自动化毕业设计英文文献翻译
机械制造及自动化毕业设计---外语文献翻译

攀枝花学院本科毕业设计(论文)外文译文院(系):机电工程学院专业:机械设计制造及其自动化姓名:**************学号:ZJD02043外语文献翻译摘自: 《制造工程与技术(机加工)》(英文版)《Manufacturing Engineering and Technology—Machining》机械工业出版社2004年3月第1版页P560—564美s. 卡尔帕基安(Serope kalpakjian)s.r 施密德(Steven R.Schmid) 著原文:20.9 MACHINABILITYThe machinability of a material usually defined in terms of four factors:1、Surface finish and integrity of the machined part;2、Tool life obtained;3、Force and power requirements;4、Chip control.Thus, good machinability good surface finish and integrity, long tool life, and low force And power requirements. As for chip control, long and thin (stringy) cured chips, if not broken up, can severely interfere with the cutting operation by becoming entangled in the cutting zone.Because of the complex nature of cutting operations, it is difficult to establish relationships that quantitatively define the machinability of a material. In manufacturing plants, tool life and surface roughness are generally considered to be the most important factors in machinability. Although not used much any more, approximate machinability ratings are available in the example below.20.9.1 Machinability Of SteelsBecause steels are among the most important engineering materials (as noted in Chapter 5), their machinability has been studied extensively. The machinability of steels has been mainly improved by adding lead and sulfur to obtain so-calledfree-machining steels.Resulfurized and Rephosphorized steels. Sulfur in steels forms manganese sulfide inclusions (second-phase particles), which act as stress raisers in the primaryshear zone. As a result, the chips produced break up easily and are small; this improves machinability. The size, shape, distribution, and concentration of these inclusions significantly influence machinability. Elements such as tellurium and selenium, which are both chemically similar to sulfur, act as inclusion modifiers in resulfurized steels.Phosphorus in steels has two major effects. It strengthens the ferrite, causing increased hardness. Harder steels result in better chip formation and surface finish. Note that soft steels can be difficult to machine, with built-up edge formation and poor surface finish. The second effect is that increased hardness causes the formation of short chips instead of continuous stringy ones, thereby improving machinability.Leaded Steels. A high percentage of lead in steels solidifies at the tip of manganese sulfide inclusions. In non-resulfurized grades of steel, lead takes the form of dispersed fine particles. Lead is insoluble in iron, copper, and aluminum and their alloys. Because of its low shear strength, therefore, lead acts as a solid lubricant (Section 32.11) and is smeared over the tool-chip interface during cutting. This behavior has been verified by the presence of high concentrations of lead on thetool-side face of chips when machining leaded steels.When the temperature is sufficiently high-for instance, at high cutting speeds and feeds (Section 20.6)—the lead melts directly in front of the tool, acting as a liquid lubricant. In addition to this effect, lead lowers the shear stress in the primary shear zone, reducing cutting forces and power consumption. Lead can be used in every grade of steel, such as 10xx, 11xx, 12xx, 41xx, etc. Leaded steels are identified by the letter L between the second and third numerals (for example, 10L45). (Note that in stainless steels, similar use of the letter L means “low carbon,” a condition that improves their corrosion resistance.)However, because lead is a well-known toxin and a pollutant, there are serious environmental concerns about its use in steels (estimated at 4500 tons of lead consumption every year in the production of steels). Consequently, there is a continuing trend toward eliminating the use of lead in steels (lead-free steels). Bismuth and tin are now being investigated as possible substitutes for lead in steels.Calcium-Deoxidized Steels. An important development is calcium-deoxidized steels, in which oxide flakes of calcium silicates (CaSo) are formed. These flakes, in turn, reduce the strength of the secondary shear zone, decreasing tool-chip interfaceand wear. Temperature is correspondingly reduced. Consequently, these steels produce less crater wear, especially at high cutting speeds.Stainless Steels. Austenitic (300 series) steels are generally difficult to machine. Chatter can be s problem, necessitating machine tools with high stiffness. However, ferritic stainless steels (also 300 series) have good machinability. Martensitic (400 series) steels are abrasive, tend to form a built-up edge, and require tool materials with high hot hardness and crater-wear resistance. Precipitation-hardening stainless steels are strong and abrasive, requiring hard and abrasion-resistant tool materials.The Effects of Other Elements in Steels on Machinability. The presence of aluminum and silicon in steels is always harmful because these elements combine with oxygen to form aluminum oxide and silicates, which are hard and abrasive. These compounds increase tool wear and reduce machinability. It is essential to produce and use clean steels.Carbon and manganese have various effects on the machinability of steels, depending on their composition. Plain low-carbon steels (less than 0.15% C) can produce poor surface finish by forming a built-up edge. Cast steels are more abrasive, although their machinability is similar to that of wrought steels. Tool and die steels are very difficult to machine and usually require annealing prior to machining. Machinability of most steels is improved by cold working, which hardens the material and reduces the tendency for built-up edge formation.Other alloying elements, such as nickel, chromium, molybdenum, and vanadium, which improve the properties of steels, generally reduce machinability. The effect of boron is negligible. Gaseous elements such as hydrogen and nitrogen can have particularly detrimental effects on the properties of steel. Oxygen has been shown to have a strong effect on the aspect ratio of the manganese sulfide inclusions; the higher the oxygen content, the lower the aspect ratio and the higher the machinability.In selecting various elements to improve machinability, we should consider the possible detrimental effects of these elements on the properties and strength of the machined part in service. At elevated temperatures, for example, lead causes embrittlement of steels (liquid-metal embrittlement, hot shortness; see Section 1.4.3), although at room temperature it has no effect on mechanical properties.Sulfur can severely reduce the hot workability of steels, because of the formation of iron sulfide, unless sufficient manganese is present to prevent such formation. Atroom temperature, the mechanical properties of resulfurized steels depend on the orientation of the deformed manganese sulfide inclusions (anisotropy). Rephosphorized steels are significantly less ductile, and are produced solely to improve machinability.20.9.2 Machinability of Various Other MetalsAluminum is generally very easy to machine, although the softer grades tend to form a built-up edge, resulting in poor surface finish. High cutting speeds, high rake angles, and high relief angles are recommended. Wrought aluminum alloys with high silicon content and cast aluminum alloys may be abrasive; they require harder tool materials. Dimensional tolerance control may be a problem in machining aluminum, since it has a high thermal coefficient of expansion and a relatively low elastic modulus.Beryllium is similar to cast irons. Because it is more abrasive and toxic, though, it requires machining in a controlled environment.Cast gray irons are generally machinable but are. Free carbides in castings reduce their machinability and cause tool chipping or fracture, necessitating tools with high toughness. Nodular and malleable irons are machinable with hard tool materials.Cobalt-based alloys are abrasive and highly work-hardening. They require sharp, abrasion-resistant tool materials and low feeds and speeds.Wrought copper can be difficult to machine because of built-up edge formation, although cast copper alloys are easy to machine. Brasses are easy to machine, especially with the addition pf lead (leaded free-machining brass). Bronzes are more difficult to machine than brass.Magnesium is very easy to machine, with good surface finish and prolonged tool life. However care should be exercised because of its high rate of oxidation and the danger of fire (the element is pyrophoric).Molybdenum is ductile and work-hardening, so it can produce poor surface finish. Sharp tools are necessary.Nickel-based alloys are work-hardening, abrasive, and strong at high temperatures. Their machinability is similar to that of stainless steels.Tantalum is very work-hardening, ductile, and soft. It produces a poor surfacefinish; tool wear is high.Titanium and its alloys have poor thermal conductivity (indeed, the lowest of all metals), causing significant temperature rise and built-up edge; they can be difficult to machine.Tungsten is brittle, strong, and very abrasive, so its machinability is low,although it greatly improves at elevated temperatures.Zirconium has good machinability. It requires a coolant-type cutting fluid,however, because of the explosion and fire.20.9.3 Machinability of Various MaterialsGraphite is abrasive; it requires hard, abrasion-resistant, sharp tools.Thermoplastics generally have low thermal conductivity, low elastic modulus, and low softening temperature. Consequently, machining them requires tools with positive rake angles (to reduce cutting forces), large relief angles, small depths of cut and feed, relatively high speeds, andproper support of the workpiece. Tools should be sharp.External cooling of the cutting zone may be necessary to keep the chips from becoming “gummy” and sticking to the tools. Cooling can usually be achieved w ith a jet of air, vapor mist, or water-soluble oils. Residual stresses may develop during machining. To relieve these stresses, machined parts can be annealed for a period of time at temperatures ranging from C ︒80 to C ︒160 (F ︒175to F ︒315), and then cooled slowly and uniformly to room temperature.Thermosetting plastics are brittle and sensitive to thermal gradients duringcutting. Their machinability is generally similar to that of thermoplastics.Because of the fibers present, reinforced plastics are very abrasive and aredifficult to machine. Fiber tearing, pulling, and edge delamination are significant problems; they can lead to severe reduction in the load-carrying capacity of the component. Furthermore, machining of these materials requires careful removal of machining debris to avoid contact with and inhaling of the fibers.The machinability of ceramics has improved steadily with the development of nanoceramics (Section 8.2.5) and with the selection of appropriate processing parameters, such as ductile-regime cutting (Section 22.4.2).Metal-matrix and ceramic-matrix composites can be difficult to machine, depending on the properties of the individual components, i.e., reinforcing or whiskers, as well as the matrix material.20.9.4 Thermally Assisted MachiningMetals and alloys that are difficult to machine at room temperature can be machined more easily at elevated temperatures. In thermally assisted machining (hot machining), the source of heat—a torch, induction coil, high-energy beam (such as laser or electron beam), or plasma arc—is forces, (b) increased tool life, (c) use of inexpensive cutting-tool materials, (d) higher material-removal rates, and (e) reduced tendency for vibration and chatter.It may be difficult to heat and maintain a uniform temperature distribution within the workpiece. Also, the original microstructure of the workpiece may be adversely affected by elevated temperatures. Most applications of hot machining are in the turning of high-strength metals and alloys, although experiments are in progress to machine ceramics such as silicon nitride.SUMMARYMachinability is usually defined in terms of surface finish, tool life, force and power requirements, and chip control. Machinability of materials depends not only on their intrinsic properties and microstructure, but also on proper selection and controlof process variables.译文:20.9 可机加工性一种材料的可机加工性通常以四种因素的方式定义:1、分的表面光洁性和表面完整性。
自动化专业毕业论文外文文献翻译

目录Part 1 PID type fuzzy controller and parameters adaptive method (1)Part 2 Application of self adaptation fuzzy-PID control for main steam temperature control system in power station (7)Part 3 Neuro-fuzzy generalized predictive control of boiler steam temperature ..................................................................... (13)Part 4 为Part3译文:锅炉蒸汽温度模糊神经网络的广义预测控制21Part 1 PID type fuzzy controller and Parametersadaptive methodWu zhi QIAO, Masaharu MizumotoAbstract: The authors of this paper try to analyze the dynamic behavior of the product-sum crisp type fuzzy controller, revealing that this type of fuzzy controller behaves approximately like a PD controller that may yield steady-state error for the control system. By relating to the conventional PID control theory, we propose a new fuzzy controller structure, namely PID type fuzzy controller which retains the characteristics similar to the conventional PID controller. In order to improve further the performance of the fuzzy controller, we work out a method to tune the parameters of the PID type fuzzy controller on line, producing a parameter adaptive fuzzy controller. Simulation experiments are made to demonstrate the fine performance of these novel fuzzy controller structures.Keywords: Fuzzy controller; PID control; Adaptive control1. IntroductionAmong various inference methods used in the fuzzy controller found in literatures , the most widely used ones in practice are the Mamdani method proposed by Mamdani and his associates who adopted the Min-max compositional rule of inference based on an interpretation of a control rule as a conjunction of the antecedent and consequent, and the product-sum method proposed by Mizumoto who suggested to introduce the product and arithmetic mean aggregation operators to replace the logical AND (minimum) and OR (maximum) calculations in the Min-max compositional rule of inference.In the algorithm of a fuzzy controller, the fuzzy function calculation is also a complicated and time consuming task. Tagagi and Sugeno proposed a crisp type model in which the consequent parts of the fuzzy control rules are crisp functional representation or crisp real numbers in the simplified case instead of fuzzy sets . With this model of crisp real number output, the fuzzy set of the inference consequence willbe a discrete fuzzy set with a finite number of points, this can greatly simplify the fuzzy function algorithm.Both the Min-max method and the product-sum method are often applied with the crisp output model in a mixed manner. Especially the mixed product-sum crisp model has a fine performance and the simplest algorithm that is very easy to be implemented in hardware system and converted into a fuzzy neural network model. In this paper, we will take account of the product-sum crisp type fuzzy controller.2. PID type fuzzy controller structureAs illustrated in previous sections, the PD function approximately behaves like a parameter time-varying PD controller. Since the mathematical models of most industrial process systems are of type, obviously there would exist an steady-state error if they are controlled by this kind of fuzzy controller. This characteristic has been stated in the brief review of the PID controller in the previous section.If we want to eliminate the steady-state error of the control system, we can imagine to substitute the input (the change rate of error or the derivative of error) of the fuzzy controller with the integration of error. This will result the fuzzy controller behaving like a parameter time-varying PI controller, thus the steady-state error is expelled by the integration action. However, a PI type fuzzy controller will have a slow rise time if the P parameters are chosen small, and have a large overshoot if the P or I parameters are chosen large. So there may be the time when one wants to introduce not only the integration control but the derivative control to the fuzzy control system, because the derivative control can reduce the overshoot of the system's response so as to improve the control performance. Of course this can be realized by designing a fuzzy controller with three inputs, error, the change rate of error and the integration of error. However, these methods will be hard to implement in practice because of the difficulty in constructing fuzzy control rules. Usually fuzzy control rules are constructed by summarizing the manual control experience of an operator who has been controlling the industrial process skillfully and successfully. The operator intuitively regulates the executor to control the process by watching theerror and the change rate of the error between the system's output and the set-point value. It is not the practice for the operator to observe the integration of error. Moreover, adding one input variable will greatly increase the number of control rules, the constructing of fuzzy control rules are even more difficult task and it needs more computation efforts. Hence we may want to design a fuzzy controller that possesses the fine characteristics of the PID controller by using only the error and the change rate of error as its inputs.One way is to have an integrator serially connected to the output of the fuzzy controller as shown in Fig. 1. In Fig. 1,1K and 2K are scaling factors for e and ~ respectively, and fl is the integral constant. In the proceeding text, for convenience, we did not consider the scaling factors. Here in Fig. 2, when we look at the neighborhood of NODE point in the e - ~ plane, it follows from (1) that the control input to the plant can be approximated by(1)Hence the fuzzy controller becomes a parameter time-varying PI controller, itsequivalent proportional control and integral control components are BK2D and ilK1 P respectively. We call this fuzzy controller as the PI type fuzzy controller (PI fc). We can hope that in a PI type fuzzy control system, the steady-state error becomes zero.To verify the property of the PI type fuzzy controller, we carry out some simulation experiments. Before presenting the simulation, we give a description of the simulation model. In the fuzzy control system shown in Fig. 3, the plant model is a second-order and type system with the following transfer function:)1)(1()(21++=s T s T K s G (2) Where K = 16, 1T = 1, and 2T = 0.5. In our simulation experiments, we use thediscrete simulation method, the results would be slightly different from that of a continuous system, the sampling time of the system is set to be 0.1 s. For the fuzzy controller, the fuzzy subsets of e and d are defined as shown in Fig. 4. Their coresThe fuzzy control rules are represented as Table 1. Fig. 5 demonstrates the simulation result of step response of the fuzzy control system with a Pl fc. We can see that the steady-state error of the control system becomes zero, but when the integration factor fl is small, the system's response is slow, and when it is too large, there is a high overshoot and serious oscillation. Therefore, we may want to introduce the derivative control law into the fuzzy controller to overcome the overshoot and instability. We propose a controller structure that simply connects the PD type and the PI type fuzzy controller together in parallel. We have the equivalent structure of that by connecting a PI device with the basic fuzzy controller serially as shown in Fig.6. Where ~ is the weight on PD type fuzzy controller and fi is that on PI type fuzzy controller, the larger a/fi means more emphasis on the derivative control and less emphasis on the integration control, and vice versa. It follows from (7) that the output of the fuzzy controller is(3)3. The parameter adaptive methodThus the fuzzy controller behaves like a time-varying PID controller, its equivalent proportional control, integral control and derivative control components are respectively. We call this new controller structure a PID type fuzzy controller (PID fc). Figs. 7 and 8 are the simulation results of the system's step response of such control system. The influence of ~ and fl to the system performance is illustrated. When ~ > 0 and/3 = 0, meaning that the fuzzy controller behaves like PD fc, there exist a steady-state error. When ~ = 0 and fl > 0, meaning that the fuzzy controller behaves like a PI fc, the steady-state error of the system is eliminated but there is a large overshoot and serious oscillation.When ~ > 0 and 13 > 0 the fuzzy controller becomes a PID fc, the overshoot is substantially reduced. It is possible to get a comparatively good performance by carefully choosing the value of αandβ.4. ConclusionsWe have studied the input-output behavior of the product-sum crisp type fuzzy controller, revealing that this type of fuzzy controller behaves approximately like a parameter time-varying PD controller. Therefore, the analysis and designing of a fuzzy control system can take advantage of the conventional PID control theory. According to the coventional PID control theory, we have been able to propose some improvement methods for the crisp type fuzzy controller.It has been illustrated that the PD type fuzzy controller yields a steady-state error for the type system, the PI type fuzzy controller can eliminate the steady-state error. We proposed a controller structure, that combines the features of both PD type and PI type fuzzy controller, obtaining a PID type fuzzy controller which allows the control system to have a fast rise and a small overshoot as well as a short settling time.To improve further the performance of the proposed PID type fuzzy controller, the authors designed a parameter adaptive fuzzy controller. The PID type fuzzy controller can be decomposed into the equivalent proportional control, integral control and the derivative control components. The proposed parameter adaptive fuzzy controller decreases the equivalent integral control component of the fuzzy controller gradually with the system response