TPM讲座_东风日产中文译稿
东风日产客户用车知识讲座资料XX春季版
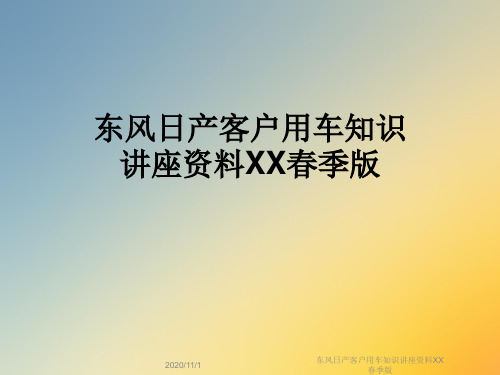
东风日产客户用车知识讲座资料XX 春季版
空调除雾
如何快速有效地除去车窗上的雾气呢?
Q 车窗起雾了怎么办?
东风日产客户用车知识讲座资料XX 春季版
汽车收音机
有时听收音机感觉有杂音,不清晰
Q 汽车收音机在哪些地方易受影响?
A 1)AM/FM强电场干扰,如广播电台大厦,电视发射塔,机场等附近; 2)AM/FM弱电场,如高山周围,隧道路,乡村等电台信号较弱的地方; 3)AM变电干扰,如发电站,变电所,电网附近等易受交变电流影响的 地方; 4)FM多重干扰,如城市高楼群,FM信号受到高楼间折射,易受干扰;
意义上的100%的成功率,极低概率的偶发失效是正常的; 5. 排除以上可能后,有可能是系统不良引起的失效,例如,钥
匙触点接触不良,请您前往NISSAN专营店进行检测。
智能钥匙 遥控钥匙
东风日产客户用车知识讲座资料XX 春季版
节油驾驶
实际使用油耗高于型录的经济油耗
Q为什么实际使用油耗与型录的油耗不一致?
东风日产客户用车知识 讲座资料XX春季版
2020/11/1
东风日产客户用车知识讲座资料XX 春季版
引言
ABS异音?
雨刮问题? “GuGu”音?
为什么…???
灯光不平?
如何除雾?
变速箱冲击?
《常见IQS问题QA》
???
东风日产客户用车知识讲座资料XX 春季版
儿童安全锁
从车外可以打开,车内中控锁解锁时也打不开
TPM发言稿
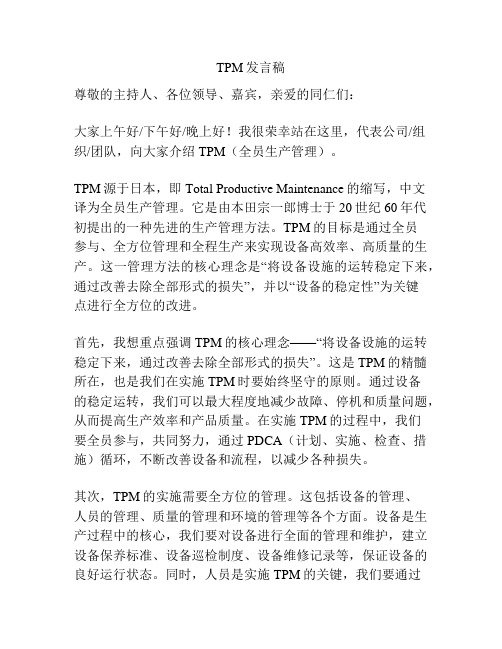
TPM发言稿尊敬的主持人、各位领导、嘉宾,亲爱的同仁们:大家上午好/下午好/晚上好!我很荣幸站在这里,代表公司/组织/团队,向大家介绍TPM(全员生产管理)。
TPM源于日本,即Total Productive Maintenance的缩写,中文译为全员生产管理。
它是由本田宗一郎博士于20世纪60年代初提出的一种先进的生产管理方法。
TPM的目标是通过全员参与、全方位管理和全程生产来实现设备高效率、高质量的生产。
这一管理方法的核心理念是“将设备设施的运转稳定下来,通过改善去除全部形式的损失”,并以“设备的稳定性”为关键点进行全方位的改进。
首先,我想重点强调TPM的核心理念——“将设备设施的运转稳定下来,通过改善去除全部形式的损失”。
这是TPM的精髓所在,也是我们在实施TPM时要始终坚守的原则。
通过设备的稳定运转,我们可以最大程度地减少故障、停机和质量问题,从而提高生产效率和产品质量。
在实施TPM的过程中,我们要全员参与,共同努力,通过PDCA(计划、实施、检查、措施)循环,不断改善设备和流程,以减少各种损失。
其次,TPM的实施需要全方位的管理。
这包括设备的管理、人员的管理、质量的管理和环境的管理等各个方面。
设备是生产过程中的核心,我们要对设备进行全面的管理和维护,建立设备保养标准、设备巡检制度、设备维修记录等,保证设备的良好运行状态。
同时,人员是实施TPM的关键,我们要通过培训和教育,提高员工的技能和意识,让每个员工都成为质量控制和问题解决的能手。
此外,我们还要注重质量管理,不断改进流程和操作方法,提高产品的一致性和客户满意度。
最后,环境的管理是TPM的重要组成部分,我们要注重设备的清洁和管理,减少能源的消耗和废物的生成,实现环境友好型生产。
最后,我想谈一下TPM的好处和挑战。
TPM的好处主要体现在三个方面:首先,它可以提高生产效率和产品质量,减少停机和故障,从而提高生产线的运行稳定性和产能利用率。
东风日产发言稿

东风日产发言稿英文回答:Ladies and gentlemen, esteemed guests,。
It is with great pleasure and honor that I stand before you today as a representative of Dongfeng Nissan to share our vision, our journey, and our commitment to shaping the future of mobility.For over two decades, Dongfeng Nissan has been at the forefront of the automotive industry in China, consistently pushing the boundaries of innovation and excellence. As the joint venture between Dongfeng Motor Corporation and Nissan Motor Co., Ltd., we have leveraged the strengths of both companies to create a formidable force in the automotive landscape.Our success stems from our unwavering commitment to our customers, a commitment that drives us to deliver productsand services that exceed expectations. We believe thatevery customer is unique, with their own individual needs and preferences. That's why we offer a diverse range of vehicles, from sedans and SUVs to electric vehicles and commercial vehicles, to meet the demands of everydiscerning customer.Innovation is the