铣刀功率和切削力计算
机械加工刀具基础知识
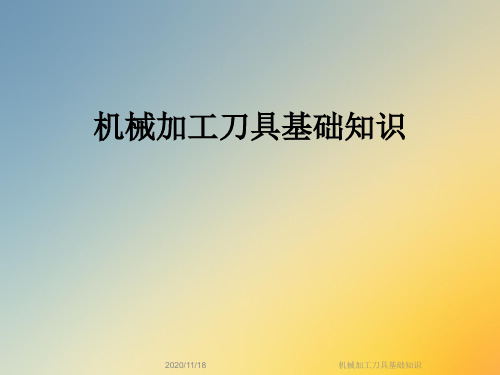
切削要素
切削层参数(parameters of undeformed chip)
机械加工刀具基础知识
1.1 切削运动及切削要素
二、切削运动及切削用量 1.主运动和切削速度 主运动(primary motion) 是使刀具和工件之间产生相 对运动,促使刀具接近工件 而实现切削的运动。
机械加工刀具基础知识
机械加工刀具基础知识
1.2 切削刀具及其材料
一、切削刀具 2.车刀切削部分的主要角度
背吃刀量和进给量一定时,主偏角愈小,切削层公称宽 度愈大而公 称厚度愈小,即切下宽而薄的切屑。
机械加工刀具基础知识
1.2 切削刀具及其材料
一、切削刀具 2.车刀切削部分的主要角度
主、副偏角小时,已加 工表面残留面积的高度hc亦 小,因而可减小表面粗糙度 的值,并且刀尖强度和散热 条件较好,有利于提高刀具 寿命。
机械加工刀具基础知识
1.2 切削刀具及其材料
一、切削刀具 2.车刀切削部分的主要角度 (2)车刀的主要角度
车刀设计、制造、刃磨 及测量时,必须考虑的主要角 度,如图所示。 1)主偏角kr在基面中测量的主 切削平面与假定工作平面间的 夹角。 2)副偏角k’r在基面中测量的 副切削平面与假定工作平面间 的夹角。
机械加工刀具基础知识
1.2 切削刀具及其材料
二、刀具材料 1.刀具材料应具备的性能
较高的硬度和耐磨性
足够的强度和韧度
较高的耐热性
良好的工艺性和经济性
机械加工刀具基础知识
1.2 切削刀具及其材料
二、刀具材料 2.常用的刀具材料
常用刀具材料基本性能
机械加工刀具基础知识
1.2 切削刀具及其材料
二、刀具材料 2.常用的刀具材料
铣工工艺第十三章铣刀几何参数和铣削用量的选择

铣工工艺第十三章铣刀几何参数和铣削用量的选择铣刀是铣削加工中最为重要的切削工具之一,其几何参数的选择对于加工质量、效率和刀具寿命有着重要的影响。
本章将介绍铣刀几何参数的选择原则和铣削用量的确定方法。
一、铣刀几何参数的选择原则1.刀尖半径(RE)的选择:刀尖半径的大小直接影响到切削力和表面质量。
在一般情况下,刀尖半径越大,切削力越小,表面质量越好。
但是,过大的刀尖半径会导致铣削面积减小,加工效率降低。
因此,需要根据具体情况选择合适的刀尖半径。
2.刀具倾角(AP)的选择:刀具倾角的大小决定了铣削切削力的方向和大小。
一般情况下,刀具倾角越大,切削力越小,表面质量越好。
但是,过大的刀具倾角会导致切削力的方向与进给方向夹角过大,容易引起振动和切削不稳定。
因此,需要根据具体情况选择合适的刀具倾角。
3.切削刃数(Z)的选择:切削刃数的选择与铣削切削力和切削效率有关。
一般情况下,切削刃数越多,每刃切削力越小,切削效率越高。
但是,过多的切削刃数会导致刀具刃间距过小,切削润滑效果差,容易引起刀具卡刃、切削热等问题。
因此,需要根据具体情况选择合适的切削刃数。
4.刀具材料的选择:刀具材料的选择直接影响到刀具的切削性能和寿命。
一般情况下,硬度较高、耐磨性好的刀具材料能够提高刀具的使用寿命。
常用的刀具材料有硬质合金、高速钢和陶瓷等。
需要根据具体情况选择合适的刀具材料。
二、铣削用量的选择方法铣削用量的选择是指切削速度、进给量和切削深度的确定。
铣削用量的选择直接影响到加工效率、表面质量和刀具寿命。
1.切削速度的选择:切削速度的选择应根据刀具材料、工件材料和切削润滑条件等因素综合考虑。
一般情况下,切削速度越高,加工效率越高,但是过高的切削速度会导致刀具温度升高,刀具寿命降低。
需要根据实际情况选择合适的切削速度。
2.进给量的选择:进给量的选择应根据切削力和切削表面质量的要求综合考虑。
一般情况下,进给量越大,加工效率越高,但是过大的进给量会导致切削力增大,切削表面质量降低。
铣刀的切削原理

