sinx干法刻蚀工艺
4、干法蚀刻(dryetch)原理介绍

4、⼲法蚀刻(dryetch)原理介绍前⾯已经简单介绍⼲法蚀刻的基本过程,这⼀节深⼊介绍⼲法蚀刻的基本原理,包括物理蚀刻,化学蚀刻,和反应离⼦蚀刻。
物理蚀刻主要是⽤plasma轰击wafer表⾯,粒⼦与粒⼦之间发⽣碰撞,达到蚀刻的⽬的,整个过程全部是物理变化,没有新的物质⽣成。
物理蚀刻是各向异性的,蚀刻⽅向沿着plasma速度⽅向,其他⽅向基本没有蚀刻,物理蚀刻没有选择性,⾼能离⼦可能会损伤器件。
化学蚀刻主要是⽤plasma与wafer表⾯材料发⽣化学反应,⽣成副产物,然后被抽⾛的过程,化学蚀刻有个要求就是副产物主要是⽓体,容易被抽⾛,化学蚀刻是各项同性的,但蚀刻过程中会产⽣聚合物polymer,会沉积在侧壁,实现各向异性的效果,通过调节化学蚀刻⽓体⽐例可以实现不同flim的选择⽐。
反应离⼦蚀刻的原理是综合物理和化学蚀刻的过程,⼀般的⼲法蚀刻都是反应性离⼦蚀刻,单纯的物理和化学蚀刻很少在⼯业上应⽤。
图1 physical etching ⽰意图图2 chemical etching⽰意图图3 reactive ion etching ⽰意图物理蚀刻主要是⽤氩⽓(Ar)轰击wafer表⾯材料,由于Ar是惰性⽓体,不会影响plasma的化学性质,物理蚀刻效果明显。
化学蚀刻主要⽤含碳氟⽓体(CXFY),基本原理是F⾃由基与Si结合⽣成⽓态的SiF4,副产物容易被抽⾛。
碳氟⽓体(CF4,CHF3,C3F8等)在化学蚀刻过程中⽣成的不饱和物质会发⽣链化反应⽣成聚合物(polymer),沉积在侧壁的polymer会阻⽌横向蚀刻的进⾏,这对吃出⾼的深宽⽐形貌有利,但沉积在电极和chamber⾥的polymer是defect source,掉下来就会形成surface particle 和pattern fail,这是dry etch 两种典型的defect。
氟碳⽐(F/C)决定polymer的⽣成,其中F/C越⼩,⽣成的polymer越多,反之F/C越⼤,⽣成的polymer越少,其中的原理是F主要与Si反应⽣成 SiF4, C是形成polymer的源头,C含量越⾼,polymer越多,⾄于为什么是碳⽣成polymer,这涉及到⾼分⼦材料的知识,这⾥不仔细介绍,感兴趣的朋友可以私底下找我交流。
干法刻蚀工艺总结

干法刻蚀工艺总结离子束刻蚀机(IBE-150A)背景:利用辉光放电原理将氩气分解为氩离子,氩离子经过阳极电场的加速对样品表面进行物理轰击,以达到刻蚀的作用。
把Ar、Kr或Xe之类惰性气体充入离子源放电室并使其电离形成等离子体,然后由栅极将离子呈束状引出并加速,具有一定能量的离子束进入工作室,射向固体表面撞击固体表面原子,使材料原子发生溅射,达到刻蚀目的,属纯物理过程。
技术指标:装片:一片六英寸衬底、或1片四英寸,向下兼容。
抽气速度:30min由ATM到1.0×10-3Pa极限真空度:2×10-4Pa离子能量:300eV-400eVICP刻蚀机(OXFORD ICP 180)背景:通入反应气体使用电感耦合等离子体辉光放电将其分解,产生的具有强化学活性的等离子体在电场的加速作用下移动到样品表面,对样品表面既进行化学反应生成挥发性气体,又有一定的物理刻蚀作用。
因为等离子体源与射频加速源分离,所以等离子体密度可以更高,加速能力也可以加强,以获得更高的刻蚀速率,以及更好的各向异性刻蚀。
另外,由于该系统使用了Cl基和Br基的刻蚀气体,因此该ICP系统适合于对Ⅲ-Ⅴ族化合物材料进行刻蚀。
技术指标:ICP离子源:0~3000WRF射频源:0~600W装片:1片四英寸,向下兼容基底刻蚀温度:0℃-200℃可调。
刻蚀气体:BCl3、Cl2、HBr、Ar、O2可刻蚀材料包括:GaN、GaAs、InP等Ⅲ-Ⅴ族化合物材料ICP刻蚀机(STS HRM)背景:通入反应气体使用电感耦合等离子体辉光放电将其分解,产生的具有强化学活性的等离子体在电场的加速作用下移动到样品表面,对样品表面既进行化学反应生成挥发性气体,又有一定的物理刻蚀作用。
因为等离子体源与射频加速源分离,所以等离子体密度可以更高,加速能力也可以加强,以获得更高的刻蚀速率,以及更好的各向异性刻蚀。
该系统使用了F基的刻蚀气体,具有Bosch工艺,适合于对硅材料进行大深宽比刻蚀。
第二章干法刻蚀的介绍

