选择性溶解法
废催化剂回收利用提炼工艺有哪些

废催化剂回收利用提炼工艺有哪些废催化剂指的是在催化剂使用过程中变得无法再继续使用的残留物。
由于催化剂的高价值,从废催化剂中回收和利用其中的有用成分已成为一项重要的环保和资源节约措施。
废催化剂回收利用的提炼工艺主要包括以下几种:1. 焙烧方法焙烧法是一种常用的废催化剂回收利用工艺。
通过将废催化剂在高温下进行焙烧,将其中的有害物质和杂质烧除,得到高纯度的有用成分。
这种方法的优点是操作简单、成本较低,但同时也存在能耗高、排放污染物等问题。
2. 溶液浸取法溶液浸取法利用溶剂的选择性溶解性质,将废催化剂中的有用成分溶解出来。
常用的溶剂包括酸、碱和有机溶剂等。
通过对废催化剂的多次浸取和分离,可以逐步提取出目标成分。
这种方法的优点是选择性强、回收率高,但同时也需要处理大量的废液,对环境造成一定的影响。
3. 燃烧还原法燃烧还原法是一种通过高温气氛中的燃烧和还原反应,将废催化剂中的有害物质和杂质转化为无害物质,并回收利用有用成分的方法。
在高温还原气氛中,有害物质和杂质被还原为气体或金属等形式,而有用成分则以固体形式存在。
这种方法的优点是可回收高纯度的有用成分,但同时也需要高温和特殊的还原气氛条件。
4. 调整反应条件法调整反应条件法是一种通过改变反应条件来实现废催化剂回收利用的方法。
催化剂的活性往往与反应条件密切相关,通过调整反应温度、压力、气氛等条件,可以促使废催化剂中的有用成分重新表现出活性。
这种方法的优点是操作简单、成本低,但对于不同的废催化剂,需要找到最合适的反应条件。
5. 粉碎提取法粉碎提取法是一种通过机械碾磨废催化剂,再利用物理或化学方法提取有用成分的工艺。
通过细碎废催化剂,增加表面积,有利于后续的提取操作。
然后利用不同的提取剂、溶剂或分离技术,将有用成分从废催化剂中分离出来。
这种方法的优点是操作简便、废催化剂利用率较高,但对于废催化剂的破碎和提取过程会产生一定的能耗和环境污染。
6. 超声辅助提取法超声辅助提取法是一种利用超声波在液体中产生的空化效应,促进物质的溶解和扩散的技术。
18种常用工业废水处理方法
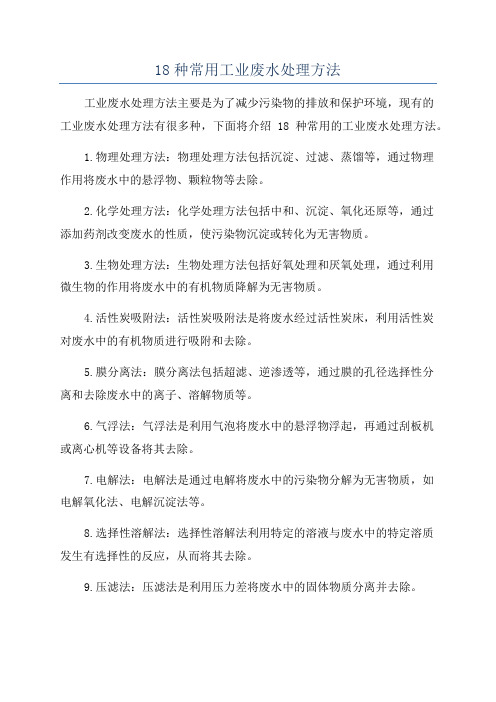
18种常用工业废水处理方法工业废水处理方法主要是为了减少污染物的排放和保护环境,现有的工业废水处理方法有很多种,下面将介绍18种常用的工业废水处理方法。
1.物理处理方法:物理处理方法包括沉淀、过滤、蒸馏等,通过物理作用将废水中的悬浮物、颗粒物等去除。
2.化学处理方法:化学处理方法包括中和、沉淀、氧化还原等,通过添加药剂改变废水的性质,使污染物沉淀或转化为无害物质。
3.生物处理方法:生物处理方法包括好氧处理和厌氧处理,通过利用微生物的作用将废水中的有机物质降解为无害物质。
4.活性炭吸附法:活性炭吸附法是将废水经过活性炭床,利用活性炭对废水中的有机物质进行吸附和去除。
5.膜分离法:膜分离法包括超滤、逆渗透等,通过膜的孔径选择性分离和去除废水中的离子、溶解物质等。
6.气浮法:气浮法是利用气泡将废水中的悬浮物浮起,再通过刮板机或离心机等设备将其去除。
7.电解法:电解法是通过电解将废水中的污染物分解为无害物质,如电解氧化法、电解沉淀法等。
8.选择性溶解法:选择性溶解法利用特定的溶液与废水中的特定溶质发生有选择性的反应,从而将其去除。
9.压滤法:压滤法是利用压力差将废水中的固体物质分离并去除。
10.离子交换法:离子交换法是通过离子交换树脂将废水中的离子和溶解物质去除。
11.燃烧法:燃烧法是将废水进行高温燃烧,将有机物质氧化为二氧化碳和水。
12.植物吸附法:植物吸附法利用植物根系对废水中的污染物进行吸附和降解。
13.低温等离子体方法:低温等离子体方法是利用低温等离子体对废水中的有机物和溶解物进行氧化降解。
14.纳米材料法:纳米材料法通过添加纳米材料将废水中的有机物、重金属等污染物去除。
15.活性氧化法:活性氧化法通过添加氧化剂将废水中的有机物进行氧化降解,如高级氧化法、臭氧氧化法等。
16.高级处理方法:高级处理方法包括超临界水氧化、气相催化氧化等,能够对废水中难降解的有机物质进行高效处理。
17.胶体团聚法:胶体团聚法通过添加电解质或聚合物使废水中的胶体颗粒发生团聚,从而易于沉淀和去除。
乙二醇和水分离的方法
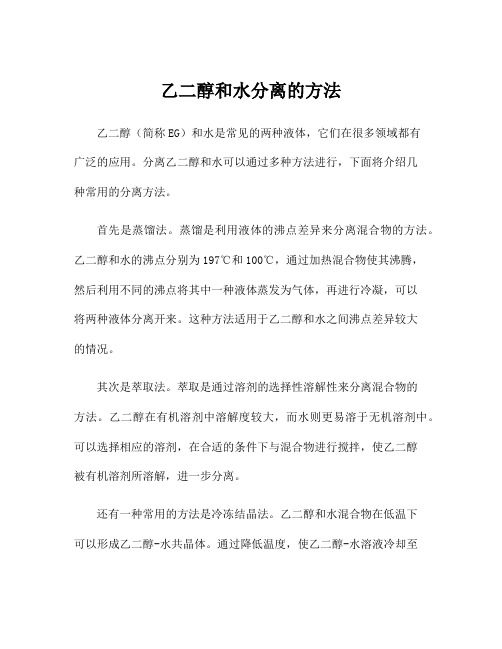
乙二醇和水分离的方法乙二醇(简称EG)和水是常见的两种液体,它们在很多领域都有广泛的应用。
分离乙二醇和水可以通过多种方法进行,下面将介绍几种常用的分离方法。
首先是蒸馏法。
蒸馏是利用液体的沸点差异来分离混合物的方法。
乙二醇和水的沸点分别为197℃和100℃,通过加热混合物使其沸腾,然后利用不同的沸点将其中一种液体蒸发为气体,再进行冷凝,可以将两种液体分离开来。
这种方法适用于乙二醇和水之间沸点差异较大的情况。
其次是萃取法。
萃取是通过溶剂的选择性溶解性来分离混合物的方法。
乙二醇在有机溶剂中溶解度较大,而水则更易溶于无机溶剂中。
可以选择相应的溶剂,在合适的条件下与混合物进行搅拌,使乙二醇被有机溶剂所溶解,进一步分离。
还有一种常用的方法是冷冻结晶法。
乙二醇和水混合物在低温下可以形成乙二醇-水共晶体。
通过降低温度,使乙二醇-水溶液冷却至共晶体形成的温度以下,可以使乙二醇结晶出来。
然后通过过滤等手段将乙二醇晶体和水分离开来。
还可以利用分子筛吸附分离法。
分子筛是一种多孔结构的固体材料,具有选择性吸附功能。
选用合适的分子筛,将乙二醇-水混合物通过吸附塔,使乙二醇在分子筛的孔径内被吸附住,而水则通过筛子流出,从而实现乙二醇和水的分离。
另外,也可以利用膜分离法进行乙二醇和水的分离。
膜分离是利用不同溶质在膜材料上的透过性和选择性来实现分离的过程。
可以选择合适的膜材料,通过渗透压或压力,将乙二醇和水分离开来。
还可以利用离心法进行分离。
通过速度梯度离心机的离心过程,利用乙二醇和水在离心力作用下的不同离心系数,从而将其分离。
综上所述,乙二醇和水的分离方法包括蒸馏法、萃取法、冷冻结晶法、分子筛吸附分离法、膜分离法和离心法等多种方法。
根据具体情况选择合适的方法,可以有效地实现乙二醇和水的分离。
分离方法分类

分离方法分类在科学研究和工程实践中,分离是一种常见的操作,用于将混合物中的不同组分进行分离。
分离方法可以根据不同的原理和操作步骤进行分类。
本文将根据分离原理将分离方法分为以下几类:物理分离方法、化学分离方法和生物分离方法。
一、物理分离方法1. 过滤法:通过孔隙或滤纸等物质的筛选作用,将固体颗粒从混合物中分离出来。
过滤法常用于固液分离,如饮用水中的悬浮物去除。
2. 蒸馏法:利用混合物中各组分的不同沸点或蒸汽压,将液体组分从混合物中分离出来。
蒸馏法广泛应用于液体组分的分离,如酒精的提纯。
3. 结晶法:通过溶解度的差异,将溶液中的固体组分以晶体的形式分离出来。
结晶法常用于固体物质的纯化和提纯,如食盐的制备。
4. 离心法:利用离心力的作用,将混合物中的固体颗粒或悬浮液离心沉淀,从而实现固液分离。
离心法常用于生物医药领域,如细胞沉淀和血液分离。
二、化学分离方法1. 萃取法:利用溶剂的选择性溶解性,将混合物中的组分从溶液中分离出来。
萃取法广泛应用于化学分析和有机合成中,如天然产物的提取。
2. 气相色谱法:利用气相色谱柱对气体混合物进行分离,根据各组分在固定相和流动相中的相互作用力的差异实现分离。
气相色谱法常用于分析有机化合物的成分和含量。
3. 液相色谱法:利用液相色谱柱对液体混合物进行分离,根据各组分在固定相和流动相中的相互作用力的差异实现分离。
液相色谱法广泛应用于药物分析和环境监测领域。