lifeblood of our company. We invest heavily in research and development, constantly exploring new technologies and pushing the limits of what is possible. Our commitment to innovation has led to the development of cutting-edge features and technologies that enhance the driving experience, improve safety, and promote sustainability.Sustainability is not just a buzzword for us; it is a core value that guides our every decision. We believe that we have a responsibility to protect the environment for future generations. That's why we are dedicated to reducing our carbon footprint, promoting electric vehicles, and implementing sustainable manufacturing practices.As we look to the future, we are excited by the opportunities that lie ahead. The automotive industry is undergoing a transformative period, with new technologies and trends emerging at an unprecedented pace. Dongfeng Nissan is well-positioned to embrace these changes and lead the way in the era of smart, connected, and autonomous vehicles.We are confident in our ability to continue to deliver exceptional products and services to our customers, while also playing a leading role in shaping the future of mobility. Our commitment to innovation, customer satisfaction, and sustainability will continue to guide us as we strive to become the most trusted and respected automotive brand in China and beyond.Thank you for your time and attention.中文回答:各位尊敬的来宾,女士们、先生们:今天,我非常荣幸代表东风日产站在这里,与大家分享我们的愿景、历程以及我们对塑造未来移动出行方式的承诺。
TPM全面生产维护培训讲义
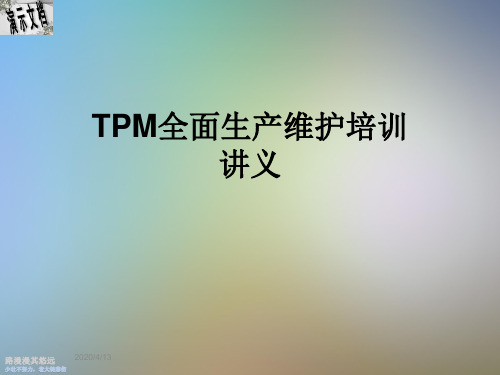
➢ 不良品率降低。
➢ 员工技能水平提高
➢ 生产及管理周期缩短。
健康 诊断
劣化测定
检查
(诊 断)
早期 治疗
劣化复原
预防修理
(提前改善)
路漫漫其悠远
预防保全
陈旧的设备管理观念
我是生产人员,你是维修人员。 设备我操作,维修你负责。 我修理,你设计。 我设计,你操作。 只要稼动率,不要可动率。 只有救火队,没有保养队。 只有单兵作战,没有团队合作。 迷信高速度的设备等。
P
Perfect
Production
M
路漫漫其悠远
Maintenance Management
设备管理的意义
获得过程(设备计划)
调查 研究
①
设计
制作
②
安装
使用过程(设备保全)
运行
保全
③
废弃
广义的含义
广义的设备管理 --- ① ② ③ 狭义的设备管理 --- ③
路漫漫其悠远
预防保全
Preventive Maintenance
立PM奖。 • 1971年,丰田(TOYATA)汽车公司的供应商日本电装,发扬光大了PM
活动,首次推出TPM概念。 • 1982年第一本标准化的TPM专著问世,书名为«TPM活动程序» • 1989年TPM的定义又一次被修改,内容得到进一步充实。
路漫漫其悠远
TPM活动的定义
1. 以最大限度地提高设备效率为目标(综合效率化); 2. 建立以生产设备为对象的预防保全系统; 3. 包括设备的计划、使用、保全等全部部门; 4. 从TOP到第一线工作人员的全体人员参加; 5. 教给员工管理方法,以小组的自主活动推进PM。
◎
东风日产客户用车知识讲座新改版
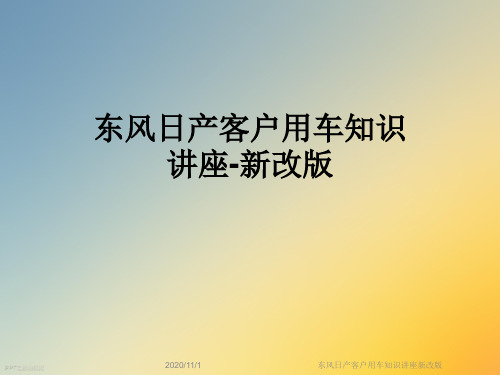
•3.被保险人的银行卡或者存折(卡或存折上需要有 日期标注,出险后开的户头不行).
பைடு நூலகம்
PPT文档演模板
东风日产客户用车知识讲座新改版
• 儿童安全锁
•Q • 从车外可以打开,车内中控锁解锁时也打
•为什么后排车门不能从车内打开?
不开
•A •
请从车外打开后车门,将儿童安全锁的开关
置于解锁位置。
• 如下图所示:
玻璃表面会有水珠形成。 • 3)乘客进入车内后,因为人的呼吸会使车内空气湿度和温度 • 上升,当车外环境温度相对车内温度较低时,车内湿度大的 • 空气遇到冰冷的车窗玻璃就会凝结成小雾珠,吸附在车窗内 • 表面,就形成了雾。
PPT文档演模板
东风日产客户用车知识讲座新改版
• 空调除雾
• 如何快速有效地除去车窗上的雾气呢?
