论我国机械加工工艺中存在的技术误差问题及对策分析
机械加工工艺技术的误差及改善对策

机械加工工艺技术的误差及改善对策在机械加工工艺中,误差是一个不可避免的问题。
无论是人为因素还是机械设备的精度,都可能导致加工件的尺寸或形状出现偏差。
如何降低误差、提高加工精度,是每个机械加工工艺技术人员都面临的挑战。
本文将探讨机械加工工艺技术中的误差及改善对策,希望能给广大机械加工工艺技术人员一些参考。
一、误差的类型1.尺寸误差尺寸误差是指加工件的实际尺寸与设计尺寸之间的偏差。
尺寸误差通常是由刀具磨损、刀具偏差、材料变形等因素引起的。
若尺寸误差不能控制在一定范围内,将直接影响加工件的装配和使用。
2.形状误差形状误差是指加工件的实际形状与设计形状之间的偏差。
形状误差通常是由夹具变形、工件振动、加工参数设定不合理等因素引起的。
形状误差会使得加工件无法满足设计要求,严重影响产品质量。
3.表面质量误差表面质量误差是指加工件表面粗糙度、毛刺、磨痕等问题。
表面质量误差通常是由切削参数选择不合理、切削润滑不良等因素引起的。
表面质量误差会影响产品的外观和功能,降低产品的使用寿命。
二、改善对策1.精确的工艺规程制定精确的工艺规程是减少误差的第一步。
工艺规程包括刀具选择、切削参数、夹具设计、工艺路线等内容。
只有在工艺规程明确、准确的情况下,才能有效降低误差的产生。
2.精准的加工设备精准的加工设备是减少误差的关键。
先进的数控机床、高精度的刀具、灵活可靠的夹具,能够提高加工的精度,减少误差的产生。
3.优化的加工参数合理的加工参数能够降低误差的产生。
比如选择合适的切削速度、进给量和切削深度,可以有效控制加工件的表面质量误差;合理的切削参数选择,可以减少刀具的磨损和偏差,降低尺寸误差的产生。
4.严格的质量控制严格的质量控制是减少误差的保障。
通过检测、测量、校正等手段,及时发现并纠正加工误差,确保产品的质量达标。
5.人员的技术培训技术人员的技术培训是减少误差的基础。
只有技术人员具备足够的加工技术知识、操作技能,才能正确使用加工设备,合理制定工艺规程,有效控制误差的产生。
机械加工工艺的技术误差问题及对策

机械加工工艺的技术误差问题及对策【摘要】机械加工工艺中的技术误差是一直存在且影响重大的问题。
本文通过对误差产生原因、分类与特点、检测与测量方法、补偿技术以及提高精度的方法进行分析和讨论,旨在找出问题根源并提出解决方案。
误差产生原因分析包括机床、工件、刀具等多方面因素,通过系统地分类与特点及检测与测量方法,可以更准确地了解误差程度和来源。
误差补偿技术则是针对已知误差进行校正,提高了加工质量和精度。
本文提出了一些提高精度的方法,如加强设备维护、采用先进的加工工艺等。
通过对机械加工工艺的技术误差问题及对策的分析和总结,有助于提高加工精度、减少损耗,提高生产效率。
【关键词】机械加工工艺、技术误差、误差产生原因、误差分类、误差特点、误差检测、误差测量、误差补偿、精度提高、对策、总结。
1. 引言1.1 机械加工工艺的技术误差问题及对策机械加工是制造业中一项重要的工艺,而在机械加工过程中难免会有技术误差的产生。
技术误差可能会导致产品质量下降,甚至影响整个生产过程。
如何有效地解决机械加工工艺中的技术误差问题成为了一个亟待解决的难题。
对于机械加工工艺中技术误差问题的解决,首先需要对误差产生的原因进行深入分析。
误差产生的原因可能包括材料性能、机床精度、刀具磨损、操作人员技术水平等多个方面。
只有全面地找出误差产生的源头,才能有针对性地进行修正和改进。
对技术误差进行分类和特点分析也是解决问题的重要一环。
不同类型的误差可能需要采取不同的对策,因此对误差进行准确定位至关重要。
了解误差的特点也有助于我们更好地把握误差的性质和规律。
在解决技术误差问题时,选择合适的检测与测量方法也至关重要。
通过精准的测量和检测,可以及时发现误差,并采取有效的措施加以修正。
误差补偿技术和提高精度的方法也是解决问题的重要途径。
机械加工工艺中的技术误差问题需要我们从多个方面入手,全面分析和解决。
只有通过对误差产生原因的分析、误差分类与特点的研究、误差的检测与测量方法的选择、误差补偿技术的运用以及提高精度的方法的实施,我们才能更好地解决机械加工工艺中的技术误差问题,提高产品质量,提升生产效率。
机械加工工艺的技术误差问题及对策分析

机械加工工艺的技术误差问题及对策分析机械加工工艺是制造业中非常重要的一个环节,而技术误差问题是在机械加工过程中经常会遇到的一个难题。
技术误差问题一旦出现,不仅会影响产品的质量和精度,还会导致生产周期延长和成本增加。
对于机械加工工艺的技术误差问题及对策分析,是非常值得关注和深入研究的话题。
一、技术误差问题概述在机械加工过程中,技术误差是很难完全避免的。
技术误差主要表现为尺寸、形位和表面粗糙度方面的误差。
这些误差会直接影响产品的质量和精度,严重影响产品的使用性能和寿命。
技术误差问题不仅仅是机械加工工艺本身的问题,更是机械加工人员是否具备高水平的技术素养和严格的操作规范。
1. 设计误差:如果产品的设计尺寸、形位公差设置不合理,也会直接导致技术误差的产生。
2. 材料误差:材料的成分、硬度、力学性能等参数不符合要求,也会对机械加工产生影响。
3. 加工设备精度不足:机床、刀具、夹具等加工设备的精度不足,也会直接导致技术误差的产生。
4. 操作不当:加工人员操作不当,比如刀具磨损严重、刀具切削速度过快或过慢、切削进给量不合理等,都会引起技术误差。
5. 环境因素:加工环境的温度、湿度、灰尘等因素也会对机械加工产生影响,导致技术误差的产生。
三、对策分析1. 严格的产品设计与工艺标准产品设计的合理性和工艺标准的严格性是避免技术误差的关键。
