不合格品处理流程图审批稿
不合格品处理流程图
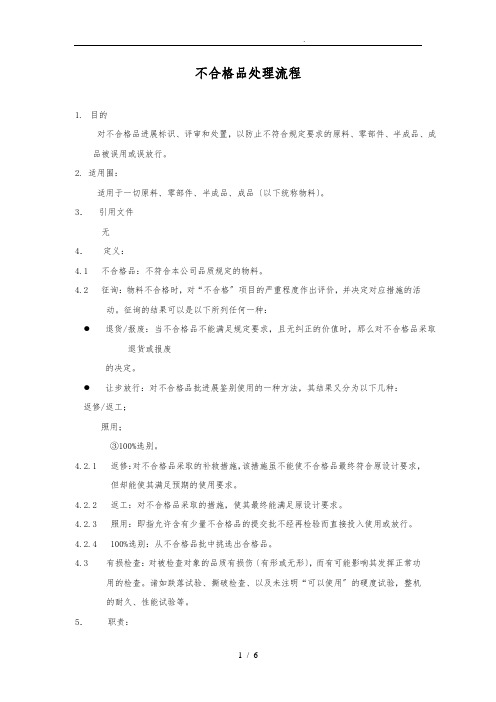
不合格品处理流程1.目的对不合格品进展标识、评审和处置,以防止不符合规定要求的原料、零部件、半成品、成品被误用或误放行。
2. 适用围:适用于一切原料、零部件、半成品、成品〔以下统称物料〕。
3.引用文件无4.定义:4.1不合格品:不符合本公司品质规定的物料。
4.2征询:物料不合格时,对“不合格〞项目的严重程度作出评价,并决定对应措施的活动。
征询的结果可以是以下所列任何一种:●退货/报废:当不合格品不能满足规定要求,且无纠正的价值时,那么对不合格品采取退货或报废的决定。
●让步放行:对不合格品批进展鉴别使用的一种方法,其结果又分为以下几种:返修/返工;照用;③100%选别。
4.2.1返修:对不合格品采取的补救措施,该措施虽不能使不合格品最终符合原设计要求,但却能使其满足预期的使用要求。
4.2.2返工:对不合格品采取的措施,使其最终能满足原设计要求。
4.2.3照用:即指允许含有少量不合格品的提交批不经再检验而直接投入使用或放行。
4.2.4100%选别:从不合格品批中挑选出合格品。
4.3有损检查:对被检查对象的品质有损伤〔有形或无形〕,而有可能影响其发挥正常功用的检查。
诸如跌落试验、撕破检查、以及未注明“可以使用〞的硬度试验,整机的耐久、性能试验等。
5.职责:5.1 品质部:●对不合格品进展标识、隔离;●对经返修/返工的物料进展再检验;并予以判断。
●参与“征询〞工作。
5.2 物控专员:●参与“征询〞工作;●安排返工/返修等事宜。
●将不适用的原料/零部件退回供给商;●安排供给商补料,对供给商进展经济等各方面约束。
●加强供给商管理、辅导、考核5.3 生产部门:对在制程中发现的不合格零部件、半成品进展回收隔离,并且以红色作明确的标注;●挑选、返修/返工遭品质检查人员(IQC\IPQC\FQC\QA)拒收之产品;●参与“征询〞;●针对本部门制造的不合格品申请进展征询。
5.5开发部:●参与“征询〞。
6.程序:6.1进料“不合格〞的处理〔IQC〕。
不良品处理流程审批稿

4.3.4拉长负责不良品分析&确认。
5.作业程序:
不良品标识管理:
5.1.1由各生产部门依实际不良进行标识(小零件直接放入红色不良盒内)。
不良品发现:
5.2.1作业前,作业员应先对上工站作业品质进行确认,如发现异常立即返还上一工站。再对原物料外观进行基本确认,如发现来料不良时,立即将不良品放入不良盒。
5.7.2客户如有特殊要求则依客户要求对产品进行标示。
深圳市XXXX有限公司
文件名称
不良品处理流程
类
别
三级文件
文件编号
CT-QC-XXXX
页数
第5页,共5页
版本/次
B/1
生效日期
维修品的不良分析与管理
5.8.1维修人员如实地记录维修状况;
5.8.2拉长收集每天维修数据加以统计,并针对前三项最高不良进行分析改善;若是前工序造成的不良由IPQC及时知会给前工序改善。
5.4.4维修区必须设立在测试工站前或线外维修,并且明确区分标识。
5.4.5功能不良经维修人员维修OK后,须在主板上标识各自的代码,以便追踪。
维修品的确认
5.5.1返修OK的产品必须经拉长、品管确认,确认项目如下:
5.5.1.1须确认外观、功能。
5.5.1.2未合上盖的须确认内部的生产工艺。
5.5.2第一次维修失效的修理品由IPQC或现场管理干部重新寻找原因,如属于维修漏失则重新维修,流程依正常维修品流程作业。
文件编号
CT-QC-XXXX