三、生物分离方法1. 离心法:利用离心力将生物颗粒(如细胞、细胞器等)从混合物中分离出来。
离心法是生物学研究中常用的分离方法,如细胞分离和亚细胞组分分离。
2. 电泳法:利用电场对带电生物颗粒进行分离,根据其电荷和大小的差异实现分离。
电泳法常用于分析和纯化DNA、蛋白质等生物大分子。
3. 过滤法:利用孔隙或滤纸等物质的筛选作用将生物颗粒从混合物中分离出来。
过滤法常用于细胞培养中的细胞分离和微生物的筛选。
以上是根据分离原理对分离方法进行分类的一些常见方法。
古人是如何知道金矿的他们是如何提炼黄金的
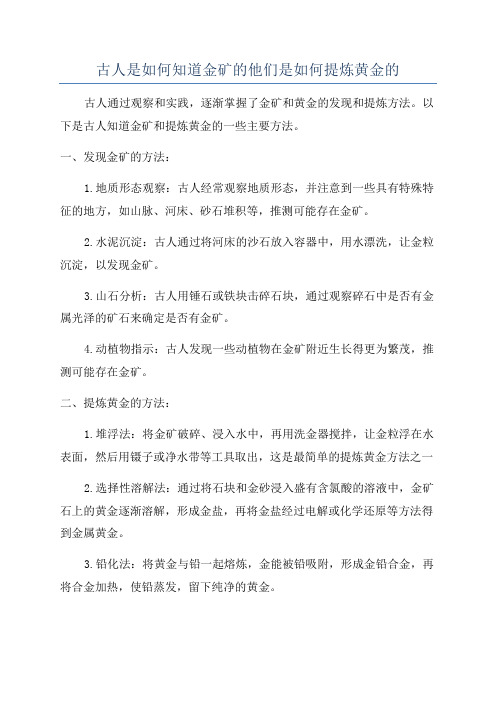
古人是如何知道金矿的他们是如何提炼黄金的古人通过观察和实践,逐渐掌握了金矿和黄金的发现和提炼方法。
以下是古人知道金矿和提炼黄金的一些主要方法。
一、发现金矿的方法:
1.地质形态观察:古人经常观察地质形态,并注意到一些具有特殊特征的地方,如山脉、河床、砂石堆积等,推测可能存在金矿。
2.水泥沉淀:古人通过将河床的沙石放入容器中,用水漂洗,让金粒沉淀,以发现金矿。
3.山石分析:古人用锤石或铁块击碎石块,通过观察碎石中是否有金属光泽的矿石来确定是否有金矿。
4.动植物指示:古人发现一些动植物在金矿附近生长得更为繁茂,推测可能存在金矿。
二、提炼黄金的方法:
1.堆浮法:将金矿破碎、浸入水中,再用洗金器搅拌,让金粒浮在水表面,然后用镊子或净水带等工具取出,这是最简单的提炼黄金方法之一
2.选择性溶解法:通过将石块和金砂浸入盛有含氯酸的溶液中,金矿石上的黄金逐渐溶解,形成金盐,再将金盐经过电解或化学还原等方法得到金属黄金。
3.铅化法:将黄金与铅一起熔炼,金能被铅吸附,形成金铅合金,再将合金加热,使铅蒸发,留下纯净的黄金。
4.火烧法:将黄金矿石破碎,然后放入火中烧煮,使其中的有机物质
燃尽,熔化金屑。
再用水冲刷,将黄金与碎石分离。
总结起来,古人发现金矿的方法主要是通过观察地质形态、水泥沉淀、山石分析和动植物指示。
而提炼黄金的方法主要包括堆浮法、选择性溶解法、铅化法和火烧法等。
这些方法虽然相对简单粗糙,但在古人没有现代
科技设备的情况下,仍然能够有效地提取黄金。
聚乙烯废料回收技术(2)

聚乙烯塑料二段法裂解工艺技术摘要:一、引言二、聚乙烯的回收技术现状三、聚乙烯废料回收行业中存在的问题四、聚乙烯塑料二段法裂解五、展望六、完毕语一、引言随着石油化工的开展,聚乙烯生产得到迅速开展,产量约占塑料总产量的1/4。
1983年世界聚乙烯总生产能力为24.65Mt,在建装置能力为 3.16Mt。
聚乙烯的应用涉及到我们生活的方方面面,聚乙烯制品更是成为了我们生产生活不可缺少的一局部。
据世界观察研究所公布的数字显示,全世界每年制品塑料回收再利用率不到10%。
欧洲制品塑料回收率相对较高,但欧盟成员国中还有一半的回收率仍低于30%。
日本的塑料回收利用率也到达了26%。
而我们选择此课题的主要背景为以下几点:1聚乙烯行业开展前景好2国内外聚乙烯工业现状理想3聚乙烯所制塑料形成“白色污染〞严重聚乙烯与人们的生产生活息息相关,对经济开展起着不可无视的作用,但是同时聚乙烯废料对环境造成的危害及其重大,不可无视;而对于塑料垃圾的回收再利用是一个利国利民的好工程,同时也是造福子孙后代的好事。
所以,如何回收利用好聚乙烯废料得到了越来越多的关注,处理好聚乙烯废料成为迫在眉睫的事情。
二、聚乙烯的回收技术现状1、别离分选技术别离筛选是废旧塑料回收的重要环节。
国内外开发了多种别离分选方法。
仪器识别与别离技术:近红外线具有识别有机材料的功能,采用近红外线技术的光过滤器识别塑料的速度可达2000次/秒以上,常见塑料〔PE、PP、PS、PVC、PET〕可以明确的被区别开来,当混合塑料通过近红外光谱分析仪时,装置能自动分选出5种常见的塑料,速度可到达20~30片/min。
水力旋分技术:利用水力旋风别离器将混合塑料经粉碎、洗净等预处理后装入储槽,然后定量输送至搅拌器,形成的浆状物通过离心泵送入旋风别离器,在别离器中密度不同的塑料被分别排出。
选择性溶解法:将混合塑料参加二甲苯、乙酮等溶剂中,它可在不同的温度下选择性溶解、别离不同的塑料,损耗很小。
药物溶解方法有哪些方法

药物溶解方法有哪些方法药物溶解方法是指将药物以溶解的形式投入某种溶液中,使药物完全分散在溶液中,并使溶液中的活性成分达到最大溶解度,以便于药物的有效吸收利用。
药物溶解方法的选择及操作对于药物的疗效及药物的治疗效果有着重要影响。
下面将介绍一些常见的药物溶解方法。
1. 搅拌溶解法:搅拌溶解法是将药物加入溶剂中,然后通过搅拌或者超声波等机械方法将药物颗粒分散均匀。
这种方法适用于药物颗粒较大以及不易溶解的情况,能够提高溶解速度和溶解度。
2. 热溶解法:热溶解法是通过升高溶剂温度来增加药物分子的动力学活性,使药物分子速度增加,从而加快药物的溶解速度。
然而,需要注意的是,并不是所有药物都适合使用热溶解法,因为有些药物在高温下易发生降解或者变性。
3. 溶剂溶解法:溶剂溶解法是使用较好的溶剂将药物溶解。
溶剂的选择非常重要,需要根据药物的物化特性以及溶剂的选择性进行选择。
常用的溶剂有水、乙醇、甘油等。
4. 胶体溶解法:胶体溶解法是指将药物转化为胶体状态,使药物分散在溶液中。
这种方法适用于药物颗粒较小、不易溶解的情况,能够提高溶解度和稳定性。
5. 离子交换溶解法:离子交换溶解法是通过与溶剂中的离子进行交换,使药物溶解。
这种方法适用于药物为离子或离子型溶质的情况。
6. 浓度梯度溶解法:浓度梯度溶解法是指在不同浓度的溶液中,通过浓度差使药物分子从低浓度到高浓度的溶液中分布,从而加快药物的溶解速度。
7. 凝胶溶解法:凝胶溶解法是将药物溶解在凝胶中,通过凝胶孔隙的扩散来实现药物的溶解。
这种方法适用于药物对溶剂敏感或者溶解度较低的情况。
总结起来,药物溶解方法包括搅拌溶解法、热溶解法、溶剂溶解法、胶体溶解法、离子交换溶解法、浓度梯度溶解法和凝胶溶解法等。
在选择溶解方法时,需要综合考虑药物的物化特性、稳定性以及溶剂的选择性,以期达到最佳的溶解效果。
含钯硅胶中钯回收
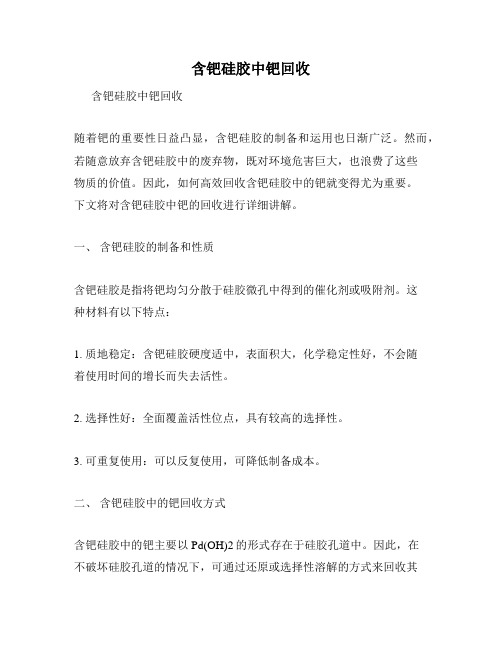
含钯硅胶中钯回收
含钯硅胶中钯回收
随着钯的重要性日益凸显,含钯硅胶的制备和运用也日渐广泛。
然而,若随意放弃含钯硅胶中的废弃物,既对环境危害巨大,也浪费了这些
物质的价值。
因此,如何高效回收含钯硅胶中的钯就变得尤为重要。
下文将对含钯硅胶中钯的回收进行详细讲解。
一、含钯硅胶的制备和性质
含钯硅胶是指将钯均匀分散于硅胶微孔中得到的催化剂或吸附剂。
这
种材料有以下特点:
1. 质地稳定:含钯硅胶硬度适中,表面积大,化学稳定性好,不会随
着使用时间的增长而失去活性。
2. 选择性好:全面覆盖活性位点,具有较高的选择性。
3. 可重复使用:可以反复使用,可降低制备成本。
二、含钯硅胶中的钯回收方式
含钯硅胶中的钯主要以Pd(OH)2的形式存在于硅胶孔道中。
因此,在
不破坏硅胶孔道的情况下,可通过还原或选择性溶解的方式来回收其
中的钯。
1. 还原法
将含钯硅胶放入还原气氛中,如用氢、乙烷等还原剂反应,则钯可还原成Pd0,即为纯钯。
2. 溶解法
利用选择性溶解剂将含钯硅胶中的钯分离出来。
一般可使用的化学品有HN02、硝酸等。
黄色Pd(NO3)2生成于溶液中,经撇去其他成分后即可得到纯钯。
三、含钯硅胶中的钯回收效果
在实验室条件下,采用还原法或溶解法均可回收含钯硅胶中的钯。
其中,还原法可以直接得到较纯的钯,溶解法则需要通过后续的纯化过程才能获得高纯钯。
总的来说,含钯硅胶数产特别广泛,回收其中的钯也一直受到工程技术人员的关注。
