8D报告培训教材(经典)
8D报告培训教材

根本原因确定
深入分析
对已经确认的问题原因进行进一 步分析,找出根本原因。
跨部门合作
邀请相关部门和专家共同参与分 析,确保根本原因确定的准确性
和全面性。
制定措施
根据根本原因,制定相应的纠正 和预防措施,避免问题再次发生
。
04
纠正措施与预防措施
纠正措施制定
问题分析
对发生的问题进行深入分析,找出根本原因。
8D报告培训教材
目录
• 8D报告概述 • 问题识别与定义 • 原因分析与验证 • 纠正措施与预防措施 • 效果评估与持续改进 • 8D报告编写技巧与注意事项 • 案例分析与实战演练
01
8D报告概述
定义与背景
定义
8D报告是一种结构化的问题解决 工具,用于识别、分析和解决产 品或过程中的问题。
背景
05
效果评估与持续改进
效果评估
01
评估标准
制定明确的评估标准,包括问题解决率、客户满意度、生产效率等关键
指标,以便客观地衡量8D报告的效果。
02
数据收集
收集相关的数据和信息,如问题发生频率、处理时长、资源消耗等,以
便对8D报告的执行情况进行全面分析。
03
结果分析
对收集到的数据进行分析,识别改进的机会和潜在问题,为持续改进提
避免方法包括制定具体的实施 计划、明确责任人和完成时间 、提供必要的资源支持等。
04
验证效果不佳
避免方法包括制定科学的验证 方案、收集客观的数据进行验 证、及时调整纠正措施等。
07
案例分析与实战演练
案例介绍与背景
案例来源
选取具有代表性的实际案例,涉及产品缺陷、客户投诉等问题。
质量管理8D报告培训(经典教材)含案例分析解析

供应链质量管理
随着全球化和供应链的 不断发展,供应链质量 管理将成为未来质量管 理的重点之一,确保整 个供应链的质量稳定性
和可靠性。
质量文化
质量文化将更加深入人 心,成为企业核心竞争 力的重要组成部分。企 业将更加注重培养员工 的质量意识和技能,营 造全员参与、共同关注
质量的良好氛围。
明确目标和期望
在实施8D方法前,明确解决问 题的目标和期望,使团队成员 能够有针对性地开展工作。
跨部门协作与沟通
加强团队之间的跨部门协作与 沟通,确保信息传递的准确性 和及时性。
持续改进与反馈
在实施过程中不断进行总结和反 馈,持续改进8D方法的实施效果
,提高组织的质量管理水平。
8D方法与其他质量管理方法的比较
结果
通过8D方法的实施,食品生产线的污染问题得到了有效解决,提高 了产品的安全性和消费者的健康保障。
04
8D方法解析
8D方法的优势和局限性
系统性的解决问题流程
8D方法提供了一套系统性的流程, 从发现问题到解决问题,确保问题的 全面解决。
团队协作
鼓励团队成员共同参与,发挥集体智 慧,提高解决问题的效改进生产工艺,提高材料质量,优化设备参数等,确保问题得到根本解
决。
案例一:汽车制造业的质量问题
6. 实施永久对策
将改进后的工艺、材料和设备应用于 生产,并持续监控效果。
7. 防止问题的再次发生
加强员工培训,提高质量意识,定期 对工艺、设备和材料进行检查和维护。
8. 总结和预防措施
2. 成立专项团队
组织研发、生产、品质等部门人员,共同分析并解决此问题。
案例二:电子产品生产的质量问题
01
8D报告培训教材

2.
描述 问题
实施
和验证
3.
临时
(限制)行动
4.
寻找潜在原因
选择可能 原因
N 潜在原因 是根本 原因吗?
Y
寻找可能的 解决方法
验证
5. 改进行动
实施
6.
永久性
改进行动
7.
预防
问题重现
8.
祝贺你的 小组
2021/5/27 确利达—创造企业新动力!
8
我们是谁?
我们都是同事、领导者、教练和 导师。
我们互相依赖,我们是公司的脊 梁。
2021/5/27 确利达—创造企业新动力!
50
确定和分析可能的原因
评价所有现有的有关问题的信 息和数据。 在问题被发现的同时,评价正 在发生的事件。 是什么导致了质量水平的不同?
运用分析工具:
运用数据
为了有效地解决问题 有必要对已确定的所
&
有可能原因进行调查?
先前提到的工具 因果分析图 FMEA 和控制计划 图表 过程图
验证
5. 改进行动
实施
6.
永久性
改进行动
7.
预防
问题重现
8.
祝贺你的 小组
33
请 分 析:
纠 正…… 纠正措施…… 预防措施……
2021/5/27 确利达—创造企业新动力!
34
纠正 为消除已经发现的不合格所采取的的措施 可涉及:返修,返工或降级
2021/5/27 确利达—创造企业新动力!
