01-WP-F-008 异常改善计划书A0
品质异常单怎么写改善对策模板

品质异常单怎么写改善对策模板品质异常单怎么写改善对策模板一、引言品质异常是企业在生产过程中难免会遇到的问题之一。
对品质异常的及时处理和改善是保证产品质量并提升客户满意度的关键。
品质异常单作为记录和追踪品质异常问题的工具,在品质管理中起到至关重要的作用。
本文将从品质异常单的定义和重要性入手,深入探讨如何撰写改善对策模板,帮助企业提高品质管理水平。
二、品质异常单的定义和重要性1. 品质异常单的定义品质异常单是指记录和追踪品质异常问题的文件,通常包括问题描述、发生时间、责任人、原因分析以及改善对策等信息。
通过对品质异常进行有效的记录和跟踪,企业可以及时了解问题发生的情况,并采取相应的改善措施,以确保产品质量和客户满意度。
2. 品质异常单的重要性(1)问题记录和追踪:品质异常单可以帮助企业准确记录和追踪相应的品质异常问题,为问题解决提供可靠的依据。
(2)问题分析和改善:品质异常单中包含的问题描述、原因分析和改善对策等信息,可以帮助企业深入了解问题的本质,找出问题的根本原因,并制定相应的改善对策。
(3)沟通和合作:品质异常单可以促进内部各个部门之间的沟通和合作,加强问题解决的效率和协同性。
三、品质异常单改善对策模板的撰写在撰写品质异常单改善对策模板时,可以按照以下步骤进行。
1. 问题描述在品质异常单中的问题描述部分,应该对问题进行具体而准确的描述,包括问题发生的具体情况、对产品质量和客户满意度的影响等。
通过清晰的问题描述,能够帮助读者全面了解问题的性质和严重程度。
2. 原因分析在品质异常单中的原因分析部分,需要对问题的根本原因进行深入分析。
可以使用五个为什么的方法,逐层剖析问题的根本原因。
还可以运用鱼骨图、流程图等常用工具,帮助读者更好地理解问题产生的原因。
在原因分析过程中,需要避免主观臆断,而是进行事实依据和数据分析。
3. 改善对策在品质异常单中的改善对策部分,应该提出明确具体的改善对策和行动计划。
改善对策的制定应该根据问题的原因分析,确保对策的针对性和有效性。
QA-003品质异常及损耗工时单(A4单面30本)
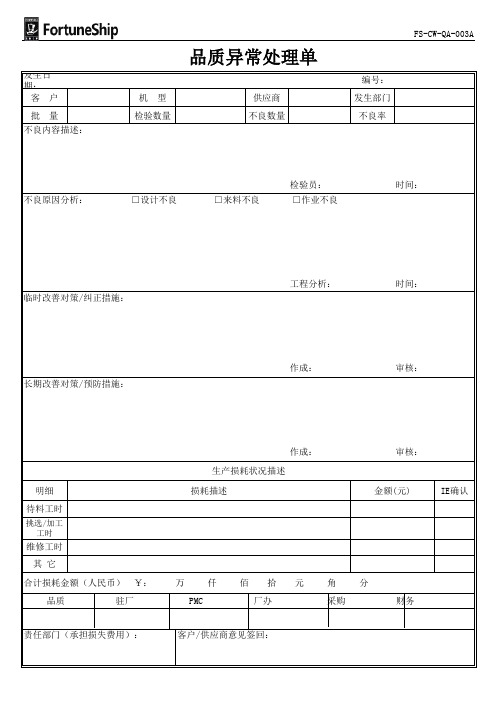
发生日期:客 户机 型供应商发生部门批 量检验数量
不良数量
不良率
检验员:
时间:
工程分析:
时间:
作成:
审核:
作成:
审核:
明细IE确认
责任部门(承担损失费用):客户/供应商意见签回:
合计损耗金额(人民币) ¥: 万 仟 佰 拾 元 角 分
品质 驻厂 PMC 厂办 采购 财务
维修工时其 它
挑选/加工工时
待料工时
不良内容描述:
生产损耗状况描述
损耗描述金额(元)不良原因分析:
长期改善对策/预防措施:
临时改善对策/纠正措施:
FS-CW-QA-003A
品质异常处理单
编号:□设计不良 □来料不良 □作业不良。
以8D手法完成品质异常改善
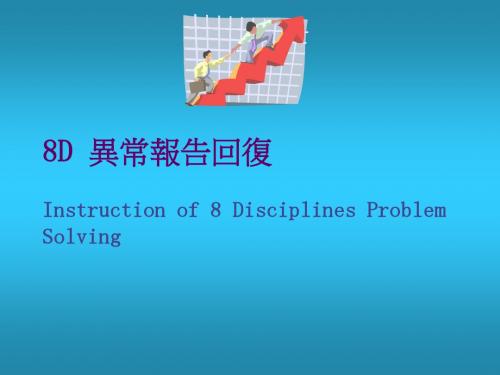
D4- Identify the root causes 介定根本原因
首先考虑一下出现目前情况的可能原因。 集中精力考虑手头现有的资料,同时注 意倾听别人的意见。 尽力做到客观地去看待问题会使你将那 些表面上看来错综复杂的问题简单化。