•报案 ----95512 (平安) ----95518 (中保) ----95500 (太平洋)
• 报案时记得说明车辆的 •保单号或车牌号码,出险地
点、时间、经过哦!
东风日产客户用车知识讲座新改版
• 保险理赔新规定
•2009年11月1日起广东保险业全面实行<<机动车辆保险 赔款支付全额转帐管理办法>>.具体内容如下:
•4、使用、操作不当造成的损坏也不在保修范
围
•详情还得看保修手册!
PPT文档演模板
东风日产客户用车知识讲座新改版
• 出险理赔流程
• 发生事故
• 现场报案
• 拔打保险管家24小时服务热
线
• 保险事故车到店接待
• 定损 • 车辆维
修 • 客户提车
PPT文档演模板
• 金江专营店24小时服
TPM培训讲义课件

01
根据生产需求,明确设备应具备的功能、性能参数及技术要求
。
设计方案评估与优化
02
对设备设计方案进行全面评估,确保满足生产需求、降低成本
、提高可靠性。
设备布局与配套设施规划
03
合理规划设备布局,确保设备安全、高效运行;同时考虑配套
设施如电力、气源、排水等。
设备采购、安装及调试流程
01
02
03
设备采购
按照预防性维护计划,对设备进行定期检查、保养、更换易损件等 活动,防止设备故障发生。
建立检查记录与档案
对每次检查、保养、维修等活动进行记录,建立设备档案,方便后 续管理和维护。
03
CATALOGUE
计划保全与故障排除技巧
计划保全策略制定及实施步骤
设备状况评估
定期检查设备运行状态,收集 设备运行数据,评估设备性能
确定团队领导及核心成 员角色定位
建立有效的团队协作与 沟通机制
设定团队目标与工作计 划
培训需求分析和课程体系设计
01
02
03
04
调研分析员工技能现状及培训 需求
制定针对不同岗位和层级的培 训课程
设计符合TPM理念的课程体 系架构
评估课程效果并持续优化更新
内部讲师选拔培养及激励机制
制定内部讲师选拔标准与流程
01
02
03
04
维修流程梳理
对设备维修流程进行全面梳理 ,明确各环节职责及工作要求
。
维修效率提升措施
制定并实施维修效率提升措施 ,如采用快速维修工具、优化
维修步骤等。
维修人员培训
加强维修人员技能培训,提高 维修效率和质量。
维修备件管理
TPM全面生产维护(中英文版)
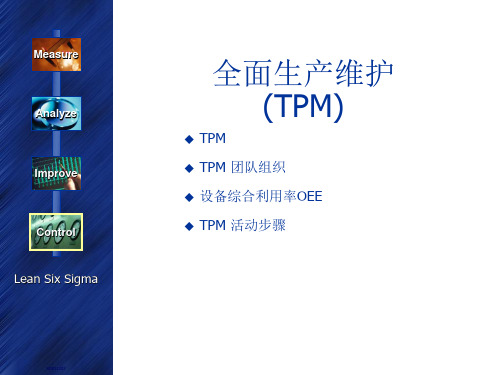
Revised 1-12-02
Total Productive Maintenance (TPM)
• Cp & Cpk • SupplyChainAccelerator
Analysis • Multi-Vari • Box Plots • Interaction Plots • Regression • ANOVA • C&E Matrices • FMEA
Measure Analyze Improve Control
Lean Six Sigma
全面生产维护 (TPM)
TPM
TPM 团队组织 设备综合利用率OEE TPM 活动步骤
RD011202
Measure Analyze Improve Control
Lean Six Sigma
Total Productive Maintenance (TPM)
Analysis • Internal Rate of Return
Analysis • Discounted Cash Flow
Analysis • PIP Management Process • RACI • Quad Charts
• Process Mapping • Value Analysis • Brainstorming • Multi-Voting Techniques • Pareto Charts • C&E/Fishbone Diagrams • FMEA • Check Sheets • Run Charts • Control Charts • Gage R&R
from Voice of the Customer • Finalize Project Focus and Key Metrics • Complete PDF
精益生产之全面生产维护__TPM(中英文双语版).

脑力风暴 拉系统 减少设置 TPM 流程图 标杆管理 亲和图 DOE 假设检验 力场分析图 树状图 甘特图
•
• • • • •
查检表 运行图 柱状图 散布图 控制图 柏拉图 互动回顾 愚巧法
Revised 1-12-02
3
Lean Six Sigma Improvement Process Road Map
定义
• • • • •
测量
• • • • • •
分析
• • • • •
改进
• • • • •
控制
• • • • • •
选定题目 列出客户 从顾客之声中列出关建需 求 定出项目焦点和重要指标 完成 PDF
绘制业务流程图 绘制价值流程图 制定数据收集计划 测量系统分析 收集数据 过程能力分析
•
•
提出关键因子 区分关键因子 验证关键因子 评枯每个关键因子对结果 的影响 量化机会 根本原因排序 寻找根本原因针对关键因 子
Define
• • •
Measure
• • • •
Analyze
• • • • •
Improve
• • • • •
Control
• • • • • • •
• •
Identify Problem Develop List of Customers Develop List of CTQ’s from Voicoject Focus and Key Metrics Complete PDF
关键因子确认 发掘潜在的解决方法 选择方案 优化方案 实行方案
•
过程变革和控制 制定控制计划 计算最终财务 过程指标 项目过渡给未来项目管理者 项目鉴 别 转化机会
TPM——讲义PPT课件

•2020/3/28
•29
2 自主保养step2导入推动 哲理小故事
•小蜗牛:为什么我们从生下来,就要背负这个又重又硬的壳呢? •妈妈:因为我们的身体没有骨骼的支撑,只能爬,又爬不快,所以
要这个壳的保护!
