无损探伤常用知识(图)
无损检测基础知识(全)

除了管道和无法进入内部的小直径容器只能采用双壁透照外,大多数容器壳 体的焊缝照相都采用单壁透照,透照时可以把射线源放在外面而把胶片贴在 内壁(称为外透法),也可以把射线源放在里面而胶片贴在外面(称为内透 法)。
山东特检院工程中心
1.1射线照相法的原理
x射线管是一种两极电子管,将阴极灯丝通电,使之白炽,电子就在 真空中放出 ,如果两极之间加几十千伏以至几百千伏的电压(叫做管 电压)时,电子就从阴极向阳极方向加速飞行,获得很大的动能,当 这些高速电子撞击阳极时,与阳极金属原子的核外库仑场作用,发生 轫致幅射而放出x射线。
未焊透等 • 使用过程中缺陷:如裂纹、减薄、氢损伤(氢鼓泡、氢
致裂纹)、腐蚀等
山东特检院工程中心
按检测对象分: 铸件:气孔、夹渣、夹砂、密集气孔、冷隔、密集气孔、
缩孔和疏松、裂纹 锻件:缩孔和缩管、非金属夹杂物、夹砂、龟裂、锻造裂
纹、白点 钢管:纵裂纹、横裂纹、表面划伤、翘皮和折叠、夹杂和
够达到质量要求的焊接工艺。又如,在进行铸造工艺设计时,通过射线照相
探测试件的缺陷发生情况,并据此改进浇口和冒口的位置,最终确定台适的 铸造工艺。
四、降低生产成本
在产品制造过程中进行无损检测,往往被认为要增加检测费用,从而使
制造成本增加。可是如果在制造过程中间的适当环节正确地进行无损检测,
就是防止以后的工序浪费,减少返工,降低废品率,从而降低制造成本。例
如,在厚板焊接时,如果在焊接全部完成后再无损检测,发现超标缺陷需要
返修,要花费许多工时或者很难修补。因此可以在焊至一半时先进行一次无
损检测,确认没有超标缺陷后再继续焊接,这样虽然无损检测费用有所增加,
但总的制造成本降低了。又如,对铸件进行机械加工,有时不允许机加上后
无损探伤
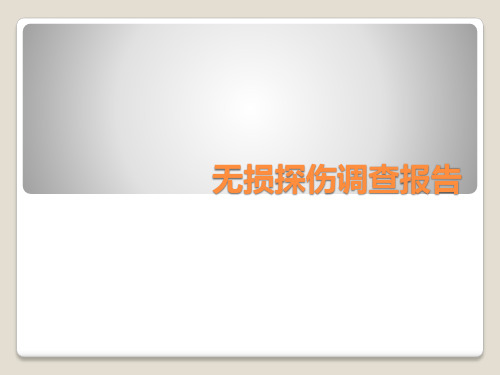
无损探伤的方法
涡流探伤:
优点: 适于自动化检测(可直接以电信号输出) 非接触式检测,无需耦合剂且速度快 适用范围较广(既可检测缺陷也可检测材质、形状与尺寸变化 等) 缺点: 只限用于导电材料 对形状复杂试件及表面下较深部位的缺陷检测有困难,检测结 果尚不直观,判断缺陷性质、大小及形状尚难 适用范围: 用于钢铁、有色金属等导电材料所制成的试件,不适于玻璃、 石头和合成树脂等非金属材料。
无损探伤的方法
渗透探伤:
渗透探伤是利用毛细现象检查材料表面缺陷的 一种无损检验方法。这种方法主要依靠于荧光渗透 液,这种渗透液在第二次世界大战期间,大量用于 检查军用飞机轻合金零件,渗透探伤便成为主要的 无损检测手段之一,获得广泛应用。
无损探伤的方法
渗透探伤: 渗透探伤包括荧光法和着色法,这两种方法都包括 渗透、清洗、显象和检查四个基本步骤。
无损探伤的前景
前景:
3.具有很大的市场潜力: 从世界的角度来看,中国的无损检测技术应用具有很 大的市场潜力,已经引起国外众多无损检测厂商的注意。 据初步估计,我国量近几年花费了数亿经费从外国引进了 大型无损检测设备。国内除了近几年来陆续有多家国外公 司进入我国开办公司或办事处,设立代理。积极参与我国 举办的各种无损检测仪器设备展览会等以外,目前更多的 国外厂商正在探索进入我国市场的途径,把进入我国无损 检测市场提上了议事日程。
无损探伤的方法
涡流探伤:
涡流探伤是利用电磁感应原理,用激磁线圈使 导电构件内产生涡电流,借助探测线圈测定涡电流 的变化量,从而获得构件缺陷的有关信息,检测导 电构件表面和近表面缺陷的一种探伤方法。
无损探伤的方法
涡流探伤:
在涡流探伤中,往往是根据被检测的形状,尺寸、材 质和质量要求(检测标准)等来选定检测线圈的种类。 常用的检测线圈有三类: 穿过式线圈、内插式线圈、探头式线圈 检测线圈的电气连接也不尽相同,有的检测线圈使用 一个绕组,既起激励作用又起检测作用,称为自感方式。 有的由激励绕组与检测绕组分别绕制,称为互感方式,有 的线圈本身就是电路和一个组成部分,称为参数型线圈。
无损检测知识培训:着色探伤和磁粉探伤

无损检测知识培训:着色探伤和磁粉探伤汪成洋一、着色探伤一、着色探伤原理介绍着色探伤是无损检测的一种方法,它是一种表面检测方法,主要用来探测诸如肉眼无法识别的裂纹之类的表面损伤,如检测不锈钢材料近表面缺陷(裂纹)、气孔、疏松、分层、未焊透及未熔合等缺陷(也称为PT检测)。
适用于检查致密性金属材料(焊缝)、非金属材料(玻璃、陶瓷、氟塑料)及制品表面开口性的缺陷(裂纹、气孔等)。
二、着色探伤的基本原理主要利用毛细现象使渗透液渗入缺陷,经清洗剂清洗使表面渗透液清除,而缺陷中的渗透液残留,再利用显像剂的毛细管作用吸附出缺陷中残留的渗透液而达到检验缺陷的目的。
