德马克铁合金电炉部分设备简介
铁合金烘烤炉说明[新版]
![铁合金烘烤炉说明[新版]](https://img.taocdn.com/s3/m/690c9ffd80c758f5f61fb7360b4c2e3f572725a0.png)
合金烘烤炉说明书合金烘烤炉是烘烤铁合金的专用设备,通过对硅铁、锰铁、铬铁、钼铁、钛铁、钒铁等合金炉料进行脱水份烘烤,在200℃内进行脱游离水份烘烤,在400-600℃内进行脱结晶水份烘烤。
使合金达到要求温度,能满足炼钢工艺要求,实现缩短冶炼时间,提高钢材质量的目的。
一、技术说明:由于合金料在200℃左右脱游离水,在400-600℃内脱结晶水,合金料需要脱水,加热温度必须达到400℃以上,因此铁合金烘烤装置作为烘烤铁合金的专用设备,必须满足以下要求:1、合金料经过加热,达到400-500℃;2、加热形式:间接加热形式,采用烘烤炉形式,形成过热风(500-600℃),用过热风加热合金块;3、燃烧采用过氧燃烧,煤气燃烧率在99%以上,形成无害烟气;4、燃烧器口采用耐热钢,延长使用寿命;5、控制方式:手动控制;自动点火;6、点火气体:乙炔或天然气;7、燃烧介质:转炉煤气;二、工作原理及特点:1、转炉煤气通过燃烧器燃烧,产生约1200℃左右的高温烟气,吹进燃烧室,在燃烧室内与所配冷风初步混合,并在高温下进一步反应,燃尽高炉煤气(一氧化碳);形成无毒的约800℃左右的高温烟气;在燃烧室末端,热烟气与配风充分混合,形成500-600℃左右的热风。
2、由于合金使用上,炼钢是间断性出料,加热是连续性加热,且加热的热风喷口在合金料仓的底部,形成自下向上逆流加热,使料仓出料接近热风温度,达到400-500℃。
3、由于热风温度过高,为保证热效率,可以给热风管道加保温。
三、设备构成:设备由转炉煤气燃烧器,混风用热风炉,助燃风机,冷风混风风机,热风管路及电控系统组成。
1、燃烧器含自动点火烧嘴:自动点火烧嘴和煤气烧嘴头均为不锈钢;2、混风用热风炉由燃烧室,内衬(不锈钢)及热风炉外壳组成,混风机构实现最后热风,实现烘烤用的热风3、观火孔可以清楚观测火焰样式,掌控火焰燃烧情况。
4、助燃风机供烧嘴燃烧用空气。
5、冷风混风风机直接进入混风用热风炉,迅速提升自己温度,降低高温热风温度,调和成工艺需要的热风温度。
铁合金生产工艺与设备

铁合金生产工艺与设备
铁合金是一种含有铁和其他合金元素的材料,广泛应用于钢铁行业和其他领域。
铁合金生产涉及到多个环节和工艺步骤,同时需要使用一系列的设备来完成。
铁合金生产的工艺流程通常包括原料准备、熔炼、浇铸和后处理等步骤。
下面将对每个步骤进行详细描述:
1. 原料准备:铁合金的原料通常包括铁矿石、合金元素和还原剂。
铁矿石经过破碎、磨矿和磁选等处理后,与合金元素(如硅、锰等)和还原剂(如焦炭)按一定比例混合。
同时,根据需要进行化验分析,确保原料的质量和合理配比。
2. 熔炼:原料经过配料后,进入熔炼炉中进行加热熔化。
熔炼一般采用电炉、高炉或转炉等设备。
其中,电炉主要用于生产高合金铁,高炉适用于大规模生产铸铁,转炉适用于生产铸钢。
3. 浇铸:熔化的金属液通过铁水包或者废钢包装入浇铸机中,然后进行浇铸。
浇铸一般分为两种:连续浇铸和间歇浇铸。
连续浇铸适用于大规模连续生产,间歇浇铸适用于较小量的特殊合金的生产。
4. 后处理:浇铸后,铁合金需要进行冷却、固化和除渣等处理。
此外,还需要对产品进行打磨、修整和品质检测等工序,确保产品达到规定的技术要求。
在铁合金生产中,使用的设备包括破碎机、磁选机、磨矿机、
电炉、高炉、转炉、浇铸机、冷却装置、除渣设备、打磨机、质检设备等等。
这些设备在生产过程中充当了不同的角色,以确保合金的质量和生产效率。
总而言之,铁合金生产工艺涉及到原料准备、熔炼、浇铸和后处理等多个步骤,同时需要使用一系列的设备来完成。
这些工艺和设备的合理运用,对于铁合金的质量和生产效率起着至关重要的作用。
国外矿热炉技术发展现状浅析

国外矿热炉技术发展现状浅析李静隋欣杨宝玉闫志新中钢集团吉林电器设备有限责任公司吉林中国摘要通过对德国西马克公司矿热炉技术开发应用情况、芬兰欧托昆普及GLPS公司技术在南非应用情况的简单介绍,了解国外矿热炉技术发展动态,为我国矿热炉技术研发提供一点参考。
