数控铣削加工工艺
第六章 数控铣削加工工艺
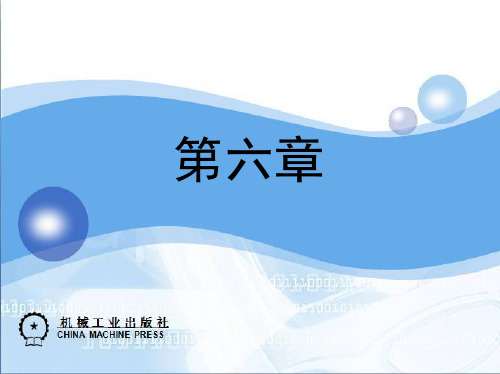
图6-33 几种常用的成形铣刀
第一节 数控铣削加工工艺的制订
2.铣刀的选择 (1)面铣刀主要参数的选择 标准可转位面铣刀直径为ϕ1 6~ϕ630mm,应根据侧吃刀量ae,选择适当的铣刀直径, 尽量包容工件整个加工宽度,以提高加工精度和效率,减 小相邻两次进给之间的接刀痕迹和保证铣刀的寿命。
图6-34 面铣刀几何角度的标注
第六章
第一节 数控铣削加工工艺的制订
一、零件的工艺性分析 1.零件的结构工艺性分析 1)检查零件的加工要求,如加工尺寸公差、几何公差及表 面粗糙度在现有的加工条件下是否可以得到保证,是否还 有更经济的加工方法或方案。 2)分析零件的形状、结构及尺寸的特点,确定零件上是否 有妨碍刀具运动的部位,是否有会产生加工干涉或加工不 到的区域,零件的最大形状尺寸是否超过机床的最大行程, 零件的刚性随着加工的进行是否有太大的变化等。
第一节 数控铣削加工工艺的制订
3)在零件上是否存在对刀具形状及尺寸有限制的部位和尺 寸要求,如过渡圆角、倒角、槽宽等,这些尺寸是否过于 凌乱,是否可以统一。 4)保证基准统一原则。 5)分析零件的变形情况。 2.零件毛坯的工艺性分析 1)毛坯应有充分、稳定的加工余量。 2)分析毛坯的余量大小及均匀性。 3)分析毛坯的装夹适应性。
第一节 数控铣削加工工艺的制订
图6-3 通用可调气动台虎钳 a)通用可调气动台虎钳 b) 、c)更换调整件 1、2—可更换调整件 3—活动钳口 4—粗调螺杆 5—活塞杆
6—杠杆 7—活塞
第一节 数控铣削加工工艺的制订
图6- 4 通用可调夹具系统 1—基础件 2—立式液压缸 3—卧式液压缸 4、5—销
第一节 数控铣削加工工艺的制订
图6-8 用鼓形铣刀分层铣削变斜角
数控铣削加工工艺与编程实例
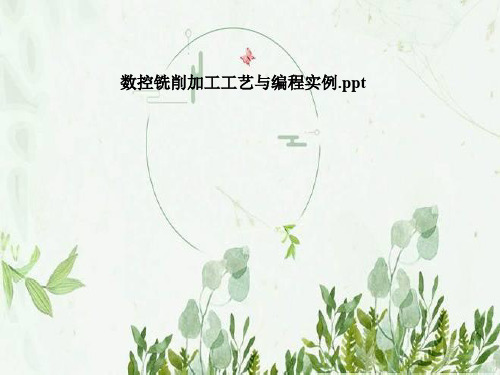
(3)工、量、刃具选择
(4)合理选择切削用量
2.编制参考程序 1)认真阅读零件图,确定工件坐标系。根据工件坐标系 建立原则,X、Y向加工原点选在φ60H7mm孔的中心, Z向加工原点选在B面(不是毛坯表面)。工件加工原点 与设计基准重合,有利于编程计算的方便,且易保证零 件的加工精度。Z向对刀基准面选择底面A,与工件的定 位基准重合,X、Y向对刀基准面可选择φ60H7mm毛坯 孔表面或四个侧面。 2)计算各基点(节点)坐标值。如图3-112所示各圆的 圆心坐标值见表3-32。
子程序:
3.6.4 加工中心零件的编程与操作
图3-105所示为端盖零件,其材料为45钢,毛坯尺寸为 160mm×160mm×19mm。试编写该端盖零件的加工 程序并在XH714加工中心上加工出来。
(1)加工方法 由图3-105可知,该盖板材料为铸铁,故毛坯为铸件,四 个侧面为不加工表面,上下面、四个孔、四个螺纹孔、 直径为φ60mm的孔为加工面,且加工内容都集中在A、 B面上。从定位、工序集中和便于加工考虑,选择A面为 定位基准,并在前道工序中加工好,选择B面及位于B面 上的全部孔在加工中心上一次装夹完成加工。 该盖板零件形状较简单,尺寸较小,四个侧面较光滑, 加工面与非加工面之间的位置精度要求不高,故可选机 用平口钳,以盖板底面A和两个侧面定位,用机用平口 钳的钳口从侧面夹紧。
3)参考程序:数控加工程序单见表3-33。
加工φ160mm中心线上孔的子程序的数控加工程序单见 表3-33。
加工φ100mm中心线上孔的子程序的数控加工程序单见 表3-33。
3.操作步骤及内容 1)机床上电。合上空气开关,按“NC启动”。 2)回参考点。选择“机械回零”方式,按下“循环启动”按钮,完成 回参考点操作。返回零点后,X、Y、Z三轴向负向移动适当距离。 3)刀具安装。按要求将所有刀具安装到刀库,注意刀具号是否正 确。 4)清洁工作台,安装夹具和工件。检查坯料的尺寸,确定工件的 装夹方式(用机用虎钳夹紧)。将机用虎钳清理干净装在干净的工 作台上,通过百分表找正、找平机用虎钳并夹紧,再将工件装正在 机用虎钳上,工件伸出钳口8mm左右。
