挡纱肋盘压铸模设计
压铸模具结构设计方案(PPT 57页)_15082

彈簧 斜度配
檔塊 斜銷
A向
滑塊座 滑塊入子
定位銷
四.2.抽芯結構
滑塊機構
导滑T形槽
螺絲連接
导滑T形槽張板
四.2.抽芯結構
滑塊機構
四.2.抽芯結構
滑塊機構
四.2.抽芯結構
滑塊機構
四.2.抽芯結構
油壓抽芯機構
油壓:產品抽芯行程太長(一般大於50mm),或側凹形狀均在 母模側,或母模側外觀不允許有拆模線時使用.
二.機器選擇配置 a.根據產品性質及要求確定冷,熱室機選擇 b.確定模穴數,並計算產品總投影面積Ap(cm2)
c. 估算鎖模力 壓鑄機機械能力用鎖模力表示,鎖模力大小一 般以頓來表示.故估算如下: T=1.3A*P/1000 其中:A為流道,溢流井,產品面積總和(cm2) A可估算為1.3~1.5Ap(產品投影面積) P為鑄造壓力(kg/cm2) 鑄造壓力大小確定原則如下:
成 Auto CAD 2D ,產品形狀復雜的一面作為公模﹐而產品 形狀簡單的或者有外觀要求的一面作為母模 (注:產品與模 具是mirror關係) c.模具中心線﹐射出中心線﹐模框及模仁大小……
四yout設計
d.根據產品定主分型面,確定射出中心與產 品之相對位置如需滑塊抽心或抽真空等結
構時方案需同時布置.一般有公,母平面圖,
X斷面圖,Y斷
面圖.必要時增
加視圖.
PT3/8
PT3/8
模具中心 導柱
機台中心
母平面圖
PT1/4
PT1/4
PT3/8
PT1/4
射出中心
四yout設計
公模平面圖
压铸模具设计范文

压铸模具设计范文压铸模具设计是指为了生产压铸件而设计的模具,其主要任务是将液态金属注入模具中,并在模具中冷却、凝固,最终得到所需形状的金属零件。
压铸模具设计的主要工作包括设计模具的结构、选材、计算模具的合理尺寸和形状等。
一、压铸模具结构设计1.模具整体结构设计:根据压铸件的形状和尺寸,确定模具的整体结构。
一般情况下,压铸模具采用上下模结构,上模为固定模,下模为活动模。
针对复杂形状的压铸件,可能需要设计多个滑模和拉杆。
2.模腔设计:根据压铸件的形状和尺寸,确定模腔的几何形状和尺寸。
模腔的设计应保证在模具关闭时,模腔中的液态金属能够充满整个腔体,并且在冷却凝固过程中,金属能够均匀收缩,避免产生缩孔和其他缺陷。
3.浇口和导流系统设计:浇口和导流系统的设计对于压铸件的质量和生产效率有着重要的影响。
浇口的设计应尽量避免金属的湍流流动,避免气泡的产生。
导流系统的设计应考虑金属的顺序填充和排气,以及冷却和凝固过程中的温度控制。
二、压铸模具选材压铸模具的选材应根据金属的性能和压铸工艺的要求来确定。
通常情况下,模具会选用高强度和耐磨损的合金钢作为材料,以保证模具的使用寿命和精度。
同时,还需要考虑模具的热传导性能,以确保压铸件能够快速冷却、凝固。
三、压铸模具尺寸和形状计算1.模具尺寸计算:模具尺寸的计算包括模腔尺寸、模板尺寸、滑模尺寸、导流系统尺寸等。
模具尺寸的计算需要考虑压铸件的最终尺寸、缩孔和收缩率等因素。
2.模具形状计算:模具的形状计算主要是指模腔内部的曲面和棱角的设计。
对于复杂形状的压铸件,需要使用CAD软件进行三维建模和形状优化,以确保模具的制造精度和压铸件的质量。
压铸模具设计需要充分考虑压铸件的形状和尺寸、材料的性能、压铸工艺要求等因素,通过合理的结构设计、选材和计算,能够提升压铸件的质量和生产效率。
在设计过程中,还需要考虑模具的制造难度和制造成本,以确保模具的可行性和经济性。
压铸件设计及压铸模设计

压铸件的精度较高,表面光洁,且稳定性好,因此,压铸件具有很好的互换性。
压铸件的尺寸精度取决于压铸件的设计、模具结构以及模具制造的质量。
通常,压铸件的尺寸精度比模具的精度低三到四级左右。
压铸件尺寸稳定性取决于工艺因素、操作条件、模具修理次数及其使用期限等各方面因素。
压铸件的尺寸精度一般按机械加工精度来选取,在满足使用要求的前提下,尽可能选取较低的精度等级。
此外,同一压铸件上不同部位的尺寸可按照实际使用要求选取不同的精度,以提高经济性。
1. 长度尺寸压铸件能达到的尺寸公差及配合尺寸公差等级见表3.1。
压铸件的表面形状和位置主要由压铸模的成型表面决定,而压铸模成型表面的形位公差精度较高,所以对压铸件的表面形位公差一般不另行规定,其公差值包括在有关尺寸的公差范围内。
对于直接用于装配的表面,类似机械加工零件,在图中注明表面形状和位置公差。
对于压铸件而言,变形是一个不可忽视的问题,整形前和整形后的平面度和直线度公差按表3.7选取。
平行度、垂直度和倾斜度公差按表3.8选取。
同轴度和对称度公差按表3.9选取。
压铸件的表面粗糙度取决于压铸模成型零件型腔表面的粗糙度,通常压铸件的表面粗糙度比模具相应成型表面的粗糙度高两级。
若是新模具,压铸件的表面粗糙度应达到GB 1031—83的R a2.5~0.63 µm,要求高的可达到R a0.32 µm。
随着模具使用次数增加,压铸件的表面粗糙度逐渐增大。
不论零件如何复杂,都可以将其分解为壁、连接壁的圆角、孔和槽、肋、凸台、螺纹等部分,这些部分就是组成零件的结构单元。
压铸件壁的厚薄对其质量有很大的影响。
压铸件表面约0.8~1.2 mm的表层由于快速冷却而晶粒细小、组织致密,因为它的存在使压铸件的强度较高。
而若是厚壁压铸件,其壁中心层的晶粒粗大,易产生缩孔、缩松等缺陷。
通常,压铸件的力学性能随着壁厚增加而降低,而且也增加了材料的用量和压铸件的重量。
图3.1为铸件壁厚对抗拉强度的影响。
压铸工艺及模具设计压铸8_p21

有关要素的形位公差
选用精度
导柱固定部位的轴线与导滑部分轴线的同轴度 圆形镶块各成型台阶表面对安装表面的同轴度
导套内径与外径轴线的同轴度 套板内镶块固定孔轴线与其它各套板上的孔的公共轴线的同轴度
导柱或导套安装孔的轴线与套板分型面的垂直度 套板的相邻两侧面与工艺基准面的垂直度
被测面最大直 线长度
公差值
≤160 0.06
>160~ 250
0.08
>250~ 400
0.10
>400~ 630
0.12
(mm)
>630~ 1000
0.16
>1000~ 1600
0.20
表8-6 导柱、导套对座板安装面的垂直度
(mm)
导柱、导套的有效 长度
公差值
≤40 0.015
>40~63 0.020
压铸工艺及模具设计
滑 导柱,导套(斜销,
动
弯销等)
配 合
推杆
零
件
复位杆
模 动、定模套板,支 架 承板,垫块,动、 结 定模底板,推板, 构 推杆固定板
零
件
