 精 车 蜗 杆 外 圆 至  ̄4 m ,表 面 1 2m 2 热 处理 。调 质T 3 略 ) . 2 5( 粗 糙度 3 2Jl 去 除蜗 杆 表面 和 两 端 毛刺 。 . I ll , 3. 精 车外 圜 半 ( )采 用 图4 示 左 、右 两侧 刃精 车 刀 。用 百分 表 校 正 2 所 ( )用 三 爪 自定 心 卡 盘 装 夹 4 外 圆 并校 正 。车 两 端 左 侧 ( 1 4 背走 刀 方 向 )精 车 刀 并 对 刀 ,低 速 精 车 第 一 条 螺 旋 面 钻 中 心孔 ( 3 6 。 中 心孔 表 面 粗 糙 度 值 要 小 且 圆整 。 A/) 槽 右 侧 面至 车 刀 主 刀 刃 与 齿 根 圆相 触 及 ,表 面 粗糙 度 达 规 保 证 总 长达 尺寸 要 求 。 定 要 求 ,记 录 中滑 板 进 刀 刻 度 值 为O 若 表 面粗 糙 度 不 够 理 ( )采 用 一 夹 一 顶 的装 夹 方 式 , 半精 车 外 圆 。① 车左 想 则 可 使 用 小 拖 板 赶 刀 、修 光 ,但 须 保 证 齿 厚 单 边 余 量 不 2 端 台阶 。外 圆各 留精车 余 量 l ,长 度至 尺 寸要 求 。② 工 件调 得 小 于 0 1 m m .m。 头 ,车右 端 台阶 。外 圆各 留精车余 量 l ,长 度至尺 寸要 求 。 m 然 后 以百 分 表 和 小 拖 板 刻 度 配 合 作 轴 向分 线 ,使 小 4 半精 车 蜗杆 外圆 。粗 车蜗 杆 . 拖 板 移 动 一 个 齿 距 ,用 直 进 法 精 车第 二 条 螺 旋 槽 同方 向侧 ( )调 整车 床 。准 备 刀具 。 1 面 , 直 至 到 记 录 中拖 板 进 刀 刻 度 处 , 表 面 粗 糙 度 达 要 求 。 ( )按模数 ×头数 ( x3 2 3 )。调整 车床挂轮和各手柄位 置。 用 同样 方 法 车好 第 三 条螺 旋 槽 。 ( ) 采 用 一 夹 一 顶 装 夹 方 式 。夹 右 端 2 m 外 圆使 台 3 Om 精 车牙 面 的加工 顺序 : 1 牙侧 a 一2 槽 面 槽牙 侧c 面一 3 槽牙 阶 紧 贴 卡 爪 。百 分 表 校 正 蜗 杆 外 圆 调 动 量 控 制 在 0 0 m . 2 m以 侧e 一3 面 槽牙侧 f 面一2 牙侧d 一 1 槽 面 槽牙侧 b ,如 图8 示 。 面 所 内并夹 紧 。顶尖 顶 一 端 。 半精 车 蜗 杆 外 圆至 4 . m 及 两 端 2 5m 倒 角2 。 。 O ( )粗 车 蜗杆 。蜗 杆 有关 参 数 值 见表 1 4 。
浅谈蜗杆的车削

浅谈蜗杆的车削作者:桑艳平来源:《现代企业文化·理论版》2008年第12期【摘要】蜗轮、蜗杆组成的运动副常用于减速传动机构中,蜗杆的齿形较大,在切削时很难把握。
通过革新刀具、合理使用刻度和选择切削用量,采用这种新的车削蜗杆的方法大大提高了生产质量和生产效率,是一种可以推行的蜗杆加工方法。
【关键词】蜗杆模数刃磨;刻度线;刀体;加工步骤蜗杆的车削加工具有很重要的位置。
蜗杆、蜗轮组成的运动副常用于减速传动机构中,以传递两轴在空间成900交错的运动。
蜗杆的齿形与梯形螺纹很相似,其轴向剖面图形状为梯形。
常用的蜗杆有米制(齿形角为400)和英制(齿形角为290)两种。
我国大多数采用米制蜗杆。
工业上最常用的是阿基米德蜗杆(即轴向直轮廓蜗杆),蜗杆的车削方法和梯形螺纹相似,但蜗杆的齿形比梯形螺纹的齿形大,车削时刀具和工件容易发生振动,使工件变形甚至会产生“扎刀”现象。
为解决这样的问题,这里介绍的车削蜗杆的方法主要是对刀具、刀体车削方法进行了改进,使粗车时能够进行强力切削,而且振动小,能保证顺利排屑,不产生“扎刀”现象。
当熟练地掌握了这种加工方法以后,生产效率比一般的车削方法有所提高。
下面就以教学中加工模数mx=6的单头的蜗杆为例,介绍此革新方法车削蜗杆的主要过程和加工特点,车削时采用工件材料为45钢。
一、改进一般的弹性刀为刚性刀1.刀块材料:高速钢(W18Cr4V),刀体材料:45钢(刀体需经热处理,HRC38—42)。
2.刀体可以转动。
在粗车时,如用一般的“死体刀”,由于工件螺旋角的关系,需把刀块一侧刃的后角刃磨得较大,使刀头强度减小,不能进行强力切削。
而采用可以旋转角度的刀体,在车削时,就能根据工件螺旋角的大小,把刀体转过这个角度。
这时刀块只要刃磨成和一般车刀相同的后角即可,不需要磨成大后角,保持了刀头强度,有利于强力切削。
3.刀体采用刚性强的刀体,一般的弹性刀体在较大的轴向切削力的影响下,会发生扭转变形使所车蜗杆的轴向齿形角发生变化和螺距产生变化和螺距产生误差,降低加工精度。
浅谈蜗杆车削中减少振纹的方法
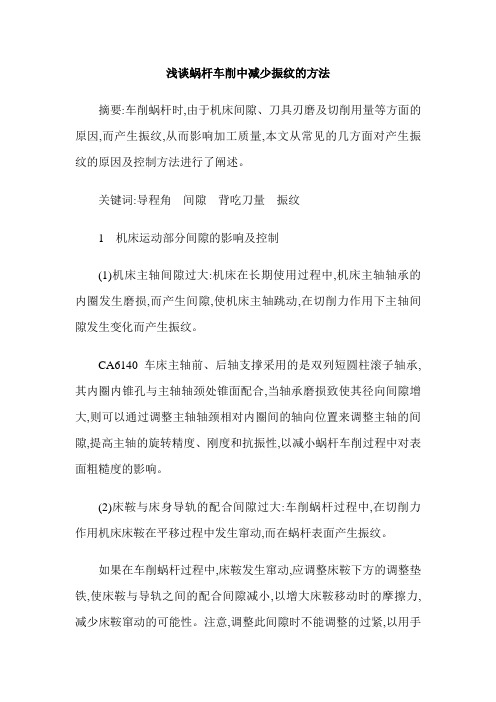
浅谈蜗杆车削中减少振纹的方法摘要:车削蜗杆时,由于机床间隙、刀具刃磨及切削用量等方面的原因,而产生振纹,从而影响加工质量,本文从常见的几方面对产生振纹的原因及控制方法进行了阐述。
关键词:导程角间隙背吃刀量振纹1 机床运动部分间隙的影响及控制(1)机床主轴间隙过大:机床在长期使用过程中,机床主轴轴承的内圈发生磨损,而产生间隙,使机床主轴跳动,在切削力作用下主轴间隙发生变化而产生振纹。