数控铣床与铣削加工工艺

数控铣床与铣削加工工艺引言数控铣床是一种广泛应用于制造业的机床,通过其高精度和高效率的加工能力,可以实现各种复杂零件的铣削加工。
本文将介绍数控铣床的基本原理、工作过程以及常见的铣削加工工艺。
数控铣床的基本原理数控铣床是利用计算机技术控制加工过程的一种机床。
它通过内置的电脑控制系统,以预先输入的加工程序为基础,自动控制刀具在工件上进行铣削加工。
数控铣床的加工精度高、效率高,并且可以实现复杂零件的加工。
数控铣床由控制系统、驱动系统、机械系统和辅助系统组成。
其中,控制系统负责接收和处理加工程序,并将其转化为指令;驱动系统负责控制各个轴向的运动,实现刀具的准确定位和运动;机械系统则完成刀具与工件之间的相对运动;辅助系统包括刀具库、自动换刀装置等。
数控铣床的工作过程数控铣床的工作过程主要分为加工准备、程序输入、参数设定、加工操作和加工结束等几个步骤。
1.加工准备:准备好需要加工的工件和刀具,确保工件和刀具的安装正确。
2.程序输入:将加工程序输入到数控铣床的控制系统中。
加工程序是一组描述加工过程的指令,包括切削速度、切削深度、刀具半径等。
3.参数设定:根据工件的要求和加工程序的要求,设定数控铣床的各项参数,如进给速度、主轴转速、切削深度等。
这些参数的设定直接影响加工的效果和质量。
4.加工操作:启动数控铣床的控制系统,根据输入的加工程序和参数进行加工操作。
数控铣床会根据程序的要求,控制刀具在工件上进行准确的运动,进行铣削加工。
5.加工结束:加工完成后,数控铣床会自动停止运动,并提示操作员进行下一步操作。
常见的铣削加工工艺铣削是数控铣床最主要的加工工艺之一,它包括平面铣削、曲面铣削、镗削、拉削等多种形式。
平面铣削平面铣削是指将工件表面上的不规则区域修整平整的加工过程。
铣床刀具进行水平方向上的直线运动,通过多次铣削,使工件表面呈现平整的平面形状。
曲面铣削曲面铣削是指将工件表面上的曲面进行加工,使其达到指定的形状和尺寸。
数控铣削加工工艺与编程

数控铣削加工工艺与编程一、数控铣削主要加工对象数控铣削是机械加工中最常用的加工方法之一,它主要包括平面铣削和轮廓铣削,还可以对零件进行钻、扩、铰、镗、锪加工及攻螺纹等。
数控铣床有立式、卧式、龙门式三类,数控铣床加工工艺以普通铣床加工工艺为基础,数控加工中心从结构上看是带刀库的镗铣床,除铣削加工外,也可以对零件进行钻、扩、铰、镗、锪加工及攻螺纹等,因此数控铣床与数控加工中心从工艺上看加工工艺类似,主要适用于下列几类零件的加工。
1、平面类零件平面类零件是指加工面平行、垂直于水平面或其加工面与水平面的夹角为定角的零件,这类零件的特点是,各个加工表面是平面,或展开为平面。
如图4-1所示的三个零件都属于平面类零件,其中的曲线轮廓面M和正圆台面N,展开后均为平面。
图4-1 平面类零件2、变斜角类零件加工面与水平面的夹角呈连续变化的零件称为变斜角类零件。
图4-2是飞机上的一种变斜角梁缘条,该零件在第②肋至第⑤肋的斜角α从3°10′均匀变12肋又均匀化为2°32′,从第⑤肋至第⑨肋再均匀变化为1°20′,最后到第○变化至0°。
变斜角类零件的变斜角加工面不能展开为平面,但在加工中,加工面与铣刀圆周接触的瞬间为一条直线。
加工变斜角类零件最好采用四坐标和五坐标数控铣床摆角加工,在没有上述机床时,也可在三坐标数控铣床上进行二轴半控制的近似加工。
图4-2 变斜角零件3、曲面类零件加工面为空间曲面的零件称为曲面类零件。
曲面类零件的加工面不仅不能展开为平面,而且它的加工面与铣刀始终为点接触。
加工曲面类零件一般采用三坐标数控铣床。
加工曲面类零件的刀具一般使用球头刀具,因为其他刀具加工曲面时更容易产生干涉而过切邻近表面。
加工立体曲面类零件一般使用三坐标数控铣床,采用以下两种加工方法。
