常规金相试样的切取
金相制样 标准

金相制样标准
金相制样标准主要包括以下步骤:
1. 试样选取:根据实验需求,选取具有代表性的试样。
2. 镶嵌:为了便于机械磨抛,将金相试样镶嵌成标准尺寸大小。
3. 切割:使用砂轮切割机或电火花切割机进行切割,同时应采取冷却措施,以减少由于受热而引起的试样组织变化。
4. 磨抛:通过逐道次机械研磨和抛光,获得平整且呈镜面的试样表面。
磨抛包括粗磨和细磨两步,粗磨消除毛边和磨痕,细磨为抛光做好准备。
5. 抛光:使用抛光织物和抛光液进行抛光,使试样表面更加平整光滑。
6. 蚀刻:使用蚀刻剂对试样表面进行蚀刻,使组织结构更加清晰。
7. 观察:使用显微镜对蚀刻后的试样进行观察和分析。
在整个过程中,需要保证试样的表面无划痕、无变形、无外来物质,并保持平整。
同时,试样的尺寸和形状应便于握持和磨制,通常采用直径15~20mm、高15~20mm的圆柱体或边长15~20mm的立方体。
以上是金相制样的基本步骤和要求,实际操作中可能还需要根据具体情况进行调整和优化。
常见金相样品切割方式简单介绍
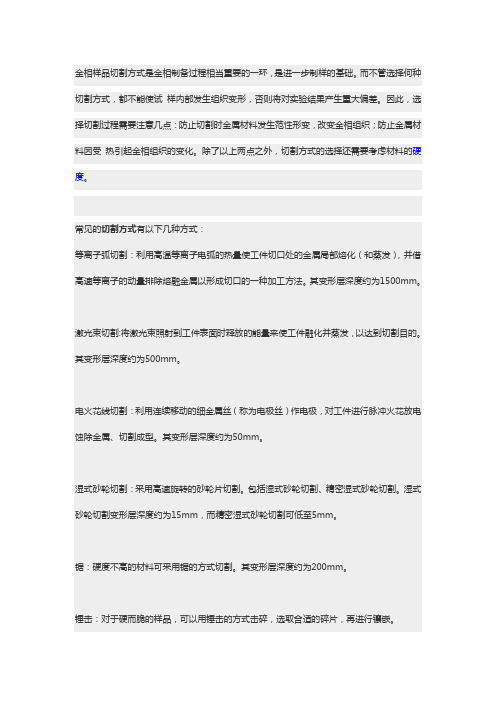
金相样品切割方式是金相制备过程相当重要的一环,是进一步制样的基础。
而不管选择何种切割方式,都不能使试样内部发生组织变形,否则将对实验结果产生重大偏差。
因此,选择切割过程需要注意几点:防止切割时金属材料发生范性形变,改变金相组织;防止金属材料因受热引起金相组织的变化。
除了以上两点之外,切割方式的选择还需要考虑材料的硬度。
常见的切割方式有以下几种方式:
等离子弧切割:利用高温等离子电弧的热量使工件切口处的金属局部熔化(和蒸发),并借高速等离子的动量排除熔融金属以形成切口的一种加工方法。
其变形层深度约为1500mm。
激光束切割:将激光束照射到工件表面时释放的能量来使工件融化并蒸发,以达到切割目的。
其变形层深度约为500mm。
电火花线切割:利用连续移动的细金属丝(称为电极丝)作电极,对工件进行脉冲火花放电蚀除金属、切割成型。
其变形层深度约为50mm。
湿式砂轮切割:采用高速旋转的砂轮片切割。
包括湿式砂轮切割、精密湿式砂轮切割。
湿式砂轮切割变形层深度约为15mm,而精密湿式砂轮切割可低至5mm。
锯:硬度不高的材料可采用锯的方式切割。
其变形层深度约为200mm。
锤击:对于硬而脆的样品,可以用锤击的方式击碎,选取合适的碎片,再进行镶嵌。
一般来说,对于硬度较低的材料,可以用锯、车、刨等加工方法;对于硬度较高的材料,可以用砂轮切片机切割或电火花切割等方法。
其中湿式砂轮切割是金相试样的最佳切割方式。
因为其切割过程中加入了高压冷却水,可防止由于表面过热而造成损伤。
而电火花线切割,锯或者激光切割等方式都会导致材料切割质量的低劣。
金相检验操作规程

金相检验操作规程1.试样金相试样面积小于400mm2,厚(高)度15-20mm为宜。
若试样面积过小,应经镶嵌后再进行磨制。
低倍组织酸侵试样厚度(高)度为20mm左右,酸侵低倍试样检测面应经过车加工或磨加工,表面粗糙度应不大于1.6μm。
试样检测面不得由油污及加工伤痕,必要时应预先清除。
试样的标识应清晰。
2.高倍检验操作规程2.1金相试样制备操作规程2.1.1金相试样的切取试样切取的方向、部位和数量,应根据有关技术条件的规定。
试样可用手锯、锯床或切割机等切取,必要时也可用气割法切取,但烧割边缘必须与正式试样保持相当距离,以去除热影响区。
取好的试样先在平面磨床或砂轮机上把检测面磨平,磨面上的磨痕应均匀一致。
磨样时应对试样进行冷却,以免金属组织受热发生变化。
2.1.2金相试样的磨制试样需经粗磨和细磨,粗磨用水磨砂纸,细磨用金相砂纸,应根据需要选择合适的砂纸及磨制道次。
磨样时须把前一道的磨痕磨去,方向与前一道的工序相垂直。
磨样时要防止试样磨面温度过高而使组织发生变化。
2.1.3金相试样的抛光常用的时机械抛光的方法,即把经过细磨的试样在抛光机上进行抛光。
抛光织物采取丝绒或绸布,抛光粉采用金刚砂。
抛光面光洁度要达到镜面,不允许有夹杂物拖尾、麻点、过热等现象,抛光后将试样清洗干净。
2.1.4金相试样化学侵蚀操作规程试样侵蚀前抛光面应保持干净,不得有油污或指痕,以免影响所显示组织的清晰度。
