推进感应淬火替代渗碳淬火的应用
渗碳后的几种热处理方法

渗碳后的几种热处理方法
渗碳只能改变零件表面的化学成分,要使零件获得外硬内韧的性能,渗碳热处理后还必须进行淬火加低温回火,来改善钢的强韧性和稳定零件的尺寸。
根据工件的成分、形状和力学性能等,渗碳后常采用以下几种热处理方法。
1)直接淬火+低温回火
将零件自热处理炉中取出直接淬火,然后回火以获得表面所需的硬度。
直接淬火的条件有两点:渗碳热处理后奥氏体晶粒度在5-6级以上;渗碳层中无明显的网状和块状碳化物。
20CrMnTi等钢在渗碳后大多采用直接淬火。
2)预冷直接淬火+低温回火
预冷的目的是减小零件变形;使表面的残余奥氏体因碳化物的析出而减少。
预冷直接淬火表面硬度略有提高,但晶粒没有变化,预冷温度应高于Ar3,防止心部析出铁素体,温度过高影响预冷过程中碳化物的析出,残余奥氏体量增加,同时也使淬火变形增大。
3)一次加热淬火+低温回火
将渗碳件快冷至室温后再重新加热进行淬火和低温回火,适用于淬火后对心部有较高强度和较好韧性要求的零件。
4)高温回火+淬火+低温回火
经高温回火后残余奥氏体分解,渗层中碳和合金元素以碳化物形式析出,易于机械加工同时残余奥氏体减少。
主要用于Cr-Ni合金钢零件。
5)二次淬火+低温回火
将工件冷至室温后,再进行两次淬火,然后低温回火。
这是一种同时保证心部与表面都获得高性能的热处理方法。
两次淬火有利于减少表面的残余奥氏体数量。
6)二次淬火+冷处理+低温回火
也称为高合金钢减少表层残余奥氏体量的热处理。
7)渗碳热处理后感应加热淬火+低温回火
多用于齿轮和轴类零件。
渗碳淬火钢的组织-概述说明以及解释
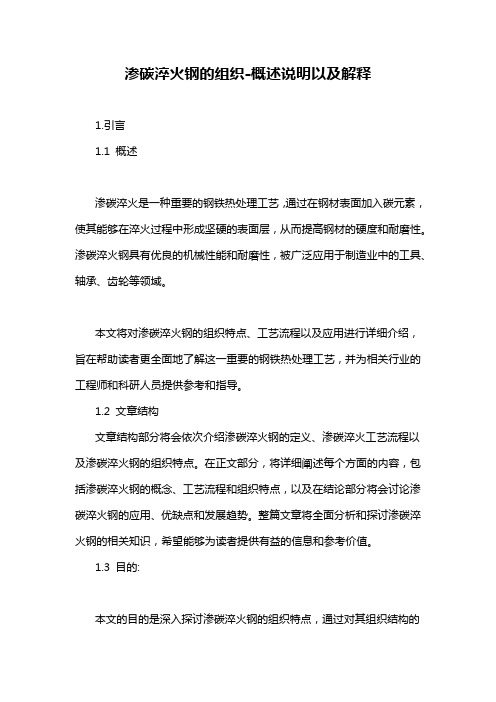
渗碳淬火钢的组织-概述说明以及解释1.引言1.1 概述渗碳淬火是一种重要的钢铁热处理工艺,通过在钢材表面加入碳元素,使其能够在淬火过程中形成坚硬的表面层,从而提高钢材的硬度和耐磨性。
渗碳淬火钢具有优良的机械性能和耐磨性,被广泛应用于制造业中的工具、轴承、齿轮等领域。
本文将对渗碳淬火钢的组织特点、工艺流程以及应用进行详细介绍,旨在帮助读者更全面地了解这一重要的钢铁热处理工艺,并为相关行业的工程师和科研人员提供参考和指导。
1.2 文章结构文章结构部分将会依次介绍渗碳淬火钢的定义、渗碳淬火工艺流程以及渗碳淬火钢的组织特点。
在正文部分,将详细阐述每个方面的内容,包括渗碳淬火钢的概念、工艺流程和组织特点,以及在结论部分将会讨论渗碳淬火钢的应用、优缺点和发展趋势。
整篇文章将全面分析和探讨渗碳淬火钢的相关知识,希望能够为读者提供有益的信息和参考价值。
1.3 目的:本文的目的是深入探讨渗碳淬火钢的组织特点,通过对其组织结构的分析和解释,帮助读者了解渗碳淬火钢的内部构造和性能特点。
同时,通过对渗碳淬火钢的组织特点进行研究,可以更好地指导工程实践中的应用,促进材料的优化设计和性能提升。
此外,还将探讨渗碳淬火钢的应用领域、优缺点以及未来发展趋势,为读者提供全面的了解和参考。
通过本文的阐述,旨在推动渗碳淬火钢在工业生产中的应用和发展,促进材料加工和工程领域的进步。
2.正文2.1 渗碳淬火钢的定义渗碳淬火是一种金属材料的表面处理技术,通过在金属表面强化碳元素的浓度,然后进行淬火处理,使得材料在表面形成高碳含量的硬化层,从而提高材料的硬度和耐磨性。
渗碳淬火钢是通过将金属材料在含碳气氛中加热至一定温度,使得碳原子渗透到金属表面,形成碳化层,然后经过淬火处理,使碳元素固溶在铁基体中,形成马氏体组织,最终实现对材料性能的提升。
渗碳淬火钢的应用范围广泛,包括汽车零部件、机械零件、工程机械等领域。
通过渗碳淬火处理,可以提高材料的表面硬度和耐磨性,延长材料的使用寿命,同时也能够提高材料的抗拉强度和抗疲劳性能,使其在高强度、高磨损环境下表现出色。
感应淬火与渗碳淬火

扭力轴花键感应淬火与渗碳淬火的工艺实践分析感应淬火与渗碳淬火同属表面硬化工艺,早在50年代,兵器部541工厂研究院坦克扭力轴即指出“感应淬火的成本为渗碳淬火的1/3,其后又提出:高频电流淬火工艺具有加热时间短、零件氧化皮少、变形小、工作环境洁净、可以在线生产等一系列优点。
”然而,时至今日,渗碳淬火工艺在中小模数齿轮等领域,仍广泛应用于生产。
其原由是渗碳零件表面碳浓度高,耐磨性更优、工夹具简单和中、小零件批量装炉方便等多种因素。
感应淬火需要专用的感应器,工装、管理费用等相对高些,一汽研究所下属公司曾对连杆大头内孔渗碳与感应淬火的单件总成本作精细的对比,渗碳件材料加39道工序的加工费为14.73分,而感应淬火件28道工序相对费用为12.73分。
单件成本相差2分。
感应淬火对复杂形状的工件仿轮廓淬火具有难度,小内孔、不通孔的底面、卡盘爪的阶梯面、活塞的沟槽、曲面件等部位,不如渗碳工艺简便,因此,在选择表面硬化工艺时,应从工装、材料、工序数、产品寿命等作具体分析再确定,不能仅从节能一点来选取。
渗碳与感应淬火在工艺与装备研发上,近年来均有很大的进展。