(1)行切加工法采用三坐标数控铣床进行二轴半坐标控制加工,即行切加工法。
如图4-3所示,球头铣刀沿XY平面的曲线进行直线插补加工,当一段曲线加工完后,沿X方向进给ΔX再加工相邻的另一曲线,如此依次用平面曲线来逼近整个曲面。
数控铣削加工工艺与编程
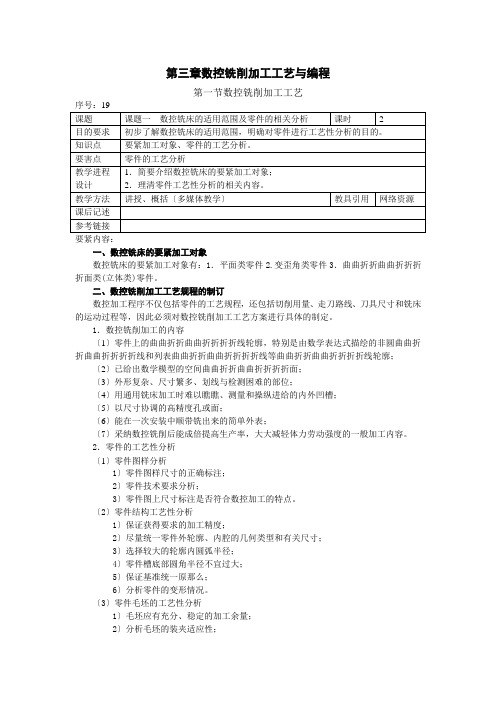
第三章数控铣削加工工艺与编程第一节数控铣削加工工艺序号:19要紧内容:一、数控铣床的要紧加工对象数控铣床的要紧加工对象有:1.平面类零件2.变歪角类零件3.曲曲折折曲曲折折折折面类(立体类)零件。
二、数控铣削加工工艺规程的制订数控加工程序不仅包括零件的工艺规程,还包括切削用量、走刀路线、刀具尺寸和铣床的运动过程等,因此必须对数控铣削加工工艺方案进行具体的制定。
1.数控铣削加工的内容〔1〕零件上的曲曲折折曲曲折折折折线轮廓,特别是由数学表达式描绘的非圆曲曲折折曲曲折折折折线和列表曲曲折折曲曲折折折折线等曲曲折折曲曲折折折折线轮廓;〔2〕已给出数学模型的空间曲曲折折曲曲折折折折面;〔3〕外形复杂、尺寸繁多、划线与检测困难的部位;〔4〕用通用铣床加工时难以瞧瞧、测量和操纵进给的内外凹槽;〔5〕以尺寸协调的高精度孔或面;〔6〕能在一次安装中顺带铣出来的简单外表;〔7〕采纳数控铣削后能成倍提高生产率,大大减轻体力劳动强度的一般加工内容。
2.零件的工艺性分析〔1〕零件图样分析1〕零件图样尺寸的正确标注;2〕零件技术要求分析;3〕零件图上尺寸标注是否符合数控加工的特点。
〔2〕零件结构工艺性分析1〕保证获得要求的加工精度;2〕尽量统一零件外轮廓、内腔的几何类型和有关尺寸;3〕选择较大的轮廓内圆弧半径;4〕零件槽底部圆角半径不宜过大;5〕保证基准统一原那么;6〕分析零件的变形情况。
〔3〕零件毛坯的工艺性分析1〕毛坯应有充分、稳定的加工余量;2〕分析毛坯的装夹适应性;3〕分析毛坯的余量大小及均匀性。
小结:数控铣床要紧加工对象的特点、零件的工艺性分析。
序号:20课题课题二数控铣削工艺路线课时 2目的要求具体了解制定数控铣削工艺路线的各个环节,明确各项细那么,掌握“合理〞度。
知识点加工方法、工序、加工顺序、装夹方案、进给路线、切进、切出、行切、环切。
要害点加工方法、加工顺序、进给路线、切进、切出教学进程设计1.具体介绍数控铣削工艺路线的各个环节;2.强调合理性;3.举例引证。
数控加工零件的工艺分析与数控铣削加工工艺

数控加工零件的工艺分析与数控铣削加工工艺数控加工是指利用计算机数控系统,通过编写程序控制机床工作来加工零件的一种加工方式。
在工业生产中,数控加工因其高精度、高效率、高灵活性等优点而被广泛应用。
其中数控铣削是一种常见的数控加工方式,本文将从工艺分析、数控铣削加工工艺等方面进行探讨。
一、数控加工零件的工艺分析工艺分析是数控加工的一项前置工作,它的目的是确定加工工艺,选择合适的加工设备和刀具,制定加工程序等,从而保证加工质量和效率。
具体而言,工艺分析主要包括以下几个方面:1. 零件的材质和形状:不同材质的加工性能不同,加工时需要选择相应的切削参数和刀具;而零件的形状和结构也会影响加工难度和精度,需要对其进行全面分析和评估。
2. 加工精度和表面质量要求:根据零件的要求,确定加工精度和表面质量目标,制定相应的切削参数和工艺措施。
3. 工序分析:对零件进行逐个工序分析,确定加工顺序、加工方向、加工路径和刀具选择等重要内容,同时把握好每个工序的加工质量和效率。
4. 刀具选择:根据加工材料、零件形状和要求,选择合适的刀具和刀具尺寸,保证零件的加工质量和加工效率。
5. 加工程序制定:通过数控编程软件,编写机床加工程序,包括各种切削参数、刀具路径、指令参数等信息,为数控加工提供参考。
二、数控铣削加工工艺数控铣削是一种高速旋转的刀具在工件表面上进行切削的加工方式,它广泛应用于金属、塑料等材料制件的加工中。
数控铣削在工件制作中具有大量价值和应用,且数控铣削加工工艺也是半自动化和自动化制造中的重要工艺之一。
