课题6:数控铣削综合加工实例
铣工 综合加工实例
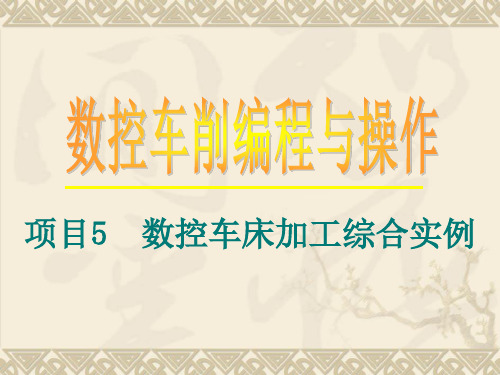
数控车床加工综合实例
任务一 综合加工实例
本任务加工如图 88 所示典型轴类零件,毛 坯尺寸为φ 50 mm×105 mm,材料为45 钢。本任 务要求学生能够熟练地确 定该零件的加工工艺,正 确地编制零件的加工程序, 并完成零件的加工。
1.零件图工艺分析
该零件主要加工外轮廓表面,零件轮廓包括球头、外圆、 螺纹、沟槽、锥体等表面,其中多个直径尺寸与轴向尺寸有较 高的尺寸精度,各主要外圆表面的表面粗糙度值均为Ra1.6 μ m ,其余表面的表面粗糙度值均为Ra3.2μ m ,说明该零件 对尺寸精度和表面粗糙度有比较高的要求,因此,加工工艺应 安排粗车和精车。零件左右两端的轮廓不能同时加工完成,需 要掉头装夹。
2.左端加工程序
O8006; 程序名 N5 G98 M03 S600; 每分钟进给,主轴正转,转速为 600 r/min N10 M08 T0202; 切削液开,选 2 号刀,执行 2 号刀补 N20 G00 X52.0 Z1.0; 快速靠近工件 N30 G71 U2.0 R0.5; 粗车循环,车去大部分加工余量 N40 G71 P50 Q120 U1.0 W0.2 F100;N50 G00 X0; X 向进刀 N55 G01 Z0 F60; 到达圆弧起点 N60 G03 X26.0 Z-5.0 R19.0; 加工 R19 mm 圆弧 N70 G01 Z-10.0; 加工φ 26 mm 外圆 N80 X30.0; 加工端面 N90 Z-28.0; 加工φ 30 mm外圆
N330 N340 N350 N360 N380 N390 N400
M03 S600 T0303; 换螺纹刀,主轴正转,转速为600 r/min G00 X32.0 Z-7.0; 快速靠近工件 G92 X29.0 Z-25.0 F1.5; 螺纹循环,第一次切入0.8 mm X28.5; 第二次切入 0.5 mm X28.38; 第三次切入 0.12 mm G00 X100.0 Z50.0; 退至安全点 M30; 程序结束
铣削加工实例

主轴转速n(r/min)主要根据允许的切削速度c(m/min)选取。
n 1000vC πD
式中: vc————切削速度,由刀具的耐用度决定; D——工件或刀具直径(mm)。 主轴转速n要根据计算值在机床说明书中选取标准值,
并填入程序单中。
切削用量
建立刀补指令格式:
G17 G01(G00)G41(G42) X_ Y_ D## G18 G01(G00)G41(G42) X_ Z_ D## G19 G01(G00)G41(G42) Y_ Z_ D## 撤消刀补指令格式: G01(G00) G40 X_ Y_ Z_
图 3.20 G41与G42 的判断
• 背吃刀量ap与进给量 f 影响
• 因 切为 削切 面削 积面。切积削AD面=积a的p f增,大所将以使背变吃形刀力量和a摩p与擦进力给增量大f,的切增削大力都也将将增增大大,
但两者对切削力影响不同。
• 由 影于 响进 比给 进量给量f 的f大增。大会减小切削层的变形,所以背吃刀量ap对切削力的
• 在生产中,如机床消耗功率相等,为提高生产效率,一般采用提高进给 量而不是背吃刀量的措施。
格式中,Z值是属于G00或G01的程序指令值,同样有G90和G91两种编程方式。 H为刀长补偿号,它后面的两位数字是刀具补偿寄存器的地址号,如H01是指01
号寄存器,在该寄存器中存放刀具长度的补偿值。刀长补偿号可用H00~H99来指定。
+Z G43
+Z G44
程序中指令点
(Hxx)值
实际到达点
(Hxx)值
工件
图 3.21 刀补过程图
3.2.1 刀具的长度补偿
使用刀具长度补偿功能,可以在当实际使用刀具与编程时估计的刀具 长度有出入时,或刀具磨损后刀具长度变短时,不需重新改动程序或重新
数控铣削综合编程实例
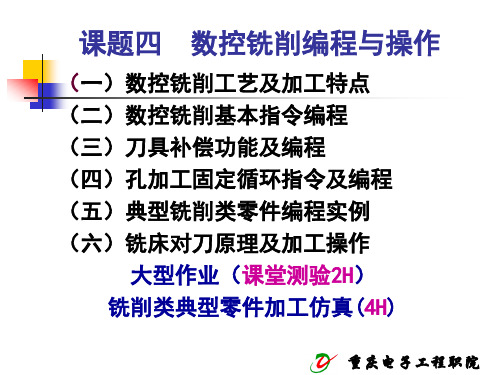
艺 分 析 及
X-75 Y0; G01 Z0 F100; X75; (上平面加工) G00 Z100 M05; G28;
编
程
重庆电子工程职业学院
课题四 数控铣床和加工中心编程
3、程序编制
T02 M06 ;(外轮廓加工)
典 G00 G43 Z5 H02 M03;
型 X-40 Y-40;
零
G41 X-25 Y-40 D02; G01 Z-4 F100;
铣Φ14、Φ35内圆腔
(G41)
O1000 G28 T01 M06 G54 M03 S800 M08 G00 G43 Z20 H01 G99 G81 X0 Y0 Z-1 R3 F100 X12.25 Y0 X17 Y17 X0 Y12.25 X-17 Y17 X-12.25 Y0 X-17 Y-17 X0 Y-12.25 G98 X17 Y-17 G49 G00 Z50 M05 G28 T02 M06 G00 G43 Z20 H02 M03 G99 G81 X0 Y0 Z-5 R3 F100 X12.25 Y0 X17 Y17 X0 Y12.25 X-17 Y17 X-12.25 Y0 X-17 Y-17 X0 Y-12.25 G98 X17 Y-17 G49 G00 Z50 M05
锪4-Φ8孔(G82) 铣Φ14、Φ35内圆 腔
(G41)
重庆电子工程职业学院
课题四 数控铣床和加工中心编程
程序编写
1)T01中心钻9-Φ3
(G43 G81)
2)T02钻头9-Φ6孔
(G43 G81)
数控铣削加工综合实例

数控铣削加工综合实例加工如图10-1所示零件(单件生产),毛坯为80mm×80mm×19mm长方块(80mm×80mm四面及底面已加工),材料为45钢。
任务实施的具体方法及步骤1.分析零件图样该零件包含了平面、外形轮廓、型腔和孔的加工,孔的尺寸精度为IT8,其它表面尺寸精度要求不高,表面粗糙度全部为Ra3.2,没有形位公差项目的要求。
2.工艺分析1)加工方案的确定根据零件的要求,上表面采用端铣刀粗铣→精铣完成;其余表面采用立铣刀粗铣→精铣完成。
2)确定装夹方案该零件为单件生产,且零件外型为长方体,可选用平口虎钳装夹。
工件上表面高出钳口11mm左右。
3)确定加工工艺加工工艺见表10-1。
4)进给路线的确定(1)外轮廓粗、精加工走刀路线(2)型腔粗、精加工走刀路线(3)孔精加工走刀路线5)刀具及切削参数的确定10.2.2 参考程序编制1.工件坐标系的建立以图示的上表面中心作为G54工件坐标系原点。
2.基点坐标计算(略)3.参考程序1)上表面加工程序上表面采用面铣刀加工,其参考程序见表10-5。
表10-5 上表面加工参考程序2)外轮廓、孔、型腔粗加工程序外轮廓、孔、型腔粗加工采用立铣刀加工,其参考程序见表10-6至10-8。
表10-6 外轮廓、孔、型腔粗加工程序表10-7 外轮廓加工子程序表10-8 型腔加工子程序3)外轮廓、孔、型腔精加工程序外轮廓、孔、型腔精加工采用立铣刀加工,其参考程序见表10-9。
表10-9 外轮廓、孔、型腔精加工程序布置作业(时间:2分钟)10-2 练习编写图10-5所示零件加工工艺及程序,毛坯为80mm×80mm×19mm长方块(80mm×80mm四面及底面已加工),材料为45钢。
课题6:数控铣削综合加工实例(1)
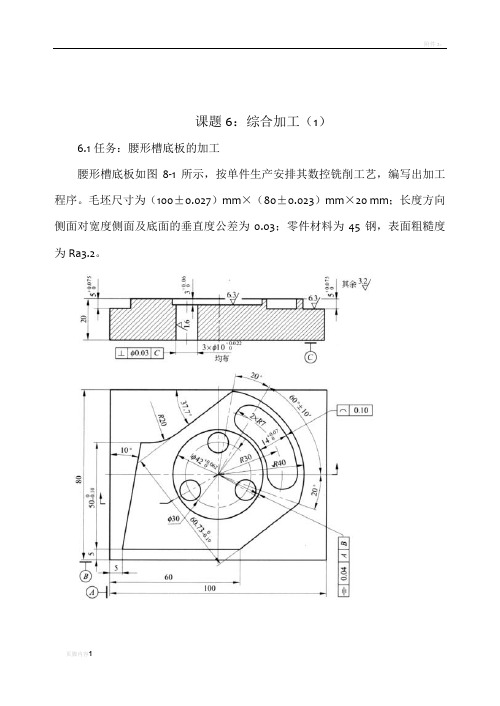
附件2:课题6:数控铣削综合加工实例(1)理论:1.掌握铣削加工的工艺知识;2.掌握综合件的编程思路。
技能:1.能编制综合件的加工程序;2.能熟练使用数控铣床仿真软件;3.能完成综合件仿真加工。
编制综合件的加工程序综合件仿真加工专业课(理实一体)讲授法、引导文教学法、案例教学法、示范法、练习法多媒体、网络或投影仪4/4 0杨丰回顾:铣削单项加工项目1.任务:加工要求、零件图2.相关知识:(1)工艺知识(2)编程知识3.项目实施4.小结课题6:综合加工(1)6.1任务:腰形槽底板的加工腰形槽底板如图8-1所示,按单件生产安排其数控铣削工艺,编写出加工程序。
毛坯尺寸为(100±0.027)mm×(80±0.023)mm×20 mm;长度方向侧面对宽度侧面及底面的垂直度公差为0.03;零件材料为45钢,表面粗糙度为Ra3.2。
6.2 任务决策和实施6.2.1 工艺(1)工艺分析工艺分析该零件包含了外形轮廓、圆形槽、腰形槽和孔的加工,有较高的尺寸精度和垂直度、对称度等形位精度要求。
编程前必须详细分析图纸中各部分的加工方法及走刀路线,选择合理的装夹方案和加工刀具,保证零件的加工精度要求。
外形轮廓中的50和60.73两尺寸的上偏差都为零,可不必将其转变为对称公差,直接通过调整刀补来达到公差要求;3×φ10孔尺寸精度和表面质量要求较高,并对C面有较高的垂直度要求,需要铰削加工,并注意以C面为定位基准;φ42圆形槽有较高的对称度要求,对刀时X、Y方向应采用寻边器碰双边,准确找到工件中心。
加工过程如下:①外轮廓的粗、精铣削,批量生产时,粗精加工刀具要分开,本例采用同一把刀具进行。
粗加工单边留0.2mm余量。
②加工3×φ10孔和垂直进刀工艺孔。
③圆形槽粗、精铣削,采用同一把刀具进行。
④腰形槽粗、精铣削,采用同一把刀具进行。
(2)刀具与工艺参数选择见表8-1、表8-2。
数控铣床典型零件加工实例

模块五数控铣床典型零件加工实例本单位从综合数控技术的实际应用出发,列举了典型数控铣削编程实例,如果但愿掌握这门技术,就应该仔细的理解和消化它,相信有着触类旁通的效果。
学习目标常识目标:●学会对工艺常识、编程常识、操作常识的综合运用能力目标:●能够对适合铣削的典型零件进行工艺阐发、程序编制、实际加工。
一、数控铣床加工实例1——槽类零件毛坯为70㎜×70㎜×18㎜板材,六面已粗加工过,要求数控铣出如图2-179所示的槽,工件材料为45钢。
图2-179 凹槽工件1.按照图样要求、毛坯及前道工序加工情况,确定工艺方案及加工路线1〕以已加工过的底面为定位基准,用通用机用平口虎钳夹紧工件前后两侧面,虎钳固定于铣床工作台上。
2〕工步挨次①铣刀先走两个圆轨迹,再用左刀具半径抵偿加工50㎜×50㎜四角倒圆的正方形。
②每次切深为2㎜,分二次加工完。
2.选择机床设备按照零件图样要求,选用经济型数控铣床即可到达要求。
3.选择刀具现采用φ10㎜的平底立铣刀,定义为T01,并把该刀具的直径输入刀具参数表中。
4.确定切削用量切削用量的具体数值应按照机床性能、相关的手册并结合实际经验确定,详见加工程序。
5.确定工件坐标系和对刀点在XOY平面内确定以工件中心为工件原点,Z标的目的以工件上外表为工件原点,成立工件坐标系,如图2-118所示。
采用手动对刀方法〔操作与前面介绍的数控铣床对刀方法不异〕把点O作为对刀点。
6.编写程序考虑到加工图示的槽,深为4㎜,每次切深为2㎜,分二次加工完。
为编程便利,同时减少指令条数,可采用子程序。
该工件的加工程序如下:O0001;主程序N0010 G90 G00Z2.S800T01M03;N0020X15.Y0M08;N0030G01 Z-2. F80;N0040M98 P0010;调一次子程序,槽深为2㎜N0050G01Z-4.F80;N0060M98 P0010; 再调一次子程序,槽深为4mmN0070G00 Z2.N0080 G00X0Y0Z150. M09;N0090M02主程序结束O0010 子程序N0010G03X15.Y0I-15.J0;N0020G01X20.;N0030G03X20.YO I-20.J0;N0040G41G01X25.Y15.;左刀补铣四角倒圆的正方形N0050G03X15.Y25.I-10.J0;N0060G01X-15.;N0070G03X-25.Y15.I0J-10.;N0080G01Y-15.N0090G03X-15.Y-25.I10.J0;N0100G01X15.;N0110G03X25.Y-15.I0J10.;N0120G01Y0;N0130G40G01X15.Y0; 左刀补打消N0140 M99;子程序结束7.程序的输入〔拜见模块四具体操作步调〕8.试运行〔拜见模块四具体操作步调〕9.对刀〔拜见模块四具体操作步调〕选择“自动方式〞,按“启动〞开始加工。
数控铣削项目六PPT课件
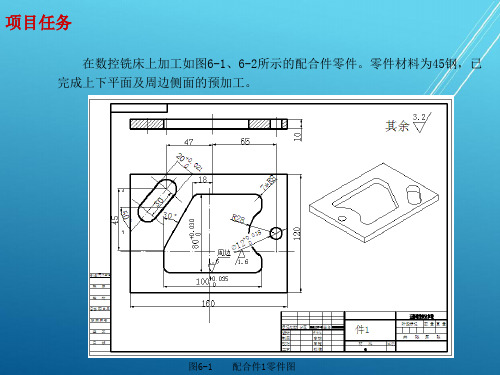
项目实施
配合件2的加工方案为: 1)铣削平面,保证尺寸28.5mm,选用Φ80mm面铣刀。 2)粗加工两个凸台外轮廓,选用Φ16mm三刃立铣刀。 3)铣削边角料,选用Φ16mm三刃立铣刀。 4)钻中间位置孔,选用Φ11.8mm直柄麻花钻。 5)扩中间位置孔,选用Φ35mm锥柄麻花钻。 6)精加工两个凸台外轮廓,并保证8mm和10mm的高度,选用Φ12mm四刃立铣刀。 7)粗镗Φ38.5mm孔,选用Φ37.5mm粗镗刀。 8)精镗Φ38mm孔,选用Φ38mm精镗刀。 9)点孔加工,选用Φ3mm中心钻。 10)钻孔加工,选用Φ11.8mm直柄麻花钻。 11)铰孔加工,选用Φ12mm机用铰刀。 12)孔口R5圆角,选用Φ14mm三刃立铣刀。
(3)加工方法及刀具的选择: 在进行配合件加工时,要合理控制好首件凸、凹结构的尺寸大小,一般 取尺寸偏差的上、下偏差,为加工配合工件尺寸精度和配合精度奠定基 础。根据图样要求首先加工件1,然后加工件2。件2加工完成后,必须 在拆卸之前与件1进行配合,若间隙偏小,可改变刀具半径补偿,将轮 廓进行再加工,直至配合情况良好后方可取下件2。
项目实施
(4)切削用量的选择: 工件材料为45钢,主轴转速选择时,粗加工及去除余量时取较低值,精加 工时选择最大值;粗加工时进给速度选择较大值,精加工进给速度应选择较小 值;轮廓深度有公差要求时分两次切削,留一些精加工余量。 3.数控加工工艺文件 件1、件2数控加工工序卡如表6-2、6-3所示。
表6-2 件1零件数控加工工序卡
Learning Is To Achieve A Certain Goal And Work Hard, Is A Process To Overcome Various Difficulties For A Goal
数控铣床加工实例

数控铣床加工实例——钻孔类零件
工艺分析及处理
(4)刀具和切削用量的选择 影响切削用量的因素很多,工件的材料和硬度、加工
的精度要求、刀具的材料和耐用度、是否使用切削液等都 直接影响到切削用量的大小。在数控程序中,决定用量的 参数是主轴转速S和进给速度F,主轴转速S、进给速度F 值的选择与在普通机床上加工时的值相似,可以通过计算 的方法得到,也可查阅金属切削工艺手册,或根据经验数 据给定。本例S设为1000 r/min 。
数控铣床加工实例——挖槽类零件
工艺分析及处理
(1)零件图的分析
工件毛坯为100 mm× 80 mm×25 mm的长方体零件, 材料为45钢,要加工成型中间的环 形槽。
数控铣床加工实例——挖槽类零件
工艺分析及处理
(2)加工方案及刀具选择 根据零件图分析,要加工的部位是一个环形 槽,中间的凸台作为槽的岛屿,外轮廓转角处的 半径是R4,槽较窄处的宽度是10 mm,所以选用 直径¢6mm的直柄键槽铣刀较合适。
N600 M30 ;
程序结束
数控铣床加工实例——平面轮廓类零件
数控铣床加工实例——平面轮廓类零件
工艺分析及处理
(1)零件图的分析
工件毛坯为¢85mm ×30mm的圆柱 件,材料为硬铝,加工其上部轮廓后形成 如图所示的凸台。加工部分凸台的精度不 高,可以按照图纸的基本尺寸进行编程, 一次铣削完成。
数控铣床加工实例——挖槽类零件
注意:
(1)根据以上特征和要求,对于挖槽的编程和加工要选择合适的刀具 直径,刀具直径太小将影响加工效率,刀具直径太大可能使某些转角处 难以切削,或由于岛屿的存在形成不必要的区域。
(2)由于圆柱形铣刀垂直切削时受力情况不好,因此要选择合适的刀 具类型,一般可选择双刃的键槽铣刀,并注意下刀时的方式,可选择斜 向下刀或螺旋形下刀,以改善下刀切削时的刀具受力情况。
数控铣床典型零件加工实例
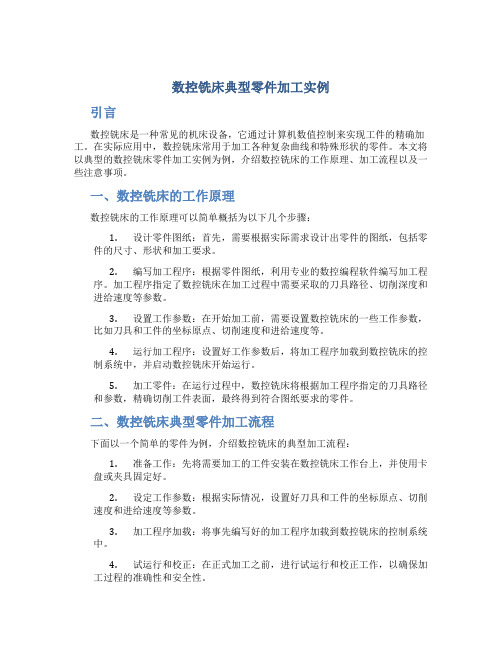
数控铣床典型零件加工实例引言数控铣床是一种常见的机床设备,它通过计算机数值控制来实现工件的精确加工。
在实际应用中,数控铣床常用于加工各种复杂曲线和特殊形状的零件。
本文将以典型的数控铣床零件加工实例为例,介绍数控铣床的工作原理、加工流程以及一些注意事项。
一、数控铣床的工作原理数控铣床的工作原理可以简单概括为以下几个步骤:1.设计零件图纸:首先,需要根据实际需求设计出零件的图纸,包括零件的尺寸、形状和加工要求。
2.编写加工程序:根据零件图纸,利用专业的数控编程软件编写加工程序。
加工程序指定了数控铣床在加工过程中需要采取的刀具路径、切削深度和进给速度等参数。
3.设置工作参数:在开始加工前,需要设置数控铣床的一些工作参数,比如刀具和工件的坐标原点、切削速度和进给速度等。
4.运行加工程序:设置好工作参数后,将加工程序加载到数控铣床的控制系统中,并启动数控铣床开始运行。
5.加工零件:在运行过程中,数控铣床将根据加工程序指定的刀具路径和参数,精确切削工件表面,最终得到符合图纸要求的零件。
二、数控铣床典型零件加工流程下面以一个简单的零件为例,介绍数控铣床的典型加工流程:1.准备工作:先将需要加工的工件安装在数控铣床工作台上,并使用卡盘或夹具固定好。
2.设定工作参数:根据实际情况,设置好刀具和工件的坐标原点、切削速度和进给速度等参数。
3.加工程序加载:将事先编写好的加工程序加载到数控铣床的控制系统中。
4.试运行和校正:在正式加工之前,进行试运行和校正工作,以确保加工过程的准确性和安全性。
5.开始加工:确认一切正常后,启动数控铣床开始加工。
根据加工程序指示,数控铣床将按照设定的刀具路径和参数进行切削工件。
6.完成加工:零件加工完毕后,停止数控铣床的运行,并对加工后的零件进行检查和质量评估。
7.清洁和保养:及时清洁数控铣床,保持设备的良好状态。
对刀具和夹具进行保养和更换,以保证下次使用时的正常运行。
三、数控铣床加工实例注意事项在进行数控铣床零件加工时,需要注意以下几个方面:1.设计合理的刀具路径:在编写加工程序时,应尽量优化刀具路径,减少切削时间和能耗,提高加工效率和质量。
课题6:数控铣削综合加工实例_1.doc
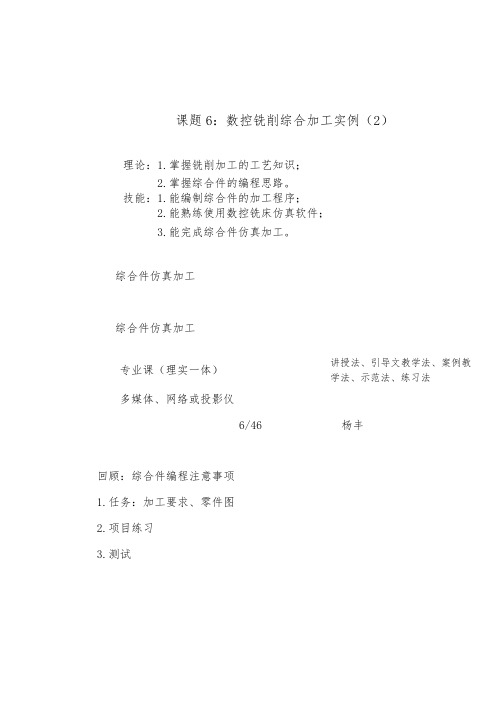
课题6:数控铣削综合加工实例(2)理论:1.掌握铣削加工的工艺知识;2.掌握综合件的编程思路。
技能:1.能编制综合件的加工程序;2.能熟练使用数控铣床仿真软件;3.能完成综合件仿真加工。
综合件仿真加工综合件仿真加工专业课(理实一体)讲授法、引导文教学法、案例教学法、示范法、练习法多媒体、网络或投影仪6/46杨丰回顾:综合件编程注意事项1.任务:加工要求、零件图2.项目练习3.测试课题6:综合加工练习(2)任务:十字槽底板加工加工如图9-11所示十字槽底板,零件毛坯尺寸为76mm×76mm×23 mm;六面已加工过,粗糙度为Ra1.6,零件材料为45钢,数量为1个。
美文欣赏十字槽底板零件图1、走过春的田野,趟过夏的激流,来到秋天就是安静祥和的世界。
秋天,虽没有玫瑰的芳香,却有秋菊的淡雅,没有繁花似锦,却有硕果累累。
秋天,没有夏日的激情,却有浪漫的温情,没有春的奔放,却有收获的喜悦。
清风落叶舞秋韵,枝头硕果醉秋容。
秋天是甘美的酒,秋天是壮丽的诗,秋天是动人的歌。
2、人的一生就是一个储蓄的过程,在奋斗的时候储存了希望;在耕耘的时候储存了一粒种子;在旅行的时候储存了风景;在微笑的时候储存了快乐。
聪明的人善于储蓄,在漫长而短暂的人生旅途中,学会储蓄每一个闪光的瞬间,然后用它们酿成一杯美好的回忆,在四季的变幻与交替之间,散发浓香,珍藏一生!3、春天来了,我要把心灵放回萦绕柔肠的远方。
让心灵长出北归大雁的翅膀,乘着吹动彩云的熏风,捧着湿润江南的霡霂,唱着荡漾晨舟的渔歌,沾着充盈夜窗的芬芳,回到久别的家乡。
我翻开解冻的泥土,挖出埋藏在这里的梦,让她沐浴灿烂的阳光,期待她慢慢长出枝蔓,结下向往已久的真爱的果实。
4、好好享受生活吧,每个人都是幸福的。
人生山一程,水一程,轻握一份懂得,将牵挂折叠,将幸福尽收,带着明媚,温暖前行,只要心是温润的,再遥远的路也会走的安然,回眸处,愿阳光时时明媚,愿生活处处晴好。
数控铣削编程案例

数控铣削编程案例一、铣削四方凸台 1.零件图2.实体图3.程序4.刀具半径补偿后的刀轨路径图(刀具为Φ20立铣刀,D01=10.2)O1201;N10 G90 G80 G40 G69 G21N20 G54 G00 X100 Y100; N30 G00 Z100; N40 M03 S800; N50 G00 Z10;N60 G00 X55 Y0;N70 G01 Z-5 F80; N80 G41 G01 X55 Y20 D01 F150;N90 G03 X35 Y0 R20; N100 G01 X35 Y-20; N110 G02 X20 Y-35 R15; N120 G01 X-20 Y-35; N130 G02 X-35 Y-20 R15; N140 G01 X-35 Y20; N150 G02 X-20 Y35 R15; N160 G01 X20 Y35; N170 G02 X35 Y20 R15;N180 G01 X35 Y0; N190 G03 X55 Y-20 R20; N200 G01 G40 X55 Y0; N210 G00 Z100; N220 Y150; N230 M30;5.仿真加工结果图1.零件图2.实体图如图所示计算A点坐标:AB/OA=SIN600 AB=30.311A 点坐标值为(17.5,30.311) 4.程序5. 刀具半径补偿后的刀轨路径图(刀具为Φ35立铣刀,D01=17.5)6. 仿真加工结果图O1202;N10 G90 G80 G40 G69 G21N20 G54 G00 X100 Y100; N30 G00 Z100;N40 M03 S800;N50 G00 Z10;N60 G00 X0 Y-50.311;N70 G01 Z-5 F80;N80 G41 G01 X20 Y-50.311 D01 F150;N90 G03 X0 Y-30.311 R20; N100 G01 X-17.5 Y-30.311; N110 G01 X-35 Y0 ; N120 G01 X-17.5 Y30.311; N130 G01 X17.5 Y30.311; N140 G01 X35 Y0; N150 G01 X17.5 Y-30.311; N160 G01 X0 Y-30.311; N170 G03 X-20 Y-50.311 R20;N180 G01 G40 X0 Y-50.311; N190 G00 Z100; N200 Y150; N210 M30三、铣削对称轮廓 1.零件图2.实体图3.程序4. 刀具半径补偿后的刀轨路径图O1203; 主程序N10 G90 G80 G40 G69 G21 N20 G54 G00 X100 Y100; N30 G00 Z100; N40 M03 S600; N50 G00 Z10; N60 G00 X-50 Y-60;N70 G01 Z-5 F80;N80 G41 G01 X-30 Y-60 D01 F150;N90 M98 P0301; N100 G90 G01 Z10; N110 G00 G40 X0 Y-60 ; N120 G01 Z-5 F80;N121 G01 X10 Y-60 D01 F150; N130 M98 P0301; N140 G01 G40 X0 Y-60; N150 G90 G00 Z100; N160 Y150;N170 M30; O0301; 子程序 N10 G91 G01 X0 Y80; N20 G02 X20 Y0 R10; N30 G01 X0 Y-45; N40 G01 X-30 Y0 N50 M995.仿真结果四、铣削四方型腔1.零件图2.实体图3.程序4. 刀具半径补偿后的刀轨路径图5.仿真结果O1204N10 G90 G80 G40 G69 G21;N20 G54 G00 X100 Y100;N30 G00 Z100;N40 M03 S600; N50 G00 Z10; N60 G00 X20 Y0; N70 G01 Z-5 F80;N80 G41 G01 X20 Y10 D01 F150;N90 G03 X10 Y0 R10;N100 G01 X10 Y-5;N110 G02 X5 Y-10 R5; N120 G01 X-5 Y-10; N130 G02 X-10 Y-5 R5; N140 G01 X-10 Y5; N150 G02 X-5 Y10 R5; N160 G01 X5 Y10; N170 G02 X10 Y5 R5; N180 G01 X10 Y0; N190 G03 X20 Y-10 R10; N200 G01 G40 X20 Y0;N210 G41 G01 X20 Y-10 D01 F150; N220 G03 X30 Y0 R10; N230 G01 X30 Y20; N240 G03 X20 Y30 R10; N250 G01 X-20 Y30; N260 G03 X-30 Y20 R10; N270 G01 X-30 Y-20; N280 G03 X-20 Y-30 R10; N290 G01 X20 Y-30; N300 G03 X30 Y-20 R10;N310 G01 X30 Y0; N320 G03 X20 Y10 R10; N330 G01 G40 X20 Y0; N340 G00 Z100; N350 Y150; N360 M30;五、铣削图形旋转1.零件图2.实体图3.程序4. 刀具半径补偿后的刀轨路径图(刀具直径Φ15mm )5.仿真结果六、铣削型腔槽板 1.零件图O1205N10 G90 G80 G40 G69 G21; N20 G54 G00 X100 Y100; N30 G00 Z100; N40 M03 S600; N50 G00 Z10; N60 G00 X6 Y0; N70 G01 Z-10 F80;N80 G41 G01 X6 Y-10 D01 F150; N90 G03 X16 Y0 R10; N100 G03 X16 Y0 I-16 J0;N110 G03 X6 Y10 R10; N120 G01 G40 X6 Y0; N130 G01 Z-5; N140M98 P0501 N150 G68 X0 Y0 R90 N160 M98 P0501 N170 G68 X0 YO R180 N180 M98 P0501 N190 G68 X0 Y0 R270 N200 M98 P0501N210 G69 N220 G00 Z100 N230 Y150; N240 M30; O0501 N10 G01 X0 Y0N20 G01 G41 X0 Y-9 D01 N30 G01 X28 Y-9 N40 G03 X28 Y9 R9 N50G01 X0 Y9N60 G01 G40 X0 Y0 N70 M992.实体图3.七、铣削图形镜像与缩放1.零件图2.实体图3.。
- 1、下载文档前请自行甄别文档内容的完整性,平台不提供额外的编辑、内容补充、找答案等附加服务。
- 2、"仅部分预览"的文档,不可在线预览部分如存在完整性等问题,可反馈申请退款(可完整预览的文档不适用该条件!)。
- 3、如文档侵犯您的权益,请联系客服反馈,我们会尽快为您处理(人工客服工作时间:9:00-18:30)。
课题6:综合加工(1)6.1任务:腰形槽底板的加工腰形槽底板如图8-1所示,按单件生产安排其数控铣削工艺,编写出加工程序。
毛坯尺寸为(100±0.027)mm×(80±0.023)mm×20 mm;长度方向侧面对宽度侧面及底面的垂直度公差为0.03;零件材料为45钢,表面粗糙度为Ra3.2。
6.2 任务决策和实施6.2.1 工艺(1)工艺分析工艺分析该零件包含了外形轮廓、圆形槽、腰形槽和孔的加工,有较高的尺寸精度和垂直度、对称度等形位精度要求。
编程前必须详细分析图纸中各部分的加工方法及走刀路线,选择合理的装夹方案和加工刀具,保证零件的加工精度要求。
外形轮廓中的50和60.73两尺寸的上偏差都为零,可不必将其转变为对称公差,直接通过调整刀补来达到公差要求;3×φ10孔尺寸精度和表面质量要求较高,并对C 面有较高的垂直度要求,需要铰削加工,并注意以C面为定位基准;φ42圆形槽有较高的对称度要求,对刀时X、Y方向应采用寻边器碰双边,准确找到工件中心。
加工过程如下:①外轮廓的粗、精铣削,批量生产时,粗精加工刀具要分开,本例采用同一把刀具进行。
粗加工单边留0.2mm余量。
②加工3×φ10孔和垂直进刀工艺孔。
③圆形槽粗、精铣削,采用同一把刀具进行。
④腰形槽粗、精铣削,采用同一把刀具进行。
(2)刀具与工艺参数选择见表8-1、表8-2。
表8-1 数控加工刀具卡表8-2 数控加工工序卡用平口虎钳装夹工件,工件上表面高出钳口8mm左右。
校正固定钳口的平行度以及工件上表面的平行度,确保精度要求。
6.2.2程序编制在工件中心建立工件坐标系,Z轴原点设在工件上表面。
(1)外形轮廓铣削①去除轮廓边角料安装φ20立铣刀(T01)并对刀,去除轮廓边角料程序如下: O0001;N10 G17 G21 G40 G54 G80 G90 G94 ; 程序初始化N20 G00 Z50.0 M07; 刀具定位到安全平面,启动主轴 N30 M03 S400;N40 X-65.0 Y32.0; 去除轮廓边角料 N50 Z-5.0;N60 G01 X-24.0 F80; N70 Y55.0;N80 G00 Z50.0; N90 X40.0 Y55.0; N100 Z-5.0;N110 G01 Y35.0; N120 X52.0; N130 Y-32.0; N140 X40.0; N150 Y-55.0N160 G00 Z50.0 M09; N170 M05;N180 M30; 程序结束② 粗、精加工外形轮廓P0(15,-65) P1(15,-50) P2(0,-35)P3(-45,-35)P4(-36.184,15) P5(-31.444,15) P6(-19.214,19.176) P7(6.944,39.393) P8(37.589,-13.677) P9(10,-35) P10(-15,-50)P11(-15,-65) 刀具由P0点下刀,通过P0 P1直线建立左刀补,沿圆弧P1 P2切向切入,走完轮廓后由圆弧P2 P10切向切出,通过直线P10 P11取消刀补。
粗、精加工采用同一程序,通过设置刀补值控制加工余量和达到尺寸要求。
外形轮廓粗、精加工程序如下(程序中切削参数为粗加工参数):O0002;P 0P 2P 3 P 5 P 6P 9P 11 8-2 外形轮廓各点坐标及切入切出路线N10 G17 G21 G40 G54 G80 G90 G94 ;程序初始化N20 G00 Z50.0 M07;刀具定位到安全平面,启动主轴N30 M03 S500;精加工时设为700r/minN40 G00 X15.0 Y-65.0;达到P0点N50 Z-5.0;下刀N60 G01 G41 Y-50.0 D01 F100;建立刀补,粗加工时刀补设为10.2mm,精加工时刀补设为9.95mm(根据实测尺寸调整);精加工时F设80mm/min N70 G03 X0.0 Y-35.0 R15.0;切向切入N80 G01 X-45.0 Y-35.0;铣削外形轮廓N90 X36.184 Y15.0;N100 X-31.444 ;N110 G03 X-19.214 Y19.176 R20.0;N120 G01 X6.944 Y39.393;N130 G02 X37.589 Y-13.677 R40.0;N140 G01 X10.0 Y-35;N150 X0;N160 G03 X-15.0 Y-50.0 R15;切向切出N170 G01 G40 Y-65.0;取消刀补N180 G00 Z50.0 M09N190 M05;N230 M30;程序结束(2)加工3×φ10孔和垂直进刀工艺孔首先安装中心钻(T02)并对刀,孔加工程序如下:O0003;N10 G17 G21 G40 G54 G80 G90 G94 ;程序初始化N20 G00 Z50.0 M07;刀具定位到安全平面,启动主轴N30 M03 S2000;N40 G99 G81 X12.99 Y-7.5 R5.0 Z-5.0 F80;钻中心孔,深度以钻出锥面为好N50 X-12.99;N60 X0.0 Y15.0;N70 Y0.0;N80 X30.0;N100 G00 Z180.0 M09;刀具抬到手工换刀高度N105 X150 Y150;移到手工换刀位置N110 M05;N120 M00;程序暂停,手工换T03刀,换转速N130 M03 S600;N140 G00 Z50.0 M07;刀具定位到安全平面N150 G99 G83 X12.99 Y-7.5 R5.0 Z-24.0 Q-4.0 F80;钻3×φ10底孔和垂直进刀工艺孔N160 X-12.99;N170 X0.0 Y15.0;N180 G81 Y0.0 R5.0 Z-2.9;N190 X30.0 Z-4.9;N200 G00 Z180.0 M09;刀具抬到手工换刀高度N210 X150 Y150;移到手工换刀位置N220 M05;N230 M00;程序暂停,手工换T04刀,换转速N240 M03 S200;N250 G00 Z50.0 M07;刀具定位到安全平面N260 G99 G85 X12.99 Y-7.5 R5.0 Z-24.0 Q-4.0 F80;铰3×φ10孔N270 X-12.99;N280 G98 X0.0 Y15.0;N290 M05;N300 M30;程序结束(3)圆形槽铣削安装φ16立铣刀(T05)并对刀,圆形槽铣削程序如下:①粗铣圆形槽O0004;N10 G17 G21 G40 G54 G80 G90 G94 ;程序初始化N20 G00 Z50.0 M07;刀具定位到安全平面,启动主轴N30 M03 S500;N40 X0.0 Y0.0;N50 Z10.0;N60 G01 Z-3.0 F40;下刀N70 X5.0 F80;去除圆形槽中材料N80 G03 I-5.0;N90 G01 X12.0;N100 G03 I-12.0;N110 G00 Z50 M09;N120 M05;N130 M30;程序结束②半精、精铣圆形槽边界半精、精加工采用同一程序,通过设置刀补值控制加工余量和达到尺寸要求。
程序如下(程序中切削参数为半精加工参数):O0005;N10 G17 G21 G40 G54 G80 G90 G94 ;程序初始化N20 G00 Z50.0 M07;刀具定位到安全平面,启动主轴N30 M03 S600;精加工时设为750r/minN40 X0.0 Y0.0;N50 Z10.0;N60 G01 Z-3.0 F40;下刀N70 G41 X-15.0 Y-6.0 D05 F80;建立刀补,半精加工时刀补设为8.2mm,精加工时刀补设为7.98mm(根据实测尺寸调整);精加工时F 设60mm/min N80 G03 X0.0 Y-21.0 R15.0;切向切入N90 G03 J21.0; 铣削圆形槽边界 N100 G03 X15.0 Y-6.0 R15.0; 切向切出 N110 G01 G40 X0.0 Y0.0; 取消刀补 N120 G00 Z50 M09; N130 M05;N140 M30; 程序结束(4)铣削腰形槽 ① 粗铣腰形槽安装φ12立铣刀(T06)并对刀,粗铣腰形槽程序如下: O0006;N10 G17 G21 G40 G54 G80 G90 G94 ; 程序初始化N20 G00 Z50.0 M07; 刀具定位到安全平面,启动主轴 N30 M03 S600;N40 X30.0 Y0.0; 到达预钻孔上方 N50 Z10.0;N60 G01 Z-5.0 F40; 下刀N70 G03 X15.0 Y25.981 R30.0 F80; 粗铣腰形槽 N80 G00 Z50 M09; N90 M05;N100 M30; 程序结束 ② 半精、精铣腰形槽A0(30,0) A1(30.5,-6.5) A2(37,0)A3(18.5,32.043) A4(11.5,19.919) A5(23,0) A6(30.5,6.5)半精、精加工采用同一程序,通过设置刀补值控制加工余量和达到尺寸要求。
程序如下(程序中切削参数为半精加工参数):O0007;N10 G17 G21 G40 G54 G80 G90 G94 ; 程序初始化N20 G00 Z50.0 M07; 刀具定位到安全平面,启动主轴 N30 M03 S600; 精加工时设为800r/min N40 X30.0 Y0.0; N50 Z10.0;N60 G01 Z-3.0 F40; 下刀N70 G41 X30.5 Y-6.5 D06 F80; 建立刀补,半精加工时刀补设为8-3 腰形槽各点坐标及切入切出路线A 36.1mm,精加工时刀补设为5.98mm(根据实测尺寸调整);精加工时F 设60mm/minN80 G03 X37.0 Y0.0 R6.5;切向切入N90 G03 X18.5 Y32.043 R37.0;铣削腰形槽边界N100 X11.5 Y19.919 R7.0 ;N110 G02 X23.0 Y0 R23.0;N120 G03 X37.0 R7.0;N130 X30.5 Y6.5 R6.5;N140 G01 G40 X30.0 Y0.0;取消刀补N150 G00 Z50 M09;N160 M05;N170 M30;程序结束注意事项:(1)铣削外形轮廓时,刀具应在工件外面下刀,注意避免刀具快速下刀时与工件发生碰撞;(2)使用立铣刀粗铣圆形槽和腰形槽时,应先在工件上钻工艺孔,避免立铣刀中心垂直切削工件;(3)精铣时刀具应切向切入和切出工件。