挤出机成型条件表
挤出成型工艺参数

图4.3所示的温度曲线只是稳定挤出过程中 温度的宏观表示。表4.是几种塑料挤出成型的参考温度。
表4.1 热塑性塑料挤出成型的温度参数
塑料名称
丙烯酸类聚合物 醋酸纤化物
聚酰胺(PA) 聚乙烯(PE)
加料段 室温 室温 室温~90 室温
挤出温度/°C
压缩段
均化段
100~170
约200
110~130
约150
塑料成型工艺与模具设计
挤出成型工艺参数
温度
挤出成型工艺参数
压力 挤出速度
牵引速度
1. 挤出成型温度应指塑料熔体的温度,
该温度在很大程度上取决于料筒和螺杆的 温度。
图4.3所示为沿料筒轴线方向测得的聚 乙烯的温度曲线。
图4.3聚乙烯挤出成型的温度曲线
1 料筒温度曲线;2 螺杆温度曲线;3 物料(PE) 的温度;4 物料(PE)的平均温度; 5 物料 (PE)的最低温度;D 料筒的直径
调整螺杆转速是控制挤出速度的主要 措施。
4. 牵引速度
挤出成型必须设置牵引装置。从机头 和口模中挤出的塑件,在牵引力作用下将 会发生拉伸取向。
牵引速度与挤出速度的比值称为牵引 比(牵伸比、拉伸比),其值必须≥1。
塑料成型工艺与模具设计
140~180
约270
90~140
约180
机头及口模段 175~210 175~190 180~270 160~200
原料中的水分/%
≤0.025 <0.5 <0.3 <0.3
硬聚氯乙烯(HPVC) 室温~60
120~170
约180
170~190
<0.2
软聚氯乙烯及氯乙 烯共聚物
挤出成型工艺—挤出成型原理(塑料成型加工课件)
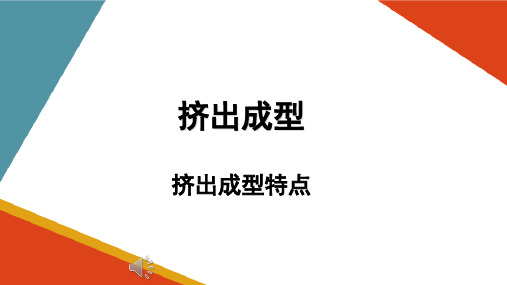
二、挤出成型过程
既有混合过 程,也有成 型过程
树脂原料 加热黏流 塑料熔体
助剂
混合过程
加压 挤出连续体
一定规格的 制品
切割 成型连续体
冷却定型
成型过程
以 管 材 挤 出 原料 成型为例
挤出连续体
熔体
定型连续体
制品
三、挤出成型特点
1. 可以连续化生产,生产效率高。 2. 设备自动化程度高,劳动强度低。 3. 生产操作简单,工艺控制容易。 4. 原料适应性强,适用大多数热塑性树脂和少数热固性 树脂。 5. 可生产的产品广泛,同一台挤出机,只要更换不同的 辅机,就可以生产不同的制品。
挤出成型
挤出成型特点
一、挤出成概述
挤出成型又叫挤出模塑,是利用加热使塑料熔融塑化成 为流动状态,然后在机械力(螺杆或柱塞的挤压)的作用下, 使熔融塑料通过一定形状的口模制成具有恒定截面连续的制 品,适用于绝大部分热塑性树脂和部分热固性树脂。
除了用于挤出造粒、染色、树脂掺和等共混改性,还可用于塑 料薄膜、网材、带包覆层的产品、截面一定、长度连续的管材、板 材、片材、棒材、打包带、单丝和异型材等塑料制品的生产。
料表面接近或达到黏流温度,表面发黏。
要求:输送能力要稍高于熔融段和均化段。
2. 压缩段 (熔融段)
位置:螺杆中部一段。 作用:输送物料,使物料受到热和剪切作用熔 融塑化,并进一步压实和排出气体。 特点:物料逐渐由玻璃态转变为粘流态,在熔 融段末端物料为粘流态。 要求:螺杆结构逐渐紧密,使物料进一步压实。
(3)横流(环流) 由垂直于螺棱方向的分速
度引起的使物料在螺槽内产生翻 转运动。对生产能力没有影响, 但能促进物料的混合和热交换。
(4)漏流 由机筒与螺棱间隙处形成的
挤出成型的类型
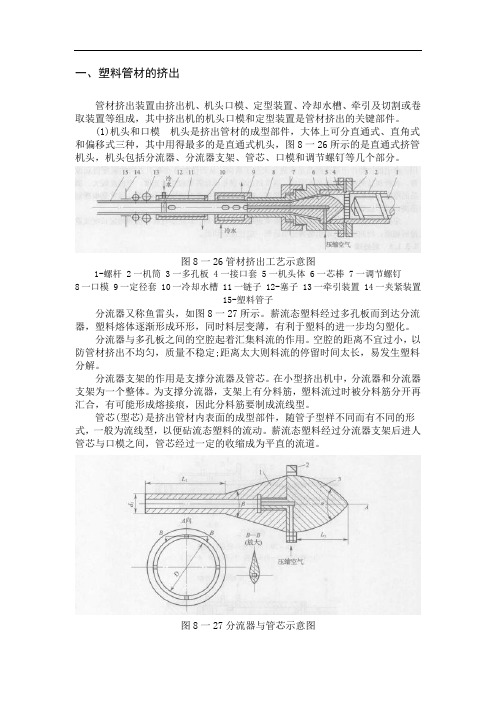
一、塑料管材的挤出管材挤出装置由挤出机、机头口模、定型装置、冷却水槽、牵引及切割或卷取装置等组成,其中挤出机的机头口模和定型装置是管材挤出的关键部件。
(1)机头和口模机头是挤出管材的成型部件,大体上可分直通式、直角式和偏移式三种,其中用得最多的是直通式机头,图8一26所示的是直通式挤管机头,机头包括分流器、分流器支架、管芯、口模和调节螺钉等几个部分。