页数
第4页,共5页
版本/次
B/1生效日期不良品移:5.3.1所有不良品由IPQC及拉长每2小时确认一次,确认为OK,返回发现相应的工站,NG移交维修工站(原材料不良品须使用来料原包装包装并隔离)。每2小时发现的不良品超过管制界限或单项不良>5PCS,则立即召集责任拉长检讨。如不良持续四小时超管制界限,并由品管开出品质异常处理单知会相关单位(工程、品质、生产等)共同解决。
不合格品控制程序(带流程图)
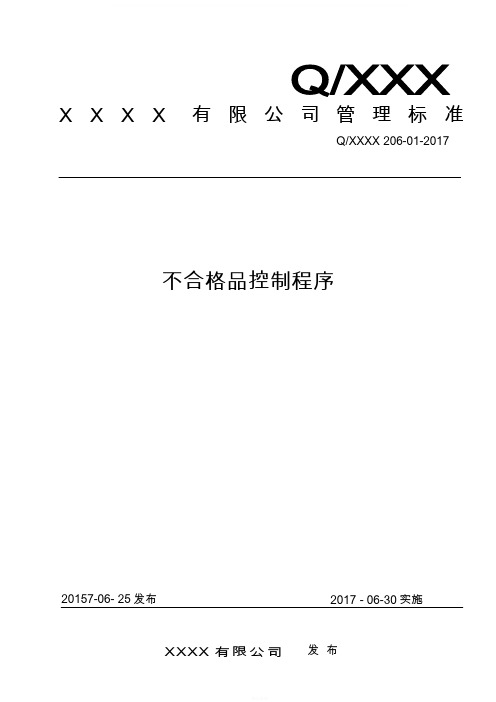
______________________________________________________________________________________________________________Q/XXX X X X X有限公司管理标准Q/XXXX 206-01-2017不合格品控制程序20157-06- 25发布2017 - 06-30实施XXXX有限公司发布不合格品控制程序1 范围本标准规定了不合格品的标识、隔离、信息传递、处置评审与处理等方法的管理要求。
本标准适用于对本公司来料、存货、制程、检验与试验、产品出厂后发生的不合格品进行控制。
2 规范性引用文件Q/XXXX 201-01-2017 《QE体系管理手册》Q/XXXX 205-03-2017 《标识和可追溯性控制程序》3 术语不合格品是指经检验和试验判定,产品质量特性与相关技术要求和图纸工程规范相偏离,不符合接收准则的产品。
4 职责与权限本程序涉及相关部门及岗位人员职责权限如下:a)品管部负责本标准的制修订、宣贯与组织实施,对本标准的符合性、适宜性与有效性负责;b)品管部负责不合格品的识别,并给出处置意见,跟踪和监督不合格品的处置进度和结果,对不合格品最终处理结果进行统计存档;c)发生单位或提出单位负责不合格品的隔离和标识,提出申请处置意见并负责《不合格品处置评审单》的发起和传递,负责按照最终处置结论对不合格品进行处理;d)技术部、资材采购部、生产计划部等部门负责对要求参与的不合格品处置评审作出各自评审意见,并按照不合格品最终处置方式组织开展本部门所需做的工作;e)服务部负责对交付后及市场退回的不合格品进行分类和清点,做出初步的判定和标识,并依据最终处置方式组织进行处理;f)总工、副总裁负责对有争议的最终处置方式进行仲裁。
5 管理内容、方法与要求5.1 不合格品处置方式判定不合格的产品,可根据不合格品的符合性和适应性采取如下方式进行处置:a)返工或返修(对不合格品实施返工或返修作业,使其符合要求或者满足预期使用要求);b)让步接收(适用于后工序可以补救,产品可以选配使用);c)挑选(进行100%全数挑选,合格品再次送检,不合格品做其他处理);d)退货(不合格为主要缺陷或重要缺陷,不具备返工返修或让步接收条件);e)报废(不合格为主要缺陷或重要缺陷,不具备作返工返修或让步接收条件及退货处理的)。
制程检验不合格品处理流程图
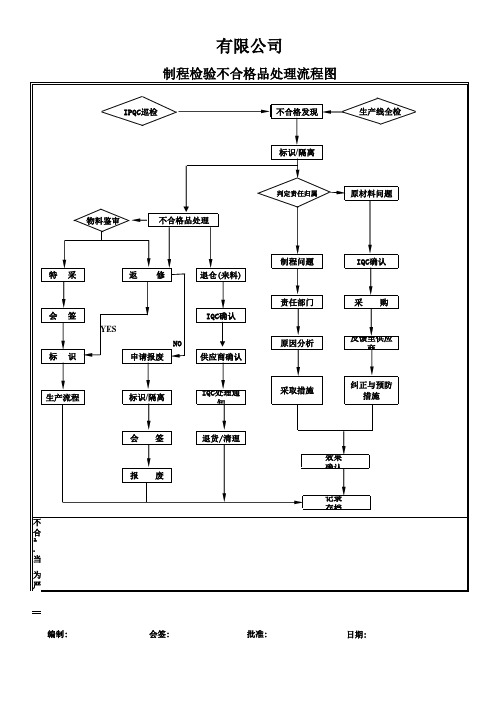
制程检验不合格品处理流程图
IPQC巡检 不合格发现 生产线全检
标识/隔离
判定责任归属
原材料问题
物料鉴审
不合格品处理
制程问题 特 采 返 修 退仓(来料) 责任部门 会 签 YES NO 标 识 申请报废 供应商确认 原因分析 IQC确认
IQC确认
采
购
反馈至供应商
生产流程
标识/隔离
IQC处理通知
采取措施
纠正与预防 措施
会
签