T8A (T10A) 4Cr5MoSiV1,3Cr2W8V (3Cr2W8) T8A(T10A) T8A(T10A)
45
Q235 铸钢
50~55HRC
压铸模零件中最重要的零件是与金属液接触的成型工 作零件,通常用热作模具钢制成。按性能分,它属于高热 强热模钢;按合金元素分,它属于中合金热模钢。由于被 压铸材料的温度差别较大,因而对压铸模的材料及性能要 求也不同。用于制造锌合金、镁合金和铝合金的压铸模的 材料,必须具有高的回火抗力和冷热疲劳抗力,及良好的 渗氮(氮碳共渗)工艺性能。
压铸型(模)设计
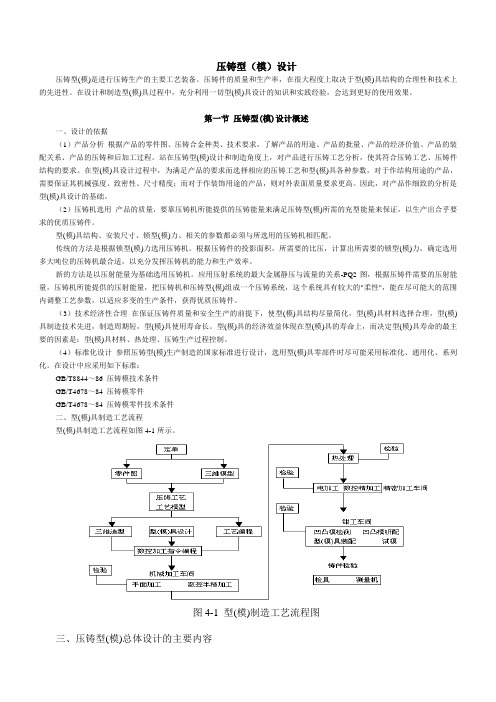
压铸型(模)设计压铸型(模)是进行压铸生产的主要工艺装备。
压铸件的质量和生产率,在很大程度上取决于型(模)具结构的合理性和技术上的先进性。
在设计和制造型(模)具过程中,充分利用一切型(模)具设计的知识和实践经验,会达到更好的使用效果。
第一节压铸型(模)设计概述一、设计的依据(1)产品分析根据产品的零件图、压铸合金种类、技术要求,了解产品的用途、产品的批量、产品的经济价值、产品的装配关系、产品的压铸和后加工过程。
站在压铸型(模)设计和制造角度上,对产品进行压铸工艺分析,使其符合压铸工艺、压铸件结构的要求。
在型(模)具设计过程中,为满足产品的要求而选择相应的压铸工艺和型(模)具各种参数,对于作结构用途的产品,需要保证其机械强度、致密性、尺寸精度;而对于作装饰用途的产品,则对外表面质量要求更高。
因此,对产品作细致的分析是型(模)具设计的基础。
(2)压铸机选用产品的质量,要靠压铸机所能提供的压铸能量来满足压铸型(模)所需的充型能量来保证,以生产出合乎要求的优质压铸件。
型(模)具结构、安装尺寸、锁型(模)力、相关的参数都必须与所选用的压铸机相匹配。
传统的方法是根据锁型(模)力选用压铸机。
根据压铸件的投影面积,所需要的比压,计算出所需要的锁型(模)力,确定选用多大吨位的压铸机最合适,以充分发挥压铸机的能力和生产效率。
新的方法是以压射能量为基础选用压铸机。
应用压射系统的最大金属静压与流量的关系-PQ2图,根据压铸件需要的压射能量,压铸机所能提供的压射能量,把压铸机和压铸型(模)组成一个压铸系统,这个系统具有较大的"柔性",能在尽可能大的范围内调整工艺参数,以适应多变的生产条件,获得优质压铸件。
(3)技术经济性合理在保证压铸件质量和安全生产的前提下,使型(模)具结构尽量简化,型(模)具材料选择合理,型(模)具制造技术先进,制造周期短,型(模)具使用寿命长。
型(模)具的经济效益体现在型(模)具的寿命上,而决定型(模)具寿命的最主要的因素是:型(模)具材料、热处理、压铸生产过程控制。
压铸模具结构及设计剖析
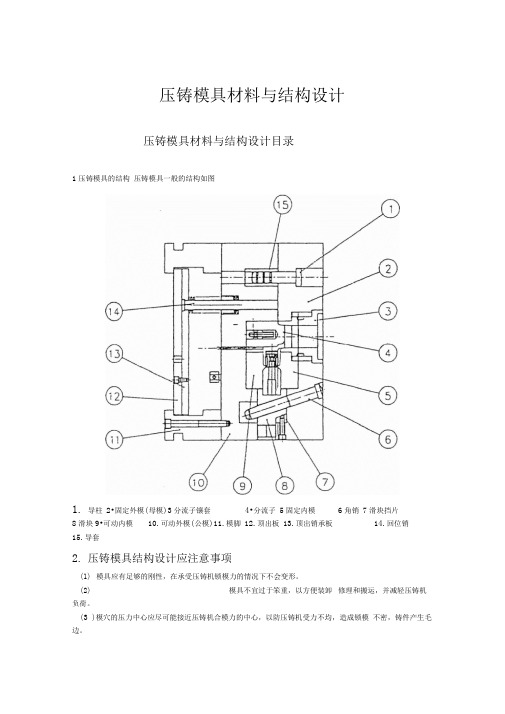
压铸模具材料与结构设计压铸模具材料与结构设计目录1压铸模具的结构压铸模具一般的结构如图1.导柱2•固定外模(母模)3分流子镶套4•分流子5固定内模6角销7滑块挡片8滑块9•可动内模10.可动外模(公模)11.模脚12.顶出板13.顶出销承板14.回位销15.导套2.压铸模具结构设计应注意事项(1)模具应有足够的刚性,在承受压铸机锁模力的情况下不会变形。
(2)模具不宜过于笨重,以方便装卸修理和搬运,并减轻压铸机负荷。
(3 )模穴的压力中心应尽可能接近压铸机合模力的中心,以防压铸机受力不均,造成锁模不密,铸件产生毛边。
(4)模具的外形要考虑到与压铸机的规格的配合:(a)模具的长度不要与系杆干涉。
(b )模具的总厚度不要太厚或太薄,超出压铸机可夹持的范围。
(c)注意与料管(冷室机)或喷嘴(热室机)之配合。
(d)当使用拉回杆拉回顶出出机构时,注意拉回杆之尺寸与位置之配合。
(5)为便于模具的搬运和装配,在固定模和可动模上方及两侧应钻螺孔,以便可旋入环首螺栓。
3内模(母模模仁)(1 )内模壁厚内模壁厚基本上不必计算其强度,起壁厚大小决定于是否可容纳冷却水管通过,安排溢流井,及是否有足够的深度可攻螺纹,以便将内模固定于外模。
由于冷却水管一般直径约10mm,距离模穴约25mm,因此内模壁厚至少要50mm。
内模壁厚的参考值如下表。
(2)内模与外模的配合内模的高度应该比外模高出0.05-0.1m m,以便模面可确实密合,并使空气可顺利排出。
其与外模的配合精度可用H8配h7,如下图所示。
內模孔H8內模與外模之配合(3)内模与分流子的配合分流子的功用是将熔汤由压铸机导至模穴内,因此其高度视固定模的厚度而定。
分流子的底部与内模相接,使流道不会接触外模,如下图,内模与分流子的配合可用H7配h6。
內蟆與分流子之配合4外模(1) 固定外模固定外模一般不计算强度,但设计时要注意留出锁固定压板或模器的空间。
(2) 可动外模可动外模的底部厚度可用下面的公式计算:其中:h :外模底部之厚度(mm ) p :铸造压力(kg/cm 2) L :模脚之间距(mm ) a :成品之长度(mm )b :成品之宽度(mm)5PabL 332 EBdr f ■-►_ I J,B :外模之宽度(mm)E:钢的杨氏模数=2.1 x 106kg/cm 2d:外模在开模方向的最大变形量( mm), 一般取d< 0.05mm.例:某铸件长300mm宽250mm铸造压力选定280( kg/cm2),外模之宽度560( mr)i 模脚之间距360 (mm ,最大变形量取0.05 (mr)所以2P=280(kg/cm )L=360(mm)a=300(mm)b=250(mm)B=560(mm)6 2E=2.1 x 10 kg/cmd=0.05(mm)5X 280 X 300 X 250 X 360」32 X 2.1 X 10 & X 560 X 0 45计算得h=138mm5•模脚(1)模脚变形量模脚主要的功能在提供模具之顶出空间,其强度计算公式为7 WH d = -Eab其中:d:变形量(mm),通常要小于0.05mm.W:锁模力/2(kg)H :模脚高度(mm)=顶出距离+顶出板厚度+顶出销承板厚度+前进止动距离(防止顶出板撞到外模)+后退止动距离(防止顶出板撞到压铸机)4 2E:钢的杨氏模数=2.1 x 10 ( kg/mm )a:模脚长度(mm)b:模脚宽度(mm)例:压铸机锁模力315吨,模脚高度130 (mm),模脚长度560 ( mm),模脚宽度80( mm )。
压铸模设计
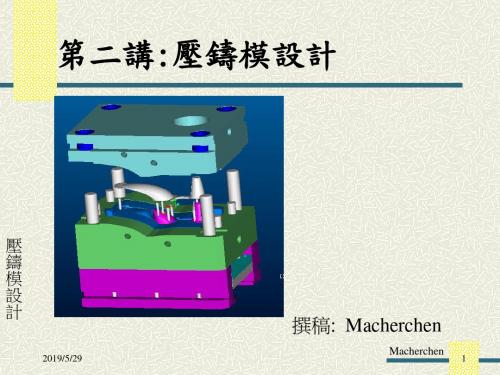
鑄 模 設
為基準,減去斜度值及加工余量,另一端按脫模斜度 相應增大.