图8一26管材挤出工艺示意图1-螺杆 2一机筒 3一多孔板 4一接口套 5一机头体 6一芯棒 7一调节螺钉8一口模 9一定径套 10一冷却水槽 11一链子 12-塞子 13一牵引装置 14一夹紧装置15-塑料管子分流器又称鱼雷头,如图8一27所示。
薪流态塑料经过多孔板而到达分流器,塑料熔体逐渐形成环形,同时料层变薄,有利于塑料的进一步均匀塑化。
分流器与多孔板之间的空腔起着汇集料流的作用。
空腔的距离不宜过小,以防管材挤出不均匀,质量不稳定;距离太大则料流的停留时间太长,易发生塑料分解。
分流器支架的作用是支撑分流器及管芯。
在小型挤出机中,分流器和分流器支架为一个整体。
为支撑分流器,支架上有分料筋,塑料流过时被分料筋分开再汇合,有可能形成熔接痕,因此分料筋要制成流线型。
管芯(型芯)是挤出管材内表面的成型部件,随管子型样不同而有不同的形式,一般为流线型,以便砧流态塑料的流动。
薪流态塑料经过分流器支架后进人管芯与口模之间,管芯经过一定的收缩成为平直的流道。
图8一27分流器与管芯示意图1一芯棒 2一分流器支架 3一分流器在管材挤出过程中,机头压缩比表示豁流态塑料被压缩的程度。
机头压缩比是分流器支架出口处流道环形面积与口模及管芯之间的环形截面积之比。
压缩比太小不能保证挤出管材的密实,也不利于消除分料筋所造成的熔接痕;压缩比太大则料流阻力增加。
机头压缩比按塑料性质在3一10的范围内变化。
口模结构如图8一28所示。
口模的平直部分与管芯的平直部分构成管子的成型部件,这个部分的长短影响管材的质量。
挤出成型的原理和工艺流程
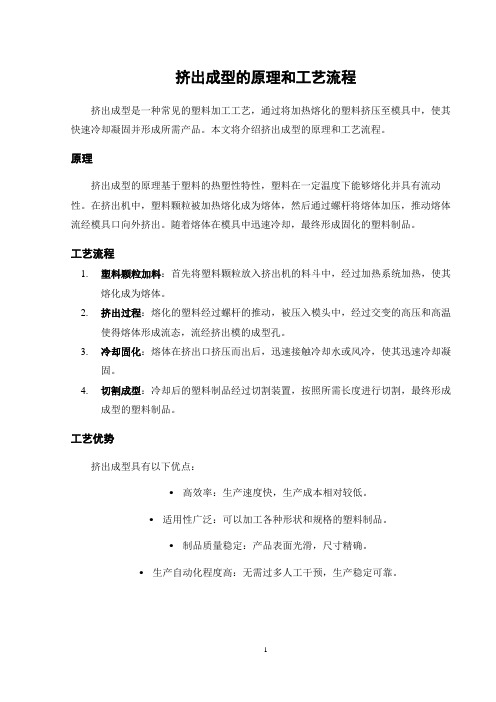
挤出成型的原理和工艺流程
挤出成型是一种常见的塑料加工工艺,通过将加热熔化的塑料挤压至模具中,使其快速冷却凝固并形成所需产品。
本文将介绍挤出成型的原理和工艺流程。
原理
挤出成型的原理基于塑料的热塑性特性,塑料在一定温度下能够熔化并具有流动性。
在挤出机中,塑料颗粒被加热熔化成为熔体,然后通过螺杆将熔体加压,推动熔体流经模具口向外挤出。
随着熔体在模具中迅速冷却,最终形成固化的塑料制品。
工艺流程
1.塑料颗粒加料:首先将塑料颗粒放入挤出机的料斗中,经过加热系统加热,使其
熔化成为熔体。
2.挤出过程:熔化的塑料经过螺杆的推动,被压入模头中,经过交变的高压和高温
使得熔体形成流态,流经挤出模的成型孔。
3.冷却固化:熔体在挤出口挤压而出后,迅速接触冷却水或风冷,使其迅速冷却凝
固。
4.切割成型:冷却后的塑料制品经过切割装置,按照所需长度进行切割,最终形成
成型的塑料制品。
工艺优势
挤出成型具有以下优点:
•高效率:生产速度快,生产成本相对较低。
•适用性广泛:可以加工各种形状和规格的塑料制品。
•制品质量稳定:产品表面光滑,尺寸精确。
•生产自动化程度高:无需过多人工干预,生产稳定可靠。
应用领域
挤出成型广泛应用于塑料制品生产行业,如管道、板材、型材、薄膜、包装材料等领域。
其高效率、高质量的特点使其成为塑料制品生产中不可或缺的一环。
总的来说,挤出成型作为一种常见的塑料加工工艺,通过简单高效的操作流程,可以生产出质量稳定的塑料制品,在工业生产中发挥着重要作用。
挤出成型—挤出理论(高分子成型课件)

四、挤出机的挤出理论
3 熔体输送理论 流动流动状态:
①正流Qd:沿正轴向口模/机头方向流动。由旋转螺杆挤压造成。 ②逆流Qp:沿正方向相反,由机头压力引起。 ③横流Qt:环流。不影响总流量。但对熔体的混合、塑化、热交换起重要 作用。 ④漏流Qc 物料在螺杆与机筒之间间隙向加料口方向回流,可降低挤出量 。一般情况下漏流Qc很小,但磨损严重时,漏流Qc增加急剧增加。
p在挤出过程中,由于螺杆 和料筒机构、机头、过滤 网以及过滤板的阻力,使 塑料内部存在压力。
p压力可以提高挤出熔体的混合均匀性和稳定性,提高产品致密 度, 是塑料变为均匀熔体并得到致密塑件的重要条件之一。 p螺杆转速的变化,加热、冷却系统的不稳定都对产生压力波动 产生影响,对制品质量产生不利影响。 p为保证制品质量,应尽可能减少压力的波动。