产品设计要合理设置公差,严格控制尺寸、形位和表面粗糙度等要求,避免设计误差的产生。
工艺标准也要明确相关参数,确保每道工序的加工技术要求得到满足。
2. 材料的严格把控材料的选用直接影响机械加工的质量和精度,在材料的选用方面要严格把控,确保材料的质量和性能符合要求。
3. 加工设备的精度保证加工设备的精度是保证机械加工质量和精度的基础。
在购买、维护和保养加工设备时,要严格把控设备的精度,确保设备的正常运行和高效加工。
4. 加工人员的素质提升加工人员的技术水平和操作规范直接影响机械加工的质量和精度。
机械加工工艺的技术误差问题及对策分析

机械加工工艺的技术误差问题及对策分析机械加工工艺是指通过特定的工艺方法,对工件进行加工、修整和改变尺寸、形状、位置和性能的一种制造过程。
在机械加工过程中,由于各种因素的影响,往往会产生一定的技术误差。
这些技术误差不仅影响产品的质量,还可能导致工艺流程的无效和浪费。
分析机械加工工艺的技术误差问题,并提出相应的对策,对于提高产品加工精度和工艺稳定性具有重要意义。
一、机械加工工艺的技术误差问题机械加工工艺的技术误差主要包括以下几个方面:1. 尺寸误差:在机械加工中,尺寸误差是最常见的问题之一。
尺寸误差包括绝对误差和相对误差。
绝对误差是指零件尺寸与设计尺寸之间的差值,而相对误差则是指零件尺寸与其它相关尺寸之间的差值。
尺寸误差的产生与机床精度、刀具磨损、材料性质等因素有关。
2. 形状误差:机械加工中的形状误差主要指零件的形状与设计要求不符。
形状误差的主要原因是加工过程中的变形和变量等因素引起的。
在铣削加工中,切削力的变化会导致零件变形,从而使得加工出的零件形状与设计要求不一致。
3. 位置误差:机械加工中的位置误差主要指零件加工位置与设计位置之间的偏差。
位置误差的产生与机床的定位精度、夹具的刚性以及加工过程中的振动和变形等因素有关。
位置误差会导致零件之间的位置关系发生变化,进而影响到装配的质量和精度。
4. 表面质量误差:机械加工中的表面质量误差主要指零件表面的光洁度、粗糙度、平整度等指标与设计要求之间的差异。
表面质量误差的产生与刀具的磨损、切削参数的选择以及加工液的使用等因素有关。
1. 优化机床和刀具:应根据加工要求选择合适的机床和刀具,尽可能提高其精度和刚性。
还应定期对机床和刀具进行维护和保养,及时更换磨损严重的刀具,以减小机床和刀具对加工质量的影响。
2. 控制加工参数:加工参数的选择对于控制技术误差具有重要作用。
通过合理调整加工参数,可以有效地减小尺寸误差和形状误差。
在铣削加工中,可以控制切削力的大小和方向,以减小零件变形和形状误差。
机械加工工艺的技术误差问题及对策
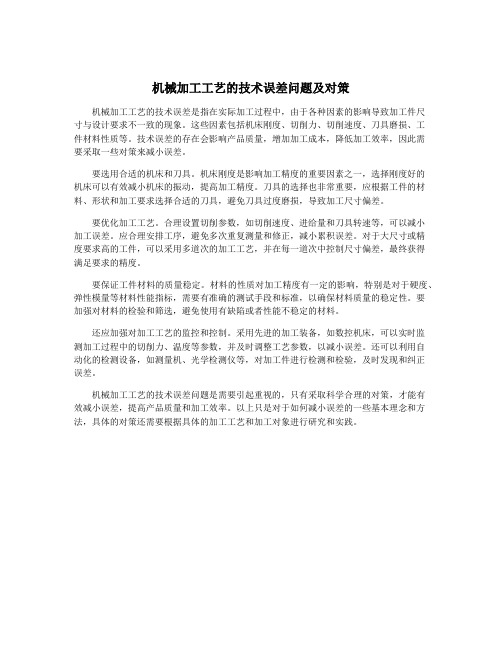
机械加工工艺的技术误差问题及对策机械加工工艺的技术误差是指在实际加工过程中,由于各种因素的影响导致加工件尺寸与设计要求不一致的现象。
这些因素包括机床刚度、切削力、切削速度、刀具磨损、工件材料性质等。
技术误差的存在会影响产品质量,增加加工成本,降低加工效率,因此需要采取一些对策来减小误差。
要选用合适的机床和刀具。
机床刚度是影响加工精度的重要因素之一,选择刚度好的机床可以有效减小机床的振动,提高加工精度。
刀具的选择也非常重要,应根据工件的材料、形状和加工要求选择合适的刀具,避免刀具过度磨损,导致加工尺寸偏差。
要优化加工工艺。
合理设置切削参数,如切削速度、进给量和刀具转速等,可以减小加工误差。
应合理安排工序,避免多次重复测量和修正,减小累积误差。
对于大尺寸或精度要求高的工件,可以采用多道次的加工工艺,并在每一道次中控制尺寸偏差,最终获得满足要求的精度。
要保证工件材料的质量稳定。
材料的性质对加工精度有一定的影响,特别是对于硬度、弹性模量等材料性能指标,需要有准确的测试手段和标准,以确保材料质量的稳定性。
要加强对材料的检验和筛选,避免使用有缺陷或者性能不稳定的材料。
还应加强对加工工艺的监控和控制。
采用先进的加工装备,如数控机床,可以实时监测加工过程中的切削力、温度等参数,并及时调整工艺参数,以减小误差。
还可以利用自动化的检测设备,如测量机、光学检测仪等,对加工件进行检测和检验,及时发现和纠正误差。
机械加工工艺的技术误差问题是需要引起重视的,只有采取科学合理的对策,才能有效减小误差,提高产品质量和加工效率。
以上只是对于如何减小误差的一些基本理念和方法,具体的对策还需要根据具体的加工工艺和加工对象进行研究和实践。
机械加工工艺的技术误差问题及对策
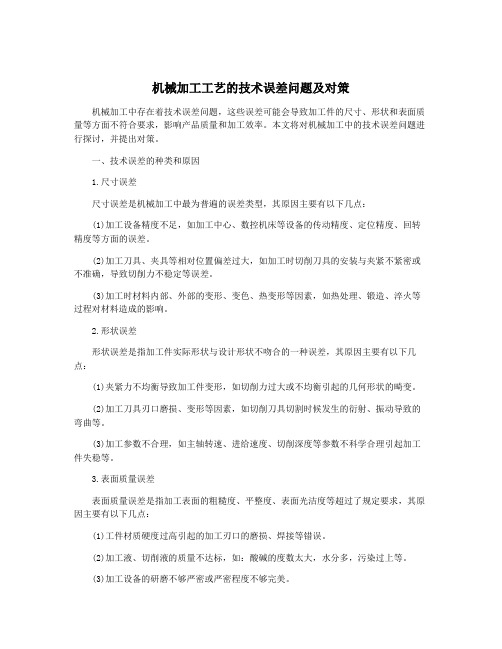
机械加工工艺的技术误差问题及对策机械加工中存在着技术误差问题,这些误差可能会导致加工件的尺寸、形状和表面质量等方面不符合要求,影响产品质量和加工效率。
本文将对机械加工中的技术误差问题进行探讨,并提出对策。
一、技术误差的种类和原因1.尺寸误差尺寸误差是机械加工中最为普遍的误差类型,其原因主要有以下几点:(1)加工设备精度不足,如加工中心、数控机床等设备的传动精度、定位精度、回转精度等方面的误差。
(2)加工刀具、夹具等相对位置偏差过大,如加工时切削刀具的安装与夹紧不紧密或不准确,导致切削力不稳定等误差。
(3)加工时材料内部、外部的变形、变色、热变形等因素,如热处理、锻造、淬火等过程对材料造成的影响。
2.形状误差形状误差是指加工件实际形状与设计形状不吻合的一种误差,其原因主要有以下几点:(1)夹紧力不均衡导致加工件变形,如切削力过大或不均衡引起的几何形状的畸变。
(2)加工刀具刃口磨损、变形等因素,如切削刀具切割时候发生的衍射、振动导致的弯曲等。
