进货检验控制流程图
进料检验控制程序

进料检验控制程序1、目的为保证来料的质量、数量、规格等符合本公司的要求,提供良好的物料,满足生产之所需,特制定本程序。
2、范围适用于公司所有原材料、辅助材料,外发加工品的检验管理。
3、术语与定义来料检验:对供应商提供的原材料、辅助材料,或由外协加工商协助加工的产品进行的检验。
4、来料检验控制过程风险乌龟图5、工作流程和内容6、附加说明6.1控制措施:6.1.1供应商来料要附带产品质量检验报告。
6.1.2供应商与组织签订技术协议、质量保障协议等技术要求。
6.1.3出现质量索赔依据《质量索赔流程》进行处理。
6.2进货异常处理:A、来料检验批合格率低于99.73%时,采购工程师和质量工程师联系供应商来厂处理并制定处置方案。
B、来料为同一供应商同一物料检验连续3批拒收;不同物料,同一供应商物料检验连续5批拒收,采购要发《8D报告》给供应商进行改善。
质量检验员要对拒收物料进行加严检查。
C、供应商改善合格后要返回《8D报告》,改善后的物料检验连续五批合格方可恢复正常检验抽样。
D、如果供应商改善后连续五批中有一批不合格,则继续改善;五批次中有两批和两批以上物料拒收则重新考核供应商。
7、参考文件《不合格品管理程序》《库房管理程序》《记录管理程序》《文件管理程序》《产品标识和追溯程序》《检验抽样准则》《检验抽样表》8、使用表单8.1《采购订单》8.2《进货验证记录》8.3《采购入库单》8.4《合格标签》8.5《不合格标签》8.6《供应商物料检验反馈报告》8.7《不合格品处置单》8.8《8D报告》。
外购件及自制件检验控制程序含流程图
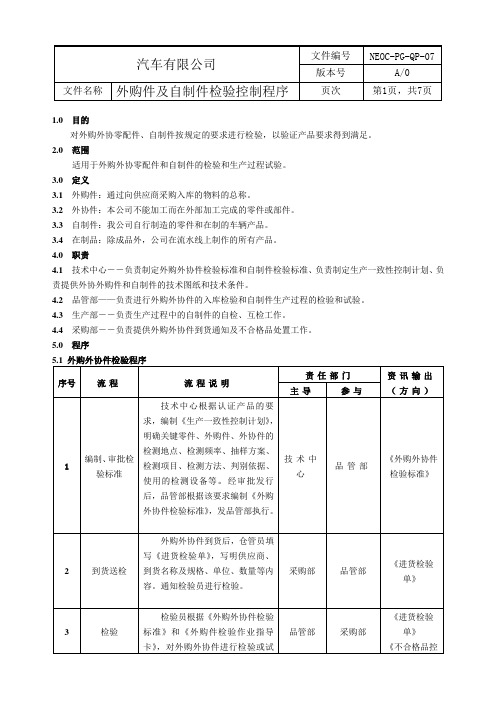
1.0目的
对外购外协零配件、自制件按规定的要求进行检验,以验证产品要求得到满足。
2.0范围
适用于外购外协零配件和自制件的检验和生产过程试验。
3.0定义
3.1外购件:通过向供应商采购入库的物料的总称。
3.2外协件:本公司不能加工而在外部加工完成的零件或部件。
3.3 自制件:我公司自行制造的零件和在制的车辆产品。
3.4 在制品:除成品外,公司在流水线上制作的所有产品。
4.0职责
4.1 技术中心――负责制定外购外协件检验标准和自制件检验标准、负责制定生产一致性控制计划、负责提供外协外购件和自制件的技术图纸和技术条件。
4.2 品管部——负责进行外购外协件的入库检验和自制件生产过程的检验和试验。
4.3 生产部――负责生产过程中的自制件的自检、互检工作。
4.4 采购部――负责提供外购外协件到货通知及不合格品处置工作。
5.0程序
附录1:
附录2:。
产品质量检验管理程序(含流程图)
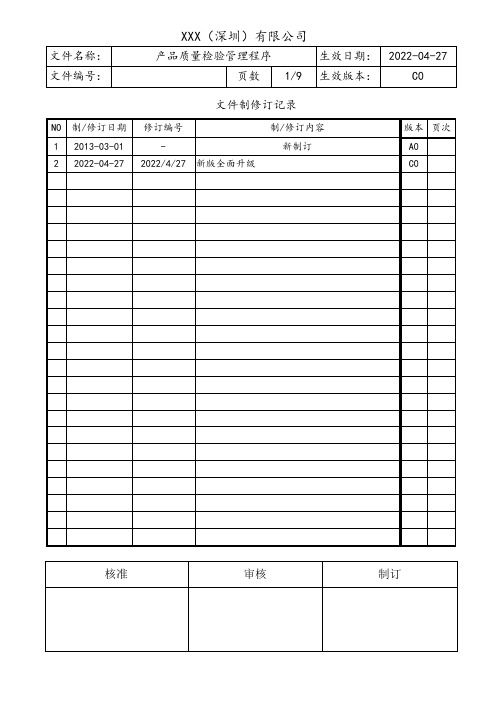
文件制修订记录1.0目的为了有效测量与监控产品从进料、制程、成品及出货各阶段检验作业能始终符合产品工程规范的各项要求。
2.0范围:适用于品管IQC、IPQC、QA过程作业。
3.0权责:3.1品管部:负责各阶段品质检验的执行、标识、追溯的管理、实际验货。
3.2工程部:产品作业标准的制定与检查。
3.3生产部:依生产计划、工程标准、验收标准执行生产作业。
3.4业务部:依订单需求验收出货数量。
3.5资材部:采购物料的外部联络。