35
纠正措施
2021/5/27 确利达—创造企业新动力!
31
3D
实施和验证
临时(限制)行动
2021/5/27 确利达—创造企业新动力!
8DReport培训教材

3 – 为什么?
4 – 为什么? 4 – 为什么?
32
5 – 为什么? 5 – 为什么?
5Why分析公司近期案例
2品0全11年部8停月线2日。,(铜运陵5W锐H展Y解反决馈方,法我司为7什月么份会所发供生的Q?J1为00什3产么品没,有出检现测气出门来环?带为间什隙么无会法出调厂配?,)产 从法(试验、检验、探测)方面分析(为什么该问题没有被检测到)
四问:为何吃早餐晚了?
答:因为起床晚了;
五问:为何起床晚了?
答:因为忘了上闹钟了……
15
课程内容
5Why质量工具简介 5Why工具应用方法 5Why问题解决方式 5Why经典案例解析
16
5 why质量工具简介
丰田生产方式创始人大野耐一总是爱在车间走来走去,停下来向 工人发问。他反复地就一个问题,问“为什么”,直到回答令他满意, 被他问到的人也心里明白为止——这就是后来著名的“五个为什么”。
恰当地定义问题。
不断提问为什么前一个事件会发生,直到回答“没有好的理由”或直 到一个新的故障模式被发现时才停止提问。
解释根本原因以防止问题重演。
文件中所有带有“为什么”的语句都会定义真正的根源(通常需要至 少5个“为什么”)
总体5个为什么图表
问题
1 – 为什么?
1 – 原因
2 -为什么?
2 -原因
2
什么是8D?
在撰写8D报告的时候,务必要保证下面的问题被清 楚准确有理有据地回答:
D2-问题是什么? D3~D6-问题如何解决? D7-将来该问题如何预防
3
什么是8D?
务必保证以下的问题被如实回答: 1.对零件的知识进行了充分的论证 2.完全确定了根本原因并聚焦于该原因 3.遗漏点已经被识别 4.确定与根本相匹配的纠正措施 5.纠正措施计划的验证已经被确定 6.包括了实施纠正措施的时间计划 7.有证据显示供方将把纠正措施纳入整个系统。
质量管理8D报告培训(经典教材)含案例分析_2022年学习资料
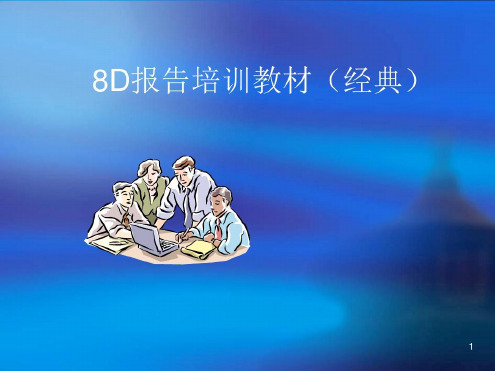
四.8D聚一D3临时对策-定义、验证和执行临时控制行动,保证在永-久纠正措施实施前,将问题与内外部顾客隔。-需要考虑的问题:-1.防止继续产生不-2减小产生的不良和-良品(减少不良品产-后续可能产生不良对-客户 影响。-14
∥NEWASIA-折-亚州州-四.8D步骤一D3临时对策-确定并执行应先采取的临时措施,以遏制外界/内部客 户问题的扩大。-临时措施的确定应考虑从供应商零件库存--供应商零件-在途品-内部零件/材料一生产制程一仓库 存一交付在-途品一客户端减少和降低(消除)后果的产生。-临时措施一直要持续实施至后续的永久对策的执行有效,方可撤消-临时措施实施中,应及时跟踪和验证其效果-15
D1--成D步骤D1建立小组-选择小组成员的准则-■选择具有相-■小组成员的-■各类成员之-■按需要调整技能、知识、-人数控制在4到-间职责、任务-团队成员-资源、权力等-10个之间-合理搭配-的人作为团队-1
四.8D素一D2问题描述-以客户的角度和观点详细描述其所感受到的问题现象,-将所遭遇的问题,以量化的方式, 明确出所涉及的人-事,时,地,为何,如何,多少-什么是问题??-期望-目标-现实-12
四.8D斐聚一D4原因分析-鱼骨图分析-员工品质意识淡薄-机-手工喷涂-标准执行-力差-人员变动大-杜邦油 性能-不良-车顶饰条附着力不良-素材表面-输送链台车-要打磨-漆渣太厚-复押半成品-喷涂房-表面粒点-环境 -未对半成品-进行检验-法-料-21
四.8D斐聚一D4原因分析->人人员相关信息是否有变更->机-设备维修保养记录-5M1E->料物料更改记录 主料、辅料)->环-温湿度记录-法工艺更改记录,-生产原始记录->测-检测条件方法人员-常用方法-1.对操 员现场询问2.现场观察-3.模拟试验-4.DO试验-5.异常记录-22
8d报告培训教材

六.結論:
• 8D格式用于監控解決問題的過程,它不是 一個詳盡的報告或複雜的分析,描述工具, 而是一個包含了解決問題的每個步驟的 集合,因而可從其中找到經提煉的基本信 息.
