材料加工组织性能控制(第十章)XXXX9
工程材料施工质量控制(3篇)

第1篇一、材料选购与验收1. 材料选购:在材料选购过程中,要充分考虑材料的性能、质量、价格等因素,选择符合国家标准的优质材料。
同时,要关注材料的环保性能,确保工程项目的绿色、可持续发展。
2. 材料验收:在材料进场时,要严格按照相关标准和规定进行验收,确保材料的质量符合要求。
验收内容包括:外观质量、尺寸偏差、物理性能、化学成分等。
二、材料储存与保管1. 储存:材料应按照类别、规格、批次等进行分类储存,避免材料受潮、受热、受污染等影响。
对于易燃、易爆、有毒等危险品,要采取严格的安全措施。
2. 保管:建立健全材料保管制度,明确责任,确保材料在储存过程中的安全。
定期检查材料质量,发现问题及时处理。
三、施工过程中的质量控制1. 施工方案:根据工程特点,制定合理的施工方案,确保施工过程中的材料使用符合设计要求。
2. 施工工艺:严格按照施工工艺进行操作,确保施工过程中的材料使用质量。
3. 施工监控:加强施工过程中的监控,及时发现并解决材料使用过程中的问题,确保工程质量的稳定性。
四、材料检测与评估1. 检测:对施工过程中使用的材料进行定期检测,确保材料质量符合要求。
2. 评估:根据检测结果,对材料质量进行评估,为材料采购、储存、使用提供依据。
五、施工人员培训与考核1. 培训:加强对施工人员的培训,提高他们的质量意识和技术水平,确保施工过程中的材料使用质量。
2. 考核:对施工人员进行定期考核,确保他们具备相应的施工技能和质量意识。
总之,工程材料施工质量控制是确保工程质量的关键环节。
通过以上措施,可以有效提高工程材料施工质量,为我国工程建设事业的发展贡献力量。
在实际工作中,要不断总结经验,创新质量控制方法,为我国工程建设事业提供有力保障。
第2篇一、材料选择1. 严格审查材料供应商资质,选择信誉良好、质量稳定的供应商。
2. 根据工程设计要求,选择符合国家或行业标准、性能优良的材料。
3. 对进口材料,需了解其质量标准,确保其符合我国相关法规和规定。
材料组织性能控制复习题及答案完整版

1.弹性变形与塑性变形的区别弹性变形:可逆性:材料尺寸只发生暂时性改变,外力撤除,变形消失;单值性:σ=E ε,τ=G γ;应力应变成比例;全程性:弹性变形持续至材料断裂前;弹性变形的实质:金属原子自平衡位置产生可逆位移。
塑性变形:不可逆性:材料发生的不可逆的永久性变形;应力与应变的关系偏离虎克定律;先进性弹性变形,当达到屈服极限后发生塑性变形;塑性变形的主要机制为滑移和孪生。
2.在拉伸应力应变曲线上标出试样产生颈缩的位置,并分析其成因。
颈缩位置为工程应力应变曲线的最高点即抗拉强度点。
颈缩是均匀塑性变形和不均匀塑性变形(集中塑性变形)二者取一的结果。
当加工硬化使材料强度增加不足以抵偿横断面积减少造成承载能力下降时,便会产生集中变形,出现细颈。
塑性变形产生两个变化,一是加工硬化,二是横截面积减小。
金属在拉伸试验时塑性变形是由一段段变形实现的。
每段变形由开始、变形、停止、转出完成的,如果某一段塑性变形停不了,转不出,这段就要发生集中塑性变形——颈缩。
工程应力应变曲线3.工程应力-应变曲线与真应力-应变曲线的区别。
工程应力:0e P A σ=,工程应变:L L ε∆=;真应力:00()(1)t e P P P L L A L A A L lσσε+∆====+,真应变:ln ln ln ln(1)l Ldl L L e l L l L ε+∆==-==+⎰。
工程应力应变是以拉伸式样的原始尺寸进行计算的,故其应力值偏小,应变值偏大;并且出现载荷达到最大值后下降现象;真应变应力曲线随着应变的增加应力值持续上升,直至断裂,表明变形过程中一直有加工硬化,即使出现颈缩后,颈缩出的真应力值也是上升的。
4.韧窝的尺寸、深度与金属材料韧性的关系韧窝大小、深浅及数量取决于材料断裂时夹杂物或第二相粒子的大小、间距、数量及材料的塑性和形变强化指数以及外加应力的大小和状态。
如果夹杂物或第二相粒子多,材料的塑性和韧性较差则断口上形成的韧窝尺寸较小也较浅。
钢铁材料组织与性能控制(推荐五篇)
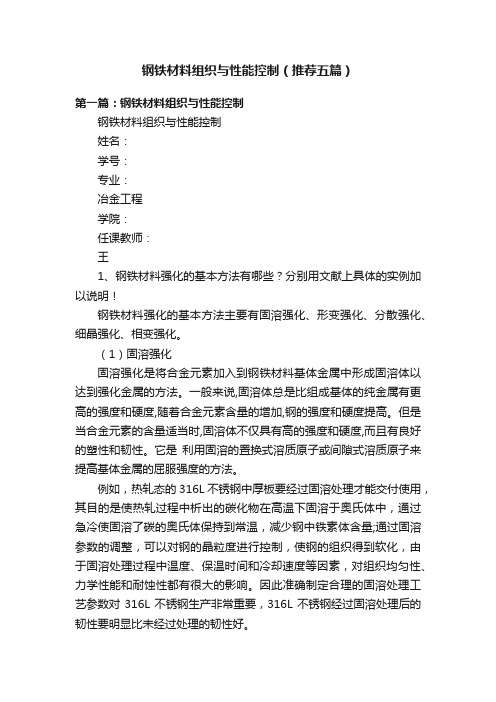