4.0定义:无5.0作业内容:5.1进料检验5.1.1收料5.1.1.1供应商依据采购订单交货到公司仓库。
5.1.1.2仓管依据采购订单核对送货单是否一致,如若不符则退货并要求供应商重新交货,符合则点收数量并开出[进货单]。
5.1.1.3仓管将[进货单]连同要求供应商提供的相关文件(如材质报告、检验报告、测试报告等)交品管部,通知IQC进行检验。
5.1.1.4检验参照依据AQL表或依客户端需求作抽样检验。
5.1.1.5品管部IQC接到[进货单]后对供应商所提供的文件进行验证,(有法规环保类要求的产品必须依客户指定或经国家认可有检测能力机构出具的测试报告,如“SGS报告”等);品管部可以根据批量大小、价值贵重程度来对供应商所提供产品的材质进行一次确认。
5.1.1.5下列几项物料必须由品管部进料检验:a)生产性原材料。
b)外发加工产品。
c)包装材料等。
5.1.2需应用下列一种或多种方法进行验收、检验5.1.2.1接收检验及测试:a)核对材质证明(限自购原材料,样品或来料加工产品可不需要提供材质证明),核对供应商提供的相关文件。
b)依《检验标准书》逐项检验与填写[进料检验报告],无《检验标准书》时,依图面求或样板检验,检验结果可直接记录于[进料检验报告]上。
c)凡属客户提供来料进行加工,如无图面,依据客户提供的规格进行检验;如既无规格又无图面,IQC只针对其外观进行检验并记录于[进料检验报告]上。
检验和测量的控制程序
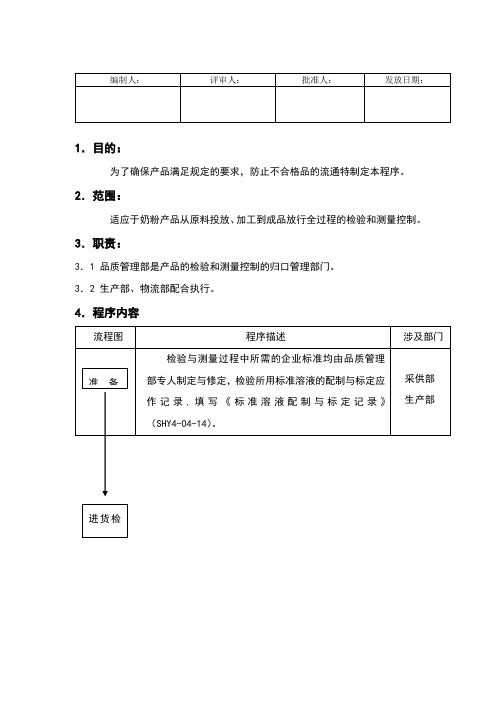
1.目的:
为了确保产品满足规定的要求,防止不合格品的流通特制定本程序。
2.范围:
适应于奶粉产品从原料投放、加工到成品放行全过程的检验和测量控制。
3.职责:
3.1 品质管理部是产品的检验和测量控制的归口管理部门。
3.2 生产部、物流部配合执行。
4.程序内容
5. 参考文件:
《质量手册》
《产品标识和可追溯性控制程序》 SHY(Q)2-10《不合格品的控制程序》 SHY(Q)2-18 《原材料、产品检验执行标准》 SHY3-04-07
6.引用表格:
《奶粉理化检验原始记录(一)、(二)》 SHY4-04-01《奶粉检验报告单》 SHY4-04-02《奶粉卫生检验原始记录》 SHY4-04-03《原材料初检报告单》 SHY4-04-04《部门取样单(原料)》 SHY4-04-12《生产过程控制巡检表》 SHY4-04-10《—班—日奶粉包装质量考核表》 SHY4-04-11《成品检验记录》 SHY4-04-22《成品检验报告单》 SHY4-04-23《部门取样单(成品)》 SHY4-04-16《标准溶液配制与标定记录》 SHY4-04-14《-库房巡检表》 SHY4-04-26。
产品检验流程图

文件编号:
序号
节点检验
责任部门
相关检验内容说明
文件/记录
1
生产检验
任务单
技术部门
采购部门
质检部门
生产、技术、质检进行合同评审,图纸审核发放,制定相应的采购进度计划,生产计划,技术工艺检验标准实施
《采购物料清单》
图纸技术工艺文件
检验标准发放
2
编制实施质检计划标准文件
检验部门
依据采购物料单与生产计划表编制产品检验计划
6
缺陷分析与修订
检验部门
技术部
检验过程中发现的问题,做出质量问题纠正和预防措施,及时修订技术检验标准
《纠正和预防措施程序》
《检验标准》
产 品 检 验工 作流 程 图
生产部门
