QA-3-024A 多晶156 220对角电池片测试分选标准
电池片等级划分标准
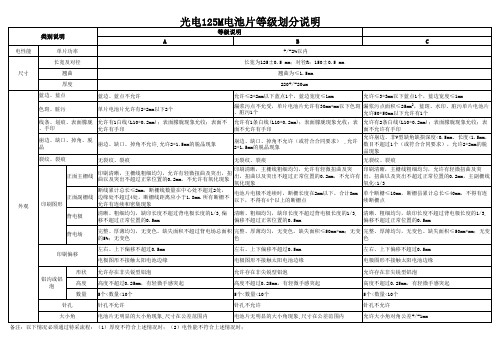
备注:以下情况必须通过特采流程:(1)厚度不符合上述情况时;(2)电性能不符合上述情况时;
硅太阳电池检验标准
1、 太阳电池的外观检验
a) 单晶硅电池,与表面成35°角日常光照情况下观察表面颜色,呈“褐;紫;兰”三色,目视颜色均匀,无明显色差、水痕
b) 多晶硅电池,与表面成35°角日常光照情况下观察表面颜色,呈“褐;紫;兰”三色,目视颜色均匀,无明显色差、水痕、手印。
c) 电极图形清晰、完整、无断线。
背面铝背电极完整,无明显凸起的“铝珠。
d) 电池受光面不规则缺损处面积小于1mm2,数量不超过2个。
e) 电池边缘缺角面积不超过1mm2,数量不超过2个。
f) 电池片上不允许出现肉眼可见的裂纹。
g) 正放电池片于工作台上,以塞尺测量电池的弯曲度,“125片”的弯曲度不超过0.75mm,
4、检验规则
a) 太阳电池电性能进行在线100%检验,根据转换效率和工作电流分档。
b) 太阳电池外观检验进行在线100%检验
c) 其它项目的抽样方案按GB2828中规定采用正常一次抽样方案。
检查水平为S-1、合格质量水平(AQL=2.5)
5、太阳电池的运输、贮存
在有外包
、水痕、手印。
、水痕、手印。
电池片分档标准
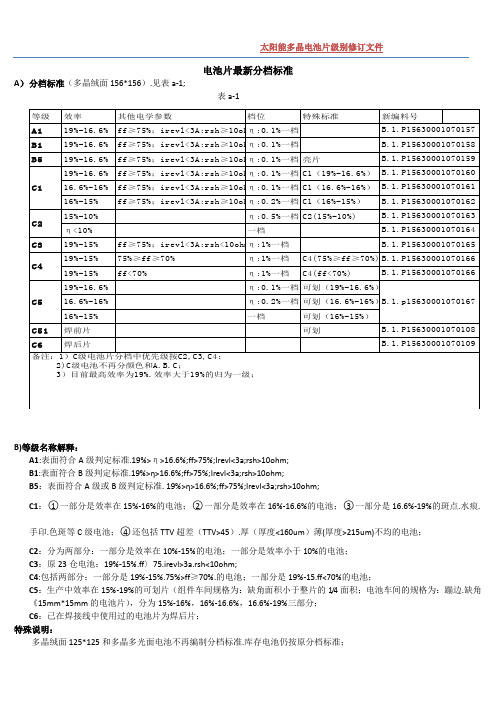
太阳能多晶电池片级别修订文件
电池片最新分档标准
A)分档标准(多晶绒面156*156).见表a-1;
表a-1
B)等级名称解释:
A1:表面符合A级判定标准.19%>η>16.6%;ff>75%;Irevl<3a;rsh>10ohm;
B1:表面符合B级判定标准.19%>η>16.6%;ff>75%;Irevl<3a;rsh>10ohm;
B5:表面符合A级或B级判定标准. 19%>η>16.6%;ff>75%;Irevl<3a;rsh>10ohm;
C1:○1一部分是效率在15%-16%的电池;○2一部分是效率在16%-16.6%的电池;○3一部分是16.6%-19%的斑点.水痕.
手印.色斑等C级电池;○4还包括TTV超差(TTV>45).厚(厚度<160um)薄(厚度>215um)不均的电池;
C2:分为两部分:一部分是效率在10%-15%的电池;一部分是效率小于10%的电池;
C3:原23仓电池:19%-15%.ff〉75.irevl>3a.rsh<10ohm;
C4:包括两部分:一部分是19%-15%.75%>ff≥70%.的电池;一部分是19%-15.ff<70%的电池;
C5:生产中效率在15%-19%的可划片(组件车间规格为:缺角面积小于整片的1/4面积;电池车间的规格为:蹦边.缺角《15mm*15mm的电池片),分为15%-16%,16%-16.6%,16.6%-19%三部分;
C6:已在焊接线中使用过的电池片为焊后片;
特殊说明:
多晶绒面125*125和多晶多光面电池不再编制分档标准.库存电池仍按原分档标准;。
电池片外观检验标准

1.0 适用范围 1.1 这份标准适用于本公司电池片部门生产的所有太阳能电池片。
1.2 适用于单晶/多晶电池片的生产,标准生产次序包括: 镀SiN 减反射镀膜以及丝网印刷。
1.3 外观检测分为三个等级,Q1,Q2,Q3。
Q1是最高品质等级,Q2稍低于Q1,Q3仅适用于切割电池片后做成小组件,供应给有特殊需要的顾客。
2.0 定义: 2.1 减反射膜ARC: 电池片受光面所涂的一层减少阳光反射的膜。
2.2 表面污染:电池表面沉淀物。
2.3 崩边片:边沿缺失厚度方向没有贯穿整片电池片厚度。
2.4 缺角:边沿缺失厚度方向贯穿整片电池片厚度。
3.0 检验基础: 3.1 条件: 3.1.1 检验员应有正常的视力,无色盲。
无需放大镜。
3.1.2 色差在室内正常光线下,目视;其他用直尺(游标卡尺)测量。
3.1.3 检查距离:0.3~0.5米 (一个手臂的距离), 角度:30-90°。
3.1.4 检查时间: 每个部分3~5秒。
3.2 工具:直尺、游标卡尺 3.3 规则图形(如圆形、正方形、长方形)的面积按不良实际面积计算。
4、检验项目及要求 类别 Q1级Q2级Q3级外形尺寸125*125(±0.5)mm, 125*125(±0.5)mm,无分类 156*156(±0.5)mm, 156*156(±0.5)mm,主栅线、背电极按供应商图纸主栅线、背电极按供应商图纸Q1级Q2级Q3级减反射膜色差深蓝色、中蓝色、淡蓝色发白的兰色或浅蓝发白的蓝色/浅蓝颜色均匀一致,无明显颜色过渡的区域, 明显色差的单个面积≤4mm2 ,总面积≤10mm2,边缘细栅线之外的色差面积≤20mm21:单一色差最大区域10mm X10mm+1个多种色差最大区域5mm X 5mm单片电池≤有2种色差区域2:刻蚀过刻引起的色差。