計
2019/5/29
Macherchen
25
三.壓鑄模零部件設計
d 中心距尺寸:
CM=(1+K’) CZ (CM )±δZ/2 =[(1+K’) CZ] ±δZ/2
中心距尺寸在加工製造和磨損過程中不受影響及上下
壓
偏差對稱分布.
鑄
模
設
計
2019/5/29
Macherchen
26
三.壓鑄模零部件設計
e 成型中心邊距尺寸: 1). 磨損後增大的成型中心邊距
(C’M )±δZ/2 =[(1+K’) C’Z -△/24 ] ±δZ/2
2). 磨損後減小的成型中心邊距
壓
(C’M )±δZ/2 =[(1+K’) C’Z +△/24 ] ±δZ/2
壓 鑄 模 設 計
2019/5/29
Macherchen
13
三.壓鑄模零部件設計
(3)避免銳角的鑲拼
壓 鑄 模 設 計
2019/5/29
Macherchen
14
三.壓鑄模零部件設計
(4)防止熱處理變形的鑲拼
壓 鑄 (5)便於更換維修的鑲拼 模 設 計
2019/5/29
Macherchen
15
三.壓鑄模零部件設計
3)壓鑄件上和模具上的中心距尺寸均采用雙向等值正負偏差,它
壓
們的基本尺寸為平均值.
鑄
模
設
計
2019/5/29
Macherchen
20
三.壓鑄模零部件設計
3. 影響壓鑄件尺寸精度的因素:
压铸模具设计和制造手册
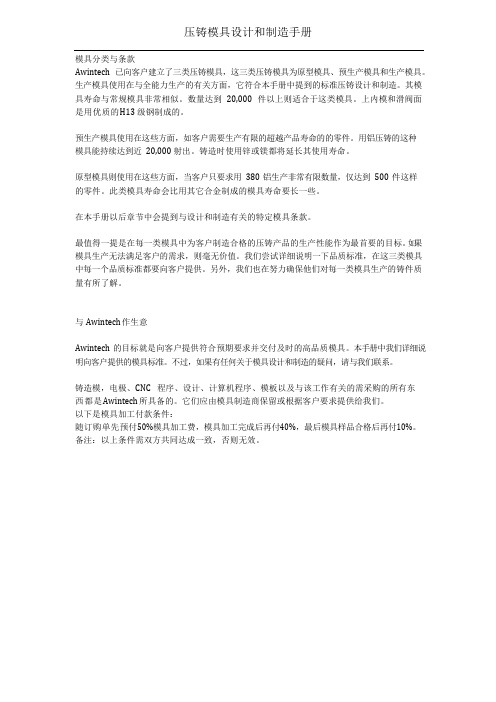
模具分类与条款Awintech 已向客户建立了三类压铸模具,这三类压铸模具为原型模具、预生产模具和生产模具。
生产模具使用在与全能力生产的有关方面,它符合本手册中提到的标准压铸设计和制造。
其模具寿命与常规模具非常相似。
数量达到20,000 件以上则适合于这类模具。
上内模和滑阀面是用优质的H13 级钢制成的。
预生产模具使用在这些方面,如客户需要生产有限的超越产品寿命的的零件。
用铝压铸的这种模具能持续达到近20,000 射出。
铸造时使用锌或镁都将延长其使用寿命。
原型模具则使用在这些方面,当客户只要求用380 铝生产非常有限数量,仅达到500 件这样的零件。
此类模具寿命会比用其它合金制成的模具寿命要长一些。
在本手册以后章节中会提到与设计和制造有关的特定模具条款。
最值得一提是在每一类模具中为客户制造合格的压铸产品的生产性能作为最首要的目标。
如果模具生产无法满足客户的需求,则毫无价值。
我们尝试详细说明一下品质标准,在这三类模具中每一个品质标准都要向客户提供。
另外,我们也在努力确保他们对每一类模具生产的铸件质量有所了解。
与Awintech 作生意Awintech 的目标就是向客户提供符合预期要求并交付及时的高品质模具。
本手册中我们详细说明向客户提供的模具标准。
不过,如果有任何关于模具设计和制造的疑问,请与我们联系。
铸造模,电极、CNC 程序、设计、计算机程序、模板以及与该工作有关的需采购的所有东西都是Awintech 所具备的。
它们应由模具制造商保留或根据客户要求提供给我们。
以下是模具加工付款条件:随订购单先预付50%模具加工费,模具加工完成后再付40%,最后模具样品合格后再付10%。
备注:以上条件需双方共同达成一致,否则无效。
目录1.0.0 模具分类与条款1.1.0 与Awintech 作生意1.2.0 总体步骤与规格1.3.0 胚模规格1.4.0 料表1.5.0 上内模1.6.0 公模滑块零件1.7.0 拉圾钉1.8.0 顶出系统1.9.0 加热与冷却2.0.0 胚模零件2.1.0 液压汽缸筒和接近开关2.2.0 合金工具钢的热处理2.3.0 合金工具钢表面处理2.4.0 焊接2.5.0 金属进料与真空系统2.6.0 文档资料与证明2.7.0 压铸冲模设计和制造总指南和专用指南设计检测表模具加工检测表Awintech 模具改善表Awintech 模具检测规划报告拉极钉概要热电偶安装设计压铸机台板布局真空安装规格1.2.0 总体步骤与规格1、Awintech 会向模具供应商提供最新的客户产品印刷物或资料库用以询价,模具设计和制造。
压铸工艺及模具设计 第9章 压铸模设计实例
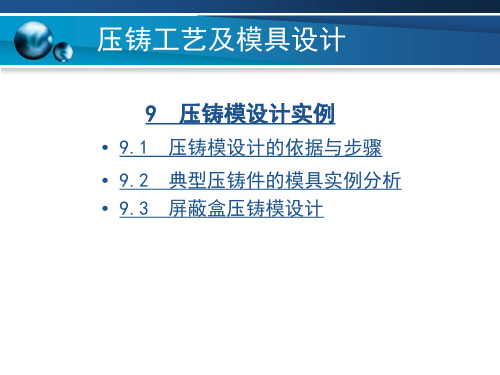
压铸工艺及模具设计
7. 注意事项 由于左右滑块成型面积较大,所以在 计算机床的锁模力时应充分考虑,否则锁模力不够,压铸 时将出现涨型,甚至损坏模具;由于滑块需配作,同时还 应考虑温度升高对模具的影响,故设计及制造精度要求较 高;模具特别是滑块部位应经常清洗,以防压铸时金属液 的窜入而出现滑块卡死,另外,导块及楔紧块磨损后也应 及时更换,该模具设计使用寿命8~10万次,实际使用寿 命达10万次以上。
5. 冷却系统 该模具在定模型芯、动定模衬上均设 计了水循环冷却系统(图中未画出),当模具温度升高时可 对模具进行冷却,提高铸件品质,延长模具使用寿命。
6. 模具特点 由于滑块的作用,开模时利用开模力 使铸件自动脱离定模型芯而留在动模内,铸件顶出力较小, 铸件易于脱模;由于滑块采用滚珠结构,故滑块虽较大, 但运动平稳,不会出现卡死现象。
距尺寸将直接影响装配性能的好坏,因此该模具设计制 造难度较大,在模具设计与制造中要充分考虑各方面因 素的影响。
压铸工艺及模具设计
图9-3 抗扭支架
模具结构如图9-4所示。
压铸工艺及模具设计
图9-4 模具结构
1-定模座板 2-浇口套 3-导柱 4-定模镶块 5-定模套板 6-推杆 7-导套8-动模套板 9-分流锥 10-推杆 11-动模镶块 12-支承板 13-推板导柱 14-垫铁 15-复位杆 16-推杆固定板 17-推板导套 18-动模座板 19-推板 20-复位拉杆 21-限位钉 22-拉杆 23-抽芯滑块 24-楔块 25-斜销 26-压板 27-型芯
压铸工艺及模具设计
(3) 预复位 为解决合模时侧型芯与推杆干涉的问题, 合模时,在液压抽芯器动作前,与机床复位缸联动的复 位杆带动模具推杆固定板(包括顶杆)退回,然后抽芯 器再带动侧型芯合模,实现预复位动作。
压铸模设计.doc
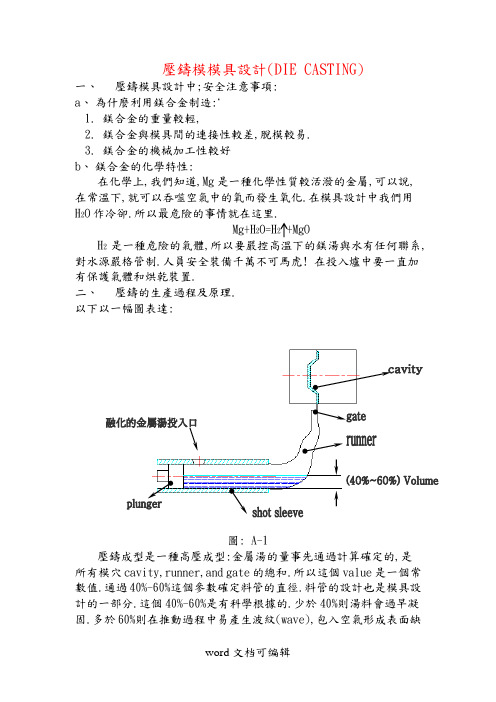