检验合格后,流入下道工序生产
5
成品检验
检验部门
根据产品出货检验程序实施检验 并做好记录
《出货检验程序》
《产品出货检验单》
《质量问题返馈单》
《不合格品处置单》
成品出库单
技术部门
发现不合格品由技术部审核按《不合格品控制程序》执行
采购部门
经技术判定不合格品需通知返修与退货处理
库管人员
经检验合格的产品,需办理入库,准备发货
采购部
经技术部判定不符合的产品通知返修与退货处理
库管人员
检验合格的材料与外协件,交仓库人员办理入库
4
控制点工
序检验
检验部门
根据过程检验程序,实施首检 巡检记录,发现问题填写质量问题反馈单,
《过程检验程序》
《产品巡检记录表》
《质量问题反馈单》
《不合格品控制程序》
技术部门
进厂原料质量控制流程
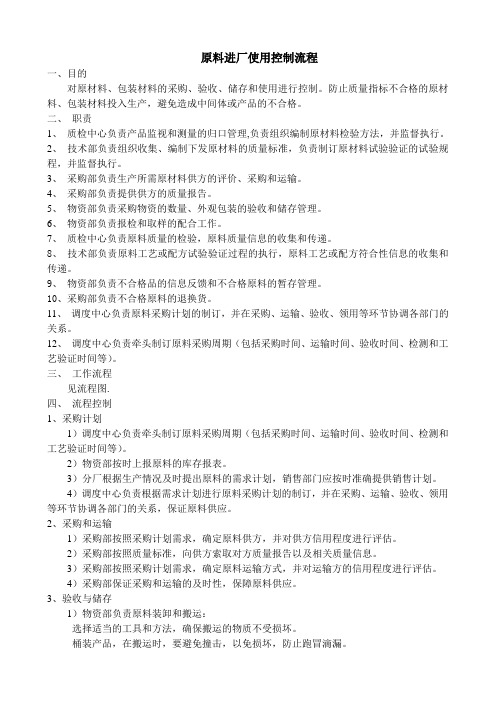
原料进厂使用控制流程一、目的对原材料、包装材料的采购、验收、储存和使用进行控制。
防止质量指标不合格的原材料、包装材料投入生产,避免造成中间体或产品的不合格。
二、职责1、质检中心负责产品监视和测量的归口管理,负责组织编制原材料检验方法,并监督执行。
2、技术部负责组织收集、编制下发原材料的质量标准,负责制订原材料试验验证的试验规程,并监督执行。
3、采购部负责生产所需原材料供方的评价、采购和运输。
4、采购部负责提供供方的质量报告。
5、物资部负责采购物资的数量、外观包装的验收和储存管理。
6、物资部负责报检和取样的配合工作。
7、质检中心负责原料质量的检验,原料质量信息的收集和传递。
8、技术部负责原料工艺或配方试验验证过程的执行,原料工艺或配方符合性信息的收集和传递。
9、物资部负责不合格品的信息反馈和不合格原料的暂存管理。
10、采购部负责不合格原料的退换货。
11、调度中心负责原料采购计划的制订,并在采购、运输、验收、领用等环节协调各部门的关系。
12、调度中心负责牵头制订原料采购周期(包括采购时间、运输时间、验收时间、检测和工艺验证时间等)。
三、工作流程见流程图.四、流程控制1、采购计划1)调度中心负责牵头制订原料采购周期(包括采购时间、运输时间、验收时间、检测和工艺验证时间等)。
2)物资部按时上报原料的库存报表。
3)分厂根据生产情况及时提出原料的需求计划,销售部门应按时准确提供销售计划。
4)调度中心负责根据需求计划进行原料采购计划的制订,并在采购、运输、验收、领用等环节协调各部门的关系,保证原料供应。
2、采购和运输1)采购部按照采购计划需求,确定原料供方,并对供方信用程度进行评估。
2)采购部按照质量标准,向供方索取对方质量报告以及相关质量信息。
3)采购部按照采购计划需求,确定原料运输方式,并对运输方的信用程度进行评估。
4)采购部保证采购和运输的及时性,保障原料供应。
3、验收与储存1)物资部负责原料装卸和搬运:选择适当的工具和方法,确保搬运的物质不受损坏。
进货检验流程及规范
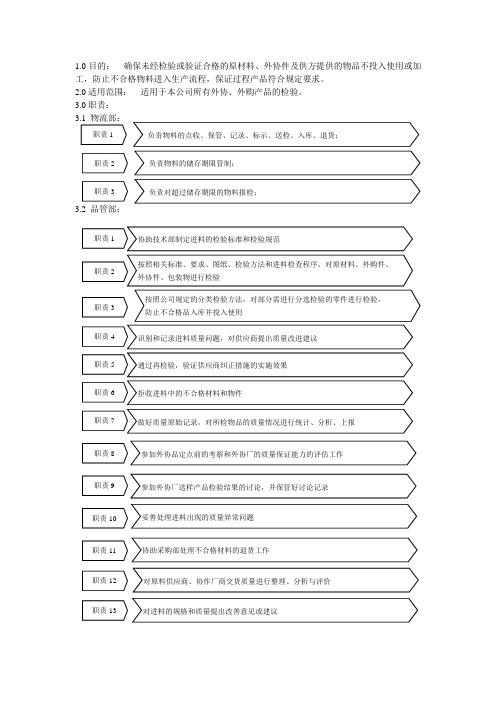
1.0目的:确保未经检验或验证合格的原材料、外协件及供方提供的物品不投入使用或加工,防止不合格物料进入生产流程,保证过程产品符合规定要求。
2.0适用范围:适用于本公司所有外协、外购产品的检验。
3.0职责:3.2 品管部:3.3采购部:3.4 生产部:5.1 入库送检:物流部在规定时间完成物料点收(含质量证明文件或检测报告)、标识,填写《送检单》,填写内容要求完整,物料到库半小时内送品管部报检。