试样在盛有侵蚀剂的器皿中侵蚀,侵蚀时试样应轻微摆动,但不可擦伤抛光面。
应根据不同的需要选择侵蚀剂,并注意侵蚀适度。
侵蚀后试样应保持干燥(在酒精中浸泡、用电吹风吹干),以待观察。
配置侵蚀剂时遵照先加酒精或水、后加酸液的顺序。
侵蚀操作时要注意安全,防止酸液或酸雾对人体造成伤害。
2.2金相显微镜操作规程操作者在使用显微镜前,应仔细阅读显微镜的使用说明书,了解显微镜的功能及使用方法。
初学者操作显微镜应在专人指导下进行。
测试前应保持操作者的手及试样清洁干燥。
简述金相试样制备的基本过程
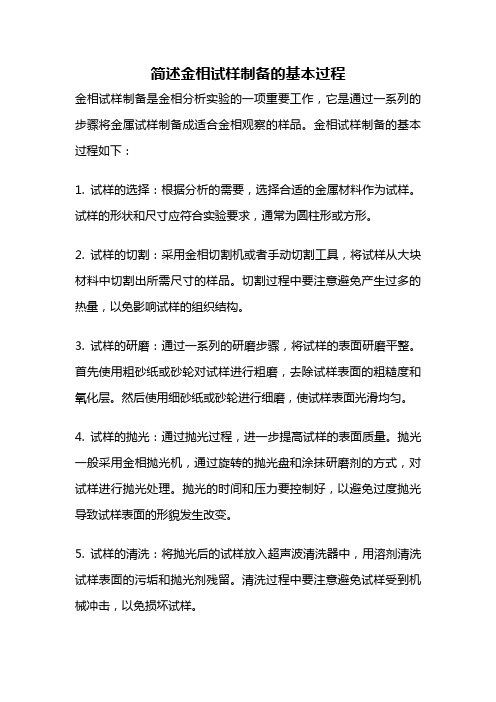
简述金相试样制备的基本过程金相试样制备是金相分析实验的一项重要工作,它是通过一系列的步骤将金属试样制备成适合金相观察的样品。
金相试样制备的基本过程如下:1. 试样的选择:根据分析的需要,选择合适的金属材料作为试样。
试样的形状和尺寸应符合实验要求,通常为圆柱形或方形。
2. 试样的切割:采用金相切割机或者手动切割工具,将试样从大块材料中切割出所需尺寸的样品。
切割过程中要注意避免产生过多的热量,以免影响试样的组织结构。
3. 试样的研磨:通过一系列的研磨步骤,将试样的表面研磨平整。
首先使用粗砂纸或砂轮对试样进行粗磨,去除试样表面的粗糙度和氧化层。
然后使用细砂纸或砂轮进行细磨,使试样表面光滑均匀。
4. 试样的抛光:通过抛光过程,进一步提高试样的表面质量。
抛光一般采用金相抛光机,通过旋转的抛光盘和涂抹研磨剂的方式,对试样进行抛光处理。
抛光的时间和压力要控制好,以避免过度抛光导致试样表面的形貌发生改变。
5. 试样的清洗:将抛光后的试样放入超声波清洗器中,用溶剂清洗试样表面的污垢和抛光剂残留。
清洗过程中要注意避免试样受到机械冲击,以免损坏试样。
6. 试样的腐蚀:某些金属材料需要进行腐蚀处理,以去除试样表面的氧化层和其他不良组织。
腐蚀一般采用酸性溶液,如酸性硝酸或酸性硫酸溶液。
腐蚀时间要根据试样的材料和要求进行控制,过长的腐蚀时间可能会导致试样的形貌和组织结构发生变化。
7. 试样的洗净:将腐蚀后的试样放入清水中进行反复洗净,以去除腐蚀液的残留物。
洗净过程中要避免试样受到机械冲击,以免试样变形或损坏。
8. 试样的干燥:将洗净后的试样放入烘箱或用吹风机进行干燥,以去除试样表面的水分。
干燥过程中要控制好温度和时间,以避免试样的热膨胀和变形。
9. 试样的打磨:对于需要进行金相观察的试样,还需要进行一定程度的打磨处理,以获得更好的观察效果。
打磨一般采用细砂纸和研磨液,通过手工或机械的方式对试样进行打磨,使试样表面更加光滑。
宏观金相检测标准
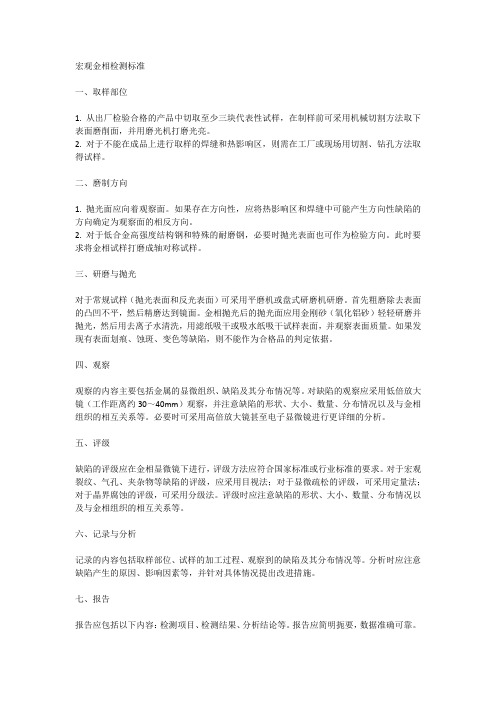
宏观金相检测标准一、取样部位1. 从出厂检验合格的产品中切取至少三块代表性试样,在制样前可采用机械切割方法取下表面磨削面,并用磨光机打磨光亮。
2. 对于不能在成品上进行取样的焊缝和热影响区,则需在工厂或现场用切割、钻孔方法取得试样。
二、磨制方向1. 抛光面应向着观察面。
如果存在方向性,应将热影响区和焊缝中可能产生方向性缺陷的方向确定为观察面的相反方向。
2. 对于低合金高强度结构钢和特殊的耐磨钢,必要时抛光表面也可作为检验方向。
此时要求将金相试样打磨成轴对称试样。
三、研磨与抛光对于常规试样(抛光表面和反光表面)可采用平磨机或盘式研磨机研磨。
首先粗磨除去表面的凸凹不平,然后精磨达到镜面。
金相抛光后的抛光面应用金刚砂(氧化铝砂)轻轻研磨并抛光,然后用去离子水清洗,用滤纸吸干或吸水纸吸干试样表面,并观察表面质量。
如果发现有表面划痕、蚀斑、变色等缺陷,则不能作为合格品的判定依据。
四、观察观察的内容主要包括金属的显微组织、缺陷及其分布情况等。
对缺陷的观察应采用低倍放大镜(工作距离约30~40mm)观察,并注意缺陷的形状、大小、数量、分布情况以及与金相组织的相互关系等。
必要时可采用高倍放大镜甚至电子显微镜进行更详细的分析。
五、评级缺陷的评级应在金相显微镜下进行,评级方法应符合国家标准或行业标准的要求。
对于宏观裂纹、气孔、夹杂物等缺陷的评级,应采用目视法;对于显微疏松的评级,可采用定量法;对于晶界腐蚀的评级,可采用分级法。
评级时应注意缺陷的形状、大小、数量、分布情况以及与金相组织的相互关系等。