钢铁材料组织与性能控制(推荐五篇)第一篇:钢铁材料组织与性能控制钢铁材料组织与性能控制姓名:学号:专业:冶金工程学院:任课教师:王1、钢铁材料强化的基本方法有哪些?分别用文献上具体的实例加以说明!钢铁材料强化的基本方法主要有固溶强化、形变强化、分散强化、细晶强化、相变强化。
(1)固溶强化固溶强化是将合金元素加入到钢铁材料基体金属中形成固溶体以达到强化金属的方法。
一般来说,固溶体总是比组成基体的纯金属有更高的强度和硬度,随着合金元素含量的增加,钢的强度和硬度提高。
但是当合金元素的含量适当时,固溶体不仅具有高的强度和硬度,而且有良好的塑性和韧性。
它是利用固溶的置换式溶质原子或间隙式溶质原子来提高基体金属的屈服强度的方法。
例如,热轧态的 316L 不锈钢中厚板要经过固溶处理才能交付使用,其目的是使热轧过程中析出的碳化物在高温下固溶于奥氏体中,通过急冷使固溶了碳的奥氏体保持到常温,减少钢中铁素体含量;通过固溶参数的调整,可以对钢的晶粒度进行控制,使钢的组织得到软化,由于固溶处理过程中温度、保温时间和冷却速度等因素,对组织均匀性、力学性能和耐蚀性都有很大的影响。
因此准确制定合理的固溶处理工艺参数对 316L 不锈钢生产非常重要,316L 不锈钢经过固溶处理后的韧性要明显比未经过处理的韧性好。
(2)形变强化利用形变使钢强化的方法。
也称应变强化或加工硬化。
对于不再经受热处理,并且使用温度远低于材料再结晶温度的金属材料(譬如低碳低合金钢),经常利用冷加工(冷形变)手段使之通过形变强化来提高强度。
例如,奥氏体不锈钢304L和304LN的形变结构中出现层错、晶界、和退火孪晶处的位错塞积、位错胞状组织和形变孪晶。
形变过程中发生的组织结果变化均产生加工硬化,其中位错塞积和形变孪晶的贡献大。
高强度高碳钢冷拔钢丝,它是工业上强度最高的钢铁制品,抗拉强度可以达到4000MPa, 这就是用强烈冷变形的方法取得的。
(3)分散强化分散强化是在钢铁材料中第二相以细小弥散的颗粒均匀分布于基体金属中产生显著的强化作用,使钢铁材料的强度提高。
材料加工组织性能控制新
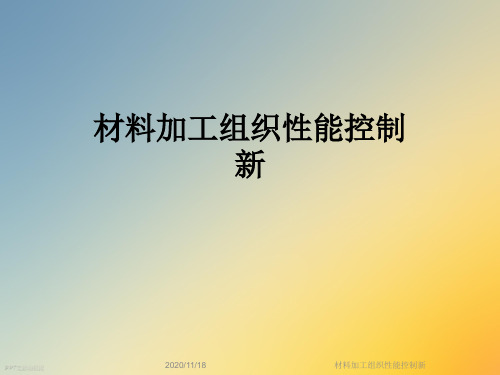
制工艺
0
5
•常规工艺
•850850
•8
•4042 •4045
•-
•60064
0
PPT文档演模板
材料加工组织性能控制新
• 3.2 钢的奥氏体形变与再结晶(I型控制轧制) • 3.2.1热变形过程中的奥氏体再结晶行为 • 3.2.1.1 动态再结晶
PPT文档演模板
材料加工组织性能控制新
(1)奥氏体再结晶区控制轧制(又称I型控制轧制)
条件:950℃以上 再结晶区域变形。 主要目的:对加热时粗化的初始晶粒轧制再结晶 细化 相变后细小的晶粒。相变前的晶粒越 细,相变后的晶粒也变得越细。
PPT文档演模板
材料加工组织性能控制新
(2)奥氏体未再结晶区控制轧制(又称为Ⅱ型控 制轧制) 条件: 950C~Ar3之间进行变形。 目的:晶粒沿轧制方向伸长,晶粒内部产生形 变带。晶界面积,的形核密度 ,进一步促 进了晶粒的细化。
•(1)细化相变前的奥氏体 晶粒;(2)在细化奥氏体 晶粒的前提下,进一步使奥 氏体处于加工硬化状态; (3)在相变温度区间加速 冷却。
•3.1.2.4 合金元素的作用(微合金元素作用再讲)PPT文档演模板
材料加工组织性能控制新
3.1.3 控制轧制的类型
•控制轧制方式示意图
•(a) 奥氏体再结晶区控轧;(b) 奥氏体未再结晶区控轧;(c) (+)两相区控 轧
Controlled
PPT文档演模板
材料加工组织性能控制新
•低温轧制的 优点:细化 铁素体晶粒。
PPT文档演模板
•图3-l 各种轧制程序的模式图 • CR-—控制轧制;AcC一控制冷却
材料加工组织性能控制新
3.1.2 铁素体晶粒尺寸的控制
材料加工组织性能控制XXXX(第十章)
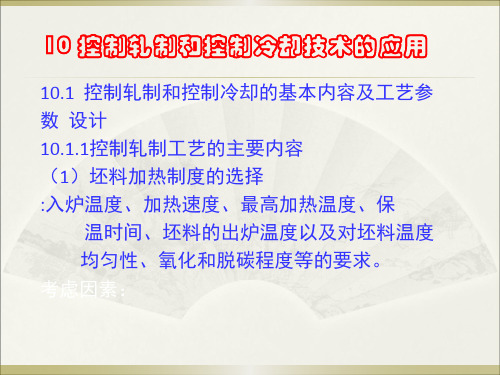
终轧温度:
(2) 双机架中厚板轧机的控制轧制工艺 形式:二辊—四辊式,三辊—四辊式、四辊—四 辊式
举例:2800二辊—四辊式:
控制轧制工艺: (a)粗轧终了温度:
道次压下率: 总压下率: (b)四辊精轧机分成两个阶段:部分再结晶的 上限范围轧制,道次压下率:
轧制温度: 未再结晶区轧制,道次压下率:
10 控制轧制和控制冷却技术的应用
