材料加工组织性能控制XXXX(第十章)
材料加工组织性能控制第九章
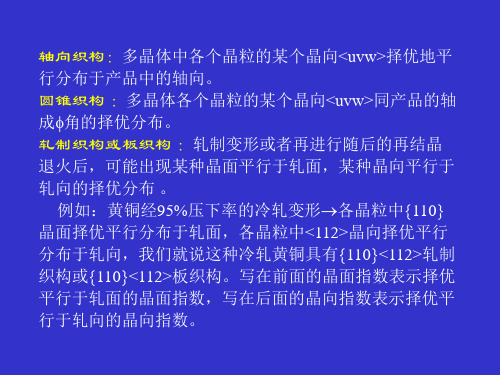
(3)定向成核一选择成长联合理论 再结晶退火时可能发生三种基本的织构变:
再结晶退火后保持了形变织构;再结晶时形变织 构全部或部分地被其它的一个或几个再结晶织构 组分所代替,这种代替可能出现在再结晶的不同 阶段,而且再结晶早期阶段上出现的再结晶织 构,在后期常常又可被新的织构代替;再结晶时 形变织构全部或部分地被无序取向的新晶粒代 替。
08Al:钢中析出铝的氮化物A1N, {111}组分
过饱和固溶体强烈的分解温度高于 的变形晶
600℃。
深
粒比{001} 组分的变
冲
形晶粒容
钢
易形成再
板
结晶核心,
08F:析出的基本上是铁的碳化物 (渗碳体),过饱和固溶体强烈的分 解温度在500℃左右。
容易发生 过饱和固 溶体分解。
08Al钢板: 控制工艺:再结晶退火时的加热速度要慢一些, 还未加热到A1N强烈析出的温度时,{111}取向的 再结晶核心在有利的条件下已顺利地形成,使这种 核心在数量上占据优势。 注意:加热速度不要过高,否则出现加热到 600—700℃时还未到{111}取向再结晶核心的形成 温度,就开始出现A1N的析出,析出的弥散氮化物 对{111}组分的晶粒中再结晶形核的阻碍作用比 {001}组分中的阻碍作用大。于是形成的再结晶核 心中,占优势的将可能是{001}取向的晶核。
08F钢板: 提高{111}再结晶织构的织构度,应提高再结 晶退火时的加热速度,“跑过”碳化物强烈析出 的 温度(500)以防止析出的弥散碳化物阻碍{111}取 向的再结晶核心的形成。否则,碳化物在{111} 取向晶粒的区域中强烈析出,就严重地阻碍了它 们的再结晶核心的形成,而在{001)取向晶粒的区 域中,阻碍作用较微弱,因而有利于{001}取向 的再结晶核心的形成。有利于形成{001}取向的 再结晶织构。
钢材组织性能的控制(最全)
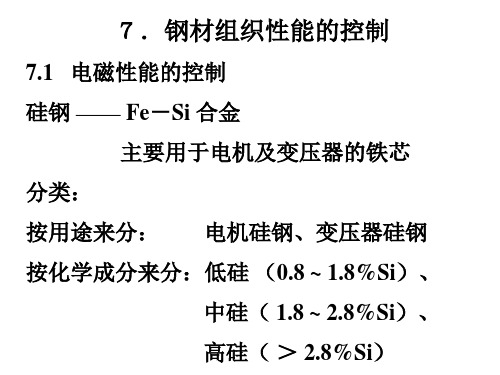
检验→入库
1.加热
提高加热温度、延长加热时间对磁性有利
① 使有利夹杂充分固溶 ② 铁素体晶粒尺寸变大 ③ 使有害夹杂聚集长大,减小其有害性 ④ 脱 C↑ ⑤ 减小偏析现象 板坯的加热温度控制在 1300℃左右,最高 可达 1350℃。
2.热轧 ① 终轧温度 T终℃> 850℃ ε↑,等轴晶深度↑ 快
T卷℃≤620℃, 若卷取温度高,就会导
致AlN析出,不利于形成饼形晶粒。
② 冷轧工艺控制 总压下率在 30%~65% ,冲压性能最好
ε↑↑ , d↓↓ →
电机用硅钢:要求磁各向异性越小越好,纵横方向的 B25 差别小于10% 变压器用硅钢:要求轧制方向为[001]晶向,B↑ 采用有取向的硅钢片 (100)[001] 或 (110)[001]
4.磁致伸缩小
5.表面质量好,厚度均匀
表面平整,填充系数高
厚度不均,噪音增大,电机振动增大
二.影响电磁性能的主要因素 1.晶粒大小 d↑ → B↑、P↓ 磁性好 如图示:d ↓ ,P1 ↑
电机 变压器 厚 0.5 mm 厚 0.35mm 1.0 ~ 2.5%Si 3.0 ~ 4.5%Si
冷轧硅钢片:≤ 3.5%Si 无取向硅钢片 多用于电机
取向硅钢片
2.8 ~ 3.5%Si
单取向硅钢片:高斯织构 (110)[001]
变压器
厚0.35mm
双取向硅钢片:立方织构 (001)[100] 仪表工业 厚0.025 ~ 0.1mm
——ζs/ζb
d↑, ζs ↓—— ζs/ζb ↓,冲压性能↑
d↑↑, ζb ↓—— 杂质因晶界减少而集中,
脆性↑,冲压制品表面易 出现桔皮状
一般,适宜的晶粒尺寸为 6~8 级
《材料加工工艺和设备》课程教学大纲

课程讲 授、作 业、讨论
课程讲 授、作 业、讨论
课程讲 授、作 业、讨论
教学内容 学时 教学方式 作业及要求
基本要求
考查方式
材料加工工艺
与设备基础
2
课堂讲授
掌握材料加工工艺 和设备特点;与材 料 加 工 原 理 的 关 课堂提问 系;与过程控制的关 系
材料加工工艺 设计方法
《材料加工工艺和设备》课程教学大纲
课程基本信息(Course Information)