5.2 进货检验流程: 5.2.1品管部收到《送捡单》(含质量证明文件或检测报告)半小时内回复检验及完成时间。
5.2.2 标准确认: 来料检验员根据具体来料标识卡、物流部报检单,查找相对应来料检验标准。
5.2.3抽样: 根据来料数量按《产品抽样检验管理办法》确定抽样方案并取样。
5.2.4测量/实验:5.2.4.1 进料检验进行来料标识确认:送货单位、产品名称、规格型号、日期、是否环保等内容标识完整;标识卡内容不完整或者无物流标识,物流部负责纠正,品管部进行跟踪验证。
5.2.4.2 检测实验报告及其他质量证明文件的确认、点收:确认无误按《文件控制程序》归档备查,如送货单位无检测实验报告及其他质量证明文件,内部联络采购部,依《不符合、纠正和预防措控制程序》处理。
5.2.4.3 产品包装防护确认:目测检查产品包装外箱是否满足搬运、运输及储存要求,不符合要求,内部联络采购部,依《不符合、纠正和预防措控制程序》处理。
5.2.4.4外观检查:不允许有麻点,色差、锈迹、裂纹、油污、碰伤、字迹清楚、破损、缩水、水纹、变形等,按品管部检验标准执行。
5.2.4.5尺寸测量:按品管部图纸及检验标准执行。
5.2.4.6性能实验:按品管部图纸及检验标准执行。
5.2.4.7报告填写:依据来料标识及《报检单》填写《来料检验报告》抬头栏:供应商名称、来料日期、数量、客户名称、合同编号、检验员、检验日期及抽样方案Ac-----接收数Re------拒收数等。
进货检验控制程序
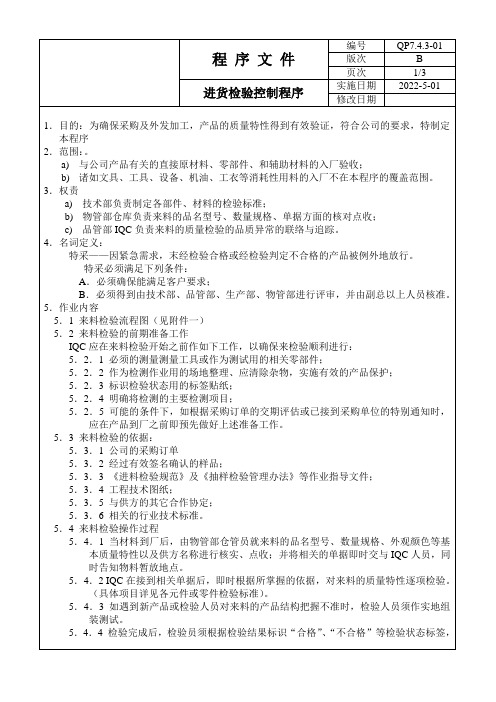
5.6原村料特采作业
5.6.1当因生产急需,对末经检验合格或已判定为不合格的产品实施特采时,由生产部或物控部提出书面的特采申请,详细注明不合格情形、特采理由和应对措施。
5.6.2特采需由技术部、品管部、采购部、生产部进行评审,确保资源正确使用。
5.3.4工程技术图纸;
5.3.5与供方的其它合作协定;
5.3.6相关的行业技术标准。
5.4来料检验操作过程
5.4.1当材料到厂后,由物管部仓管员就来料的品名型号、数量规格、外观颜色等基本质量特性以及供方名称进行核实、点收;并将相关的单据即时交与IQC人员,同时告知物料暂放地点。
5.4.2 IQC在接到相关单据后,即时根据所掌握的依据,对来料的质量特性逐项检验。(具体项目详见各元件或零件检验标准)。
5.4.3如遇到新产品或检验人员对来料的产品结构把握不准时,检验人员须作实地组装测试。
5.4.4检验完成后,检验员须根据检验结果标识“合格”、“不合格”等检验状态标签,
程序文件
编号
QP7.4.3-01
版次
B
页次
2/3
进货检验控制程序
பைடு நூலகம்实施日期
2022-5-01
修改日期
以便于搬运入库工作时的识别。
5.4.5正常情况下,检验员在接到相关的单据后4小时内完成检验,并开出《来料检验报告》
B.必须得到由技术部、品管部、生产部、物管部进行评审,并由副总以上人员核准。
5.作业内容
5.1来料检验流程图(见附件一)
5.2来料检验的前期准备工作
IQC应在来料检验开始之前作如下工作,以确保来检验顺利进行:
供方选择与评价控制程序(带流程图)
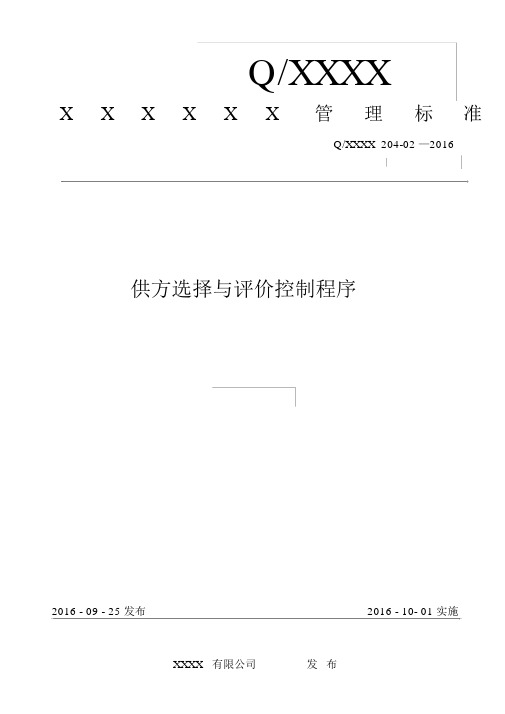