壓鑄模模具設計(DIE CASTING)一、壓鑄模具設計中;安全注意事項:a、為什麼利用鎂合金制造:`1.鎂合金的重量較輕,2.鎂合金與模具間的連接性較差,脫模較易.3.鎂合金的機械加工性較好b、鎂合金的化學特性:在化學上,我們知道,Mg是一種化學性質較活潑的金屬,可以說,在常溫下,就可以吞噬空氣中的氧而發生氧化.在模具設計中我們用H2O作冷卻.所以最危險的事情就在這里.Mg+H2O=H2 +MgOH2是一種危險的氣體,所以要嚴控高溫下的鎂湯與水有任何聯系,對水源嚴格管制.人員安全裝備千萬不可馬虎! 在投入爐中要一直加有保護氣體和烘乾裝置.二、壓鑄的生產過程及原理.以下以一幅圖表達:圖: A-1壓鑄成型是一種高壓成型:金屬湯的量事先通過計算確定的,是所有模穴cavity,runner,and gate的總和.所以這個value是一個常數值.通過40%-60%這個參數確定料管的直徑.料管的設計也是模具設計的一部分.這個40%-60%是有科學根據的.少於40%則湯料會過早凝固.多於60%則在推動過程中易產生波紋(wave),包入空氣形成表面缺陷.影響成品品質!三、壓鑄工藝對成型品的要求壓鑄工藝要求成型品最好具有均一壁厚,確保湯料可同時到每一個角落,如果產品壁厚不均勻,則溶流會沿所受阻力較小的路徑前進.從而形成了我們不愿見到的”air traps”,”weld lines”,等等.當我們的客戶所設計的成品,其肉厚不很均勻,產生的直接後果是開模困難,我們應采取盡可能的辦法去與之溝通,使其最大量地變更產品設計,以期達到最佳開模效果.四、成型工藝運動過程.Show as the following diagram:Pressure curve圖: A-2運動行程分為兩個階段,第一階段活塞慢速推進.當湯料到達澆口點,迅速提升壓力,進行高壓射出的動作,待cavity被充滿之后,進行一階段保壓運動.整個射出成型需要15/1000s左右,沒有高科技電腦的即時控制,這麼短的時間內完成兩段射出,簡直難以想像!五、模具設計的部分我們必須進行強度校核,可以利用電腦優越的計算性能編寫出確實可行的計算程式,進行強度校核及撓度計算等一些相關問題,通過”Computer aided engineering”的分析,優化結構設計和澆道設計.使我們的設計更加向科學化,系統化,現代化的方向邁進! 做讓客戶放心, 讓客戶稱心!以下進行具體的設計撿論:設計之前,特約定如下:S→stroke:(行程)Sma→location that I make the stroke (metal at gate)( ejector ) →part Length +5mm (頂出行程)S→section:SA→gate section (澆口截面積)∙SV→section vending(逃氣孔截面積) ∙SR→runner section(澆道截面積) ∙A→projected area:AP→projected area part (零件投影面積) ∙AO→projected area overflow(溢料部分投影面積) ∙AS→slide projected area (滑塊投影面積) ∙AR→runner projected area (澆道投影面積) ∙AIM→total projected area (全部的投影面積) ∙圖: A-3AIM = Ao + Ap + A RSpeed: velocity:Vma: velocity of gate (澆口速度)Vc: plunger velocity (活塞速度) (在控制點處) FLI: Force opening (KN) (FLN>FLI)FLN: Force closing (KN)圖: A-4PIM3:Pressure→第三段行程處壓力 (Maximum Pressure)為了更清楚地撿論PIM3,Show as the following diagram:圖: A-5Flow rate, Cavity fill time 的計算:設定:Qm → Flow rate:TF → Cavity fill time:As we known:Qm = d㎡╳π/4 ╳Vc (π→園周率)= Adm ╳Vc (活塞表面積與活塞推進速度)= VMA ╳SA (澆口速度與澆口截面積)= VL ╳SV (逃氣孔速度與逃氣截面積)由物理學原理:我們知道:SV,有最大值;如果大於這個最大值,則會產生overflow的問題;而VL<300mps,當然,我們要求越多的溢料口,對成型有利,但是太多的溢料口,其弊端可想而知.每次開模後,注意要使用離型劑進行清除,我設計的溢料口要確保有足夠的逃氣截面積,計算時要注意一些回饋信息.Qm=(Mρ+Mο)/S ╳T F( Mο≒1/3 Mρ)其中:T F (經驗值)≒S∕100C X: S=1.5mm. ∴TF=0.015s對TF值的部分¸影響因素很多。
压铸模设计 (有设计图纸)

压铸模设计(有设计图纸)有全套图纸摘要随着与国际接轨的脚步不断加快,市场竞争的日益加剧,人们已经越来越认识到产品质量、成本和新产品的开发能力的重要性。
而模具制造是整个链条中最基础的要素之一,模具制造技术现已成为衡量一个国家制造业水平高低的重要标志,并在很大程度上决定企业的生存空间。
虽然中国模具工业在过去十多年中取得了令人瞩目的发展,但许多方面与工业发达国家相比仍有较大的差距。
例如,CAD/CAE/CAM技术的普及率不高;许多先进的模具技术应用不够广泛等等,致使相当一部分大型、精密、复杂和长寿命模具依赖进口。
本说明书结合电梯踏板的模具设计系统地阐述了压铸与模锻技术的基本原理,分析了压铸与模锻工艺主要参数的确定方法,论述了压铸模与锻模主要零部件设计方法,并介绍了模具的加工制造及维修保养。
关键词:压铸模具加工制造维修保养有全套图纸有全套图纸ABSTRACTWith the nation of footstep join to the worldcontinuously ,market competition is turning worse ,people is already known the important of quality ,cost ,and the ability of develop new product . but the manufacturing to the molding is one of the most basal factors in the whole chain ,the molding tool manufacturing technique hasbecome to measure the important marking of a national manufacturing industry level now ,and decide the existence space of the business enterprise to a large extent .Although in the passed ten years of development ,the Chinese molding tool industry gain the harvest ,but compare to developed country westill have something to study .for example ,the universality rate of the technical of CAD/CAE/CAM is not high ;many of molding tool technique is not applied enough etc, caucus