•小蜗牛:毛虫姐姐没有骨头,也爬不快,为什么她不用背这壳呢? •妈妈:因为毛虫姐姐能变成蝴蝶,天空会保护她啊。
2 -原因
表
文件中所有带有“为什么”的语句都3 -为会什么定? 义真正的3根-原源因 (通常需要至少5个“为什么”)
4 -为什么?
4 -原因
5 -为什么?
5 –根源
•2020/3/28
•35
2 自主保养step2导入推动
5Why质量工具简介
注意!!!
五个为什么
问五次为什么
5
•2020/3/28
•36
•2020/3/28
•8
1 TPM基础概念回顾
“一套三表”的概念
何谓“一套三表”?
《自主保养暂定基准书》----岗位操作员每月例行常规保养项目标准
《自主保养查检表》--------依照《自主保养暂定基准书》的执行记 录
《不良点标签汇总表》------执行保养的过程中发现异常(不良点) 记录,
并追踪复原、改善
奇怪为什麽?每周都要 换 O型密封圈。
换上一个 O型密封圈, 再换上一个活塞杆。
•2020/3/28
•20
2 自主保养step2导入推动
一个月之后,汽缸又
开 始漏油。
为什么 活塞杆
又
损坏,认真观察发现是
工
•2020/3/28
•21
2 自主保养step2导入推动
换上一个 O型密封圈, 再换上一个活塞杆, 加上一个盖子。
东风日产客户用车知识讲座新改版.pptx
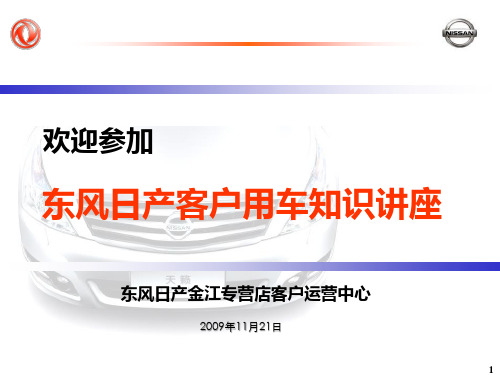
更好
A车与天籁车收信功能作比较图
A车 天籁
35 30 25 20 15 10
5 0
扰 干 重 FM多 场 电 FM弱 场 电 FM强 场 电 AM变 场 AM弱电 场 AM强电
12
空调除雾
为什么车窗会起雾呢,如何快速消除车窗起雾现象呢?
Q 车窗起雾了怎么办?
A 现象: • 车窗的外侧有小水珠出现 • 车窗的内侧起雾了-影响我的视 线
11
汽车收音机
有时听收音机感觉有杂音,不清晰
Q 汽车收音机在哪些地方易受影响?
A 1)AM/FM强电场干扰,如广播电台大厦,电视发射塔,机场等附近; 2)AM/FM弱电场,如高山周围,隧道路,乡村等电台信号较弱的地方; 3)AM变电干扰,如发电站,变电所,电网附近等易受交变电流影响的 地方; 4)FM多重干扰,如城市高楼群,FM信号受到高楼间折射,易受干扰;
1. 对于前风挡玻璃: ①除雾模式1 → ② 外循环 →③ 开启A/C → ④风量设为最大 MAX
前风挡除雾标识 后风挡除雾标识
2.对于后风挡玻璃&后视镜: 开启 ,15分钟后自动关闭;
当后窗除雾按钮按下时,嵌在后风挡玻璃以及后视镜玻璃夹层中的电阻丝就自动通电发热,加热玻璃,快速地去除 表面的雾气/霜。
欢迎参加
东风日产客户用车知识讲座
东风日产金江专营店客户运营中心
2009年11月21日
1
引言
变速箱冲击?
磨合期?保修期?
为什么…???
常见问题处理?
???
出险处理流程?
定期保养?
2
目录
新车磨合期 保修期注意事项 定期保养注意事项 保险理赔处理 汽车驾驶小常识
3
东风日产发言稿

东风日产发言稿
尊敬的各位媒体朋友、各位汽车行业同仁:
大家好!
