材料加工组织性能控制(第五、六章)XXXX9.pptx
合集下载
材料加工组织性能控制第九章
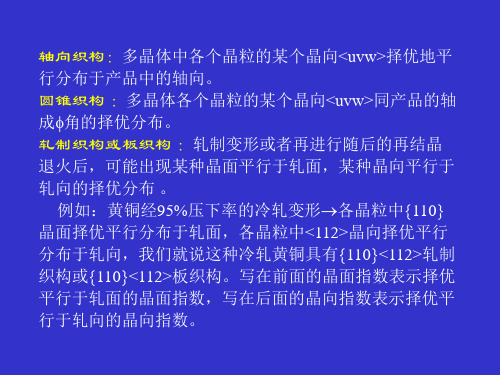
(3)定向成核一选择成长联合理论 再结晶退火时可能发生三种基本的织构变:
再结晶退火后保持了形变织构;再结晶时形变织 构全部或部分地被其它的一个或几个再结晶织构 组分所代替,这种代替可能出现在再结晶的不同 阶段,而且再结晶早期阶段上出现的再结晶织 构,在后期常常又可被新的织构代替;再结晶时 形变织构全部或部分地被无序取向的新晶粒代 替。
08Al:钢中析出铝的氮化物A1N, {111}组分
过饱和固溶体强烈的分解温度高于 的变形晶
600℃。
深
粒比{001} 组分的变
冲
形晶粒容
钢
易形成再
板
结晶核心,
08F:析出的基本上是铁的碳化物 (渗碳体),过饱和固溶体强烈的分 解温度在500℃左右。
容易发生 过饱和固 溶体分解。
08Al钢板: 控制工艺:再结晶退火时的加热速度要慢一些, 还未加热到A1N强烈析出的温度时,{111}取向的 再结晶核心在有利的条件下已顺利地形成,使这种 核心在数量上占据优势。 注意:加热速度不要过高,否则出现加热到 600—700℃时还未到{111}取向再结晶核心的形成 温度,就开始出现A1N的析出,析出的弥散氮化物 对{111}组分的晶粒中再结晶形核的阻碍作用比 {001}组分中的阻碍作用大。于是形成的再结晶核 心中,占优势的将可能是{001}取向的晶核。
08F钢板: 提高{111}再结晶织构的织构度,应提高再结 晶退火时的加热速度,“跑过”碳化物强烈析出 的 温度(500)以防止析出的弥散碳化物阻碍{111}取 向的再结晶核心的形成。否则,碳化物在{111} 取向晶粒的区域中强烈析出,就严重地阻碍了它 们的再结晶核心的形成,而在{001)取向晶粒的区 域中,阻碍作用较微弱,因而有利于{001}取向 的再结晶核心的形成。有利于形成{001}取向的 再结晶织构。
材料加工组织性能控制(第四章)XX9

材料加工组织性能控制(第四章)XX9
2)低温终轧: a)奥氏体状态: b)变形的影响: c)慢冷的结果: 3)高碳钢和高碳合金钢:
PPT文档演模板
材料加工组织性能控制(第四章)XX9
轧后控冷分三阶段: 一次冷却:从终轧温度Ar3或Arcm温度范 围。 目的: (1)控制变形奥氏体的组织状态; (2)固定位错;(3)降低相变温度。 一次冷却开始快冷温度的影响:
•1-轧制温度1000C ;2-轧制温度950C ; 3-轧制温度850C
PPT文档演模板
材料加工组织性能控制(第四章)XX9
4.3.2 贝氏体的影响
•图4-7 抗张强度随贝氏体和 (或)珠光体的体积分数的
变化
PPT文档演模板
•图4-8 贝氏体(+珠光体)的体 积百分数与vTrs的关系,N-
晶粒度
PPT文档演模板
材料加工组织性能控制(第四章)XX9
2)喷射冷却:将水加压由喷嘴喷出的时 候,如果超过连续喷流的流速时则水流发 生破断,形成液滴群冲击被冷却的钢材表 面。 应用:一般冷却及各种用途的喷嘴。 缺点:控制的冷却能力范围不太宽,需要 比其它方法施加更高的压力。
PPT文档演模板
材料加工组织性能控制(第四章)XX9
材料加工组织性能控制(第四章)XX9
4.3.3 马氏体的影响
•生成10%的马氏 体可使vTrs提高 30℃。因此,作 为控制冷却材料, 基本上不应使其 生成马氏体。
控制冷却设备:必须能均匀控制长、宽、 厚方向钢板的性能。 冷却方式:同时冷却型、通过冷却型。
PPT文档演模板
材料加工组织性能控制(第四章)XX9
PPT文档演模板
•图2-9 轧制后冷却对抗拉强度、断面转 变温度的影响
材料加工组织性能控制教学课件

材料的密度、热膨胀系数、热导 率等指标,反映材料的物理属性。
材料的耐腐蚀性、抗氧化性、耐 候性等指标,反映材料在化学环 境中的稳定性。
材料组织性能的影响因素
1 2 3
成分与组织 材料的成分和组织结构对性能有决定性影响,如 钢铁材料中的碳含量和显微组织结构。