要把好铣削的关,需要具备以下几点:1. 刀具选择:刀具的选择是影响加工效率和加工质量的重要因素之一。
首先需要考虑切削材料,选择高速钢、硬质合金、陶瓷等材质的刀具;其次要考虑刀具尺寸和形状,根据零件的要求选择合适的刀具。
2. 切削参数:切削参数包括切削速度、进给量和切削深度等,这些参数的选定与零件材料、刀具材料、刀具尺寸和表面质量等因素密切相关。
数控加工工艺 (3)
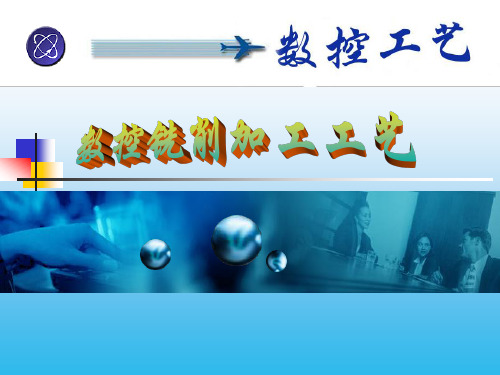
背吃刀量ap为平行于铣刀轴线测量的切削层尺寸,单位为mm 。端铣时ap为切削层深度;而圆周铣时,ap为被加工表面的宽度
。
侧吃刀量ae为垂直于铣刀轴线测量的切削层尺寸,单位为mm。 端铣时ae为被加工表面的宽度;而圆周铣时为切削层的深度。
背吃刀量或侧吃刀量的选取主要由加工余量和对表面质量的要求 决定。
4.铣削内外轮廓的进给路线
当内部几何元素相切无交点时,为防止刀补取消时在轮廓拐角处 留下凹口,刀具切入切出点应远离拐角。
当整圆加工完毕时,不要在切点处直接退刀,而应让刀具沿切线 方向多运动一段距离,以免取消刀补时,刀具与工件表面相碰, 造成工件报废。
铣削外圆的切入切出路径
从拐角切入切 出,容易产 生过切现象。
(1)直角沟槽的铣削 直角通槽主要用三面刃铣刀来铣削,也可用立铣刀、槽铣刀和
合成铣刀来铣削。对封闭的沟槽则都采用立铣刀或键槽铣刀。 (2)键槽的铣削方法 ①铣通键槽 ②铣封闭键槽 (3)T形槽的铣削 ①铣T形槽的步骤 ②铣T形槽应注意的事项
T形槽的铣削步骤
22
数控加工工艺
二、常见零件的数控铣削方法
二、数控铣削加工工序的划分 1.加工阶段的划分
(1)加工阶段 (2)数控铣加工工序的划分原则
按所用刀具划分。如加工中心,减少换刀次数。 按安装次数划分。减少定位误差。 按粗、精加工划分。减少误差复映,提高加工精度。 按加工部位划分。减少空行程,提高效率。
30
数控加工工艺
二、数控铣削加工工序的划分
14
数控加工工艺
三、铣刀的选择
1.铣刀形式的选择
铣刀的选择必须符合铣刀使用的规范;超规范的使用会损坏铣刀, 造成废品。
第3章数控铣削加工工艺(教案9)

第3章 数控铣削加工工艺
(3) 铣刀端刃圆角半径r的选择。铣刀端刃圆角半径 r的大小一般应与零件上的要求一致。但粗加工铣刀因尚 未切削到工件的最终轮廓尺寸,故可适当选得小些,有 时甚至可选为“清角” (即r=0~0.5mm),但不要造 成根部“过切”的现象。
(4) 立铣刀几何角度的选择。对于立铣刀,主要
第3章 数控铣削加工工艺 2. 夹具的选择 (1) 为了保持零件安装位置与机床坐标系及编程坐标系方 向的一致性,夹具应能保证在机床上实现定向安装,同时还要
求能协调零件定位面与机床之间保持一定的坐标尺寸关系。
(2) 在加工过程中,为了保证夹具与铣床主轴套筒或刀套、
刀具不发生干涉,夹具在设计和制造时应尽可能开敞, 使待加 工面充分暴露在外,同时夹紧机构元件与加工面之间应保持一
5) 鼓形铣刀
如图3-20所示的鼓形铣刀,它的切削刃分布在半径 为R的圆弧面上,端面无切削刃。加工时控制刀具上下位 置,相应改变刀刃的切削部位,可以在工件上切出从负 到正的不同斜角。R越小,鼓形铣刀所能加工的斜角范围 越广,但所获得的表面质量也越差。这种刀具的缺点是
刃磨困难,切削条件差, 而且不适于加工有底的轮廓表
还可用负前角。前角的数值主要根据工件材料和刀具材料来选择,
5°。主偏角κr 在45°~90°范围内选取,铣削铸铁时取κr=45°,
第3章 数控铣削加工工艺
· 立铣刀主要参数的选择