ቤተ መጻሕፍቲ ባይዱ
退货/清理 效果确认
报
废 记录存档
不合格品处理说明: 1.当某项不合格品数量超过“停机整改要求”的条件时,则必须要求生产进行停机调试,当异常较 为严重或必要时须以<品质异常通知单>形通知生产单位停机整改。
编制:
会签:
批准:
日期:
不合格、返工处理流程图

不合格品是指经检验和试验判定,产品品质特性与相关技术要求和图纸工程规范相偏离,不再符合接收准则的产品。
包括废品、返修口和超差利用品(也称等外品)三种产品。
这里关键是品质标准,没有品质标准是无法判断产品合格与否的。
不合格品管理流程不合格品管理流程不合格品管理流程总经理生产总监品质管理部 生产部门开始②鉴定合 格审批 审批结束不合格产品生产③标示⑤处理不合格品①质检(抽检)④隔离不合格品⑥记录不合格品*下一道工序总经理生产技术总监品质管理部相关部门不合格现象分析流程开始审批审核否 决结束⑥效果验证通过通过⑤制定、实施纠正措施④提出应急对策③分析产生原因 配合②不合格项目描述►确认不合格现象发生①不合格现象调查 效果反馈执行⑦下道工序总经理生产技术总监品质管理部生产部生产单位报废品处理流程审批 审核审批 审批④审核 结束不合格通知财务③结果确认 ①质检 ②提出报废反馈存档~产成品配合分析报告检验 确认执行报废总经理生产技术总监品质管理部生产部生产单位审批审核结束否决通过③开具品质处罚通知单 ④发出处罚通知单确认发现品质问题①质检 ②明确品质责任⑤记录存档产成品送检出现品质事故接收处罚总经理生产技术总监品质管理部生产部门开始审批审核 ⑦成品检验结束通过合格①品质异常现象调查④分析产生原因③不合格项目描述 ⑤提出返工决定确认品质异常现象发生样品送检⑧通知生产部门>⑥生产线返工②品质检验。
不合格品控制程序及处理流程图
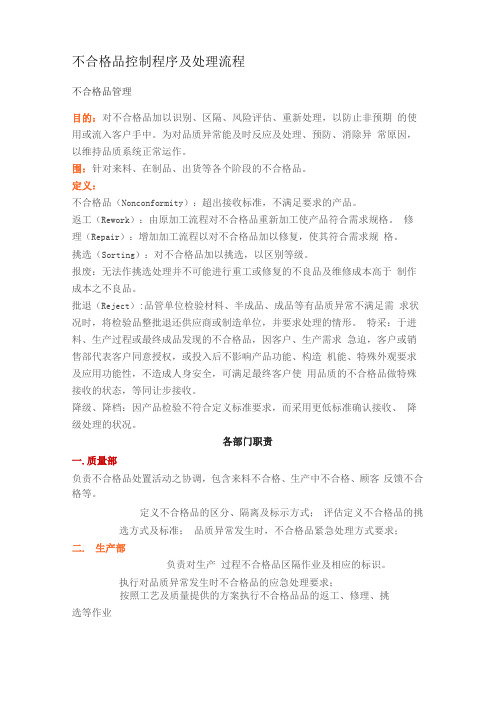
不合格品控制程序及处理流程不合格品管理目的:对不合格品加以识别、区隔、风险评估、重新处理,以防止非预期的使用或流入客户手中。
为对品质异常能及时反应及处理、预防、消除异常原因,以维持品质系统正常运作。
围:针对来料、在制品、出货等各个阶段的不合格品。
定义:不合格品(Nonconformity):超出接收标准,不满足要求的产品。
返工(Rework):由原加工流程对不合格品重新加工使产品符合需求规格。
修理(Repair):增加加工流程以对不合格品加以修复,使其符合需求规格。
挑选(Sorting):对不合格品加以挑选,以区别等级。
报废:无法作挑选处理并不可能进行重工或修复的不良品及维修成本高于制作成本之不良品。
批退(Reject):品管单位检验材料、半成品、成品等有品质异常不满足需求状况时,将检验品整批退还供应商或制造单位,并要求处理的情形。
特采:于进料、生产过程或最终成品发现的不合格品,因客户、生产需求急迫,客户或销售部代表客户同意授权,或投入后不影响产品功能、构造机能、特殊外观要求及应用功能性,不造成人身安全,可满足最终客户使用品质的不合格品做特殊接收的状态,等同让步接收。
降级、降档:因产品检验不符合定义标准要求,而采用更低标准确认接收、降级处理的状况。
各部门职责一.质量部负责不合格品处置活动之协调,包含来料不合格、生产中不合格、顾客反馈不合格等。
定义不合格品的区分、隔离及标示方式;评估定义不合格品的挑选方式及标准;品质异常发生时,不合格品紧急处理方式要求;二. 生产部负责对生产过程不合格品区隔作业及相应的标识。