关键词矿热炉埋弧炉直流等离子炉概述在世界铁合金生产过程中,原料供应和生产成本始终处于最重要的地位。
南非因为拥有丰富的矿产资源,长期以来铁合金生产一直处于领先地位。
随着时间的推移,优质矿产资源日益减少,加上环境保护意识的增强,有效利用劣质矿产资源,降低生产成本成为铁合金生产商不断追求的目标,矿热炉生产技术的发展主要就是围绕这条主线展开的。
一、原料美国政府地质局最新调查表明[1]:世界铬铁矿资源总量超过120亿吨。
世界上铬铁矿资源丰富的国家主要有南非、哈萨克斯坦、印度、巴西等国。
南非和哈萨克斯坦是世界上两个铬铁矿资源最丰富的国家,其铬铁矿资源量约占世界铬铁矿资源量的95%。
全世界商品级铬资源(Cr2O3 45%)大约在4.74亿吨。
南非占全世界经济储量的75%,全部储存在布什维尔德杂岩体[1]。
最大矿山体是LG3和LG4铬铁矿层,在布什维尔德杂岩体西部,Cr2O3 50%、Cr/Fe=2.0。
经济分组是LG6、Cr/Fe=1.5-2.0,MG1/2、Cr/Fe=1.5-1.8和UG2(见表1)[2]。
UG2、Cr/Fe =1.3-1.4是铂族金属的主要来源。
表1 UG2、MG2和LG6铬矿组分、尺寸分布和平均颗粒尺寸象铬矿一样,南非大量的锰矿集中在西北地区卡拉哈尔锰矿。
据美国地质局最新调查表明南非占全球已探明锰矿储量的80%。
南非锰矿有两种类型:一种是碳酸盐型,品位低(含锰38%)、Mn/Fe比高(含铁4%),另一种是硅酸盐型,品位高(含锰40%-48%)、Mn/Fe比低(含铁18%-12%)。
与铬矿和锰矿相比,矿石中钒含量很低,通常在2%左右。
据美国地质局估计全世界钒矿储量为6300万吨。
某冶炼厂设备简介

某冶炼厂设备简介1. 引言某冶炼厂是一家专注于金属冶炼产业的现代化企业。
为了满足不断增长的市场需求,该厂采用先进的设备和技术进行生产。
本文将对某冶炼厂的主要设备进行简要介绍。
2. 设备一:高炉高炉是某冶炼厂的核心设备之一,用于冶炼金属。
该高炉采用最新的炉体设计,具有高效节能的特点。
高炉内部采用先进的喷煤技术,可以充分利用煤炭资源,并确保高炉的稳定运行。
高炉还配备了先进的自动控制系统,可以对温度、压力等参数进行实时监控和调节,确保产品质量的稳定性。
3. 设备二:炼铁设备炼铁设备是某冶炼厂的重要设备之一,用于将矿石炼制成铁水。
该炼铁设备采用先进的炼铁工艺,具有高度自动化和智能化的特点。
炼铁设备包括矿石破碎、矿石烘干、矿石熔化和铁水出炉等环节。
整个炼铁过程实现了全程闭路控制,大大提高了产品的质量和产量。
4. 设备三:冷却设备冷却设备是某冶炼厂的必备设备之一,用于冷却高温金属材料。
冷却设备采用先进的风冷系统和水冷系统,可以根据不同材料的冷却需求进行灵活配置。
冷却设备还配备了高效的换热器,可以充分利用余热资源,实现能源的节约和循环利用。
5. 设备四:过滤设备过滤设备是某冶炼厂的重要设备之一,用于去除金属材料中的杂质和废气。
过滤设备采用先进的过滤技术,具有高效过滤和精准分离的特点。
过滤设备还配备了可调节的过滤介质,可以根据不同材料的特性进行调整,提高过滤效果和工艺控制。
6. 设备五:除尘设备除尘设备是某冶炼厂的必备设备之一,用于去除生产过程中产生的粉尘和废气。
除尘设备采用先进的静电除尘和湿式除尘技术,可以有效净化废气和回收金属材料。
除尘设备还配备了高效的吸附剂和过滤介质,可以提高除尘效率和处理效果。
7. 设备六:输送设备输送设备是某冶炼厂的关键设备之一,用于将原料和成品从一个地方输送到另一个地方。
输送设备采用先进的输送技术,包括皮带输送、螺旋输送和气力输送等。
输送设备具有高效、安全、可靠的特点,在整个生产过程中起到了至关重要的作用。
鞍钢的历史

鞍钢的历史1904年日俄战争爆发,俄国战败后签订了《朴茨茅斯和约》,日本夺取了原由俄国控制的长春至大连之间的南满铁路和旅大租借地。
1906年,日本为加强对东北的政治和经济侵略,于大连设立了南满洲铁道株式会社(简称满铁)作为在经济上侵略中国东北地区的大本营。
1909年8月,满铁派人对鞍山地区进行非法的秘密探矿,先后调查了铁石山、西鞍山、东鞍山、大孤山、樱桃园、关门山、小岭子、弓长岭等十余座铁矿山,并发现了大石桥菱镁矿、烟台粘土矿等资源,发现鞍山地区是开矿建厂冶炼钢铁的宝地。