to import a larger number the complications and the longevity life molding tool .This manual systematically combined the molding tool to die-casting with the mold technical basic principle by introduce the design of the elevator pedal, analyze the method to make certain to the main parameter of die-casting and the mold craft, introduce the method to process and maintain .Keyword: Die-casting mould process maintain有全套图纸有全套图纸目录1 压铸工艺概论 (1)1.1 压铸生产过程和特点 (1)1.1.1 压铸生产过程 (1)1.1.2压铸特点 (1)1.2 压铸合金的基本要求和种类 (2)1.2.1对压铸合金的基本要求 (2)1.2.2压铸合金的种类 (2)1.3 压铸件的结构工艺性 (4)1.3.1壁厚 (4)1.3.2 铸孔 (4)1.3.3 铸造圆角和脱模斜有全套图纸有全套图纸度 (4)1.3.4 螺纹、齿轮和槽隙 (5)1.3.5 图案、文字和标志 (6)1.3.6 镶嵌件 (6)1.4 压铸主要工艺参数的选择与调整 (7)1.4.1压力 (7)1.4.2速度 (9)1.4.3温度 (10)1.4.4时间 (12)1.4.5涂料…………………………………………………………………12 2 压铸机…………………………………………………………………………142.1 压铸机的种类和工作原理 (14)2.1.1压铸机的型号和种类 (14)2.1.2压铸机结构形式和压铸过程 (13)2.1.3压铸机的主要技术参数 (18)3 踏板的压铸模具设计 (20)有全套图纸有全套图纸3.1压铸机的选用 (20)3.1.1锁模力计算 (20)3.1.2压室容量 (22)模距3.1.3 开离 (23)3.1.4 装模尺寸 (23)3.2浇铸系统和溢流、排气系统的设计 (23)3.2.1 内浇口的设计 (24)3.2.2 直浇道的设计 (26)3.2.3 横浇道的设计 (27)3.2.4溢流槽和排气槽的设计 (28)3.2.5动、定模导柱和导套的设计…………………………………………293.2.6模板的设计 (30)3.2.7 抽芯结构的设计 (34)3.2.8 推出机构的设计 (35)3.2.9模具厚度与动模座板行程的核算 (37)4 压铸模的技术要求及选材……………………………………………………有全套图纸有全套图纸 394.l 压铸模总装的技术要求 (39)4.1.1 压铸模装配图上需注明的技术要求 (39)4.1.2压铸模外形和安装部位的技术要求 (40)4.1.3 总体装配精度的技术要求 (41)4.2 结构零件的公差与配合 (41)4.2.1结构零件轴与孔朗配合和精度 (41)4.2.2 滑动零件的配合 (41)4.3 零件的表面粗糙度 (42)4.4 压铸模零件的材料选择及热处理要求 (43)4.4.1 压铸模所处的工作状况及对模具的影响 (43)4.4.2 影响压铸模寿命的因素及提高模具寿命的措施 (44)4.4.3 压铸模材料的选择和热处理……………………………………46 模具的加工制造及维修保养 (47)5.1 金属模具的加工制造……………………………………………………475.1.1 金属模县毛坯的获取方法 (47)5.1.2模样及铸有全套图纸有全套图纸型 (47)5.1.3 金属模具的机械加工 (50)5.2模具的快速制造 (60)5.2.1 快速成形技术的原理、主要方法及特点 (60)5.2.2 模具毛坯的快速制造方法 (62)5.3 铸造模具的维护保养 (64)5.3.1铸模的预防性维护保养 (64)5.3.2铸模的修复性维护 (65)5.3.3工装模具的清洗技术 (68)参考文献 (71)1 压铸工艺概论压力铸造是将熔融合金在高压、高速条件下充型,并在高压下冷却凝成形的精密铸造方法,简称比铸。
压铸模设计说明书
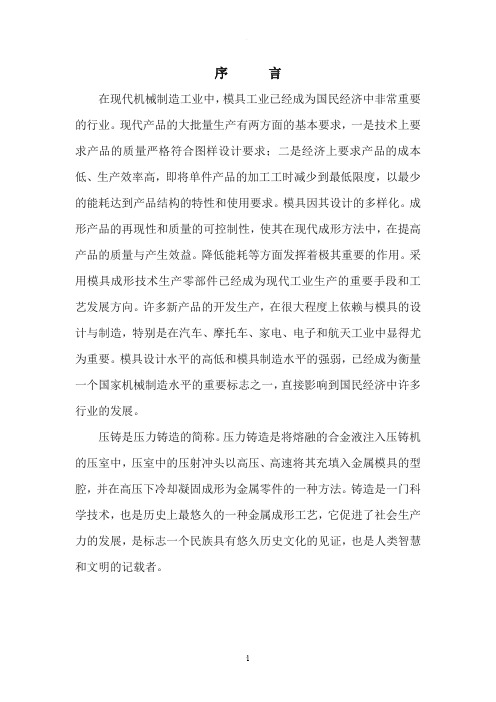
序言在现代机械制造工业中,模具工业已经成为国民经济中非常重要的行业。
现代产品的大批量生产有两方面的基本要求,一是技术上要求产品的质量严格符合图样设计要求;二是经济上要求产品的成本低、生产效率高,即将单件产品的加工工时减少到最低限度,以最少的能耗达到产品结构的特性和使用要求。
模具因其设计的多样化。
成形产品的再现性和质量的可控制性,使其在现代成形方法中,在提高产品的质量与产生效益。
降低能耗等方面发挥着极其重要的作用。
采用模具成形技术生产零部件已经成为现代工业生产的重要手段和工艺发展方向。
许多新产品的开发生产,在很大程度上依赖与模具的设计与制造,特别是在汽车、摩托车、家电、电子和航天工业中显得尤为重要。
模具设计水平的高低和模具制造水平的强弱,已经成为衡量一个国家机械制造水平的重要标志之一,直接影响到国民经济中许多行业的发展。
压铸是压力铸造的简称。
压力铸造是将熔融的合金液注入压铸机的压室中,压室中的压射冲头以高压、高速将其充填入金属模具的型腔,并在高压下冷却凝固成形为金属零件的一种方法。
铸造是一门科学技术,也是历史上最悠久的一种金属成形工艺,它促进了社会生产力的发展,是标志一个民族具有悠久历史文化的见证,也是人类智慧和文明的记载者。
第一章压铸设计的特点压力铸造的主要成形工艺特征是液态金属以高压、高速充填金属模具的型腔,并且在高压下结晶、凝固和成形,因此压铸成形过程中金属液流动的状态将会影响到压铸件的质量。
同时,针对压铸的工艺特点,压铸件的结构工艺性对压铸件质量的影响也需要引起足够的重视。
压铸机是压力铸造的基本设备,压铸的过程是通过压铸机实现的。
压铸机一般可分为热压室压铸机和冷压室压铸机两大类,本次设计使用的是冷压室压铸机。
冷压室压铸机的压室与熔化合金的坩埚是分开的,压铸时,需要从熔化炉的坩埚内盛取金属液注入压室后再进行压铸。
按照压铸模与压室的相对位置,冷压室压铸机又可分为立式、卧式和全立式三种形式。
本次设计选用的是卧式压铸机。
压铸模具设计

压铸模具设计参考
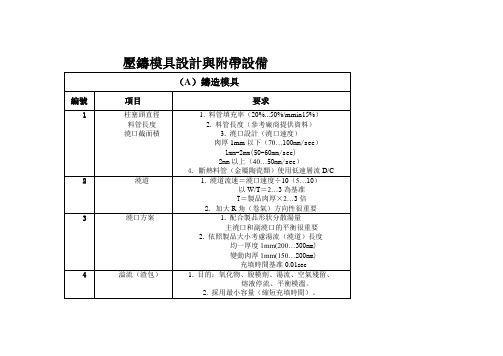
3.降低鑄造壓力。
4.考慮脫械劑的類型。
5. 機械頂出平衡。
(A)鑄造模具
編號
項目
要求
14
起泡、氣孔
1.開模時模溫高(冷卻時間、模具冷卻、湯溫)。
2.低速射出太快、太短(卷氣)。
3.高速射料位置優化(例:在模腔1/3處起高速)。
4.溶液中含氣量過多。
5.澆口方案改進。
6.須有氣孔和縮孔的分辯對策。