(1) 铣刀直径D的选择。一般情况下,为减少走刀次数, 提高铣削速度和铣削量,保证铣刀有足够的刚性以及良好的散热 条件,应尽量选择直径较大的铣刀。但选择铣刀直径往往受到零 件材料,刚性,加工部位的几何形状、尺寸及工艺要求等因素的 限制。图3-22所示零件的内轮廓转接凹圆弧半径R较小时, 铣刀 直径D也随之较小,一般选择D=2R。 若槽深或壁板高度H较大, 则应采用细长刀具,从而使刀具的刚性变差。 铣刀的刚性以铣刀 直径D与刃长l的比值来表示,一般取D/l>0.4~0.5。 当铣刀的 刚性不能满足D/l>0.4~0.5的条件(即刚性较差)时,可采用直 径大小不同的两把铣刀进行粗、精加工。先选用直径较大的铣刀 进行粗加工,然后再选用D、l均符合图样要求的铣刀进行精加工。
数控铣削零件加工工艺设计及自动编程

数控铣削零件加工工艺设计及自动编程数控铣削是一种利用数控设备进行精密加工的方法。
它可以将图纸上的零件准确地加工成为实物。
在进行数控铣削加工时,需要对工艺进行设计并进行自动编程,以保证加工精度和效率。
一、工艺设计1. 零件分析在进行工艺设计之前,需要先对零件进行分析。
分析的主要目的是确定零件的加工形式以及加工顺序。
根据零件的材质、形状、尺寸和表面粗糙度等参数,确定最佳的加工策略。
2. 加工顺序在确定加工策略之后,需要根据操作工艺的要求以及零件的结构特点,确定加工的顺序。
常用的加工顺序包括:粗加工、半精加工、精加工、面加工等。
3. 工艺参数在加工零件时,需要设置一些工艺参数。
这些参数包括:切削速度、进给速度、切削深度等。
在进行数控铣削加工前,需要根据零件的具体要求进行设置,以确保加工精度和效率。
二、自动编程进行数控铣削加工时,需要通过自动编程的方法将加工路径和参数输入数控设备中。
具体步骤如下:1. 绘制零件的加工图在进行自动编程前,需要先绘制零件的加工图。
绘制时需要注意各部位的尺寸和位置关系。
2. 数控程序生成在绘制完成后,需要根据加工顺序以及加工路径进行数控程序的生成。
数控程序的生成一般分为两种方式:手动编程和自动编程。
手动编程需要对数控编程语言有一定的掌握,而自动编程则是利用专业的自动编程软件来生成数控程序。
3. 程序输入数控设备中程序生成后,需要将程序通过数据传输线缆或U盘等存储设备输入数控设备中。
在输入程序时,需要检查程序的正确性以及设备的状态,以确保加工过程的顺利进行。
总结:数控铣削是一种高精度的加工方法,其加工精度和效率受到工艺设计和自动编程的影响。
在进行数控铣削加工时,需要进行工艺设计并进行自动编程,以确保加工质量和工作效率。
数控铣削加工工艺分析
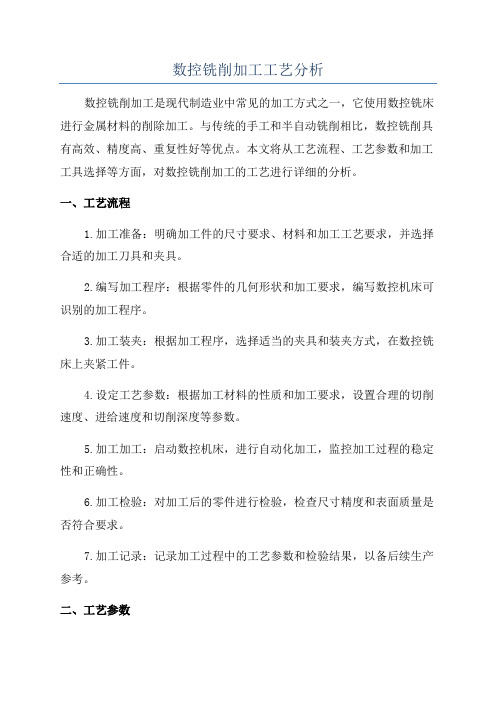
数控铣削加工工艺分析数控铣削加工是现代制造业中常见的加工方式之一,它使用数控铣床进行金属材料的削除加工。
与传统的手工和半自动铣削相比,数控铣削具有高效、精度高、重复性好等优点。
本文将从工艺流程、工艺参数和加工工具选择等方面,对数控铣削加工的工艺进行详细的分析。
一、工艺流程1.加工准备:明确加工件的尺寸要求、材料和加工工艺要求,并选择合适的加工刀具和夹具。
2.编写加工程序:根据零件的几何形状和加工要求,编写数控机床可识别的加工程序。
3.加工装夹:根据加工程序,选择适当的夹具和装夹方式,在数控铣床上夹紧工件。
4.设定工艺参数:根据加工材料的性质和加工要求,设置合理的切削速度、进给速度和切削深度等参数。
5.加工加工:启动数控机床,进行自动化加工,监控加工过程的稳定性和正确性。
6.加工检验:对加工后的零件进行检验,检查尺寸精度和表面质量是否符合要求。
7.加工记录:记录加工过程中的工艺参数和检验结果,以备后续生产参考。
二、工艺参数1.切削速度:是指刀具在单位时间内切削的长度。
根据加工材料的硬度和切削性能,合理选择切削速度,既能保证加工效率,又能保证刀具寿命。
2.进给速度:是指刀具在单位时间内在加工方向上移动的距离。
进给速度的选择应考虑切削力和切削表面的要求。
3.切削深度:是指刀具在一次进给过程中所削除的材料层厚度。
切削深度的选择应使得切削力合理,既能保证加工效率,又能避免切削表面的质量。
4.刀具半径补偿:数控铣床会自动根据刀具半径补偿值进行补偿,使得加工轮廓与设计轮廓一致。