三、着色探伤的工作标准1、工件表面预清理在被检表面施加渗透剂前,应使用清洗剂将工件表面清洗干净,使得被检表面无油污、锈蚀、切屑、漆层及其他污物(如检验焊缝时,在焊缝表面及焊缝边缘不应有氧化皮、焊渣、飞溅等污物),然后,使得被检工件表面要充分干燥。
2、着色渗透用渗透剂对已处理干净的工件表面均匀喷涂后,渗透5-15分钟。
3、清洗、干燥在渗透5-15分钟之后,施加显象剂之前:(1)要使用清洗剂将喷在工件表面的渗透剂清洗干净,使得被检表面要清洁(2)用干净的纱布擦干或在室温下自然干燥注:清除多余的渗透剂时,应防止过清洗或清洗不足(保证工件表面没有渗透剂即可)4、显像将显像剂充分摇匀后,对被检工件表面(已经清洗干净、干燥后的工件)保持距离150mm-300mm均匀喷涂,喷洒角度为30°- 40°,显像时间不小于7分钟。
5、观察1、观察显示迹痕,应从施加显像剂后开始,直至迹痕的大小不发生变化为止,约7-15分钟,观察显像应在显像剂施加后7~60分钟内进行。
2、观察显示迹痕,必须在充足的自然光或白光下进行。
3、观察显示迹痕,可用肉眼或5--10倍放大镜。
4、不能分辨真假缺陷迹痕时,应对该部位进行复试。
6、结果判断和记录1、根据显示迹痕的大小和色泽浓淡来判断缺陷的大小和严重程度。
无损探伤常用标准

无损探伤常用标准一、DL/T821-2002、GB3323-2005 、JB/T4730-2005对管道透照要求标准管道规格透照方式投影要求透照厚度透照次数象质计型号象质计放置备注D L /T 821-2002>Ф89 双壁单影 分段 TA=2T+hL1≤15mm 分3段(120°) L1>15mm 分4段(90°)R ’10系列 胶片侧1.DL/T821象质计放在胶片侧时其象质指数应通过对比试验或提高1级;GB/T3323、 JB/T4730可查表确定;≤Ф89~ >Ф76 双壁双影 椭圆3-10mm TA=0.8{(D-T )×T }1/2+T ≮2次(90°) Ⅰ型 射源侧≤Ф76 双壁双影 椭圆3-10mm TA=0.8{(D-T )×T }1/2+T 允许1次 Ⅱ或Ⅰ型 G B /T 3323-2005>Ф100双壁单影分段 W 查图表R ’10系列 胶片侧≤Ф100 双壁双影 倾斜椭圆透照 垂直透照WT/D 0<0.12 (90°)二次T/D 0≥0.12 (60°)三次专用 (5根等径) 射源侧平行焊缝 J B /T 4730-2005>Ф400双壁单影 单壁单影 分段 W 或T K=1.1 查图表 R ’10系列 查表胶片侧 射源侧400≥Ф>Ф100 双壁单影分段WK=1.2 查图表 R ’10系列 查表 胶片侧或射源侧 ≤Ф100双壁双影椭圆:T ≤8,q ≤Do/4 WT/D ≤0.12,90°二次 T/D >0.12,60°三次专用象质计射源侧垂直:T >8,二、DL/T821-2002标准透照厚度与象质计线号(线径)关系透照厚度≤6>6~8>8~12>12~16>16~20>20~25>25~32>32~50>50~80>80~120>120~150>150~175象质指数Z线编号15 14 13 12 11 10 9 8 7 6 5 4线径mm 0.125 0.16 0.20 0.25 0.32 0.40 0.50 0.63 0.80 1.00 1.25 1.60三、GB/T3323-2005管道A级透照应识别的丝径(丝号)W190.050 W18 0.063 W17 0.080 W16 0.100 W15 0.125 W14 0.16 W13 0.20 W12 0.25 W11 0.32 W10 0.40 W9 0.50 W8 0.63 W7 0.80 W6 1.00 W5 1.25 W4 1.60 W3 2.00 W2 2.50 W1 3.20 双壁单影 胶片侧 ≤1.2 1.2-2.0 2.0-3.5 3.5-5.0 5.0-10 10-15 15-22 22-38 38-48 48-60 60-85 85-125 125-225 225-375 >375双壁双影 射源侧<1.2 1.2-2.0 2.0-3.5 3.5-5.0 5.0-7.0 7.0-12 12-18 18-3030-40 40-50 50-6060-8585-120 120-220 220-380 >380四、JB/T4730-2005标准管子透照AB 级象质计的选用决定①透照方式②放置位置③公称厚度范围④技术等级(AB )五、DL/T821-2002、对Ф≤89管子的透照厚度与象质指数速查表管子规格透照厚度象质指数管子规格透照厚度象质指数管子规格透照厚度象质指数Ф89×4 18.75 11 Ф48×3 12.29 12 Ф24×2 7.3 14 Ф89×5 21.39 10 Ф48×3.5 13.48 12 Ф24×3 9.34 13 Ф89×6 23.85 10 Ф48×4 14.61 12 Ф24×4 11.15 13 Ф89×7 26.17 9 Ф48×5 16.73 11Ф22×2 7.06 14 Ф83×4 18.22 11 Ф45×3 11.97 13 Ф22×3 9.03 13 Ф83×5 20.79 10 Ф45×4 14.24 12 Ф22×4 10.78 13 Ф83×6 23.19 10 Ф45×5 16.31 11Ф83×7 25.45 9 Ф20×2 6.8 14 Ф83×8 27.59 9 Ф42×3 11.65 13 Ф20×3 8.71 13Ф42×4 13.86 12 Ф20×4 10.4 13 Ф76×4 17.58 11 Ф42×5 15.88 12Ф76×5 20.07 10 Ф19×2 6.66 14 Ф76×6 22.39 10 Ф40×2.5 10.24 13 Ф19×3 8.54 13 Ф76×7 24.58 10 Ф40×3 11.43 13 Ф19×410.19 13 Ф76×8 26.66 9 Ф40×4 13.6 12Ф18×2 6.52 14 Ф70×3 14.34 12 Ф38×2.5 10.04 13 Ф18×3 8.36 13 Ф70×4 16.99 11 Ф38×3 11.19 13 Ф18×4 9.98 13 Ф70×5 19.42 11 Ф38×4 13.32 12Ф70×6 21.67 10 Ф17×2 6.38 14 Ф70×7 23.8 10 Ф35×2.5 9.71 13 Ф17×3 8.18 13Ф35×3 10.83 13 Ф17×4 9.76 13 Ф63.5×3 13.77 12 Ф35×4 12.90 12Ф63.5×4 16.34 11 Ф16×2 6.23 14 Ф63.5×5 18.68 11 Ф32×2.5 9.37 13 Ф16×3 7.99 14Ф32×3 10.46 13 Ф16×4 9.54 13 Ф60×3 13.46 12 Ф32×4 12.47 12Ф60×4 15.97 12 Ф14×2 5.9 15 Ф60×5 18.26 11 Ф30×2.5 9.13 13 Ф14×3 7.59 14Ф30×3 10.20 13 Ф14×4 9.05 13 Ф57×3 13.18 12 Ф30×4 12.15 12Ф57×4 15.64 12 Ф12×1.5 4.67 15 Ф57×5 17.89 11 Ф29×2.5 9.01 13 Ф12×2 5.75 15Ф29×3 10.06 13 Ф12×2.5 6.39 14 Ф51×3 12.6 12 Ф29×4 12 13Ф51×4 14.97 12 Ф10×1.5 4.35 15Ф51×5 17.13 11 Ф25×2 7.42 14 Ф10×2 5.2 15Ф25×3 9.49 13 Ф10×2.5 5.96 15Ф25×4 11.33 13六、管道焊缝射线探伤透照片数表七、DL/T821-2002、GB/T3323-2005、JB/T4730-2005钢管道质量分级(底片评级)圆缺T<25,评定区10×10 条缺未焊透(不加垫板)内凹与(咬边) 备注T≤10 10-15 15-25单个多个Do>100(Φ89)Do≤100(Φ89)Do>100(Φ89)Do≤100(Φ89)ⅠJB4730 1 2 3 不允许不允许不允许不允许不允许不允许1、综合评级:JB/T4730:在条形DL/T821 1 2 3 不允许不允许不允许不允许比≤10%T深≤1.0累长≤25%总长比≤10%T深≤1.0累长≤30%总长评定区缺陷等级相同,则降一级,不同时以低级别定;DL/T821:要求各级别之和-1,(大Ⅲ者为Ⅳ)GB3323 1 2 3 不允许不允许不允许不允许/ 比≤10%T深≤1.0长不限ⅡJB4730 3 6 94≤T/3≤2012T内6L≯T4比≤10%T深≤1.0单长≤T/3(4 ≤20 )6T内≯T(4)300内≯30比≤10%T深≤1.0累长≤10%总长比≤15%T深≤1.5单长3T内≯T累长≯100比≤15%T深≤1.5累长≤30%总长GB3323:二种之和-1,三种之和-22、发现裂纹未熔合即为Ⅳ级DL/T821 3 6 912412-60T/3T≥6020内6L≯T410%T深≤1.5T≤12时≯4,12-36时T/3≥36时≯12, 