铣刀的切削原理
铣刀是一种常用的机械切削工具,用于铣削金属、木材和其他各种材料。
其切削原理主要包括以下几个方面:
1. 刀具旋转:铣刀通过主轴与刀座相连接,并在机床上高速旋转。
刀具的旋转提供切削运动和切削力。
2. 刀具进给:铣刀在旋转的同时,通过机床进给系统,控制刀具相对于工件的位置和移动速度。
刀具进给决定切削深度和工件上每单位时间的切削长度。
3. 切削力:由于刀具与工件之间的相对运动,切削力在切削过程中产生。
切削力作用于刀具上,使其对工件进行切削。
切削力主要由径向切削力和轴向切削力组成。
4. 切削削角:铣刀的切削削角是刀具切削过程中的重要参数。
它决定了切削过程中切削面的形状和切削力的大小。
常见的切削削角有前角、主后角和径向后角。
5. 切削液:为了降低切削温度、减小摩擦和磨损,并帮助排屑和冷却刀具,通常在铣削过程中会使用切削液进行冷却和润滑。
总之,铣刀的切削原理是通过旋转的刀具与工件的相对运动,形成一定的切削力,对工件进行切削加工。
切削过程中,刀具的旋转和进给以及切削力的作用是关键
因素。
4Cr16Mo模具钢立铣加工过程中的切削力系数

co s 2φ (2φ - sin 2φ)
- (2φ - sin 2φ) - 1 co s 2φ
Fx
φ ex
(7)
Fy
φ st
全齿 (如铣槽) 铣削实验最为方便 , 此时切入角
φst = 0 ,切出角φex =π. 而在顺铣时 ,则有
φst ( z) = π - arcco s (1 - ae / R) , φex = π (8)
触角 ,
φj ( z)
=φ+ ( j -
1)φp -
t
an R
β
z
(3)
铣刀的刀齿齿间角φp = 2π/ N ( N 为刀齿数) ,β为刀
具螺旋角.
在实际测量过程中 , 所测力为作用在铣刀上的
进给抗力和切深抗力 ,分别用 Fx (φ) 和 Fy (φ) 表示.
通过下列变换可以实现微元力的转换 :
d Fx , j [φj ( z) ] =
© 1994-2010 China Academic Journal Electronic Publishing House. All rights reserved.
26
上 海 交 通 大 学 学 报
第 43 卷
其加工参数 ,其切削力系数为常数 ,并据此提出铣削 力的解析模型 ,根据该模型可以得出特定条件下的 切削力系数. 为了更准确地预测铣削力 , Kline 等[2] 假设切削力系数为每齿进给量 、径向切深和轴向切 深的多项式函数 ,而这需要通过更为复杂的数学方 法来对切削力系数进行预测. 尹力等[3] 利用偏最小 二乘回归 ( PL SR) 方法和混合位级正交设计方法对 铣削力模型系数进行预测 ,减少了实验次数 ,并给出 槽铣加工 L Y12 和 45 # 钢材料的仿真实例.
Milling铣削山特维克重要刀具参数

通过使铣刀移动偏离中央,就会得到 恒定的和有利的切削力方向。(通俗的 理解,使刀片从厚吃刀点切入,从薄 吃刀点切出,如后页)
29
铣削原理 –铣屑厚度
30
刀具进入和退出时需考虑的要点
1. 2. 3.
刀具的中心线完全位于工件 宽度之外。
49
铣削时可获得良好的表面质量
表面光洁度
使用wiper(修光刃)刀片,可获得更 高的生产效率和更好的表面光洁度
标准刀片 一个wiper (修光刃) 刀片
将进给率限制到平行刃带的60% 正确的安装wiper(修光刃)刀片
fn1 = 0.8 x bs1≤
fn1 = 0.8 x bs1≤
进给 fn
刀具的中心线与工件边缘处 于同一条直线。(最差,最 不好)
刀具的中心线完全位于工件 宽度之内。
点击上图
31
铣削原理 – 铣屑厚度
切屑宽度与进给值
32
铣削原理 –铣屑厚度
主偏角与切屑厚度
33
切削力和主偏角
90°主偏角 45°主偏角 圆刀片刀具
薄壁零件 装夹较差的零件 要求准确的90度形状
ap × ae × vf × Pc = k c 60 × 106
点击返回机床功率扭矩页面
16
铣削原理 – 铣削公式
17
计算切削参数
面铣示例
已知
需要计算
vc = 225 m/min
fz = 0.21mm zn = 5 Dc = 125 mm ap = 4 mm
4
n (rpm)
vf (mm/min)
48
选择刀片牌号
车削功率和扭矩计算