第二章干法刻蚀的介绍第一篇:第二章干法刻蚀的介绍第二章干法刻蚀的介绍2.1刻蚀、干法刻蚀和湿法腐蚀 2.1.1关于刻蚀刻蚀,是指用化学或物理方法有选择地从硅片表面去除不需要的材料的过程。
刻蚀的基本目的,是在涂胶(或有掩膜)的硅片上正确的复制出掩膜图形[1]。
刻蚀,通常是在光刻工艺之后进行。
我们通常通过刻蚀,在光刻工艺之后,将想要的图形留在硅片上。
从这一角度而言,刻蚀可以被称之为最终的和最主要的图形转移工艺步骤。
在通常的刻蚀过程中,有图形的光刻胶层〔或掩膜层)将不受到腐蚀源显著的侵蚀或刻蚀,可作为掩蔽膜,保护硅片上的部分特殊区域,而未被光刻胶保护的区域,则被选择性的刻蚀掉。
2.1.2干法刻蚀与湿法刻蚀在半导体制造中有两种基本的刻蚀工艺:干法刻蚀和湿法腐蚀。
干法刻蚀,是利用气态中产生的等离子体,通过经光刻而开出的掩蔽层窗口,与暴露于等离子体中的硅片行物理和化学反应,刻蚀掉硅片上暴露的表面材料的一种工艺技术法[1]。
该工艺技术的突出优点在于,可以获得极其精确的特征图形。
超大规模集成电路的发展,要求微细化加工工艺能够严格的控制加工尺寸,要求在硅片上完成极其精确的图形转移。
任何偏离工艺要求的图形或尺寸,都可能直接影响产品性能或品质,给生产带来无法弥补的损害。
由于干法刻蚀技术在图形轶移上的突出表现,己成为亚微米尺寸下器件刻蚀的最主要工艺方法。
在特征图形的制作上,已基本取代了湿法腐蚀技术。
对于湿法腐蚀,就是用液体化学试剂(如酸、碱和溶剂等)以化学的方式去除硅片表面的材料。
当然,在通过湿法腐蚀获得特征图形时,也要通过经光刻开出的掩膜层窗口,腐蚀掉露出的表面材料。
但从控制图形形状和尺寸的准确性角度而言,在形成特征图形方面,湿法腐蚀一般只被用于尺寸较大的情况(大于3微米)。
由于这一特点,湿法腐蚀远远没有干法刻蚀的应用广泛。
但由于它的高选择比和批量制作模式,湿法腐蚀仍被广泛应用在腐蚀层间膜、去除干法刻蚀残留物和颗粒等工艺步骤中。
干法刻蚀工艺文件
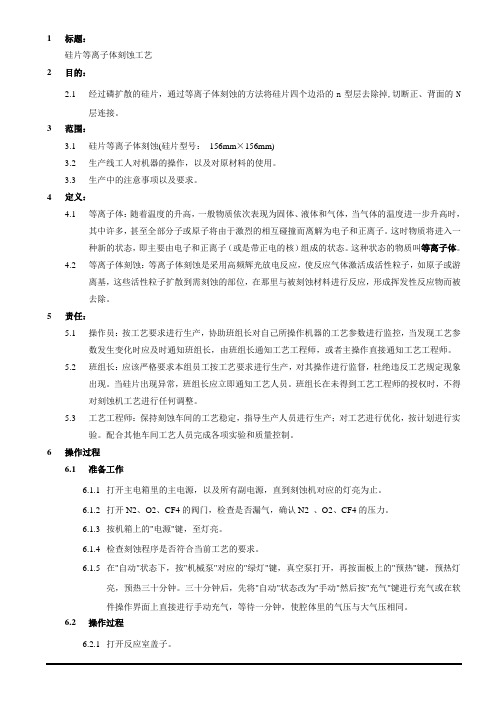
1标题:硅片等离子体刻蚀工艺2目的:2.1经过磷扩散的硅片,通过等离子体刻蚀的方法将硅片四个边沿的n型层去除掉,切断正、背面的N层连接。
3范围:3.1硅片等离子体刻蚀(硅片型号:156mm×156mm)3.2生产线工人对机器的操作,以及对原材料的使用。
3.3生产中的注意事项以及要求。
4定义:4.1等离子体:随着温度的升高,一般物质依次表现为固体、液体和气体,当气体的温度进一步升高时,其中许多,甚至全部分子或原子将由于激烈的相互碰撞而离解为电子和正离子。
这时物质将进入一种新的状态,即主要由电子和正离子(或是带正电的核)组成的状态。
这种状态的物质叫等离子体。
4.2等离子体刻蚀:等离子体刻蚀是采用高频辉光放电反应,使反应气体激活成活性粒子,如原子或游离基,这些活性粒子扩散到需刻蚀的部位,在那里与被刻蚀材料进行反应,形成挥发性反应物而被去除。
5责任:5.1操作员:按工艺要求进行生产,协助班组长对自己所操作机器的工艺参数进行监控,当发现工艺参数发生变化时应及时通知班组长,由班组长通知工艺工程师,或者主操作直接通知工艺工程师。
5.2班组长:应该严格要求本组员工按工艺要求进行生产,对其操作进行监督,杜绝违反工艺规定现象出现。
当硅片出现异常,班组长应立即通知工艺人员。
班组长在未得到工艺工程师的授权时,不得对刻蚀机工艺进行任何调整。
5.3工艺工程师:保持刻蚀车间的工艺稳定,指导生产人员进行生产;对工艺进行优化,按计划进行实验。
配合其他车间工艺人员完成各项实验和质量控制。
6操作过程6.1准备工作6.1.1打开主电箱里的主电源,以及所有副电源,直到刻蚀机对应的灯亮为止。
6.1.2打开N2、O2、CF4的阀门,检查是否漏气,确认N2 、O2、CF4的压力。
6.1.3按机箱上的"电源"键,至灯亮。
6.1.4检查刻蚀程序是否符合当前工艺的要求。
6.1.5在"自动"状态下,按"机械泵"对应的"绿灯"键,真空泵打开,再按面板上的"预热"键,预热灯亮,预热三十分钟。
干法腐蚀

干法刻蚀
求助编辑
干法刻蚀是用等离子体进行薄膜刻蚀的技术。
当气体以等离子体形式存在时,它具备两个特点:一方面等离子体中的这些气体化学活性比常态下时要强很多,根据被刻蚀材料的不同,选择合适的气体,就可以更快地与材料进行反应,实现刻蚀去除的目的;另一方面,还可以利用电场对等离子体进行引导和加速,使其具备一定能量,当其轰击被刻蚀物的表面时,会将被刻蚀物材料的原子击出,从而达到利用物理上的能量转移来实现刻蚀的目的。
