五金冲压标准华为内部标准
五金冲压标准-华为内部标准
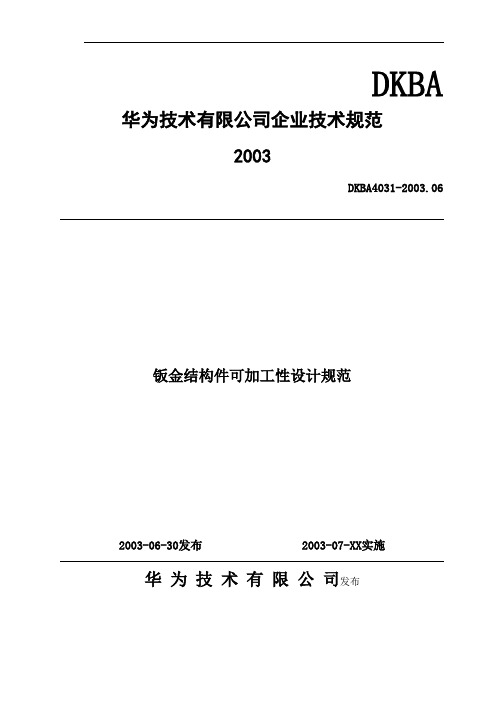
DKBA 华为技术有限公司企业技术规范2003DKBA4031-2003.06 钣金结构件可加工性设计规范2003-06-30发布2003-07-XX实施华为技术有限公司发布目次前言 (5)1范围和简介 (6)1.1范围 (6)1.2简介 (6)1.3关键词 (6)2规范性引用文件 (6)3冲裁 (6)3.1冲裁件的形状和尺寸尽可能简单对称,使排样时废料最少。
. 63.2冲裁件的外形及内孔应避免尖角。
(6)3.3冲裁件应避免窄长的悬臂与狭槽 (7)3.4冲孔优先选用圆形孔,冲孔有最小尺寸要求 (7)3.5冲裁的孔间距与孔边距 (8)3.6折弯件及拉深件冲孔时,其孔壁与直壁之间应保持一定的距离83.7螺钉、螺栓的过孔和沉头座 (8)3.8冲裁件毛刺的极限值及设计标注 (9)3.8.1冲裁件毛刺的极限值 (9)3.8.2设计图纸中毛刺的标注要求 (9)4折弯 (10)4.1折弯件的最小弯曲半径 (10)4.2弯曲件的直边高度 (10)4.2.1一般情况下的最小直边高度要求 (10)4.2.2特殊要求的直边高度 (11)4.2.3弯边侧边带有斜角的直边高度 (11)4.3折弯件上的孔边距 (11)4.4局部弯曲的工艺切口 (12)4.4.1折弯件的弯曲线应避开尺寸突变的位置 (12)4.4.2当孔位于折弯变形区内,所采取的切口形式 (12)4.5带斜边的折弯边应避开变形区 (13)4.6打死边的设计要求 (13)4.7设计时添加的工艺定位孔 (13)4.8标注弯曲件相关尺寸时,要考虑工艺性 (14)4.9弯曲件的回弹 (14)4.9.1折弯件的内圆角半径与板厚之比越大,回弹就越大。
.. 144.9.2从设计上抑制回弹的方法示例 (14)5拉伸 (15)5.1拉伸件底部与直壁之间的圆角半径大小要求 (15)5.2拉伸件凸缘与壁之间的圆角半径 (15)5.3圆形拉伸件的内腔直径 (15)5.4矩形拉伸件相邻两壁间的圆角半径 (15)5.5圆形无凸缘拉伸件一次成形时,其高度与直径的尺寸关系要求165.6拉伸件设计图纸上尺寸标注的注意事项 (16)5.6.1拉伸件产品尺寸的标准方法 (16)5.6.2拉伸件尺寸公差的标注方法 (16)6成形 (16)6.1加强筋 (17)6.2打凸间距和凸边距的极限尺寸 (17)6.3百叶窗 (17)6.4孔翻边 (18)7附录 (19)7.1附录A:高碳钢、低碳钢对应的公司常用材料牌号列表 (19)7.2附录B 压印工艺、压花工艺简介 (20)7.2.1压印工艺 (20)7.2.2压花工艺 (20)8参考文献 (21)前言本规范的其他系列规范:无与对应的国际标准或其他文件的一致性程度:无规范代替或作废的全部或部分其他文件:无与其他规范或文件的关系:无与规范前一版本相比的升级更改的内容:第一版,无升级更改信息。
五金冲压标准-华为内部标准
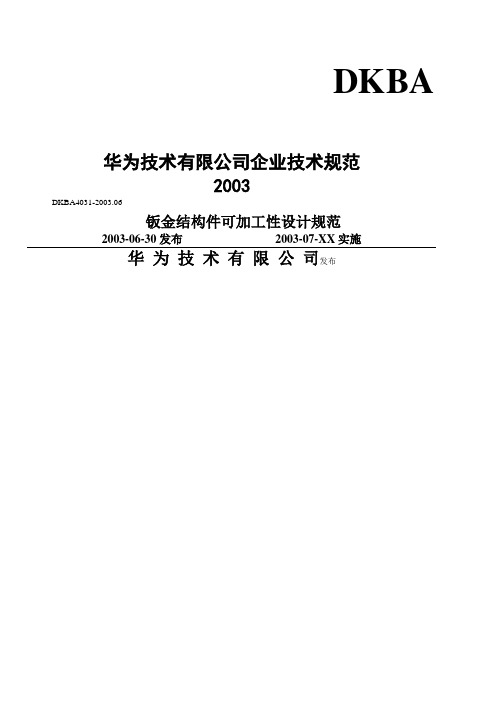
DKBA华为技术有限公司企业技术规范2003DKBA4031-2003.06钣金结构件可加工性设计规范2003-06-30发布2003-07-XX实施华为技术有限公司发布目次前言 .................................................................................................................................................................. 1范围和简介 .............................................................................................................................................1.1范围1.2简介1.3关键词2规范性引用文件...................................................................................................................................... 3冲裁 .........................................................................................................................................................3.1冲裁件的形状和尺寸尽可能简单对称,使排样时废料最少。
3.2冲裁件的外形及内孔应避免尖角。
3.3冲裁件应避免窄长的悬臂与狭槽3.4冲孔优先选用圆形孔,冲孔有最小尺寸要求3.5冲裁的孔间距与孔边距3.6折弯件及拉深件冲孔时,其孔壁与直壁之间应保持一定的距离3.7螺钉、螺栓的过孔和沉头座3.8冲裁件毛刺的极限值及设计标注3.8.1冲裁件毛刺的极限值....................................................................................3.8.2设计图纸中毛刺的标注要求........................................................................ 4折弯 .........................................................................................................................................................4.1折弯件的最小弯曲半径4.2弯曲件的直边高度4.2.1一般情况下的最小直边高度要求 ................................................................4.2.2特殊要求的直边高度....................................................................................4.2.3弯边侧边带有斜角的直边高度 ....................................................................4.3折弯件上的孔边距4.4局部弯曲的工艺切口4.4.1折弯件的弯曲线应避开尺寸突变的位置 ....................................................4.4.2当孔位于折弯变形区内,所采取的切口形式 ............................................4.5带斜边的折弯边应避开变形区4.6打死边的设计要求4.7设计时添加的工艺定位孔4.8标注弯曲件相关尺寸时,要考虑工艺性4.9弯曲件的回弹4.9.1折弯件的内圆角半径与板厚之比越大,回弹就越大。
五金冲压品检验标准

4.抽样依据﹕
4.1依抽样计划表的正常抽样﹐且AQL﹕CR=0,Maj=0.65%﹔Min=1.5%。
4.2若客户有要求时﹐则依客户的要求抽样检验。
5.检验级域的定义
5.1A面﹕消费者使用操作时﹐必须看到的面﹐如产品的正面或组件的外露正面。
材料下料是否造成形状变形
1.平台
2.塞规
3.电镀/烤漆﹕电镀/烤漆表面不允许露底材﹐起泡﹑剥落等现象﹐包含内装件。
电镀表面有无电镀不良
目视
天久电子有限公司
文件编号
版本
A0
类别
五金冲压成品检验标准
制定日期
规范
页次
1/3
检验项目
检验规格(内容)
检验重点
使用量测
仪器
判定水准
CR
MAJ
MIN
4.锈斑﹕表面不可有任何锈斑包含内装件。
5.2B面﹕消费者使用操作时﹐偶尔看到的面﹐如产品的上下面或组件的上下面。
5.3C面﹕消费者使用操作时﹐不易看到的面﹐如组件的面或单件的凹陷处。
5.4D面﹕消费者使用操作时﹐不能看到的面﹐如组件的内面或单件的背面。
6.检测工具﹕卡尺﹑针规﹑投影机
7.检验项目﹕
检验项目
检验规格(内容)
检验重点
使用量测
天久电子有限公司
文件编号
版本
A0
类别
五金冲压成品检验标准
制定日期
规范
页次
1/3
1.目的:
为了确保出货后之产品质量达到客户满意度﹐并提高公司之信誉。
2.适用范围
公司内所有五金冲压产品。
3.定义:
钣金冲压件质量要求