今天,我们详细讲述了此话题,希望对相关领域的读者有所帮助。
塑料回收——精选推荐

废旧塑料通常以填埋或焚烧的方式处理。
焚烧会产生大量有毒气体造成二次污染。
填埋会占用较大空间;塑料自然降解需要百年以上;析出添加剂污染土壤和地下水等。
因此,废塑料处理技术的发展趋势是回收利用,但目前废塑料的回收和再生利用率低。
究其原因,有管理、政策、回收环节方面的问题,但更重要的是回收利用技术还不够完善。
废旧塑料回收利用技术多种多样,有可回收多种塑料的技术,也有专门回收单一树脂的技术。
近年来,塑料回收利用技术取得了许多可喜的进展,本文主要针对较通用的技术做一总结。
1 分离分选技术废旧塑料回收利用的关键环节之一是废弃塑料的收集和预处理。
尤其我国,造成回收率低的重要原因是垃圾分类收集程度很低。
由于不同树脂的熔点、软化点相差较大,为使废塑料得到更好的再生利用,最好分类处理单一品种的树脂,因此分离筛选是废旧塑料回收的重要环节。
对小批量的废旧塑料,可采用人工分选法,但人工分选效率低,将使回收成本增加。
国外开发了多种分离分选方法。
1.1 仪器识别与分离技术意大利Govoni公司首先采用X光探测器与自动分类系统将PVC从相混塑料中分离出来[1]。
美国塑料回收技术研究中心研制了X射线荧光光谱仪,可高度自动化的从硬质容器中分离出PVC 容器。
德国Refrakt公司则利用热源识别技术,通过加热在较低温度下将熔融的PVC从混合塑料中分离出来[1]。
近红外线具有识别有机材料的功能,采用近红外线技术[1]的光过滤器识别塑料的速度可达2000次/秒以上,常见塑料(PE、PP、PS、PVC、PET)可以明确的被区别开来,当混合塑料通过近红外光谱分析仪时,装置能自动分选出5种常见的塑料,速度可达到20~30片/min。
1.2 水力旋分技术日本塑料处理促进会利用旋风分离原理和塑料的密度差开发了水力旋风分离器。
将混合塑料经粉碎、洗净等预处理后装入储槽,然后定量输送至搅拌器,形成的浆状物通过离心泵送入旋风分离器,在分离器中密度不同的塑料被分别排出。
金的化学精炼方法
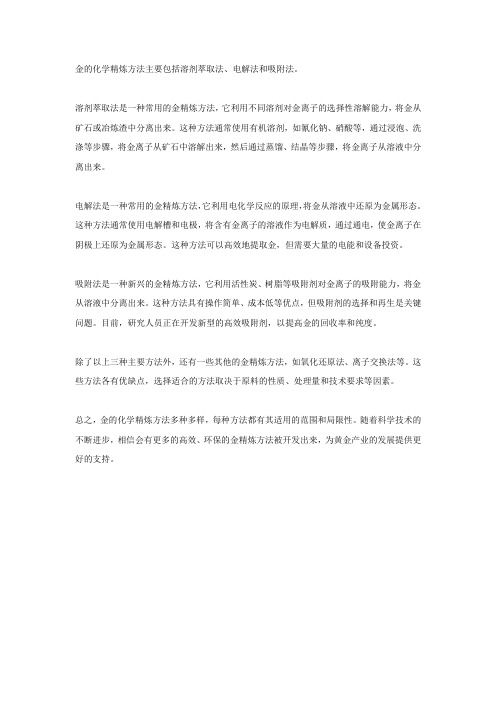
金的化学精炼方法主要包括溶剂萃取法、电解法和吸附法。
溶剂萃取法是一种常用的金精炼方法,它利用不同溶剂对金离子的选择性溶解能力,将金从矿石或冶炼渣中分离出来。
这种方法通常使用有机溶剂,如氰化钠、硝酸等,通过浸泡、洗涤等步骤,将金离子从矿石中溶解出来,然后通过蒸馏、结晶等步骤,将金离子从溶液中分离出来。
电解法是一种常用的金精炼方法,它利用电化学反应的原理,将金从溶液中还原为金属形态。
这种方法通常使用电解槽和电极,将含有金离子的溶液作为电解质,通过通电,使金离子在阴极上还原为金属形态。
这种方法可以高效地提取金,但需要大量的电能和设备投资。
吸附法是一种新兴的金精炼方法,它利用活性炭、树脂等吸附剂对金离子的吸附能力,将金从溶液中分离出来。
这种方法具有操作简单、成本低等优点,但吸附剂的选择和再生是关键问题。
目前,研究人员正在开发新型的高效吸附剂,以提高金的回收率和纯度。
除了以上三种主要方法外,还有一些其他的金精炼方法,如氧化还原法、离子交换法等。
这些方法各有优缺点,选择适合的方法取决于原料的性质、处理量和技术要求等因素。
总之,金的化学精炼方法多种多样,每种方法都有其适用的范围和局限性。
随着科学技术的不断进步,相信会有更多的高效、环保的金精炼方法被开发出来,为黄金产业的发展提供更好的支持。
碳酸盐矿物铁同位素测试的选择性溶解方法研究——以白云鄂博矿床赋矿白云岩为例

作者简介 : 孙剑 , 博 士研 究生 , 地球化学专业 。E — ma i l : s u oi a n t c @1 6 3 . c o n。 r 通讯作者 : 朱祥坤 , 研究员 , 主要从事 同位素地球化学研究 。E — ma i l : x i a n g k u n @c a g s . a c . c n 。
摘要 : 碳酸盐矿物铁 同位素测试 的选择性溶解方法包括稀盐酸溶解 法和 稀醋 酸溶 解 法 , 已应 用 于一般地 质样 品 。但 是 对 于白云鄂 博矿床 这 类矿物
组成 复 杂的特殊 样 品 , 这 两种 方法 能否适 用仍 需要 进 一 步研 究。本 文在 常 温 下对 白云石 、 磁铁 矿 、 赤铁矿 、 黄铁矿、 钠 闪石 和 黑 云母 等 白云鄂 博 矿床
云石单 矿物进 行 全部 溶 解所 获 得 的铁 同位 素 组 成 : 赋 矿 白云岩 E一1 6的
F e 值 分 别 为 一0 . 6 9 % 。 、一0 . 6 2 % 。 、一 0 . 6 9 ‰; 赋 矿 白 云岩 E一2 6的6 F e 值 分 别 为 一0 . 1 9 % e 、 一0 . 1 8 % e 、
一
28 —
第 1 期
孙剑 , 等: 碳酸盐矿物铁 同位 素测试 的选择性溶解方法研究—— 以白云鄂博 矿床赋矿 白云岩为例
中常见的含铁矿物进行稀盐酸( 0 . 5 ~ 1 m o l / L盐酸) 溶解条件 实验 。结果 显示, 稀 盐酸在 短 时 间 内( 约3 h ) 能 够 有效 地 溶 解碳 酸 盐矿 物 中的铁 , 而
铁 氧化 物 、 硫化 物 、 硅酸 盐矿 物的铁 溶 解率基 本都 <1 % 。 实验 选取 典型 的 白云鄂博 矿床赋 矿 白云岩 , 对 比 了稀 盐 酸溶 解 法 、 稀 醋 酸溶 解 法 与分 离 白
PET和PVC塑料常用的分离方法

PET和PVC塑料常用的分离方法关键词:塑料材料,PET塑料,PVC塑料,分离法1、熔融分离法利用热源识别PVC是近年开发的一种分离方法,根据两种材料不同的熔点和温度范围,通过加热在较低温度下将熔融的PVC从混合塑料中分离出来。
PET塑料的熔点高于PVC塑料的熔点,德国公司根据受扭力作用时PVC塑料与PET塑料在受力部分产生不同的不同的熔融温度特性,利用加热将在较低温度下熔融的PVC从混合塑料中分离出来。
将破碎PET和PVC碎片通过装有加热器及温度控制的传送带,PVC熔融粘附在带上,这样可与PET分离开,此系统处理能力为450一90Kg/H。
2、电选分离点选分离法分为静电分选和摩擦带电分选。
静电分离法是利用电晕放电或摩擦带电使研究对象带电,然后依次来分选带不同电性和电量的塑料颗粒,塑料带电顺序是:(负)PVE<PET<PP<PE<PS<^BS<PE(正),摩擦带电是根据塑料一边相互接触摩擦后塑料材料表面的电量来判断类型,如PET与PVC摩擦后PET带正电荷,PVC带负电荷。
3、浮降法(湿分离)对分离密度差较小的PET/PVC塑料,利用其疏水性和亲水性的不同进行分离,用特定的药品处理粉碎的废塑料,调整润湿时间、温度、浓度、PH值等来改变塑料的水润湿性,废塑料在浮游缸中,用空气鼓泡,气泡附着在疏水性塑料颗粒上面成俘游,再使用凝聚剂收集浮游的废塑料。
1990年美国G00DYEAR公司用于处埋PVC/PET的分离,首先在浮游缸中用NAOH处理粉碎的PVC和PET颗粒5一lomlm,使PET表面水合,用非离子表面活性剂调节,用空气鼓泡搅拌,疏水性的PVC树脂因附着气泡而浮游,亲水性的PET下沉。
Koble.R.w等采用含0.25%增塑剂DIDP(邻苯二甲酸二异癸酷)的水溶液处理PVC、PET混合物,使PVC 变得疏水,而PET不变,最终PVC的回收率达98%以上。
AbbaiM等人根据丹宁酸对PET材料的抑制作用,调节实际用量,在回收塑料中使PET塑料的分离率可以达到88.40%,Pongstabodees等人用木质素磺酸钙浮选分离PVC和PET,并指出液相PH值、调整时间、浮选粒度以及起泡剂种类是控制分选过程的关键因素。