5.加工顺序:根据零件的几何形状和切削力的分布情况,合理选择加工顺序,避免零件变形和加工过程中的切削力过大。
三、加工工具选择1.刀具材料:刀具材料应具有一定的硬度、耐磨性和耐冲击性,常用的刀具材料有硬质合金、高速钢和陶瓷等。
2.刀具形状:根据零件的几何形状和加工要求,选择合适的刀具形状,如平面铣刀、立铣刀、球头铣刀等。
3.切削刃数:根据加工材料的硬度和切削性能,选择合适的刀具刃数,既能保证加工效率,又能保证刀具寿命。
数控铣削加工工艺与编程
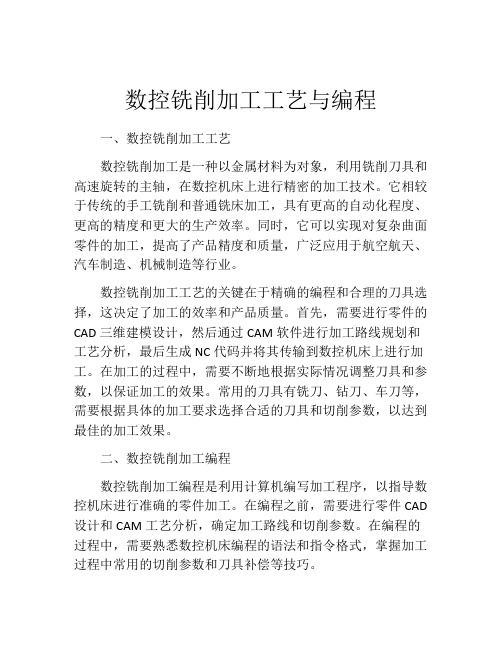
数控铣削加工工艺与编程一、数控铣削加工工艺数控铣削加工是一种以金属材料为对象,利用铣削刀具和高速旋转的主轴,在数控机床上进行精密的加工技术。
它相较于传统的手工铣削和普通铣床加工,具有更高的自动化程度、更高的精度和更大的生产效率。
同时,它可以实现对复杂曲面零件的加工,提高了产品精度和质量,广泛应用于航空航天、汽车制造、机械制造等行业。
数控铣削加工工艺的关键在于精确的编程和合理的刀具选择,这决定了加工的效率和产品质量。
首先,需要进行零件的CAD三维建模设计,然后通过CAM软件进行加工路线规划和工艺分析,最后生成NC代码并将其传输到数控机床上进行加工。
在加工的过程中,需要不断地根据实际情况调整刀具和参数,以保证加工的效果。
常用的刀具有铣刀、钻刀、车刀等,需要根据具体的加工要求选择合适的刀具和切削参数,以达到最佳的加工效果。
二、数控铣削加工编程数控铣削加工编程是利用计算机编写加工程序,以指导数控机床进行准确的零件加工。
在编程之前,需要进行零件CAD 设计和CAM工艺分析,确定加工路线和切削参数。
在编程的过程中,需要熟悉数控机床编程的语法和指令格式,掌握加工过程中常用的切削参数和刀具补偿等技巧。
编程的第一步是确定加工坐标系和切削速度。
加工坐标系是数控机床的工作坐标系,其坐标轴的方向和位置需要与零件CAD设计的坐标系一致,才能使零件加工的精度和效率最佳。
切削速度是在加工过程中刀具和工件的相对速度,需要根据刀具的刃口材料、硬度和工件材料进行调整,以达到最佳的加工效果。
其次,需要编写切削路径和刀具指令。
切削路径是指刀具在工件表面上的运动轨迹,要尽可能地减少切削时间和切削力,以保证零件表面的精度和质量。
刀具指令是指对刀具运动的详细描述,包括切削深度、切削速度、切削方向、回刀位置等。
最后,需要进行NC程序的调试和参数优化。
调试是指通过模拟运行和实物测试等手段,不断检查和调整程序的正确性和合理性,确保加工过程的稳定性和精度。
数控铣削加工工艺
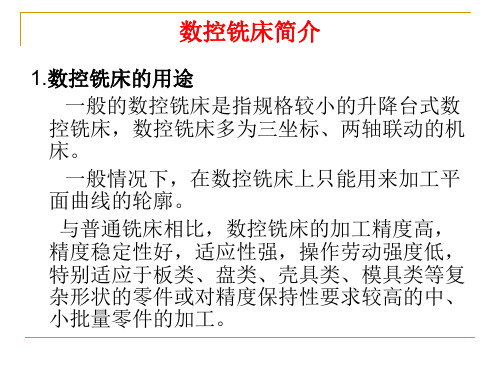
立式数控 铣床
卧式数控 铣床
多坐标联 动的卧式 加工中心
适于加工箱体、箱盖、平面凸轮、样板、形状复杂 的平面或立体零件,以及模具的内、外型腔等。 适于加工复杂的箱体类零件、泵体、阀体、壳体等。
用于加工各种复杂的曲线、曲面、叶轮、模具等。
6.2.2 数控铣削加工零件的工艺性分析
零件的工艺性分析是制定数控铣削加工工艺 的前提,主要内容包括: (1)零件图及其结构工艺性分析 ① 分析零件的形状、结构及尺寸特点 零件上是否有妨碍刀具运动的部位 是否有会产生加工干涉或加工不到的区域 零件外形尺寸是否超过机床行程范围 零件刚性在加工过程中是否太有大的变化
数控铣床简介
1.数控铣床的用途 一般的数控铣床是指规格较小的升降台式数
控铣床,数控铣床多为三坐标、两轴联动的机 床。
一般情况下,在数控铣床上只能用来加工平 面曲线的轮廓。
与普通铣床相比,数控铣床的加工精度高, 精度稳定性好,适应性强,操作劳动强度低, 特别适应于板类、盘类、壳具类、模具类等复 杂形状的零件或对精度保持性要求较高的中、 小批量零件的加工。
6.1 数控铣削加工的主要对象
1.平面类零件 加工面平行或垂直于水平面,或加工面与水平面的夹角为定角的零件