Q/XXXXX X X X X X管理标准Q/XXXX 204-02 —2016供方选择与评价控制程序2016 - 09 - 25 发布2016 - 10- 01 实施供方选择与评价控制程序1范围本办法适用于公司采购部对供方选择与评价管理。
本办法确定了对供方选择与评价管理流程及方法。
2规范性引用文件Q/XXXX 201-01-2016 《质量、环境、职业健康安全管理手册》Q/XXXX 204-04-2012 《零部件委外加工管理办法》Q/XXXX 204-05-2011《采购价格审批监管制度》3术语3.1供方提供产品的组织或个人。
3.2合格供方临时供方通过小批量供货验证,某种规格物料的产品质量、供货能力、服务及价格评价合格,可以为公司批量提供该种物料的供方。
3.3优秀供方经过对合格供方评价,合格供方评价分数在规定分数以上的合格供方确认为优秀供方。
4职责与权限本程序涉及相关部门及岗位人员职责权限如下:a)资材采购部负责本制度修订、宣贯和实施,对本制度符合性、适宜性与有效性负责;同时负责供方信息收集、沟通;负责组织对供方开发、调查、筛选、评价、选定和考核;负责供方档案的资料齐套、更新等归档的管理。
b)技术部负责参与供方的开发、选择和评价;负责《采购物料样品确认单》及《小批量物料试用报告单》的确认。
c)品保部负责供方来料的检验,参与供方的评价、考核和评比;负责各供方月进货质量统计上报。
d)生产部负责对供方物料《小批量试用报告单》试用结果的填写;参与供方评价。
e)管理者代表负责来料质量事故最终处理和《供方评价表》的审核。
f)总裁负责《合格供方名册》审批意见签署。
5管理内容、方法与要求5.1开发供方时机5.1.1新开发产品供方选择当配套客户指定的材料生产厂家或技术部开发产品寻找新材料而现有供方不能提供时,任何部门提供可靠讯息,采购部发出多家《供方调查表》,必要时组织相关部门现场调查,对多家调查结果进行评估,样品合格后,择优取用。
进货检验和试验控制程序(含表格)
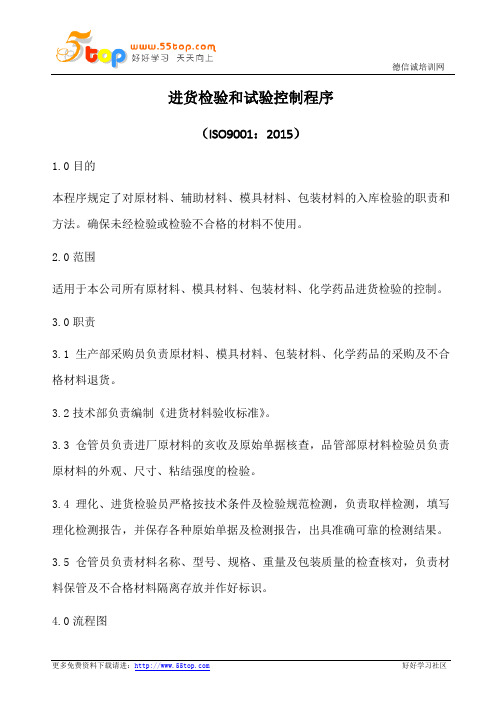
进货检验和试验控制程序(ISO9001:2015)1.0目的本程序规定了对原材料、辅助材料、模具材料、包装材料的入库检验的职责和方法。
确保未经检验或检验不合格的材料不使用。
2.0范围适用于本公司所有原材料、模具材料、包装材料、化学药品进货检验的控制。
3.0职责3.1生产部采购员负责原材料、模具材料、包装材料、化学药品的采购及不合格材料退货。
3.2技术部负责编制《进货材料验收标准》。
3.3仓管员负责进厂原材料的亥收及原始单据核查,品管部原材料检验员负责原材料的外观、尺寸、粘结强度的检验。
3.4理化、进货检验员严格按技术条件及检验规范检测,负责取样检测,填写理化检测报告,并保存各种原始单据及检测报告,出具准确可靠的检测结果。
3.5仓管员负责材料名称、型号、规格、重量及包装质量的检查核对,负责材料保管及不合格材料隔离存放并作好标识。
4.0流程图5.0工作程序5.1采购产品进厂后,仓管员根据订购单核对材料名称、规格、型号、数量、材质是否一致。
产品合格证、材料检验报告单等证明文件是否齐全。
若全部符合则暂收并用送检单的形式通知品管部检验。