10.1 控制轧制和控制冷却的基本内容及工艺参 数 设计 10.1.1控制轧制工艺的主要内容 (1)坯料加热制度的选择 :入炉温度、加热速度、最高加热温度、保
温时间、坯料的出炉温度以及对坯料温度 均匀性、氧化和脱碳程度等的要求。 考虑因素:
(2)选择和设计控制轧制工艺的类型
(4)控轧控冷钢化学成分的调整
碳: 锰 :细化晶粒、提高强度、增加韧性、降低相变 温度Ar3 ,作用:1)扩大了加工温度范围 ;2) 使铁素体晶粒长大机会减少。 一般控制在1.3-1.5%之间 。 硫: 磷 :不大于0.02% 。
10.1.2 控制冷却工艺设计(已讲过,略) 10.2控制轧制和控制冷却技术在钢板生产中的应用 10.2.1 热轧带钢的控制轧制和控制冷却 ➢ 5个步骤: 1)加热中,微合金化元素碳氮化合物的溶解。 2)再结晶临界温度以下施以大的变形。 3) 微合金化元素碳氮化合物的变形诱导析出延缓再结 晶。 4)未再结晶并强烈变形的奥氏体发生相变。 5)分配冷却剂量来控制冷却和调整所需要的卷取温度。
图10-16 终轧温度和卷取温度对双相钢性能的影响
2) 卷取温度对双相钢性能的影响
图10-16 终轧温度和卷取温度对双相钢性能的影响
10.3 连铸连轧理论与应用 10.3.1 五种典型工艺图
材料加工组织性能控制(第十章)XX9
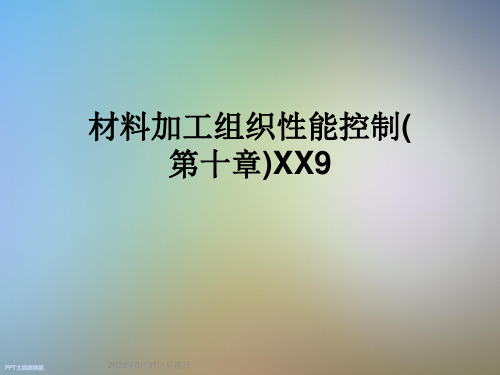
•表2 20g锅炉钢板控制轧制和控制冷却工艺
•表10-3 16Mng锅炉钢板控制轧制和控制冷却工艺(S含量<0.025% )
•
(2)压力容器用中厚钢板的控制轧制和控 制冷却
碳素钢容器板和低合金容器板:出炉温度 ≥1150℃;高合金钢容器板的板坯出炉温度为 1200℃。
•
10.1.3 热轧双相钢的控制轧制和控制冷却 10.1.3.1 双相钢的组织、性能特点、生产方法
•
工艺2: “热送轧制”工艺(HotChargeRolling, 简称HCR)。 特点: 工艺3: 特点:
•
工艺4: 特点: 工艺5:“冷装炉”轧制工艺(即ColdChargeRolling,简称CCR)。
•
连铸连轧组织转变特点: (1)铸坯冷却强度大,晶粒细、均匀,板坯
的微观偏析分布更均匀。 (2)原始晶粒尺寸结构与传统有所不同
•
(2) 控轧控冷工艺参数对双相钢组织性能的影响 1)终轧温度的影响
•图10-16 终轧温度和卷取温度对双相钢性能的影响
•
2) 卷取温度对双相钢性能的影响
•图10-16 终轧温度和卷取温度对双相钢性能的影响
•
10.14. 连铸连轧理论与应用 10.1.4.1 五种典型工艺图
•工艺1:连铸坯直送轧制工艺(Continuous •castin-Hot direct rolling,即CC—HDR)。 •特点:
传统冷装:γ→α→γ重结晶过程,细化的奥氏 体组织。 直轧工艺:相对粗大的原始奥氏体晶粒。 混晶组织:
•
(3)合金元素的溶解量和作用效果不同 (4)薄板坯连铸连轧轧制过程的热脆 (5)必要的总变形量及变形规程的安排 (总变形量、奥氏体细化变形量和奥氏体强 化变形量)。
精品 课后习题及参考答案-材料性能学课后习题与解答

材料性能学课后习题与解答绪论1、简答题什么是材料的性能?包括哪些方面?[提示] 材料的性能定量地反映了材料在给定外界条件下的行为;解:材料的性能是指材料在给定外界条件下所表现出的可定量测量的行为表现。
包括○1力学性能(拉、压、、扭、弯、硬、磨、韧、疲)○2物理性能(热、光、电、磁)○3化学性能(老化、腐蚀)。
第一章单向静载下力学性能1、名词解释:弹性变形塑性变形弹性极限弹性比功包申格效应弹性模量滞弹性内耗韧性超塑性韧窝解:弹性变形:材料受载后产生变形,卸载后这部分变形消逝,材料恢复到原来的状态的性质。
塑性变形:微观结构的相邻部分产生永久性位移,并不引起材料破裂的现象。
弹性极限:弹性变形过度到弹-塑性变形(屈服变形)时的应力。
弹性比功:弹性变形过程中吸收变形功的能力。
包申格效应:材料预先加载产生少量塑性变形,卸载后再同向加载,规定残余应力(弹性极限或屈服强度)增加;反向加载,规定残余应力降低的现象。
弹性模量:工程上被称为材料的刚度,表征材料对弹性变形的抗力。
实质是产生100%弹性变形所需的应力。
滞弹性:快速加载或卸载后,材料随时间的延长而产生的附加弹性应变的性能。