因此,干法刻蚀是晶圆片表面物理和化学两种过程平衡的结果。
干法刻蚀又分为三种:物理性刻蚀、化学性刻蚀、物理化学性刻蚀。
其中物理性刻蚀又称为溅射刻蚀。
很明显,该溅射刻蚀靠能量的轰击打出原子的过程和溅射非常相像。
(想象一下,如果有一面很旧的土墙,用足球用力踢过去,可能就会有墙面的碎片从中剥离)这种极端的刻蚀方法方向性很强,可以做到各向异性刻蚀,但不能进行选择性刻蚀。
化学性刻蚀利用等离子体中的化学活性原子团与被刻蚀材料发生化学反应,从而实现刻蚀目的。
由于刻蚀的核心还是化学反应(只是不涉及溶液的气体状态),因此刻蚀的效果和湿法刻蚀有些相近,具有较好的选择性,但各向异性较差。
人们对这两种极端过程进行折中,得到目前广泛应用的一些物理化学性刻蚀技术。
例如反应离子刻蚀(RIE --Reactive Ion
Etching)和高密度等离子体刻蚀(HDP)。
这些工艺通过活性离子对衬底的物理轰击和化学反应双重作用刻蚀,同时兼有各向异性和选择性好的优点。
目前RIE已成为超大规模集成电路制造工艺中应用最广泛的主流刻蚀技术。
干法蚀刻原理

干法蚀刻原理
干法蚀刻是一种在半导体制造中常用的加工方法,其原理是利用化学反应在晶圆表面形成蚀刻物质,在特定条件下去除表面物质,从而达到加工效果。
干法蚀刻的主要特点是使用气体或等离子体作为反应介质,不需要使用液体溶液,因此可以避免液体蚀刻中出现的污染和激光硅晶片表面毛刺缺陷的问题。
干法蚀刻的反应过程主要有三种:物理反应、化学反应和生物反应。
物理反应是指利用高能粒子进行物理撞击,使表面物质受到磨蚀和削减。
化学反应是指利用化学反应使物质在表面发生化学变化,形成新的化合物,从而达到腐蚀效果。
生物反应是指利用生物体的代谢产物,通过生化反应来发生腐蚀作用。
干法蚀刻在半导体制造中的应用非常广泛,可以制造出各种微细结构和纳米级别的元器件。
- 1 -。
硅的干法刻蚀
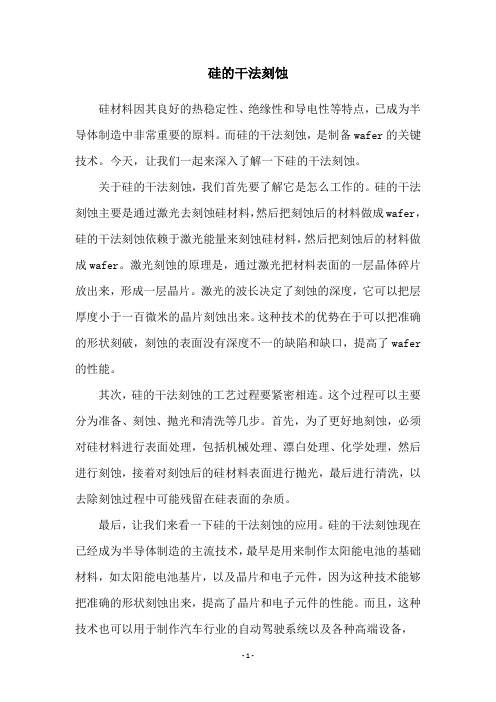
硅的干法刻蚀
硅材料因其良好的热稳定性、绝缘性和导电性等特点,已成为半导体制造中非常重要的原料。
而硅的干法刻蚀,是制备wafer的关键技术。
今天,让我们一起来深入了解一下硅的干法刻蚀。
关于硅的干法刻蚀,我们首先要了解它是怎么工作的。
硅的干法刻蚀主要是通过激光去刻蚀硅材料,然后把刻蚀后的材料做成wafer,硅的干法刻蚀依赖于激光能量来刻蚀硅材料,然后把刻蚀后的材料做成wafer。
激光刻蚀的原理是,通过激光把材料表面的一层晶体碎片放出来,形成一层晶片。
激光的波长决定了刻蚀的深度,它可以把层厚度小于一百微米的晶片刻蚀出来。
这种技术的优势在于可以把准确的形状刻破,刻蚀的表面没有深度不一的缺陷和缺口,提高了wafer 的性能。
其次,硅的干法刻蚀的工艺过程要紧密相连。
这个过程可以主要分为准备、刻蚀、抛光和清洗等几步。
首先,为了更好地刻蚀,必须对硅材料进行表面处理,包括机械处理、漂白处理、化学处理,然后进行刻蚀,接着对刻蚀后的硅材料表面进行抛光,最后进行清洗,以去除刻蚀过程中可能残留在硅表面的杂质。
最后,让我们来看一下硅的干法刻蚀的应用。
硅的干法刻蚀现在已经成为半导体制造的主流技术,最早是用来制作太阳能电池的基础材料,如太阳能电池基片,以及晶片和电子元件,因为这种技术能够把准确的形状刻蚀出来,提高了晶片和电子元件的性能。
而且,这种技术也可以用于制作汽车行业的自动驾驶系统以及各种高端设备,
总之,硅的干法刻蚀是一种高效的技术,可以把正确的形状刻蚀出来,提高硅材料的性能,应用范围也非常广泛,在半导体制造以及汽车行业有着重要的作用。
通过以上的介绍,相信大家对硅的干法刻蚀有了更深一步的了解。
干法蚀刻原理

干法蚀刻原理
干法蚀刻是一种高精度微纳加工技术,对集成电路制造、MEMS、
光学器件制造等领域有广泛应用。
下面将介绍干法蚀刻的原理和步骤。
第一步:准备工作
在进行干法蚀刻前,必须准备好样品和刻蚀室。
样品要求平整、
无裂纹、无杂质,并在表面上涂上一层保护层。
刻蚀室内必须保持高
度洁净,且要有良好的通风设施,用于排放有害气体。
第二步:刻蚀气体的选择
干法蚀刻的刻蚀气体有多种选择。
常用气体包括氧气、氟气、氯
气等。
选择合适的刻蚀气体对于达到最佳的蚀刻效果有重要作用。
第三步:晶圆的定位和加热