工艺与处理 材料的加工工艺和处理条件对组织结构和性能有 重要影响,如铸造、锻造、焊接等工艺。
分类
根据加工方式的不同,材料加工可分 为铸造、锻造、焊接、热处理、表面 处理等。
材料加工的重要性与应用领域
重要性
材料加工是制造业的核心环节,对国民经济的发展和国防建设具有重要意义。
应用领域
材料加工广泛应用于航空航天、汽车、船舶、能源、电子信息等领域。
材料加工技术的发展趋势
智能化
采用智能技术提高材料加工的 自动化和智能化水平,降低人
高强度钢的组织性能控制
要点一
总结词
高强度钢是一种具有高强度和良好塑性的钢材,广泛应用 于汽车、建筑和机械等领域。其组织性能控制对于保证材 料的质量和稳定性至关重要。
要点二
详细描述
高强度钢的组织性能控制主要包括细化晶粒、降低杂质含 量和合金元素调整等手段。通过控制轧制和热处理工艺, 可以获得具有优良综合性能的高强度钢板。同时,高强度 钢的焊接性能也需要通过合理的焊接工艺进行控制,以确 保其在加工和使用过程中的稳定性和可靠性。
04
材料加工组织性能控制技术
计算机模拟与优化技术
计算机模拟技术
通过计算机模拟材料加工过程中的物理、化学和力学行为,预测材料的组织性能,优化 加工工艺参数。
优化算法
应用各种优化算法,如遗传算法、粒子群算法等,寻找最佳的加工工艺参数组合,提高 材料的性能。
材料加工质量管理ppt课件

采用PP管及配件:根据给水设计图配置好PP管及配件,用管件在 管材垂 直角切 断管材 ,边剪 边旋转 ,以保 证切口 面的圆 度,保 持熔接 部位干 净无污 物
材料加工质量管理 JJiilliinnUUnniivveerrssiittyyDDrr。。mmoonntt。。WWaanngg QQiiaanngg
图5- 1控 制图示 例 控 制图 上有 5条 线,由 上至 下分 别是: 1. 公差上限 TU 2. 上控制界限 UCL (Up Control Limit) 3. 控制中心线 CL (Control Li ne)
4. 下控制界限 LCL (Lower Control Li mit) 5. 公差下限 TL
2. 点子多次出现在中心线一侧,包括: (1)连 续 11点中 ,至少 有10点 位于中 心线同 一侧 (2)连 续 14点中 ,至少 有12点 位于中 心线同 一侧 (3)连 续 17点中 ,至少 有14点 位于中 心线同 一侧 (4)连 续 20点中 ,至少 有16点 位于中 心线同 一侧
第二节 计量值控制图 (一) x —R控制图 x —R控制图是 x 控制图和R控制图的联用形式。其中,x 控制图主 要 用于 观察 平均值 的变 动, R控 制图用 于观 察分布 的幅 度。 它是一
种 常用 的典 型的计 量值 控制图 。 (二);x — R控制图用途 x—R控制图适用范围广。因为,x 服从正态分布是经常出现的,当 x是 非 正态 分布 时,则 当 n>4或5时, 根据 中心极 限定 理,近 似正 态
采用PP管及配件:根据给水设计图配置好PP管及配件,用管件在 管材垂 直角切 断管材 ,边剪 边旋转 ,以保 证切口 面的圆 度,保 持熔接 部位干 净无污 物
材料加工质量管理 JJiilliinnUUnniivveerrssiittyyDDrr。。mmoonntt。。WWaanngg QQiiaanngg
材料加工与性能优化ppt课件

试管作较彻底的预热。
完整版PPT课件
27
第三单元 复合材料的制造
完整版PPT课件
28
一、复合材料的基本概念
1、复合材料的定义
将两种或两种以上的性质不同的材料经过 特殊的加工制成的材料称为复合材料。
2、复合材料的组成:
基体― 起粘结作用
复合材料
增强体―起骨架作用
完整版PPT课件
29
3、复合材料和合金比较:
成分 形成工艺
复合材料
Hale Waihona Puke 合金两种或两种以 两种或两种以上金 上不同材料 属材料或金属与非
金属
特殊加工
熔合
性质
优于原材料
完整版PPT课件
30
预测