12T内6L≯T10%T深≤1.5累长≤10%总长比≤15%T深≤2.0累长≤25%总长比≤15%T深≤2累长≤30%总长GB3323 3 6 912412-60T/3T≥6020内6L≯T不允许15%T深≤1.5累长≤10%周长/比≤20%T深≤2.0长不限ⅢJB4730 6 12 186≤2/3T306T内3L≯T6比≤15%T 深≤1.5单长≤2/3T(6≤30)3T内≯T;300内≯40比≤15%T深≤1.5累长≤15%总长比≤20%T深≤3.0≤30%总长累长≯100比≤20%T深≤2.0累长≤30%总长DL/T821 6 12 18 T≤969-452/3TT≥45306T内3L≯T6比≤15%T 深≤2.0T≤9时≯6,9-30时2/3T≥30时≯20,6T、3L内≯T比≤15%T深≤2.0总长≤15%周长比≤20%T深≤3.0累长≤25%总长比≤20%T深≤3.0累长≤30%总长GB3323 6 12 18 T≤969-452/3TT≥45306T内3L≯T同条渣比≤20%T深≤2.0累长≤15%周长/比≤25%T深≤3.0长不限Ⅳ①深孔②Φ>T/2③放宽1-2点备注①圆缺,长:宽=3②评定区③点数换算④不计点⑤Ⅰ级1评定区T≤252被检厚度<12T或6T可按比例换算DL/T820规定氩弧焊口不允许未焊透DL/T820允许咬边。
常用无损探伤及使用原则

工业无损探伤的方法很多,目前国内外最常用的探伤方法有五种,即人们常称的五大常规探伤方法.本文将首先介绍五大常规探伤方法及其特点,并结合电厂管道焊接的特定条件和需求,选出适合探伤方法。
除以上五大常规方法外,近年来又有了红外,声发射等一些新的探伤方法.五大常规方法是指:1、射线探伤法 RT:检测内部有气孔,夹渣、未焊透等体积型缺陷,不易发现裂纹等面积型缺陷。
2、超声波探伤法 UT:纵波,横波适用于探测内部缺陷, 表面波适宜于探测表面缺陷,但对表面的条件要求高.3、磁粉探伤法 MT:能探查气孔, 夹杂,未焊透等体积型缺陷, 但更适于检查因淬火, 轧制, 锻造,铸造,焊接,电镀,磨削,疲劳等引起的裂纹。
4、涡流探伤法 ET:能确定表面及近表面缺陷的位置和相对尺寸5、渗透探伤法 PT。
能确定表面开口缺陷的位置、尺寸和形状。
一、射线探伤方法:射线探伤是利用射线的穿透性和直线性来探伤的方法. 这些射线虽然不会像可见光那样凭肉眼就能直接察知,但它可使照相底片感光,也可用特殊的接收器来接收.常用于探伤的射线有 x 光和同位素发出的γ射线,分别称为x光探伤和γ射线探伤.当这些射线穿过(照射)物质时,该物质的密度越大,射线强度减弱得越多,即射线能穿透过该物质的强度就越小.此时,若用照相底片接收,则底片的感光量就小;若用仪器来接收,获得的信号就弱。
因此,用射线来照射待探伤的零部件时,若其内部有气孔,夹渣等缺陷,射线穿过有缺陷的路径比没有缺陷的路径所透过的物质密度要小得多,其强度就减弱得少些,即透过的强度就大些,若用底片接收,则感光量就大些,就可以从底片上反映出缺陷垂直于射线方向的平面投影; 若用其它接收器也同样可以用仪表来反映缺陷垂直于射线方向的平面投影和射线的透过量。
由此可见,一般情况下,射线探伤是不易发现裂纹的,或者说,射线探伤对裂纹是不敏感的.因此,射线探伤对气孔,夹渣,未焊透等体积型缺陷最敏感.即射线探伤适宜用于体积型缺陷探伤,而不适宜面积型缺陷探伤。
无损探伤常用标准

条缺
未焊透(不加垫板)
内凹与(咬边)
备注
T≤10
10-15
15-25
单个
多个
Do>100(Φ89)
Do≤100(Φ89)
Do>100(Φ89)
Do≤100(Φ89)
Ⅰ
JB4730
1
2
3
不允许
不允许
不允许
不允许
不允许
不允许
1、综合评级:
JB/T4730:
在条形评定区缺陷等级相同,则降一级,不同时以低级别定;
>44-54
/
/
/
/
/
双双/双单胶片侧
100<Φ≤400
≤2.0
>2-3.5
>3.5-5.5
>5.5-11
>11-17
>17-26
>26-39
>39-51
>51-64
>64-85
>85-125
>125-225
>225-375
>375
/
单壁单影
射源侧>Φ400
≤2.0
>2-3.5
>3.5-5.0
>5.0-7
0.063
W17
0.080
W16
0.100
W15
0.125
W14
0.16
W13
0.20
W12
0.25
W11
0.32
W10
0.40
W9
0.50
W8
0.63
W7
0.80
W6
1.00
W5
1.25
W4
1.60