六、记录与分析记录的内容包括取样部位、试样的加工过程、观察到的缺陷及其分布情况等。
分析时应注意缺陷产生的原因、影响因素等,并针对具体情况提出改进措施。
七、报告报告应包括以下内容:检测项目、检测结果、分析结论等。
报告应简明扼要,数据准确可靠。
以上是宏观金相检测的基本标准,实际操作中还需要根据具体的材料、产品和使用环境等因素进行调整和优化。
金相检验培训

金相检验培训培训内容:一、金相试样切取方法:1、铸件取样时不能直接从浇口或冒口上切取金相试样。
2、切取和制备金相时应注意保证不破坏铸铁的基体组织结构,如不能直接用无冷却液砂轮机上切割试样。
3、将切好金相样块锐边倒角,以免损伤手和抛光布。
二、研磨方法:1、在砂纸上沿垂直原划痕的方向打磨试验面,不要来回磨,要沿一个方向,用力要适度,直到除去原有划痕。
2、使用砂纸的顺序为:0#~W40#→W14#→W7#,磨完W7#的砂纸后可转入抛光。
3、铸铁抛光要防止石墨脱落,为此要慢速抛光,用力适度,抛光时的磨削方向必须垂直于抛光面上划痕的方向,抛光过程中要注意不断加水,不能有油污混入抛光布或水中,以免影响质量。
抛光表面光亮如镜,看不到有明显划痕时,即可用无水酒精将试样表面清洗干净,用电吹风将试样表面吹干。
三、浸蚀1、试样一般采用2%~5%硝酸酒精溶液浸蚀。
2、检查曲轴、法兰、气缸试样基体浸蚀时间为3~5秒,均匀涂搽,检验滚子试样基体浸蚀时间为10~15秒,均匀涂搽。
四、石墨分布形状:1、石墨分布形状分为六种:A型(片状)、B型(菊花状)、C型(块片状)、D型(枝晶点状)、E型(枝晶片状)、F型(星状)。
2、对石墨分布显微观察应在末浸蚀的试样上进行,放大倍数为100倍。
五、石墨长度:1、石墨长度分为八级:1级(﹥100mm)、2级(﹥20~100mm)、3级(﹥25~50mm)、4级(﹥12~25mm)、5级(﹥6~12mm)、6级(﹥3~6mm)、7级(﹥1.5~3mm)、8级(≤1.5mm)。
目镜上有刻度尺寸可测量。
在末浸蚀的试样上,放大倍数为100倍。
选择有代表性视场,按其中最长三条以上石墨的平均值评定。
被量的视场不少于三个。
2、石墨长度的评级对于铸件具有重要的实际意义。
因为石墨在铸件中相当于裂纹缺陷,裂纹越长破断应力就越小,说明铸件的性能越差,抗拉性能随石墨长度的增加而降低。
六、基体组织特征基体组织特征按其铸态或经热处理后状态列入七种:铁素体、片状珠光、粒状珠光体、屈氏体、粒状贝氏体、针状贝氏体、马氏体。
金相试样步骤

金相试样步骤金相试样是对材料进行显微组织的观察和分析的一种实验方法。
它是金属材料科学研究的重要手段之一、通过金相试样可以观察材料内部的组织结构、晶粒结构等性质,从而深入了解其物理、化学、机械等性质。
以下是金相试样的步骤:1.取样:要制备金相试样,首先要从待研究的金属材料中取出一定数量的样品。
取样时应注意不要对材料造成太大的损伤,以免影响材料的组织结构。
2.打磨:取出的样品需要经过粗磨和细磨处理。
粗磨的目的是去除表面的氧化物或污垢,细磨则是使样品表面非常光滑,为后续的抛光和腐蚀处理做好准备。
3.抛光:将磨好的样品抛光至光滑无痕迹,一般使用半自动或全自动金相抛光机,选用300到2000号研磨纸,抛光过程需要水冷却,以免样品在高速旋转时发热变形。
4.腐蚀:将抛光好的样品用腐蚀剂进行腐蚀。
腐蚀的目的是去除样品表面氧化层,暴露材料内部的组织。
腐蚀剂的选择根据不同的材料而定,如钢材可以用1% 的Nital溶液,铝材可以用10%的氢氧化钠溶液。
腐蚀时间的确定是根据样品的大小和腐蚀剂的浓度而定的,一般在1到5分钟内完成。
5.清洗:对腐蚀后的样品进行清洗,以将残留的腐蚀剂彻底去除。
样品需要用洗涤液或者酒精进行多次清洗,并用氮气干燥以清洁且无水。
6.显微观察:将清洗好的样品放入金相显微镜中,使用各种镜片进行观察。
金相显微镜包含多个光学部件如长聚焦镜头、短聚焦镜片、目镜和视野卡等,并配有照相机和数码相机等精密配件,以便于对样品的组织结构进行观察和拍摄。
通过以上步骤,我们就可以得到金相试样,观察到材料的微观组织结构。
由于不同的样品需要不同的处理方法,因此真正的制作过程将根据样品类型和实验要求进行调整,以求得最佳的结果。
金相试样步骤范文