D4- Identify the root causes 介定根本原因
8D 異常報告回復
Instruction of 8 Disciplines Problem Solving
異
8D 問題解決的指引
小組組成 問題說明 根本原因
臨時措施
長期糾正措施
效果確認
OK
NG
預防再發生
結案(嘉許)
解决问题
主动地承认问题的存在, 对问题寻根究底。 找出解决方案和采取行动, 都需要作出大量努力
了解到問題的來源
必须征求别人对于为什么会出现这种问题的看 法,并且要进一步了解别人是如何工作的。 一旦做完以上那些事情,就能够详细写出认为 什么是问题之真正所在,甚至可以画出一张图 表来。人们常常并不是不知道如何解决问题, 而是没有花时间去真正认清目前的形式。 就像一名医生,只有掌握了一系列症状后,才 能作出正确的诊断。
咨询
如果这个决策可能会直接影响到别人。 比如工作调动,向他们进行咨询可以使 你评估正在考虑的有关意见的好处,甚 至找到新的解决方法。
测试如果正要对一个棘手的问题进行决策, 那么对不同的解决方法进行测试是找出 哪个方法会产生最优结果的上策。 小規模、小批量、模擬試行 考虑的时间过长,或用太多的时间去做 试验,解决问题会更难
利弊法
在对可择方案加上制约条件后,你的选 择就剩下很少了。这时你需要采用利弊 法进行筛选。 比較各方案之好處及坏處,並考慮副作 用及客觀因素
异常改善报告-回复模板

文档密级:《抛光作业规范》设定的产品非直接外观面所对应的模区分 C ontrol :(明确防止再发生的手段?)完成日期完成日期流程标准变更(含附件)责任人仁表面抛光砂纸太粗(600#)。
的间隙。
3.SIP 规定‐‐‐B 壳和A 壳、电外、侧键空配后进行检查。
因为规定不合理导致QC 在整机装配时无法看见侧键变形造成的间隙过大的现象,从而误判OK 。
《抛光作业规范》设定的产品非直接外观面所对
应的模仁表面抛光砂纸调整成800#。
图2图1C8650 B壳 模具抛光作业规范第1页,共2页
异常改善报告11文档密级:长期改善后实际效果改善动作已全部完成,效果确认OK 李勤云2011-7-18
完善模具的《抛光作业规范》:
提升定模仁中的非直接外观面的抛光等级(从600#提升到800#)2011-9-14华为机密,未经许可不得扩散第2页,共2页。
面向生产WP的品质改善研修——质量改进的工具与技术

人员
4、因果图
★Tips
◆要因的抽出是否有遗漏? •有否遗漏大的要因?-机械别 –材料别
–治工具别 –作业者别 –方法别 •对于末端的要因,是否能具体地采取行动(能取得数据或条件)?
◆各要因是否有系统的整理? •大骨/中骨/小骨是否按照次序整理?要因的大小是否相反? •是否排上无特别关系的要因? ◆特性要因图是否想办支使其容易采取对策? •认为影响力大的要因是否明确? •要因的表达是否笼统? •要因是否分类为自部门与他部门? •现在已标准化,以及尚未标准化的是否明确? •现在所测定或图表化的是否明确? •要因可能测定与否? •要因控制与否? •对于特性的贡献度以及其它的要因的影响是否被检讨而加以整理?