5.2品管部接到仓管员通知后,速派进货检验员按《原材料检验标准》/《包装材料验收标准》/《模具材料验收标准》进行检验;化学药品的验收按进货单及标签上的“使用说明”进行。
5.3化验员对原材料、模具材料材质成份按《化验操作规程》进行化验,并把原始数据记录在《理化检验报告单》上,经主管审核后将结果送交进货检验员。
5.4进货检验员对所采购的产品按验收标准一一核对,当要求检验的项目完成后,将所有检验结果记录到“检验报告”单上,送交仓管员。
5.5仓管员将检验合格的采购产品按“搬运贮存控制程序”执行;对不合格采购产品按《不合格品控制程序》执行。
5.6进厂原材料的紧急放行5.6.1当客户急需产品,原材料来不及等检验结果出来就投产时,由生产车间填写《紧急放行例外转序申请审批表》,经品管部主管审核,管理者代表或总经理批准后,方可按“紧急放行”处理,原材料立即投入生产车间加工。
IATF16949过程监视和测量控制程序(含乌龟图)

过程监视和测量控制程序(IATF16949-2016)1.目的规定对产品的特性进行监视和测量,以验证产品已满足规定的要求。
2.范围适用于本公司从原材料进厂到产品出厂全过程的监视和测量。
3.定义无4.职责4.1品管部负责产品实现过程中从原材料进货到产品交付的全程检验。
4.2技术部负责提供产品标准等必要的技术文件。
4.3生产部负责生产过程的自检。
5.程序内容5.1技术部根据产品的需要确定必要的检验和试验手段并提供产品标准等必要的技术文件。
5.2品管部根据技术部的策划安排品管员,品管员应通过专业培训经考核合格,并授权。
5.3品管部按技术部提供的产品标准及检验标准制定作业指导书,适当时也可直接利用产品标准或检验标准。
作业指导书须经品管部主管核准后方可生效。
5.4计数数据接受抽样计划的接受准则必须是零缺陷,除此以外的接受准则必须经顾客批准。
5.5进料检验.(附页一:进料检验流程图)5.5.1品管部应根据原材料对产品质量的影响程度制定“原材料分类表”,确定需检验的原材料范围。
5.5.2需检验范围之内的原材料必须经规定的检验合格后方可投入使用,需检验范围之外的原材料品管员应检查其合格证后方可接收使用。
5.5.3对于重要原材料,如:铝锭,必须要厂家提供合格证明,并要对其进行检验以验证合格证的真实性。
5.5.4如因生产急需来不及验证需放行时,生管课应按《应急计划》规定办理手续。
相关部门应对该产品作出明确标识,并作好记录,以便一旦发现不符合规定要求时,能立即更改和更换。
5.5.5原材料进厂后,仓管员应将其堆放在指定区域,并填写“送检单”通知品管员检验。
5.5.6品管员接“送检单”后,根据检验标准及作业指导书的规定进行检验,并做好相应检测记录。
5.5.7原材料经检验合格品管员应及时通知仓库管理员入库,并按《标识和可追溯性程序》予以标识。
5.5.8经检验不合格的原材料按《标识和可追溯性程序》予以标识及隔离,并按照《不合格品控制程序》处理不合格品。
产品检验流程图(参考模板)
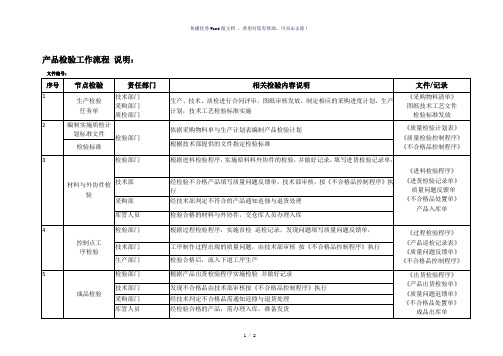
检验合格后,流入下道工序生产
5
成品检验
检验部门
根据产品出货检验程序实施检验并做好记录
《出货检验程序》
《产品出货检验单》
《质量问题返馈单》
《不合格品处置单》
成品出库单
技术部门
发现不合格品由技术部审核按《不合格品控制程序》执行
采购部门
经技术判定不合格品需通知返修与退货处理
库管人员