利用选择性溶解法研究NEPE推进剂的微观结构
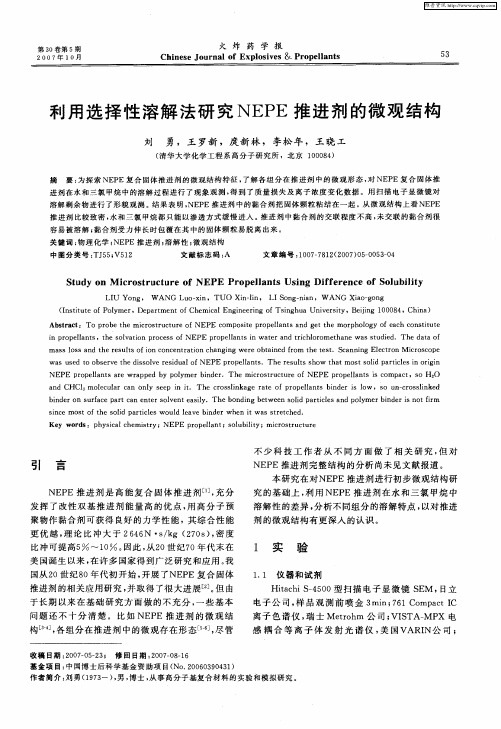
( 华 大 学 化 学 工 程 系 高 分子 研 究 所 ,北 京 1 0 8 ) 清 0 04 摘 要: 为探 索 N P E E复 合 固体 推 进 剂 的微 观 结 构 特 征 , 了解 各 组 分 在 推 进 剂 中 的 微 观 形 态 , NE E 复 合 固体 推 对 P
关键词 : 物理 化学 ; E E推 进 剂 ; 解 性 ; 观 结 构 N P 溶 微 中 图分 类 号 : J 5 V5 2 T 5 ; 1 文献 标 志码 : A 文 章 编 号 :0 77 1 (0 70 -0 30 1 0 —8 2 2 0 ) 50 5-4
S u y o i r s r t r f NEPE o la lt t d n M c o t uc u e o Pr pe l nt i g D f e e e o o u iiy
进 剂 在 水 和 三 氯 甲烷 中的 溶 解 过 程 进 行 了现 象 观 测 , 到 了 质 量 损 失 及 离 子 浓 度 变 化 数 据 。用 扫 描 电子 显 微 镜 对 得 溶 解 剩 余 物 进 行 了 形 貌 观 测 。 果 表 明 , E E推 进 剂 中 的黏 合 剂 把 固体 颗 粒粘 结 在 一起 。 微 观 结 构 上 看 N P 结 N P 从 E E 推 进 剂 比较 致 密 , 和 三 氯 甲烷 都 只 能 以 渗 透 方 式 缓 慢 进 入 。 进 剂 中 黏合 剂 的 交联 程度 不 高 , 交 联 的黏 合 剂 很 水 推 未 容 易被 溶 解 ; 合剂 受 力 伸 长 时 包 覆 在其 中的 固体 颗 粒 易 脱 离 出来 。 黏
维普资讯
第 3 第 5期 o卷
20 年 1 7 0 0月
有机物的分离和提纯方法

有机物的分离和提纯方法1.结晶法结晶法是最常用的分离和提纯方法之一、通过在溶液中冷却或者加入合适的溶剂,使溶质在饱和溶液中析出结晶,从而实现分离和提纯的目的。
结晶法适用于溶解度随温度变化较大的化合物,比如有机物中一些酮、醛、酸类物质等。
2.蒸馏法蒸馏法是一种通过液体混合物的沸点差异来实现分离和提纯的方法。
通常情况下,液体混合物会在加热的作用下产生汽化,然后通过冷凝器冷却回至液态。
不同成分的汽化温度不同,可以通过控制温度来使目标物质单独汽化,从而实现分离和提纯。
蒸馏法适用于成分之间的沸点差异较大的化合物混合物。
3.萃取法萃取法是通过溶剂的选择性溶解性来实现分离和提纯的方法。
通常情况下,在含有两个或多个有机溶剂的体系中,将需要提纯的有机物溶于其中一个溶剂中,其他杂质则溶解于另外一个溶剂中。
通过分离这两个相,然后将目标物质从溶剂中蒸发或者析出结晶,从而实现分离和提纯的目的。
4.色谱法色谱法是一种通过固定相和流动相的选择性吸附和移动性来实现分离和提纯的方法。
根据固定相的性质,色谱法分为很多种,比如薄层色谱、柱层析、气相色谱等。
色谱法适用于物质之间的吸附性质差异较大的化合物。
5.洗涤法洗涤法是利用溶剂的吸附性质来实现分离和提纯的方法。
通常情况下,将混合溶液与吸附剂接触,使目标物质被吸附在吸附剂上,然后通过适当的洗涤提取和洗滤来得到目标物质。
洗涤法适用于有机物与杂质之间的吸附性质差异较大的情况。
以上是一些常用的有机物的分离和提纯方法。
在实际操作中,还应该根据具体的化合物性质和实验条件选择合适的方法进行分离和提纯。
分离汽油和水的方法
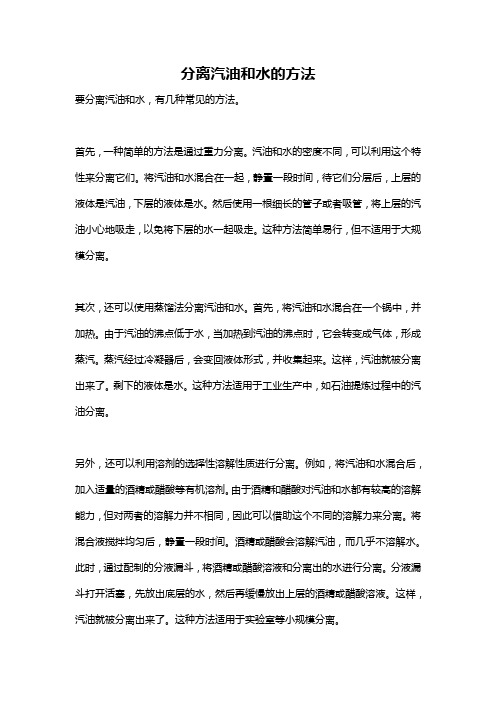
分离汽油和水的方法要分离汽油和水,有几种常见的方法。
首先,一种简单的方法是通过重力分离。
汽油和水的密度不同,可以利用这个特性来分离它们。
将汽油和水混合在一起,静置一段时间,待它们分层后,上层的液体是汽油,下层的液体是水。
然后使用一根细长的管子或者吸管,将上层的汽油小心地吸走,以免将下层的水一起吸走。
这种方法简单易行,但不适用于大规模分离。
其次,还可以使用蒸馏法分离汽油和水。
首先,将汽油和水混合在一个锅中,并加热。
由于汽油的沸点低于水,当加热到汽油的沸点时,它会转变成气体,形成蒸汽。
蒸汽经过冷凝器后,会变回液体形式,并收集起来。
这样,汽油就被分离出来了。
剩下的液体是水。
这种方法适用于工业生产中,如石油提炼过程中的汽油分离。
另外,还可以利用溶剂的选择性溶解性质进行分离。
例如,将汽油和水混合后,加入适量的酒精或醋酸等有机溶剂。
由于酒精和醋酸对汽油和水都有较高的溶解能力,但对两者的溶解力并不相同,因此可以借助这个不同的溶解力来分离。
将混合液搅拌均匀后,静置一段时间。
酒精或醋酸会溶解汽油,而几乎不溶解水。
此时,通过配制的分液漏斗,将酒精或醋酸溶液和分离出的水进行分离。
分液漏斗打开活塞,先放出底层的水,然后再缓慢放出上层的酒精或醋酸溶液。
这样,汽油就被分离出来了。
这种方法适用于实验室等小规模分离。
此外,还有一种常见的方法是使用分子筛分离。
分子筛是一种能够选择性吸附分子的物质,可以根据分子大小和极性选择性地吸附汽油分子,而不吸附水分子。
将汽油和水混合后,通过将混合液经过分子筛柱处理,在柱内汽油分子被吸附,水分子通过。
然后通过某种方法将吸附的汽油分子释放出来,从而完成分离。
这种方法适用于工业生产中需要高效分离的情况。
总的来说,分离汽油和水有多种方法可选择,包括重力分离、蒸馏法、溶剂选择性溶解和分子筛分离等。
根据实际需要和条件,可以选择合适的方法进行分离。
常见有机合成中的溶剂选择与优化方法

常见有机合成中的溶剂选择与优化方法在有机合成中,溶剂是非常重要的因素之一。
选择适合的溶剂可以提高反应效率、选择性和产率。
本文将讨论常见有机合成中的溶剂选择与优化方法,帮助读者正确选择相应的溶剂,以实现合成目标。
一、溶剂选择的基本原则1. 反应物的溶解性:首先考虑反应物在溶剂中的溶解性。
溶剂应能完全溶解反应物,以保证反应物之间的充分接触。
2. 反应动力学:溶剂的极性和粘度与反应速率有密切关系。
通常情况下,较偏极性的溶剂更有利于快速反应,但需要注意反应生产物的稳定性。
3. 选择性:溶剂的选择也会影响反应的选择性。
有些溶剂可能会促进副反应的发生,导致反应产物失去纯度。
因此,选择具有较低催化活性或选择性的溶剂是重要的。
二、常见有机溶剂的特点和应用1. 液相有机合成中的常用溶剂乙酸乙酯(EtOAc):作为极性溶剂,EtOAc广泛用于有机合成中。
其熔点低、挥发性好、可与多种有机物溶解,是一种理想的反应介质。
二甲基甲酰胺(DMF):DMF是一种极性溶剂,能够溶解许多有机化合物。
同时,由于其较高的沸点和较低的挥发性,可适用于高温反应和惰性气氛下的反应。
醚类溶剂(如乙醚和四氢呋喃):醚类溶剂具有极性较低、惰性较高的特点,适用于氢氧化金属的反应、金属卤化物的还原和多数酯化反应。
2. 水作为溶剂的有机合成随着对环境友好型溶剂需求的增加,水逐渐成为有机合成中的重要溶剂之一。
水作为绿色溶剂具有许多优点:广泛、廉价、不易燃烧、可回收和对环境友好。
然而,水同时也具有一定的限制,如水溶液中的有机物溶解度较差,易发生水解等。
因此,在使用水作为溶剂时,需要仔细考虑反应条件和控制水分。
三、常见溶剂的优化方法1. 溶剂的回收利用:为了减少溶剂的浪费和成本,可以选择适当的溶剂回收方法。
通常,通过蒸馏、萃取和萃取法等方法可以对溶剂进行回收利用。
2. 溶剂的替代选择:在涉及环境污染和可再生能源方面的要求下,绿色溶剂持续发展并应用于有机合成。
浓缩可以通过何种方式进行?