U钻钻削功率和扭矩的计算 Power consuming and Torque force
例:工件材料为高合金钢,硬度HRC50,钻削直径20mm,Vc= 40m/min,f=0.07mm/r,Kc=4500N/mm2,
=0.9,计算钻削功率和扭矩。
KcfVc (D2-d2) P= D 240000
D: hole diameter
d: core diamerer
T= F力 x(D/2) =P x9549/RPM 钻削功率P=4500 0.07 40 20/240000 0.9=1.2KW 转速 n=40 1000/3.14 20=636rpm
扭矩 T=1.2 9549/636=18NM
T= F力 x(D/2) =P x9549/RPM
铣削功率和扭矩的计算 铣削三要素
Cutting data formulas
铣削功率和扭矩的计算 Power consuming and Torque force
Torque (Nm) = kW (nett) x 9549 RPM
铣削功率和扭矩的计算 Power consuming and Torque force
面铣刀直径80mm, 6个刀片刃口,铣削的材料分别为铸 铝合金(kc:800) 和奥氏体不锈钢(kc:2400), 若刀片的切 削速度为600m/min和150m/min, 每齿进刀为fz=0.2mm/z, 切深ap=4mm, 切宽ae=60mm, 问他们的铣削功率和扭矩
N铝=2388rpm vf铝=2865mm/r p铝=9.16kw T铝=36Nm N不锈钢=597rpm vf不锈钢=716mm/r p不锈钢=6.87kw T不锈钢=109Nm
镗削功率和扭矩计算
铣刀功率和切削力计算
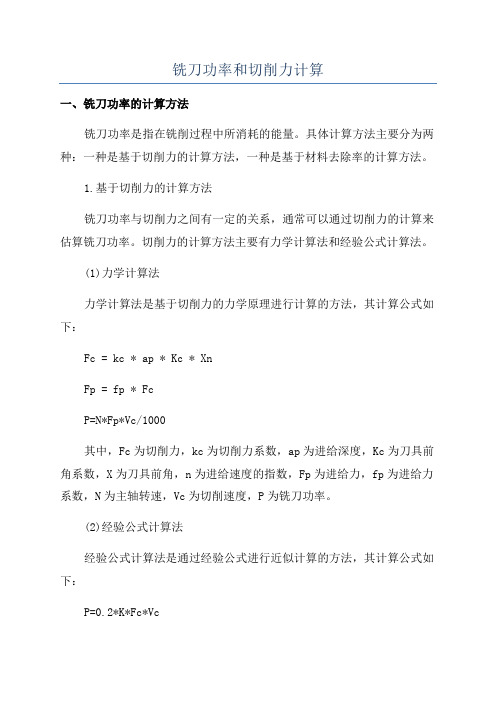
铣刀功率和切削力计算一、铣刀功率的计算方法铣刀功率是指在铣削过程中所消耗的能量。
具体计算方法主要分为两种:一种是基于切削力的计算方法,一种是基于材料去除率的计算方法。
1.基于切削力的计算方法铣刀功率与切削力之间有一定的关系,通常可以通过切削力的计算来估算铣刀功率。
切削力的计算方法主要有力学计算法和经验公式计算法。
(1)力学计算法力学计算法是基于切削力的力学原理进行计算的方法,其计算公式如下:Fc = kc * ap * Kc * XnFp = fp * FcP=N*Fp*Vc/1000其中,Fc为切削力,kc为切削力系数,ap为进给深度,Kc为刀具前角系数,X为刀具前角,n为进给速度的指数,Fp为进给力,fp为进给力系数,N为主轴转速,Vc为切削速度,P为铣刀功率。
(2)经验公式计算法经验公式计算法是通过经验公式进行近似计算的方法,其计算公式如下:P=0.2*K*Fc*Vc其中,K为修正系数,Fc为切削力,Vc为切削速度,P为铣刀功率。
2.基于材料去除率的计算方法基于材料去除率的计算方法是通过材料去除率和铣削效率之间的关系来计算铣刀功率的方法,其计算公式如下:Q = Vc * fz * apη=Q/PcP=η*Pc其中,Q为材料去除率,Vc为切削速度,fz为进给量,ap为进给深度,η为铣削效率,Pc为切削功率,P为铣刀功率。
二、切削力的计算方法切削力是铣削过程中所产生的力,其大小和方向与切削参数、工件材料以及机床刚度等因素有关。
常用的切削力计算方法有力学计算法和经验公式计算法。
1.力学计算法力学计算法是通过力学原理对切削力进行计算的方法,其计算公式如下:Fc = kc * ap * Kc * XnFp = fp * Fc其中,Fc为切削力,kc为切削力系数,ap为进给深度,Kc为刀具前角系数,X为刀具前角,n为进给速度的指数,Fp为进给力,fp为进给力系数。
2.经验公式计算法经验公式计算法是通过经验公式进行近似计算的方法,其计算公式如下:Fc = K * (ap * fz * ae)^m其中,K为修正系数,ap为进给深度,fz为进给量,ae为切削宽度,m为材料硬度指数,Fc为切削力。
第八章铣刀