DKBA 华为技术有限公司内部技术规范DKBA0.450.0040 REV C钣金冲压件质量要求Specification For Sheet-metalPunching Part2012年07月30日发布 20012年09月1日实施华为技术有限公司Huawei Technologies Co., Ltd.版权所有侵权必究All rights reserved修订声明Revision declaration 本规范拟制与解释部门:整机工程部基础平台部本规范的相关系列规范或文件:无相关国际规范或文件一致性:无替代或作废的其它规范或文件:无相关规范或文件的相互关系:无目录1.技术要求 (7)1.1.外观及表面状态一般要求 (7)1.1.1.零件的毛刺面朝向要求 (7)1.1.2.冲裁类平板零件圆角要求 (7)1.1.3.零件上止裂孔、工艺槽要求 (7)1.1.4.弯曲零件未注圆角R要求 (8)1.1.5.翻边攻丝质量要求 (8)1.1.6.自铆质量要求 (10)1.1.7.零件表面的外观要求 (11)1.2.钣金冲压件毛刺的要求 (11)1.2.1.毛刺的高度定义 (11)1.2.2.结构件的毛刺区域分类 (11)1.2.3.钣金冲压件毛刺质量要求 (15)1.2.4.钣金冲压件的熔渣要求 (16)1.2.5.钣金冲压件的接刀痕的要求 (16)1.3.钣金冲压件公差要求 (16)1.3.1.公差要求 (16)1.3.2.钣金件冲压公差等级代号及数值 (17)1.3.3.其它说明 (21)2.检验规则 (22)2.1.检验类别 (22)2.1.1.一般检验 (22)2.1.2.补充检验 (22)2.2.检验原则 (22)2.3.检验规定 (22)图目录图 1 折弯件毛刺方向示意图 (7)图 2 平板件的尖角示意图 (7)图 3 止裂孔直径示意图 (8)图 4 工艺槽口示意图 (8)图 5 翻边攻丝示意图 (9)图 6 薄板连接用带锥台翻边攻丝孔结构示意图 (9)图 7 自铆连接示意图 (10)图 8 钣金件毛刺示意图 (11)图 9 户外机柜类A、B类区域判断示意图 (13)图 10 室内机柜类A、B类区域判断示意图 (14)图 11 插箱类A、B类区域判断示意图 (14)图 12 拉手条及面板等小五金类A、B类区域判断示意图 (15)图 13 盒式类A、B类区域判断示意图 (15)图 14 倒角高度示意图 (16)表目录表 1 平板件圆角半径r值 (7)表 2 普通翻边高度H值和螺纹最少反复打入次数 (9)表 3 薄板连接用带锥台翻边攻丝孔翻边高度H值和螺纹最少反复打入次数 (9)表 4 自铆参数表 (10)表 5 自铆连接点最小承力表 (10)表 6 毛刺高度的极限值 (15)表 7 钣金公差数值表 (17)钣金冲压件质量要求Specification For Sheet-metal Punching Part范围Scope:本规范规定了华为的钣金冲压件(表面处理前)的质量要求、检验规则。
华为标准

(例如对于人的皮肤)时引起,并在相邻
导体间有放电火花通过。当带有静电荷势
能的人触摸PCBA时就会静电放电。当静
电放电经由导体图形到达对静电敏感的元
器件里时,元器件、PCBA就会有损伤。
即使静电放电低到使人感觉不到时(低于
3500V),对于ESDS元器件仍有损害。
某些易受到EOS/ESD损害的元器件
敏感度的大致范围详见表1-1。
3.0 元器件安装的位置和方向 3.1 方向 3.1.1 水平 3.1.2 垂直 3.2 安装 3.2.1 轴向引线元器件水平安装
3.2.2 径向引线元器件水平安装 3.2.3 轴向引线元器件垂直安装 3.2.4 径向引线元器件垂直安装 3.2.5 双列直插封装 3.2.5.1 双列直插封装和单列直插封装插座 3.2.6 卡式板边连接器 3.2.7 引脚跨越导体 3.2.8 应力释放 3.2.8.1 端子--轴向引线元器件 3.3 引脚成型 3.4 损伤 3.4.1 引脚 3.4.2 DIPS 和SOIC 3.4.3 轴向引线元器件 3.4.3.1 玻璃体 3.4.4 径向(双引脚) 3.5 导线/引脚端头 3.5.1 端子 3.5.1.1 缠绕量 3.5.1.3 引脚/导线弯曲应力的释放 3.5.1.4 引脚/导线安装 3.5.2 导线/引脚端头--导线安装 3.5.2.1 绝缘间距 3.5.2.2 绝缘损伤 3.5.2.3 导体变形 3.5.2.4 导体损伤 3.5.3 印制板--导线伸出量 3.5.4 软性套管绝缘
焊盘宽度
检验用
>0.5mm 1.75X-4X
0.25~0.5mm
10X
<0.25mm
20X
仲裁用 10X 20X 30X
仲裁情况只应该用于鉴定检验中不合 格的产品。对使用了各式各样焊盘宽度的 PCBA,可以使用较大放大倍数检验整个 PCBA。
华为技术有限公司内部技术规范--金属材料质量要求

DKBA 华为技术有限公司内部技术规范DKBA0.400.0114 REV.1.0金属材料质量要求Requirement for the metal material修订声明Revision declaration 本规范拟制与解释部门:整机工程部结构造型设计部本规范的相关系列规范或文件:无相关国际规范或文件一致性:无替代或作废的其它规范或文件:无相关规范或文件的相互关系:无目录Table of Contents1规定的材料81.1材料牌号及化学成份81.2材料的机械性能91.2.1基本力学性能91.2.2工艺性111.3对预镀钢板的特殊要求111.3.1表面镀层厚度及表面处理方式111.3.2表面外观质量111.3.3镀层附着性试验121.3.4表面耐蚀性121.3.5表面接触电阻131.3.6与有机涂层的结合力132替代材料133附录:预镀钢板外观花纹图片154参考文献REFERENCE DOCUMENT 16表目录List of Tables 表1 钢材牌号及化学化学成份8表2 材料力学性能要求10表3 替代材料表13图目录List of Figures 图1 耐指纹电镀锌钢板:均匀的灰色15图2 热镀铝锌板:小晶花15图3 热浸镀锌板:大晶花16图4 热浸镀锌板(GI料):无晶花、但有锌纹16金属材料质量要求Requirement for the metal material范围Scope:本规范规定了华为技术有限公司结构产品所用到的金属材料的质量要求。
本规范适用于华为技术有限公司结构产品的设计、生产、和质量检验。
简介Brief introduction:本文说明了华为技术有限公司结构产品中所用到的所有金属原材料的种类以及每种材料的详细质量指标要求、检测方法和质量控制要求。
包括材料牌号、化学成份、强度等等项目。
本文所提到的压铸材料仅是指压铸加工用的原材料,对于压铸件产品的质量请参见其它规范。
五金冲压件技术要求标准

五金冲压件技术要求标准一、引言五金冲压件是制造业中常见的零部件,广泛应用于汽车、航空航天、家电、机械设备等行业。
为了保证五金冲压件的质量和性能,制定了一系列的技术要求标准,从材料选取、工艺流程、设备要求等方面进行规范。
二、材料要求1. 材料选择:五金冲压件的材料应符合相关国家标准,如GB/T 1220、GB/T 3077等。
应根据零部件的使用环境和要求选择适当的材料,包括钢材、铝合金、铜合金等。
2. 材料性能:五金冲压件材料应具有良好的机械性能,包括强度、硬度、塑性等指标。
应对材料进行严格的化学成分检测和力学性能测试。
3. 表面处理:对五金冲压件的表面进行防锈、防腐、涂装等处理,以保证产品的表面质量和使用寿命。
三、工艺流程要求1. 冲压工艺:应根据产品的结构和要求确定合理的冲压工艺,包括模具设计、模具加工、成型工艺参数的选择等。
2. 成型精度:五金冲压件的成型精度应符合相关标准要求,包括尺寸精度、形位公差、表面质量等。
3. 工艺控制:对冲压工艺进行严格的控制和检测,确保产品的质量稳定和一致性。
四、设备要求1. 冲压设备:应选用先进的数控冲床、冲压机等设备,确保产品的生产效率和质量。
2. 模具设备:应具备高精度、高耐磨的模具加工设备,保证模具的精度和寿命。
3. 检测设备:应配置相应的检测设备,包括三坐标测量机、硬度计、拉力试验机等,对产品进行全面的检测。
五、质量控制要求1. 品质管理体系:应建立完善的品质管理体系,包括从材料采购、工艺控制、产品检测等各个环节的管理和控制。
2. 出厂检验标准:制定五金冲压件的出厂检验标准,包括外观检验、尺寸检验、力学性能检验等。
3. 不良品处理:建立完善的不良品处理流程,及时发现和处理不合格品,保证产品的合格率和稳定性。
六、环保要求1. 废水、废气处理:五金冲压件生产过程中应注意废水、废气的处理,达到环保要求。
2. 资源利用:在生产过程中应尽量节约资源,减少能源消耗和废弃物产生。
五金冲压员工考核制度范本

第一章总则第一条为规范五金冲压生产员工的考核工作,提高员工的工作效率和质量,激发员工的工作积极性,特制定本制度。
第二条本制度适用于公司所有五金冲压生产岗位的员工。
第三条考核工作应遵循公平、公正、公开的原则,以员工的工作表现、技能水平和工作态度为主要考核内容。
第二章考核内容第四条考核分为以下几个方面:1. 工作质量:考核员工完成生产任务的质量,包括产品尺寸精度、表面质量、材料消耗等。
2. 工作效率:考核员工完成生产任务的速度,包括生产节拍、设备利用率等。
3. 安全生产:考核员工在生产过程中遵守安全操作规程的情况,包括设备维护、个人防护等。
4. 培训学习:考核员工参加培训、学习的情况,包括专业技能、安全知识等。