11.耐 压
不良现象
4、因果图
★概念 对作为问题的特征(结果)及对其影响的要素(原因)进行整理,汇 总成鱼骨状的图形,称之为因果图(特性要因图、鱼刺图、石川图) ★结构
大原因(大骨) 小骨 中骨
主骨
特性
特性(结果) 因素(原因)
4、因果图
★作用
◆改善解析——QCDMS,配合排列图分析
◆制程管制——对异常找出关键因素、查明真正原因 ◆制定操作标准——特性要因分析清楚后,可针对原因适当因应 ◆实施品管教育——制作特性要因图的过程就是教育
查检重点
一般的标准形态 检讨设定的区间幅度及测量人员的 判读有无偏差存在 理论上,对规格值而言,已能控制下 限值,或是某些数值以下的数值不取 作假的测试定数据,检查失误,测定 误差等均可能产生此一现象 此现象往往由于多组不同平均值的 分布混合所致,判断必须加以层别化 来分析 一般为两组不同的数据混入所致,必 须加以层别后来判断问题之所在 数据中有一小部份的不同群组的数 据混入,必须调查数据的履历,确认 工程有无异常、测量上有无异常, 或者有无其它工程的数据混入等。
品质异常改善报告(推荐3篇)

品质异常改善报告第1篇1、锂电生产工艺和品质控制流程的学习与实践。
通过学习圆柱锂离子电池工艺流程图,各型号圆柱锂离子电池SOP、工艺文件,品质控制计划文件,结合日常实践交流工作,熟悉、掌握了锂电生产工艺、品质控制流程和各工序品质控制重点等相关专业知识并运用到实际工作中,督导IPQC严格按工艺文件和品质标准文件执行现场的品质检验工作。
2、品质异常处理流程的学习与实践。
学习公司内部品质异常处理的流程:异常确认,原因分析及对策拟定,改善对策执行及确认,异常跟进处理,异常结案;异常的确认严格依据检验标准执行,分析异常的初步原因并反馈至相关部门协助他们共同处理,使现场品质异常得到快速有效的处理;工作中定义了QC检验注意事项:产品异常和制程异常的区别,现场人、机、料、环、法要素的把控,异常状况详细信息5W,2H的正确填写,并在早会上对QC宣导。
3、品质专案的学习和品质改善会议的召开。
五月初期和中期参加了公司电池壳体生锈品质改善会议,熟悉并撑握品质专案改善处理流程,会议上定出了品质异常解决方案和完成时间,会后督导和跟进改善效果;品质改善会议主要以品质周会为主,每周提前一天把上周的品质数据以表格和图表的形式反应出来,提交部门经理审核后向各部门召开品质周改善会议,品质周会的召开促进了部门内部,部门与部门之间更多的沟通、互动、交流与学习,锻炼了个人独立分析和处理问题的能力。
品质异常改善报告第2篇经对近期时间所出现的异常缺失原因所作的反思,为预防类似事件再次发生,制定如下预防改善方案。
1、尔后不论何种机台生产生产何种料号,严格要求于生产前均需要制作首件,且每轴皆要制作首件,首件经品保确认OK后方可正式量产,预防PIN钉偏造成尺寸偏移不良的出现;2、严格要求品保确认首件的先后顺序,先确认首件外观,再确认首件尺寸,并要求将确认结果记录在“首件检查日报表”内;3、品保人员确认尺寸时,要求结合工程提供的简图用卡尺测量槽/边/孔/外形尺寸,并将测量数据记录在“首件检查报表”内;4、不能用卡尺测量的尺寸,品保人员要将首件送二次元处对尺寸作全测确认首件;品保首件确认OK后,送品保组长审核确认并建立首件OK样品,将首件样品放置于制作机台处,以便操作员/品保对量产后产品以首件作对比确认用;5、量产中生产下机的每趟板均要求操作员做自检确认,主要检查底板与面板(底板主要检查有无漏捞/未捞透,面板主要检查多捞及刮伤等),操作员及品保检验均要记录检查数据与结果,特别是品保人员要记录检验的数量与频率,要与生产记录相对应;7、产线干部/品保干部对组员的执行状况作验收/确认/查核,未按要求作业的人员要进行必要的处罚;8、每日每周对组员进行品质不良宣导/客诉宣导,让其了解厂内及客诉品质异常,教育训导员工品质意识;9、利用公司相关品质统计表张贴公布品质,使全体员工认识品质,优劣对比激发品质竞争气氛,提升公司品质现状;10、干部自我反省,增强责任感与使命感,以身作则,发挥督导力与管理力。