5.立铣刀
一般有三到四个刀齿。 用于加工平面、台阶、 槽和相互垂直的平面, 圆柱上的切削刃是主 切削刃,端面上分布 着副切削刃。工作时 只能沿刀具的径向进 给,而不能沿铣刀的
轴线方向作进给运 动。。
用立铣刀铣槽时槽宽有扩张,故应取直 径比槽宽略小的铣刀。
8.1.2 按刀齿齿背形式分
1.尖齿铣刀 尖齿铣刀的特点是齿背经铣制而成,并在切削刃后 磨出一条窄的后刀面,铣刀用钝后只需刃磨后刀面, 上述铣刀基本为尖齿铣刀。
立铣刀
三面刃、两 面刃铣刀
螺旋角 45°~60° 25°~30° 30°~45° 15°~20°
(4)主偏角与副偏角的选择
常用的主偏角有45°、60°、75°、90°。工 艺系统的刚性好,取小值;反之,取大值。副偏角一 般为5°~10°。
圆柱铣刀只有主切削刃,没有副切削刃,因此 没有副偏角。主偏角为90°。
(a)对称铣; (b)不对称逆铣;(c)不对称顺铣 图8.15 端铣的三种方式
2.圆周铣的铣削方式
逆铣
铣刀切入工件时的切削速度方向与工件的 进给方向相反 。刀齿的切削厚度从零逐
渐增大。当接触角大于一定数值时,容易 使工件的装夹松动而引起振动。但铣削过
程比较平稳 。(图8.16a)
铣刀切入工件时的切削速度方向与工件的 进给方向相同 。刀齿的切削厚度切入时 最大,而后逐渐减小 。会使工作台带动
ADav
Q vc
aea pv f
d0n
a paea f z
d0
图8.13 螺旋齿圆柱铣刀的切削宽度
3.铣削用量的选择 (1)背吃刀量的选择
应当根据工件的加工精度、铣刀 的耐用度及机床的刚性,首先选 定背吃刀量,然后选取进给量,
铣 削 原 理

1.1 铣削方式
1.周铣 周铣是指利用分布在铣刀圆柱面上的切削刃来形成平面(或
表面)的铣削方法。 周铣又分为两种铣削方式,即逆铣和顺铣,如图所示。
逆铣和顺铣
如图所示为逆铣、顺铣时的铣削分力作用方向。
逆铣、顺铣时的铣削分力作用方向
2.端铣
1
2ห้องสมุดไป่ตู้
3
4
端铣时每齿切 下的切削层厚 度变化较小, 因此,铣削力 变化较小;周 铣时每齿切下 的切削层厚度 变化较大,因 此,铣削力波 动较大。
Fc2 Fc2N Ff2 Ff2N
由于铣刀刀齿位置是随时变化的,因此,当铣刀接触角 ψi不同时,各铣削分力的大小是不同的,即
Ff Fccos i FcNsin(i 逆铣为“+”,顺铣为“-”) FfN Fcsin i FcNcos(i 逆铣为“+”,顺铣为“-”)
同理,端铣时,也可将铣削力按上述方法分解。
螺旋齿圆柱形铣刀的切削宽度
3)切削层横截面积
铣刀每个切削齿的切削层横截面积AD=hDbD。铣刀的总切 削层横截面积应为同时参加切削的刀齿切削层横截面积之和。
但是,由于铣削时铣刀的切削层厚度、切削层宽度及工作齿
数均随时间而变化,因而总切削面积∑AD也随时间而变化,使 得计算较为复杂。为了计算简便,常采用平均切削层横截面
对称端铣与不对称端铣
1.2 铣削要素和切削层参数
1.铣削要素 铣削时,必须选择下列铣削用量要素,如图所示。
铣削要素
1)背吃刀量
背吃刀量是指待加工表面和已加工表面间的垂直距离,用
符号 ap 表示,单位为mm。
2)铣削宽度
铣削宽度是指垂直于铣削深度和走刀方向测量的切削层尺寸,用
a 符号 e 表示,单位为mm。
车削、钻削、铣削加工的标准切削力模型

车削、镗削、钻削、铣削加工的标准切削力模型M. Kaymakci, Z.M. Kilic, Y. Altintas摘要一个标准的切削力学模型是预测在铣削、镗削、车削和钻削加工过程中切削力系数的工具。
嵌入物在参考物的定向是数学建模遵循ISO工具的定义标准。
由作用在前刀面的摩擦力和法向力组成的变换矩阵转化成参考坐标系,取决于加工材料和切削刃的几何形状。
而这些力再进一步转化为铣床、镗床、车床和钻床坐标系中初步赋值的具体参数,在切削试验的标准模型进行了验证。
关键词切削力车削铣削镗削钻削1.前言目前研究的目的是开发一种可用于预测的进程模型,以完善之前代价昂贵、操作复杂的物理实验。
这种结合材料性能、切削方式、刀具种类、过程动力学和结构动力学的进程模型,是应用于预测在金属切削加工过程中的切削力、扭矩、工具、形状误差和振动。
仿真和加工工艺规划,可预测机床和其零部件的操作是否是可行的,或优化切削条件和刀具种类,以获得更高的材料去除率。
建立铣削、镗削、车削和钻削加工过程的力学模型,为以前的研究提供了宝贵的贡献。
切削力模型需要考虑切削力作用在切削刃的作用面积和切削力系数,再从加工测试中进行校准。
将沿切削刃的受力分布建模并相加,以预测作用在机械上的总负荷。
有Fu[1]等人提出的在端面铣削的机械方法是一个示范性的应用,对切削力模型的全面审查则已由埃曼等人[2]提出了,Armarego [ 3 ]提出的通过正交斜变换[ 4 ],可以从平均剪切应力、剪切角和摩擦系数预测切削力系数,建模时,由于固体边沿和几何形状[5]的连续变化,通常都采用斜变换法来解决问题。
本文中将对由Luttervelt[6]和Altintas[7]等人发表的以机械切削力学为基础的方法进行回顾。
2000年以来,学者们更趋向于研究如何应用数值的方法来预测金属切削过程中的切削力系数。
有限元法和滑移线场模型用于预测切削力系数,也应用于对切削力的预测[8-10],数值模型完全基于材料的在加工过程的应变、应变率、温度变化和摩擦系数。
刀具复习资料