5. 团队协作:考核员工在团队中的协作能力,包括沟通、配合等。
6. 工作态度:考核员工的工作态度,包括责任心、主动性、积极性等。
第三章考核方法第五条考核方法分为以下几种:1. 日常考核:由生产组长根据员工日常表现进行考核,每周进行一次。
2. 专项考核:针对特定项目或事件进行考核,如新产品试制、技术改造等。
3. 定期考核:每月底进行一次月度考核,年度末进行一次年度考核。
第四章考核标准第六条考核标准分为优秀、良好、合格、不合格四个等级。
1. 优秀:各项考核指标均达到优秀水平,具有较强的责任心、主动性和创新能力。
2. 良好:各项考核指标基本达到要求,工作态度良好,能积极完成生产任务。
3. 合格:各项考核指标基本达到要求,但存在一定不足,需加强改进。
4. 不合格:各项考核指标未达到要求,工作态度不端正,影响生产进度和质量。
第五章奖惩措施第七条对考核优秀的员工,给予一定的物质奖励和精神鼓励,如晋升、加薪等。
第八条对考核不合格的员工,进行批评教育,并采取相应的改进措施。
情节严重的,予以降职、辞退等处理。
第六章附则第九条本制度由公司人力资源部负责解释和修订。
第十条本制度自发布之日起施行。
五金冲压员工考核制度范本到此结束。
钣金冲压件质量要求
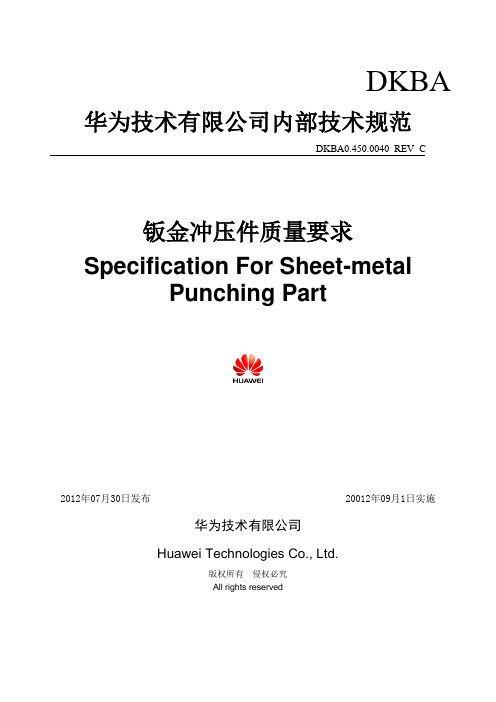
DKBA 华为技术有限公司内部技术规范DKBA0.450.0040 REV C钣金冲压件质量要求Specification For Sheet-metalPunching Part2012年07月30日发布 20012年09月1日实施华为技术有限公司Huawei Technologies Co., Ltd.版权所有侵权必究All rights reserved修订声明Revision declaration 本规范拟制与解释部门:整机工程部基础平台部本规范的相关系列规范或文件:无相关国际规范或文件一致性:无替代或作废的其它规范或文件:无相关规范或文件的相互关系:无规范号主要起草部门专家主要评审部门专家修订情况DKBA0.450.0040 REV C 基础平台部:潘建军(00118387)肖春秀(00053994) 整机工程部:郭天次(0014571)许志敏(00114402),黄涛(00121968)张实(00118600),钟宏辉(00121959),张润孝(00049797)MQE:陈亮(00068994)SQE:王进(00151357)1、增加了自铆质量要求;2、刷新了钣金件公差要求。
DKBA0.450.0040 REV B 质量成本管理部:肖春秀53994 整机工程部:周伟 00123276,郑玲 00119690李俊周 00123308,魏华 00102167杨曦晨 00152131,和永超57041MQE:曾松来00125372TQC:马宝兴39736CEG:郑连东 001149491、将外观表面的定义引用于DKBA0.400.00212、增加了翻边攻丝的质量要求;DKBA0.450.0040 REV1.0 质量成本管理部:肖春秀53994 质量成本管理部:盛辉21628、周伟16271结构平台开发部:郑玲15593MQE:陈军17658TQC:马宝兴39736新归档目录1.技术要求 (6)1.1.外观及表面状态一般要求 (6)1.1.1.零件的毛刺面朝向要求 (6)1.1.2.冲裁类平板零件圆角要求 (6)1.1.3.零件上止裂孔、工艺槽要求 (7)1.1.4.弯曲零件未注圆角R要求 (7)1.1.5.翻边攻丝质量要求 (8)1.1.6.自铆质量要求 (9)1.1.7.零件表面的外观要求 (10)1.2.钣金冲压件毛刺的要求 (10)1.2.1.毛刺的高度定义 (10)1.2.2.结构件的毛刺区域分类 (10)1.2.3.钣金冲压件毛刺质量要求 (14)1.2.4.钣金冲压件的熔渣要求 (15)1.2.5.钣金冲压件的接刀痕的要求 (15)1.3.钣金冲压件公差要求 (15)1.3.1.公差要求 (15)1.3.2.钣金件冲压公差等级代号及数值 (16)1.3.3.其它说明 (20)2.检验规则 (22)2.1.检验类别 (22)2.1.1.一般检验 (22)2.1.2.补充检验 (22)2.2.检验原则 (22)2.3.检验规定 (22)图目录图 1 折弯件毛刺方向示意图 (6)图 2 平板件的尖角示意图 (6)图 3 止裂孔直径示意图 (7)图 4 工艺槽口示意图 (7)图 5 翻边攻丝示意图 (8)图 6 薄板连接用带锥台翻边攻丝孔结构示意图 (8)图 7 自铆连接示意图 (9)图 8 钣金件毛刺示意图 (10)图 9 户外机柜类A、B类区域判断示意图 (12)图 10 室内机柜类A、B类区域判断示意图 (13)图 11 插箱类A、B类区域判断示意图 (13)图 12 拉手条及面板等小五金类A、B类区域判断示意图 (14)图 13 盒式类A、B类区域判断示意图 (14)图 14 倒角高度示意图 (15)表目录表 1 平板件圆角半径r值 (6)表 2 普通翻边高度H值和螺纹最少反复打入次数 (8)表 3 薄板连接用带锥台翻边攻丝孔翻边高度H值和螺纹最少反复打入次数 (9)表 4 自铆参数表 (9)表 5 自铆连接点最小承力表 (9)表 6 毛刺高度的极限值 (15)表 7 钣金公差数值表 (16)钣金冲压件质量要求Specification For Sheet-metal Punching Part范围Scope:本规范规定了华为的钣金冲压件(表面处理前)的质量要求、检验规则。
华为技术有限公司内部技术规范--金属材料质量要求

DKBA 华为技术有限公司内部技术规范DKBA0.400.0114 REV.1.0金属材料质量要求Requirement for the metal material修订声明Revision declaration 本规范拟制与解释部门:整机工程部结构造型设计部本规范的相关系列规范或文件:无相关国际规范或文件一致性:无替代或作废的其它规范或文件:无相关规范或文件的相互关系:无目录Table of Contents1规定的材料81.1材料牌号及化学成份81.2材料的机械性能91.2.1基本力学性能91.2.2工艺性111.3对预镀钢板的特殊要求111.3.1表面镀层厚度及表面处理方式111.3.2表面外观质量111.3.3镀层附着性试验121.3.4表面耐蚀性121.3.5表面接触电阻131.3.6与有机涂层的结合力132替代材料133附录:预镀钢板外观花纹图片154参考文献REFERENCE DOCUMENT 16表目录List of Tables 表1 钢材牌号及化学化学成份8表2 材料力学性能要求10表3 替代材料表13图目录List of Figures 图1 耐指纹电镀锌钢板:均匀的灰色15图2 热镀铝锌板:小晶花15图3 热浸镀锌板:大晶花16图4 热浸镀锌板(GI料):无晶花、但有锌纹16金属材料质量要求Requirement for the metal material范围Scope:本规范规定了华为技术有限公司结构产品所用到的金属材料的质量要求。
本规范适用于华为技术有限公司结构产品的设计、生产、和质量检验。
简介Brief introduction:本文说明了华为技术有限公司结构产品中所用到的所有金属原材料的种类以及每种材料的详细质量指标要求、检测方法和质量控制要求。
包括材料牌号、化学成份、强度等等项目。
本文所提到的压铸材料仅是指压铸加工用的原材料,对于压铸件产品的质量请参见其它规范。
五金冲压标准华为内部标准

五金冲压标准华为内部标准公司内部档案编码:[OPPTR-OPPT28-OPPTL98-OPPNN08]DKBA华为技术有限公司企业技术规范2003钣金结构件可加工性设计规范2003-06-30发布2003-07-XX实施华为技术有限公司发布目次前言.........................................................1 范围和简介....................................................范围..............................................简介..............................................关键词............................................2 规范性引用文件................................................3 冲裁..........................................................冲裁件的形状和尺寸尽可能简单对称,使排样时废料最少。
冲裁件的外形及内孔应避免尖角。