3.模溫分佈。
4.表面處理(長中子抽出斜度0.5度以下)。
5.抽出傾斜凸1.5度以上、凹1.0度以上。澆口部壁2.0度以上、分流錐部3度以上。
6.自動噴霧A:中子內側,中子進入噴霧(沒壓中子)模具內安裝噴霧嘴(注意中子行程)。B:噴霧液與毛邊的清掃,中子滑動部位加抽水孔。
7.脫械劑的類型。
13
變形
1.加大頂針尺寸和數量。
壓鑄模具設計與附帶設備
(A)鑄造模具
編號
項目
要求
1
柱塞頭直徑
料管長度
澆口截面積
1.料管填充率(20%...50%/mmin15%)
2.料管長度(參考廠商提供資料)
3.澆口設計(澆口速度)
肉厚1mm以下(70…100mm/sec)
1mm-2mm(50-60mm/sec)
2mm以上(40…50mm/sec)
1.搭配足夠熔解能力的熔解爐。
2.溶液氣化少(爐體構造、燃燒器的選擇、隔熱)。
3.材料成份變化少。
4.溶液處理容易。
5.爐內容易清理。
6.節省能源。
6
保溫爐
1.溶液溫度穩定(在設定溫度的±5度為基准)。
2.溶液氧化少。
7
水冷卻系統
压铸模模具设计(一)

压铸模模具设计(一)由物理学原理:我们知道:SV,有最大值;如果大于这个最大值,则会产生overflow的问题;而VL<300mps,当然,我们要求越多的溢料口,对成型有利,但是太多的溢料口,其弊端可想而知.每次开模后,注意要使用离型剂进行清除,我设计的溢料口要确保有足够的逃气截面积,计算时要注意一些回馈信息.Qm=(Mρ Mο)/S ╳ TF ( Mο≒1/3Mρ)其中:TF (经验值)≒S∕100CX: S=1.5mm. ∴TF=0.015s对TF值的部分¸影响因素很多。
The same part, but the gate location is difference:图: A-6SFLOW1>SFLOW2TF1Temperature of the mold is higher; The value of TF is shorter.SFLOW is longer, TF is shorter.以一成品为例:图: A-7这一成型品共有7个overflow:每个overflow的重量是5 g设Mρ=150 g:∴ Qm = MA/1.75×TF=150 7×5/(1.75×0.015)= 7050cm3/s∵Qm= VMA×SA∴SA= Qm/ VMAVMA 的值一般由经验得出:其常见值为40~80 m/s.以一般经验来考虑:图1的VMA值可大一些;而途图2的VMA值须小一些.现取值为50 m/s;∴SA=Qm/VMA=7050/50=141mm*mm以上就是我们所求的浇口截面积大小¸通常我们按具体情况决定具体的参数值:SO we decideSA=141=10×14.1=1×141=0.5×282……分成许许多多种类 :The following is design of the overflow:图: A-8压铸模具结构设计类似于塑模但由于压铸模必须承受较大之冲力及变形.因此,结构设计上强度大于塑模.以下列出压铸模异于塑模之要点.(一).模仁结构设计:成品边缘距模仁至少60mm.(见图A-9)公母模板的确定:模仁外边到模板外缘宽度(B)至少90mm厚度,为2倍之模仁厚. (见图A-9)模脚内侧进入模仁外缘垂直线至少20mm. (见图A-9)A板隔热板(材料S40000),厚度约12mm. (见图A-9)下固定板至少50mm.夹模厚50MM四边夹模,直接用螺丝锁,不用压板.上下顶出板厚分别为30`35mm,尽量减少宽度,从而增大模脚而使公模板变形减少.公母模仁表面均需出模板面0.1mm,切不可太大.否则,产生毛边镁通汤溅出,将极其危险.模仁尽量避免有尖锐之角点,尖点将导致应力集中.压铸时使模仁爆裂,模仁内水孔末端拐角也应有R 角.图A-9(二).RP设计可选用偏小径φ18~φ20mm,位置于模仁内. (见图A-10) EGP设计应注意:不可插入公模板,至少留1mm间隙. (见图A-9) 顶板顶出时不可靠在公模板上,至少留5mm间隙.STP可用10个左右数量,比塑模多.从下固定板锁公模板之螺丝S-1,在连接处加上圆环,插入板内定位.(如图A-11)GP应倒装在母模侧. (见图A-10)水平方向需装入0度定位块. (见图A-10)KO孔位置请见压铸机上顶杆位置,切不可用注塑成型机位置.料管中心与压铸机中心距为0~250mm,50MM为一级.图 A-10图 A-11拆模(3D)设计注意要点:所有地方除PL线外¸均至少应做R0.2圆角。
压铸模设计
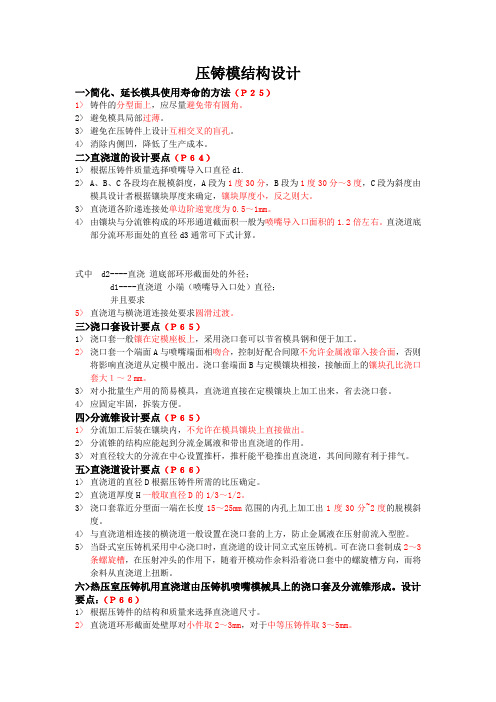
压铸模结构设计一>简化、延长模具使用寿命的方法(P25)1>铸件的分型面上,应尽量避免带有圆角。
2>避免模具局部过薄。
3>避免在压铸件上设计互相交叉的盲孔。
4>消除内侧凹,降低了生产成本。
二>直浇道的设计要点(P64)1>根据压铸件质量选择喷嘴导入口直径d1.2>A、B、C各段均在脱模斜度,A段为1度30分,B段为1度30分~3度,C段为斜度由模具设计者根据镶块厚度来确定,镶块厚度小,反之则大。
3>直浇道各阶递连接处单边阶递宽度为0.5~1mm。
4>由镶块与分流锥构成的环形通道截面积一般为喷嘴导入口面积的1.2倍左右。
直浇道底部分流环形面处的直径d3通常可下式计算。
式中 d2----直浇道底部环形截面处的外径;d1----直浇道小端(喷嘴导入口处)直径;并且要求5>直浇道与横浇道连接处要求圆滑过渡。
三>浇口套设计要点(P65)1>浇口套一般镶在定模座板上,采用浇口套可以节省模具钢和便于加工。
2>浇口套一个端面A与喷嘴端面相吻合,控制好配合间隙不允许金属液窜入接合面,否则将影响直浇道从定模中脱出。
浇口套端面B与定模镶块相接,接触面上的镶块孔比浇口套大1~2mm。
3>对小批量生产用的简易模具,直浇道直接在定模镶块上加工出来,省去浇口套。
4>应固定牢固,拆装方便。
四>分流锥设计要点(P65)1>分流加工后装在镶块内,不允许在模具镶块上直接做出。
2>分流锥的结构应能起到分流金属液和带出直浇道的作用。
3>对直径较大的分流在中心设置推杆,推杆能平稳推出直浇道,其间间隙有利于排气。
五>直浇道设计要点(P66)1>直浇道的直径D根据压铸件所需的比压确定。
2>直浇道厚度H一般取直径D的1/3~1/2。
3>浇口套靠近分型面一端在长度15~25mm范围的内孔上加工出1度30分~2度的脱模斜度。
压铸模具设计制作标准
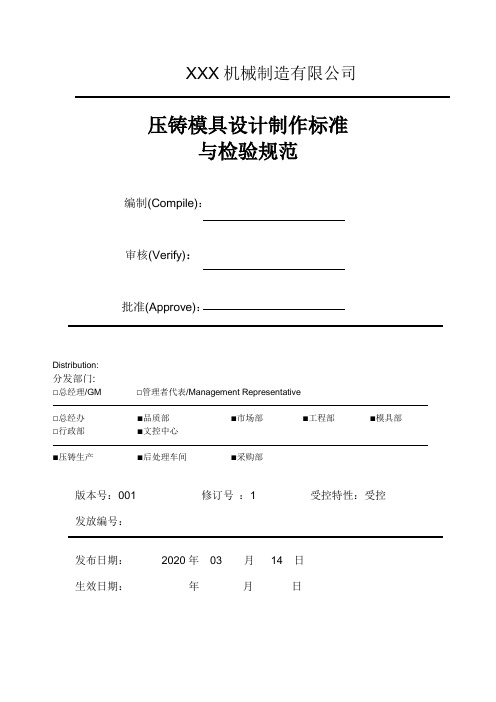
XXX 机械制造有限公司
压铸模具设计制作标准 与检验规范
编制(Compile):
审核(Verify):
晰的表达出四方块的大小和异形镶件在四方块中的位置, 3D 在 3D 图上把此四方块做出来与之相结合。
重点强调:做完后互相检查,正确后才下发。 8.7. 其他考虑: 8.7.1. 小于 ø3 的孔不铸造出来,可设置引针孔用加工的方法钻