(3)加工参数不合理,如主轴转速、进给速度、切削深度等参数不科学合理引起加工件失稳等。
3.表面质量误差表面质量误差是指加工表面的粗糙度、平整度、表面光洁度等超过了规定要求,其原因主要有以下几点:(1)工件材质硬度过高引起的加工刃口的磨损、焊接等错误。
(2)加工液、切削液的质量不达标,如:酸碱的度数太大,水分多,污染过上等。
(3)加工设备的研磨不够严密或严密程度不够完美。
1.选择高精度设备和刀具在进行加工前,要根据所需的工艺要求,选择合适的高精度设备和刀具,如:数控机床、加工中心等,确保设备传动精度、定位精度、回转精度等方面的误差越小越好。
同时,要使用具有高精度、高强度和高耐磨性的刀具,以达到加工精度的要求。
2.严格控制加工参数在进行加工时,要严格控制加工参数,如:主轴转速、进给速度、切削深度等,确保参数的合理科学,能够提高加工效率的同时保证加工质量。
3.优化加工工艺流程在加工过程中,要根据实际情况不断优化工艺流程,及时排查和处理加工中的问题,提高加工质量。
浅议机械加工工艺技术的误差原因及对策

浅议机械加工工艺技术的误差原因及对策机械加工工艺技术在现代制造业中占据着非常重要的位置,具有广泛的应用。
但在实际的生产过程中,由于各种因素的影响,往往会出现误差,影响产品的质量和加工效率。
了解机械加工工艺技术中误差的原因,并采取相应的对策,对于提高产品质量,降低成本,提高生产效率具有重要意义。
本文将从误差的原因和对策两个方面对机械加工工艺技术中的误差进行浅议。
一、误差的原因(一)工艺设计的误差工艺设计是制造产品的第一步,它直接关系到产品的精度和质量。
如果工艺设计存在误差,就会直接影响到产品的加工精度。
常见的工艺设计误差包括:加工尺寸选取不当、刀具路径选取错误、工艺参数设置不合理等。
(二)机床设备的误差机床设备是机械加工的重要工具,其精度和稳定性直接关系到产品的加工精度。
机床设备误差主要包括:机床刚性不足、机床精度不高、机床磨损严重、机床变形等。
(三)刀具磨损刀具是机械加工中的重要工具,其磨损情况会直接影响加工精度。
刀具磨损主要包括:刀尖磨损、刃口刀损、刀脸磨损等。
(四)材料性能材料的物理性能和化学性能对加工精度也有很大的影响。
比如材料硬度不均匀、内应力大等因素都会影响产品的加工精度。
二、对策(一)加强工艺设计在工艺设计过程中,需加强对产品的分析和计算,选取合适的加工尺寸和工艺参数。
提高工艺设计的精度和合理性,减小工艺设计误差对产品加工精度的影响。
(二)提高机床设备精度对于机床设备的精度,需要加强设备的维护与保养,定期检查机床的精度,及时更换磨损严重的零部件,保证机床设备的稳定性和精度。
(三)改善刀具选择和使用选择合适的刀具,并合理安排刀具的使用次序和时间,减小刀具的磨损。
加强对刀具的润滑和冷却,延长刀具的寿命。
及时更换磨损严重的刀具,保证刀具的精度和合理性。
(四)优化材料选取和处理在材料的选取和处理上,需要加强对材料性能的了解和分析,选取质量良好,硬度均匀的材料。
在材料处理过程中,采用合理的热处理和淬火工艺,减小材料的内应力,提高加工精度。
机械加工工艺的技术误差问题及对策

机械加工工艺的技术误差问题及对策机械加工工艺的技术误差是指在加工过程中由于工艺、设备、操作等因素导致的加工尺寸与设计要求之间的偏差。
这些误差会对零件的质量和性能造成不利影响,因此需采取相应的对策来减小误差。
本文将从设备选型、工艺参数控制、工艺改进等方面探讨机械加工工艺的技术误差问题及对策。
一、设备选型方面的对策设备选型是机械加工工艺误差控制的重要方面。
在选购加工设备时,应确保设备的精度、稳定性、刚性等方面符合加工要求,以减小误差的产生。
1.选择精度更高的设备对于要求加工高精度零件的工艺,应选择精度更高的加工设备,如高精度数控机床等,以提高加工精度,并减小误差的产生。
2.选用稳定性较好的设备设备的稳定性对加工精度影响很大。
选用稳定性较好的设备可以减小外界因素(如温度、振动等)对加工精度的影响,降低误差的发生率。
3.考虑设备的刚性刚性是指设备在加工过程中承受载荷时变形程度的能力。
设备刚性好,能够更好地抵抗加工过程中的振动和变形,从而提高加工精度,降低误差的发生。
二、工艺参数控制方面的对策控制合理的工艺参数是减小机械加工工艺误差的关键,下面将从切削速度、进给量、切削深度等角度分析工艺参数的控制对策。
1.合理控制切削速度切削速度是指加工过程中工件与刀具相对运动的速度。
切削速度的选择要根据加工材料的硬度、材料的切削性能以及机床和刀具的性能等因素综合考虑。
如果切削速度过快,容易导致刀具寿命下降,加工表面质量下降,误差增大;而切削速度过慢,则不仅会影响生产效率,还容易产生负载过重等问题。
在实际加工过程中要根据具体情况调整切削速度,以确保加工精度。
三、工艺改进方面的对策工艺改进是减小机械加工工艺误差的重要手段。
通过改进现有的工艺流程、技术手段来减小误差的产生,提高加工精度。
1.优化工艺流程通过优化加工工艺流程,合理安排加工顺序,避免二次调整导致误差的累积。
合理的工艺流程有助于提高加工效率,降低误差的发生率。
2.改进工艺技术手段利用先进的数控技术、自动化技术以及传感技术等,改进加工工艺技术手段,提高机床的加工精度,减小误差的产生。
机械加工工艺的技术误差问题及对策

机械加工工艺的技术误差问题及对策【摘要】在机械加工工艺中,技术误差问题是一个不可避免的挑战。
本文从机械加工中的技术误差问题、影响因素分析、误差对策措施、提高加工精度的方法和常见的误差修正工艺等方面进行了探讨。
通过对误差问题的深入分析,提出了一些应对策略和加工精度提升的方法。