感应淬火工艺具有优势的项目可列举如下:1.深层渗碳方面齿轮的渗碳层深与其模数有关,常选用的层深为(0.15~0.20)m。
对中、小模数齿轮,此值在0.2~1.0mm,一般渗碳工艺即可达到,但对大模数齿轮,如m=80的齿轮(见图1)和m=63齿条等,其层深要求常≥4mm,如采用渗碳,则必须深层渗碳,仅渗碳周期即不低于100h,更不论齿条长度几十米对设备装炉的要求了,而感应淬火是单齿扫描淬火,从电源容量与升降机构方面考虑,要简单得多。
国外另一实例是冶金设备的内孔,用感应淬火代深层渗碳。
2.畸变小方面渗碳齿轮由于是整体加热,时间长、温度高,所以淬火后畸变大,有些齿轮则需压模淬火才解决问题,因此,它的周期长、耗电大、成本高,感应淬火相对有利,国内已有企业成功地将渗碳内齿圈改为感应淬火用于生产的实例。
EMA先进的齿轮感应技术

作者:艾玛感应科技(北京)有限公司感应热处理技术是上世纪20-30 年代建立起来的,成立于二战之后1946 年的德国EMA公司是较早开始研究与应用感应热处理技术的专业公司之一。
六十多年来,EMA 公司不断拓展和推新感应热处理技术的应用和发展,使得EMA 公司不仅成为欧洲著名的感应技术和设备供应商,客户包括奥迪、宝马、博世等世界著名的汽车及另部件制造商以及丹麦等国家的风电设备制造商,同时,也成为为全球感应热处理系统的领军公司之一,在齿轮感应淬火应用,数字化感应电源技术方面处于世界前列。
2000 年德国EMA 公司加入了爱协林集团,2005 年以爱协林热处理系统(北京)有限公司为依托,成立了EMA 北京事业部。
这样,在EMA 技术服务于中国市场的同时,为中国客户提供了贴近快速服务。
随着业务的快速发展,即将成立EMA 感应科技(北京)有限公司,值此齿协成立20 年之际,恭贺20 年来齿轮行业取得的进步,并把EMA 先进的齿轮感应热处理技术推荐给大家,以期为我们的齿轮行业做出贡献。
一感应淬火数字化晶体管中高频电源齿轮感应淬火工艺技术的进步离不开感应电源技术和控制技术的进步。
EMA 的齿轮感应淬火的电源经历了以下几个阶段:机械发电机变频电源(50 年代)--可控硅固态电源(70 年代)---IGBT 晶体管电源(90 年代)--TIV/TIC 串/并晶体管电源)--- 数字化晶体管电源(2000 年),这是世界上首台数字化的IGBT晶体管电源,其主要特点:·全数字逆变控制,所有的参数设置通过软件,有完备的数字接口,因此,可以适合任意控制要求,联网要求,以及远程参数设置和维护要求;一套控制单元适合所有频率;·功率因数cosφ 始终接近1, 无论满功率输出或非满功率输出;效率高;·覆盖频率范围宽,从50Hz 到100KHz ;·功率范围大,从20KW 到5000 KW;可以看出,EMA 的感应淬火电源始终走在世界前列,其卓越的性能为热处理工艺实施提供了充分的支持,广泛的选择。
感应淬火替代渗碳淬火

感应淬火最早得到应用是为了提高零件表面硬度,以满足耐磨性的要求。
经过几十年的发展,感应淬火已经发展成为应用范围最为广泛的热处理技术,在汽车、铁路、船舶、工程机械、机床以及军工等行业形成了完善的技术和质量体系。
感应淬火替代渗碳淬火是其推广应用的一个重要领域,基于其突出的经济性和较高的技术指标,受到业界的重视。
对于两者的比较,在以下几个方面进行分析。
经济性先进的技术是用最低的成本获得满足需求的性能,经济性是技术应用首先考虑的因素。
1.设备投资感应淬火设备的投资是比较小的。
如中等规格齿轮的淬火设备,一条齿轮连续炉渗碳线投资约800万元,加上淬火压床、吊具等辅助设备合计约1500万元。
按照相同的产能对比,需要2台感应淬火机床,每套自动淬火机床的价格约100万元,仅仅是渗碳设备的10%~20%。
与多用炉相比,1套感应淬火机床的产能至少与3台多用炉相当,其投资相当于多用炉(包括辅助系统)的50%。
设备的占地面积和安装方面也是费用支出的重要部分。
渗碳设备占地面积大,对厂房的水、电、气要求较高,造成生产厂房需要较大的投资,安装费用也较高。
感应淬火设备占地面积小,安装简便,费用要少很多。
2.生产运行费用和生产节拍感应淬火生产运行费用低,也是其具有推广价值的重要指标。
统计显示,感应淬火的能耗为渗碳淬火的20%左右,淬火介质的消耗为30%左右,设备维护和消耗备件的费用为20%左右,生产三废的排放也非常低。
感应淬火为快速加热,加热时间为几秒到几十秒,生产节拍非常快。
对于降低人工成本、降低在制品率有优势。
3.热处理零件用材料发达国家的感应淬火用材料有一个专门的系列,但专用材料不表示高成本,只是为达到更好的效果而做的调整。
感应淬火选材范围是最广泛的,并且由于其特有的优异性能可以选用低成本的材料替代价格较高的渗碳材料。
渗碳处理的温度高、时间长,需要特别注意控制其晶粒长大,所以渗碳用钢中必须含有一定含量的细化晶粒合金元素。
4.热处理后的加工在渗碳淬火的实践中,往往在后续的磨削工序出现渗碳层被磨掉的问题,其原因就是渗碳层相对较浅,热处理变形后偏磨。
中频感应淬火工艺参数对渗碳泵筒基体硬度的影响