....................冲裁件应避免窄长的悬臂与狭槽......................冲孔优先选用圆形孔,冲孔有最小尺寸要求............冲裁的孔间距与孔边距..............................折弯件及拉深件冲孔时,其孔壁与直壁之间应保持一定的距离螺钉、螺栓的过孔和沉头座..........................冲裁件毛刺的极限值及设计标注......................冲裁件毛刺的极限值............................设计图纸中毛刺的标注要求......................4 折弯..........................................................折弯件的最小弯曲半径..............................弯曲件的直边高度..................................一般情况下的最小直边高度要求..................特殊要求的直边高度............................弯边侧边带有斜角的直边高度....................折弯件上的孔边距..................................局部弯曲的工艺切口................................折弯件的弯曲线应避开尺寸突变的位置............当孔位于折弯变形区内,所采取的切口形式........带斜边的折弯边应避开变形区........................打死边的设计要求..................................设计时添加的工艺定位孔............................标注弯曲件相关尺寸时,要考虑工艺性................弯曲件的回弹......................................折弯件的内圆角半径与板厚之比越大,回弹就越大。
五金冲压件技术要求标准

五金冲压件技术要求标准五金冲压件作为一种常见的零部件,广泛应用于汽车、家电、机械设备等各个领域,因此其技术要求标准显得尤为重要。
下面就五金冲压件的技术要求标准进行详细的阐述。
一、原材料选择五金冲压件的原材料选择对其质量起着决定性作用。
通常情况下,五金冲压件所选用的原材料应具有良好的塑性变形能力和焊接性能,能够满足强度要求,并具有良好的表面质量。
常见的五金冲压件原材料包括冷轧钢板、镀锌钢板、不锈钢板、铝合金板等。
在原材料的选择上,应根据产品的具体使用场景和要求来合理选择,以确保产品性能的稳定性和可靠性。
二、冲压工艺要求1.模具设计:五金冲压件的模具设计应考虑到冲压件的结构、尺寸精度、表面质量等因素,确保产品的一致性和稳定性。
2.冲压设备:应配备高精度、高稳定性的冲床设备,并保持设备的良好状态,确保冲压速度、压力等参数符合要求。
3.冲压工艺控制:应建立冲压工艺流程并进行严格控制,包括送料、定位、冲压、脱模等工序均应符合要求,以确保产品的尺寸精度和表面质量。
4.件型结构:五金冲压件的结构设计应合理,以确保产品的安装和使用性能,避免因工艺导致的变形或断裂等缺陷。
5.材料回弹控制:在冲压过程中要合理控制材料的回弹变形,确保产品尺寸精度和表面要求。
三、表面处理要求五金冲压件在生产过程中往往需要进行表面处理,以满足不同的使用要求。
常见的表面处理工艺包括镀锌、喷涂、电镀等。
在表面处理过程中,应确保处理层的厚度、附着力、耐腐蚀性等指标满足产品的要求。
四、质量检测要求1.尺寸检测:应建立尺寸检测标准,采用高精度的检测设备进行尺寸检测,确保产品的尺寸精度。
2.表面质量检测:应建立表面质量标准,采用目视、手感等方式对产品表面进行检测,并可借助检测仪器进行表面粗糙度、平整度等指标的检测。
3.力学性能检测:对五金冲压件的拉伸强度、屈服强度、延伸率等力学性能进行检测,以确保产品的使用性能。
4.包装运输:应建立包装标准,并对产品包装进行检测,以确保产品在运输过程中不受损。
五金冲压件技术要求标准
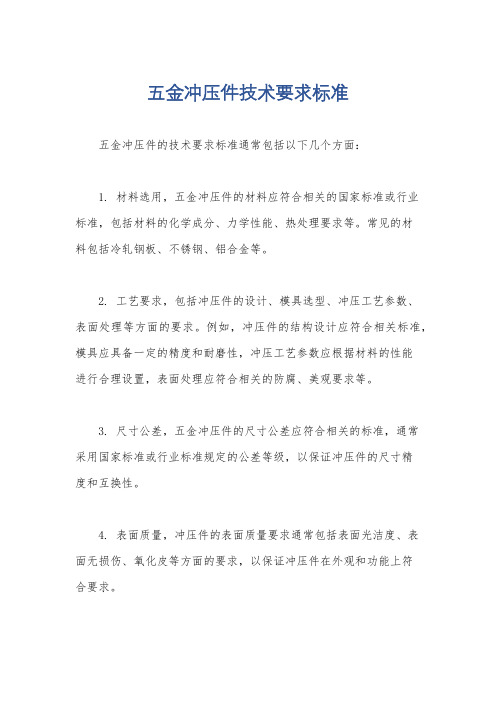
五金冲压件技术要求标准
五金冲压件的技术要求标准通常包括以下几个方面:
1. 材料选用,五金冲压件的材料应符合相关的国家标准或行业
标准,包括材料的化学成分、力学性能、热处理要求等。
常见的材
料包括冷轧钢板、不锈钢、铝合金等。
2. 工艺要求,包括冲压件的设计、模具选型、冲压工艺参数、
表面处理等方面的要求。
例如,冲压件的结构设计应符合相关标准,模具应具备一定的精度和耐磨性,冲压工艺参数应根据材料的性能
进行合理设置,表面处理应符合相关的防腐、美观要求等。
3. 尺寸公差,五金冲压件的尺寸公差应符合相关的标准,通常
采用国家标准或行业标准规定的公差等级,以保证冲压件的尺寸精
度和互换性。
4. 表面质量,冲压件的表面质量要求通常包括表面光洁度、表
面无损伤、氧化皮等方面的要求,以保证冲压件在外观和功能上符
合要求。
5. 检测要求,冲压件的检测通常包括外观检查、尺寸检测、材料性能检测等,要求符合相关的检测标准,以保证冲压件的质量。
总的来说,五金冲压件的技术要求标准是为了保证冲压件的质量、性能和可靠性,同时也是为了满足客户的需求和相关的法律法规要求。
具体的要求会根据不同的产品、行业和国家而有所不同。
钣金冲压件质量要求

DKBA华为技术有限公司内部技术规范DKBA0.450.0040 REV C钣金冲压件质量要求Specification For Sheet-metalPunching Part2012年07月30日发布 20012年09月1日实施华为技术有限公司Huawei T echnologies C o.,L td.版权所有侵权必究All r ights r eserved修订声明Revision d eclaration 本规范拟制与解释部门:整机工程部基础平台部本规范的相关系列规范或文件:无相关国际规范或文件一致性:无替代或作废的其它规范或文件:无相关规范或文件的相互关系:无目录1.技术要求 (7)1.1.外观及表面状态一般要求 (7)1.1.1.零件的毛刺面朝向要求 (7)1.1.2.冲裁类平板零件圆角要求 (8)1.1.3.零件上止裂孔、工艺槽要求 (8)1.1.4.弯曲零件未注圆角R要求 (9)1.1.5.翻边攻丝质量要求 (9)1.1.6.自铆质量要求 (10)1.1.7.零件表面的外观要求 (11)1.2.钣金冲压件毛刺的要求 (11)1.2.1.毛刺的高度定义 (11)1.2.2.结构件的毛刺区域分类 (11)1.2.3.钣金冲压件毛刺质量要求 (15)1.2.4.钣金冲压件的熔渣要求 (16)1.2.5.钣金冲压件的接刀痕的要求 (16)1.3.钣金冲压件公差要求 (16)1.3.1.公差要求 (16)1.3.2.钣金件冲压公差等级代号及数值 (17)1.3.3.其它说明 (21)2.检验规则 (22)2.1.检验类别 (22)2.1.1.一般检验 (22)2.1.2.补充检验 (22)2.2.检验原则 (22)2.3.检验规定 (22)1.TECHNICAL R EQUIREMENTS (28)1.1.G ENERAL R EQUIREMENTS F OR A PPEARANCE A ND S URFACE (28)1.1.1.The b urr s urface i s r equired t o b e i nside t he p arts,a s s hown i n E rror! R eference s ource n ot f ound.: (28)1.1.2.Blanked a nd s heared p anel p arts’t aper a ngles w ith o ut er s hapes a nd i nner e dges s maller t han o r e qual t o 90°w hich a re n ot n oted o n t he d rawing s hould b e m ade a s f illets (as s hown i n F igure 2) w ith a r adius (r) s pecified a sTable 1. 