CA6140车床主轴前、后轴支撑采用的是双列短圆柱滚子轴承,其内圈内锥孔与主轴轴颈处锥面配合,当轴承磨损致使其径向间隙增大,则可以通过调整主轴轴颈相对内圈间的轴向位置来调整主轴的间隙,提高主轴的旋转精度、刚度和抗振性,以减小蜗杆车削过程中对表面粗糙度的影响。
(2)床鞍与床身导轨的配合间隙过大:车削蜗杆过程中,在切削力作用机床床鞍在平移过程中发生窜动,而在蜗杆表面产生振纹。
如果在车削蜗杆过程中,床鞍发生窜动,应调整床鞍下方的调整垫铁,使床鞍与导轨之间的配合间隙减小,以增大床鞍移动时的摩擦力,减少床鞍窜动的可能性。
注意,调整此间隙时不能调整的过紧,以用手能够平稳摇动床鞍为宜,此时能有效提高床鞍与床身导轨之间的联接刚性,减小由于床鞍窜动而引起的振纹。
(3)中、小滑板丝杠与丝杠螺母配合间隙大:在蜗杆车削时,出现时而车削时而不切削的现象(断续状态),这是由于丝杠与丝杠螺母间存在间隙产生让刀,如果这种现象不及时消除,易引发振动从而导致振纹的出现。
在车削蜗杆前应调整中、小滑板的丝杠与丝杠螺母的间隙,调整时以转动滑板每圈有0.5mm的间隙量为宜,同时调整滑板的镶条,以增强滑板与导轨的联接刚度,调整量为以手动转动手柄能够感觉到间隙量的存在为宜。
通过对机床主轴、床鞍与导轨间隙及中、小滑板的间隙调,可以有效的提高机床运动部分的刚性及运动精度,能够有效的减小蜗杆车削加工中产生振纹的情况。
2 工件系统刚性的影响及控制由于蜗杆的导程大、牙槽深,切削面积大,则要求工件安装在机床上要有足够的刚性,来抵抗切削力的作用,否则,在切削过程中由于工件系统刚性差,易产生振动,而在蜗杆表面出现振纹。
蜗杆加工方法

在数控车床上快速车削蜗杆的方法摘要:在数控车床上车削较大导程的蜗杆、梯形螺纹和锯齿螺纹,由于工件的齿形深,需要切除的毛坯余量多,一般是选择较低的切削速度和高速钢成形刀,使用G32和G76等指令车削,加工精度特别是表面粗糙度很难达到图纸要求,加工难度较大。
针对出现的加工精度低、生产效率低等特点,说明如何有效地发挥数控车床的高精度,高速度、定位精度高、生产效率高的优势。
我们以沈阳CAK3675v 华中数控系统的车床来论述快速车削蜗杆的方法。
如图1关键词:蜗杆数控车床成形刀硬质合金宏程序蜗杆和大导程螺纹车削的进刀方法有多种,如直进法、左右切削法、斜进法和切槽法等。
以前车削蜗杆等大导程零件的方法是:选用较低主轴转速(数控车床最低速为100转/分时转动无力)和高速钢成形车刀,车削蜗杆时的生产效率低。
为解决上述问题,我认为应从刀具材料、几何形状及角度和车削方法来谈谈快速车削蜗杆和大导程螺纹的方法。
一、突破传统选择刀具的习惯,合理选择车削蜗杆的刀具角度,使刀具的刀尖角小于齿形角车削蜗杆刀具的刀尖角如果等于蜗杆的齿形角。
这种刀具在车削时两侧刀刃与工件侧面容易发生摩擦,甚至三个刀刃同时参加切削,易产生较大的切削力而损坏刀具。
如果选择车刀的刀尖角35小于蜗杆的齿形角40,(如图2)这种车刀在车削时,可防止三个刀刃同时参加切削,减少了摩擦、切削力,能很好地避免“闷车”、“扎刀”和打刀的情况发生。
二、在数控车床上使用硬质合金车刀高转速车削蜗杆成为现实以前,车削加工蜗杆和大导程螺纹,只能用高速钢车刀低速车削加工,生产效率非常低。
如果将车刀的刀尖角磨小,使车刀的刀尖角35小于蜗杆的齿形角40,可避免三个刀刃同时参加切削,切削刀显剧下降,这时可使用较高的切削速度和硬质合金车刀对蜗杆进行车削。
当工件直径、导程越大时,可获得的线速度越高,加工出的工件表面质量越好,而且生产效率明显提高。
彻底解决在数控车床不能用硬质合金刀具车削蜗杆和大导程螺纹零件。
9.2多线螺纹和多线蜗杆的分线方法

概念 分线:
多线螺纹(蜗杆)的各螺旋槽在轴向是等距离分布的,在端面上螺旋线 的起点是等角分布的,而进行等距分布(或等角度分布)的操作叫分线。
多线螺纹(蜗杆)与单线的不同之处 :
车多线螺纹(蜗杆)与车单线螺纹(蜗杆)的不同之处是:按导程计算 交换齿轮,按螺纹(蜗杆)线数分线。
利用交换齿轮分线:当车床交换齿轮Z的齿数是螺纹线数(或蜗杆头数) 的整数倍时,就可以在交换齿轮上进行分线。
圆周分线法
例: 车削三头蜗ຫໍສະໝຸດ ,可按以下步骤进行: 车好第一条螺旋后,停机,在交换齿轮Z1上用粉笔做好三等分(设主轴 到Z1的传动比为1)记号1、2、3。随后把Z2齿轮与 Z1齿轮脱开,用手 转动卡盘,使记号2的一个齿转到原来3的位置上,并与 Z2记号4处啮合, 就可以车削第二条螺旋槽。第三条螺旋槽用同样方法进行。 用交换齿轮分线的优点是分线精度高,但比较麻烦。
解:
轴向分线法
利用百分表和量块分线
把百分表固定在刀架上,并在床鞍上装一固定挡块。当车第一条螺旋槽 时,在挡块与百分表之间放入厚度等于两倍轴向齿距(2p )的量块,并 移动小滑板,使百分表触头接触量块,并调整百分表指针至零位,当车 好第一条螺旋槽后,调一块厚度为一个轴向齿距p的量块,移动小滑板, 使百分表触头接触量块至指针零位,即可车削第二条螺旋槽。
圆周分线法
当车好第一条螺旋槽后,使工件与滑板之间的传动链分离,并 把工件转过α=360 /n角度,再接通传动链车另一条螺旋槽的方 法,称为圆周分线法。