将晶圆放置在刻蚀平台上,并进行准确的定位。
为了加速刻蚀速度,在刻蚀过程中需要加热晶圆,通常使用辐射热源加热。
第四步:刻蚀过程
在氧气等氧化性较强的气体环境中,晶圆表面的保护层会被氧化,从而产生气体。
这些气体通过微观孔洞扩散到晶圆表面形成气体区。
随着刻蚀的进行,气体区扩大,产生大量的气体流动,对晶圆表面进
行蚀刻。
在氟气等氟化性较强的气体环境中,晶圆表面的保护层会被氟化,从而形成气体。
这些气体通过微观孔洞扩散到晶圆表面形成气体区。
随着刻蚀的进行,气体区扩大,产生大量的气体流动,对晶圆表面进
行蚀刻。
第五步:刻蚀结束
当刻蚀达到一定深度或刻蚀速度变慢时,就需要停止刻蚀。
此时,将晶圆从刻蚀室中取出,并检查刻蚀效果。
以上就是干法蚀刻的基本步骤和原理。
干法蚀刻具有高精度、高
速度、低污染等优点,但会产生大量有害废气,需要加强安全防护和
环境保护。
干法刻蚀工艺的流程
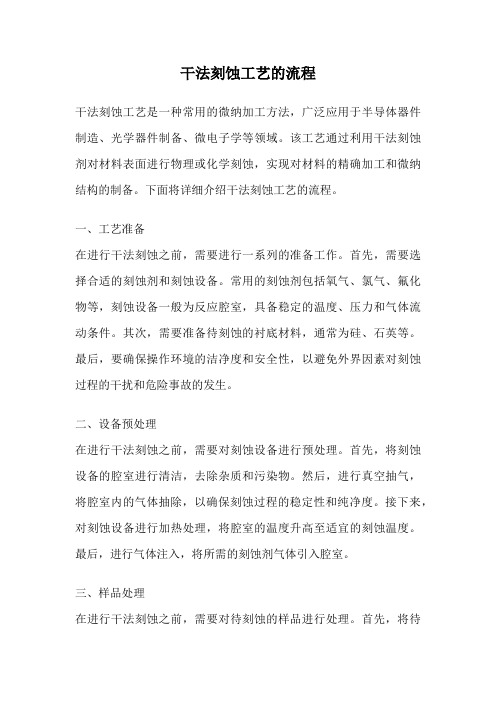
干法刻蚀工艺的流程干法刻蚀工艺是一种常用的微纳加工方法,广泛应用于半导体器件制造、光学器件制备、微电子学等领域。
该工艺通过利用干法刻蚀剂对材料表面进行物理或化学刻蚀,实现对材料的精确加工和微纳结构的制备。
下面将详细介绍干法刻蚀工艺的流程。
一、工艺准备在进行干法刻蚀之前,需要进行一系列的准备工作。
首先,需要选择合适的刻蚀剂和刻蚀设备。
常用的刻蚀剂包括氧气、氯气、氟化物等,刻蚀设备一般为反应腔室,具备稳定的温度、压力和气体流动条件。
其次,需要准备待刻蚀的衬底材料,通常为硅、石英等。
最后,要确保操作环境的洁净度和安全性,以避免外界因素对刻蚀过程的干扰和危险事故的发生。
二、设备预处理在进行干法刻蚀之前,需要对刻蚀设备进行预处理。
首先,将刻蚀设备的腔室进行清洁,去除杂质和污染物。
然后,进行真空抽气,将腔室内的气体抽除,以确保刻蚀过程的稳定性和纯净度。
接下来,对刻蚀设备进行加热处理,将腔室的温度升高至适宜的刻蚀温度。
最后,进行气体注入,将所需的刻蚀剂气体引入腔室。
三、样品处理在进行干法刻蚀之前,需要对待刻蚀的样品进行处理。
首先,将待刻蚀的样品放置在刻蚀设备的样品台上,并固定好位置。
然后,对样品进行清洁,去除表面的污染物和杂质,以提高刻蚀效果和加工质量。
接下来,对样品进行预处理,如涂覆保护层或光刻胶等,以保护待刻蚀区域或定义刻蚀图案。
最后,将样品放置在刻蚀设备的腔室中,准备进行刻蚀加工。
四、刻蚀过程在进行干法刻蚀之前,需要设置好刻蚀的参数。
首先,设定刻蚀剂的流量和温度,以控制刻蚀剂的供应量和活性。
然后,设定刻蚀时间,以控制刻蚀的深度和速率。
接下来,设定刻蚀设备的压力和功率,以控制刻蚀过程的稳定性和效果。
最后,启动刻蚀设备,开始进行刻蚀加工。
在刻蚀过程中,刻蚀剂会与样品表面发生反应,使其发生物理或化学变化,进而实现材料的刻蚀。
通过控制刻蚀剂的流量、温度和时间等参数,可以控制刻蚀的深度和形貌,实现对材料的精确加工。
半导体工艺-干法刻蚀-铝刻蚀
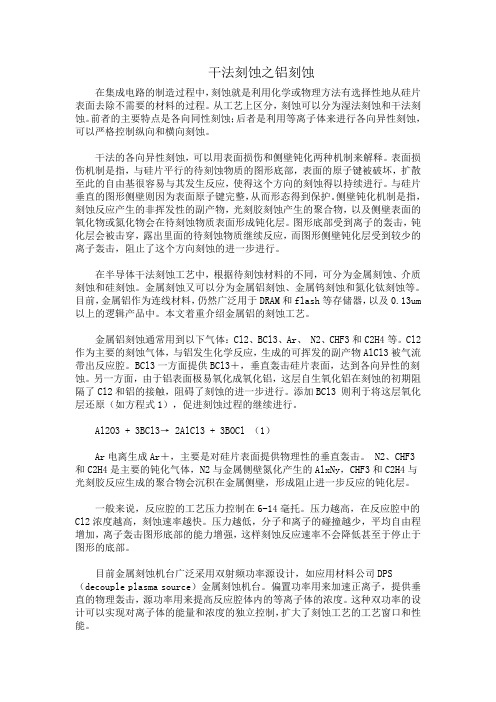
干法刻蚀之铝刻蚀在集成电路的制造过程中,刻蚀就是利用化学或物理方法有选择性地从硅片表面去除不需要的材料的过程。
从工艺上区分,刻蚀可以分为湿法刻蚀和干法刻蚀。
前者的主要特点是各向同性刻蚀;后者是利用等离子体来进行各向异性刻蚀,可以严格控制纵向和横向刻蚀。
干法的各向异性刻蚀,可以用表面损伤和侧壁钝化两种机制来解释。
表面损伤机制是指,与硅片平行的待刻蚀物质的图形底部,表面的原子键被破坏,扩散至此的自由基很容易与其发生反应,使得这个方向的刻蚀得以持续进行。
与硅片垂直的图形侧壁则因为表面原子键完整,从而形态得到保护。
侧壁钝化机制是指,刻蚀反应产生的非挥发性的副产物,光刻胶刻蚀产生的聚合物,以及侧壁表面的氧化物或氮化物会在待刻蚀物质表面形成钝化层。
图形底部受到离子的轰击,钝化层会被击穿,露出里面的待刻蚀物质继续反应,而图形侧壁钝化层受到较少的离子轰击,阻止了这个方向刻蚀的进一步进行。
在半导体干法刻蚀工艺中,根据待刻蚀材料的不同,可分为金属刻蚀、介质刻蚀和硅刻蚀。
金属刻蚀又可以分为金属铝刻蚀、金属钨刻蚀和氮化钛刻蚀等。
目前,金属铝作为连线材料,仍然广泛用于DRAM和flash等存储器,以及0.13um 以上的逻辑产品中。
本文着重介绍金属铝的刻蚀工艺。