木材切削原理与刀具课程思考题第一章1、切削定义(要素:使用刀具;按一定轨迹运动;工件要达到要求的尺寸、形状、精度和表面质量)刀具相对工件按预定轨迹运动,切除一部分工件材料或使之分离,使加工部位或工件获得一定精度之尺寸、形状、表面质量。
2、切削运动(要点:切削运动是主运动和进给运动的合成;主运动速度的数量级一般比进给运动大得多;主运动速度计算,常用单位;进给运动速度三种表示方式:进给速度、每转进给量、每齿进给量以及它们的常用单位和换算关系。
)3、刀具角度:一刃四角(前角、后角、刃倾角、刃偏角)的定义(包括坐标平面和测量平面);它们对切削现象(切削力、屑片变形、刀具磨损、切削质量等)的影响。
前角:在主截面或法向截面内度量的刀齿前面与基面之夹角。
后角:在主截面或法向截面内度量的刀齿后面与切削平面之夹角。
楔角:刀齿或刀片前后面之夹角。
切削角:刀齿或刀片前刀面与切削平面之夹角。
刃倾角:在切削平面内刀齿的切削刃与基面投影之夹角。
刃偏角:在基面内刀齿的切削刃与进给速度矢量之夹角。
前角:影响屑片的变形和破坏程度;影响切削力,并和后角一起影响刀齿强度和锐钝程度。
前角小,切屑变形大,破坏程度增加,切削阻力大,顺纹切削时不易劈裂;前角大则相反。
前后角都大时,楔角变小,刀齿锋利,但强度减弱,易变钝或破损。
后角:影响后刀面与工件的摩擦阻力并与前角一起影响刀齿强度和锐钝程度。
后角小,后刀面与切削表面间的压挤程度增加,摩擦阻力增大,整个切削阻力增大。
刃偏角:影响切削力各分力之比例(主要是进给力)和屑片的宽厚比。
例如外圆车削时,主刃偏角大,则进给阻力大。
刃倾角:影响各切削分力之比例和屑片流出的方向。
4、切削层的几何参数:切削厚度、宽度、深度、面积的定义;当一种切削方式切削厚度变化时(如平面铣削)如何计算最大、最小和平均切削厚度?切削厚度或屑片厚度a[mm]:相邻两切削轨迹间的垂直距离。
切削深度h[mm]:已加工表面和待加工表面间的垂直距离。
第四讲 铣刀
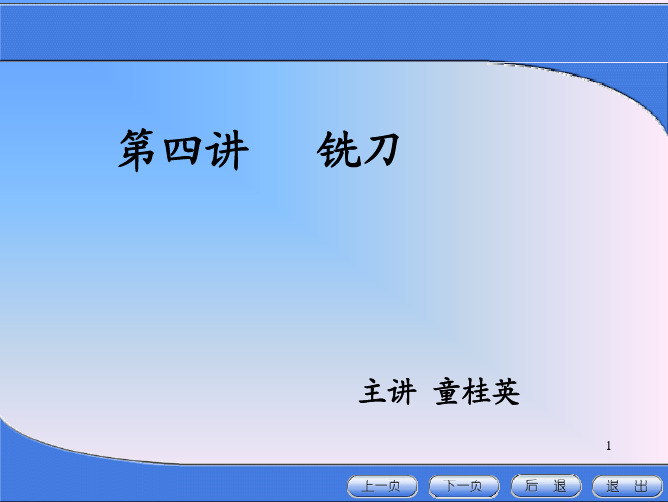
24
4-10 端铣刀 的几何 角度
25
二、铣刀几何参数的特点 1.前角 表4- 1是铣刀前角的常用数值。和车刀一样,铣刀的前 角主要根据工件材料选择。工件材料越软,塑性越高时, 切屑塑性变形较大,切屑与前面摩擦较大,前角取值也应 较大;工件材料硬度较高,塑性较低时,前角宜取小些。 铣削脆性材料时.切屑沿前面滑走距离短,切削力和热集 中在刃区,铣刀前角不宜大而取较小的正值。 由于铣削有冲击,故应保证切削刃有较高的强度。一般情 况下,铣刀前角小于车刀的前角;高速钢铣刀比硬质合金 铣刀前角可大一些;硬质合金端铣刀切削时冲击大,前角 应取更小数值或负值;硬质合金铣刀采用正前角时,应加 负倒棱(负倒棱宽度b γ1≦αf )
19
图4—8带 柄铣刀的 安装
20
第二节
铣刀的几何角度
铣刀型式虽多,但以圆柱铣刀和端铣刀为基 本型式。圆柱铣刀和端铣刀的切削部分都可 看作车刀到头的演变,所不同的是铣刀回转、 刀齿数多。 因此研究铣刀的角度要抓住一 个刀齿去分析。 一、 圆柱铣刀的几何角度 1、坐标平面 1).基面Pr 铣刀切削刃选定点的基面是通过该点并包含 轴线的平面,如图4—9所示。
8
铣床可加工的零件如图4—4所示。铣床加工的公 差等级一般为IT9~IT8;表面粗糙度Ra值一般为 6.3~1.6µm。
9
10
4-4 铣削加工举例
11
五、 铣刀及其安装 (一)铣刀 铣刀实质上是一种由几把单刃刀具组成的多刃 刀具,它的刀齿分布在圆柱铣刀的外回转表面 或端铣刀的端面上。常用的铣刀刀齿材料有高 速钢和硬质合金两种。 铣刀的分类方法很多,这里仅根据铣刀安装方 法的不同分为两大类: 带孔铣刀和带柄铣刀。如图4-5
21
2).切削平面Ps 铣刀切削刃选定点的切削平面是加工表面在该点的切平 面(图4—9)。 3.主剖面P0 由图4—9可知,圆柱铣刀的主剖面Po与进给剖面Pf,(图 中未标出)重合,是垂直于轴线的端剖面。 4、法剖面Pn 法剖面Pn是垂直于主切削刃的平面。只有在选定点的 切削平面视图中才能表示该点的法剖面Pn(图4-9) 5、进给剖面Pf和切深剖面Pp 它们都垂直于基面Pr,,如图4-9所示。
铣刀功率和切削力计算【秘籍】