在结论部分指出了技术误差问题的重要性和未来发展趋势,并对整个内容进行了总结。
通过本文的研究,可以更好地理解和解决机械加工中的技术误差问题,从而提高加工的精度和效率。
未来,随着科技的发展和工艺不断的优化,机械加工工艺将有望取得更大的进步。
【关键词】机械加工工艺、技术误差、影响因素、误差对策、加工精度、误差修正、重要性、发展趋势、总结。
1. 引言1.1 背景介绍在现代制造业中,机械加工工艺是一项至关重要的技术。
通过机械加工,我们可以将原材料加工成各种零部件,从而制造出各种产品。
在机械加工过程中,技术误差问题往往是一个不可忽视的挑战。
技术误差指的是加工过程中产生的偏差,影响加工精度和质量。
随着现代工业的发展和对产品精密度要求的提高,技术误差问题变得越来越突出。
这不仅影响了产品的质量和性能,还增加了生产成本和时间。
解决技术误差问题,提高加工精度,成为了制造业中亟待解决的重要问题。
本文将深入探讨机械加工中的技术误差问题,分析误差产生的影响因素,提出误差对策措施,并总结常见的误差修正工艺。
我们还将探讨如何提高加工精度的方法,并展望未来技术误差问题的发展趋势。
通过本文的研究,希望能为解决机械加工工艺中的技术误差问题提供一些思路和启发。
2. 正文2.1 机械加工中的技术误差问题机械加工中的技术误差问题是影响加工质量的重要因素之一。
在加工过程中,由于各种原因导致的误差会直接影响到工件的精度和表面质量,甚至可能导致加工失败。
深入了解和解决技术误差问题对于提高加工质量和效率至关重要。
机械加工中常见的技术误差问题包括尺寸误差、形状误差、位置误差和表面质量误差等。
机械加工工艺的技术误差问题及对策分析

机械加工工艺的技术误差问题及对策分析一、引言机械加工工艺是制造行业中非常重要的一环,其质量直接影响到产品的性能和质量。
在机械加工过程中难免会出现技术误差,导致产品不符合设计要求,甚至影响到产品的使用效果。
对于机械加工工艺中的技术误差问题需要进行深入的分析,并提出相应的对策,以保证产品质量和生产效率。
二、机械加工工艺中的技术误差问题在机械加工过程中,技术误差是不可避免的。
技术误差主要包括以下几个方面:1. 设备精度误差机械加工设备的精度直接影响到产品加工的精度。
如果设备本身存在精度误差,那么加工出的产品也会存在相应的误差。
数控机床的定位精度、刀具的磨损、传动件的松动等都会导致产品加工精度下降。
2. 刀具磨损在机械加工中,刀具是直接与工件接触的工具,其磨损会直接影响到产品的加工精度。
如果刀具磨损严重,就会导致产品表面粗糙、尺寸偏差等问题。
3. 工序误差机械加工通常是由多道工序组成的,每个工序都会对产品加工精度产生影响。
如果某个工序出现误差,就会传导到整个加工过程中,导致产品精度下降。
4. 材料性能误差在机械加工中,材料的硬度、韧性、延展性等性能会直接影响到产品的加工精度。
如果材料性能不稳定,就会导致产品加工精度难以保证。
以上这些技术误差问题都会影响到产品的加工精度和质量,甚至导致产品无法使用。
对于这些技术误差问题需要有针对性地进行分析,并提出相应的对策分析。
三、对策分析针对机械加工工艺中的技术误差问题,可以采取以下对策进行解决:1. 提高设备精度首先要解决的是设备精度误差问题。
可以通过定期对设备进行维护和保养,及时更换损坏的零部件,来保证设备的精度。
现代化的数控机床可以通过自动补偿来修正设备误差,提高加工精度。
2. 优化刀具管理刀具的磨损是导致产品加工精度下降的重要原因之一。
可以通过建立刀具管理制度,定期检查刀具的磨损情况,及时更换磨损严重的刀具,以保证产品加工精度。
3. 加强工序管理针对工序误差问题,可以通过加强工序管理来减少误差的传导。
机械加工工艺的技术误差问题及对策

机械加工工艺的技术误差问题及对策机械加工工艺是制造行业中非常重要的一环,它直接关系到产品的质量和精度。
在实际的生产中,技术误差问题往往会给机械加工工艺带来很大的困扰,影响产品的质量和生产效率。
本文将就机械加工工艺中的技术误差问题及对策进行分析和探讨。
一、技术误差问题的表现及原因分析1. 表现:产品尺寸精度不高、表面粗糙度大、工件形状偏差严重、工艺加工难度大等。
2. 原因分析:a. 机床精度不高:机床是机械加工的核心设备,如果机床自身精度不足,就会影响到加工工艺的准确性。
b. 加工工艺参数不合理:包括切削速度、进给速度、切削深度、刀具选择等参数,如果设定不合理,就会导致技术误差的产生。
c. 加工材料质量不良:原材料的质量直接关系到最终产品的质量,如果原材料质量不良,也会导致技术误差问题的产生。
d. 刀具磨损严重:刀具的使用磨损会导致加工质量下降,形成技术误差。
二、对策建议1. 优化机床精度a. 更新机床设备:选择高精度、高稳定性的机床设备,能够有效地提高加工精度和准确性。
b. 定期维护保养:对机床设备进行定期的维护保养和检修,确保设备处于最佳工作状态。
2. 合理设置加工工艺参数a. 充分了解加工工艺的原理和特点,结合实际情况调整加工参数,确保每一个参数的设置都是合理、科学的。
b. 对于不同的材料和工件,要进行适当的加工试验,找出最佳的加工工艺参数。
3. 严格把控原材料质量a. 选用优质原材料:要求原材料供应商提供质量可靠的原材料,以确保产品的质量稳定性。
b. 加强原材料验收:对进厂的原材料进行全面的检验和验收,发现质量问题及时退货处理。
4. 合理选择和使用刀具a. 选择合适的刀具:根据加工材料和要求,选择合适的刀具,确保刀具的切削性能和寿命。
b. 定期更换刀具:对刀具进行定期的检查和更换,确保刀具的磨损程度符合加工要求,避免因刀具磨损产生技术误差。