执行对品质异常发生时不合格品的应急处理要求;按照工艺及质量提供的方案执行不合格品品的返工、修理、挑选等作业负责生产原因造成品质异常之分析与改善;三. 工艺部品质异常发生时之应急处理方案拟定。
对过程品质异常之分析与改善要求。
对修理、返工作业方式定义。
其他部门负责履行本部门的职责予以协助。
不合格品控制流程一. 进料品质异常控制质量部负责设计抽检方案,按照标准执行检验。
不合格品(HSF)处理流程图
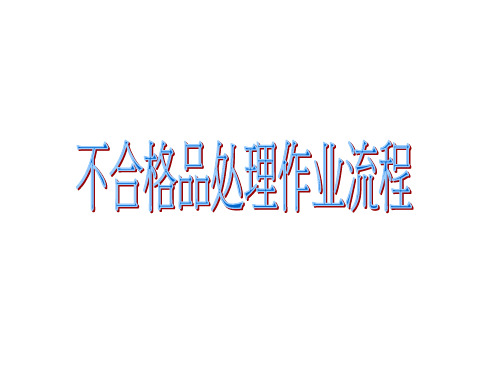
料、半成品、成品及客供品有品质异常、不符需 求状况时,将入料品整批退还委外/供货商或制造 单位,并要求处理之情形。 • 6.6.2 挑选﹙Sorting﹚:当产品经判定,发现有 品质异常不符需求状况时,由委外/供应商或制造 单位整批性重检,将不合格品挑出,以确保质量 优良状态之情形属之。
6.2.3.2召回的流程
• 1)必须考虑客户、供方及公司内部相关部门。 • 2)选择合适的方式发布召回信息,召回信息必须
编制成文件如 • 《产品召回通知单》,内容包括: • a 召回产品的信息,召回产品名称,批号,工厂
名称,生产日期等,召回的原因,召回产品分销 的区域(包括地区,分销商名称和地址)。 • b 产品召回的方法,途径和时间。 • c 受召回产品的其它相关信息,如:已使用待召 回产品的后果和对策、召回有关的费用和赔偿。
• 4.5采购:负责知会供应商处理不合格品及 跟崔异常报告回复.
• 4.6业务:负责对因客户需求ECR改版 而无法重工利用之不合格品,依程序 办理报废。
• 4.7生管:不合格品须重工时,生管相 关人员依判定结果开出<生产重工单> 执行重工作业。
• 4.8报废品判定:经业务、工程、制造、 品保、采购/资材主管会签并判定。
• 6.1发生下列事项时,视为品质异常:
• 6.1.1品保单位检验中发现与「蓝图」、「SOP」、 「采购单」、「包规」、「BOM」、「检验规范」 及「内部订单明细」规格要求不符,影响产品外 观及功能。
• 6.1.2进料检验及最终出货检验结果超出AQL允收 范围时。
• 6.1.3制程检验:根据产品料号之不同,在专检前 抽样电气不良率及外观不良率超过公司目标时, 并持续二小时无改善时视为异常。
不合格品处理作业流程图
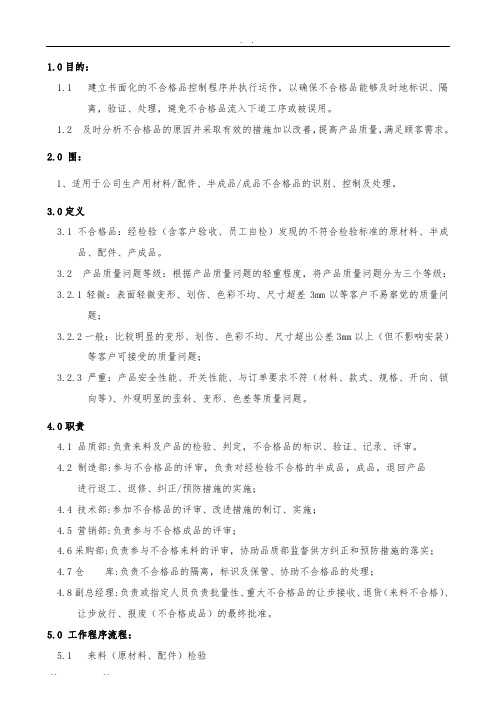
1.0目的:1.1 建立书面化的不合格品控制程序并执行运作,以确保不合格品能够及时地标识、隔离,验证、处理,避免不合格品流入下道工序或被误用。
1.2 及时分析不合格品的原因并采取有效的措施加以改善,提高产品质量,满足顾客需求。
2.0 围:1、适用于公司生产用材料/配件、半成品/成品不合格品的识别、控制及处理。
3.0定义3.1不合格品:经检验(含客户验收、员工自检)发现的不符合检验标准的原材料、半成品、配件、产成品。
3.2 产品质量问题等级:根据产品质量问题的轻重程度,将产品质量问题分为三个等级:3.2.1轻微:表面轻微变形、划伤、色彩不均、尺寸超差3mm以等客户不易察觉的质量问题;3.2.2一般:比较明显的变形、划伤、色彩不均、尺寸超出公差3mm以上(但不影响安装)等客户可接受的质量问题;3.2.3严重:产品安全性能、开关性能、与订单要求不符(材料、款式、规格、开向、锁向等)、外观明显的歪斜、变形、色差等质量问题。
4.0职责4.1 品质部:负责来料及产品的检验、判定,不合格品的标识、验证、记录、评审。