六、挤出工艺的影响因素
3 挤出速率
p挤出速率因素影响较多(机头阻力、螺杆与料筒结构、螺杆转速、 加热冷却系统和塑料特性等)但主要与螺杆转速有关,提高转速,可 提高挤出产量,但塑化质量不高,因而挤出速率要大小合适。 p挤出速率在生产过程中也存在波动现象,挤出速率的波动影响制品 几何形状和尺寸。生产中应保证挤出速率的稳定。
LDPE 15~20 3~4 90~100 100~140 140~160 140~160
PP
22~25 2.5~4 140~160 165~185 180~200 160~185
PC
16~25 2.5~3 200~240 240~250 230~255 200~22100
六、挤出工艺的影响因素
2 压力
tan tanb
四、挤出机的挤出理论
建塑成型之挤出

芯棒口模之间的环形截面积与管材截 面积之比称为拉伸比。 拉伸比I = (R12-R22) / (r12- r22) I = (86.52-63.32)/(902-73.62) = 1.3
4.4.6定型冷却 ① 定型 是挤出管材生产中的一道重要工序。直接 关系到管材能否有正确的尺寸。 管坯从口模中挤出时,基本还处于熔融状 态。为了避免管坯在重力作用下变形,并且能 按所设计的管材的形状和尺寸成型,必须立即 定径和冷却。使温度显著下降而硬化和定型。 确保管坯离开定型装置后不致于由于牵引、自 重、冷却水的压力而变形。
二、简述用单螺杆挤出机制备管材的工 艺过程。
三、什么是最佳工作点?:物料的密度 g/cm3 b:管材壁厚 cm V:挤出线速度 m/min r1:管材外径 cm r2:管材内径 cm
4.4.4 最佳工作点 Q = AN / (1+B/K) ΔP = AηN /(K+B) K= C平均t3 / 12 L
C平均:环形口模圆周的平均长度 t:口模缝隙宽度 L:口模平直部分长度
◆定型法 定型板法 外径定型法 内压定型法 定型法 真空定型法 内径定型法 管材外表面公差 定外径 管材内表面公差 定内径 实际应用中,内压定型法和真空定型 法使用广泛。
◆定型套长度 对于聚烯烃,如采用内压定型法,经验式:
L = 100 b2 V
L 定型套长度 cm b 管材厚度 cm V 挤出速度 cm/s
牵引
纵拉
取向
◆牵引方式 滚轮式牵引机构 中小口径管材 履带式牵引机构 大口径管材
◆牵引速度
与挤出速度匹配
4.4.8 切割 牵引装置将定型冷却后的管子递送到 预定长度后,即可开动切割装置将管子切 断。
圆盘锯切割 自由行星锯切割
挤出成型:单螺杆挤出机的基本结构、成型原理、工艺与流程[专业参考]
![挤出成型:单螺杆挤出机的基本结构、成型原理、工艺与流程[专业参考]](https://img.taocdn.com/s3/m/9f17c9dd804d2b160b4ec0c7.png)
二、加料装置 锥形料斗 粉料、粒料容积可容纳>1h的用量
有截断装置、侧面有视孔、计量装置 有些有真空装置 有加热装置(防止吸水) 有搅拌器,能自动加料
专业参考
7
三、料筒
金属圆筒, 耐热、耐压、强度高、坚固耐磨、 耐腐蚀的合金钢或内衬合金钢的复合钢管制成;
料筒长度是直径的15~30倍,使物料得到充分 加热和塑化;
2
挤出成型
定义:在挤压作用下物料受热熔化,强 行通过口模,截面恒定,连续型材 。
适用:所有的热塑性塑料,部分热固性 塑料, 可生产管、薄膜、线缆包复物及 其型材
占挤出制品:40~50% 挤出机可用于混合、造粒和着色、共混
专ห้องสมุดไป่ตู้参考
3
挤出成型
单螺杆挤出机的基本结构 挤出成型原理 挤出成型工艺与过程
固体床沿挤出方向逐渐减小。
从上述的熔化实验研究可知:
(1)塑料的整个熔化过程是在螺杆熔融区进行的
(2)沿挤出方向固体床宽度逐渐减小直到为零,其减小部分被熔融所占 有
(3)沿挤出方向固体床厚度逐渐减小直到为零,其减小部分形成熔膜
(4)熔化作用发生在熔膜和固体床的界面上,有一部分发生在固相与熔
池的迁移面.