利用卡盘卡爪分线:当工件在两顶尖装夹时,可用四爪单动卡盘或三爪 自定心卡盘的卡爪对二、三、四头的蜗杆或螺纹进行分线。分线时只需 要把顶尖松开,把工件连同夹头转动一个角度,由卡盘上另一卡爪拨动, 顶好顶尖后,即可车削另一条螺旋槽。 这种分线方法较简单,但精度不高,适用于齿面还需磨削的多线螺纹 (蜗杆)。
浅谈普通车床加工蜗杆的车削技巧
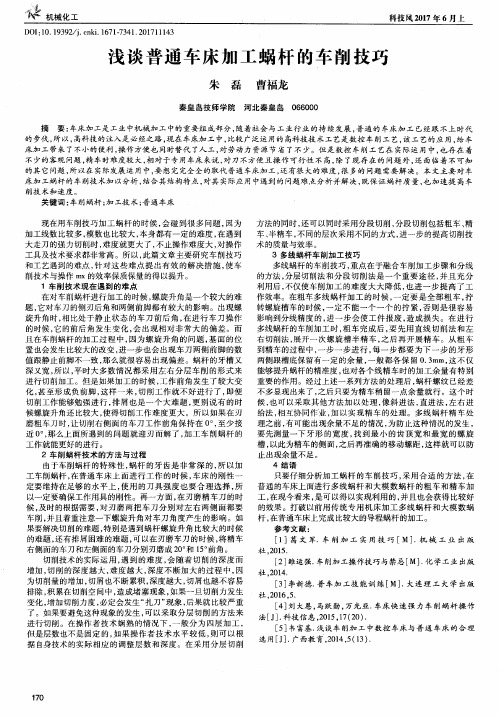
摘 要: 车床加工是工业 中机械加工 中的重要 组成部分 , 随着社会 与工业行 业的持 续发展 , 普通 的车床加 工 已经跟 不上 时代 的步伐 , 所 以, 高科技 的注入是 必经之路 , 现在 车床加 工 中, 比较广泛运用的 高科技技术工艺是数控 车削工 艺, 该工 艺的应 用 , 给 车 床 加工带来 了不小的便 利 , 操作方便也 同时替代 了人工 , 对 劳动 力资源 节省 了不 少。但是 数控 车削工 艺在 实际运 用 中, 也 存在 着 不少的客 观 问题 , 精车 时难度较 大, 相 对于专用车床 来说 , 对刀不方便且操 作可行 性不 高, 除 了现 存在 的问题 外 , 还面 ・ 临着不可知 的其它问题 , 所 以在 实际发展运 用中, 要 想完完全全 的取代普通 车床加 工, 还有很 大的难度 , 很 多的问题 需要解 决。本 文主要对 车 床加工蜗杆的车削技 术加以分析 , 结合其结构特点 , 对其 实际应 用中遇到 的问题难点分析并解 决, 既保证蜗杆 质量 , 也 加速提 高车
舐 鲁机 械 化 工
一
科 技 风 2 0 1 7 年 6 月 上
D O I : 1 0 . 1 94 1 . 2 0 1 7 1 1 1 4 3
浅 谈 普通 车 床 加工 蜗 杆 的车 削 技巧
朱 磊 曹福龙
河北秦皇 岛 0 6 6 0 0 0 秦 皇 岛技 师 学 院
削技 术 和 速 度 。
关键词 : 车削蜗杆 ; 加工技 术 ; 普通车床 现在用车削技巧加 工蜗 杆 的时候 , 会碰 到很多 问题 , 因为 加工线数 比较多 , 模数也 比较大 , 本身都有一定 的难度 , 在遇到 大走刀的强力切削 时 , 难度就更大 了, 不止操作难度 大 , 对操作 工具及技术要求都非常高。所以 , 此 篇 文 章 主 要 研 究 车 削 技 巧 和工艺遇到的难点 , 针对 这些难 点提 出有效 的解决 措施 , 使车 削技术与操作 m x的效率保质保量的得以提升。 1车 削 技 术 现 在 遇 到 的 难 点 在对车削蜗杆 进行 加工 的时候 , 螺旋升角是一个较大 的难 题, 它对车刀的侧 刃后 角和两侧 前脚都有较 大的影响 。出现螺 旋升角时 , 相比处于静止 状态 的车 刀前后 角 , 在 进行 车刀操作 的时候 , 它的前后角 发生 变化 , 会 出现相对非 常大 的偏差 。而 且在 车削蜗杆 的加 工过 程 中, 因为 螺旋升 角的 问题 , 基面 的位 置也会发生 比较大 的改变 , 进一步也会 出现 车刀两侧前脚 的数 值跟静止前脚 不一致 , 那么就很容易 出现偏差 。蜗杆 的牙槽 又 深 又宽 , 所 以, 平 时大多数 情况都 采用左 右分 层车削 的形 式来 进行 切削加工 。但是如果加工 的时候 , 工作 前角发生 了较 大变 化, 甚 至形 成负 前脚 , 这样一来 , 切 削工作就不 好进行 了 , 即便 切削工作能够勉强进行 , 排 屑也是 一个 大难题 , 更别 说有 的时 候螺旋升角还 比较大 , 使得切削工作 难度更大 。所 以如果在刃 磨粗车刀时 , 让切削右侧 面 的车刀工作前 角保持在 0 。 , 至 少接 近0 。 , 那么上面所遇到 的问题就迎 刃而解 了 , 加工 车削蜗 杆 的 工作就能更好 的进行 。 2 车 削 蜗 杆 技 术 的 方 法 与 过 程 由于车削蜗杆 的特殊性 , 蜗杆 的牙齿 是非 常深 的 , 所 以加 工车削蜗杆 , 在 普通车床 上面进 行工作 的 时候 , 车床 的刚性一 定要维持在足够 的水平上 , 使 用的刀 具强度 也要合 理选择 , 所 以一定要确保工作用具 的刚性 。再一 方面 , 在 刃磨精车刀 的时 候, 及时的根据需要 , 对刃磨 两把 车刀分 别对左 右两侧 面都要 车削 , 并且着重注意一下螺旋升角对车 刀角度产生 的影响。如 果要解决切 削的难题 , 特别是遇到蜗杆螺旋 升角 比较大 的时候 的难 题 , 还有排 屑困难 的难题 , 可 以在 刃磨车刀的时候 , 将 精车 右侧面的车刀和左侧面的车刀分 别刃磨成 2 0 。 和1 5 。 前 角。 切削技术的实际运用 , 遇 到 的难 度 , 会随着 切削 的深 度而 增加 , 切 削 的深 度越大 , 难度越 大 , 深 度不 断加大 的过 程 中, 因 为切削量的增加 , 切屑也不断 累积 , 深度越大 , 切 屑也越不容易 排除 , 积 累在切 削空间 中, 造成 堵塞现象 , 如果一旦切削力发生 变化 , 增加切削力度 , 必定会 发生“ 扎刀” 现象 , 后 果就 比较严重 了。如果要避免这种现象的发生 , 可 以采取分层切 削的方法来 进行切削 。在操作者 技术 娴熟 的情 况下 , 一般 分为 四层加 工 , 但是层数也不是 固定 的, 如果操 作者 技术水 平较低 , 则 可 以根 据 自身技术 的实 际相应 的调整 层数 和深度 。