原油常减压装置节能技术
炼油厂常减压装置节能新技术措施分析
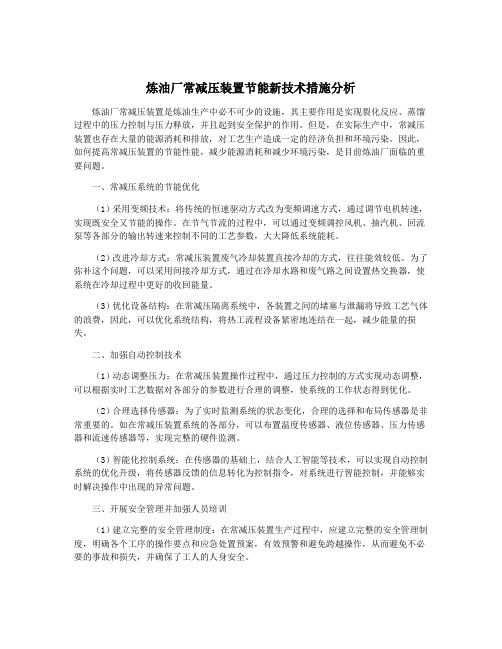
炼油厂常减压装置节能新技术措施分析炼油厂常减压装置是炼油生产中必不可少的设施,其主要作用是实现裂化反应、蒸馏过程中的压力控制与压力释放,并且起到安全保护的作用。
但是,在实际生产中,常减压装置也存在大量的能源消耗和排放,对工艺生产造成一定的经济负担和环境污染。
因此,如何提高常减压装置的节能性能,减少能源消耗和减少环境污染,是目前炼油厂面临的重要问题。
一、常减压系统的节能优化(1)采用变频技术:将传统的恒速驱动方式改为变频调速方式,通过调节电机转速,实现既安全又节能的操作。
在节气节流的过程中,可以通过变频调控风机、抽汽机、回流泵等各部分的输出转速来控制不同的工艺参数,大大降低系统能耗。
(2)改进冷却方式:常减压装置废气冷却装置直接冷却的方式,往往能效较低。
为了弥补这个问题,可以采用间接冷却方式,通过在冷却水路和废气路之间设置热交换器,使系统在冷却过程中更好的收回能量。
(3)优化设备结构:在常减压隔离系统中,各装置之间的堵塞与泄漏将导致工艺气体的浪费,因此,可以优化系统结构,将热工流程设备紧密地连结在一起,减少能量的损失。
二、加强自动控制技术(1)动态调整压力:在常减压装置操作过程中,通过压力控制的方式实现动态调整,可以根据实时工艺数据对各部分的参数进行合理的调整,使系统的工作状态得到优化。
(2)合理选择传感器:为了实时监测系统的状态变化,合理的选择和布局传感器是非常重要的。
如在常减压装置系统的各部分,可以布置温度传感器、液位传感器、压力传感器和流速传感器等,实现完整的硬件监测。
(3)智能化控制系统:在传感器的基础上,结合人工智能等技术,可以实现自动控制系统的优化升级,将传感器反馈的信息转化为控制指令,对系统进行智能控制,并能够实时解决操作中出现的异常问题。
三、开展安全管理并加强人员培训(1)建立完整的安全管理制度:在常减压装置生产过程中,应建立完整的安全管理制度,明确各个工序的操作要点和应急处置预案,有效预警和避免跨越操作,从而避免不必要的事故和损失,并确保了工人的人身安全。
石油炼制中常减压装置的节能分析

石油炼制中常减压装置的节能分析石油炼制是现代工业生产中不可或缺的重要环节,而在石油炼制过程中,常减压装置是一个至关重要的设备,其作用是将高温高压的加氢裂化反应产生的粗油进行脱汽、分馏和分解。
在炼油厂中,常减压装置占据着重要地位,因此其能否节能,直接影响到整个生产过程的经济效益。
在本文中,将对石油炼制中常减压装置的节能情况进行分析,并提出相应的节能措施。
需要明确的是,常减压装置在炼油厂中的主要作用是将高温高压的加氢裂化反应产生的粗油进行分解、分馏和脱汽。
在这个过程中,大量的热能被消耗,因此如何减少能源的消耗,提高能源利用率,是常减压装置节能的重要方面。
在炼油厂中,常减压装置的节能主要体现在以下几个方面:1.优化设计:常减压装置的设计应符合能源利用效率高、操作适用性强、维护方便等要求。
采用先进的设计理念和技术,合理配置设备,减少能源的浪费,提高设备的工作效率。
2.设备更新:随着科技的不断发展,常减压装置的设备也在不断更新换代。
新型设备在节能方面有较大的优势,因此及时更新设备,是提高节能效果的重要手段。
3.优化操作:在日常生产中,通过优化操作流程和技术手段,减少能源的浪费,提高设备的利用效率。
4.能源回收:在常减压装置的运行过程中,可以采用能源回收技术,将废热、废气等能源进行有效回收利用,减少能源的浪费。
上述四点是炼油厂中常减压装置节能的主要方面,下面将对这些方面进行详细分析。
常减压装置的节能问题是十分重要的,不仅关系到炼油厂的经济效益,也关系到环境保护和可持续发展。
在实际生产中,应采取各种措施,提高常减压装置的节能水平,为企业的可持续发展做出贡献。
希望通过本文的分析,能够引起相关行业的重视,推动常减压装置的节能工作取得更好的效果。
石油炼制中常减压装置的节能分析

石油炼制中常减压装置的节能分析石油炼制过程中的常减压装置是一种非常重要的设备,它通过将高温高压的原料油降压至合适的温度和压力,从而为下一步的炼制工序提供了合适的条件。
在炼油工业中,常减压装置占据着非常重要的地位,因此如何提高其能效和节能减排成为了当前炼制企业亟待解决的问题之一。
本文将就石油炼制中常减压装置的节能性能进行分析与探讨。
常减压装置通过将高压、高温气体减压至低温低压气体,达到冷凝和液化的目的。
它的节能性能主要体现在以下几个方面:1. 器件优化:常减压装置中的调压阀、换热器、压缩机等器件的设计和选择对于节能至关重要。
通过优化设计和选型,可以减少能量损失,提高能效。
2. 热能回收:在减压过程中,往往伴随着大量的热能损失。
通过热交换器的设计和应用,可以实现热能的回收和再利用,提高能源利用率。
3. 过程优化:合理的工艺设计和运行控制对于节能也起着至关重要的作用。
通过减少不必要的能量消耗,优化过程流程,实现能源的最大化利用。
4. 新技术应用:随着科技的不断发展,新材料、新工艺、新技术不断涌现,如使用高效节能的换热器、节能调压阀等,也为常减压装置的节能提供了新的途径。
在实际的炼制过程中,石油企业可以通过对常减压装置的技术改造和优化来实现节能减排的目标,并且能够获得可观的经济效益。
加强对常减压装置人员的培训和技术支持,也是提高其节能性能的重要手段。
传统的常减压装置在工作过程中存在许多不足之处,主要表现在以下几个方面:1. 能耗较高:传统的常减压装置由于设计和工艺的限制,能耗较高,能效较低。
3. 设备老化:由于长期运行,设备容易老化,导致性能下降,能效降低。
为了解决传统常减压装置存在的问题,提高其能效和节能性能,炼制企业可以采取以下措施:1. 技术改造:对现有的常减压装置进行技术改造,采用新材料、新工艺和新技术,提高其能效和节能性能。
2. 设备更新:更新老化设备,选择高效节能的调压阀、换热器等器件,提高能源利用率。
炼油厂常减压装置节能新技术措施分析