金相试样步骤范文金相试样(Metallographic sample)是对材料进行金相组织分析的一种重要方法。
通过金相试样,可以观察材料内部组织的形貌特征,了解材料的组织结构、晶粒大小、相含量以及相分布等信息。
金相试样的制备过程包括试样切割、磨削、粗磨、细磨、腐蚀、清洗和脱脂等步骤。
下面将详细介绍金相试样的制备步骤。
1. 试样切割(Sample cutting):首先,需要根据需要研究的材料样品的尺寸和形状,使用金相切割机或其他适用的设备将样品切割成所需的形状和尺寸。
为了避免造成试样表面变色和损坏,切割过程中需要使用液体冷却剂。
2. 试样粗磨(Rough grinding):将切割好的试样固定在金相磨床上,通过使用带有不同颗粒大小的砂纸或金刚石砂轮对试样进行磨削,以去除试样表面的切割痕迹和粗糙度。
初始磨削过程中,选用较粗的砂纸或金刚石砂轮,然后逐渐过渡到较细的颗粒,直到试样表面平滑均匀。
3. 试样细磨(Fine grinding):经过粗磨后,使用不同颗粒大小的砂纸或金刚石砂轮对试样进行细磨,以进一步提高试样表面的精度和光洁度。
与粗磨相似,细磨也需要逐渐过渡到较细的颗粒,直到试样表面看起来光滑无痕迹。
为了避免产生过多的热量,细磨过程中需要时常冲洗试样以降低表面温度。
4. 试样腐蚀(Etching):为了更好地观察试样内部的组织结构和晶粒大小,需要对试样进行腐蚀处理。
根据不同的材料和所需观察的特定信息,选择适当的腐蚀试剂。
腐蚀试剂可以是酸性的,也可以是碱性的,例如石墨酸、氯铬酸、乙醇、亚铁氯化物等。
腐蚀的时间和温度也需要进行控制,以获得所需的蚀坑尺寸和清晰度。
5. 清洗和脱脂(Cleaning and degreasing):腐蚀后的试样表面会残留有一定的试剂和腐蚀物,为了避免对后续观察造成干扰,需要对试样进行清洗和脱脂处理。
首先,将试样放入洗涤皿中,使用温水和肥皂溶液进行清洗,去除表面的腐蚀试剂和腐蚀物。
金相试样的制备

金相试样的制备样品制备的基本步骤:取样、镶嵌、磨光、抛光四个步骤。
每项操作都必须严格、细心,因为任何阶段上的失误都可能影响以后的步骤;在极端的情况下,不正确的制样可能造成组织的假像,从而得出错误的结论。
样品制备的方式:手工制样、机械制样、自动制样。
一、金相试样的截取选取合适的、具有代表性的试样是金相研究和检验中至关重要的第一步,必须注意取样得部位、数量、尺度、磨面的取向和试样的截取方法。
取样必须恰到好处地给材料提出统计上的可靠描述。
1、取样的原则:取样部位的选取取决于被检验材料或零件的特点、加工工艺过程及热处理过程、使用情况等。
根据检验目的和要求,通常分为两大类:系统取样、指定取样。
⑴系统取样:选取的试样必须能表征被检验材料或零件的特点,即要有代表性。
常规检验所取试样的部位、形状、数量、尺寸等都有明确的规定,详见有关标准:国标(GB)、冶标(YB)、航标(HB)。
例如,标准中规定:棒材、钢锭、钢胚,在材料两端取样;热轧型材则同时取横向、纵向两组试样;航空压气机盘则要从径向、轴向、弦向同时取样。
⑵指定取样:根据所研究的问题,有针对性的取样。
例如:零件失效分析的试样即属此类,必须根据零件使用部位、受力情况、出现裂纹的部位和形状等具体情况,抓住关键部位分别在材料失效部位和完好部位取样,以便对比分析,找出失效的原因。
比如裂纹源区就是重要的取样部位。
磨面取向:根据生产工艺、产品形状、研究目的而定。
形状尺寸:通常是Φ12×12mm的圆柱体或是12×12×12 mm的正方体;实际工作中还要具体问题具体分析。
试样太大、太小都不好;太大,则制备样品时费时费力;太小,则操作不便。
试样边缘无特殊要求时要磨制出倒角。
取样数量:实际生产中,某一材料、某一项目的检验,通常不会是单独的一个样品,一般是3~4个,以求统计上的可靠性。
在研究结果和检验报告上所列举的金相照片,必须注明截取部位和检验面的方向,甚至画图说明。
金相试样切割截取位置的简述

金相试样切割截取位置的简述金相检验中,样品的截取非常重要,如果金相检验被用来做评价指标,所取试样对于所研究的材料应具有代表性。
金相检验的意图或目的通常决定了取样的位置。
按研究目的不同,金相检验可划分为三种:一、普通研究或常规制样试样应从可揭示被研究材料最大差异的部位选取。
例如,铸件宜从中预期会发生最大和最小偏析的位置选取试样。