于是满铁总裁中村雄次郎提出掠夺鞍山地区钢铁资源的计划,由大汉奸于冲汉和日本人镰田弥助出面,组建中日合办振兴铁矿无限公司。
1916年7月中日合办振兴铁矿无限公司总局在奉天成立,资本14万日元,名义上中日投资各半,实则由满铁全额初资。
在千山设采矿总局,两年后总局迁鞍山。
1917年获得了大孤山、樱桃园、东鞍山、西鞍山、王家堡子、对面山、关门山、小岭子、铁石山等8个矿区的开采权。
其总面积达14578亩。
1921年又获得的白家堡子、一担山、新关门山等3个矿区的开采权。
仅在1926年—1933 年采量480万吨。
该总局经营到1940年宣布解散,并入昭和制钢所。
1916年满铁在办公司的同时开始鞍山制铁所的建厂工作。
1916年,日本政府批准建立鞍山制铁所,1917年4月3日举行“地镇祭”,动工修建高炉。
1918年5月15日,“鞍山制铁所”正式成立,八田郁太郎任鞍山制铁所所长,建厂工程大部分在年底完成。
1919年3月,炼焦厂开始生产焦炭。
4月29日,1号高炉点火,标志鞍山制铁所正式投产。
1931年“九一八”事变后,日本占领了东北全境。
1933年,日本政府在军部支持下,将原定在朝鲜兴建的昭和制钢所改迁鞍山,由满铁全额出资,在鞍山制铁所已有基础上,兴建制钢厂、轧材厂,成为钢铁联合企业。
株式会社鞍山昭和制钢所为日本法人,属满铁的子会社,社长为伍堂卓雄。
德马克铁合金电炉部分设备简介

德马克铁合金电炉部分设备简介德马克的铁合金电炉现在仍然是国际上比较先进的技术,结构坚固耐用,使用寿命长。
从1987年开始我们对德马克电炉设备进行了消化和试制,并成功的运用到6000KV A和12500KV A硅铁电炉的设计中,取得了令人满意的效果,使我国的铁合金电炉技术达到了国际水平。
近几年,通过对这套设备的消化、试制及移植,已掌握了德马克电炉技术。
现把德马克电炉有自己特点的部分设备作简单介绍,以便和大家交流。
一、压力环压力环的作用是压紧铜瓦抱住电极,使电流经铜瓦均匀的通过电极进入炉内。
德马克的压力环是由两个半环组成的,内部水路很复杂,冷却水先进入下腔,然后沿着外圈水冷腔由下而上循环,再进入里圈循环,最后排出。
外圈水冷腔很窄,内圈较宽,压力环靠近火焰部分冷却效果非常好,这样就保证了压力环的使用寿命长。
压力环是用由波纹管组成的伸缩箱顶紧铜瓦,伸缩箱的组数与铜瓦块数相同,成一一对应的关系,这就是压力环比锥型环优越的地方。
压力环能同时均匀地压紧每块铜瓦,锥形环作不到这一点。
因此,使用压力环能延长铜瓦使用寿命。
伸缩箱其实就是一种特殊结构的液压缸,用波纹管代替了液压缸的缸体。
当液压系统给压时,波纹管伸长,带动压缩箱压紧铜瓦;撤压时,波纹管靠自身弹力弹回松开铜瓦。
波纹管密封性好,不会漏油。
二、铜瓦德马克铜瓦与我国铜瓦的最大区别是冷却水的水路。
德马克铜瓦水路是钻成的,因此冷却效果好得多,使用寿命长,一般在三年以上。
另外,铜瓦制造方法也与我们不同,德马克的铜瓦是用离心浇铸法浇铸,然后再经过锻造,铜瓦内表面还要进行机加工,要求一根电极上的几块铜瓦一起加工,因此,铜瓦内表面的光洁度和椭圆度都能得到保证,使铜瓦与电极接触好,导电性好。
铜瓦是用紫铜制造。
三、短网与水冷电缆德马克的水冷电缆是卡环式的。
卡环有两个作用:一是卡紧与其相连的导电铜管;二是导电,电流由导电铜管经卡环流入电缆中的铜绞线,再经另一端的卡环流向另一导电铜管。
铁合金矿热炉烟气回收能源利用述评

2 0 ~ 00 0N , 口烟气 温 度 20 40℃。 50 0 3 0 炉 5~0 烟气余热 属于中温余热 , 废气 流量 较少 , 热品位 较 低; 烟气 温度 、 流量具有 一定 的波动性 , 波动 范围 大 ; 气 中 的 硅 微 粉 极 细 , 均 粒 径 05 02I 烟 平 . ., m, z
的确定 、 热锅炉的低温换 热技Байду номын сангаас 、 热锅 炉的清 余 余 灰 技术 ( 械振 打 、 机 燃气 爆燃 、 立式余 热锅 炉机 械