大家知道铣刀功率和切削力计算是怎样的吗?下面,小编为大家简单介绍一下,一起来看看吧。
一、按照主轴转速1000rpm ,进给速度0.1mm/转,钻穿1.8mm 约需要时间1s 。
切削力Ff刀具材料:高速钢加工方式:钻公式:Ff=309*D*f^(0.8)*(Kp)功率:D = 8功率:f = 0.1功率:Kp = 0.75(按铜合金多相平均HB>120)计算结果= 293.839切削力矩M工件材料:灰铸铁(HB190)刀具材料:高速钢加工方式:钻公式:M=0.21*D^(2)*f^(0.8)*(Kp)功率:D = 8功率:f = 0.1功率:Kp = 0.75(按铜合金多相平均HB>120)计算结果= 1.597二、铣削切削力计算:铣削切削力计算类别:工件材料:碳钢、青铜、铝合金、可锻铸铁等刀具材料:高速钢铣刀类型:端铣刀公式:F=(Cp)*(ap)^(1.1)*(fz)^(0.80)*D^(-1.1)*B^(0.95)*z*(Kp) 功率:Cp = 294功率:ap = 1.8功率:fz = 0.5功率:D = 8功率:B = 8功率:z = 4功率:Kp = 0.75计算结果= 707.914扩展资料:钻铣床铣刀切削力计算方法:一切削力的来源,切削合力及其分解,切削功率研究切削力,对进一步弄清切削机理,对计算功率消耗,对刀具、机床、夹具的设计,对制定合理的切削用量,优化刀具几何参数等,都具有非常重要的意义。
金属切削时,刀具切入工件,使被加工材料发生变形并成为切屑所需的力,称为切削力。
切削力来源于三个方面:克服被加工材料对弹性变形的抗力;克服被加工材料对塑性变形的抗力;克服切屑对前刀面的摩擦力和刀具后刀面对过渡表面与已加工表面之间的摩擦力。
切削力的来源上述各力的总和形成作用在刀具上的合力Fr(国标为F)。
为了实际应用,Fr 可分解为相互垂直的Fx(国标为Ff)、Fy(国标为Fp)和Fz(国标为Fc)三个分力。
铣削力计算

第1 页共8 页铣削功率的计算硬质合金铣刀和高速钢铣刀铣削功率N的计算公式分别见表3及表4,在表3及表4中,各个符号的定义如下:D 为铣刀直径(mm);t 为铣削深度(mm);Sz为每齿走刀量(mm/齿);B为铣削宽度(mm);Z为铣刀齿数;n为铣刀每分钟转数;Kn为修正系数见表3表4的第3栏,计算所得的N是铣刀磨钝后的数值。
系数Cn及指数q、x、y、u、p、f值均见表3,表4的第2栏。
各类铣刀的t及B的定义见下图。
第 2 页 共 8 页铣 削 分 力 的 计 算由表3及表4的公式计算出铣削功率N 后,就可由功率N 求铣削时的圆周切削力Pz :式中,N 为铣削功率(千瓦),V 为铣削速度(米/分),Pz 为圆周铣削力(公斤)。
知道了Pz 分力后,则铣刀的走刀抗力P H ,轴向抗力Po 等便可用图4至图8所示的比例值来近似计算。
各类铣刀的切削分力比例值如下:10260PzV Ν×=VN10260Pz ××=第3 页共8 页一、(圆柱)平铣刀、三面刄铣刀、锯片铣刀等。
1、逆铣(图4)P H=(1.~1.2)P zP V=(0.2~0.3)P zP0=0.28P z tgw12、顺铣(图5)P H=(0.8~0.9)P zP V=(0.75~0.8)P zP0=0.28P2 tgw1二、端面铣刀和立铣刀1、对称铣削(图6)=(0.3~0.4)P zPP V=(0.85~0.95)P zP0=(0.5~0.55)P z第4 页共8 页2、不对称逆铣(图7)P H=(0.6~0.9)P ZP V=(0.45~0.7)P ZP0=(0.5~0.55)P Z(P0见图6)3、不对称顺铣(图8)P H=(0.15~0.3)P ZP V=(0.9~1.0)P ZP0=(0.5~0.55)P Z1、计算所得的功率N值都是铣刀在磨损限度值内的数值。
2、高速钢铣刀用冷却液,硬质合金铣刀不用冷却液。
(完整版)金属切削的计算方法