经检验合格的产品,需办理入库,准备发货
产品检验工作流程说明:
文件编号:
序号
节点检验
责任部门
相关检验内容说明
文件/记录
1
生产检验
任务单
技术部门
采购部门
质检部门
生产、技术、质检进行合同评审,图纸审核发放,制定相应的采购进度计划,生产计划,技术工艺检验标准实施
《采购物料清单》
图纸技术工艺文件
检验标准发放
2
编制实施质检计划标准文件
检验部门
依据采购物料单与生产计划表编制产品检验计划
6
缺陷分析与修订
检验部门
技术部
检验过程中发现的问题,做出质量问题纠正和预防措施,及时修订技术检验标准
《纠正和预防措施程序》
《检验标准》
产品检验工作流程图
采购部
经技术部判定不符合的产品通知返修与退货处理
库管人员
检验合格的材料与外协件,交仓库人员办理入库
4
控制点工
序检验
检验部门
根据过程检验程序,实施首检巡检记录,发现问题填写质量问题反馈单,
《过程检验程序》
《产品巡检记录表》
《质量问题反馈单》
《不合格品控制程序》
技术部门
工序制作过程出现的质量问题,由技术部审核按《不合格品控制程序》执行
检验控制程序
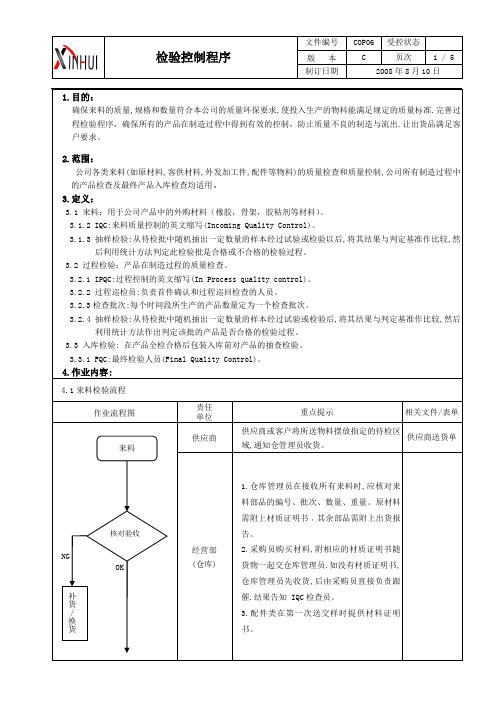
1.目的:确保来料的质量,规格和数量符合本公司的质量环保要求,使投入生产的物料能满足规定的质量标准.完善过程检验程序,确保所有的产品在制造过程中得到有效的控制,防止质量不良的制造与流出.让出货品满足客户要求。
2.范围:公司各类来料(如原材料,客供材料,外发加工件,配件等物料)的质量检查和质量控制,公司所有制造过程中的产品检查及最终产品入库检查均适用。
3.定义:3.1 来料:用于公司产品中的外购材料(橡胶,骨架,胶粘剂等材料)。
3.1.2 IQC:来料质量控制的英文缩写(Incoming Quality Control)。
3.1.3抽样检验:从待检批中随机抽出一定数量的样本经过试验或检验以后,将其结果与判定基准作比较,然后利用统计方法判定此检验批是合格或不合格的检验过程。
3.2 过程检验:产品在制造过程的质量检查。
3.2.1 IPQC:过程控制的英文缩写(In Process quality control)。
3.2.2 过程巡检员:负责首件确认和过程巡回检查的人员。
3.2.3检查批次:每个时间段所生产的产品数量定为一个检查批次。
3.2.4抽样检验:从待检批中随机抽出一定数量的样本经过试验或检验后,将其结果与判定基准作比较,然后利用统计方法作出判定该批的产品是否合格的检验过程。
3.3 入库检验: 在产品全检合格后包装入库前对产品的抽查检验。
3.3.1 FQC:最终检验人员(Final Quality Control)。
4.作业内容:4.1来料检验流程作业流程图责任单位重点提示相关文件/表单NGOK 供应商供应商或客户将所送物料摆放指定的待检区域,通知仓管理员收货。
供应商送货单经营部(仓库)1.仓库管理员在接收所有来料时,应核对来料部品的编号、批次、数量、重量。
原材料需附上材质证明书﹐其余部品需附上出货报告。
2.采购员购买材料,附相应的材质证明书随货物一起交仓库管理员.如没有材质证明书,仓库管理员先收货,后由采购员直接负责跟催.结果告知 IQC检查员。
进货检验工作流程培训
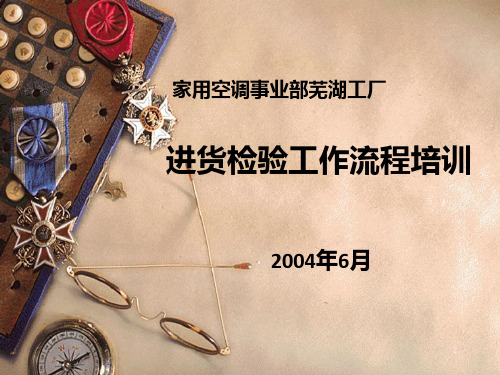
16
谢 谢!