专业参考
38
(3)横流 物料沿X轴和Y轴两方向在螺槽内往复流动,也 是螺杆旋转时螺杨的推挤作用和阻挡作用所造成的, 仅限于在每个螺槽内的环流,对总的挤出生产率影响 不大.但对于物料的热交换、混合和进一步均匀塑比 影响很大
(4)漏流 物料在螺杆和料筒的间隙沿着螺杆的轴向往料 斗方向的流动、它头和门模等对物料的阻力所产生的 反压流动,由于螺杆和料筒间的间隙很小,故在—般 情况下漏流流率要比正流和逆流小很多。
挤出成型的工艺参数有哪些
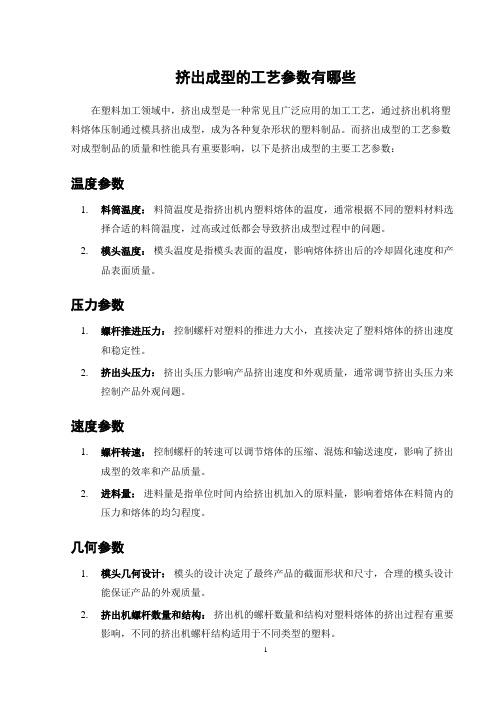
挤出成型的工艺参数有哪些在塑料加工领域中,挤出成型是一种常见且广泛应用的加工工艺,通过挤出机将塑料熔体压制通过模具挤出成型,成为各种复杂形状的塑料制品。
而挤出成型的工艺参数对成型制品的质量和性能具有重要影响,以下是挤出成型的主要工艺参数:温度参数1.料筒温度:料筒温度是指挤出机内塑料熔体的温度,通常根据不同的塑料材料选择合适的料筒温度,过高或过低都会导致挤出成型过程中的问题。
2.模头温度:模头温度是指模头表面的温度,影响熔体挤出后的冷却固化速度和产品表面质量。
压力参数1.螺杆推进压力:控制螺杆对塑料的推进力大小,直接决定了塑料熔体的挤出速度和稳定性。
2.挤出头压力:挤出头压力影响产品挤出速度和外观质量,通常调节挤出头压力来控制产品外观问题。
速度参数1.螺杆转速:控制螺杆的转速可以调节熔体的压缩、混炼和输送速度,影响了挤出成型的效率和产品质量。
2.进料量:进料量是指单位时间内给挤出机加入的原料量,影响着熔体在料筒内的压力和熔体的均匀程度。
几何参数1.模头几何设计:模头的设计决定了最终产品的截面形状和尺寸,合理的模头设计能保证产品的外观质量。
2.挤出机螺杆数量和结构:挤出机的螺杆数量和结构对塑料熔体的挤出过程有重要影响,不同的挤出机螺杆结构适用于不同类型的塑料。
其他参数1.冷却参数:产品挤出后需要经过冷却固化阶段,控制冷却方式和速度对产品的成型完整性和尺寸稳定性具有重要作用。
2.模具温度:模具温度对产品的收缩率和表面质量有直接影响,适当调节模具温度能够改善产品的表面光滑度和尺寸精度。
以上便是挤出成型的主要工艺参数,通过对这些参数的合理控制和调节,可以提高挤出成型制品的质量稳定性和生产效率,从而满足不同行业对塑料制品的需求。
PMMA成型法

注射成型
成型的条件因机器能力、制品形状、以及模具的构造等不同而不同。成型时,请按下表所示料筒以及模具的温度为标准,设定正确的条件。而且须注意品种不同流动性不同,成型温度不尽相同。
标准成型条件
预备干燥
80~90℃
75~85℃
70~75℃
4~6小时
4~6小时
4~6小时
模具温度(℃)
50~90
40~70
40~60
料筒温度(℃)
210~260
190~260
170~260
注射压力(MPa)
80~140
80~140
80~140
挤出成型
的挤出成型可以使用通常的挤出机,使用排气挤出机时,通常不需预备干燥,但使用非排气式挤出机时需要充分进行干燥。
干燥条件根据挤出成型情况而定,因丙烯酸树脂的熔融粘度高,所以需用高压挤出机。挤出成型条件因机器种类、螺杆形状和产品形状不同而不同,例示条件如下:
(1)脱离模具后用水冷却时,提高水的温度或缩短用水冷却的时间
(2)提高模具温度
·喷射痕
这是发生在产品表面的、以进料口为中心的细年轮状的条纹。可通过下列对策防止其发生:
(1)提高料筒温度
(2)提高模具温度
(3)增大注射压力和提高注射速度,使其迅速填满加料孔
(4)延长成型周期
(5)增大浇口(主流道·分流道·进料口)的横截面面积,并缩短其长度使树脂更易流动
(1)充分干燥
(2)降低料筒温度,增大注射压力
(3)提高注射速度
(4)降低熔融状态时的螺杆转速,调节背压
(5)若是薄形成型,提高模具温度,降低料筒温度
(6)确定熔融状态的时间
挤出成型的基本过程
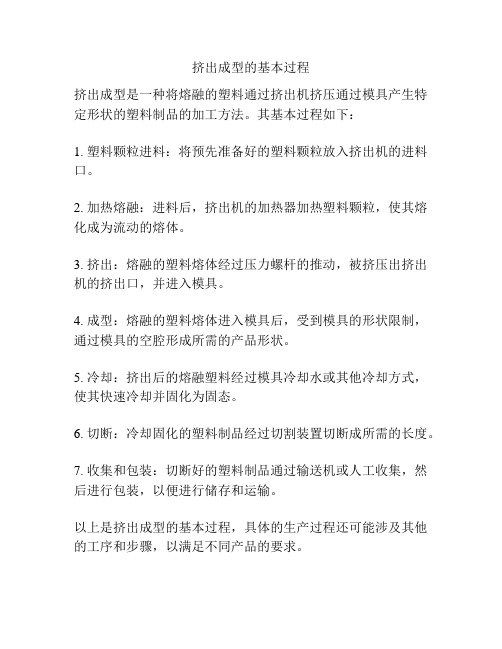
挤出成型的基本过程
挤出成型是一种将熔融的塑料通过挤出机挤压通过模具产生特定形状的塑料制品的加工方法。
其基本过程如下:
1. 塑料颗粒进料:将预先准备好的塑料颗粒放入挤出机的进料口。
2. 加热熔融:进料后,挤出机的加热器加热塑料颗粒,使其熔化成为流动的熔体。
3. 挤出:熔融的塑料熔体经过压力螺杆的推动,被挤压出挤出机的挤出口,并进入模具。
4. 成型:熔融的塑料熔体进入模具后,受到模具的形状限制,通过模具的空腔形成所需的产品形状。
5. 冷却:挤出后的熔融塑料经过模具冷却水或其他冷却方式,使其快速冷却并固化为固态。
6. 切断:冷却固化的塑料制品经过切割装置切断成所需的长度。
7. 收集和包装:切断好的塑料制品通过输送机或人工收集,然后进行包装,以便进行储存和运输。
以上是挤出成型的基本过程,具体的生产过程还可能涉及其他的工序和步骤,以满足不同产品的要求。
挤出成型工艺及挤出模

三、典型挤出机头结构
1、管材挤出成型机头
三、典型挤出机头结构
1、管材挤出成型机头
2、棒材挤出成型机头
2、棒材挤出成型机头
2、棒材挤出成型机头
3、吹塑薄膜挤出成型机头
3、吹塑薄膜挤出成型机头
3、吹塑薄膜挤出成型机头
3、吹塑薄膜挤出成型机头
4、电线电缆挤出成型机头
4、电线电缆挤出成型机头
(3)塑件的定型与冷却 管材的定径方法:定径套、定径环、定径板
3、挤出成型工艺
(3)塑件的定型与冷却
3、挤出成型工艺
(4)塑件的牵引Biblioteka 卷曲和切割 在冷却得同时,连续均匀地将塑件引出。
牵引速度略大于挤出速度
不同的塑件,牵引速度不同。
4、挤出成型工艺条件
(1)温度 加料段的温度不宜过高,压缩段和均化段的温度可高一些。
5、温度调节系统:使挤出成型设备具有一定温度。
6、定径套:对塑件进行冷却定型,以获得完好的塑件。
定型模:让从口模中挤出的塑料的既定形状稳定下来
三、典型挤出机头结构
1、管材挤出成型机头
(1)直通式
三、典型挤出机头结构
1、管材挤出成型机头
(2)直角式
三、典型挤出机头结构
1、管材挤出成型机头
(3)旁侧式
二、挤出成型模具的组成及分类
挤出机头:挤出塑料制件成型的主要部件产生必要的成型压力。
1、口模和芯棒:相当于型腔和型芯,用于成型塑件的内外表面。
2、过滤网和过滤板:将塑料熔体的螺旋运动转变为直线运动,并过滤杂 质。
3、分流器和分流器支架:使塑料熔体平稳地进入成型区,同时进一步加 热和塑化。
4、机头体:组装并支承机头的各个零部件。
挤出成型工艺参数

挤出成型工艺参数挤出成型是一种常见的塑料加工工艺,通过加热和压力将塑料材料挤出模具,使其成型。
在进行挤出成型时,需要考虑多种工艺参数以确保最终产品的质量和效率。
下面将介绍一些常见的挤出成型工艺参数及其影响。
1. 温度温度是影响挤出成型的关键参数之一。
挤出机的加热区通常分为多个温区,每个温区设定的温度会影响塑料塑化和流动的速度。
过高或过低的温度都会导致产品质量下降。
通常需要根据不同的塑料材料和产品要求来调整各个温区的温度。
2. 压力挤出机的压力参数也至关重要。
通过调节挤出机的螺杆转速和压力,可以控制塑料在模具中的流动速度和压缩程度。
适当的压力可以确保挤出的均匀性和稳定性,同时要避免过高的压力导致挤出机的堵塞或破裂。
3. 螺杆速度螺杆速度是影响挤出成型产量和质量的重要参数。
合适的螺杆转速可以保证塑料材料在挤出机内均匀混合并顺利挤出,从而得到一致的成型产品。
调整螺杆速度还可以控制产品的厚度和尺寸。
4. 模具设计除了挤出机的参数外,模具设计也对挤出成型的效果起着至关重要的作用。
不同形状和尺寸的产品需要设计不同的模具结构,以确保最终产品的精度和表面质量。
优秀的模具设计可以降低挤出成型的能耗和材料浪费。
5. 冷却系统挤出成型后的塑料制品需要通过冷却系统迅速冷却固化,并保持其形状稳定。
冷却系统的设计和控制可影响产品的收缩率和表面质量。
合理的冷却系统可以提高挤出生产效率和产品质量。
综上所述,挤出成型工艺参数的选择和控制对最终产品的质量和生产效率具有重要影响。
生产过程中需要仔细调整和监控温度、压力、螺杆速度、模具设计以及冷却系统等关键参数,以确保挤出成型过程稳定、高效,并获得符合要求的产品。
塑料成型工艺第六章 挤出成型

c、物料全部熔融,变为粘流融的物料量逐渐减少,大约在压 缩段的结束处,全部物料熔融而转变为粘流态, 但这时各点的温度尚不很均匀。