出。除非长度小于直径便可铸出。
8.7.2. 动模的型芯是否容易顶出。 8.7.3. 型芯和滑块是否可以安装冷却水。 8.7.4. 避免型芯在浇口处被冲刷。
5.8. 为防止生产过程中模具铭牌掉落,故铭牌安装后固定铭牌的螺 丝不能超出模架平面,所以每套模具都要在动模架操作侧中间位置开 一个 125X75X3mm 的槽,以方便安装铭牌。在操作侧的模脚上必须 刻上产品料号,清晰可见。
5.9. 固定外模及活动外模需制作 4 个敲模孔。 5.10. 外模四周加工撬开槽。 5.11. 浇口套必须加装冷却水,冷却环厚度 10MM 以上,水管孔为 PT 1/4,冷却环热套装配,与外模装配。 5.12. 跨距大于 150MM 时都应考虑加支撑。支撑柱直径(或宽)不 小于 50MM,尽可能靠近压射变形位。 5.13. 大型模具(配合压铸机在 800 吨及以上的)地侧要加模脚支 撑。(所有模具支撑脚不得用圆柱支撑,需要用铸铁方形支撑;安 装时不得有干涉,特殊模具无法制作时需要提出) 5.14. 四根导柱用螺丝锁紧在固定模架上,同时导柱要加工排屑槽, 导柱顶端要做成带 20 度斜度的锥形状。【见下图所示】
压铸模设计实例
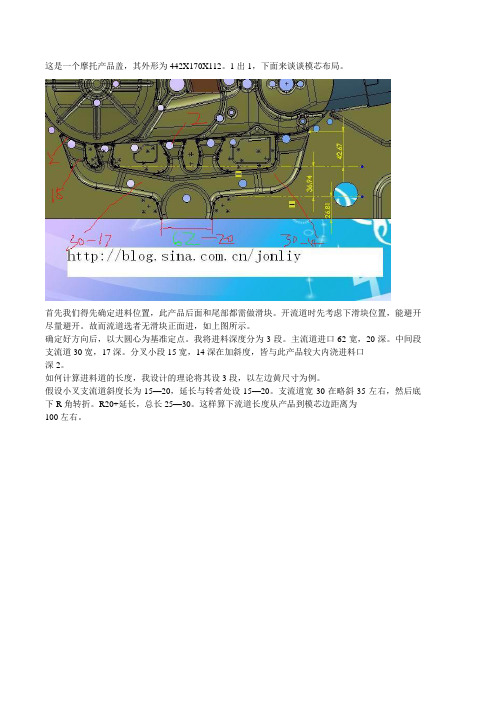
这是一个摩托产品盖,其外形为442X170X112。
1出1,下面来谈谈模芯布局。
首先我们得先确定进料位置,此产品后面和尾部都需做滑块。
开流道时先考虑下滑块位置,能避开尽量避开。
故而流道选者无滑块正面进,如上图所示。
确定好方向后,以大圆心为基准定点。
我将进料深度分为3段。
主流道进口62宽,20深。
中间段支流道30宽,17深。
分叉小段15宽,14深在加斜度,皆与此产品较大内浇进料口深2。
如何计算进料道的长度,我设计的理论将其设3段,以左边黄尺寸为例。
假设小叉支流道斜度长为15—20,延长与转者处设15—20。
支流道宽30在略斜35左右,然后底下R角转折。
R20+延长,总长25—30。
这样算下流道长度从产品到模芯边距离为100左右。
渣包尺寸为30宽以上,长40以上,距离足够的话。
深度13—15,出模度数8—10度,底下R3—5过度。
假设渣包宽35,进料边口为5,预设渣包后留25。
那么产品到模芯边为60余量。
如有滑块得根据抽出距离另行计算或者加宽余量边,祥见以下图所示。
对于有滑块面的余量放置,假设模内抽芯距离为70,那么后面的距离为70+余量,使之滑块滑出绝对距离后始终在模芯内,余量15—20最起码。
另外边也同样的道理,这样我们可以计算出模芯的大小,然后去小归整。
设计好大小后,然后来设计模芯的厚度。
厚度的设计准则以模芯最低出开始算余量50以上。
因为底下通10水管,水管位置离产品模芯底面下来20—25距离,底下留余量为25—30,然后以分型面为定点基准,凑整数。
绿色为水管,红色,蓝色为点冷却。
一般模芯不是很厚的,如果中间没有孔位,可以直通,或环绕试。
如果无法通水管,那就采取点冷却。
一般在型腔的镶快出,凸起出,热聚处。
其深度离腔体最深出低20—30左右。
滑块的设计,皆如此产品的滑芯不是很大。
宽度方面一般滑座比滑芯大5一边,然后凑整数。
滑块高度的设计,首先确定此滑块是用油泵。
如油泵接头最大处为32,那我设置尾座面比接头高4,底下留9,这样尾座高度为45。
压铸模设计第11章压铸模设计步骤及图例[补充new]
![压铸模设计第11章压铸模设计步骤及图例[补充new]](https://img.taocdn.com/s3/m/f3fededf7c1cfad6195fa745.png)
(2)校核压室容量
查手册,可知J116型压铸机,其压室直径为40mm时, 压室内铝合金浇入量为0.7kg。经计算(计算从略),压 铸件、浇注系统及排溢系统总重量小于0.7kg,故J116型 压铸机能满足要求。
据此,初步确定选用J116型卧式冷式压铸机.
第十一章 压铸模设计步骤及图例
• 由于压铸件的品种繁多,模具的结构特征和要求各不 相同,而且不同的设计者和加工单位也有各自的特点 和习惯,因此压铸模设计程序也会有些差异。不过,
基本的设计程序应该是相同的。
• §1 压铸模设计步骤 • §2 压铸模设计举例 • §3 压铸模结构图例
§1 压铸模设计步骤
• 压铸模设计步骤一般包括以下几个方面: 1.取得必要的资料和数据
设计前,设计者必须向模具用户取得如下资料和数据: (1) 压铸件的零件图。图中零件的尺寸、尺寸公差、形位
公差、表面粗糙度、材质、热处理要求以及其他技术要求 等应该齐全。 (2) 压铸件的生产数量及交货期限。 (3) 压铸件生产单位的设备情况(即压铸机的型号)。 (4) 模具加工单位的加工能力和设备条件。 (5) 用户的其他要求。
5.参数的计算与校核
模具结构形式确定后应对有关参数进行计算或校核。
1)成型零件成型尺寸计算。
成型零件尺寸分为:型腔径向尺寸、型芯径向尺寸、型
腔深度尺寸、型芯高度尺寸及中心距尺寸或位置尺寸。
按第7章的规定和图纸要求,零件尺寸公差为IT12级,这
些尺寸可用式7-5、6、7等计算。
零件最大外形尺寸为80mm,标上公差后为800-0.30mm,
§1 压铸模设计步骤
2.分析压铸件的结构、合金材料的性能及技术要求 (1) 分析压铸件的结构能否保证铸件质量及有利成型。如压铸件的壁厚是
压铸模设计规范
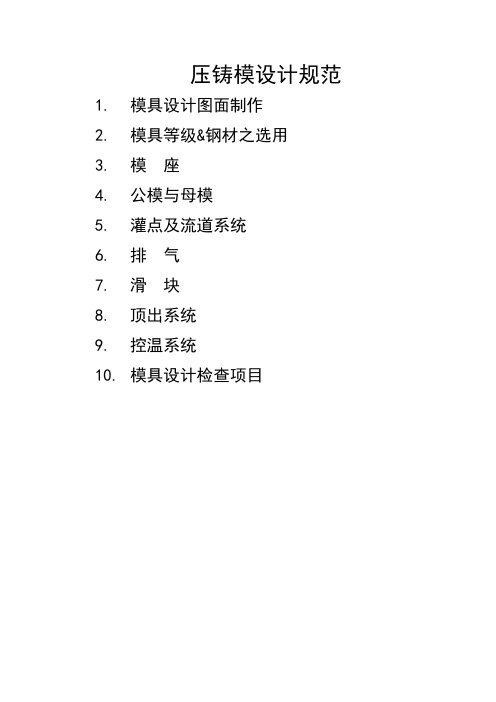
压铸模设计规范1.模具设计图面制作2.模具等级&钢材之选用3.模座4.公模与母模5.灌点及流道系统6.排气7.滑块8.顶出系统9.控温系统10.模具设计检查项目模具设计图面制作1.所有模具组立图需能完整表示出模具结构, 其图面应含一公,母模平面图,纵向与横向剖视图, 和其他足以清楚表示模具结构之详细及剖视图.2.每张图面需有图框,右下角要有标签栏.3.每张模具组立图需有材料栏, 其内容应含零件名称, 材料尺寸,硬度,零件在图面的编号及所需之数量.4.标示出所有模板, 镶块尺寸及模座的长, 宽, 高.5.标示”天侧"(TOP OF MOLD)于模具天侧及"基”(OFFSET)于偏移之导柱.6.画出完整之水路于平面及剖视图上,至少标示一个不同水路的尺寸及水管接头,并标示”IN”,”OUT"及编号于水路进出侧。
水管应制成沉头型式。
7.每个进料点需以详图标示。
8.为易于辩认各零部件,可使用下列代号:(1) GB—--导套 (2) GP—--导柱(3) RP—-—回位销(4) ST———停止销(5) SP---支撑柱9.标示锁模块, 吊模孔位置与尺寸.10. 标示主流道及分流道尺寸。
模具等级&钢材之选用模具等级1.CLASS A1.1 要求寿命: 100万模次1.2说明: 用于要求快速生产或非常高之生产量, 产品尺寸要求严格, 模具以最高品质之钢材制造而成. 模具费用高昂.1.3钢材:A)模座: RAMAX 不锈钢材料, HRC34~38°。