七. 8 D steps 8D步驟
• (1) Team: Composition of the team in charge of solving the problem
8D 方法
一.范圍:
該方法适用于解決各類可能遇到的簡單或 複雜的問題. 8D 方法就是要建立一個体系,讓整個團 隊共享信息, 努力達成目標. 8D本身不提供成功解決 問題的方法或途徑, 但它是解決問題的一個很有用 的工具.
二.目標
• 提高解決問題的效率,積累解決問題的經 驗.
• 提供找出現存的与質量相關問題的框架, 杜絕或盡量減少重復問題出現.
七. 8 D steps 8D步驟
• (5)選擇長期糾正措施 • 1) 對將要執行的長期糾正措施在實施前做
進一步的确認,以核對它們是否在實施后能提供 一個合乎期望的結果. 目的是解決問題的根源, 要防止這些糾正措施帶來任何其它的負面影響, 在這种情形下,須採取其它的措施消除負面影響. • 2)選擇或創建一個測量工具,評估在糾正過程中 各項工作的功效.
• 8D格式的原則是針對出現的問題,找出問 題產生的根本原因,提出短期,中期,和長期 對策,並采取相應行動措施.
三.定義:
• (1) 8D (8 Disciplines) 方法包含8個解決問題的步驟. 它基于使用 描述工具,格式化,分析,量化等工具,從而提供徹底解決問題的指引.
• (2)問題: 被發現的具体問題,它包括: • 1) 与正常狀況相比,屬于失常的現象,在這种情況下, 需要予以
8D报告培训教材
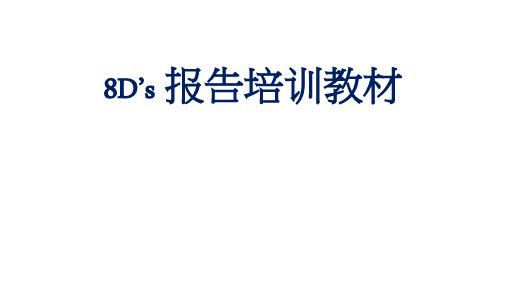
Team Problem description Short term containment actions Define and verify root cause Select permanent corrective actions Implement permanent corrective actions Actions to prevent problem recurrence Problem solved
4.7 Step 7: Actions to prபைடு நூலகம்vent problem Recurrence
•更新整个质量系统 ((Procedures,Guidelines,Specifications and Tools used concerning the problems).
•没有管理层的同意是没有办法执行的, 这是所有措施的第 一步, 然后这些措施必须立即并通过持续改善的计划去执 行。
Quality System, guidelines, procedures, instructions
1 -Team 2 –Problem description
Build the team
No Deterioration ?
Yes Document and describe
the problem
• 用5M 的方法定性并定量的定义问题发生的条件。 ( Man, Machine, Material, Method , Milieu )
• 用5W1H 来详细的描述问题 ( 附表为不同问题描述的建议)
附表:
Product Problem
Process Problem Component Problem Technology Problem
8D报告培训教材(经典)

引言:8D报告是一种常用于问题解决和质量管理的方法。
它是在上世纪80年代由美国汽车制造商提出的,并发展为一种全球普遍应用的工具。
本文将提供一份经典的8D报告培训教材,以帮助读者理解和掌握该方法的核心原则和步骤。
概述:正文内容:1.D1:建立团队1.1确定问题的召集人:由问题的负责人负责召集团队,确保问题得到适当的关注和解决。
1.2选择团队成员:团队成员应涵盖与问题相关的各个部门和专业背景,以便综合分析和解决问题。
1.3分配角色和职责:团队成员应清楚他们在团队中的角色和职责,确保每个人都能有效地贡献。
1.4设定目标与时间表:明确问题的目标和预计的解决时间,以确保整个团队朝着共同的目标努力。
1.5建立有效沟通渠道:在团队成员之间建立良好的沟通和信息共享机制,以便及时反馈和交流进展情况。
2.D2:描述问题2.1定义问题:明确问题的性质、严重程度和影响范围,确保全团队对问题有一致的理解。
2.2收集数据:收集与问题相关的数据和信息,包括问题发生的时间、地点、频率等。
2.3问题描述:利用问题描述工具(如5W1H),清晰、准确地描述问题,并尽量精确地定位问题。
2.4确定问题范围:确定问题的边界和范围,以便在后续步骤中有针对性地解决问题。
2.5确认问题的影响:评估问题对产品质量、客户满意度和运营效率等方面的影响,为后续的改进措施提供依据。
3.D3:紧急措施3.1停止损失:根据问题的严重程度,采取必要的紧急措施来避免进一步的损失和影响。