我是东风日产的代表,很荣幸能在这里和大家分享一些关于我们公司的最新动态和发展计划。
首先,我要感谢各位长期以来对东风日产的关注和支持。
作为一家致力于为消费者提供高品质汽车产品和服务的企业,我们一直秉承着“创新、务实、合作、共赢”的经营理念,不断推动企业的发展和进步。
近年来,随着中国汽车市场的不断发展和变化,东风日产一直保持着良好的发展势头。
我们不仅不断推出符合消费者需求的新车型,还积极拓展销售渠道,提升售后服务水平,努力为消费者提供更加便捷和优质的购车和用车体验。
同时,我们也非常重视科技创新和可持续发展。
未来,东风日产将继续加大在新能源汽车、智能网联技术等领域的投入,努力推
动汽车产业的转型升级,为社会和环境做出更大的贡献。
在此,我代表东风日产全体员工,再次感谢各位媒体朋友和合作伙伴的支持与厚爱。
我们将继续秉承“以客户为中心”的理念,不断提升产品质量和服务水平,为消费者创造更多的价值和美好的出行体验。
谢谢大家!。
工厂全面改善TPM专业讲座

工厂全面改善TPM专业讲座工厂全面改善TPM专业讲座尊敬的各位领导、各位同事们:大家上午好!今天我给大家做一个关于工厂全面改善TPM (Total Productive Maintenance)的专业讲座。
TPM是一种全新的设备维护管理方法,它的目标是通过全员的参与,实现设备的持续稳定运行,提高生产效率和产品质量。
接下来,我将从TPM的基本概念、实施步骤和重要性三个方面给大家做详细的介绍。
首先,让我们来了解TPM的基本概念。
TPM是通过全员参与,以实现零故障、零事故、零缺陷和零停机为目标的设备维护管理方法。
它主要包括三大支柱:设备保养活动、设备自主管理和员工参与。
其中,设备保养活动的核心是预防保养,通过定期的保养和检查,预防设备故障的发生。
设备自主管理是指将设备的操作和保养工作交给设备操作员,使其成为设备的“专家”,实现设备的稳定运行。
员工参与是TPM的灵魂,通过培养员工的意识、技能和能力,实现员工对设备的积极参与和改进,推动企业的全面发展。
然后,我们来看一下TPM的实施步骤。
TPM的实施分为六个阶段:从事实管理、创始管理、递进管理、综合管理、持续管理和创新管理。
从事实管理是指通过对现有设备运行状况的分析,找出设备故障的原因和改进的方向,为后续的改善工作做好准备。
创始管理是指制定设备保养标准和操作规程,建立设备保养体系,为设备的稳定运行提供保障。
递进管理是指通过设备保养的不断改进,提高设备的稳定性和可靠性,实现预防性保养。
综合管理是指将设备的管理与生产计划、质量控制、物料控制等其他管理工作结合起来,推动企业整体绩效的提高。
持续管理是指通过设立全员参与的机制,发挥员工的主观能动性,推动企业的全面发展。
最后,创新管理是指通过技术创新和管理创新,实现企业的持续发展和竞争优势。
最后,我们来谈谈TPM的重要性。
TPM对企业发展具有重要的推动作用。
首先,TPM能够提高设备的可靠性和稳定性,减少设备故障和停机时间,提高生产效率和产品质量。
TPM与预防保全
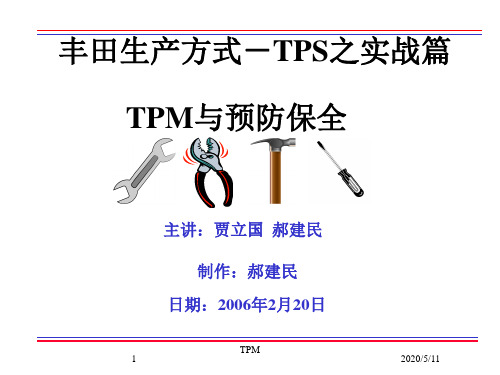
.减少查找时间 · 防止物品短缺、误用、误送 · 塑造清爽的工作场所 .节约管理费用
13 TPM 2013-8-23
整理的要点
在于制定可行、有效、合理的处理基准 1. 使用日期是否明确 2. 使用计划是在一星期或一个月以上,是否有指定的 存放场所 3. 故障品、废品的放置 4. 没有在指定场所保管,给人、车、物带来不便 5. 对业务和作业没有必要,但仍保管着的 6. 与现在生产的产品没有关联的零部件或设备 7. 无法使用的,不使用的 8. 不良品与合格品混在一起 9. 超过必要的部分废弃 10. 过多的组装部件也是不要品
素养(清心)
整理
整顿
清扫
清洁
12 TPM 2013-8-23
5S的定义
1.整理 — 就是识别和清除不必要的物品,因为不必要物品是现场的敌
人
目的:彻底根除因不必要的物品而形成的
· 将工作场所所有物品区分为有必要的与不必要的 · 把必要的东西与不必要的东西明确地、严格地区分开来;
· 不要的东西要尽快处理掉。 目标:
丰田生产方式-TPS之实战篇 TPM与预防保全
主讲:贾立国 郝建民 制作:郝建民 日期:2006年2月20日
TPM
1
2013-8-23
一、TPM与预防保全的概念 二、TPM实践 三、预防保全流程与帐票做成 四、预防保全的进度看板 五、突发故障与保全记录 六、保全指标的控制与评论 七、保全报告与设备例会
2013-8-23
整理 整顿 清洁 展开 保持 + 安全 + 节约
9
“七种”浪费
(SEVEN‘S MUDA)
1.生产过剩的浪费 2.在库的浪费 3.等待作业的浪费 4.动作的浪费 5.搬运的浪费 6.不良生产的浪费 7.加工本身的浪费
TPM培训课件
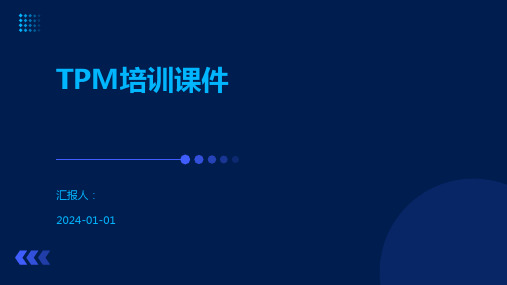
04
TPM的推进步骤
准备阶段
制定推进计划
明确推进目标、时间安排、责任分工 等,为后续推进工作提供指导。
设备清扫
对设备进行全面清扫,发现和解决潜 在问题,为后续的自主维护打下基础 。
培训宣传
组织员工参加TPM培训,提高员工对 TPM的认识和重视程度,同时通过宣 传活动营造TPM氛围。
强调生产设备的全面维护和保养,涉及设备的一生管理,包 括预防维修、日常保养、事后维修等环节,目标是提高设备 的可靠性和稳定性,降低设备故障率,提高生产效率。
TPM的目的和意义
提高设备利用率
通过减少设备故障和维 护停机时间,提高设备 的可利用率,从而提高
生产效率。
降低维护成本
通过预防性维护和保养 ,减少设备维修和更换 成本,降低生产成本。
重点管理
总结词
重点管理是对关键设备和部位进行重点维护和管理的措施,以确保这些关键设备和部位的正常运行,从而保证整 个生产线的稳定性和效率。
详细描述
重点管理要求对关键设备和部位进行定期检查、维护和更换,同时建立相应的管理档案和维修计划。此外,还需 要对这些设备和部位进行技术升级和改造,以提高其性能和可靠性。
通过对设备的全面检查和维护,确保设备处于最佳工作状态,提高 设备性能和稳定性。
延长设备使用寿命
通过科学的维护和管理,有效延长设备使用寿命,降低更换成本。
降低维修成本
减少维修人力成本
通过预防性维护,降低设备维修 的频率和难度,减少对专业维修
人员的依赖,降低人力成本。
降低备件库存成本
通过对设备的全面了解和维护, 合理预测备件需求,降低备件库
定期检查
定期对设备进行检查和维 护,确保设备始终保持良 好的运行状态。
TPM讲座

反复检查变化症状
因清扫不充分而引起的弊害
1.故障的原因
由于回转部,悬接部空压,油压系统,电气装御系统,传感品等被 污染,异物混入经过磨擦,堵塞、阻抗、通电不良等成为精度低 下或误动作等故障的原因.