M e i m r q e y i u t n h r n n r c s a a e e s d u f e u nc nd c i a de i g p o e s p r m t r o o h u p b r e a b rzn a d s ft e m a rx n t ep m a r lc r u i i g h r ne so h t i
Ab t a t T e f q e c d c o a d n n r c s ys r yn sd n u s et e t f e a a y i o o d t n n sr c : h e u n y i u t n h r e i gp o e s p a i gi i ea d o ti meo n lss f n io i g r n i b n d h i h t c i n et a d h ai gt mp rt r t e b s ft ep mp b re a b r i gh r n s a e n e e t e y c nr l d, n n t e c u s f n e ea u e, a e o u ar lc r u zn a d e sh b e f c v l o t l a d i o re o h h i s i oe h
第 3 7卷 第 6 期 ・ 术 学
Vo 7 N o . J . 3 6
湖
南AN AGRl CUL URAL l T MACHI NER V
N OV. 0 1 2 0
中频感 应淬 火工艺 参数对渗碳泵筒基体硬 度的影 响
李红莉 , 孙 博
抽油 泵筒 是抽 油泵 中重要且难 以加工 的零 件之一 。抽油 泵筒与表面硬化的柱塞组成一对摩擦副 ,要保证 柱塞转动 和 往复运动无 阻卡 、 损均匀 , 磨 更好地 适应深抽 , 抽油泵筒 应有 足够的强度 、 刚度 和疲劳强度 , 内表面还要 有高 的耐磨性 。 其 为了满足以上性能要求 , 对抽油泵筒 实施 了渗碳 、 中频 淬火 + 低温 回火 的热处理 工艺 。 通过 多次 实验 方法 , 找到 了适合基体
热处理节能工艺介绍【最新版】

热处理节能工艺介绍热处理的节能潜力很大,如何采取措施来加强节能是摆在每一位热处理工作者面前的重要课题。
下面仅就热处理工艺节能作一简单探讨。
1、降低加热温度题一般亚共析碳钢的淬火加热温度在AC3以上30~50℃,共析及过共析碳钢淬火加热温度为AC1以上30~50℃。
但近年来的研究证实,亚共析钢在略低于Ac3的α+γ两相区内加热淬火(即亚温淬火)可提高钢的强韧性,降低脆性转变温度,并可消除回火脆性。
淬火的加热温度可降低40℃。
对高碳钢采用低温快速短时加热淬火,可减少奥氏体碳含量,有利于获得良好强韧配合的板条马氏体,不仅可提高其韧度,而且还缩短了加热时间。
对于某些传动齿轮,以碳氮共渗代替渗碳,耐磨性提高40%~60%,疲劳强度提高50%~80%,共渗时间相当,但共渗温度(850℃)较渗碳温度(920℃)低70℃,同时还可减小热处理变形。
2、缩短加热时间生产实践表明,依工件的有效厚度而确定的传统加热时间偏于保守,因此要对加热保温时间公式τ=α·K·D中的加热系数α进行修正。
按传统处理工艺参数,在空气炉中加热到800~900℃时,α值推荐为1.0~1.8min/mm,这显然是保守的。
如果能将α值减小,则可大大缩短加热时间。
加热时间应根据钢种工件尺寸、装炉量等情况通过实验确定,经优化后的工艺参数一旦确定后要认真执行,才能取得显著经济效益。
3、取消回火或减少回火次数取消渗碳钢的回火,如20Cr钢装载机用双面渗碳活塞销取消回火的疲劳极限较回火的可提16%;取消低碳马氏体钢的回火,将推土机销轴套简化为20钢淬火态(低碳马氏体)使用,硬度稳定在45HRC 左右,产品强度和耐磨性显著提高,质量稳定;高速钢减少回火次数,如W18Cr4V钢机用锯条采用一次回火(560℃×1h)代替传统的560℃×1h三次回火,使用寿命提高40%。
4、用低中温回火代替高温回火中碳或中碳合金结构钢用中、低温回火代替高温回火,可获得更高的多冲抗力。
节能省时:感应加热淬火工艺

1 2 ● ‘
m eห้องสมุดไป่ตู้第
t l o k / S .o o r il O r w n 9 c n
移
参磊 … ’ …一 j 热 工 加
流 ,导体 中的 电流强度从表面 向心部呈指数规律衰 减 ,电流集 中在临近导体外表 的一薄层 ,这种现象 就是所谓的交变电流集肤效应 。感应淬火正是利用 这种集肤效应 ,使工件表面快速加热并淬火。
我公司在2 世纪8 年代引进盖斯林格弹性阻尼 0 0 联轴器 ,该产 品主要适用于柴油机动力装置中的联 轴器 。其花键轴多采用4 Cr 中频局部淬火 ,而簧 0  ̄ N 片多采用5 CV N 0 rA ̄高频局部淬火 。
—
降低结束端5 mm尺寸范 围的硬度 ,减 小该区域的 淬火应力。实践证明该方法是可行的 ,保证 了零件
∞
●