工厂产品制程异常处理及改善--课件
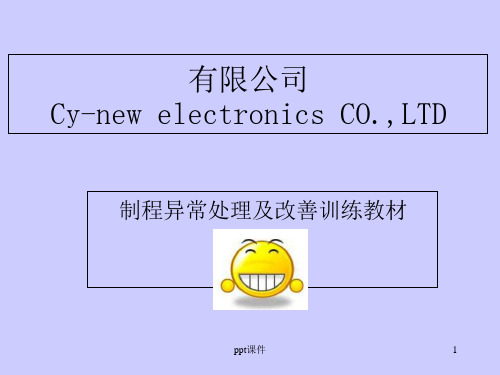
首先,要有稳定的人员
人员的流动高低,往往可以反映员工对企业的认同程度,尤 其高人员流动率的企业,一切成长的条件都会随着人员的流动而 流失。品质也是如此。
新进的员工
工作熟练度低
对机器,工具不了解
对材料不了解
造成太多变因存在
对作业方法不熟练
对品质 p求t课不件认识
8
其次,要有良好的教育训练
现代的企业管理讲究的是多元的专业化,每一项工作均有它的 专业知识及理论基础,如何将这此专业知识及理论基础演化为实 用的技巧,则需要由具有理论基础及专业经验的人来进行,也才 能尽快地填补企业内成员工作经验的不足及理念上的差异造成的 沟通协调的困难。
c,进料不良,前工 程之不良品纳入本工程 中。
3
第二部分:制程异常来源及分类
1,制程异常的来源
任何一个与产品有关的因素变动,产品也就随之 变动,因素变动的大小,产品的特性也随之大小而变 动。总体来讲,影响产品制程异常出现的因素有人, 机器,材料,方法,环境与管理六个方面。
以下,分别举例讲述:
a,异常来源之一
• 材料 (Material) 今品级对吗? 今数量对吗? 今品牌对吗? 今有杂质吗? 今存货适当吗? 今有浪费吗?
• 方法 (Method) 今标准适当吗? 今标准有修订吗? 今安全吗? 今能确保品质吗? 今工作程序适当吗? 今温度、湿度、照明适当吗?
今存放方式适当吗?
今前后工程协良好吗?
ppt课 件
b.不良情报立即回馈并采取改善行动:当发现不良时,应 立即要求前一制程的作业者注意,请其确认不良事实,并请其立 即改善。若前一制程的作业者不改善加工方法,则不良绝不会消 失,则生产线不可再继续生产,否则顺次检查将失效。生产线的 停止,可使管理人员及时发现制程的问题,并采取有效措施处理, 同时可警惕作业者,增强责任感。
制程异常分析改善汇总

防焊前五项制程问题分析:一、防焊空泡:造成原因:1、前处理不良。
(H2SO4浓度、水质、吹干段角度及风量,吸水海棉清洁度、烘干温度)。
2、磨刷后放置时间过长,室内湿度偏低。
3、印刷台面沾有油墨及其它有机溶剂,反沾板面,油墨搅拌不均。
4、预烤不足。
5、曝光能量太低或太高。
6、显影侧蚀太多。
7、HAL浸助焊剂时间太长,锡槽温度太高,浸锡时间太长。
预防措施:1、前处理作业必须按SOP要求生产。
2、磨刷后放置时间不得超过2H ,室内湿度控制在50-60%之间。
3、印刷台面保持清洁,印第一面时台面上垫一张白纸,以保证板面清洁度。
4、预烤温度保持70±2℃,烤后之板保证不粘棕片。
5、曝光能量保持在9-13格。
6、显影点控制在50-60%,避免过多侧蚀。
7、后烤通风保持良好,塞孔板必须分段烘烤。
8、HAL作业须完全按照SOP操作,不可有违规作为。
二、L/Q内圈阴影:原因分析:1、油墨过期。
2、预烤时间过长,温度过高。
3、挡点印刷时,孔环处积墨过多,印刷房湿度不够。
4、曝光前,静置时间过长。
5、显影速度过快,压力过小。
6、棕片遮光度不够。