在 采用 分层切 削 方法 的同时, 还可 以同时采用分段切 削 , 分段切 削包 括粗 车 、 精 车、 半精车 , 不 同的层次采用不同 的方式 , 进一步 的提高切削技 术 的质 量 与 效 率 。 3 多线 蜗 杆 车 削 加 工 技 巧 多线蜗 杆的车削技巧 , 重点 在于融合车削加工步骤 和分线 的方法 , 分层切削法和分 段切 削法是一 个重 要途 径 , 并 且充 分 利 用后 , 不仅使车削加 工的难 度大大 降低 , 也进 一步提 高 了工 作 效率 。在粗车 多线蜗杆 加工 的时候 , 一定 要是 全部粗 车 , 拧 转螺旋 槽车的时候 , 一 定不 能一个一个 的拧 紧 , 否则是 很容 易 影响到分线精度 的, 进一 步会使 工件报 废 , 造 成损 失。在进 行 多线蜗杆的车削加工时 , 粗 车完成后 , 要 先用 直线切 削法 和左 右切削法 , 展开一 次螺旋 槽半精 车 , 之后再 开展精 车 。从粗 车 到精车的过程中 , 一 步一步 进行 , 每一 步都要 为下 一步 的牙形 两侧跟槽底保留有一定 的余 量 , 一般都 各保 留 0 . 3 m m, 这 不仅 能够提升蜗杆的精准度 , 也对各个线精车 时的加工余量 有特别 重要 的作用。经过上述一系列 方法的处理后 , 蜗杆螺 纹已经差 不多显现 出来 了, 之后 只要为精 车稍 留一点余量 就行。这个时 候, 也可 以采 取其他方 法加 以处 理 , 像斜 进法 , 直进 法 , 左右进 给法 , 相互协 同作业 , 加 以实现精 车 的处 理。多线 蜗杆精 车处 理之前 , 有可能 出现余量不 足的情况 , 为 防止这种情 况的发生 , 要先测量一下 牙形 的宽度 , 找 到最 小 的齿顶 宽 和最 宽 的螺旋 槽, 以此为精车 的侧面 , 之后再准确 的移动螺距 , 这样就可 以防 止 出现 余 量 不 足 。
蜗杆的车削与检验
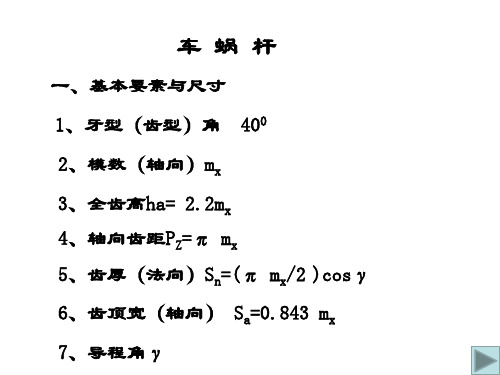
轴向齿廓:轴向剖面内的齿形轮廓为直线(齿条)状 法向齿廓:法向剖面内的齿形轮廓为曲线状 蜗杆蜗轮啮合传动轴向剖面内相当于齿轮齿条传动
轴向直廓蜗杆蜗轮传动---相当于齿轮齿条传动 蜗杆
蜗轮
N N
N-N 法向齿廓:法向剖面内的齿形轮廓为曲线状
2、法向直廓蜗杆
N
Hale Waihona Puke AAN法向齿廓:法向剖面内的齿形轮廓为直线状
偏差为 Φ36.5
-0.115 -0.380
,①求千分尺的读数M的范围。②当千分尺
的读数为40.660时,该螺纹的中径是否合格?
解: ①求量针直径
dD最佳= 0.518P=0.518×7=3.626mm 取量针直径为3.6毫米
②求M值
M=d2+4.864dD-1.866P=36.5
-0.115 -0.380
+4.864× 3.6-1.866 ×7
=40.948
-0.115 -0.380
即M的范围为40.833~40.568
因某螺纹的M值为40.660,在M的范围40.833~40.568之 外,故该螺纹的中径合格。
用单针法测螺纹中径 A= d0+M 2
A 0-25
举例
例1、用单针测量Tr36 × 6--8e的丝杆时,量得工件的实际外径
d0=35.95mm,中径的基本尺寸和极限偏差为33
-0.118 -0.543
mm,求单
针测量时A的范围?
解:①求量针直径
dD最佳= 0.518P=0.518×6=3.108mm
取量针直径为3.1毫米
②求M值
M=d2+4.864dD-1.866P=
33
-0.118 -0.543
《机加工实训(第3版)》电子教案 第十单元车削蜗杆、多线螺纹

课题一车削蜗杆
• 2)切槽法 • 当mx>3mm时,先用车槽刀将蜗杆直槽车至齿根处,然后再用粗车
刀粗车成形,如图10一6(b)所示。 • 3)分层切削法 • 当mx>5mm时,由于切削余量大,可先用粗车刀,按图10-6 (c)所示
方法,逐层地切入直至槽底。精车时,选用两边带有卷屑槽的精车刀, 将齿面精车成形,达到图样要求,如图10-6 (d)所示。 • 4.杆的测量方法 • (1)齿顶圆直径(公差较大)可用千分尺、游标卡尺测量;齿根圆直径一 般采用控制齿深的方法予以保证。 • (2)用三针和单针测量,方法与测量梯形螺纹相同。 • (3)齿厚测量法是利用齿厚游标卡尺测量蜗杆中径齿厚,如图10 -7所 示。此法适用于精度要求不高的蜗杆。
上一页 下一页 返回
课题一车削蜗杆
• 高速钢蜗杆车刀(右旋)的角度选取见表10 -2。 • (2)蜗杆车刀的装夹。 • ①车削轴向直廓蜗杆时,应采用水平装刀法,即装夹车刀时应使车刀
两侧刃组成的平面处于水平状态,且与蜗杆轴线等高。 • ②车削法向直廓蜗杆时,应采用垂直装刀法,即装车刀时,应使车刀
两侧刃组成的平面处于既过蜗杆轴线的水平面内,又与齿面垂直的状 态(见图10-3)。 • ③车削阿基米德蜗杆时,本应采用水平装刀法,但由于其中一侧切削 刃的后角变小,为使切削顺利,在粗车时也可采用垂直装刀法,但在 精车时一定要采用水平装刀法,以保证齿形正确。
ห้องสมุดไป่ตู้下一页 返回
课题一车削蜗杆
• 1. 蜗杆主要参数及技术要求 • (1)在轴向剖面内,蜗杆、蜗轮传动相当于齿条与齿轮间的传动,同