感应淬火硬度>5 H C / 8R
/ 硬化层深度 O + _ . o 8 4
/
;
/ /
的质量 ,避免了淬火裂纹的产生 ,同时满足使用要 求 ,也减少了淬火后的端部局部退火工序 。 如前所述 的端部淬 火、还有感应淬火有时存在
在齿面强化和联轴器的花键轴 、簧片等应用广泛 。 直径达2 0mm,模数2 ,单件重量达 ̄7多 , 20 5 J lt 材料 为3 C 2 iMo 0 rN 2 的大模数冶金齿轮 ,采用了单 齿仿齿 形 中频 连续加热 淬火 ,齿面硬度 和硬化 层
险。所以零件的设计如何适应工艺及操作的需要 , 就显得非常重要。如我公司生产的联轴器簧片的高 频局部淬火 ,引进 图样标注如图1 、图2 所示 。
感 应 加 热 淬 火加 热 速 度 快 ,可实 现 表 层 淬 火 , 而 无需 整 体 加 热 ,具 有 加 热时 间短 、 工件 变 形 小 、
合理使用感应加热淬火技术解决生产难题
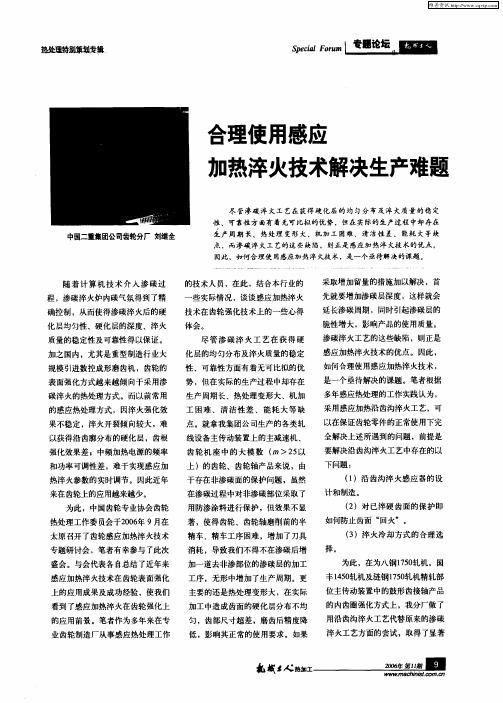
5 m的齿轮 ,多采用高频感应淬 m
火 ;而对 于模数 5 mm的齿轮 , ~8
扬长避短促进感应热处理的发展
相信 不远 的 将 来 ,在广 大热 处理 工作 者 和 感应 设 备制 造 商 的共 同努 力下 , 在 有 效控 制 感应 淬 火 的温度 和 硬 化层 深 度 均 匀 、可控 等 问题 上 下功 夫 .进一 步
热处理工作委员会于20年 9月在 06
太 原召开 了齿 轮感应加 热淬火技 术 专 题研讨会 ,笔者有幸 参与 了此次 盛会 。与会代表各 自总结 了近 年来
著,使得齿轮、齿轮轴磨削前的半
精车 、精车工序 困难 ,增加 了刀具 消耗 ,导致我们 不得不在渗 碳后增 加 一道去非渗 部位的渗 碳层的J T J n 工序 ,无形 中增加 了生 产周期 。更 主要 的还 是热处理 变形大 ,在实际 JT 中造 成齿面 的硬化 层分 布不均 J n
齿 轮 机 座 中 的 大 模 数 ( >2 以 m 5 上 )的齿轮 、齿 轮轴产 品来 说 ,由 于 存在 非渗碳面 的保护 问题 ,虽然 在 渗碳过程 中对 非渗碳 部位采取 了 用防渗涂料 进行保护 ,但效果不 显
全解决上述所遇到的问题,前提是
要解 决沿齿沟淬火 工艺中存在 的以
速 齿轮 箱大型企业 。而 其中的油 泵
齿轮 ,曾经 因为渗 碳淬火变形大而 先后 改为气体氮化 、低温气体氮碳
共渗等 ,但均 有一定问题 ,最终逐 步改为 齿部一 次性 高频加热 、整体
冷 却 淬 火 的 工艺 方 法 ,与 所谓 的
“
一
发法 ”感应加热淬 火相似 ,取
得 了较 为满 意的效 果 。对于 模数 3 重庆齿轮箱有限责任公司 邢大志
20cr渗碳淬火 维氏硬度范围

一、20Cr渗碳淬火简介20Cr是一种低碳铬钢,通常用于制造机械零件和工具,具有较高的强度和硬度。
为了提高其表面硬度和耐磨性,可以采用渗碳淬火工艺处理。
二、20Cr渗碳淬火工艺流程1. 渗碳处理:将20Cr钢件置于含有碳的气体或液体介质中,使其在高温下表面碳含量增加,形成一层碳化层。
2. 预热:将处理后的20Cr钢件进行预热,使其均匀升温至适宜的淬火温度。
3. 淬火:将预热后的20Cr钢件迅速放入冷却介质中,以快速冷却的方式使钢件表面形成马氏体组织,提高其硬度。
4. 回火:为了消除淬火过程中产生的残余应力和提高韧性,对20Cr钢件进行回火处理,使其获得适当的硬度和强度。
三、20Cr渗碳淬火后的维氏硬度范围经过20Cr钢件的渗碳淬火处理后,其维氏硬度范围通常在HRC 50-65之间。
这一硬度范围能够满足机械零件和工具在使用过程中所需的耐磨性和刚性要求。
四、20Cr渗碳淬火在实际应用中的意义1. 提高材料硬度和耐磨性:通过20Cr渗碳淬火处理,可以使20Cr钢件表面形成一层坚硬的碳化层,有效提高材料的硬度和耐磨性,延长零件和工具的使用寿命。
2. 改善材料强度和韧性:适当控制20Cr钢件的回火工艺,可以使其在获得较高硬度的保持一定的韧性,提高零件和工具的抗拉伸性能和抗冲击性能。
3. 降低成本提高效率:20Cr渗碳淬火工艺能够在一定程度上降低材料成本,同时提高零件和工具的使用寿命,减少更换和维修的频率,降低生产成本,提高生产效率。
五、20Cr渗碳淬火的注意事项1. 渗碳工艺控制:对渗碳过程中的温度、时间、介质和碳化层厚度等参数进行严格控制,确保碳化层的均匀性和适宜厚度。
2. 淬火工艺控制:淬火介质的选择、温度、冷却速度和冷却方式需要根据20Cr钢件的实际情况进行合理调整,避免出现淬火裂纹和变形等缺陷。
3. 回火工艺控制:回火工艺的温度和时间需要精确控制,以确保20Cr 钢件在获得合适硬度的能够保持一定的韧性。
感应加热技术在机械工程当中的应用 电炉转炉平炉在生产过程中的区别

感应加热技术作为一种新的技术被广泛应用到机械工程当中,其是利用电磁感应使被加热的材料(即工件)的内部产生电流,依靠这些涡流的能量来达到加热的目的。