炼油厂常减压装置节能新技术措施分析炼油厂是石油加工行业的重要组成部分,常减压装置是炼油厂中的核心设备之一。
随着能源消耗和环保问题日益受到关注,炼油厂常减压装置的节能技术也变得尤为重要。
本文将就炼油厂常减压装置节能新技术措施进行详细的分析,以期为炼油厂的节能降耗工作提供参考和借鉴。
一、炼油厂常减压装置的节能问题炼油厂中的常减压装置是用于将高压气体减压至低压,并分离出液体成分的装置。
在这一过程中,常减压装置需要消耗大量的能源,尤其是在高压气体减压的过程中,会产生大量的余热。
如何有效利用这些余热,提高能源利用率,成为了炼油厂常减压装置需要解决的节能问题。
二、常减压装置节能新技术措施1. 余热回收技术在常减压装置的使用过程中,会产生大量的余热,传统做法是将这些余热散发到环境中。
而通过余热回收技术,可以将这些余热有效地回收利用,用于加热水或者预热原料等环节,从而减少能源消耗。
现在市场上已经出现了许多余热回收设备,如热交换器、蒸汽再生装置等,可以帮助炼油厂进行余热回收,提高能源利用效率。
2. 热风循环技术炼油厂常减压装置的加热过程需要大量的热风,传统做法是直接排放到大气中,造成能源的浪费。
而采用热风循环技术,可以将已经加热过的热风再利用,从而减少能源消耗。
这种技术需要依靠一定的回收设备和系统,可以有效地提高能源利用率,减少能源消耗。
3. 高效节能设备高效节能设备的使用是节能技术的重要组成部分。
采用高效的温度控制装置、节能换热器等设备,可以在不影响设备正常运行的前提下,减少能源消耗。
目前,市场上已经有很多高效节能设备可供选择,炼油厂可以根据自身的情况选择合适的设备,提高设备的能源利用效率。
4. 远程监控和智能化控制技术通过远程监控和智能化控制技术,可以对炼油厂的常减压装置进行实时监测和控制,从而提高设备的运行效率,降低能源消耗。
智能化控制技术可以通过精准的控制和调节,降低设备运行的能源消耗。
远程监控技术可以让工作人员对设备的运行情况进行实时监测,及时发现问题并加以处理,提高设备的稳定运行和节能效果。
石油炼制中常减压装置的节能分析

石油炼制中常减压装置的节能分析石油炼制中的常减压装置是一个关键设备,用于从原油中分离各种分馏产品。
节能是当前石油炼制工业中面临的重要问题之一,因此对常减压装置的节能分析非常重要。
常减压装置中的节能措施主要包括以下几个方面:1. 热能回收利用:在常减压装置中,原油经过加热后进入分离器,随后蒸汽由底部进入加热炉,将残留油再生产出来。
这其中涉及到大量的热量传递,因此可以通过热能回收利用来降低能耗。
采用热交换器,将废热回收,用于加热原油或其他需要加热的物料,从而减少燃料消耗。
2. 废热利用:常减压装置中会产生大量的废热,如分馏塔排气中的热量。
这些废热可以通过余热锅炉回收利用,产生蒸汽或热水,用于其他工序或生活用热,减少能源的浪费。
3. 优化操作:通过对常减压装置的优化操作,如控制进料温度和压力,控制塔床温度和压力,合理调整再沸点,可以减少能源的消耗。
4. 更换高效设备:选择更加高效的设备和工艺,例如使用能耗低的压缩机、泵等设备,以及采用节能工艺,如采用低温分馏、能量集成等技术,可以降低常减压装置的能耗。
对常减压装置的节能分析可以从能源消耗和能耗结构两个方面进行。
能源消耗方面,常减压装置主要耗能在于加热原油、蒸汽供应和泵送过程。
通过合理的能源消耗模型,可以对不同的工艺参数进行模拟分析,比如不同的进料温度、压力、泵送速率等对能源消耗的影响。
通过模拟计算,可以找出能耗高的环节,并对其进行优化。
能耗结构方面,常减压装置的能耗结构主要分为机械能和热能。
机械能主要耗在泵送和压力控制过程中,热能主要耗在加热和冷却过程中。
通过能耗分析,可以评估不同能源的比例和利用效率,找出能源利用不合理的地方,并提出相应的优化建议。
常减压装置的节能分析是石油炼制工业中的重要内容,可以通过热能回收利用、废热利用、优化操作和更换高效设备等措施来降低能耗。
对常减压装置进行能源消耗和能耗结构的分析,可以找出能耗高和能源利用不合理的环节,并提出相应的优化措施。
炼油厂常减压装置节能新技术措施分析