3)均化段——均化、挤出 物料经过均化段的均化作用就比较均匀 了,最后螺杆将熔融物料定量、定压、定温地 挤入机头。 机头内的口模是个成型部件,物料通过它 便获得一定截面的几何形状和尺寸。
固体输送区:固体状态 熔融区:两相共存 熔体输送区:全部为熔体 这几个区不一定完全和前面介绍过的螺杆 的加料段,压缩段,均化段相一致。
3.塑件的定型与冷却阶段
管材的定径方法:定径套、定径环、定径板
4.塑件的牵引、卷取和切割
在冷却得同时,连续均匀地将塑件引出。
牵引速度略大于挤出速度 不同的塑件,牵引速度不同。
挤出成型所需控制的温度是机筒温度、机颈 温度、口模温度。 机筒温度分布,从喂料区到模头可能是平坦分 布,递增分布,递减分布及混合分布。主要取决 于材料物点和挤出机的结构。
表6-2
常见管材成型温度(单位:℃)
口模设臵温度,口模和芯模的温度对管子表
面光洁度有影响,在一定的范围内,口模与芯
模温度高,管子表面光洁度高。通常来讲,口
3.混合效果差,不能很好适应一些特殊塑料的加 工或混炼、着色工艺过程。
排气式螺杆 主要适用于含水和易产生挥发组分的物料。 排气原理:物料到排气段基本塑化,由于该段 螺槽突然加深,压力骤降,气体从熔体中逸处, 从排气口排出。
分离型(屏障型)螺杆 原理:在螺杆熔融段再附加一条螺纹,将原来 一个螺纹所形成的螺槽分为两个,将已熔物料和 未熔物料尽早分离,促进未熔料尽快熔融。
加热冷却系统;
螺杆转数;
螺杆和料筒的结构
研究挤出过程的压力轮廓曲线对挤出过程的了解 和改进螺杆、料筒的设计有着重要意义。
挤出成型工艺介绍工艺
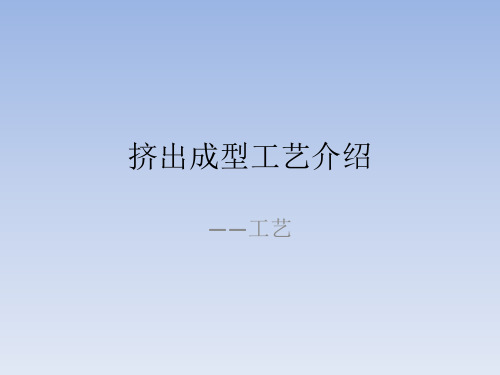
——工艺
目录
一、工艺参数设定原则 二、片材工艺流程及装置 三、工艺控制 四、常见缺陷
一、工艺参数设定原则
1、机身温度 对与普通的单组份热塑性塑料固体原料的挤出成形,挤出机机身温度设
定原则为: ①机身设定的最高温度略高于塑料的黏流温度(或熔点); ②机身设定的最低温度应至少低于塑料软化点10; ③单螺杆挤出机机身设定的最高温度与最低温度的差值不大于80; ④机身温度字加料端到熔料出口逐渐升高或与螺杆计量段对应区温度相近; ⑤在满足熔化物料的前提下,机身温度应尽可能低。
对与多层共挤出成形,除了考虑以上因素外,还应注意层间的粘接强度, 应适当提高机身温度。
一、工艺参数设定原则
2、机头温度 机头加热有三个作用: ①进一步塑化物料; ②保持熔体流动性和良好的成形性; ③熔体之间的黏合性。
熔体在机头流道中流动会产生一定的摩擦热,因此机头温度设定应考虑 满足其基本作用情况下尽可能低。通常机颈处温度略低于机身最高温度,口模各 段的温度略高于机身设定的最高温度。
对大型挤出机头,应选用内外加热装置,提高口模温度均匀性和加热效 率。
一、工艺参数设定原则
3、挤出机冷却 为了防止挤出机加料斗底部处物料因过热软化而“架桥”,导致加料不
顺畅,一般挤出机加料斗底部均设置冷却水通道,生产前应接通冷却水冷却。对 与单螺杆挤出机,可采用螺杆内部冷却方法,提高固体输送速率。 4、挤出速度
三、工艺控制
1、挤出温度 ①挤出温度应根据挤出物料的加工流变特性、热分解性能和板、片材使
用性能综合确定。挤出温度一般分6——10段控制,挤出料筒温度控制在满足均 匀塑化物料的前提下应尽可能低,机头温度除了考虑挤出产量外,还要考虑制品 表面质量要求及与结晶、取向有关的物理力学性能要求,一般比挤出料筒温度高 5—速度是决定挤出产量和质量的重要 工艺参数。
尼龙66挤出成型工艺条件

尼龙66挤出成型工艺条件一、引言尼龙66是一种热塑性高分子材料,具有良好的物理性能和热稳定性,被广泛应用于各个领域。
挤出成型是尼龙66加工的一种常用工艺,本文将详细介绍尼龙66挤出成型的工艺条件。
二、挤出成型原理挤出成型是通过将塑料熔融后挤出成型口,然后通过模具冷却固化得到所需形状的工艺。
尼龙66的挤出成型过程主要包括塑料熔融、挤出、冷却和固化四个阶段。
三、工艺条件1. 温度控制:尼龙66的熔融温度一般在250℃-280℃之间,具体的熔融温度需要根据材料的牌号和厂家提供的工艺参数进行调整。