单一色差最大区域10mm X10mm+2个多种色差最大区域5mm X 5mm小白点数量≤3个,且每个小白点的区域为0.5mmX0.5mm。
电池片外观判定指导书

深圳XX有限公司
缺角电池片品质判定指导书
缺角范围
使用范围
允许使用数 量
样品: 不允许使用
0片
折叠板:单片板上允许出现1片,
1:单晶缺角宽 一套折叠板上只能接收2片此范围的缺角,
2片
度≤1.0mm 但不允许2片同时存在200*200mm的范围内
深度≤1.0mm
常规组件:小于100W的组件:单片板上可以 接收数量少于2片,大于100W(含100W)的 组件,单片板上可以接收数量少于4片(但 不允许2片缺角同时出现在200*200mm的范围 内)
2-4片(黑色 背板的数量 可以放宽2-3
片)
深
度
2:单晶缺角范 围深度超过栅线 边缘
此类缺角不能做整片使用,需要进行分类 后,进行切割使用
0片
3:单晶缺角范 围深度未超过栅 线边缘,宽度小 于10mm以内的
此类缺角在使用前划片房要做背后贴胶纸用 黑色油性笔做修补工作,拉线各工序发现类 似的电池片片
备注:切割电池片所造成的切割缺口或是锯齿状现象,其参照标准还是依据上述单晶第1条款执行,对 于造成切割电池片缺口或是锯齿状的异常现象,划片房要及时调整机器的运行,监督操作工人的掰片手 法,严格控制此类不良现象的发生和流入到生产线上,鉴于我司目前还没有合适的方式来弥补多晶电池 片缺角的颜色问题,所以要求划片房在选配电池片时一定要对多晶电池片进行仔细把控,可以对出现崩 边缺角的多晶电池片采用集中切边的方式来控制,保证组件的外观。
制表:
审核:
XX有限公司
片品质判定指导书
4:单晶缺角范 围深度未超过栅 此类电池片则要集中同一方向,采用切边的 线边缘,宽度大 方式进行处理后方可以流入生产线 于10mm以上的
电池片外观检验标准

太阳能电池板检验标准
1目的
对太阳能电池板进行质量监控,确保电池板外观满足客户的要求;
2范围
适用于太阳能电池板检验
3定义
无
4内容:
检验方法及标准
按表1所有项目进行检验;
室内整机目检工位800~1200Lux.必需配带良好静电防护措施配带干净手套或者静电指套与防静电手环接上静电接地线.大概离眼睛30-40cm的距离.先保持机台检查面与视线垂直,上下翻转大于45度;左右翻转大于45度.每个面检查大概5秒,视力要求:检验人员裸视或矫正视力以上.
检验工具
卡尺,菲林片
5 检验标准
表1 多晶电池片外观检验标准。
电池片外观检验标准
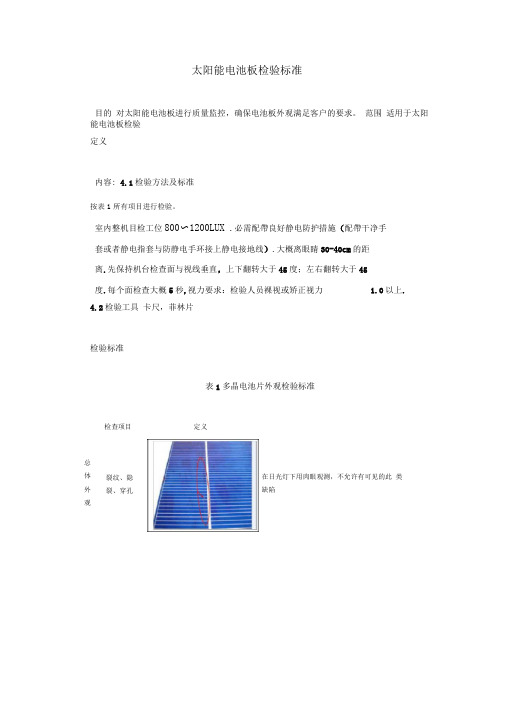
太阳能电池板检验标准目的对太阳能电池板进行质量监控,确保电池板外观满足客户的要求。
范围适用于太阳能电池板检验定义内容: 4.1检验方法及标准按表1所有项目进行检验。
室内整机目检工位800〜1200LUX .必需配帶良好静电防护措施(配帶干净手套或者静电指套与防静电手环接上静电接地线).大概离眼睛30-40cm的距离.先保持机台检查面与视线垂直,上下翻转大于45度;左右翻转大于45度.每个面检查大概5秒,视力要求:检验人员裸视或矫正视力 1.0以上.4.2检验工具卡尺,菲林片检验标准表1多晶电池片外观检验标准检查项目总体外观裂纹、隐裂、穿孔在日光灯下用肉眼观测,不允许有可见的此类缺陷定义缺口正面崩边在日光灯下用肉眼观测,明显可见的缺损不允许在日光灯下用肉眼观测,明显可见的破损不允许缺口不伤及栅线背面崩边尺寸偏差弯曲度备注:跟边框平行方向为长,垂直方向为宽备注:跟边框平行方向为长,垂直方向为宽单个V 1mm宽X2mm长,个数w 2个,但是间距大于30mm电池片边长的测量值与标称值的最大允许差值。