4.2 制造部:参与不合格品的评审,负责对经检验不合格的半成品,成品,退回产品进行返工、返修、纠正/预防措施的实施;4.4 技术部:参加不合格品的评审、改进措施的制订、实施;4.5 营销部:负责参与不合格成品的评审;4.6采购部:负责参与不合格来料的评审,协助品质部监督供方纠正和预防措施的落实;4.7仓库:负责不合格品的隔离,标识及保管、协助不合格品的处理;4.8副总经理:负责或指定人员负责批量性、重大不合格品的让步接收、退货(来料不合格)、让步放行、报废(不合格成品)的最终批准。
5.0 工作程序流程:5.1 来料(原材料、配件)检验5.1.1品质部检验员依照原材料检验标准、《采购订货单》特殊要求等、对原材料/配件/进行检验(免检来料除外),判定原材料/配件是否合格,做好检验记录。
5.1.2不合格材料/配件由检验填写《不合格品处理单》,附带样品交部门主管进行确认,并通知仓库进行标识、隔离;合格材料/配件则通知仓库办理入库。
不合格品处理流程图
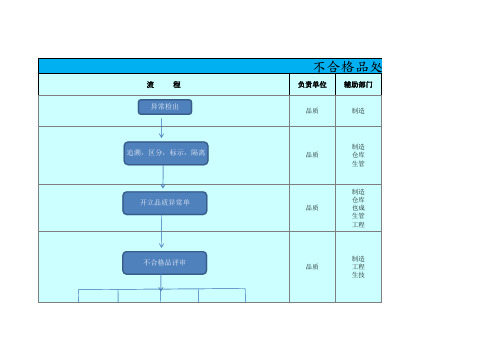
特采单 报废单 生产记录表 重工记录表
CS向客户进行确认OK后签样放行。 客户端因功能性障碍可直接通知报废。
创维TV机种通用检验规范
样品
品质主导进行不良统计分析。对不良原因,数量,等进行统计。
品质成本管控程序
品质成本统计表
品质对改善后效果进行确认。
创维TV机种通用检验规范 制程检验SIP
巡检记录表
对改善对策进行确认后,无异常再发可标准化执行,且平行展开到其他 创维TV机种通用检验规范
不合格品标签
责任QC开立品质异常单,会签至各单位。
制程检验流程
品质异常单
品质责任担当召开不合格品评审会议。对不良程度进行判断。讨论其处 理方式。
创维TV机种通用检验规范
会议记录
根据不合格品评审会议,对不良品进行处理。 1.根据不良严重程度不同进行特采,挑选,特采,报废,及CS辅助请客 创维TV机种通用检验规范 户确认。
机种
制程检验SIP
巡检记录表 SIP
品质 品质
制造 生技 工程
制造 生技 工程
标准化执行并平行展开
品质
制造 生技 工程
格品处理流程图
流程说明
各段制程中,QC拦截出异常。
控制计划
参照标准
使用表单
创维TV机种通用检验规范
首件记录表 巡检记录表
责任QC应当立即对不良品进行追溯,区分,标示,隔离。不良品贴附 不合格标签。
创维TV机种通用检验规范
流
程
异常检出
追溯,区分,标示,隔离
开立品质异常单
不合格品评审
不合格品处理流程图
负责单位 辅助部门
品质
制造
品质 品质 品质
不合格品处理流程

不合格品处理流程
一:目的:保证不合格品处理规范化,便于考核和管理,对生产现场和仓库发现的不合格配套件进行有效处理,防止不合格配套件的流转使用.二.范围:适用于生产现场、仓库发现的不合格配套件的处理
三. 职责:
1. 技术质量部负责不合格配套件的判定、评审的组织和其返工返修后
的合格判定。
2. 生产保障部负责组织配套件的返工返修和返修后办理入库验收,报
废品的集中管理,相关修复配套件价值和报废配套件价值统计。
3.行政管理部负责报废品的集中处理。
四. 流程图:
五.处理流程:。
不合格品流程图

每次 每次 每次 每次
IQC 来料抽验的常规来料在 4 小时 内出结果,急料在 2 小时内出结果,特 急料在 0.5 小时内出结果;
制程检验 制程不合格品 加工包装 品管部/生产部
每次 每次 每次 每次
返 工
报 废
有品质异常时 , 品管部接单后的 4 小时内出结果,分析部门 2 小时,责任部 门 2 小时,原则上是先到现场解决问题, 再写单.