为平面类零件。其特点是各个加工面是平面,或可以展开成平面。一般只 需用三坐标数控铣床的两坐标联动(即两轴半坐标联动)就可以把它们加工 出来。
a)带平面轮廓的平面零件 b)带斜平面的平面零件 c)带正圆台和斜筋的平面零件
件的加工面不能展开为平面,加工时,加工面与铣刀始终 为点接触。常用两轴半联动数控铣床来加工精度要求不高 的曲面;精度要求高的曲面类零件一般采用三轴联动数控 铣床加工;当曲面较复杂、通道较狭窄、会伤及毗邻表面 及需刀具摆动时,要采用四轴甚至五轴联动数控铣床加工。
数控铣削加工工艺的主要内容

数控铣削加工工艺
数控铣削加工工艺的实质,就是在分析零件精度和表面 粗糙度的基础上,对数控铣削的加工方法、装夹方式、切削 加工进给路线、刀具选择和切削用量等工艺内容进行正确而 合理的选择。
下列加工内容比较适宜采用数控铣削加工: ① 零件上的平面曲线轮廓表面(如图所示)特别是由数学表达
① 需要进行长时间占机人工进行调整的加工和粗加工。
② 零件毛坯上的加工余量不大或者不太稳定的加工部位。
③ 必须使用细长铣刀加工的部位,一般指狭长深槽和加工精 度要求不高的筋板处连接曲线。
数控机床编程与操作
式给出的非圆曲线和列表曲线建立的空间曲线。 ② 由给出数学模型的空间曲面或通过测量数据建立起来的空间
曲面。 ③形状复杂、尺寸繁多、零件画线和检测都比较困难的零件加
工部位。
数控铣削加工工艺
④ 能够在一次装夹中铣削加工出多部位的零件表面或零件 形状。
⑤ 用普通的铣床进行加工的观察、检测困难的零件加工, 以及各种内、外凹凸槽形状的零件的加工。 ★下列内容不适宜采用数控铣削加工:
- 1、下载文档前请自行甄别文档内容的完整性,平台不提供额外的编辑、内容补充、找答案等附加服务。
- 2、"仅部分预览"的文档,不可在线预览部分如存在完整性等问题,可反馈申请退款(可完整预览的文档不适用该条件!)。
- 3、如文档侵犯您的权益,请联系客服反馈,我们会尽快为您处理(人工客服工作时间:9:00-18:30)。
第1章 数控加工编程基础
2.周铣与端铣
铣刀对平面的加工,存在周铣与端铣两种方式,如图3-23 所示。周铣平面时,平面度的好坏主要取决于铣刀的圆柱素线 的直线度。因此,在精铣平面时,铣刀的圆柱度一定要好。用 端铣的方法铣出的平面,其平面度的好坏主要取决于铣床主轴 轴线与进给方向的垂直度。同样是平面加工,其方法不同对质 量影响的因素也不同。
第1章 数控加工编程基础
2)逆铣
切削处刀具的旋向与工件的送进方向相反。通俗地说,是刀 齿迎着材料“咬”,刀齿刚切入材料时切得薄,而脱离工件时 则切得厚。这种方式机床受冲击较大,加工后的表面不如顺铣 光洁,消耗在工件进给运动上的动力较大。由于铣刀刀刃在加 工表面上要滑动一小段距离,刀刃容易磨损。但对于表面有硬 皮的毛坯工件,顺铣时铣刀刀齿一开始就切削到硬皮,切削刃 容易损坏,而逆铣时则无此问题。
第1章 数控加工编程基础
第1章 数控加工编程基础
铣削外轮廓的进Biblioteka 路线为避免因切削力变化在加工表面产生刻痕,当用立铣刀铣削 外轮廓平面时,应避免刀具沿零件外轮廓的法向切入、切出, 而应沿切削起始点延伸线或切线方向逐渐切入、切离工件,图 3-25所示。
铣削内轮廓的进给路线
铣削封闭的内轮廓表面时,为避免沿轮廓曲线的法向切入、 切出,刀具可以沿一过渡圆弧切入和切出工件轮廓。图3-26所 示为铣削内轮廓的进给路线。
第1章 数控加工编程基础
3.选择进给速度
进给速度分快进(空行程进给速度)、工进(包括切入、切出 和切削时的工作进给速度)的进给速度。为提高工效,减少空 行程时间,快进的进给速度尽可能高一些,一般为机床允许的 最大进给速度。工进的进给速度V与铣刀转速n、铣刀齿数z及 每齿进给量f (单位为mm/齿)的关系为V=fzn
(3)当工件表面粗糙度值要求为Ra0.8~3.2µm时,铣削可分 粗铣、半精铣、精铣三个阶段进行。半精铣时背吃刀量或侧吃 刀量取1.5~2.0 mm;精铣时圆周铣的侧吃刀量取0.3~0.5 mm, 面铣刀的背吃刀量取0.5~1.0 mm。