7、曝光时吸真空压力未能达到要求。
改善对策:1、油墨按照先进先出的方式使用,保证在油墨保质期内使用。
2、预烤时间和温度按SOP要求作业,且烤好后及时取出防止冷烤。
3、印刷房湿度保持在50-60%之间,挡点印刷保持连贯,且印一PNL刮一次网版。
4、预烤后板静置时间不能眼过12H,最连贯4H以内对位完。
5、显影点保持在50-60%之间。
6、选用遮光度及质量较好之棕片生产。
7、吸真空不得低于600㎜Hg,且须保持导气良好。
三、卡锡珠:原因分析:1、印刷塞孔不满(量产板)。
2、退洗板导通孔内油墨未剥除干净。
3、油墨本身质量问题。
4、HAL贴胶未贴好,某些孔呈半覆盖状态。
5、HAL浸助焊剂及浸锡时间过短。
改善对策:1、从印刷各条件去改善塞孔程度。
(刮刀压力、角度、确度、速度、网目T数量)2、选用适合的退洗液,尽可能洗净导通孔内油墨,保证塞孔效果。
01012一天一夜改善模式说明会SEM合理化改善作业说明
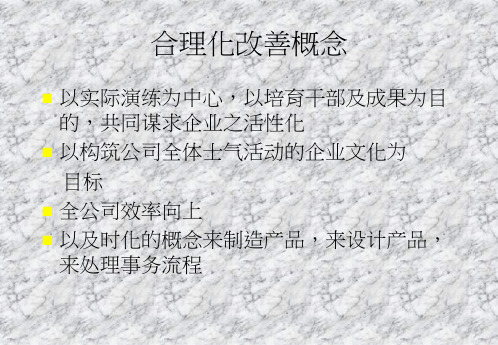
稼动时间
1班制 480‘/日
2班制 920‘/日
早班 0600---1430
中班 1400---2230
休息时间
1130—1200 吃饭 1700—1730 吃饭 0900—0910 休息时间
配置人数 6人/每班
生产前置时间 加工时间+停滞时间
段取能力
用语 1.物的流动
2.情报的流动 3.情报的种类 3-1kanban
a)引取 b)工程内
c)信号 d)其他道具
(滚球等) e)临时
3-2 指示(list)
3-3其 他 ( 电送、信号)
记
号
用语 4.kanban post
a)平准化 b)临时性 c)顺序性 5.工 程
6.生产线 7.客户
8.店面 9.临时放置 顺序性(店面)
段取时间: 10‘/回 段取回数: 5回/日 段取时间愈短,回数可愈多回,批量
可愈小
在库状况
店面在库_____日: 成品 总数/日需求数 500/250=2日
中间在库_____日 中间在制品/日需求数 300/200=1.5日
生产指示
批量生产------生产 前置时间长 计划性生产----制造过剩 后补充生产方式---依后工程需求
确认后方能生产。
合理化改善概念
以实际演练为中心,以培育干部及成果为目 的,共同谋求企业之活性化
以构筑公司全体士气活动的企业文化为 目标
全公司效率向上 以及时化的概念来制造产品,来设计产品,
来处理事务流程
对象工程线名
依工程产线最小的单位 命名
如:NO 1机械加工线 剎车管装配线
活动期间
以公历记法 一般记法
品质改善处理单(QA品质改善票)
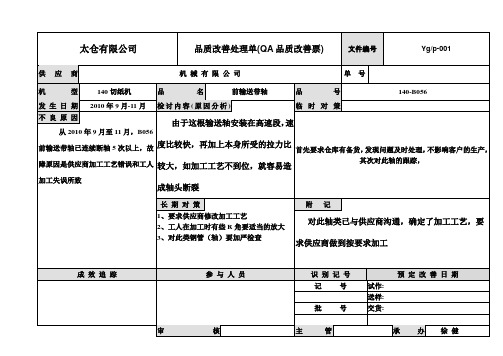
前输送带轴已连续断轴 5 次以上,故 度比较快,再加上本身所受的拉力比 首先要求仓库有备货,发现问题及时处理,不影响客户的生产,
障原因是供应商加工工艺错误和工人 较大,如加工工艺不到位,就容易造
其次对此轴的跟踪,
加工失误所致
成轴头断裂
长期对策
1、要求供应商修改加工工艺 2、工人在加工时有些 R 角要适当的放大 3、对此类钢管(轴)要加严检查
附记
对此轴类已与供应商沟通,确定了加工工艺,要 求供应商做到按要求加工
成效追踪
参与人员
审
核
识别记号 记号
批号
试作: 送样: 交货:
预定改善日期
主
管
承 办 徐健
太仓有限公司
品质改善处理单(QA 品质改善票)
文件编号
Yg/p-001
供应商
机械有限公司
单号
机
型
140 切纸机
品
名
前输送带轴
品
号