3.2隔离问题:确定问题的边界和范围,并采取措施将问题隔离,以免扩大问题的影响范围。
3.3避免重复:记录和共享已采取的紧急措施,以确保问题不会再次发生。
3.4评估措施效果:跟踪和评估已采取的紧急措施的效果,以确保其有效性和可持续性。
3.5通知相关方:在采取紧急措施后,通知相关的内部和外部利益相关方,以避免信息不对称和误解。
4.D4:根本原因分析4.1选择分析方法:根据问题的性质和数据可用性,选择合适的分析方法,如5Why、鱼骨图等。
经典 8D 培训教材

8D Method8D问题解决方法目录8D Method8D问题解决方法 (1)一.Basic of 8D 8D基本知识 (2)二. Problem solving with 8D用8D方法解决问题 (4)1). 8D Flow Chart.8D流程图 (4)2). Comments on 8D 8个步骤的注释 (5)D1 Create the problem solving team建立小组 (5)D2 Problem Description问题描述 (6)D3 Definition of containment actions确定并施行遏制措施 (7)D4 Root cause analysis分析根源原因 (8)D5 Potential corrective actions and proof of effectiveness确定可能的纠正措施,并验证其有效性 (9)D6 Introduction of corrective actions, tracking of effectiveness施行纠正措施,并跟踪其有效性 (10)D7 Preventive actions to avoid recurrence of the defect确定预防措施避免缺陷再次发生 (11)D8 Final meeting总结会议 (11)3). 1-2-14 rules. 1-2-14规则 (13)三. Quality tools for the root cause analysis 根源原因分析中常用的质量工具 (14)1. Root cause analysis根源原因分析 (14)2.Cause and effect diagram (Ishikawa)因果图 (15)一.Basic of 8D 8D基本知识.What is 8D什么是8D"8D" is a method for solving problems with 8 steps (8 disciplines).8D方法是通过8个步骤处理问题的一种方法。
8D报告编写培训资料

的DZ47-32外壳均合格。
9
D1
D2
不合格描述 成立解决小组
目的 成立解决问题所需的小组并进行小组分工
➢ 选定小组成员:
1.人数限制在4-10人 2.选取合适人员 3.根据需要变更小组成员
a.与该问题有关的人员 b.具备工艺/产品知识的人员 c.能解决问题和实施措施能力的人员 d.有相应时间参与工作的人员
生产批次管理
批次管理作用: 是有效制订紧急处置措施的前提
批次管理原则: 遵循5M1E原则,重点关注人、机、料; 重点监控工序流转、批次信息衔接
批次管理要求: 批次信息贯穿生产全过程,批次管理 需要全员参与
批次管理验证: 追溯管理,采用逆向思维
12
D1
D2
D3
不合格描述 成立解决小组 紧急处置措施
D4 根本原因分析
19
本课程的内容
一 8D基础知识 二 8D报告编写 三 8D报告现存问题
20
8D报告现存问题
➢未按时间要求提交报告 ➢小组成员资格未满足解决问题的需求 ➢根本原因没有彻底分析清楚 ➢措施没有针对根本原因制定 ➢措施制订不具体、不可量化、难执行 ➢措施不执行或部分执行 ➢未能提供合适的证据
21
8D报告评价
3 按标准化管理要求,相关措施在日常生产中给予落实执行
和推广
18
D1
D2
D3
不合格描述 成立解决小组 紧急处置措施
D4 根本原因分析
D5 长期改善措施
D6 效果验证
D7 措施标准化
D8 复发的原因
目的 8D报告最后一个阶段,确认不合格是否复发
不合格复发原因分析:
1. D3紧急处置措施,措施制订不完整或措施执行未彻底 2. D4根本原因分析不彻底或是错误 3. 改善措施在日常生产中未按要求执行
8d报告培训教材

七. 8 D steps 8D步驟
七. 8 D steps 8D步驟
• (3)短期臨時措施 • 1) 若觀察到的問題直接對產品的性能 和等級造成影響,立即采取措施(分類,重 工,延遲交貨,報廢)以确保正常生產得以 繼續進行,直到采取糾正措施將問題解決. • 2) 檢查以确保短期臨時措施有效. • 3) 若短期臨時措施有效,則實施.
8D 方法
一.范圍:
該方法适用于解決各類可能遇到的簡單或 複雜的問題. 8D 方法就是要建立一個体系,讓整個團 隊共享信息, 努力達成目標. 8D本身不提供成功解決 問題的方法或途徑, 但它是解決問題的一個很有用 的工具.