第1章 数控加工编程基础
2.选择切削速度
单从理论上讲,确定背吃刀量、进给量后,为提高生产率, 切削速度应该是越大越好因为这样可以避开积屑瘤生成的速度, 获得较低的表面粗糙度。但实际上,由于机床、刀具等的限制, 切削速度一般只能控制在100~200m/min的范围内。在铣削加 工时,切削线速度Vc也称为单齿切削量。提高Vc值也是提高生 产率的一个有效措施,但Vc与刀具耐用度的关系比较密切。随 着Vc的增大,刀具耐用度急剧下降,故Vc的选择主要取决于刀 具耐用度。另外,切削速度Vc值还要根据工件的材料硬度来做 适当的调整。。
第1章 数控加工编程基础
数控铣削加工工艺
一、铣削加工的特点和方式 1. 铣削特点
铣削是铣刀旋转作主运动,工件或铣刀作进给运动的切削加 工方法。数控铣削是一种应用非常广泛的数控切削加工方法,能 完成数控铣削加工的设备主要是数控铣床和加工中心。
数控铣削与数控车削比较有如下特点: (1)多刃切削。铣刀同时有多个刀齿参加切削,生产率高。 (2)断续切削。铣削时,刀齿依次切入和切出工件,易引起周 期性的冲击振动。 (3)半封闭切削。铣削的刀齿多,使每个刀齿的容屑空间小, 呈半封闭状态,容屑和排屑条件差。
第1章 数控加工编程基础 图3-25 铣削外轮廓的进给路线 图3-26 铣削内轮廓的进给路线
第1章 数控加工编程基础
三、铣削用量的选择
1.吃刀量的选择
背吃刀量的选取主要由工件的加工余量、精度要求及工艺 系统的刚度决定。若工件的精度要求不高,工艺系统的刚度又 足够,则最好一次切净加工余量,若工件的精度和表面粗糙度 要求较高,或工艺系统的刚度较差,则只能按先多后少的原则, 采用多次走刀加工。
第1章 数控加工编程基础
图3-23 铣刀平面加工的周铣与端铣 (a)圆柱形铣刀的周铣;(b)端铣刀的端铣; (c)立铣刀同时周、端铣;(d)键槽铣刀的周、端铣
第1章 数控加工编程基础 3.顺铣与逆铣 在周铣时,因为工件与铣刀的相对运动不同,就会有顺铣 和逆铣。周铣时的顺铣与逆铣如图3-24所示,二者之间有所差 异。顺铣与逆铣的比较如下。
(1)当工件表面粗糙度要求为Ra12.5~25µm时,如果圆周铣 削的加工余量小于5mm,端铣的加工余量小于6mm,则粗铣 一次进给就可以达到要求。但在余量较大、工艺系统刚性较差 或机床动力不足时,可分两次走刀完成。
第1章 数控加工编程基础
(2)当工件表面粗糙度要求为Ra3.2~12.5µm时,铣削可分粗 铣和半精铣两个阶段进行。粗铣时背吃刀量或侧吃刀量选取同 前。粗铣时留0.5~1.0mm余量,在半精铣时切除。
第1章 数控加工编程基础
二、进给路线的确定
确定进给路线时,要在保证被加工零件获得良好的加工精 度和表面质量的前提下,力求计算容易,走刀路线短,空刀时 间少。进给路线的确定与工件表面状况、零件表面质量、机床 进给机构的间隙、刀具耐用度以及零件轮廓形状等有关。
确定铣削进给路线应考虑的主要问题 1.铣削零件表面时,要正确选用铣削方式。 2.进给路线尽量短,以减少加工时间,提高效率。 3.进刀、退刀位置应选在零件不太重要的部位,并且使刀具 沿零件的切线方向进刀、退刀,以避免产生刀痕。当铣削内表 面轮廓时,切入、切出无法外延,铣刀只能沿法线方向切入和 切出,此时,切入点、切出点应选在零件轮廓合适的位置(一 般用圆弧过度)。
图3-24 周铣时的顺铣和逆铣 (a)顺铣;(b)逆铣
第1章 数控加工编程基础
1)顺铣
切削处刀具的旋向与工件的送进方向一致。通俗地说,是 刀齿追着材料“咬”,刀齿刚切入材料时切得深,而脱离工件 时则切得少。顺铣时,作用在工件上的垂直铣削力始终是向下 的,能起到压住工件的作用,对铣削加工有利,而且垂直铣削 力的变化较小,故产生的振动也小,机床受冲击小,有利于减 小工件加工表面的粗糙度值,从而得到较好的表面质量,同时 顺铣也有利于排屑,数控铣削加工一般尽量用顺铣法加工。