浓缩可以通过何种方式进行?一、蒸馏法蒸馏法是一种常见的浓缩方式,通过利用物质在不同温度下的汽化特性来实现浓缩。
首先,将待浓缩的溶液加热至其挥发性成分开始汽化,然后将气态的成分收集并冷却,使其重新变为液态。
这样,挥发性成分就被分离出来了,从而实现了溶液的浓缩。
蒸馏法的优点在于操作简单,可以有效地去除溶液中的杂质,但同时也存在着能耗高、操作时间长的缺点。
二、透析法透析法是一种通过渗透作用实现浓缩的方法。
透析是指通过半透膜将溶液分成浓度不同的两部分,使溶剂和小分子溶质从高浓度一侧向低浓度一侧扩散,从而实现溶液的浓缩。
透析法的优点在于操作简单,对溶液中的生物大分子不会造成损伤,但同时也存在着浓缩速度慢、半透膜的选择和维护的困难等问题。
三、气体吸附法气体吸附法是一种利用吸附材料吸附气体从而实现浓缩的方法。
吸附材料通常是选择有较强吸附能力的材料,比如活性炭。
将待浓缩的气体通过吸附材料,利用吸附剂对气体成分的选择吸附特性,从而完成气体的浓缩。
气体吸附法的优点在于操作简单,无需能量供应,但同时也存在着吸附剂选择的难题,以及吸附饱和后的再生问题。
四、萃取法萃取法是一种利用溶剂的选择性溶解性来实现浓缩的方法。
通过在待浓缩的溶液中加入适当的溶剂,使其中的目标物质溶解于溶剂中,而非目标物质则保持在原始溶液中。
然后,采用适当的分离和回收方法,将目标物质从溶剂中分离出来,从而实现溶液的浓缩。
萃取法的优点在于对目标物质具有较高的选择性,但同时也存在着溶剂的选择和回收问题。
五、冷冻浓缩法冷冻浓缩法是一种利用溶液在冰冻过程中形成冰晶而实现浓缩的方法。
通过将待浓缩的溶液暴露在低温环境中,使其冷冻,冰晶形成时会排除其中的溶剂,从而实现溶液的浓缩。
然后,通过适当的方法将冰晶与液相分离,并回收液相部分,从而浓缩溶液。
冷冻浓缩法的优点在于操作简单,无需能量供应,但同时也存在着溶剂的选择和回收问题,以及冷冻过程对某些溶液造成的影响。
以上就是浓缩可以通过的几种常见方式。
乙醇和水的分离方法

乙醇和水的分离方法一、引言乙醇和水是常见的溶液体系,其分离对于许多工业和实验室应用非常重要。
乙醇和水的分离可以通过多种方法实现,本文将介绍几种常见且有效的分离方法。
二、蒸馏法蒸馏法是最常用的乙醇和水分离方法之一。
该方法利用了乙醇和水的沸点差异,通过加热使乙醇汽化,然后冷凝收集纯净的乙醇。
具体操作时,将乙醇和水混合溶液放入蒸馏烧瓶中,将烧瓶与冷凝管连接,加热烧瓶中的溶液,使其沸腾产生蒸汽,然后在冷凝管中冷凝收集乙醇。
三、萃取法萃取法是利用溶剂的选择性溶解性质来分离乙醇和水的方法。
常用的溶剂如乙醚、石油醚等。
具体操作时,将乙醇和水混合溶液与选择性溶剂一起加入分液漏斗中,充分摇匀,然后静置,待两相分离后,打开分液漏斗的塞子,放出下层水相,留下上层乙醇相即可。
四、析出法析出法是一种通过添加适当的盐类,使乙醇和水形成不溶性盐析出而分离的方法。
常用的盐类有氯化钠、硫酸钠等。
具体操作时,将乙醇和水混合溶液加热至一定温度,然后逐渐加入盐类溶液,搅拌均匀,使乙醇和水形成不溶性的盐类沉淀,然后通过过滤或离心分离乙醇和水。
五、膜分离法膜分离法是一种基于溶质在膜上渗透性差异而实现分离的方法。
常用的膜有纳滤膜、渗透膜等。
具体操作时,将乙醇和水混合溶液通过膜分离设备,利用膜的选择性渗透性质,使乙醇和水分离,从而得到纯净的乙醇。
六、离心分离法离心分离法是利用离心力将乙醇和水的颗粒或溶液分离的方法。
具体操作时,将乙醇和水混合溶液放入离心管中,然后进行高速离心,利用离心力使乙醇和水分层,然后轻轻倾倒上层液体即可分离乙醇和水。
七、结论乙醇和水的分离是许多工业和实验室中常见的操作。
本文介绍了蒸馏法、萃取法、析出法、膜分离法以及离心分离法等几种常见且有效的分离方法。
在实际操作中,可以根据具体需求选择合适的分离方法,以获得纯净的乙醇或水。
一种树脂提纯方法
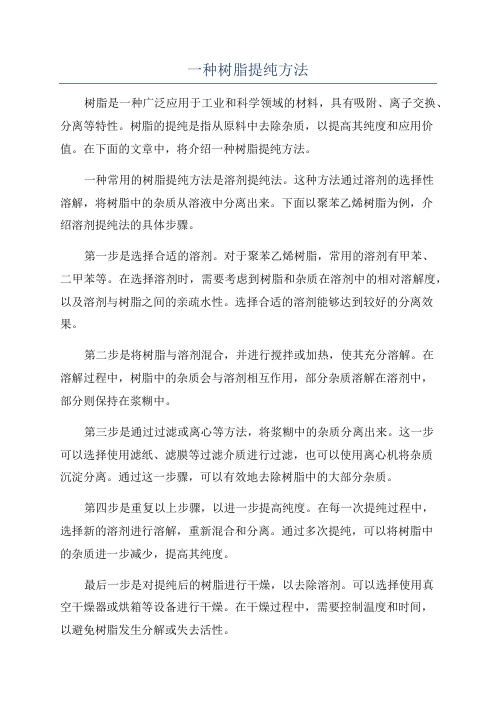
一种树脂提纯方法树脂是一种广泛应用于工业和科学领域的材料,具有吸附、离子交换、分离等特性。
树脂的提纯是指从原料中去除杂质,以提高其纯度和应用价值。
在下面的文章中,将介绍一种树脂提纯方法。
一种常用的树脂提纯方法是溶剂提纯法。
这种方法通过溶剂的选择性溶解,将树脂中的杂质从溶液中分离出来。
下面以聚苯乙烯树脂为例,介绍溶剂提纯法的具体步骤。
第一步是选择合适的溶剂。
对于聚苯乙烯树脂,常用的溶剂有甲苯、二甲苯等。
在选择溶剂时,需要考虑到树脂和杂质在溶剂中的相对溶解度,以及溶剂与树脂之间的亲疏水性。
选择合适的溶剂能够达到较好的分离效果。
第二步是将树脂与溶剂混合,并进行搅拌或加热,使其充分溶解。
在溶解过程中,树脂中的杂质会与溶剂相互作用,部分杂质溶解在溶剂中,部分则保持在浆糊中。
第三步是通过过滤或离心等方法,将浆糊中的杂质分离出来。
这一步可以选择使用滤纸、滤膜等过滤介质进行过滤,也可以使用离心机将杂质沉淀分离。
通过这一步骤,可以有效地去除树脂中的大部分杂质。
第四步是重复以上步骤,以进一步提高纯度。
在每一次提纯过程中,选择新的溶剂进行溶解,重新混合和分离。
通过多次提纯,可以将树脂中的杂质进一步减少,提高其纯度。
最后一步是对提纯后的树脂进行干燥,以去除溶剂。
可以选择使用真空干燥器或烘箱等设备进行干燥。
在干燥过程中,需要控制温度和时间,以避免树脂发生分解或失去活性。
溶剂提纯法在树脂提纯中具有一定的优势,能够有效去除杂质,提高树脂的纯度。
然而,该方法可能存在一些限制,如溶剂的选择性不够强,无法完全分离不同杂质等。
因此,在实际操作中,还需结合具体情况选择合适的提纯方法。
总结起来,树脂的提纯是一个复杂的过程,需要根据具体情况选择合适的方法。
溶剂提纯法是一种常用的方法,通过溶剂的选择性溶解和分离,可以有效去除树脂中的杂质,提高纯度。
然而,在实际操作中,还需根据树脂的性质、杂质的种类等因素,结合其他方法对树脂进行进一步的提纯。
- 1、下载文档前请自行甄别文档内容的完整性,平台不提供额外的编辑、内容补充、找答案等附加服务。
- 2、"仅部分预览"的文档,不可在线预览部分如存在完整性等问题,可反馈申请退款(可完整预览的文档不适用该条件!)。
- 3、如文档侵犯您的权益,请联系客服反馈,我们会尽快为您处理(人工客服工作时间:9:00-18:30)。
Methods for determination of degree of reaction of slag in blended cement pastesVanessa Kocaba ⁎,Emmanuel Gallucci,Karen L.ScrivenerLaboratory of Construction Materials,Ecole Polytechnique Fédérale de Lausanne,Lausanne,Switzerlanda b s t r a c ta r t i c l e i n f o Article history:Received 23May 2010Accepted 14November 2011Available online xxxx Keywords:SlagDegree of reaction SEM-BSE-IA-mapping CalorimetryChemical shrinkageTo measure the degree of reaction of slag in blended pastes,five methods were studied.Selective dissolution and differential scanning calorimetry are shown to be unreliable,SEM-BSE-IA-mapping is time consuming,but does provide good results with a reasonable degree of precision.The difference in cumulative calorimetry and chemical shrinkage curves of slag blends in comparison to blends with inert filler shows potential to iso-late the reaction of the slag.These methods have the advantage of being continuous,techniques with good precision,but the absolute heat of hydration,or contribution to chemical shrinkage of any particular slag is not known.Calibration of the calorimetry technique with SEM-BSE-IA-mapping seems to be a promising method to understand and quantify the degree of reaction of slag.©2011Elsevier Ltd.All rights reserved.1.IntroductionThe need to limit the environmental impact of cementitious mate-rials and to dispose of by-products such as slag leads to the increasing use of supplementary cementitious materials,either preblended with ground clinker or added during fabrication of concrete.It is well known that these SCMs react more slowly than cement clinker and this limits the levels of substitution,due to the need for adequate prop-erties at early ages.In order to better understand the factors affecting the rate of reaction of SCMs,it is essential to have a good method to evaluate the degree of reaction of these materials independently from the degree of reaction of the clinker component.The classic method for measurement of degree of reaction is from the bound water content [1–3].However this depends on assumptions about the quantity of water bound by the hydrate phases.The following equations illustrate the amount of bound water depends on the phase reacting (number of reacting water molecules are shown in bold).Hydration of tricalcium silicate:C 3S þð3−x þy ÞH →C x \S \H y þð3−x ÞCHð1ÞHydration of dicalcium silicate:C 2S þð2−x þy ÞH →C x \S \H y þð2−x ÞCHð2ÞHydration of tricalcium aluminate with calcium sulphate:C 3A þ3C þ32H →C 6A 3H 32ðettringite Þð3ÞorC 3A þ3CH 2þ26H →C 6A 3H 32ðettringite Þð4Þ2C 3A þC 6A 3H 32þ4H →C 4AH 12ðmonosulfoaluminate Þð5ÞC 3A þ6H →C 3AH 6ð6ÞHydration of tetracalcium aluminoferrite:C 4AF þ3CH 2þ30H →C 6A 3H 32þCH þFH 3ð7ÞC 6A 3H 32þ2C 4AF þ12H →3C 4AH 12þ2CH þ2FH 3ð8ÞC 4AF þ10H →C 3AH 6þCH þFH 3ð9ÞIt can be seen that even for typical Portland cements,the stoichi-ometry of the hydration reactions is not precisely known.In particu-lar it is known that the amount of water bound in the C \S \H varies with temperature and that the overall water combined by the alumi-nate containing phases changes over time due to sulfate and carbon-ate contents,and to the extent of ferrite reactions;all of which remain unclear [4,5].When slag is present,the use of bound water as a measure of the overall degree of hydration becomes completely unreliable due to the unknown stoichiometry of the reactions,which will also depend on the slag composition and will be further complicated by the changes in C \S \H composition which occur in blended materials.In recent decades,the use of image analysis [6]and quantitative X-ray diffraction [7–10],particularly coupled with Rietveld analysis,has proven to be effective for the measurement of the degree of reaction of clinker in cement pastes.There is good agreement between these techniques [8,11]which can also be used to compute the degree of reac-tion of the clinker components.In principle,these methodologies canCement and Concrete Research xxx (2012)xxx –xxx⁎Corresponding author.E-mail address:Vanessa.Kocaba@ (V.Kocaba).CEMCON-04371;No of Pages 150008-8846/$–see front matter ©2011Elsevier Ltd.All rights reserved.doi:10.1016/j.cemconres.2011.11.010Contents lists available at SciVerse ScienceDirectCement and Concrete Researchj ou r n a l h o m e p a g e :h t t p ://e e s.e l s e v i e r.c o m /C E MC ON /d e f a ul t.a s palso be used to measure the degree of reaction of the clinker component in blended systems.Measurement of the degree of reaction of the SCM itself poses new challenges.The reactive part of most of these materials is amorphous, so it cannot be measured directly by X-ray diffraction but the homo-geneous regions of slag can be detected and quantified by image anal-ysis[12,13].Several authors[14–20]have used selective dissolution methods (discussed in more detail below)whose intention is to dissolve the re-action products and unhydrated cement,leaving the unreacted slag.It has also been suggested[1,21]that differential thermal analysis(DTA) can be used to recrystallise slag at high temperatures(between800°C and1100°C).Some studies[22–24]have reported the use of cumula-tive heat obtained from isothermal calorimetry or the volume changes associated with chemical shrinkage.The advantage of these methodol-ogies is that they are continuous and in-situ.The problem,however,is to convert the resulting curves to a degree of slag reaction.This paper evaluatesfive methods to measure the degree of reac-tion of slag in blended pastes:–Selective dissolution.