内耗:加载时材料吸收的变形功大于卸载是材料释放的变形功,即有部分变形功倍材料吸收,这部分被吸收的功称为材料的内耗。
韧性:材料断裂前吸收塑性变形功和断裂功的能力。
超塑性:在一定条件下,呈现非常大的伸长率(约1000%)而不发生缩颈和断裂的现象。
韧窝:微孔聚集形断裂后的微观断口。
2、简答(1) 材料的弹性模量有那些影响因素?为什么说它是结构不敏感指标?解:○1键合方式和原子结构,共价键、金属键、离子键E高,分子键E低原子半径大,E小,反之亦然。
○2晶体结构,单晶材料在弹性模量在不同取向上呈各向异性,沿密排面E大,多晶材料为各晶粒的统计平均值;非晶材料各向E同性。
○3化学成分,○4微观组织○5温度,温度升高,E下降○6加载条件、负载时间。
对金属、陶瓷类材料的E没有影响。
材料的加工性能

材料的加工性能材料的加工性能是指材料在加工过程中所表现出的性能,包括可加工性、热加工性、冷加工性等多个方面。
材料的加工性能直接影响着加工工艺的选择和加工质量的稳定性,因此对于材料的加工性能的研究和评价具有重要意义。
首先,材料的可加工性是指材料在加工过程中的易加工性。
可加工性好的材料在加工过程中不易产生裂纹、变形和损伤,能够保持加工表面的平整度和精度。
而可加工性差的材料则容易产生加工难度,需要采取更多的加工措施和技术来保证加工质量。
因此,对于可加工性差的材料,需要在材料选择和加工工艺上进行更多的考量和优化。
其次,热加工性和冷加工性是材料加工性能的重要方面。
热加工性是指材料在高温下的加工性能,包括热塑性和热加工硬化性。
热塑性好的材料在高温下具有良好的塑性和延展性,适合进行热加工成形,如锻造、挤压、轧制等。
而热加工硬化性好的材料则能够在热加工过程中保持较高的硬度和强度,不易软化和变形。
冷加工性是指材料在常温下的加工性能,包括冷塑性和冷加工硬化性。
冷塑性好的材料在常温下具有良好的塑性和延展性,适合进行冷加工成形,如冷拔、冷轧、冲压等。
冷加工硬化性好的材料则能够在冷加工过程中保持较高的硬度和强度,不易软化和断裂。
此外,材料的加工性能还包括耐磨性、耐热性、耐蚀性等多个方面。
耐磨性好的材料在加工过程中不易产生磨损和磨损,能够保持加工刀具和设备的使用寿命。
耐热性好的材料在高温下不易软化和氧化,能够保持稳定的加工性能和机械性能。
耐蚀性好的材料在腐蚀介质中不易发生化学反应和腐蚀,能够保持加工表面的光洁度和精度。
综上所述,材料的加工性能是影响加工质量和加工效率的重要因素。
对于不同类型的材料,需要根据其具体的加工性能特点来选择合适的加工工艺和加工方法,以保证加工质量和经济效益的最大化。
因此,对于材料的加工性能的研究和评价具有重要的理论和实际意义。
材料加工组织性能控制第九章
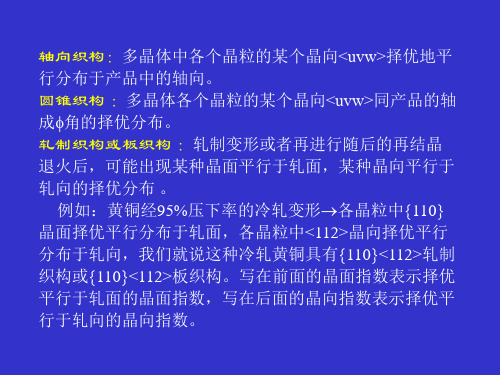
(3)定向成核一选择成长联合理论 再结晶退火时可能发生三种基本的织构变:
再结晶退火后保持了形变织构;再结晶时形变织 构全部或部分地被其它的一个或几个再结晶织构 组分所代替,这种代替可能出现在再结晶的不同 阶段,而且再结晶早期阶段上出现的再结晶织 构,在后期常常又可被新的织构代替;再结晶时 形变织构全部或部分地被无序取向的新晶粒代 替。
08Al:钢中析出铝的氮化物A1N, {111}组分
过饱和固溶体强烈的分解温度高于 的变形晶
600℃。
深
粒比{001} 组分的变
冲
形晶粒容
钢
易形成再
板
结晶核心,
08F:析出的基本上是铁的碳化物 (渗碳体),过饱和固溶体强烈的分 解温度在500℃左右。
容易发生 过饱和固 溶体分解。
08Al钢板: 控制工艺:再结晶退火时的加热速度要慢一些, 还未加热到A1N强烈析出的温度时,{111}取向的 再结晶核心在有利的条件下已顺利地形成,使这种 核心在数量上占据优势。 注意:加热速度不要过高,否则出现加热到 600—700℃时还未到{111}取向再结晶核心的形成 温度,就开始出现A1N的析出,析出的弥散氮化物 对{111}组分的晶粒中再结晶形核的阻碍作用比 {001}组分中的阻碍作用大。于是形成的再结晶核 心中,占优势的将可能是{001}取向的晶核。
08F钢板: 提高{111}再结晶织构的织构度,应提高再结 晶退火时的加热速度,“跑过”碳化物强烈析出 的 温度(500)以防止析出的弥散碳化物阻碍{111}取 向的再结晶核心的形成。否则,碳化物在{111} 取向晶粒的区域中强烈析出,就严重地阻碍了它 们的再结晶核心的形成,而在{001)取向晶粒的区 域中,阻碍作用较微弱,因而有利于{001}取向 的再结晶核心的形成。有利于形成{001}取向的 再结晶织构。