金属铝刻蚀通常用到以下气体:Cl2、BCl3、Ar、 N2、CHF3和C2H4等。
Cl2作为主要的刻蚀气体,与铝发生化学反应,生成的可挥发的副产物AlCl3被气流带出反应腔。
BCl3一方面提供BCl3+,垂直轰击硅片表面,达到各向异性的刻蚀。
另一方面,由于铝表面极易氧化成氧化铝,这层自生氧化铝在刻蚀的初期阻隔了Cl2和铝的接触,阻碍了刻蚀的进一步进行。
添加BCl3 则利于将这层氧化层还原(如方程式1),促进刻蚀过程的继续进行。
Al2O3 + 3B Cl3→ 2AlCl3 + 3BOCl (1)Ar电离生成Ar+,主要是对硅片表面提供物理性的垂直轰击。
N2、CHF3和C2H4是主要的钝化气体,N2与金属侧壁氮化产生的AlxNy,CHF3和C2H4与光刻胶反应生成的聚合物会沉积在金属侧壁,形成阻止进一步反应的钝化层。
干法刻蚀原理

干法刻蚀原理
干法刻蚀是一种常见的微纳加工技术,广泛应用于半导体、光电子、生物医学等领域。
干法刻蚀的原理是利用化学气相反应或物理干法去除材料表面的部分,从而实现微纳米结构的加工。
本文将介绍干法刻蚀的原理及其在微纳加工中的应用。
首先,干法刻蚀的原理是利用化学气相反应或物理干法去除材料表面的部分。
在化学气相反应中,通常会使用一种或多种气体,通过化学反应去除材料表面的部分。
而在物理干法中,则是利用物理手段,如离子轰击、等离子体腐蚀等去除材料表面的部分。
这两种方式都可以实现对材料表面的精确加工,从而形成所需的微纳米结构。
其次,干法刻蚀在微纳加工中有着广泛的应用。
在半导体制造中,干法刻蚀可以用于形成电路图案、蚀刻绝缘层等。
在光电子领域,干法刻蚀可以用于制备光子晶体、光波导等微纳结构。
在生物医学领域,干法刻蚀可以用于制备生物芯片、微流控芯片等。
可以说,干法刻蚀在微纳加工中扮演着至关重要的角色。
总之,干法刻蚀是一种利用化学气相反应或物理干法去除材料
表面的部分的微纳加工技术。
它在半导体、光电子、生物医学等领域有着广泛的应用。
随着科技的不断进步,相信干法刻蚀技术会在更多领域展现出其强大的潜力。
单晶硅干法刻蚀代加工

单晶硅干法刻蚀代加工
单晶硅作为半导体材料广泛应用于电子行业,单晶硅干法刻蚀是电子行业中用于制作集成电路电子元件的重要工艺。
因其具有精度高、结构紧凑、功能齐全等特点,受到越来越多的重视。
单晶硅干法刻蚀代加工是通过在单晶硅表面形成一种非晶膜来
实现的。
首先,用水素气体向单晶硅表面施加氧化热处理,以使其表面产生氧化层,氧化层可以有效地防止金属粒子进入,抑制表面失活和污染,从而使单晶硅具有高精度的加工性能。
接下来,将一种粒子状液体分布在表面上,经过恒定的电流刺激,使液体粒子的电荷发生变化,从而促进液体的分解,形成一种非晶膜。
单晶硅干法刻蚀代加工的过程是利用氧化层和非晶膜的力学性能,使多层膜的粘附力大于接触面之间的剪切力,从而进行有效的分解和消除。
接着,对非晶膜进行处理,有助于提高分解和去除效率,并有助于减少残留污垢。
此外,还可以通过水洗或酸洗来进一步去除杂质,从而实现最佳的加工结果。
单晶硅干法刻蚀代加工使得在微电子集成电路的制作中能够实
现更精确的刻蚀精度。
除了加工精度高外,它还有一个显著的优点,就是它的加工成本低廉,可以在短时间内提供大量的加工产品,满足客户的需求。
单晶硅干法刻蚀代加工技术的出现,为电子行业的发展奠定了基础,具有很强的现实意义。
它的出现,使得微电子行业能够更有效地开发新产品,制造更高精度的电子元件,节省成本,降低污染,甚至
可以提高产品的质量,提升企业的效率。
综上所述,单晶硅干法刻蚀代加工技术在微电子行业的应用前景非常广阔,它的出现为电子行业的发展带来了益处,必将在未来具有重要的作用。
干法刻蚀步骤
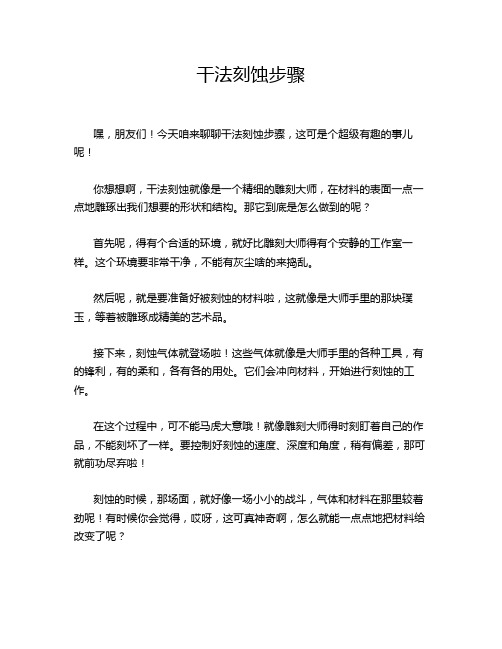
干法刻蚀步骤嘿,朋友们!今天咱来聊聊干法刻蚀步骤,这可是个超级有趣的事儿呢!你想想啊,干法刻蚀就像是一个精细的雕刻大师,在材料的表面一点一点地雕琢出我们想要的形状和结构。
那它到底是怎么做到的呢?首先呢,得有个合适的环境,就好比雕刻大师得有个安静的工作室一样。
这个环境要非常干净,不能有灰尘啥的来捣乱。
然后呢,就是要准备好被刻蚀的材料啦,这就像是大师手里的那块璞玉,等着被雕琢成精美的艺术品。
接下来,刻蚀气体就登场啦!这些气体就像是大师手里的各种工具,有的锋利,有的柔和,各有各的用处。
它们会冲向材料,开始进行刻蚀的工作。