课程代码 (Course Code)
MT340
*学时 (Credit Hours)
32
*学分 (Credits)
2
*课程名称 (Course Name)
材料加工工艺和设备 Materials manufacture processing and apparatus
课堂提问讨 工艺与性能的关系 以 及 工 艺 优 化 方论和作业 法。
齿轮钢的表面
处Байду номын сангаас工艺(或
其它表面改 性、微纳器件
2
制备的问题及
工艺设计)
课堂讲授
材料加工过
程控制基础
6
课堂讲授
过程控制中 的传感技术
2 课堂讲授
了解齿轮钢的 碳、渗氮和碳氮 渗工艺的设计
共渗课 论作堂业提
问
讨
掌握材料加工过程
控制的原理、组成、课 堂 提 问 讨
*课程目标与毕业要 求对应关系
(relationship between learning
outcomes and graduation
requirements)
毕业要求
通用版治国理政第四卷一以贯之坚持人民至上专题专题PPT课件
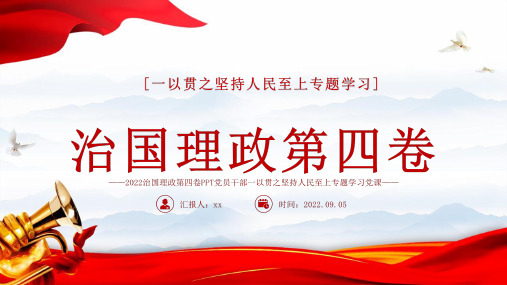
特殊情况下必须随同升降机时,应采取可靠的安全措施,并经有关负责人批准。 本方案的编制及水土保持措施的有效实施,在控制因xxxx建设造成的新增水土流失的同时,减轻xxxx区原有的水土流失,使xxxx区水土流失达到允许范围,改善区域环境,可为社会经济的可持续发展提供保障。
不得在五级和五级以上时进行大型、中型工件吊装。 边长1200~2400mm 允许偏差为:+2,-2
总 书 记 强 调
桩式墩模板用两块半圆形模板拼形而成,模板间用5mm橡胶嵌缝,φmm螺栓紧合。 ,再排入主
硬化地表区域主要为道路硬化和其他硬化,根据xxxx平面布局,硬化占地0.6267m2,小区内行人道路有3条。 ③模板分成两个半圆形加工,用Φ螺栓固定,5mm厚橡胶嵌缝止漏;
②、嵌墙暗装配电箱的箱体应与墙面齐平。 ② 工程措施的稳定性、完好程度和运行情况监测;
2.3.3 干挂石材安装程序 500/km2.a进行计算。
c.钢连接件表面镀锌层是否完好。 本工程的水土保持监测必须由具有监测资质的单位承担,从事监测工作的技术人员也应具有水利部培训合格颁发的上岗证书。
,应 (5)xxxx区平均海拔为266~269m,不做系数调整。
6.5.3绑扎下层钢筋:按弹好的间距线,摆放下层钢筋,先放置短向钢筋,再放置长向钢筋,下层钢筋弯钩朝上,绑扎下层钢筋,然后由水电专业人员进行预埋件、电线、预留孔等配套施工。 实验中试件所要达到的性能指标均为国家规范规定及业主指定的级别,且实验将在我司及业主与监理共同监督下
r、玻璃隔音降噪性能:八音段声音减低系数(SRI)应满足以下要求: ,并应及时编制开发建设xxxx水土
用油漆在立柱或剪力墙同一高度位置处作高度标记。 (3)水土流失若得不到治理,大量的地表径流携带泥沙可能随污水管道汇流后,进入xxxx区污水处理设施,使xxxx区污水处理设施处理能力下降。
材控专业指导
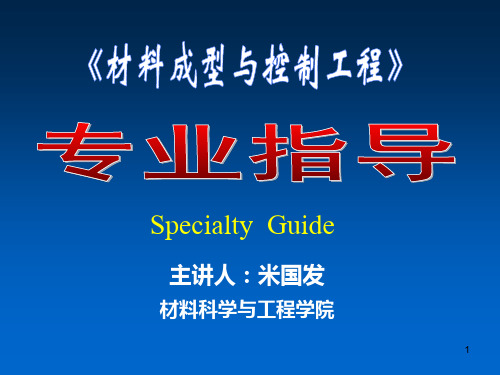
化类型的专业人才培养模式。
分别隶属“材料学院”和“机械学院”
41
材料科学与工程学院
四、我校材控专业的历史及现状:
1、专业的历史及学生就业情况:
我校于1999年成立材料成型及控制工程专业,已招收9届学生, 毕业五届学生,培养出近500名高素质的专业人才。 我校材控专业的毕业生,主要求职去向:一是企业,包括机械 制造、冶金、有色金属加工、汽车制造和其它加工企业,从事技术
8
材料科学与工程学院
焊接成形:
焊接方式:手工电弧焊、埋弧自动焊、气体保护焊、气焊 、电渣
焊、电子束焊、激光焊、电阻焊、摩擦焊、扩散焊、钎焊等。
9
材料科学与工程学院
10
材料科学与工程学院
11
材料科学与工程学院
焊接成形:
工艺参数:
电流大小、电压高低、焊接速度、焊接层数 、坡口形状等。
熔池保护方式:
质、全面发展的科学研究和高级工程技术人才。
49
材料科学与工程学院
对毕业生的知识和能力要求:
1、系统的掌握本专业领域的理论基础,包括:力学、机械学、材料 学、电子及电力电子学、自动控制理论、计算机应用技术和企业 管理等基础知识; 2.具有本专业必需的制图、计算、测试、文献检索和基本工艺操作 等基本技能及较强的计算机和外语应用能力; 3.具有本专业领域内某个专业方向所必需的专业知识,了解学科前 沿及发展趋势; 4.具有较强的自学能力、创新意识和较高的综合素质。 5.具有扎实的自然科学基础,较好的人文、艺术和社会科学基础及 正确运用本国语言、文字的表达能力;
九江长江大桥
33
材料科学与工程学院
根据航空发动机的发展趋势,预计未来发动机的主要技术指标可能为
(金属轧制工艺学)10 型材和棒材生产

2020/10/4
7
生产特点、用途及典型产品
型材的生产特点:
➢(3)产品断面形状复杂
在轧制过程中各部分金属变形不均匀,断面各处 温度不均,轧辊摩擦也不均匀,轧件尺寸难以精 确计算,轧机调整和导卫装置安装复杂,故复杂 断面型材的连轧技术发展缓慢。
➢ (2)H型钢腿部内外侧平行,腿端部呈直角,便于 组合成各种构件,与铆焊结构件相比,可以节约大 量的铆钉、焊条等辅助材料,可节省铆焊工作量 25%,加快施工进度,降低成本。
2020/10/4
14
典型产品- H型钢
➢ (3)由于采用万能法进行轧制,腿宽、厚度规格多, 且外形美观,机械性能好;并且,随着万能轧制技 术的进步,可以生产超轻型H型钢,其重量仅为同 规格普通H型钢的55~75%。
轧制理论与工艺
Rolling Theory and Technology
第三篇 型材和棒线材生产
Section 3 Shape, rod and wire producing
陈泽军
Tel:023-65111547 E-Mail: zjchen@
重庆大学 材料科学与工程学院 材料加工工程系
H型钢轧机,1998年莱芜钢铁总厂从日本引进。
2020/10/4
18
H型钢工艺流程图
2020/10/4
19
H型钢生产
万能轧制轧制H型钢
2020/10/4
20
H型钢生产
坯料准备
加热
2020/10/4
除鳞
轧制
热锯切
冷却
矫直
加强未成年人的法制教育,预防和减少未成年人犯罪青少年普法教育宣传PPT专题课件
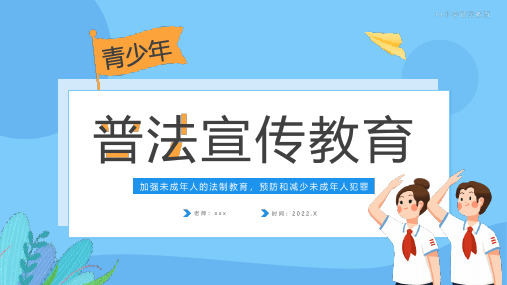
4)、实行质量一票否决制:当质量与进度等发生矛盾时,必须先质量后进度。 玻璃面板由安装在桁架上的钢爪进行固定,做填缝处理后,最终形成幕墙系统,玻璃面板、接驳件、钢方管三者互相依存、互相制约、互相影响。
青少年三大法律责任
xxxx经理应组织安全员对成品质量采取防护措施。 (12)设置断绳自动停止装置,自动停止装置动作在2m范围停止。
青少年三大法律责任
人身损害赔偿 财产损害赔偿
10、积极配合总包方安排的定期文明施工的检查和评比,虚心接受批评,并积极改正;与其他专业公司交叉作业时,相互配合,加强合作,出现问题时,共同协商,友好解决。 2.4桥下通车、行人等立体施工区域,应布设安全网。
青少年三大法律责任
额定张拉控制力以千斤顶油泵读数为准,钢绞线引伸量作为校核,设计引伸量与实际引伸量差值小于6%。 8、现场消防设施按当地消防部门的各项管理规定,由总包方进行设置;
青少年三大法律责任
4、请在施工时及时提供用电驳接点,以免因此产生窝工而影响进度; ,弹性模
青少年三大法律责任
尤其要加强施工过程中的临时防护措施,如做好临时排水系统,设置临时堆土场等; 玻璃构件在净化的玻璃加工厂加工。
青少年三大法律责任
• 强奸
• 抢劫 • 放火
• 爆炸
根据该工程的特殊地理位置,独特的造型及施工工期的要求,结合现场实际情况,我们组织成立了以主管副总经理为总指挥,以xxxx经理负责的**集团总部办公楼幕墙工程xxxx部,实施该xxxx全过程管理职能 (1)建立健全管理机制和监督机制,加强监督管理水土保持方案的实施效果;对水土保持措施的实施进度、质量与资金进行监控管理,保证水土保持措施工程质量;
对违法行为的自我防范
,xxxx主要技术管理人员也将选派具有扎实理论知识和多年实 走行轮滚动表面的凹坑、砂眼之类的面积和深度都不大的缺陷,可用焊补加工法修复。
锻件质量控制的工作内容(二)
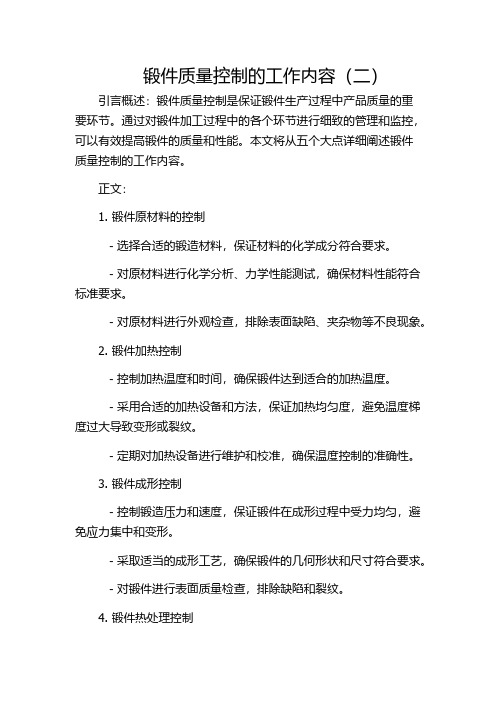
锻件质量控制的工作内容(二)引言概述:锻件质量控制是保证锻件生产过程中产品质量的重要环节。