–Recrystallisation of slag from differential scanning calorimetry.–Image analysis from BSE grey level images and EDS mappings from SEM.–Cumulative heat evolution curves from isothermal calorimetry.–Chemical shrinkage curves.2.Previous work on the selected methods2.1.Selective dissolutionThis method is based on a preferential chemical dissolution of the hydration products and unhydrated cement[14–20]leaving the unreacted slag.In recent studies[19,20,25]a modified method was pre-sented which was used in this work.Its principle is based on the as-sumption that clinker phases,their hydrates and the hydrates formed from the slag are mostly dissolved leaving the unhydrated slag as a res-idue.Ethylenediaminetetraacetic acid(EDTA),triethanolamine and so-dium hydroxide solution are claimed to dissolve the clinker minerals and calcium sulphate,at pH11.5,without a notable dissolution of the slag.Precipitation of silica and hydroxides is avoided by the addition of sodium hydroxide[14].By means of a comparative study,Luke and Glasser[17]concluded that this EDTA based modified method of Demoulian[14]was the most suitable.Previous researchers already noted that in fact the dissolution is incomplete.Taylor and Mohan[26]noted that large corrections must be made for incomplete dissolution of others phases,and esti-mated the error on the results to be about±10%.In previous studies [27,28],the authors mentioned that besides slag,some cementitious phases(such as periclase and aluminate)and hydrated phases from slag(hydrotalcite)are not dissolved either by selective dissolution. In addition,Goguel[29]identified high amounts around2to5%of undissolved cement hydration products.2.2.Differential thermal analysis/differential scanning calorimetryOne of the oldest method to determine the glass content of slag is thermal analysis:differential thermal analysis(DTA)is the most used [21,30–34]with differential scanning calorimetry(DSC)[35]as an al-ternative.Thefirst reversible exothermic peak in the temperature range700–800°C corresponds to the glass-transition temperature T g.This transition temperature mainly depends on thermal history (cooling rate)and structure[36].The two exothermic peaks with well-defined maxima in the range925–1040°C are attributed to the devitrification ing X-ray diffraction,these peaks were respectively assigned to merwinite(metastable phase)and melilite with minor components(such as larnite)[21,35].It has been suggested that quantification of the peaks could be used to determine the degree of reaction of slag[1,21,37,38].Howev-er,it is not always easy to isolate the contribution of anhydrous slag because of the background contribution.2.3.Backscattered electron images analysisBackscattered electron images(BSE/IA)allow phases to be identi-fied according to their brightness,which depends on their average atomic number.Several studies have shown that the amount of unreacted cement measured this way corresponds well to the other in-dependent measures of degree of hydration[39].For a cement paste, Scrivener et al.[39]showed that tenfields at400×magnification were sufficient to give a standard error of around0.6%.Another statisti-cal analysis[40]showed that a set of30images at200×magnification gave a mean with an error of b0.2%in pastes and mortars.In this study [40]50fields were analysed at200×magnification to obtain the lowest reasonable standard error.More recently,it was shown that the degree of hydration of cement measured by BSE/IA agrees well with that obtained by X-ray diffraction–Rietveld analysis[8].The amorphous component of a given slag source generally has a homogeneous grey level,which should allow it to be identified by image analysis.Brough and Atkinson[12,13]used this to quantify the degree of reaction of slag in alkali-activated cement mortars. Therefore,BSE/IA seems to have good potential for slag blended systems.2.4.Isothermal calorimetryIsothermal calorimetry is mainly used to the heat released by the hydration reaction at early ages(first24h)while at longer times the heat output is quite low and hardly resolved from the back-ground.Nevertheless previous researchers[41,42]suggested that fol-lowing the long term heat evolution of blended pastes could allow the reaction of supplementary cementitious materials to be monitored. This technique is investigated in the present study.2.5.Chemical shrinkageMeasurement of chemical shrinkage is based on the fact that the volume occupied by the hydration products is lower than that of the reactants.This is due to the fact that“water”has a lower specific volume when bound to a solid than when free in a liquid as reflected in the following equation:V cement t¼0ðÞþV water t¼0ðÞ>V hydrates tðÞð10ÞWhere:V cement(t=0):initial volume of cement;V waters(t=0):initial volume of water;V hydrates(t):volume of hydrates at time t.The method chosen here is dilatometry based on the protocol developed by Geiker[24]and optimised by Costoya[43].3.Materials and methods3.1.MaterialsThe chemical compositions of the three cements and the two slags investigated are given in Table1.2V.Kocaba et al./Cement and Concrete Research xxx(2012)xxx–xxx3.2.Mix design and sample preparation60%wt of cement and 40%wt of slag were preblended together for 5h in a TURBULA shaker –mixer to ensure a good homogenisation of the mixture.Hydrated mixes were prepared at room temperature (20°C)with deionised water.To avoid any scattering of measured data due to the quantity of mixed components,160g of paste were mixed in one batch to provide all the specimens for all analyses (calorimetry,chemical shrinkage,SEM and XRD).The cementitious pastes were mechanically mixed (IKA LABORTECHNIK RW20.n)at a speed of 500rpm for 3min,stopped for 2min and finally mixed at 2000rpm for 2min.The neat cement pastes were prepared at a water to cement ratio (by weight)of 0.40while the water to cement ratio of the blend pastes was adapted so that the volume to water binder remains the same as for the pure cement;this corresponds to a 0.42water to solids ratio by weight for the 40%slag blend.The hydration was stopped at different ages ranging from a few hours to several days.At early ages the hydration was stopped by freeze-drying.The sample was frozen at −80°C in a cold mixture of solid CO 2and liquid ethanol and subsequently dried by sublimation.At later ages,the water in older samples was removed by solvent ex-change in isopropanol for one week.Once dried,all specimens for SEM examination were impregnated under vacuum in an epoxy resin (EPOTEK 301)and carefully polished with decreasing grades of diamond powders down to 1/4μm.3.3.Selective dissolutionSelective dissolution was used according to the protocol given by Luke and Glasser [17]and recently used by Dyson [25].The following solutions were used:–0.05M ethylenediaminetetraacetic acid (EDTA);–0.1M Na 2CO 3solution;–a 1:1solution (by volume)of triethanolamine:water mixture;–1.0M NaOH.The different steps are the following:–125mL of EDTA and 125mL of Na 2CO 3were mixed together in a one litre conical flask.–12.5mL of the triethanolamine/water mixture was then added and the pH was checked to be 11.6±0.1.If necessary,the pH was adjusted by addition of small quantities of 1.0M NaOH.–A 0.25g of ground sample was then weighed and slowly added to the mixture in the conical flask while agitating the flask to avoid agglomeration.–The mixture was shaken in a mechanical shaker,for 30min.–The mixture was filtered through a vacuum filter using GF/C filter paper supported on a glass frit (before use the GF/C filter paper was dried at 105°C and weighed).–Care was taken to wash all residual material from the conical flask and also the walls of the funnel on to the filter.–The residue on the filter paper was washed with deionised water seven times and three times with methanol.