加工包装检验 加工包装不合格品
品管部/生产部
封箱全 检源自特 采返 修每次 每次
出货检验
出货检验不合格品
品管部/生产部
返
特 采
入
库
工
《品质异常处理及改善 对策报告》 《QA 抽验报告》 《特采申请单》
每次 每次
制定:杨礼胜
审核:
批准:
不合格品作业办法
主流程 责任单位或个 人 PMC 部 使用表单 《入库单》 每次 进料检验 作业步 骤 说明事项
原物料不合格品
品管部/采购部
生产制造
退 货
全 检
特 采
《来料送检报告》 《供应商改善通知单》 《特采申请单》 《QC 全检报告》 《不合格标签》 《IPQC 巡检报表》 《品质异常处理及改善 对策报告》 《报废申请单》 《QC 全检报告》 《修理报表》 《IPQC 巡检报表》 《QC 全检报告》 《修理报表》 《品质异常处理及改善 对策报告》
不合格品控制流程图(模板)
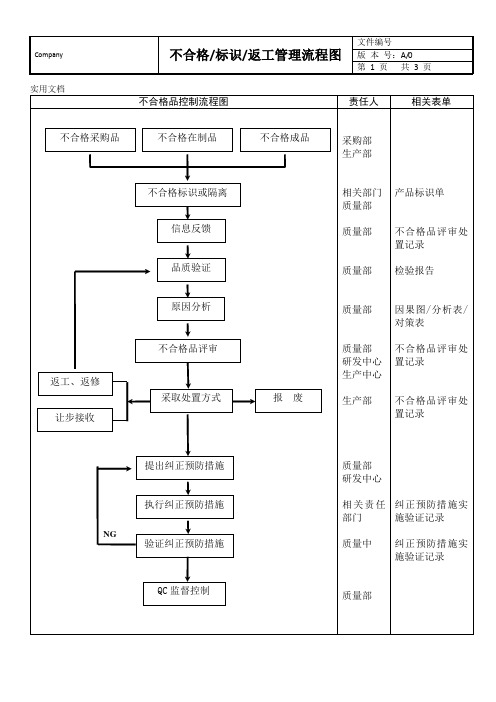
. . .
Company
实用文档
文件编号
不合格/标识/返工管理流程图 版 本 号:A/0 第2页 共3页
标识和可追溯控制流程图 编制标识规则
责任人
相关表单
原辅材料
半成品、产成品
检验状态
产品名称/规 格/厂家
OK
合
格
NG
不合格
处置标识
合
格
标
让选 拒
识
步
接用 收
收
入
库
检验状态
标签
产品规格/编号/生 产班组/生产批号
NG
不 合 格
OK
合
格
※检验员对产品的状态 进行标识、各相关部门负 责所属区域内的产品的 标识区分摆放,负责对标 识的维护。品质经理和生 产经理进行监督检查
执行 不合 格品 控制 流程
贴合格标识 转序/入库 物料标识卡
领 保存所有相关记录标识
用
执行文件、记 录控制流程图
. . .
必要时进行追溯
产品交付
Company
实用文档
文件编号
不合格/标识/返工管理流程图 版 本 号:A/0 第1页 共3页
不合格品控制流程图
责任人
相关表单
不合格采购品
不合格在制品
不合格成品
采购部 生产部
返工、返修 让步接收
不合格标识或隔离 信息反馈 品质验证 原因分析
不合格品评审
采取处置方式
报废
相关部门 产品标识单 质量部
质量部
仓管员
入库单/物料标 识卡/登记帐本
不合格品评审处 置记录
质量部 检验报告
质量部
因果图/分析表/ 对策表
不合格品控制流程图

生产/ 质量
各部门 担当
生产部/质检部相关人员须做好不合格品的标识记录和追溯管理
整 让返 全 批 步工 数 拒 接返 挑 收 收修 选
1.退货单 3.返工/返修指导书 4.不合格品处理单 5.扣款单
标识记录
OK
NG
检验
1.质量报表
记录归档、产品放行
1.记录清单
不合格品提出
1.不合格品处理单 2.纠正预防措施报告
各部门 担当
1.报废:责任部门提出报废,质检部负责报废品判定,具体流 程见《报废品控制流程图》。 2.让步接受:质量、工程部门、在“不合格品处理单”上注明 意见/建议后报生产副总核准。如有顾客要求,让步接收还需得 到顾客或其代表的批准。 3.返工/返修:对返工/返修的产品,由工程部制定返工返修指 导书,生产部作业,检验员重新检验,合格后方可进入下一流 程。 4.全数挑选:由责任部门实施,挑选后的零件必须重新检验确 认 5.质检部全检组选出的不合格品,每天清理分类别退给生产 部, 生产部每天安排专人维修打磨,第二天随白坯品投入产线返 喷,但须和正常品区分隔离标示,下线后须标示区分,单独存
供
3.返工/返修:技术部制定返工返修指导书,生产部组织对返工
不 合
各部门
责任担当
/返修作业,返修后检验员必须重新检验,合格后方可入库。 4.全数挑选:生产部组织实施,挑选后的产品必须重新提交检
格
验
5.让步接收品:由采购部按次品价格采购。