281.1.3.If a llowable a s m arked i n d esign d ocuments o r d rawings,s top h oles o r t echnical r abbets c an b e o pen a ccording t o t he f ollowing h ole d iameter a nd r abbet s ize (28)1.1.4.Parts f ormed b y c urving w ithout a c urving r adius n oted o n t he d rawing c an b e m ade w ith a n i nternally c urving r adius R n o l arger t han t(thickness o f m aterials) a nd n o s maller t han 0.2. (29)1.1.5.Requirements f or f langing-hole w ith t hread: (29)1.1.6.Requirements f or R iveting Q uality (31)1.1.7.Exterior R equirements o f p arts (32)1.2.R EQUIREMENTS F OR T HE B URR O F S HEET-M ETAL P UNCHING P ARTS (32)1.2.1.Definition o f B urr H eight: (32)1.2.2.Classifications o f b urr a reas o f s tructural p arts (32)1.2.3.Requirements f or t he b urr q uality o f s heet-metal p unching p arts (36)1.2.4.Requirements f or t he S lag o f S heet-Metal P unching P arts (37)1.2.5.Requirements f or T ool W ithdrawal M arks o n S heet-Metal P unching P arts (37)1.3.T OLERANCE R EQUIREMENTS O F S HEET-METAL P UNCHING P ARTS (38)1.3.1.Statement (38)1、T OLERANCES I N D RAWINGS,I F S PECIFIED,S HALL A LWAYS P REVAIL (38)1.3.2.Tolerance L evels a nd V alues (38)Tolerance l evels a re c lassified i nto f a nd m. f a llows l ower t olerances t han m. (38)1.3.3.Remarks (42)2.INSPECTION R ULE (43)2.1.I NSPECTION C ATEGORY (43)2.1.1.General I nspection (43)2.1.2.Supplementary I nspection (43)2.2.I NSPECTION R ULES (43)2.3.I NSPECTION P ROVISIONS (43)图目录图 1 折弯件毛刺方向示意图 (7)图 2 平板件的尖角示意图 (8)图 3 止裂孔直径示意图 (8)图 4 工艺槽口示意图 (9)图 5 翻边攻丝示意图 (9)图 6 薄板连接用带锥台翻边攻丝孔结构示意图 (10)图 7 自铆连接示意图 (11)图 8 钣金件毛刺示意图 (11)图 9 户外机柜类A、B类区域判断示意图 (13)图 10 室内机柜类A、B类区域判断示意图 (14)图 11 插箱类A、B类区域判断示意图 (14)图 12 拉手条及面板等小五金类A、B类区域判断示意图 (15)图 13 盒式类A、B类区域判断示意图 (15)图 14 倒角高度示意图 (16)表目录表 1 平板件圆角半径r值 (8)表 2 普通翻边高度H值和螺纹最少反复打入次数 (9)表 3 薄板连接用带锥台翻边攻丝孔翻边高度H值和螺纹最少反复打入次数 (10)表 4 自铆参数表 (10)表 5 自铆连接点最小承力表 (11)表 6 毛刺高度的极限值 (15)表 7 钣金公差数值表 (17)钣金冲压件质量要求Specification F or S heet-metal P unching P art范围Scope:本规范规定了华为的钣金冲压件(表面处理前)的质量要求、检验规则。
华为技术规范汇总
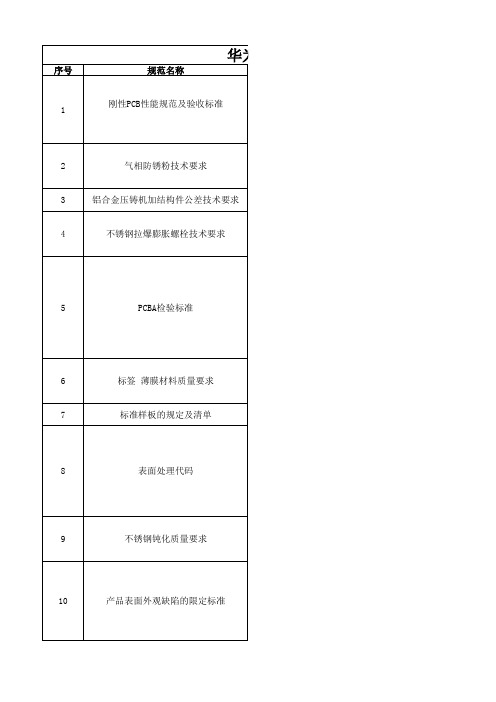
华为企业技术标准
主要内容 1、本标准规定了刚性PCB可能遇到的各种与可组装性、可靠 性有关的事项及性能检验标准。 2、对刚性PCB的相关要求做了详细的规定,包括外观、内在 特性、可靠性等,以及常规测试和结构完整性试验要求。 3、本标准适用于华为公司刚性PCB的进货检验,采购合同中 的技术条文、PCB厂家资格认证以及刚性PCB的设计参考。 气相防锈粉是一种能自动不断挥发充盈密封包装空间,甚至 孔、缝而对金属起保护作用的气相防腐蚀粉状材料。本规范 明确了此种材料的成分、防锈期限、产品规格、物料包装方 式及其包装材料、标识等等要求。 本规范规定了铝合金压铸、机械加工结构件的尺寸公差等级 及公差数值。锌合金压铸件可以参考。 1、不锈钢拉爆膨胀螺栓用于户外设备在墙体或水泥基础上 安装,适合于I型结构件在B类、C类环境下使用。2、本标准 规定了华为技术有限公司产品所用不锈钢拉爆膨胀螺栓的技 术要求。 Q/DKBA3200.1 PCBA检验标准 第一部分 SMT焊点; Q/DKBA3200.2 PCBA检验标准 第二部分 THT焊点; Q/DKBA3200.3 PCBA检验标准 第三部分 压接件; Q/DKBA3200.4 PCBA检验标准 第四部分 清洁度; Q/DKBA3200.5 PCBA检验标准 第五部分 标记; Q/DKBA3200.7 PCBA检验标准 第七部分 板材; Q/DKBA3200.8 PCBA检验标准 第八部分 跨接线; Q/DKBA3200.9 PCBA检验标准 第九部分 结构件。 1、本规范规定了结构件、电缆、包装件上粘贴使用的标签 和薄膜材料的质量性能要求。2、本规范详细规定了标签和 薄膜材料的质量要求,包括材质成份、外观颜色、粘接强度 、耐温性能、抗紫外光性能、UL认证要求、阻燃要求等。 本文件用于指导产品设计、生产及其产品生产过程中的质量 检验;供应商来料验收的抽检比例可按其它相关文件执行。 本规范规定了结构件图纸中标注表面处理时所用的代码内 容,并说明了每种工艺所对应的技术要求以及每种外观要求 应采用的标准样板。 本规范适用于华为技术有限公司结构产品的零件和组合件图 纸设计。 本文件是图纸设计时表面处理标注的选用依据。本文也可作 为选择外协加工厂以及确定加工成本的参考。 1.1 本规范规定了基体材料为不锈钢的工件进行钝化处理的 工艺要求及其质量要求。 1.2 本规范适用于不锈钢钝化工 艺评审和批生产质量检验。本文规定了不锈钢钝化的工艺鉴 定要求和批生产检验要求,包括钝化膜的外观、耐蚀性等。 本文规定了产品中结构件的表面等级划分及其外观质量要求 。 本文适用于华为技术有限公司产品的装配生产及结构件验 收;也可用于指导设计。 外购件的验收同样适用本标准。当某外购件不属于华为公司 专用型号时,也可按供应商的质 量标准对其进行验收,具体要求应参照相应外购件的技术说 备注
钣金冲压件质量要求

DKBA 华为技术有限公司内部技术规范DKBA0.450.0040 REV C钣金冲压件质量要求Specification For Sheet-metalPunching Part2012年07月30日发布 20012年09月1日实施华为技术有限公司Huawei Technologies Co., Ltd.版权所有侵权必究All rights reserved修订声明Revision declaration 本规范拟制与解释部门:整机工程部基础平台部本规范的相关系列规范或文件:无相关国际规范或文件一致性:无替代或作废的其它规范或文件:无相关规范或文件的相互关系:无目录1.技术要求 (7)1.1.外观及表面状态一般要求 (7)1.1.1.零件的毛刺面朝向要求 (7)1.1.2.冲裁类平板零件圆角要求 (7)1.1.3.零件上止裂孔、工艺槽要求 (7)1.1.4.弯曲零件未注圆角R要求 (8)1.1.5.翻边攻丝质量要求 (8)1.1.6.自铆质量要求 (10)1.1.7.零件表面的外观要求 (11)1.2.钣金冲压件毛刺的要求 (11)1.2.1.毛刺的高度定义 (11)1.2.2.结构件的毛刺区域分类 (11)1.2.3.钣金冲压件毛刺质量要求 (15)1.2.4.钣金冲压件的熔渣要求 (16)1.2.5.钣金冲压件的接刀痕的要求 (16)1.3.钣金冲压件公差要求 (16)1.3.1.公差要求 (16)1.3.2.钣金件冲压公差等级代号及数值 (17)1.3.3.其它说明 (20)2.检验规则 (22)2.1.检验类别 (22)2.1.1.一般检验 (22)2.1.2.补充检验 (22)2.2.检验原则 (22)2.3.检验规定 (22)图目录图 1 折弯件毛刺方向示意图 (7)图 2 平板件的尖角示意图 (7)图 3 止裂孔直径示意图 (8)图 4 工艺槽口示意图 (8)图 5 翻边攻丝示意图 (9)图 6 薄板连接用带锥台翻边攻丝孔结构示意图 (9)图 7 自铆连接示意图 (10)图 8 钣金件毛刺示意图 (11)图 9 户外机柜类A、B类区域判断示意图 (13)图 10 室内机柜类A、B类区域判断示意图 (14)图 11 插箱类A、B类区域判断示意图 (14)图 12 拉手条及面板等小五金类A、B类区域判断示意图 (15)图 13 盒式类A、B类区域判断示意图 (15)图 14 倒角高度示意图 (16)表目录表 1 平板件圆角半径r值 (7)表 2 普通翻边高度H值和螺纹最少反复打入次数 (9)表 3 薄板连接用带锥台翻边攻丝孔翻边高度H值和螺纹最少反复打入次数 (9)表 4 自铆参数表 (10)表 5 自铆连接点最小承力表 (10)表 6 毛刺高度的极限值 (15)表 7 钣金公差数值表 (17)钣金冲压件质量要求Specification For Sheet-metal Punching Part范围Scope:本规范规定了华为的钣金冲压件(表面处理前)的质量要求、检验规则。