刷)余热锅 炉的建设及 运行对铁合 金生产线 的影 、 响、 锅炉烟气阻力对矿热炉风机 的影响和粉尘 的回 收利用等 。 3 国内某厂硅铁矿热炉烟气余热发电实例 . 4 () 1 烟气余热参数 单 台矿热炉烟气流量 10 0 m/, 2 0 。 烟气温度 0 N h 3 0℃, 7 烟气 出炉烟 囱压力一 8 a 烟气 化学成份 : 8P , C 3 5 )、 1 1 ) N (6 7 )、 : O (. % 5 H O(. % 、 : 7 . % 1 5 O (8 6 、O 0 1 。 1. %)C (. %) 7 O 硅微粉参数 , 平均粒径 O1 一 . I 具有极强 . 一 2x 5 0 m, 的表面活l。烟尘比重0 e 3 生 . g r, 2 / 烟尘含量3 5 /m 。 a  ̄ N 。 g 硅 微 粉 化 学 成 分 :O ( 1 % ) C O(.% ) F :, S 9. 7 、 a 02 、eO ( .% ) A : ,03 、 1 l ) N O(.4 ) 02 、 I ( .%) K O( . % 、 a 1 % 、 O 4 5
可以解决荒煤气爆炸风险。但是 , 由于荒煤气 中含 有 KO、 a : N O等碱金属 氧化物 , 熔点 比较低 , 在燃烧 过程 中容易 附 着 于锅 炉 水冷 管 壁 , 以清 除造 成 堵 难 塞, 因而 该 工 艺 流 程 最 终 没 被采 用 。 目前 , 内 内 国 燃式 电石炉 回收荒煤气就有采用先烧锅炉发 电、 后 除尘 净 化排 放 的 工艺 流 程 。 因此 , 全封 闭型锰 硅 合 金 矿热 炉 荒煤 气 , 烧 锅 炉 发 电 , 气 最 后 再 经 除 先 废 尘净 化后排 放 工艺流 程应该 继续 试验 实践 。
不锈钢生产工艺简述
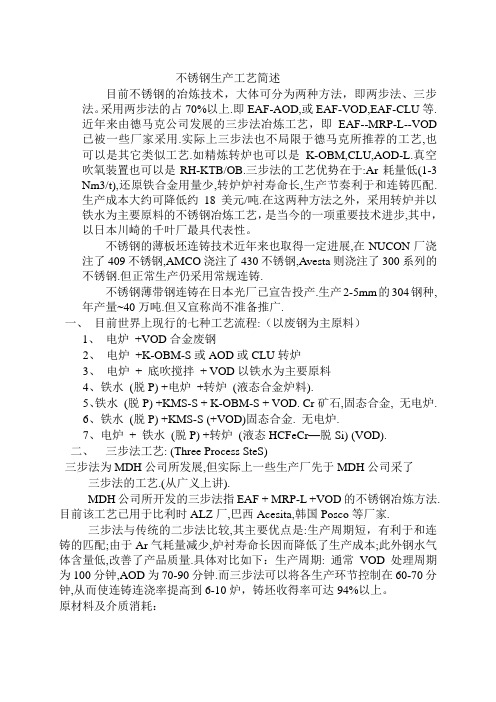
不锈钢生产工艺简述目前不锈钢的冶炼技术,大体可分为两种方法,即两步法、三步法。
采用两步法的占70%以上.即EAF-AOD,或EAF-VOD,EAF-CLU等.近年来由德马克公司发展的三步法冶炼工艺,即EAF--MRP-L--VOD 已被一些厂家采用.实际上三步法也不局限于德马克所推荐的工艺,也可以是其它类似工艺.如精炼转炉也可以是K-OBM,CLU,AOD-L.真空吹氧装置也可以是RH-KTB/OB.三步法的工艺优势在于:Ar耗量低(1-3 Nm3/t),还原铁合金用量少,转炉炉衬寿命长,生产节奏利于和连铸匹配.生产成本大约可降低约18美元/吨.在这两种方法之外,采用转炉并以铁水为主要原料的不锈钢冶炼工艺,是当今的一项重要技术进步,其中,以日本川崎的千叶厂最具代表性。
不锈钢的薄板坯连铸技术近年来也取得一定进展,在NUCON厂浇注了409不锈钢,AMCO浇注了430不锈钢,Avesta则浇注了300系列的不锈钢.但正常生产仍采用常规连铸.不锈钢薄带钢连铸在日本光厂已宣告投产.生产2-5mm的304钢种,年产量~40万吨.但又宣称尚不准备推广.一、目前世界上现行的七种工艺流程:(以废钢为主原料)1、电炉+VOD合金废钢2、电炉+K-OBM-S或AOD或CLU转炉3、电炉+ 底吹搅拌+ VOD以铁水为主要原料4、铁水(脱P) +电炉+转炉(液态合金炉料).5、铁水(脱P) +KMS-S + K-OBM-S + VOD. Cr矿石,固态合金, 无电炉.6、铁水(脱P) +KMS-S (+VOD)固态合金. 无电炉.7、电炉+ 铁水(脱P) +转炉(液态HCFeCr—脱Si) (VOD).二、三步法工艺: (Three Process SteS)三步法为MDH公司所发展,但实际上一些生产厂先于MDH公司采了三步法的工艺.(从广义上讲).MDH公司所开发的三步法指EAF + MRP-L +VOD的不锈钢冶炼方法.目前该工艺已用于比利时ALZ厂,巴西Acesita,韩国Posco等厂家.三步法与传统的二步法比较,其主要优点是:生产周期短,有利于和连铸的匹配;由于Ar气耗量减少,炉衬寿命长因而降低了生产成本;此外钢水气体含量低,改善了产品质量.具体对比如下:生产周期: 通常VOD处理周期为100分钟,AOD为70-90分钟.而三步法可以将各生产环节控制在60-70分钟,从而使连铸连浇率提高到6-10炉,铸坯收得率可达94%以上。
Mahler德国马勒烧结炉详解1

41 % H2 20,5 % CO 38,5 % N2