在这个过程中,可不能马虎大意哦!就像雕刻大师得时刻盯着自己的作品,不能刻坏了一样。
要控制好刻蚀的速度、深度和角度,稍有偏差,那可就前功尽弃啦!刻蚀的时候,那场面,就好像一场小小的战斗,气体和材料在那里较着劲呢!有时候你会觉得,哎呀,这可真神奇啊,怎么就能一点点地把材料给改变了呢?等刻蚀完成后,你再去看看那材料,哇,完全变了个样!就像一件普通的石头经过大师的雕琢,变成了一件令人惊叹的艺术品。
干法刻蚀步骤不就是这样吗?看似简单,实则充满了奥秘和技巧。
每一步都得小心翼翼,每一个环节都不能出错。
这可不是随便谁都能做好的事儿,得需要专业的知识和丰富的经验呢!咱再想想,生活中不也有很多这样的事情吗?就像学一门手艺,或者做一件很重要的事情,都得一步一个脚印,认真对待每一个细节。
不然,怎么能做出好的成果呢?所以啊,干法刻蚀步骤可不仅仅是在实验室里的那些操作,它也给我们带来了很多启示呢!让我们明白,做任何事情都要有耐心、细心和恒心。
怎么样,干法刻蚀步骤是不是很有意思?是不是让你对这个世界又多了一份好奇和探索的欲望呢?那就赶紧去了解更多吧!。
干法刻蚀的优点和过程
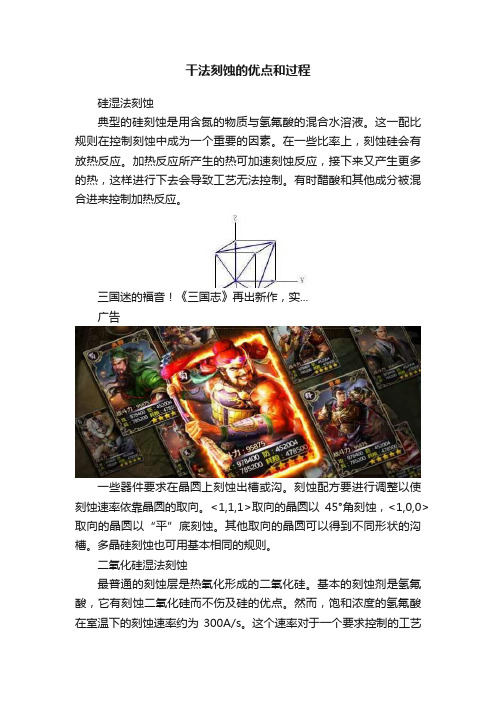
干法刻蚀的优点和过程硅湿法刻蚀典型的硅刻蚀是用含氮的物质与氢氟酸的混合水溶液。
这一配比规则在控制刻蚀中成为一个重要的因素。
在一些比率上,刻蚀硅会有放热反应。
加热反应所产生的热可加速刻蚀反应,接下来又产生更多的热,这样进行下去会导致工艺无法控制。
有时醋酸和其他成分被混合进来控制加热反应。
三国迷的福音!《三国志》再出新作,实...广告一些器件要求在晶圆上刻蚀出槽或沟。
刻蚀配方要进行调整以使刻蚀速率依靠晶圆的取向。
<1,1,1>取向的晶圆以45°角刻蚀,<1,0,0>取向的晶圆以“平”底刻蚀。
其他取向的晶圆可以得到不同形状的沟槽。
多晶硅刻蚀也可用基本相同的规则。
二氧化硅湿法刻蚀最普通的刻蚀层是热氧化形成的二氧化硅。
基本的刻蚀剂是氢氟酸,它有刻蚀二氧化硅而不伤及硅的优点。
然而,饱和浓度的氢氟酸在室温下的刻蚀速率约为300A/s。
这个速率对于一个要求控制的工艺来说太快了。
展开剩余79%在实际中,氢氟酸与水或氟化铵及水混合。
以氟化铵来缓冲加速刻蚀速率的氢离子的产生。
这种刻蚀溶液称为缓冲氧化物刻蚀或BOE。
针对特定的氧化层厚度,他们以不同的浓度混合来达到合理的刻蚀时间。
一些BOE公式包括一个湿化剂用以减小刻蚀表面的张力,以使其均匀地进入更小的开孔区。
暴露硅晶圆表面的过刻蚀可以引起表面的粗糙。
在氢氟酸工艺期间,当暴露于OH-离子时,在刻蚀中硅表面会变粗糙。
铝膜湿法刻蚀对于铝和铝合金层有选择性的刻蚀溶液是居于磷酸的。
遗憾的是,铝和磷酸反应的副产物是微小的氢气泡。
这些气泡附着在晶圆表面,并阻碍刻蚀反应。
结果既可能产生导致相邻引线短路的铝桥连,又可能在表面形成不希望出现的雪球的铝点。
特殊配方铝刻蚀溶液的使用缓解了这个问题。
典型的活性溶液成分配比是:16:1:1:2。
除了特殊配方外,典型的铝刻蚀工艺还会包含以搅拌或上下移动晶圆舟的搅动。
有时超声波或兆频超声波也用来去除气泡。
淀积氧化物湿法刻蚀晶圆上的最终膜层之一是一层在铝膜上的二氧化硅钝化膜。
干法刻蚀工艺
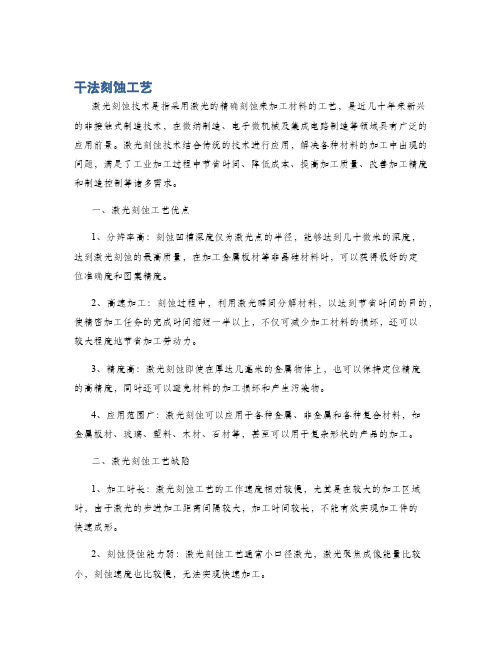
干法刻蚀工艺激光刻蚀技术是指采用激光的精确刻蚀来加工材料的工艺,是近几十年来新兴的非接触式制造技术,在微纳制造、电子微机械及集成电路制造等领域具有广泛的应用前景。
激光刻蚀技术结合传统的技术进行应用,解决各种材料的加工中出现的问题,满足了工业加工过程中节省时间、降低成本、提高加工质量、改善加工精度和制造控制等诸多需求。
一、激光刻蚀工艺优点1、分辨率高:刻蚀凹槽深度仅为激光点的半径,能够达到几十微米的深度,达到激光刻蚀的最高质量,在加工金属板材等非晶硅材料时,可以获得极好的定位准确度和图案精度。
2、高速加工:刻蚀过程中,利用激光瞬间分解材料,以达到节省时间的目的,使精密加工任务的完成时间缩短一半以上,不仅可减少加工材料的损坏,还可以较大程度地节省加工劳动力。
3、精度高:激光刻蚀即使在厚达几毫米的金属物体上,也可以保持定位精度的高精度,同时还可以避免材料的加工损坏和产生污染物。
4、应用范围广:激光刻蚀可以应用于各种金属、非金属和各种复合材料,如金属板材、玻璃、塑料、木材、石材等,甚至可以用于复杂形状的产品的加工。