通过对锻件加工过程中的各个环节进行细致的管理和监控,可以有效提高锻件的质量和性能。
本文将从五个大点详细阐述锻件质量控制的工作内容。
正文:1. 锻件原材料的控制- 选择合适的锻造材料,保证材料的化学成分符合要求。
- 对原材料进行化学分析、力学性能测试,确保材料性能符合标准要求。
- 对原材料进行外观检查,排除表面缺陷、夹杂物等不良现象。
2. 锻件加热控制- 控制加热温度和时间,确保锻件达到适合的加热温度。
- 采用合适的加热设备和方法,保证加热均匀度,避免温度梯度过大导致变形或裂纹。
- 定期对加热设备进行维护和校准,确保温度控制的准确性。
3. 锻件成形控制- 控制锻造压力和速度,保证锻件在成形过程中受力均匀,避免应力集中和变形。
- 采取适当的成形工艺,确保锻件的几何形状和尺寸符合要求。
- 对锻件进行表面质量检查,排除缺陷和裂纹。
4. 锻件热处理控制- 选择合适的热处理工艺,根据锻件的材料和性能要求进行退火、正火、淬火等处理。
- 控制热处理温度和时间,确保锻件达到所需的组织结构和硬度。
- 对热处理设备进行定期检查和维护,保证热处理过程的稳定性和可靠性。
5. 锻件检测与检验- 采用合适的检测方法,如超声波检测、射线检测、磁粉检测等,检查锻件的内部和外部缺陷。
- 进行硬度测试、拉伸试验、冲击试验等力学性能测试,确保锻件的力学性能符合标准。
- 进行尺寸测量和形状检查,检验锻件的几何尺寸和外观质量。
总结:锻件质量控制的工作内容包括锻件原材料的控制、锻件加热控制、锻件成形控制、锻件热处理控制以及锻件检测与检验。
通过严格管理和监控每个环节,可以保证锻件的质量和性能达到设计要求,提高产品的可靠性和安全性。
1.强韧性能的基本概念
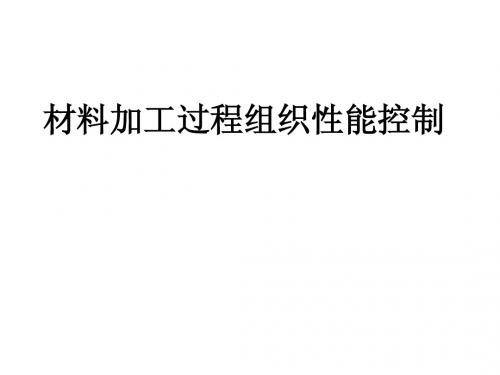
大均匀变形量。 大均匀变形量。
P=S·F V=F·l S=dS/de
dP=S·dF+F·dS=0 = + = dV=F·dl+l·dF=0 = + =
dS/S=- =-dF/F =- -dF/F=dl/l=de = =
K·en=nK·en-1
e=n =
当缩颈开始形成的时候,就是取得最大均匀变形的时刻, 当缩颈开始形成的时候,就是取得最大均匀变形的时刻,最大 均匀变形在数值上等于应变硬化指数。 均匀变形在数值上等于应变硬化指数。
测定方法 1.能量法 αK与T的关系曲线上对应于韧性状态和脆性状态下冲击韧性 的关系曲线上对应于韧性状态和脆性状态下冲击韧性 平均值的温度作为T 平均值的温度作为 c。 αK =( αKmax + αKmin )/ )/2 对应的温度 6 选取一定的冲击功所对应的温度作为Tc 选取一定的冲击功所对应的温度作为 比如:夏氏V形缺口试样,冲击功为20.34J的Tc用V15TT表示 比如:夏氏 形缺口试样,冲击功为 的 表示1 形缺口试样 表示 2.零塑性转变温度 以冲击功曲线开始上升的温度来定义T 以冲击功曲线开始上升的温度来定义 c,用NDT表示 表示
“气团+晶界”理论 气团+晶界” 气团
“Cottrell+Petch“屈服理论 屈服理论
σ<σu时,有一些位错源已脱离钉扎而开动,产生位错, < 有一些位错源已脱离钉扎而开动,产生位错, 由于晶界的阻碍,位错塞积,对相邻晶粒产生应力。 由于晶界的阻碍,位错塞积,对相邻晶粒产生应力。 离塞积群头部l远处有一位错源 点 作用在P点的应力为 点的应力为: 离塞积群头部 远处有一位错源P点,作用在 点的应力为: 远处有一位错源 (σ- σi)(d/2l)1/2 - σ:外加应力 : d:晶粒直径 : σi :位错的运动阻力
对材料成型及其控制工程的认识

对材料成型及其控制工程的认识通过这几周对专业概论的学习,我对这个专业大致的了解了,刚进入大学的我什么都不知道,然而现在我知道这个专业将来可以去做什么,了解了本专业是以铸造、锻压、焊接为主。
材料成型及控制工程是研究热加工改变材料的微观结构、宏观性能和表面形状,研究热加工过程中的相关工艺因素对材料的影响,解决成型工艺开发、成型设备、工艺优化的理论和方法;研究模具设计理论及方法,研究模具制造中的材料、热处理、加工方法等问题。
是国民经济发展的支柱产业。
也是我国较多工科院校开设的重要专业。