140-B056
发 生 日 期 2010 年 9 月-11 月 检 讨 内 容 ( 原 因 分 析 )
临时对策
不良原因 从 2010 年 9 月至 11 月,B056
由于这根输送轴安装在高速段,速
不良专案改善

CY通过团队专案检讨进一步做持续改善,以达到满足CPT客户品质要求 。
Suzhou Chon Yang Electronics Co.Ltd
2. 建立团队
Authority name
林佑泉
Department
专员
responsibility
主导整个专案推动,制定改善的目标和方向, 资源的提供。
100.00% 90.00% 80.00% 70.00% 60.00% 50.00% 40.00% 30.00% 20.00% 10.00% 0.00%
不良項目
M/L错位 M/L折偏 M/L油污 漏黄胶 漏PIN
不良率
65.61% 19.76% 13.44% 1.19% 0.00%
225
65.61% 85.38% 98.81% 100.00% 100.00%
1.后续架模员针对模具打油 后,要先进行模具上下数次 作业,使多余渗出的油渍及 时擦拭,以防作业过程造成 油渍在产品上。 2.另外规定针对机台2H一次 5S清洁。 3.产线外观检查人员先检查 产品外部在检查产品内部, 对于影响产品外观问题的产 品挑出,再经擦拭后流下一 工站。
MFG 李红秀
7/13
Suzhou Chon Yang Electronics Co.Ltd
4.4 漏工序(漏黄胶/漏铆PIN)
Issue 不良图片: 原因分析 1.铆PIN时因速度 过快,PIN脚未铆 紧导致出现PIN胶 脱落现象。 2.产品贴胶区域过 多,贴胶人员易漏 贴胶。 3.产品多工序作业 时,前工序与后工 序之间区分不明确。 4.作业方式不当, 已制品与未制品未 区分开。自检/全 检时未能及时发现 漏工序。 改善对策 1.在铆合治具上加磁,以便将PIN 吸
异常处理PDCA分析步骤

5.4 對策之檢討
直方圖
前次對策改善效果不佳,不良率僅下降0.2%.須重新設定改善目標
5.4.1 提出防止再發生之防呆措施.
單邊計數值管制表 重新對策﹕
責任人
5.4.2 檢討對策的具體化.
單邊計量值管制表 1.繼續挑選15K進行使用.
5.4.3 利用數據資料確認對策內容 5.5 對策之執行
23..A嚴C格T后要內求檢產工線位使的用裸防露靜尖電嘴托鉗盤外,包從雙T/層U開套始管到,避鎖免上理蓋線工時造位成產放品電不損可傷離. 開托 盤.
單邊計數值管制表 發現問題點﹕ACT & PRE B/I無壓﹐維修發現不良品均是由于U601壞造成.
1.2 排出其優先順序﹐并以數字化來顯示問題 單邊計量值管制表 決定問題點:找出U601不良的原因.
二
分析可能原因
腦力激蕩
2.1
用"魚骨圖"以腦力激蕩找出問題的可能原因, 提出要因.
層別法 特性要因圖
2.將此機種之經驗例入到新機種的PFMEA當中,避免后續機種發 生同樣問題. 3.內檢工具使用絕緣材料制作,以避免鐵制工具碰壓壞小原件. 4.對組裝段為員進行定向教育:產品通電后請勿用導電工具進行內部檢查.
長期效果確認﹕自實施上述對策U601不率控制在0.1~0.15%
案例說明
六
效果確認
6.1 確認對策效果
6.2 比較目標值
6.3 掌握成果(有形﹑無形)
6.4 成果的鞏固與宣導.
直方圖
效果確認﹕
管制圖 查檢表
單邊計數值管制表
第二次對策效果明顯,針對第二次對策進行效果分析. 1.由于有防靜電托盤全程使用,避免產品堆積,PCB相碰造成的放 電傷害.