二.目標
• 提高解決問題的效率,積累解決問題的經 驗. • 提供找出現存的与質量相關問題的框架, 杜絕或盡量減少重復問題出現. • 8D格式的原則是針對出現的問題,找出問 題產生的根本原因,提出短期,中期,和長期 對策,並采取相應行動措施.
• • • •
• •
五.提交報告時間要求:
• (1) 在發現問題的24小時內,提交包含所 採取的暫時措施描述的8D報告. • (2) 在發現問題的72小時內,提交包含問 題發生原因的初步分析的8D報告.
六.結論:
• 8D格式用于監控解決問題的過程,它不是 一個詳盡的報告或複雜的分析,描述工具, 而是一個包含了解決問題的每個步驟的 集合,因而可從其中找到經提煉的基本信 息.
七. 8 D steps 8D步驟
• (6)執行長期糾正措施 • 1) 執行長期糾正措施,更新相關文件. • 2) 長期糾正措施的功效可通過觀察問 題是否重復出現來評估.
七. 8 D steps 8D步驟
• (7)預防問題重復出現措施 • 1) 修正整個質量系統(特別是問題相 關的程序,技術說明書,工作說明書). • 2) 管理層同意並修正整個質量系統, 是該過程的第一步,該過程或立即開始實 施,或是一個不斷改進的計划.
8D报告培训教材

一.什么是8D
此措施以团队运作导 向以事实为基础,防 止个人主见之介入, 使问题之处理能更具 条理。
面对问题应群策群力, 相互帮助、相互提拔、 如此才干彻底处理问题。
5
二.为何要推行8D
通过建立小组训练内部合作的技 巧。
提供问题有效解决的方法。
防止相同或类似问题的再发生。
提高顾客满意度,增强其对供方 的产品和过程的信心 。
建立小组需要考虑旳要素:
小组旳领导: 小组旳资源: 小组旳组员: 人员旳数量:
谁来推动? 谁提供支持? 合作及分工? 多少为宜?
D1—四成.立8工D环作团节队—D1建立小组
选择小构成员旳准则
小构成员旳人数 控制在4到10个 之间
选择具有相 应技能、知识、 资源、权力等 旳人作为团队 组员
各类组员之 间职责、任务 合理搭配
8D报告培训教材
Boge
课堂纪律
1. 手机请关机或调成静音。 2. 请保持课堂平静,请勿交头接耳或大声讲话。 3. 如有问题请会后交流 。
一.什么是8D 二.为何要推行8D 三.何时采用8D 四.8D环节 五. 8D改善案例 结束语
目录
一.什么是8D
8D 旳原名叫做 8 Disciplines,又称团队导向问 题处理措施。是由福特企业始创,全球化品质管 制及改善旳特殊必备措施,之后已成为QS9000/ ISO TS16949、福特企业旳特殊要求。但凡做福 特旳零件,必需采用 8D 作为品质改善旳工具, 目前有些企业并非福特旳供给商或汽车业旳合作 伙伴,也很喜欢用这个以便而有效旳措施处理品 质问题,成为一种固定而有共识旳原则化问题处 理环节。
8
恭贺小组
四. 8D环节—D0问题初步了解
8D报告培训教材(经典)

析和方案策划。
四. 8D步骤—D1建立小组
建立一个小组来解决问题和执行纠正计划, 小组成员应具有过程和/或产品知识、分配的 时间、权威和需要的技能。
建立小组需要考虑的要素:
小组的领导: 小组的资源: 小组的成员: 人员的数量:
谁来推动? 谁提供支持? 合作及分工? 多少为宜?