–The filter paper was carefully removed and dried in an oven at 105°C until a constant weight was achieved.This method was followed for cement,and cement plus slag hy-drated samples.In order to study the reliability of the selectiveTable 1Chemical composition of raw materials from X-ray fluorescence analysis.Oxides Cement A Cement B Cement C Slag 1Slag 8Error SiO 224.6820.5121.0136.6134.600.40Al 2O 3 2.11 5.10 4.6312.2119.980.20Fe 2O 30.43 3.33 2.600.850.470.10CaO 68.6761.2964.1841.5932.480.40MgO 0.58 2.82 1.827.189.170.10SO 3 1.82 2.78 2.780.63 1.990.10K 2O 0.06 1.400.940.280.780.04Na 2O 0.170.240.200.180.160.03MnO 0.010.050.030.140.060.01TiO 20.050.190.140.350.670.01P 2O 50.450.370.400.010.010.01LOI 0.97 1.94 1.26−0.03−0.370.10Na 2Oeq 0.22 1.160.810.360.670.07CO 2 1.300.80 1.40––0.20Total100100100100100–Fig.1.Schematic grey level histogram for hydrated cement –slag paste at 20°C.Fig.2.Grey scale histograms showing the different components of Cement A –Slag 1paste at 28days (a)before and (b)after application of a median filter.3V.Kocaba et al./Cement and Concrete Research xxx (2012)xxx –xxxdissolution,the residues were analysed by X-ray diffraction and ex-amined by SEM.3.4.Differential scanning calorimetryDifferential scanning calorimetry measurements were made with a Netzsch DSC/DTA Model 404C Pegasus,using a 10°C/min heating rate.The hydrated samples were ground,weighed (20±4mg)and placed in an alumina crucible pan,with an empty alumina crucible as a reference.A nitrogen flux was maintained in the heating chamber to avoid carbonation of the samples during the experiment.3.5.Image analysis from BSE grey level images and EDS mappings from SEMThe polished sections were studied in backscattered electron (BSE)mode using a FEI quanta 200SEM at an accelerating voltage of 15kV.Fig.3.BSE-image analysis combined with elemental mapping illustrated on example of Cement A –Slag 8paste at 90days.Fig.4.Heat flow of 3cements with different experimental conditions.4V.Kocaba et al./Cement and Concrete Research xxx (2012)xxx –xxxThe phases were discriminated on the basis of the grey level histogram as shown in Fig.1.Slag 1had a grey level suf ficiently different from that of calcium hydroxide (CH)to allow its discrimination on the basis of the grey level only and after the application of a median filter,as illustrated in Fig.2.A median filter replaces a pixel value by the median value of the pixels in the filter (3×3)and reduces the noise produced by imperfections in the image,while preserving strong contrast varia-tions.On the other hand,Slag 8had a composition and density which lead to a grey level matching exactly that of CH,which pre-vents the discrimination of the two phases on the basis of grey level segmentation.Therefore,in order to have a consistent methodology the slag in both systems was discriminated and segmented on the basis of their chemical signature using EDS chemical mappings of magnesium (signi ficant levels of magnesium being present in the slag while not in CH)in addition to grey level as described below.The challenge of this approach is the time to acquire Mg maps with a conventional EDS detector.To improve this,a silicon drift detector (SDD),type XFlash 4030Detector from Bruker AXS Microanalysis was usedwhich can accept a maximum input count rate of one million counts per second (cps).It also has a large active detecting area of 30mm 2(com-pared to 10mm 2for the conventional EDS detector)and at the same time achieves very good energy resolution of 133eV (Mn K α)at 100,000cps.Even with this fast detector the time required to acquire 150–200fields was about 10h,but this was automated to run overnight.For all blended systems,as illustrated in Fig.3,the procedure consisted of:▪Acquisition of 150–200BSE images (recorded in 30s)combined with Mg maps (recorded in 1min 30s),at a nominal magni fica-tion of ×1000(corresponding to 254×190μm),at an accelerating voltage of 15kV and a number of counts between 80,000and 100,000cps.▪Image analysis processing which combined the BSE image with the Mg map.The grains of unreacted slag were identi fied when the grey level of the pixel corresponded to the slag (from the BSE image)and contained Mg (from the EDS mapping image).▪Calculation of the degree of reaction according to Eq.(15).Table 2Undissolved materials and corresponding degree of reaction of slag after selective bel of samplesUndissolved materials (%)Degree of reaction of slag (%)AverageStandard deviation Average Standard deviation Anhydrous S860.1 6.0––Anhydrous A-S867.5 5.7––Anhydrous B-S863.8 5.0––Anhydrous C-S861.9 5.9––A-S8hydrated for 1day 71.6 1.8−79.0 4.4B-S8hydrated for 1day 66.5 1.8−66.3 4.6C-S8hydrated for 1day 65.2 5.8−63.114.6A-S8hydrated for 90days 72.8 4.2−82.010.5B-S8hydrated for 90days 77.4 3.5−93.58.8C-S8hydrated for 90days70.14.0−75.19.9Fig.5.XRD patterns of Cement B hydrated 90days and Cement B –Slag 8hydrated 90days after selectivedissolution.Fig.6.BSE image of Cement B –Slag 8hydrated 90days after selective dissolution (C:Cement and S:Slag).5V.Kocaba et al./Cement and Concrete Research xxx (2012)xxx –xxx3.6.Isothermal calorimetryThe heat of reaction of the pastes at 20°C was measured with an iso-thermal calorimeter (TAM Air from TA instruments).It consists of 8par-allel twin measurement channels maintained at a constant temperature:one from the sample,the other for the reference sample.Preliminary work [44]underlined that it is critical to balance the speci fic heats of the sample and reference,particularly for measure-ments over the long time periods used here,where the rate of heat evolution becomes very low.In this work,the reference was deionised water calculated to have the same speci fic heat as the paste [45]:C paste p¼x water C water pþx cement C cementpð11ÞWhere:x water :mass fraction of water in paste;x cement :mass fraction of cement in paste;C pwater:speci fic heat of water;C pcement:speci fic heat of cement.Considering,the water-cement ratio of 0.4,C p water=4.18J.g −1.K −1[46]and C p cement=0.75J.g −1.K −1(based on the measured values for tricalcium silicate and dicalcium silicate [47])we found a speci fic heat of cement paste of 1.73J.g −1.K −1.The optimal quantity of paste was 15g with a 6.2g glass ampoule of water as a reference.The thermal inertia is expressed by the time constant of a calorim-eter which depends on two parameters:the sample heat capacity and the heat transfer properties of the calorimeter.The measured time constant has been used to correct the output signal (Tian correction)for the thermal inertia of the calorimeter especially at very early ages as shown below:P t ðÞ¼εU þτdUð12ÞWith:P (t ):the thermal power produced in the sample (Watts);U :the voltage output of the heat flow sensors (Volts);ε:the calibration factor (W/V);τ:the time constant of the calorimeter (s)which has been calcu-lated to be 4min.Fig.4shows the importance of correct calibration and choice of reference sample to the rate of heat evolution curves.Although the general shapes of the peaks are similar,the absolute values vary,which can lead to substantial errors when the total heat evolution is calculated by integration over long times.3.7.Chemical shrinkageThe chemical shrinkage setup was designed and optimised at EPFL [43]and it consists of a cylindrical flask (2cm height by 1cm of diam-eter)that contains the paste,on top of which a pipette is connected.The level of paste introduced in the flask was kept constant in all measurements and equal to 1cm (5g of paste).The paste was tapped in order avoid the presence of entrapped bubbles.Water was added immediately to the top of the paste,taking special care to avoid as much as possible the dilution of the paste.Table 3Results of analysis of residues after selective dissolution.100%dissolved phasesPartly dissolved phases Non-dissolved phases Anhydrous A-S8C 3S,C 2S,C 3A,anhydrite–Slag 8Anhydrous B-S8C 2S,C 3A,C 4AF,anhydrite C 3S Slag 8Anhydrous C-S8C 2S,C 3A,anhydrite C 3SC 4AF,Slag 8Hydrated A-S8EttringiteC 3S,C 2S,C \S \H,CH Hydrotalcite,Slag 8Hydrated B-S8C 4AF,ettringite C 3S,C 2S,C \S \H,CH Hydrotalcite,Slag 8Hydrated C-S8C 4AF,ettringiteC 3S,C 2S,C \S \H,CHHydrotalcite,Slag8Fig.7.Degree of reaction of slag from selective dissolution after corrections suggested in [17].Fig.8.DSC curves of anhydrouspowders.Fig.9.DSC curves of Cement A blended with Slag 8at different ages.6V.Kocaba et al./Cement and Concrete Research xxx (2012)xxx –xxxWater is added on top of the cement paste until it fills also the pi-pette.The system is sealed at the interface between the pipette and the flask with rubber lids and on top of the pipette with a coloured oil drop.This coloured oil drop is used as a tracer in the image analy-sis of the pictures of the capillary taken with a webcam.The flasks are maintained in a thermostatic bath at 20°C to avoid effects of heat re-lease on volumetric changes of the paste.As the hydration proceeds and the paste shrinks,the level of water in the pipette decreases.This level is monitored using a webcam con-nected to a computer that allows automated acquisition every 5min.To extract the level of water in the pipette,the pictures were numer-ically processed.Each curve presented is the average of a minimum of 3,but mostly 6,replicates of a cement paste system.4.Results and discussion 4.1.Selective dissolutionConsidering that the selective dissolution does dissolve the unhy-drated cement grains and their hydration products,leaving onlytheFig.10.Method for background removal algorithm on DSC curve of Cement A –Slag 8hydrated 7days.Fig.11.Apparent degree of reaction of Slag 8from DSC in Cement A –Slag 8blended pastes.7V.Kocaba et al./Cement and Concrete Research xxx (2012)xxx –xxxunreacted slag grains as undissolved residue,the degree of hydration of slag grains in pastes can be calculated from Eq.