材料成形加工行业是制造业的重要组成部分,材料成形加工技术是汽车、电力、石化、造船及机械等支柱产业的基础制造技术,新一代材料加工技术也是先进制造技术的重要内容。
铸造、锻造及焊接等材料加工技术是国民经济可持续发展的主体技术。
据统计,全世界75%的钢材经塑性加工成形,45%的金属结构用焊接得以成形。
又如我国铸件年产量已超过1400万t,是世界铸件生产第一大国。
汽车结构中65%以上仍由钢材、铝合金、铸铁等材料通过铸造、锻压、焊接等加工方法成形。
对材料加工与成型的工艺的认识:材料加工与成型的工艺分类主要按照材料的种类可分为金属塑性成形工艺及非金属成型加工。
金属塑性成形工艺是指利用金属的塑性变形来获得一定形状、尺寸和组织性能的成形加工方法。
金属塑性成形的一般特点是生产率高、生成效率高、节约原材料、节约能源、降低成本。
其中突出的优点为内部组织得以改善,性能提高。
但也存在缺点,像通常需要较大的成形力,设备体积、吨位较大;为了提高被加工材料的塑性、降低成形力,有时需要加热,脆性材料、形状过于复杂的零件不能进行塑性成形。
金属塑性成形工艺可应用于以下领域,特别是重要的零件:汽车(连杆、曲轴、大梁、齿轮、轴等)飞机(发《(1)材料成形及控制工程专业的知识结构及课程的体系建设(2)机械、材料、控制、信息等多学科融合与本专业建设的关系。
(3)强化实践性教学环节,建设专业实习基地的问题。
GCr15轴承钢的热处理工艺设计

热处理工艺课程设计说明书课程名称:金属热处理工艺学设计题目:GCr15轴承钢的热处理工艺设计院系:机械工程学院班级:材料成型及控制工程 XXXX 学号: 0 9 1 1 0 1 1 00学生姓名: idealwang指导教师:黄老师热处理工艺课程设计任务书目录1 热处理工艺课程设计的目的 --------------------42 零件的技术要求及选材 ------------------------4 2.1工作条件和技术要求 -------------------------4 2.2材料的选择 ---------------------------------52.3化学成分及合金元素的作用 -------------------63 热处理工艺课程设计的内容及步骤 ---------------7 3.1相变点的确定 ----------------------------------7 3.2热处理工艺 ----------------------------------8 3.2.1工艺流程-------------------------8 3.2.2热处理工艺参数的制定-------------10 3.2.3处理工艺卡片填写---------------------12 3.2.4作过程中的注意事项 ------------------------------12 3.3家具的设计或者选用及零件的摆布------------------------13 3.4热处理设备的选择-----------------------16 3.5组织特点和性能的分析 ------------------------------16 4总结---------------------------------------------215 收获和体会 ---------------------------------236 参考文献 -----------------------------------237 附表 1 热处理工艺卡 -------------------------25§1 热处理工艺课程设计的目的热处理工艺课程设计是高等学校金属材料工程专业一次专业课设计练习,是热处理原理与工艺课程的最后一个教学环节。
材料加工组织性能控制

3)V的影响:VN的形成阻止奥氏体再结晶 细化转变后的晶粒。问题:过多的固溶V阻止交 叉滑移而影响韧性。
(2)气体和夹杂物控制 氢:引起白点和氢脆;氮:使钢的韧性下 降;氧化物:使钢的韧性下降;硫化物:
硫+锰MnS夹杂(塑性,减轻硫的有害
影响) ,缺点:热轧钢板横向韧性。 措施:降低钢中硫含量;加锆(Zr)和稀土等 元素。
亚晶界:晶内界面,晶粒内取向差在几度范 围的各个小区域。
形成条件:①在奥氏体未再结晶区或奥氏 体、铁素体两相区变形;②冷变形后低温回火。