五金冲压检验标准

五金冲压检验标准1.0目的为了使产品在冲压生产查验过程中有据可依、正确判断,提高查验质量与效率,保证企业产品切合客户需求。
2.0范围合用企业五金冲压线3.0 定义A 级面:客户常常看到的面,如面板,机箱的上表面、正面。
B级面:不挪动的状况下,客户有时能看到的面,如机箱的后边、侧面等。
级面:产品在挪动或被翻开时才能看到的面,如机箱的底面,内部部件的表面等重要缺点〈MA〉:与设计要求偏离影响整体构造或对客户在使用过程中隐蔽不安全要素。
次要缺点〈MI〉:切合设计要求、不影响客户使用及在使用过程中无危及安全,但会对客户带来不欢乐心情。
4.0查验条件与环境4.1产品BOM与工程图各一份4.2与产品目视距离30cm,呈45角度4.3查验时间为10—15秒4.4光芒为正常日光灯60W5.0查验工具5.1游标卡尺5.2千分尺5.3角度尺5.4塞规6.0查验项目与判断6.1材质、尺寸6.1.1 五金冲压件所用的的材质、厚度要切合客户要求,若客户无特别要求按我司正常使用材质、厚度。
与之不符判断MA。
6.1.2 五金冲压件外型尺寸要切合工程图所示大小,与之不符判断MA。
6.1.3 五金冲压件的冲孔、引深的地点、直径、深浅要与工程图所示切合,与之不符判断MA。
6.1.4 五金冲压件折边角度要与工程图所示切合。
与之不符判断MA。
6.1.5 五金冲压件压边后与面的空隙小于或等于0.2MM。
与之不符判断MI。
6.2 外观.2.1缺点种类与定义刮伤:五金件表面的呈条状的浅沟。
裂痕:五金材质在冲压过程出现断裂。
氧化:材质与空气中的氧起化学变化。
变形:材质在冲压或移转过程中造成外观变异。
擦伤:材质表面相互接触摩擦所致的损害。
凸凹痕:材质表面异样突出或凹陷模痕:冲压过程中模具在材质表面留下的痕迹。
毛刺:冲孔或切边角过程中不完整留有余料。
污渍:加工过程中油渍或污物附其表面造成弊端6.2.2A级面允收标准外观允收水平B级面C级面判断刮有不同意不同意见限度样板MI伤感无同意〈可接受长同意〈可接受长感≤?CM宽≤0。
最新华为客户可靠性测试标准资料
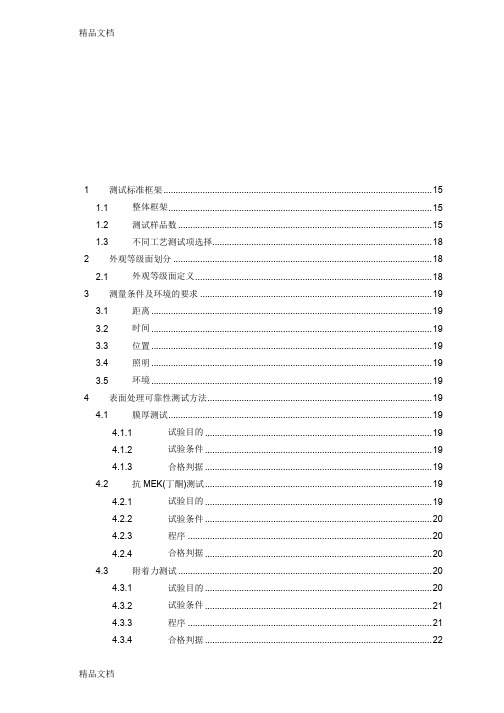
1测试标准框架 (15)1.1整体框架 (15)1.2测试样品数 (15)1.3不同工艺测试项选择 (18)2外观等级面划分 (18)2.1外观等级面定义 (18)3测量条件及环境的要求 (19)3.1距离 (19)3.2时间 (19)3.3位置 (19)3.4照明 (19)3.5环境 (19)4表面处理可靠性测试方法 (19)4.1膜厚测试 (19)4.1.1试验目的 (19)4.1.2试验条件 (19)4.1.3合格判据 (19)4.2抗MEK(丁酮)测试 (19)4.2.1试验目的 (19)4.2.2试验条件 (20)4.2.3程序 (20)4.2.4合格判据 (20)4.3附着力测试 (20)4.3.1试验目的 (20)4.3.2试验条件 (21)4.3.3程序 (21)4.3.4合格判据 (22)4.3.5等级描述说明 (22)4.3.6测试工具 (23)4.4RCA纸带耐磨测试 (23)4.4.1试验目的 (23)4.4.2试验条件 (23)4.4.3程序 (24)4.4.4合格判据 (24)4.5酒精摩擦测试 (24)4.5.1试验目的 (24)4.5.2试验条件 (24)4.5.3程序 (24)4.5.4合格判据 (25)4.6橡皮摩擦测试 (25)4.6.1试验目的 (25)4.6.2试验条件 (25)4.6.3程序 (25)4.6.4合格判据 (25)4.7振动摩擦测试 (26)4.7.1试验目的 (26)4.7.2试验条件 (26)4.7.3程序 (26)4.7.4合格判据 (27)4.7.5说明 (28)4.8铅笔硬度测试 (28)4.8.1试验目的 (28)4.8.2试验条件 (28)4.8.3程序 (28)4.8.4合格判据 (30)4.8.5测试工具 (30)4.9抗脏污测试 (30)4.9.1试验目的 (30)4.9.2试验条件 (30)4.9.3程序 (31)4.9.4合格判据 (31)4.10牛顿笔测试 (31)4.10.1试验目的 (31)4.10.2试验条件 (31)4.10.3程序 (31)4.10.4合格判据 (31)4.10.5说明 (31)4.11显微维氏硬度测试 (32)4.11.1试验目的 (32)4.11.2试验条件 (32)4.11.3程序 (32)4.11.4合格判据 (32)4.12耐化妆品测试 (32)4.12.1试验目的 (32)4.12.2试验条件 (32)4.12.3程序 (33)4.12.4合格判据 (33)4.13耐手汗测试 (33)4.13.1试验目的 (33)4.13.2试验条件 (33)4.13.3程序 (33)4.13.4合格判据 (34)4.13.5说明 (34)4.14低温存储 (34)4.14.1试验目的 (34)4.14.2试验条件 (34)4.14.3程序 (34)4.14.4合格判据 (35)4.15高温存储 (35)4.15.1试验目的 (35)4.15.2试验条件 (35)4.15.3程序 (35)4.15.4合格判据 (35)4.16交变湿热 (35)4.16.1试验目的 (35)4.16.3程序 (36)4.16.4合格判据 (36)4.17温度冲击 (36)4.17.1试验目的 (36)4.17.2试验条件 (36)4.17.3程序 (36)4.17.4合格判据 (36)4.18太阳辐射 (37)4.18.1试验目的 (37)4.18.2试验条件 (37)4.18.3程序 (37)4.18.4合格判据 (37)4.18.5说明 (37)4.19盐雾测试 (38)4.19.1试验目的 (38)4.19.2试验条件 (38)4.19.3程序 (38)4.19.4合格判据 (39)4.20水煮测试 (40)4.20.1试验目的 (40)4.20.2试验条件 (40)4.20.3程序 (40)4.20.4合格判据 (40)4.20.5说明 (40)4.21切片测试 (40)4.21.1试验目的 (40)4.21.2试验条件 (41)4.21.3程序 (41)4.21.4合格判据 (42)4.22内部件附着力测试 (42)4.22.1试验目的 (42)4.22.2试验条件 (42)4.22.3程序 (43)4.23内部件交变湿热 (43)4.23.1试验目的 (43)4.23.2试验条件 (43)4.23.3程序 (43)4.23.4合格判据 (43)4.23.5说明 (43)4.24内部件温度冲击 (43)4.24.1试验目的 (43)4.24.2试验条件 (43)4.24.3程序 (44)4.24.4合格判据 (44)4.25内部五金件阻抗测试 (44)4.25.1试验目的 (44)4.25.2试验条件 (44)4.25.3程序 (44)4.25.4合格判据 (44)4.26内部五金件高温高湿 (45)4.26.1试验目的 (45)4.26.2试验条件 (45)4.26.3程序 (45)4.26.4合格判据 (46)4.27钢丝绒测试 (46)4.27.1试验目的 (46)4.27.2试验条件 (46)4.27.3程序 (46)4.27.4合格判据 (46)4.283D涂层及小部件验证策略 (46)4.28.13D涂层 (46)4.28.2小部件 (46)5结构件强度测试方法 (47)5.1强度测试位置识别方法 (47)5.1.1试验目的 (47)5.1.2试验条件 (47)5.2.1试验目的 (48)5.2.2试验条件 (48)5.2.3程序 (49)5.2.4合格判据 (49)5.3弯折测试 (50)5.3.1试验目的 (50)5.3.2试验条件 (50)5.3.3程序 (52)5.3.4合格判据 (52)5.4拉力测试 (53)5.4.1试验目的 (53)5.4.2试验条件 (53)5.4.3程序 (54)5.4.4合格判据 (54)5.5NMT粘合质量初判 (54)5.5.1试验目的 (54)5.5.2试验条件 (54)5.5.3程序 (54)5.5.4合格判据 (55)5.6NMT剪切强度测试 (56)5.6.1试验目的 (56)5.6.2试验条件 (56)5.6.3程序 (56)5.6.4合格判据 (56)5.7NMT定向跌落测试 (56)5.7.1试验目的 (56)5.7.2试验条件 (57)5.7.3程序 (57)5.7.4合格判据 (58)5.8按键手感 (58)5.8.1试验目的 (58)5.8.2试验条件 (58)5.8.3合格判据 (58)5.9.1试验目的 (58)5.9.2试验条件 (58)5.9.3资源要求 (58)5.9.4测试步骤 (59)5.9.5合格判据 (60)5.10USB/耳机/卡托模拟插拔测试 (60)5.10.1试验目的 (60)5.10.2试验条件 (60)5.10.3程序 (61)5.10.4合格判据 (61)5.11表面能测试 (61)5.11.1试验目的 (61)5.11.2试验条件 (61)5.11.3程序 (62)5.11.4合格判据 (62)5.11.5说明 (62)5.11.6附OWENS 计算方法 (63)5.12装饰件拉拔力测试 (63)5.12.1试验目的 (63)5.12.2试验条件 (63)5.12.3程序 (63)5.12.4合格判据 (63)5.13卡托三杆弯测试 (64)5.13.1试验目的 (64)5.13.2试验条件 (64)5.13.3程序 (64)5.13.4合格判据 (64)5.14卡托横梁正向挤压测试 (65)5.14.1试验目的 (65)5.14.2试验条件 (65)5.14.3程序 (65)5.14.4合格判据 (65)5.15卡托横梁侧向挤压测试 (65)5.15.2试验条件 (66)5.15.3程序 (66)5.15.4合格判据 (66)5.16卡托扭曲测试 (67)5.16.1试验目的 (67)5.16.2试验条件 (67)5.16.3程序 (67)5.16.4合格判据 (67)5.17卡托钢片推出力测试 (68)5.17.1试验目的 (68)5.17.2试验条件 (68)5.17.3程序 (68)5.17.4合格判据 (68)5.18卡托弯折测试 (68)5.18.1试验目的 (68)5.18.2试验条件 (68)5.18.3程序 (69)5.18.4合格判据 (69)5.19螺钉防松扭力测试 (69)5.19.1试验目的 (69)5.19.2试验条件 (69)5.19.3程序 (69)5.19.4合格判据 (70)5.20螺钉破坏扭力测试 (70)5.20.1试验目的 (70)5.20.2试验条件 (70)5.20.3程序 (70)5.20.4合格判据 (70)6非功能类镜片可靠性测试方法 (71)6.1抗化学试剂测试 (71)6.1.1试验目的 (71)6.1.2试验条件 (71)6.1.3程序 (71)6.2附着力测试 (71)6.2.1试验目的 (71)6.2.2试验条件 (71)6.2.3程序 (71)6.2.4合格判据 (71)6.2.5说明 (71)6.3铅笔硬度测试 (72)6.3.1试验目的 (72)6.3.2试验条件 (72)6.3.3程序 (72)6.3.4合格判据 (72)6.3.5测试工具 (72)6.4显微维氏硬度测试 (72)6.4.1试验目的 (72)6.4.2试验条件 (72)6.4.3程序 (72)6.4.4合格判据 (73)6.5耐化妆品测试 (73)6.5.1试验目的 (73)6.5.2试验条件 (73)6.5.3程序 (73)6.5.4合格判据 (73)6.6耐手汗测试 (74)6.6.1试验目的 (74)6.6.2试验条件 (74)6.6.3程序 (74)6.6.4合格判据 (74)6.6.5说明 (74)6.7低温存储 (74)6.7.1试验目的 (74)6.7.2试验条件 (74)6.7.3程序 (74)6.7.4合格判据 (74)6.8高温存储 (75)6.8.1试验目的 (75)6.8.2试验条件 (75)6.8.3程序 (75)6.8.4合格判据 (75)6.9交变湿热 (75)6.9.1试验目的 (75)6.9.2试验条件 (75)6.9.3程序 (75)6.9.4合格判据 (75)6.10温度冲击 (76)6.10.1试验目的 (76)6.10.2试验条件 (76)6.10.3程序 (76)6.10.4合格判据 (76)6.11酒精摩擦 (76)6.11.1试验目的 (76)6.11.2试验条件 (76)6.11.3程序 (76)6.11.4合格判据 (76)6.12钢丝绒测试 (77)6.12.1试验目的 (77)6.12.2试验条件 (77)6.12.3程序 (77)6.12.4合格判据 (77)6.13盐雾试验 (77)6.13.1试验目的 (77)6.13.2试验条件 (77)6.13.3程序 (77)6.13.4合格判据 (78)6.14水煮测试 (78)6.14.1试验目的 (78)6.14.2试验条件 (78)6.14.3程序 (78)6.14.5说明 (78)6.15太阳辐射 (78)6.15.1试验目的 (78)6.15.2试验条件 (78)6.15.3程序 (78)6.15.4合格判据 (79)6.15.5说明 (79)6.16背面油墨阻抗测试 (79)6.16.1试验目的 (79)6.16.2试验条件 (79)6.16.3程序 (79)6.16.4合格判据 (79)6.17挤压测试 (79)6.17.1试验目的 (79)6.17.2试验条件 (80)6.17.3程序 (80)6.17.4合格判据 (80)6.18镜片推脱力测试 (81)6.18.1试验目的 (81)6.18.2试验条件 (81)6.18.3程序 (81)6.18.4合格判据 (81)6.19镜片背面贴膜拉拔力 (81)6.19.1试验目的 (81)6.19.2试验条件 (81)6.19.3合格判据 (81)6.20四杆弯折(强化指标)测试 (81)6.20.1试验目的 (81)6.20.2试验条件 (81)6.20.3程序 (82)6.20.4合格判据 (82)6.21落球测试 (83)6.21.1试验目的 (83)6.21.3程序 (83)6.21.4合格判据 (84)6.22环对环挤压测试 (84)6.22.1试验目的 (84)6.22.2试验条件 (84)6.22.3程序 (84)6.22.4合格判据 (84)6.23透光率 (85)6.23.1试验目的 (85)6.23.2试验条件 (85)6.23.3合格判据 (85)6.23.4说明 (85)6.24水滴角 (85)6.24.1试验目的 (85)6.24.2试验条件 (85)6.24.3合格判据 (86)6.25表面能测试 (86)7特殊工艺测试方法 (86)7.1贴片logo附着力测试 (86)7.1.1试验目的 (86)7.1.2试验条件 (86)7.1.3程序 (86)7.1.4合格判据 (86)7.2贴片logo拉拔力测试 (86)7.2.1试验目的 (86)7.2.2试验条件 (86)7.2.3判定依据 (86)7.3贴片logo环境测试 (87)7.3.1试验目的 (87)7.3.2试验条件 (87)7.3.3合格判据 (87)7.4PET板材电池盖拉拔力测试 (87)7.4.1试验目的 (87)7.4.3程序 (87)7.4.4合格判据 (87)7.5屏蔽罩性能测试 (88)7.5.1高温测试 (88)7.5.2吃锡测试 (88)7.5.3绝缘电阻测试 (88)7.5.4耐电压测试 (88)8供应商ORT测试要求 (88)8.1应用说明 (88)错误!未找到引用源。
- 1、下载文档前请自行甄别文档内容的完整性,平台不提供额外的编辑、内容补充、找答案等附加服务。
- 2、"仅部分预览"的文档,不可在线预览部分如存在完整性等问题,可反馈申请退款(可完整预览的文档不适用该条件!)。
- 3、如文档侵犯您的权益,请联系客服反馈,我们会尽快为您处理(人工客服工作时间:9:00-18:30)。
DKBA华为技术有限公司企业技术规范2003DKBA4031-2003.06 钣金结构件可加工性设计规范2003-06-30发布2003-07-XX实施华为技术有限公司发布目次前言 (5)1范围和简介 (6)1.1范围 (6)1.2简介 (6)1.3关键词 (6)2规范性引用文件 (6)3冲裁 (6)3.1冲裁件的形状和尺寸尽可能简单对称,使排样时废料最少。
. 63.2冲裁件的外形及内孔应避免尖角。
(6)3.3冲裁件应避免窄长的悬臂与狭槽 (6)3.4冲孔优先选用圆形孔,冲孔有最小尺寸要求 (7)3.5冲裁的孔间距与孔边距 (7)3.6折弯件及拉深件冲孔时,其孔壁与直壁之间应保持一定的距离73.7螺钉、螺栓的过孔和沉头座 (7)3.8冲裁件毛刺的极限值及设计标注 (7)3.8.1冲裁件毛刺的极限值 (7)3.8.2设计图纸中毛刺的标注要求 (8)4折弯 (8)4.1折弯件的最小弯曲半径 (8)4.2弯曲件的直边高度 (9)4.2.1一般情况下的最小直边高度要求 (9)4.2.2特殊要求的直边高度 (9)4.2.3弯边侧边带有斜角的直边高度 (9)4.3折弯件上的孔边距 (9)4.4局部弯曲的工艺切口 (9)4.4.1折弯件的弯曲线应避开尺寸突变的位置 (9)4.4.2当孔位于折弯变形区内,所采取的切口形式 (10)4.5带斜边的折弯边应避开变形区 (10)4.6打死边的设计要求 (10)4.7设计时添加的工艺定位孔 (10)4.8标注弯曲件相关尺寸时,要考虑工艺性 (10)4.9弯曲件的回弹 (11)4.9.1折弯件的内圆角半径与板厚之比越大,回弹就越大。