熔融温度过低会导致熔体流动性不佳,熔融温度过高则容易引起材料分解和气泡等缺陷。
2. 挤出速度:挤出速度是指塑料在挤出机进料段的进料速度,一般控制在10-30mm/s之间。
挤出速度过快会导致熔体温度下降过快,挤出速度过慢则会导致熔体在挤出机内停留时间过长,容易引起熔体分解和降解。
3. 模具温度:模具温度是指模具表面的温度,一般控制在80℃-100℃之间。
模具温度过低会导致产品冷却速度过快,容易引起产品表面缩孔和收缩不均匀;模具温度过高则容易引起产品收缩不足和变形。
4. 冷却方式:常用的冷却方式有自然冷却和水冷却两种。
自然冷却速度较慢,适用于产品尺寸较小、精度要求较高的情况;水冷却速度较快,适用于产品尺寸较大、生产效率要求较高的情况。
5. 挤出压力:挤出压力是指挤出机内塑料的压力,一般控制在50-100MPa之间。
挤出压力过低会导致挤出速度不稳定,产品表面光洁度差;挤出压力过高则容易引起产品收缩不均匀和内部应力过大。
6. 挤出机参数:挤出机的螺杆直径、螺杆长径比、螺杆转速等参数也会对挤出成型的工艺条件产生影响。
一般来说,螺杆直径较大、螺杆长径比较小、螺杆转速较低的挤出机适用于尼龙66的挤出成型。
四、注意事项1. 要保证挤出机的清洁,避免杂质和污染物的混入,以免对挤出成型的产品质量产生影响。
2. 挤出过程中应定期检查模具和挤出机的磨损情况,及时更换损坏的部件,以确保挤出成型的稳定性和产品的质量。
挤出成型工艺
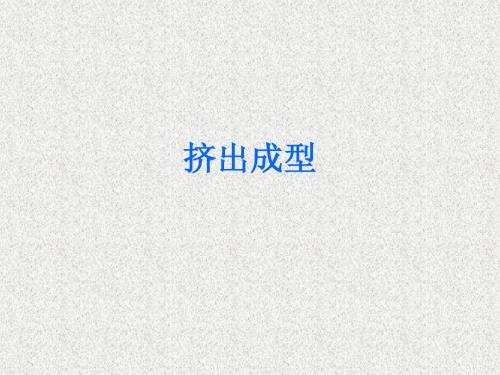
法易于进行机械加工,故多采用。
螺槽深度(h):
h↓,剪切速率↑,传热效率
↑,混合及塑化效率↑,生产率↓ 。故热敏性塑料(如PVC)宜用深 螺槽,而熔体粘度低且热稳定性好 的塑料(如聚酰胺等)宜用浅螺槽 。
螺旋升角θ
θ↑,出料快,生产能力↑,
但停留时间短,塑化↓。
实验证明,物料形状不同,对加
料段的螺纹升角要求也不一样。 1)θ=30 °左右适于粉料, 2)θ=l7°左右适于圆柱料, 3)θ=15°左右适于方块料。 出于机械加工的方便,一般取D=S ,θ=17°40’。
• a螺杆特性曲线
• 它是一组相互平行的直线族,随螺杆转速n的改变而改变。 螺杆的特性线是挤出机的重要特性之一,它表示螺杆均化 段熔体的流率与压力的关系。随着机头压力的升高,挤出 量降低,而降低的快慢决定于螺杆特性线的斜率。
b.口模特性曲线 挤出机机头是挤出机的重要组成部分, 是物料流经并获得一定几何形状、 必要尺寸精度和表面光洁度的部件。 假定熔体为牛顿流体,当其通过机 头时,其流率方程为:
实际上螺槽中熔体的总的流动是这几种流动的总 和。
挤出机的生产能力:
Q=Qd (正流)- Qp (逆流)- QL (漏流)
(4)挤出机的工作状态
要想了解整个挤出过程的特性,还必须将螺杆和机 头联合起来讨论,为此我们引入了以下几个概念: • 螺杆特性线---挤出机产量与挤出压力的关系; • 口模特性线---机头产量与机头压力的关系; • 挤出机的综合工作点---螺杆特性线与口模特性线 的交点
b、逆流方向 流动,流量为QP
c. 漏流: 由口型阻力引起,沿螺棱顶部与料筒
内表面之间的间隙中反向流动。 方向沿螺杆轴线方向,并由机头向后, 不利于产量的提高。流量用QL表示。
塑料的挤出成型工艺

Ⅱ 若在螺帽上加一定压力,再旋转螺丝,则 螺帽就会随螺丝旋转而前移。
(2) 成型时,塑料与螺杆的摩擦力应小于塑 料与料筒的摩擦力,也即螺杆的光洁度应大于料筒 的光洁度。否则,塑料只能抱着螺杆空转打滑不能 前移。
整理ppt
25
图3-6-7 螺槽中固体输送的理想模型(a) 和固体塞移动速度的矢量图(b)
主要适用于聚酰胺、聚乙烯等结晶高聚物。 c. 鱼雷头型螺杆:
特点:计量段没有螺纹,剪切作用大,塑化效果好。 (但易使物料分解)
适用范围:PS、PE、PA、PMMA、PDVC等。
整理ppt
13
Ⅱ. 等深不等距螺杆: A. 计量段h3太大,塑化效果不好。 原因:螺槽越深,物料受到的剪切作用越小。 B. 传热面积减小,不利于传热、塑化。 原因:因为螺距变小了。 C.生产率Q降低,料流不稳定。 D. 适用于L/D大的小型挤出机。 原因:因加料段d较大,螺杆强度高。