W3
2.00
W2
NDT 无损检测知识大全

射线检测(RT)是一种透射光成像技术,射线透照的必备条件: 1. 射线源(主要作用是提供可穿透被检工件的透射光); 常用的射线源有X光机、咖玛源、电子直线加速器、中子源。[X射线机、高能X射线 机、γ射线机] 2. 射线感测元件(主要作用使投射光成像); 常用射线感测元件有X光胶片、莹光屏[增感屏]、图象增强器、半导体晶体阵列。 3. 合适的工件状态; 工件表面源侧空间距离满足透照焦距需要,工件背表面的可接近性。 4. 其它附助设备; 象质计、铅字母[铅标记]、贴片夹、暗带及暗室处理设备[胶片处理设备]等。 5. 合适的透照场所(主要作用是提供有效的射线防护); 因射线透照对人体有伤害,透照场所受环保部门监督。
无损检测大全
(一)无损检测的定义和分类
定义:在不损坏试件的前提下,以物理或化学方法为手段,借助先进的技术和设备器材,对 试件的内部及表面结构、性质、状态进行检查和测试的方法。[而用人的肉眼为手段称之为 宏观检查。]
无损探伤(NDI):是无损检测早期阶段的名称,其涵义是探测和发现缺陷。 无损检测(NDT):是当前阶段的名称,其内涵不仅仅是探测缺陷,还包括探测试件的
胶片照象法;锅炉及压力容器射线检验的主要方法,射线感测元件为胶片。 实时成象法;一般用于自动检测线,射线感测元件为图象增强器或半导体晶体阵
列。 C、按记录方式不同分为
射线照相法 荧光屏成像法 气体电离法 电视成像法
射线照相法原理 射线穿透物质时,其强度会由于物质的吸收和散射而发生衰减,衰减的程度取决于物质
金属无损磁粉探伤基本知识
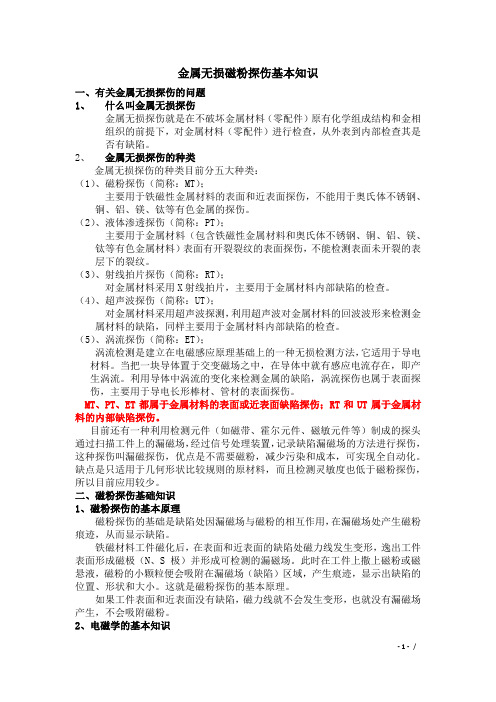
金属无损磁粉探伤基本知识一、有关金属无损探伤的问题1、什么叫金属无损探伤金属无损探伤就是在不破坏金属材料(零配件)原有化学组成结构和金相组织的前提下,对金属材料(零配件)进行检查,从外表到内部检查其是否有缺陷。
2、金属无损探伤的种类金属无损探伤的种类目前分五大种类:(1)、磁粉探伤(简称:MT);主要用于铁磁性金属材料的表面和近表面探伤,不能用于奥氏体不锈钢、铜、铝、镁、钛等有色金属的探伤。
(2)、液体渗透探伤(简称:PT);主要用于金属材料(包含铁磁性金属材料和奥氏体不锈钢、铜、铝、镁、钛等有色金属材料)表面有开裂裂纹的表面探伤,不能检测表面未开裂的表层下的裂纹。
(3)、射线拍片探伤(简称:RT);对金属材料采用X射线拍片,主要用于金属材料内部缺陷的检查。
(4)、超声波探伤(简称:UT);对金属材料采用超声波探测,利用超声波对金属材料的回波波形来检测金属材料的缺陷,同样主要用于金属材料内部缺陷的检查。
(5)、涡流探伤(简称:ET);涡流检测是建立在电磁感应原理基础上的一种无损检测方法,它适用于导电材料。
当把一块导体置于交变磁场之中,在导体中就有感应电流存在,即产生涡流。
利用导体中涡流的变化来检测金属的缺陷,涡流探伤也属于表面探伤,主要用于导电长形棒材、管材的表面探伤。
MT、PT、ET都属于金属材料的表面或近表面缺陷探伤;RT和UT属于金属材料的内部缺陷探伤。
目前还有一种利用检测元件(如磁带、霍尔元件、磁敏元件等)制成的探头通过扫描工件上的漏磁场,经过信号处理装置,记录缺陷漏磁场的方法进行探伤,这种探伤叫漏磁探伤,优点是不需要磁粉,减少污染和成本,可实现全自动化。
缺点是只适用于几何形状比较规则的原材料,而且检测灵敏度也低于磁粉探伤,所以目前应用较少。
二、磁粉探伤基础知识1、磁粉探伤的基本原理磁粉探伤的基础是缺陷处因漏磁场与磁粉的相互作用,在漏磁场处产生磁粉痕迹,从而显示缺陷。
铁磁材料工件磁化后,在表面和近表面的缺陷处磁力线发生变形,逸出工件表面形成磁极(N、S极)并形成可检测的漏磁场。
无损探伤2-射线

γ射线的半衰期
1.3 射线的产生
射线的性质,有利、有弊,应该科学地加以 利用和防范!射线学就是研究如何利用与防范射 线的科学。下面介绍产生x射线的主要设备: (1)x光管基本组成: • 阴极部件:灯丝(钨丝)——发射电子; 阴极罩——聚焦电子。 • 阳极部件:阳极靶——接收电子; 冷却介质——散热作用。 • 真空管——玻璃或金属陶瓷制作的真空外罩。
2、电离检测法
当射线通过气体时与气体分子撞击,有的气体分子 失去电子成为正离子,有的气体分子得到电子成为负离子, 此即气体的电离效应。电离效应将会产生电离电流,电离 电流的大小与射线的强度有关。如果将透过试件的X射线 通过电离室测量射线强度,就可以根据电离室内电离电流 的大小来判断试件的完整性。 这种方法对缺陷性质的判别较困难,只适用于形状 简单、表面工整的工件,应用较少。