B)模仁: ELMAX, STAVAX或CORAX不锈钢材料,需热处理至HRC54°以上.C)滑动件: 须与模仁不同材料(整面滑块可使用与模仁相同的钢材),硬度相差4°以上,并作氮化处理。
耐磨块,压块须与滑块不同材料, 可与模仁材料相同. 所有滑动件必须开油沟.D)附要求: 钢材于EDM加工或焊补后, 需再行热处理以消除应力及与始钢材硬度均一.2.CLASS B2.1 要求寿命: 50万模次3.2说明: 用于中高产量,及精密的公差要求。
- 1、下载文档前请自行甄别文档内容的完整性,平台不提供额外的编辑、内容补充、找答案等附加服务。
- 2、"仅部分预览"的文档,不可在线预览部分如存在完整性等问题,可反馈申请退款(可完整预览的文档不适用该条件!)。
- 3、如文档侵犯您的权益,请联系客服反馈,我们会尽快为您处理(人工客服工作时间:9:00-18:30)。
挡纱肋盘压铸模设计江苏射阳纺机股份有限公司(江苏射阳224300)高明朗沈鸿波
1引言
图1是挡纱肋盘铸造毛坯图,肋盘材料为ZL102,零件采用低压铸造工艺成型,模具结构见图2。
2模具结构特点———————————————————
收稿日期:1997年3月6日2.1动、定模型腔
根据铸件的形状及尺寸,模具的浇注系统采用单腔中心浇口,因为定模的型腔是形状简单的浅圆,所以定模的成型部分可直接在定模套板8上加工。
铸件的加强筋在动模型腔内成型,因为该型腔较复杂,所以动模采用镶拼式结构。
同时,由于镶块的尺寸较大,整体镶块锻造及热
D≈270mm。
又因为d1/d0≈1.7,所以d1≈102mm。
由《锻压手册》查得,d1处的径向过盈系数β2≈0.0084,所以Δt=β2d1=0.85。
压合量h=Δt/tanα,由于组合凹模的压合方法采用冷压合,压合角α取1°30′,配合面配磨,且接触面积不小于80%,所以h经计算后取13~15mm。
又由于压合后孔将收缩,收缩量约为0.3%,所以压合后应对凹模内腔尺寸进行修正,以保证其同轴度与垂直度。
齿形可采用慢走丝线切割加工,以保证齿轮同轴度、尺寸精度及表面粗糙度。
外圈材料选用40Cr,热处理硬度38~42HR C(不许高于43HRC),否则压合后易开裂。
内圈即凹模拼块材料采用LD,热处理硬度59~62HRC。
齿轮凹模刃口带高度2~3mm,反面扩孔双面0.1~0.2mm,刃口带粗糙度必须研至Ra<0.2μm,否则会拉伤工件。
为了保证齿轮有合理的磨量,齿廓应放0.2~0.25mm的磨量。
另外,为了保证凹模寿命,凹模尺寸应加工到极限负偏差,使凹模有最大的磨损量。
4.2花键凸模及上凸模
冷挤凸模的服役条件比凹模更为苛刻,首先,其没有预紧条件,其次它在交变应力、冷热循环的条件下工作。
由于毛坯端面不平整,毛坯与凹模间隙过大,以及凸、凹模不同心等都会给凸模端部造成较大的偏心弯曲应力,因此凸模应选用高强韧性材料LD。
经4副不同齿轮冷挤模实践知,应严格控制L D的热处理范围,当热处理硬度在59~62HRC时,其综合性能最佳。
当硬度高于63HRC时,凸模脆性很大,凸模端部易开裂(断裂),低于59HRC时,凸模在试模时因产生镦粗而报废,所以花键凸模及上凸模硬度应控制在61HR C左右,且表面研至镜面。
4.3其它主要零件
上凸模用弹簧夹圈固定,材料为65Mn,装模时要保证其与机床工作台垂直。
花键凸模固定板用Cr12MoV制造,热处理硬度58~62HRC,且一定要保证花键孔与外形的同轴度。
垫板也选用Cr12MoV制造,热处理硬度58~62HRC。
3根顶料杆用Cr12制造,热处理硬度56~60HRC,并保证3根顶料杆等高。
图1挡纱肋盘毛坯
处理困难,因此将整体镶块分解成24块小镶
块,并紧固在不通孔式动模套板6的镶块孔
内,构成组合镶块。
这样,锻造的小镶块组织
均匀,质量较高,还可以减少镶块在热处理时
的变形,也便于热处理后修整。
镶块的拼合间
隙可以排出型腔内的气体,还可以通过更换
镶块来改变铸件的局部结构。
浇口套与分流锥的安装用小台阶加压板式取代常见的台阶固定式,节约了耐热钢。
动、定模套板材料为QT700_2,镶块、浇口套和
分流锥材料用3Cr2W8V,压板材料用45钢。
图2模具结构
1.连板
2.连杆
3.推杆4、19.垫圈5.螺母6.动模套板7.动模镶块8.定
模套板9.浇口套10、13、14.压板11.导柱12.分流锥15.水管16.推板导
柱17.推杆固定板18.推板20.螺钉21.压铸机液压推出器22.压铸机动模
板23.压铸机定模板24.压铸机升液管
2.2动、定模导向及定位
从图1铸件结合模具分型面选择可以看
出,动、定模型腔之间在径向存在着一定的同
轴度要求,在圆周方向,动、定模则可以旋转
任意角度而不致产生错型,影响铸件的质
量。
从这点考虑,故将动、定模的导向设计成
利用动、定模套板外缘倒角的配合来实现的形式(见图3)。
定模套板的倒角与定模型腔、浇口套的配合孔等一起车出,动模套板的倒角同动模镶块安装孔、分流锥的配合孔等一起车出,这
图3图2中I部的尺寸
样,依靠动、定模套板外缘倒角的配合,能有效地保证动、定模型腔的同轴度要求。
在将动、
定模套板与压铸机相对应的安
轿车抗扭支架压铸模设计湖南机油泵股份有限公司(湖南衡东421400)袁晓斌
[摘要]通过对轿车上抗扭支架零件压铸模的设计与制造,介绍了阶梯分型模具设计要点及液压斜销复合侧抽芯设计。
关键词压铸模阶梯分型复合抽芯预复位
图1抗扭支架
装孔加工完毕及动、定模套板配合好后,利用工艺连杆暂时固定动、定模的周向位置,然后在动、定模套板上配钻导柱、导套孔,这样模具依靠导柱、导套及套板的外缘倒角共同作用,保证动、定模的导向及定位精度。
2.3推出机构
因为模具安装在双动液压低压铸造机上使用,这种压铸机备有液压推出器,所以用连杆2、连杆1分别将动模套板6、推板18与压铸机的动模板、液压推出器相联,省去了一般压铸模所用的模座、复位杆、限位钉、挡钉等结构零件,简化了模具结构与操作程序。
推出机构的推出和复位行程由压铸机上的行程开关调节并固定。
1零件工艺分析
抗扭支架是轿车上的1个重要安全性零件(见图1),材料为铝合金AlSi12(Cu),质量550g。
该件形状复杂,孔多且深,壁厚要求均匀,组织致密,并有较高的力学性能要求。
整个零件在压铸后不经机械加工,故要求有较高的形状、位置及尺寸精度,如图1中4个11mm孔距尺寸将直接影响装配性能的好坏,因此该模具设计制造难度较大,在模具设计与制造中要充分考虑各方面因素的影响。
2模具设计
2.1模具分型面的选择
一般来说,确定分型面时,应相应地考虑铸件技术条件,内浇口位置和浇注系统位置、———————————————————
收稿日期:1997年7月16日模具基本结构及铸件在动、定模各部分的位置、模具加工工艺性、型腔的溢流和排气等有关问题。
分析该支架零件,其外形虽不是很复杂,但各向差别很大,给分型面的选择造成了较大的不便。