组织设计-材料加工组织性能控制(PPT98页)

条件:c>r
图3-3 Q235钢变形条件对真应力-真应变曲线的影响 (a)变形温度的影响,变形速度 0.1s1;(b)变形速度的 影响,变形温度T=1000C
(2)控制轧制温度 奥氏体区轧制:要求最后几道次的轧制温度要 低。一般要求终轧温度尽可能接近奥氏体开始转 变温度,起到相似于正火的作用。 低碳结构钢的终轧温度: 含Nb钢的终轧温度:
采用(+)两相区轧制:要根据对钢材性能的不同 要求而确定其终轧温度。
(3) 控制变形程度 :
奥氏体区轧制 原则:1)连续轧制,不要间歇,尤 其在的高温侧(动态再结晶区),使晶粒来不及长 大; 2)道次变形量应大于临界变形量,使全部晶 粒能进行再结晶。混晶现象:
体晶粒微细化。 (2)使中间温度区(如900C 以上)的轧制道次程
序最佳化,通过反复再结晶使奥氏体晶粒微细 化。
(3)加大奥氏体未再结晶区的累积压下量,增加 奥氏体每单位体积的晶粒界面积和变形带面积。
控制轧制机理:
(1)Hall-Petch关系式:
y
0
k
y
d
1 2
(1)
(2)断口转变温度FATT(Fracture Appearance Transition Temperature) :
机械性能
b
0.2
5
(N/mm2) (N/mm2)
(%)
HRC
(%)
(J/
cm2)
加工方式
高温控制轧制 10001030 785835 1214 3846 6075
31
工艺
常规工艺
850850 600640
金属材料组织和性能的控制

– δ-Fe(体心立方晶格)→ γ-Fe(面心立方晶格) → α- Fe(体心立方晶格)
• 以不同晶体结构存在的同一种金属的晶体称为该金属的同素 异晶体。上式中的 δ-Fe、 γ -Fe 、 α - Fe 均是纯铁的同素异 晶体。
• 金属的同素异构转变与液态金属的结晶过程相似,故称为二 次结晶或重结晶。
从本质上讲,金属从一种原子排列状态(晶态或非晶态)到另一种原子规 则排列状态(晶态)的转变叫金属的结晶。
一、纯金属结晶的条件
• 通过实验,测得液体金属在结晶时的温度-时间曲线称为冷 却曲线。绝大多数纯金属(如铜、铝、银等)的冷却曲线如 下图所示。
纯金属(纯铜)的冷却曲线
液态金属和固态金属的自由 能-温度关系曲线
• 晶体长大速度G(单位时间
晶体长大的长度, m/s)越快,
则晶粒越粗。
成核速率、长大速度与过冷度的关系
• 随着过冷度的增加, 成核速率和长大 速度均会增大。当过冷度超过一定 值后,成核速率和长大速度都会下 降。这是由于液体金属结晶时成核 和长大,均需原子扩散才能进行。 当温度太低时,原子扩散能力减弱, 因而成核速率和长大速度都降低。
• 细晶强化:工程上使晶粒细化, 提高金属机械性能的方法。 • 细化铸态金属晶粒有以下措施 :
– 增大金属的过冷度 – 变质处理 – 振动 – 电磁搅拌
成核速率、长大速度与过冷度的关系
• 增大金属的过冷度
• 一定体积的液态金属中,若 成核速率N(单位时间单位 体积形成的晶核数,个 /m3·s)越大, 则结晶后的晶 粒越多, 晶粒就越细小;
• 晶粒大小可用晶粒度来表示,晶粒度号越大晶粒越细。
晶粒度表
晶粒度
1
2
3
材料加工组织性能控制(第五、六章)XXXX9

图5-15 在普碳钢和含铌钢中,单道次 的变形量和变形温度对再结晶奥氏体 晶粒尺寸的影响
总结:
铌在奥氏体中存在形式:1)加热时尚未溶到奥氏 体中的Nb(C、N);2)固溶到奥氏中的铌;3)加热 时溶解、轧制过程中又由奥氏体中重新析出的 Nb(C、N)。轧制的不同阶段,其阻止奥氏体再结 晶是不同的。
图5-2 晶粒尺寸与加热温度的关系
5.2 控制轧制过程中微量元素碳氮化合物 的析出 5.2.1 各阶段中Nb(C、N)的析出状态 (1)出炉前: 加热到1200C,均热2h:90%以上铌都 固溶到奥氏体基体中,有极少数粗大 Nb(C、N)没有固溶到奥氏体中。 1260C :保温30min,Nb(C、N)全部溶 解。