2.2 射线检测的基本原理
射线检测主要是利用它的指向性、穿透性、衰 减性等几个基本性质。具体分析(参考下图):
δ=A+X+B
X — 缺陷厚度; A — 缺陷上部厚度; B —缺陷下部厚度;
Iδ μ
μx
I0
A
X
δ
B
Ix
(1)无缺陷区的射线透射强度: Iδ=I0·-μδ e 衰减定律
(2)有缺陷区的射线透射强度: Ix = I0·-μA · -μˊX ·e-μB e e = I0·-μA·-μB ·- μX · μX ·- μˊX e e e e e = I0·-μδ ·- (μˊ-μ)X e e = Iδ · - (μˊ-μ)X e (3-2)
无损探伤

无损探伤无损探伤原理(Nondestructive Testing,NDT)无损探伤是在不损坏工件或原材料工作状态的前提下,对被检验部件的表面和内部质量进行检查的一种测试手段。
分类:射线探伤(Radiography T esting---简称RT);适用于材料表面和内部不连续的检测,对体积状缺陷有很好的检测效果。
X射线/Y射线检验;主要用于薄壁工件检验。
咖玛射线检验;一般用于中、厚板工件检验。
高能射线检测;主要用于厚壁工件检验。
中子射线检测;主要用于放射性材料检测和有机材料检测。
超声波探伤(Ultrasonic T esting---简称UT);这是一种应用灵活、发展速度很快的检测方法,主要用于材料内部缺陷检测和材料厚度测量。
磁粉探伤(Magnetic powder T esting---简称MT);它是发展最早的一种无损检测方法,主要用于铁磁性材料表面和近表面缺陷检测。
渗透探伤(Penetrate T esting---简称PT);PT 是除目视检测方法外最简单的一种检测方法,适用于一切非多孔性材料表面开口性缺陷检测。
无损探伤标准:A WS D 1.1/D1.1M-2008A WS D 1.6/D1.1M-2007EN 1290:1998+A1:2002(MT)EN1435-1997+A2:2003(RT)EN12517-1:2006(RT)EN1714-1997+A2:2003(UT)EN571-1-1997(PT)ASME IX-2007等等超声波探伤UT和射线探伤RT用于内部检测。
钢结构多用超声波,管道多用射线检测。
锻件用超声波,铸件用射线。
板材,奥氏体不锈钢厚大于6mm的用超声波检测。
磁粉探伤MT和渗透测试PT用于表层探伤,主要用于2mm之内.无损检测的目地1、改进制造工艺;2、降低制造成本;3、提高产品的可靠性;4、保证设备的安全运行。
X射线无损探伤RTX射线无损探伤原理利用X射线可以穿透物质和在物质中有衰减的特性来发现其中缺陷的一种无损探伤方法。
- 1、下载文档前请自行甄别文档内容的完整性,平台不提供额外的编辑、内容补充、找答案等附加服务。
- 2、"仅部分预览"的文档,不可在线预览部分如存在完整性等问题,可反馈申请退款(可完整预览的文档不适用该条件!)。
- 3、如文档侵犯您的权益,请联系客服反馈,我们会尽快为您处理(人工客服工作时间:9:00-18:30)。
无损探伤常用知识一、概述无损检测又称无损探伤,日本称“非破坏检查”。
它的重要地位是由其可靠性、安全性与经济性所决定的。
可靠性是指它可以在不损坏工件完好的情况下100%地检测,所以不会产生像破坏性取样检测方法所固有的漏检问题。
安全性是指它能把隐藏在材料与结构中的危害性缺陷检测出来,因而它的使用会使被检工件能安全运行。
经济效益已是国内外人所共知的事实。
由于无损检测技术的三大优越性,近年来世界各国对无损检测技术的投资也是与日俱增,美国在70年代无损检测设备的平均率就达10.5%,其中新设备增长率高达21%以上。
无损检测技术本质上属于物理检测范畴,近年来随着科学技术的发展,它成了以物理学为基础,电子学、机械学乃至化学等学科作为手段的交叉性技术学科。
无损检测大致为以下几类:㈠涡流检测(ET)主要原理:根据电磁感应定律,将一金属放入通以变频电流产生的交变磁场中去,就会产生感应电流,即涡流。
涡流检测特别适用于金属材料的自动探伤,因为涡流探伤法不象超声探伤那样需要耦合剂,所以可以实现高速高温探伤。
例如:管、棒、丝。
㈡磁粉探伤(MT)磁粉探伤主要适用于铁磁性物质的表面及近表面探伤。
原理:利用铁磁性物质内的磁导率的变化,导致切割表面或近表面磁感应线在缺陷附近,离开或进入试样表面所形成的漏磁场,通过漏磁感应在缺陷处吸引磁粉。
磁粉探伤分为干法和湿法(湿法又分为油荃于水荃),又分为荧光与非荧光检测,常用的是非荧光磁粉探伤。