强化原因:亚晶本身是位错墙,亚晶细小, 位错密度也高。强化作用方面与晶界具有类似的 性质。
对强度的影响:
式中i、K分别是Hall-Petch公式的单晶体的 屈服强度和晶界强化系数;D:没有亚晶的等轴 铁素体尺寸;d:铁素体亚晶的尺寸;fF:等轴铁 素体的分数。
冲击韧性转变温 度变化(C/原
子%)
130 -20 -5 -100 25 -10
-5 -
1)P、S的影响 P:回火脆性和影响交叉滑移; S:增加夹杂物颗粒,减小夹杂物颗
粒间距,使材料韧性下降。 措施:尽可能降低S、P含量;加入稀
土、Ti、Zr等元素。
2)C的影响 碳量,钢中珠光体量(Fe-C相图), 50%FATT 。
(3)金属的韧性 1)韧性的定义及其表示:综合应用较高冲击速
度和缺口试样的应力集中,来测定金属从变形到 断裂所消耗的冲击能量的大小。 韧性指标:Ak(J)、ak(J/cm2)
韧性-脆性转化温度Tk(C) 及表示方法
①选取一定的冲击功所对应
的温度为Tk;②用夏比V 形缺 口 试 样 , 冲 击 功 为 20.34J 的 Tk
晶界强化对强度的影响:
材料加工组织性能控制XXXX(第十章)
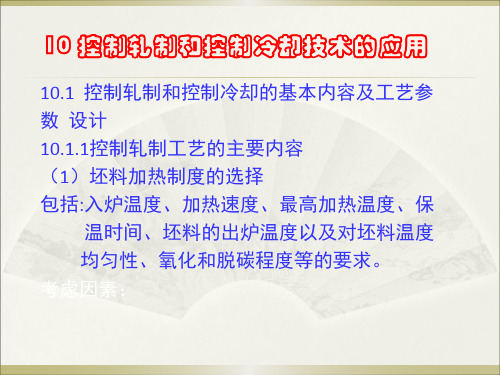
2) 卷取温度对双相钢性能的影响
图10-16 终轧温度和卷取温度对双相钢性能的影响
10.3 连铸连轧理论与应用 10.3.1 五种典型工艺图
工艺1:连铸坯直送轧制工艺(Continuous castin-Hot direct rolling,即CC—HDR)。 特点:
10 控制轧制和控制冷却技术的应用
10.1 控制轧制和控制冷却的基本内容及工艺参 数 设计 10.1.1控制轧制工艺的主要内容 (1)坯料加热制度的选择 包括:入炉温度、加热速度、最高加热温度、保
温时间、坯料的出炉温度以及对坯料温度 均匀性、氧化和脱碳程度等的要求。 考虑因素:
(2)选择和设计控制轧制工艺的类型
第一种方案:完全再结晶型控制轧制工艺。 第二种方案:完全再结晶型与未再结晶型配合的 控制轧制工艺。 第三种方案:完全再结晶型、未再结晶型和 (+)两相区轧制的三阶段控制轧制。
(3)控制轧制工艺参数的设计与确定 包括:温度制度、变形制度。 温度制度:开轧温度、中间停轧待温时的温度范 围、未再结晶区的开轧温度及终轧温度。 变形制度:按控制轧制类型进行轧制道次和变形 量的分配、每道变形量的确定、未再结晶区的总 变形量的确定以及根据钢种要求确定平整道次的 压下量。 理论和生产经验:
图10-24 三辊减定径机组上控制轧制后的组织
10.4.3 控制冷却在小型棒材生产中的应用
在线热处理:
优点: 10.4.3.1 棒材表面淬火及自回火工艺,“QTB (Quenched and Tempered Bar) ” 或 “ QTR (Quenched and Tempered Rod) ” 定义:
未再结晶阶段:
终轧温度:
- 1、下载文档前请自行甄别文档内容的完整性,平台不提供额外的编辑、内容补充、找答案等附加服务。
- 2、"仅部分预览"的文档,不可在线预览部分如存在完整性等问题,可反馈申请退款(可完整预览的文档不适用该条件!)。
- 3、如文档侵犯您的权益,请联系客服反馈,我们会尽快为您处理(人工客服工作时间:9:00-18:30)。
影响双相钢性能的组织因素:马氏体的成分和体
积分数、形状,以及铁素体的晶粒细化程度。 性能: (1)具有高强度、高韧塑性和高加工硬化率 。 (2) 双相钢板材具有板面纵向与横向力学性能差 异小的特点。 (3) 双相钢具有良好的抗疲劳性能和抗应力腐蚀 性能。 (4) 双相钢具有良好的焊接性能。
双相钢应力-应变曲线
除。 4)连轧机组许用轧制力明显的大于常规热带连轧 机组。
(2) 带钢厚度和板形精度
10.4 控制轧制控制冷却在线棒材生产中的应 用
特点: (1)变形量变化范围小。 (2)调整空延时间
控温轧制
控制余轧地制小的。两种类型:
(1)奥氏体再结晶型和未再结晶型两阶段的控轧
工艺。
加热温度:
粗轧工艺:
精轧工艺:
图10-24 三辊减定径机组上控制轧制后的组织
10.4.3 控制冷却在小型棒材生产中的应用
在线热处理:
优点: 10.4.3.1 棒材表面淬火及自回火工艺,“QTB (Quenched and Tempered Bar) ” 或 “ QTR (Quenched and Tempered Rod) ” 定义:
工艺2: “热送轧制”工艺(HotChargeRolling,简称HCR) 特点: 工艺3: 特点:
工艺4: 特点: 工艺5:“冷装炉”轧制工艺(即ColdChargeRolling,简称CCR)。
10.3.2 薄板坯连铸连轧的特点 (1)薄板坯连铸连轧生产线
图3-1 CSP工艺设备布置简图
(2)低碳钢薄板坯连铸连轧的铸态组织
图10-1 热轧带钢机组中的控制轧制参数和作用
图10-2 热轧带钢机组生产铌或钛合金钢时,各道次总动态再结晶临界变形率K 和总变形率ges的比较
a一相同微合金化元素量的影响;b-典型的微合金化元素含量
➢ 控制轧制进一步改进的工艺: 1)板坯加热温度的降低。 2)粗轧温度的降低。 3)粗轧板厚度的增加。 4)分级的冷却速度。
中温卷取型:适当加入Cr、Mo等元素合金化、 奥氏体变形后在连续冷却过程中先析出铁素体, 利用控制冷却速度使大部分奥氏体完成向铁素体 的转变。
低温卷取型:利用热连轧后具有较长的输出辊道 和轧后强烈冷却设备的优势而开发出来的。 工艺特点:
中温卷曲冷却工艺
(3) 控轧控冷工艺参数对双相钢组织性能的影响 1)终轧温度的影响
10.2.3.2 生产双相钢的方法和种类
(1)热处理双相钢
临界间双相(Intercriticaldualphase)简 称“IDP”。
奥氏体双相钢(Austenitedual phase)简称 “ADP”。
(2)热轧双相钢 控制要点: 1)调整钢的化学成分。 2)控制热轧工艺。 3)控制轧后冷却速度。 4)控制热带的卷取温度。根据卷取温度不同, 双相带钢分为中温卷取型和低温卷取型两类。
10.4.3.2 影响最终棒材性能的因素
(1)加热温度的影响: (2)变形速度的影响: (3)终轧温度及变形量的影响: (4)冷却工艺条件的影响:
未再结晶: 完全再结晶:
对综合力学性能,应尽量缩短这一段时间。
自回火温度:第二阶段终了时钢筋的表面最高温 度,又称平衡温度,此温度决定于第一阶段的冷 却时间。 合适的自回火温度取决于回火温度及棒材的化学 成分。
1)开轧温度 钢坯出加热炉温度不低于950℃。
2) 粗、中轧工序 粗、中轧采用Ⅰ型控制轧制工艺。
3)精轧工序 根据轧制钢种的不同, 精轧可采用Ⅱ型控制轧
制或两相区控制轧制,统称为低温精轧工艺。
应注意的问题:
(1)低温精轧变形率 (2)低温精轧前轧件的均温
图10-21轧件表面及芯部温降示意图 1-芯部温度; 2-1/4层温度; 3-表面温度
(3)低温精轧道次安排
(4)低温精轧适合的产品范围
大于Φ40mm的棒材不适于进行低温精轧。
(5)低温精轧的温度范围
钢种
温度范围 ℃
未再结晶轧制
两相区轧制
低碳钢
880~920
800~850
中碳钢
860~900
800~850
高碳钢
850~900
750~800
齿轮钢
850~900
780~850
连续小型棒材控制轧制时轧制表和冷却段布置
➢ 对测量技术装置各工艺步骤的可控性要求:
1)提高轧机功率以克服大的变形抗力要求。 2)提高粗轧板带剪切机功率。 3)尽可能使板带宽度和长度方向上的温度均匀。 4)在低温时也要进行温度测量和温度控制,以便 能利用低温卷取的长处。 5)在生产中测量奥氏体转变,以保证在相变过程 中进行终轧。
10.2.2 中厚板的控制轧制及控制冷却 10.2.2.1 不同类型中厚板轧机控制轧制工艺 (1) 四辊单机架中厚板轧机 控轧工艺:高温再结晶型和未再结晶型两阶段。 再结晶阶段: 未再结晶阶段: 终轧温度:
设备具有强大的轧制压力,允许采用厚度较大的 铸坯,或者可以用于轧制难变形产品,如铁素体 温度区轧制等产生高轧制力的产品。由于生产线 采用双流连铸机配置,年产量可高达250万t。
(4)步进式加热炉布置的薄板坯连铸连轧生产 线
缓冲时间的大小取决于步进炉内钢坯的存放量, 一般设计上可以考虑缓冲时间取1.5-2.0h。
C冷1~镦C钢4—水冷段;C58、50C~6—90附0 加水冷段(7与80钢~种8有50关)
轴承钢
850~9为保证尺寸的高精度,在减定径轧制时需要采取