时蜗杆的各项基本参数也是在该剖面内测量并规定为标准值。 • 米制蜗杆的各部分名称、符号及尺寸计算见表10一1。 • (2)蜗杆的一般技术要求。 • ①蜗杆的周节必须等于蜗轮的周节。 • ②法向或轴向齿厚符合要求。 • ③齿形要符合图样要求,两侧面粗糙度要小。 • ④蜗杆径向跳动不得大于允许范围。
多头蜗杆工艺分析及快捷车削法
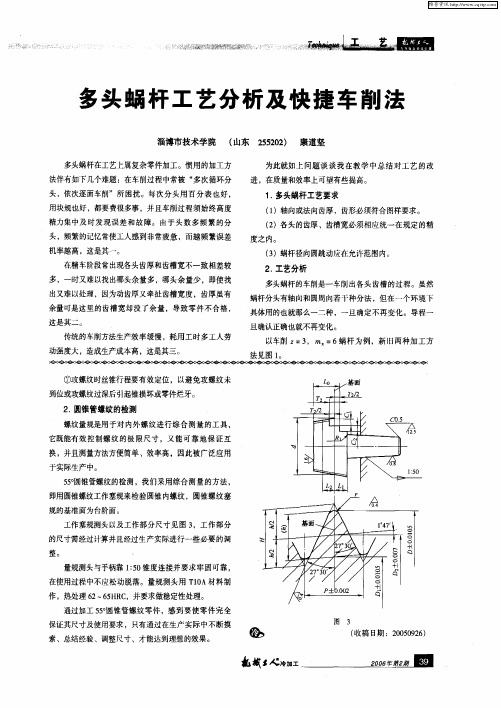
疆 礴 0
一
多头蜗 杆 工 艺分 析及 快 捷 车 削 法
淄博市技术学院 ( 山东 250 ) 康道坚 52 2
多头蜗杆在工艺上属复杂零件加工。惯用的加工方 法伴有如下几个难题:在车削过程中常被 “ 多次循环分 头, 依次逐面车削”所困扰。每次分头用百分表也好, 用块规也好 , 都要费很多事, 并且车削过程须始终高度 精力集中及时发现误差和故障。由于头数多频繁的分 头,频繁的记忆常使工人感到非常疲惫,而越频繁误差 为此就如上问题谈谈我在教学 中总结对工艺的改 进, 在质量和效率上可望有些提高。
1 多头蜗杆工艺要求 .
()轴向或法向齿厚 , 1 齿形必须符合图样要求。 ()各头的齿厚 、 2 齿槽宽必须相应统一在规定的精
度 之内。
机率越高, 这是其一。
在精车阶段常出现各头齿厚和齿槽宽不一致相差较
()蜗杆径向圆跳动应在允许范围内。 3
2 工艺分析 .
多头蜗杆的车削是一车削出各头齿槽的过程。虽然 蜗杆分头有轴向和圆周向若干种分法,但在一个环境下 具体用的也就那么一二种 ,一旦确定不再变化。导程一 旦确认正确也就不再变化。 以车削 =3 蜗杆为例,新旧两种加工方 ,m =6 法见图 1 。
2圆 . 锥管螺纹的检测
螺纹量规是用于对内外螺纹进行综合测量的工具, 它既能有效控制螺纹的极限尺寸,又能可靠地保证互
换, 并且测量方法方便简单、效率高,因此被广泛应用
于实 际生产 中。
5o 5圆锥管螺纹的检测, 我们采用综合测量的方法, 即用圆锥螺纹工作塞规来检验圆锥内螺纹,圆锥螺纹塞 规的基准面为台阶面。 工作塞规测头以及工作部分尺寸见图 3 ,工作部分 的尺寸需经过计算并且经过生产实际进行一些必要的调
如何进行高效的多线蜗杆车削加工
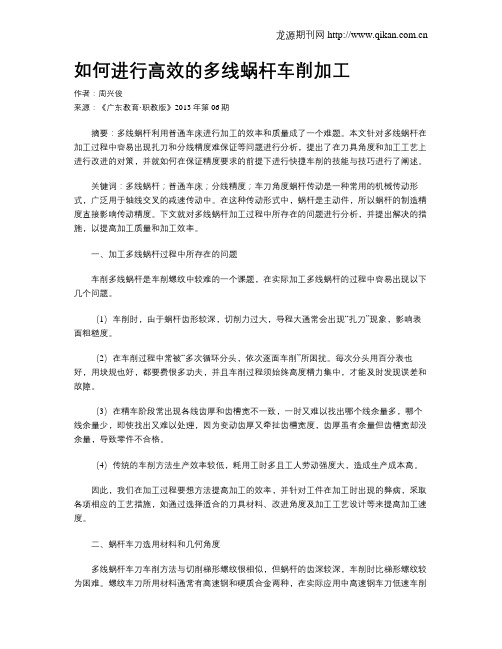
如何进行高效的多线蜗杆车削加工作者:周兴俊来源:《广东教育·职教版》2013年第06期摘要:多线蜗杆利用普通车床进行加工的效率和质量成了一个难题。
本文针对多线蜗杆在加工过程中容易出现扎刀和分线精度难保证等问题进行分析,提出了在刀具角度和加工工艺上进行改进的对策,并就如何在保证精度要求的前提下进行快捷车削的技能与技巧进行了阐述。
关键词:多线蜗杆;普通车床;分线精度;车刀角度蜗杆传动是一种常用的机械传动形式,广泛用于轴线交叉的减速传动中。
在这种传动形式中,蜗杆是主动件,所以蜗杆的制造精度直接影响传动精度。
下文就对多线蜗杆加工过程中所存在的问题进行分析,并提出解决的措施,以提高加工质量和加工效率。
一、加工多线蜗杆过程中所存在的问题车削多线蜗杆是车削螺纹中较难的一个课题,在实际加工多线蜗杆的过程中容易出现以下几个问题。
(1)车削时,由于蜗杆齿形较深,切削力过大,导程大通常会出现“扎刀”现象,影响表面粗糙度。
(2)在车削过程中常被“多次循环分头,依次逐面车削”所困扰。
每次分头用百分表也好,用块规也好,都要费很多功夫,并且车削过程须始终高度精力集中,才能及时发现误差和故障。
(3)在精车阶段常出现各线齿厚和齿槽宽不一致,一时又难以找出哪个线余量多,哪个线余量少,即使找出又难以处理,因为变动齿厚又牵扯齿槽宽度,齿厚虽有余量但齿槽宽却没余量,导致零件不合格。
(4)传统的车削方法生产效率较低,耗用工时多且工人劳动强度大,造成生产成本高。
因此,我们在加工过程要想方法提高加工的效率,并针对工件在加工时出现的弊病,采取各项相应的工艺措施,如通过选择适合的刀具材料、改进角度及加工工艺设计等来提高加工速度。
二、蜗杆车刀选用材料和几何角度多线蜗杆车刀车削方法与切削梯形螺纹很相似,但蜗杆的齿深较深,车削时比梯形螺纹较为困难。
螺纹车刀所用材料通常有高速钢和硬质合金两种,在实际应用中高速钢车刀低速车削螺纹较多。
因为高速钢车刀刃磨方便,切削刃锋利,韧性好,能承受较大的冲击力,低速车削时可获得较低的表面粗糙度值。
在数控车床上快速车削蜗杆的方法

在数控车床上快速车削蜗杆的方法在数控车床上车削较大导程的蜗杆、梯形螺纹和锯齿螺纹,由于工件的齿形深,需要切除的毛坯余量多,一般是选择较低的切削速度和高速钢成形刀,使用G32和G76等指令车削,加工精度特别是表面粗糙度很难达到图纸要求,加工难度较大.针对出现的加工精度低、生产效率低等特点,说明如何有效地发挥数控车床的高精度,高速度、定位精度高、生产效率高的优势.我们以沈阳CAK3675v华中数控系统的车床来论述快速车削蜗杆的方法.如图1蜗杆数控车床成形刀硬质合金宏程序蜗杆和大导程螺纹车削的进刀方法有多种,如直进法、左右切削法、斜进法和切槽法等.以前车削蜗杆等大导程零件的方法是:选用较低主轴转速数控车床最低速为100转/分时转动无力和高速钢成形车刀,车削蜗杆时的生产效率低.为解决上述问题,我认为应从刀具材料、几何形状及角度和车削方法来谈谈快速车削蜗杆和大导程螺纹的方法.