5. 完善质量管理体系a. 建立健全的产品质量管理体系,包括从原材料采购到生产制造的全过程质量管控。
机械加工工艺技术的误差及改善对策

机械加工工艺技术的误差及改善对策机械加工工艺技术是机械加工过程中最关键的环节之一,其误差会直接影响到工件的质量和精度。
因此,了解机械加工工艺技术的误差及改善对策对于提高机械加工质量和效率非常重要。
本文将从机械加工工艺技术误差的原因、表现和改善对策等方面进行探讨。
1、工艺参数设置不合理。
机械加工工艺参数的设置不合理是导致误差的主要原因之一。
例如,切削刀具刃口的刃角、刀具半径、送进量、转速、进给速度等参数设置不当,都会影响到加工精度。
2、机床系统误差。
机床本身的结构和精度也会影响到加工精度。
例如,机械加工中常用的滑动导轨、转子轴承等部件工作时会产生磨损,使其原有的精度产生偏差,从而影响到加工质量。
3、切削力和切削温度的影响。
在加工过程中,切削力和切削温度会引起工件表面的变形和热应力,从而导致工艺误差。
1、表面粗糙度偏大。
表面粗糙度是评价工件加工质量的一个重要指标。
当工艺技术误差较大时,工件表面粗糙度会明显偏大。
3、形状偏差过大。
形状偏差是工件实际形状与理论形状之间的差异。
当工艺技术误差较大时,工件的形状偏差也会明显偏大。
1、合理选择刀具和夹具。
选择合适的切削刀具和夹具可以降低工艺误差。
例如,使用高质量的切削刀具和夹具可以减小切削力和切削温度,从而降低工艺误差。
2、合理选择工艺参数。
合理选择工艺参数可以降低工艺误差。
例如,根据工件的材料和性质来选择合适的转速、进给速度、切削深度等参数,可以提高加工精度。
3、加强机床维护和保养。
加强机床维护和保养可以减小机床系统误差,提高机床的精度和稳定性。
例如,定期检查和更换滑动导轨和轴承等部件,可以减小机床系统误差,提高加工精度和稳定性。
4、采用新型技术和工艺。
采用新型的加工工艺和技术可以提高加工精度和效率。
例如,采用数控加工技术可以提高加工精度和自动化程度,减小工艺误差。
综上所述,机械加工工艺技术的误差及改善对策是提高机械加工质量和效率的重要手段。
机械加工工艺技术的误差是由多种因素造成的,合理选择刀具和夹具、合理选择工艺参数、加强机床维护和保养、采用新型技术和工艺等措施都可以降低工艺误差,提高加工质量和效率。
机械加工工艺的技术误差问题及对策分析
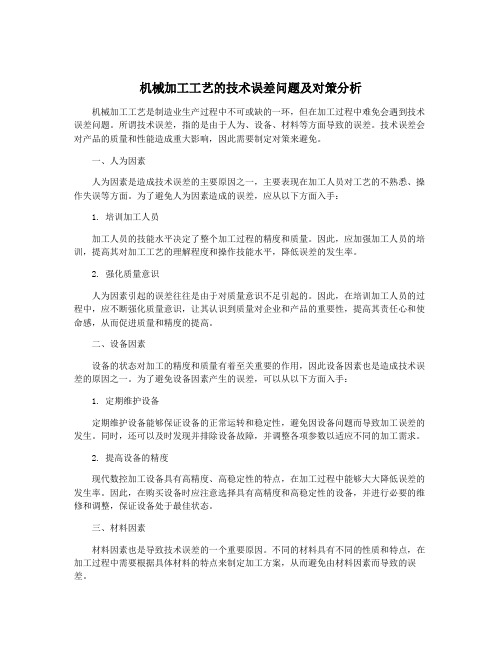
机械加工工艺的技术误差问题及对策分析机械加工工艺是制造业生产过程中不可或缺的一环,但在加工过程中难免会遇到技术误差问题。
所谓技术误差,指的是由于人为、设备、材料等方面导致的误差。
技术误差会对产品的质量和性能造成重大影响,因此需要制定对策来避免。
一、人为因素人为因素是造成技术误差的主要原因之一,主要表现在加工人员对工艺的不熟悉、操作失误等方面。
为了避免人为因素造成的误差,应从以下方面入手:1. 培训加工人员加工人员的技能水平决定了整个加工过程的精度和质量。
因此,应加强加工人员的培训,提高其对加工工艺的理解程度和操作技能水平,降低误差的发生率。
2. 强化质量意识人为因素引起的误差往往是由于对质量意识不足引起的。
因此,在培训加工人员的过程中,应不断强化质量意识,让其认识到质量对企业和产品的重要性,提高其责任心和使命感,从而促进质量和精度的提高。
二、设备因素设备的状态对加工的精度和质量有着至关重要的作用,因此设备因素也是造成技术误差的原因之一。
为了避免设备因素产生的误差,可以从以下方面入手:1. 定期维护设备定期维护设备能够保证设备的正常运转和稳定性,避免因设备问题而导致加工误差的发生。
同时,还可以及时发现并排除设备故障,并调整各项参数以适应不同的加工需求。
2. 提高设备的精度现代数控加工设备具有高精度、高稳定性的特点,在加工过程中能够大大降低误差的发生率。
因此,在购买设备时应注意选择具有高精度和高稳定性的设备,并进行必要的维修和调整,保证设备处于最佳状态。
三、材料因素材料因素也是导致技术误差的一个重要原因。
不同的材料具有不同的性质和特点,在加工过程中需要根据具体材料的特点来制定加工方案,从而避免由材料因素而导致的误差。
1. 调整加工方案不同材料在加工过程中需要采取不同的加工方案。
因此,在加工前应充分了解材料的性质和特点,制定适合材料特点的加工方案,从而提高加工的精度和质量。
2. 选择优质材料优质的材料能够在加工过程中更好地保证产品质量和精度。
机械加工工艺技术的误差及改善对策
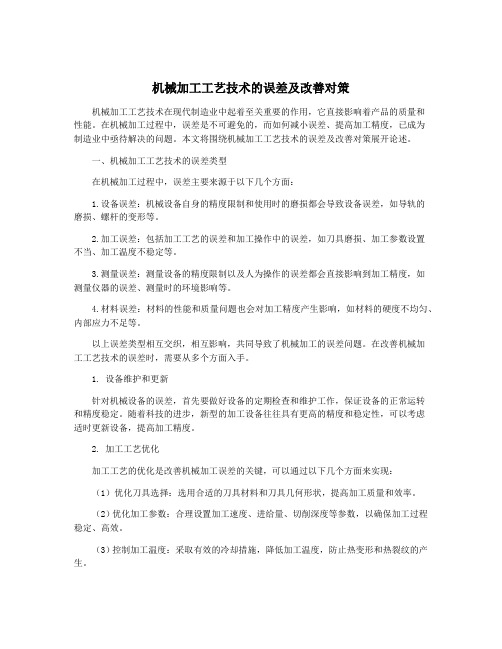
机械加工工艺技术的误差及改善对策机械加工工艺技术在现代制造业中起着至关重要的作用,它直接影响着产品的质量和性能。
在机械加工过程中,误差是不可避免的,而如何减小误差、提高加工精度,已成为制造业中亟待解决的问题。
本文将围绕机械加工工艺技术的误差及改善对策展开论述。
一、机械加工工艺技术的误差类型在机械加工过程中,误差主要来源于以下几个方面:1.设备误差:机械设备自身的精度限制和使用时的磨损都会导致设备误差,如导轨的磨损、螺杆的变形等。
2.加工误差:包括加工工艺的误差和加工操作中的误差,如刀具磨损、加工参数设置不当、加工温度不稳定等。
3.测量误差:测量设备的精度限制以及人为操作的误差都会直接影响到加工精度,如测量仪器的误差、测量时的环境影响等。
4.材料误差:材料的性能和质量问题也会对加工精度产生影响,如材料的硬度不均匀、内部应力不足等。
以上误差类型相互交织,相互影响,共同导致了机械加工的误差问题。
在改善机械加工工艺技术的误差时,需要从多个方面入手。