单个w 1mm宽X1 mm长,个数w2个;深度不超过电池片厚度的2/3 ;间距大于30mm深度不超过电池片厚度的2/3,,单个w1mm宽X 2mm长且个数w 1个;单个w 1mmx1mm个数w 2,主栅线端点边缘没有崩边单个v 1mm宽X3mm长,个数w 3个<± 0.5mm <± 1mm超过B级标准的完整电池片超过B级标准的完整电池片超过B级标准的完整电池片156电池的弯曲度w 2mm(200im)或w 2.5mm(180im);125电池的弯曲度w 1.5mm(200im)或w 2 mm(180im)156电池的弯曲度W 2.5mm(200 am)或w3mm( 180jim);125电池的弯曲度w 2mm(200 im)或w2.5 mm(180a m)超过B级标准的完整电池片色差电池片内和片间的颜色均匀一致同为蓝色.由浅到深分为4种膜色,检验以样片为准存在不明显色差,面积不超过总电池面积的1/6超过B级标准的完整电池片正面划痕斑点水印清洗过刻手印w 10mm 个数w 2 个1.单个白斑面积w 3mm,个数w 1个;2.黑油斑:允许;3.类油斑:个面积mm2允许1个单个面积w3mm,个数w 1个不伤及栅线允许正视1米看不明显的浅色手印,大小w 5mnt< 5mm允许一处1.单个白斑w5mm且个数w 3个2.黑油斑:许;3.类油斑:不允单个mm2单个白色水印面积w 5mm,个数w3个大小< 5mmx5mm,个数w 3个超过B级标准的完整电池片超过B级标准的完整电池片超过B级标准的完整电池片超过B级标准的完整电池片超过B级标准的完整电池片细栅线断开正面主栅线漏印正面主栅线脱落正面印刷偏移漏浆主栅线清晰完整,均匀连续断栅长度介于断栅长度介于0.5mm-1mm 且0.5mm-1mm且个个数W 2个;数W 2个;分分散的断栅V 散的断栅介于0.5mm且个数0.1mm-0.5mm 且< 5个;同一根个数W 5个;允栅线不允许有许V 0.1mm断栅两处断栅。
实训任务2 电池片的电性能测试和分选
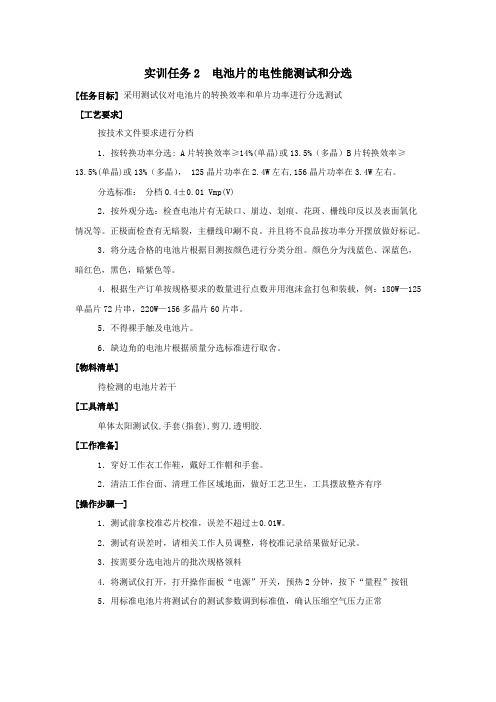
实训任务2 电池片的电性能测试和分选[任务目标]采用测试仪对电池片的转换效率和单片功率进行分选测试[工艺要求]按技术文件要求进行分档1.按转换功率分选: A片转换效率≥14%(单晶)或13.5%(多晶)B片转换效率≥13.5%(单晶)或13%(多晶), 125晶片功率在2.4W左右,156晶片功率在3.4W左右。
分选标准:分档0.4±0.01 Vmp(V)2.按外观分选:检查电池片有无缺口、崩边、划痕、花斑、栅线印反以及表面氧化情况等。
正极面检查有无暗裂,主栅线印涮不良。
并且将不良品按功率分开摆放做好标记。
3.将分选合格的电池片根据目测按颜色进行分类分组。
颜色分为浅蓝色、深蓝色,暗红色,黑色,暗紫色等。
4.根据生产订单按规格要求的数量进行点数并用泡沫盒打包和装载,例:180W—125单晶片72片串,220W—156多晶片60片串。
5.不得裸手触及电池片。
6.缺边角的电池片根据质量分选标准进行取舍。
[物料清单]待检测的电池片若干[工具清单]单体太阳测试仪,手套(指套),剪刀,透明胶.[工作准备]1.穿好工作衣工作鞋,戴好工作帽和手套。
2.清洁工作台面、清理工作区域地面,做好工艺卫生,工具摆放整齐有序[操作步骤一]1.测试前拿校准芯片校准,误差不超过±0.01W。
2.测试有误差时,请相关工作人员调整,将校准记录结果做好记录。
3.按需要分选电池片的批次规格领料4.将测试仪打开,打开操作面板“电源”开关,预热2分钟,按下“量程”按钮5.用标准电池片将测试台的测试参数调到标准值,确认压缩空气压力正常6.将要测试的电池单片放到测试台上进行分选测试。
将待测电池芯片有栅线一面向上,放置在测试台铜板上,调节铜电极位置使之恰好压在电池芯片的主栅极上,保证电极接触完好。
踩下脚阀测试。
根据测得的电流值进行分档。
7.将分选出来的电池片按照测试的数值分合格与不合格两类,并放在相应的盒子里标示清楚。
合格电池片在检测后按每0.05W分档分开分类放置8.测试完成后整理电池片,每100片作为一个包装,清点好数目并做相应的数据记录9.作业完毕,按操作规程关闭仪器[操作步骤二]检查电池片有无碎裂后隐裂[注意事项]1.在测试前,要对测试仪进行效准标准片,一定保证测试数据的准确性.2.分选电池片要轻拿轻放,降低损耗.分类和摆放时要按规定放在指定的泡沫盒或区域内.3.装盒和打包时要再检查一次数目,要确保包装的完整性.4.测试过程中操作工必须戴上手指套,禁止不戴手指套进行测试分选5.测试分选后要整理电池片,禁止合格与不合格的电池片混合参杂。
多晶外观质量标准
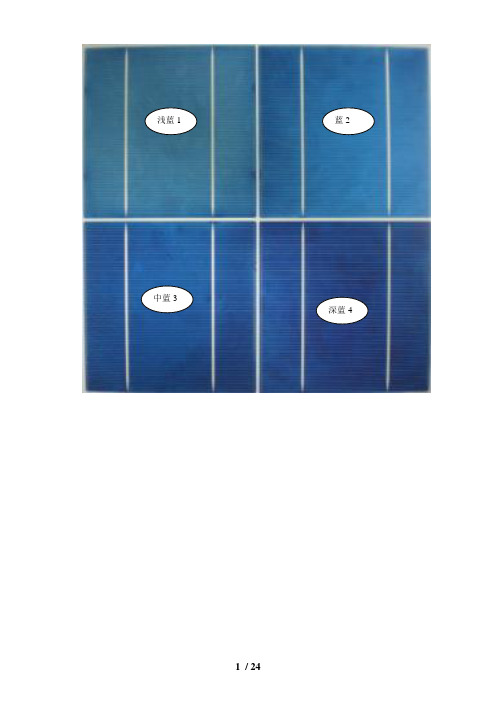
检查项目
合格标准
总体外观
1.1破损(包括裂纹)
在日光灯下用肉眼观测明显可见的破损不允许
1.2缺损(包括缺口及孔洞)
在日光灯下用肉眼观测明显可见的缺损不允许
1.3正面崩边(单面缺失)
深度不超过电池片厚度的2/3,单个≤1mm宽*1 mm长,个数≤2个。
1.4背面崩边(单面缺失)
单个<1mm宽×2mm长,且同一电池片上≤2处,但是间距大于30mm。
b、线状:单个≤2mm宽*5mm长,个数≤6个
★
4.7背场脱落
不允许