incl.(CO2+H2O)
便宜的保护气氛:
1立方米天然气可获得近5立方米吸热气氛, 或1立方米液化石油气获得13立方米吸热气氛
10
1. 气氛测量与控制 氮氢混合物 吸热气氛 用露点计或氧探头探测保护气氛 氧探针直接测量控制保护气体的质量
氧探针读出的毫伏值对应某温度下的碳势和的露点值
O R O R
MeO + H2 MeO + CO
O R
MeO
7
1. 渗碳和脱碳 平衡取决于气体组成成分的部分压力
渗碳
2CO 2CO CH4 2CO + H2
2C + O2 C + CO2 C + 2H2 C + H2O
脱碳
8
1. 吸热气氛同氮气/氢气的比较
吸热气氛 生成/供给 气体供给 应用 露点 碳势控制 气体质量控制 工艺特性 成本 - 内置发生器 - 外置发生器 - 天然气或液化石油气 - 铁,铜粉末 - 根据碳势变化在0 至 -25°C - 自动控制 - 氧探头 - 碳中性或渗碳 如果同马勒快速脱蜡区结合使 用,可以节省到50%的能量
t ime [s]
现行高效的气体冷却系统冷却速 度可超过4-8度/秒
硬度可高达HRC 50-55
22
6. 电脑控制
过程控制,电脑和软件纪录文件对操作者有以下功用: • 烧结工艺和窑炉状态即时可视化显示 • 记录在硬盘上的窑炉日志 • 不同烧结工艺曲线的管理 • 故障报警和指导 • 窑炉历史记录 • 维修保养指导 • 有电话线连接的调制解调器进行远距离故障诊断
3
1. 烧结气氛 – 不同气氛的功能和特性 2. 脱蜡区的比较: 快速燃烧脱蜡同传统脱蜡 3. 不同烧结工艺的运转成本比较 4. 烧结炉的功能性设计细节,例如传送,加热 5. 烧结硬化系统 6. 电脑控制
帮您了解高炉炼铁所用主要设备!因为了解,所以更专业!
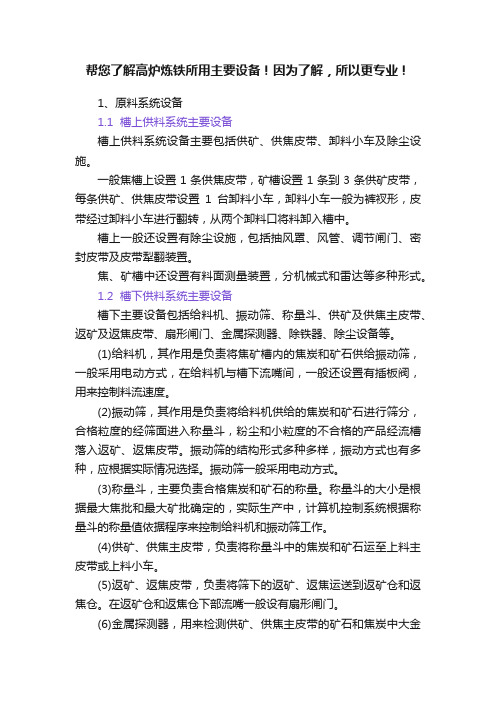
帮您了解高炉炼铁所用主要设备!因为了解,所以更专业!1、原料系统设备1.1 槽上供料系统主要设备槽上供料系统设备主要包括供矿、供焦皮带、卸料小车及除尘设施。
一般焦槽上设置1条供焦皮带,矿槽设置1条到3条供矿皮带,每条供矿、供焦皮带设置1台卸料小车,卸料小车一般为裤衩形,皮带经过卸料小车进行翻转,从两个卸料口将料卸入槽中。
槽上一般还设置有除尘设施,包括抽风罩、风管、调节闸门、密封皮带及皮带犁翻装置。
焦、矿槽中还设置有料面测量装置,分机械式和雷达等多种形式。
1.2 槽下供料系统主要设备槽下主要设备包括给料机、振动筛、称量斗、供矿及供焦主皮带、返矿及返焦皮带、扇形闸门、金属探测器、除铁器、除尘设备等。
(1)给料机,其作用是负责将焦矿槽内的焦炭和矿石供给振动筛,一般采用电动方式,在给料机与槽下流嘴间,一般还设置有插板阀,用来控制料流速度。
(2)振动筛,其作用是负责将给料机供给的焦炭和矿石进行筛分,合格粒度的经筛面进入称量斗,粉尘和小粒度的不合格的产品经流槽落入返矿、返焦皮带。
振动筛的结构形式多种多样,振动方式也有多种,应根据实际情况选择。
振动筛一般采用电动方式。
(3)称量斗,主要负责合格焦炭和矿石的称量。
称量斗的大小是根据最大焦批和最大矿批确定的,实际生产中,计算机控制系统根据称量斗的称量值依据程序来控制给料机和振动筛工作。
(4)供矿、供焦主皮带,负责将称量斗中的焦炭和矿石运至上料主皮带或上料小车。
(5)返矿、返焦皮带,负责将筛下的返矿、返焦运送到返矿仓和返焦仓。
在返矿仓和返焦仓下部流嘴一般设有扇形闸门。
(6)金属探测器,用来检测供矿、供焦主皮带的矿石和焦炭中大金属件,以免损坏皮带和炉顶设备。
(7)除铁器,用来清除矿石和焦炭中金属件。
(8)除尘设备,主要包括抽风罩、风管、调节闸门。
一般槽上槽下共用一台除尘器,分电除尘和布袋除尘两种。
电除尘器运行可靠、费用低,但除尘效果不如布袋除尘好。
布袋除尘运行费用高、维护量大,但除尘效果好。
棒材粗中轧轧件头部开裂成因及改进方案

自2019年以来,生产线堆钢事故频发,而粗轧 堆钢事故占了很大比例,其中前9机架堆钢的最主 要原因就是头部开裂(劈头)。对于产量、坯耗、能耗 等方面产生了很大影响,亟待解决。
1粗轧过程中头部开裂的成因分析 线棒作业区棒材主要生产规格为012 mm、