.. 114.9.2从设计上抑制回弹的方法示例 (11)5拉伸 (11)5.1拉伸件底部与直壁之间的圆角半径大小要求 (11)5.2拉伸件凸缘与壁之间的圆角半径 (11)5.3圆形拉伸件的内腔直径 (11)5.4矩形拉伸件相邻两壁间的圆角半径 (11)5.5圆形无凸缘拉伸件一次成形时,其高度与直径的尺寸关系要求125.6拉伸件设计图纸上尺寸标注的注意事项 (12)5.6.1拉伸件产品尺寸的标准方法 (12)5.6.2拉伸件尺寸公差的标注方法 (12)6成形 (12)6.1加强筋 (12)6.2打凸间距和凸边距的极限尺寸 (12)6.3百叶窗 (12)6.4孔翻边 (12)7附录 (13)7.1附录A:高碳钢、低碳钢对应的公司常用材料牌号列表 (13)7.2附录B 压印工艺、压花工艺简介 (15)7.2.1压印工艺 (15)7.2.2压花工艺 (15)8参考文献 (15)前言本规范的其他系列规范:无与对应的国际标准或其他文件的一致性程度:无规范代替或作废的全部或部分其他文件:无与其他规范或文件的关系:无与规范前一版本相比的升级更改的内容:第一版,无升级更改信息。
本规范由整机工程部结构造型设计部提出。
本规范主要起草和解释部门:结构造型设计部本规范主要起草专家:结构造型设计部:邓在明(10166)、盛辉(21628)、李俊周(17743)。
本规范主要评审专家:结构造型设计部:曾喜能(7700)、田雨(15962)、向子上(17314)、王永刚(21437)、许剑明(21269)、刘长林(20072)、李浩(25479)。
本规范批准部门:整机工程部结构造型设计部本规范所替代的历次修订情况和修订专家为:钣金结构件可加工性设计规范1范围和简介1.1范围本规范规定了钣金结构设计所要注意的加工工艺要求。
本规范适用于钣金结构设计必须遵守的加工工艺要求。
1.2简介我司产品结构件主要是由钣金材料经过冲压加工而成,这些冲压件的几何形状、尺寸和精度对冲压工艺影响很大。
冲压件具有良好的加工工艺性有利于节省材料、减少工序、提高模具使用寿命和产品质量,同时,可以有效的降低产品成本。
按钣金件的基本加工方式,如冲裁、折弯、拉伸、成型,本规范通过阐述每一种加工方式所要注意的工艺要求,提出对钣金件结构设计的限制。
1.3关键词钣金、冲裁、折弯、拉伸、成形、排样、最小弯曲半径、毛边、回弹、打死边2规范性引用文件下列文件中的条款通过本规范的引用而成为本规范的条款。
凡是注日期的引用文件,其随后所有的修改单(不包括勘误的内容)或修订版均不适用于本规范,然而,鼓励根据本规范达成协议的各方研究是否可使用这些文件的最新版本。
凡是不注日期的引用文件,其最新版本适用于本规范。
3冲裁分为普通冲裁和精密冲裁,由于加工方法的不同,冲裁件的加工工艺性也有所不同。
目前我司通信产品结构件一般只用到普通冲裁。
下面介绍冲裁的工艺性,是指普通冲裁的结构工艺性。
3.1冲裁件的形状和尺寸尽可能简单对称,使排样时废料最少。
图3.1.1 冲裁件的排样3.2冲裁件的外形及内孔应避免尖角。
在直线或曲线的连接处要有圆弧连接,圆弧半径R≥0.5t。
(t为材料壁厚)图3.2.1 冲裁件圆角半径的最小值3.3冲裁件应避免窄长的悬臂与狭槽冲裁件的凸出或凹入部分的深度和宽度,一般情况下,应不小于1.5t(t为料厚),同时应该避免窄长的切口与和过窄的切槽,以便增大模具相应部位的刃口强度。
见图3.3.1。
图3.3.1 避免窄长的悬臂和凹槽3.4冲孔优先选用圆形孔,冲孔有最小尺寸要求冲孔优先选用圆形孔,冲孔最小尺寸与孔的形状、材料机械性能和材料厚度有关。
图3.4.1 冲孔形状示例* 高碳钢、低碳钢对应的公司常用材料牌号列表见第7章附录A。
表1冲孔最小尺寸列表3.5冲裁的孔间距与孔边距零件的冲孔边缘离外形的最小距离随零件与孔的形状不同有一定的限制,见图3.5.1。
当冲孔边缘与零件外形边缘不平行时,该最小距离应不小于材料厚度t;平行时,应不小于1.5t。
图3.5.1 冲裁件孔边距、孔间距示意图3.6折弯件及拉深件冲孔时,其孔壁与直壁之间应保持一定的距离折弯件或拉深件冲孔时,其孔壁与工件直壁之间应保持一定的距离(图3.6.1)图3.6.1 折弯件、拉伸件孔壁与工件直壁间的距离3.7螺钉、螺栓的过孔和沉头座螺钉、螺栓过孔和沉头座的结构尺寸按下表选取取。
对于沉头螺钉的沉头座,如果板材太薄难以同时保证过孔d2和沉孔D,应优先保证过孔d2。
表2用于螺钉、螺栓的过孔*要求钣材厚度t≥h。
表3用于沉头螺钉的沉头座及过孔*要求钣材厚度t≥h。
表4用于沉头铆钉的沉头座及过孔3.8冲裁件毛刺的极限值及设计标注3.8.1冲裁件毛刺的极限值冲裁件毛刺超过一定的高度是不允许的,冲压件毛刺高度的极限值(mm)见下表。
f mg f m g f m g f m g>0.7 ~1.0 0.12 0.17 0.23 0.09 0.13 0.17 0.05 0.07 0.1 0.03 0.04 0.05>1.0 ~1.6 0.17 0.25 0.34 0.12 0.18 0.24 0.07 0.11 0.15 0.04 0.06 0.08>1.6 ~2.5 0.25 0.37 0.5 0.18 0.26 0.35 0.11 0.16 0.22 0.06 0.09 0.12>2.5 ~4.0 0.36 0.54 0.72 0.25 0.37 0.5 0.2 0.3 0.4 0.09 0.13 0.18* f级(精密级)适用于较高要求的零件;m级(中等级)适用于中等要求的零件;g级(粗糙级)适用于一般要求的零件。
表5冲压件毛刺高度的极限值3.8.2设计图纸中毛刺的标注要求* 毛边方向:BURR SIDE。
* 需要压毛边的部位:COIN或COIN CONTINUE 。
一般不要整个结构件断口全部压毛边,这样会增加成本。
尽量在下面情况使用:暴露在外面的断口;人手经常触摸到的锐边;需要过线缆的孔或槽;有相对滑动的部位。
图3.8.2.1 钣金结构设计图纸中毛刺的标注示例4 折弯4.1折弯件的最小弯曲半径材料弯曲时,其圆角区上,外层收到拉伸,内层则受到压缩。
当材料厚度一定时,内r越小,材料的拉伸和压缩就越严重;当外层圆角的拉伸应力超过材料的极限强度时,就会产生裂缝和折断,因此,弯曲零件的结构设计,应避免过小的弯曲圆角半径。
公司常用材料的最小弯曲半径见下表。
序号材料最小弯曲半径08、08F、10、10F、DX2、SPCC、E1-T52、0Cr18Ni9、1Cr18Ni9、1Cr18Ni9Ti、1100-H24、T2 0.4t●t为材料壁厚,M为退火状态,Y为硬状态,Y2为1/2硬状态。
表6公司常用金属材料最小折弯半径列表4.2弯曲件的直边高度4.2.1一般情况下的最小直边高度要求弯曲件的直边高度不宜太小,最小高度按(图h>2t。
图4.2.1.1 弯曲件的直边高度最小值4.2.2特殊要求的直边高度如果设计需要弯曲件的直边高度h≤2t,,则首先要加大弯边高度,弯好后再加工到需要尺寸;或者在弯曲变形区内加工浅槽后,再折弯(如下图所示)。
图4.2.2.1 特殊情况下的直边高度要求4.2.3弯边侧边带有斜角的直边高度当弯边侧边带有斜角的弯曲件时(图4.2.3),侧面的最小高度为:h=(2~4)t>3mm图4.2.3.1 弯边侧边带有斜角的直边高度4.3折弯件上的孔边距孔边距:先冲孔后折弯,孔的位置应处于弯曲变形区外,避免弯曲时孔会产生变形。
孔壁至弯边的距离见表下表。
表7折弯件上的孔边距4.4局部弯曲的工艺切口4.4.1折弯件的弯曲线应避开尺寸突变的位置局部弯曲某一段边缘时,为了防止尖角处应力集中产生弯裂,可将弯曲线移动一定距离,以4.6打死边的设计要求打死边的死边长度与材料的厚度有关。
如下图所示,一般死边最小长度L≥3.5t+R。
其中t为材料壁厚,R为打死边前道工序(如下图右所示)的最小内折弯半径。
图4.6.1 死边的最小长度L4.7设计时添加的工艺定位孔为保证毛坯在模具中准确定位,防止弯曲时毛坯偏移而产生废品,应预先在设计时添加工艺定位孔,如下图所示。
特别是多次弯曲成形的零件,均必须以工艺孔为定位基准,以减少累计误差,保证产品质量。
图4.7.1 多次折弯时添加的工艺定位孔4.8标注弯曲件相关尺寸时,要考虑工艺性图4.9.2.1 设计上抑制回弹的方法示例5 拉伸5.1拉伸件底部与直壁之间的圆角半径大小要求如下图所示,拉伸件底部与直壁之间的圆角半径应大于板厚,即r1≥t 。
为了使拉伸进行得更顺利,一般取r1=(3~5)t,最大圆角半径应小于或等于板厚的8倍,即r1≤8t。
图5.1.1 拉伸件圆角半径大小5.2拉伸件凸缘与壁之间的圆角半径拉伸件凸缘与壁之间的圆角半径应大于板厚的2倍,即r2≥2t,为了使拉伸进行得更顺利,一般取r2=(5~10)t,最大凸缘半径应小于或等于板厚的8倍,即r2≤8t5.3圆形拉伸件的内腔直径圆形拉伸件的内腔直径应取D ≥d+10t5.4矩形拉伸件相邻两壁间的圆角半径矩形拉伸件相邻两壁间的圆角半径应取r3 ≥3t,为了减少拉伸次数应尽可能取r3 ≥H/5,以便一次拉出来。