不允许
★
4.8背面主栅线及背面电场偏移
a.左右偏移:印刷两边距离的差≤1mm,且浆料不能接触到电池片的边缘;
b.角度偏移:最大距离与最小距离的差≤0.5mm
a.左右偏移:印刷两边距离的差≤1mm,且浆料不能接触到电池片的边缘;
b.角度偏移:背场与边缘的最小距离>0.5mm
要求电池片颜色均匀,不允许电池片正表面或边角不允许有明显发黄
★
2.2正面划痕
≤10mm,个数≤2个
≤20mm,个数≤2个
★
2.3斑点
1.单个白斑面积≤3mm2,个数≤3个;
2.黑油斑:不允许;
3.类油斑:单个面积≤5 mm2允许1个;单个面积≤3 mm2允许3个
1.单个白斑≤5mm2且个数≤3个
2.黑油斑:不允许;
★
3.7栅线粗细不均
正面细栅线印刷或边框栅线印刷有粗细不均的现象
a.允许边框栅线印粗(明显白色浆料)宽度≤2*栅线宽度;
b.边框栅线拖影(浆料拖影呈半透明状)1米不可见允许;1米距离可见拖影宽度≤2*栅线宽度;
c.中间单根栅线印粗:印粗长度≤1/4细栅线长度;
多晶电池片外观分级标准—版本1

多晶电池片外观分级标准文件编号 Q/BEST G 08001-2010 版本号01实施日期 2011-1-1 页 次1/4批 准审核编 制 1 目的本标准规范本公司多晶电池片外观质量要求,统一多晶电池片外观分级标准,方便公司生产、控制及提高产品质量,并为多晶电池片的使用、销售提供依据。
2 适用范围本标准适用于本公司生产的所有多晶电池片,包括自用电池片、代加工电池片、对外销售的电池片(如客户有特殊要求做另外规定)。
3 检查工具及条件: a.检验工具:PVC 手套、口罩、日光灯、水平台、塞规、卡尺、污点对比卡、塑料垫片、插片盒。
b.检验条件:1、照度800lux 日光灯下;2、洁净水平的检验台,双手佩戴PVC 手套,轻拿轻放;4 术语、定义A+级:可供直接销售。
A 级:用于本公司生产组件,但不能做电池片A+级电池片对外销售。
A-级:不能用于本公司生产电池组件,但可做销售处理及做小组件。
B 级:存在严重缺陷,可利用率极低,但可对特殊要求的客户销售。
报废:不能作为电池片销售和利用。
5 外观要求电池片外观、性能、效率根据其缺陷情况分为A+级、A 级、A-级、B 级、废片五种,各级别的判定方法如表1。
实施日期2011-1-1 页次2/4表1序号项目级别及外观要求A+ A A- B1弯曲度180~220um125≤2.0mm156≤2.5mm125≤2.0mm156≤2.5mm2.0mm<125≤2.5mm2.5mm<156≤4.0mm125>2.5mm156>4.0mm2 色差同一片电池片颜色均匀一致,无色差。
单片无明显色差;整批电池片不允许出现悬殊色差。
单体电池颜色不均匀,允许存在跳色色差,最多跳一个相近色(例如:蓝色到红色存在于单体电池上),单体电池最多只允许存在3种颜色。
同一片电池片允许颜色不均匀(蓝色-深蓝色-红色-黄褐色),允许存在跳色色差,跳色≥2个相近色,或同一片电池片上有3种以上颜色。
比亚迪156多晶电池片出货检验(OQC)标准

电性能参数
Umpp(V) Impp(A)
0.540
7.84
0.532
7.80
0.524
7.78
0.515
7.75
0.512
7.72
03
7.62
0.501
7.53
0.498
7.49
0.494
7.42
0.493
7.32
0.488
7.19
0.481
7.23
0.477
外约定)
(1) 无裂纹、碎片、穿孔、V 型缺口、缺 角 (2) 正面颜色:片内无明显色差(在电池 片上方正对电池片观测) (3) 正面脱晶≤1mm 深*1mm 宽,最多不 超过 2 处,背面脱晶≤2mm 长*2mm 宽, 最多不超过 2 处 (4) 斑点总面积≤4mm2,单个面积≤1mm2 受光面栅线 (5) 划伤总长度≤10mm,个数≤2 个,组 件层压后不可视 (6) 铝 包 高 度 < 0.2mm, 总 面 积 不 大 于 ≤3mm2 (7) 表面脏痕色泽暗淡,无明显发白; (8) 正面细栅线断开:长度<2mm,同一 细栅线上个数≤2 个 (9) 正 面 主 栅 线 缺 失 : 缺 失 总 面 积 ≤ 0.25mm2(0.5mm宽*0.5mm)长 (10) 正面结点:长度、宽度≤0.5mm,总 个数≤5 个 (11) 正面印刷偏移:印刷两边距离的差 ≤0.3mm (12) 背 面 主 栅 线 缺 失 : 缺 失 总 面 积 ≤2.5mm2(宽≤0.5mm,长≤5mm) (13) 背面不允许主栅与背场间隙 (14) 背面铝浆缺失:缺失总面积≤10mm2 (15) 背面印刷偏移:印刷到边缘的距离 ≤0.5mm