感应加热系统的基本组成包括感应线圈、交流电源和工件。
根据加热对象的不同,可以把线圈制作成不同的形状。
线圈和电源相连,电源为线圈提供交变电流,流过线圈的交变电流产生一个通过工件的交变磁场,该磁场使工件产生涡流来加热。
感应加热是伴随着汽车工业和拖拉机工业的诞生而起步的。
由于其具有加热效率高、速度快、可控性好及易于实现机械化和自动化等优点。
目前常用的最有效的热处理工艺,具有下列多种应用:表面淬火、透热淬火、回火和消除应力(低温)、退火和正火(高温)、焊缝退火、粉末金属烧结等。
已在熔炼、铸造、弯管、热锻、焊接和表面热处理等行业广泛应用。
在铸造方面,正在迅速发展双联熔炼工艺,即利用中频炉保温改性,进行球墨铁或合金钢的精密浇铸;在锻造方面,利用敢于加热实现快速透热热锻,不仅减少了氧化皮损耗而且大大地增加了锻模的寿命,其材料利用率可达85%,锻件表面粗糙度可小于50μm;在焊接、淬火方面,国外一方面致力于开发大功率全固态高频电源,一方面致力于开发高度自动化热处理成套处理系统。
我国目前每年大约需要1000万t铸件,而铸造行业仍以冲天炉熔炼、一般铸铁的铸造为主,吨位较小,导致温度及成份波动大,废品率高。
较好的铸造业废品率也在6%~15%间,而一般铸造厂的废品率则高达30%。
感应淬火技术在汽车制造业的应用前景分析1、感应淬火工艺随着汽车工业的迅速发展,我国采用感应淬火的零件的种类和品种不断增加。
目前我国汽车零件感应淬火用材料包括:45#、40Cr、55MnVS、40MnB、42CrMo、35#、ZG45、球铁、合金铸铁等。
感应加热淬火介质包括:水、聚乙烯醇、聚迷水溶性淬火介质、UCON、豪富顿251等。
所采用的加热方式及应用主要包括:横向磁场静止一次加热淬火(销轴类零件、凸轮轴);横向磁场连续加热淬火(减振器杆、变速叉轴、扭杆等);横向磁场多段连续加热淬火(起动机轴、空压机轴等);纵向磁场整体一次加热淬火(半轴等);仿形感应器零件旋转加热淬火(球头销);感应接触加热淬火(转向齿条);内孔的一次及连续加热淬火(输出法兰、钟型壳内腔);阶梯轴类零件的旋转加热淬火(小红旗后轮毂轴、转向节);平面类零件的一次及连续加热淬火(钢板弹簧横向限位板);薄壁类复杂零件一次及连续加热淬火(前轮毂、滑动轴叉);复杂形状零件的一次加热淬火(钟型壳变截面轴);槽口一次淬火(变速叉);复杂回线工件旋转一次加热淬火(曲轴)等。
浅谈钢件渗碳后的淬火

符合要求 , 但变形大 ,尺寸不合格 。用 高温冷却 速度 约
l0C s O  ̄/ 的热 油,各项指标 都符合要求 ( 括尺寸 和硬 包 度的 C k值) p 。当热油 的高 温冷却速度 下降至约 8  ̄/ 5C s 时 , 变浅 ,不符合要 求 。当冷却 速度 恢复 至约 9 5一 l0C/ 后 ,各项 指标 又都 符合要求 。查 一些标准油 的 O ̄ s 特性资 料 ,未发 现 高 温 冷 却 速 度 为 10C/ 0  ̄ s的热 油 。 而我们 的 生 产实 际却 需 要 这 种 非 标 准 油 。有 资料 显 示 :油 的低 温冷却 速度变慢也会 导致 变浅 。由于 目 前一般用 户都缺乏 冷却速度 检测 手段 和检 测技 术 ,因 此笔者 建 议 :淬火 油 供 应 商 应 以满 足 客户 需 求 为 己 任 ,花大力气 帮助用 户选择 与生产 能够 满 足质量 要求
拌来 提高 冷 却 速 度 的方 法 时 ,还 必 须 注 意槽 中介 质 流 动的均 匀 性 。合 理 配 置搅 拌 器 的数 量 与 位 置 ,适
当采用 筛 网节 流 ,都 可改善 流动 的均匀性 。
3 .心部 硬 度 主 要取 决 于 淬火 温 度
图 1
在 相 同渗 碳 和 冷 却 介 质 条 件 下 ,工 件 的 心 部 硬
02rm。零件的平 面度 、孑 距 、开度等 尺寸要求严 格 , .5 a L
常出现 一 面硬 、一 面 软 的 现 象 。这 是 工 件 在水 流 冲
击 下 ,形 成 一 面 迎 流 、一 面 背 流 ,而 迎 流 面冷 却 速 度 大 ,背 流 面冷 却 速 度 低 所 造 成 的 。在 采 用增 加搅
在热 处 理 行 业 中 ,长期 存 在 “ 热 轻 冷 ” 的 倾 向 , 重 这在一 定程 度上也 约束 了淬火 冷却技 术 的发展 。 下面在这里仅谈几点粗 浅的看法 ,以供同行参考 。
渗碳淬火和回火处理

渗碳淬火和回火处理一、引言渗碳淬火和回火处理是金属材料热处理中常用的两种工艺,它们可以显著提高材料的硬度和强度,并改善其耐磨性、抗疲劳性和耐腐蚀性。
本文将分别介绍渗碳淬火和回火处理的原理、工艺和应用。
二、渗碳淬火处理渗碳淬火是一种将碳元素渗入金属表面并快速冷却的热处理工艺。
它主要用于钢材的加工,以提高其硬度和耐磨性。
渗碳淬火处理的主要过程包括预处理、渗碳、淬火和回火。
1. 预处理在渗碳淬火处理之前,需要对钢材进行预处理,包括去除表面氧化物和油脂、清洗和磨削。
这样可以有效地提高渗碳的效果,并保证处理后的材料质量。