一、突破传统选择刀具的习惯,合理选择车削蜗杆的刀具角度,使刀具的刀尖角小于齿形角车削蜗杆刀具的刀尖角如果等于蜗杆的齿形角.这种刀具在车削时两侧刀刃与工件侧面容易发生摩擦,甚至三个刀刃同时参加切削,易产生较大的切削力而损坏刀具.如果选择车刀的刀尖角35小于蜗杆的齿形角40,如图2这种车刀在车削时,可防止三个刀刃同时参加切削,减少了摩擦、切削力,能很好地避免“闷车”、“扎刀”和打刀的情况发生.二、在数控车床上使用硬质合金车刀高转速车削蜗杆成为现实以前,车削加工蜗杆和大导程螺纹,只能用高速钢车刀低速车削加工,生产效率非常低.如果将车刀的刀尖角磨小,使车刀的刀尖角35小于蜗杆的齿形角40,可避免三个刀刃同时参加切削,切削刀显剧下降,这时可使用较高的切削速度和硬质合金车刀对蜗杆进行车削.当工件直径、导程越大时,可获得的线速度越高,加工出的工件表面质量越好,而且生产效率明显提高.彻底解决在数控车床不能用硬质合金刀具车削蜗杆和大导程螺纹零件.只要数控车床能承受,尽可能选择较高的线速度,在车削模数Ms=4时,选用350转/分钟.如图3图2 刀尖角35小于齿形角40 图3 硬质合金车刀三、利用数控车床的精度高、定位准,用车削斜面的方法代替成形刀车削蜗杆,能保证蜗杆的齿形角如果蜗杆车刀的刀尖角直接决定被加工螺纹牙形角的大小,这显然是用成形刀来车削蜗杆.当使用成形刀车削较大导程蜗杆工件时,有可能整过刀刃甚至是三个刀刃同时参加切削,切削力陡增.由于数控车床在低转速转动时无力,用成形刀在数控车床上车削蜗杆或大导程螺纹会出现“闷车”和“扎刀”.为解决以上问题,可用左右分层车削斜面的方法取代成形刀法来车削蜗杆和大导程螺纹,可彻底避免在车削中经常出现三个刀刃同时参加切削而导致切削力增大、排屑不畅、“闷车”和“扎刀”等现象.车削斜面的方法是:车螺纹时,车刀在第一次往复车削后,刀尖在通过轴线剖面的牙侧上车削出了A点,经过多次往复循环车削,刀尖在通过轴线剖面的牙侧上分别车削出了B、C、D、E、F……N个点,将ACEN和BDF等多个点分别连接起来成为两条倾斜的直线,形成了蜗杆两侧的齿面和齿形角.如图4图4 蜗杆齿侧的形成四、使用宏程序能满足加工加工要求粗车如图1模数Ms=4的蜗杆,大约只需10分钟左右.粗车蜗杆的加工宏程序如下:%0001T0303M03S350F1001=蜗杆全齿高2=齿根槽宽W=3= 刀头宽t=WHLIE 1GE04=12+ 计算X轴尺寸.齿根圆为5=1TAN20PI/1802+2 计算Z轴尺寸WHLIE 5GE3G00 X50 Z8 M08 循环起点G00 Z8+5-3/2 Z轴向右边移动G82 X4 Z-87 车蜗杆G00 Z8-5-3/2 Z轴向右边移动G82 X4 Z-87 车蜗杆5=5-3 每次循环的切削宽度ENDW1= 每次循环的切削深度ENDWG0X150Z8M09M30精车时必须修改粗车的宏程序如下:1、测量粗车后的法向齿厚Sn/Cos20=Sx轴向齿厚.2、将宏程序的程序段2=修改为2=+ Sx/2轴向齿厚/23、将宏程序的程序段1=修改为1=4、将宏程序的WHLIE 5GE3、5=5-3、ENDW删除.5、将修改后的宏程序重新调用加工一次,精车蜗杆大约只需10分钟左右.修改后,精车蜗杆宏程序如下:%0001T0303M03S350F1001=蜗杆全齿高2=+ Sx/2 齿根槽宽+轴向齿厚Sx/23= 刀头宽t=WHLIE 1GE04=12+ 计算X轴尺寸.齿根圆为5=1TAN20PI/1802+2 计算Z轴尺寸G00 X50 Z8 M08 循环起点G00 Z8+5-3/2 Z轴向右边移动G82 X4 Z-87 车蜗杆G00 Z8-5-3/2 Z轴向右边移动G82 X4 Z-87 车蜗杆1= 每次循环的切削深度ENDWG0X150Z8M09M30五、结束语在数控车床上快速车削蜗杆和大导程螺纹的方法有三个特点:一是摆脱了在普通车床上车削蜗杆要求工人有较高的操作技能和技巧.二是解决了数控车床不能车削大导程的蜗杆和螺纹.三是充分利用了数控车床的精度高、定位准的特点,突破了传统的选择蜗杆车刀的习惯,将刀具的刀尖角选得小于齿形角,车削时防止了三个刀刃同时参加切削,排屑顺利,减小了切削力,使用硬质合金车刀,高速切削蜗杆和大导程螺纹成为现实在数控车床上加工较大直径和较大导程的蜗杆优势更大.粗车和精车如图1的蜗杆大约需要20分钟左右的时间,生产效率有了较大的提高,是普通车床的10倍左右.在数控车床上车削蜗杆和大导程螺纹注意三点:一是要求有编辑和修改宏程序、准备车刀和安装工件的能力.二是用硬质合金车刀车削梯形螺纹,不能选用过高的主轴转速,应考虑车床的承受能力.如车削模数Ms=4的蜗杆,主轴转速可选350转/分左右,否则,会由于大滑板换向太快而影响车床丝杆和螺母的精度.三是如果被切削的工件直径较小,车削时的线速度较低,车削出齿侧的表面粗糙度只能达到左右.当车削较小直径的工件时,可在数控车床上粗车,留下较小的精车余量,然后选用高速钢车刀低速精车来解决工件的表面粗糙度.资料来源。
蜗杆怎么加工-蜗杆的加工工艺