复合材料
基体材料 的类型
增强体材料 的化学组成
性能
金属
C
陶瓷
SiO2
合成树脂 SiO2、Al2O3
耐酸碱,化学稳定性好,强度高,密 度小,韧性好
强度高,抗冲击,绝缘性好,耐热温度 低于300℃
目 D.分子复合材料 标
检 测 4.飞机、火箭的机翼和机身以及导弹的壳体、
尾翼中的复合材料是 A A .金属基复合材料 B .树脂基复合材料 C.绝缘基复合材料 D.智能复合材料
完整版PPT课件
37
5 用短线把下列物质、用途、主要性能相连接。
物质
用途
性能
玻璃钢
制造骨和股关节
耐腐蚀强
光纤
制造排水管道
(3)加热到发生反应时,试管内粉末会出现翻腾现象,随之黄色 粉末慢慢变黑。到试剂呈黑色而不再有翻腾现象时,停止加热,留 在试管里的是自燃铁粉。
(4)在制取自燃铁粉时有大量气体产生,极可能发生冲料现象,
金属材料组织与性能的控制概述PPT(58张)

动等,以破碎晶体,获得更多的晶核,细化晶 粒。
电磁搅拌 将正在结晶的金属放入交变电磁场中,由
于电磁感应,液态金属会翻滚,从而破坏正在 结晶的树枝状晶体的枝晶,增加形核数目,细 化晶粒。
第四讲 金属的结晶
重点
–结晶的必要充分条件——过冷度
• 过冷度与冷却速度有关
–结晶的过程
• 形核、核长大
–晶粒的控制
1394℃
912℃
-Fe
-Fe
-Fe
金 属 的 同 素 异 构 转 变
纯金属的结晶-同素异构转变
纯金属的结晶-同素异构转变
固态相变的晶界形核
纯金属的结晶-同素异构转变
同素异构转变的特点 l 有过冷现象,有固定的转变温度 l 新晶体的形成也包括形核和长大两个过程; l 要较大的过冷度; l 转变时引起体积发生变化,产生较大的内应力相之间关系的一来自简明示图,又称平衡图或状态 图;
相图表示合金在缓慢冷却条件下平衡相与成 分、温度之间关系的图形,它是研制新材料,制 定合金的熔炼、铸造、压力加工和热处理工艺以 及进行金相分析的重要依据。
二元合金的结晶
平衡相、平衡组织
如果合金在某一温度停留任意长的时间,合 金中各相的成分是均匀的和不变的,各相的相 对质量也不变,该合金处于相平衡状态,此时 合金中的各相称为平衡相,由这些平衡相所构 成的组织称为平衡组织。
改变熔体的过冷度即可改变相变驱动力,控制结晶过程的进行。
结晶过程:
形核、长大
纯金属的结晶-同素异构转变
同素异构转变(重结晶) 金属在固态下随温度的改变,由一种晶格转
变为另一种晶格的现象; 如:铁、钴、钛
同素异构晶体 同属于一种金属,但具有不同晶体结构的晶
电磁搅拌 将正在结晶的金属放入交变电磁场中,由
于电磁感应,液态金属会翻滚,从而破坏正在 结晶的树枝状晶体的枝晶,增加形核数目,细 化晶粒。
第四讲 金属的结晶
重点
–结晶的必要充分条件——过冷度
• 过冷度与冷却速度有关
–结晶的过程
• 形核、核长大
–晶粒的控制
1394℃
912℃
-Fe
-Fe
-Fe
金 属 的 同 素 异 构 转 变
纯金属的结晶-同素异构转变
纯金属的结晶-同素异构转变
固态相变的晶界形核
纯金属的结晶-同素异构转变
同素异构转变的特点 l 有过冷现象,有固定的转变温度 l 新晶体的形成也包括形核和长大两个过程; l 要较大的过冷度; l 转变时引起体积发生变化,产生较大的内应力相之间关系的一来自简明示图,又称平衡图或状态 图;
相图表示合金在缓慢冷却条件下平衡相与成 分、温度之间关系的图形,它是研制新材料,制 定合金的熔炼、铸造、压力加工和热处理工艺以 及进行金相分析的重要依据。
二元合金的结晶
平衡相、平衡组织
如果合金在某一温度停留任意长的时间,合 金中各相的成分是均匀的和不变的,各相的相 对质量也不变,该合金处于相平衡状态,此时 合金中的各相称为平衡相,由这些平衡相所构 成的组织称为平衡组织。
改变熔体的过冷度即可改变相变驱动力,控制结晶过程的进行。
结晶过程:
形核、长大
纯金属的结晶-同素异构转变
同素异构转变(重结晶) 金属在固态下随温度的改变,由一种晶格转
变为另一种晶格的现象; 如:铁、钴、钛