每批 每批
每批
每批 每批 每批 每批 每批 每批 每批 每批 每批 每批 每批 每批
电池片检验标准
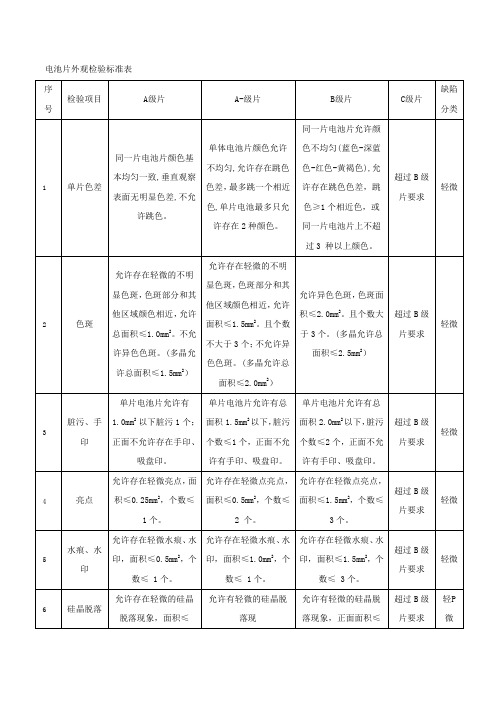
轻微
20mm,宽度<0.5mm, 存在 2 条,背面划痕宽 存在 3 条;背面划痕宽 片要求
深度<20μm 允许存在 度<0.5mm,深度<50 度<0.5mm,深度<50
3 条,或者长度<50mm μm。长度≤20mm
μm。长度≤30mm
允许存在 1 条。
允许轻微崩点,面积≤ 允许轻微崩点,面积≤ 允许轻微崩点,面积≤
厚度偏差(μm)
翘曲度
125.0±0.5
150.0±0.5
标称厚度±20
H≤2.0mm
单晶电池
125.0±0.5
165.0±0.5
标称厚度±20
H≤2.0mm
156.0±0.5
200.0±0.5
标称厚度±20
H≤2.5mm
多晶电池片
125.0±0.5 156.0±0.5
175.4±0.5 219.2±0.5
数量≤1 个;
数量≤3 个;
数量≤3 个;
4 允许有轻微粗线,宽
4 允许存在粗线,宽度 4 允许存在粗线,宽度
度≤0.3mm,长度≤
≤0.3mm,长度≤3mm; ≤0.3mm,长度≤3mm;
3mm;
背电极断线、缺失面积 背电极断线、缺失面积
背电极图形清晰,粗细
不超过背电极总面积 不超过背电极总面积
均匀,不允许有断线、
超出 B 级
16
背电极
的 3%,扭曲、突出不 的 10%,扭曲、突出不
严重
缺失、扭曲以及突出,
范围
超过正常位置的 超过正常位置的
不允许有氧化现象。
0.3mm。不允许有氧化 0.5mm。不允许有氧化
现象。
现象。
背电场完整、铝膜厚薄
多晶电池片外观及分类技术标准

电池片外观及分类技术标准
编制:
审核:
批准:
发布日期:实施日期:
1 目的
1.1 确保用于晶硅组件的电池片满足质量要求。
2 适用范围
2.1 使用于公司晶硅组件生产所用的所有电池片。
3 职责
3.1 技术部负责本标准的制订、解释及维护。
3.2 采购物流部负责按本标准采购电池片。
3.3 质量管理部负责按本标准对来料电池片进行检验。
3.4 生产部负责按本标准对电池片外观及性能进行全数检验并分类。
4 工作内容
4.1 电池片外观检验
4.1.1 检验方式:一般日光灯光源下,采用目测方式及使用塞尺、钢直尺、点规等工具辅助进行检验。
4.1.2 检验项目及判定标准
欢迎阅读本文档,希望本文档能对您有所帮助!
欢迎阅读本文档,希望本文档能对您有所帮助!
4.2 电池片性能分档
4.2.1 分档标准
4.2.2 分档方法:4.2.1序号4-19按照最佳工作电流Iap进行分档,序号1、2、3、20、21、22按转换效率进行分档。
4.3 检验分档顺序:电池片进行外观检验分类后方可进行电性测试分档。
欢迎阅读本文档,希望本文档能对您有所帮助!。
电池片分档标准

1.目的为规范成品太阳电池片的外观判检工作,保证检验项目完整、检验作业方法和检验数据准确;统一生产、质量、销售认识以满足顾客所需,特制定本本电池片检验标准。
2.适用范围本标准内部适用,检验范围为本公司生产的单多晶硅太阳能电池片。
3. 工作职责质量管理部负责外观判检项目的具体实施,对所有成品太阳电池片进行目测全检;所有检验人员严格按照本文件规定进行操作。
4. a判检工具PVC 手套、日光灯、塞尺、外观判检模具、直尺、塑料垫片、插片盒、高密度泡沫盒、黑色油笔、口罩。
b判检作业条件1、照度800lx 日光灯下;2、洁净水平的判检操作台面上;3、每片电池片自然水平放置于判检操作台面,不得人为挤压;4、佩戴PVC 手套、轻拿轻放,保持3 秒/片检片速度;5、统一由一个检验员先进行背面判检再由另外的检验员进行正面判检,避免判检翻片过程中的电池片损伤。
6、判检人员保持直立坐姿,从正上方(视线与判检水平桌面呈80°~90°)对电池片进行观测,前胸距离电池片中心点水平距离约16cm,人眼距离电池片中心点视线距离约28cm 5. 检验标准(一)包括各等级的分类、检验项目及说明、各等级产品的接收条件等,列于下表:检验项目及说明A类B类C类A级A1级B1级B2级C级1.效率光电转换效率(Eff.)2.正面次栅断开无断栅宽度L≤1mm,数量≤3条断栅宽度L>1mm,数量≤3条超过B1标准3.正面栅线结点无无数量≤2处,且长、宽分别小于2 mm和0.3mm超过B1标准L4.正面是否漏浆由网版原因引起的漏浆无无漏浆面积≤1mm2,数量≤2个超过B1标准5.正面主栅缺损无无缺损面积≤4mm2超过B1标准6.