蜗杆怎么加工| 蜗杆的加工工艺内容来源网络,由“深圳机械展(11万㎡,1100多家展商,超10万观众)”收集整理!更多cnc加工中心、车铣磨钻床、线切割、数控刀具工具、工业机器人、非标自动化、数字化无人工厂、精密测量、3D打印、激光切割、钣金冲压折弯、精密零件加工等展示,就在深圳机械展.在经济全球化的格局下,我国制造业发展越来越迅速,齿轮的使用范围也越来越广泛,齿轮中的蜗轮蜗杆对其传递与转换的作用也是别的齿轮无法代替的。
那么蜗杆是怎么加工?它的加工工艺又是什么?本文,贤集网小编主要就是讲的这些内容!蜗杆的加工工艺1、确定毛坯的材料⑴具有优良的加工性能,能得到良好的表面光洁度和较小的残余内应力,对刀具磨损作用较小。
⑵抗拉极限度一般不低于588MPa。
⑶有良好的热处理工艺性,淬透性好,不易淬裂,组织均匀,热处理变形小,能获得较高的硬度,从而保证蜗杆的耐磨性和尺寸的稳定性。
⑷材料硬度均匀,金相组织符合标准。
常用的材料有:T10A,T12A,45,9Mn2V,CrMn 等。
其中9Mn2V有较好的工艺性和稳定性,但淬透性差;优点是热处理后变形小,适用于制作高精度零件,但其容易开裂,磨削工艺性差,蜗杆的硬度越高越耐磨,但制造时不易磨削。
2、加工定位基面的选择蜗杆定位基面:从结构上分,蜗杆有两种形式,套装蜗杆,整体蜗杆。
套装蜗杆以内孔加工基面,因此应先精加工内孔,然后以内孔为基面加工外圆及支承轴颈,螺纹的加工同样以内孔为基面,因此需要心轴。
一般精密分度蜗杆的内孔精度要求是很高的,有的需要进行研磨老保证精度。
一般精度分度蜗杆内孔应不低于1级精度,表面粗糙度不低于0.12,内孔的端面振摆应不小于0.005mm。
蜗杆装在心轴上加工时,应首先检查两端轴肩的径向跳动是否在规定允差之内,以后每道工序均应校验,在蜗杆装配时,同样要校验两端轴肩的径向跳动,心轴精度必须等于或高于与套装蜗杆相配的轴精度。
整体蜗杆以中心孔为加工基面,对中心孔的要求很高,应该有保锥,保证光洁度和接触面积,每道工序前要检查和修正中心孔,对支承轴颈应保证与中心孔同轴度和本身的几何精度,在半精加工和精加工工序前,都应检查支承轴颈的径向,跳径和端面的轴向振摆是否在公差以内。
- 1、下载文档前请自行甄别文档内容的完整性,平台不提供额外的编辑、内容补充、找答案等附加服务。
- 2、"仅部分预览"的文档,不可在线预览部分如存在完整性等问题,可反馈申请退款(可完整预览的文档不适用该条件!)。
- 3、如文档侵犯您的权益,请联系客服反馈,我们会尽快为您处理(人工客服工作时间:9:00-18:30)。
利用普通车床加工多头蜗杆,有其一定的技术难度,现以三头蜗杆的车削加工为例,说明车削加工技术特点。
三头蜗杆的零件图如图1所示,轴向模数为3mm,材料为45钢。
在车削时,由于齿形深、切削面大、导程角大、车刀走刀速度快,增加了切削难度。
一、三头蜗杆结构分析
1.分线精度高
图1所示的三头蜗杆,在车削时要对蜗杆进行分线,如果分线出现误差,使车的蜗杆周节不相等,则会直接影响蜗杆与涡轮的啮合精度,增加不必要的磨损,降低使用寿命。
2.齿槽深
由于全齿高h=2.2mm,m=2.2×3=6.6mm,所以车削时要求车刀反复单边多次插入6.6mm,容易在车削中“扎刀”,因此,对刀具的刚性和强度、韧性有较高的要求。
3.导程大、刀具强度低
由tanγ=l/πda=(3.14×3×3)/(3.14×4×36),可得γ=14°。
因此刀具顺走刀方向的后角=14°+3°=17°,导致刀具强度急剧降低。
4.刀具速度快
图1所示的蜗杆导程l=zmπ=28.275mm,蜗杆长度仅为60mm,刀具走刀速度快,极易造成车刀与卡盘和尾座相撞。
5.切屑排出困难
由于导程大、齿槽深,在加工时又受导程角的影响,螺纹的待加工表面旋转时挡住了切屑,使切屑排出困难。
二、刀具材料和刀具角度选取原则
1.刀具材料选取原则
2.刀具角度选取原则
为了提高蜗杆的加工质量,车削时应采用粗车和精车两阶段,采用4把刀加工,即蜗杆粗车刀、齿根槽精车刀、左及右两侧面精车刀各一把。
(1)蜗杆粗车刀(右旋),如图2所示。
因此,按下列原则选择蜗杆粗车刀:①车刀左右切削刃之间的夹角要大于齿形角,主要是为了控制精车余量,因车削此蜗杆的齿形角为40º,所以车刀左右切削刃之间的夹角可选择40º30′。
②切削钢件时,应磨有10º~15º的径向前角。
③径向后角应为6º~8º。
④进给方向的后角为(3º~5º)+γ,背着进给方向后角为(3º~5º)-γ,因为此蜗杆的导程角为14°,所以进给方向的后角可取17°~19°,背着进给方向的后角可取-12°~-9°。
⑤为了便于左右切削,并留有精加工余量,刀头宽度应小于齿根槽宽。
⑥刀尖适当倒圆。
(2)齿根槽精车刀,如图3所示。
按下列原则选择齿根槽精车刀:①车刀的刀头宽度与齿根槽宽度必须相等。
②为了避免刀具刮伤已车好的表面,左右切削刃之间的夹角要小于40°,可取39°左右。
(3)左右两侧刃分别精车刀(右侧刃),如图4所示。
按下列原则选择精车刀(右侧刃):①车刀左侧刃与刀柄中心线夹角等于齿形半角,车刀的右侧刃不参与切削,又为了避免刀刃与齿面接触,车刀右侧刃与刀柄中心线夹角可小于齿形半角。
切削刃的直线度要好,表面粗糙度值要小。
②为了保证齿形角的正确,一般径向前角取0º~4º。
③为了保证切削顺利,都应磨有较大纵向前角(γ0=15º~20º)。
左侧刃精车刀的刀具角度与右侧刃相似。
特别指出的是:这种车刀的前端刀刃不能进行
切削,只能依靠两侧刀刃精车两侧齿面。