17
密封胶泥 条码纸、碳带
封口塞、胶管、塑料胀管蜗壳固定 衬套、管口夹、温包卡、电线压板
、塑料垫圈、 插子套
穿墙套筒及盖 胶粘带
不转移胶带
海棉件
型号规格 所有规格 所有规格
所有规格 所有规格 所有规格
供方名称 所有厂家 泰昌橡胶、宁波北仑 马塘橡塑厂 德业、荣事达、天大、百年 北仑 、顺德洁康、山东雪圣
所有规格
湖州星丰
扎线 盒装钉
所有规格 所有规格
佳宏 镇江文教
隔音棉
所有规格(带 胶层的除外)
所有厂家
胶水
所有规格
所有厂家
泡沫胶
所有规格
所有厂家
钣材
所有规格
所有厂家
9
认可进货
检验流程: 暂收认可进货物料(仓管员)——物料验 收(进货检验员,至少每周一次对认可进 货物料进行日常检验抽查)——物料合格 则对产品出厂检验报告签名确认(进货检 验员),不合格则反馈至工程部或其他相 关部门(进货检验员)
6
驻厂检验
由进货检验派检验员驻到附近相关外协厂, 对各零部件供应厂商的生产过程进行控制, 解决生产过程中出现的质量问题,并对供应 我司的零部件,根据企业标准及检验作业指 导书的要求对其进行检验
检验流程:与来料检验流程相同,不合格物 料由外协厂翻修或返检后,重新报检
7
认可进货
▪ 进货检验时仅对供方提供该批物料的检验报 告、物料的名称、型号规格、数量及外包装 等进行验证的一种进货检验方式。
4
筛选检验
对部分关键零部件的关键特性进行全检,如, 电机的外观、异音、电气特性;电控的功能、 遥控器的外观、功能进行全检
进货检验和试验程序(含表格)
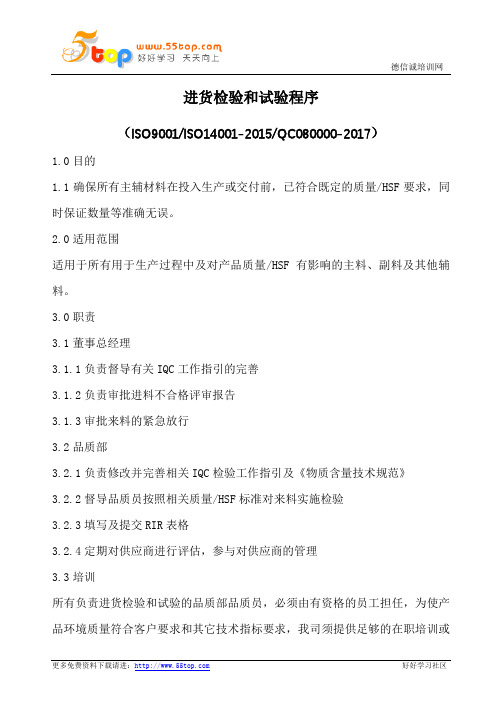
进货检验和试验程序(ISO9001/ISO14001-2015/QC080000-2017)1.0目的1.1确保所有主辅材料在投入生产或交付前,已符合既定的质量/HSF要求,同时保证数量等准确无误。
2.0适用范围适用于所有用于生产过程中及对产品质量/HSF有影响的主料、副料及其他辅料。
3.0职责3.1董事总经理3.1.1负责督导有关IQC工作指引的完善3.1.2负责审批进料不合格评审报告3.1.3审批来料的紧急放行3.2品质部3.2.1负责修改并完善相关IQC检验工作指引及《物质含量技术规范》3.2.2督导品质员按照相关质量/HSF标准对来料实施检验3.2.3填写及提交RIR表格3.2.4定期对供应商进行评估,参与对供应商的管理3.3培训所有负责进货检验和试验的品质部品质员,必须由有资格的员工担任,为使产品环境质量符合客户要求和其它技术指标要求,我司须提供足够的在职培训或聘请具有经验的品质专业人员,必要时持资质上岗证。
对于培训及培训记录的控制可参考“人力资源管理程序”。
4.0定义4.1主料/辅料收货及检验报告(ReceivingInspectionReport/RIR)由货仓部于收到采购物料时发出,然后交品质部安排进行检验及填上有关的检验结果。
4.2IQC(IncomingQualityControl)来料质量控制4.3免检类物料:详细见《免检类来料工作指引》。
4.4要检来料:原纸、白胶浆、水墨、彩标、外来纸板。
4.5物质含量技术规范参考ROHS及客户物质含量技术参数要求制定的。
5.0运作程序5.1IQC工作指引以及《物质含量技术规范》的制定与控制5.1.1品质部主管负责对本公司各类物料建立IQC工作指引。
IQC工作指引的控制程序可参考“文件系统控制程序”。
5.1.2对客户有害物质的控制进行收集、整理,参照ROHS指令、94/62/EC包装指令制定《物质含量技术规范》。
当客户要求有更改时,品质部应及时向管理者代表提出重新修订《物质含量技术规范》。