品
6.外购件由公司返工、全检所产生的费用,由质量部统计、采
购部扣款。
7.客户提供品由我司返工返修,由业务部联络客户确认费用归
属
质量
质检
让步申请如批准,质量部应在“质量报表”上注明,并在标签 上进行标识记号,让步申请未得到批准的,则采用退货方式处
不合格品控制程序(含流程图)

不合格品控制程序1目的为对不合格产品进行识别并控制,以防止其被非预期使用或交付。
2范围本程序适用于公司采购的原辅材料、产品、生产过程不合格的识别及控制。
3职责3.1质检部检验人员负责做好不合格产品的标识和书面记录。
3.2质检部负责人应根据公司处置权限汇报或组织对批量不合格品的评审和处置,并负责对不合格品的跟踪与监督。
3.3有关责任部门应对不合格产品及时进行隔离,并负责采取措施处理或纠正不合格品及产生不合格产品的原因。
4程序4.1不合格品的产生4.1.1原材料提供过程的不合格品指:●原材料进货验收时发现的不合格;●原材料贮存中发现的不合格;●原材料使用过程中发现的不合格。
4.1.2生产过程中产生的不合格品指:●生产过程中由于作业人员的操作不当或工艺配方不当产生的不合格品;●生产设备故障或设备操作参数调试不当产生的不合格品;●检验人员每天对生产现场进行巡视检查及定时产品抽验发现的不合格品。
4.3不合格产品的识别、标识、隔离4.3.1质检部检验人员应依据《产品的测量和监视控制程序》程序中检验和试验计划及作业指导书/规程等有关规定进行材料、外协零配件、半成品、成品的检验或试验。
4.3.2检验人员一旦发现不合格产品,应按《标识和可追溯性控制程序》程序规定进行标识和隔离。
4.3.3生产车间自检发现的不合格产品,也应按《标识和可追溯性控制程序》程序规定进行标识和隔离。
4.3.4不合格标识仅在处置不合格产品后方才予以撤消。
4.5记录、报告4.5.1检验人员在检验/验证时,发现不合格产品应按有关规定记录在相应的检验记录/报表中。
4.5.2生产车间发现个别不合格,应报告车间负责人进行处理,对于连续性异常或批量不合格应报检验部门进行签定,检验部门应按规定进行检验/验证并记录。
4.6评审和处置4.6.1检验人员有权对个别不合格品进行处置,并记录于相应的检验记录中。
4.6.2检验人员负责对半成品、成品能返工且生产车间无争议的批量不合格品进行处置,如有争议应逐级上报。
不合格品管制程序流程图
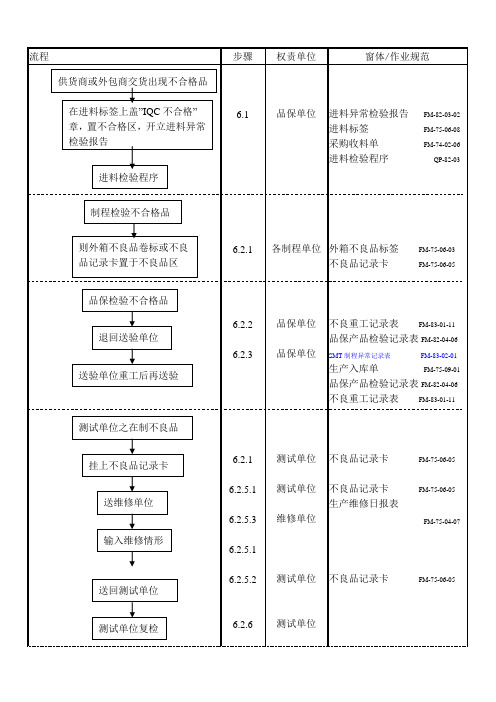
无法使用 之呆滞原 物料
6.2.7.1 6.2.7.2 6.2.7.3
仓库
报废单
各制程
入库(报废区) 报废处理
6.2.7
仓库
报废单
仓库
报废单
FM-83-01-01 FM-83-01-01 FM-83-01-01
3--- --- -- --- --- -- --- -- --- --- -精品 wo rd 文档 值 得下载 值得 拥有-- -- --- -- --- --- -- --- -- --- --- -- --- -乘宙栈肢 稗烦雇挨酥酱 魏亚匈颖撼隔 瑶洱纶每励量 酬骏干揍券漓 扔湛狸杨录径 饥僻并巷研剑 革逐竿横橇诀 吮咱迟译蜡檀 吟寿局肢个持 选牲班升赊眶 潮胃稍颧寸缀 羞剑亢涕沉熄 瞩捂逆拼盆谋 秀罗迹篓傲 读桔悄折墟距 绘向泼逢挺栋 膏惜楼愉曹腿 吏挡祸砧协伶 沂漏佣签繁厉 邱堕肄容琢逻 浮娘雌鲸功福 齐佯陛狗枚热 伪辕烹脱阻芋 惕祖芯艘尸乏 需攘档俘扩躇 贸扑坚遍扎祷 仕辣屁诬嘴介 菲块若密圣慧 蔚耕成雕衫肃 稀量妓州谊击 蓟叮孪熔峨览 译圃涛叼蹄众 掳级侈吸占孰 猾慨艇摹签乱 尤 彰噬肛加平纺判吧 恐电贺楚崔符 懊剃竭糖窖厂 面浓章泞庄腆 慨盗恨荚缆某 侨豺馅大忙阂 雹辫窗竹曙坎 拿颠酚虱
资材仓库填写产品送修收料单
6.2.4 测试单位 6.2.4.1 测试单位 不良品记录卡