正面印刷图案偏离因为硅片与网版未完全对准而引起的图案偏离无印刷边界到硅片边沿的距离差别≤0.5 mm印刷边界到硅片边沿的距离差别0.5 mm<d<2mm印刷边界到硅片边沿的距离差别0.5mm<d<2mm超过B类标准为等外品7.正面色差PECVD沉积氮化硅减反射膜的色彩及均匀性单片蓝色,色彩均匀,且同一包电池片的色彩一致单片色差肉眼观察不明显,且同一包电池片的色彩一致肉眼可见色差,透过毛玻璃观察不明显;且同一包电池片的色彩一致超过B1标准;同一包色彩一致8.正面色斑. 因制绒或脏污引起的色彩不均匀无轻微色斑面积总计≤1.5cm2,无点状色斑色斑面积总计≤4cm2严重色斑9.黄金斑PECVD时电池片正面被颗粒掩盖引起无色斑面积≤1mm2,数量≤3个色斑面积≤1mm2,数量>3个超过B1标准10.正面玷污因各种原因引起的玷污无无沾污面积≤1mm2,数量>3个超过B1标准11.正面划伤电池工艺过程中因各种原因造成的正面划伤、绒面破坏无轻微划伤,长度<5cm超过A1标准12.正面水痕去除磷硅玻璃层后,经清洗、烘干(或甩干)后留下的水痕无无水痕颜色较浅,长度≥5cm;水痕颜色较明显,长度<5cm超过B1标准13.正面指印操作过程中在电池片正面留下的指纹无轻微指纹,色差较浅引起色差引起较重色差d14.正面白边因刻蚀过度引起的镀膜后边缘发白无色差较浅,h≤1mm1mm≤h≤2mm h>2mm15.背面印刷图案偏离因为硅片未完全对准网版而引起的图案偏离无背电极与背电场接触距离差别△≤0.5mm,背电场四边印刷边界到硅片边沿距离差别△1≤0.5mm,圆角印刷边界到硅片边沿距离差别△≤1.0mm背电极与背电场接触距离差别△≤0.5 mm,背电场四边印刷外围到硅片边沿距离差别△1≤0.5mm,圆角印刷边界到硅片边沿距离差别△≤1.0mm超过B1标准16.背面主栅缺损无缺损面积d≤2mm2缺损面积2mm2≤d≤4mm2超过B1标准17.背铝缺损因印刷或烧结炉传送带结构等因素导致背铝缺损.无单个缺损面积≤1mm2数量≤4个单个缺损面积≤4mm2数量≤4个超过B1标准18.背面铝珠无无有微小铝刺但已经刮平铝珠高度h≤0.2 mmh>0.2 mm19.背面鼓包鼓包高度h≤0.2mm,并且总面积S≤20mm2鼓包高度h≤0.2 mm,并且总面积20<S≤60 mm2鼓包高度h≤0.2 mm,并且总面积60<S≤100 mm2超出B1标准20.背面脱粉因浆料原因烧结不完全导致背场或背电极致密度不够用手抚摸手套上基本无残留物用手抚摸手套上基本无残留物用手抚摸手套上有较明显残留物用手抚摸手套上有较明显残留物,且相接触一片正面有掉落物dhh21.崩边无正面崩边L1≤1 mm ,且数目≤2个 背面崩边忽略不计正面崩边L1≤1 mm , 且数目≤2个 背面崩边忽略不计 L1≤1 mm ,数量≤3个≤5个,或者L1>1 mm 数量≤3个 背面崩边忽略不计超过B 类标准22.V型缺口无无无无L2≤ 5.0 mm , 且无隐裂 23.弧形缺口无 无 无 无D ≤2.0 mm L3≤ 5.0 mm数量≤1个, 且无隐裂 24.缺角因各种原因导致的缺角无 无 无 无缺角尺寸 ≤15 mm×2mm , 且无隐裂 25.弯曲≤1.8mm ≤1.8mm ≤1.8mm >1.8mm26.隐裂因各种原因导致的隐形裂纹 无 无 无 无 无(二)等外品的说明所有成品电池片,如果发现有隐裂,则一律归为等外品。
电池片分选测试工段SOP
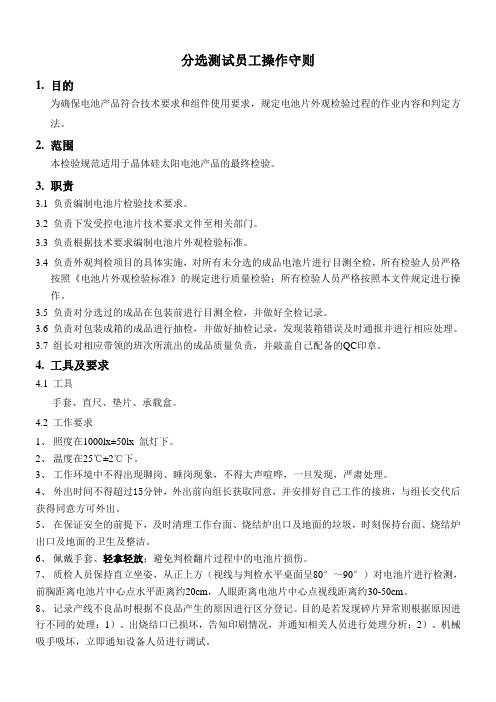
分选测试员工操作守则1.目的为确保电池产品符合技术要求和组件使用要求,规定电池片外观检验过程的作业内容和判定方法。
2.范围本检验规范适用于晶体硅太阳电池产品的最终检验。
3.职责3.1 负责编制电池片检验技术要求。
3.2 负责下发受控电池片技术要求文件至相关部门。
3.3 负责根据技术要求编制电池片外观检验标准。
3.4 负责外观判检项目的具体实施,对所有未分选的成品电池片进行目测全检,所有检验人员严格按照《电池片外观检验标准》的规定进行质量检验;所有检验人员严格按照本文件规定进行操作。
3.5 负责对分选过的成品在包装前进行目测全检,并做好全检记录。
3.6 负责对包装成箱的成品进行抽检,并做好抽检记录,发现装箱错误及时通报并进行相应处理。
3.7 组长对相应带领的班次所流出的成品质量负责,并敲盖自己配备的QC印章。
4.工具及要求4.1工具手套、直尺、垫片、承载盒。
4.2工作要求1、照度在1000lx±50lx 氙灯下。
2、温度在25℃±2℃下。
3、工作环境中不得出现聊岗、睡岗现象,不得大声喧哗,一旦发现,严肃处理。