炼油厂常减压装置节能新技术措施分析石油炼制工艺中,常减压装置是一个非常重要的环节。
它主要用于将原油中的各种烃类分离出来,通过降低管道中的压力来使原油蒸发,从而实现烃类的分离。
在常减压装置的运行中,能源消耗是一个非常重要的问题,因此寻找并应用节能的新技术措施非常有必要。
一、热能回收利用技术炼油过程中,常减压装置中产生了大量的废热。
传统上,这些废热会直接排放到大气中。
为了更好地节能减排,可以采用热能回收利用技术,将这些废热进行回收利用。
具体的方法有两种:1.余热回收:常减压装置中产生的废热可以用于加热其他生产环节所需的介质。
可以将废热用于加热炼油厂内的其他装置,或者用于加热其他生产过程中需要的水,从而达到节能的目的。
2.发电回收:常减压装置中的废热可以用于发电。
通过将废热转化为蒸汽,再通过蒸汽发电机转化为电能,从而实现能量的回收利用。
二、节能控制技术常减压装置的节能措施还可以从控制方面入手。
通过合理的控制装置的运行,可以达到节能减排的目的。
具体措施如下:1.优化操作参数:通过对装置的操作参数进行优化调整,可以减少能耗,提高经济效益。
控制蒸汽的流量和压力,控制再沸器的进出口温度等。
2.自动化控制:引入自动化控制系统,实现对常减压装置的自动化控制和监测,可以降低人工干预的程度,减少能源的浪费。
三、改进设备结构和设计常减压装置的结构和设计也可以进行改进,从而达到节能的目的。
具体改进措施如下:1.改进节流装置:优化节流装置的结构参数和材料选择,减小阻力,降低能耗。
2.改善换热器传热效果:通过改进换热器的结构和设计,提高传热效率,降低能量损耗。
3.优化常减压装置的结构:通过优化常减压装置的结构,减小内部压力损失,降低能源的消耗。
炼油厂常减压装置的节能新技术主要包括热能回收利用技术、节能控制技术和改进设备结构和设计。
通过应用这些新技术措施,可以有效地降低能源消耗,提高能源利用效率,达到节能减排的目的。
石油炼制中常减压装置的节能分析
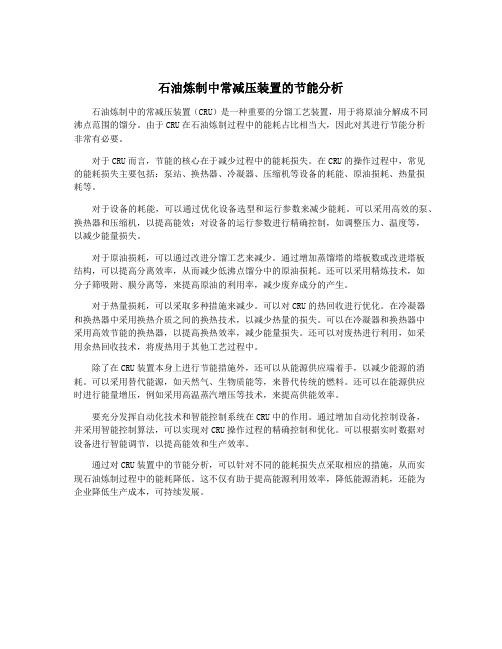
石油炼制中常减压装置的节能分析石油炼制中的常减压装置(CRU)是一种重要的分馏工艺装置,用于将原油分解成不同沸点范围的馏分。
由于CRU在石油炼制过程中的能耗占比相当大,因此对其进行节能分析非常有必要。
对于CRU而言,节能的核心在于减少过程中的能耗损失。
在CRU的操作过程中,常见的能耗损失主要包括:泵站、换热器、冷凝器、压缩机等设备的耗能、原油损耗、热量损耗等。
对于设备的耗能,可以通过优化设备选型和运行参数来减少能耗。
可以采用高效的泵、换热器和压缩机,以提高能效;对设备的运行参数进行精确控制,如调整压力、温度等,以减少能量损失。
对于原油损耗,可以通过改进分馏工艺来减少。
通过增加蒸馏塔的塔板数或改进塔板结构,可以提高分离效率,从而减少低沸点馏分中的原油损耗。
还可以采用精炼技术,如分子筛吸附、膜分离等,来提高原油的利用率,减少废弃成分的产生。
对于热量损耗,可以采取多种措施来减少。
可以对CRU的热回收进行优化。
在冷凝器和换热器中采用换热介质之间的换热技术,以减少热量的损失。
可以在冷凝器和换热器中采用高效节能的换热器,以提高换热效率,减少能量损失。
还可以对废热进行利用,如采用余热回收技术,将废热用于其他工艺过程中。
除了在CRU装置本身上进行节能措施外,还可以从能源供应端着手,以减少能源的消耗。
可以采用替代能源,如天然气、生物质能等,来替代传统的燃料。
还可以在能源供应时进行能量增压,例如采用高温蒸汽增压等技术,来提高供能效率。
要充分发挥自动化技术和智能控制系统在CRU中的作用。
通过增加自动化控制设备,并采用智能控制算法,可以实现对CRU操作过程的精确控制和优化。
可以根据实时数据对设备进行智能调节,以提高能效和生产效率。
通过对CRU装置中的节能分析,可以针对不同的能耗损失点采取相应的措施,从而实现石油炼制过程中的能耗降低。
这不仅有助于提高能源利用效率,降低能源消耗,还能为企业降低生产成本,可持续发展。
石油炼制中常减压装置的节能分析

石油炼制中常减压装置的节能分析石油是世界上最主要的能源资源之一,石油炼制是将原油中的各种化学成分分离、转化和精制成为各种石油产品的过程。
在石油炼制过程中,常减压装置是必不可少的一部分,它可以有效地将原油中的沸点高于产品要求的各种馏分和残余液体进行分离,从而提高产品质量和提取各种高附加值产品。
常减压装置在炼油过程中也是能源消耗的重要部分,因此对于常减压装置的节能分析显得尤为重要。
常减压装置的节能分析主要从以下几个方面进行考虑:炼油工艺的优化、装置的设计和运行参数的合理选择、新技术的应用以及设备的维护管理等方面。
针对炼油工艺的优化,可以通过对炼油流程的全面分析和研究,找出节能的潜在点,降低能耗。
可以通过优化不同操作阶段的条件和参数设定,达到节能的目的。
在加热方式上可以采用高效节能的蒸汽加热,而不是燃料燃烧加热。
在冷却方面可以采用余热回收技术,将废热转化为能源,从而减少原油的能耗。
在装置的设计和运行参数的选择上,应该尽量考虑减小压力、温度的消耗,减少能源的浪费。
还可以通过加强设备的维护管理来保证设备的正常运行,避免能源的浪费。
新技术的应用也是实现常减压装置节能的重要手段之一。
采用高效的蒸汽回收装置,将废蒸汽中的热能进行回收利用,从而减少了工艺中的蒸汽消耗。
又如采用了新型的换热器设备,这些设备的换热效率更高,能够有效提高能源利用率。
还可以采用自动化控制系统,在保障产品质量的前提下,合理地控制各个工艺参数,实现节能的目的。
对于常减压装置的节能分析,需要从工艺优化、装置设计及运行参数的合理选择、新技术应用和设备维护管理等方面进行考虑。
只有通过全面的分析和研究,采取相应的措施,才能够实现常减压装置的节能目标。
随着能源资源的短缺和环境保护意识的提高,常减压装置的节能问题将越来越受到重视,只有不断地进行技术革新和管理创新,才能使炼油工艺更加节能环保。
石油炼制中常减压装置的节能分析

石油炼制中常减压装置的节能分析石油炼制过程中,炼油塔通常会采用常减压装置。
该装置能够实现有效的蒸汽排放和溶剂回收,在生产过程中具有非常重要的作用。
然而,常减压装置的大量蒸汽排放不仅浪费了能源资源,同时还对环境造成了污染。
因此,为了提高石油炼制生产过程的能效,减少能源的消耗和环境污染,需要对常减压装置进行节能分析。
1、技术方面升级技术:在现有的萃取塔中安装冷凝回收装置,将从排气管道中引出的温度高达90°的热蒸汽冷凝回收,然后再送回原系统作为回收溶剂使用。
这样可有效地减少蒸汽排放,提高了石油炼制过程的能源利用效率。
改进操作流程:通过改进设备以及操作流程等措施,降低常减压过程中的能耗。
2、管理方面有组织程序的操作:建立和落实那么进行常减压操作的程序和标准化措施,从而保证操作过程的合理性和规范化程度,减少误操作带来的损失。
提高员工技能:通过生产技能培训和考核,加强员工的操作技能,提高工作效率和安全生产水平。
优化管理模式:强制执行科学合理的计划管理模式,定期对设备进行检测和维修保养,减少设备故障率。
3、设备方面优化设备结构:通过改进设备结构和工艺流程,减少热量损失,提高设备的能效。
定期维护保养:通过定期对设备进行维护保养,保证常减压装置的稳定运行和长期使用效果。
定时检测设备运行状态:建立和落实常减压设备的定时检测制度,对重要设备进行状态监测,及时发现问题并解决。
总之,采取有效的技术、企业管理和设备措施,对石油炼制生产过程中的常减压装置进行节能分析是非常必要的。
这不仅能够减少对能源的浪费,还能减少对环境的污染,提高生产效率,降低生产成本,实现可持续发展战略。
石油炼制中常减压装置的节能分析