二、激光刻蚀工艺缺陷1、加工时长:激光刻蚀工艺的工作速度相对较慢,尤其是在较大的加工区域时,由于激光的步进加工距离间隔较大,加工时间较长,不能有效实现加工件的快速成形。
2、刻蚀侵蚀能力弱:激光刻蚀工艺通常小口径激光,激光聚焦成像能量比较小,刻蚀速度也比较慢,无法实现快速加工。
3、加工精度受物理环境变化:激光刻蚀工艺是基于激光特定波长,光束密度及聚焦深度的精确控制,加工精度受环境变化特别敏感,一般由环境因素引起的变化都会影响加工的精度,使精度变动不能满足要求。
4、利用率低:激光刻蚀加工能利用率较低,需要做多次分布式去毛刺等操作,耗费时间且容易损坏加工表面,所以对零件的质量要求较高。
第10章干法刻蚀

第10章干法刻蚀
26
反应离子束刻蚀
• 大束径离子束刻蚀:束径10~20 cm,效率高,质量均匀。 常用大束径离子束设备有两种:
Kaufman型:热阴极、
ECR型:冷阴极
磁控管阳极组合放电
放电ECR离子源
第10章干法刻蚀
27
气体离化团束加工技术
• 材料表面改性技术的发展要求轰击离子注入到靶材表面的深度在 数纳米范围内,而低能离子束很难实现这一要求。
• 气体离化团束 (GCIB) 中束团的动能由组成原子共享,平均每个 原子的入射能量约在10 eV以下。因而,在碰撞过程中,团束原 子的整体运动使得团束仅对靶材表面的前几个原子层产生轰击效 应。
30 kV的气体离化团束设备图
第10章干法刻蚀
28
气体离化团束加工技术
• GCIB的优点:
➢ 浅层注入,损伤小; ➢ 高产额溅射(比单原子离子高出100倍以上); ➢ 侧向溅射,利于表面平坦化; ➢ 表面清洁效率高。
第10章干法刻蚀
15
干法刻蚀的机制
等离子体干法刻蚀机理及刻蚀参数对比
刻蚀参数 刻蚀机理 侧壁剖面
物理刻蚀 RF场垂直片面 物理离子溅射
各向异性
化学刻蚀 物理和化学刻蚀 RF场平行片面 RF场垂直片面
活性元素 化学反应
离子溅射和活性 元素化学反应
各向同性
各向异性
选择比 刻蚀速率
低/难提高 (1:1)
高
很高 (500:1)
慢
高(5:1 ~100:1)
适中
线宽控制
好
非常差
很好
第10章干法刻蚀
16
干法刻蚀的过程
硅片的等离子体刻蚀过程图
第10章干法刻蚀
干法刻蚀工艺

干法刻蚀工艺干法刻蚀工艺可分为物理性刻蚀与化学性刻蚀两种方式。
物理性刻蚀是利用辉光放电将气体(如氩)电离成带正电的离子,再利用偏压将离子加速,溅击在被刻蚀物的表面而将被刻蚀物的原子击出,该过程完全是物理上的能量转移,故称为物理性刻蚀。
其特色在于,具有非常好的方向性,可获得接近垂直的刻蚀轮廓。
但是由于离子是全面均匀地溅射在芯片上,所以光刻胶和被刻蚀材料同时被刻蚀,造成刻蚀选择性偏低。
同时,被击出的物质并非挥发性物质,这些物质容易二次沉积在被刻蚀薄膜的表面及侧壁上。
因此,在超大规模集成化制作工艺中,很少使用完全物理方式的干法刻蚀方法。
化学性刻蚀或称为等离子体刻蚀( PLASMA Etching,PE),是利用等离子体将刻蚀气体电离并形成带电离子、分子及反应性很强的原子团,它们扩散到被刻蚀薄膜表面后与被刻蚀薄膜的表面原子反应生成具有挥发性的反应产物,并被真空设备抽离反应腔。
因这种反应完全利用化学反应,故称为化学性刻蚀。
这种刻蚀方式与前面所讲的湿法刻蚀类似,只是反应物与产物的状态从液态改为气态,并以等离子体来加快反应速率。
因此,化学性干法刻蚀具有与湿法刻蚀类似的优点与缺点,即具有较高的掩膜/底层的选择比及等向性。
鉴于化学性刻蚀等向性的缺点,在半导体工艺中,只在刻蚀不需要图形转移的步骠(如光刻胶的去除)中应用纯化学刻蚀方法。
最为广泛使用的方法是结合物理性的离子轰击与化学反应的反应离子刻蚀( RIE)。
这种方式兼具非等向性与高刻蚀选择比的双重优点。
刻蚀的进行主要靠化学反应来实现,加入离子轰击的作用有两方面。
1)破坏被刻蚀材质表面的化学键以提高反应速率。
2)将二次沉积在被刻蚀薄膜表面的产物或聚合物打掉,以使被刻蚀表面能充分与刻蚀气体接触。
由于在表面的二次沉积物可被离子打掉,而在侧壁上的二次沉积物未受到离子的轰击,可以保留下来阻隔刻蚀表面与反应气体的接触、使得侧壁不受刻蚀,所以采用这种方式可以获得非等向性的刻蚀效果。
干法刻蚀工艺总结

干法刻蚀工艺总结离子束刻蚀机(IBE-150A)背景:利用辉光放电原理将氩气分解为氩离子,氩离子经过阳极电场的加速对样品表面进行物理轰击,以达到刻蚀的作用。