014 mm、O16 mm的HRB400E,这是一条由高速线 材轧线改造的。故有必要对其棒材生产工艺进行简 单介绍。
1.1该生产线的主要工艺设备 1) 200 n?蓄热式步进加热炉,最大加热能力为
每小时1101,加热钢坯长度为5.7-6.25 mo 2) 粗中轧机组为单线连续式布置,直流调速电
机单独传动。其中1—4架轧辐直径600 mm,5—9 架 480 mm,中轧 10—13 架 350 mm0
3) 预精轧机组为德国德马克公司进口 ,14,16架 为悬臂水平轧机,15、17架为悬臂立式机架,单线连 续式布置,直流调速电机单独传动。其中14—17架 轧辐直径275 mm。
4 )/1棒R轧机组为德国德马克公司进口 ,15。/75°交 替布置的悬臂式精轧机,直流调速电机集体传动。高 速无扭轧制,全部碳化铸辐环,表面光洁、尺寸精度
铁合金电炉的介绍及应用

铁合金电炉冶炼铁合金的主要设备,铁合金电炉分为还原电炉和精炼电炉两类。
铁合金电炉冶炼铁合金的主要设备。
铁合金电炉分为还原电炉和精炼电炉两类。
还原电炉又称埋弧电炉或矿热电炉,采取电极插入炉料的埋弧操作,还原电炉有敞口、封闭(或半封闭),炉体有固定、旋转等各种形式。
精炼电炉用于精炼中碳、低碳、微碳铁合金。
电炉容量一般为1500~6000千伏安,采用敞口固定或带盖倾动形式。
前者类似还原电炉,可配备连续自焙电极;后者类似电弧炼钢炉,使用石墨或炭质电极。
简介tiehejin dianlu铁合金电炉ferroalloy furnace冶炼铁合金的主要设备。
分类铁合金电炉分为还原电炉和精炼电炉两类。
还原电炉又称埋弧电炉或矿热电炉,采取电极插入炉料的埋弧操作,还原电炉有敞口、封闭(或半封闭),炉体有固定、旋转等各种形式。
50年代以前普遍采用敞口固定式电炉(图1a铁合金还原电炉),随着环境保护要求的提高和余热利用技术的进展,对不同产品分别采用封闭式电炉(图1b铁合金还原电炉)或矮烟罩、半封闭式电炉(图1c铁合金还原电炉)。
炉体旋转可以消除悬料、减少结壳“刺火”使布料均匀、反应区扩大,以利炉况顺行。
电炉容量(在铁合金生产中指电炉变压器容量,按千伏安计,用以标志电炉能力)在50年代以前一般从几百至一万千伏安左右,后来逐渐向大型化发展。
70年代新建电炉一般为20000~40000千伏安,最大的封闭式电炉达75000千伏安,最大的半封闭炉达96000千伏安。
现代铁合金电炉一般为圆形炉体,配备三根电极。
大型锰铁电炉有采用矩形多电极的。
大型硅铁电炉有些装备旋转机构,炉体以30~180小时旋转360°的速度沿水平方向旋转或往复摆动。
封闭电炉设置密封的炉盖,半封闭电炉在烟罩下设有可调节开启度的操作门,以控制抽入空气量和烟气温度。
电极系统广泛采用连续自焙电极,最大的直径可达2000毫米,有的还做成中空式。
连续自焙电极由薄钢板电极壳和电极糊组成,在运行中电极糊利用电流通过时产生的热量和炉热的传导辐射自行焙烧。
康迪克电炉炼钢技术的优点及发展前景

因此, 其交流变压器如表 3 所列。
表 3 康迪克电炉炼钢的主 要技术参数
变压器功率 变压器 25M W( 36M VA) 变压器 52M W( 72M VA)
出钢周期 60min 100t 60min 200t
产量 75 万 t/ 年 150 万 t/ 年
变压器 78M VA( 108M VA)
30min 100t 60min 300t 30min 150t 20min 100t
在此我们对三种类型电炉: 传统电弧炉、竖炉 和 CONT IARC 的能源利用作了比较。
温度 600℃ 1 量 58kWh/ t ( 传统电弧炉) 。
温度 300℃ 800N m3/ t 的废气燃烧后或预热 到 900℃, 需能量 94kWh/ t ( 竖炉) 。
·4 7·
2) 竖炉 55M VA( →64% ) 3) CONT IARC 36MVA ( →43% ) 下面概括了这种 CONT IARC 电炉的主要特 性, 这种新的技术思路同时成为现实。即: 此工艺具有生产率高, 电极消耗低的优点。可 通过对加入炉料预热的最优化, 使单位能耗( 电能 及基本能源) 降低。并且电网干扰( 波动) 低, 还有 环境优化和低的冷却水量等特性。
CON T IARC= 73% 这 项 对 比 清 晰 地 说 明, 这 种 新 型 的