相对小的变形量。
(b)
(a)
(c)
(2)为充分发挥控冷的效果,控轧必须采用相对 大的变形量。
解决方法: 1)紧凑式轧机的大压下与减定径机 组的轻压下相组合,再配以较低的变形温度;2)采 用2 架大变形量的减径轧机,与随后2 架小变形量的 定径轧机相结合。
10.2.3 热轧双相钢的控制轧制和控制冷却 10.2.3.1 双相钢的组织形貌、性能特点、生产 方法
双相钢: 由两相或两相以上的复合相组成的多
晶体材料。包括:由铁素体和约20%左右的马氏 体构成的高成型性的低合金高强度双相钢;由板 条马氏体和5%以下的残余奥氏体所构成的高强 度高韧性结构钢,以及由马氏体和奥氏体或铁素 体和奥氏体构成的双相不锈钢。
优点:
工艺过程: (1) 淬火阶段: (2) 回火阶段:
图1 Tempeore(表面预先淬火)工艺及其与CCT曲线的关系
(3) 最终冷却阶段:冷床上完成。最终组织:
关键工艺参数:终轧温度,淬火时间,水的流量 或者压力。 最终棒材产品的机械性能取决于:表面马氏体环 形面积与总断面面积之比;回火马氏体机械性能; 心部的组织形态。 回火马氏体的性能取决于:棒材化学成分和回火 温度。
(2) 双机架中厚板轧机的控制轧制工艺 形式:二辊—四辊式,三辊—四辊式、四辊—四 辊式
举例:2800二辊—四辊式:
控制轧制工艺: (a)粗轧终了温度:
道次压下率: 总压下率: (b)四辊精轧机分成两个阶段:部分再结晶的 上限范围轧制,道次压下率:
轧制温度: 未再结晶区轧制,道次压下率:
轧制温度: 终轧温度: (c)轧后采用控制冷却,快冷终止温度650℃。
(5)单流单机座炉卷轧机(TSP)
适合多品种、低投资为目的的配置方式。铸坯厚 度为50-70mm,最小产品厚度1.5mm,设计年产 量为50万t。缺点:带钢表面粗糙度不好 。
(6)无头连铸连轧(ECR)工艺生产线的理想配置
10.3.6 CSP热带性能与精度 (1) 性能
性能差异的原因:
1)铸坯在连铸机内的冷却过程钢水的过冷度大。 2)电磁搅拌和液芯压下技术的采用。 3) 轧制过程温差造成的带钢性能差基本上被消
(4)控轧控冷钢化学成分的调整
碳: 锰 :细化晶粒、提高强度、增加韧性、降低相
变 温度Ar3 ,作用:1)扩大了加工温度范围 ;2) 使铁素体晶粒长大机会减少。 一般控制在1.3-1.5%之间 。 硫: 磷 :不大于0.02% 。
10.1.2 控制冷却工艺设计(已讲过,略) 10.2控制轧制和控制冷却技术在钢板生产中的应用 10.2.1 热轧带钢的控制轧制和控制冷却 ➢ 5个步骤: 1)加热中,微合金化元素碳氮化合物的溶解。 2)再结晶临界温度以下施以大的变形。 3) 微合金化元素碳氮化合物的变形诱导析出延缓再结 晶。 4)未再结晶并强烈变形的奥氏体发生相变。 5)分配冷却剂量来控制冷却和调整所需要的卷取温度。
10 控制轧制和控制冷却技术的应用
10.1 控制轧制和控制冷却的基本内容及工艺参 数 设计 10.1.1控制轧制工艺的主要内容 (1)坯料加热制度的选择 :入炉温度、加热速度、最高加热温度、保
温时间、坯料的出炉温度以及对坯料 温度
均匀性、氧化和脱碳程度等的要求。 考虑因素:
(2)选择和设计控制轧制工艺的类型
图10-16 薄板坯连铸连轧产品与传统热轧产品的性能比较 1-20个普通带卷的平均值;2-20个CSP带卷的平均值
10.3.5 薄板坯连铸连轧生产线的配置 典型的薄板坯连铸连轧生产线工艺流程: 钢水中间包结晶器二冷区飞剪机 均热炉高压水除鳞(立辊轧边机) (粗轧机组)保温炉高压水除鳞 精轧机组近距离卷取机层流冷却远 距离卷取机打包入库。
(2)奥氏体再结晶型、未再结晶型和两相区 轧制的三阶段的控轧工艺。 粗轧工艺: 中 轧工艺: 精轧工艺:
连续小型棒材控制轧制时轧制表和冷却段布置
C1~C4—水冷段;C5、C6—附加水冷段(与钢种有关)
10.4.1 低温轧制
目的: 技术要点: (1)加热温度和粗轧工序: (2)中轧机组与精轧机组: (3)轧件的冷却强度必须在计算机控制下完成
(1)只有精轧机的薄板坯连铸连轧生产线
两条生产线的区别: 铸坯厚度约为50-70mm,设计年产量多在150万t, 产品最小厚度1.0mm。
(2)单流连铸机与粗精机组的薄板坯连铸连轧 生产线配置