把Ar、Kr或Xe之类惰性气体充入离子源放电室并使其电离形成等离子体,然后由栅极将离子呈束状引出并加速,具有一定能量的离子束进入工作室,射向固体表面撞击固体表面原子,使材料原子发生溅射,达到刻蚀目的,属纯物理过程。
技术指标:装片:一片六英寸衬底、或1片四英寸,向下兼容。
抽气速度:30min由ATM到1.0×10-3Pa极限真空度:2×10-4Pa离子能量:300eV-400eVICP刻蚀机(OXFORD ICP 180)背景:通入反应气体使用电感耦合等离子体辉光放电将其分解,产生的具有强化学活性的等离子体在电场的加速作用下移动到样品表面,对样品表面既进行化学反应生成挥发性气体,又有一定的物理刻蚀作用。
因为等离子体源与射频加速源分离,所以等离子体密度可以更高,加速能力也可以加强,以获得更高的刻蚀速率,以及更好的各向异性刻蚀。
另外,由于该系统使用了Cl基和Br基的刻蚀气体,因此该ICP系统适合于对Ⅲ-Ⅴ族化合物材料进行刻蚀。
技术指标:ICP离子源:0~3000WRF射频源:0~600W装片:1片四英寸,向下兼容基底刻蚀温度:0℃-200℃可调。
刻蚀气体:BCl3、Cl2、HBr、Ar、O2可刻蚀材料包括:GaN、GaAs、InP等Ⅲ-Ⅴ族化合物材料ICP刻蚀机(STS HRM)背景:通入反应气体使用电感耦合等离子体辉光放电将其分解,产生的具有强化学活性的等离子体在电场的加速作用下移动到样品表面,对样品表面既进行化学反应生成挥发性气体,又有一定的物理刻蚀作用。
因为等离子体源与射频加速源分离,所以等离子体密度可以更高,加速能力也可以加强,以获得更高的刻蚀速率,以及更好的各向异性刻蚀。
该系统使用了F基的刻蚀气体,具有Bosch工艺,适合于对硅材料进行大深宽比刻蚀。
- 1、下载文档前请自行甄别文档内容的完整性,平台不提供额外的编辑、内容补充、找答案等附加服务。
- 2、"仅部分预览"的文档,不可在线预览部分如存在完整性等问题,可反馈申请退款(可完整预览的文档不适用该条件!)。
- 3、如文档侵犯您的权益,请联系客服反馈,我们会尽快为您处理(人工客服工作时间:9:00-18:30)。
sinx干法刻蚀工艺
一、引言
干法刻蚀工艺是一种常用于微电子制造中的重要工艺,被广泛应用于半导体器件、光电子器件以及微纳加工领域。
其中,sinx干法刻蚀工艺是一种常见且重要的技术,本文将对其原理、工艺流程以及应用进行介绍。
sinx干法刻蚀工艺是基于化学气相刻蚀技术实现的。
其主要原理是通过将硅表面暴露于含有氟气和氧气的刻蚀气体环境中,形成硅氧化物(SiOx)层,而后使用氟气将其刻蚀去除。
由于刻蚀速率与刻蚀气体的浓度、温度、压力等因素相关,因此可以通过调节这些参数来控制刻蚀速率和刻蚀深度,从而实现对硅表面的精确刻蚀。
三、sinx干法刻蚀工艺流程
sinx干法刻蚀工艺主要包括前处理、刻蚀和后处理三个步骤。
1. 前处理:首先需要对待刻蚀的硅表面进行清洗,以去除表面的杂质和有机物。
常用的清洗方法包括酸洗、碱洗和超声清洗等。
清洗后,将硅片放入刻蚀室中,进行真空抽取和预热处理。
2. 刻蚀:在刻蚀室中,加入刻蚀气体,常用的刻蚀气体有氟化氢(HF)和氟化氮(NF3)等。
调节刻蚀气体的流量、温度和压力等参数,控制刻蚀速率和刻蚀深度。
刻蚀过程中,通过监测刻蚀速率
以及表面形貌等参数,进行实时调节和控制。
3. 后处理:刻蚀完成后,需要对刻蚀后的硅片进行清洗和去除刻蚀残留物。
然后,进行表面抛光和再清洗等步骤,以保证硅片表面的光洁度和无尘污。
最后,进行检测和质量控制,确保刻蚀工艺的稳定性和一致性。
四、sinx干法刻蚀工艺应用
sinx干法刻蚀工艺在微电子制造中有着广泛的应用。
主要应用于制备硅氧化物(SiOx)薄膜,用于制作MOS场效应晶体管、光电子器件和微纳加工等领域。
此外,sinx干法刻蚀工艺还可以用于制备硅纳米线、纳米孔洞和微纳结构等,用于研究和应用于纳米器件和生物传感器等领域。
五、总结
sinx干法刻蚀工艺是一种重要的微电子制造工艺,通过调节刻蚀气体的浓度、温度和压力等参数,可以实现对硅表面的精确刻蚀。
该工艺应用广泛,可用于制备硅氧化物薄膜和制作各种微纳器件。
在实际应用中,需要进行严格的工艺控制和质量检测,以确保刻蚀效果和产品质量的稳定性。
随着微纳加工技术的发展,sinx干法刻蚀工艺将继续发挥重要作用,并在新的应用领域中有更广阔的发展前景。