同素异构晶体 同属于一种金属,但具有不同晶体结构的晶
材料加工组织性能控制XXXX(第十章)
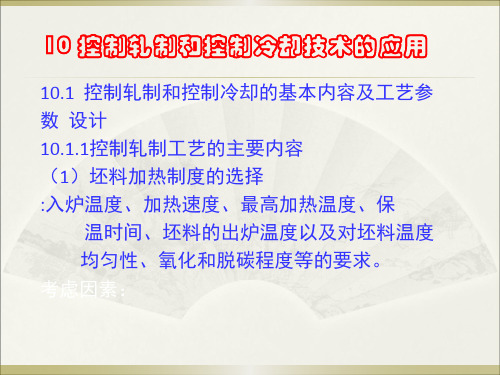
未再结晶阶段:
终轧温度:
(2) 双机架中厚板轧机的控制轧制工艺 形式:二辊—四辊式,三辊—四辊式、四辊—四 辊式
举例:2800二辊—四辊式:
控制轧制工艺: (a)粗轧终了温度:
道次压下率: 总压下率: (b)四辊精轧机分成两个阶段:部分再结晶的 上限范围轧制,道次压下率:
轧制温度: 未再结晶区轧制,道次压下率:
10 控制轧制和控制冷却技术的应用
10.1 控制轧制和控制冷却的基本内容及工艺参 数 设计 10.1.1控制轧制工艺的主要内容 (1)坯料加热制度的选择 :入炉温度、加热速度、最高加热温度、保
温时间、坯料的出炉温度以及对坯料温度 均匀性、氧化和脱碳程度等的要求。 考虑因素:
(2)选择和设计控制轧制工艺的类型
(4)控轧控冷钢化学成分的调整
碳: 锰 :细化晶粒、提高强度、增加韧性、降低相变 温度Ar3 ,作用:1)扩大了加工温度范围 ;2) 使铁素体晶粒长大机会减少。 一般控制在1.3-1.5%之间 。 硫: 磷 :不大于0.02% 。
10.1.2 控制冷却工艺设计(已讲过,略) 10.2控制轧制和控制冷却技术在钢板生产中的应用 10.2.1 热轧带钢的控制轧制和控制冷却 ➢ 5个步骤: 1)加热中,微合金化元素碳氮化合物的溶解。 2)再结晶临界温度以下施以大的变形。 3) 微合金化元素碳氮化合物的变形诱导析出延缓再结 晶。 4)未再结晶并强烈变形的奥氏体发生相变。 5)分配冷却剂量来控制冷却和调整所需要的卷取温度。
图10-16 终轧温度和卷取温度对双相钢性能的影响
2) 卷取温度对双相钢性能的影响
图10-16 终轧温度和卷取温度对双相钢性能的影响
10.3 连铸连轧理论与应用 10.3.1 五种典型工艺图
终轧温度:
(2) 双机架中厚板轧机的控制轧制工艺 形式:二辊—四辊式,三辊—四辊式、四辊—四 辊式
举例:2800二辊—四辊式:
控制轧制工艺: (a)粗轧终了温度:
道次压下率: 总压下率: (b)四辊精轧机分成两个阶段:部分再结晶的 上限范围轧制,道次压下率:
轧制温度: 未再结晶区轧制,道次压下率:
10 控制轧制和控制冷却技术的应用
10.1 控制轧制和控制冷却的基本内容及工艺参 数 设计 10.1.1控制轧制工艺的主要内容 (1)坯料加热制度的选择 :入炉温度、加热速度、最高加热温度、保
温时间、坯料的出炉温度以及对坯料温度 均匀性、氧化和脱碳程度等的要求。 考虑因素:
(2)选择和设计控制轧制工艺的类型
(4)控轧控冷钢化学成分的调整
碳: 锰 :细化晶粒、提高强度、增加韧性、降低相变 温度Ar3 ,作用:1)扩大了加工温度范围 ;2) 使铁素体晶粒长大机会减少。 一般控制在1.3-1.5%之间 。 硫: 磷 :不大于0.02% 。
10.1.2 控制冷却工艺设计(已讲过,略) 10.2控制轧制和控制冷却技术在钢板生产中的应用 10.2.1 热轧带钢的控制轧制和控制冷却 ➢ 5个步骤: 1)加热中,微合金化元素碳氮化合物的溶解。 2)再结晶临界温度以下施以大的变形。 3) 微合金化元素碳氮化合物的变形诱导析出延缓再结 晶。 4)未再结晶并强烈变形的奥氏体发生相变。 5)分配冷却剂量来控制冷却和调整所需要的卷取温度。
图10-16 终轧温度和卷取温度对双相钢性能的影响
2) 卷取温度对双相钢性能的影响
图10-16 终轧温度和卷取温度对双相钢性能的影响
10.3 连铸连轧理论与应用 10.3.1 五种典型工艺图
钢材组织性能的控制课件

总结词
高强度钢材具有较高的抗拉强度和屈服点,广泛应用于建筑、桥梁、船舶、汽车等领域。
详细描述
高强度钢材在建筑领域中用于制造高层建筑的承重结构,如梁、柱、板等,能够提高建 筑物的承载能力和抗震性能。在桥梁建设中,高强度钢材可用于制造大型桥梁的主梁和 桥面板,增加桥梁的跨度和承载能力。在汽车制造中,高强度钢材主要用于制造汽车底