整理ppt
18
2 双螺杆挤出机主要参数 (1)螺杆直径/mm: 国外多在28--340 mm。 (2)螺杆长径比: 整体式:过去多为7—18,有增大趋势。 组合式:可达36:1以上。 (3)螺杆的转向:同向(混料),异向(生产 制品)。 (4)螺杆承受的扭矩 (5)推力轴承的承载能力 (6)驱动功率、加热功率和加热段数。
则 Va=l×N。由图3-6-8中螺杆的几何关系可求出: πD=b1+b2= l·cotθ+l·cotφ= l(cotθ+ cotφ)
整理ppt
30
πD 所以 l =
cotθ+cotφ
(3-6-3)
πDN
πDNtanθ·tanφ
图1: 挤出成型工艺流程图

5
图 6: 熔融基本步骤的主要机理概述
机理概述见图 6。
13. 聚合物加工中的分布函数和混合物特征表述
分子量分布函数 分数的表达式
分布方差
首先定义 Mx 为具有 x 个重复单位的分子的分子浓度。于是可以得到摩尔分数和高分子质量
压延成型工艺流程图见图 2。 6. 什么是塑料的二次成型? 塑料的二次成型与一次成型的区别是什么? 给出两种以上利用二次成型技术生产的
塑料制品 二次成型是指在一定条件下,将经高分子材料一次成型所得的片、板、棒等型材通过再次加工成型,以获得
最终制品的技术。 二次成型和一次成型的主要区别在于:一次成型是通过材料的流动或塑性形变而成型,成型过程中伴随着
固体颗粒的输送熔融增压和泵送混合熔体反应脱挥与脱模微结构化的聚合物添加剂反应助剂颗粒在熔融混合反应的微结构化聚合物共混混合和反应聚合物加工的概念明细表共混主要与分散与分布混合相关或是添加剂混入单一聚合物基质材料或是创建两种及以上聚合物之稳定物理共混物
1
1. 单螺杆挤出机中螺杆可分为哪几段,每段螺杆在结构上的特点,每段螺杆对物料起的作用 可分为三段:(深槽) 喂料段、(压缩) 过渡段、(浅槽) 计量段。 喂料段必须深到足以容纳低松密度塑料颗粒,产生必要的扭矩输送固体,产生足够的压力压缩颗粒至固体
其他低分子组分。在后反应器操作中,需要排出这些挥发物,以回收溶剂和单体、消除残留气味和味道、赋予聚
床。大部分熔融发生在相对长的压缩段中,需要减少槽深以改善熔融效率。计量段浅槽能合理地均化熔体,熔体 来自熔融区的部分熔态区域,能够给这些部分熔态区带来更均匀的温度。 2. 画出挤出成型工艺的流程图
精选挤出成型工艺与设备概述
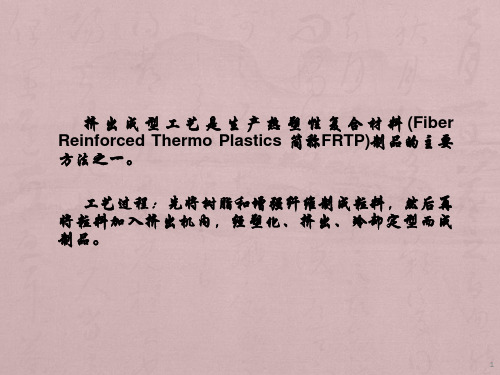
SJSZ系列锥形双螺杆挤出机
2、设备
生产短纤维粒料的主要设备是挤出机和造粒机头,它不需要单独的牵引和切粒机。A、挤出机 B、造粒机头 长纤维粒料的造粒是采用冷切法,其原因是不使纤维从粒料中抽出,短纤维粒料的造粒是采用热切法。因为从机头挤出来的料条中纤维已经很短,可以不经冷却直接通过造粒机头造粒。构造见P296
图11-19 固体物料在螺槽中的熔融过程 1-熔膜;2-熔池;3-迁移面(分界面);4-熔结的固体粒;5-未熔结的固体粒子
(1)正流
(2)逆流
(3)横流
(4)漏流
图11-20 螺杆几何构造
11.4 FRTP管挤出成型工艺
1 挤管工艺
FRTP管的成型条件与普通塑料管工艺基本相似,只是成型温度要提高10-20℃。
6)耐疲劳性能、抗蠕变性能
7)防止开裂、改善电性能
2 纤维含量对FRTP性能的影响
3 纤维质量对性能的影响
(1)纤维直径对性能的影响
各种树脂品种的FRTP的最佳纤维含量不同。
一般来讲,纤维直径越细,强度越高,但有时相差不大,可能是因为纤维细强度高,但同样含量纤维用在CM中,弱界面也随之增加,加工过程中纤维磨损严重,强度损失也较大。
11.5.2 挤出机主机
一、分类及构造
按工作原理分
螺杆式
无螺杆式
单螺杆式
双螺杆式
普通型
高速自热型
按排气状况分
排气式
分段组合式
按用途分
造粒挤出机
超高分子量挤出机
混炼挤出机
安装位置分
立式挤出机
卧式挤出机
目前用的最广泛的是卧式单螺杆和双螺杆挤出机。
二、单螺杆挤出机(前11-25图)