2.品质不良的原因
异物直接混入制品中,或因设备的误动作而造成
3.强制劣化的原因
灰尘,污染落入缝隙而使检查困难,或加油困难造成中断等,是引起设备 强制劣化的原因.
3. 如果设备事前正常管理,就不会出现故障,若没有故障,自然就能预 防不良、灾害;
4、如果员工技能能够得到保证,就不会出现作业性不良,不会有不良品 流到市场; 4. 由人和设备、产品技术,决定竞争力; 5. 随着企业的发展,我们还会迫切需要能够降低制造成本的TPM活动;
TPM 8大活动支柱 TPM 体系由通常的下述八个支柱构成
的工厂、创造清洁的工厂、创造可视化的工厂。
5S具体内容
整理 整顿
物品分类,除去不必要的物品。 合理放置,方便使用。
清扫
清洁 清心
对角落清扫,清扫时检查。
制订可维持的基准。 养成良好的习惯,自觉遵守规则。
5S活动的5个阶段
通过TPM-消除不合理
不合理的思想概念:300:29:1
◇4-技能教育和设备检查
◇5-整理基准书做综合检查 ◇6-树立品质标准系统 ◇7-自主管理
以人员组装流水线为主的自主保全6STEP活动 ◇1-初期清扫 ◇2-发生源及困难部位的解决 ◇3-鉴定标准设定
通过感官彻底去除灰尘污染 去除,改善发生源/困难场所 标准的可视化管理,流水线效率化 作业条件的检查、操作最易化 均衡化生产 构筑品质均一,生产灵活的线体
对微小缺陷的思考方法
全面生产维护(TPM)讲义(改)

❖ 这种以提高生产设备效率达到提高生产能力的生产模式是一种内涵式的 发展模式,较之传统的以增加生产要素提高产能的外延式发展更加符合 可持续发展的战略目标。
❖ 许多世界级企业已经证明,现代设备管理可以在无需增加资源投入的条 件下较大幅度地提高设备的生产能力。
2021/8/5
13
❖ (5)设备管理对可持续发展战略的影响
5
2、什么是机制?
❖ 机制就是制度加方法或者制度化了的方法。 其含 义为“因为这个方法的存在,使得一件事不得不被 完成到最好” 。
❖ (1)机制是经过实践检验证明有效的、较为固定 的方法,不因组织负责人的变动而随意变动,而单 纯的工作方式、方法是可以根据个人主观随意改变 的。
❖ (2)机制本身含有制度的因素,并且要求所有相 关人员遵守,而单纯的工作方式、方法往往体现为 个人做事的一种偏好或经验。
❖
传统的工业生产过程中,生产能力的提高通常是通过增加固定资产
投资或员工的加班加点也就是资源的投入实现的。但是这种资源投入型
的生产方式由于固定成本的增加并不能有效提高企业生产经营的效益,
同时这种粗放型的生产方式也不利于资源的节约和环境保护。
❖ 现代设备管理的理念是通过加强设备管理,提高设备的综合效率以 实现生产能力的提高。因为生产设备综合效率的提高可以减少各种形式 的设备非计划停机时间,从而实现提高设备生产能力的目标。
2021/8/5
25
6. 日本对PM的改进完善
❖ 为了解决设备管理中的诸多问题,日本把美国维护设备的 经验进行了总结:
❖ 将装备出现故障以后采取应急措施的事后处置方法称为 “事后保全(BM)”;
❖ 将装备在出现故障以前就采取对策的事先处置方法称为 “预防保全(PM)”;
TPM新闻发言稿

TPM新闻发言稿尊敬的各位嘉宾、媒体朋友们:大家上午好,感谢大家出席今天的新闻发布会。
我是XXXX (公司/机构)的代表XXXX(职位),很荣幸向大家介绍我们主要推出的TPM(Total Productive Maintenance)的新闻和项目。
TPM,全面生产维护,是一种通过全员参与,不断提高设备可靠性和生产效率的方法和理念。
它起源于日本,并逐渐在世界范围内得到广泛应用。
TPM的目标是通过消除设备的各种损失和长时间停机,提高设备的整体效率,降低成本,提升品质,并实现安全和人员发展。
首先,我想向大家简要介绍一下TPM的背景和意义。
在过去几十年里,全球制造业竞争日益激烈,各行业面临来自不同国家和地区的竞争对手。
为了在激烈的市场竞争中立于不败之地,企业需要改善生产效率,提高产品质量,降低成本。
设备是生产的核心,因此设备的可靠性和效率对于企业的成败至关重要。
然而,在实际生产过程中,我们常常面临设备损坏、故障和长时间停机等问题,这不仅会导致生产延误,还会造成巨大的经济损失。
TPM作为一种综合管理和改进手段,通过从根本上解决设备问题,提高设备的可靠性和稳定性,从而实现设备长期稳定运行和高效生产。
它不仅仅是一种工具或方法,更是一种持续改进的文化和态度。
TPM的核心是全员参与和团队合作,从设备操作员到管理层,每个人都需要参与到TPM的实施中来。
那么,TPM的目标和实施过程是什么呢?首先,TPM的目标就是通过充分利用设备所有人员的力量和智慧,最大限度地提高生产效率,优化设备运行状态,实现高质量、低成本、高效益的生产。