CON T IARC 电炉是当今最节 能的, 因此也 是最 经济 的炼钢 工艺, 这也强 调了每 小时产 钢 100t ( 相当于年产 75 万 t ) 所必需的变压器功率。
1) 传统电弧炉 86M VA( →100% )
约 85 万 t , 生产费 用 CONT IARC 便宜 42% , 与 传统电炉相比 直接成本消耗每年节约 960 万美
矿热炉机械设备

2、矿热炉机械设备2.1 电极把持器2.1.1 电极把持器的作用和分类电极把持器是电炉机械设备的重要组成部份,它的作用有如下三点:1. 将强大的电流传递给电极;2. 将铜瓦牢固地加紧在电极上;3. 配合压放和升降电极。
电极把持器悬挂在炉口的上方,全部构件都处于高温区,承受着炉口辐射和炉气的作用,而且通电部位还会产生热量,不通电部位因感应电流感应也要发热,以必须通水冷却。
把持器的结构,要求尽量简单、电损耗小、操作方便、检修时更换容易、材质要求在高温下有较高的机械性能,并具有和绝缘隔磁的性能。
电极把持器根据构造的不同,可分为吊挂式和横臂式两类,用的较多的吊挂式,横臂式大多用在功率不大,电极直径较小的炉子上,其装置与炼钢电炉上的电极装置相似。
以下仅对吊挂式电机把持器进行综述。
电极把持器广义来讲有电极夹紧环、导电铜瓦、吊挂装置、水冷大套、电极把持筒和横梁等组成,实为电极把持器系统;窄义讲则仅指使铜瓦压紧电极的那部分装置。
电极把持器使铜瓦压紧电极的装置形式是很多的,目前国外采用较多的有气动弹簧式、液压波纹管式,油马达传动的锥形环式及水压橡皮膜式等。
鉴于我国的技术水平,目前国内矿热炉常见的有液压一锥形环式电极把持器(图2-1)图2-1 液压一锥形式电极把持器和水平项紧压力环式把持器(图2-2)。
1-铜瓦;2-锥形环;3-吊架;4-护板;5-电极把持筒;6-横梁;7-松紧油缸;8-吊杆;9-弹簧;10-顶杆;11-压放抱闸;12-压放油缸;13-槽钢图2-2 水平项紧压力环式把持器1-电机壳;2-压力环;3-铜瓦;4-密封套装置;5-压力环上吊环;6-铜管;7-铜瓦吊杆;8-夹布输水胶管;9-水管;10-无缝钢管油管;11-下把持筒;12-铜管;13-电极密封装置;14-硅酸铝纤维毡2.1.2电极夹紧环(2)整体型锥面电极夹紧环整体型锥面电极夹紧环,简称锥形环,是一个整体构件,里环断面带一倾斜角。
材质可用非磁性钢或普通钢,有铸造件和铆焊件两种。
德国75000KVA电石炉简介
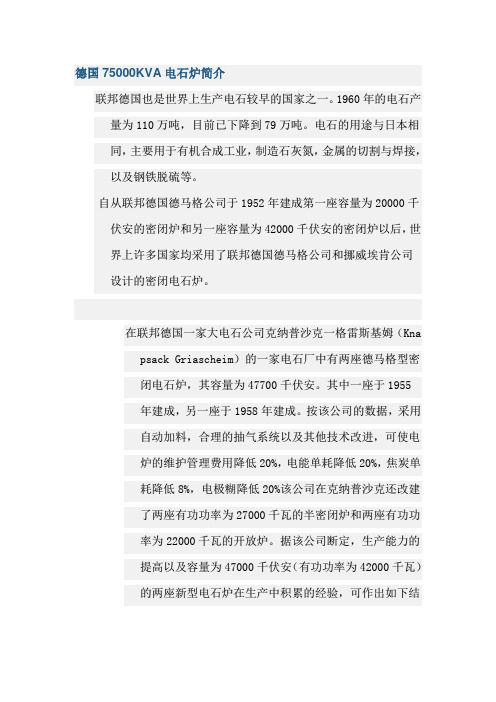
德国75000KVA电石炉简介联邦德国也是世界上生产电石较早的国家之一。
1960年的电石产量为110万吨,目前已下降到79万吨。
电石的用途与日本相同,主要用于有机合成工业,制造石灰氮,金属的切割与焊接,以及钢铁脱硫等。
自从联邦德国德马格公司于1952年建成第一座容量为20000千伏安的密闭炉和另一座容量为42000千伏安的密闭炉以后,世界上许多国家均采用了联邦德国德马格公司和挪威埃肯公司设计的密闭电石炉。
在联邦德国一家大电石公司克纳普沙克一格雷斯基姆(K n a p s a c k G r i a s c h e i m)的一家电石厂中有两座德马格型密闭电石炉,其容量为47700千伏安。
其中一座于1955年建成,另一座于1958年建成。
按该公司的数据,采用自动加料,合理的抽气系统以及其他技术改进,可使电炉的维护管理费用降低20%,电能单耗降低20%,焦炭单耗降低8%,电极糊降低20%该公司在克纳普沙克还改建了两座有功功率为27000千瓦的半密闭炉和两座有功功率为22000千瓦的开放炉。
据该公司断定,生产能力的提高以及容量为47000千伏安(有功功率为42000千瓦)的两座新型电石炉在生产中积累的经验,可作出如下结论:当煤,电价格处于稳定的条件下,今后电石仍是化学工业所用乙炔的最重要原料。
⏹用优质原料联邦德国另一家大电石公司是西多伊特斯歇—卡尔克斯蒂克斯托弗韦尔(S u d d e u t s c h e-K a l k s t i c k s t o f f w e k e)公司,有一座容量42000千伏安的德马格型密闭电石炉。