适用于锻件、铸件、焊逢的表面检测。
㈢射线探伤(RT)射线,这里只介绍χ射线与γ射线,此外中子射线也渐渐用于探伤,但不普及。
χ射线是靠来自χ射线管中阴极上高压电子撞击到阳极靶上而产生的。
而γ射线是某些稳定元素被中子轰击后转变为不稳定的放射性同位素时放出来的。
χ射线与γ射线都是波长很短的电磁波,因而对钢铁的穿透力都很强。
射线探伤主要用于铸件与焊缝探伤。
㈣渗透探伤(PT)主要根据毛细管现象、是否渗透,液体及固体种类、接触面光洁度、毛细管直径等因素决定,当其它条件相同时,毛细管直径越小,液体渗透性就越强,一般深为0.02mm宽为0.001mm的表面裂纹是容易发现的。
渗透法包括荧光渗透法和着色渗透法。
我厂一般用着色渗透法。
主要适用于各种材料包括非金属材料表面开口缺陷的检测。
㈤超声波探伤(UT)超声波探伤是利用超声波的性质判断材料缺陷和异常的一种物理手段。
超声波是看不见听不到的。
金属材料超声波探伤用的超声波通常是指频率为1MHZ—10MHZ范围的弹性波,其波长为1mm-0.1mm的量级,就一般工业用金属材料的多晶结构而言,此波长范围内的超声波能够很好的传播。
通常超声波探伤就是利用超声波探测并确定隐藏在金属材料内部缺陷的技术,就目前而言,主要是根据物体内部出现缺陷区域的表面发生超声波的散射的原理进行工作的。
这就要求了解缺陷在产生缺陷回波上有什么影响,即涉及超声波与缺陷相互作用的问题。
由于材料中实际缺陷的千差万别,故对形成缺陷回波间的区别,一般难于说清楚,加之缺陷回波声的特性的影响因素很多,要完全说清楚事实上难于办到。
缺陷位置、形状大小及性质等影响,在理论上简单的考察,但在实际探伤时如何进行考察,还需从理论上和实践经验上进行综合分析。
超声波的产生和接收:声波是一种机械波,超声波是一种频率很高的声波,通常可用电磁方式使纸片振动产生声波,但用这种方法产生超声波,效率很低,因此可使用具有压电或电磁致伸缩效应的材料产生超声波,当在压电材料(也称压电晶片)两面的电极上加以电压,它就会按照电压的正负和大小,在厚度方向产生伸、缩的特点。
利用这一性质,若加上变频电压就会产生变频伸缩现象,如果把这个伸缩振动设法加到被检材料上,材料质点也会随之产生振动,从而产生声波,在材料内传播。
超声波的接收是同超声波的发射完全相反的过程,即超声波射达被检材料表面,使表面产生振动,并使压电晶片随之产生伸缩,在电极间产生电压,此电压经放大后,就可在仪器示波管上进行观察和测定。
也就是由电能转换为机械能,再由机械能转换为电能。
1.探头:超声波探头探型式、晶片尺寸大小、功用,使用条件基本上分成直探头、斜探头、双晶探头、聚焦探头。
探伤中常用的是单晶片直探头和斜探头。
直探头可用于锻件、铸件、焊缝的超声波探伤。
双晶探头主要用于薄工件的探伤。
斜探头主要应用焊缝的超声波探伤。
2.探伤方法分类及脉冲反射法原理探伤方法分类:可分成脉冲反射法、穿透法和共振法三大类。
其中脉冲反射法广泛。
脉冲反射法:是根据超声波在物体内传播中遇到异质界面而产生反射的原理,它是通过探伤仪荧光屏上反射波的位置、波高及形状尺寸对物体中缺陷及材料的性质进行判断的一种检测方法。
穿透法:是根据声波穿透物体后的能量变化状况,来判断物体内部质量的方法。
两个探头分别放在被检物体的相对两面,一个为发射探头,一个为接收探头,主要适用于自动检测,对探头位置和相对距离要求严格。
共振法:共振法是用频率可调的连续正弦波激励压电晶片,使其发射的超声波频率改变,利用工件呈共振状态测量工件厚度或判断有无缺陷的方法。
共振法主要用于制成共振式测厚仪,测量表面光滑的板材、管件及复合材料的厚度及夹层缺陷。
3 按显示方式分类超声波探伤图形的显示方式:有A型显示、B型显示,目前材料探伤几乎用的全是A型显示。
A型显示是用直角坐标显示的方法。
B型显示即为图显示,B型显示可把缺陷在一个垂直断面上分布情况显示出来,比较直观,用于医学方面较多。
4 直探头探伤的定位定量定位:只要仪器线性好,可利用T、F、B三者的关系对缺陷定位。
定量:对面积大于截面或长度大于声束截面直径的缺陷,可采用6dB 法确定缺陷的大小和长度。
对于面积小于声束截面的缺陷可采用当量法评价其当量大小,一般实际探伤中所采用的当量法主要是试块对比法和A VG曲线法及当量计算法,焊缝检测用DAC法。
AVG法(距离—增益—当量)又称DGS。
斜探头DAC曲线又称距离—波幅曲线锻件常见缺陷:残余缩孔、疏松、非金属夹杂物、裂纹、白点、粗晶、偏析。
焊接缺陷:咬边、焊瘤、烧穿、未焊透、未熔合、夹渣、气孔、裂纹、焊缝尺寸不合格。
咬边、焊瘤、烧穿、焊缝尺寸不合格为表面缺陷,其余为内部焊接缺陷。