process time, so as to increase the damping of the system when the system is about to settle down, meanwhile keeps the proportional control component unchanged so as to guarantee quick reaction against the system's error. With the parameter adaptive fuzzy controller, the oscillation of the system is strongly restrained and the settling time is shortened considerably.We have presented the simulation results to demonstrate the fine performance of the proposed PID type fuzzy controller and the parameter adaptive fuzzy controller structure.Part 2 Application of self adaptation fuzzy-PID control for main steam temperature control system inpower stationZHI-BIN LIAbstract: In light of the large delay, strong inertia, and uncertainty characteristics of main steam temperature process, a self adaptation fuzzy-PID serial control system is presented, which not only contains the anti-disturbance performance of serial control, but also combines the good dynamic performance of fuzzy control. The simulation results show that this control system has more quickly response, better precision and stronger anti-disturbance ability.Keywords:Main steam temperature;Self adaptation;Fuzzy control;Serial control1. IntroductionThe boiler superheaters of modem thermal power station run under the condition of high temperature and high pressure, and the superheater’s temperature is highest in the steam channels.so it has important effect to the running of the whole thermal power station.If the temperature is too high, it will be probably burnt out. If the temperature is too low ,the efficiency will be reduced So the main steam temperature mast be strictly controlled near the given value.Fig l shows the boiler main steam temperature system structure.Fig.1 boiler main steam temperature systemIt can be concluded from Fig l that a good main steam temperature controlsystem not only has adequately quickly response to flue disturbance and load fluctuation, but also has strong control ability to desuperheating water disturbance. The general control scheme is serial PID control or double loop control system with derivative. But when the work condition and external disturbance change large, the performance will become instable. This paper presents a self adaptation fuzzy-PID serial control system. which not only contains the anti-disturbance performance of serial control, but also combines the good dynamic character and quickly response of fuzzy control .1. Design of Control SystemThe general regulation adopts serial PID control system with load feed forward .which assures that the main steam temperature is near the given value 540℃in most condition .If parameter of PID control changeless and the work condition and external disturbance change large, the performance will become in stable .The fuzzy control is fit for controlling non-linear and uncertain process. The general fuzzy controller takes error E and error change ratio EC as input variables .actually it is a non-linear PD controller, so it has the good dynamic performance .But the steady error is still in existence. In linear system theory, integral can eliminate the steady error. So if fuzzy control is combined with PI control, not only contains the anti-disturbance performance of serial control, but also has the good dynamic performance and quickly response.In order to improve fuzzy control self adaptation ability, Prof .Long Sheng-Zhao and Wang Pei-zhuang take the located in bringing forward a new idea which can modify the control regulation online .This regulation is:]1,0[,)1(∈-+=αααEC E UThis control regulation depends on only one parameter α.Once αis fixed .the weight of E and EC will be fixed and the self adaptation ability will be very small .It was improved by Prof. Li Dong-hui and the new regulation is as follow;]1,0[,,,3,)1(2,)1(1,)1(0,)1({321033221100∈±=-+±=-+±=-+=-+=ααααααααααααE EC E E EC E E EC E E EC E UBecause it is very difficult to find a self of optimum parameter, a new method is presented by Prof .Zhou Xian-Lan, the regulation is as follow:)0(),ex p(12>--=k ke αBut this algorithm still can not eliminate the steady error .This paper combines this algorithm with PI control ,the performance is improved .2. Simulation of Control System3.1 Dynamic character of controlled objectPapers should be limited to 6 pages Papers longer than 6 pages will be subject to extra fees based on their length .Fig .2 main steam temperature control system structureFig 2 shows the main steam temperature control system structure ,)(),(21s W s W δδare main controller and auxiliary controller,)(),(21s W s W o o are characters of the leading and inertia sections,)(),(21s W s W H H are measure unit.3.2 Simulation of the general serial PID control systemThe simulation of the general serial PID control system is operated by MATLAB, the simulation modal is as Fig.3.Setp1 and Setp2 are the given value disturbance and superheating water disturb & rice .PID Controller1 and PID Controller2 are main controller and auxiliary controller .The parameter value which comes from references is as follow :667.37,074.0,33.31)(25)(111111122===++===D I p D I p p k k k s k sk k s W k s W δδFig.3. the general PID control system simulation modal3.3 Simulation of self adaptation fuzzy-PID control system SpacingThe simulation modal is as Fig 4.Auxiliary controller is:25)(22==p k s W δ.Main controller is Fuzzy-PI structure, and the PI controller is:074.0,33.31)(11111==+=I p I p k k s k k s W δFuzzy controller is realized by S-function, and the code is as fig.5.Fig.4. the fuzzy PID control system simulation modalFig 5 the S-function code of fuzzy control3.4 Comparison of the simulationGiven the same given value disturbance and the superheating water disturbance,we compare the response of fuzzy-PID control system with PID serial control system. The simulation results are as fig.6-7.From Fig6-7,we can conclude that the self adaptation fuzzy-PID control system has the more quickly response, smaller excess and stronger anti-disturbance.4. Conclusion(1)Because it combines the advantage of PID controller and fuzzy controller, theself adaptation fuzzy-PID control system has better performance than the general PID serial control system.(2)The parameter can self adjust according to the error E value. so this kind of controller can harmonize quickly response with system stability.Part 3 Neuro-fuzzy generalized predictive controlof boiler steam temperatureXiangjie LIU, Jizhen LIU, Ping GUANAbstract: Power plants are nonlinear and uncertain complex systems. Reliable control of superheated steam temperature is necessary to ensure high efficiency and high load-following capability in the operation of modern power plant. A nonlinear generalized predictive controller based on neuro-fuzzy network (NFGPC) is proposed in this paper. The proposed nonlinear controller is applied to control the superheated steam temperature of a 200MW power plant. From the experiments on the plant and the simulation of the plant, much better performance than the traditional controller is obtained.Keywords: Neuro-fuzzy networks; Generalized predictive control; Superheated steam temperature1. IntroductionContinuous process in power plant and power station are complex systems characterized by nonlinearity, uncertainty and load disturbance. The superheater is an important part of the steam generation process in the boiler-turbine system, where steam is superheated before entering the turbine that drives the generator. Controlling superheated steam temperature is not only technically challenging, but also economically important.From Fig.1,the steam generated from the boiler drum passes through the low-temperature superheater before it enters the radiant-type platen superheater. Water is sprayed onto the steam to control the superheated steam temperature in both the low and high temperature superheaters. Proper control of the superheated steam temperature is extremely important to ensure the overall efficiency and safety of the power plant. It is undesirable that the steam temperature is too high, as it can damage the superheater and the high pressure turbine, or too low, as it will lower the efficiency of the power plant. It is also important to reduce the temperaturefluctuations inside the superheater, as it helps to minimize mechanical stress that causes micro-cracks in the unit, in order to prolong the life of the unit and to reduce maintenance costs. As the GPC is derived by minimizing these fluctuations, it is amongst the controllers that are most suitable for achieving this goal.The multivariable multi-step adaptive regulator has been applied to control the superheated steam temperature in a 150 t/h boiler, and generalized predictive control was proposed to control the steam temperature. A nonlinear long-range predictive controller based on neural networks is developed into control the main steam temperature and pressure, and the reheated steam temperature at several operating levels. The control of the main steam pressure and temperature based on a nonlinear model that consists of nonlinear static constants and linear dynamics is presented in that.Fig.1 The boiler and superheater steam generation process Fuzzy logic is capable of incorporating human experiences via the fuzzy rules. Nevertheless, the design of fuzzy logic controllers is somehow time consuming, as the fuzzy rules are often obtained by trials and errors. In contrast, neural networks not only have the ability to approximate non-linear functions with arbitrary accuracy, they can also be trained from experimental data. The neuro-fuzzy networks developed recently have the advantages of model transparency of fuzzy logic and learning capability of neural networks. The NFN is have been used to develop self-tuning control, and is therefore a useful tool for developing nonlinear predictive control. Since NFN is can be considered as a network that consists of several local re-gions, each of which contains a local linear model, nonlinear predictive control based onNFN can be devised with the network incorporating all the local generalized predictive controllers (GPC) designed using the respective local linear models. Following this approach, the nonlinear generalized predictive controllers based on the NFN, or simply, the neuro-fuzzy generalized predictive controllers (NFG-PCs)are derived here. The proposed controller is then applied to control the superheated steam temperature of the 200MW power unit. Experimental data obtained from the plant are used to train the NFN model, and from which local GPC that form part of the NFGPC is then designed. The proposed controller is tested first on the simulation of the process, before applying it to control the power plant.2. Neuro-fuzzy network modellingConsider the following general single-input single-output nonlinear dynamic system:),1(),...,(),(),...,1([)(''+-----=uy n d t u d t u n t y t y f t y ∆+--/)()](),...,1('t e n t e t e e (1)where f[.]is a smooth nonlinear function such that a Taylor series expansion exists, e(t)is a zero mean white noise and Δis the differencing operator,''',,e u y n n n and d are respectively the known orders and time delay of the system. Let the local linear model of the nonlinear system (1) at the operating point )(t o be given by the following Controlled Auto-Regressive Integrated Moving Average (CARIMA) model:)()()()()()(111t e z C t u z B z t y z A d ----+∆= (2) Where )()(),()(1111----∆=z andC z B z A z A are polynomials in 1-z , the backward shift operator. Note that the coefficients of these polynomials are a function of the operating point )(t o .The nonlinear system (1) is partitioned into several operating regions, such that each region can be approximated by a local linear model. Since NFN is a class of associative memory networks with knowledge stored locally, they can be applied to model this class of nonlinear systems. A schematic diagram of the NFN is shown in Fig.2.B-spline functions are used as the membership functions in theNFN for the following reasons. First, B-spline functions can be readily specified by the order of the basis function and the number of inner knots. Second, they are defined on a bounded support, and the output of the basis function is always positive, i.e.,],[,0)(j k j j k x x λλμ-∉=and ],[,0)(j k j j k x x λλμ-∈>.Third, the basis functions form a partition of unity, i.e.,.][,1)(min,∑∈≡j mam j k x x x x μ(3)And fourth, the output of the basis functions can be obtained by a recurrence equation.Fig. 2 neuro-fuzzy network The membership functions of the fuzzy variables derived from the fuzzy rules can be obtained by the tensor product of the univariate basis functions. As an example, consider the NFN shown in Fig.2, which consists of the following fuzzy rules: IF operating condition i (1x is positive small, ... , and n x is negative large),THEN the output is given by the local CARIMA model i:...)()(ˆ...)1(ˆ)(ˆ01+-∆+-++-=d t u b n t y a t y a t yi i a i in i i i a )(...)()(c i in i b i in n t e c t e n d t u b c b -+++--∆+ (4)or )()()()()(ˆ)(111t e z C t u z B z t yz A i i i i d i i ----+∆= (5) Where )()(),(111---z andC z B z A i i i are polynomials in the backward shift operator 1-z , and d is the dead time of the plant,)(t u i is the control, and )(t e i is a zero mean independent random variable with a variance of 2δ. The multivariate basis function )(k i x a is obtained by the tensor products of the univariate basis functions,p i x A a nk k i k i ,...,2,1,)(1==∏=μ (6)where n is the dimension of the input vector x , and p , the total number of weights in the NFN, is given by,∏=+=nk i i k R p 1)( (7)Where i k and i R are the order of the basis function and the number of inner knots respectively. The properties of the univariate B-spline basis functions described previously also apply to the multivariate basis function, which is defined on the hyper-rectangles. The output of the NFN is,∑∑∑=====p i i i p i ip i i i a y aa yy 111ˆˆˆ (8) 3. Neuro-fuzzy modelling and predictive control of superheatedsteam temperatureLet θbe the superheated steam temperature, and θμ, the flow of spray water to the high temperature superheater. The response of θcan be approximated by a second order model:The linear models, however, only a local model for the selected operating point. Since load is the unique antecedent variable, it is used to select the division between the local regions in the NFN. Based on this approach, the load is divided into five regions as shown in Fig.3,using also the experience of the operators, who regard a load of 200MW as high,180MW as medium high,160MW as medium,140MW as medium low and 120MW as low. For a sampling interval of 30s , the estimated linear local models )(1-z A used in the NFN are shown in Table 1.Fig. 3 Membership function for local modelsTable 1 Local CARIMA models in neuro-fuzzy modelCascade control scheme is widely used to control the superheated steam temperature. Feed forward control, with the steam flow and the gas temperature as inputs, can be applied to provide a faster response to large variations in these two variables. In practice, the feed forward paths are activated only when there are significant changes in these variables. The control scheme also prevents the faster dynamics of the plant, i.e., the spray water valve and the water/steam mixing, from affecting the slower dynamics of the plant, i.e., the high temperature superheater. With the global nonlinear NFN model in Table 1, the proposed NFGPC scheme is shown in Fig.4.Fig. 4 NFGPC control of superheated steam temperature with feed-for-ward control.As a further illustration, the power plant is simulated using the NFN model given in Table 1,and is controlled respectively by the NFGPC, the conventional linear GPC controller, and the cascaded PI controller while the load changes from 160MW to 200MW.The conventional linear GPC controller is the local controller designed for the“medium”operating region. The results are shown in Fig.5,showing that, as expected, the best performance is obtained from the NFGPC as it is designed based on a more accurate process model. This is followed by the conventional linear GPC controller. The performance of the conventional cascade PI controller is the worst, indicating that it is unable to control satisfactory the superheated steam temperature under large load changes. This may be the reason for controlling the power plant manually when there are large load changes.Fig.5 comparison of the NFGPC, conventional linear GPC, and cascade PI controller.4. ConclusionsThe modeling and control of a 200 MW power plant using the neuro-fuzzy approach is presented in this paper. The NFN consists of five local CARIMA models.The out-put of the network is the interpolation of the local models using memberships given by the B-spline basis functions. The proposed NFGPC is similarly constructed, which is designed from the CARIMA models in the NFN. The NFGPC is most suitable for processes with smooth nonlinearity, such that its full operating range can be partitioned into several local linear operating regions. The proposed NFGPC therefore provides a useful alternative for controlling this class of nonlinear power plants, which are formerly difficult to be controlled using traditional methods.Part 4 为Part3译文:锅炉蒸汽温度模糊神经网络的广义预测控制Xiangjie LIU, Jizhen LIU, Ping GUAN摘要:发电厂是非线性和不确定性的复杂系统。
电气自动化专业毕业设计英文翻译

电气自动化专业毕业设计英文翻译1 Computer structure and functionThis section introduces the internal architecture of a computer and describes how instructions are stored and interpreted and explains how the instruction execution cycle is broken down into its various components.At the most basic level, a computer simply executes binary-coded results. For a general-purpose programmable computer, four necessary elements are the memory, central processing unit (CPU, or simply processor), an external processor bus, and an input/output system as indicated in Fig.3-1 A-1.Fig. 3-1A-1 Basic elements of a computerThe memory stores instructions and data.The CPU reads and interprets the instructions, reads the data required by each instruction, executes the action required by the instruction, and stores the results back in memory. One of the actions that is required of the CPU is to read data from or write data to an external device. This is carried out using the input/output system.The external processor bus is a set of electric conductors that carries data, address and control information between the other computer elements.1-1 The memoryThe memory of a computer consists of a set of sequentially numbered locations. Each location is a register in which binary information can be stored. The “number”of a location is called its address. The lowest address is 0. The manufacturer defines a word length for the processor that is an integral number of locations long. In each word the bits can represent either data or instructions. For the Intel 8086/87 and Motorola MC6800 microprocessors, a word is 16 bits long, but each memory locationhas only 8 bits and thus two 8-bit locations must be accessed to obtain each data word. In order to use the contents of memory, the processor must fetch the contents of the right location. To carry out a fetch, the processor places (enables) the binary-coded address of the desired location onto the address lines of the external processor bus. The memory then allows the contents of the addressed memory location to be read by the processor. The process of fetching the contents of a memory location does not alter the contents of that location.Instructions in memory Instructions stored in memory are fetched by the CPU and unless program branches occur, they are executed in the sequence they appear in memory. An instruction written as a binary pattern is called a machine-language instruction. One way to achieve meaningful patterns is to divide up the bits into fields as indicated in Fig. 3-1A-2, with each field containing a code for a different type of information.0001 0101 1000 XXXX 0100 0001 1000 XXXX 0011 XXXX XXXX 0100 Fields Opcode Immediate code Operand data Branch addressSet ‘5’ in location 8 Subtract ‘1’ f rom location 8 If zero, bran ch to location 416-bit instruction words... ... XXXX : not u sed (or “don ’t care”)Fig. 3-1A-2 Arrangement of program and data in memoryEach instruction in our simple computer can be divided up into four fields of 4 bits each. Each instruction can contain operation code (or opcode, each instruction has a unique opcode), operand address, immediate operands, branch address.In a real instruction set there are many more instructions. There is also a much large number of memory locations in which to store instructions and data. In order to increase the number of memory locations, the address fields and hence theinstructions must be longer than 16 bits if we use the same approach. There are a number of ways to increase the addressing range of the microprocessor without increasing the instruction length: variable instruction field, multiword instructions, multiple addressing modes, variable instruction length. We will not discuss them in detail.Data in memory data is information that is represented in memory as a code. For efficient use of the memory space and processing time, most computers provide the capability of manipulating data of different lengths and representations in memory. The various different representations recognized by the processor are called its data types. The data types normally used are: bit, binary-coded decimal digit (4-bit nibble, BCD), byte (8 bits), word (2 bytes), double word (4 bytes).Some processors provide instructions that manipulate other data types such as single-precision floating-point data types (32bits) and double-precision floating-point data types (64 bits). There is another type of data—character data. It is also usually represented in 8 bits. Each computer terminal key and key combination (such as shift and control functions) on a standard terminal keyboard has a 7-bits code defined by the American Standard Code for Information Interchange (ASCII).Type of memory In the applications of digital control system, we also concerned with the characteristics of different memory techniques. For primary memory, we need it to be stored information temporarily and to be written and got information from successive or from widely different locations. This type memory is called random-access memory (RAM). In some case we do not want the information in memory to be lost. So we are willing to use special techniques to write into memory. If writing is accomplished only once by physically changing connections, the memory is called a read-only memory (ROM). If the interconnection pattern can be programmed to be set, the memory is called a programmable read-only memory (PROM). If rewriting can be accomplished when it is necessary, we have an erasable programmable read-only memory (EPROM). An electronically erasable PROM is abbreviated EEPROM.1-2 The CPUThe CPU’s job is to fetch instructions from memory and execute these instructions. The structure of the CPU is shown in Fig. 3-1A-3. It has four main components: an arithmetic and logical unit (ALU), a set of registers, an internal processor bus and controller.Fig.3-1A-3 Central processing unit (CPU)These and other components of the CPU and their participation in the instruction cycle are described in the following sections.Arithmetic and Logical Unit (ALU) The ALU provides a wide arithmetic operations, including add, subtract, multiply, and divide. It can also perform Boolean logic operations such as AND, OR, and COMPLEMENT on binary data. Other operations, such as word compares, are also available. The majority of computer tasks involve the ALU, but a great amount of data movement is required in order to make use of the ALU instructions.Registers A set of registers inside the CPU in used to store information.Instruction register When an instruction is fetched, it is copied into the instruction register, where it is decoded. Decoding means that the operation code is examined and used to determine the steps of the execution sequence.Programmer’s model of the CPU The collection of registers that can be examined or modified by a programmer is called the programmer’s model of the CPU.The only registers that can be manipulated by the instruction set, or are visibly affected by hardware inputs or the results of operations upon data, are the registers represented in the model.Flag register The execution sequence is determined not only by the instruction but also by the results of the previous instructions. For example, if an addition is carried out in the ALU, data on the result of the addition (whether the result is positive, negative, or zero, for example) is stored in what is known as a flag register, status register, or condition register. If the next instruction is a conditional branch instruction, the flag word is tested in that instruction to determine if a branch if a branch is required.Program counter (instruction pointer)The address of the next instruction is located in a register called the program counter.Data registers When an instruction uses the registers to store data, the reference to the register in the instruction is called register addressing. The reasons of making use of the internal registers to store data are that they can make the instructions shorter and make execution faster.Address registers The internal registers can also be used for the storage of address of data in memory data. In such a case, the instruction word contains a register number (i.e. a register address). In the register is contained the address of memory data to be used in the instruction. This form of addressing is called register indirect addressing. The contents of the register are said to point to the data in memory.Internal Processor Bus The internal processor bus moves data between internal register. A bus is a set of closely grouped electric conductors that transfers data, address, and control information between functional blocks of the CPU. Data from a source register can be passed to a destination register when both are enabled onto (connected to) the bus.Controller The controller provides the proper sequence of control signals for each instruction in a program cycle to be fetched from memory. A total program cycle comprises many instruction cycle, each instruction cycle can be divided up into itscomponent machine cycles and each machine cycle comprises a number of clock cycle.In order to fetch an instruction, for example illustrated in Fig.3-1A-4, the address in the program counter is placed on the address lines of the external bus (AB) at the onset of clock cycle C1. Simultaneously, using a code on the control lines of the bus (CB), the CPU informs all devices attached to the bus that an “opcode” fetch machine cycle is being executed by the CPU. The memory allows the memory address to select the memory location containing the instruction. At C2 the controller places a “read”command onto the control bus which allows the memory data to be placed onto the data bus. The controller then gates the data into the instruction register and removes the read command from the control bus in C3. At C4, the controller removes the address from the address bus and begins to decode the operation-code portion of the instruction to see what steps are required for execution. The decoding operation may take several more clock cycle at the end of which the “opcode fetch” machine cycle.Fig. 3-1A-4 A timing diagram for "operation-code fetch "External attention requests It is often necessary to stop the normal instruction processing sequence. One type of external attention request is the reset request. In thecase of an unrecoverable error, a computer system may be required to reset itself .This would have the effect of initializing all important registers in the system and starting instruction execution from a standard memory location-usually location 0.An input that is more commonly activated during the normal course of events is the interrupt request. An interrupt request signal from an external device can cause the CPU to immediately execute a service subroutine which carries out the necessary actions. After completing the service subroutine, the processor will continue the task from which it was originally interrupted.The third type of input is the bus request, or direct memory access(DMA) request. It is possible to have a terminal interface that stores up all the characters in a line of text until it receives a "carriage return." Then the interface requests the use of the system bus, at which time the complete line of data is transferred to memory as fast as possible. In this way the processor simply becomes inactive until the transfer is completed.1-3 BusesThe bus is the most important communication system in a computer system. Under control of the CPU, a data source device and a data destination device are "enabled" onto(equivalent to being connected to) the bus wires for a short transmission.External processor bus The internal processor bus described in Sec. is connected to the external processor bus by a set of bus buffers located on the microprocessor integrated circuit.System bus The microcomputer board can communicate with other boards by connecting its bus to an external system bus through a connector.1-4Computer Input and OutputA set of registers external to the CPU is associated with what is known as the input/output (I/O) system. The I/O system is connected to the external processor bus using control, address, and data buses through an I/O registers in an interface. There are basically two ways that are used to address I/O register.In the first method, called I/O-mapped input/output, the operation code itself hasspecial I/O instructions that address a numbered register in the interface called an I/O port.The second method of addressing I/O registers gives the I/O ports addresses that lie within the memory address range of the CPU. This is called memory-mapped I/O. Of course there must not be any memory locations at the same address as I/O locations.One of the benefits of the memory-mapped approach is that the full range of memory addressing modes is available to the addressing of I/O registers.2Fundamentals of Computer and Networks2-1 Organization of Computer SystemA computer is a fast and accurate symbol manipulating system that is organized to accept, store, and process data and produce output results under the direction of a stored program of instructions. This section explains why a computer is a system and how a computer system is organized. Key elements in a computer system include input, processing, and output devices. Let's examine each component of the system in more detail.Input Devices Computer system use many devices for input purpose. Some INPUT DEVICES allow direct human/machine communication, while some first require data to be recorded on an input medium such as a magnetizable material. Devices that read data magnetically recorded on specially coated plastic tapes or flexible or floppy plastic disks are popular. The keyboard of a workstation connected directly to (or ONLINE to) a computer is an example of a direct input device. Additional direct input devices include the mouse, input pen, touch screen, and microphone. Regardless of the type of device used, all are components for interpretation and communication between people and computer systems.Central Processing Unit The heart of any computer system is the central processing unit (CPU). There are three main sections found in the CPU of a typical personal computer system: the primary storage section, the arithmetic-logic section,and the control section. But these three sections aren't unique to personal computers. They are found in CPUs of all sizes.Output Device Like input units, output device are instruments of interpretation and communication between humans and computer system of all size. These device take output results from the CPU in machine-coded form and convert them into a form that can be used (a) by people (e.g. a printed and /or displayed report) or (b) as machine input in another processing cycle.In personal computer systems, display screen and desktop printers are popular output devices. Larger and faster printers, many on-line workstations, and magnetic tape drives commonly found in large systems.The input/output and secondary storage units are sometimes called peripheral devices (or just peripherals). This terminology refers to the fact that although these devices are not a part of the CPU, they are often located near it. Besides, a computer system also includes buses, ROM(read only memory), RAM(random access memory), parallel port and serial port, hard disk, floppies and CD(compact disk)drive, and so on.2-2 Operating SystemOperating systems have developed over the past thirty years for two main purposes. First, they provide a convenient environment for the development and execution of programs. Second, operating systems attempt to schedule computational activities to ensure good performance of the computing system.The operating system must ensure correct operation of the computer system. To prevent user programs form interfering with the proper operation of the system, the hardware was modified to create two modes: user mode and monitor mode. Various instructions (such as I/O instructions and halt instructions) are privileged and can only be executed in monitor mode. The memory in which the monitor resides must also be protected from modification by the user. A timer prevents infinite loops. Once these changes (dual mode, privileged instructions, memory protection, timer interrupt) have been made to the basic computer architecture, it is possible to write a correct operating system.As we have stated, operating systems are normally unique to their manufacturers and the hardware in which they are run. Generally, when a new computer system is installed, operational software suitable to that hardware is purchased. Users want reliable operational software that can effectively support their processing activities.Though operational software varies between manufacturers, it has similar characteristics. Modern hardware, because of its sophistication, requires that operating systems meet certain specific standards. For example, considering the present state of the field, an operating system must support some form of on-line processing. Functions normally associated with operational software are:1)Job management;2)Resource management;3)Control of I/O operations4)Error recovery;5)Memory management.2-3 NetworksCommunication between distributed communities of computers is required for many reasons. At a national level, for example, computers located in different parts of the country use public communication services to exchange electronic messages (mail) and to transfer files of information from one computer to another. Similarly, at a local level within, say, a single building, distributed communities of computer-based workstations use local communication networks to access expensive shared resources—for example, printers and disks tapes and copiers, etc.—that are also managed by computers. Clearly, as the range of computer-based products and associated public and local communication networks proliferate, computer-to-computer communication will expand rapidly and ultimately dominate the field of distributed systems.Although the physical separation of the communicating computers may vary considerably from one type of application to another, or, at the heart of any computer communication network is the data communication facility which, may be a PSDN, aprivate LAN or perhaps a number of such networks interconnected together. However, irrespective of the type of data communication facility, an amount of hardware and software is required within each attached computer to handle the appropriate network-dependent protocols. Typically, these are concerned with the establishment of a communication channel access the network and with the control of the flow of messages across this channel. The provision of such facilities is only part of the network requirements, however, since in many applications the communicating computers may be of different forms of data representation interface between user (application) programs, normally referred to as application processes or APs, and the underlying communication services may be different. For example, one computer may be a small single-user computer, while another may be a large multi-user system.3 Stepper motorStepper motor is the electric pulse signals into angular displacement or linear displacement of the open-loop stepper motor control element pieces. In the case of non-overloaded, the motor speed, stop position depends only on the pulse frequency and pulse number, regardless of load changes, when the driver receives a step pulse signal, it will drive a stepper motor to Set the direction of rotation of a fixed angle, called the "step angle", which the angle of rotation is fixed step by step operation. Number of pulses can be controlled by controlling the angular displacement, so as to achieve accurate positioning purposes; the same time by controlling the pulse frequency to control the motor rotation speed and acceleration, to achieve speed control purposes.3-1 WorkInduction motor is a stepper motor, does it work is the use of electronic circuits, the DC power supply into a time-sharing, multi-phase timing control current, this current stepper motor power supply, the stepper motor to work properly , The drive is sharing power supply for the stepper motor, the polyphase timing controller.Although the stepper motor has been widely used, but the stepper motor does notlike a normal DC motor, AC motor in the conventional use. It must be double-ring pulse signal; power driver circuit composed of the control system can be used. Therefore, it is not easy with a good stepping motor, which involves mechanical, electrical, electronics and computers, and much other specialized knowledge.As the stepper motor actuators, electromechanical integration, one of the key products, widely used in a variety of automatic control systems. With the development of microelectronics and computer technology, increasing demand for stepper motor has applications in all areas of the national economy.3-2 CategoriesNow more commonly used include the reaction of step motor stepper motor (VR), permanent magnet stepper motor (PM), hybrid stepper motors (HB) and single-phase stepper motor.3-3 Permanent magnet stepper motorPermanent magnet stepper motor is generally two-phase, torque, and smaller, usually 7.5 degree step angle or 15 degrees;Permanent magnet stepper motor output torque, dynamic performance, but a large step angle.3-4 Reaction Stepper MotorReaction is generally three-phase stepping motor can achieve high torque output, step angle of 1.5 degrees is generally, but the noise and vibration are large. Reaction by the stepper motor rotor magnetic circuit made of soft magnetic materials, a number of the stator phase excitation winding, the use of permeability changes in torque.Step Motor simple structure, low production costs, step angle is small; but the dynamic performance is poor.3-5 Hybrid Stepping MotorHybrid Step Motor combines reactive, permanent magnet stepper motors of both, it's a small step angle, contribute a large, dynamic performance, is currently the highest performance stepper motor. It is also sometimes referred to as PermanentMagnet Induction Stepping Motor. It consists of two phases and the five-phase: the general two-phase step angle of 1.8 degrees and the general five-phase step angle 0.72 degrees. The most widely used Stepper Motor. Stepper motor drive for energy saving 3-6 Three-phase stepper motor drive special features:◆180% low torque output, low frequency characteristics of a good run◆Maximum output frequency 600Hz, high-speed motor control◆full range of detection of protection (over voltage, under voltage, overload)instantaneous power failure restart◆acceleration, deceleration, such as dynamic change in the stall protection functionto prevent◆Electrical dynamic parameters of automatic recognition function to ensurestability and accuracy of the system◆quick response and high-speed shutdown◆abundant and flexible input and output interface and control, versatility◆use of SMT production and three full-mount anti-paint treatment process, productstability and high◆full range of Siemens IGBT power devices using the latest, to ensure the qualityof high-quality3-7 Basic principlesUsually for the permanent magnet rotor motor, when current flows through the stator windings, the stator windings produce a magnetic field vector. The magnetic field will lead to a rotor angle of the magnetic field makes the direction of a rotor and the stator's magnetic field direction. When the stator magnetic field vector rotating at an angle. As the rotor magnetic field is also transferred from another perspective. An electrical pulse for each input, the motor turning a point forward. It is the angular displacement of the output and input the number of pulses proportional to speed and pulse frequency is proportional to. Power to change the order of winding, the motor will reverse. Therefore, the number of available control pulse, frequency and power the motor windings of each phase in order to control the stepper motor rotation.3-8 Induction Stepping Motor3-8-1 features: Induction, compared with the traditional reactive, structural reinforced with a permanent magnet rotor, in order to provide the working point of soft magnetic materials, and the stator excitation magnetic field changes only need to provide to provide the operating point of the consumption of magnetic materials energy, so the motor efficiency, current, low heat. Due to the presence of permanent magnets, the motor has a strong EMF, the damping effect of its own good, it is relatively stable during operation, low noise, low frequency vibration. Induction can be seen as somewhat low-speed synchronous motor. A four-phase motor can be used for four-phase operation, but also can be used for two-phase operation. (Must be bipolar voltage drive), while the motor is not so reactive. For example: four phase, eight-phase operation (A-AB-B-BC-C-CD-D-DA-A) can use two-phase eight-shot run. Not difficult to find the conditions for C =, D =. a two-phase motor's internal winding consistent with the four-phase motors, small power motors are generally directly connected to the second phase, the power of larger motor, in order to facilitate the use and flexible to change the dynamic characteristics of the motor, its external connections often lead to eight (four-phase), so that when used either as a four-phase motors used, can be used for two-phase motor winding in series or parallel.3-8-2 classification:Induction motors can be divided in phases: two-phase motor, three phase motor, four-phase motor, five-phase motor. The frame size (motor diameter) can be divided into: 42BYG (BYG the Induction Stepping motor code), 57BYG, 86BYG, 110BYG, (international standard), and like 70BYG, 90BYG, 130BYG and so are the national standards.3-8-3 the stepper motor phase number of static indicators of terms: very differently on the N, S the number of magnetic field excitation coil. Common m said. Beat number: complete the necessary cyclical changes in a magnetic field pulses or conducting state with n said, or that turned a pitch angle of the motor pulses needed to four-phase motor, for example, a four-phase four-shot operation mode that AB -BC-CD-DA-AB, shot eight four-phase operation mode that A-AB-B-BC-C-CD-D-DA-A. Step angle: corresponds to a pulse signal, the angulardisplacement of the rotor turne d with θ said. θ = 360 degrees (the rotor teeth number of J * run shot), the conventional two, four-phase, the rotor teeth 50 tooth motor as an example. Four step run-time step angle θ = 360 ° / (50 * 4) = 1.8 degrees (commonly called the whole step), eight-shot running step angle θ = 360 ° / (50 * 8) = 0.9 degrees (commonly known as half step.) Location torque: the motor is not energized in the state, its locked rotor torque (as well as by the magnetic field profile of harmonics caused by mechanical error) static torque: the motor under the rated static electricity, the motor without rotation, the motor shaft locking torque. The motor torque is a measure of volume (geometry) standards, and drive voltage and drive power, etc. has nothing to do. Although the static torque is proportional to the electromagnetic magnetizing ampere turns, and fixed air gap between the rotor teeth on, but over-use of reduced air gap, increase the excitation ampere-turns to increase the static torque is not desirable, this will cause the motor heating and mechanical noise.3-9 Characteristics of the stepper motor1. The general accuracy of the stepper motor step angle of 3-5%, and not cumulative.2. Appearance of the stepper motor to allow the maximum temperature.Stepper motor causes the motor temperature is too high the first magnetic demagnetization, resulting in loss of torque down even further, so the motor surface temperature should be the maximum allowed depending on the motor demagnetization of magnetic material points; Generally speaking, the magnetic demagnetization points are above 130 degrees Celsius, and some even as high as 200 degrees Celsius, so the stepper motor surface temperature of 80-90 degrees Celsius is normal.3. Stepper motor torque will decrease with the increase of speed.When the stepper motor rotates, the motor winding inductance of each phase will form a reverse electromotive force; the higher the frequency the greater the back emf. In its role, the motor with frequency (or speed) increases with the phase current decreases, resulting in decreased torque.4. Low-speed stepper motor can operate normally, but if not higher than a certain speed to start, accompanied by howling.。
自动化专业-外文文献-英文文献-外文翻译-plc方面

1、外文原文(复印件)A: Fundamentals of Single-chip MicrocomputerTh e si ng le-ch i p mi cr oc om pu ter is t he c ul mi nat i on o f bo th t h e d ev el op me nt o f th e d ig it al com p ut er an d t he int e gr at ed ci rc ui ta r gu ab ly th e t ow m os t s i gn if ic ant i nv en ti on s o f t h e 20t h c en tu ry[1].Th es e to w t ype s o f a rc hi te ct ur e a re fo un d i n s i ng le—ch ip m i cr oc om pu te r。
S o me em pl oy th e s p li t p ro gr am/d at a me mo ry of t he H a rv ar d ar ch it ect u re, sh ow n in Fi g.3-5A—1,ot he r s fo ll ow t hep h il os op hy, wi del y a da pt ed f or ge n er al—pu rp os e c o mp ut er s an dm i cr op ro ce ss or s, of ma ki ng no lo gi c al di st in ct io n be tw ee n p ro gr am a n d da ta m em or y a s i n th e Pr in cet o n ar ch it ec tu re,sh ow n in F ig。
3-5A-2.In g en er al te r ms a s in gl e—ch i p mi cr oc om pu ter isc h ar ac te ri zed b y the i nc or po ra tio n of al l t he uni t s o f a co mp ut er i n to a s in gl e de v i ce,as s ho wn i n F ig3—5A—3。
自动化专业英语原文和翻译
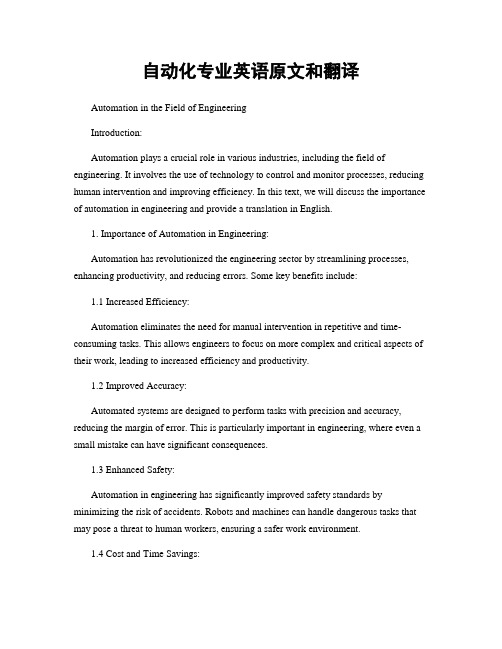
自动化专业英语原文和翻译Automation in the Field of EngineeringIntroduction:Automation plays a crucial role in various industries, including the field of engineering. It involves the use of technology to control and monitor processes, reducing human intervention and improving efficiency. In this text, we will discuss the importance of automation in engineering and provide a translation in English.1. Importance of Automation in Engineering:Automation has revolutionized the engineering sector by streamlining processes, enhancing productivity, and reducing errors. Some key benefits include:1.1 Increased Efficiency:Automation eliminates the need for manual intervention in repetitive and time-consuming tasks. This allows engineers to focus on more complex and critical aspects of their work, leading to increased efficiency and productivity.1.2 Improved Accuracy:Automated systems are designed to perform tasks with precision and accuracy, reducing the margin of error. This is particularly important in engineering, where even a small mistake can have significant consequences.1.3 Enhanced Safety:Automation in engineering has significantly improved safety standards by minimizing the risk of accidents. Robots and machines can handle dangerous tasks that may pose a threat to human workers, ensuring a safer work environment.1.4 Cost and Time Savings:By automating processes, engineering companies can reduce labor costs and save time. Automated systems can work continuously without breaks, leading to faster project completion and reduced operational expenses.2. Examples of Automation in Engineering:Automation is widely used in various branches of engineering. Here are a few examples:2.1 Manufacturing Automation:In the field of manufacturing, automation is extensively utilized to streamline production lines. Robots and computer-controlled machines are employed to carry out tasks such as assembly, welding, and quality control. This not only improves efficiency but also ensures consistent product quality.2.2 Process Automation:Process automation involves the use of control systems to monitor and regulate industrial processes. In engineering, this can include tasks such as temperature control, pressure regulation, and flow management. By automating these processes, engineers can optimize efficiency and ensure consistent output.2.3 Building Automation:Building automation systems are used to control and monitor various aspects of a building, such as lighting, HVAC (heating, ventilation, and air conditioning), and security. These systems improve energy efficiency, comfort, and security while reducing operational costs.2.4 Transportation Automation:Automation has greatly impacted the transportation sector, particularly in engineering fields such as automotive and aerospace. Automated assembly lines and robotic systems are used in vehicle manufacturing, while autopilot systems and advanced navigation technologies have revolutionized the aviation industry.3. Translation:自动化在工程领域的重要性引言:自动化在各个行业中都扮演着重要角色,其中包括工程领域。
自动化专业中英文对照外文翻译文献
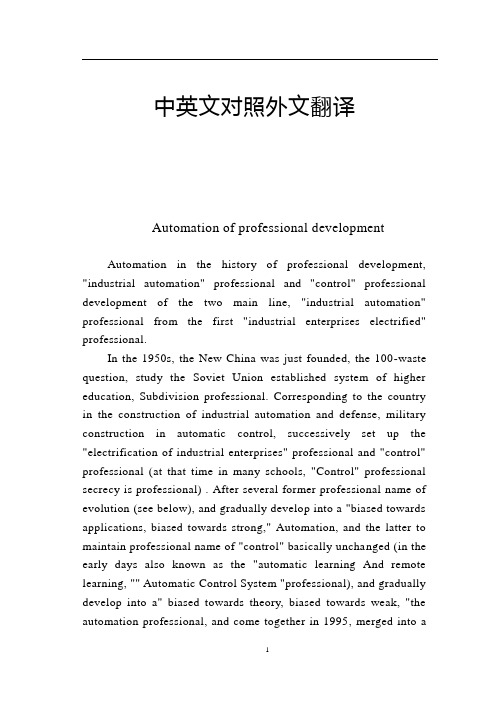
中英文对照外文翻译Automation of professional developmentAutomation in the history of professional development, "industrial automation" professional and "control" professional development of the two main line, "industrial automation" professional from the first "industrial enterprises electrified" professional.In the 1950s, the New China was just founded, the 100-waste question, study the Soviet Union established system of higher education, Subdivision professional. Corresponding to the country in the construction of industrial automation and defense, military construction in automatic control, successively set up the "electrification of industrial enterprises" professional and "control" professional (at that time in many schools, "Control" professional secrecy is professional) . After several former professional name of evolution (see below), and gradually develop into a "biased towards applications, biased towards strong," Automation, and the latter to maintain professional name of "control" basically unchanged (in the early days also known as the "automatic learning And remote learning, "" Automatic Control System "professional), and gradually develop into a" biased towards theory, biased towards weak, "the automation professional, and come together in 1995, merged into aunified" automatic "professional . In 1998, according to the Ministry of Education announced the latest professional undergraduate colleges and universities directory, adjusted, the merger of the new "automated" professional include not only the original "automatic" professional (including "industrial automation" professional and "control" professional ), Also increased the "hydraulic transmission and control of" professional (part), "electrical technology" professional (part) and "aircraft guidance and control of" professional (part).Clearly, one of China's automation professional history of the development of China's higher education actually is a new development of the cause of a microcosm of the history, but also the history of New China industrial development of a miniature. Below "industrial automation" professional development of the main line of this example, a detailed review of its development process in the many professional name change (in real terms in the professional content changes) and its industrial building at the time of the close relationship.First a brief look at the world and China's professional division history. We know that now use the professional division is largely from the 19th century to the beginning of the second half of the first half of the 20th century stereotypes of the engineering, is basically industry (products) for the objects to the division, they have been the image of people Known as the "industry professionals" or "trade associations." At present the international education system in two categories, with Britain and the United States as the representative of the education system not yet out of "industry professionals" system, but has taken the "generalist" the road of education and the former Soviet Union for Europe (close to the Soviet Union) as the representative The education system, at the beginning of theimplementation of "professionals" education, professional-very small, although reforms repeatedly, but to the current "industry professionals" are still very obvious characteristics.In the 1950s, just after the founding of New China, a comprehensive study and the Soviet Union and sub-professional very small; Since reform and opening up, only to Britain and the United States to gradually as the representative of the education system to move closer, and gradually reduce the professional, the implementation of "generalist" education through a number of professional Restructuring and merger (the total number of professionals from the maximum of 1,343 kinds of gradually reducing the current 249 kinds), although not out of "industry professionals" and "Mei Ming," but many of the colleges and universities, mostly only one of a Professional, rather than the past more than a professional.Before that, China's first professional automation from the National University in 1952 when the first major readjustment of the establishment of professional - electrified professional industrial enterprises. At that time, the Soviet Union assistance to the construction of China's 156 large industrial enterprises, automation of much-needed electrical engineering and technical personnel, and such professional and technical personnel training, and then was very consistent with China's industrial construction. By the 1960s, professional name changed to "industrial electric and automation," the late 1970s when to resume enrollment "Electric Industrial Automation" professional. This is not only professional name changes, but has its profound meaning, it reflects China's industries from "electrified" step by step to the "automatic" into the real history and that part of the development trend of China's automation professional reflects how urgent countries Urgent for the country'seconomic construction services that period of history and development of real direction.1993, after four years of the third revision of the undergraduate professional directories, the State Education Commission issued a call "system integrity, more scientific and reasonable, the harmonization of norms," the "ordinary professional directory of undergraduate colleges and universities." "Electric Industrial Automation" and "production process automation" merger of the two professional electrician to set up a kind of "industrial automation" professional, by the then Ministry of Industry Machinery centralized management colleges and universities to set up industrial automation teaching guide at the Commission, responsible for the "Industrial Automation "professional teaching and guiding work at the same time," Control "was attributable to the professional category of electronic information, the then Ministry of Industry of electronic centralized management control to set up colleges and universities teaching guide at the Commission, responsible for the" control " Professional teaching guide our work. After the professional adjustment, further defined the "industrial automation" professional and "control" professional "- both strong and weak, hardware and software into consideration and control theory and practical system integration, and the movement control, process control and other targets of control "The common characteristics with the training objectives, but also the basic set of" industrial automation "biased towards strong, professional, biased towards applications," Control "professional biased towards weak, biased towards the theory of professional characteristics and pattern of division of labor. 1995, the State Education Commission promulgated the "(University) undergraduate engineering leading professional directory", the electrical category "industrialautomation" professional and the original electronic information such as "control" of professional electronic information into a new category of "automatic" professional . As this is the leading professional directory, are not enforced, coupled with general "industrial automation" strong or weak, both professional "into" a weak professional category of electronic information is not conducive to professional development and thus many Schools remain "industrial automation" professional and "control" the situation of professional co-exist. Since 1996 more, again commissioned by the Ministry of National Education Ministry of Industry and electronic machinery industries of other parts of the establishment of the new session (second session) centralized management guidance at the University Teaching Commission, making the leading professionals have not been effective Implemented.1998, to meet the country's economic construction of Kuan Koujing personnel training needs, further consolidation of professional and international "generalist" education track by the Ministry of Education announced a fourth revision of the latest "Universities Undergraduate Catalog." So far in the use of the directory, the total number of professionals from the third amendments to the 504 kinds of substantially reduced to 249 species, the original directory is strong, professional electrician and a weak professional category such as electronics and information into categories Electric power, the unity of Information, a former electrician at the same time kind of "industrial automation" professional and the type of electronic information "control" professional formal merger, together with the "hydraulic transmission and control of" professional (part) , "Electric technology" professional (part) and "aircraft guidance and controlof" professional (part), the composition of the new (enforcement) are electrical information such as "automatic" professional. According to statistics, so far the country has more than 200 colleges and universities set up this kind of "automatic" professional. If the name of automation as part of their professional expertise (such as "electrical engineering and automation," "mechanical design and manufacturing automation," "agricultural mechanization and automation" and other professionals) included Automation has undoubtedly is the largest in China A professional.Of the characteristics of China's automation professional:Recalling China's professional history of the development of automation, combined with the corresponding period of the construction of China's national economy to the demand for automation and automated the development of the cause, it is not difficult to sum up following professional characteristics:(1) China's automation professional is not only a relatively long history (since 1952 have been more than 50 years), and from the first day of the establishment of professional automation, has been a professional one of the countries in urgent need, therefore the number of students has also been The largest and most employers welcome the allocation of the professional one.(2) China's automation is accompanied by a professional from the electrification of China's industrial automation step by step to the development of stable development, professional direction and the main content from the first prominent electrified "the electrification of industrial enterprises" step by step for the development of both the electric and automation " Industrial electric and automation ", highlighting the electrical automation" Electric Industrial Automation "and prominent automation" industrial automation ", then the merger of professional education reform in1995 and" control "of professional content into a broader" automated " Professional. From which we can see that China's automation professional Although the initial study in the Soviet education system established under the general environment, but in their development and the Soviet Union or the United States and Britain did not copy the mode, but with China's national conditions (to meet national needs for The main goal) from the innovation and development of "cross-industry professionals," features the professional.自动化专业的发展自动化专业的发展历史中,有“工业自动化”专业与“自动控制”专业两条发展主线,其中“工业自动化”专业最早源于“工业企业电气化”专业。
自动化专业英语原文和翻译

自动化专业英语原文和翻译Automation in the Manufacturing Industry: An OverviewIntroduction:Automation plays a crucial role in the manufacturing industry, revolutionizing production processes and enhancing efficiency. This article provides an in-depth analysis of the concept of automation in the manufacturing sector, highlighting its benefits, challenges, and future prospects. It also includes a translation of the text into English.Section 1: Definition and Importance of AutomationAutomation refers to the use of technology and machinery to perform tasks with minimal human intervention. In the manufacturing industry, automation is essential for streamlining operations, reducing costs, and improving product quality. It allows companies to achieve higher production rates, increased precision, and improved safety standards.Section 2: Benefits of Automation in Manufacturing2.1 Increased ProductivityAutomation enables manufacturers to produce goods at a faster rate, leading to increased productivity. With the use of advanced robotics and machinery, repetitive tasks can be performed efficiently, allowing workers to focus on more complex and creative aspects of production.2.2 Enhanced Quality ControlAutomated systems ensure consistency and accuracy in manufacturing processes, leading to improved product quality. By minimizing human error, automation reduces defects and variations, resulting in higher customer satisfaction and reduced waste.2.3 Cost ReductionAutomation helps in reducing labor costs by replacing manual work with machines and robots. Although initial investment costs may be high, long-term savings are significant due to increased efficiency and reduced dependence on human labor.2.4 Improved Workplace SafetyAutomation eliminates the need for workers to perform hazardous or physically demanding tasks. Robots and machines can handle tasks that pose risks to human health and safety, thereby reducing workplace accidents and injuries.2.5 Increased FlexibilityAutomated systems can be easily reprogrammed to adapt to changing production requirements. This flexibility allows manufacturers to respond quickly to market demands, introduce new products, and customize production processes.Section 3: Challenges in Implementing Automation3.1 Initial InvestmentImplementing automation requires substantial capital investment for purchasing and integrating machinery, software, and training. Small and medium-sized enterprises (SMEs) may face financial constraints in adopting automation technologies.3.2 Workforce AdaptationAutomation may lead to job displacement, as certain tasks previously performed by humans are now handled by machines. Companies need to provide training and re-skilling opportunities to ensure a smooth transition for their workforce.3.3 Technical ComplexityAutomation systems often involve complex integration of various technologies, such as robotics, artificial intelligence, and data analytics. Companies must have skilled personnel capable of managing and maintaining these systems effectively.Section 4: Future Trends in Automation4.1 Collaborative RobotsCollaborative robots, also known as cobots, are designed to work alongside humans, assisting them in tasks that require precision and strength. These robots can improve productivity and safety by working in close proximity to humans without the need for extensive safety measures.4.2 Internet of Things (IoT) IntegrationThe integration of automation systems with the Internet of Things allows for real-time monitoring and control of manufacturing processes. IoT enables seamless communication between machines, sensors, and data analytics platforms, leading to predictive maintenance and optimized production.4.3 Artificial Intelligence (AI)AI technologies, such as machine learning and computer vision, enable automation systems to learn and adapt to new situations. AI-powered robots can analyze data, make decisions, and perform complex tasks with minimal human intervention, revolutionizing the manufacturing industry.Conclusion:Automation has become an integral part of the manufacturing industry, offering numerous benefits such as increased productivity, enhanced quality control, cost reduction, improved workplace safety, and increased flexibility. While challenges exist, such as initial investment and workforce adaptation, the future of automation looks promising with the emergence of collaborative robots, IoT integration, and artificial intelligence. Embracing automation technologies will undoubtedly pave the way for a more efficient and competitive manufacturing sector.Translation:自动化在创造业中的应用:概述简介:自动化在创造业中扮演着重要的角色,革新了生产过程,提高了效率。
自动化专业毕业设计外文翻译--现地控制单元在水电厂自动化中的应用
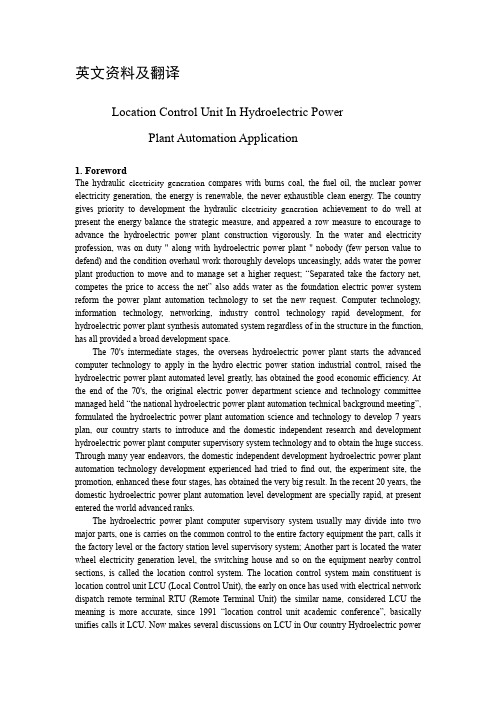
英文资料及翻译Location Control Unit In Hydroelectric PowerPlant Automation Application1. ForewordThe hydraulic electricity generation compares with burns coal, the fuel oil, the nuclear power electricity generation, the energy is renewable, the never exhaustible clean energy. The country gives priority to development the hydraulic electricity generation achievement to do well at present the energy balance the strategic measure, and appeared a row measure to encourage to advance the hydroelectric power plant construction vigorously. In the water and electricity profession, was on duty " along with hydroelectric power plant " nobody (few person value to defend) and the condition overhaul work thoroughly develops unceasingly, adds water the power plant production to move and to manage set a higher request; “Separated take the factory net, competes the price to access the net” also adds water as the foundation electric power system reform the power plant automation technology to set the new request. Computer technology, information technology, networking, industry control technology rapid development, for hydroelectric power plant synthesis automated system regardless of in the structure in the function, has all provided a broad development space.The 70's intermediate stages, the overseas hydroelectric power plant starts the advanced computer technology to apply in the hydro-electric power station industrial control, raised the hydroelectric power plant automated level greatly, has obtained the good economic efficiency. At the end of the 70's, the original electric power department science and technology committee managed held “the national hydroelectric power plant automation technical background meeting”, formulated the hydroelectric power plant automation science and technology to develop 7 years plan, our country starts to introduce and the domestic independent research and development hydroelectric power plant computer supervisory system technology and to obtain the huge success. Through many year endeavors, the domestic independent development hydroelectric power plant automation technology development experienced had tried to find out, the experiment site, the promotion, enhanced these four stages, has obtained the very big result. In the recent 20 years, the domestic hydroelectric power plant automation level development are specially rapid, at present entered the world advanced ranks.The hydroelectric power plant computer supervisory system usually may divide into two major parts, one is carries on the common control to the entire factory equipment the part, calls it the factory level or the factory station level supervisory system; Another part is located the water wheel electricity generation level, the switching house and so on the equipment nearby control sections, is called the location control system. The location control system main constituent is location control unit LCU (Local Control Unit), the early on once has used with electrical network dispatch remote terminal RTU (Remote Terminal Unit) the similar name, considered LCU the meaning is more accurate, since 1991 “location control unit academic conference”, basically unifies calls it LCU. Now makes several discussions on LCU in Our country Hydroelectric powerplant automated system application and the development.2. LCU applicationIn the hydroelectric power plant computer supervisory system LCU with the power plant production process connection, is directly in the system most has the object-oriented distribution characteristic the control device. The location control unit controlled member mainly includes following several parts:(1) power plant generating set, mainly has the hydraulic turbine, the generator, the auxiliary engine, the transformer and so on;(2) switching house, mainly has the generatrix, the circuit breaker, the isolator, the earth knife switch and so on;(3) public utility, mainly has the factory to use electricity the system, the oil system, the aqueous system, the direct current system and so on;(4) strobe, mainly has the water inlet strobe, the flood discharge strobe and so on.The LCU general arrangement nearby the power plant production equipment, to is accused the object movement operating mode to carry on the real-time surveillance and the control, is the power plant computer supervisory system compares the first floor control section. The primary data carries on gathering and the pretreatment in this, each kind of control adjustment order all sends out and completes the control closed loop through it, it is in the entire supervisory system very important, to the reliable request very high control device. Uses in the hydroelectric power plant LCU may divide into unit LCU, public LCU, switching house LCU according to the monitoring object and the installment position and so on. But and disposes according to the LCU itself structure divides, then may divide into the single trigger --linear structure LCU, take programmable controller (PLC) as foundation LCU, the intelligent location controller and so on three kinds. First kind of LCU many for hydroelectric power plant automation initial period product, at present basic no longer has used in the new system. Moreover still had few small hydroelectric power plants to use based on industry PC machine (called labor controlled machine IPC) the control system, below only discussed is in the mainstream status PLC and the intelligent location controller (the recent several years still had is called PCC (Programmable Computer Controller), PAC (Programmable Automation Controller) product, should also be possible to classify).2.1 programmable controller (PLC)The PLC definition has many kinds. International electrician committee (IEC) to PLC the definition is: The programmable controller is one kind of digital operation electronic system, for designs specially in the industry environment application. It uses the programmable the memory, uses in its internally stored program, carries out the logic operation, the sequential control, fixed time, counts with the arithmetic operation and so on face user's instruction, and through digital, the simulation input and the output, controls each kind of type the machinery or the production process. The programmable controller and the related equipment, all should according to easy form a whole with the industry control system, easy to expand its function the principle design.At first, needed to produce as a result of the American automobile industry has been possible to say was primitive PLC. Although the PLC being published time does not calculate long too, but along with the microprocessor appearance, large-scale, the ultra large scale integrated circuit technique of manufacture and the data communication technology rapid development, the PLC application and the technology also obtained the rapid development, its developing processapproximately separable three stages:(1) early time PLC (at the end of 60's -70's intermediate stages): Early PLC is called the programmable logical controller generally.(2) intermediate stage PLC (in 70's intermediate stage - 80's, later period): Starts in the 70's to use the microprocessor to take PLC the central processing element (CPU). Thus, causes PLC to result in the function big enhancement. In the software aspect, in the original logic operation, fixed time, counted and so on in the function foundations to increase functions and so on arithmetic operation, data processing and data communication, from diagnosis. In the hardware aspect, has developed the simulation quantity module, the long-distance I/O module as well as each kind of special function module, enables PLC the application scope to expand rapidly to needs the automatic control very many professions.(3) near future PLC (in the 80's, later period until now) enters in for the 80's, the later period, because the microprocessor hardware technique of manufacture rapid development, simultaneously the market price large scale drop, will cause each PLC manufacturer to be possible to use a higher scale the microprocessor. In order to further enhance PLC the processing speed, the very many manufacture manufacturer also developed has developed the special-purpose logical processing chip. Afterwards PLC has also integrated Ethernet, technologies and so on Web Server, has provided the function rich necessary software, causes the user community to use handily.On the century 80's to the 90's intermediate stages, are PLC develops the quickest time, the yearly rate continuously maintenance is 30%~40%. In this time, the PLC data acquisition handling ability, the numeral operational capability, the man-machine connection and network traffic capacity all obtains the large scale enhancement, PLC enters the process control domain gradually, unified after the partial industry control device substitutes gradually in certain applications has been at the dominant position in the process control domain the DCS system. Because PLC has the versatility strongly, the reliability high, the easy to operate, the programming simple, the adaptation surface broad and so on the characteristics, caused it is specially in the sequential control obtained the extremely widespread application in the industrial automation control.Applies PLC in the hydroelectric power plant production equipment monitoring begins in on the century 80's, because PLC defers to the industry use environment the standard to carry on the design generally, the reliability high, antijamming ability strong, the programming simple practical, met inserts the performance good very quickly accepts by the power plant user and system integration business, obtained the good application. At present includes in Our country Hydroelectric power plant use widespread PLC: GE Fanuc Corporation's GE Fanuc 90 series, German Siemens Corporation's S5, S7 series, French Schneider Corporation's Modicon Premium, Atrium and Quantum, American Rockwell Corporation PLC5, Control Logix, Japanese OMRON Corporation's SU-5, SU-6, SU-8, Japanese MITSUBISHI Corporation's FX2 series and so on. Because each kind of PLC principle of design difference is big, the product function, the performance as well as may constitute the location system scale to have the very big difference. Generally speaking, according to the different power plant in the security performance (including reliability, maintainable and so on), aspect and so on application function, control scale, system structure actual demands carries on the choice, may find appropriate PLC. At present there is big part of power plants the automated system all uses the PLC constitution location control section, and matches through the reasonable disposition, they basically all can shoulder the corresponding responsibility in the system, completes the corresponding function.But PLC took but one kind of general automated installment, is by no means designs specially for the hydroelectric power plant automation, this has in the special request profession application in the water and electricity automation also to be able to have some not suitable place inevitably, presently lists following several points:(1) PLC by “scanning”the way work, cannot satisfy the event resolution and the system clock synchronization request. The hydroelectric power plant computer supervisory system all is a multi-computer system, in order to guarantee the event resolution should have certain event besides PLC itself to respond ability and the high accuracy clock, but also requests in the overall system between various part of main equipment clock synthesis precision also to have to guarantee in a millisecond level. But take PLC as the foundation location control device if does not take the special measure, is unable to guarantee the hydroelectric power plant safe operation to the event resolution and the system clock synchronization request.(2) general PLC origin mainly aims at the machine-finishing profession, later gradually will expand all the various trades and occupations. Although present PLC has strongly from diagnosis function, but regarding the input, the output unit, it only from diagnoses the module level. This produces this kind of emphasis regarding our country electric power “the safety first” the profession said that, has certain being short of, often needs to add seperately the special security measure.(3) general PLC all has certain surge suppression ability generally, basically may suit the majority of profession application. But says regarding the hydroelectric power plant automated system, as a result of the equipment working conditions particularity, three level of surge suppression ability which the general PLC surge suppression ability and the technology standard request also has some disparities.2.2 intelligent location controllerApplies the many another kind of location control unit in Hydroelectric power plant automated system to be supposed to be the intelligent location controller, like ABB Corporation AC450, south auspicious group's SJ-600 series, Elin Corporation's SAT1703 and so on.AC450 is being suitable which ABB Corporation produces in industry environment Advant Controller series location control unit one kind, mainly applies in other profession DCS. It has included the module which by Motorola 68040 primarily processor CPU modules and I/O, MasterBus and so on many kinds of may elect, supports centralized I/O and distributional I/O, may act according to the different application demand to use the different module to constitute the suitable location subsystem.SAT1703 is the multi-processor system which Austrian Elin Corporation produces, it is loaded with different connection processor subsystem AK1703, AME1703 and AM1703 including 3. Each sub-system by the host processor, the connection template (module), constitutions and so on connection module, can realize the data processing, the control and the correspondence function, uses SMI in the LCU interior (Serial Module Interconnector) to carry on the correspondence. SAT1703 location control unit uses OS/2 operating system, the movement control software is ToolBox.SJ-600 series is on the international telegram automation research institute the century at the end of 90's for the domestically produced intelligence distributional location control unit which moves under the bad industry environment produces, by the master control module, the intelligent I/O module, the power source module as well as connects various modules and the master controlmodule scene bus network is composed. Moved reliably in the national dozens of large and middle scale hydroelectric power plants. Below SJ-600 has the main characteristic:(1), the master control module uses conforms to IEEE1996.1's embedded module standard PC104, has the reliability high, the scene environment compatibility strong and so on the characteristics. Uses low power loss embedded CPU, may choose the CPU model from 486 to the Pentium series.(2) 32 intelligence I/O module. All modules use 32 embedded CPU, this CPU designs specially for the embedded control, on the software uses the board level real-time operating system and the unification procedure code, only is different moves the corresponding duty according to the module. Has used large-scale programmable logic chip (EPLD) and the Flash memory, simplified the system design, enhanced the reliability. The intellectualized I/O module except may complete the data acquisition and the pretreatment independently, but also has very strongly from the diagnosis function, has provided the reliable control security and the convenience breakdown localization ability.(3) has the field bus network system structure, the system uses two network architectures, first is the factory cascade control network, connects LCU and the factory level computer, constitutes the distributed computer supervisory system; Second is I/O main line network, the connection master control module and the intelligent I/O module (location or long-distance), constitutes the distributional location control subsystem. All I/O module provides two field bus network connection, these modules all may disperse the arrangement, forms the redundant reliable distributional redundant system.(4) LCU direct connection high speed network. The network has become in the computer supervisory system the important part, it involves to the power plant control strategy and the movement way. Beforehand location controller many is the use private network carries on the connection with on position machine system, but conforms to the open standard network. If AC450 uses MB300 network with on position machine system connection, but with uses TCP/IP agreement the system connection only to be able to carry on through the special-purpose module by the VIP way the data transmission which limits.(5) has provided the direct GPS synchronized clock connection, does not need to program and the establishment. GPS to when may go directly to the module level, satisfied had the special request situation to the clock, like SOE and so on.(6) provides based on IEC61131-3 standard control language, in retained trapezoidal programming language in and so on the chart, structure text, instruction list foundations, developed the use “to see namely obtained”the technical design visualization flow chart programming language. The support control flow online debugging and playbacking, suits the complex control flow extremely the production and the maintenance.(7) in view of hydroelectric power plant automation specialized application development special-purpose function module.现地控制单元在水电厂自动化中的应用1. 前言水力发电与燃煤、燃油、核能发电相比,能源是可再生的、永不枯竭的清洁能源。
自动化专业毕业设计外文翻译1

外文资料Programmable Logic Controllers (PLC), a computing device invented by Richard E. Morley in 1968, have been widely used in industry including manufacturing systems, transportation systems, chemical process facilities, and many others. At that time, the PLC replaced the hardwired logic with soft-wired logic orso-called relay ladder logic (RLL), a programming language visually resembling the hardwired logic, and reduced thereby the configuration time from 6 months down to 6 days [Moody and Morley, 1999].Although PC based control has started to come into place, PLC based control will remain the technique to which the majority of industrial applications will adhere due to its higher performance, lower price, and superior reliability in harsh environments. Moreover, according to a study on the PLC market of Frost and Sullivan [1995], an increase of the annual sales volume to 15 million PLC per year with the hardware value of more than 8 billion US dollars has been predicted, though the prices of computing hardware is steadily dropping. The inventor of the PLC, Richard E Morley, fairly considers the PLC market as a 5-billion industry at the present time.Though PLCare widely used in industrial practice, the programming of PLC based control systems is still very much relying on trial-and-error. Alike software engineering, PLC software design is facing the software dilemma or crisis in a similar way. Morley himself emphasized this aspect most forcefully by indicating:“If houses were built like software projects, a single woodpecker could destroy civilization.”Particularly, practical problems in PLC programming are to eliminate software bugs and to reduce the maintenance costs of old ladder logic programs. Though the hardware costs of PLC are dropping continuously, reducing the scan time of the ladder logic is still an issue in industry so that low-cost PLC can be used.In general, the productivity in generating PLC is far behind compared to other domains, for instance, VLSI design, where efficient computer aided design tools are in practice. Existent software engineering methodologies are not necessarily applicable to the PLC based software design because PLC-programming requires a simultaneous consideration of hardware and software. The software design becomes, thereby, more and more the major cost driver. In many industrial design projects,more than SO0/a of the manpower allocated for the control system design and installation is scheduled for testing and debugging PLC programs [Rockwell, 1999].In addition, current PLC based control systems are not properly designed to support the growing demand for flexibility and reconfigurebility of manufacturing systems. A further problem, impelling the need for a systematic design methodology, is the increasing software complexity in large-scale projects.The objective of this thesis is to develop a systematic software design methodology for PLC operated automation systems. The design methodology involves high-level description based on state transition models that treat automation control systems as discrete event systems, a stepwise design process, and set of design rules providing guidance and measurements to achieve a successful design. The tangible outcome of this research is to find a way to reduce the uncertainty in managing the control software development process, that is, reducing programming and debugging time and their variation, increasing flexibility of the automation systems, and enabling software reusability through modularity. The goal is to overcome shortcomings of current programming strategies that are based on the experience of the individual software developer.A systematic approach to designing PLC software can overcome deficiencies in the traditional way of programming manufacturing control systems, and can have wide ramifications in several industrial applications. Automation control systems are modeled by formal languages or, equivalently, by state machines. Formal representations provide a high-level description of the behavior of the system to be controlled. State machines can be analytically evaluated as to whether or not they meet the desired goals. Secondly, a state machine description provides a structured representation to convey the logical requirements and constraints such as detailed safety rules. Thirdly, well-defined control systems design outcomes are conducive to automatic code generation- An ability to produce control software executable on commercial distinct logic controllers can reduce programming lead-time and labor cost. In particular, the thesis is relevant with respect to the following aspects.In modern manufacturing, systems are characterized by product and process innovation, become customer-driven and thus have to respond quickly to changing system requirements. A major challenge is therefore to provide enabling technologies that can economically reconfigure automation control systems in response to changing needs and new opportunities. Design and operational knowledge can be reused in real-time, therefore, giving a significant competitive edge in industrial practice.Studies have shown that programming methodologies in automation systems have not been able to match rapid increase in use of computing resources. For instance, the programming of PLC still relies on a conventional programming style with ladder logic diagrams. As a result, the delays and resources in programming are a major stumbling stone for the progress of manufacturing industry. Testing and debugging may consume over 50% of the manpower allocated for the PLC program design. Standards have been formed to fix and disseminate state-of-the-art design methods, but they normally cannot participate in advancing the knowledge of efficient program and system design.A systematic approach will increase the level of design automation through reusing existing software components, and will provide methods to make large-scale system design manageable. Likewise, it will improve software quality and reliability and will be relevant to systems high security standards, especially those having hazardous impact on the environment such as airport control, and public railroads.The software industry is regarded as a performance destructor and complexity generator. Steadily shrinking hardware prices spoils the need for software performance in terms of code optimization and efficiency. The result is that massive and less efficient software code on one hand outpaces the gains in hardware performance on the other hand. Secondly, software proliferates into complexity of unmanageable dimensions; software redesign and maintenance-essential in modern automation systems-becomes nearly impossible. Particularly, PLC programs have evolved from a couple lines of code 25 years ago to thousands of lines of code with a similar number of 1/O points. Increased safety, for instance new policies on fire protection, and the flexibility of modern automation systems add complexity to the program design process. Consequently, the life-cycle cost of software is a permanently growing fraction of the total cost. 80-90% of these costs are going into software maintenance, debugging, adaptation and expansion to meet changing needs中文翻译1968年,Richard E. Morley创造出了新一代工业控制装置可编程逻辑控制器(PLC),现在,PLC已经被广泛应用于工业领域,包括机械制造也、运输系统、化学过程设备、等许多其他领域。
自动化专业毕业设计外文翻译5
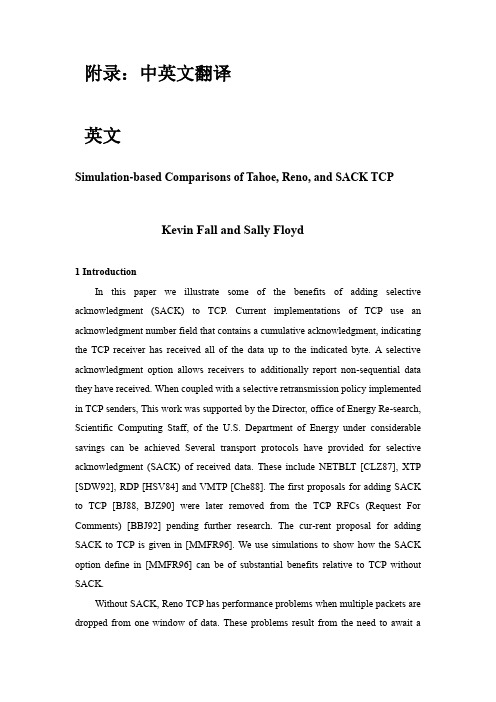
附录:中英文翻译英文Simulation-based Comparisons of Tahoe, Reno, and SACK TCPKevin Fall and Sally Floyd1 IntroductionIn this paper we illustrate some of the benefits of adding selective acknowledgment (SACK) to TCP. Current implementations of TCP use an acknowledgment number field that contains a cumulative acknowledgment, indicating the TCP receiver has received all of the data up to the indicated byte. A selective acknowledgment option allows receivers to additionally report non-sequential data they have received. When coupled with a selective retransmission policy implemented in TCP senders, This work was supported by the Director, office of Energy Re-search, Scientific Computing Staff, of the U.S. Department of Energy under considerable savings can be achieved Several transport protocols have provided for selective acknowledgment (SACK) of received data. These include NETBLT [CLZ87], XTP [SDW92], RDP [HSV84] and VMTP [Che88]. The first proposals for adding SACK to TCP [BJ88, BJZ90] were later removed from the TCP RFCs (Request For Comments) [BBJ92] pending further research. The cur-rent proposal for adding SACK to TCP is given in [MMFR96]. We use simulations to show how the SACK option define in [MMFR96] can be of substantial benefits relative to TCP without SACK.Without SACK, Reno TCP has performance problems when multiple packets are dropped from one window of data. These problems result from the need to await aretransmission timer expiration before re-initiating data flow. Situations in which this problem occurs are illustrated later in this paper (for example, see Section 6.4).Not all of Reno's performance problems are a necessary consequence of the absence of SACK. To show why, we implemented a variant of the Reno algorithms in our simulator, called New-Reno. Using a suggestion from Janey Hoe [Hoe95, Hoe96], New-Reno avoids many of the retransmit timeouts of Reno without requiring SACK. Nevertheless, New-Reno does not perform as well as TCP with SACK when a large number of packets are dropped from a window of data. The purpose of our discussion of New-Reno is to clarify the fundamental limitations of the absence of SACK. In the absence of SACK, both Reno and New-Reno senders can retransmit at most one dropped packet per round-trip time, even if senders recover from multiple drops in a window of data without waiting for a retransmit timeout. This characteristic is not shared by Tahoe TCP, which is not limited to retransmitting at most one dropped packet per round-trip time. However, it is a fundamental consequence of the absence of SACK that the sender has to choose between the following strategies to recover from lost data:1retransmitting at most one dropped packet per round-trip time, or2retransmitting packets that might have already been successfully delivered.To illustrate the advantages of TCP with SACK, we show simulations with SACK TCP, using the SACK implementation in our simulator. SACK TCP is based on a conservative extension of the Reno congestion control algorithms with the addition of selective acknowledgments and selective retransmission. With SACK, a sender has a better idea of exactly which packets have been successfully delivered as compared with comparable protocols lacking SACK. Given such information, a sender can avoid unnecessary delays and retransmissions, resulting in improved throughput. We believe the addition of SACK to TCP is one of the most important changes that should be made to TCP at this time to improve its performance.In Sections 2 through 5 we describe the congestion control and packet retransmission algorithms in Tahoe, Reno, New-Reno, and SACK TCP. Section 6 shows simulations with Tahoe, Reno, New-Reno, and SACK TCP in scenariosranging from one to four packets dropped from a window of data. Section 7 shows a trace of Reno TCP taken from actual Internet traffic, showing that the performance problems of Reno without SACK are of more than theoretical interest. Finally, Section 8 discusses possible future directions for TCP with selective acknowledgments, and Section 9 gives conclusions.2 Tahoe TCPModern TCP implementations contain a number of algorithms aimed at controlling network congestion while maintaining good user throughput. Early TCP implementations followed a go-back-n.model using cumulative positive acknowledgment and requiring a retransmit timer expiration to re-send data lost during transport. These TCPs did little to minimize network congestion.The Tahoe TCP implementation added a number of new algorithms and refinements to earlier implementations. The new algorithms include Slow-Start, Congestion Avoidance, and Fast Retransmit [Jac88]. The refinements include a modification to the round-trip time estimator used to set retransmission timeout values. All modifications have been described elsewhere [Jac88, Ste94].The Fast Retransmit algorithm is of special interest in this paper because it is modified subsequent versions of TCP. With Fast Retransmit, after receiving a small number of duplicate acknowledgments for the same TCP segment (dup ACKs), the data sender infers that a packet has been lost and retransmits the packet without waiting for a retransmission timer to expire, leading to higher channel utilization and connection throughput.3 Reno TCPThe Reno TCP implementation retained the enhancements incorporated into Tahoe, but modified the Fast Retransmit operation to include Fast Recovery [Jac90]. The new algorithm prevents the communication path (“pipe”) from going empty after Fast Retransmit, thereby avoiding the need to Slow-Start to refill it after a single packet loss. Fast Recovery operates by assuming each dup ACK received represents a single packet having left the pipe. Thus, during Fast Recovery the TCP sender is ableto make intelligent estimates of the amount of outstanding data.In Reno, the sender's usable window becomes other gateways that fail to monitor the average queue size) until the number of dup ACKs reaches tcprexmtthresh, and thereafter tracks the number of duplicate ACKs. Thus, during Fast Recovery the sender “inflate” its window by the number of dup ACKs it has received, according to the observation that each dup ACK indicates some packet has been removed from the network and is now cached at the receiver. After entering Fast Recovery and retransmitting a single packet, the sender effectively waits until half a window of dup ACKs have been received, and then sends a new packet for each additional dup ACK that is received.4 New-Reno TCPWe include New-Reno TCP in this paper to show how a simple change to TCP makes it possible to avoid some of the performance problems of Reno TCP without the addition of SACK. At the same time, we use New-Reno TCP to explore the fundamental limitations of TCP performance in the absence of SACK.The New-Reno TCP in this paper includes a small change to the Reno algorithm at the sender that eliminates Reno's wait for a retransmit timer when multiple packets are lost from a window [Hoe95, CH95]. The change concerns the sender's behavior during Fast Recovery when a partial ACK is received that acknowledges some but not all of the packets that were out-standing at the start of that Fast Recovery period. In Reno, partial ACKs take TCP out of Fast Recovery by “deflating” the usable window back to the size of the congestion window. In New-Reno, partial ACKs do not take TCP out of Fast Recovery. Instead, partial ACKs received during Fast Recovery are treated as an indication that the packet immediately following the acknowledged packet in the sequence space has been lost, and should be retransmitted. Thus, when multiple packets are lost from a single window of data, New-Reno can recover without a retransmission timeout, retransmitting one lost packet per round-trip time until all of the lost packets from that window have been retransmitted. New-Reno remains in Fast Recovery until all of the data outstanding when Fast Recovery was initiated has been acknowledged.The implementations of New-Reno and SACK TCP in our simulator also use a “maxburst” parameter. In our SACK TCP implementation, the “maxburst” parameter limits to four the number of packets that can be sent in response to a single incoming ACK, even if the sender's congestion window would allow more packets to be sent. In New-Reno, the “maxburst” parameter is set to four packets outside of Fast Recovery, and to two packets during Fast Recovery, to more closely reproduce the behavior of Reno TCP during Fast Recovery. The “maxburst” parameter is really only needed for the first window of packets that are sent after leaving Fast Recovery. If the sender had been prevented by the receiver's advertised window from sending packets during Fast Recovery, then, without “maxburst” ,it is possible for the sender to send a large burst of packets upon exiting Fast Recovery. This applies to Reno and New-Reno TCP, and to a lesser extent, to SACK TCP. In Tahoe TCP the Slow-Start algorithm prevents bursts after recovering from a packet loss. The bursts of packets upon exiting Fast Recovery with New-Reno TCP are illustrated in Section 6 in the simulations with three and four packet drops. Bursts of packets upon exiting Fast Recovery with Reno TCP are illustrated in [Flo95].5 SACK TCPThe SACK option follows the format in [MMFR96]. From [MMFR96], the SACK option field contains a number of SACK blocks, where each SACK block reports a non-contiguous set of data that has been received and queued. The first block in a SACK option is required to report the data receiver's most recently received segment, and the additional SACK blocks repeat the most recently reported SACK blocks [MMFR96]. In these simulations each SACK option is assumed to have room for three SACK blocks. When the SACK option is used with the Timestamp option specified for TCP Extensions for High Performance [BBJ92], then the SACK option has room for only three SACK blocks [MMFR96]. If the SACK option were to be used with both the Timestamp option and with T/TCP (TCP Extensions for Transactions) [Bra94], the TCP option space would have room for only two SACK blocks.The 1990 “Sack” TCP implementation on our previous simulator is from StevenMcCanne and Sally Floyd, and does not conform to the formats in [MMFR96]. The new “Sack1”implementation contains major contributions from Kevin Fall, Jamshid Mahdavi, and Matt Mathis.The congestion control algorithms implemented in our SACK TCP are a conservative extension of Reno's congestion control, in that they use the same algorithms for increasing and decreasing the congestion window,The SACK TCP implementation in this paper, called “Sack1”in our simulator, is also discussed in [Flo96b, Flo96a].and make minimal changes to the other congestion con-trol algorithms. Adding SACK to TCP does not change the basic underlying congestion control algorithms. The SACK TCP implementation preserves the properties of Tahoe and Reno TCP of being robust in the presence of out-of-order packets, and uses retransmit timeouts as the recovery method of last resort. The main difference between the SACK TCP implementation and the Reno TCP implementation is in the behavior when multiple packets are dropped from one window of data.中文翻译:1介绍在这篇论文中,我们将介绍使用选择重发(sack)选项的TCP协议的益处,拥塞控制,算法一般分为两类:基于窗口的和基于位率的拥塞控制算法,基于窗口的控制算法是通过源端限制数据报的传送,并且不应答。
自动化专业毕业设计外文翻译--输入力矩受限的机器人鲁棒自适应控制
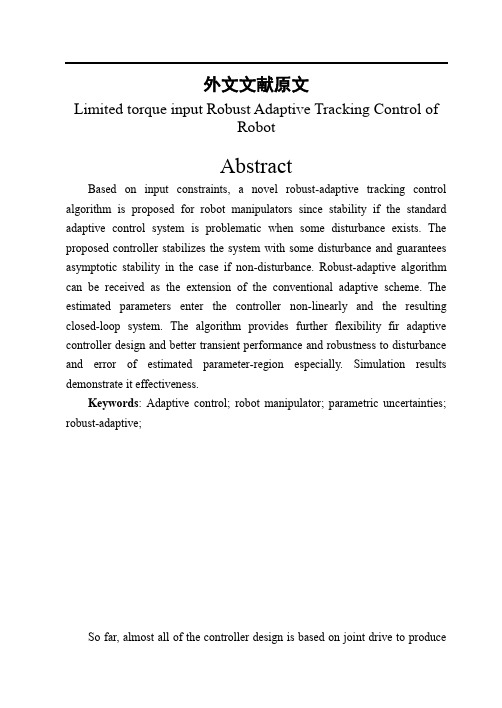
外文文献原文Limited torque input Robust Adaptive Tracking Control ofRobotAbstractBased on input constraints, a novel robust-adaptive tracking control algorithm is proposed for robot manipulators since stability if the standard adaptive control system is problematic when some disturbance exists. The proposed controller stabilizes the system with some disturbance and guarantees asymptotic stability in the case if non-disturbance. Robust-adaptive algorithm can be received as the extension of the conventional adaptive scheme. The estimated parameters enter the controller non-linearly and the resulting closed-loop system. The algorithm provides further flexibility fir adaptive controller design and better transient performance and robustness to disturbance and error of estimated parameter-region especially. Simulation results demonstrate it effectiveness.Keywords: Adaptive control; robot manipulator; parametric uncertainties; robust-adaptive;So far, almost all of the controller design is based on joint drive to produceany torque on the basis of; and is subject to the physical conditions, the output of the drive torque is limited, so the controller may lead to the control failure or deterioration of the quality control.Therefore the controller design must take into account the limited joint drive dynamic capability.For example, the operation of the industry to help the robot, some parameters are uncertain or unknown, adaptive control is based on the estimated parameters to deal with such issues one of the main control strategy, using the robot dynamic equations of linear parametric nature, through an integral operator estimates the robot parameters. As integral part of the role in the continued interference conditions, stability control system is not easy, so appropriate to limit or adjust the integral part of the role of the adaptive system to achieve an effective means of stabilization. Son ah estimated parameters can limit the extent required, thereby increasing the robustness of adaptive control system. However, this algorithm has six switch component, a little complicated, but really is the parameter is not specified range, it cannot give the system control quality and robustness of information.This paper presents a simple robust adaptive control algorithm, when the estimated parameters field contains the parameters of the true value, the closed-loop system to achieve asymptotically stable tracking; when there is interference or the estimated parameters with the true value of free parameter that is when the error system is stable.1. MANIPULATOR DYNAMIC MODEL AND CHARACTERISTIC MODELConsider a robotic manipulator with n degrees of freedom. The continuous Lagrange dynamic model is given by()(,)()M q q C q q q G q u ++= Where q ∈R n and q ∈R nare the vector of generalized joint coordinates and velocity coordinates, respectively. The inertia matrix M(q)-M T (q)> 0 ,and there exist two constant positive scalars M min and M max such that minM ≤M ≤max M , nu R ∈is the vector of commanded generalized force, and (,)C q qq andG(q) are the terms due to Carioles, Centripetal and gravity forces. In actual application, the uncertain parameters and un-modeled dynamics usually exist in the established dynamic model in (1).When the sample time sT is small enough, at instant t=k s T q and q can be approximated by()(1)s q k q k q T --≈ and 2(1)2()(1)s q k q k q k qT +-+-≈ . Respectively Using the above relationships thediscrete-time representation of (1) becomes ()()()()()()()()()()12211S M q k q k f k q k f k q k G k u k T '∙+--+=(2a) Premultiplying(2a) by ()()21sT mM q k -results in()()()()()()()()1211q k f k q k f k q k G k k u k β'+---+- where()()()()()()112,s f k I T M q k C q k qk -=- , ()()()()()()12,s f k I T M q k C q k qk -=-+ ()()()()()()()()2121s s G k T M q k G q k k T Mq k β--'==and I denotes the unitary diagonal matrix with an appropriate dimension.If the designed (),,u t q q (),,u t q q is continuous in t ,q and q , then the solution (q,q ) of (1) will be continuously differentiable. Let()()()1,,W q qM q C q q -= and (),ij w q q be ij-th element of matrix (),ij W q q ; We define()()()()11111SF k f k f k T =--and then ΔF1(k) can be expressed as()()()()()()()1,1,1F k W q k qk W q k q k =--- For the ij-th element Δf1,ij(k) of matrix ΔF1(k)we can get()()()()()()()()1,,1,1ij ij ij f k w q k qk w q k q k =---- =()()()()()()()1111,|1ij q q k T qq k w q qq k q k q ςς=-=-∂---∂()()()()()()()1111,|1ij q q k T qq k w q qq k q k q ςς=-=-∂---∂ =()()()()()11211,|1ij s q q k T qq k w q q T q k q ςςς=-=-∂--∂ ()()()()()11311,|1ij s q q k T qq k w q qT q k q ςςς=-=-∂--∂with 0≤1ς≤1,and 2ς,3ς≈1 for a small sample time Ts . From (3), it can beseen that ΔF1(k)→0 as Ts converges to zero in a compact set of (),q q(),q q.Similar properties can also be achieved for the coefficient matrixes f2(k),()G k '()G k ' and β (k) .In a compact set of (),q q, the following properties can be deduced from (3)and the expressions of the coefficient matrixes of (2b):Property 1: If the sample time Ts is small enough,then all coefficient matrixes of (2b) are slowly time varying;Property 2: f1(k)→2I,f2(k)→ −I and f1(k)+f2(k)→I, as the sample time Ts converges to zero. Then we can define the discrete equation (2b) with Properties 1 and 2 as the robotic manipulator characteristic model.2. MULTI-VARIABLE GSA CONTROLLER WITH NN COMPENSATIONDiscrete equation (2b) can be expressed as follows:()()()()1T q k k k e k θφ+=+()()()()1T q k k k e k θφ+=+ (4) Where()()()()()12,,,Tk f k f k k G k θβ'=⎡⎤⎣⎦,()()()(),1,,1TT T T Tk q k q k u k φ⎡⎤=--⎣⎦,e(k) denotes the vector of white noise with zero mean. In the case of ()G k ' ≡0, ()k θand ()k φ can be reduced to()()()()12,,Tk f k f k k θβ=⎡⎤⎣⎦()()()(),1,,TT T Tk q k q k u k φ⎡⎤=-⎣⎦Then the elements of q(k +1) can be expressed as()()()()1i i j q k k k e k φθ+=+ (5)wherei = 1,…,n, i q (k+1)) is the element i of q(k +1), ()i e k is the element i of e(k) and ()i k θ is the column i of the matrix()()()()()()()()()()()11111T T TP k k k P k p k k p k k k P k k φφλλφφ-⎡⎤--=∙--⎢⎥+-⎢⎥⎣⎦()k Θ . When the coefficient matrixes are unknown, it can be estimated by()ˆk Θ=π (q(k),q(k−1),...,u(k−1),...) , (6a) where ()ˆk Θis the estimated coefficie nt matrix of Θ(k) at the instant t=kTs , and ()π∙ denotes an estimation operator. Considering the coefficient matrixesof the characteristic model being slowly time-varying, we can obtain the selected estimation operator by the weighted least squares method (WLS)[13], namely()()()()()()()()()()()()1ˆ111i i i i TP k k k k q k k k k k P k k φθθφθλφφ-+=+∙+-+-, ()()()()()()()()()()()11111T T TP k k k P k p k k p k k k P k k φφλλφφ-⎡⎤--=∙--⎢⎥+-⎣⎦with λ(k+1)=μ0λ(k)+(1−μ0), 0<μ0 ≤1, and ()ˆik θ the column i of the matrix ()ˆk Θ. Given a desired smooth trajectory ()d q t , the adaptive control controller is designed as follows()()()()T G c u k u k u k u k =++ (7)with the feed forward control law designedas()()()()()()()()()()112ˆˆˆ11T d d du k k k I q k f k q k f k q k βε-=+∙+---(7a) and the multi-variable GSAC feedback law as()()()()()()()()()()11122ˆˆˆˆ1Gdu k k k I L fk q k L f k q k G k βε-'=+∙--+ (7b)where ()()()d qk q k q k =- is the tracking error andε(k) >0 is a small scalar that avoids the estimated matrix ()ˆk β being singular. The term of ()cu k will be designed later; L1 and L2 are golden-section coefficients, that is,210.6182L =≈130.3822L =≈, 210.6182L =≈,which satisfy the relationship L1+L2=1 and 212L L = Substituting (7) into (2), we can get()()()()()()()()22112111s c M q k q k L f qk L f q k k T u k +---=- (8)()()()()()()()()()()()()()()()()()()()()()()()()()()()()()()()()()11121222122122ˆˆˆ11d s c k M q k M k q k M q k f M k f k L q k L q k M q k s k M q k L f k s k M q k L I f k f k q k k T u k M q k L f k s k =-+--++=----+-=- ()()()()()()()()()()()()()()()2212ˆˆˆˆ11d M q k f M k f k L q k L q k M q k G k M k G q k ---+-+-and ()()()()12ˆˆsM k T k k I βε-=+.Defining the tracking filtered error s(k +1) as and using the relationships L1+L2=1 and 212L L =,212L L = (8) can be expressed as()()()()()()()()()()()()()222121M q k s k M q k L f k s k M q k L I f k f k qk +=---- ()()21s c k T u k +- =()()()()22M q k L f k s k - (9)()()()()()()()()2212ˆˆˆs c M q k L I f k f k q k k T u k +--+- Which()()()()()()()()1212k k M q k L I f k f k qk =--- ()()()()()()212ˆˆˆM q k L I f k f k q k +-- Assuming ,()()()ˆM k M q k =,()()()()()11ˆˆM k f k M q k f k = and ()()()()()22ˆˆM k f k M q k f k =,if ()c u k is selected as ()()()()()()()2212ˆˆˆc s u k T M q k L I f k f k q k -=-- then Δ(k) = 0 , and then (9) can be written as()()()221s k L f k s k +=-()()()221s k L f k s k +=- (10)Since in Property 2 ()2f k I →-()2f k I →-as Ts → 0 in a compact set of (),q q(),q q , a small sample time Ts can be selected such that the inequality ()221L f k < can be satisfied. Therefore, the tracking filtered error s(k)asymptotically converges to zero in this case. The convergence of s(k) to zero in turn guarantees the convergence of q(k) to zero. Because of the dynamics of the estimator and the time-varying coefficients of the characteristic model, it is almost impossible to satisfy the above assumptions. Therefore, we can design a suitable compensation control law ()c u k to avoid possibly the case that the control performance is deteriorated or that the close loop system is even unstable due to the estimation errors. Hence ()c u k is designed as()()()()()()()()()()()2212ˆˆˆc s i i i u k T M k L I f k f k q k k k Ty k k ψδ-=--+=+()()()111s k q k L q k +=+-()()()()()()()()2212ˆˆˆc s u k T M k L I f k f k q k k -=--+ (11) where ()ˆkis the estimate of Δ(k) . Assuming Δ(k) is smooth enough and bounded, it then can be approximated by the linearly parameterized NN to any required degree of accuracy [6,14]. Then the element Δi(k) of Δ(k) can be expressed as()()()i i i k Ty k k ψδ=+ (12)where i= 1,…n, T n i R ψψ∈ is the column i of the optimal NN weightmatrix,1T n ψψψψ⎡⎤=⎣⎦…,.Activation functions ()()(),,Tn y k y k y k ψ⎡⎤=⎣⎦… represent the basis function vector, which can be selected as any one of Gaussian radial basis, B-spine basis, Wavelet basis, and etc. [14], and δi (k) denotes the element I of the NN reconstruction error vectork δ(k), namely()()()1,T n k k k δδδ=⎡⎤⎣⎦…, .Using compensation control law ()c u k , (9) can be written as ()()()()()()()221M q k s k M q k L f k s k +=-()()11ˆˆ,Tn n y k k ψψψψψψδ⎡⎤+--+⎣⎦… (13) Where ()ˆi k ψis the estimate of i ψ, and ()max sup i kk ψδδ=<∞ An estimate ()ˆi k ψis now obtained by minimizing the cost function ()()()()1112T J s k M q k s k =++ (14)After substituting (13) into (14), the gradient of the cost function in (14) is derived as()()1ˆT Jy k s k ψ∂=-+∂ (15) According to the gradient descent method the NN weight adaptation law can be designed as()()()()ˆˆ11T k k y k s k ψψα+=++ (16) with α > 0 . Then the compensation control law ()c u k in (11) can bewritten as()()()()()()()()2122211ˆˆTc s su k M k L I f k f k qk k y k T T ψ=--+ (17) In view of the case ()()12ˆˆ0I fk f k --≈ the term ()cu k can be simplified as()()()21ˆTc su k k y k T ψ=4. SIMULATION RESULTSConsider a planar, two-link, articulated manipulator as in [3] (as presented in Fig. 1), whose dynamics can be written explicitly as()1112111212212222210M M qq u hq h q q M M q q u hq --+⎛⎫⎛⎫⎛⎫⎛⎫⎛⎫+= ⎪ ⎪⎪ ⎪ ⎪⎝⎭⎝⎭⎝⎭⎝⎭⎝⎭Where122123242cos sin M M a a q a q ==++ 11132322cos 2sin M a a q a q =++ 222M a =3242sin cos h a q a q =-With 22211111c e e ce e a I m l I m l m l =++++,22e e ce a I m l =+31cos e ce e a m l l δ=,41sin e ce e a m l l δ=,111,1,2,30,e e m l m δ==== 110.12,0.5,0.25,c e I I I ===and 0.6ce l =. In the simulation, the sample time Ts = 2ms, the initial values and the parameters of the estimator and the controller are selected as P(0) =1×310I,λ(0) = 0.96 , μ0 = 0.98 , the anti -singularity factors(k) can be designed as ε(k) =5×610-exp(−kTs).According to the Property 2, the initial estimate values of the characteristicmodel coefficient matrixes are chosen as ()()12ˆˆ02,0f I f I ==-A basis set of activation function y(k) can be selected as in the Random Vector Function Link net [16], namely,()()()T y k V X k σ= (19) with V a randomly selected matrix and X(k) the NN input vector. ()σ∙can be chosen as the h yperbolic tangent function, and X(k) can be taken as()()()()(),1,,,1TT T T Td d X k q k q k q k q k ⎡⎤=-⎣⎦.The adaptation gain for the NN weight tuning is taken as α = 0.005 , and the initial values of the weights are set to zeros.The desired trajectory is chosen as()()()301cos 2,451cos 2T d q t t t ππ⎡⎤=--⎣⎦(20)外文翻译输入力矩受限的机器人鲁棒自适应控制摘要在输入力矩受限的情况下,提出一种全的简单鲁棒自适应控制算法。
自动化专业英语原文和翻译

自动化专业英语原文和翻译英文原文:Automation in the field of engineering has brought about significant advancements and revolutionized various industries. With the help of cutting-edge technology and innovative solutions, automation has become an integral part of many processes, increasing efficiency and productivity.In the field of automation engineering, professionals are responsible for designing, developing, and implementing automated systems and machinery. These systems are designed to perform tasks with minimal human intervention, reducing the risk of errors and improving overall performance.Automation engineering involves the use of various tools and technologies such as programmable logic controllers (PLCs), robotics, and computer-aided design (CAD) software. These tools enable engineers to design and control complex systems, ensuring smooth operations and optimal performance.One of the key benefits of automation in engineering is the ability to streamline processes and reduce manual labor. By automating repetitive tasks, engineers can focus on more complex and critical aspects of their work, leading to increased productivity and higher quality output.Moreover, automation plays a crucial role in enhancing safety in various industries. By replacing human workers with automated systems, the risk of accidents and injuries can be significantly reduced. Automated systems are designed to follow strict safety protocols and can perform tasks in hazardous environments that may be dangerous for humans.In addition to improving efficiency and safety, automation also offers cost-saving benefits. Although the initial investment in automation technology may be high, the long-term savings in labor costs and increased productivity outweigh the initial expenses.Automation can also lead to reduced material wastage and improved resource management.Automation engineering professionals play a vital role in the design and implementation of automated systems. They are responsible for conducting thorough analysis, developing system requirements, and ensuring seamless integration of automation technology into existing processes. They also provide technical support and troubleshooting expertise to address any issues that may arise.In conclusion, automation in the field of engineering has revolutionized various industries by increasing efficiency, productivity, and safety. Automation engineering professionals play a crucial role in designing and implementing automated systems, utilizing cutting-edge technology and innovative solutions. With the continuous advancements in automation technology, the future of engineering looks promising, with even greater possibilities for improved performance and streamlined processes.中文翻译:自动化在工程领域带来了重大的进步,并对各行各业进行了革命性的改变。
自动化专业毕业设计英文翻译--供水专用变频器的设计和应用

DESIGN AND IMPLEME.NTATION OF A VARIABLE FREQUENCY REGULATORY SYSTEM FOR WATER SUPPL YABSTRACTThe designs of the variable frequency constant pressure water supply for a single hydraulic pump and high power multiple hydraulic motors systems are presented in this paper. This system can save energy by controlling the speed of the pipe motors which depend upon the number of consumers in use. This system was also uccessfully implemented in most of the modern buildings in. Shanghai, China. Finally, the choice criteria for variable frequency regulators for water supply system will be discussed.INTRODUCTIONIt is inevitable to install high level water storage systems or reservoirs for a multiple story building or residential areas. This kind of system results in increasing construction cost and cleaning problems. Nevertheless, hydraulic pumps are used toraise the energy level of the water. The conventional high level reservoir system is in fact a pressure regulatory system. This pressure (head) is proportional to the height of the reservoir. Resistance of pipes is varying from time to time. When number of users increases, that means number of relief valves to be open is increased. It in turn reduces the resistance of the pipes. In order to reduce the construction cost, eliminate the cleansing problem of the high level reservoirs, and make the system simple, a variable frequency constant pressure closed loop system is presented to control the speeds of the hydraulic pumps.In this paper, the designs of the variable frequency constant pressure water supply for a single hydraulic pump and high power multiple hydraulic motors systems are presented. From static characteristics of water flow system, the critical point canbe obtained to achieve the minimization of energy consumed. The implementation of this system is also discussed. The choice of variable frequency regulators for water supply system is finally presented.ADVANTAGESOFTHEPROPOSEDSYSTEMIn short, the advantages of this proposed variable frequency constant pressure system for water supply are1. In a 3 hydraulic motors system, the capacity of the variable frequency regulator is just one-third of the capacity of the overall system. The cost is much reduced.2. Since the system consists of multiple pumping motors, they can be controlled by PLC such that the system is more reliable.3. Energy saving can be achieved by controlling the speed of pump motors, pressure can be kept constant no matter what water flow is (from zero to its maximum capacity)4. Each pumping imotor can be started smoothly by using this variable frequency regulator, it reduces pulse current. This kind of water supply system could become a new trend in modern multiple-story building design.PRINCIPLE OF OPERATIONThe principle of operation was initially illustrated by a single pump system. Fig. 1 shows a block diagram of a variable frequency constant pressure system which is suitable for single pump or small scale water flow system. The model type is JS.5-P1. The pressure sensor (PS) transducers the water pressure in pipes to e1ectrical signals. This signal will go to pressure regulator (PR) through an amplifier (A)and a comparator compared with the set value of waterpressure. The difference will come to the PID control to regulate the output frequency as well as the speeds of electric motors and hydraulic pumps. The constant pressure can then be achieved. Fig. 2 shows static characteristics of this constant pressure water supply system. Curves 1 and 2 represent relationship between the pressure head (H) and flow rate (Q) for different speeds of the pump. Curves 3 and 4 represent for different values of resistance of pipe. To simply the exposition, per unit values are adopted in the Fig. 2. Hence,H*=H/H N, Q*=Q/Q Nwhere H N and Q N are the set values of head and flow rate.In this system, both flow rate and the resistance of pipes are varying because the flow rate is proportional to number of valves to be opened. Curve 3 represents the resistance of pipe when the flow rate reaches the maximum point. It intercepts with the H* - Q* at point a , which is the set point for operation. Curve 4is for resistance of pipe when the flow rate is less and only part of valves to be opened.If there is no frequency regulator, it works at point b' only. At this moment, the head pressure exceeds the set value. The flow rate Q is proportional to the speed of the pump, n. Head pressure H is thus proportional to the square of the speed, n2. The speed of the pump can be controlled by the frequency regulator. It becomes the curve 2, which intercepts curve 4at point b, it is a new set (working) point. At this time, the set speed should be n*= n/nN = K (K<l). Obviously, the point b is lower than point b'. It in turn means that H at point b is less than that at point b'.Hb < Hb'It achieves the purpose of energy saving.FURTHER MODIFICATIONThis JSS-P1 model was suitable for single pump water supply system. When the flowrate is little, the pressure can be much reduced. For example, Hp* varies from 1 to Hp-* which is less than 1 (Hp-* < 1). It is able to save much energy. From thisworking principle, it was modified to suit a large scale multiple pumping water supply system. A new model of JS5-P2 was then developed. Fig. 3shows a block diagram of a variable frequency constant pressure system consisting of 3 same capacity pumps. It was modified from the JSS-P1 model. It is designed for multi- pumps water supply system which programmable logic control (PLC) is involved such that the number of hydraulic motors in operation can be determined by the flow rate. The rest of motors are in stand-by mode and the energy saving can be realized. From Fig. 3, the system was composed of pressure sensor (PS), pressure amplifier (A), pressure regulator (AP), signal identifier (AI), programmable logic control (PLC), and frequency regulator. The main feature of this system is that one set of variable frequency regulator is in use to control one hydraulic motor. The rest is idling at starting. If the water flow is within the preset range. This motor is running according its characteristic curve. When the flow rate is increased, The second motor will be smoothly started. The preset value of pressure in pipes can be maintained. There arethree values for operating these motors, 0-33.3%, 33.3-66.6% and 66.6-100%.In brief, the first pump motor will work if the flow rate falls within 33.3% of operation. The operating region is within curves 1 and 4in the Fig. 4.When the flow rate increases, beyond 33.3%, frequency regulator keeps the output frequency at 50 Hz, PLC will control of on-off state of the motors such that the first pump motor is supplied by the mains. The speed of the first pump motor runs at rated speed. The frequency regulator also set the second pump motor in stand-by mode. The operating region of the second motor is within curves 2and 5in the Fig. 4.When the flow rate is continuously increased and beyond 66.6%, and the frequency regulator reaches its rated frequency 50 Hz, PLC will command the second motor to connect to the mains again and the third one at stand-by mode. The operating region of the third one fallswithin curves 3and 6 in the Fig. 4. If the flow rate is reduced from 66.6% to 33.3%, PIX will command to one of the pump motors cut off from the mains. When the flowrate further reduces, and less than 33.3%, there will be only one motor connected to the mains. From the working principle, the three pump motors are operated in turnto meet the requirement of energy saving.CRITERIA FOR FREQUENCY, REGULATORFor the load of the hydraulic pump, the torque is proportional to the square of the motor speed, it is also proportional to the square of the supply frequency, f2. To a electric motor, the torque is equal to C m *Φm*I2*cosα, where C m, is a constant, Φm, is the magnetic flux of rotating field, I2 is the rotor current, and cosα is the power factor of rotor circuit. I2normally cannot exceed its rated value.If the voltage drop in the stator is negligible, $, will be proportional to supply voltage V. In order to maintain, the supply voltage V should be required to be proportional to the square of the frequency. Therefore, the characteristic of V versus f should be set to be a quadratic relationship.CONCLUSIONThis type of variable frequency constant pressure closed loop system for water supply was designed and implemented in Shanghai, China. The performance was proven satisfactory. A copy of a photograph of this system was shown in Fig. 5. All four advantages of this proposed system were fully realized. This system is one of the energy saving methods in tall building design.Automation System S7-300:Getting Started CPU 31xC: Commissioning1. Step: Installing the mounting rail and modulesRail installation sequenceFrom left to right: Power supply PS 307 - CPU 313C.The synopsis will provide you with an overview of the overall configuration.Install and ground the mounting rail1. Screw on the mounting rail (screw size: M6) so that at least 40 mm space remains above and below the rail. When mounting it on a grounded metallic panel or on a grounded device mounting panel made of steel sheet, make sure you have a low impedance connection between the mounting rail and the mounting surface.2. Connect the rail to the protective conductor. An M6 screw is provided on the rail for this purpose. Minimum cross-section from the cable to the protective conductor: at least 10 mm2. Installing modules on the mounting rail1. Hook the power supply module onto the rail, slide it until it reaches the grounding screw of the rail and then screw it tight.2. Hook the CPU onto the rail (1),slide it along as far as the module on the left (2), and swing it down into place (3).3. Bolt the CPU tight, applying a torque of between 0.8 and 1.1 Nm.4. Insert the micro memory card into the CPU (4); this is essential for operation. If you do not know the content of the micro memory card, erase it first on the programming device.2. Step: Wiring modulesWiring the power supply and the CPU1. Open the front panel covers of the power supply module and CPU.2. Unscrew the strain relief clamp on the power supply module.3. Remove the insulation from the power cord, attach the cable end sleeves (for stranded conductors), and connect them to the power supply.4. Screw the strain-relief assembly tight.5. Insert two short connecting cables between the power supply and the CPU and screw them tight.6. Check that the line voltage selector switch is set to the correct line voltage.The default line voltage setting for the power supply module is 230 VAC. To label a front connector, follow the steps outlined below: To change the voltage, remove the protective cap with a screwdriver, set the switch to the required line voltage and replace the protective cap. Wiring the front connectors of the DI and DO1. Open the right front panel of the CPU 313C.2. Place the front connector into wiring position. You do this by pushing a front connector into the CPU until it latches. In this position, the front connector still protrudes from the CPU. In the wiring position a wired front connector has no contact with the module.3. Remove 6 mm of the insulation from the ends of the wires that go into the front connector. Attach cable end sleeves to these ends.4. Wire the front connector (DI side) as follows:– Terminal 1: L+ of the power supply– Terminal 3: Button 1– Terminal 4: Button 2– Terminal 20: M of the power supply5. Wire the front connector (DO side) as follows:– Terminals 21 and 31: L+ of the power supply– Terminal 30: M of the power supply.6. Wire the free cable ends of the button with L+ of the power supply.7. Lead the wires downwards out of the front connector.8. Secure the front connector with the screws (this establishes contact with the module).9. Close the front panel covers of the power supply module and the front panel of the CPU.3. Step: Commissioning hardwareProcedure1. Use the PG cable to connect the programming device to the CPU. When using a cable with PROFIBUS connectors, remember to switch on the integrated terminating resistors. Close the front panel cover of the CPU, then set the mode selector switch on the CPU to STOP.2. Connect the mains cable, then switch on the power supply module PS 307.The DC24V LED on the power supply is lit. All the LEDs on the CPU light up briefly; the SF LED and the DC5V LED stay lit. The STOP LED then flashes slowly to indicate a CPU memory reset.3. Perform a CPU memory reset:– Turn the mode switch to MRES. Hold the mode selector at this position until the STOP LED lights up for the second time and then remains lit (approx. 3 seconds). Then release it.– You must press the mode switch back to MRES within 3 s. The STOP LED begins to flash rapidly and the CPU performs a reset. You can now release the mode switch.The CPU has completed the memory reset when the STOP LED remains permanently lit again.4. Start your programming device, then run SIMATIC Manager from your Windows Desktop.A window opens with SIMATIC Manager.5. Select button 1.The LED of I124.1 lights up. No DO LED lights up.6. Select button 2. The LED of I124.2 lights up. No DO LED lights up.4. Step: Programming the circuitProcedure1. Follow the instructions of the STEP 7 "New Project" wizard on the programming device and set up a new project with the following data:– CPU type: CPU 313C– Block to be created: OB 1– Project name: S7_Pro1A window, divided into two parts, opens with the title S7_Pro1 -- .2. Double-click the OB1 icon in the right-hand part of the window. The editor for editing the OB 1 block opens.3. In the "View" menu, select "LAD" to change to the ladder logic programming language. At the bottom of the left-hand window, a current path is displayed in network 1.4. Carefully click on the horizontal line representing the current path. The line is highlighted.5. On the toolbar, click twice on the --||-- icon (normally-open contact) and then once on the –( ) icon (coil). The icons are inserted into the current path.6. Click on the red question mark for the left-hand normally- open contact in the current path. The normally-open contact is highlighted and the question mark is replaced with a text input box containing the cursor.7. Enter I124.1 and press Return. The left-hand normally-open contact is now called I124.1.8. Label the right button in the same way with I124.2 and the coil with Q124.0.9. Close the editor and click Yes when you are prompted to save. The editor is closed and OB 1 is saved.5. Step: Configuring hardwareProcedure1. In SIMATIC Manager, click on SIMATIC 300 Station in the left-hand part of the window. The Hardware and CPU 313C icons appear in the right-hand part of the window.2. Double-click the Hardware icon in the right-hand part of the window.The editor for editing the hardware opens.3. If the catalog is not shown in the right section of the window, you can activate it by selecting Catalog in the View menu.4. Expand SIMATIC 300 and CPU-300 until you see CPU 313C.5. Insert the CPU 313C by dragging it to slot 2 (top or bottom left-hand window).6. Check that the order number displayed for slot 2 in the lower left-hand part of the window matches the order number of your CPU. You may need to expand the width of the order number column to see the entire number. If it does: Skip to the next step. If it does not: Expand CPU-300 in the catalog until you see CPU 313C and replace the CPU in slot 2 by dragging the CPU with the correct order number from the catalog.7. Perform steps 3 and 4 for the power supply module PS 307 too. You insert the PS 307 in slot 1.8. Go to the Station menu and select Save and compile. The hardware configuration is compiled and saved.9. Close the editor. The editor is closed.6. Step: Trial runProcedure1. Use the SIMATIC 300 station and CPU 313C to browse to the S7 program. In SIMATIC Manager click on Blocks in the right-hand part of the window. Blocks will now be highlighted.2. Select Download from the PLC menu to transfer the program and hardware configuration to the CPU. Confirm all windows with Yes. The program and configuration are downloaded from the programming device to theCPU. The program is now stored on the Micro Memory Card (in the load memory), where it is unaffected by power failures and resets.3. Set the CPU's mode switch to RUN. The STOP LED is switched off. The RUN LED starts to flash and then assumes a continuous signal.4. Press each of the buttons alternately. The LEDs of inputs I124.1 and I124.2 light up alternately. The LED of output Q124.0 is not lit.5. Press both buttons simultaneously. The LEDs of inputs I124.1 and I124.2 light up simultaneously. The LED of output Q124.0 is lit. This would switch on a connected finalcontrolling element or indicator.Further InformationDiagnostics/Correction of ErrorsWrong operation, faulty wiring or a faulty hardware configuration may cause errors which the CPU, CP or IE/PB-Link indicate with the SF group error LED after CPU memory reset. How to analyze such errors and alarms is described in the CPU31xC and CPU 31x operating instructions, Setup and Programming with STEP 7 manuals.Manuals containing further informationFor more in-depth Getting Started information, we recommend Getting Started and Exercises with STEP 7Service & Support on the InternetIn addition to our documentation, we offer a comprehensive online knowledge base on the Internet at:/automation/service&supportThere you can find:• A newsletter containing the latest information on your Siemens products.• The documents you need using our search engine in Service & Support.• the bulletin board, a worldwide knowledge exchange for users and experts.• your local contact for Automation & Drives in our contact database.• Information about on-site services, repairs, spare parts. You will find much more under "Services".第一部分供水专用变频器的设计和应用摘要:本文提出了一种用于变频恒压供水的单个液压泵和高功率多液压电机系统的设计方法。
自动化专业毕业设计--中英文翻译

中英文翻译Classification of control systems there are three ways: by automatic classification methods in order to participate in the control mode classification, to adjust the law category.One way to control category 1, the open-loop control system if the computer output of open loop control system to exercise control of the production process, but the control results --- the state of the production process does not affect the computer control systems, computer \ controller \ production and other sectors does not constitute a closed loop, is called open-loop control system computer. the production process of the state is no feedback to the computer, but by the operator to monitor the status of the production process, decision control program, and tell the computer to control the role of exercising control. 2, closed loop control system computer to the production of an object or process control, the state can directly influence the production process computer control system, called the closed-loop control system computer. Control of the computer monitor in the operator, the automatic acceptance of the production process state test results, calculate and determine the control scheme, the direct command and control units (devices) of action, the role of exercising control of the production process. In such systems, aircraft control components under control of control information sent to control device operation, the other running equipment condition as the output, measured by the detection part, the feedback as input to the control computer; to make control Computer \ Control Components \ production \ test components form a closed loop. We will call this form of control computer control closed-loop control. Closed loop control system computer, using a mathematical model to set the value of the production process and test results of the best value of the deviation between the feedback and control the production process to run at their best. 3, line control system as long as the computer controlled production of the controlled object or process, to exercise direct control, without human intervention are called the control computer on-line control, or on-line control system. 4, offline control system control computer does not directly participate in the control object or the controlled production process. It only managed to complete the process of the controlled object or the status of testing, and testing of data processing; and then develop control programs, the output control instruction, operator reference control instructions manually controlled operation to control parts of the object or subject control process control. This control form is called off-line computer control system. 5, real-time control system control computer real-time control system iscontrolled by the control of the object or process, or request when the request processing control, the control function in a timely manner to address and control systems, commonly used in the production process is interrupted for the occasion. Such as steel, each one refining furnace steel is a process; and if the process rolling, rolling out each piece of steel considered a process, each process is repeated. Only enter the process only requires a computer control. Once control of the computer, it requires a computer from the production process information in the required time to respond to or control. Such systems often use sophisticated interrupt system and interrupt handling procedures to achieve. In summary, an online system is not necessarily a real-time system. But a real-time system must be an online system.Second, in order to participate in the control mode to Category 1, direct digital control system by the control computer to replace conventional analog instruments and direct regulation to control the production process, as the computer as digital signals, so named after the DDC control. Actually controlled the production process control components, control signals received by the process controller input / output channels of D / (D / A) converter output of the digital control computer volume to be converted into analog; analog input control machine to go through the process of input / output channels of analog / digital (A / D) converter into a digital number into the computer. DDC control systems often use a small computer or microprocessor, the time-sharing system to achieve multiple points of control. Is in fact a discrete sampling with the controller, to achieve discrete multi-point control. DDC computer control system that has become the main control computer control system forms. DDC control of the advantage of flexibility, large, focused on high reliability and low cost. Can use several forms of digital computing circuits, or even dozens of loop production process, integral to proportional --- --- differential (PID) control to maintain the industrial state of the controlled object at a given value, the deviation small and stable. And as long as the change of control algorithms and applications can achieve more complex control. Such as feedforward control and the best control. Under normal circumstances, DDC-level control often more complex as the implementation of advanced control level. 2, supervisory computer control system supervisory computer control system for a particular production process, according to the production process of various states, according to the production process of the mathematical model to calculate the best production equipment should be running a given value, and the best value automatically or manually on the DDCExecutive-level computer or analog meter to align the regulation or control of the target set. By a DDC or adjust the instrument at various points on the production process (running equipment) to exercise control. SCC system is that it can guarantee the production process is always controlled the situation in the best condition to run, so get the most benefit. SCC results directly affect the merits of the first of its mathematical model, this should always improve the operation process model, and modify the control algorithm, and application control procedures. 3, multi-level control systems in modern manufacturing enterprises in the production process not only the need to address the problem of online control, and Huan Zhi Li called for a solution of production problems, the daily product line, the number of arrangements for planning and scheduling, and Rose plans develop a long term planning, notice Xiaoshou prospects, there was multi-level control system. DDC class is mainly used for direct control of the production process, for PID, or feedforward control; SCC level is mainly used for optimal control or adaptive control or learning control calculation, and command and control the same DDC class report back to the MIS class. DDC level usually microcomputers, SCC-level general use of small computers or high-end microcomputers. MIS Workshop main function of governance is based on plant-level production of varieties issued, the number of orders and collect up the production process of the state of information, at any time reasonable schedule to achieve optimal control, command and SCC-level supervisory control. Factory management level MIS main function is to accept the company and factory production tasks assigned by the actual situation of optimized computing, Zhi Ding factory production plans and short-term (ten days or weeks or days) arrangements, and then issued to the plant-level production tasks. Corporate governance level MIS main function is to guess the market demand computing to develop strategic long-term development planning, and contract orders, raw material supply situation and the production conditions, comparison of the optimal production program selection and calculation, work out the entire company business a long time (months or ten days) of the production plan, sales plan, assigned to the task of the factory management level. MIS-level main function is to achieve real-time information processing, decision-makers at all levels to provide useful information, make on the production planning \ scheduling and management programs to plan the coordination and management control in the optimal state. This one can control the size and scope of enterprise size divided into several levels. Each level has to be addressed accordingto the size of the amount of information to determine the type of computer used. MIS generally use small computer shop class or high-grade micro-computer, the factory management level of the MIS with a medium-sized computer, and corporate governance level MIS is to use large-scale computer, or use super computer. 4, distributed control or distributed control system distributed control or distributed control, the control system is divided into a number of independent local control subsystems to complete the controlled production process control task. Since the emergence of micro-computers and rapid development of distributed control to provide for the realization of the material and technical basis, in recent years, decentralized control can be different almost normal development, and has become an important trend in the development of computer control. Since the 70's, appeared focused on distributed control system, called DCS. It is a decentralized local control of the new computer control system.Three, classified according to the law regulating 1, program control if the computer control system the division of a predetermined time function control, such control is called program control. Such as the furnace temperature-time curves Anzhao some control on the process control. Here the procedure is time-varying changes have to determine the corresponding value, rather than the computer running. 2, sequence control in the process control based on the generated sequence control, computer, over time, as can be determined according to the corresponding control value and previous results at the moment both to exercise on the production process control system, called the order of the computer control . 3, proportional - integral - differential analog PID control regulation of conventional PID control instrument can be completed. Micro-computer can also be achieved with PID control. 4, feedforward control is usually the feedback control system, have certain effects on the interference in order to generate feedback over the role of inhibitory control of interference, and thus delay the control of undesirable consequences. In order to overcome the negative lag control, with the computer accepts the interference signal after the, did not produce effects in the Huan insert a feedforward control Zuoyong, it Ganghao interference point in the interference of the control to completely offset the effect on the variable, it was Ming Wei Yin Er disturbance compensation control. 5, optimal control (optimal control) system control computer, such as to have controlled object is best known as the best run of the control system control system. Such as computer control system is limited in the existing conditions, select appropriate control law(mathematical model), the controlled object indicators in optimal running condition. Such as the largest output, consumption of the largest, highest quality standards, such as the least scrap rate. Best is determined by a set of mathematical models, sometimes several in a limited range of the best indicators of the pursuit of individual, sometimes the best indicators of comprehensive requirements. 6, the adaptive control system, optimal control, when the working conditions or qualifications change, we can not get the best control effects. If the situation changes in working conditions, the control system can still be controlled in the best state of the object's control, such control system called the adaptive system. This requires mathematical model reflects the change in the conditions, how to achieve the best state. Control computer to detect changes in terms of the information given by the laws of mathematical models to calculate, to change the control variables, the controlled objects still in the best condition. 7, self-learning control system if the computer can keep the results under the controlled object gain experience running their own change and improve the control law so that more and better control effect, this control system is called self-learning control system. Above mentioned optimal control, adaptive control and self-learning control are related to multi-parameter, multi-variable complex control systems, are all problems of modern control theory. Determine the stability of the system, many factors affect the control of complex mathematical models, have to be a production control, production technology, automation, instrumentation, programming, computer hardware, each with various personnel to be realized. Controlled object by the length of reaction time required to control the number of points and mathematical models to determine the complexity of the computer use scale. Generally speaking, a strong need to functionality (speed and computing power) of the computer can be achieved. The Zhuzhong control, can be a single type also is not single, you can combine several forms to achieve control of the production process. This should address the actual situation of the controlled object, the system analysis, system design determined at the time.Keywords :open the control,closed loop control控制系统的分类有三种方法:以自动控制方式分类、以参于控制方式分类、以调节规律分类。
自动化专业毕业设计外文翻译--走进数字博物馆展览智能化:模块化的框架,艺术审美的超媒体

毕业设计(论文)外文文献翻译译文一:文献出处:Int J Digit Libr (2004) 4: 64–68/Digital Object Identifier (DOI)10.1007/s00799-003-0059-3走进数字博物馆展览智能化:模块化的框架,艺术审美的超媒体摘要在目前基于Web的超媒体环境下,建设和维持一个大规模的互动展览超媒体是一项艰巨的任务。
特别是编排风格繁多的多媒体创作,非常费时费力。
我们把发展智能数字博物馆展览系统作为第一步,本文提出了一种细粒度的模块化框架即分解一个典型的超媒体造型并将其介绍成细粒式模块(FGSM)。
一个基于“单声道媒体处理程序”的超媒体文档和一个数字博物馆展览管理框架已经被设计出来用以帮助我们理解FGSM的概念。
我们已经实施了基于Web的创作系统,允许内容提供商能够有效地构建起集媒体中心,互动性,美观于一体的超媒体网站。
今后,有关的优化和约束求解技术将用来最终实现数字博物馆智能展览的目标。
关键词:数字博物馆;展览;超媒体1.简介“博物馆是人们能够探索灵感,学习和享受的地方。
他们是机构收集,维护和访问,通过文物标本展现他们的社会。
”一个博物馆的基本任务包括收集,保存,研究和教育。
所有这些活动汇集在博物馆展览的公共展坛,目前这些都是博物馆对公众的主要吸引力。
同样,数字博物馆也是意料中必须建设的大型虚拟展览,实现高层次出席。
虚拟展览的主题基本上是一个编舞介绍数位典藏文物。
不论对身体还是虚拟博物馆展览的发展都是一个多学科的任务,通常需要观众专家,内容专家,通信专家和技术专家的积极参与。
由于参观者对博物馆的欣赏模式展览包括思考,理解,发现的相互作用,虚拟展览设计预计将超越只是提供单调平原网页的最终用户。
相反,考虑到美学展览需要提供先进的多媒体演示。
数字博物馆展览网站还必须考虑信息技术可用性优势,提高参与一个互动的个人设置。
然而,在当前基于Web的超媒体环境中,建设和维持一个大规模的吸引力展览的互动超媒体是复杂和困难的。
自动化专业英语原文和翻译
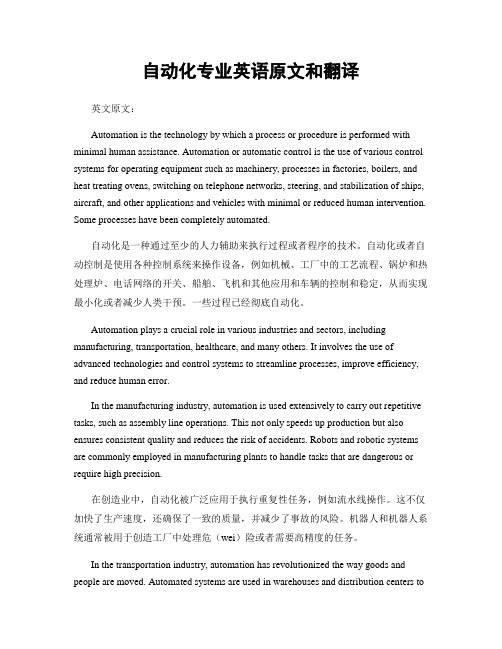
自动化专业英语原文和翻译英文原文:Automation is the technology by which a process or procedure is performed with minimal human assistance. Automation or automatic control is the use of various control systems for operating equipment such as machinery, processes in factories, boilers, and heat treating ovens, switching on telephone networks, steering, and stabilization of ships, aircraft, and other applications and vehicles with minimal or reduced human intervention. Some processes have been completely automated.自动化是一种通过至少的人力辅助来执行过程或者程序的技术。
自动化或者自动控制是使用各种控制系统来操作设备,例如机械、工厂中的工艺流程、锅炉和热处理炉、电话网络的开关、船舶、飞机和其他应用和车辆的控制和稳定,从而实现最小化或者减少人类干预。
一些过程已经彻底自动化。
Automation plays a crucial role in various industries and sectors, including manufacturing, transportation, healthcare, and many others. It involves the use of advanced technologies and control systems to streamline processes, improve efficiency, and reduce human error.In the manufacturing industry, automation is used extensively to carry out repetitive tasks, such as assembly line operations. This not only speeds up production but also ensures consistent quality and reduces the risk of accidents. Robots and robotic systems are commonly employed in manufacturing plants to handle tasks that are dangerous or require high precision.在创造业中,自动化被广泛应用于执行重复性任务,例如流水线操作。
- 1、下载文档前请自行甄别文档内容的完整性,平台不提供额外的编辑、内容补充、找答案等附加服务。
- 2、"仅部分预览"的文档,不可在线预览部分如存在完整性等问题,可反馈申请退款(可完整预览的文档不适用该条件!)。
- 3、如文档侵犯您的权益,请联系客服反馈,我们会尽快为您处理(人工客服工作时间:9:00-18:30)。
成绩:*******大学毕业设计 (论文)英文翻译院(系):*******专业班级:******毕业设计论文方向:计算机过程控制翻译文章题目:一种新的PID加前馈控制器设计学生姓名:*****学号: *****指导教师:******2012年 4月10 日一种新的PID加前馈控制器设计摘要本文中提出,一个新的PID加前馈控制器的设计和调整过程。
它包括确定一个假设一阶加死区时间模型前馈信号,以实现预定义的过程输出的过渡时间的过程。
然后,PID参数整定,以确保良好的负载扰动抑制和任何常规方法闭环系统的参考信号获得通过过滤适当的设定点的阶跃信号。
仿真和实验结果表明,该方法优于典型的(反)基于模型的方法,由于其简单,因此,适合在分布式控制系统,以及在单基站控制器来实现。
关键词:过程控制;PID控制;前馈控制;调整;1. 介绍比例 - 积分 -微分(PID)控制器,由于能够达到良好的成本/效益比,所以是控制器行业最为广泛使用的。
事实上,由于他们的易用性,他们可以在一定宽的范围内提供令人满意的性能。
自动整定技术已经开发,以帮助操作员选择适当的参数值,在这种方式下,使用它们所需的专业知识也越来越少。
然而,众所周知,这些控制器的性能很大程度上取决于,除了PID参数的整定,适当实施这些额外的功能,如反饱和,集点过滤,前馈等。
在当下,高效的设计这样一个功能的方法越来越容易实现,这都归因于在集散式控制系统(DCS)以及在单基站控制器的计算能力的提升。
在任何情况下为了维护使用控制器的方便性,这些功能应该尽可能对是用户透明的,或者说是直观地。
在此背景下,本文提出了一种新的PID加前馈控制器的设计方法。
事实上,对于PID控制器,虽然调节往往是首要关注的,但同时,在许多应用中,实现一个高性能的设定值后的工作也很重要。
为了解决这个问题,典型的做法是采用两度自由控制器,也就是采用前馈补偿器(线性的)。
众所周知的的集点加权策略的使用属于这个框架。
这种方法的主要缺点是减少超调,是以较慢的给定响应为代价的。
为了克服这一缺点,通常使用一种基于逆模型前馈响应(见第2.1节及图1)。
另外,也已经提出了使用一个变量的设定点权重。
但必须指出,在这种情况下,调节和伺服控制性能不可能更加独立,而且整体控制方案设计更为复杂。
实际上,众所周知,在设定点以下性能的显著改善可以通过采用非线性前馈行动,正如所示,其中一项由Bang-Bang控制策略激发了的技术实现了设定点变化的快速响应。
本文提出的方法采用了非线性目的是当设定点需要改变时获得一个用户自定义的前馈行动过程输出的过渡时间。
该技术依赖于假设一个一阶加死区时间(FOPDT)过程模型并为预定义的输出过渡时间运用一个确定的值恒定的信号。
然后,为了应付不可避免的模型不确定性,PID参数的整定目的是确保良好的负载抗扰性能,而且给定闭环信号取决于适当过滤给定阶跃信号。
在这种方式中,在设定点以下,不损害去负荷能力的情况下获得高性能。
必须强调的是,这篇文章的目的是提出一种基于模型的前馈的控制行为的设计方法,而不是派生条件应用这样一个前馈的行为(关于模型的不确定性),这样的目的是有益的。
对于后者问题的标准方法在当前的工业背景下根本不存在,尽管有显著的结果已经在最近的文献中呈现。
本文组织如下:在第2节,总体方法会进行详细解释,说明例子会在第3节中描述,而实验结果在第4节和结论在最后一节进行总结。
2. 方法论2.1. 前馈设计拟议方法的目的是设计一个基于PID控制器加前馈术语旨在实现过程输出y值从Y0到Y1在持续时间S中间隔时间的过渡。
在下面,为清晰起见,不失一般性,将承担从Y0=0,Y1> 0。
通常情况下,一个PID加前馈控制方案,目的是提高设置点响应,按图 1所示的方案能够实现。
其中M (S )是一个参考模型,它提供了设定值变化所需的响应,同时G(S)被认为是()G(S)=()M S PS其中,()Ps 是过程传递函数P(S)的最小相位部分。
新设计的PID 加前馈控制方案如图2,同时实现了以下的方法:首先,这个过程是由FOPDT 模型描述,即:()1Is K P s e Ts -=+ 许多不同的方法(例如著名的面积法)已经制定,目的是通过一个简单的鉴别实验来确定的模型参数(见例[2,11])。
在此模型基础上,前馈模块FF 的输出ff u 定义如下:ff u 值是确定的,琐碎的计算后,在这样一种方式的过程输出y 在t L τ=+时是y1。
结果是:这样,如果这一过程完全由模型(2)描述,输出的过渡时间间隔在[L ,τ+L]间发生然后,在t τ≥时假设恒定值为()ff u t 的情况下,在t L τ=+时刻,输出值定为y1。
为了应付不可避免的模型不确定性和负载扰动,必须提供反馈动作。
这是通过执行一个PID 控制器来完成的,它的整定过程在2.2节讨论中有讨论。
然后,一个合适的参考信号f y 必须被应用到闭环系统,期望的f y 等于将获得期望的的过程输出以防此过程完全仿照式(2)中的来完成。
因此,幅值y1的阶跃参考信号sp y 必须被系统过滤。
1()1ffIs Ku y F s e Ts -=+ 然后饱和在y1的水平。
注1.新方法利用这样一个事实:输出要求过渡过程,而不是跟踪一般的参考信号。
后一种情况的典型控制图方案1必须被采纳。
注2.从实用的角度来看,直接过渡时间τ可以由用户直接或通过(可能)更直观的推理而获得。
例如,用户可能会选择一个开环系统的带宽和闭环系统的带宽之间的比,通过这样τ值可以轻松确定。
显然,减少的τ值意味着UFF 值(而且因此整体操纵变量)增加,太低的τ值可能意味着确定的控制变量由于执行器的饱和不能被应用。
因此,另外,运营商可能会根据所需的控制力度首选ff u 的值(定义的ff u 通常作为一个操纵变量上限的百分比)并最终确定τ值。
注3.以防在瞬态响应中新的设定点值被选中,这足以为新值确定前馈动作并对当前应用进行总结。
类似地,最新的设定值变化决定ff u 的参考信号必须归结到一个和前一个相关的(见第3节)。
注4.请注意,参数τ能够处理的性能,稳定性和控制活动之间的权衡问题。
这被认为是一个整定过程中非常有用的功能,因为它在公式本身整定的物理意义方面给出了一个宝贵的见解,因此,操作者可以很容易地适应特定应用。
2.2. 鲁棒性和PID 设计由于前馈的动作是基于一个简单的FOPDT 工厂的模型,鲁棒性问题必须要进行讨论。
建模误差的补偿留给反馈PID 控制器。
在这方面,考虑[7],其中的分析是非常有用的,它表明,由于期望与实际输出之间的误差导致的建模的偏差可以被视为一个负载扰动的影响。
()()()(1()()),()d P s F s G s P s C s P s -=+ 其中,C (s )是PID 控制器的传递函数(见(6))。
因此,考虑过程的输出是前馈的影响叠加动作和负载扰动的结果(即真正的负载扰动和因为建模误差而产生的一个“虚拟”的d )和考虑在标称情况下,设定点以下的性能只由前馈的动作决定,在考虑到其加载抗扰性能的情况下进行PID 控制器的整定是明智的。
例如,可以使用众所周知的Ziegler-Nichols 整定规则[2]。
3. 举例说明在展示实验结果之前,2个说明型例子是为了更好地评估提出的方法,以便更好地与2.1节中提到的标准技术进行比较。
请注意,这一分析的目的是要表明,拟议的技术在设计一种基于模型的前馈控制方案中是有效的,而不是展示当使用基于模型的前馈动作很方便。
在这两个例子中,假设y1 =1,即在ţ=0时刻,被应用于YSP 的单位阶跃信号的响应能被估计到。
被采用的PID 控制器用下面的传递函数来描述:1()(1),1d p d i T s C s K T T s s N=+++ 其中,N = 10,比例增益KP ,积分时间常数Ti 和微分时间常数Td 根据著名的基于阶跃响应的齐格勒 - 尼科尔斯公式整定而来[2]。
3.1. 例一一个FOPDT 系统被认为是:0.51()1s P s e s -=+ 而且过渡时间已被选定为τ =0.5秒。
通过提出公式(4),我们得到ff u = 2.54,即前馈信号()ff u t ,当00.5t ≤<时等于2.54,0.5t s ≥时等于1。
请注意在这种情况下,过程被完美地模仿,我们得到了PID 控制器的输出当0t s ≥时为0,即参考信号f y ,因为闭环系统与所获得的过程的输出是等价的。
为了比较,图1的经典控制方案也被应用到相同的过程。
通过选择0.51()0.51sM s e s -=+ 我们得到(看(1))1().0.51s G s s +=+ 产生的前馈信号和过程输出也在图 3(虚线)中显示。
此外,在此例中PID 控制器在0t s ≥时的输出是零,这是因为没有模型的不确定性。
似乎通过新方法建立时间已经缩短了五倍左右,这很明显,因为在经典控制方案中,0.5作为整个系统的时间常数(这是第一顺序),而不是实际的过渡过程时间。
为了更好地评估结果的意义,已经通过将参考模型的时间常数值设定为5τ来实施方便的控制方案,即: 0.511(),()0.110.11s s M s e G s s s -+==++ 结果再次显示在图 3中(虚线点线)。
从这可以看出,设定的时间值与获得的新方法在这个例子中已经通过多增加的控制力度而取得了成功。
从结果中提出,显而易见的,通过采取一个简单的非线性前馈动作使得性能显着提高(尽管对用户没有额外的设计工作)。
实际原因明显的可以看到,是为了得到实现所需的过程输出过渡所需的时间,信号才保持在一个恒定的水平,但这个结果通过一个线性的前馈动作是不能得到的。
为了更好地了解设计的方法,也给出了在一个暂态响应中改变设定点值的例子(见备注3)。
具体来说,在时间t=0.25,设置点的值从1变为2。
在相同的情况下,过程输出和控制变量在图 4中可以看到(注意,PID控制器的输出对于每个控制方案来说仍然是零)。
再次看出,新方法能够基本实现和经典控制同样的结果,而且相对更加简洁。
最后,这个例子中,在设定点响应进行估计时有负载扰动发生。
特别地,在时间t =0.1,阶跃扰动的振幅0.5被应用到控制变量。
PID控制器增益KP =2,TI = 1和Td= 0.25(注使用为了避免控制变量中的过多的振荡减少了Ziegler-Nichols公式中的比例增益)。
有关新方法的结果在图5中显示。
值得再次强调的是,由此产生的过程输出(和操纵变量)是一个无负载扰动(见图3)和一个只在负载存在时发生的输出(即具有恒定的设定点值)的叠加。
应用于经典方法和结果的同样的考虑,为了简洁就不再显示。
3.2. 例2作为第二个例子,一个带死区时间的四阶过程已经得到解决:0.541().(1)s P s e s -=+ 运用面积法,它的结果为:K =1,T=2.12,L 为2.38。