在检验板带或钢丝时,试样宜取自每卷的尾部。
二、失效分析取样位置应尽可能靠近断口或失效源。
金相检验前应完成断口形貌的研究,或者至少应留有断口的记录。
在多数情况下,应在完好的区域取样来进行结构和性能的对比。
三、研究型研究性质决定了取样的位置,方向等,取样位置往往比常规检验更广泛。
选定进行研究金相的取样位置后,应确定待检验截面的类型。
1、对于铸件,垂直表面的截面可显示铸件由外至内的组织结构变化。
2、经热加工或冷加工的金属,横向和纵向截面都应加以考察。
特殊的检验可能要求金相试样表面与产品的原始表面平行。
3、对于线材和小截面圆钢,选取穿过试样中心的纵截面比横截面更合适。
选择与材料的主轴线相垂直的横截面进行取样分析,常常用于揭示以下信息:1、从中心到表面存在结构上的变化2、非金属夹杂物在截面上散乱分布4、钢铁材料表面的脱碳5、表面缺陷的深度,6、腐蚀的深度,7、保护涂层的厚度,8、保护涂层的结构。
在平行于材料主轴的纵截面取样分析,通常用于揭示以下信息:1、钢中夹杂物含量2、通过晶粒的变形判断塑性变形程度3、有无带状组织4、热处理后的显微组织。
在检验报告结果和显微照片中应指明表面的检验位置。
适当指示表面位置的方法。
金相试样的制备及金相组织观察

金相试样的制备及金相组织观察金相试样是金相学中的重要实验手段,用于观察金属材料的晶体结构、相组成和组织形态等信息。
下面我们将介绍金相试样的制备方法及金相组织观察过程。
一、金相试样的制备方法1.试样的切割:首先需要从金属材料中切割出代表性的试样。
切割试样时应注意保持试样尺寸的标准,确保试样的大小符合实验要求。
2.粗磨:经切割获得的试样通常都有较粗糙的表面。
因此需要进行粗磨,以便进一步处理。
粗磨可以使用粗磨纸或砂轮进行,以去除试样表面粗糙度和切割留下的锋利边缘。
3.嵌埋:经过粗磨后的试样需要进行嵌埋。
嵌埋是将试样固定在一个透明的树脂中,以便进行后续的研磨和观察。
常用的嵌埋材料有环氧树脂和酚醛树脂。
4.精磨:嵌埋好的试样需要进行精磨,使试样表面更加光滑细腻。
精磨可以使用细磨纸或细磨粉进行,常见的精磨粉有二氧化硅粉和氧化铝粉。
5.抛光:精磨后的试样表面通常仍然存在一些微小的研磨痕迹和表面附带物。
为了进一步减小试样表面的痕迹和提高试样表面的光洁度,可以进行抛光。
抛光可以使用砂轮、刚玉研磨粉或抛光膏进行。
6.腐蚀:一些试样需要进行腐蚀处理,以便观察金相组织。
腐蚀可以通过直接浸泡试样在腐蚀剂中,或者使用腐蚀电解槽进行。
7.清洗:试样制备完成后,需用酒精/丙酮和超声清洗剂进行清洗,以彻底清除试样表面的污染物和残留物。
最后使用纯酒精对试样进行干燥。
二、金相组织观察过程1.试样装入金相显微镜:制备好的金相试样需要装入金相显微镜进行观察。
可以将试样固定在显微镜的试样夹上,并通过显微镜的调节装置使试样位于镜头的焦点上。
2.调焦:通过调节显微镜的焦距,使试样清晰可见。
根据试样的形状和纵深,需要调整显微镜的焦距,以确保试样表面和内部的细节都能清晰显示。
3.选择放大倍率:根据所需观察的试样细节,选择合适的放大倍率进行观察。
通常金相显微镜的放大倍率范围从10倍至1000倍不等。
4.观察金相组织:通过显微镜观察试样中的金相组织。
常规金相试样的切取

常规金相试样的切取取样是金相试样制备的第一道工序,若取样不当,则达不到检验目的,因此,所取试样的部位、数量、磨面方向等应严格按照相应的标准规定执行。
(一)取样部位和磨面方向的选择取样部位必须与检验目的和要求相一致,使所切取的试样具有代表性。
必要时应在检验报告单中绘图说明取样部位、数量和磨面方向。
例如,检验裂纹产生的原因时,应在裂纹部位取样,而旦还应在远离裂纹处取样,以资比较,检验铸件时;应在垂直于模壁的横断面上取样,对于大型铸件,还应从表面至中心的横断面上取3~5个试样,磨制横断面,由表面到中心逐个进行观察、比较。
图1-1表示轧制型材金相试样的切取方位,一般纵断面(图1-1中的1、2、4、5)主要用于(1)检验非金属夹杂物的数量、大小和形状;(2)检验晶粒的变形程度,(3)检验钢材的带状组织,以及通过热处理对带状组织的消除程度。