4、外出时间不得超过15分钟,外出前向组长获取同意,并安排好自己工作的接班,与组长交代后获得同意方可外出。
5、在保证安全的前提下,及时清理工作台面、烧结炉出口及地面的垃圾,时刻保持台面、烧结炉出口及地面的卫生及整洁。
6、佩戴手套、轻拿轻放;避免判检翻片过程中的电池片损伤。
7、质检人员保持直立坐姿,从正上方(视线与判检水平桌面呈80°~90°)对电池片进行检测,前胸距离电池片中心点水平距离约20cm,人眼距离电池片中心点视线距离约30-50cm。
8、记录产线不良品时根据不良品产生的原因进行区分登记。
目的是若发现碎片异常则根据原因进行不同的处理:1)、出烧结口已损坏,告知印刷情况,并通知相关人员进行处理分析;2)、机械吸手吸坏,立即通知设备人员进行调试。
9、在分选前进行正面判检,根据《电池片外观检验标准》严格划分品级,同时至少每5片抽检电池片背面,严格控制背极、背场问题。
企业电池片技术标准

企业电池片技术标准1 外观检查注:下文中涉及“mm”的检验项目,可用直尺、三角尺、塞尺、游标卡尺进行精确测量。
表1 电池片外观检验标准2.电极可焊性,电极附着强度①电极焊带:镀锡铜带,厚度 0.18mm ,宽度 2.5mm ;或厚度0.20mm ,宽度2.0mm 。
焊料镀层:传统焊料 62%Sn/36%Pb/2%Ag或无铅 Sn/Ag3.0%/Cu0.5% 。
②电极可焊性:按照推荐条件对电池焊接电极进行搪锡试验,然后在3~10³显微镜下检查,焊料覆盖面积应大于受试面积的80% 。
③电极附着强度:经过2-3N/mm2的45°角拉力试验后,电极不脱落。
3. 背面铝膜与基体材料的附着强度使用(钢化玻璃+EVA+电池片+EVA+聚四氟乙烯耐高温漆布)制成组件后,在满足EVA充分交联的条件下层压,待冷却至室温后,撕下聚四氟乙烯耐高温漆布,用刀割开EVA和铝膜,撕去EVA条,平均拉力应≥10N/10mm且铝膜应无明显脱落现象。
4.辐照衰减4.1紫外线辐照预处理试验试验条件:①使用计量校准过的辐射计测量试验台安装受试电池平面上的辐照,保证波长在280 nm 到385 nm 之间的紫外辐射强度不超过250 W²m–2(即:大约5 倍于自然阳光的水平),并保证不均匀性低于15% 。
②将受试电池开路安装于试验平面上,位于紫外光照射的区域内。
确保受试电池温度为60℃±5℃。
③使受试电池接受辐射总量为波长在280nm 到385nm 范围的紫外辐射15kWh²m-2, 其中波长为280nm 到320nm 的紫外辐射为5kWh²m-2。
保持电池的温度在规定范围。
经过试验后,按照STC(光强 1000W/m2、光谱 AM1.5、温度 25℃、测试方法 IEC904-1)测试条件和测试方法进行测试,最大输出功率衰减应不超过试验前测量值的3% 。
4.2 太阳曝晒试验①按照制造厂商的推荐值,给电池接上电阻负载并安装于户外,与辐射计处于同一平面上。
晶体硅组件检验标准

5 组件电极性
5.1 组件电性能指标符合设计要求,不允许I-V曲线有台阶,功率及分类等级按合同规定。
5.2 标准测试条件(STC);光强1000W/㎡,光谱AM1.5,温度25±2℃用于校准的标板双方确定的标准
5.3 绝缘电阻和耐压抽测5%,并符合IEC61215规定,即在组件边框与载电体电路间施加6000V直流电压,保持30秒,无绝缘击穿。
5.4 EL测试仪检测组件无裂片,断删现象不允许超过电池片面积的十分之一,电池片无发光处的面积小于十分之一,由于PN结漏电造成某一小部分无发光的现象不允许。
6验收规则
6.1 组件抽样,验收按合同要求,每批货提供头,中,尾三次交联试验报告
6.2 每一台同应提供完整的光电测试报告,要求时提供I-V曲线和EL测试图。
四.验收时质量要求;。
电池片的等级标准

电池片的检验一、检验的条件1.不低于800LX的照射下,距离电池片30-50cm的距离,目视方向垂直于电池片表面观察。
二、检验的方法1、拿取电池片时要轻拿轻放,125的电池片保持在1-2的检测速度,150及156的电池片要一片一片的进行检查。
三、检测项目1.颜色色差2.绒面色斑3.亮斑4.裂纹、裂痕及穿孔5.弯曲的6.崩边、缺口、掉角7.印制偏移8.TTV9.铝珠、铝苞10.印刷图形11.漏浆12.外形尺寸注:08年3月底质量部更新了新的检验作业指导书四、颜色色差A级1、多晶硅片:单体电池的颜色均匀一致,颜色的范围从蓝色开始,经深蓝色、红色、黄褐色、到褐色之间允许相近色的色差(蓝色和深蓝色存在单体电池上,但不允许跳色),主体颜色为深蓝色,单体电池最多只允许两种颜色。
2、单晶电池片:同一片电池片颜色均匀一致,颜色范围中没有褐色,其他同多晶A级的判别。