品质异常处理方法及案例-分析ppt课件
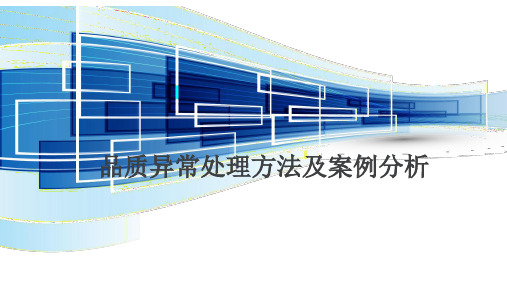
不良原因验证: 取10把用魔术贴扎好的线材,先进行全检无外观问题后,再堆放在一起,然后模拟周转拿线方式滑动魔术贴后, 全检发现其中有2把线材中的2PCS已经被刮伤,证明不良的产生原因成立。
流出原因:
Cable 刮伤不良分析改善报告
制程作业流程为:--- --->拆魔术贴--->电气测试--->绕线并装OPP--->外观检查--->包装;因外观检查在装OPP 之后,当刮伤的位置在绕线的内测时,就会造成检验人员无法检验到,导致不良流出。
2、以上对策展开到相似的产品
20途品,无需处理。
2020/3/31
三、原因分析
Cable 刮伤不良分析改善报告
通过从人员、机器、材料、方法、环境因素逐项分析,可判定由于作业方法不当(使用魔术贴扎线),导致 cable线材刮伤,分析过程如下:
影响因素
分析现状
人员均经过培训后上岗位,外观检
人员 查人员均有上岗证
改善前 魔术贴会刮伤线材
改善后 PE膜不会刮伤线材
2.在绕线工位之前,增加线材外观全检工位,然后在绕线后在检查外观一次,避免刮伤不良漏检验出。
变更作业流程前:--- --->拆魔术贴--->电气测试--->绕线并装OPP--->外观检查--->包装
变更作业流程后:--- --->拆魔术贴--->电气测试--->外观检查(1)--->绕线并装OPP--->外观检查(2) --->包装。切入日期:1月8日,责任人:IE/张
前期(试产)
中期(生产过程)
后期(成品)
品质输入:
FMEA
QCP 异常汇总清单
首件记录表 IQPC 巡检记录表
SPC 异常反馈单 ESD及5S稽核记录表
OQC产品检验报告 产品信赖性检验报告 产品送检记录表 OQC异常反馈单 样品检验记录表
P008 持续改进管理程序

1 目的公司鼓励全体员工围绕公司生产经营管理目标,提高员工综合素质,提升运营效率和服务品质工作等方面,通过全员的共同参与,从质量、安全、成本优化和顾客满意等方面获取改进的潜能,不断改进公司的产品质量和生产率,降低成本,提高顾客满意度、员工满意度,增强市场竞争力。
2 范围2.1 持续改善的范围包括品质提升、技术改进、节能降耗、缩短交期、合理化建议及VAVE项目。
2.1.1品质提升是指有关改进和完善公司产品质量管理体系方面的办法。
2.1.2技术改进是对机器设备、工具、工艺技术等方面所作的改进和革新。
2.1.3提案范围不限于本部门内部,也可以提出其他部门持续改善提案;2.1.4合理化建议是指有关改进和完善公司生产环境和运营管理等方面的办法和措施,主要划分为以下几个方面:●与安全、卫生、环境有关;●降低报废、返工和返修率、消除各种浪费;●生产流程优化、费用减低、人员优化等;●仓储物流包装方面的建议;●降低能耗方面的建议;●提高劳动生产率方面(设备、工艺、技能、技术)的建议;●顾客反馈,如抱怨、投诉等;●业务上有关及其他有益提案等;2.2对于发现安全、技术、品质管理上有重大缺陷,并提出改进方案,从而避免了不必要的损失,即使营运费用增加,亦应属于本范围。
提案范围不限于本部门内部,也可以提出其他部门持续改善提案;2.3持续改进定义的范围不包括:2.3.1发牢骚、抱怨、诋毁、攻击他人等行为;2.3.2涉及个人隐私、道德评价问题;2.3.3涉及薪资调整、人事任命问题;2.3.4公司采购降价、新开发项目改进等;2.3.5考虑排他性,不得重复提报;2.3.6属于公司规章制度下应该做但没做,现提出需要去做的提案;2.3.7因管理不到位或其他原因导致应该执行而未执行,现在又提出需要执行的提案;2.3.8只是反映状况和问题,自己无具体可行的改善内容;2.3.9以上条款最终解释权在持续改善执行委员会。
3 职责3.1全体员工都是持续改善的参与者,有权对全公司的各项工作提出建议和立项改善。