为了实现这一目标,TPM需要依靠以下主要的实施步骤:1. 了解设备:全员组织参与设备的了解和分析,通过设备巡检和点检等手段,掌握设备的运行状态和问题,为设备改进提供数据支持。
2. 开展设备保养:制定和执行全新的设备维护计划,包括日常保养、定期保养和预防性保养等,以确保设备的稳定性和可靠性。
3. 消除故障:通过分析和处理设备故障,不断优化设备维修流程,缩短设备故障的修复时间。
- 1、下载文档前请自行甄别文档内容的完整性,平台不提供额外的编辑、内容补充、找答案等附加服务。
- 2、"仅部分预览"的文档,不可在线预览部分如存在完整性等问题,可反馈申请退款(可完整预览的文档不适用该条件!)。
- 3、如文档侵犯您的权益,请联系客服反馈,我们会尽快为您处理(人工客服工作时间:9:00-18:30)。
何谓自主保全・・・设备的预防 医学
设备的健康诊断
父母(作业员)向医生(保全员)详细说明, 可以早期恢复 身体情况的观察・・・・・身体情况从何时开始变差的? 发热?食欲呢?有没有异常声音?
何谓自主保全・・・设备的预防 医学 自主保全的作用
发现不及时・・・ ・需要做手术 (设备拆解修理)
早期发现设备疾病・・・・家庭常备药即可治疗
STEP 1~3 繰り返し
STEP 4~5 数据収集 损失改善活動 构建提高竞争力活动体制
保全技能培训
改良保全,计划保全,预防保全
1. TOP的
社内报上记载 TPM导入决议宣言TPM社内讲习会宣言 干部 : 阶层别合宿研修 Champion 一般 : 页面上映会 委员会, 专门分会 推进事务局 Bench Mark(水准点)和目标 目标设定 效果预测 导 入 实 施 阶 段
7. 组成生产效率化体质 7.1 个别改善
综合总结了“工作的标准化和改善”、“人财的 培养” 维持・提升制造现场QCT水准的的机制
TPM的推进 同期生产的实现 NPW
TQM
Q、C、T 提升 SQC 接头(JIT) IFA 自主保全
追求NPW “两个无限” 无限同期于顾客 无限的课题表面化和改革 自主保全 层次提升活动 计划保全体制诊断 降低6大损失 提升OEE的活动
Maintenance 全员参加的生产保全
TPM ・・・・TOTAL Procuctive
何谓TPM・・・・・ TPM5大支柱
自主保全 ・・・・ 计划保全 ・・・・ 专项改善 ・・・・ 制造主导的故障防止活动 保全主导的故障防止活动 制造・保全・技术・品保・其他部门 合力开展的损失改善活动
人材培养 ・・・・ 设备精通人员的培养 (异常发现力・修理复原力・改善力・维持管理力) MP活动 ・・・・反馈到新一代免维护设备
成本 コスト (C)
何谓TPM・・・・ TPM的目的
3、生产性提升和维持管理
1、生产性和设备可靠性提升 结果系・・・ OEE・JPMH・JPH的提升 要因系・・・ ①设备可靠性提升・・・故障防止・早期复原 ②自主保全日常活动・・・利用5感发现异常 ③减少自主保全故障的活动・・・STEP1~4 ④6大损失的改善(故障损失为MUST)
良品数量 良品重量
不良损失 暖机损失 头尾料损失
(15)能源损失
有效能源
(16)模具/治工具损失
(14)成品率损失
损耗损失 多余的损失
单位成本的效率化------------阻碍[物料效率化]得3大损失
TPM的推动方法
TPM展开进程(12阶段)
区分 S T E P 要 点
区分 S T E P 要 点 追求生产效率化的极限 PROJECT TEAM 活动 工作岗位小集团活动 STEP 方式, 诊断和合格证
2、维持管理 ・计划保全・自主保全的定期点检 ・追求自主保全点检的效率化 3、人的培养 (培养精通设备的人才) ・异常发现技能 ・修理复原技能 ・改善技能
何谓TPM・・・・TPM的目的
4、 “0挑战”
“0”挑战
Байду номын сангаас故障0
不良0
灾害0
何谓TPM・・・・ TPM的效果
有形效果 S Q C T :停工、非停工灾害零 :减少工程不良率 :降低制造成本 : 提升OEE、JPMH ・减少突发故障件数 ・提升设备稼动率 ・削减库存 :增加改善件数
目标 手 段 分 类
正常运转
实 老化防止
施 活 老化测定
动 老化复原
分 担 运转 保全 技术
◎ ◎ ◎ ◎ ◎ ◎ ◎ ○
维 持 活 动
日常保全
正确操作 准备、调整 清扫 ·潜在缺陷的找出 ·改善 加油 再紧固 使用条件, 老化的日常检查 小整备 定期点检 定期诊断 定期维修 倾向诊断
定期保全 设 备 综 合 效 率 提 升
5S活动
进度 2007
已实施 2008
开展中 2009
6 7 8 9 10 11 12 1 2 3 4 5 6 7 8 9 10 11 12 1 2 3 4 5 6 7 8 9 10 11 12 1 2 3 4 5 6 7 8 9 10 11 12
STEP 1
STEP 2
STEP 3 STEP 1
STEP2
这是自主保全!