三、切削液的选取
在车蜗杆的过程中采用的切削液是用纯碱与皂粉的比为3∶1(约1.5kg)加水30kg混合稀释而成,该切削液主要特点是可以使切屑顺利排出,散热效果明显,加工表面光洁,切削时没有油烟影响等优点。
四、三头蜗杆实际加工过程
三头蜗杆的轴向模数为m=3mm,齿形角为20º,螺旋线方向为右旋,导程角为14°,工件材料为45钢,毛坯为热轧圆钢,尺寸为φ50×190mm。
在机械加工前,安排调质处理t235。
工序安排应将粗车、精车分开,工件装夹要牢固。
1.粗车各外圆
(1)用三爪自定心卡盘装夹毛坯外圆,伸长约110mm,车平端面,粗车蜗杆外圆φ44×106mm。
φ28mm的外圆至φ30×41.5mm。
φ25的外圆至φ27×17.5mm。
(2)掉头夹工件φ44的外圆,校正后夹紧悬伸长度约70mm,车端面,保证总长187mm。
(3)粗车φ20的外圆至φ22×29.5mm,粗车φ25的外圆至φ27×21.5mm。
车φ28的外圆至φ30×23mm。
2.热处理,调质t235(略)
3.半精车外圆
(1)用三爪自定心卡盘装夹φ44外圆并校正。
车两端面钻中心孔(a3/6)。
中心孔表面粗糙度值要小且圆整。
保证总长达尺寸要求。
(2)采用一夹一顶的装夹方式,半精车外圆。
①车左端台阶。
外圆各留精车余量1mm,长度至尺寸要求。
②工件调头,车右端台阶。
外圆各留精车余量1mm,长度至尺寸要求。
4.半精车蜗杆外圆,粗车蜗杆
(1)调整车床。
准备刀具。
(2)按模数×头数(3×3)。
调整车床挂轮和各手柄位置。
(3)采用一夹一顶装夹方式。
夹右端φ20mm外圆使台阶紧贴卡爪。
百分表校正蜗杆外圆调动量控制在0.02mm以内并夹紧。
顶尖顶一端。
半精车蜗杆外圆至φ42.5mm及两端倒角20°。
(4)粗车蜗杆。
蜗杆有关参数值见表1。
①为了提高加工速度和质量,笔者采用开倒、顺车的切削方法,先用切槽刀在工件表面先车三条螺旋槽,切槽刀的宽度a≈p-(fx+0.5)=0.843mx+0.5=6.4mm。
槽深0.1mm。
在装刀时,要保证主切削刃与工件轴线平行。
②蜗杆刀的装夹。
粗车蜗杆时使用如图2所示的刀具。
在装夹蜗杆刀时比较困难,容易把车刀装歪。
在装刀时可以用样板对刀,也可以用万能角度尺对刀。
笔者用百分表进行对刀,如图5所示。
使百分表触头与刀柄侧面接触,然后摇动中拖板,如果表的指针都处于同一位置,说明刀的角度已装好。
用此种方法对刀,要求在磨刀时采用的样板如图6所示。
此样板要求b面与c面平行,a面与b面、c面垂直。
③分线方法。
笔者采用的是轴向分线法,先调整好小拖板与机床导轨平行度后,利用小滑板刻度确定直线移动分线,在车好一条螺旋槽后,利用小滑板刻度配合百分表使车刀移动一个螺距,再车相邻的另一条螺旋槽,从而达到分线的目的。
④车削方法。
采用开倒、顺车方法切削。
并使蜗杆的粗车刀在刚车好的槽的范围内进行左右切削。
车好第一螺旋槽以后,再车第二条、第三条、螺旋槽,由于刚才切槽刀宽度已经控制蜗杆槽粗车的宽度,所以能控制好每单边都留0.2mm的精车余量,如图7所示。
5.精车蜗杆
(1)用两顶尖装夹。
先精车蜗杆外圆至φ42mm,表面粗糙度ra3.2μm,去除蜗杆表面和两端毛刺。
(2)采用图4所示左、右两侧刃精车刀。
用百分表校正左侧(背走刀方向)精车刀并对刀,低速精车第一条螺旋槽右侧面至车刀主刀刃与齿根圆相触及,表面粗糙度达规定要求,记录中滑板进刀刻度值为0。
若表面粗糙度不够理想则可使用小拖板赶刀、修光,但须保证齿厚单边余量不得小于0.1mm。
然后以百分表和小拖板刻度配合作轴向分线,使小拖板移动一个齿距,用直进法精车第二条螺旋槽同方向侧面,直至到记录中拖板进刀刻度处,表面粗糙度达要求。
用同样方法车好第三条螺旋槽。
精车牙面的加工顺序:1槽牙侧a面→2槽牙侧c面→3槽牙侧e面→3槽牙侧f面→2槽牙侧d面→1槽牙侧b面,如图8所示。
(3)换刀,用百分表校正右侧精车刀并对刀,按(2)所述方法低速精车齿槽左侧面,并用齿厚卡尺测量,保证法向齿厚尺寸为4.57mm,记录中拖板刻度值。
完成后,用相同方法作轴向分线,车削第二、第三条螺旋槽左侧齿面,使其齿厚与前者相等,表面粗糙度达ra1.6μm。
精车除了要细心之外,还应熟练掌握“多次循环分线,依次逐面车削”原则。
为保证加工质量,精车时应采取以下措施:
①切削厚度:精车齿槽两侧面切削深度要小(尤其是最后两刀),ap=0.01~0.02mm,使车下的切屑如铝箔一样薄而发亮,每走一刀都要仔细观察和分析排屑情况,判断车刀是否保持锋利。
②切削速度:精车蜗杆时主轴转速要放慢。
转速过高,齿面表面粗糙度难以保证,一般n以10r/min为宜。
③要充分浇注切削液。
④勤测量:由于分线误差、车刀磨损、让刀等诸多因素,易造成多头蜗杆齿距误差,精车时应勤用单针测量法控制蜗杆分度圆直径,力求各头一致,还要用齿厚卡尺测量蜗杆各头齿厚并作记录。
最后利用小拖板赶刀进行修正,使各头齿厚相等,使齿距得到保证。
最后用图3所示的齿根槽精刀精车第一、二、三线齿根圆直径至尺寸φ28.8mm。
6.精车各台阶外圆至规定尺寸
表面粗糙度达要求;倒角1×45°。
加工三头蜗杆的过程表明,合理选用刀具和加工工艺,即使对难度大的零件,也可顺利完成并能在加工技术上有所突破,操作技能可以迅速提高。