回火
回火是将淬火后的钢材加热到低于其脆性温度的某一温度范围,保温一段时间 后冷却下来的一种热处理工艺。回火可以消除淬火产生的内应力,稳定组织结 构,提高钢材的综合力学性能。
03 钢材组织性能的 控制方法
合金元素的添加和控制
合金元素
在钢中加入一定量的合金元素, 如铬、镍、钨等,可以改变钢材 的力学性能和耐腐蚀性。
耐磨钢材的应用
总结词
耐磨钢材具有较高的硬度和耐磨性,广 泛应用于矿山、采石场、水泥厂等磨损 严重的场合。
VS
详细描述
在矿山和采石场中,耐磨钢材用于制造挖 掘机、破碎机和磨机等设备的易损件,能 够承受高速磨损和冲击。在水泥厂中,耐 磨钢材主要用于制造窑炉的耐火材料和研 磨体的衬板等部件,能够提高设备的耐用 性和生产效率。此外,耐磨钢材还可用于 制造输送带、铁路道岔和船舶甲板等耐磨 件。
环保和可持续发展
降低能耗和排放
01
优化炼钢工艺和节能减排技术,降低钢材生产过程中的能耗和
污染物排放。
循环利用和再生利用
02
推动废旧钢材的循环利用和再生利用,减少资源浪费和环境污染。
绿色包装和运输
03
采用环保包装和运输方式,减少钢材产品在运输过程中的能耗
和排放。Βιβλιοθήκη THANKS感谢观看
热处理工艺的影响
高强度钢材具有较高的抗拉强度和屈服点,广泛应用于建筑、桥梁、船舶、汽车等领域。
详细描述
高强度钢材在建筑领域中用于制造高层建筑的承重结构,如梁、柱、板等,能够提高建 筑物的承载能力和抗震性能。在桥梁建设中,高强度钢材可用于制造大型桥梁的主梁和 桥面板,增加桥梁的跨度和承载能力。在汽车制造中,高强度钢材主要用于制造汽车底
回火
回火是将淬火后的钢材加热到低于其脆性温度的某一温度范围,保温一段时间 后冷却下来的一种热处理工艺。回火可以消除淬火产生的内应力,稳定组织结 构,提高钢材的综合力学性能。
03 钢材组织性能的 控制方法
合金元素的添加和控制
合金元素
在钢中加入一定量的合金元素, 如铬、镍、钨等,可以改变钢材 的力学性能和耐腐蚀性。
耐磨钢材的应用
总结词
耐磨钢材具有较高的硬度和耐磨性,广 泛应用于矿山、采石场、水泥厂等磨损 严重的场合。
VS
详细描述
在矿山和采石场中,耐磨钢材用于制造挖 掘机、破碎机和磨机等设备的易损件,能 够承受高速磨损和冲击。在水泥厂中,耐 磨钢材主要用于制造窑炉的耐火材料和研 磨体的衬板等部件,能够提高设备的耐用 性和生产效率。此外,耐磨钢材还可用于 制造输送带、铁路道岔和船舶甲板等耐磨 件。
环保和可持续发展
降低能耗和排放
01
优化炼钢工艺和节能减排技术,降低钢材生产过程中的能耗和
污染物排放。
循环利用和再生利用
02
推动废旧钢材的循环利用和再生利用,减少资源浪费和环境污染。
绿色包装和运输
03
采用环保包装和运输方式,减少钢材产品在运输过程中的能耗
和排放。Βιβλιοθήκη THANKS感谢观看
热处理工艺的影响
材料加工组织性能控制

措施:
3)V的影响:VN的形成阻止奥氏体再结晶 细化转变后的晶粒。问题:过多的固溶V阻止交 叉滑移而影响韧性。
(2)气体和夹杂物控制 氢:引起白点和氢脆;氮:使钢的韧性下 降;氧化物:使钢的韧性下降;硫化物:
硫+锰MnS夹杂(塑性,减轻硫的有害
影响) ,缺点:热轧钢板横向韧性。 措施:降低钢中硫含量;加锆(Zr)和稀土等 元素。
亚晶界:晶内界面,晶粒内取向差在几度范 围的各个小区域。
形成条件:①在奥氏体未再结晶区或奥氏 体、铁素体两相区变形;②冷变形后低温回火。
强化原因:亚晶本身是位错墙,亚晶细小, 位错密度也高。强化作用方面与晶界具有类似的 性质。
对强度的影响:
式中i、K分别是Hall-Petch公式的单晶体的 屈服强度和晶界强化系数;D:没有亚晶的等轴 铁素体尺寸;d:铁素体亚晶的尺寸;fF:等轴铁 素体的分数。
冲击韧性转变温 度变化(C/原
子%)
130 -20 -5 -100 25 -10
-5 -
1)P、S的影响 P:回火脆性和影响交叉滑移; S:增加夹杂物颗粒,减小夹杂物颗