1. 设备维护和更新针对机械设备的误差,首先要做好设备的定期检查和维护工作,保证设备的正常运转和精度稳定。
随着科技的进步,新型的加工设备往往具有更高的精度和稳定性,可以考虑适时更新设备,提高加工精度。
2. 加工工艺优化加工工艺的优化是改善机械加工误差的关键,可以通过以下几个方面来实现:(1)优化刀具选择:选用合适的刀具材料和刀具几何形状,提高加工质量和效率。
(2)优化加工参数:合理设置加工速度、进给量、切削深度等参数,以确保加工过程稳定、高效。
(3)控制加工温度:采取有效的冷却措施,降低加工温度,防止热变形和热裂纹的产生。
3. 测量技术提升提高测量设备的精度和稳定性,采用先进的测量技术,如激光测量、光学测量等,保证对加工精度的准确测量和监控。
4. 材料选择与处理在选择材料时,应根据产品的要求和加工工艺的特点,选择适合的材料,以降低加工误差的可能性。
对于材料的处理也要严格控制,避免在加工过程中产生不均匀的硬度、残余应力等问题。
浅议机械加工工艺技术的误差原因及对策

浅议机械加工工艺技术的误差原因及对策机械加工工艺技术是指在机械加工过程中,通过一系列的工艺技术来保证加工件的尺寸精度、表面质量和形位公差的要求。
在实际的加工过程中,由于各种原因导致的误差问题时有发生,严重影响了加工件的质量。
了解机械加工工艺技术的误差原因及对策对于提高加工质量和效率具有重要意义。
一、误差产生的原因1. 设计和加工图纸的问题:加工工艺技术中的误差有时候源自于设计图纸或者加工图纸的问题。
如果设计中的尺寸有误或者是因为缺陷塌陷引起的,那么在加工过程中就会存在很大的误差,设计图纸和加工图纸的准确性对于机械加工工艺技术是至关重要。
2. 加工设备的精度问题:机加工设备的精度对于加工质量有着重要的影响。
如果加工设备的精度不高,那么加工出来的零件就会存在一定的误差。
必须要保证加工设备的精度和稳定性,才能够保证加工零件的质量。
3. 刀具磨损和刀具的使用寿命:在机械加工工艺技术中,刀具的磨损和使用寿命是一个非常重要的因素。
如果刀具的磨损严重或者是使用寿命到了,那么在加工过程中就会导致零件的误差。
要保证刀具的磨损和寿命是非常重要的。
4. 加工工艺参数的选择:在机械加工工艺技术中,加工工艺参数的选择对于加工精度有着非常重要的影响。
如果加工工艺参数选择不当,就会导致零件出现误差。
加工工艺参数的选择是需要非常慎重的。
5. 加工人员的技术水平:加工人员的技术水平也是影响加工质量的一个重要因素。
如果加工人员的技术水平不高,那么在加工过程中就会出现很多的误差。
提高加工人员的技术水平是非常重要的。
二、对策的建议1. 完善设计和加工图纸:加工零件之前,需要对设计图纸和加工图纸进行认真审核,确保图纸的准确性和完整性,避免因设计和加工图纸的问题引起误差。
2. 提高加工设备的精度和稳定性:保养加工设备,定期维护和保养加工设备,提高加工设备的使用寿命和精度,确保加工设备的精度和稳定性。
3. 确保刀具的质量和使用寿命:选择优质的刀具材料,正确使用和保养刀具,确保刀具的质量和使用寿命,减少刀具磨损造成的误差。
机械加工工艺技术的误差及改善对策
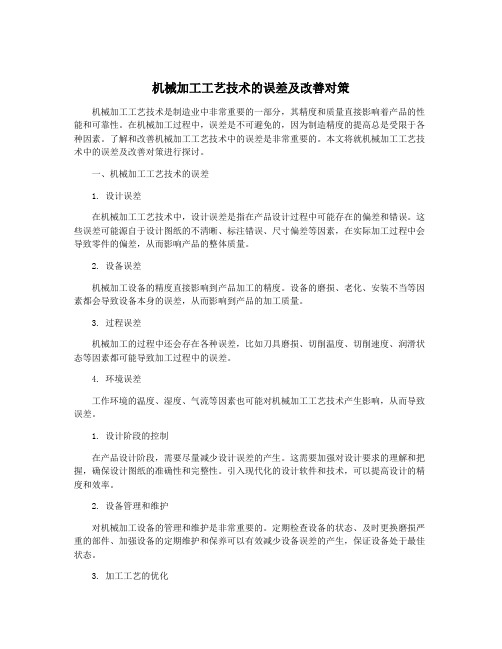
机械加工工艺技术的误差及改善对策机械加工工艺技术是制造业中非常重要的一部分,其精度和质量直接影响着产品的性能和可靠性。
在机械加工过程中,误差是不可避免的,因为制造精度的提高总是受限于各种因素。
了解和改善机械加工工艺技术中的误差是非常重要的。
本文将就机械加工工艺技术中的误差及改善对策进行探讨。
一、机械加工工艺技术的误差1. 设计误差在机械加工工艺技术中,设计误差是指在产品设计过程中可能存在的偏差和错误。
这些误差可能源自于设计图纸的不清晰、标注错误、尺寸偏差等因素,在实际加工过程中会导致零件的偏差,从而影响产品的整体质量。
2. 设备误差机械加工设备的精度直接影响到产品加工的精度。
设备的磨损、老化、安装不当等因素都会导致设备本身的误差,从而影响到产品的加工质量。
3. 过程误差机械加工的过程中还会存在各种误差,比如刀具磨损、切削温度、切削速度、润滑状态等因素都可能导致加工过程中的误差。
4. 环境误差工作环境的温度、湿度、气流等因素也可能对机械加工工艺技术产生影响,从而导致误差。
1. 设计阶段的控制在产品设计阶段,需要尽量减少设计误差的产生。
这需要加强对设计要求的理解和把握,确保设计图纸的准确性和完整性。
引入现代化的设计软件和技术,可以提高设计的精度和效率。
2. 设备管理和维护对机械加工设备的管理和维护是非常重要的。
定期检查设备的状态、及时更换磨损严重的部件、加强设备的定期维护和保养可以有效减少设备误差的产生,保证设备处于最佳状态。
3. 加工工艺的优化通过科学的加工工艺优化,可以减小加工误差。
选择合适的刀具、合理的切削参数、优化的切削路径等都可以提高加工的精度和质量。
4. 环境控制合理控制加工环境的温度、湿度等参数,尽量减小外界因素的干扰,有利于提高加工精度。
5. 质量管理加强对产品质量的检测和控制是非常重要的。
建立科学的质量管理体系,进行全面的质量监控,可以及时发现问题,并采取有效的措施进行改进。
6. 人员培训加强对操作人员的培训和管理,提高其对加工工艺技术的理解和掌握,有利于减小人为因素对产品加工的影响。
机械加工工艺的技术误差问题及策略分析

机械加工工艺的技术误差问题及策略分析想保证机械加工零部件的精密度,就必须要严格对待机械加工工艺的技术误差问题,因为一些误差问题的出现对零部件的质量问题会造成直接的影响,甚至影响未来机械加工行业的发展。