2. 渗碳渗碳是将碳元素渗入钢材表面的过程。
常用的渗碳方法有气体渗碳、液体渗碳和固体渗碳等。
其中,气体渗碳是最常用的方法之一。
在气体渗碳中,将钢材放入渗碳炉中,通过一定的温度和时间,使炉内的渗碳气体与钢材表面发生化学反应,将碳元素渗入钢材表面形成一层高碳含量的渗层。
淬火是将渗碳后的钢材迅速冷却的过程,目的是使钢材的组织转变为马氏体,从而提高其硬度和强度。
淬火过程中,通常采用水、油或盐浴等不同的冷却介质,根据钢材的材质和要求来选择合适的淬火介质。
4. 回火回火是将淬火后的钢材进行加热处理的过程,目的是调整其硬度和强度,并改善其韧性和耐脆性。
回火温度和时间的选择要根据具体的钢材材质和要求来确定。
通常,回火温度越高,硬度降低,而韧性和韧性提高。
三、渗碳淬火处理的应用渗碳淬火处理广泛应用于各种机械零件的制造和加工过程中。
例如,汽车发动机曲轴、凸轮轴和齿轮等零件,需要具有较高的硬度和耐磨性,以保证其使用寿命和可靠性。
此外,渗碳淬火处理还用于制造机床导轨、滚珠丝杠和模具等高精度零件,以提高其表面硬度和耐磨性。
四、回火处理回火是一种通过加热处理来改善金属材料性能的方法。
它可以调整材料的硬度、强度和韧性,并减轻冷处理后的内应力。
回火处理的过程包括加热、保温和冷却。
回火处理中的加热温度通常在材料的临界点以下,以避免再次形成马氏体。
大型轴承套圈渗碳、淬火及模具设计应用

2 压 床 淬 火 机 构及 模具 设 计
GIEAS ON NO5 7淬 火 压 床 是 从 美 国 引 进 的 , 3 专
周 期 长 ( 圈 1 , 得 变 形 量 控 制 成 为 淬 火 过 程 中 的 关 见 )使
键 环 节 。 为 解 决 这 个 矛 盾 , 们 以 格 里 森 淬 火 压 床 为 压 我 淬 设 备 , 计 制 造 了 系列 轴 承 内 、 圈 淬 火 模 具 , 在 实 设 外 并
际 应 用 中不 断 改 进 完 善 , 得 了满 意 效 果 。 取
涨缩 口; 涨套外 表 面沿 轴线开有 一 定数量 的导油槽 . 在
增强 油 降效果 。 组 合模具 在工 件淬 火过程 中 , 制 内 此 控
图 3 轴 承 内 圈 摸具 及 压 淬 机构
1密封 圈 ; - 2斥却 窜 罩 ; 3抟 却 室 ;一 压 头 崖 : 4外 5内 压头 缝 ; 中心 压 士座 ;- 具 涨 芯 ;一 具 藏套 ; 6 7模 8接 0导 袖 槽 ;0轴 承 内 嗣 ; 1模 具 座 ;2定 位 调 整 圈 一 1 1一 1一
维普资讯
《 II艺 0 年弟2 热 》2 2 0 期
理
经 验 交流
着 2
大 型 轴 承 套 圉渗 碳 、 火 及 模 具 设 计 应 用 淬
De in& Ap l ai n o ef rB gBe rn n ’ Ca b rzn sg p i t fDi o i a ig RigS r u ii g& Qu n hn c o e c ig
动力总成曲轴感应淬火表面强化工艺应用成功案例

动力总成曲轴感应淬火表面强化工艺应用成功案例出于提升曲轴表面强化工艺水平的目标,从工艺实施对这项新技术在批量生产中的可行性进行了较全面的介绍。
在确保新工艺正常运行和产品品质稳定的前提下,进行了硬化层的性状检测,通过了全面的、严格的工艺验证。
一、小型铸铁曲轴的表面强化工艺用于1.6L及以下的小排量发动机的曲轴一般称为小型曲轴。
众所周知,轴颈圆角是加工中难度最大,也是发动机运行时易成为裂纹起源的重要区域,出于提高曲轴疲劳强度的目的,就必须对圆角进行强化处理(见图1蓝色部位)。
图1 曲轴的表面强化区域发动机曲轴的常用强化工艺一般有三种:(1)轴颈面淬火+圆角滚压工艺(见图2a)。
(2)轴颈面滚压强化+圆角滚压强化工艺。
(3)圆角淬火强化工艺(见图2b)。
目前最常用的是第一和第三种,而本文主要探讨介绍的就是第三种——圆角淬火强化工艺。
图2事实上,对中大功率发动机曲轴轴颈表面及圆角实施一次性感应淬火强化处理已有成功经验,可是,对于以铸铁材质为主的批量更大、前景更广的小排量发动机曲轴却仍然还是空白。
因为实施这项工艺时,表面强化区域是一个既包含轴颈面又包含左右两侧圆角的弧形区域,与中大功率发动机相比,此时曲轴被强化的圆角更小,很多情况下甚至仅为1.0~1.2mm,从而大大增加了对其进行淬火加热的难度。
故在执行淬火工艺时,若没有更为精巧的圆角淬火感应器(淬火头),以及更严谨的控制技术,就很难有效地对凹处(R角)进行可靠的强化处理。
包括美国通用在内的众多汽车厂,迄今对小型铸铁曲轴进行强化处理时,依然采用“轴颈面感应淬火+圆角滚压”作为主流工艺。
而近年来,为简化生产流程,提高产品质量,降低制造成本,将这一工艺替代机械滚压强化已成功地在德国、日本等主流汽车企业获得应用。
二、小排量发动机曲轴圆角感应淬火强化工艺的实践1.半开放式感应淬火线圈的应用和结构优化为了使“轴颈表面和圆角一次性感应淬火”能适应小型铸铁曲轴批量生产的需要,在试生产阶段就需要解决诸如:高性能的专用感应淬火头的结构、确定最佳的热处理工艺参数(包括对淬火头的调整),以及通过对感应淬火头采取的一些节能优化措施,使其在提升曲轴的强化质量的同时,又有较明显的节能效果。