备注:广泛用于QS9001/ ISO9001/ TS16949 (变更为
IATF16949/VDR6.3)解决质量问题的8D isciplines。
一.什么是8D
以团队运作导向以事 实为基础,避免个人 主见之介入,使问题 之解决能更具条理。
面对问题应群策群力, 互相帮助、相互提拔、 如此才能彻底解决问题。
• 确定并执行应先采取的临时措施,以遏制外界/内部客 户问题的扩大。
• 临时措施的确定应考虑从供应商零件库存---供应商零 件在途品--内部零件/材料—生产制程—仓库储存—交 付在途品—客户端减少和降低(消除)后果的产生。
• 临时措施一直要持续实施至后续的永久对策的执行有 效后,方可撤消。
• 临时措施实施中,应及时跟踪和验证其效果。
五.8D改善案例
D0.了解问题
2009年11月4日“众盛精密机械厂”投诉,在其包装 车间对“ALT-5检测器”进行包装时,使用公司的MHT 机用膜时一拉就断裂, 并发现使用的机用膜端口破裂 。造成ALT-5检测器包装工作进度延误,顾客要求派 人处理。
五.8D改善案例
D1.成立小组
•按问题涉及范围确定小组成员: •责属单位:生管部、业务部、仓储部、品管部 •责属人员:
五.8D改善案例
D5.长期对策
5.1决定采用长期对策
质量管理8D报告培训含案例分析

3.验证 预防再发 对策有效 后,可以 停止临时 措施。
四. 8D步骤-D7效果确认及标准化
验证预防再发对策并监控长期的效果。 水平展开,以防同一问题及类似问题再 度发生。将相关对策形成书面文件(管 理制度、程序文件、作业指导书、表单、 技术文件、工程图纸等)。
质量管理8D报告培训含案例分析
五.8D改善案例
D0:发生时间线
(Time-Line)
12/08 8:25 动力运行金晓 栋从5#动力栋 赶至2#1F现场
12/08 8:31
12/08 8:32
动力运行金晓栋 金晓栋与曹健东手
至屋顶机房复位 动开启电梯轿厢门,
后返回1F现场 14名被困人员解困
12/08 8:50 签约单位 维修人员 赶至现场
四. 8D步骤—D2问题描述
问题描述方法:5W/2H
WHO WHAT
5W2H 谁
什么
解释 识别那一个客户(内/外部)在抱怨
问题的症状,无法用文字描述清楚的,借助 于数字或图片将问题表达清楚
WHEN WHERE WHY HOW
何时 何地 为什么 怎么样
记入问题发生的日期 记入问题发生的场所 识别已知的解释 在什么的模式或状态这问题会发生
四. 8D步骤-D8恭贺小组(结案)
恭贺小组的每一成员,问题解决完成,对小 组成员的努力予以肯定。
对所有积极参与的小组成员 进行适当的承认
对小组的效益进行沟通和文件化
质量管理8D报告培训含案例分析
四. 8D步骤
注意事项 上述各项步骤,不一定必须完全依序进行,各步骤之顺 序可因个别问题而异。
质量管理8D报告培训含案例分析
8D报告培训教材

8D 方法
一.范圍:
該方法适用于解決各類可能遇到的簡單或 複雜的問題. 8D 方法就是要建立一個体系,讓整個團 隊共享信息, 為努力達成目標. 8D本身不提供成功解 決問題的方法或途徑, 但它是解決問題的一個很有 用的工具.
二.目標
• 提高解決問題的效率,積累解決問題的經 驗. • 提供找出現存的与質量相關問題的框架, 杜絕或盡量減少重復問題出現. • 8D格式的原則是針對出現的問題,找出問 題產生的根本原因,提出短期,中期,和長期 對策,並采取相應行動措施.
四.在下列情形中須提交8D報告:
• • (1)當客戶在工厂現場的稽核中發現不合格項或缺陷時, 對于嚴重 不良,主要不良及重複發生的次要不良須提交8D報告. (2)OQC發現嚴重不良,主要不良及重複發生的次要不良時須提交 8D報告. (3)當市場上發現有重複發生的產品缺陷時須提交8D報告. (4) 當ORT測詴過程中發現缺陷時須提交8D報告. (5)IPQC在同一生產現場連續發現三個相同不良現象或三個相同 不良現象 (6)要對那些需要長期糾正措施來解決的缺陷采取行動時須提交 8D報告. (7)被程序文件定義要求8D報告其他情形.
七. 8 D steps 8D步驟
• (8) 項目完畢 • 1) 關注的問題被解決,确認,核實,和紀 錄被權威人士審核通過.
八.推薦的流程
八.推薦的流程
附圖--1
附圖--2
附圖--3
附圖--4
七. 8 D steps 8D步驟
• (4) 定義和核實原因 • 1) 從問題描述中尋找最有可能的一些原因,若有可 能,做一些測詴幫助尋找原因. • 2) 檢查所有考慮到的可能原因, 將它們會帶來的結 果与觀察到的結果比較, 原因/結果矩陣圖可幫助選擇 优先考慮哪個原因. • 3) 識別問題的种類.(設計,程序,製程,材料,人員技巧). • 4) 探尋可能的解決方案,列出可行性,效果,實施時間 等. • 5) 建立將要實施的那些措施的檢驗標准. • 6) 盡量利用各种圖表
- 1、下载文档前请自行甄别文档内容的完整性,平台不提供额外的编辑、内容补充、找答案等附加服务。