石油炼制中常减压装置的节能分析1. 引言1.1 石油炼制的背景石油是一种重要的能源资源,被广泛应用于工业生产、交通运输、农业等各个领域。
石油的开采和加工对人类社会的发展起着至关重要的作用,其中石油炼制是将原油中的各种组分按照其沸点进行分离的过程。
石油炼制的主要产品包括汽油、柴油、煤油、燃料油等,这些产品广泛应用于汽车、船舶、发电等领域。
常减压装置是炼油厂中的重要设备,其作用是在炼油过程中通过减压操作,将原油中的重质组分与轻质组分有效分离,达到提高产品质量和产量的目的。
常减压装置在炼油过程中起到了至关重要的作用,是实现石油炼制过程中节能减排的重要装置之一。
通过对常减压装置的节能分析和优化,可以有效提高炼油厂的生产效率,减少能源消耗和环境污染,符合绿色发展的要求。
【石油炼制的背景】的内容简要介绍了石油炼制的重要性和常减压装置在其中的作用,为接下来对常减压装置的节能分析提供了必要的背景知识。
1.2 常减压装置的作用常减压装置是石油炼制过程中的重要设备,主要用于将高温高压的裂解气体进行降压和冷却,以满足下游工艺装置的需要。
常减压装置的主要作用包括降压、分离和提纯。
在石油炼制过程中,常减压装置可以有效地控制裂解气体的压力和温度,从而保证炼油装置的正常运行。
常减压装置还可以实现气体和液体的分离,将有害物质从裂解气体中去除,保证产品的纯度和质量。
常减压装置还可以将裂解气体中的重质烃物质重新回收利用,提高资源利用率,降低能源消耗和环境排放。
常减压装置在石油炼制过程中扮演着重要的角色,是实现节能减排的重要手段之一。
2. 正文2.1 常减压装置的节能原理常减压装置的节能原理是通过减少炼油过程中的能量消耗,提高能源利用效率来实现节能减排的目的。
常减压装置在炼油过程中主要起到蒸馏和分馏的作用,通过控制压力和温度等操作参数,将原油分解为不同组分,提取出有价值的产品。
在这个过程中,能源消耗主要集中在加热和蒸发过程中,而常减压装置通过优化操作参数,减少过程中的能量损失,提高能源利用效率,从而实现节能减排的效果。
石油炼制中常减压装置的节能分析

石油炼制中常减压装置的节能分析节能是石油炼制过程中的重要环节,随着能源问题的日益突出,节能成为了石油炼制行业发展的关键。
常减压装置作为石油炼制过程中的一个重要设备,其节能优化也是炼油企业努力的方向。
本文将从常减压装置的工艺流程及设备特点出发,分析其节能优化的方法和措施。
常减压装置是石油炼制过程中的一个重要环节,主要用于分离原油中的不同组分。
其工艺流程一般包括加热、常减压和冷凝三个阶段。
在加热阶段,原油被加热至一定温度,以提高其蒸发性;在常减压阶段,原油被进一步加热,使其在较低的压力下蒸发,从而实现分离;在冷凝阶段,蒸发出的油气被冷凝成液态,进一步分离出不同组分的油品。
常减压装置的节能优化主要可以从以下几个方面入手。
首先是加热阶段的节能优化。
加热过程中,可以采用先进的加热设备,如传热效率高的换热器;对进入加热器的原油进行预热,以减轻加热器的负荷;对加热器进行热能回收,将废热用于加热其他流体等,从而提高能源利用效率。
其次是常减压阶段的节能优化。
常减压装置一般采用多级减压设备,通过逐级降低压力,使原油在不同温度下蒸发,实现组分的分离。
在常减压过程中,可以采用适当的温度和压力,使蒸汽压力和冷凝温度得到优化,从而减少能量损耗。
常减压设备的密封性能也是影响能源利用的重要因素,通过对密封系统的改进,减少泄漏,进一步提高能源利用效率。
最后是冷凝阶段的节能优化。
常减压装置在冷凝阶段,将蒸发出的油气冷凝成液态,通过冷凝器进行冷凝。
在冷凝过程中,可以采用高效的冷凝设备,如换热器等,以提高冷凝效率;对冷凝器的水冷方式进行优化,如采用冷却塔等,减少能源消耗。
除了上述几个方面外,常减压装置的节能优化还可以从运营管理层面入手。
可以制定合理的运行方案,如减少停工次数,降低设备启停的能耗;加强人员培训,提高操作人员的技术水平和管理能力,减少人为因素对能源消耗的影响;定期检修设备,保证设备的正常运行,减少能源损耗等。
常减压装置的节能优化需要从多个方面入手,包括工艺流程的优化、设备的改进以及运营管理的提升。
石油炼制中常减压装置的节能分析

石油炼制中常减压装置的节能分析随着工业化进程的不断推进,石油成为了现代社会不可或缺的能源来源。
石油炼制是将原油中的各种组分通过一系列物理和化学过程进行分离和转化,得到各种石油产品的过程。
在这个过程中,常减压装置是一个非常重要的设备,它主要用于将高压蒸汽和原料液体减压至合适的压力,以满足下游装置的工艺要求。
常减压装置的能耗一直是炼油厂关注的焦点,本文将对石油炼制中常减压装置的节能进行分析。
一、常减压装置的能耗概况常减压装置主要的能耗包括压缩能耗、冷却能耗、泵送能耗和燃料能耗等。
压缩能耗占据了主要部分,因为在减压过程中需要耗费大量的能量来实现高压气体的减压。
常减压装置中还需要进行多级冷却来降低物料温度,以及泵送原料和产品所需的能耗也不能忽视。
常减压装置的能耗是相当可观的,因此如何降低其能耗,提高能源利用效率成为炼油厂亟待解决的问题。
二、节能措施常减压装置的节能措施主要包括以下几个方面:1. 采用先进的设备和工艺技术常减压装置中的泵、压缩机、换热器等设备的能效直接影响整个装置的能耗水平,因此选择高效的设备是降低能耗的重要手段。
通过优化工艺流程、提高系统集成度、改进操作方式等手段,也能够有效降低常减压装置的能耗。
2. 热能回收利用在常减压装置的运行过程中,会产生大量的热能,可以通过换热器进行回收利用。
可以将高温高压气体的余热用于蒸汽发生、原油加热等环节,从而减少了额外的能源消耗,提高了能源利用效率。
3. 节能改造对既有的常减压装置进行节能改造也是降低能耗的有效途径。
更换低能耗的泵、压缩机设备,加装节能型换热器等措施都能够有效降低能耗,提高石油炼制的能源利用效率。
三、节能效果分析通过以上节能措施的实施,常减压装置的能耗明显得到了降低。
采用了先进的设备和工艺技术后,设备的能效得到了提高,从而降低了压缩能耗和冷却能耗。
热能回收利用也使得大量的余热得到了有效利用,减少了对外部能源的需求。
通过对既有设备的节能改造,使得设备的能效得到提升,进一步减少了常减压装置的能耗。
石油炼制中常减压装置的节能分析