1.最大扭矩采用镗孔的方法进行公式来源《机械加工工艺设计实用手册》或《金属切削原理及刀具》《金属切削原理》(陶乾编)ypzFZ=9.81CFZ•apM=计算公式xFZ•f yFZ•(60υ)nFZ•KFZPZ=Cpz•t•sM切=(kg)FZ•d32⨯10Pz•D(kg.mm)2M切•n(kW)P=FZ•υ⨯10-3若采用双刃刀片则:背吃刀量为单刃的两倍N=716200⨯1.36(其中t=ap;S=f;)注:n—转每分钟(r/min)2.机床的最大切削抗力试验采用钻削的方法进行(钻削抗力的计算)公式来源计算公式JB/T4241-1993《卧式铣镗床技术条件》《机械加工工艺设计实用手册》《金属切削原理及刀具》《金属切削原理》(P1319)(p193)(陶乾编)(p274)F=595•D•S0.8F=9.81•CF•dF•f YF•KFF=CF•dF•f YF•KFZ X P=C P•D•S YP3.钻削扭矩M的计算公式来源计算公式公中系和数式的数指《机械加工工艺实用手册》(p193)《金属切削原理与刀具》第二版(p192-p195)《金属切削原理》(陶乾编)(p274)M=9.81•CM•d ZM•f yM•KMM=CM•dxF•f yM•KM•10-3表15-31:CM=0.021、ZM=2.0、YM=0.8、KM=1.0d=80、f1=0.8、f2=1表13-2:CM=225.63、XM=1.9、YM=0.8、KM=1d=8 0、f1=0.8、f2=1M=CM•D1.9•S0.8表13-2:CM=23.3、D=80、S1=f1=0.8、S2=f2=14.钻削功率的计算公式来源计算公式《机械加工工艺实用手册》《金属切削原理与刀具》(p193表13(p1319、表15-31)-2)《金属切削原理》(陶乾编)(p229)2M•υPm=d2M•υPm=2π•M•n或Pm=dPm=M•n716200⨯1.365.车削、镗孔时切削力的指数公式及指数计算公式主切削力F ZF Z=9.81C F Z•ap削)xFZ •f yFZ •(60υ)0nFZ •K FZ (N)(铸铁切F Z=9.81⨯92•a p•f 0.75•(60υ)•K FZ1切深抗力F y 进给抗力F x切削时消耗的功率P m切削扭矩MF y=9.81C Fy•ap F x=9.81C Fx•apzFy •f yFy •(60υ)•K Fy (N)nFy zFx •f yFx •(60υ)•K Fx (N)nFx 式中υ的单位为m/sP m=F Z•υ⨯10-3(kW)M Z =公式中的系数和指数加工材料刀具材料加工形式F Z⨯d032⨯10公式中的系数及指数主切削力F Z C FZXF Z 1.00.721.01.01.01.0yF Z 0.750.81.70.751.00.750.75nF Z -0.1500.71000切深抗力F y C Fy 19914294XF y 0.90.730.9yF y 0.60.670.75nF y -0.30进给抗力F X C FX 29454XF X yF x 1.01.20.50.65nF x -0.4结构钢及铸钢σb =0.637Gpa (=65kgf/mm )结构钢及铸钢σb =0.637Gpa (=65kgf/mm 2)不锈钢1Gr18Ni9Ti,HB=141灰铸铁2硬质合金外圆纵车、横车及镗孔切槽及切断切螺纹270367133180222191204高速钢外圆纵车、横车及镗孔切槽及切断成形车削硬质合金外圆纵车、横车及镗孔硬质合金高速钢外圆纵车、横车及镗孔切螺纹外圆纵车、横车及镗孔切槽及切断外圆纵车、横车及镗孔92103114158811.01.01.01.00.751.80.751.00.7500.8200054119430.90.90.90.750.750.754651381.01.21.00.40.650.4HB=190可煅铸铁HB=150硬质合金高速钢外圆纵车、横车及镗孔切槽及切断外圆纵车、横车及镗孔切槽及切断10013955751.01.01.01.00.751.00.661.00000880.90.75401.20.65中等硬度不均质铜合金高速钢HB=120铝及铝硅合金高速钢外圆纵车、横车及镗孔切槽及切断40501.01.00.751.0006.铣削力的计算公式F Z=M =9.81C F•a pq F X FZ •a fW F Y FZ •a eW FZ FZ •Zd 0•n 0•60F Z•d0(N ﹒m )32⨯10•KFZ (N )P m =π•d 0•n0F Z •υ(kW)其中υ=(m/s ),υf =f •n 0=a f •Z •n 0,10001000d 0-铣刀外径mm ;n 0-铣刀转速(r/s),Z-铣刀齿数。
铣削公式和定义 工程.doc

铣削公式和定义工程公式切削速度 (vc)(m/min)主轴转速 (n)(rpm)每齿进给量 (fz)(mm)金属去除率 (Q)(cm?/min)工作台进给或进给速度 (vf)(mm/min)扭矩 (Mc)(Nm)净功率要求 (Pc) (kW)平均切屑厚度 (hm),侧铣(mm)面铣(mm)在将工件中央对准铣刀放置时。
注意: aros和arcsin用度表示特定切削力 (kc) (N/mm?)如果γ0,使用γ0= 0°,那么公式变为:特定铣刀公式具有直切削刃的刀具在特定深度的最大切削直径(mm)。
面铣 (对中工件) 直切削刃和侧铣 (ae >Dcap/2) mm。
侧铣 (ae >Dcap/2) 直切削刃,mm。
使用圆刀片的刀具在特定深度的最大切削直径(mm)。
面铣圆刀片 (ae >Dcap/2)mm。
侧铣 (ae >Dcap/2) 和圆刀片 (ap球头立铣刀在特定深度的最大切削直径(mm)。
每齿进给量 (mm/齿),刀具对中。
每齿进给量 (mm/齿),侧铣。
内圆坡走铣 (3轴) 或圆弧铣 (2轴) 计算公式周边进给率(mm/min)刀具中心进给率(mm/min)径向切深(mm)对于实体式工件, Dw = 0和 ae eff = Dm/2每齿进给量(mm)当扩孔时每齿进给量(mm)外圆坡走铣 (3轴) 或圆弧铣 (2轴)计算公式周边进给率(mm/min)刀具中心进给率(mm/min)每齿进给量(mm)铣刀主偏角– kr (度)主切削刃角 (kr) 是影响切削力方向和切屑厚度的主要因素。
刀具直径– Dc (mm)刀具直径 (Dc)在PK部位上测量,主切削刃在这里与平行刃带相遇。
Dc 是在大多数情况下出现在订货号的直径,但CoroMill 300除外,它使用D3 。
要考虑的最重要直径是(Dcap) –在实际切削深度 (ap) 处的有效切削直径–用于计算实际切削速度 (ve)。
加工中心铣孔顶刀计算

加工中心铣孔顶刀计算
加工中心是一种多功能的数控机床,可以进行多种加工操作,其中包括铣削。
在加工中心进行铣削操作时,铣孔顶刀是一个重要的刀具。
铣孔顶刀通常用于加工中心上进行孔加工,包括钻孔、铰孔和铣孔等操作。
在进行铣孔顶刀计算时,首先需要考虑的是刀具的直径和长度。
刀具的直径决定了孔的尺寸,而刀具的长度则决定了刀具在加工过程中的切削深度。
选择合适的刀具直径和长度可以确保加工质量和效率。
需要考虑切削参数,包括进给速度、转速和切削深度等。
这些参数直接影响加工中心的加工效率和切削质量。
通常情况下,进给速度和转速需要根据材料的硬度和刀具的材质来确定,而切削深度则需要根据加工要求和刀具的长度来选择。
还需要考虑刀具的刃数和刃型。
刃数越多,切削力越小,加工效率越高,但刃数过多会增加刀具的成本。
刃型的选择也会影响切削力和加工质量,不同的刃型适用于不同的加工材料和加工条件。
在进行铣孔顶刀计算时,还需要考虑切削力和刀具磨损情况。
切削力直接影响刀具的寿命和加工质量,需要通过合理的刀具选择和切削参数来控制。
刀具磨损会影响加工质量和加工效率,需要定期检查和更换刀具,以保证加工质量和效率。
总的来说,加工中心铣孔顶刀计算是一个综合考虑刀具、切削参数、切削力和刀具磨损等因素的过程。
只有在这些因素都得到合理的控制和选择,才能确保加工中心的铣孔加工质量和效率。
在实际操作中,操作人员需要根据具体的加工要求和加工条件,进行合理的铣孔顶刀计算,以获得最佳的加工效果。
铣刀盘直经与机床功率对照袁

铣刀盘直经与机床功率对照袁
目录
1.铣刀盘直径与机床功率的关系
2.铣刀盘直径的选择
3.结论
正文
在机械加工中,铣刀盘是一种常用的切削工具。
铣刀盘的直径大小和机床的功率有很大的关系,因为这直接影响到铣刀盘的切削效率和加工质量。
铣刀盘直径与机床功率的关系主要表现在以下几个方面:
首先,铣刀盘的直径决定了切削时的线速度。
线速度是切削效率的关键因素之一,它直接影响到铣刀的切削深度和进给速度。
而线速度又与机床的功率密切相关,因为机床的功率决定了电机的转速,而电机的转速又决定了铣刀盘的线速度。
其次,铣刀盘的直径也影响到切削力的大小。
切削力是切削过程中的另一个重要因素,它直接影响到铣刀的耐用性和加工质量。
铣刀盘的直径越大,切削力就越大,因此需要更高的机床功率来驱动。
因此,在选择铣刀盘直径时,需要根据实际加工情况来选择。
如果加工的材料硬度较高,或者加工的深度较大,就需要选择直径较大的铣刀盘,以提高切削效率和切削力。
但是如果机床的功率不足,就无法驱动直径较大的铣刀盘,这就需要选择直径较小的铣刀盘。
总的来说,铣刀盘直径与机床功率的关系是相互影响的。
铣刀盘的直径决定了切削的效率和质量,而机床的功率又决定了铣刀盘直径的选择。
第1页共1页。