- 2、"仅部分预览"的文档,不可在线预览部分如存在完整性等问题,可反馈申请退款(可完整预览的文档不适用该条件!)。
- 3、如文档侵犯您的权益,请联系客服反馈,我们会尽快为您处理(人工客服工作时间:9:00-18:30)。
• 识别可能的解决方案。
– 修改搬运、贮存作业方法,将原来搬运 和堆放高度3层改为 2层,减少重力。 – 改变包装方法,每卷产品用托盘运装。 – 包装箱内部增加泡沫,以减少碰撞冲力。 – ……。
五.8D改善案例
D5.长期对策
5.1决定采用长期对策
四. 8D步骤—D4原因分析
深入明 确问题
进一步明确问题
(不良解析)
各个可疑原因排查
对现场人机料环法 测进行观察测量, 有历史数据的对数据 进行初步分析
从流程分析
(流程图)
团队协 作:
列出所 有可能 的疑点
关键原因确认
统计分析 DOE验证 机理分析
疑 点 验 证
质量问题5M1E分析
(鱼翅图分析)
关键原因-是否为根本原因
临时措施
消除问题及后果
只能治标 (可能再发)
长期措施
消除问题原因
可以治本 (不会再发)
四. 8D步骤—D4原因分析
用统计工具列出可以用来解释问题起因的所 有潜在原因,再分别针对每一可能原因予以 测试,最终确定产生问题的根本原因。
需要考虑的问题:
1.列可能 原因时要 周全。 2. 原因和结 果要有论证, 说得通。 3.原因一定是根本 原因,而非表面 原因。
选取最佳的的长期对策来解决根本原因。 同时也选取最佳的长期对策来控制根本原 因的影响。
需要考虑的问题:
1. 一定是针对根本原 因来制定措施,一个 原因可能有几条措施。 2.必要时对已 经明确的措 施进行验证。 3.措施 尽量具 体化。
四. 8D步骤—D6预防再发对策
计划和执行选取的预防再发对策。去除 临时行动。 需要考虑的问题:
总计
23
100
五.8D改善案例 4.2确定选择最有可能的原因
端 口 破 15 损 数
20 69.56 52.17
86.93
100 % 75 50
10 5 0
25
0 A B C D E F G
H
五.8D改善案例
4.3 确定根本原因并识别可能的方案
• 通过小组因果分析,验证统计确定产品堆放高度过高 、包装方式不合理是导致产品端口受损根本原因。
WHY 中间原因
WHY 根本原因
四. 8D步骤—D4原因分析
5-WHY分析案例1
状态1
一辆汽车出了故障不能行驶(WHY1)
引擎故障(WHY2) 火花塞不点火(WHY3)
状态2-原因1 状态3-原因2
状态4-原因3
状态5-原因4
火花塞潮湿沾水(WHY4)
引擎盖密封差漏水(WHY5) 密封圈老化
状态6-原因5
什么程度 问题发生的程度、量
13
四. 8D步骤—D3临时对策
定义、验证和执行临时控制行动,保证在永 久纠正措施实施前,将问题与内外部顾客隔 离。
需要考虑的问题:
1.防止继续产生不 良品(减少不良品产 生)。
2.减小产生的不良和 后续可能产生不良对 客户的影响。
四. 8D步骤—D3临时对策
• 确定并执行应先采取的临时措施,以遏制外界/内部客 户问题的扩大。 • 临时措施的确定应考虑从供应商零件库存---供应商零 件在途品--内部零件/材料—生产制程—仓库储存—交 付在途品—客户端减少和降低(消除)后果的产生。 • 临时措施一直要持续实施至后续的永久对策的执行有 效后,方可撤消。 • 临时措施实施中,应及时跟踪和验证其效果。
四. 8D步骤-D7效果确认及标准化
效果确认 实事求是,以事实和数据为依据,对数据用统计工具处 理后得出相应的结论,不应未做对比分析即判定效果。
16.00% 14.00% 12.00% 10.00% 8.00% 6.00% 4.00% 2.00% 0.00%
slot1
slot2
slot3
slot4
• 经确认后,没有不良品再流出的可能,不会再扩大损 失。
五.8D改善案例 D4. 原因分析
• • • • 识别可能原因(因果图) 选择最有可能的原因(矩阵图) 确定是否是根本原因 识别可能方案
五.8D改善案例 4.1 因果分析
环
库房湿度大
法
速度设定多快 包装方式不合理
产品堆放高度过高
端 面 受 伤 PE强度不稳定
小组成员的 人数控制在4到 10个之间
四. 8D步骤—D2问题描述
以客户的角度和观点详细描述其所感受到的问题现象, 将所遭遇的问题,以量化的方式,明确出所涉及的人, 事,时,地,为何,如何,多少。
什么是问题???
期望 问题
期望 目标
现实
四. 8D步骤—D2问题描述
问题描述方法:5W/2H
5W2H WHO WHAT WHEN WHERE WHY HOW HOW MUCH 谁 什么 何时 何地 为什么 怎么样 解释 识别那一个客户(内/外部)在抱怨 问题的症状,无法用文字描述清楚的,借助 于数字或图片将问题表达清楚 记入问题发生的日期 记入问题发生的场所 识别已知的解释 在什么的模式或状态这问题会发生
小组的领导: 小组的资源: 小组的成员: 人员的数量: 谁来推动? 谁提供支持? 合作及分工? 多少为宜?