何谓TPM・・・ 减少故障→生产 效率化
时间
<人的高效化> <设备的高效化> 投入时间
就业工时
除外工时
(支援其他部门)
工作时间 负荷时间
计划 停止
计划停止 (8) 停机损失 (1) 故障损失
负荷时间
阻 碍 人 的 效 率 化 的 5 大 损 失
等待指示的损失 等待材料损失 设备停止损失 设备性能损失 方法顺序损失 技能/士气损失
无形效果 1. 营造人员意识改变,自己的 设备自己保护的氛围 2. 只要做就可实现的自信和 想要进一步改善的干劲 3. 5S 得到贯彻的整洁岗位 4. 来访者有良好印象的企业形 象
M
TPM的推进
推进制造理想姿态的共性管理・改善工具
TQM推动的管理循环
→活动支柱
日产生产方式 (NPW) 制造的理想姿态
何谓TPM・・・・・
设备保全方式
生产保全 保全预防
全员参加TPM
TPM的5本柱 TPM ・・・全员参加的生产保全 MP活动
专项改善
改良保全
预防保全
自主保全 计划保全
人材培养
事后保全
最大的特点是 ・“操作员的自主保全”(自己的设备自己维护) ・全员参加(所有关联部门、从领导到一线)的活动
何谓TPM・・・ 设备保全的分工
2. TPM导入教育和 导 入 准 备 阶 段
7.2 自主保全 7.3 计划保全 7.4 运转, 保全 SKILL UP 训练 8. 造成新制品, 新设备的 初期管理体质 9. 组成成品质保全体制
3. TPM推进机构组织
4. TPM基本方针和
5. TPM展开
导入准备开始到实施 制定 Master Plan
TPM讲座
TPM概要
TOTAL Procuctive Maintenance
Agenda
1、何谓TPM 2、NPW的推进
何谓TPM・・・・・
TPM的历史
1950 事後保全 事后保全 Breakdown Maintenance
1960
1970
1980
预防保全时代 予防保全時代 Preventive Manitenance
生产保全时代 生産保全時代 Productive Maintenance
TPM 时代 TPM時代
Total Productive Maintenance
何谓TPM・・・・・
TPM的定义
①打造极限追求生产体系效率化(综合效率化)的 企业体质 ②以生产体系整个生命周期为对象, 在现场利用现物建立 “灾害0、不良0、故障0”等预防 所有损失的机制, ③现场、技术、管理等所有部门, ④从高层领导到一线员工的全体人员参加, ⑤以重复小集团的形式实现损失零。
同期生产 TQM JIT SQC GK(现场管理) TPM
全部门明确目的和作用,统一活动方向,切实推 动管理循环,以便登上更高层次
JIT・SQC・TPM → 排除浪费的工具
JIT:以物的流动为切入口的综合改善
SQC:专项问题的分析・解析
TPM:以设备可靠性为切入口的综合改善 GK(现场管理) →日产生产方式的基础
TPM
活动
计划保全 专项改善 人材培养 MP活动
Grow Up Meister计划 编制MP信息表
何谓TPM・・・・ 设备的预防医学
何谓自主保全・・・设备的预防 医学 各人的作用
如果把设备比喻为人 会是这样 设备・・・・婴儿・・・・即使不舒服也无法表达 作业员 ・・父母・・・・通过日常观察来观察设备身体状况 保全员 ・・医生・・・ ・听取父母说明判断身体情况
2、打造有价值的商品 以最小投入(费用)最为有效地运行设备,实现最佳的设备的 产出(Q、C、T)的费用效果比。
生産の3要素=投入資源 生产的3要素=投入资源 価値ある商品 有价值的商品
INPUT
1、人 1、人 2、もの 2、物料 3、設備 3、设备 → 生産活動 生产活动 →
OUTPUT
品質 (Q) 品质 納期 (D) 交期 (T)
保全预防
保证保全和修理等的便利性 CM・・・・ Corrective Maintenance 改良保全 故障发生前预防其发生 (1951年左右 自美国导入) PM・・・・ Preventive Maintenance
预防保全
事后保全
发生故障后修理 ( PM以前是保全主流方式) BM・・・・ Breakdown Maintenance
何谓TPM・・・・・
TPM的定义 (狭义)
①以达到最高设备效率(综合效率化)为目标, ②确立针对设备全寿命周期的PM综合体系, ③设备的规划部门・使用部门・保全部门等所有部门,
④从高层领导到一线员工全体人员参加, ⑤通过士气管理、即小集团自主活动推进PM。
何谓TPM・・・・・ 何谓保全
通过综合活动提高生产性,实现盈利的保全 (当前的主流) PM・・・・ Procuctive Maintenance 生产保全 从设计阶段即确保可维护性优良的设备 MP・・・・ Maintenance Prevention
(9)管理损失 (10)动作损失
作业损失 时间
编成损失 时间 不良损失 时间
净作业工时 运转时间 有效工时 纯运转时间
价值工时 价值 (生产时间) 运转时间
停止损失
(2) 准备调整损失 (3)刀具损失
清扫检查 等待指示 等待材料 等待工作 等待 确认质量 (调整测定)