粒间距,使材料韧性下降。 措施:尽可能降低S、P含量;加入稀
土、Ti、Zr等元素。
2)C的影响 碳量,钢中珠光体量(Fe-C相图), 50%FATT 。
(3)金属的韧性 1)韧性的定义及其表示:综合应用较高冲击速
度和缺口试样的应力集中,来测定金属从变形到 断裂所消耗的冲击能量的大小。 韧性指标:Ak(J)、ak(J/cm2)
韧性-脆性转化温度Tk(C) 及表示方法
①选取一定的冲击功所对应
的温度为Tk;②用夏比V 形缺 口 试 样 , 冲 击 功 为 20.34J 的 Tk
晶界强化对强度的影响:
3)V的影响:VN的形成阻止奥氏体再结晶 细化转变后的晶粒。问题:过多的固溶V阻止交 叉滑移而影响韧性。
(2)气体和夹杂物控制 氢:引起白点和氢脆;氮:使钢的韧性下 降;氧化物:使钢的韧性下降;硫化物:
硫+锰MnS夹杂(塑性,减轻硫的有害
影响) ,缺点:热轧钢板横向韧性。 措施:降低钢中硫含量;加锆(Zr)和稀土等 元素。
亚晶界:晶内界面,晶粒内取向差在几度范 围的各个小区域。
形成条件:①在奥氏体未再结晶区或奥氏 体、铁素体两相区变形;②冷变形后低温回火。
强化原因:亚晶本身是位错墙,亚晶细小, 位错密度也高。强化作用方面与晶界具有类似的 性质。
对强度的影响:
式中i、K分别是Hall-Petch公式的单晶体的 屈服强度和晶界强化系数;D:没有亚晶的等轴 铁素体尺寸;d:铁素体亚晶的尺寸;fF:等轴铁 素体的分数。
冲击韧性转变温 度变化(C/原
子%)
130 -20 -5 -100 25 -10
-5 -
1)P、S的影响 P:回火脆性和影响交叉滑移; S:增加夹杂物颗粒,减小夹杂物颗
粒间距,使材料韧性下降。 措施:尽可能降低S、P含量;加入稀
土、Ti、Zr等元素。
2)C的影响 碳量,钢中珠光体量(Fe-C相图), 50%FATT 。
(3)金属的韧性 1)韧性的定义及其表示:综合应用较高冲击速
度和缺口试样的应力集中,来测定金属从变形到 断裂所消耗的冲击能量的大小。 韧性指标:Ak(J)、ak(J/cm2)
韧性-脆性转化温度Tk(C) 及表示方法
①选取一定的冲击功所对应
的温度为Tk;②用夏比V 形缺 口 试 样 , 冲 击 功 为 20.34J 的 Tk
晶界强化对强度的影响:
工程材料——金属材料组织和性能控制课件

合金相
通过添加合金元素,可以形成具有不 同性能的合金相。合金相的组成和结 构决定了其物理、化学和机械性能。
金属的显微组织与织构
显微组织
金属的显微组织决定了其宏观性能。通过控制显微组织的形 貌、分布和相对含量,可以优化金属材料的性能。常见的显 微组织包括固溶体、金属化合物和机械混合物。
织构
金属的织构是指其晶体取向与外力方向之间的关系。织构对 金属材料的力学性能、电磁性能和加工性能具有重要影响。 织构的控制方法包括塑性变形、热处理和合金化等。
所需形状的工艺。
铸造工艺分类
根据铸造过程中金属的熔炼和浇注 方式的不同,铸造工艺可分为砂型 铸造、金属型铸造、压力铸造等。
铸造工艺的应用
铸造工艺广泛应用于机械、汽车、 航空航天、船舶等行业的零件制造。
金属材料的塑性加工工 艺
塑性加工工艺简介
塑性加工是一种通过施加外力使金属材料发生塑性变形,从而获 得所需形状和性能的工艺。
导热性能良好的金属可以 快速传递热量。
金属材料的化学特性
耐腐蚀性
化学稳定性
金属材料的耐腐蚀性取决于其抵抗氧 化和酸碱腐蚀的能力,一些金属材料 如不锈钢具有较好的耐腐蚀性。
金属材料在化学反应中的稳定性,决 定了其在特定环境下的化学行为和反 应。
抗氧化性
金属材料在高温下与氧气反应的能力, 抗氧化性能决定了金属在高温环境下 的使用寿命。
03
金属材料的性能控制
金属材料的力学性能
强度
金属材料在受到外力作用时抵抗变形和断 裂的能力,包括抗拉强度、抗压强度等。
塑性
金属材料在受到外力作用时发生屈服而不 发生断裂的能力。
韧性
金属材料在受到外力作用时吸收能量、抵 抗冲击的能力。
通过添加合金元素,可以形成具有不 同性能的合金相。合金相的组成和结 构决定了其物理、化学和机械性能。