横断面(图1-1中的3)主要用于:(1)·检验从表面到中心的金相组织变化情况,(2)检验表层各种缺陷,如氧化,脱碳,过烧、折叠等,(3)检验表面热处理结果,如表面淬火的淬硬层,化学热处理的渗碳层,氮化层,碳氮共渗层以及表面镀铬,镀铜层等:(4)检验非金属夹杂物在整个断面上的分布,(5)测定晶粒度等。
一般说来,在进行非金属夹杂物评定时,应磨制纵横两个面,在观察铸件组织,表层缺陷以及测定渗层厚度、镀层厚度,晶粒度等均需磨制横断面,在进行破断(失效)综合分析时,往往需要切取几个试样,同时磨制纵横两个面进行观察分析。
(二)取样方法金相试样一般为ф12×12mm或ф18×20mm的圆柱体或12×12×12mm的立方体。
若太小则操作不便,若太大则磨制平面过大,增长磨制时间且不易磨平。
由于被检验材料或零件的形状各异,也有用不规则外形的试样。
非检验表面缺陷、渗层、镀层的试样,应将棱边倒圆,防止在磨制中划破砂纸和抛光织物,避免在抛光时试样飞出造成事故。
金相试样制备方法

金相试样制备方法时间:2010-01-08 22:05:48来源:作者:点击:1次金相检验是研究金属及合金部组织的重要方法之一,为了在金相显微镜下正确有效地观察到部显微组织,就需制备能用于微观检验的样品――金相试样,也可称之为磨片。
金相试样制备的主要程序为:取样—嵌样(对于小样品)—磨光—抛光一浸蚀等。
一、取样原则用金相显微镜对金属的一小部分进行金相研究,其成功与否,可以说首先取决所取试样有无代表性。
在一般情况下,研究金属及合金显微组织的金相试样应从材料或零件在使用中最重要的部位截取;或是偏析、夹杂等缺陷最严重的部位截取。
在分析失效原因时,则应在失效的地方与完整的部位分别截取试样,以探究其失效的原因。
对于生长较长裂纹的部件,则应在裂纹发源处、扩展处、裂纹尾部分别取样,以分析裂纹产生的原因。
研究热处理后的零件时,因组织较均匀,可任选一断面试样。
若研究氧化、脱碳、表面处理(如渗碳)的情况,则应在横断面上观察。
有些零部件的“重要部位”的选择要通过对具体服役条件的分析才能确定。
二、试样截取无论采取何种截取方法截取试样,都必须保证不使试样观察面的金相组织发生变化。
软材料可用锯、车、刨等方法切取;硬材料可用水冷砂轮切片机、电火花切割等方法切取;硬而脆的材料(如白口铸铁),也可用锤击法获取。
对于要测量表面处理层深的试样,要注意切割面与渗层面垂直。
研究轧制材料时,如研究夹杂物的形状、类型、材料的变形程度、晶粒拉长的程度、带状组织等,应在平行于轧制方向上截取纵向试样;如研究材料表层的缺陷、非金属夹杂物的分布,应在垂直轧制方向上截取横向试样。
金相试样较理想的形状是圆柱形和正方柱体。
以具体情况而定。
一般可取高为10~15mm,直径Φ1O~15mm;方形试样边长为10~15mm为宜。
在实际工作中,由于被检材料和零件的品种极多,要在材料和零件上截取理想的形状与尺寸有一定的困难,一般可按实际情况决定。
但是以试样的高度为其直径或边长的一半为宜,形状与大小以便于握在手中磨制为原则。
金相试样的制备内容

P-2型抛光机 主要由电动机1、塑料 盘2、抛光盘3、抛光 织物4、套紧圈5、抛 光罩6、电动机开关盒 7和底座或支架、工作 台面及抛光盘盖等组 成。其转速为1340r/min。
抛光操作过程及其应注意的事项:
a) 添加抛光液状态
b) 初期抛光状态 C)抛光过程中向中心加水
d) 抛光时的试样转动
金相试样的制备内容
2019/11/24
(一)金相试样的制备 制备内容包括:取部位 截取的方法 试样的尺寸
应具有代表性 锯、车、铣、刨等
一般ф15~20×10~20mm
(1)取样的部位——轧后钢材不同部位
(a)轧后钢材不同部位
(b) 热处理后的钢材
钢中非金属夹杂物取样部位示意图 钢棒(左)、钢管(右)脱碳层取样部位示意图
(2)试样截取方法
硬度低于30HRC 可用锯、车、铣、刨等方
法截取
硬度大于30HRC 可用水冷式砂轮切片机、钼丝 切割机等方法截取
2.金相试样的镶嵌
XQ-2型金相试样镶嵌机
金相试样机械镶嵌方法
3. 金相试样的磨制 (1)粗磨——在砂轮机上用砂轮磨制
e) 抛光末期精抛状态
抛光操作过程及其应注意的事项:
甩尾现象
沾污现象
抛光缺陷
抛光后用水清洗
电解抛光设备及其原理:
热风机吹干
5. 金相试样显微组织的显示方法
浸蚀法 化学浸蚀法
擦蚀法
显示方法
物理显示法
擦蚀法 擦蚀法 擦蚀法 擦蚀法