石油炼制中常减压装置的节能分析石油炼制中的常减压装置是炼油过程中不可或缺的一环,其主要功能是将高温高压的原料油通过减压作用来分解和蒸馏,从而得到不同级别的石油产品。
常减压装置在操作过程中会产生大量的能量损失,不仅降低了能源利用率,还增加了能源的消耗成本。
对常减压装置进行节能分析和优化是非常必要的。
常减压装置主要包括加热炉、主减压塔、吸收塔等组成部分。
在这些组成部分中,其中的加热炉是能耗最高的部分,因此在节能分析中应重点关注。
我们可以对常减压装置进行能量流图分析,以了解能量的流向和损失情况。
常减压装置中的能量主要来自于加热炉,加热炉通过燃烧燃料产生的烟气和空气混合物来提供热量。
烟气中的热量通过对流和辐射传递给加热炉内的管道和设备,然后再传递给原料油,并使其升温。
在能量流图分析过程中,我们可以发现能量的损失主要来自于以下几个方面:1. 空气过量供应导致能量的浪费。
在加热炉中,空气通过风机供应给燃烧器,用于燃烧燃料。
如果供氧过量,将导致燃烧不充分,增加了未燃尽的燃料和CO的排放,同时将烟气中的热量带走,造成能量的浪费。
2. 管道和设备表面的散热损失。
在常减压装置中,管道和设备表面均会散发热量,这些热量无法被利用,而是直接损失掉,从而造成了能量的浪费。
3. 多级减压塔的能量损失。
常减压装置通常采用多级减压塔结构,每一级的减压塔都会损失一部分能量。
这是因为在减压塔内,原料油在不断降压的过程中会发生蒸发和冷却,从而造成能量的损失。
针对以上能量损失问题,可以采取以下几种节能措施来优化常减压装置的能源利用效率:1. 控制空气供应量。
通过精确控制燃烧风量,可以保证燃烧充分,减少未燃尽的燃料和CO的排放,并降低烟气中的热量损失。
2. 加强保温措施。
对管道和设备进行保温处理,减少热量的散失,提高能量的利用率。
3. 优化减压塔结构。
通过合理设计减压塔的结构和参数,可以减少能量的损失。
增加塔板数目、增加效率塔板高度等措施都可以提高减压效果,减少能量损失。
石油炼制中常减压装置的节能分析

石油炼制中常减压装置的节能分析石油炼制过程中,常减压装置是一个关键的设备,用于降低原油的压力,使其能够在后续的处理过程中更好地分离和提炼。
常减压装置的操作虽然能够实现石油炼制的需要,但也存在能源浪费和环境污染的问题。
通过对常减压装置的节能分析,可以找到改善措施,减少能源消耗和环境影响。
常减压装置中的节能技术主要有以下几个方面:1. 循环利用能源:常减压装置中的流体经过减压后,产生大量的低温低压废热和废气。
通过对这些废热和废气进行有效利用,可以减少对额外能源的需求。
可以利用废热进行余热回收,用于加热或蒸汽生成。
通过合理设计废气收集和处理系统,减少有害气体的排放。
2. 引入先进技术:常减压装置的设计和运行中,可以采用一些先进的技术,提高能源利用效率。
采用节能型设备,改善设备的传热传质性能,提高设备的热力学效率。
在操作控制方面,可以采用先进的自动化控制系统,实现更加精确的控制,避免能源的浪费。
3. 优化工艺条件:通过优化常减压装置的工艺条件,可以减少能源的消耗。
合理选取工作压力和温度,减少能源的传输损失。
通过合理安排减压阶段,提高石油分馏的效率,减少副产物的形成。
对于不同类型的原油,采取不同的操作策略,以最大限度地保证能源的利用效果。
进行常减压装置的节能分析需要从技术、经济和环境等方面进行综合考虑。
在技术方面,需要综合考虑常减压装置的主要设备、工艺参数和运行条件等因素。
通过对各个环节的分析,确定存在的能源浪费问题,提出改进措施。
对于能源利用率低的设备,可以进行能效改造,提高设备的能源利用效率。
对于操作不当导致的能源浪费问题,可以加强培训和管理,确保操作人员正确使用设备。
在经济方面,需要进行能源消耗成本和改进措施成本的评估。
通过经济分析,确定节能改进措施的经济可行性,为节能技术的推广和应用提供依据。
还需要考虑节能措施对产品质量和生产效率的影响,确保节能措施的实施不会降低工艺效益。
在环境方面,需要评估常减压装置对环境的影响。
常减压蒸馏装置节能分析
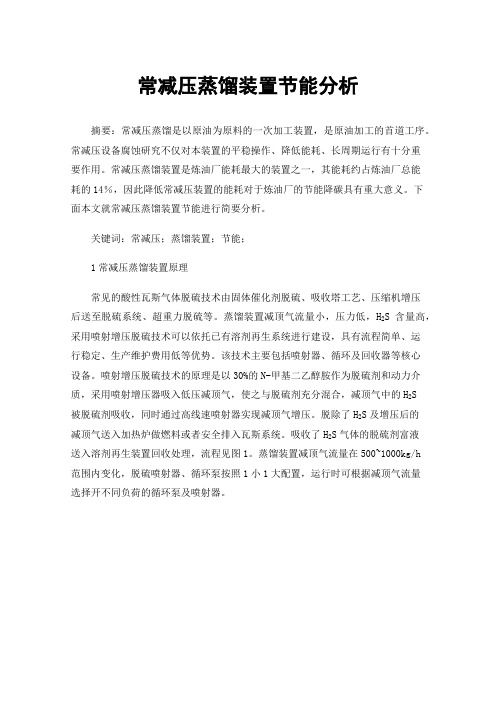
常减压蒸馏装置节能分析摘要:常减压蒸馏是以原油为原料的一次加工装置,是原油加工的首道工序。
常减压设备腐蚀研究不仅对本装置的平稳操作、降低能耗、长周期运行有十分重要作用。
常减压蒸馏装置是炼油厂能耗最大的装置之一,其能耗约占炼油厂总能耗的14%,因此降低常减压装置的能耗对于炼油厂的节能降碳具有重大意义。
下面本文就常减压蒸馏装置节能进行简要分析。
关键词:常减压;蒸馏装置;节能;1常减压蒸馏装置原理常见的酸性瓦斯气体脱硫技术由固体催化剂脱硫、吸收塔工艺、压缩机增压后送至脱硫系统、超重力脱硫等。
蒸馏装置减顶气流量小,压力低,H2S含量高,采用喷射增压脱硫技术可以依托已有溶剂再生系统进行建设,具有流程简单、运行稳定、生产维护费用低等优势。
该技术主要包括喷射器、循环及回收器等核心设备。
喷射增压脱硫技术的原理是以30%的N-甲基二乙醇胺作为脱硫剂和动力介质,采用喷射增压器吸入低压减顶气,使之与脱硫剂充分混合,减顶气中的H2S被脱硫剂吸收,同时通过高线速喷射器实现减顶气增压。
脱除了H2S及增压后的减顶气送入加热炉做燃料或者安全排入瓦斯系统。
吸收了H2S气体的脱硫剂富液送入溶剂再生装置回收处理,流程见图1。
蒸馏装置减顶气流量在500~1000kg/h范围内变化,脱硫喷射器、循环泵按照1小1大配置,运行时可根据减顶气流量选择开不同负荷的循环泵及喷射器。
图1喷射增压脱硫系统流程2常减压蒸馏装置节能措施降低常减压蒸馏装置的能耗主要有3种途径,降低工艺总用能、提高热量回收率和提高能量转换效率。
在降低工艺总用能方面,需要结合全厂总流程,从装置流程设置和产品结构方面优化降低装置用能;在提高热量回收率方面,主要措施有利用“窄点”技术深度优化换热网络、装置间采用热联合、采用高效传热设备和加强低温热的回收利用等;在提高热量转化效率方面,主要措施有强化加热炉的传热提高加热炉的热效率和采用高效节能变频电机等。
结合国内某炼油厂的常减压蒸馏装置设计工作(加工规模为15.0Mt/a,设计加工中东原油),拟从提高热量回收率和降低工艺总用能等方面深入探讨如何有效降低常减压蒸馏装置的能耗和碳排放。
石油炼制中常减压装置的节能分析

石油炼制中常减压装置的节能分析石油炼制是一种能源转化过程,它将原油转化为各种有用的石油产品,如汽油、柴油、煤油等。
在石油炼制过程中,常减压装置是其中一个重要的装置,它可以通过减压分离来提取原油中的不同组分,从而获得所需的产品。
常减压装置是石油炼制过程中的一个关键步骤,它可以将高温高压的原油通过减压分离,将原油分解成不同的馏分。
常减压装置主要由蒸馏塔、换热器、冷凝器等设备组成。
在传统的常减压装置中,存在一些能量损耗的问题。
由于常减压装置需要对原油进行加热,以提高其温度和压力,这就需要大量的能量输入。
在常减压装置中,需要对产生的气体进行冷却和液化处理,这同样会导致能量的损耗。
为了解决这些能量损耗问题,可以采用一些节能措施。
可以通过优化设备的结构和工艺参数,减少对原油的加热需求。
可以采用先进的换热器和加热方式,提高换热效率,减少加热能耗。
可以采用低温冷凝技术,将产生的气体进行冷凝和液化处理,以回收部分能量。
还可以通过选择合适的蒸馏塔和分离操作条件,提高石油产品的纯度,减少后续加工过程中的能量损耗。
除了以上的节能措施,还可以考虑一些辅助设备的使用,如余热回收装置、能量转换装置等,以提高能量利用效率。
还可以采用先进的自动控制系统,对常减压装置的运行过程进行精确控制,以优化能量利用和减少能量损耗。
常减压装置在石油炼制中起着重要的作用,但其能源消耗也是一个问题。
通过采取一系列的节能措施,可以减少能源的消耗,提高能源利用效率,实现石油炼制过程的节能减排。
这也有助于减少对化石燃料的依赖,推动石油炼制行业向着更加可持续的方向发展。
炼油厂常减压装置节能新技术措施分析

炼油厂常减压装置节能新技术措施分析炼油厂常减压装置是炼油过程中重要的装置之一,它主要用于将高温高压的油气降压并冷却,以保证炼油过程的安全性和稳定性。
常减压装置的运行消耗大量的能源,造成能源浪费和环境污染,因此需要采取节能措施来降低能源消耗。
1. 优化常减压装置的结构:通过改变常减压装置的结构设计,减少局部压降,提高设备的能效。
可以采用多级联合减压的形式,将原来的单级减压改为多级减压,减少单级减压过程中的能量损失。
2. 提高常减压装置的传热效率:常减压装置中的传热过程是能源消耗的重要环节。
可以采用增加传热面积的方法,如增加传热管束数量或采用表面增强传热技术,提高传热效率,减少能源消耗。
3. 优化常减压装置的操作方式:通过优化常减压装置的操作方式,减少能源的消耗。
可以采用变压降操作策略,根据炼油过程中油气的压力变化,调整减压装置的压降,以最低的能量消耗实现安全的减压。
4. 应用先进的控制技术:采用现代化的控制系统和自动化技术,实现常减压装置的精细化控制和优化操作。
通过精确控制常减压装置的压力、温度等参数,提高设备的运行效率,减少能源浪费。
5. 温度回收利用技术:常减压装置中的冷凝器常常需要大量的冷却水,造成能源的浪费。
可以采用温度回收利用技术,将冷凝器排出的高温水回收利用,用于其他工艺环节或生活热水供应,减少能源消耗。
6. 应用节能设备和材料:选择高效节能的设备和材料,如高效换热器、高效节能电机等,减少能源的消耗,提高设备的能效。
在炼油厂常减压装置的节能措施分析中,可以从结构优化、传热效率提高、操作方式优化、控制技术应用、温度回收利用技术以及应用节能设备和材料等多个方面入手,共同促进常减压装置的节能改造,降低能源消耗,提高炼油过程的能效。
石油炼制中常减压装置的节能分析

石油炼制中常减压装置的节能分析石油炼制是想要从原油中提取出各种有用产品的重要过程。
然而,这个过程需要巨大的能量消耗,并且由于炼制厂的运营成本越来越高,节能成为了非常重要的目标。
在石油炼制过程中,常减压装置是一个非常重要的能源消耗设施。
因此,探索并改进常减压装置的能效将是一个重要的节能方案。
常减压装置是为了从原油中分离出不同的油品而开发的一种设备。
其中一个典型的常减压塔通常包含了一系列的分离圈,用于在降低压力的环境下对不同种类的石油产品进行分离。
然而,该过程需要大量的热量来将油品加热到熔点或者沸点,以实现分离。
因此,为了减少能源消耗并提高能源效率,在常减压装置中采用了一些节能技术。
目前,为了提高常减压装置的能效,许多厂家采用了一些节能的技术。
例如:1.采用高效的换热器在常减压装置中,热量是一个非常关键的因素,因此,采用高效的换热器可以将热量的利用效率提高到更高的水平。
高效的换热器能够将热量从一个加热指定的流体或气体中获取,并将这些热量传递到另一个流体或气体中。
因此,使用高效的换热器可以最大限度地利用热量,减少热量损失,提高常减压装置的能效。
2.使用低能耗的泵在常减压装置中,泵是用于输送油品的一个关键设备。
然而,传统的泵通常需要使用大量的能量,同时还需要消耗很多电能。
由于能源的成本不断上涨,使用低能耗的泵已经成为了一个非常流行的节能方案。
效率高、噪音低和维修成本低的涡轮式泵和转子式泵是当前比较流行的节能泵产品。
3.使用节能的热交换器在石油炼制过程中,热能耗费是非常高的。
通常,热交换器被用于调节和优化传热,以最小化能源消耗。
一些新型的热交换器能够使用嵌入或者堆叠的传热板来提高传热效率,从而实现更加高效的能源利用。
总的来说,常减压装置的节能方案需要采用多种技术,以提高常减压装置的能效。
这些节能技术可以包括使用高效的换热器、低能耗的泵和节能的热交换器。
随着技术的不断提升和节能设备的不断改进,节能技术将在石油炼制和全球其他行业中得到广泛的应用。
原油常减压装置节能技术

第24卷第3期2006年6月天 然 气 与 石 油N atural G asAnd OilVol.24,No.3J un.2006 收稿日期:2005207229 作者简介:王颖华(19742),男,河南方城人,工程师,在读工程硕士,主要从事油田规划设计工作。
电话:(0377)63837822。
原油常减压装置节能技术王颖华(河南南阳河南油田设计院,河南南阳473132)摘 要:由于常减压装置消耗能量约占炼油厂总用能的25%~30%,已成为炼油厂中消耗量最大的装置,因此,我国各炼油厂对常减压装置进行以降低能耗为中心的技术改造就显得十分必要。
详细介绍了适用于常减压装置节能的新工艺、新设备以及优化操作。
工艺方面主要有采用过滤脱盐新技术对原油进行深度脱盐、采用强化蒸馏新工艺提高原油蒸馏拔出率、优化产出、增产柴油;设备方面主要使用规整填料和新型塔板改善分馏塔分馏效率、使用新型燃烧器提高加热炉效率、使用新型换热器提高热回收率、采用变频技术降低装置电耗;优化操作方面主要有利用计算机进行监控与管理和改善操作条件。
最后对国内原油常减压装置节能改造提出了一些建议,以供炼油企业在进行原油常减压装置改造时参考。
关键词:常减压装置;工艺;设备;优化操作;节能文章编号:100625093(2006)0320059206 文献标识码:A 由于原油常减压装置消耗能量约占炼油厂总用能的25%~30%,已成为炼油厂中消耗量最大的装置,因此面对日趋激烈的市场竞争,我国各炼油厂对其进行以降低能耗为中心的技术改造就显得十分必要。
1 采用新技术改进工艺过程改进工艺过程是常减压装置节能的重要手段,包括改进工艺生产流程、采用节能新工艺、新技术等内容。
1.1 采用过滤脱盐新技术对原油进行深度脱盐电脱盐是常减压装置的第一道工序。
当今的电脱盐工艺是炼油厂降低能耗、减轻设备结垢和腐蚀、减少催化剂消耗及改善产品质量的重要工艺过程,并直接关系到炼油厂经济效益。
石油炼制中常减压装置的节能分析

石油炼制中常减压装置的节能分析
石油炼制中常减压装置是一个重要的装置,用于将高压的原料原油通过减压操作分离
出不同组分,常减压装置的节能分析对于提高能源利用率和降低生产成本具有重要意义。
常减压装置采用了蒸汽膨胀式减压,通过适当的减压操作,能够将原油中的低沸点组
分分离出来,从而减少了反应器的负荷,提高了能源利用率。
与传统的冷凝式减压相比,
蒸汽膨胀式减压需要更少的能量输入,减少了能源消耗。
常减压装置还采用了废热回收技术,在冷凝过程中将废热回收利用,用于加热其他工
艺流程的介质。
这种废热回收技术不仅减少了能源的消耗,同时也降低了生产过程中的二
氧化碳排放量,对于环境保护具有积极的意义。
常减压装置还采用了先进的控制系统,能够精确控制温度、压力等参数,实现最佳的
操作效果。
通过对操作参数的精确控制,可以减少能源的浪费,提高能源利用效率。
常减压装置还可以通过热交换器和冷凝器等附属设备的设置,进一步提高能源利用效率。
通过热交换器和冷凝器的运用,可以将高温的废热回收利用,提高了热能的利用效率,减少了能源的浪费。
石油炼制中常减压装置的节能分析具有重要的意义。
通过采用蒸汽膨胀式减压、废热
回收技术、先进的控制系统以及热交换器和冷凝器等附属设备的设置,可以有效降低能源
的消耗,提高能源利用效率,降低生产成本,对于企业的可持续发展具有重要的促进作用。
还需要进一步研究和开发更加高效节能的常减压装置技术,为石油炼制行业的绿色发展做
出更大的贡献。
- 1、下载文档前请自行甄别文档内容的完整性,平台不提供额外的编辑、内容补充、找答案等附加服务。
- 2、"仅部分预览"的文档,不可在线预览部分如存在完整性等问题,可反馈申请退款(可完整预览的文档不适用该条件!)。
- 3、如文档侵犯您的权益,请联系客服反馈,我们会尽快为您处理(人工客服工作时间:9:00-18:30)。
第24卷第3期2006年6月天 然 气 与 石 油N atural G asAnd OilVol.24,No.3J un.2006 收稿日期:2005207229 作者简介:王颖华(19742),男,河南方城人,工程师,在读工程硕士,主要从事油田规划设计工作。
电话:(0377)63837822。
原油常减压装置节能技术王颖华(河南南阳河南油田设计院,河南南阳473132)摘 要:由于常减压装置消耗能量约占炼油厂总用能的25%~30%,已成为炼油厂中消耗量最大的装置,因此,我国各炼油厂对常减压装置进行以降低能耗为中心的技术改造就显得十分必要。
详细介绍了适用于常减压装置节能的新工艺、新设备以及优化操作。
工艺方面主要有采用过滤脱盐新技术对原油进行深度脱盐、采用强化蒸馏新工艺提高原油蒸馏拔出率、优化产出、增产柴油;设备方面主要使用规整填料和新型塔板改善分馏塔分馏效率、使用新型燃烧器提高加热炉效率、使用新型换热器提高热回收率、采用变频技术降低装置电耗;优化操作方面主要有利用计算机进行监控与管理和改善操作条件。
最后对国内原油常减压装置节能改造提出了一些建议,以供炼油企业在进行原油常减压装置改造时参考。
关键词:常减压装置;工艺;设备;优化操作;节能文章编号:100625093(2006)0320059206 文献标识码:A 由于原油常减压装置消耗能量约占炼油厂总用能的25%~30%,已成为炼油厂中消耗量最大的装置,因此面对日趋激烈的市场竞争,我国各炼油厂对其进行以降低能耗为中心的技术改造就显得十分必要。
1 采用新技术改进工艺过程改进工艺过程是常减压装置节能的重要手段,包括改进工艺生产流程、采用节能新工艺、新技术等内容。
1.1 采用过滤脱盐新技术对原油进行深度脱盐电脱盐是常减压装置的第一道工序。
当今的电脱盐工艺是炼油厂降低能耗、减轻设备结垢和腐蚀、减少催化剂消耗及改善产品质量的重要工艺过程,并直接关系到炼油厂经济效益。
用过滤法对原油进行脱盐脱水的技术是一种对乳化原油破乳的新技术[1]。
该技术首先要选择一种良好的固体吸附剂作为过滤材料,并制成破乳过滤柱。
武汉石油化工设备研究所研制成功这种过滤材料,是一种硅铝酸盐的多孔材料,其主要性能如下:颗粒直径为1~4nm ,平均有效半径为11nm ,孔容积超过 1.9×10-6m 3/kg ,比表面积约为0.68m 2/g ;该多孔材料的表面凹凸不平,表面的原子性质不尽相同,该材料中除含有A I ,Si 外,还有其它多种元素组成;亲水性强,有一定的亲油性;有足够的强度,长期浸在100℃以上的原油中不溶解,能经受反冲洗再生时颗粒间的摩擦而不破碎。
用这种过滤材料对原油进行脱盐脱水,其过滤脱盐工艺与原电脱盐工艺指标对比,见表1。
表1 过滤脱盐工艺与原电脱盐工艺指标对比工艺指标电脱盐(二级送电、三级沉降)过滤脱盐(一级过滤、一级送电、三级沉降)脱后含盐/μg .L -15.11 2.17脱后含水/(%)0.300.15脱盐温度/℃105~13096~110注水量/(%)4.0~6.0 1.5~3.0破乳剂量/μg .g -125~3015~20排水带油/μg .g -130~8030每吨原油电耗/kW .h0.610.20表1数据表明,过滤法脱盐脱水后,原油平均含盐量为2.17mg/L ,原油平均含水量为0.15%,原油含盐含水合格率为91.23%,达到了较好的效果。
过滤法工艺具有明显的节电、节水、节省破乳剂的效果。
1.2 采用强化蒸馏新工艺提高原油蒸馏拔出率据文献报道[2],常减压渣油中仍含有5%~7%的轻组分,而这部分轻质油的拔出并非是能够通过提高蒸馏效率所能达到的。
相反,加入活化剂强化原油蒸馏着眼于挖掘这部分潜含的轻质油,从根本上提高轻质油的拔出率。
在国外,前苏联新乌发炼油厂将减三线精制抽出油(芳烃含量为74.9%,其中重质芳烃占32.6%)在减压炉前混入重油进行工业试验,试验过程中工艺参数稳定,与常规蒸馏无异,抽出油的加入量以2%最佳,此时减压蒸馏的拔出率增加7.7%(相对进料)或4.3%(相对原油),用作润滑油、基础油时性质毫无劣化。
在燃料油型装置上,抽出油加入2.5%(对进料)时,蜡油拔出率绝对增长3.6%(对蜡油);在西西伯利亚原油中加入适量的C 12~C 14高级脂肪醇可以提高轻质馏分油的收率,在脂肪醇含量为4%~5%(对进料)时,蜡油拔出率绝对增长3.6%(对蜡油)。
上海石化股份有限公司对其1#、2#常减压装置常压重油使用“强-2”添加剂,结果表明,“强-2”的最佳加入量为2%,气相绝对增率达到+1.20%~+1.40%。
另外,重油强化蒸馏的V GO 产品除了康氏残炭与化学族组成中双环芳烃、多环芳含量略高外,其它分析指标变动不大,对后序工艺过程影响不大;胜利炼油厂在第一套常减压装置上进行了强化蒸馏的工业试验,取得了成功。
添加剂注入量为50μg/g ,常压炉出口温度(365±1)℃,常三线生产A GO (常压瓦斯油)时终馏点为370~380℃,减压炉出口温度(384±2)℃,减压真空不小于98.66kPa ,减三、减四线集油箱液面高度60%~80%,加T118添加剂后蜡油平均拔出率可提高1.04个百分点(对原油),加T218-A 添加剂后蜡油平均拔出率可提高1.41个百分点(对原油)。
加剂后拔出蜡油的颜色变浅,质量改善,将其作为FCC 原料可提高轻质油收率及总液体收率。
1.3 优化产出增产柴油将柴油馏分尽可能全部从常压塔拔出,不仅可以降低减压炉负荷,改善减压塔操作,而且对提高装置平稳率和节能降耗将起到至关重要的作用。
济南炼油厂从减一线、常三线(0#柴油)组成分析数据发现,减一线含有60%的柴油馏分,见表2。
因此,实施减一线补常二中的改造项目,理论上能达到提高柴油收率的目的[3]。
表2 济南炼油厂减一线、常三线组成分析数据项目/比重D 420馏程/℃KK 10%30%50%70%90%95%凝固点/℃减一线0.86322622873023143253383466常三线0.8337209248268283306336343-1改造方法:减一线泵出口增设一条支路打入常二中油返塔管线,改造后流程,见图1。
图1 减一线补常二中改造流程 在其它条件基本不变的情况下,通过流量控制阀控制减一线补入量为4~5t/h ,并适当调整常二中回流量,合适的组分就由14层板下抽出后作为常三线(0#柴油)。
通过上述技术改造,直馏柴油收率约增加3%,每年可为该厂(常压车间原油加工量为180×104t/a )创收效益1566万元。
06 天 然 气 与 石 油2006年2 采用新型、高效、低耗设备以降低能耗2.1 对塔内件进行改造,改善分馏效率分馏塔是原油蒸馏过程的核心设备,塔内传质构件即塔板、塔填料是油品分馏塔最关键的部件。
对于一个操作方案已定的分馏塔,塔内传质构件选用是否得当,直接关系着能否高产、优质、低消耗地完成各项任务。
2.1.1 使用规整填料,提高传质效率近十年来,蒸馏装置发展趋势是现代规整填料塔逐步取代传统填料塔,且大部分取代大型板式塔。
目前规整填料种类多、形状不同、特性各异。
Mella2 pak填料(带孔波纹板,材质为不锈钢料等,比表面积700m2/m3)是瑞士Sulzer公司的专利产品,它的问世是20世纪70年代规整填料史上一座重要里程碑。
如今,Mellapak的换代产品已经出现,他们是瑞士KU HN I公司的Rombopak填料、德国RASCHIG 公司的Raschig-Superpak填料、我国天津大学Zu2 pak填料等。
某炼油厂常压塔中部浮阀塔用波纹填料代替,其中包括液体分布器,支承栅等内件,并用常三线供二中回流返回到填料上方,技术改造投产成功,强化了塔的分离能力,如表3所示。
表3 常三线分析结果比较项 目HK/℃97%/℃常三干点/℃常三与常二重迭/℃改造前260~270310~325270~29520~25改造后270~285305~315270~29515~20更换波纹填料后,常二中的运行并不影响320 #重液蜡产品质量,相反得到改善,馏程变窄与常三重迭下降近10℃,另外减少了汽提蒸气用量,提高了换热终温,降低了常压负荷,节省了大量冷却水,缓和了本厂供水矛盾,经济效益显著,1.2个月即可收回改造投资。
在乱堆填料、规整填料和塔板的比较中,规整填料的压降低,另外,规整填料还有传质效率高、处理量大,规整填料塔的放大效应小等优点。
山东东营垦利石化总厂在改造中将填料由矩鞍环改为金属板波纹规整填料(规整250Y),其性能特性,如表4所示[4]。
表4 金属板波纹规整填料性能型号比表面积/m2・m-3空隙率/(%)理论塔板压力降/Pa・m-1板厚/mm峰高/mm倾角开孔率/(%)堆积重度F因子/m(s・(kg・m3)0.5)-1250Y250972~3266.60.211.4458.5200 2.5 改造后,运行正常,操作稳定,减压拔出率比改造前提高了6.08%,由于整个塔空隙率增大,处理能力有了较大的提高。
2.1.2 使用新型塔板改善分馏效率板式塔历来应用最广,20世纪50年代开发的浮阀塔板,尤其是F1浮阀更具优势,应用颇广。
但随着塔器技术不断进步,发现F1浮阀存在着一些缺点,各种新型高效塔板应运而生,并获得了广泛应用。
我国华东理工大学研究和开发了导向浮阀塔板,并获得国家专利。
导向浮阀吸取了条阀和导向筛板导向孔的各自特点,在条阀阀面上开1~2个导向孔,以发挥气流推液的作用。
由于导向孔的设置,导向浮阀具有较小的液面梯度、塔板上液相返混较小且可消除塔板上液体滞止区。
实验研究和工业应用表明,导向浮阀塔板和F1型浮阀塔板相比,处理能力可提高30%以上,塔板效率提高10%~20%,塔板压降减小20%左右。
导向浮阀塔板开发成功以来,已在常压塔 3800获得广泛应用,取得了显著的经济效益。
L1型条型浮阀为长方形,在生产中,气体从两侧流出与塔板上的液流方向互相垂直,塔板上的液体返混程度明显减少。
由于其结构为长方形,故不会象F1型浮阀那样因旋转而脱落,适用于装置长周期安全生产。
在相同的条件下,条型浮阀塔板的雾沫夹带小,故其允许上限气速较高。
在相同条件下,条型浮阀塔板的稳定操作区大,其操作弹性大;梯型浮阀除了具有条型浮阀的特性外,还具有有效的导流作用,泄漏量小,故其允许的气相负荷下限较低。
长庆石油勘探局炼油厂应用新型的L1型条型浮阀和梯型浮阀塔板对常压塔进行了改造,将塔内第5~48层塔板改为L1型条型浮阀塔板,针对提16第24卷第3期王颖华:原油常减压装置节能技术 馏段高液相负荷,低气相负荷的特点,对塔内1~4层塔板在国内率先采用目前国际最先进的梯型浮阀塔板。