二、无损检测术语平底孔:平底的圆柱形盲孔,其圆平面用作为超声反射体。
横孔:平行于探测面并于所置的探头成正交方向的圆柱形钻孔,其圆柱面形成的反射体。
探伤灵敏度:在规定条件(频率、增益、抑制等)下能探出最小缺陷的能力。
扫查灵敏度:为防止漏检,在初探中所采用的较规定灵敏度高的灵敏度。
规定灵敏度:根据产品的技术要求(规程、说明书等)确定的灵敏度。
当量:用于缺陷比较的某种类型的人工缺陷的大小。
当量法:在一定的探测条件下,用某种规则的人工缺陷反射体尺寸来表证被检件中实际缺陷相对尺寸的一种定量方法。
平底孔当量:指相同距离上的缺陷给出的超声指示与某一尺寸平底孔的超声指示相当。
半波高度法:在同一探测条件下,将探头从获得最大反射回波的位置,移动至回波高度为原来的半值来评价反射体尺寸的方法。
缺陷指示长度:将超声探伤估定缺陷的始端和终端位置投影在探伤材料表面上并连接其两点间的长度。
缺陷指示面积:缺陷指示长度于宽度或高度的乘机三、常用国内标准和欧洲标准的评判比较GB 7233-87本标准规定了厚度等于或大于30mm的碳钢和低合金钢铸件的超声探伤方法:以及根据超声探伤结果对铸件进行质量评级的方法。
所用的超声探伤方法仅限于A型显示脉冲反射法。
在订货时,由供需双方商定铸钢件超声探伤的以下要求:a.检测的区域及使用的探头;b.纵波直探头探伤灵敏度;c.铸钢件质量的合格等级,允许对平面型缺陷和非平面型缺陷提出不同的质量等级要求。
纵波直探头探伤允许采用φ3、φ4、φ6当量平底孔三种灵敏度。
供需双方应规定铸钢件每个区域的探伤灵敏度。
按交货时铸钢件的外形,将铸钢件的截面厚度划分为三层:外层、内层、外层。
铸钢件的厚度或截面尺寸小于90mm者,各层各占厚度或截面尺寸的三分之一。
铸钢件的厚度或截面尺寸等于或大于90mm者,凡是距铸钢件某一表面30mm以内的范围为外层,其余部分为内层。
评定时,采用317×317mm2(面积约100000mm2)的评定框。
位于评定框边界线上的缺陷,计算缺陷的尺寸时,只计入该缺陷框内部分的尺寸。
平面型缺陷质量等级的划分非平面型缺陷质量等级的划分②一个缺陷的面积,等于该缺陷的最大尺寸和与其垂直方向的最大尺寸之积。
③位于外层的间距小于25 mm的两个或多个缺陷,在计算一个缺陷的面积时,视为一个缺陷。
其“一个缺陷的面积”等于这些缺陷面积之和。
DIN1690 第二部分SEP1922见附页超声波检验时缺陷的最大允许值YB/T 036.10-92本标准适用于冶金设备(包括矿山、冶炼、轧钢、环保等)的零部件厚度或直径不小于60mm的碳钢及合金钢锻件的超声波探伤。
本厂常用本标准2级。
缺陷等级分类A1 单个缺陷的等级分类按照表A1规定表A1A2 条状缺陷的等级分类按表A2的规定表A2A3 允许中心部位(1/5直径或厚度)存在密集缺陷区,但其中最大当量的缺陷不得超过表A1中相应级别的规定。
非中心部位允许存在的密集缺陷应由供需双方商定。
A4 如能判断确认是白点、裂纹和缩孔者可不受上述条款所限,应评为超标缺陷。
A5 锻钢件探伤质量验收等级及本标准未尽事宜应由供需双方协商确定。
SEP1921适用于直径或边长大于100mm的锻件和锻造条钢的超声波检查。
无延伸:即我们说的单个缺陷,但缺陷间距应大于5倍较大者。
有延伸:探头移动时,至少在一个方向无振幅下降,用半值法求延伸长度,要考虑探头的声场特性。
验收条件注:面积大小由用户规定,氧气瓶压机规定为1300cm相邻缺陷间距应≥相邻缺陷中较大缺陷直径的5倍,否则算作有延伸信号:信噪比≤dB时,应与用户协商。
JB/T 5000.15-1998本标准中超声波探伤不适用于曲率半径小于125mm、探测厚度小于50mm 锻件的纵波探伤以及内外经之比小于75%的环形或筒形锻件超声痕波探伤。
也不适用于澳氏体不锈钢等粗晶材料的超声波探伤。
本厂常用本标准Ⅱ级。
不同缺陷类型的质量等级划分缺陷类型的质量等级。
2 密集区缺陷范围的计算是以密集区最大长度范围×最大宽度范围×最大深度范围。
相邻密集区间的间距不得小于150mm。
否则,应视为一个密集区。
存在多个密集区时,应分别计算其密集区范围,然后累积求和,按累积值评定。
若密集区深度范围小于或等于50mm时,则按50mm计算其深度范围;若密集区长度范围小于或等于50mm时,则按50mm 计算其长度范围。
3 由于超声波探伤存在局限性和不足,除了从生产工艺、缺陷产生的部位及其大致走向和分布能对缺陷性质进行估判外,纯粹从超声波探伤技术上是无法对缺陷进行定性的,因此,在使用5.11.2时,最好用其他有效方法对缺陷定性进行辅助说明,如缺陷已露出表面、金相检验等方法。