化学浸蚀的原理:是利用试剂对金属试样中各相或组 织的浸蚀速度、着色能力不同,在抛光面上呈现出高 低不平的峰谷及色泽的差异,在可见光的垂直照射下, 对光线的吸收和反射不同,从而显示出各种明暗不同 的组织来。
金相试样如何取样
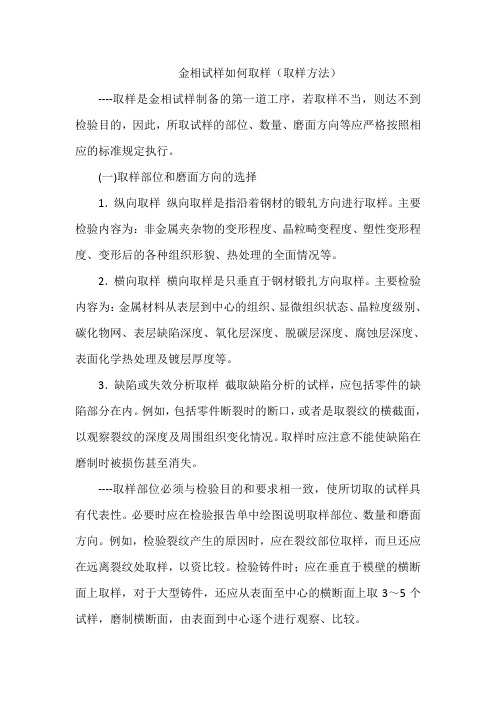
金相试样如何取样(取样方法)----取样是金相试样制备的第一道工序,若取样不当,则达不到检验目的,因此,所取试样的部位、数量、磨面方向等应严格按照相应的标准规定执行。
(一)取样部位和磨面方向的选择1.纵向取样纵向取样是指沿着钢材的锻轧方向进行取样。
主要检验内容为:非金属夹杂物的变形程度、晶粒畸变程度、塑性变形程度、变形后的各种组织形貌、热处理的全面情况等。
2.横向取样横向取样是只垂直于钢材锻扎方向取样。
主要检验内容为:金属材料从表层到中心的组织、显微组织状态、晶粒度级别、碳化物网、表层缺陷深度、氧化层深度、脱碳层深度、腐蚀层深度、表面化学热处理及镀层厚度等。
3.缺陷或失效分析取样截取缺陷分析的试样,应包括零件的缺陷部分在内。
例如,包括零件断裂时的断口,或者是取裂纹的横截面,以观察裂纹的深度及周围组织变化情况。
取样时应注意不能使缺陷在磨制时被损伤甚至消失。
----取样部位必须与检验目的和要求相一致,使所切取的试样具有代表性。
必要时应在检验报告单中绘图说明取样部位、数量和磨面方向。
例如,检验裂纹产生的原因时,应在裂纹部位取样,而旦还应在远离裂纹处取样,以资比较。
检验铸件时;应在垂直于模壁的横断面上取样,对于大型铸件,还应从表面至中心的横断面上取3~5个试样,磨制横断面,由表面到中心逐个进行观察、比较。
图1-1表示轧制型材金相试样的切取方位,一般纵断面(图1-1中的1、2、4、5)主要用于(1)检验非金属夹杂物的数量、大小和形状;(2)检验晶粒的变形程度,(3)检验钢材的带状组织,以及通过热处理对带状组织的消除程度。
横断面(图1-1中的3)主要用于:(1)·检验从表面到中心的金相组织变化情况,(2)检验表层各种缺陷,如氧化,脱碳,过烧、折叠等,(3)检验表面热处理结果,如表面淬火的淬硬层,化学热处理的渗碳层,氮化层,碳氮共渗层以及表面镀铬,镀铜层等:(4)检验非金属夹杂物在整个断面上的分布,(5)测定晶粒度等。
金相分析制样流程
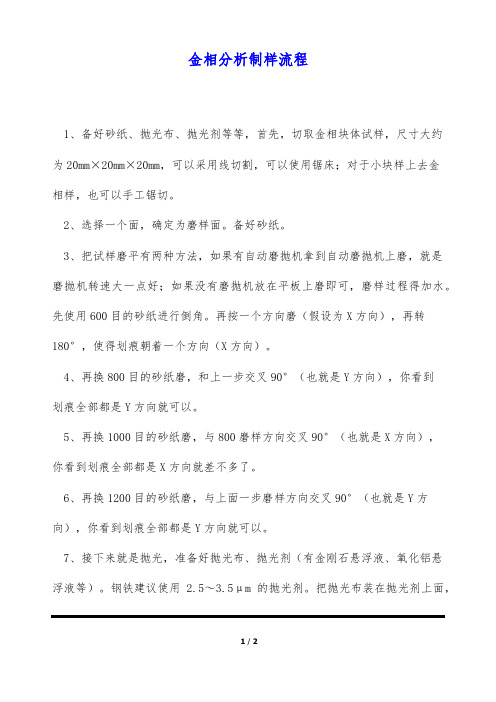
金相分析制样流程
1、备好砂纸、抛光布、抛光剂等等,首先,切取金相块体试样,尺寸大约
为20mm×20mm×20mm,可以采用线切割,可以使用锯床;对于小块样上去金
相样,也可以手工锯切。
2、选择一个面,确定为磨样面。
备好砂纸。
3、把试样磨平有两种方法,如果有自动磨抛机拿到自动磨抛机上磨,就是
磨抛机转速大一点好;如果没有磨抛机放在平板上磨即可,磨样过程得加水。
先使用600目的砂纸进行倒角。
再按一个方向磨(假设为X方向),再转180°,使得划痕朝着一个方向(X方向)。
4、再换800目的砂纸磨,和上一步交叉90°(也就是Y方向),你看到
划痕全部都是Y方向就可以。
5、再换1000目的砂纸磨,与800磨样方向交叉90°(也就是X方向),
你看到划痕全部都是X方向就差不多了。
6、再换1200目的砂纸磨,与上面一步磨样方向交叉90°(也就是Y方向),你看到划痕全部都是Y方向就可以。
7、接下来就是抛光,准备好抛光布、抛光剂(有金刚石悬浮液、氧化铝悬
浮液等)。
钢铁建议使用 2.5~3.5μm的抛光剂。
把抛光布装在抛光剂上面,
把抛光剂摇匀后喷到抛光布上面,然后启动抛光剂。
试样放在上面抛光记得手放着就可,不要乱动。
得加适量水,防止发热!注意划痕方向与旋转方向垂直进行切削。
8、抛光至无划痕就可以了,抛光好后进行水冲洗。
记得吹干,要不然会生锈。
精品资料欢迎下载。
金相试样的制备的方法

金相试样的制备的方法金相试样的制备主要包括取样及磨制,如果取样的部位不具备典型性和代表性,其检查结果将得不到正确的结论,而且会造成错误的判断。
金相试样截取的方向、部位及数量应根据金属制造的方法、检验的目的、技术条件或双方协议的规定选择有代表的部位进行切取。
金相试样的制备,磨抛及侵蚀参照GB/T 13298—1991《金属显微镜组织检验方法》的有关规定进行。