因此,相关的机械制造人员对于在加工制造过程中出现的误差问题,要具体分析其产生的原因,并采取合理的解决措施,使误差发生的情况尽可能的减少,进而提高了零件的精确度,提升了产品的质量,同时也促进了我国机械加工制造业未来在国际社会上的发展。
标签:机械加工工艺;技术误差;解决对策一、引起机械加工工艺的技术误差原因分析1.定位过程中的误差在机械加工工艺流程中,在机器的具体定位环节,很容易出现误差问题。
零件在定位过程中出现误差问题一般会有两种表现情况,首先就是基准的重合出现偏差,其次就是定位副的加工不准。
所以要想保证机器加工的精密性,在零部件的加工过程中就务必要重视各仪器的具体定位环节,尤其是基准的重合和定位副的加工情况。
对于基准的重合情况,要选择科学合理的几何要素,如果之前设计的基准线与重新定位的基准出现偏差,要具体分析现场情况,避免出现基准不吻合的现象。
定位副的加工不准,比如定位副之间或制造的配合方面出现偏差就会造成机器设备的不准确,这种情况一般会在调整法进行零件加工制造的过程中出现。
2.机床制造过程中的误差在机器生产机床的过程中,如果操作不当很容易出现误差问题,尤其导轨的误差现象。
导轨制作安装过程的精确性是保证机床顺利正常使用的前提,因为机床多数部件的具体位置和相对运动都是以导轨为基准的,所以导轨安装过程的精密性是机床制作的关键关注点。
在机械加工过程中机床出现导轨误差主要表现就是导轨安装过程中出现角度偏差,比如前后不同的导轨在同一个垂直面内出现平行度的偏差,或者水平面和垂直面的导轨出现垂直偏差。
此外,机床制造过程中还会出现其他误差问题,比如在平时机器运行过程中,传送链被不停的磨损,就会影响后期的运转,进而产生了传送链误差。
机械加工工艺的技术误差问题及对策
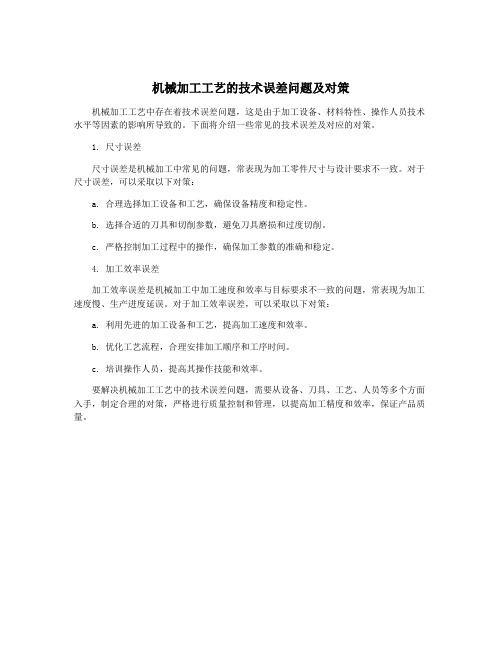
机械加工工艺的技术误差问题及对策
机械加工工艺中存在着技术误差问题,这是由于加工设备、材料特性、操作人员技术水平等因素的影响所导致的。
下面将介绍一些常见的技术误差及对应的对策。
1. 尺寸误差
尺寸误差是机械加工中常见的问题,常表现为加工零件尺寸与设计要求不一致。
对于尺寸误差,可以采取以下对策:
a. 合理选择加工设备和工艺,确保设备精度和稳定性。
b. 选择合适的刀具和切削参数,避免刀具磨损和过度切削。
c. 严格控制加工过程中的操作,确保加工参数的准确和稳定。
4. 加工效率误差
加工效率误差是机械加工中加工速度和效率与目标要求不一致的问题,常表现为加工速度慢、生产进度延误。
对于加工效率误差,可以采取以下对策:
a. 利用先进的加工设备和工艺,提高加工速度和效率。
b. 优化工艺流程,合理安排加工顺序和工序时间。
c. 培训操作人员,提高其操作技能和效率。
要解决机械加工工艺中的技术误差问题,需要从设备、刀具、工艺、人员等多个方面入手,制定合理的对策,严格进行质量控制和管理,以提高加工精度和效率,保证产品质量。
机械加工工艺的技术误差问题及对策

机械加工工艺的技术误差问题及对策
机械加工中存在着各种技术误差,这可能导致制造的产品不符合设计要求,甚至无法
正常使用。
因此,及时识别和解决这些问题是至关重要的。
以下是机械加工工艺的技术误
差问题及对策。
1.刀具磨损:经过一段时间的使用,刀具会出现磨损,导致削减效果下降,精度降低。
为了避免这种情况,应在加工前检查刀具磨损情况,及时更换磨损的刀具。
2.加工时的振动:在机械加工过程中,机床、刀具和工件之间的振动会影响加工精度。
解决振动问题的方法是通过减少振动源、改进加工参数等途径去除振动。
3.加工跳动误差:金属切削加工时,切削刀具可能产生跳动。
跳动是由于切削刀具自
身质量、切削参数、材料硬度及其他因素所导致的。
为了避免跳动,在选择刀具时应选用
高质量、重量均匀的刀具,调整加工参数。
4.加工后产生的弯曲误差:当材料制成薄片或长条形时,它们可能出现弯曲,得到不
良收率。
为了避免弯曲,可以选择适当的夹具或支承手段,或调整加工参数。
另外,应避
免产生过大的加工剩余量。
5.温度误差:机械加工时,材料的温度还是一个重要因素。
材料的变形受到温度的影响。
普通材料加工时,它们常常在常温下进行处理。
但是特殊材料(如高温合金)加工时需
要考虑温度问题。
一种解决方案是采用冷却剂,同时工件加工前要先进行预热。
总之,在机械加工中,要时刻注意各种技术误差,以保证制造出高质量、精度符合要
求的产品。
正确的加工参数选择、刀具的磨损检查、加工过程振动的消除等措施是保证加
工质量的重要手段。
- 1、下载文档前请自行甄别文档内容的完整性,平台不提供额外的编辑、内容补充、找答案等附加服务。
- 2、"仅部分预览"的文档,不可在线预览部分如存在完整性等问题,可反馈申请退款(可完整预览的文档不适用该条件!)。
- 3、如文档侵犯您的权益,请联系客服反馈,我们会尽快为您处理(人工客服工作时间:9:00-18:30)。
D01:10.19392/ki.1671-7341.201718148论我国机械加工工艺中存在的技术误差问题及对策分析
杨柠嘉
沈阳大学辽宁沈阳110044
摘要:机械加工工艺技术精度影响着机械产品的质量和使用性能,机械加工工艺的技术误差是影响我国机械行业进步的重 要条件。
本文对机械加工行业生产工艺中经常存在的技术误差进行了总结和归纳,并针对具体误差提出了应对控制对策,望能对 机械加工行业的发展和进步提供一定的借鉴。
关键词:机械加工;工艺;技术;误差
科技风2〇17年9月下_________________________________________________________________________________机械化工