金属的显微组织与织构
显微组织
金属的显微组织决定了其宏观性能。通过控制显微组织的形 貌、分布和相对含量,可以优化金属材料的性能。常见的显 微组织包括固溶体、金属化合物和机械混合物。
织构
金属的织构是指其晶体取向与外力方向之间的关系。织构对 金属材料的力学性能、电磁性能和加工性能具有重要影响。 织构的控制方法包括塑性变形、热处理和合金化等。
所需形状的工艺。
铸造工艺分类
根据铸造过程中金属的熔炼和浇注 方式的不同,铸造工艺可分为砂型 铸造、金属型铸造、压力铸造等。
铸造工艺的应用
铸造工艺广泛应用于机械、汽车、 航空航天、船舶等行业的零件制造。
金属材料的塑性加工工 艺
塑性加工工艺简介
塑性加工是一种通过施加外力使金属材料发生塑性变形,从而获 得所需形状和性能的工艺。
导热性能良好的金属可以 快速传递热量。
金属材料的化学特性
耐腐蚀性
化学稳定性
金属材料的耐腐蚀性取决于其抵抗氧 化和酸碱腐蚀的能力,一些金属材料 如不锈钢具有较好的耐腐蚀性。
金属材料在化学反应中的稳定性,决 定了其在特定环境下的化学行为和反 应。
抗氧化性
金属材料在高温下与氧气反应的能力, 抗氧化性能决定了金属在高温环境下 的使用寿命。
03
金属材料的性能控制
金属材料的力学性能
强度
金属材料在受到外力作用时抵抗变形和断 裂的能力,包括抗拉强度、抗压强度等。
塑性
金属材料在受到外力作用时发生屈服而不 发生断裂的能力。
韧性
金属材料在受到外力作用时吸收能量、抵 抗冲击的能力。
- 1、下载文档前请自行甄别文档内容的完整性,平台不提供额外的编辑、内容补充、找答案等附加服务。
- 2、"仅部分预览"的文档,不可在线预览部分如存在完整性等问题,可反馈申请退款(可完整预览的文档不适用该条件!)。
- 3、如文档侵犯您的权益,请联系客服反馈,我们会尽快为您处理(人工客服工作时间:9:00-18:30)。
图5-15 在普碳钢和含铌钢中,单道次 的变形量和变形温度对再结晶奥氏体 晶粒尺寸的影响
总结:
铌在奥氏体中存在形式:1)加热时尚未溶到奥氏 体中的Nb(C、N);2)固溶到奥氏中的铌;3)加热 时溶解、轧制过程中又由奥氏体中重新析出的 Nb(C、N)。轧制的不同阶段,其阻止奥氏体再结 晶是不同的。
5.2.2 影响Nb(C、N)析出的因素 (1)变形量和析出时间
图5-6 在含有0.06%C、0.041%Nb和0.0040%N的钢中,变形量对沉淀的影响 1-67%变形;2-50%变形;3-33%变形;4-17%变形
(2)变形温度
1)析出量相等时,未 再结晶区轧制所需时间 短。原因:
2)析出量一定时,在 高温所需等温时间短, 低温所需等Байду номын сангаас时间长。
(1)微量元素对动态再结晶临界变形量的影响
机理:1)合金元素 偏析于晶粒边界而 引起的溶质原子的 拖拉作用;2)合 金元素的碳氮化合 物在晶界沉淀而引 起的钉扎作用。
图5-9 实验钢1000C变形时真应力-真应变曲线
(2) 微量元素对再结晶数量的影响
图5-10 1000C终轧后晶粒再结晶面积百分率与析出Nb量的关系
硫(S)、钙(Ca)、稀土金属(REM)及锆(Zr)。 控制钢
的塑性
微合金化元素: 特点:与碳、氮结合成碳化物、氮化物和 碳氮化物,高温下溶解,低温下析出。 作用:(1)加热:阻碍原始奥氏体晶粒长 大; (2)轧制:抑制再结晶及再结晶后的晶粒长 大;(3)低温:析出强化作用。
5.1 溶度积(溶解度乘积)
5. 微合金元素在控制轧制中的作用
HSLA钢中常用合金元素及夹杂元素分类:
1)微合金化元素:铌(Nb)、钒(V)、 钛(Ti)、铝(Al)和硼(B)。
2)置换元素:硅(Si)、锰(Mn)、 钼(Mo)、铜(Cu)、镍(Ni)和铬(Cr)。
控制钢的强 度、韧性、 相变显微组 织
3)夹杂及硫化物形状控制的添加元素:磷(P)、
特点: (1)TiN: (2) VC: (3) NbC和TiC: (2)晶格结构:Al,其余 元素; (3)氮化物与碳化物的比 较; (4)含钛钢:首先形成氮 化钛。