多用炉热处理渗碳工艺及应用分析
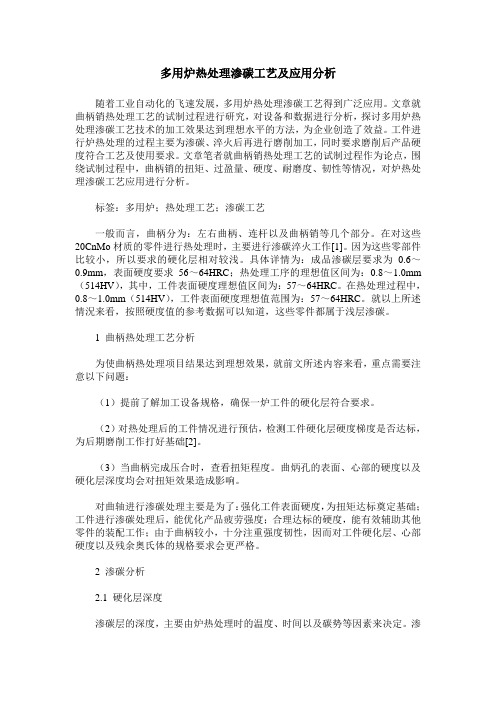
多用炉热处理渗碳工艺及应用分析随着工业自动化的飞速发展,多用炉热处理渗碳工艺得到广泛应用。
文章就曲柄销热处理工艺的试制过程进行研究,对设备和数据进行分析,探讨多用炉热处理渗碳工艺技术的加工效果达到理想水平的方法,为企业创造了效益。
工件进行炉热处理的过程主要为渗碳、淬火后再进行磨削加工,同时要求磨削后产品硬度符合工艺及使用要求。
文章笔者就曲柄销热处理工艺的试制过程作为论点,围绕试制过程中,曲柄销的扭矩、过盈量、硬度、耐磨度、韧性等情况,对炉热处理渗碳工艺应用进行分析。
标签:多用炉;热处理工艺;渗碳工艺一般而言,曲柄分为:左右曲柄、连杆以及曲柄销等几个部分。
在对这些20CnMo材质的零件进行热处理时,主要进行渗碳淬火工作[1]。
因为这些零部件比较小,所以要求的硬化层相对较浅。
具体详情为:成品渗碳层要求为0.6~0.9mm,表面硬度要求56~64HRC;热处理工序的理想值区间为:0.8~1.0mm (514HV),其中,工件表面硬度理想值区间为:57~64HRC。
在热处理过程中,0.8~1.0mm(514HV),工件表面硬度理想值范围为:57~64HRC。
就以上所述情況来看,按照硬度值的参考数据可以知道,这些零件都属于浅层渗碳。
1 曲柄热处理工艺分析为使曲柄热处理项目结果达到理想效果,就前文所述内容来看,重点需要注意以下问题:(1)提前了解加工设备规格,确保一炉工件的硬化层符合要求。
(2)对热处理后的工件情况进行预估,检测工件硬化层硬度梯度是否达标,为后期磨削工作打好基础[2]。
(3)当曲柄完成压合时,查看扭矩程度。
曲炳孔的表面、心部的硬度以及硬化层深度均会对扭矩效果造成影响。
对曲轴进行渗碳处理主要是为了:强化工件表面硬度,为扭矩达标奠定基础;工件进行渗碳处理后,能优化产品疲劳强度;合理达标的硬度,能有效辅助其他零件的装配工作;由于曲柄较小,十分注重强度韧性,因而对工件硬化层、心部硬度以及残余奥氏体的规格要求会更严格。
45钢淬火和低碳钢渗碳淬火
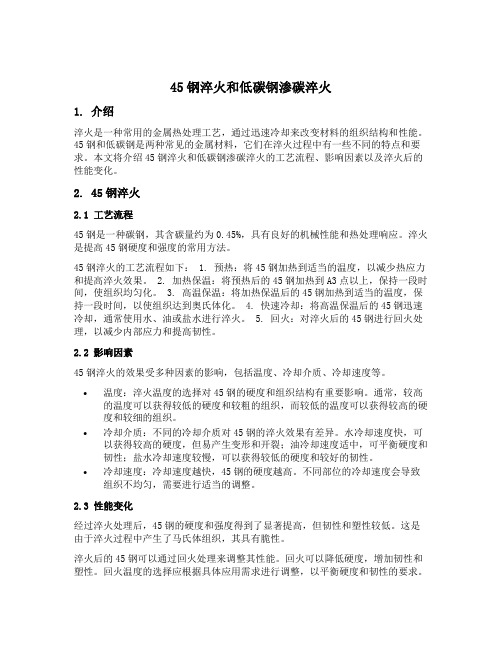
45钢淬火和低碳钢渗碳淬火1. 介绍淬火是一种常用的金属热处理工艺,通过迅速冷却来改变材料的组织结构和性能。
45钢和低碳钢是两种常见的金属材料,它们在淬火过程中有一些不同的特点和要求。
本文将介绍45钢淬火和低碳钢渗碳淬火的工艺流程、影响因素以及淬火后的性能变化。
2. 45钢淬火2.1 工艺流程45钢是一种碳钢,其含碳量约为0.45%,具有良好的机械性能和热处理响应。
淬火是提高45钢硬度和强度的常用方法。
45钢淬火的工艺流程如下: 1. 预热:将45钢加热到适当的温度,以减少热应力和提高淬火效果。
2. 加热保温:将预热后的45钢加热到A3点以上,保持一段时间,使组织均匀化。
3. 高温保温:将加热保温后的45钢加热到适当的温度,保持一段时间,以使组织达到奥氏体化。
4. 快速冷却:将高温保温后的45钢迅速冷却,通常使用水、油或盐水进行淬火。
5. 回火:对淬火后的45钢进行回火处理,以减少内部应力和提高韧性。
2.2 影响因素45钢淬火的效果受多种因素的影响,包括温度、冷却介质、冷却速度等。
•温度:淬火温度的选择对45钢的硬度和组织结构有重要影响。
通常,较高的温度可以获得较低的硬度和较粗的组织,而较低的温度可以获得较高的硬度和较细的组织。
•冷却介质:不同的冷却介质对45钢的淬火效果有差异。
水冷却速度快,可以获得较高的硬度,但易产生变形和开裂;油冷却速度适中,可平衡硬度和韧性;盐水冷却速度较慢,可以获得较低的硬度和较好的韧性。
•冷却速度:冷却速度越快,45钢的硬度越高。
不同部位的冷却速度会导致组织不均匀,需要进行适当的调整。
2.3 性能变化经过淬火处理后,45钢的硬度和强度得到了显著提高,但韧性和塑性较低。
这是由于淬火过程中产生了马氏体组织,其具有脆性。
淬火后的45钢可以通过回火处理来调整其性能。
回火可以降低硬度,增加韧性和塑性。
回火温度的选择应根据具体应用需求进行调整,以平衡硬度和韧性的要求。
3. 低碳钢渗碳淬火3.1 工艺流程低碳钢是一种含碳量较低的钢材,通常在淬火前需要进行渗碳处理,以提高其硬度和耐磨性。
螺母渗碳淬火
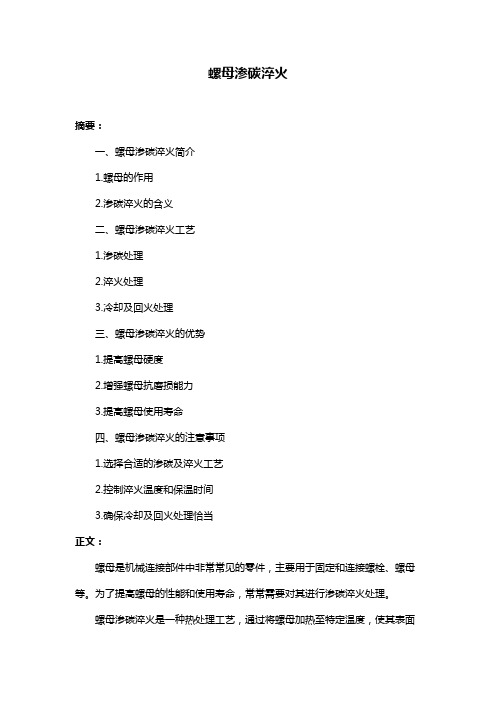
螺母渗碳淬火摘要:一、螺母渗碳淬火简介1.螺母的作用2.渗碳淬火的含义二、螺母渗碳淬火工艺1.渗碳处理2.淬火处理3.冷却及回火处理三、螺母渗碳淬火的优势1.提高螺母硬度2.增强螺母抗磨损能力3.提高螺母使用寿命四、螺母渗碳淬火的注意事项1.选择合适的渗碳及淬火工艺2.控制淬火温度和保温时间3.确保冷却及回火处理恰当正文:螺母是机械连接部件中非常常见的零件,主要用于固定和连接螺栓、螺母等。