近年来,我国社会经济发展水平不断提高,机械工业迅猛崛起,机械产品种类繁多,层出不穷,广泛应用于各行各业。
而随着机械工业产品及产量不断提高,机械产品的工艺精度和质量要求不断受到人们的重视。
当代机械加工企业多数采用生产线作业,工艺技术精度直接影响着产品的质量及性能。
因此,研究和分析技术工艺的误差产生原因,并找出有针对性的控制和减缓对策,对于促进机械行业生产效率的提升、推动机械工业快速发展的有着重要的意义。
i工艺技术误差分类及原因分析
机械加工生产过程中,工艺技术误差主要分为以下几种。
1.1定位误差
在实际加工生产过程中,定位误差出现,主要是由于工艺技术人员在操作过程中忽视了定位基准的重要性,没有确定正确的几何要素。
工艺技术人员确定的基础与预先设定的设计基础之间存在偏差,导致基准误差的出现。
由于定位副间的配合间隙发生了变动,因此,机械加工工艺的定位副加工就会出现不同程度的误差问题[1]。
定位误差很容易导致制造的机械产品出现配合变动,即定位副的机械加工出现了误差不准确问题[1]。
1.2机床制造误差
机床制造误差主要是指工件的位置与运行基准之间存偏差。
机床制造误差又可分为传动链误差、导轨误差以及主轴回转误差等[2]。
机械加工过程中,传动链不断运转,始终处于磨损状态,其误差直接影响着机械产品制造和装配质量。
导轨误差的主要是运行基准与主要工件的位置出现偏差,这就导致机床成形的精度降低。
主轴回转的误差主要原因是主轴实际回转轴线与平均回转轴线间出现的差异,这也会影响零件的工艺精度。
1.3加工器具误差
加工器具误差在机械加工中较为常见,最直观的体现是刀具与夹具误差。
导致加工器具的误差发生的原因有以下两个方面:①加工器具在使用过程中不可避免的产生一定的磨损,这些磨损会降低机械产品的生产精度和质量。
例如,刀具的磨损会导致生产出的产品的尺寸和形状达不到预想的设计要求,而产品的建工位置与夹具的使用情况有关,如果夹具出现磨损,生产加工时,产品位置就会产生一定的变动,由此便产生了几何误差;②机械行业使用的加工器具多种多样,材质、型号千差万别,也会使生产的机械产品呈现一定的差异。
1.4变形后的工艺系统误差
当加工的机械产品的强度低于机床、加工器具的强度时,则很容易使器具发生形变。
这种因形变导致的误差是机械加工中常见的现象。
例如,但加工直径较小的机械产品时,如果刀杆强度低,很易导致刀杆在加工过程中产生不同程度的变形,致使产品的加工精度和质量降低。
而外圆车刀的硬度相对较高,其生产过程形变较小,其导致的误差也较小,基本可忽略,从而保证了产品的精度和质量。
另外材质均匀程度、加工切削力度的调整均会增加器具变形后的工艺系统误差的产生几率[3]。
2减少机械加工工艺技术的误差的对策分析
2.1严格遵循生产原则
在机械产品加工生产过程中,加工顺序应遵循一定的原则,如“基准先行”、“先粗后精”、“先主后次”、“先面后孔”等。
应尽量选择多表面加工的基准,确保加工表面具有良好的位置精度,减少定位误差的产生,同时,也应尽量使设计基准和定位基准重合,减少误差的产生。
2.2减少生产加工的直接误差
事实上,某些直接误差是可以通过一定的方法来降低的,而且在众多方法中,减少直接误差是相对简单易学,操作成本比较低的方法,在行业内应用也最为广发。
在实际加工过程中,工艺技术人员应明确技术误差产生原因,高度重视每个生产环节,要根据实际机械产品类型及所处生产作业条件,来对具体操作进行适当的调整,及时修复和改善误差。
例如,机械加工过程中,机械运转和摩擦,会释放大量的热量,而热量和力度的变化很容易造成轴车形变,此时,可以采取轴车对切、走刀反方向为对切的方法来缓解,利用弹簧性能来防止轴车形变。
由此可见,加工生产过程中,遵循一定控制策略可以有效减少直接误差,不改变原有机械加工状态,有效降低技术误差对产品精度和质量的不良影响。
2.3填补和补偿误差
技术误差也可以通过误差填补和补偿的方式来有效的降低。
所谓填补和补偿,就是对机械加工误差产生的原因加以分析和研究,然后通过适当增加材料的方法来进行误差填补和补偿,进而降低零件加工误差[4],即通过人为有意识的制造一定的新误差,来平衡加工过程中的原始误差,是二者互相抵消。
例如,数控机床的滚珠丝杆螺距经常因磨损而小于标准值,此时,可以补偿装配时预加拉伸力,利用正应力补偿误差,降低误差影响所带来的影响[4]。
2.4减少温度变形
机械加工会产生热量,大量的热就会导致设备产生受热变形,导致误差产生。
机床热变形是机械工艺技术误差产生的途径之一。
此时,要对其进行控制,降低机床设备的温度,通常可以采取以下几种种方式加以缓解:①切断或减少机床和热源之间联系;②使用润滑剂减少摩擦热量的产生;③采用冷却液进行设备冷却;④安装散热装置。
2.5合理利用误差分组
所谓误差分组法,就是将工件进行分组,主要依据是工件尺寸的不同和工艺技术误差的大小,这样有利于缩小每组的平均误差,后续再根据实际情况进行适当的调整,尽量缩小整体误差。
3结语
总之,机械加工工艺的技术误差影响着机械设备的精准性,决定着产品质量和和外观精度。
为控制和避免工艺技术误差的影响,加工生产过程中,相关工艺技术人员要注意工艺技术误差产生的原因,有针对性的采取有效的控制对策来降低误差所带来的影响,保证产品精度和质量。
参考文献:
[1]吴生宁.机械加工工艺的技术误差及对策分析[V.中国科技投资,2017(2).
[2]李帅.机械加工工艺技术的误差与原因探究[J].硅谷,2015(2) +151-152.
[3 ]曹津炼.机械加工工艺技术的误差与原因探究[J].科 技与创新,2015(3 )+142.
[4 ]张金平.浅谈机械加工工艺中的技术误差问题[J].科 技创新与应用,2016(31)+160.
175。