图5-1 中碳化物和氮化物的溶度积
特点: (1)铌钢: (2)钒钢和Si-Mn钢: (3)钛钢: 机理:沉淀对奥氏体晶 粒边界起钉扎作用使钛 钢具有高于1250℃的极 高的晶粒细化温度。
(4) 奥氏体向铁素体转变过程中和在铁素体内 Nb(C、N)的析出状态 1)碳氮化物在和中的溶解度不同相变后,产 生快速析出。 相间析出(相间沉淀): 冷却速度大、析出温度低相间沉淀排间距小 析出质点也小。 析出时间长质点长大。 2)相变后内剩余的固溶铌继续析出,质点大小 决定于冷却速度。 3)冷却到室温,1015%左右的铌未从铁素体中 析出。
各阶段Nb(C、N)平均析出速度: 不同析出温度的影响:
终轧温度的影响: 高温轧制后冷却到相变温度:铌的平均析出速度 不大、析出颗粒较大( 200 Å左右)。原因: 低温轧制:加大了冷却过程中铌的析出速度,析 出颗粒细小( 50100Å )。原因:
控制轧制就是应用这种微细的Nb(C、N)析出质 点固定亚晶界而阻止奥氏体晶粒再结晶,达到 细化晶粒的目的。
0.008
0.10
-
3
D45
0.05
0.005
0.12
0.23
4
32675A 0.045
0.006
0.10
0.17
5.3 再结晶的延迟
图5-3 中的静态再结晶动力学 (a)Si-Mn钢;(b)含0.04%Nb的钢
预应变为0.50
图5-4 中的静态再结晶动力学 (a)含0.08%Ti的钢;(b)含0.10%V 的钢 变形温度900C预应变为0.50
图5-7 温度-时间-沉淀动力学曲线、形变对沉淀动力 学的影响
规程1:在再结晶区变形、发生了再结晶
规程2:附加有未再结晶区变形、未发生再结晶
(3)钢的成分变化
图5-8 铌钢经50%变形 后在900C 时的沉淀图
曲线
钢号
铌,%
氮,%
碳,%
钼,%
1
76320
0.04
0.003
0.19
-
2
D43
0.04
5.3.5 微量合金元素对再结晶晶粒大小的影响
图5-14 铌对热轧1道次后的再结晶晶粒度的影响 (不含铌钢和含0.03%铌的钢的基本成分相同)
1-加热状态下含0.03%Nb的钢
2-加热到1250C后压下65%并且再结晶终了的不 含铌钢
3-加热到1250C后压下70%并且再结晶终了的含 0.03%铌钢
(2)出炉后到轧制前: 在轧制前,从固溶体中析出Nb(C、N)数量很少。
(3)在变形奥氏体中:
图5-3 钢中析出Nb量与变形量和变形停留时间的关系 Nb(P):沉淀相中的Nb量占钢中Nb量的%
变形温度对含铌低合金钢析出的影响: 850880C:变形加剧固溶体的分解,析 出粗大 的碳氮化物 固溶体中含铌量, 析出的碳氮化物没有参加弥散强化。 800700C变形:扩散速度 ,粗大质点碳 化物析出困难,冷却过程中析出大量细小 质点。
图5-16 含铌钢在变形50%以后等温时间内的再结晶与沉淀 (0.10%C、0.99%Mn、0.04%Nb、0.008%N)
1-100%再结晶;2-50%再结晶;3-0%再结晶;4-20%沉淀;550%沉淀;6-75%沉淀;7-100%沉淀
(3) 微量元素对再结晶速度的影响
图5-11 铌对含有0.05%C、1.8%Mn钢 再结晶速度的影响
5.3.4 微量元素对静态再结晶 临界变形量的影响
图5-13铌对奥氏体再结晶临界压下率的影响(1道次) 1-加热温度1250C,0.13%Nb,晶粒度:1.7级 2-加热温度1250C,0.03%Nb,晶粒度:2.8级 3-加热温度1150C,0.03%Nb,晶粒度:2.4级 4-加热温度1250C,不含Nb,晶粒度:0.4级
图5-2 晶粒尺寸与加热温度的关系
5.2 控制轧制过程中微量元素碳氮化合物 的析出 5.2.1 各阶段中Nb(C、N)的析出状态 (1)出炉前: 加热到1200C,均热2h:90%以上铌都 固溶到奥氏体基体中,有极少数粗大 Nb(C、N)没有固溶到奥氏体中。 1260C :保温30min,Nb(C、N)全部溶 解。