为了提高螺母的性能和使用寿命,常常需要对其进行渗碳淬火处理。
螺母渗碳淬火是一种热处理工艺,通过将螺母加热至特定温度,使其表面渗入碳元素,然后迅速冷却,使碳元素在螺母表面形成高碳马氏体。
这种高碳马氏体具有很高的硬度和抗磨损能力。
接下来,对螺母进行回火处理,以降低内应力并提高韧性。
螺母渗碳淬火具有以下优势:1.提高螺母硬度:经过渗碳淬火处理后,螺母表面形成高碳马氏体,硬度得到显著提高,有利于提高螺母的抗磨损能力。
2.增强螺母抗磨损能力:渗碳淬火处理使螺母表面具有更高的硬度,从而降低螺母在使用过程中的磨损,提高螺母的使用寿命。
3.提高螺母使用寿命:经过渗碳淬火处理后,螺母的抗磨损能力得到显著提高,延长了螺母的使用寿命。
在实施螺母渗碳淬火处理时,需要注意以下几点:1.选择合适的渗碳及淬火工艺:不同的螺母材料和工况要求需要采用不同的渗碳及淬火工艺。
合理的工艺选择是保证螺母性能的关键。
2.控制淬火温度和保温时间:淬火温度的选择和保温时间的控制直接影响到螺母渗碳淬火的效果。
过高或过低的淬火温度以及过长或过短的保温时间都会导致螺母性能下降。
3.确保冷却及回火处理恰当:冷却速度对螺母渗碳淬火效果有重要影响。
冷却过快或过慢都会影响螺母性能。
此外,回火处理要充分考虑螺母的硬度、韧性等性能要求,以达到最佳的回火效果。
总之,螺母渗碳淬火是一种有效的提高螺母性能和使用寿命的热处理工艺。
渗碳后常用的淬火方法

渗碳后常用的淬火方法
淬火是一种常见的热处理方法,常用于提高材料的硬度和强度。
在渗碳后,淬火是必不可少的一步,它能够使材料的晶体结构发生变化,从而改善其力学性能。
下面将介绍几种常用的淬火方法。
1. 水淬火
水淬火是最常见的淬火方法之一。
它的原理是将渗碳后的材料迅速浸入冷却介质中,如水中。
水的高传热性能和高比热容使得材料迅速冷却,从而形成较硬的组织结构。
然而,水淬火容易产生内应力和变形,需要注意控制冷却速度,以避免材料的裂纹和变形。
2. 油淬火
油淬火是另一种常用的淬火方法。
相比水淬火,油的冷却速度较慢,可以减少内应力和变形的风险。
油的传热性能和比热容相对较低,使得材料能够在更温和的环境中快速冷却,从而获得适当的硬度和韧性。
3. 气淬火
气淬火是一种新型的淬火方法,它利用高速气流将热处理件迅速冷却。
相比传统的冷却介质,气体淬火具有更快的冷却速度和更低的冷却温度。
这种方法不仅可以获得优异的硬度和强度,还可以避免由于油和水淬火而产生的污染和环境污染问题。
4. 盐浴淬火
盐浴淬火是一种特殊的淬火方法,适用于一些特殊材料的处理。
它利用高温盐浴将材料迅速加热到淬火温度,然后迅速冷却。
盐浴淬火能够快速均匀地加热材料,并且由于盐浴的热容量大,冷却过程也相对平稳,能够有效控制材料的变形和应力。
淬火是渗碳后常用的一种热处理方法,有利于提高材料的硬度和强度。
不同的淬火方法适用于不同的材料和工艺要求,需要根据具体情况选择合适的淬火方法。
45钢淬火和低碳钢渗碳淬火
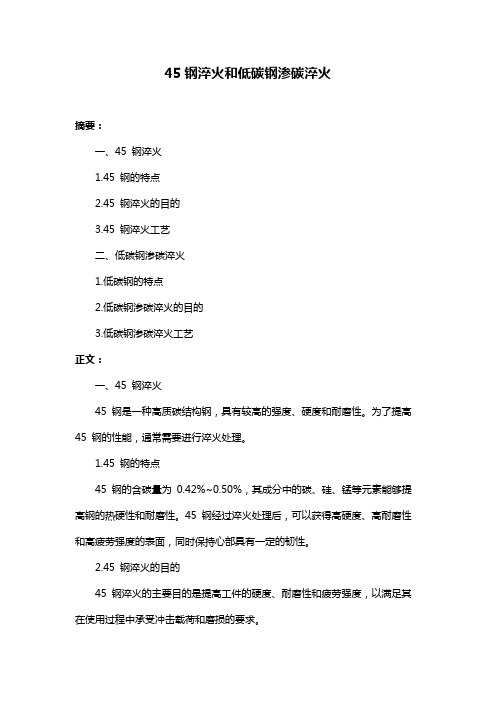
45钢淬火和低碳钢渗碳淬火摘要:一、45 钢淬火1.45 钢的特点2.45 钢淬火的目的3.45 钢淬火工艺二、低碳钢渗碳淬火1.低碳钢的特点2.低碳钢渗碳淬火的目的3.低碳钢渗碳淬火工艺正文:一、45 钢淬火45 钢是一种高质碳结构钢,具有较高的强度、硬度和耐磨性。
为了提高45 钢的性能,通常需要进行淬火处理。
1.45 钢的特点45 钢的含碳量为0.42%~0.50%,其成分中的碳、硅、锰等元素能够提高钢的热硬性和耐磨性。
45 钢经过淬火处理后,可以获得高硬度、高耐磨性和高疲劳强度的表面,同时保持心部具有一定的韧性。
2.45 钢淬火的目的45 钢淬火的主要目的是提高工件的硬度、耐磨性和疲劳强度,以满足其在使用过程中承受冲击载荷和磨损的要求。
3.45 钢淬火工艺45 钢的淬火工艺一般采用冷却速度较快的油冷或水冷方法。
淬火过程中,需要严格控制冷却速度、淬火时间和淬火介质的选择,以保证淬火效果的稳定性和可靠性。
二、低碳钢渗碳淬火低碳钢具有较好的可塑性、韧性和焊接性能,但在耐磨性和硬度方面较差。
为了提高低碳钢的性能,可以采用渗碳淬火工艺。
1.低碳钢的特点低碳钢的含碳量较低,通常在0.10%~0.25% 之间。
其成分中的碳、硅、锰等元素可以提高钢的可塑性和韧性,但耐磨性和硬度较差。
2.低碳钢渗碳淬火的目的低碳钢渗碳淬火的主要目的是提高钢件的表面硬度、耐磨性和疲劳强度,同时保持心部具有良好的韧性。
3.低碳钢渗碳淬火工艺低碳钢渗碳淬火工艺包括渗碳、淬火和回火三个步骤。
渗碳过程中,钢件表面通过碳的渗透,形成高碳浓度层;淬火过程中,钢件在高碳浓度层处迅速冷却,形成硬度高、耐磨性好的马氏体;回火过程中,对淬火后的钢件进行加热处理,以降低内应力和硬度,提高韧性。
总之,45 钢淬火和低碳钢渗碳淬火都是为了提高钢件的性能,通过不同的工艺方法,使钢件在不同方面得到优化。