(4) 奥氏体向铁素体转变过程中和在铁素体内 Nb(C、N)的析出状态 1)碳氮化物在和中的溶解度不同相变后,产 生快速析出。 相间析出(相间沉淀): 冷却速度大、析出温度低相间沉淀排间距小 析出质点也小。 析出时间长质点长大。 2)相变后内剩余的固溶铌继续析出,质点大小 决定于冷却速度。 3)冷却到室温,1015%左右的铌未从铁素体中 析出。
r:厚向异性系数
r w t
r (r0 2r45 r90 ) / 4
r:厚向异性系数r在板面上随方向的变化,决定凸 耳的形成程度,不影响板料成形性能。
r r0 r90 2r45 2
图6.4冷轧压下率对铝镇静钢薄板 织构和各向异性值的影响
r-平面各向异性;rm-平均法 向各向异性
图6.5冷轧压下率对软钢薄板法向 各向异性(rm)的影响(高温卷取)
图6.11.1 IF钢再结晶退火后的硬度变化规律 a- 加热温度与硬度(保温2h);b-保温时间与硬度
T1-Ti-IF钢;N1-Ti+Nb-IF钢
材料加工组织性能控制(第四章)XXXX9
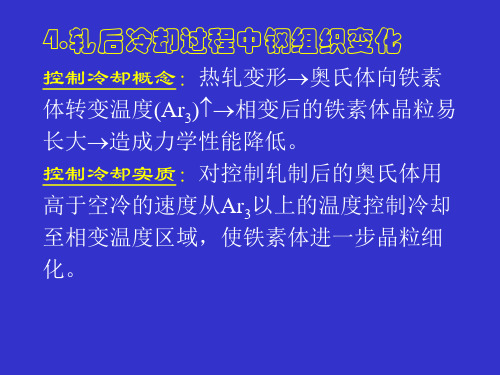
控制冷却设备:必须能均匀控制长、宽、 厚方向钢板的性能。 冷却方式:同时冷却型、通过冷却型。
图2-9 轧制后冷却对抗拉强度、断面转 变温度的影响
4.1 CCT曲线及转变产物 目的: 等温转变曲线(TTT曲线):反映过冷奥氏体等温 转变的规律; 连续冷却转变曲线(CCT曲线):在连续冷却转变 过程中,钢中的奥氏体在不断降温的条件下发生 转变的。 CCT曲线的测量: 膨胀法测CCT曲线原理:各相具有不同的比容: 马氏体>体素体>珠光体>奥氏体>碳化物 。
图4-6 控制轧制CCT曲线在不同冷却 速度时的组织形态 实线:Nb钢;虚线:Si-Mn钢
三次冷却(空冷):相变后至室温范围内的冷 却。 目的: 对低碳钢:没有什么影响。 对含Nb钢:发生碳氮化物析出。 对高碳钢或高碳合金钢:
冷却方法:
1)喷水冷却(喷流冷却):水从压力喷嘴中以一定 压力喷出ห้องสมุดไป่ตู้流,而水流为连续的,没有间断现 象,但是呈紊流状态。 优点:穿透性好,在水膜比较厚的时候采用。 应用:中厚钢板轧后冷却和钢板淬火时;在型钢 冷却中进行局部冷却。 缺点:水的喷溅利害,水的利用率较差。
4.轧后冷却过程中钢组织变化
控制冷却概念:热轧变形奥氏体向铁素 体转变温度(Ar3)相变后的铁素体晶粒易 长大造成力学性能降低。 控制冷却实质:对控制轧制后的奥氏体用 高于空冷的速度从Ar3以上的温度控制冷却 至相变温度区域,使铁素体进一步晶粒细 化。
工艺:从Ar3以上的温度开始,在相变终了 温度附近(550500℃)结束,然后进行空 冷。 组织:细晶粒铁素体和微细弥散型贝氏体 的混合组织。 对强度及韧性的影响:
图4-17 热轧的终轧温度 同抗拉强度及夏比断口
转折温度的关系
4.4.3 压下率的影响
- 1、下载文档前请自行甄别文档内容的完整性,平台不提供额外的编辑、内容补充、找答案等附加服务。
- 2、"仅部分预览"的文档,不可在线预览部分如存在完整性等问题,可反馈申请退款(可完整预览的文档不适用该条件!)。
- 3、如文档侵犯您的权益,请联系客服反馈,我们会尽快为您处理(人工客服工作时间:9:00-18:30)。
(2) 双机架中厚板轧机的控制轧制工艺 形式:二辊—四辊式,三辊—四辊式、四辊—四 辊式 1) 二辊—四辊式中厚钢板轧机的控制轧制工艺 举例:2800二辊—四辊式:
控制轧制工艺: (a)粗轧终了温度:
道次压下率: 总压下率: (b)四辊精轧机分成两个阶段:部分再结晶的 上限范围轧制,道次压下率:
表10-2 20g锅炉钢板控制轧制和控制冷却工艺 表10-3 16Mng锅炉钢板控制轧制和控制冷却工艺(S含量<0.025%)
(2)压力容器用中厚钢板的控制轧制和控
制冷却
碳素钢容器板和低合金容器板:出炉温度 ≥1150℃;高合金钢容器板的板坯出炉温度为 1200℃。
10.1.3 热轧双相钢的控制轧制和控制冷却 10.1.3.1 双相钢的组织、性能特点、生产方法
(2)特别高的屈服强度的钢(最小屈服强度 值:700MPa,且冷成型性能应非常好 ) 成分:0.08%C,l.3%Mn,0.1%Mo,0.05%Nb、 0.18%Ti和0.002%B 工艺: (1)高温加热;(2)温度较低的粗轧过 程中,碳化钛和碳化铌的变形诱导析出;(3) 终轧温度为850C左右,析出其他的合金碳化 物;(4)高的冷却速度,卷取温度必须显著低 于贝氏体开始温度。 性能:
较低(表 面质量较
差) 小
90-150 平行板型 中,最大5.0 粗轧1-2机架+卷 取精轧4-6机架 与传统工艺相当 与传统工艺相当
中
200-300 平行板型 低,最大2.5 粗轧1-3机架 ,精轧7机架
多 高
大
1)不同工艺与产品厚度关系 2)产品规格的市场需求 3)设备与产品花色的关系 (2)压缩比 (3) 连铸坯的加热 1)隧道式辊底加热炉 加热炉炉子长约150~200m,有缓冲功能。炉内辊 道速度可分段控制,输入端辊道速度最低,以适 应连铸速度较低的特点;中部和末端速度较高, 有利于钢坯快速通过;出炉段辊道速度则与F1速 度相匹配。
(2)单流连铸机与粗精机组的薄板坯连铸连轧 生产线配置
连铸坯厚度大多数为70-90mm,设计年产量多在150 万t,产品最小厚度0.8-1.2mm。
(3) 双流连铸机与粗、精轧机组的薄板坯连铸连 轧生产线配置
设备具有强大的轧制压力,允许采用厚度较大的 铸坯,或者可以用于轧制难变形产品,如铁素体 温度区轧制等产生高轧制力的产品。由于生产线 采用双流连铸机配置,年产量可高达250万t。
大压下量、高刚度轧机是薄板坯连铸连轧工艺的 特点之一。
(7)半无头轧制 半无头轧制工艺:将几块中间坯焊接在一起,然 后通过精轧机进行连续轧制。在进入卷取机之 前,用一台高速飞剪将其分切到要求的卷重。
作用: 1)有利于生产超薄带钢和宽而薄的带钢,拓宽产 品大纲; 2)稳定轧制条件以利于产品质量; 3)消除了与穿带和甩尾的麻烦; 4)显著提高了轧机的作业率和金属收得率。
(8)铁素体轧制 传统热轧工艺:精轧温度在Ar3以上 ,不可进入 两相区轧制,否则,带来如下问题:1)带材的 跑偏和板形缺陷;2)。引起带钢机械性能不均 匀和最终产品的厚度波动 。 铁素体轧制优点:1)轧制力低;2)减少了氧化 铁皮的产生和工作辊的磨损,提高了带钢表面质 量;3)降低了输出辊道上冷却水的消耗。
工艺2: “热送轧制”工艺(HotChargeRolling, 简称HCR)。 特点: 工艺3: 特点:
工艺4: 特点: 工艺5:“冷装炉”轧制工艺(即ColdChargeRolling,简称CCR)。
连铸连轧组织转变特点: (1)铸坯冷却强度大,晶粒细、均匀,板坯
的微观偏析分布更均匀。 (2)原始晶粒尺寸结构与传统有所不同
(2) 控轧控冷工艺参数对双相钢组织性能的影响 1)终轧温度的影响
图10-16 终轧影响
图10-16 终轧温度和卷取温度对双相钢性能的影响
10.14. 连铸连轧理论与应用 10.1.4.1 五种典型工艺图
工艺1:连铸坯直送轧制工艺(Continuous castin-Hot direct rolling,即CC—HDR)。 特点:
图10-1 热轧带钢机组中的控制轧制参数和作用
图10-2 热轧带钢机组生产铌或钛合金钢时,各道次总动态再
结晶临界变形率K和总变形率ges的比较 a一相同微合金化元素量的影响;b-典型的微合金化元素含量
控制轧制应用实例:
(1)生产用车辆的车架结构 成分:0.08%C、1.0%Mn、0.12%Ti。 工艺:(1)加热过程,氮化钛溶解度极小保 持析出状态保证钢的耐时效性。(2)终轧温 度在约860C;(3)冷却辊道进行快速冷却; (4)过冷至600C的卷取温度。 性能:
10.1.4.3 薄板坯连铸连工艺与设备参数分析 (1)薄板坯厚度的选择
表10.2 薄、中、厚板坯3种连铸工艺的特性
连铸工 薄板坯连
艺
铸
中板坯连铸
厚板坯连铸
铸坯厚 度/mm 结晶器 类型 铸速 /mmin-1 轧制线 主要设
备 品种 质量
投资
40-70 漏斗型 高,最大
6.0 精轧(4-6
机架)
以低碳钢 为主
10.1.4.5 薄板坯连铸连轧生产线的配置 典型的薄板坯连铸连轧生产线工艺流程: 钢水中间包结晶器二冷区飞剪机 均热炉高压水除鳞(立辊轧边机) (粗轧机组)保温炉高压水除鳞 精轧机组近距离卷取机层流冷却远 距离卷取机打包入库。
(1)只有精轧机的薄板坯连铸连轧生产线
两条生产线的区别: 这种配置线铸坯厚度约为50-70mm,设计年产量多 在150万t,产品最小厚度1.0mm。
10 控制轧制和控制冷却技术的应 用