(13):αSelectivedissolutionSLAG¼R cement −R pasteR cementð13ÞWhere:R cement :undissolved residue from the blended anhydrous cement;R paste :undissolved residue from the cement paste.Table 2shows the percentage of non-dissolved materials and the supposed degree of reaction of slag for the hydrated mixes.From the data it is evident that the undissolved materials (expressed as a per-centage of the total amount),do not correspond only to the unreacted slag because the percentage is much higher than the initial content of the slag (40%wt),which would imply a negative degree of reaction.In order to study the reliability of the selective dissolution,the res-idues were examined by XRD and SEM.The residues showed undis-solved phases (other than slag)in both the anhydrous blends and hydrated samples.Fig.5shows XRD patterns of Cement B hydrated for 90days and Cement B –Slag 8hydrated 90days after selective dis-solution.The pattern of Cement B clearly shows the presence of phases from the cement that selective dissolution should remove in the blended pastes:notably belite and portlandite.The pattern from the blended paste also indicates the presence of hydrotalcite from the hydration of slag and which should also be removed by the selec-tive dissolution.Fig.6shows the residue from the selective dissolu-tion of Cement B –Slag 8hydrated 90days,embedded in resin and polished for examination by SEM-BSE,this clearly shows the presence of undissolved cement grains,hydrated phases and agglomerates.The characterisation of the different phases in the selective disso-lution residues by XRD analysis and SEM is summarised in Table 3.For the anhydrous blends,selective dissolution did not completely dis-solve the clinker phases for Cements B and C.Dissolution was better for Cement A probably due to its higher fineness compared to Ce-ments B and C.For the hydrated mixes,only ettringite and ferrite were 100%dissolved,the other anhydrous and hydratedphasesFig.12.Degree of reaction of slag from SEM-BSE-IA-mapping in (a)systems A,(b)systems B and (c)systemsC.Fig.13.Degree of reaction of (a)Slag 1and (b)Slag 8from SEM-BSE-IA-mapping in blended pastes.8V.Kocaba et al./Cement and Concrete Research xxx (2012)xxx –xxxwere not completely dissolved and hydrotalcite was also observed in the residues by XRD.Since the sample mass of0.25g appeared very small,measure-ments were repeated adapting the procedure with higher masses (0.5g,1.0g and1.5g)and some tests with smallerfiltration system were also conducted.These modifications made no significant differ-ence to the results.Some authors[17]have proposed a modification to recalculate the degree of reaction of slag with the following formula:αSelectivedissolution SLAG tðÞ¼100−w2þ%SLAG t¼0ðÞ%DISSOLVEDSLAG w1ðÞ−%CEMENT t¼0ðÞC r w1ðÞSLAG1100ð14ÞWhere:w1:weight of sample(ignited weight);w2:weight of residue(105°C dry weight);C r:percentage of residue from cement divided by100;%SLAG(t=0):percentage of initial slag in the blended cement(equal to40%);%CEMENT(t=0):percentage of initial cement in the blended ce-ment(equal to60%).%DISSOLVED SLAG:assumption of6%of slag dissolves.This approach gives the results shown in Fig.7.Although the degrees of reaction are now positive,they are very high,especially at1day.It might be argued that further work,for example,on optimising the grinding process could have led to better results for the selective disso-lutions method.However,this underlines the problem of the reproduc-ibility of the method betweens labs.In a recent study of selective dissolution methods forfly ash,Ben Haha et al.[48]noted the different assumptions needed to calculate the amount of reaction are a major cause of errors,which renders such methods inadequate for quantifying the degree of reaction.It is also clear from the literature that very diver-gent results are reported for this method by different workers studying nominally similar slags:For example,Escalante et al.[20]find degrees of reaction of about20%after3months compared to values of around 40%reported by Luke and Glasser[17]and Lumley et al.[19].In the light of the current results and the diversity of results in the literature,we consider,that;while such methods could be suitable to enrich materials with respect to certain phases for other characterisa-tion methods such as NMR[28,49],they are not reliable for the quan-titative determination of the degree of reaction.4.2.Differential scanning calorimetryFig.8shows the DSC curves of three anhydrous powders:pure Ce-ment A,pure Slag8and the A-S8blended powder.For the raw slag and the blended powder,the recrystallisation peaks of slag can be identified between850and1050°C.The objective was to isolate and measure the recrystallisation peak in order to quantify the degree of reaction of slag.The experiments were conducted on one blended system(Cement A–Slag8).The DSC curves at various hydration times(Fig.9)show that the recrystallisation peak decreases with time,but there is also a strong change in the background.The large contribution of the background was already noted in previous DSC analyses on plain OPC[50].To remove the contribution of the background,a manual method with the DSC software was judged too subjective.So a background re-moval algorithm was applied with two different choices of reasonable backgrounds which led to two different degrees of reaction of slag for each analysed sample.An example of the method is shown in Fig.10 and the results are shown in Fig.11.As for results from selective dis-solution,it is seen that there is an unreasonably high degree of hydra-tion at7days and little evolution in time thereafter.It was concluded that the DSC method was unreliable due to the large error produced by the background.4.3.Image analysis from BSE grey level images and EDS mappings from SEMAssuming the original volume of the slag in the paste,the degree of reaction of slag can be estimated by image analysis of the area frac-tion(equivalent to volume fraction)remaining at a given time:αSEM‐IASLAGtðÞ¼Vf anhydrousslag t¼0ðÞ−Vf anhydrousslag tðÞanhydrousslagð15ÞWhere:Vf anhydrous slag(t=0):remaining volume fraction of initial anhy-drous slag;Vf anhydrous slag(t):remaining volume fraction of unreacted slag after time t.Fig.12shows the degree of reaction of slag for all the systems as a function of type of cement.With the fast EDS detector it was possible to obtain results with reasonable precision;the errors indicated in Fig.12take into account the deviation between different sets of im-ages from the same sample and the deviation from different possible treatments to define the border of slag grain.The errors are higheratFig.15.Degree of reaction of Slag8from SEM-BSE-IA-mapping,DSC and selective dissolution.0,0110100102030405060708090100Degreeofreactionofslag(%)Time (days)DR-SEM of S8 in A-S8DR-SEM of S8 in B-S8DR-SEM of S8 in C-S8DR-Dissolution of S8 in A-S8DR-Dissolution of S8 in B-S8DR-Dissolution of S8 in C-S8Fig.14.Degree of reaction of Slag8from selective dissolution and SEM-BSE-IA-mapping.9V.Kocaba et al./Cement and Concrete Research xxx(2012)xxx–xxx。