D1—成立工作团队
四. 8D步骤—D1建立小组
选择小组成员的准则
选择具有相 应技能、知识、 资源、权力等 的人作为团队 成员 各类成员之 间职责、任务 合理搭配 按需要调整 团队成员
四. 8D步骤—D4原因分析
5-WHY分析案例2
状态1
生产线现场油污操作员行走滑倒
WHY1
状态2-原因1
状态3-原因2
机器漏油
机器橡胶密封不好
WHY2
WHY3
状态4-原因3
状态5-原因4 状态6-原因5
密封橡胶圈质量差
密封橡胶圈过期老化
WHY4
WHY5
未规定橡胶圈期限和检查
四. 8D步骤—D5长期对策
对所有积极参与的小组成员 进行适当的承认
对小组的效益进行沟通和文件化
四. 8D步骤
注意事项 上述各项步骤,不一定必须完全依序进行,各步骤之顺 序可因个别问题而异。
五.8D改善案例
D0.了解问题
1999 年 11 月 4 日客户“浙江精密机械厂”投诉,在其 包装车间对“ALT-5检测器”进行包装时,使用公司的 MHT机用膜时一拉就断裂, 并发现使用的机用膜端口 破裂。造成 ALT-5检测器包装工作进度延误,顾客要 求派人处理。
一.什么是8D
此方法以团队运作导 向以事实为基础,避 免个人主见之介入, 使问题之解决能更具 条理。
面对问题应群策群力, 互相帮助、相互提拔、 如此才能彻底解决问题。
5
二.为什么要推行8D
通过建立小组训练内部合作的技 巧。 提供问题有效解决的方法。
防止相同或类似问题的再发生。 提高顾客满意度,增强其对供方 的产品和过程的信心 。
四. 8D步骤—D3临时对策
纠正措施(对策)
为消除已发现的不合格或其它不期望情况的原因所采取 的措施。
预防措施(预防再发对策)
为消除潜在不合格或其它潜在不期望情况的原因所采取 的措施。
预防措施与纠正措施的区别
采取纠正措施是为了防止发生,而采取预防措施是为了防 止再发生。
四. 8D步骤—D3临时对策
三. 何时采用8D
重复发生,一直没有解决的问题 何时 采用 8D
比较重大的制程品质问题
客户要求回复的品质投诉
四. 8D步骤
原因分析
0 1
问题初步了解
4
确定可能原因
5
长期对策
建立小组
选择最可能原因
6
预防再发对策
2
问题描述
NO
最有 可能的原因 是否是根本 原因?
YES
7 效果确认及标准化
3
临时对策
确定根本原因
slot5
改善前
改善后
数据来源: 时 间:
数据点多按日期来建议走势图,数据点少可用上面的柱状图
四. 8D步骤-D7效果确认及标准化
标准化
标准化是把企业所积累的技术、经验,通过 文件的方式进再发、 教育训练。
四. 8D步骤-D8恭贺小组(结案)
恭贺小组的每一成员,问题解决完成,对小 组成员的努力予以肯定。
8
恭贺小组
四. 8D步骤—D0问题初步了解
问题初步了解(立项和准备工作)
– 鉴定是否有进行8D 的必要; – 立项和确定主题; – 收集资料。
此过程尽量获取内部 和外部的问题信息、 数据、进行初步的分 析和方案策划。
四. 8D步骤—D1建立小组
建立一个小组来解决问题和执行纠正计划, 小组成员应具有过程和/或产品知识、分配的 时间、权威和需要的技能。 建立小组需要考虑的要素:
5-WHY分析
四. 8D步骤—D4原因分析
鱼骨图分析
员工品质意识淡薄 手工喷涂
标准执行 力差 人员变动大
杜邦油漆性能 不良
输送链台车 漆渣太厚
素材表面 要打磨 喷涂房 环境差 复押半成品 表面粒点 未对半成品 进行检验
四. 8D步骤—D4原因分析
人--人员相关信息是否有变更 机--设备维修保养记录, 5M1E 分析 料--物料更改记录(主料、辅料) 环--温湿度记录 法--工艺更改记录,生产原始记录, 测--检测条件方法人员
8D报告培训教材
Boge 2012.08.15
课堂纪律
1. 手机请关机或调成静音。 2. 请保持课堂安静,请勿交头接耳或大声讲话。 3. 如有问题请会后交流 。
目录
一.什么是8D 二.为什么要推行8D 三.何时采用8D
四.8D步骤
五. 8D改善案例 结束语
一.什么是8D
8D 的原名叫做 8 Disciplines,又称团队导向问 题解决方法。是由福特公司始创,全球化品质管 制及改善的特殊必备方法,之后已成为QS9000/ ISO TS16949、福特公司的特殊要求。凡是做福 特的零件,必需采用 8D 作为品质改善的工具, 目前有些企业并非福特的供应商或汽车业的合作 伙伴,也很喜欢用这个方便而有效的方法解决品 质问题,成为一个固定而有共识的标准化问题解 决步骤。