该炉最大功率为35000千瓦,最大生产能力为日产电石255吨,单位电耗2940度,电石质量304升/公斤。
焦炭中的固定碳含量为91~94%,石灰中的氧化钙含量为96%。
⏹80年代.联邦德国伍德(U H D E)公司为某厂建成世界上最大的电石炉,其主要参数如下:⏹容量75000千伏安(三台单相变压器)⏹型式密闭型⏹电极直径1500毫米⏹一次电压22万伏⏹二次电压260~280伏⏹二次电流14.5万安⏹功率因数80%⏹日产电石435吨⏹净化后炉气10320立方米/时⏹联邦德国为了降低电石成本,开辟粉末原料的利用。
金属冶炼中的设备及工具介绍

汇报人:可编辑 2024-01-06
CONTENTS
目录
• 金属冶炼设备 • 金属冶炼工具 • 金属冶炼中的安全设备与工具 • 新技术与未来发展
CHAPTER
ห้องสมุดไป่ตู้01
金属冶炼设备
炼铁设备
01
02
03
高炉
用于将铁矿石还原成液态 铁,是炼铁过程中最主要 的设备。
直接还原炉
采用非高炉炼铁工艺,通 过直接还原方式将铁矿石 转化为海绵铁。
用于金属板材和管材的轧制,根据用途可分为热轧机 和冷轧机。
矫直机
用于对轧制后的金属板材进行矫直,提高板材的平直 度和表面质量。
剪切机
用于金属板材和管材的定尺剪切,以满足不同规格和 长度要求。
CHAPTER
02
金属冶炼工具
耐火材料
耐火材料
性能
在金属冶炼过程中,耐火材料是必不 可少的工具之一。它能够承受高温环 境,为金属熔炼提供良好的保护。
新材料的应用
高性能耐火材料
研发和采用高性能的耐火材料,提高冶炼设备的耐高温、耐磨损 性能,延长设备使用寿命。
新型过滤材料
采用新型的过滤材料,对金属溶液进行高效过滤,提高产品质量和 减少废品率。
高强度结构材料
采用高强度结构材料,减轻设备重量,提高设备刚度和稳定性,降 低能耗和生产成本。
自动化与智能化发展
耐火材料的性能主要取决于其化学成 分、矿物组成和显微结构。优质的耐 火材料应具备较高的耐火度、热稳定 性和抗侵蚀性。
种类
耐火材料有多种类型,如粘土、高岭 土、莫来石等,它们具有不同的物理 和化学性质,适用于不同的冶炼工艺 。
冶炼炉辅助工具
铁合金冶炼设备与工艺的节油与低碳减排技术

铁合金冶炼设备与工艺的节油与低碳减排技术1.铁合金作为重要的基础材料,广泛应用于钢铁、有色金属、化工等行业。
然而,铁合金冶炼过程的高能耗和高排放问题日益凸显,已经成为制约行业可持续发展的瓶颈。
因此,研究铁合金冶炼设备与工艺的节油与低碳减排技术具有重要的现实意义。
2. 铁合金冶炼设备铁合金冶炼设备主要包括高炉、炼铁炉、炼钢炉、感应炉等。
其中,感应炉是目前应用最广泛的铁合金冶炼设备,具有节能、高效、环保等优点。
感应炉冶炼铁合金时,炉子内部产生强磁场,使炉料产生热量,从而实现冶炼过程。
感应炉的优点在于可以实现对冶炼过程的精准控制,提高铁合金的质量和产量。
3. 铁合金冶炼工艺铁合金冶炼工艺主要包括高温还原法、直接还原法、熔融盐法等。
其中,高温还原法是目前应用最广泛的铁合金冶炼工艺,其原理是在高温条件下,将铁矿石与还原剂(如焦炭、煤气等)进行反应,从而得到铁合金。
高温还原法的优点在于工艺成熟、设备简单、成本较低。
4. 节油技术节油技术主要从提高燃料利用率、优化设备运行参数、开发新能源等方面进行。
提高燃料利用率方面,可以通过改进燃烧设备、优化燃烧过程、提高燃烧效率等手段实现。
优化设备运行参数方面,可以通过调整设备的工作参数,如炉温、炉压、转速等,实现节油效果。
开发新能源方面,可以研究新型高效燃料,提高新能源在铁合金冶炼过程中的应用比例。
5. 低碳减排技术低碳减排技术主要从减少污染物排放、提高资源利用率、开发清洁能源等方面进行。
减少污染物排放方面,可以通过改进排放处理设备、优化排放工艺、提高排放标准等手段实现。
提高资源利用率方面,可以通过回收利用废弃物、提高原料利用率、降低能耗等手段实现。
开发清洁能源方面,可以研究新型清洁能源,如太阳能、风能、生物质能等,并将其应用于铁合金冶炼过程。
6. 结论铁合金冶炼设备与工艺的节油与低碳减排技术是解决铁合金冶炼过程高能耗和高排放问题的关键。
通过改进冶炼设备、优化冶炼工艺、提高燃料利用率、减少污染物排放等手段,可以降低铁合金冶炼过程中的能源消耗和碳排放。