10.1 控制轧制和控制冷却技术在钢板生产 中的应用 10.1.1 热轧带钢的控制轧制和控制冷却 5个步骤: 1) 加热中,微合金化元素碳氮化合物的溶 2) 解。 2)再结晶临界温度以下施以大的变形。
3) 微合金化元素碳氮化合物的变形诱导析 出延缓再结晶。 4)未再结晶并强烈变形的奥氏体发生相变。 5)分配冷却剂量来控制冷却和调整所 需要的卷取温度。
双相钢: 特点:
性能上: (1)很低的屈强比; (2)很大的冷加工硬化,特别是在小变形量时; (3)很高的断裂延伸率,特别是均匀延伸率。 工艺上: (1)成型性;(2)焊接性;(3)耐腐蚀性。
生产方法: 1)热处理双相钢; 2)热轧双相钢。 10.1.3.2 热轧双相钢的控制轧制和控制 冷却 (1) 钢的成分对双相钢性能的影响 碳: 对强度、屈强比及塑性的影响。 硅:具有排碳作用。 锰:提高淬透性,导致屈强比降低 。
图10-15 母材及焊缝R的曲线 比较
10.1.2.2 典型专用钢板所采用的控制轧制和控制 冷却工艺 (1)锅炉用中厚钢板的控制轧制和控制冷却工艺 20g,16Mng: 特点:1)加热温度不应过高。总变形量>75%时, 加热温度对原始奥氏体粗化影响铁素体晶粒的作用 减弱;2)钢中S含量对常温冲击值有明显影响。
图10-5 卷取温度对8mm厚热轧 钛合金带钢力学性能的影响
图10-6 卷取温度对贝氏体或铁 素体-珠光体型热轧宽带钢屈服
强度的影响
1-贝氏体钢;2- 铁素体-珠光体 钢;3-开始形成贝氏体( Bs)
10.1.2 中厚板控制轧制及控制冷却 10.1.2.1 不同类型中厚板轧机控制轧制工艺 (1) 四辊单机架中厚板轧机 控轧工艺:高温再结晶型和未再结晶型两阶段。 再结晶阶段: 未再结晶阶段: 终轧温度:
(4)步进式加热炉布置的薄板坯连铸连轧生产 线
缓冲时间的大小取决于步进炉内钢坯的存放量, 一般设计上可以考虑缓冲时间取1.5-2.0h。
(5)单流单机座炉卷轧机(TSP)
适合多品种、低投资为目的的配置方式。采用单 机座炉卷轧机,铸坯厚度为50-70mm,最小产品厚 度1.5mm,设计年产量为50万t。最大缺点:带钢 表面粗糙度不好 。
(2) 带钢厚度和板形精度
(6)无头连铸连轧(ECR)工艺生产线的理想配置
10.1.4.6 CSP热带性能与精度 (1) 性能
性能差异的原因: 1)铸坯在连铸机内的冷却过程钢水的过冷度大。 2)电磁搅拌和液芯压下技术的采用。 3)在薄板坯连铸连轧生产线上,轧制过程温差造 成的带钢性能差基本上被消除。 4)连轧机组许用轧制力明显的大于常规热带连轧 机组,因而采用的道次变形量也明显地大于常规 轧机,因而成品带钢的组织就更均匀,晶粒更细 化。
三种控轧工艺比较:
①高温奥氏体再结晶型控轧与轧后快速冷却配合 工艺; ②高温奥氏体再结晶型与奥氏体未再结晶型(低 温终轧)工艺; ③高温奥氏体再结晶型与高温多道次小变形(不 发生再结晶)工艺与轧后控制冷却工艺相配合。 性能:
图10-14 母材的裂纹顶端张开 位移COD(R)与裂纹尺寸增长 量a关系
均热段。
(4) 轧件宽度的在线调整 在线调宽自动控制AWC(Automatic Width Control);液压宽度自动控制
HAWC(Hydraulic Automatic WidthControl) 立式轧机。 (5)无相变加热对产品组织的影响 影响:1);2);3)对合金钢的影响。
(6)轧制线轧机数量与轧制负荷特点 常规热带工艺下精轧机组的压下率:Fl=40%~ 50%,F2=40%~45%,F3=35%~40%,F4=30 %~40%,F5=25%~35%,F6=20%~28%, F7=10%~15%。 连铸连轧工艺精轧机组的压下率:Fl=40%~50 %,F2=55%,F3=65%,F4=50%。
图10-16 薄板坯连铸连轧产品与传统热轧产品的性能比较 1-20个普通带卷的平均值;2-20个CSP带卷的平均值
2)感应加热 ISP技术(Inline Strip Production)是在加热炉中采用 排列在辊道上的一组感应线圈进行感应加热。在 长为18~20m的炉中,大约每米设置一个感应线 圈,改变线圈中电流的强度可以控制加热速度, 而改变电流的频率,则可以调节对钢坯的加热深 度。最大加热效率达到70%,带坯感应加热温升 可达到1050~l100C,有非常灵活的控制加热和