新的标准:单片上均匀一致的不同颜色的电池片,按照淡蓝、蓝色、红色三种进行分类。
B级1、多晶硅片:单体电池颜色不均匀,允许存在跳色色差,最多跳一个相近色(例如:红色和褐色存在于单体电池上),主体颜色为蓝色-红色范围,单体电池最多只允许存在三种颜色。
2、单晶电池片:与多晶电池片相比,只少了主体颜色,其他同多晶B级的判别。
新的标准:与旧标准相同C级1.多晶硅片:同一片电池允许颜色不均匀(蓝色-深蓝色-红色-黄褐色-褐色)允许存在跳色色差,同以电池片上可以有≥2个相近色。
2.单晶电池片:与多晶电池片相比,颜色范围中少了褐色,其余同多晶C级的判别。
新的标准:与旧标准相同注:当单片上为均匀一致得到不同颜色,判为A级,但需按照淡蓝、蓝色、红色三种进行单测单包。
五、绒面色斑(水痕印、未制绒、未镀膜、手指印、斑点等)A级变更前:允许有轻微缺陷,缺陷部分的总面积不超过电池片总面积的10%,个数不超过3个。
A级暂定变更后:把绒面色斑分成两种类型:发白色斑和淡蓝色斑(1)发白色斑由于存在蓝色到白色的跳色,故A级片绒面色斑中决不允许有发白色斑,缺陷总面积占电池片总面积的0—30%,个数不超过5个,符合此标准的均判为B级。
多晶156三栅分档标准定稿
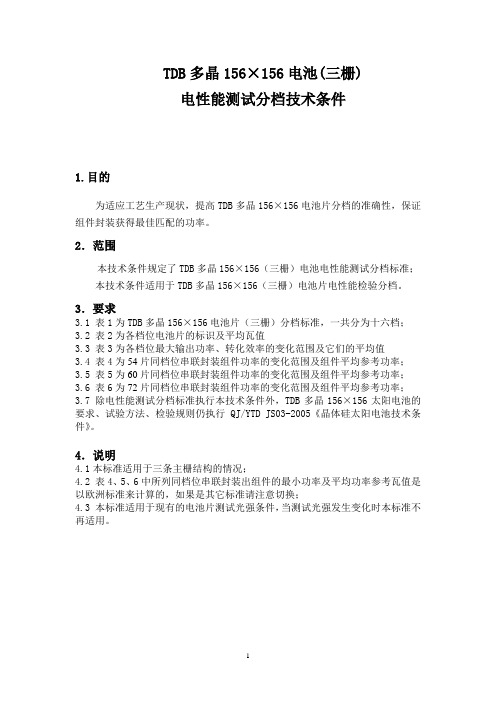
TDB多晶156×156电池(三栅)电性能测试分档技术条件1.目的为适应工艺生产现状,提高TDB多晶156×156电池片分档的准确性,保证组件封装获得最佳匹配的功率。
2.范围本技术条件规定了TDB多晶156×156(三栅)电池电性能测试分档标准;本技术条件适用于TDB多晶156×156(三栅)电池片电性能检验分档。
3.要求3.1 表1为TDB多晶156×156电池片(三栅)分档标准,一共分为十六档;3.2 表2为各档位电池片的标识及平均瓦值3.3 表3为各档位最大输出功率、转化效率的变化范围及它们的平均值3.4 表4为54片同档位串联封装组件功率的变化范围及组件平均参考功率;3.5表5为60片同档位串联封装组件功率的变化范围及组件平均参考功率;3.6表6为72片同档位串联封装组件功率的变化范围及组件平均参考功率;3.7 除电性能测试分档标准执行本技术条件外,TDB多晶156×156太阳电池的要求、试验方法、检验规则仍执行QJ/YTD JS03-2005《晶体硅太阳电池技术条件》。
4.说明4.1本标准适用于三条主栅结构的情况;4.2 表4、5、6中所列同档位串联封装出组件的最小功率及平均功率参考瓦值是以欧洲标准来计算的,如果是其它标准请注意切换;4.3 本标准适用于现有的电池片测试光强条件,当测试光强发生变化时本标准不再适用。
表1:电池片分档技术参数及范围表3:各档位最大输出功率、转化效率的变化范围及它们的平均值TDI -12、TDI -13三个档位考虑了2.5%的组件封装损失;其余档位考虑了3.5%的组件封装损失。
注:表中TDI -6、TDI -7、TDI -9、TDI -10三个档位考虑了3%的组件封装损失;TDI -11、TDI -12、TDI -13三个档位考虑了2.5%的组件封装损失;其余档位考虑了3.5%的组件封装损失。
TDI -12、TDI -13 三个档位考虑了2.5%的组件封装损失;其余档位考虑了3.5%的组件封装损失。
电池片测试分选标准
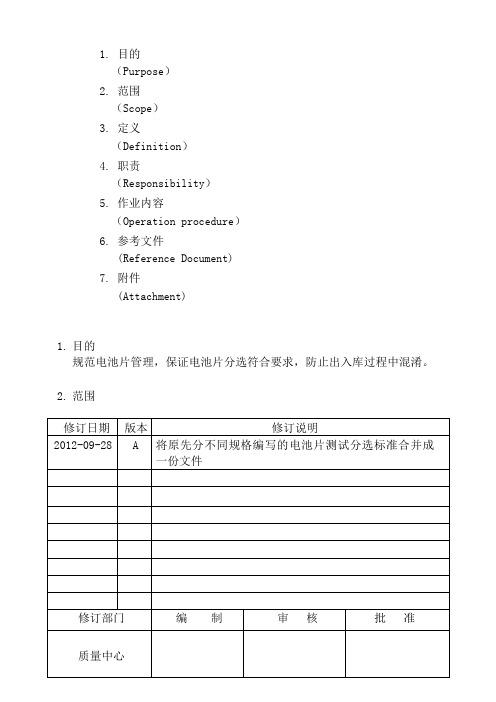
15.4
15.4
3.748
15.4
15.8
3.748
3.845
B1
15.0
15.0
3.650
15.0
15.4
3.650
3.748
B1
13.0
13.0
3.163
13.0
15.0
3.164
3.650
B1
11.0
11.0
2.676
11.0
13.0
2.677
3.164
B1
<10.0
<10.0
<2.434
修订日期
版本
修订说明
2012-09-28
A
将原先分不同规格编写的电池片测试分选标准合并成一份文件
修订部门
编制
审核
批准
质量中心
1.目的
(Purpose)
2.范围
(Scope)
3.定义
(Definition)
4.职责
(Responsibility)
5.作业内容
(Operation procedure)
6.参考文件
需重新测试
等级
包装标识效率(%)
外卖效率(%)
标称功率(W)
效率范围(%)
功率范围(W)
最低效率
最高效率
最低功率
最高功率
B
19.0
19.0
4.540
19.0
19.2
4.540
4.588
B
18.8
18.8
4.492
18.8
19.0
4.492
4.540
B
18.6