一、金相试样的选取1(纵向取样纵向取样是指沿着钢材的锻轧方向进行取样。
主要检验内容为:非金属夹杂物的变形程度、晶粒畸变程度、塑性变形程度、变形后的各种组织形貌、热处理的全面情况等。
2(横向取样横向取样是只垂直于钢材锻扎方向取样。
主要检验内容为:金属材料从表层到中心的组织、显微组织状态、晶粒度级别、碳化物网、表层缺陷深度、氧化层深度、脱碳层深度、腐蚀层深度、表面化学热处理及镀层厚度等。
3(缺陷或失效分析取样截取缺陷分析的试样,应包括零件的缺陷部分在内。
例如,包括零件断裂时的断口,或者是取裂纹的横截面,以观察裂纹的深度及周围组织变化情况。
取样时应注意不能使缺陷在磨制时被损伤甚至消失。
试样尺寸以磨面面积小于400mm2,高度15,20mm为宜。
试样可用手锯、砂轮切割机、显微切片机、化学切割装置、电火花切割机、剪切、锯、刨、车、铣等截取,必要时也可用气割法截取。
硬而脆的金属可以用锤击法取样。
不论用哪种方法切割,均应注意不能使试样由于变形或过热导致组织发生变化。
对于使用高温切割的试样,必须除去热影响部分。
二、金相试样的镶嵌在金相试样的制备过程中,有许多试样直接磨抛(研磨、抛光)有困难,所以应进行镶嵌。
经过镶嵌的样品,不但磨抛方便,而且可以提高工作效率及试验结果准确性。
通常进行镶嵌的试样有:形状不规则的试件;线材及板材;细小工件;表面处理及渗层镀层;表面脱碳的材料等。
样品镶嵌的常用方法有:1(机械镶嵌法机械镶嵌法系试样放在钢圈或小钢夹中,然后用螺钉和垫块加以固定。
- 1、下载文档前请自行甄别文档内容的完整性,平台不提供额外的编辑、内容补充、找答案等附加服务。
- 2、"仅部分预览"的文档,不可在线预览部分如存在完整性等问题,可反馈申请退款(可完整预览的文档不适用该条件!)。
- 3、如文档侵犯您的权益,请联系客服反馈,我们会尽快为您处理(人工客服工作时间:9:00-18:30)。
常规金相试样的切取
取样是金相试样制备的第一道工序,若取样不当,则达不到检验目的,因此,所取试样的部位、数量、磨面方向等应严格按照相应的标准规定执行。
(一)取样部位和磨面方向的选择
取样部位必须与检验目的和要求相一致,使所切取的试样具有代表性。
必要时应在检验报告单中绘图说明取样部位、数量和磨面方向。
例如,检验裂纹产生的原因时,应在裂纹部位取样,而旦还应在远离裂纹处取样,以资比较,检验铸件时;应在垂直于模壁的横断面上取样,对于大型铸件,还应从表面至中心的横断面上取3~5个试样,磨制横断面,由表面到中心逐个进行观察、比较。
图1-1表示轧制型材金相试样的切取方位,一般纵断面(图1-1中的1、2、4、5)主要用于(1)检验非金属夹杂物的数量、大小和形状;(2)检验晶粒的变形程度,(3)检验钢材的带状组织,以及通过热处理对带状组织的消除程度。
横断面(图1-1中的3)主要用于:(1)检验从表面到中心的金相组织变化情况,(2)检验表层各种缺陷,如氧化,脱碳,过烧、折叠等,(3)检验表面热处理结果,如表面淬火的淬硬层,化学热处理的渗碳层,氮化层,碳氮共渗层以及表面镀铬,镀铜层等:(4)检验非金属夹杂物在整个断面上的分布,(5)测定晶粒度等。
一般说来,在进行非金属夹杂物评定时,应磨制纵横两个面,在观察铸件组织,表层缺陷以及测定渗层厚度、镀层厚度,晶粒度等均需磨制横断面,在进行破断(失效)综合分析时,往往需要切取几个试样,同时磨制纵横两个面进行观察分析。
(二)取样方法
金相试样一般为ф12×12mm或ф18×20mm的圆柱体或12×12×12mm的立方体。
若太小则操作不便,若太大则磨制平面过大,增长磨制时间且不易磨平。
由于被检验材料或零件的形状各异,也有用不规则外形的试样。
非检验表面缺陷、渗层、镀层的试样,应将棱边倒圆,防止在磨制中划破砂纸和抛光织物,避免在抛光时试样飞出造成事故。
反之,检验表层组织的试样,严禁倒角并应保证磨面平整。
不论采用何种方式取样,都须防止因温度升高而引起组织变化或因受力而产生塑性变形。
如淬火马氏体因温度升高而转变为回火马氏体;裂纹处因受热而使其扩展。
最好是采用线切割取样。
试样尺寸以磨面面积小于400平方毫米,高度15~20mm为宜。
并经砂轮预磨。
形状不规则的试件、线材及板材、细小工件、表面处理及渗层镀层、表面脱贫碳的材料需要做好镶嵌。