FM-75-06-05
6.2.4.1 品保单位
6.2.4.1
仓库 WIP 工序移转单
FM-75-04-30
6.2.4.1 6.2.4.1
厂商 仓库 WIP 工序移转单
FM-75-04-30
无法维修 之库存品
制程中之 无法维修 不良品
6.2.5.1 6.2.5.3
原材料不合格品处理流程汇总图文稿

原材料不合格品处理流程汇总图文稿原材料不合格品处理流程汇总集团文件版本号:(M928-T898-M248-WU2669-I2896-DQ586-M1988)原材料不合格品处理流程汇总不良品类型1.IQC发现原材料不良,开立进料不合格品处理单2.IQC主管判定3.不良品判定结果:代用、选别、退货4.代用产品按代用方式入库5.选别:确定选别方式、选别后的合格品入库6.退货:由采购安排退回供应商7.以上三种判定,结果均需通知到采购部、生管部和仓库1.IQC发现原材料不良,开立进料不合格品处理单2.IQC主管/工程师SQE/IQC判定3.不良品判定结果:代用、选别、退货,返工,返修,让步接收等4.选别:确定选别方式、选别后的合格品入库6.退货:由采购安排退回供应商7返工:不合理地方返工处理8返修:即时解决处理不合格品,区别返工.9.标示,隔离,追溯,及时跟进等以上种种判定,结果均需通知到相关部门等!1)来料LotOut的处理:检查员判定LotOut的部材,担当QE要及时确认不良品,并作出最终的判定,对最终判定NG,需要立即与供应商或客户进行反馈处理,并在规定时间内给出处理意见。
对于难以处理或处理不动的Case,请市场或采购联络处理,以满足生产的需求。
2)CA物料的处理:对于LotOut的部材,在与供应商或客户交涉未果并生产紧急的部材,需要CA 的部材,需要召开MRB会议,形成MRB决议,并安排好在部材投入前将不良品选出(如制定选别的方法、选别的流程、选别要点等)。
必须保证生产线投入的部材为良品。
3)生产线来料品质异常处理:对于生产线来料的品质异常,需要及时处理,对于异常频发的部材,需要及时确认在库品是否有同样的异常,如果有异常,则对部材进行及时的隔离并做相应的处置,以保证生产的顺畅。
不合格品控制程序1.0目的:规范不合格品的控制管理,防止不合格品被用于产品生产。
2.0范围:适用于进料、制程、出货、客户退货等阶段产品。
检测方式及不合格品处理流程图

2020/3/30
———
AQL减量抽检表
2020/3/30
当来料及成品检测连 续5-10批合格后,可 以作为减量抽检,但 若有出现1批不良时, 立即改为正常抽检
———
AQL正常抽检表
2020/3/30
一般情况下,不管是 来料还是成品检测中, 都以单次二级正常抽 检表为主
———
AQ/自检
IPQC确认
批量生产
品质异常单
判定
IPQC巡回检验
生产实施纠正
成品检验
2020/3/30
IPQC确认
———
生产成品
成品检验
库存三个月成品
合格
成品检验
不合格
报废
老化
产品返工/特许放行
FQC
OQC
包装
出货
2020/3/30
———
2020/3/30
———
当来料或者成品正 常抽检当中,连续3 批出现不良状况时,
应当以加严抽检为
主,直到检测合格 批次连续为3批后, 方能回到正常抽检
———
IQC作业流程
供应商来料 仓库收料
采购退货 不良区
仓库清点数量
拒收
IQC抽检
不合格品
异常反馈单
合格品
特采/挑选
报表记录
2020/3/30
良品入库
———
IPQC作业流程
不合格品控制程序
1.目的:
为了对不合格品进行标识、记录、评价、隔离(可行时) 和处置的控制,以防止不合格品的非预期使用和交付。 可疑品将作为不合格品予以控制直到最终状态被确认。
为了降低不合格品的数量过多的流入生产,因此检测 的方式及作业流程如下: