干法刻蚀技术的应用与发展
干法刻蚀技术

干法刻蚀技术干法刻蚀技术是一种常用于微纳加工领域的表面加工技术。
它通过利用化学反应或物理作用,将材料表面的一部分物质去除,从而实现对材料的精确加工和微纳结构的制备。
干法刻蚀技术具有高精度、高效率和可重复性等优点,因此在微电子、光学器件、生物医学和纳米材料等领域得到广泛应用。
干法刻蚀技术主要包括物理干法刻蚀和化学干法刻蚀两种方式。
物理干法刻蚀是利用物理能量对材料进行刻蚀,常见的方法有离子束刻蚀和反应离子刻蚀。
离子束刻蚀是利用高能离子束对材料表面进行轰击,使表面原子或分子脱离并被抛射出去,从而实现刻蚀效果。
反应离子刻蚀则是在离子束刻蚀的基础上引入反应气体,使离子与气体发生化学反应,增加刻蚀速率和选择性。
化学干法刻蚀是利用化学反应将材料表面的物质转化为气体或溶液,从而实现刻蚀效果。
常见的化学干法刻蚀方法有湿法刻蚀和等离子体刻蚀。
湿法刻蚀是将材料浸泡在特定的腐蚀液中,通过化学反应溶解材料表面的物质。
等离子体刻蚀则是利用等离子体中的高能粒子对材料表面进行刻蚀,其刻蚀速率和选择性可以通过调节等离子体参数进行控制。
干法刻蚀技术在微纳加工中具有广泛的应用。
在微电子领域,干法刻蚀技术被用于制备集成电路中的细微结构,如晶体管和电容器等。
在光学器件制造中,干法刻蚀技术可以用于制备光纤、光栅和微透镜等微结构。
在生物医学领域,干法刻蚀技术被应用于制备微流控芯片和生物传感器等微器件。
此外,干法刻蚀技术还可以用于制备纳米材料,如纳米线、纳米颗粒和纳米孔等。
干法刻蚀技术的发展离不开对材料表面和刻蚀过程的深入研究。
科学家们通过对材料表面的分析和刻蚀机理的探索,不断改进和优化干法刻蚀技术,提高其加工精度和效率。
同时,随着纳米科技的快速发展,对于更小尺寸和更高精度的微纳结构的需求也在不断增加,这对干法刻蚀技术提出了更高的要求。
干法刻蚀技术作为一种重要的微纳加工技术,在各个领域都发挥着重要作用。
通过不同的刻蚀方式和参数的调节,可以实现对材料的精确加工和微纳结构的制备。
drie干法蚀刻原理
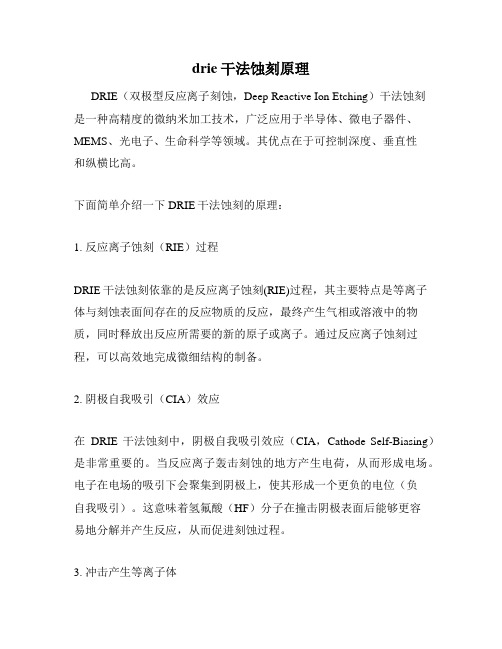
drie干法蚀刻原理DRIE(双极型反应离子刻蚀,Deep Reactive Ion Etching)干法蚀刻是一种高精度的微纳米加工技术,广泛应用于半导体、微电子器件、MEMS、光电子、生命科学等领域。
其优点在于可控制深度、垂直性和纵横比高。
下面简单介绍一下DRIE干法蚀刻的原理:1. 反应离子蚀刻(RIE)过程DRIE干法蚀刻依靠的是反应离子蚀刻(RIE)过程,其主要特点是等离子体与刻蚀表面间存在的反应物质的反应,最终产生气相或溶液中的物质,同时释放出反应所需要的新的原子或离子。
通过反应离子蚀刻过程,可以高效地完成微细结构的制备。
2. 阴极自我吸引(CIA)效应在DRIE干法蚀刻中,阴极自我吸引效应(CIA,Cathode Self-Biasing)是非常重要的。
当反应离子轰击刻蚀的地方产生电荷,从而形成电场。
电子在电场的吸引下会聚集到阴极上,使其形成一个更负的电位(负自我吸引)。
这意味着氢氟酸(HF)分子在撞击阴极表面后能够更容易地分解并产生反应,从而促进刻蚀过程。
3. 冲击产生等离子体DRIE干法蚀刻采用了高能量电离辉光放电(HEDP)的方式产生等离子体。
这种放电方式可以使气体在较低的压力下进行电离,从而产生高浓度的反应物,以保持较高的刻蚀速率和质量。
4. 双极金属反应DRIE干法蚀刻使用阴极和阳极的双金属反应体系,这种体系可以形成一种稳定的化学反应,可以产生氟化物(F^-)和钨酸根(WO4^-2 )等反应物,以加速刻蚀过程。
在DRIE干法蚀刻过程中,通过调节工艺参数如气体流速,功率密度等,可以控制反应离子轰击材料表面的能量和反应速率,有效地实现高精度加工的控制。
总之,DRIE干法蚀刻的原理是基于反应离子蚀刻、阴极自我吸引效应、等离子体和双极金属反应体系。
可以实现高精度和高质量的微纳米结构制备,是微纳加工领域中的一项重要技术。
drie干法蚀刻原理
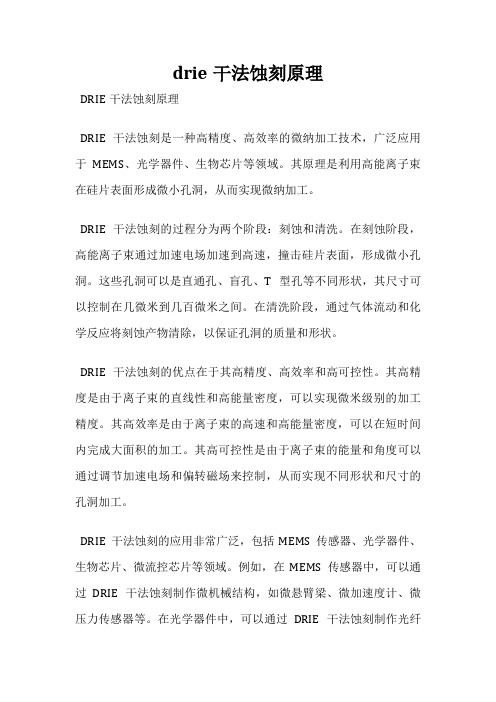
drie干法蚀刻原理
DRIE干法蚀刻原理
DRIE干法蚀刻是一种高精度、高效率的微纳加工技术,广泛应用于MEMS、光学器件、生物芯片等领域。
其原理是利用高能离子束在硅片表面形成微小孔洞,从而实现微纳加工。
DRIE干法蚀刻的过程分为两个阶段:刻蚀和清洗。
在刻蚀阶段,高能离子束通过加速电场加速到高速,撞击硅片表面,形成微小孔洞。
这些孔洞可以是直通孔、盲孔、T型孔等不同形状,其尺寸可以控制在几微米到几百微米之间。
在清洗阶段,通过气体流动和化学反应将刻蚀产物清除,以保证孔洞的质量和形状。
DRIE干法蚀刻的优点在于其高精度、高效率和高可控性。
其高精度是由于离子束的直线性和高能量密度,可以实现微米级别的加工精度。
其高效率是由于离子束的高速和高能量密度,可以在短时间内完成大面积的加工。
其高可控性是由于离子束的能量和角度可以通过调节加速电场和偏转磁场来控制,从而实现不同形状和尺寸的孔洞加工。
DRIE干法蚀刻的应用非常广泛,包括MEMS传感器、光学器件、生物芯片、微流控芯片等领域。
例如,在MEMS传感器中,可以通过DRIE干法蚀刻制作微机械结构,如微悬臂梁、微加速度计、微压力传感器等。
在光学器件中,可以通过DRIE干法蚀刻制作光纤
阵列、光栅、微透镜等。
在生物芯片中,可以通过DRIE干法蚀刻制作微孔阵列、微通道、微阀门等。
DRIE干法蚀刻是一种非常重要的微纳加工技术,其原理简单、操作方便、加工精度高,可以满足不同领域的微纳加工需求。
干法刻蚀
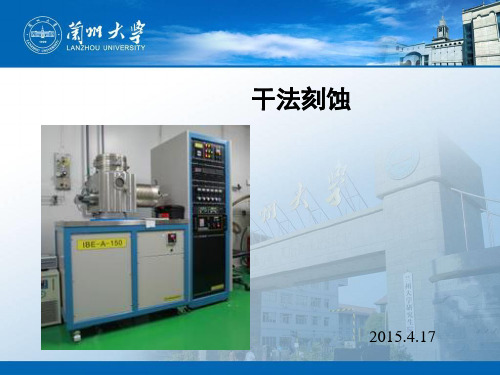
2
干法刻蚀技术的分类
物理化学刻蚀:
物理和化学混合作用的机理可以理解为离子轰击改善化学刻蚀作用。加入离子 撞击的作用:一是将待蚀刻物质表面的原子键结破坏,以加速蚀刻速率;二是 将再沉积于待蚀刻物质表面的产物或聚合物打掉,以便待蚀刻物质表面能再与 反应蚀刻气体接触
3
典型的干法刻蚀模式及原理
离子束刻蚀(IBE):
3
典型的干法刻蚀模式及原理
电感耦合等离子体刻蚀(ICP):
ICP系统有2个独立的射频电源 RF1和RF2,一个接到反应室外 的电感线圈,另一个接反应室 内的电极。给反应室外的线圈 加压时,反应室内产生交变的 电磁场,当电场达一定程度时, 气体产生放电现象,进入等离 子态,交变的电磁场使等离子 体中电子路径改变,增加等离 子体密度
3
典型的干法刻蚀模式及原理
GaAs刻蚀
GaN刻蚀
3
典型的干法刻蚀模式及原理
RIE与ICP比较:
RIE 离子密度低( ~109 ~1010/cm3) 离子密度与离子能量不能分别控 制 离子能量低,刻蚀速率低 低压下刻蚀速率低 DC Bias损伤大 ICP 离子密度高(>1011/cm3)(刻蚀速率 高) 离子密度由ICP功率控制,离子能 量由RF功率控制 在低离子能量下可控离子流量达 到高刻蚀速率 低压下由于高离子流量从而维持 高刻蚀速率 DC Bias损伤小
干法刻蚀
2015.4.17
1
2 3
刻蚀技术中的术语
干法刻蚀技术的分类
典型的干法刻蚀模式及原理
4
干法刻蚀技术的应用
1
刻蚀技术中的术语
刻蚀
用物理的、化学的或同时使用化学和物理的方 法,有选择地把没有被抗蚀剂掩蔽的那一部分 材料去除,从而得到和抗蚀剂完全一致的图形
光学材料的干法刻蚀研究
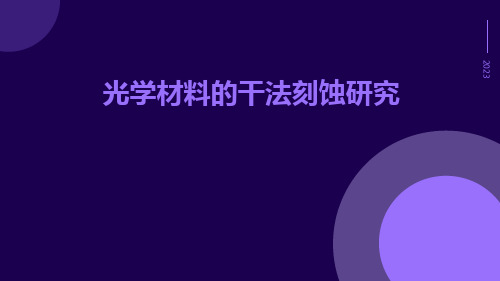
2023
光学材料的干法刻蚀研究
CATALOGUE
目录
引言干法刻蚀技术的基础理论光学材料的干法刻蚀过程研究光学材料干法刻蚀的损伤及表征光学材料干法刻蚀的优化策略结论与展望
01
引言
1
课题背景及意义
2
3
光学材料在通讯、能源、环境、安全等领域应用广泛,提升其加工质量和效率具有重要意义
干法刻蚀技术以其优点在光学材料加工中具有重要应用价值
研究不足及改进空间
需要深入研究干法刻蚀技术的反应机制,以提高刻蚀过程的可控性和重复性。
针对不同类型的光学材料,需要进一步探索更加优化的刻蚀工艺参数和气体选择。
加强干法刻蚀技术在实际生产中的应用研究,实现大规模工业化生产。
研究干法刻蚀技术的环保和节能减排措施,促进可持续发展。
未来需要进一步深入研究干法刻蚀技术的反应机制、物理模型和数值模拟方法,以提高刻蚀质量和加工效率。
探索新型光学材料的干法刻蚀技术,以及与其他先进制造技术的结合应用。
未来研究展望
THANK YOU.
谢谢您的观看
刻蚀后,光学材料表面的态密度也会发生改变,影响表面的浸润性和光学性能。
表面态密度变化
干法刻蚀对光学材料表面的损伤
透射率变化
刻蚀会改变光学材料的光透射率,影响其在特定波长范围内的透射性能。
干法刻蚀对光学材料性能的影响
折射率变化
刻蚀会改变光学材料的折射率,从而影响光的传播速度和方向。
机械强度变化
刻蚀过程中可能会对光学材料的机械强度造成影响,降低其耐磨、耐压等性能。
研究光学材料的干法刻蚀技术对提升应用领域性能和效率具有重要意义
研究光学材料的干法刻蚀机制及工艺,提升刻蚀质量和效率
干法蚀刻原理

干法蚀刻原理干法蚀刻是一种基于化学反应进行材料加工的技术,通过气相中的化学反应来控制材料表面的加工,是一种高精度微纳加工技术。
干法蚀刻主要应用于半导体和微电子制造工艺中,可以用于制备芯片、微电子器件、MEMS和光学器件等。
干法蚀刻原理是基于气相反应原理,主要是通过离子束或者反应性气体在材料表面发生的化学反应来实现微观结构的加工。
在干法蚀刻中,反应气体一般为电离态,进入蚀刻室后被加速成高能量离子束,然后当离子束撞击目标材料表面时,会产生能量转移,从而使目标材料表面的化学键发生断裂产生反应。
当反应物进一步扩散到目标材料表面时会发生化学反应,生成新的化合物并释放气体产物。
这个过程中材料表面产生了各种化学反应,从而产生了微观的空洞和分子结构变化,实现了微细结构加工的效果。
干法蚀刻技术主要分为两种类型:物理性干法蚀刻和化学性干法蚀刻。
物理性干法蚀刻主要是利用粒子束对材料表面进行削除加工,常用的物理性干法蚀刻包括离子束刻蚀、反应离子束刻蚀、电子束刻蚀等。
化学性干法蚀刻则是利用反应性气体来实现化学反应加工,常用的化学性干法蚀刻包括等离子刻蚀、化学气相沉积、反应性离子束沉积等。
等离子体刻蚀是一种最常用的化学性干法蚀刻技术,它主要是在高频或微波磁场的作用下产生高温、高压、高电位的等离子体,将反应气体激发成离子状态,并在等离子体的作用下进行材料表面的化学反应。
等离子体刻蚀是一种高效的微米级结构加工方法,可用于制造微型元件、微流体芯片、光学器件、生物芯片等领域。
化学气相沉积是干法蚀刻技术的另一种重要应用,它是利用反应性气体在表面反应沉积出薄膜来制备材料。
化学气相沉积过程主要是利用气体中的化学成分,在材料表面上发生化学反应,使薄膜有自组装和自组织的特性,从而自行组成所需要的形状和特性。
总之,干法蚀刻原理是利用物理性和化学性干法蚀刻技术来实现微米、纳米级结构加工的一种高精度微纳加工技术,这种技术的应用领域很广,包括微型元件、微流体芯片、光学器件、生物芯片等领域。
刻蚀相关知识点总结

刻蚀相关知识点总结刻蚀技术主要分为湿法刻蚀和干法刻蚀两种。
湿法刻蚀是在溶液中通过化学反应去除材料表面的工艺,而干法刻蚀是在气相中通过物理或化学反应去除材料表面的工艺。
下面将详细介绍刻蚀的相关知识点。
一、刻蚀的基本原理1. 湿法刻蚀原理湿法刻蚀是利用化学溶液对材料表面进行腐蚀或溶解的工艺。
湿法刻蚀的原理是在溶液中加入具有特定功能的化学试剂,使其与被刻蚀物质发生化学反应,从而去除材料表面的部分物质。
湿法刻蚀通常可以实现较高的刻蚀速率和较好的表面质量,但需要考虑溶液中的成分和温度对环境的影响。
2. 干法刻蚀原理干法刻蚀是利用气相中的等离子体或化学反应对材料表面进行腐蚀或清除的工艺。
干法刻蚀的原理是在高能离子束或化学气体的作用下,使被刻蚀物质表面发生物理或化学反应,从而去除材料表面的部分物质。
干法刻蚀通常可以实现更高的加工精度和更好的表面质量,但需要考虑设备的复杂性和成本的影响。
二、刻蚀的工艺参数1. 刻蚀速率刻蚀速率是刻蚀过程中单位时间内去除的材料厚度,通常以单位时间内去除的厚度为单位。
刻蚀速率的选择需要综合考虑刻蚀材料的性质、刻蚀条件、刻蚀设备和加工要求等因素。
2. 刻蚀选择性刻蚀选择性是指在多种材料叠加或混合结构中选择性地去除某一种材料的能力。
刻蚀选择性的选择需要考虑被刻蚀材料和其它材料之间的化学反应性和物理性质的差异,以实现精确的刻蚀。
3. 刻蚀均匀性刻蚀均匀性是指在整个刻蚀过程中去除材料的厚度分布情况。
刻蚀均匀性的选择需要考虑刻蚀设备和刻蚀条件对被刻蚀物质的影响,以实现均匀的刻蚀。
4. 刻蚀深度控制刻蚀深度控制是指在整个刻蚀过程中去除材料的深度分布情况。
刻蚀深度控制的选择需要综合考虑刻蚀设备和刻蚀条件对被刻蚀物质的影响,以实现精确的刻蚀深度。
5. 刻蚀环境控制刻蚀环境控制是指在整个刻蚀过程中对刻蚀环境(如溶液中的成分、气相中的气体、温度和压力等)的控制。
刻蚀环境控制的选择需要考虑被刻蚀材料的特性和加工的要求,以实现良好的刻蚀效果。
刻蚀设备简介演示

利用射频电源产生的高频电场,将气体激发为等离子体,通过反应气体与材料 表面的化学反应来刻蚀表面。
激光刻蚀设备
激光诱导等离子刻蚀设备
通过高能激光束照射材料表面,产生等离子体,实现表面刻蚀。
激光烧蚀刻蚀设备
利用高功率激光束将材料表面烧蚀,实现物理刻蚀。
其他类型刻蚀设备
电化学刻蚀设备
刻蚀设备简介演示
汇报人: 2023-11-23
目录
• 刻蚀设备概述 • 刻蚀设备类型 • 刻蚀设备的关键部件 • 刻蚀设备的操作与维护 • 刻蚀技术的发展趋势与挑战 • 刻蚀设备的应用案例
01
刻蚀设备概述
Chapter
定义与分类
刻蚀设备定义
刻蚀设备是一种用于材料表面处 理的设备,通过物理或化学方法 实现材料表面的选择性去除。
将准备好的样品放入设备中的指定位 置,关闭腔体并启动真空系统。
开始刻蚀
满足安全条件后,启动刻蚀设备并 进行实时监测,记录刻蚀过程中的 数据。
刻蚀结束与清洗
当刻蚀达到预定时间或达到预定工 艺条件时,关闭设备并解除真空状 态,取出样品进行清洗。
常见问题及解决方案
检查工艺参数是否设置正确,如 气体流量、压力等参数是否稳定 ,同时确认样品表面是否平整、 无污染。
应,从而提高刻蚀效果。
组成部分
真空系统通常包括真空泵、真空 测量仪器和管路等部分,以确保
真空环境的稳定和准确控制。 Nhomakorabea控制系统
定义
控制系统是用于监控和控制刻蚀设备各部件的电 子系统。
功能
它确保设备在刻蚀过程中能够稳定运行,并对异 常情况进行监测和报警。
组成部分
控制系统通常包括传感器、控制器和执行器等部 分,以实现对设备各部件的精确控制和监测。
石英干法刻蚀应用

石英干法刻蚀应用全文共四篇示例,供读者参考第一篇示例:石英干法刻蚀是一种常用的微纳加工技术,广泛应用于纳米加工、微加工及集成电路制造等领域。
石英干法刻蚀是一种无液相参与的刻蚀方法,其原理是在真空环境下,利用气相氟化剂对硅等材料进行氟化反应,产生气相产物,并将刻蚀产物通过真空泵除去,从而实现对材料的刻蚀。
石英干法刻蚀具有高速、高精度、高可靠性等优点,被广泛应用于微加工领域。
石英干法刻蚀的应用范围非常广泛,包括但不限于微纳加工、集成电路制造、MEMS器件制造等领域。
在微纳加工领域,石英干法刻蚀被广泛应用于制备光子晶体、微纳米结构、微纳米器件等。
在集成电路制造中,石英干法刻蚀被用于制备半导体器件、光刻版等。
在MEMS器件制造领域,石英干法刻蚀被用于制备微机械器件、声波器件等。
石英干法刻蚀在这些领域的应用,极大地推动了微纳加工技术的发展,促进了微电子工业的繁荣。
石英干法刻蚀的特点是可控性高、重复性好、工艺简单等。
石英干法刻蚀不需要使用液相刻蚀剂,避免了液相刻蚀剂对器件表面的污染,提高了器件的质量和稳定性。
石英干法刻蚀的加工环境为真空环境,减少了氧化反应,可以避免氧气对表面的影响,保证了加工的精度和速度。
石英干法刻蚀的工艺简单,不需要复杂的设备和繁琐的操作,降低了制造成本,提高了生产效率。
石英干法刻蚀的工艺流程一般包括前处理、主刻蚀、后处理等步骤。
前处理是准备待加工材料的过程,包括清洗表面、涂覆光刻胶、曝光、显影等。
主刻蚀是将材料置于真空腔内,加热并通入氟化剂进行刻蚀。
后处理是清洗刻蚀产物,并去除光刻胶等。
石英干法刻蚀的工艺流程简单易控制,适用于各种材料的加工。
石英干法刻蚀是一种重要的微纳加工技术,具有广泛的应用前景。
随着微纳加工技术的不断发展,石英干法刻蚀技术将会得到更广泛的应用,推动微电子工业的发展。
石英干法刻蚀技术的不断完善和改进,将为微纳加工领域带来更多的创新和突破。
相信在不久的将来,石英干法刻蚀将会成为微纳加工领域的主流技术,为人类社会带来更多的便利和发展机遇。
光学材料的干法刻蚀研究

案例二:玻璃基光学材料的干法刻蚀
总结词
玻璃基光学材料具有优异的光学性能和机械性能,广泛应用于各种光学元件的制作。而干法刻蚀技术在该领域 中也发挥了重要作用。
详细描述
干法刻蚀技术在玻璃基光学材料的加工中,能够实现高精度、高效率的刻蚀,同时避免了湿法刻蚀中的化学腐 蚀问题。此外,通过选择不同的刻蚀气体和参数,还可以实现对玻璃基光学材料进行各向同性或异性的刻蚀。
05
结论与展望
研究成果总结
干法刻蚀技术
在干法刻蚀技术方面,我们取得了重要的突破。通过精 确控制反应参数,我们成功地实现了对光学材料的精确 刻蚀,得到了高质量的刻蚀图案和结构。
材料适应性
我们的方法成功地应用于多种光学材料,包括玻璃、晶 体、陶瓷和金属氧化物等,这表明我们的方法具有广泛 的材料适应性。
更广泛的适用范围
目前干法刻蚀技术主要应用于半导体制造领域,但随着光学材料和其他新材料的发展,未 来干法刻蚀技术的应用范围将更加广泛。例如,光学材料具有高度透明性和硬度等特点, 未来干法刻蚀技术有望在光学材料加工领域取得重要突破。
未来研究方向
干法刻蚀过程的物理机制研究
深入探究干法刻蚀过程中的物理机制,包括反应动力学、薄膜应 力等,为优化刻蚀工艺和提高刻蚀质量提供理论支持。
成本与可持续性
我们的方法涉及高精度的设备和材料,这可能导致制造成本较高。此外,干法刻蚀过程需要使用大量的化学试剂和气体, 对环境可能产生一定影响,因此需要进一步研究可持续性和环保性更强的替代方案。
对未来研究的建议
工艺优化
进一步研究干法刻蚀过程中的各种参数对刻 蚀效果的影响,以进一步优化工艺条件,提 高刻蚀质量和效率。
总结词
硅基光学材料由于其稳定的物理化学性质以及优异的机械性能,成为了光学领域的重要材料。而干法刻蚀技术 以其高精度、高效率的优点,在硅基光学材料的加工中得到了广泛应用。
硅的干法刻蚀

硅的干法刻蚀硅是当今半导体制造技术中最重要的材料,由于它的高硬度,良好的热稳定性,抗腐蚀性和低成本,因此在集成电路和其他电子应用中被广泛应用。
硅的干刻蚀技术是制作复杂的集成电路和封装电子元件的关键步骤。
本文将介绍硅干刻蚀技术包括其基本原理、应用和技术发展。
硅的干刻蚀是一种高分辨率,选择性的微刻蚀技术,用于将集成电路模式刻蚀在表面的硅片上。
它通常是由一个氦氖激光器或一组激光器将高功率,短脉冲激光束分解成一系列的微刻蚀点。
这些点被组合成不同形状和尺寸的模式,以及封装电子元件。
这种技术具有良好的精度和可靠性,可以制造出具有良好功能性能的集成电路。
硅干刻蚀技术的应用范围广泛,但最常用的应用是在制作集成电路和封装电子元件时,硅干刻蚀可用于制作精细的微型结构,例如低拉出把手或深孔结构,以及高集成度的微处理器或微控制器。
其他应用还包括生物细胞模拟芯片,复杂的光学系统,X射线成像芯片,半导体传感器,平板显示器,多媒体芯片,太阳能电池等。
此外,硅干刻蚀技术也可以用于制作几何复杂和微小的结构,例如深孔或微孔,从而实现对多孔材料的集成制造。
由于硅的干刻蚀具有高分辨率,可靠性,低成本和精确控制,因此它在未来的应用中也将具有更大的发展。
最后,要强调的是,硅的干刻蚀技术可以实现高分辨率、选择性和高可靠性的微刻蚀,具有多种应用,并且技术发展也有潜力在未来发挥出更大的作用。
不管是在集成电路制造,还是在其他电子应用领域,都能得到硅的干刻蚀技术的重要贡献。
综上所述,硅的干刻蚀是一种重要的微刻蚀技术,它的应用范围广泛,具有良好的精度,可靠性和可控性。
硅的干刻蚀技术的发展前景乐观,对集成电路制造和其他电子应用领域都具有重要的作用。
darc层干法刻蚀

darc层干法刻蚀
DARC (Doped Amorphous Carbon) 层干法刻蚀是一种常用的纳
米加工技术,主要用于制备纳米级别的器件和结构。
在 DARC 层干法刻蚀中,首先需要制备一个 DARC 膜,一般
采用化学气相沉积(CVD)技术。
DARC 膜具有较高的导电
性和光透明性,对光刻胶和光刻步骤友好。
接下来,在光刻步骤中,将光刻胶涂覆在 DARC 膜上,并利
用掩模光刻技术制作出所需的图形。
然后,通过曝光和显影步骤,将光刻胶中未曝光区域去除,从而得到所需的光刻胶图案。
随后,进行干法刻蚀步骤。
通常使用的干法刻蚀方法有辉光放电刻蚀(Glow Discharge Etching, GDE)和反应离子刻蚀(Reactive Ion Etching, RIE)等。
这些方法利用等离子体生成
的化学反应或物理碰撞将 DARC 膜刻蚀掉,形成所需的纳米
结构。
在干法刻蚀过程中,需要对刻蚀参数进行精确控制,包括刻蚀气体的种类和浓度、功率、压力等。
这些参数的选择将直接影响刻蚀速率和刻蚀选择性。
通过DARC 层的干法刻蚀,可以制备出各种纳米器件和结构,如纳米线、纳米孔、纳米槽等。
这些纳米结构在纳米电子学、纳米光学和生物传感等领域具有广泛的应用。
纳米刻蚀工艺中的干法刻蚀与湿法刻蚀比较

纳米刻蚀工艺是纳米制造中的一项关键技术,它通过物理或化学方法去除材料,以达到制造纳米级别结构的目的。
在纳米刻蚀工艺中,干法刻蚀和湿法刻蚀是两种主要的刻蚀方法,它们各自具有不同的特点,也适用于不同的应用场景。
首先,让我们来看看干法刻蚀。
在干法刻蚀中,我们通常使用物理手段如离子刻蚀、反应离子刻蚀(RIE)、机械研磨等。
这些方法的主要优点是刻蚀速度快,对材料的兼容性好,能够处理各种不同类型的材料。
然而,这种方法也存在一些缺点。
首先,它对设备的要求较高,需要专门的设备和技术支持。
其次,由于其刻蚀过程中可能产生微小碎片,因此在处理敏感材料时需要特别小心。
此外,干法刻蚀对于深宽比的保持相对较差,即对同一尺寸的图形,干法刻蚀可能需要更大的实际面积。
接下来是湿法刻蚀,这种方法主要利用化学反应来去除材料。
常见的湿法刻蚀技术包括化学腐蚀、等离子体腐蚀等。
与干法刻蚀相比,湿法刻蚀对许多材料具有更强的兼容性,特别是在高分子材料和绝缘材料上。
此外,湿法刻蚀在处理大面积样品时更具优势,因为它不需要精确的定位和设备支持。
然而,湿法刻蚀也存在一些问题,如腐蚀液的选择和配比需要严格控制,以及对一些材料可能产生过敏反应的风险。
而且,湿法刻蚀的刻蚀深度较浅,对于深结构可能无法达到预期的刻蚀效果。
总的来说,干法刻蚀和湿法刻蚀各有优缺点,适用于不同的应用场景。
在选择使用哪种方法时,我们需要考虑待处理材料的性质、刻蚀速度的需求、设备的可用性以及成本等因素。
而且,随着技术的进步,我们期待在未来看到更多创新的纳米刻蚀方法出现,以满足更复杂、更高精度的纳米制造需求。
刻蚀设备发展现状及未来趋势分析
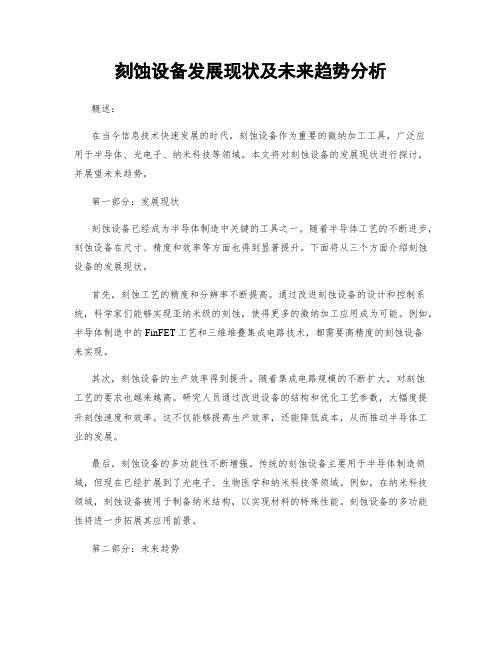
刻蚀设备发展现状及未来趋势分析概述:在当今信息技术快速发展的时代,刻蚀设备作为重要的微纳加工工具,广泛应用于半导体、光电子、纳米科技等领域。
本文将对刻蚀设备的发展现状进行探讨,并展望未来趋势。
第一部分:发展现状刻蚀设备已经成为半导体制造中关键的工具之一。
随着半导体工艺的不断进步,刻蚀设备在尺寸、精度和效率等方面也得到显著提升。
下面将从三个方面介绍刻蚀设备的发展现状。
首先,刻蚀工艺的精度和分辨率不断提高。
通过改进刻蚀设备的设计和控制系统,科学家们能够实现亚纳米级的刻蚀,使得更多的微纳加工应用成为可能。
例如,半导体制造中的FinFET工艺和三维堆叠集成电路技术,都需要高精度的刻蚀设备来实现。
其次,刻蚀设备的生产效率得到提升。
随着集成电路规模的不断扩大,对刻蚀工艺的要求也越来越高。
研究人员通过改进设备的结构和优化工艺参数,大幅度提升刻蚀速度和效率。
这不仅能够提高生产效率,还能降低成本,从而推动半导体工业的发展。
最后,刻蚀设备的多功能性不断增强。
传统的刻蚀设备主要用于半导体制造领域,但现在已经扩展到了光电子、生物医学和纳米科技等领域。
例如,在纳米科技领域,刻蚀设备被用于制备纳米结构,以实现材料的特殊性能。
刻蚀设备的多功能性将进一步拓展其应用前景。
第二部分:未来趋势随着科学技术的快速发展和应用需求的不断增加,刻蚀设备在未来将继续发展。
下面将从两个方面展望未来刻蚀设备的趋势。
首先,刻蚀设备将更加追求高精度和高效率。
随着集成电路逐渐接近纳米级尺寸,对刻蚀设备工艺的精度要求将进一步提高。
未来的刻蚀设备将更加注重微纳米加工的精确性,以满足更高级别的应用需求。
与此同时,提高生产效率也将成为刻蚀设备发展的重要方向。
其次,刻蚀设备将向多功能化方向发展。
随着科技进步,人们期望刻蚀设备能够满足越来越多领域的微纳加工需求。
未来刻蚀设备将更加注重多功能性的设计,以满足不同材料和不同工艺的刻蚀需求。
例如,可同时实现湿法和干法刻蚀的设备将更加受欢迎。
金属干法蚀刻工艺研究报告

金属干法蚀刻工艺研究报告金属干法蚀刻工艺研究报告摘要:金属干法蚀刻作为一种精密加工工艺,近年来在制造领域得到广泛应用。
本文通过实验研究,探究了金属干法蚀刻的工艺原理、工艺参数及其影响因素,并对金属干法蚀刻的优势和应用前景进行了讨论。
1. 引言金属干法蚀刻是一种不使用溶液的蚀刻工艺,通过控制高能粒子束以及粒子束的扫描轨迹,实现对金属材料表面进行高精度的刻蚀。
与传统的湿法蚀刻相比,金属干法蚀刻具有无废水排放、环保节能、刻蚀速度快、加工精度高等优势。
然而,金属干法蚀刻的工艺参数及其对加工结果的影响尚需进一步研究。
2. 实验与结果本实验选择了不同金属材料进行金属干法蚀刻实验,分别对刻蚀速度、刻蚀深度和刻蚀质量进行了测试和分析。
实验结果表明,金属干法蚀刻的刻蚀速度与激光功率、扫描速度以及材料的热导率密切相关,其中激光功率对刻蚀速度影响最为显著。
刻蚀深度和刻蚀质量与激光功率和扫描速度呈正相关,但与热导率呈负相关。
此外,不同金属材料的刻蚀效果也有所差异,高热导率的金属材料刻蚀速度较快,但刻蚀质量相对较差。
3. 工艺参数与影响因素3.1 激光功率激光功率是金属干法蚀刻的重要工艺参数,它决定了刻蚀速度和刻蚀深度。
较高的激光功率可以获得较快的刻蚀速度,但过高的激光功率会导致材料表面产生氧化、溶蚀等问题。
3.2 扫描速度扫描速度对金属干法蚀刻的刻蚀深度和刻蚀质量具有一定影响。
较高的扫描速度可以增加刻蚀厚度,但过高的扫描速度会导致表面粗糙度增加。
3.3 材料热导率材料的热导率对金属干法蚀刻的刻蚀速度和刻蚀深度有显著影响。
热导率越高,刻蚀速度越快,但刻蚀质量相对较差。
4. 优势与应用前景金属干法蚀刻相比传统的湿法蚀刻具有一系列优势,如无废水排放、精度高等。
这使得金属干法蚀刻在微电子制造、微机械加工等领域具有广阔应用前景。
同时,随着激光技术和粒子束技术的不断发展,金属干法蚀刻的加工效率还将进一步提升,应用领域也将不断拓展。
多晶干法刻蚀

多晶干法刻蚀是一种重要的半导体工艺步骤,主要应用于制造集成电路。
以下是关于多晶干法刻蚀的详细解释:
1. 刻蚀多晶硅时,必须确保掩膜上的尺寸准确地转移到多晶硅上。
2. 刻蚀后的轮廓也非常重要,例如,如果多晶硅刻蚀后栅极侧壁有倾斜,可能会屏蔽后续工艺中源极和
漏极的离子注入,导致杂质分布不均,同时沟道的长度会随栅极倾斜的程度而改变。
3. 对sio2的刻蚀选择比要足够高,这是因为需要去除阶梯残留,避免多晶硅电极间短路的发生。
同时,
多晶硅一般覆盖在很薄的栅极氧化层上,如果氧化层被完全刻蚀,则氧化层下的源极和漏极区域可能会被快速刻蚀。
4. 选择适当的刻蚀气体也是非常重要的。
CF4、SF6等F原子为主的等离子体是常用的刻蚀气体,但这类
气体也存在负载效应,即被刻蚀材料裸露在等离子体中面积较大的区域时刻蚀速率比在面积较小的区域时慢,导致局部刻蚀速率的不均匀。
5. 在干法刻蚀中,多晶硅相对于氮化硅和二氧化硅下层的选择性较差,因此需要非常精确地优化干蚀刻
配方和蚀刻时间的精细控制。
6. 另外,对于多晶硅的干法刻蚀,控制其过度刻蚀也非常重要。
这是因为过度刻蚀可能会导致多晶硅的
电阻不均匀。
总之,多晶干法刻蚀是一项复杂的工艺步骤,涉及精确的尺寸控制、化学选择性和物理特性考虑等多个方面。
硅的干法刻蚀

硅的干法刻蚀
硅的干法刻蚀是指在不使用任何化学试剂或溶液的情况下,通过加热和压力来破坏材料表面的氧化层,从而获得所需要的物质。
这种方法通常被称为“空气刻蚀”或“空气刀片”。
干法刻蚀技术已经广泛应用于各个领域,包括半导体、光伏电池等。
它可以用于制造芯片上的多晶硅(Si)层,也可以用于清除表面的杂质和污染物,如氧化物、金属残留物等。
此外,干法刻蚀还能够提高器件性能并降低生产成本。
然而,由于缺乏实验室测试设备,人们对于干法刻蚀技术的了解仍然有限。
因此,在进行干法刻蚀操作之前,建议先进行实验室测试,确保其安全性和可靠性。
同时,在操作过程中,应严格遵守相关规范和标准,避免出现意外事故。
- 1、下载文档前请自行甄别文档内容的完整性,平台不提供额外的编辑、内容补充、找答案等附加服务。
- 2、"仅部分预览"的文档,不可在线预览部分如存在完整性等问题,可反馈申请退款(可完整预览的文档不适用该条件!)。
- 3、如文档侵犯您的权益,请联系客服反馈,我们会尽快为您处理(人工客服工作时间:9:00-18:30)。
设备参数
设备设计、电源、电源频率、压力、温度、气流速率、
真空状况、工艺菜单
工艺参数
等离子体-表面相互作用:表面材料、复合金属的不同层、表面温度、表面电荷、表面形貌;化学和无理要求;
时间
质量指标
刻蚀速率、选择比、均与性、特性曲线、关键尺寸、残留物
其他相关因素
净化间规、操作过程、维护过程、预防维护计划
2.2刻蚀作用
干法刻蚀系统中,刻蚀作用是通过化学作用或物理作用,或者是化学和物理的共同作用来实现的。在纯化学机理中,等离子体产生的反应元素(自由基和反应原子)与硅片表面的物质发生反应。为了获得高的选择比(即为了与光刻胶或下层材料的化学反应最小),进入腔体的气体(一般含氯或氟)都经过了慎重选择。等离子体化学刻蚀由于它是各向同性的,因而线宽控制差。反应中产生的挥发性生成物被真空泵抽走。
第2章干法刻蚀的机制和原理
2.1刻蚀工艺
在半导体制造中有两种基本的刻蚀工艺:干法刻蚀和湿法腐蚀。干法刻蚀是把硅片表面曝露与其他中产生的等离子体,等离子体通过光刻胶中开除的残空,与硅片发生物理或者化学反应(或这两种反应),从而去掉曝露的表面材料。干法刻蚀是亚微米尺寸下刻蚀器件的最主要方方法。而湿法腐蚀一般只用于尺寸较大的情况下(大于3微米)。湿法腐蚀仍然用来腐蚀硅片上的某些层或用来去除干法刻蚀后的残留物。
3.1介质的干法刻蚀
对于200mm硅片,介质的干法刻蚀是最复杂的刻蚀过程;而对于300mm硅片,介质刻蚀将遇到最大的挑战。氧化物刻蚀的最大困难在于随着特征尺寸缩小,在通互连中用于双层大马士革技术的层间介质的新的沟槽刻蚀工艺以及需要刻蚀低K层间介质所带来的更严格的工艺规。
3.1.1氧化物
刻蚀氧化物通常是为了制作接触孔和通孔。这些事很关键的应用,要求在氧化物中刻蚀出具有高深宽比的窗口。对于DRAM应用中的0.18um图形,深宽比希望能达到6:1,对下层的硅和硅化物、多晶硅的选择比要求大约50:1。有一些新的氧化物刻蚀应用,如有新沟槽刻蚀和高深宽比刻蚀要求的双大马士革结构,也有低的深宽比通孔刻蚀,如非关键性的氧化物刻蚀应用。
第3章干法刻蚀的应用
在集成电路制造过程中需要多种类型的干法刻蚀工艺,这些应用涉及在生产线上用到的所有材料。我们将按被刻蚀材料的种类:介质、硅和金属,来阐述干法刻蚀。随着关键尺寸的缩小、较高的深宽比窗口以及新材料砸硅片制造过程的应用对这三类的刻蚀提出了挑战。优化刻蚀条件是产品开发人员要解决的关键问题。一般来说,一个成功的干法刻蚀要求:
图1-1 底切现象
自1970年以来,元件制造首先开始采用电浆刻蚀技术(也叫等离子体刻蚀技术),人们对于电浆化学性的了解与认识也就越来越深。在现今的半导体集成电路或LCD制造过程中,要求精确地控制各种材料尺寸至次微米大小,而且还必须具有极高的再现性,电浆刻蚀是现今技术中唯一能极有效率地将此工作在高良率下完成的技术,因此电浆刻蚀便成为半导体制造以及TFT LCD Array制造中的主要技术之一。
3.1.1.3侧壁剖面
在局部(LI)氧化层介质中的接触窗口尺寸通常与具有高深宽比的最小特征尺寸相等。对于这种类型的应用,需要高度各项异性的垂直侧壁剖面。一个重要的因素是高密度等离子体重高方向性的离子轰击。
图2-1物理溅射(sputter)机理
1、各相异性刻蚀。
2、低刻蚀选择比。
3、并且因轰击效应使得被刻蚀膜层表面产生损伤。
4、反应副产物多为非挥发性,容易累积于腔体部。
2.1.2化学刻蚀
纯化学反应性蚀刻,则是利用各式能量源(RF,DC,microwave等)给予气体能量,产生电浆,进而产生化学活性极强的原(分)子团,原(分)子团扩散至待蚀刻物质的表面,与待蚀刻物质反应产生挥发性之反应生成物,最后挥发性生成物被真空设备抽离反应腔。因这种反应完全利用化学反应来达成,故谓之化学反应性蚀刻。这种蚀刻方式相近于湿式蚀刻,只是反应物及产物的状态由液态改变为气态,并利用电浆来促进蚀刻的速率。因此纯化学反应性蚀刻拥有类似于湿式蚀刻的优点及缺点,特点有:
刻蚀也可以分成有图形刻蚀和无图形刻蚀。有图形的刻蚀采用掩蔽层(有图形的光刻胶)来定义要刻蚀掉的表面材料区域,只有硅片上被选择的这一部分在刻蚀过程中刻掉,有图形刻蚀可用来在硅片上制作多种不同的特征图形,包括栅、金属互联线、通孔、接触孔和沟槽。无图形刻蚀、反过来或剥离是在整个硅片没有掩膜的情况下进行的,这种刻蚀工艺用于剥离掩蔽层(如STI氮化硅剥离和用于制备近体馆注入侧墙的硅化物工艺后钛的剥离)。反刻是在想要把某一层膜的总的厚度减小时采用的(如当平坦化硅片表面是需要见效形貌特征)。光刻胶是另一个剥离的例子。总的来说。有图形刻蚀和无图形刻蚀工艺能够采用干法刻蚀或湿法腐蚀技术来实现。
干法刻蚀也可以根据被刻蚀的材料类型来分类。按材料分,刻蚀主要分成三种:金属刻蚀、介质刻蚀和硅刻蚀。介质刻蚀是用于介质材料的刻蚀,如二氧化硅。接触空和通孔结构制作需要刻蚀介质,从而在ILD中刻蚀出窗口,而具有高深度宽比(窗口的深于宽的比值)的窗口刻蚀具有一定的挑战性。硅刻蚀(包括多晶硅)应用于需要去除硅的场合,如刻蚀多晶硅晶体管栅和硅槽电容。金属刻蚀主要是在金属层上去掉铝合金复合层,制作出互联线。
3.1.1.2光刻胶选择比
为了防止形成倾斜的侧墙,获得高的氧化硅/光刻胶选择比是很重要的。光刻胶用于定义要刻蚀的图形。在接触孔和通孔的刻蚀中,数百万的孔被同时刻蚀,每个孔中都需要去除精确数量的表层材料,而孔常常位于不同的深度,一种见效光刻胶选择比的因素是在高密度等离子体重活性氟原子的有效生成。自由的氟原子会刻蚀掉有机的光刻胶的选择比。另外,需要刻蚀抗反射涂层,这延长了刻蚀时间,进一步减小了光刻胶的厚度。
3.1.1.1下层材料的选择比
氧化物刻蚀的主要困难之一是获得对下层材料(通常是硅、氮化硅或者一层抗反射图层)的高的选择比。获得对硅的高选择比的一种方法是通过在化学气体中加入洋气来控制氧化物和硅之间的选择比。少量洋气能改善氧化物刻蚀和硅刻蚀的速率。当氧气浓度大至大约20%时,氧化物刻蚀比硅刻蚀要更快,增大了选择比,减少了对下层硅的刻蚀。另一种提高选择比的方法是在气体混合物中加入氢气,减少硅的刻蚀速率,当氢气浓度达到大约40%是,硅刻蚀的速率几乎为零。同时,氧化物刻蚀速率在氢气浓度地狱40%的时候几乎不受什么影响。
1、对不需要刻蚀的材料(主要是光刻胶和下层材料)的高选择比。
2、获得可接受的产能的刻蚀速率。
3、好的侧壁剖面控制、
4、好的片均匀性。
5、低的期间损伤。
6、宽的艺制造窗口。
对于每一种特殊的干法刻蚀应用,关键的刻蚀工艺参数通过工艺优化来确定。其中一些参数在表(3-1),在许多情况下,优化是通过工艺设备的计算机模拟来实现的。因为用硅片进行实际的样机测试需要很高的成本。
总结与展望总结与展望一总结本文简单描述了干法刻蚀的机理和原理了解干法刻蚀的在集成电路制造工艺的一些应用熟悉了干法刻蚀设备的构成和主要性能指干法技术的出现是由于集成电路制造工艺的需要其发展也是伴随集成电路的不断微细化和高集成化而完善更新
干法刻蚀技术的应用与发展
摘要
在半导体生产中,干法刻蚀是最主要的用来去除表面材料的刻蚀方法。而干法刻蚀是一个惯称,它指的是在低气压下雨等离子体有关的腐蚀方法。经过二十多年的发展,经历了多样化的发展过程,使技术不断完善和创新。一定程度上,干法刻蚀的水平决定了集成电路器件性能和生产规模。
1、各向同性刻蚀
2、高刻蚀选择比
3、高刻蚀速率
4、低表面损伤
5、反应腔体洁净度较易维持
图2-2化学反应性刻蚀机理
在半导体以及LCD制程中,纯化学反应性蚀刻应用的情况通常为不需做图形转换的步骤,如光阻的去除等。
图2-3 基于化学反应机制的理想乾蚀刻过程
如图2-3所示,一个仅基于化学反应机制的理想乾蚀刻过程可分为以下几个步骤:(1)刻蚀气体进入腔体,在电场作用下产生电浆形态之蚀刻物种,如离子及自由基(Radicals);(2)蚀刻物种藉由扩散、碰撞或场力移至待蚀刻物表面;(3)蚀刻物种吸附在待蚀刻物表面一段时间;(4)进行化学反应并产生挥发性之生成物;(5)生成物脱离表面;(6)脱离表面之生成物扩散至气体中并排出。上述步骤中若其中一个停止发生,则整个反应将不再进行。而其中生成物脱离表面的过程最为重要,大部份的反应物种皆能与待蚀刻物表面产生快速的反应,但除非生成物有合理的气压以致让其脱离表面,否则反应将不会发生。
广义而言,所谓的刻蚀技术,是将显影后所产生的光阻图案忠实地转印到光阻下的材质上,形成由光刻技术定义的图形。它包含了将材质整面均匀移除及图案选择性部分去除,可分为湿式刻蚀(wet etching)和干式刻蚀(dry etching)两种技术。湿式刻蚀具有待刻蚀材料与光阻及下层材质良好的刻蚀选择比(selectivity)。然而,由于化学反应没有方向性,因而湿式刻蚀是各向同性刻蚀。当刻蚀溶液做纵向刻蚀时,侧向的刻蚀将同时发生,进而造成底切(Undercut)现象,导致图案线宽失真,如下图所示。
干式刻蚀通常指利用辉光放电(glow discharge)方式,产生包含离子、电子等带电粒子以及具有高度化学活性的中性原子、分子及自由基的电浆,来进行图案转印(pattern transfer)的刻蚀技术。干法刻蚀是亚微米尺寸下刻蚀器件的最主要方法,广泛应用于半导体或LCD前段制程。和其他一些技术。比如气相腐蚀、激光诱导腐蚀,以及无掩膜的聚焦离子束腐蚀等,虽然亦有别于“湿法”,但已自成体系,一般不列入干法刻蚀之中。经过二十多年的发展,出现多种干法刻蚀结构形式,她们具有各自的时代背景,也有各自的特点。
还有一种是物理和化学混合作用机理,其中离子轰击改善化学刻蚀作用。刻蚀剖面可以通过调节等离子体条件和气体组分从各向同性向异性改变。这种物理和化学混合作用机理刻蚀能获得好的线宽控制并有不错的选择比,因而在打多少数干法刻蚀工艺中被采用。
干法刻蚀系统可以是各向同性或各向异性的刻蚀机,这取决于RF电场相对于硅片表面的方向。意思是指正离子溅射的发生是硅片表面还是硅片的边缘。如果这个电场是垂直于硅片表面,刻蚀作用就是重正离子溅射和一些基本的化学反应,如果这个电场平行于硅片表面,物理的溅射作用就很弱,因此刻蚀作用主要是表面材料和活性元素之间的化学反应。